In conversation: Matt Faulks
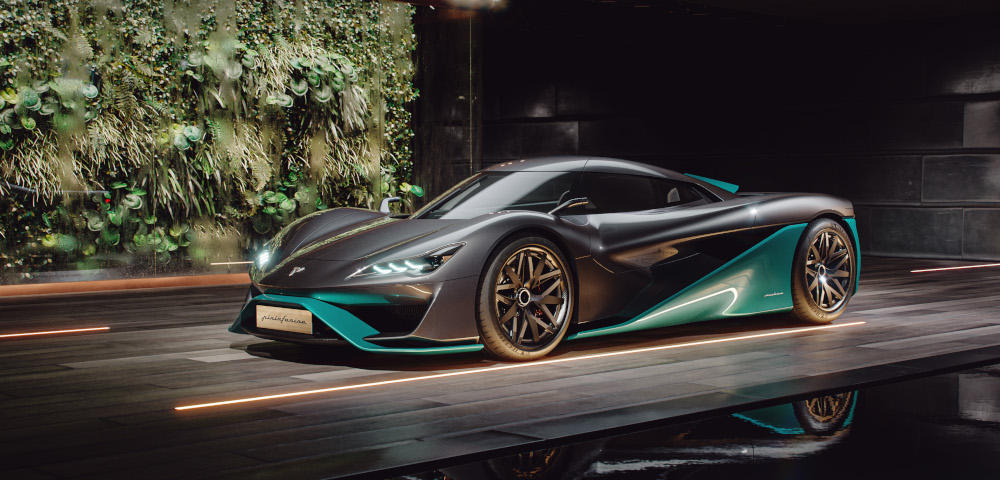
(Photos courtesy of Viritech)
Hypercars to HGVs
Viritech’s CTO tells Rory Jackson how fuel cell developments for its Apricale hypercar will feed into its upcoming heavy goods vehicles
Anyone who works in electrified and low-carbon automotive engineering should remember that developing solutions to the zero-emissions challenge is not a zero-sum game. Just as solar, wind, tidal and nuclear power all have a part to play in clean energy grids, battery and hybridised EVs alike are key to transitioning us towards sustainable mobility.
Any innovation in one could be an enabler or outright saviour for the other, hence battery, IC engine-hybrid and hydrogen EVs are not enemies of each other, and engineers across all these technologies will produce their best solutions through collaboration against their real, shared enemy – inefficiency, and the undue emissions that come with it.
These are the sentiments and driving philosophy of Matt Faulks, CTO of Viritech, the UK-based company known for its hydrogen-electric hypercar the Apricale (officially unveiled in its prototype form last year). It is also gaining attention for the rapid development of its 44 tonne Jovian FCEV (fuel cell EV) trucks and more besides in its future plans.
This inclusive attitude towards battery-electric powertrains might sound strange coming from the technology head of a company leading the charge for hydrogen-electric mobility and economies, but the hunt for efficiency has informed much of Faulks’ career in motorsport.
“I’ve worked in motorsport and with Formula One technology for over a decade – it might look strange that I’m now dedicated to carbon-neutral automotive, but you’d be hard-pressed to say that a modern Formula One car isn’t efficient,” he says.
“I started my motorsport apprenticeship just as data analytics were coming into the picture for race teams, so I got a great grounding in how to optimise fine engineering details, through racing as well as contracts with a lot of universities.”
He also notes that motorsport careers can be far more flexible than traditional automotive engineering careers, something that can educate motorsport engineers in the rapid creativity and persistence needed when engineering all-new powertrain configurations and production processes.
“There was a 24-hour race in 2003 where we had an engine failure in the first hour,” he recalls. “Most teams give up in that situation, and many people there were amused that we didn’t, but we changed the engine, and lost about 45 minutes getting the car back on track. Twenty-two hours later we finished [Le Mans, LM] P3 for our efforts.
“That podium stuck with me, because when you’re taking on complex, leading-edge systems there’s always a reason to give up or look for an easier, simpler way out. That mentality of sticking with it and pushing a little more – so long as there’s a commercial case for it and we think we can solve the challenge it presents – is something I’ve tried to bring to every project I’ve worked on. If we’re going to make zero-emissions HGVs, [heavy goods vehicles], aircraft and ships a reality in time to make a meaningful difference to climate change, we need that mentality.”
Hydrogen engineering
Viritech is best-known for the Apricale, its 800 kW (1088 bhp) hydrogen-electric hypercar. Weighing just under 1000 kg with a carbon monocoque chassis and a Pininfarina-designed body of recycled carbon and natural fibre, it has a top speed of more than 200 mph running on Dymag wheels and Michelin Pilot Sport 4 tyres. An approximate range of 350 miles is derived from 5.4 kg of hydrogen gas (pressurised to 700 bar) with a 6 kWh lithium-NMC battery pack configured for an 800 V DC output.
