In conversation: Stephen Lambert
The trickle-down effect
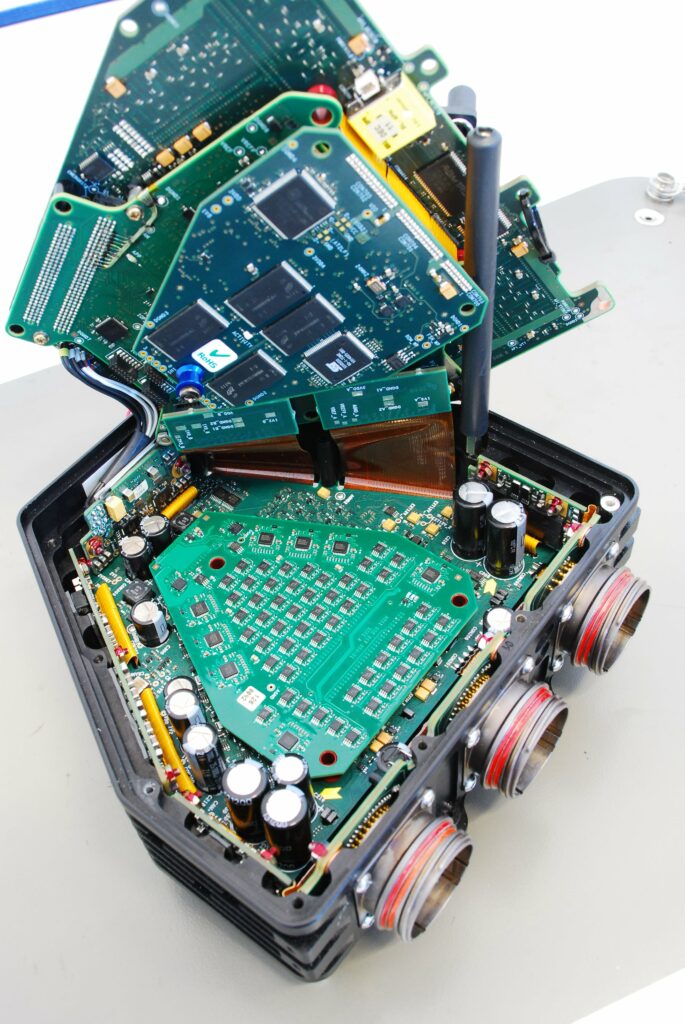
(Images courtesy of McLaren Applied)
McLaren Applied’s head of electrification talks to Rory Jackson about how the company’s race-bred technology will filter through to e-mobility
Despite coming from a farming community in South Wales, Stephen Lambert had a great interest in software engineering from an early age, with programming taking up much of his attention during his secondary school education.
That however would be replaced by a career move into automotive engineering, which has involved him in motorsport as well as e-mobility projects. In the lead-up to that, he recalls, “By the time I was at university for my software engineering degree, I’d started driving and realised how fun cars were – and by comparison, how much less exciting software programming by itself was.”
That passion has stayed with Lambert and has inspired him, as head of electrification at McLaren Applied, to produce HV solutions optimised for where he sees the electrified world going.
These experiences have led him through a range of roles dealing with cutting-edge e-mobility technology, including as principal engineer for hybrid and EV integration at Lotus, battery systems engineer at McLaren Racing – specifically for the energy recovery systems in its Honda Formula One powertrains raced from 2015 – and some battery manufacturing and engineering companies.
From batteries to inverters
At Lotus, Lambert worked on demonstrator vehicles including a hybrid Lotus Evora and the fully electric Rolls-Royce 102EX. It was through such projects that he built up experience in battery design and engineering.
Recalling his university days again, he says, “The supervisor on my fourth-year project wanted to set up a doctorate that was aligned with something called Formula Hybrid, which was a precursor to the electric Formula Student series. I soon found myself working with Potenza Technology, who were working with Westfield Sportscars and wanted us to investigate how we could electrify one of the latter’s cars.”
Lambert took up the challenge and soon a Westfield hybrid EV was built, which he was able to show at the Goodwood Festival of Speed in 2010. Soon after, he and his colleagues designed and built a diesel-powered Formula Three car that featured a number of technologies to make it more eco-friendly than the typical machinery in the series, and to prove out what was then being called ‘green automotive’.
At the time, there were no reliable supply chains for EV or HEV batteries, so he moved to Goodwolfe Energy to build battery packs first-hand.
“The opportunity then came up to help develop the battery system in the MP4-30, McLaren’s 2015 Honda-powered Formula One car,” he says. “My experiences at Lotus and Goodwolfe were key here.”
