Robert Hoevers
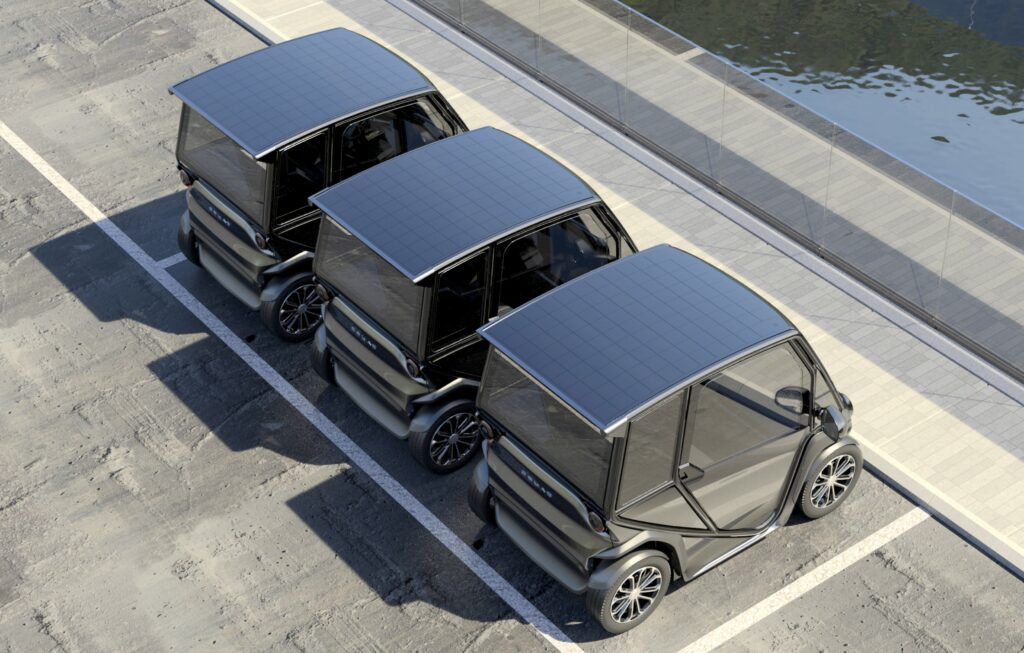
(Courtesy of Squad Mobility)
Solar flair
Squad Mobility’s CEO tells Rory Jackson the story behind developing the company’s solar-powered urban runabout
Although DC fast charging and hydrogen refuelling are gaining in popularity for quickly replenishing EV energy stores, considerable infrastructural investment is needed if sufficient charging stations and hydrogen supply points are to be made available for consumers and commercial fleets.
While solar panels are a relative rarity among the technologies being adapted for e-mobility, solar-electric powertrains can be charged wherever there is sunlight, without needing to be plugged in – potentially making them much more convenient than the more infrastructurally dependant battery-electric and hydrogen EVs around the world.
This ease of charging is one reason that Robert Hoevers, CEO of Netherlands-based Squad Mobility, has led his team to develop the solar-powered Squad Solar City Car over the past few years.
The Squad is a two-seater road vehicle reminiscent of a golf cart. It has a panel of solar cells on its cabin roof, and has been designed to be used as an easy-access ride-sharing platform similar to the e-scooters and e-bikes proliferating throughout the urban centres of the world.
While the EV looks simple at first glance, Hoevers (along with his co-founder Chris Klok) has led the design and engineering of the Squad by drawing on experiences and career positions held across not only e-mobility companies but racing organisations and IC-engine automotive OEMs as well.
“When I was in middle school, my older brother bought a Yamaha XT off-roading motorcycle, a bike I still love to this day. He picked me up from school on it, and that was the first time I remember really wanting to spend my life making vehicles that moved fast,” Hoevers says.
Indeed, the years following his university education in Industrial Design Engineering at Delft were spent on a range of different road and race vehicle projects.
The road to e-mobility
Hoevers’ turning point towards electric powertrains came in 2009, when he founded EPowerGP, one of the organisations that would ultimately lead to the founding of Formula E.
“Working at EPowerGP taught me a lot about what you can actually do with electric drivetrains, how different people want to change or configure them and why, and how racing or commercial regulations for them can form,” he explains.
“For example, it always struck me as strange that Formula E initially stuck to a central e-motor with a mechanical differential, when using separate motors in the rear with electronic differentials, or potentially four-wheel drive, would make so much more sense.”
Hoevers’ move into solar technology came gradually. During his fourth and fifth years heading EPowerGP, he also worked at BonGo Innovations, a retailer for home photovoltaic (PV) systems, and in 2018 he started working at solar EV maker Lightyear.
That company was spun out from Solar Team Eindhoven, which has won the World Solar Challenge numerous times and has gained a lot of attention for its Lightyear One EV. This is a large hatchback that is due to start serial production this year, and it features solar cells across its roof that charge at an average rate of 0.996 kW – enough for 12 km per hour.