At the time of writing, the FCEV was in its late stages of testing, and production facilities are in development, on track for the car’s commercial release in 2023.
Although the Apricale has been front and centre of Viritech’s marketing to date, Faulks says the car’s true raison d’etre is actually the development and proving of technologies that will one day go into hydrogen-electric HGVs (licensed or produced by Viritech for use by OEMs and Tier-1s as required), as well as future heavy-duty vehicles on land, air and sea. These include looking at which supply chains can be used or created to fulfil scale production of Viritech’s key enabling technologies, and hence help remove the obstacles to hydrogen powertrain and fuel cell EV adoption.
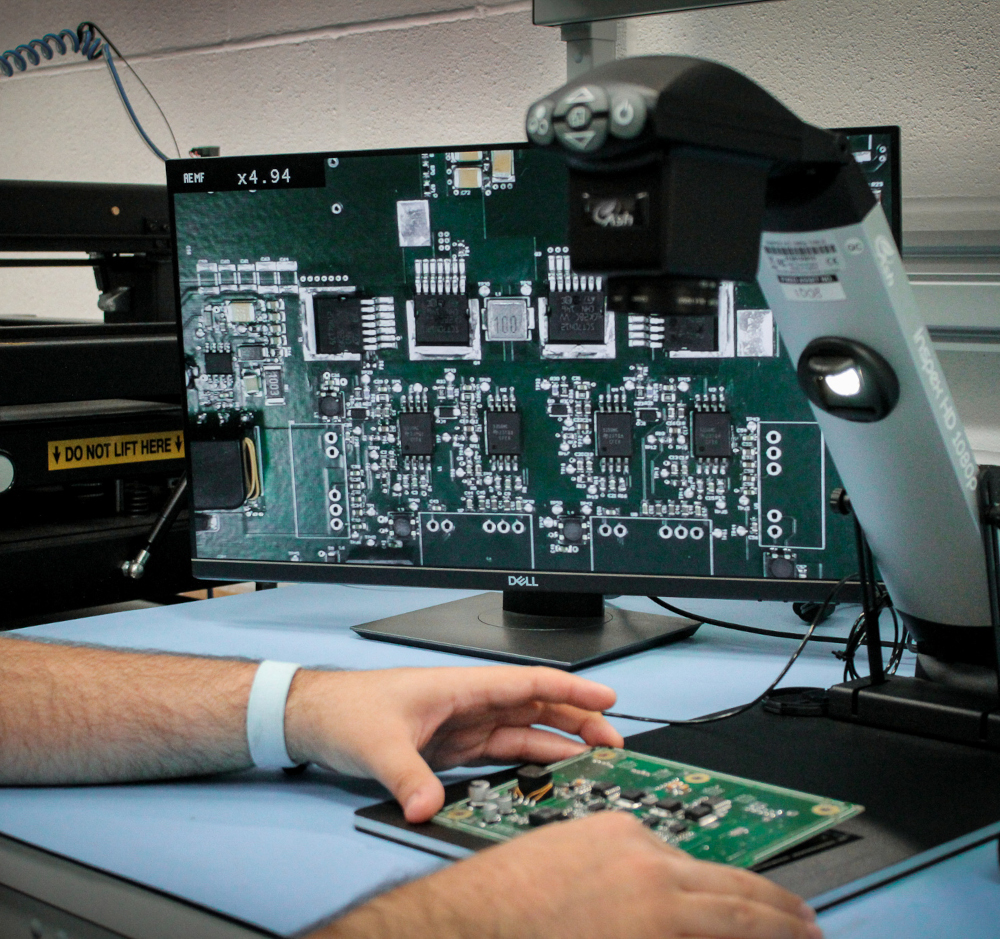
“HGVs contribute a massive amount to road pollution, and the heavier the vehicle, the better hydrogen fits as the energy carrier for electrifying it,” Faulks notes.
“We’re not anti-battery; they actually form a key part of how our powertrains function, but vehicle mass is compounded terribly when you try to satisfy HGV ranges with packs alone. Hydrogen is hundreds of times more energy-dense, which is why it works so well for vehicles with high power output requirements and high duty cycles, such as trucks and hypercars.”
Also, Viritech is fuel cell-agnostic, and can effectively use any type as its FCEVs’ power plants. Faulks expresses a particular interest in high-temperature PEM fuel cells (PEMFCs) and lauds the scale production of PEMFCs by Toyota and Bosch as well as the innovative PCBFC (printed circuit board fuel cell) designs of Bramble Energy, noting that the breadth of innovation in fuel cells makes it inefficient to put all of Viritech’s eggs in one basket.