Much of the technology he worked with from the late 2000s to the early 2010s was oriented around lithium iron phosphate (LFP). Companies such as A123 Systems were focused on LFP and saw it as the battery technology of the future, as well as a safe direction for cell developments to go in.
“It didn’t have the best energy density, but it had good power density, and certainly for high-performance applications it was seen as a really interesting technology,” Lambert recounts.
“Certainly over the past 5 years, NMC has taken hold in EVs – most EVs on the road have either NMC or NCA cells in their packs – but what’s really interesting is how we’re seeing LFP come back around and becoming much more dominant, especially in lower-cost markets, as well as in heavy-duty and high-performance applications where you need a higher power density and charging rate without making your EV less safe.”
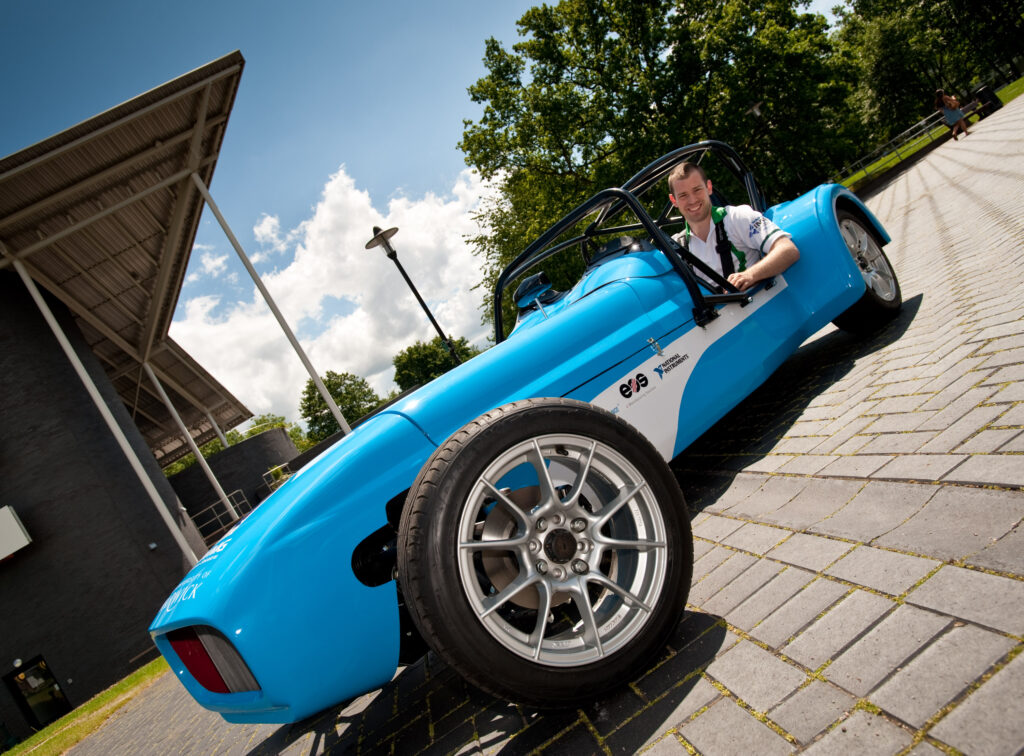
The exact chemistry used in the McLaren MP4-30 remains a secret, having been a very particular chemistry specified to an exact set of requirements for the racecar’s powertrain. Its development started with chemical fundamentals and ended with homologation testing of the fully assembled pack.
Lambert left McLaren Racing in mid-2015 but then joined McLaren Applied as head of electrification in November 2016, and found himself once again working in the McLaren Technology Centre.
“I was offered the chance to spearhead McLaren Applied’s strategy for a scalable electrification business,” he says. “It was transitioning from being a consultancy service into a product maker, and since I already lived in Woking [southern England] – running Vayon Energy Storage – and because I still knew a lot of people in McLaren, they asked me to join.”
Going in, he had imagined he would be remaking McLaren Applied into a battery company, particularly given its ongoing work in Formula One and Formula E on electrified drivetrains, and his own copious experience in batteries. However, he soon realised the company actually had a bigger edge (relative to the rest of the industry) in power electronics and functional safety-critical systems, and that this would be invaluable for what e-mobility was going to need in the future.
“We saw efficiency, particularly through 800 V automotive architectures and silicon carbide [SiC], being a major driver in the future,” he says. “In that light, a lot of what McLaren Applied was accomplishing with inverters for Formula One and Formula E was directly in line for where the automotive industry was going to go.”
This was followed by concept development, prototype iteration and some further market research to confirm that power electronics was the right direction to go in. That resulted in the IPG5, the company’s first inverter product aimed at the high-end EV industry of the 2020s and beyond.