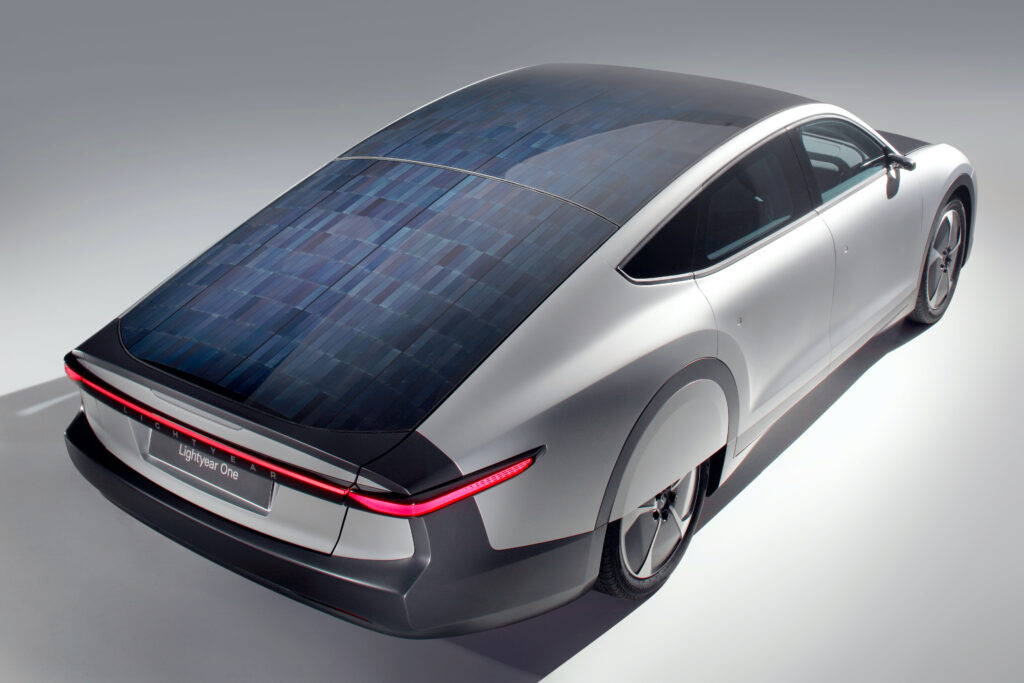
(Courtesy of Lightyear)
“The Lightyear One incorporates a number of great EV technologies, such as in-wheel motors that independently controlled using advanced torque vectoring, but Chris and I felt it was something of a shame that the car was rather expensive – it’s a large and advanced passenger EV – so this great platform for sustainable mobility wouldn’t be accessible to everybody,” Hoevers explains.
“It’s especially striking to me because solar is priced so incredibly low now. A kilowatt of solar cells – which is what the Lightyear One has sitting on its roof – costs only €200. A €150,000 car shouldn’t be necessary to get the clean energy benefits of €200 worth of solar cells, especially when PV reduces the quantity of batteries your car needs.”
Seeing an opportunity to provide a highly affordable clean energy vehicle, Hoevers and Klok founded Squad Mobility in May 2019, with much of their initial r&d focused on determining which vehicle design made the most sense for their goals of affordability and widespread access.
Hoevers and Klok soon identified huge room for growth in the personal, shared urban mobility market, where numerous single-person scooters and bikes exist but where there are practically no robust solutions for transporting two people (or one person with luggage).
The first prototype was completed earlier this year, although Hoevers notes that the automotive world often quibbles over what actually constitutes a prototype.
“The first tangible, life-size recreation of a new car design is often actually a side-view print of the car, which is placed on the ground or attached to a wall so that the company can judge early on how the driver or riders actually fit into it. The public will never see these ‘prototypes’ of course, because to the uninitiated they look quite strange,” he says.
“Producing a mock-up is very important though, not necessarily for showcasing the design at auto events but more for judging the driver’s ergonomics – their field of view, leg room, the height of the roof, the space between them and their passengers. All these and more have to be suitable or people won’t want to drive the car.”
