Thierry Caussat
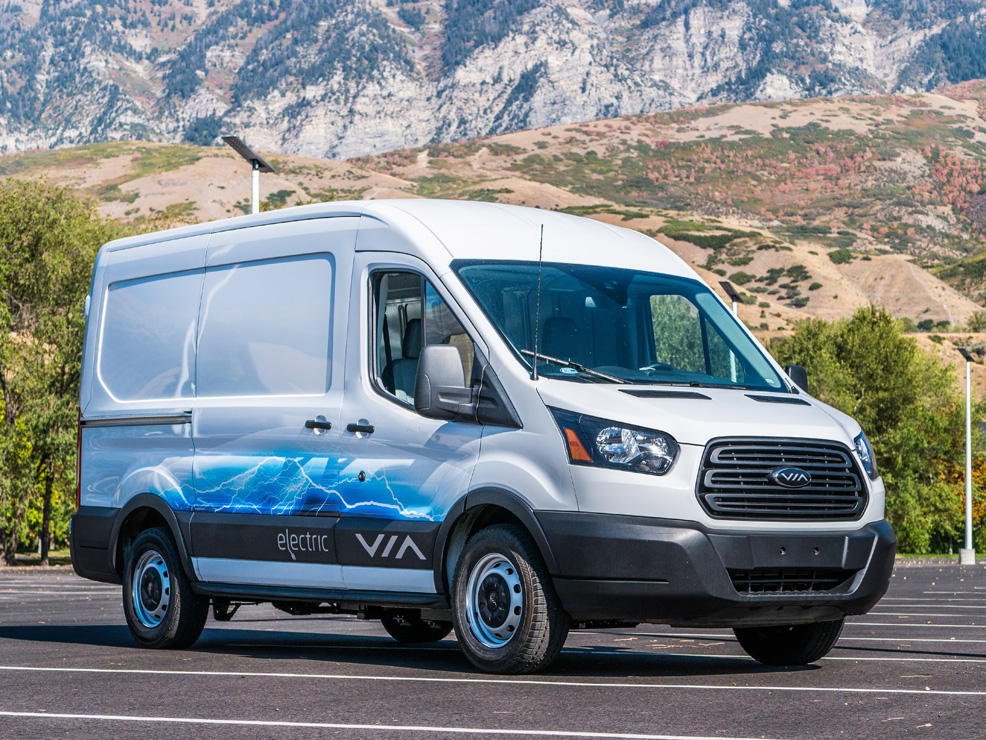
(Images courtesy of VIA Motors)
The next generation – VIA Motors’ CTO takes Rory Jackson through the company’s series of advances towards fully electric mobility solutions.
The next generation
Throughout his childhood in Toulouse, France, Thierry Caussat could often hear the sound of Airbus’ Concorde airliners screaming across the sky. The sound of high-tech engineering incarnate, as he interpreted it, was always overhead. Now the CTO of Utah based VIA Motors, this has stayed a constant in his life.
“To be near high-tech projects felt natural to me, and visiting cities where there weren’t sights or sounds of engineering would feel strange, so of course I pursued engineering through to my higher education,” he recounts. “As a teenager, my professor recognised my interest in engineering early on and encouraged me to pursue my studies further, which led me to earning a range of diplomas, extending to a PhD in electrotechnics.”
In addition to extensive studies of electrical engineering theory during that time, Caussat also built up about six years of practical experience as a technician for automation and robotics. The work entailed developing and optimising algorithms for electrical machine control systems, amassing the technical knowledge and skills that would serve him well in his professional career.
He continues, “One of the companies I worked for was Leroy-Somer, which builds industrial induction motors and motor inverters to drive them. I contributed to an array of new technologies they wanted to implement in their inverters, particularly algorithms for driving motors more efficiently and intelligently.”
“For my PhD, I developed autocalibration software to enable their inverters to identify the parameters of machines on the fly and alter their performance as needed. The whole thing was organised through the National Lab at ENSEEIHT in Toulouse, whose professors are always looking for students with potential, to encourage them to take their studies and research further. So I learned from the university, carried out r&d at the National Lab, and transferred technological competencies to Leroy-Somer.
“After that, I worked for Valeo, a Tier 1 supplier to automotive companies in France for many years.”
Early electric automotive projects
“My first major project with Valeo was as a software developer engineering a butterfly wiper system. We replaced the large and complex mechanical butterfly system with two simple electric motors and a detailed algorithm that tracked the wipers’ trajectories.”