Software-defined vehicles
While some might still be puzzled at the migration of former race engineers into e-mobility, Lambert echoes similar sentiments to those of Viritech’s Matt Faulks (EME 17, January/February 2023), and defines Formulas One and E as “essentially competitions in efficiency, with a clear trickle-down of technology from both to applicable areas of automotive.
“In Formula E, the cars are all the same apart from the driver and drivetrain. Since the energy limit is the same for all the teams, the only way to engineer an advantage is with a more efficient drivetrain.
“There are clear parallels with automotive e-mobility: when the OEMs chase efficiency, they make better vehicles. They can use a smaller and lighter battery, because they need less onboard energy, which means they get a lighter EV, which further reduces the energy they need, and that means the cooling system required is lighter, and so on.”
So, with Tesla’s dominance of the EV market effectively over, and every OEM as well as hundreds of start-ups rushing to release an affordable EV alongside their existing but more expensive models, Lambert anticipates the next wave or evolution in e-mobility to revolve around a grand push for efficiency, particularly with regard to power and energy.
“[UK magazine] Autocar carried out a great series of tests to identify which EVs were the most fun to drive, and the driver’s experience is something many engineers forget is actually a huge part of what influences the success of vehicle brands,” he says.
“First place was taken by the Porsche Taycan, second was the BMW i40, and the Tesla Model 3 came somewhere in the middle. But the part that was really interesting was that third place was taken by the Kia EV6.
“It might sound mad to have a Kia being listed up there with a BMW and a Porsche, but the truth is that Kia – and its parent company Hyundai – have done a great job of chasing efficiency. The EV6 has 800 V SiC power electronics, which means it charges really quickly and its battery doesn’t need to be too big or heavy. It also has a very weight-efficient body and chassis.”
He adds that a very fast rate of control typically becomes necessary when integrating SiC power electronics, principally to enable tighter control loops over the inverter and, by extension, the motor. That adds an extra layer of controllability to how the car handles.
Given how this improves overall driving experience, Lambert and McLaren Applied anticipate a future trend in electrification (after the push for efficiency) to focus on this subjective but very tangible area, once OEMs catch on to how efficiency makes for a more enjoyable drive.
“EVs can give you plenty of speed and torque in a straight line, but other than that, high-performance OEMs are struggling to figure out how to get customers engaged with their cars when there isn’t an IC engine inside,” Lambert observes.
“We think it’ll come down to software in the inverter. The inverter essentially controls the drivetrain and the dynamic response, and when you start playing with the software with the driver experience in mind, you can start to do some really interesting things.
“That’s really why the latest buzz-term is ‘software-defined vehicle’. You can start defining how an EV’s drivetrain works through the software in either its inverter or vehicle control unit. Even two vehicles with the same drivetrain could respond in totally different ways based on how they’ve been programmed.”
The IPG5 inverter
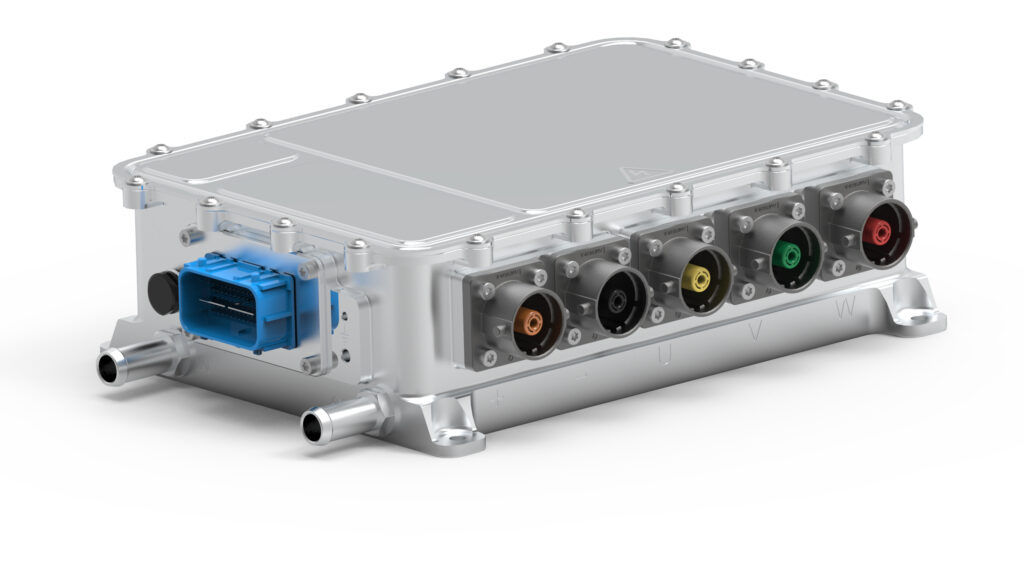
These factors have informed McLaren Applied’s development of the IPG5, as have lessons it has learned from motorsport. However, Lambert and his team knew from the outset that it would need to be developed from the ground up, rather than being derived from a motorsport design, given the need for cost optimisation, functional safety and scalability of production.