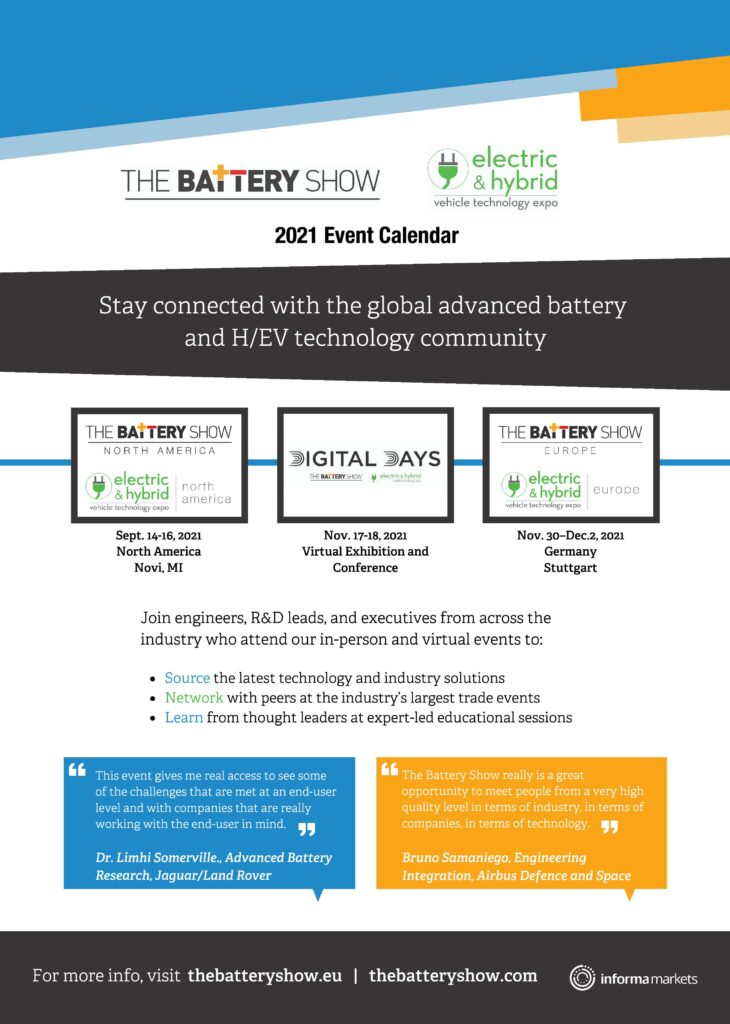
Charged by the sun
The core aspect of the Squad is, of course, its solar array. To successfully engineer a solar-recharged EV, two figures must first be optimised. The first is the yield of the solar cells, as in how much energy they will typically generate. The second is the energy consumption of the EV – and naturally, this figure must be minimised while the former is maximised.
“That’s from an engineering perspective, but again, we want the benefits of solar to be widely accessible to people seeking convenient personal mobility, so we need to consider the consumer perspective too, so the component prices are also very important to us,” Hoevers explains.
A wide range of solar cell materials and designs are now available as mass-produced commodities, with prices often running proportionally to yield. To strike a balance between cost, yield and availability, Hoevers and his team have installed panels of monocrystalline silicon in the Squad’s roof.
“Mass-produced commodities give you the best per-unit price, but we also wanted a decent yield – monocrystalline silicon cells give us a yield of 22%, which is pretty decent for our purposes,” Hoevers says. “Our roof area is about 1.2-to-1.3 m2, and about 1 m wide, which corresponds size-wise to the types of solar panels supplied wholesale for houses. That’s a major reason why we’ve been able to get a very good price on our solar components.”
While solar materials of much higher yield are available, such as gallium arsenide or even multi-junction cells that combine semiconductors to achieve upwards of 30% efficiency, a panel of such PV cells could cost 10 times the price of a single Squad.
Even going to cells with slightly higher yield (with 23-25% efficiency, for example) would bring exponential increases in price, Hoevers notes. He has no doubt however that higher-yield solar panels will be mass-produced in the future, and is closely watching developments in solar supply chains to see where production costs are likely to fall.
“An efficiency of 22% was considered lofty and exotic 10 years ago, and things are only moving faster in solar tech and manufacturing,” he observes.
“And if we want to get as much range as possible from our passive solar recharging without sacrificing weight, we need the highest energy density commercially available, so NMC lithium-ion batteries were a must-have to guarantee the lowest weight relative to kilowatt-hours that the Squad can store.”
The battery pack is made from four modules, each storing up to 1.5 kWh of energy, while the solar cells can charge at a rate of up to 250 W. The solar panel is expected to enable up to 20 km of driving per day during summer across most of the EU, while the batteries store enough energy for 100 km (and can also be charged using a 220 V input).
“Depending on customisations here and there, each Squad should cost between €5000 €10,000, positioning them between electric scooters which are €2500-5000, and conventional city cars that cost around €12,000-13,000,” Hoevers says. “That price works for mass production, and in EU certification terms it works for classing them as L6e – legally speaking, they’re effectively four-wheeled mopeds.”
Light, safe and aerodynamic
As mentioned, the energy consumption of the car has been a critical factor in making it viable for reliable and cost-effective urban mobility.
To improve energy efficiency, Hoevers and his team spent a lot of time and resources on optimising weight and aerodynamics. As such, its frame is a major part of its design.
“As with solar cells, if you try to go exotic with body and chassis materials to reduce weight, for example by making it all out of carbon fibre, you might find yourself burning through a lot of money very quickly,” he notes.
“During my years in racing, I saw brilliant uses of carbon fibre, but I also saw that it’s not coming down in price particularly quickly. It’s also not the easiest material to mass-produce, despite there being many variants for different price and performance requirements.
