Immersive cooling
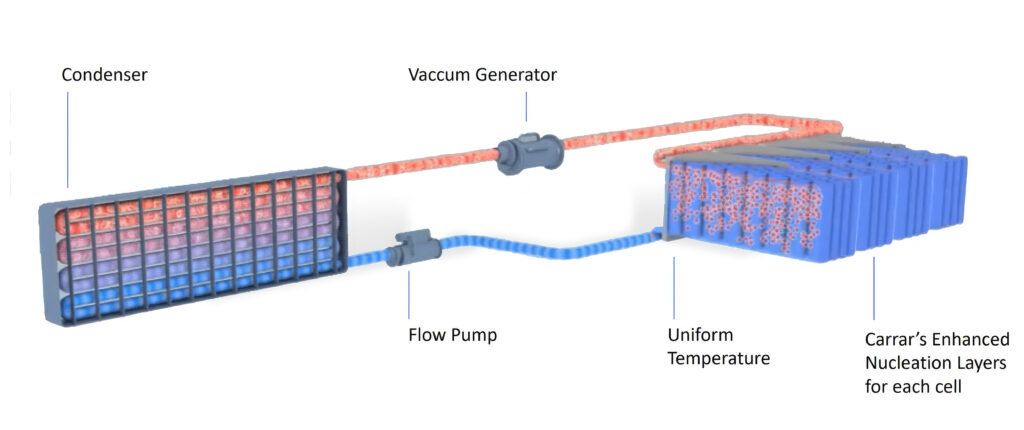
(Image courtesy of Carrar)
Flow motion
Nick Flaherty explains the advantages of immersion cooling and the various forms that approach can take
Immersive cooling can significantly improve the performance of e-mobility powertrain designs, allowing higher charging and discharging rates and extending the life of battery packs by keeping the temperature of battery cells under much tighter control.
Immersive cooling technology is being adopted in the data centre, with dielectric fluids covering processor boards to carry heat away from higher performance chips. The same approach is being used for electronic control units (ECUs), battery packs and even motors in vehicle designs. This cuts out many elements of a traditional liquid cooling system, such as the cold plates that are inserted in battery packs or the heat sinks for power electronics, reducing the weight of the powertrain. The use of immersive cooling can also allow components to be closer together, reducing the overall size of the powertrain.
There are several different ways of implementing immersive cooling. One of these is employing single phase dielectric fluids that can carry away heat from a battery pack, using a radiator to disperse the heat. Dual phase liquids close to their boiling point are also used to take the heat from cells to turn into a gas that is then recovered in a condenser. The move to using hydrogen also opens up the opportunities to use the liquid hydrogen as a coolant in battery packs and even in motors before being used by a fuel cell stack to produce power.
The adoption of immersive cooling also puts more pressure on the design of the fluid conveyancing systems, whether by hoses or steel or aluminium pipes, around a vehicle.
Single phase cooling
Single phase cooling uses a dielectric fluid with a high thermal capacity to carry heat away. The fluid has to be insulating so that it can be used with the electronics in a battery pack such as temperature, voltage and current sensors, and also for the busbars that carry large amounts of current.
The viscosity of the fluid is key for the ability to pump the dielectric around the pack and to the radiator. “We started almost five years ago with a couple of research projects,” said Andrew Ennever head of electrification at Ricardo which has developed several immersion systems. “Immersion cooling was an opportunity to improve thermal performance,” he explained.
In 2021, Ricardo joined the Inception collaborative research project, led by Blue Bear Systems (now Green Jets). The Inception project’s objective was to develop a highly power-dense, zero emission, quiet and efficient aircraft propulsion module.
“We developed a highly power dense immersion cooled battery pack, that wraps around the inner surface of the propulsion module nacelle. The pack is made up of 32 extremely lightweight bonded composite and foam modules, each module containing 48 Molicel cells,” added Ennever.
The immersion cooling allows the significantly higher operating temperature of 75 C and faster charging at 6C rates if the cell chemistry allows without getting too far above the operating temperature.
This higher charging rate is key for a fast operational turnaround on the ground to recharge the batteries of a UAV. Immersion cooling also extends battery lifetime due to even temperature distribution in the cells and between the cells, which cause slower degradation rates and increased pack life.