That is why little of the company’s IP is in membrane electrode assemblies, bipolar plates or other technologies that are key to hydrogen fuel cell stacks. Its r&d has gone far more heavily into two other areas instead. The first are the energy management systems needed to balance the loads between battery and fuel cell across the entire driving envelope of an FCEV.
Energy management innovations
In the pursuit of efficiency, Viritech decided early on that using the fuel cell purely as a range extender would effectively mean combining the worst of both worlds into its powertrains.
“Nor were we going to copy Toyota’s approach, although optimising FCEV parts to work with an existing production line is genius, and really on-brand for them,” Faulks muses. “But on the surface, the Apricale and Mirai seem to function the same way: a fuel cell provides cruising power while a battery powers the transients. But the Mirai works using a roughly 130 kW PEMFC with a small battery that covers the transients while the fuel cell ramps up; that means its peak power is 130 kW.
“Through our Tri-Volt energy management architecture though, our peak deployable power has nothing to do with the FC’s size. Our ranges aren’t constrained by our battery sizes, and our performances aren’t constrained by our fuel cell sizes, so we don’t need a whopping great 800 kW fuel cell or a huge and heavy battery, which is critical to building a lightweight e-hypercar.
“Instead we can just use a 200 kW fuel cell, as well as a lightweight 6 kWh battery that can discharge at 100C – we’ve been building packs like that in Formula One for years – and combine them through a high-end DC-DC converter and some clever control systems. That gets you the 800 kW and ramp rates needed for sprinting with a hypercar, torque for a fully loaded HGV or take-off for an eSTOL aircraft.
“Say we want to do a 200 mph sprint. We max-out our starting acceleration using just the battery’s 600 kW output as the fuel cell ramps up, and beyond 125 mph we add the latter’s energy on top of the former.
“After that sprint, say we want to pull back to a 150 mph cruise: we can maintain that speed using just 175-180 kW from the fuel cell alone. And every time we slow down we’re regenerating a lot of energy for replenishing the battery, which again is easy to do because we have a very high C-rate pack.”
The high regeneration rates of Viritech’s energy management approach bear some similarity to those of the Riversimple Rasa FCEV (featured in EME 10, Summer 2021). Faulks notes however that that car’s energy deployment topology is less flexible and sophisticated than that being proven in the Apricale, in which any combination of fuel cell and battery can be used for the power, torque and speed modes unique to each application.
“While supercapacitors work great for the Rasa, they don’t fit our energy density requirements; our batteries pack a lot of energy into very small spaces,” he says. “Ultracapacitors give us megawatts per second, whereas conventional battery EV (BEV) packs give us kilowatts per hour. We needed something in between, at hundreds of kilowatts per minute.”
The company has therefore developed its own proprietary DC-DC converter in-house using silicon carbide (SiC) technology to achieve the high switching speeds necessary for sending kilowatts per minute to its inverters using both battery and fuel cell simultaneously.
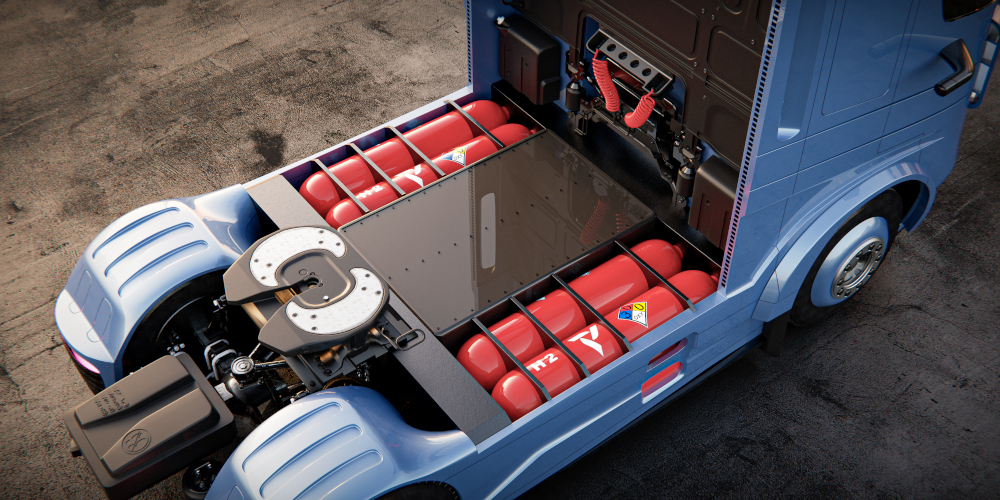
“In functional terms, we use SiC in our DC-DC for the same reasons it’s used in e-machine inverters: it’s lighter, smaller, and easier to mass-produce than silicon MOSFETs and IGBTs,” Faulks says. “All that, together with its power density and minimal cooling requirements, mean you’d be crazy not to go that route.