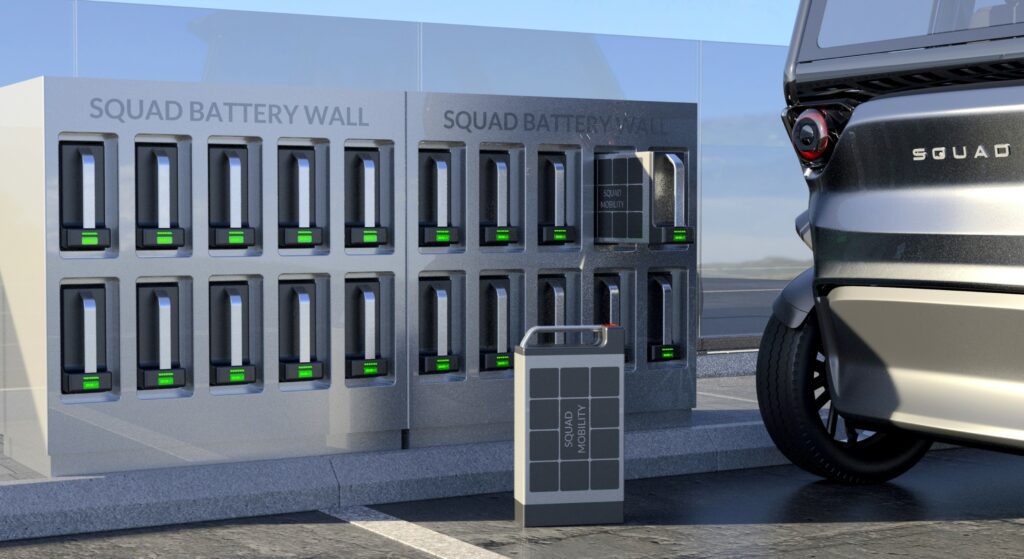
(Courtesy of Squad Mobility)
“You do see some marvels with carbon though. BMW for example have done a great job with the i3 to implement it with carbon fibre, but those are far more the exception than the rule in the automotive world.”
The major weight-saving move for the Squad has been to make the entire frame and chassis as extruded aluminium profiles. Customer feedback was a key motivator for going down this route – much of the research and trialling of the car has taken place in areas by the sea, and in city districts with hotel resorts and marinas.
“The air in those places is thick with saltwater humidity, so a request we kept getting was, ‘Please, make an aluminium version, or else it’s going to corrode really badly.’ Durability is necessary for commercial fleet and ride-sharing operators to get plenty of years of return on their investments,” Hoevers says.
He adds that aluminium is one of the most widely and efficiently recycled materials in the world, being a very pure element rather than a composite, with 60-90% of newly produced aluminium anticipated to be re-used later in its lifetime (depending on where it is made and exported). Making a lot of the car from aluminium therefore chimed with his and Klok’s earlier goal of widely accessible and highly sustainable mobility.
“Aerodynamics are a little less important than weight or sustainability, because we’re making a low-speed vehicle; it’s really only at higher speeds that drag becomes a serious issue,” he notes. “That said, airflow is still a major consideration in our design work because it also affects how we cool the PV cells.”
Cooling is critical to maintaining solar yield. As with any conductive material, excess heat is tied inextricably to losses, and Squad Mobility intends for its cars to be fully useable in hot cities where sunlight is most plentiful, from southern Europe to the Arabian Gulf and beyond.
“An aluminium backing is installed underneath our PV roof. That’s primarily done for mechanical reinforcement, but it also comes with the secondary benefit of acting as a very effective heat sink,” Hoevers explains.
“We’ve designed the roof shape not just to have airflow rushing over the top, but also the interior of the car guides a wash of cooling air underneath the roof to cool the aluminium. That means we maintain that 22% yield almost all of the time, without needing any cooling fans or other power-parasitic active thermal management systems.”
Passenger safety has also been a major factor in determining the shape of the Squad. As Hoevers explains, the structure has been designed to protect against crashes from both front and rear, although he adds that they were not required by certification to do so, and to his knowledge none of their competitors in their weight classes have done so.
“We also have a full roll cage, or rollover structure if you prefer, which is also not a requirement but fits well with the size and shape of the frame,” he says. “It helps protect passengers from shock or injury if there’s an accident, and further boosts the ruggedness and longevity of the Squad.
“Customers in the ride-sharing market tend not to always be careful with their vehicles. After all, they only have them for the afternoon in many cases, so we want our EVs to last even if customers are quite rough with them.”
To make the most efficient drivetrain possible, Hoevers and his team looked at a wide range of different configurations, including reductions, differentials and e-motor arrangements. The best solution overall for cost and energy efficiency was found to be a direct drive powertrain with two permanent magnet in-wheel motors at the rear and two inverters on the chassis.
Having the motors sitting in the wheels has also helped with packaging, as the batteries and other electrical and electronic systems could be moved around more freely, with no motors, gearing or axles to block them. The inverters are kept separate from the in-wheel motors to make it easier to mount and replace them if better systems come along in the future.
“We use field-oriented control inverters, which are a little more expensive than trapezoidal control but they’re much better in terms of performance, quietness and efficiency,” Hoevers adds. “They also give a smooth, controllable power output, which is great for rider comfort as well as regenerative braking.