Precise and consistent electronic wiper control was a safety-critical imperative for the team, as wipers failing during rainstorms could pose a major hazard for the vehicle’s driver and passengers. Because of this, at one point Caussat’s software contained more lines of code for the safety and redundancy of the wipers than it did for actually controlling them. After three years of working with the butterfly systems, he moved to work at Valeo Electronic as a software development engineer in its Expert Centre, where his primary task was inspecting different Valeo branches and determining if their software met the standards established by himself and his colleagues.
“Based on what I saw and studied there, I started to change the way I thought about electrical systems,” he says. “In the 1990s, it was more common to write code for a system’s software while the system architecture was still being developed, so engineers could be a bit all over the place during development. Back then, we’d write direct and extensive instructions deep into microcontrollers so we could maximise our utility from them, as they were much more expensive at the time.
“It’s a far cry from how the control team works at VIA today though. Even programming in C and checking it in the compiler is becoming a thing of the past; more and more often we’ll work primarily using model-based design, to simplify the process of making complex algorithms.
“However, the systems approach and holistic mapping out of functions experience I acquired at Valeo was not in vain, as I have since applied them to VIA’s engineering methodology, resulting in a powerful and efficient process that allows for quality rapid prototyping.”
His transfer to the US came in 2000, a move precipitated by Valeo’s purchase of a company called ITT Automotive in 1998. ITT had previously acquired Delco Remy, a former GM brand famous for heavy-duty starters and alternators, and Caussat was asked to go to the US and bring Valeo’s culture into Delco Remy’s engineering development projects.
“I started in Michigan, working on different projects and focusing on ‘anti-pinch’ software for window-lift mechanisms and sunroofs, first for Chrysler and then for other OEMs such as Ford and GM. Those systems are still used in their vehicles,” he says.
“In 2006, Valeo decided to sell the branch I was working at in the US, to electric motor manufacturer Nidec. At the time, some friends had already left for a company called Raser Technologies, in Utah, that was developing electric vehicles, and they asked me to join them, anticipating that I could bring a lot in terms of software development capability for electric machines.
“That’s when it hit me, that working in e-mobility meant the perfect opportunity to combine my knowledge of electric machines from university with my experiences in automotive engineering from Valeo – all under the systems based approach I’d adopted back in my Valeo Electronic days, so I joined Raser in April 2006.”
Not long after that, Raser split its business divisions between geothermal and automotive engineering, the latter being renamed VIA Motors.
Pioneering automotive HV
Upon joining Raser, Caussat began working from a blank sheet to create an all-new software architecture for controlling PM motors using high voltage inverters – a considerable step up from writing individual functions for Leroy-Somer’s induction motor inverters. Other differences included the use of an automotive API to program the microcontroller he and his team selected, and embedding self-diagnostic functions into it using the KWP2000 protocol.
“With the all-new inverter hardware the other half of the team had designed, we created a prototype inverter that was tested in a Hummer H3 HEV. We removed its transmission and put in a dual-inverter system – one for propulsion, the other for the generator – with the two of them back to back he says.
“We’d used industrial IGBTs to design the inverters as 700 V systems, far beyond the usual limit of 300-400 V at the time, because we wanted a really compact and powerful solution and there were no automotive IGBTs back then. But the chargers, DC-DC converters or other components to support 700 V didn’t exist then.
“Perhaps we tried to go too far too early, but given that 700 V systems aren’t so unusual anymore and 1000 V systems aren’t far away, time has vindicated our approach.”
In 2010, after his company’s rebranding, Caussat became director of r&d at VIA. He took on new responsibilities for systems architecture and personnel management, and steered their development strategy away from producing electrical hardware towards a greater focus on the niches of intelligent control software and systems integration.
“It’s important to note that these days we’re not designing motors or inverters; we’re systems engineers,” he says. “We simulate architectures, integrate components and write software to create electric powertrains for customers who need to reduce the costs, inefficiencies and inconveniences of their commercial fleets. For fleet managers, optimising performance always comes second to optimising cost. A holistic systems based approach is crucial for that.”
That approach was key to VIA’s first-generation drive system, a comprehensive conversion kit for turning GM’s Silverado pick-up trucks and express vans into PHEVs with series hybrid powertrains. It was launched in 2015 and was aimed at fleet managers.