“And the argument of it being too expensive doesn’t hold much water when we’re seeing so many BEV inverters using SiC. Granted, it’s more complicated, and the control system requirement is much higher, but the benefits make it worthwhile, especially in terms of lighter weight. Right now a 60 kW DC-DC weighs 25-30 kg; we want something under 10 kg if we’re to make power electronics with the low weights and very high outputs and duty cycles necessary for commercial EV fleets in the future.”
To develop the control architecture required for Viritech’s high-power, high-speed energy management, the company keeps all the necessary software programming and hardware design and manufacturing in-house, including making its own PCBs, and keeping abreast of automotive requirements such as ISO 26262 and ASIL-D.
“Both the control board and the DC-DC board are modular,” Faulks adds. “We have a specified design for each, and we can daisy-chain them for ever-higher power requirements, so scaling our technology for bigger EVs is sensible and straightforward.”
Rethinking hydrogen tanks
As mentioned, energy management has been one major area of focus for Viritech’s r&d, the other has been how to pressurise hydrogen at 700 bar with minimal mechanical complexity, and hence improve the energy density of hydrogen gas (which is less than its very high specific energy). The company says that, typically, 5 kg of hydrogen requires a 100 kg tank, which also needs either heavy attachments for cars or external frames for trucks.
In Viritech’s FCEV chassis, therefore, the hydrogen tanks double as structural, load-bearing members. That does not mean the tanks are subjected to huge torsional loads; however, extensive FEA and testing is performed to ensure the safety of the tanks and their contents under all load cases.
“While there’s lots of talk about lightweight vessels, in reality there’s a certain pressure delta you have to work to, with a minimum requirement of carbon and resin no matter what,” Faulks says. “We’re heavily researching Type 5 [linerless] tanks, but to reduce that minimum material requirement without adding insane costs requires breaking the laws of physics.
“As standard, the tanks are actually engineered to three times their failure rate and hence could hold 2100 bar of pressure, so using that strength to support the chassis allows us to take weight out elsewhere. As I’m talking to you I’m sat just 75 m from one of our test mules that has a structural pressure vessel in it, currently pressurised to 700 bar; we’re continuously studying how best to apply that tank’s strength in different monocoques, and nothing beats real-world data for research quality.”
Electric energy economies
Viritech also sees the green grid of future sustainable economies as being well-placed for producing and storing hydrogen gas, which Faulks notes would address the supply issues that some tout as a reason not to use as part of efforts at decarbonisation.
“The argument stands that BEVs and FCEVs aren’t emissions-free because the grid isn’t emissions-free, which isn’t untrue,” he says. “But let’s say it’s 30 years in the future, and 100% of Britain’s energy is supplied by wind, tidal and solar energy, and instead of petrol and diesel we have plug-in and hydrogen stations.
“If we’re to take all our energy from wind, waves and sunlight, we’re not going to have a consistent supply from the grid. There will be periods of excess production, so we might as well make hydrogen from it for cleaner, denser energy storage and transportability. Then we can expend that hydrogen in fuel cell generators, rather than overload the grid or cover areas of the country in massive and not particularly green battery stations.”
Viritech is now exploring the potential for such grid usage through a hydrogen energy station proof-of-concept design, which it is developing with two commercial partners also interested in how an optimally efficient nationwide refuelling and recharging infrastructure might be developed.
Future green tech
Although Viritech plans only limited production of the Apricale, bulk production of its energy management systems in-house and of its hydrogen storage and battery systems by suppliers are expected to follow, to enable production of the Jovian and other commercial fleet FCEVs.
“Toyota and Intelligent Energy have shown us that PEMFCs can be mass-produced, and Bosch are scaling up production as we speak. And the necessary mineral and rare earth supply chains to do that are essentially no different to what we use for making catalytic converters. In contrast to batteries, those are the one bit of production IC-engined cars that we’re actually very good at recycling, because they’re worth it on a per-gram basis.”
Viritech is also working with a large, undisclosed OEM on how best to recover and reuse the carbon from its structural tanks. That will most likely find a second life as chopped fibres in monocoques, and then a third life as further-chopped fibres in dashboards and interior trim panels, eventually serving in seat fillers or similar applications.
Faulks meanwhile plans to steer his company’s research into cost-optimising its battery technologies for truck manufacturing, and closely watches companies such as Superdielectrics for their promised developments of supercapacitors with higher energy densities than lithium-ion batteries.