“We use a single pedal drive system. Getting the regeneration right is vital for that, because if it’s too harsh you can give customers whiplash, yet if it’s too soft or doesn’t respond you won’t brake quickly enough.”
He adds that the company also looked into induction motors, but found that within the L6-L7 size class they came with a much smaller range of inverters to choose from. Their cost and controllability relative to those of small-form PM motor-inverter arrangements were problematic as well.
Future plans
While the current Squad car is classed as an L6e vehicle, Hoevers aims to produce a four-seater, class L7 version in the future, which will be faster and better at tackling inclines.
“We’re capped at 4 kW now – 2 kW per e-motor – but an L7 EV can output 7 kW or more,” he says. “That will give us more flexibility to design such a vehicle according to how the users want them.”
As that also brings opportunities to trial and adopt more efficient EV technologies, Hoevers and his colleagues are keeping a close eye out for new kinds of motors, inverters, battery cells and all the other critical points of an electric powertrain, whether it be new COTS systems or whether they decide to try their hand at designing such parts in-house.
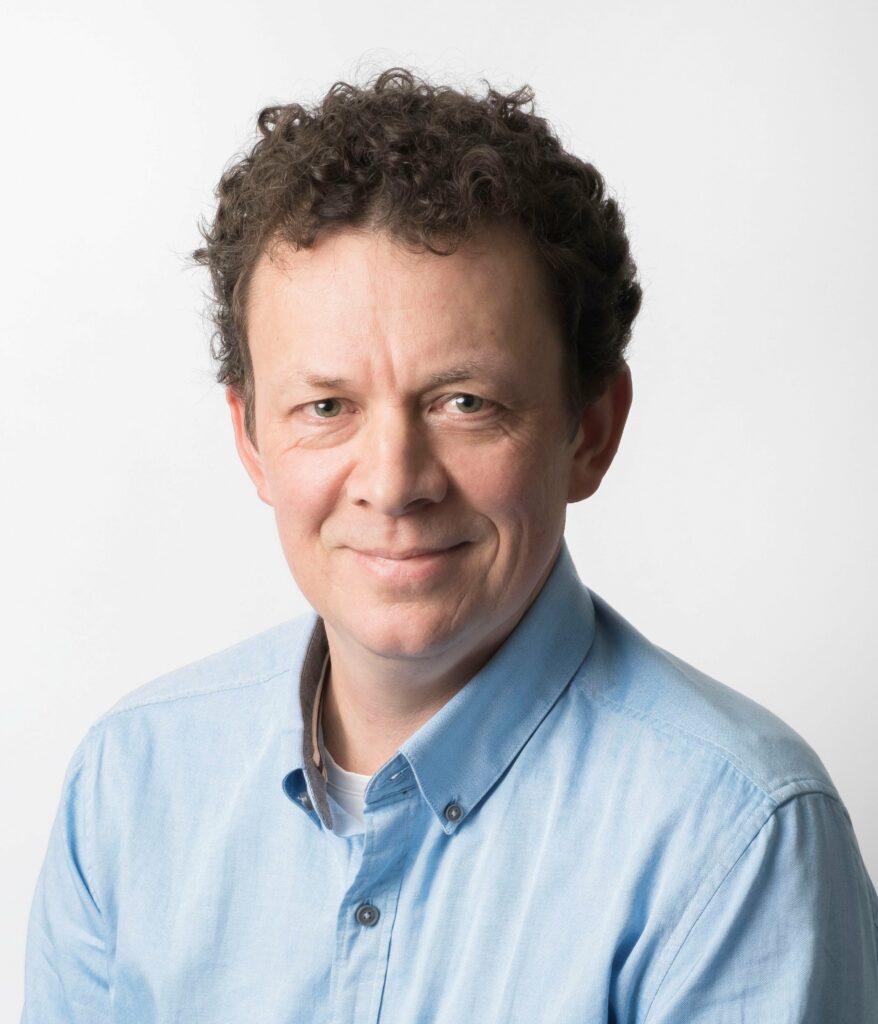
Robert Hoevers
Robert Hoevers is the CEO and co-founder of Squad Mobility, which is based in Breda, Netherlands.
He was educated at Rijnlands Lyceum Wassenaar before studying at the Technical University of Delft from 1989 to 1996 and achieving an MSc in Industrial Design Engineering.
Between 1996 and 2009 he held numerous positions across a variety of industries, primarily in IC engine-based racing but also across web development, food processing, home heating systems and others.
In 2009, he founded EPowerGP (which helped lead to the founding of Formula E), and he would go on to work as the commercial manager for Chinese e-mobility firm NIO and its Formula E team.
In 2018 he then started working for solar EV maker Lightyear. After about a year there he chose to form Squad Mobility as a new company to produce a solar EV that would be inexpensive and widely accessible compared with the Lightyear One.