The advantage of the immersion cooling is bringing components closer together to improve the volumetric density over other cooling approaches as the cooling fluid can be used with the battery pack, the power electronics and to cool the motor.
“We can achieve increased volumetric power density because the battery cells can be packaged more closely together”, explained Bahareh Yazdani, Ricardo’s Technical Authority for batteries. “This is possible because the dielectric cooling fluid, passing between the cells, improves cooling performance. The improved cooling performance also enables downsizing of components like the busbar and removal of complex components like the cold plate.
“These weight savings offset the increased mass of the cooling fluid and pump, meaning we can achieve a similar, or slightly improved, gravimetric power density too. It also helps us maintain or reduce the overall battery pack cost.”
Using immersion cooling also extends equipment lifetime as it eliminates hot spots in the batteries since the dielectric fluid surrounds the cells. This allows higher performance with higher discharge and charging rates and avoids the risk of thermal runaway. That happens when a cell overheats and causes the neighbouring cells to heat up, potentially leading to a fire.
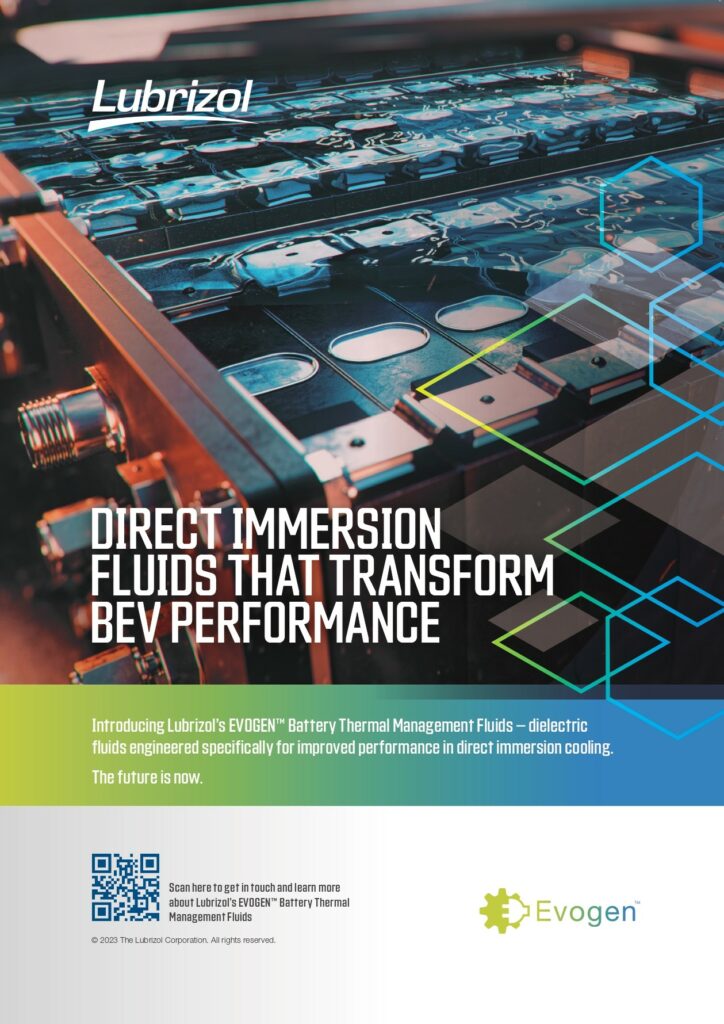
“The dielectric is a good shield between the cells,” said Yazdani. “We have tried to instigate thermal runaway and we haven’t been able to.”
The dielectric is an organic fluid based on esters and Ricardo worked with the fluid suppliers for compatibility of the fluid for the immersion system. “The viscosity, heat capacity and thermal conductivity all need to be optimised to give the best performance,” said Yazdani. “The viscosity is key for the definition of the pump.”
Unlike oil or refrigerant fluids, the dielectric fluid is recyclable and can be filtered and reused for the lifetime of the pack.
A key part of the design is to simulate the best pressure release valve. If the cells vent gas then the size of the valve needs to allow the gas to escape without letting the dielectric out. The pressure is used to drive the flow of the dielectric through the battery pack at around 3 Pa (three atmospheres). The pressure depends on the size of the module and the form of the cells, whether they are pouch, cylindrical or prismatic.