“For instance, in motorsport we might use an FPGA for controlling the inverter, which gets us very fast and reliable processing, but they are expensive, and there are functional safety concerns around them,” Lambert says.
“So a lot of r&d went into finding similarly powerful processors that were rated for automotive safety. That might have meant sacrificing some programming freedom, but if it recreated the speed and quality of controllability we’ve previously achieved in motorsport – and does so within automotive requirements – then it would be worth it.”
The mechanical design of the inverter also had to be rethought to enable quick and straightforward manufacturing, as opposed to the intricate designs, low-volume numbers and long lead times of motorsport inverters. In its current mechanical form, the IPG5 weighs 5.5 kg, and measures 262.5 x 176 x 82 mm. I has a peak gravimetric power density of just over 90 kVA/kg (or just over 130 kVA/litre if considering volumetric power density) and complies with ISO 26262, ASIL-D.
It supplies power up to a peak of 900 V or current up to 540 Arms, assuming a liquid-coolant flow rate of 10 litres/minute, an 8 kHz switching frequency (although its peak variable switching frequency is 32 kHz) and an operating power efficiency of 97%, up to 99% at peak.
Most of that efficiency comes from the use of SiC technology, which Lambert notes has been used by McLaren Applied for developing inverters for Formula One and Formula E since 2012. Lambert and his team therefore spent further time looking into factors such as cost optimisation, transistor quality and supply chain reliability, eventually choosing STMicroelectronics as its SiC supplier as a result.
“When it comes to designing and optimising SiC topologies, some companies will just swap out their silicon MOSFETS for SiC MOSFETs and think it’ll be fine,” Lambert says. “That will work, and the inverter will be slightly more efficient, but the inverter is not making the best of the new transistors, whether that be in terms of motor speed, switching frequency, or how the motor is optimised.
“Some people forget that when you use SiC, you unlock higher speeds for your motor. And if you have a faster motor, you can make it smaller for the same amount of power. Also, if you want to produce higher volumes of vehicles, taking out motor mass could be a lifesaver because of the raw materials costs you’re saving, on top of the weight you’re taking out.”
Beyond that, the controllability necessary for using SiC can as mentioned offer new software-defined capabilities, be it for greater efficiency, driveability and so on.
“Matlab Simulink’s auto code generation has been key to the success of McLaren Applied’s systems in Formula One for years now,” Lambert says. “In many ways it’s our bread and butter, and we’ve now taken it into automotive with some control products that could be directly embedded with code from Simulink before production.
“At the time, nobody else was doing that, and that capability is closely linked to our simulation work. If you can simulate something and then copy & paste the Simulink model into your code, it massively reduces your development time.”
Future plans
Lambert and his colleagues view EVs as one part of a burgeoning low-carbon world. It will be filled with consumers actively interested in their own energy usage, and who expect greater connectivity with and access to data between their vehicles and their homes through software-defined portals.
“As powertrains become more efficient, EVs will start to be seen as these big energy stores sitting next to houses,” he says. “And as well as that opening up V2X opportunities, everything – the EV, the chargers in your house, your heat pump and local renewable energy turbines – will need power electronics.”
He comments that GaN will be useful for LV automotive applications such as DC-DC converters and OBCs, noting that GaN laptop chargers are finding commercial success given their small size and minimal cooling needs. That will push GaN towards widespread use in the low-carbon world, he says, although he anticipates SiC continuing to dominate higher-current systems working above the 650 V limit that GaN tends to be capped to.
“EV powertrains won’t sit still either. Even as they become more software-defined, there will definitely be a big shift towards fully integrated drive units, with motors, inverters and transmissions all consolidated together,” he says.
“High-performance EVs in particular will push the development of more torque-vectoring EDUs, with control of individual motors to individual wheels. That’ll be something especially exciting to look out for.”