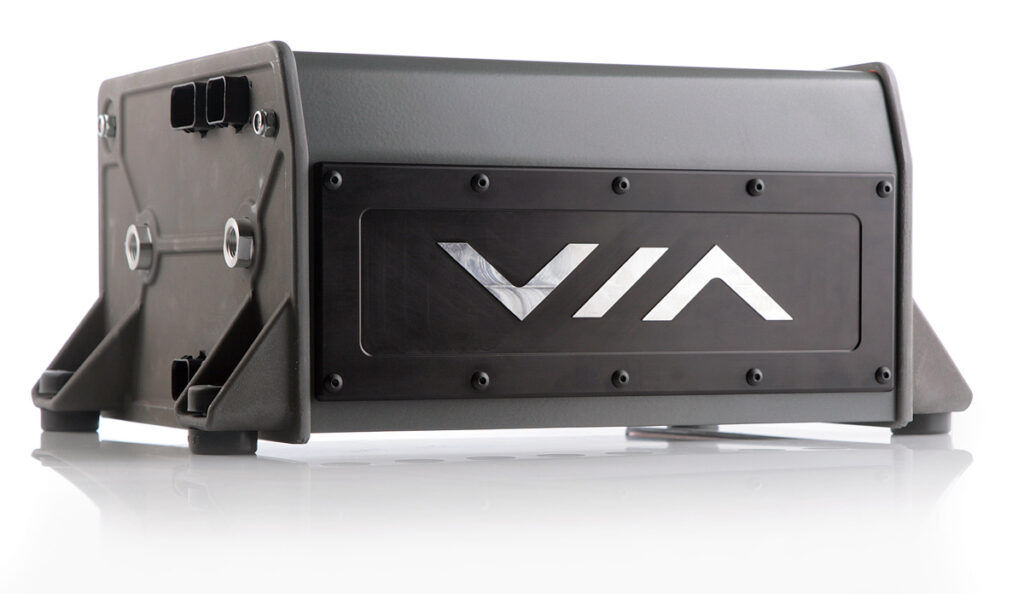
First-generation powertrain
This powertrain used a modular battery pack from A123, which incorporated VIA’s power distribution box for supplying high voltages to the other onboard components. These included a Remy synchronous electric motor (producing 415 Nm of torque) and a TM4 inverter.
“We also developed a bidirectional onboard charger, which was very useful for some end-users such as Pacific Gas & Electric who would arrive at a job site off the grid or at night time. With vehicle-to-grid [V2G] charging, they could plug their lamps or devices into their GM PHEV and start working,” Caussat says.
“Developing that V2G capability was also useful for the military, as their bases often have independent ‘micro-grids’ that stand to benefit by conserving the energy their EVs and HEVs don’t use.”
VIA mainly chose to electrify these two vehicles as its team included a former senior GM engineer who had good relations with the company, ensuring close access to the necessary data for designing a suitable electric powertrain.
Such data typically encompasses three key categories. First is CAD data for integrating electric powertrain components. Then come the signal and comms data for simulating components, the interactions between them, and combined performance outputs across vehicles. CAN data is vital for developing safety and control software across the powertrain systems.
“The third category is system information data, to understand where each signal starts, where it is going and why it was sent,” Caussat adds. “For example, stability control of a vehicle rests on the comms between several ECUs, including the braking system, the transmission and the engine control module [in a standard layout].
“Successful conversion of an existing vehicle rests on knowing which signals and functions depend on which interconnections between subsystems to recover this function through the VIA electric powertrain.”
About 250 units of the first-gen powertrain were produced and deployed for more than 70 customers across the US, including FedEx, Coca-Cola and Duke Energy. These end-users provided in-depth feedback that was cycled into the development of VIA’s next-generation drive system, which began in 2015.
Second-generation powertrain
By this time, Caussat and the rest of VIA’s management team had determined that vehicle conversion was not an efficient direction for the company, as it entailed end-users willingly buying a completed ICE vehicle and then spending more still to switch out many of its core components.
For the second generation therefore, the company sought powertrain-less ‘gliders’ (consisting essentially of everything on the vehicle other than the powertrain components) to skip the unnecessary cost of removing engines and ancillary engine components. That reduced lead times and costs, and opened the required space and flexibility for VIA to make full battery-electric versions of light-duty cab trucks and medium-duty cargo vans with ranges of 100-230 km“However, many of the components and much of the technology on the second generation were the same as the first, albeit with improvements based on the lessons learned,” Caussat says. “For example, we revamped our software to make it much more modular, and we created our own engineering development platform, VDrive IDE [Intelligent Development Environment], which is now a critical tool for our in-house virtual modelling and testing.”