“You want a minimum cell to cell distance but the best performance and not to destroy the thermal exchange and stop the flow of the fluid and you need to consider cell swelling in pouch,” said Ennever. Using pouch cells needs a support framework for the cells with channels between the cells for the fluid to flow, but this is lighter than a cold plate system that would have to be implemented every two cells.
Another advantage is that immersion cooling also cools the busbars directly. Tab welding is the main hot spot, and the immersive cooling fluid can completely surround the busbars. This in turn allows for smaller, lighter busbars to be used.
Ricardo has completed several immersion cooled battery projects for customers in both passenger car and heavy-duty truck markets.
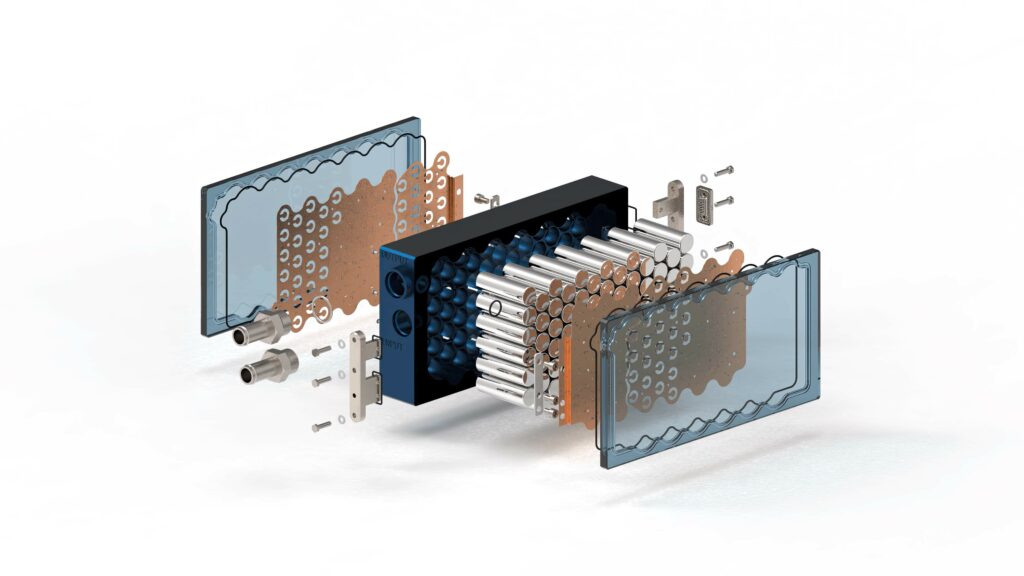
(Image courtesy of Ricardo
Dual phase immersive cooling
Carrar and Röchling Automotive are developing the first EV battery modules with Two-Phase immersion thermal management. The partnership results in lightweight, fully-sealed battery modules built in plastic for simplified manufacturing. These can be built to fit any battery cell and every chemistry.
“The Carrar thermal management solution prevents thermal runaway and greatly increases the safety of the batteries for electric vehicles,” said Marco Barbolini, global product manager, Röchling Automotive. “Keeping the battery temperature at the optimal range, Carrar also enables batteries to last twice as long, helping to cut back on battery production and its environmental impact.”
“We treat everything in the system as an evaporator so the battery cells are the evaporator,” said Eitam Friedman, chief technology officer at Carrar. He explains that Carrar is using commercial refrigerant liquids as the cooling fluid, ones which have a low boiling point, and is adjusting that boiling point to match the ideal temperature of battery cells. “What we have developed is manipulating the boiling process at very low heat densities so we manage to have great heat dissipation capabilities. In normal operation this leads to low heat generation, but in a pack it is large amounts of heat so we reduce the temperature difference between the boiling point and the cell.”
While many cooling systems have a thermal gradient of 10 to 15 C, the dual phase immersive cooling has a gradient of just 1.5 to 2 C, which allows lighter enclosures so the system is more efficient. For an operating temperature of 25 to 26 C for the pack the target boiling point of the liquid will be 24 or 23 C within atmospheric pressure, although Carrar can work in a slight vacuum and positive pressure meaning that can be a temperature of anywhere from 15 to 35 C as Friedman explains.
“It’s easier to design for positive pressure, harder for vacuum and because the pressure range is low it is not for a very deep vacuum,” Friedman said.