Stephen Lambert
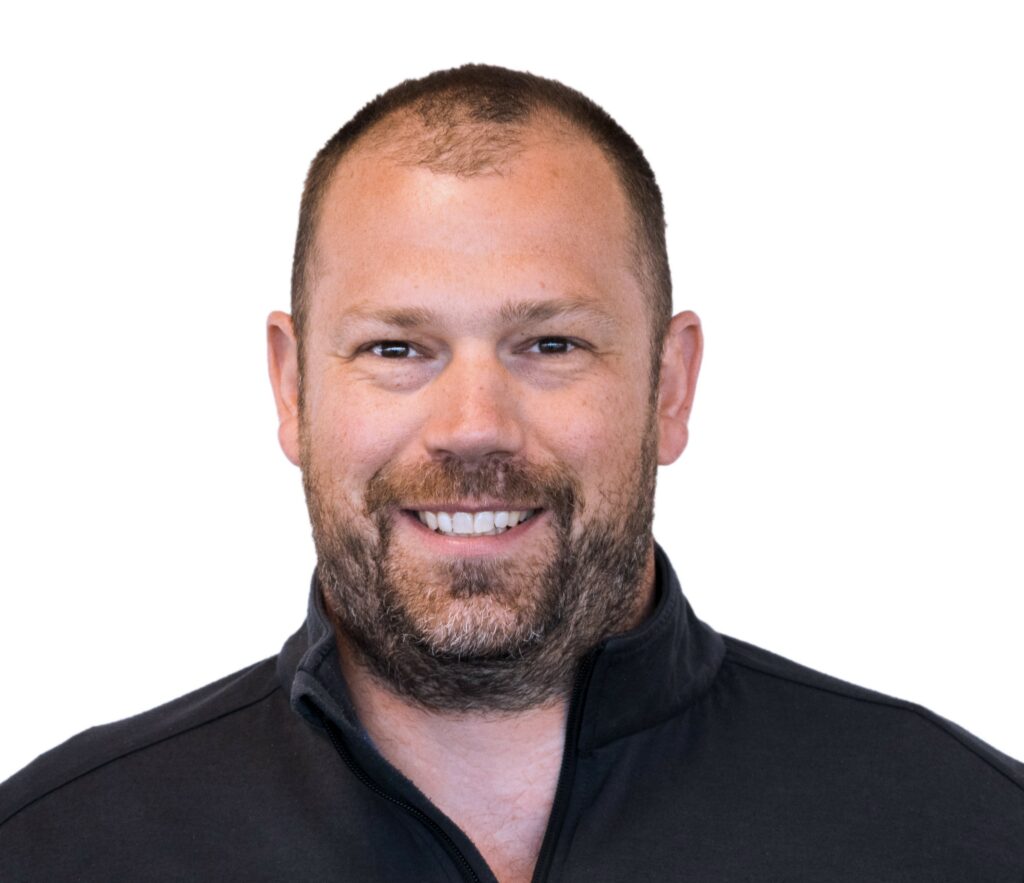
Stephen Lambert was born in Abergavenny, in South Wales, UK, and completed his secondary education at Hereford Cathedral School.
He went on to study at the University of Warwick from 2002 to 2006 for his MEng degree in Computer Systems Engineering, where he took part in Formula Student and became the electrical and electronics team leader for his racing group. While there, he designed an electronic clutchless gear-change control system, which won an award for innovative use of electronics in a Formula Student racecar.
From 2006 he worked as a research engineer for his engineering doctorate (also at Warwick) while working as a project engineer at Potenza Technology, before going on to work at Lotus as principal engineer for hybrid and EV integration. He left Lotus in 2012 to work as engineering manager at battery company Goodwolfe Energy, and then in 2013 became the battery systems engineer for McLaren Racing’s Formula One team.
Working as the managing director of battery maker Vayon Energy Storage from late 2015 to late 2016, he moved to McLaren Applied in November 2016 to become head of electrification, a position he still holds.
Since 2019 he has also served as chairman of the Automotive Electronics Systems Innovation Network, a not-for-profit aimed at facilitating networking and collaboration to take on challenges facing the automotive electronics industry, such as identifying sectors where higher levels of funding or skilled graduates are needed for companies to thrive.