VDrive IDE was created to accurately simulate in virtual environments the systems VIA was programming, to predict the results of software changes and integrations in how the vehicle would perform and respond on different routes and architectures. This includes accounting for the effects of different powertrain component selections and CAN comms exchanges between them.
“Not a lot of companies have this ability to test and analyse the integrity of control software to the extent that we do in a virtual environment,” Caussat notes.
“We also created another tool around that time, called Night-Owl. This compiles our latest code into software at night, applies it across various test cases, uses VDrive IDE to simulate how those cases play out – with our latest software controlling the EVs in our virtual environments – then analyses the results for us to look at in the morning.
“That helps us work much faster and more flexibly, by quickly informing us which piece of code needs to be improved or which powertrain components consistently perform sub optimally compared with others.”
Development of the second generation powertrain is now complete and is available to VIA customers.
Third-generation powertrain
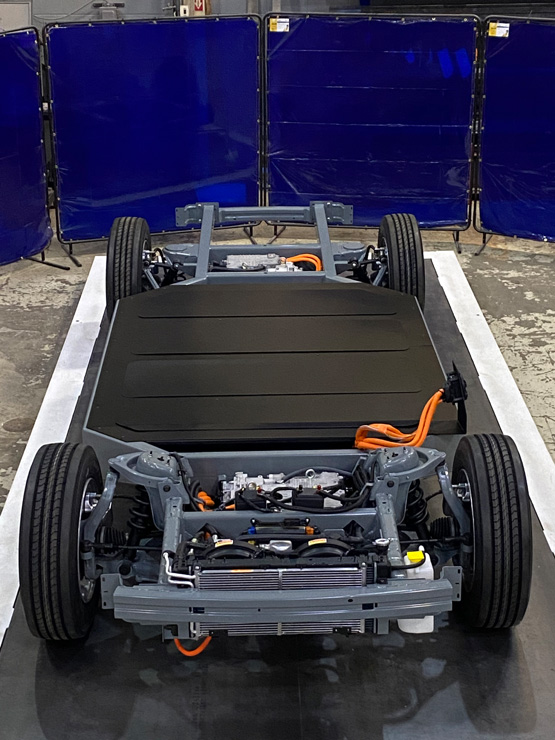
The modularity and flexibility fostered by Caussat’s engineering team in VIA’s software development is now being extended to its hardware integrations, with the unveiling of VIA’s Commercial High-Efficiency Modular Architecture (CHEMA) concept.
The CHEMA is VIA’s third-generation drive system, and provides an architectural map for swapping different components in and out of a skateboard’-type powertrain design according to customer needs. That includes different suspensions, brakes, energy storage and drive systems.
“The CHEMA skateboards are unconstrained by the parameters of other companies’ chassis. We can receive requests from customers for cost, performance, standards and so on, and provide them with a CHEMA powertrain tailored to fit their specifications,” Caussat says. “Our simulation capabilities allow us to quickly trial new batteries, motors and inverters.
“Our main control algorithm sits on a single system, with two microcontrollers for safety reasons, and we’re working towards ISO 26262 guidelines while tending towards keeping everything on that one device. As we’re AUTOSAR-compliant though, we envision that in future some of our control functions will be transmitted to some of our electronic system devices elsewhere in the vehicle, such as the motor inverter.”
Conclusion
At time of writing, the company’s third generation system prototypes were in fabrication, with proof-of-concept trials to begin soon after. These will test and define key aspects of the CHEMA, such as the mechanical, electrical, thermal and signal interactions between parts, to gauge how the interfaces between the modular frames, powertrains and cabins can be optimised to ensure the system’s balance and long life.