ONLINE PARTNERS
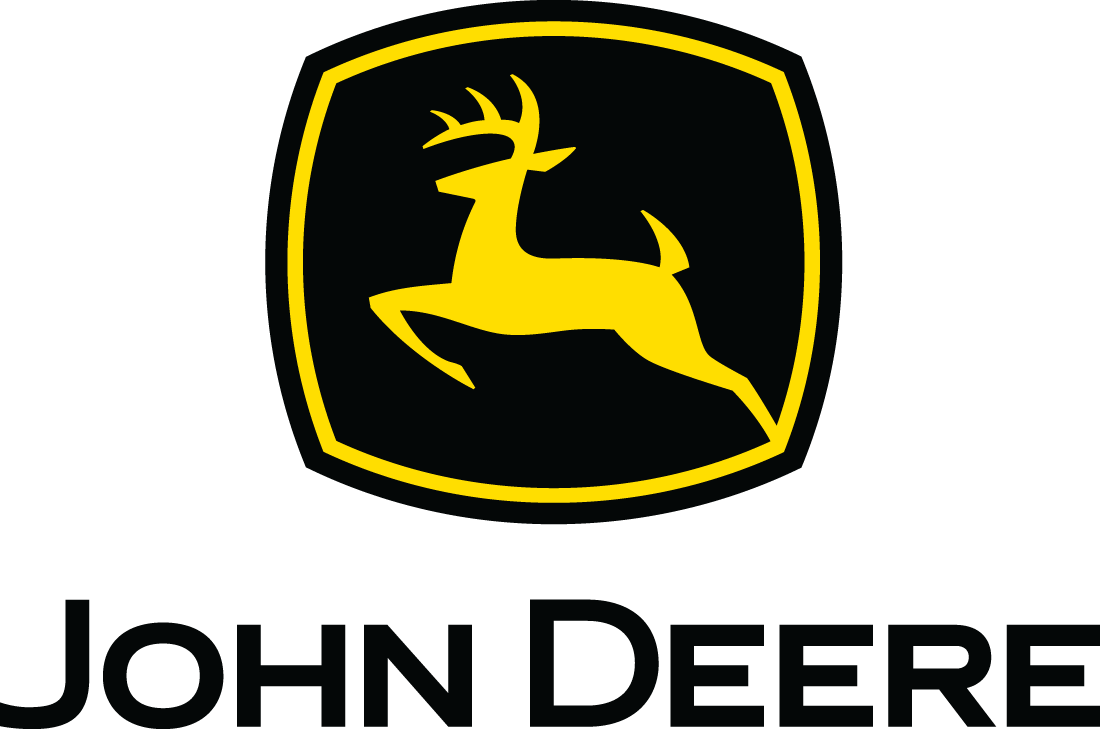
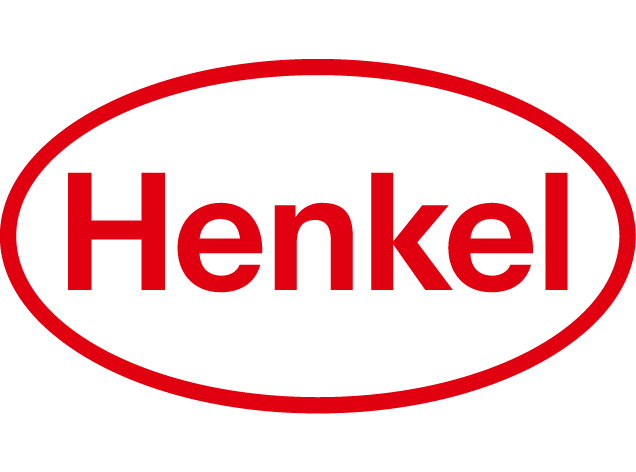