ONLINE PARTNERS
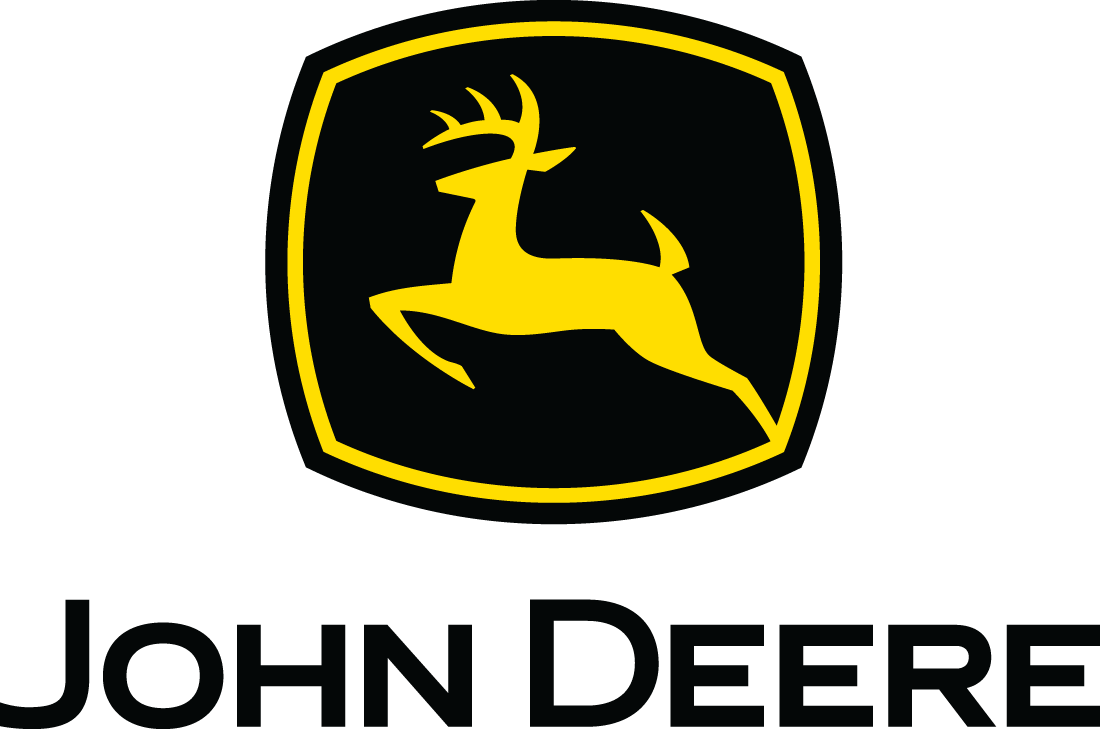
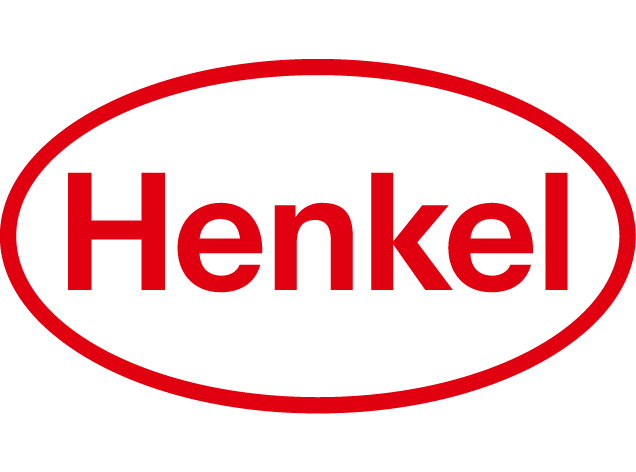