Bio – Thierry Caussat
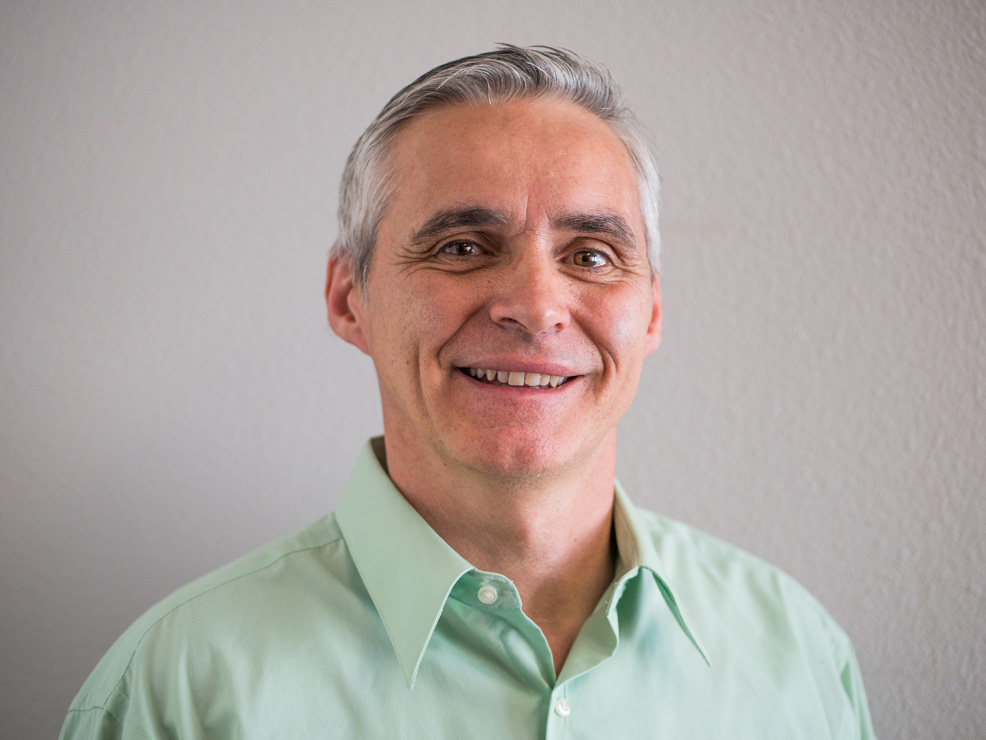
Thierry Caussat was born and raised in Toulouse, where he achieved a Masters and PhD in electrotechnics at INP-ENSEEIHT. He gained particular proficiency in software programming for electrical machine control systems, through work with