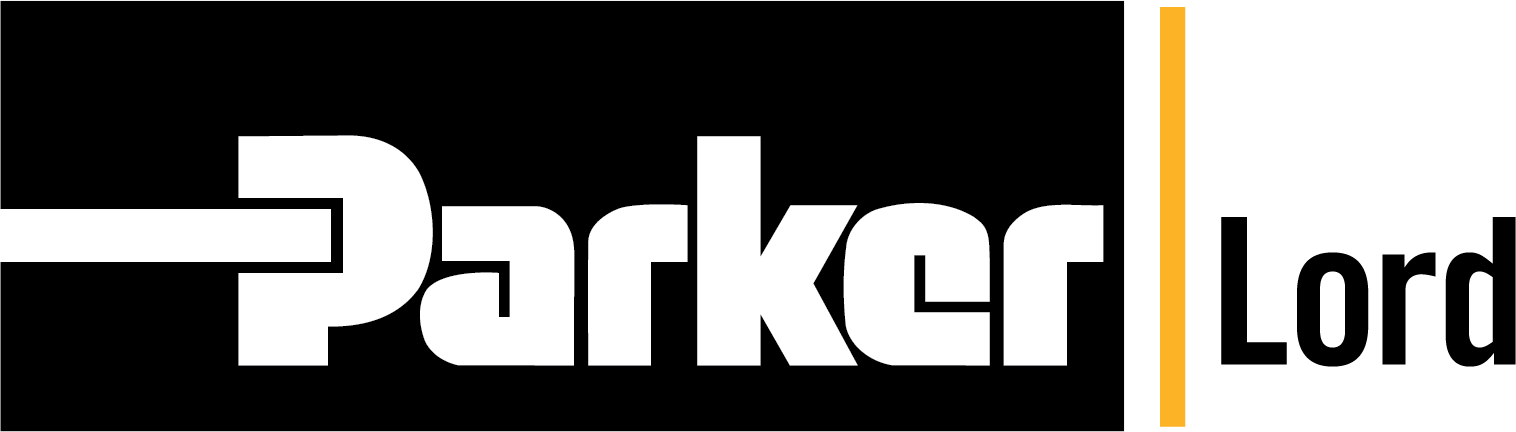
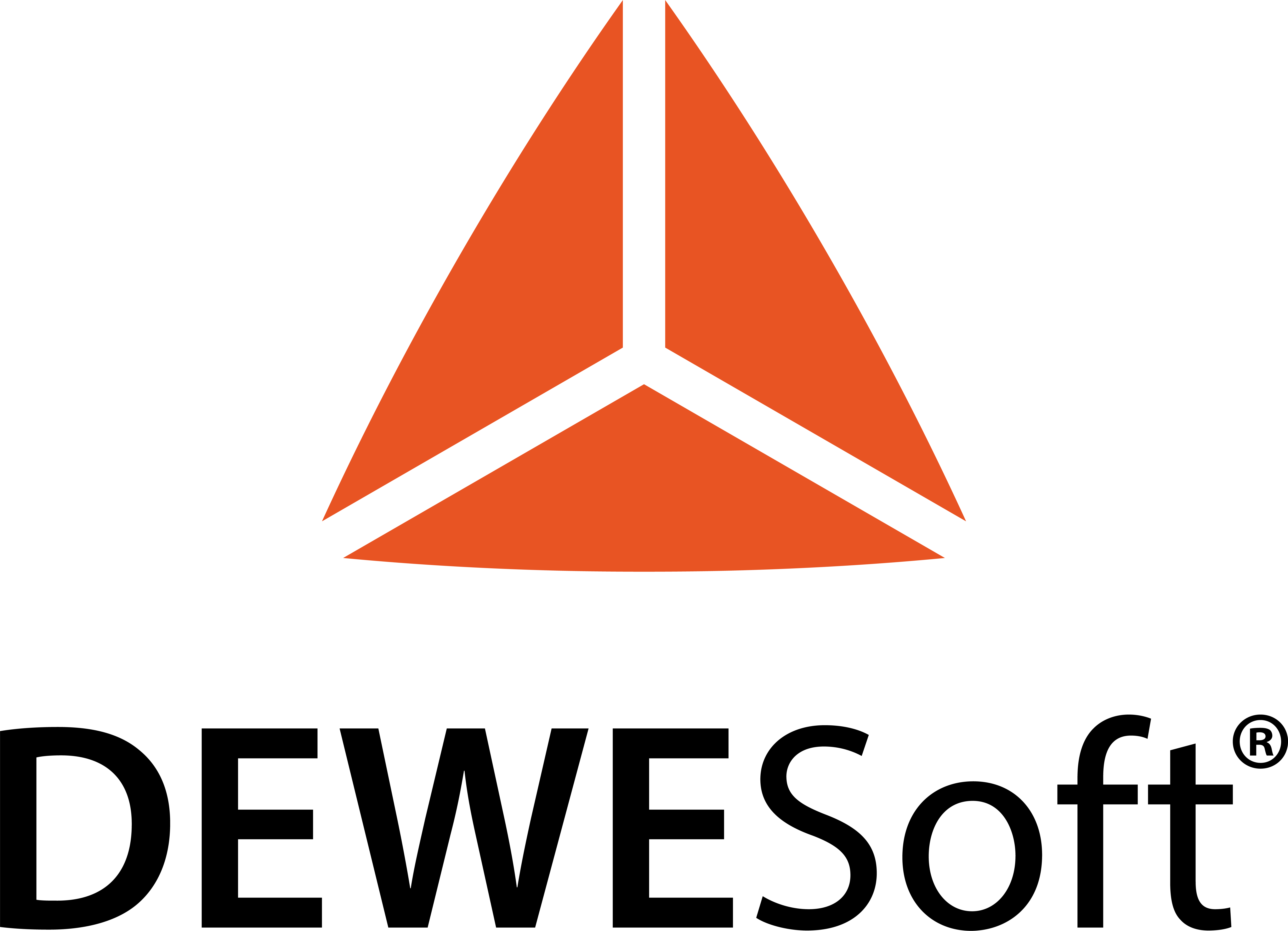
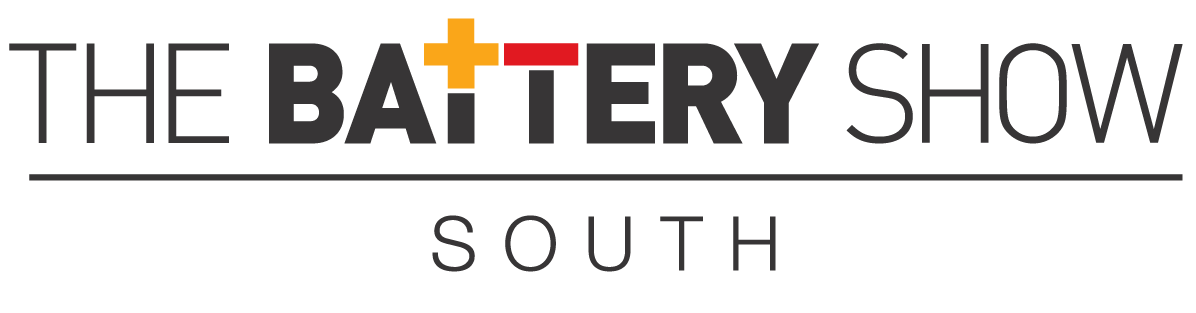