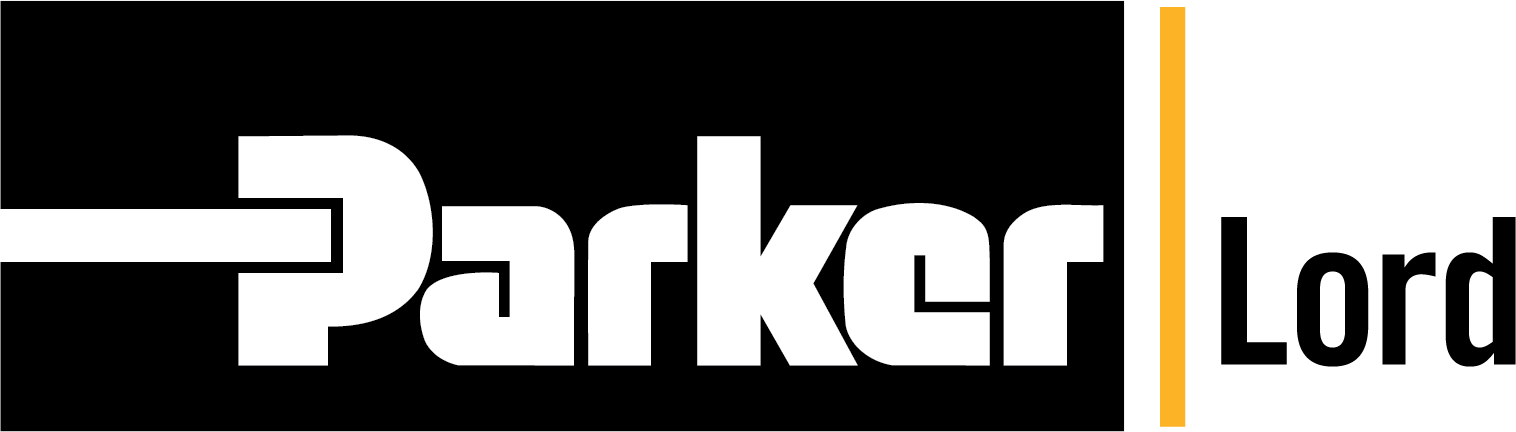
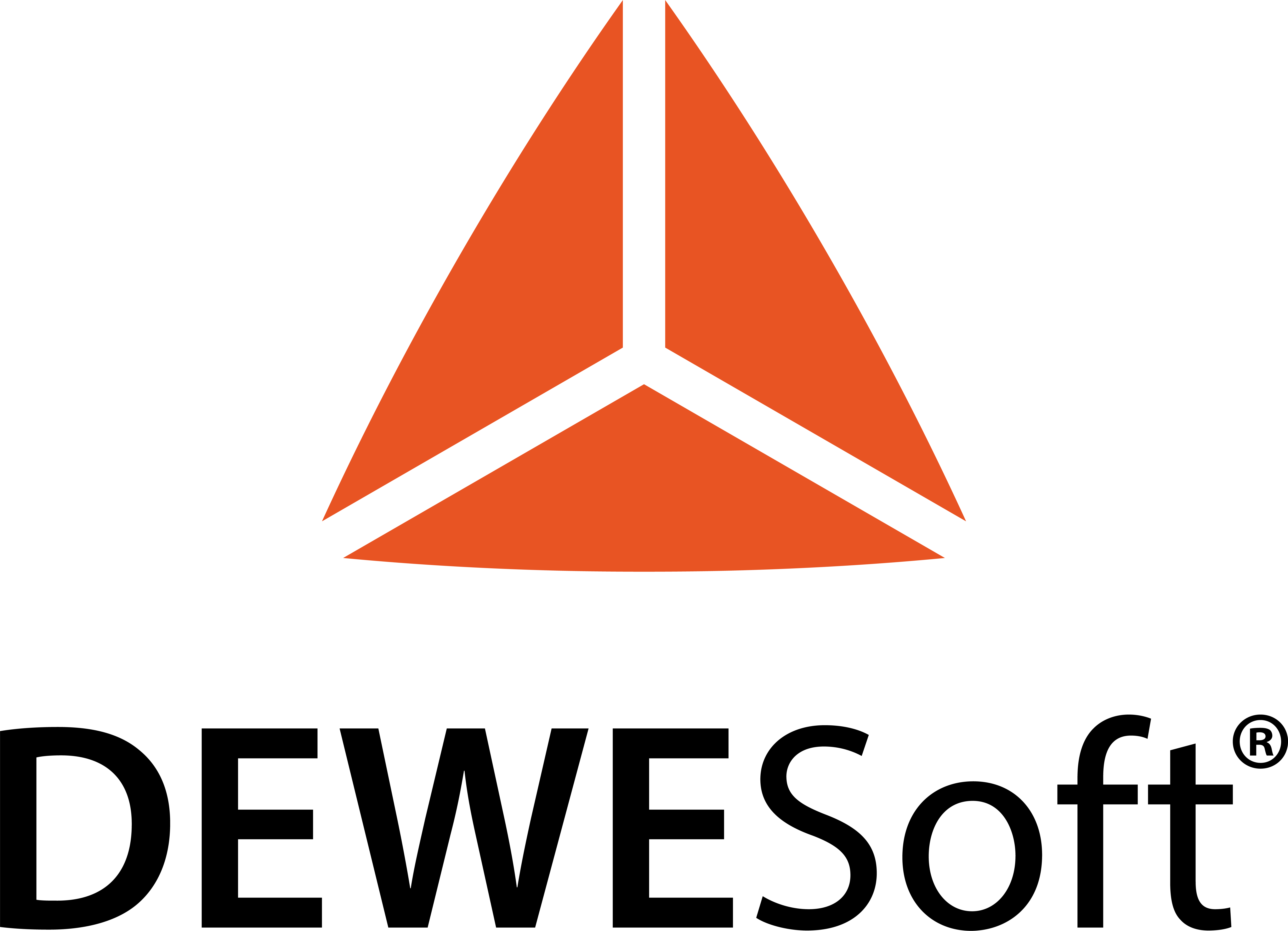
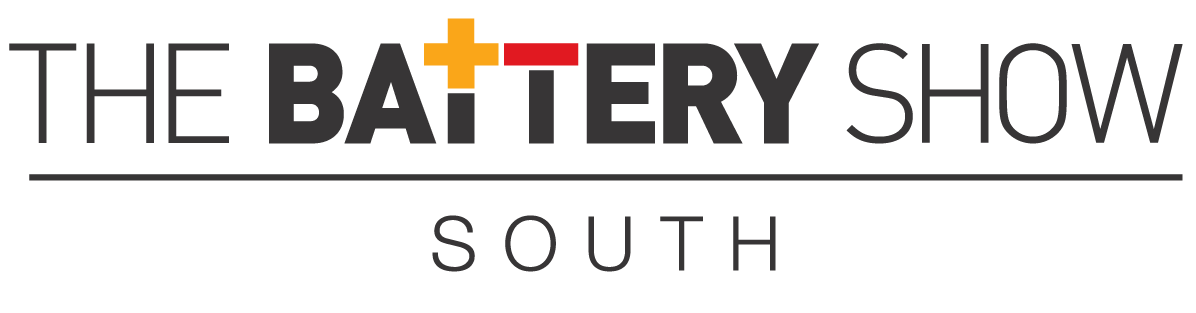