He and his colleagues also track developments in LFP cells, which use similar materials and hence supply chains as fuel cells, and stand to reduce the EV world’s dependence on nickel, manganese and cobalt. He also keeps a close eye on HT-PEMFCs (‘HT’ meaning high temperature) anticipating much of the heavy-duty e-mobility industry investing in this technology and its scalability in the future.
“Although we’re on track to manufacture our hypercar and start prototyping the FCEV truck later this year, with aircraft and marine testing mules to follow in the years ahead, for us it isn’t principally about building EVs – spreading our enabling technology for high-efficiency powertrains is everything to us,” he says.
“If a world without carbon emissions is going to happen, we need the best combinations of technologies for every application, starting with the best of batteries and fuel cells.”
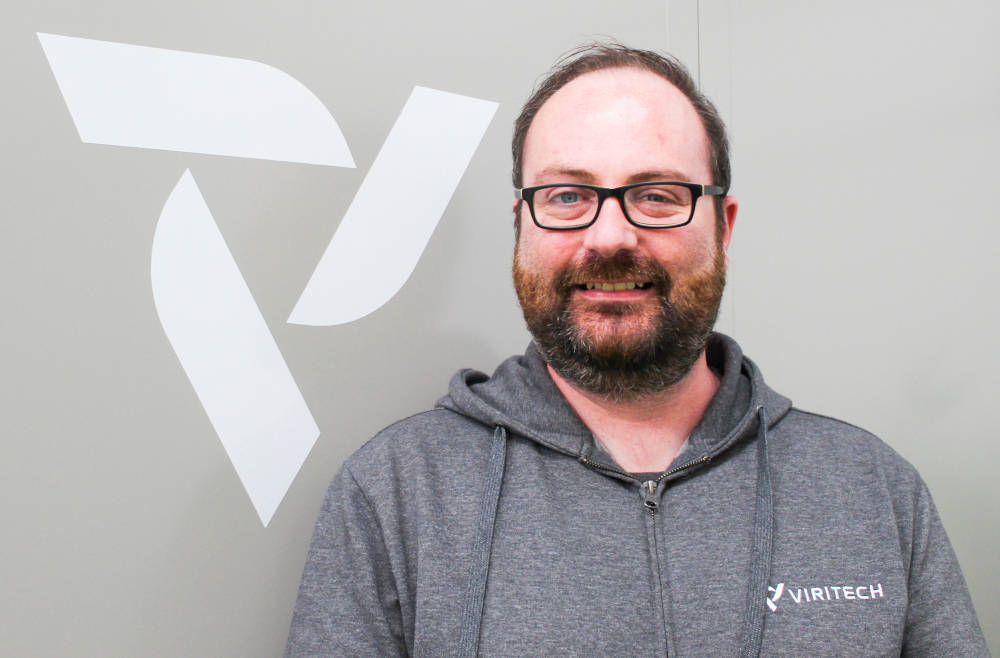
Matt Faulks
Faulks began his motorsport apprenticeship at 16 while at college, electing at 18 to continue down the apprenticeship route with Formula Ford. He went on to work across teams in the British Touring Car Championship and Formula One, as well as some high-performance roadcars including the 580 kg, 305 bhp BAC Mono, before co-founding Viritech with CEO Timothy Lyons in 2020.
Before that he also founded and managed TDF for 9 years, which contributed to Formula One Management-s Global Partner programme across the late 2010s.
Faulks now works from Viritech’s facilities in the MIRA Technology Park, in Leicestershire, England.