“This type of fluid handling is an engineering challenge we are solving all the time. It’s easier to work in positive pressure for the other components,” he said. Carrar controls the pressure inside the pack, typically from 0.7 bar to 1.1 bar, so that the boiling point of the refrigerant will be at the required temperature.
The fluid then goes as vapour to a compressor and to a condenser to bring it back to liquid and then goes back to the modules. Keeping the temperature at 25 C allows fast charging and discharging at rates of 3C or even higher. “When you are talking about phase change you are talking about the specific heat to latent heat transfer and with latent heat there is almost no limit to the amount of heat you can remove in theory,” Friedman said.
The limit is the condenser. A rule of thumb is that a condenser is four times more efficient than a radiator. “We have shown that we can extend the time of the high C rate; eg for 2C or 3C we can do it continuously. For a 60 x 40 mm condenser that is 30 mm thick we can dissipate 25 kW while keeping the batteries at 25 C.”
The biggest reservoir is the battery modules, but the gas phase from the outlet of the modules travels to the condenser and there is a small volume to pump some of the refrigerant back to the modules. A 100kW battery pack typically uses 20 litres of dielectric in the pack with 2 litres circulating in the rest of the system.
Compressor
Another part of the system is a compressor, which is only needed for specific applications such as high ambient temperatures or for fast charging.
“It depends on the ambient temperature if we need a compressor; it’s usually only needed for high ambient, say at 45 C, or for fast charging,” Friedman said. “We are developing a specific compressor for our system with a coefficient of performance (COP) of 5, so with 5 kW input we can dissipate 25 kW of heat with a typical 2 litre volume.
The compressor sees only the vapour and this is one of the challenges; to compress the vapour to 3 or 5 bar at 55 C at the inlet to the condenser. “We need to keep the refrigerant as close to the boiling point as possible so we design the system to the extreme points; 45 C or -30 C, and usually these are the challenges,” remarks Friedman. “In the medium range the system is much more efficient as the compressor can control the speed of converting the vapour to fluid and in this way manage the pressure differences.”
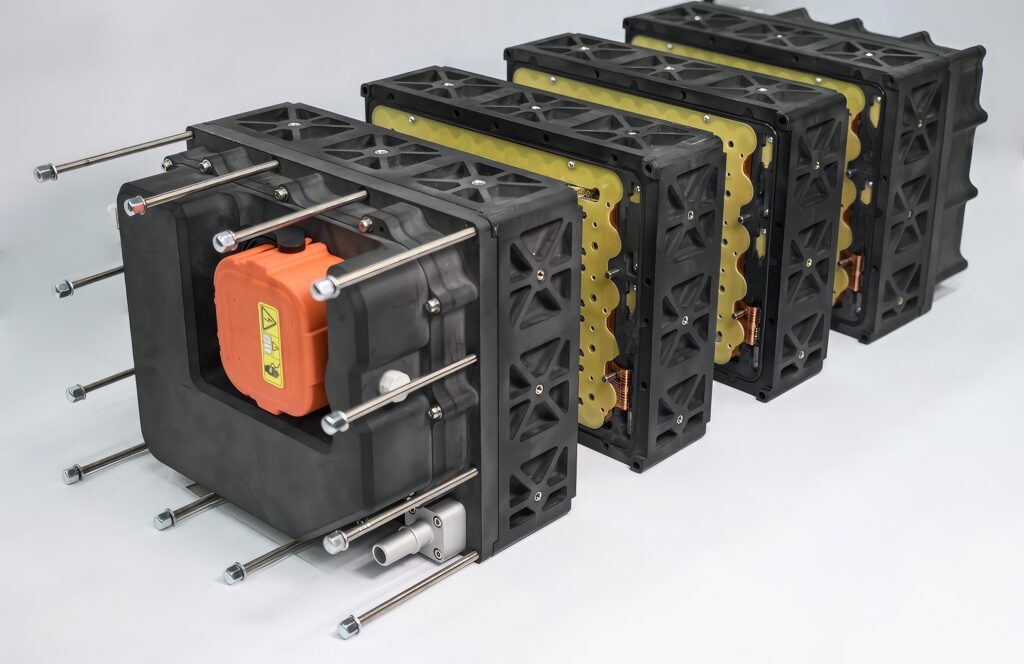
(Image courtesy of XING Mobility)
Cooling pumps
Using immersive cooling also fundamentally changes the design of the e-mobility platform.