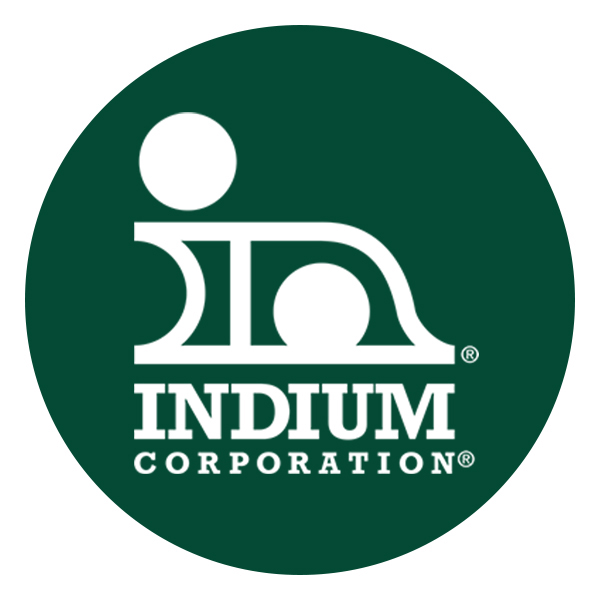
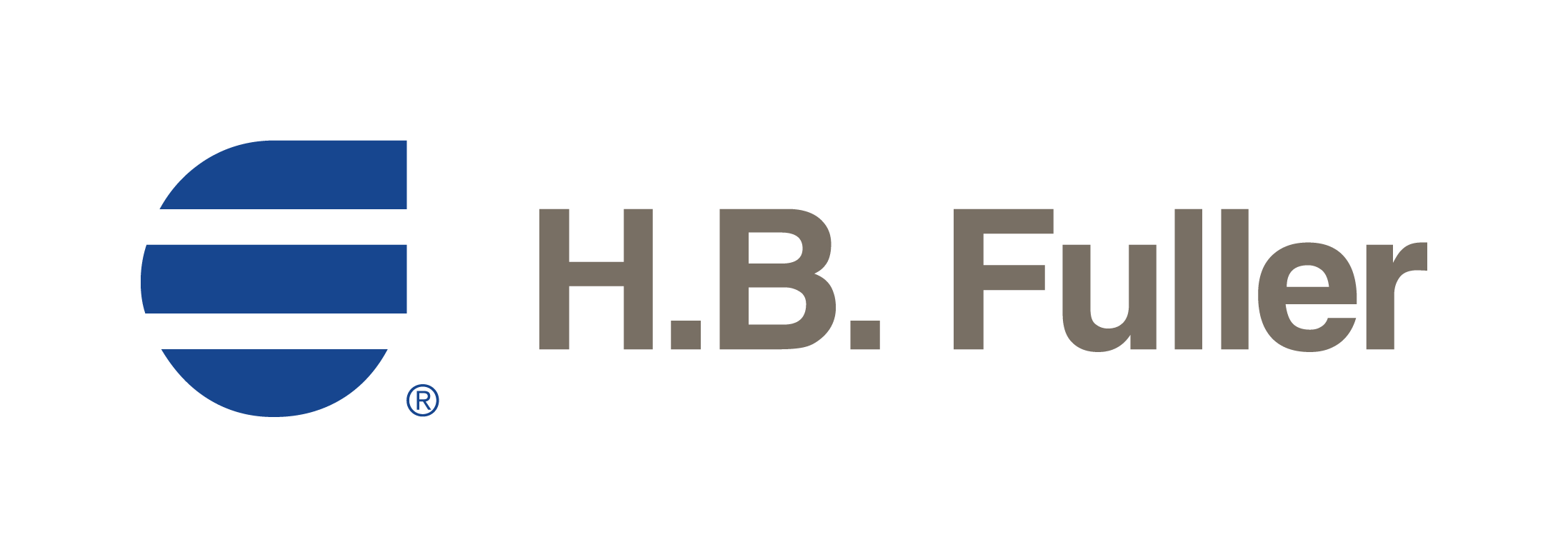