French induction motor company Leroy-Somer (now Nidec Leroy-Somer).
After completing his doctorate in 1995, he worked for automotive giant Valeo on a range of software systems, and moved to Michigan in 2000 to provide engineering leadership at some new US-based acquisitions Valeo had made.
In 2006, he moved to Utah to work at VIA Motors (previously Raser Technologies), where he has spearheaded the development of the company’s various generations of drive systems, and furthered its capabilities in simulating, testing and integrating new electric powertrain components and architectures.
ONLINE PARTNERS
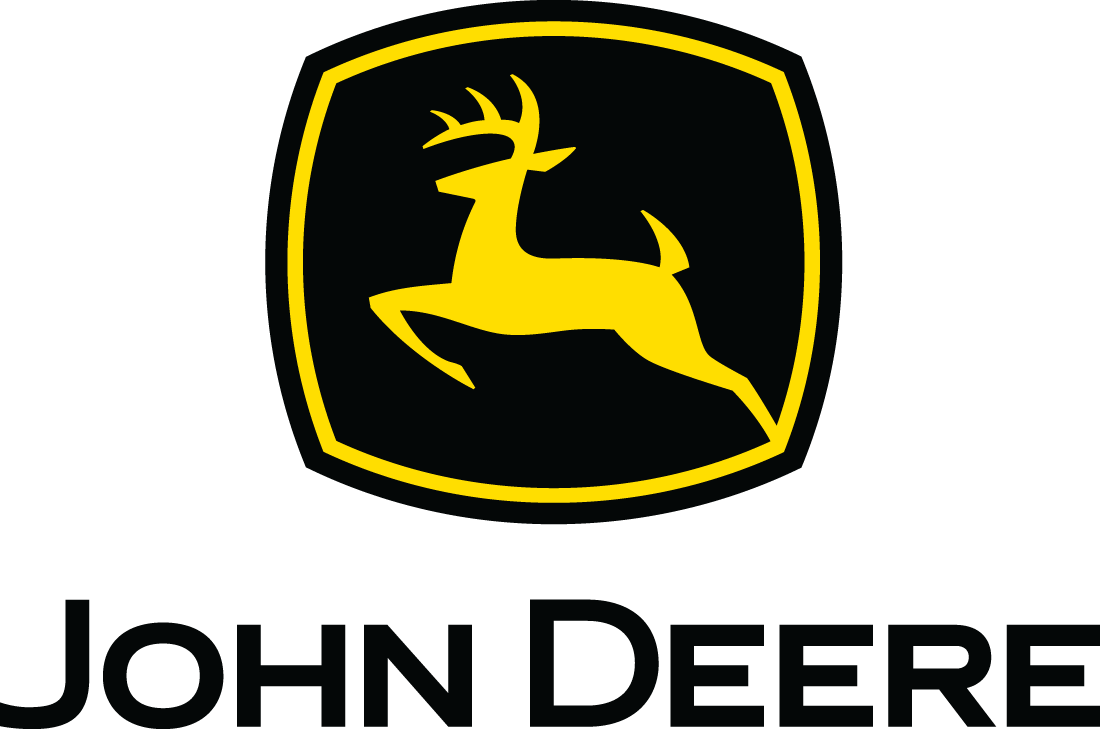
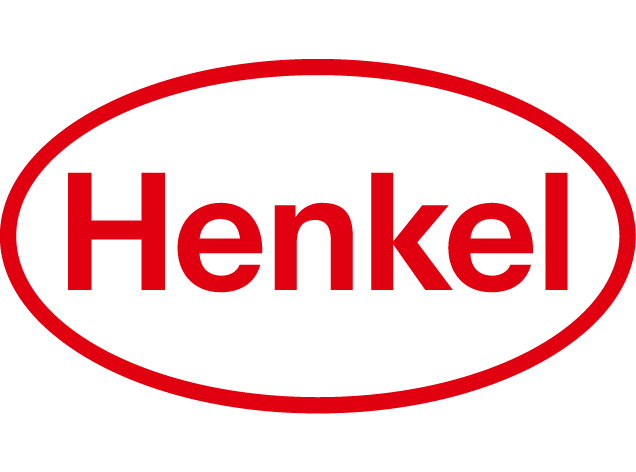
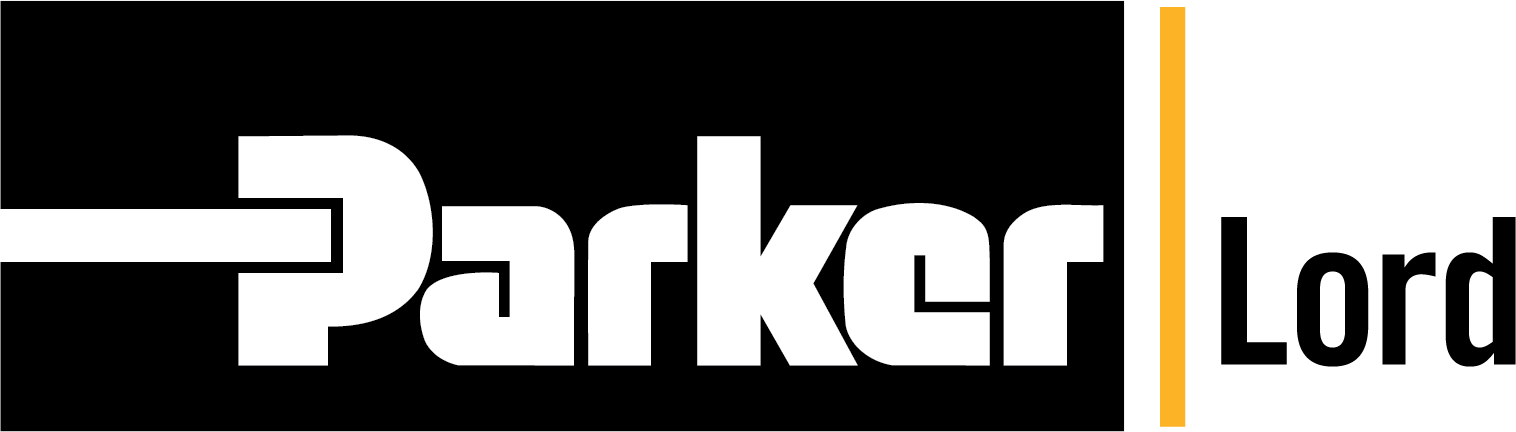
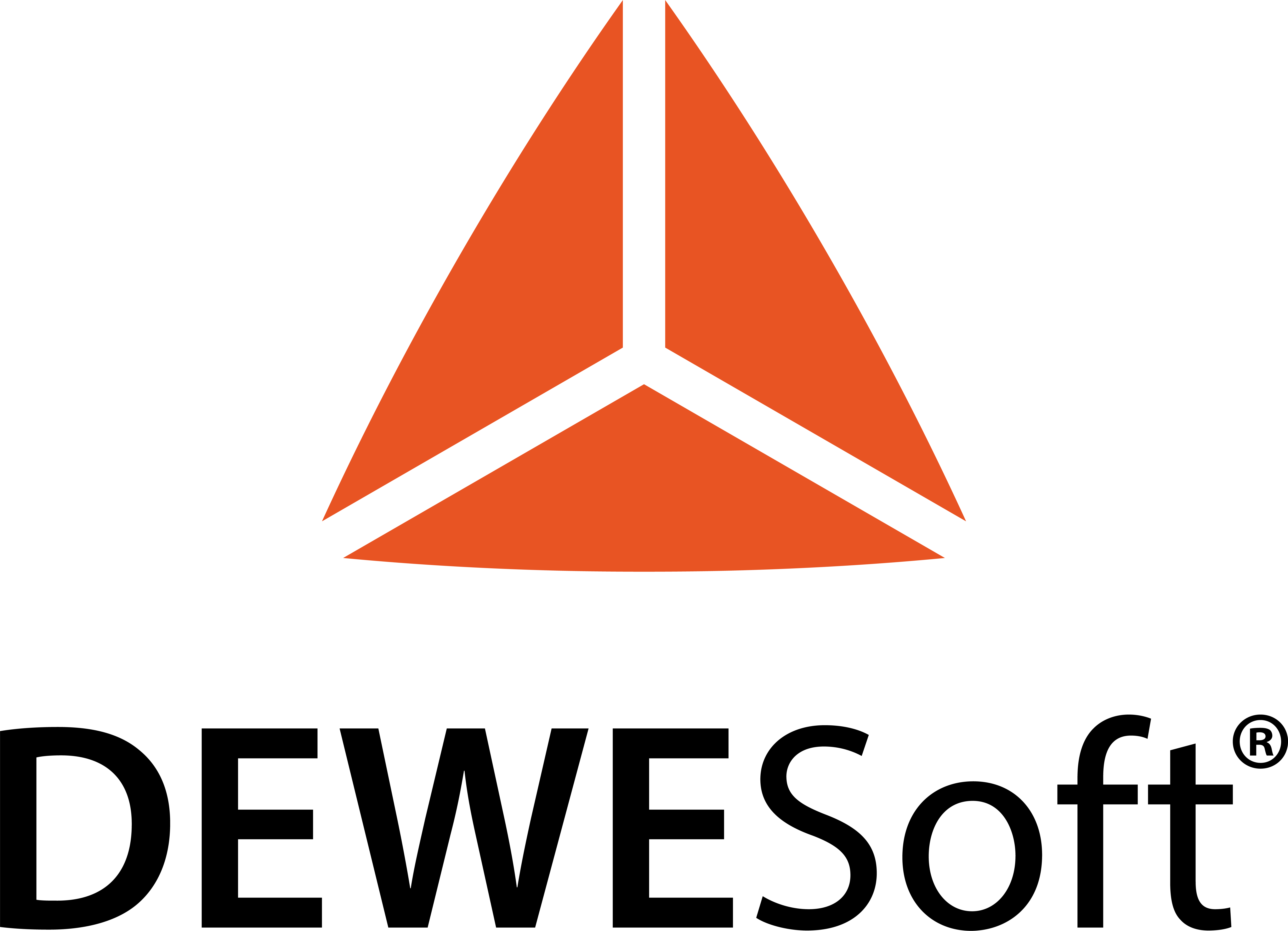
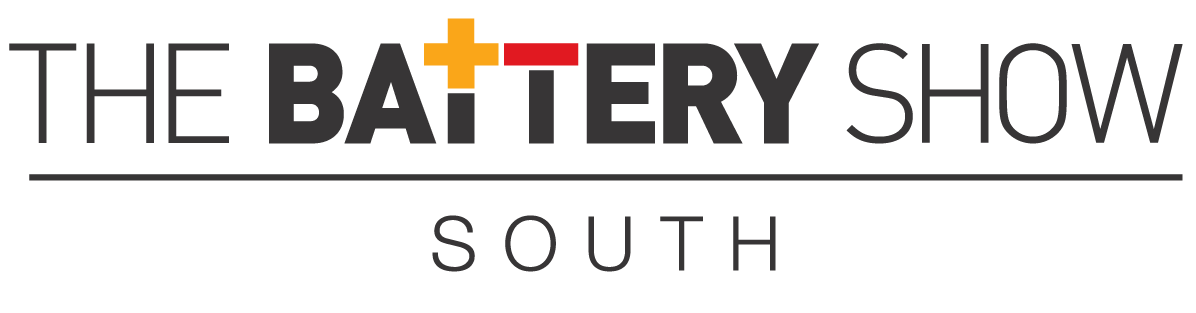
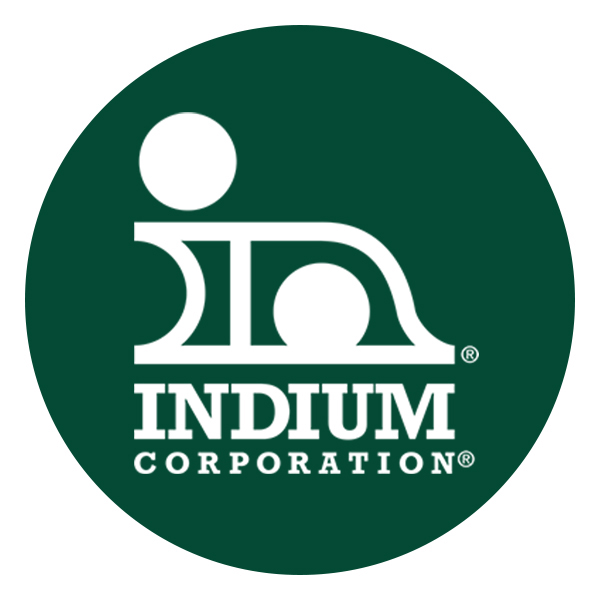
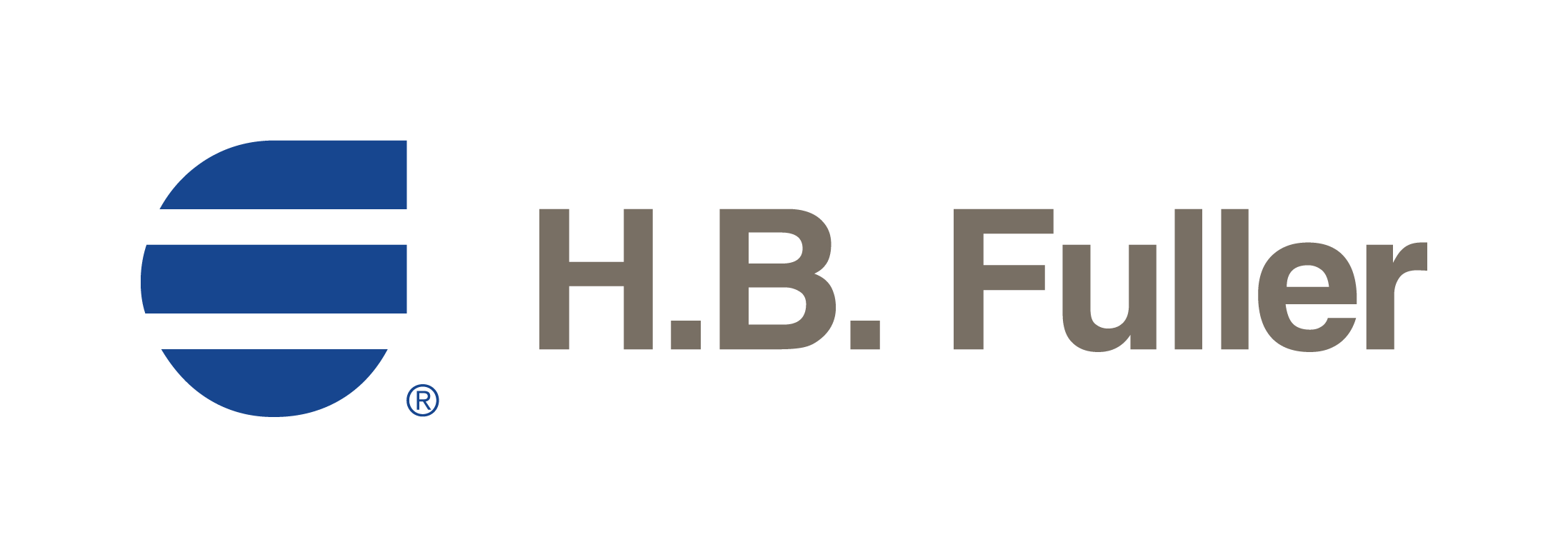