ONLINE PARTNERS
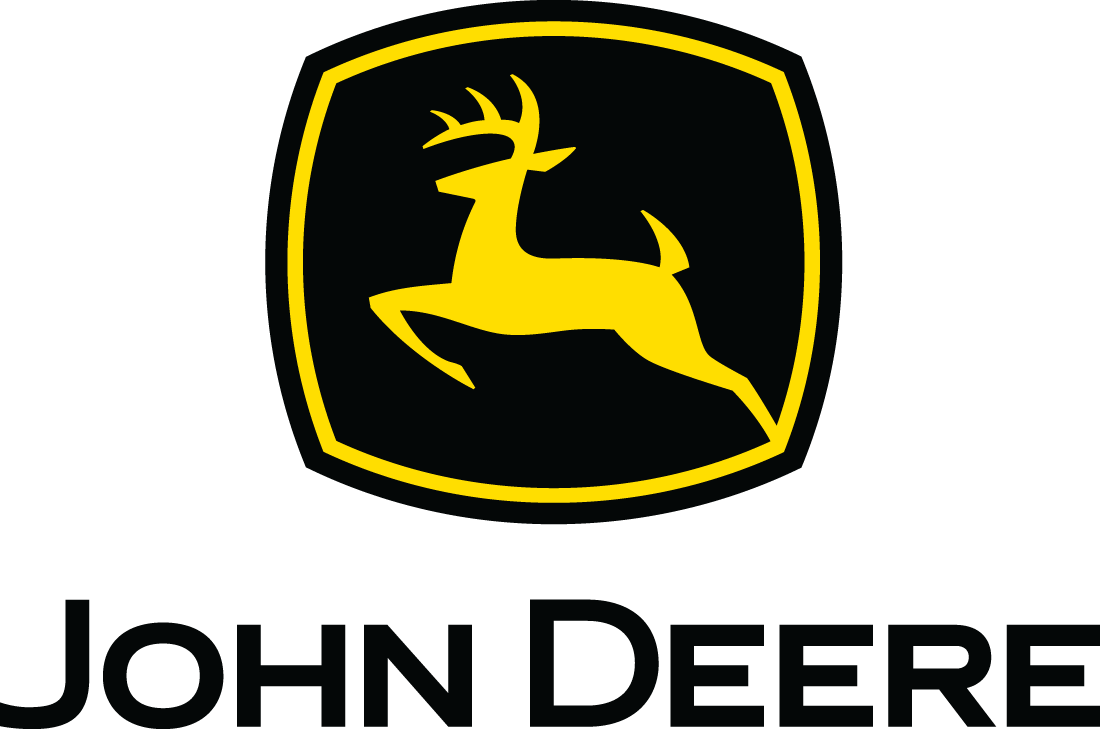
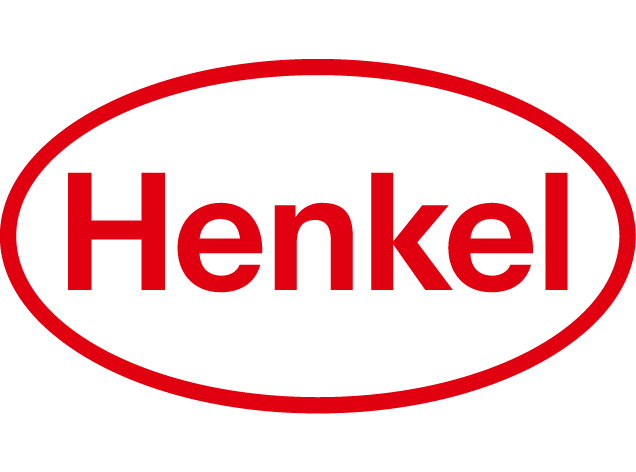