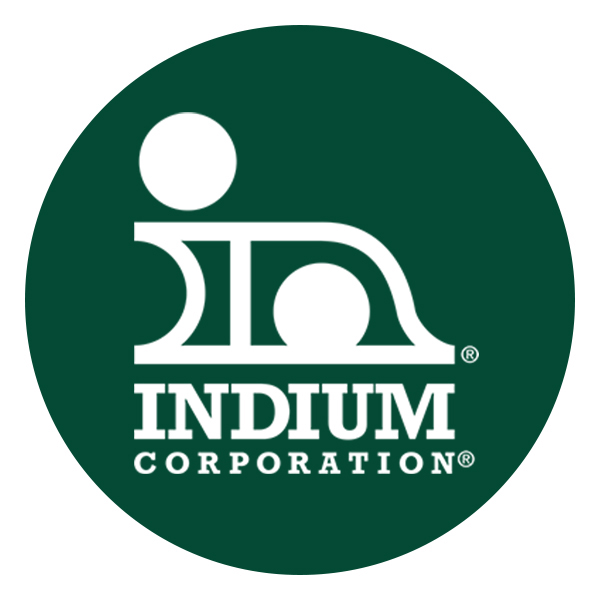
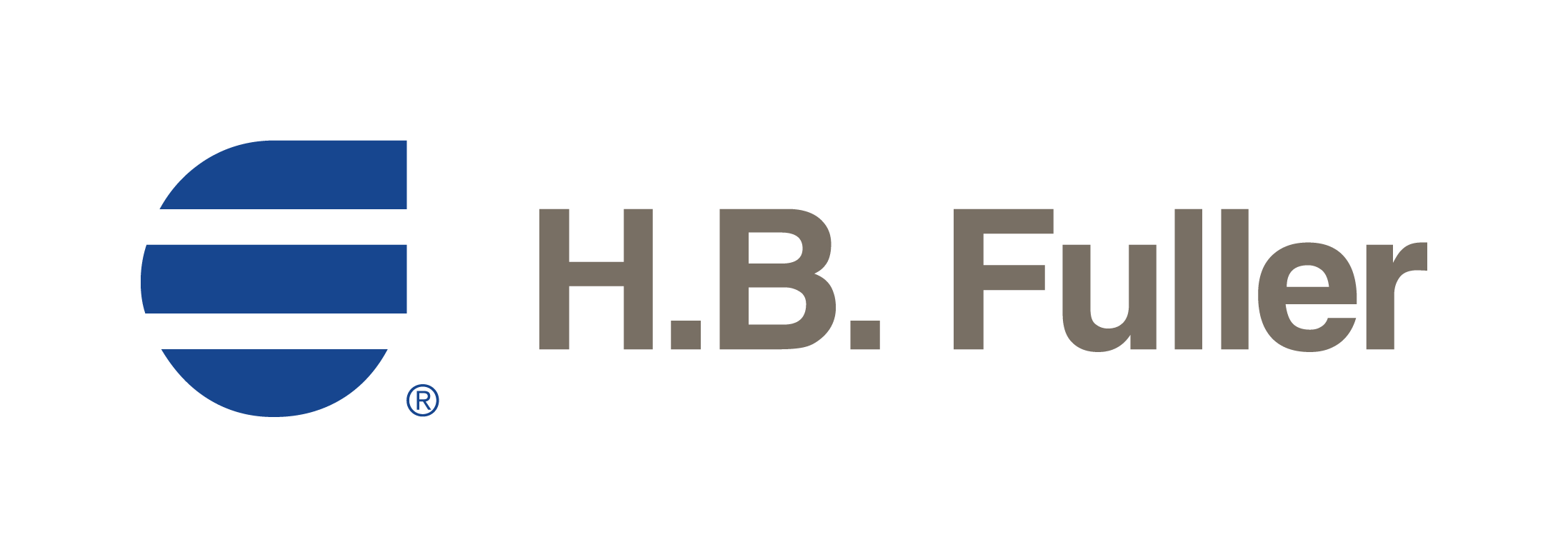