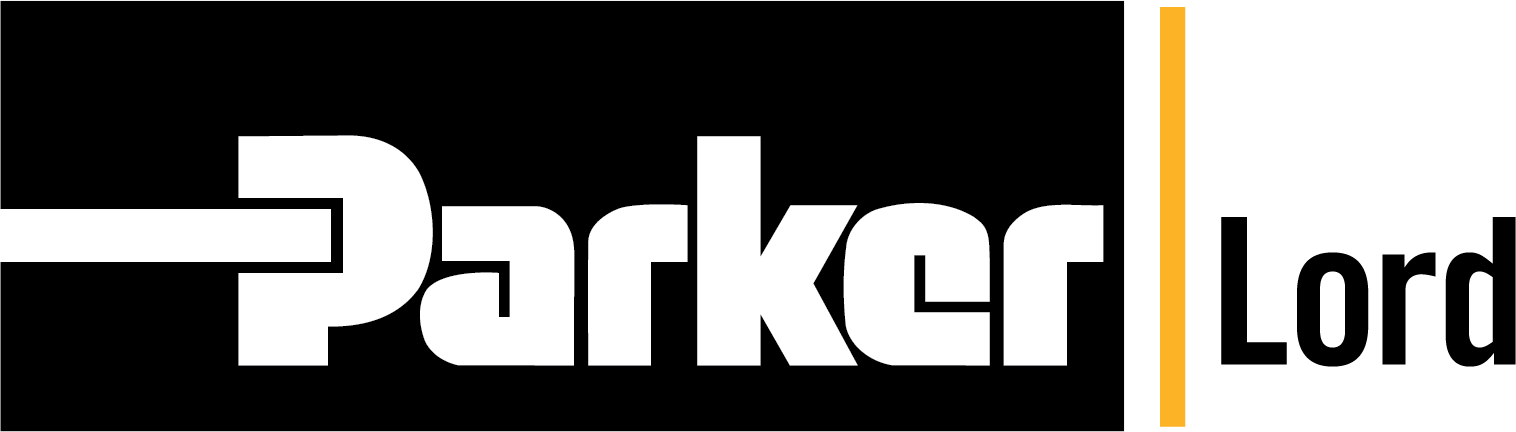
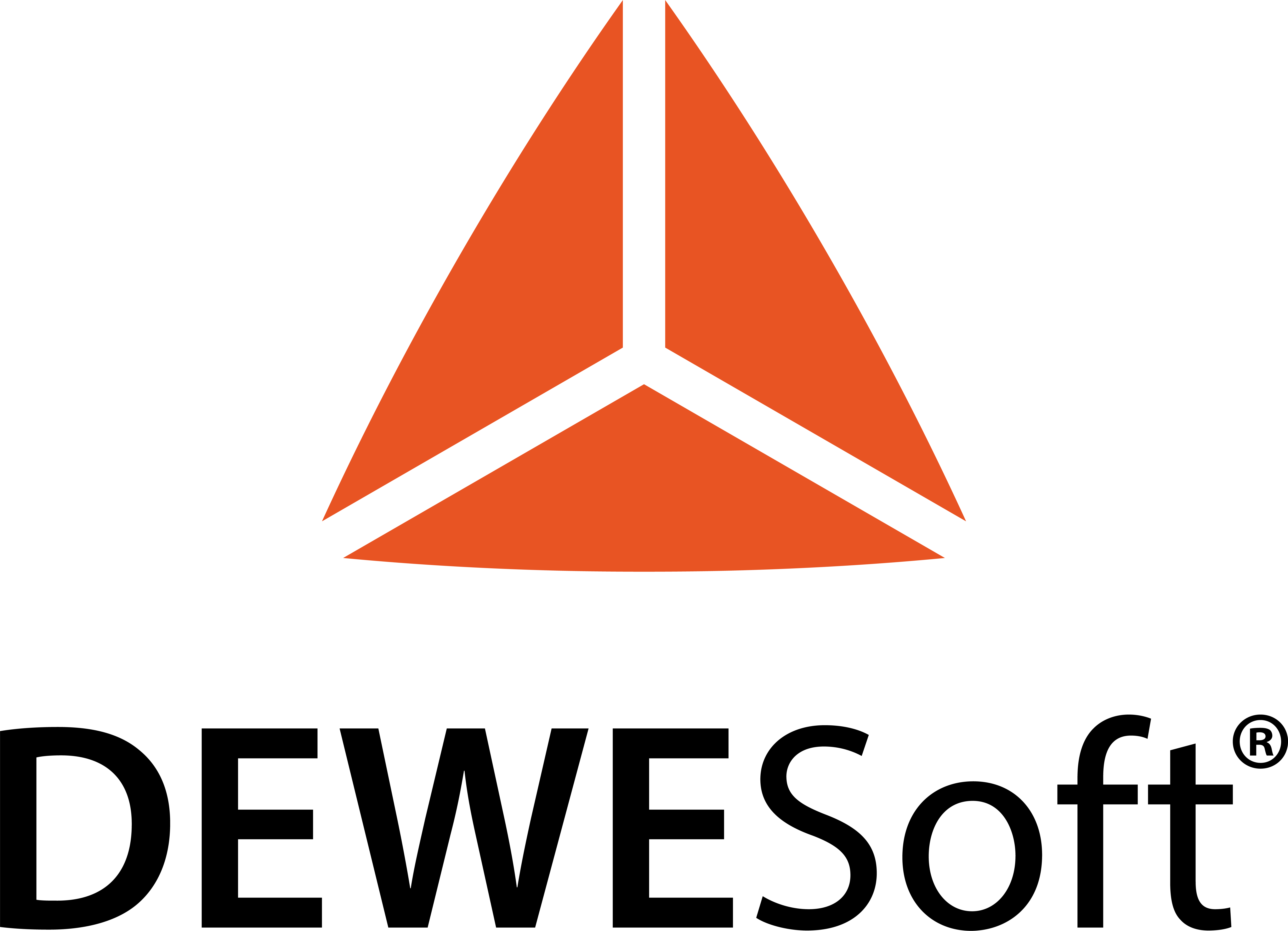
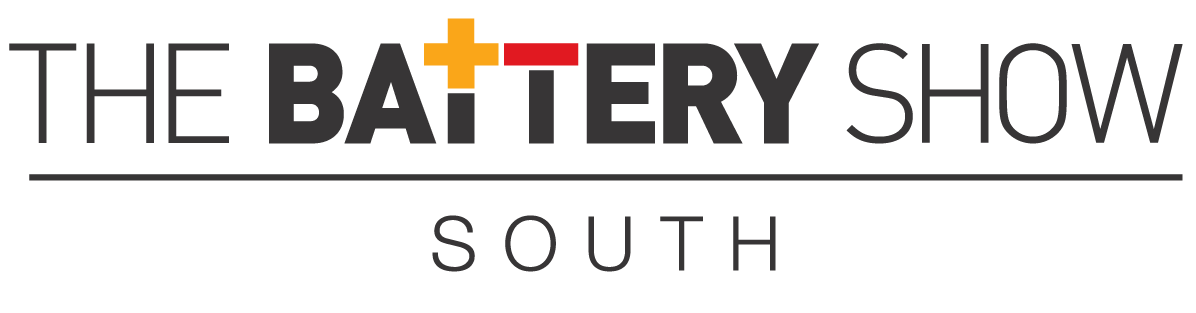
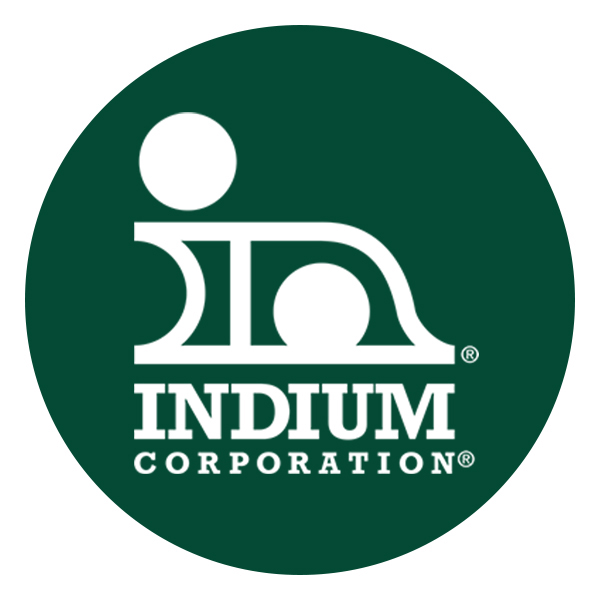
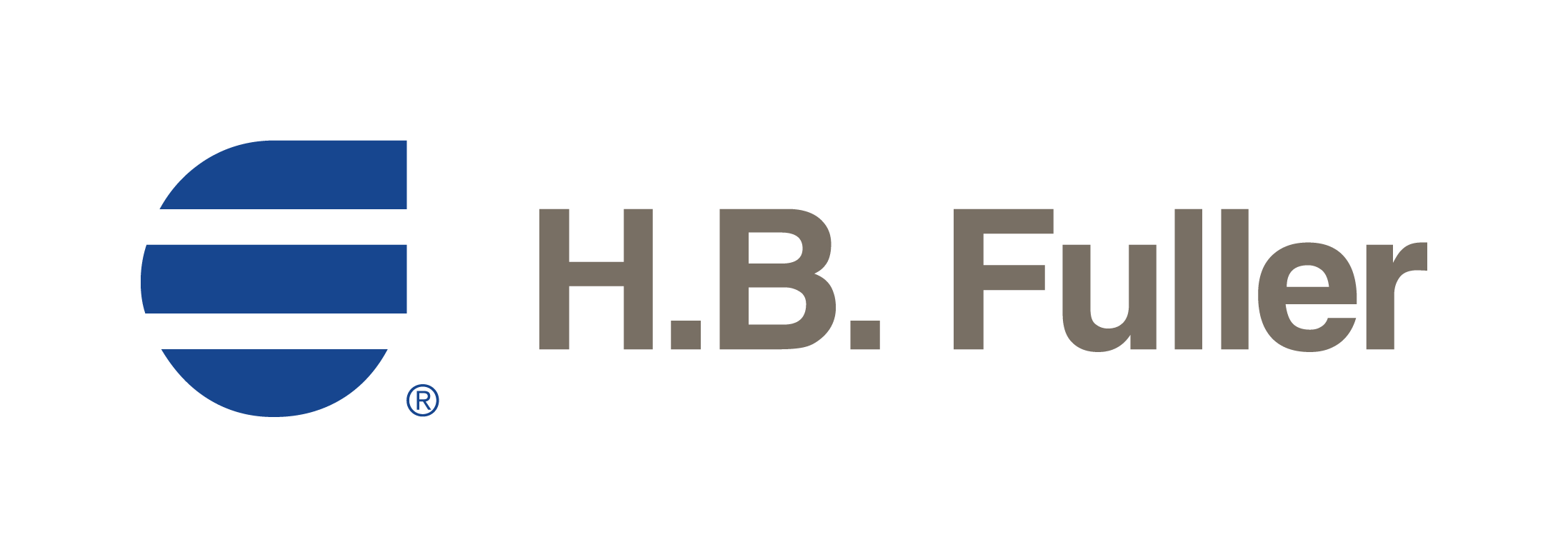