With today’s IC engine systems there is usually a large pump that works with the cabin heating and air conditioning system (HVAC) and those hoses are relatively short. The move to EV designs means the need for cooling is more distributed throughout the vehicle, requiring longer hoses.
“We want to replace the radiator system with the condenser so the only additional component is the compressor”, said Friedman. “We are gaining other advantages in other areas as we don’t need a cold plate or thermal paste and we reduce the number of assembly steps at the OEM.”
“These electric vehicles have more and longer hoses and tubes with smaller diameters regardless of the powertrain,” said Kyle St John, who works on pipe and hose designs as applications engineer for fluid conveyance at Danfoss. “The cooling has to travel to different parts of the vehicle with the battery in the middle and a motor at each end compared to a traditional centralised internal combustion engine vehicle.
“Linking all the elements together raises the question of how you manage the rest of the systems, for example warming the battery and the cabin. With a two phase solution there will be little or no heat from the battery case to be used for the cabin. Now you don’t have a working fluid in the vehicle to use in other ways,” St John said.
“The biggest factors that come to mind are cleanliness and the fluid type,” St John added. “These immersive cooling systems tend to be cleaner than a lot of other systems. There’s a lot of advancement in the fluids and analysis of what fits best; whether that is a different hose material or tubes made out of steel or aluminium for the cleanliness.
“Customers determine the size of the hose or tube depending on the size of the system and that’s the key for more viscous fluids or longer runs in the hoses. As far as fluid compatibility goes right now there isn’t anything different but when you consider bend radius for smaller systems, that could change it.”
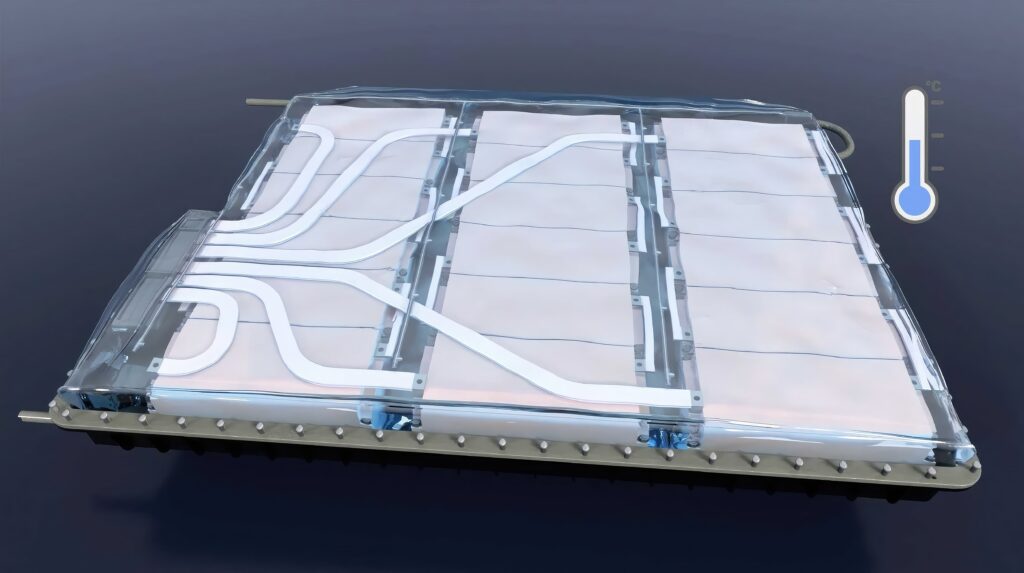
(Image courtesy of Valeo)
Choice of fluid
Carrar can use any low pressure refrigerant that is suitable for a high voltage system but needs a dielectric value at least 10 times higher than the battery pack voltage at 800V to 1000V. This means there are two candidate fluids commercially available. These are SF-33, a proprietary hydrofluoroolefin (HFO) from Opteon and the R1233zd from Honeywell.
“Because we use a low pressure range we can design the modules with lightweight polymer materials instead of aluminium, which is usually needed to transfer heat out of a pack,” said Friedman. “It also isolates from the outside temperature; this is why we can design very light systems and we can reduce the pack weight by 20 kg. That’s a lot for the OEMs.
“For the refrigerant a single phase needs a lot of liquid but dual phase needs less so we are not changing the amount of cooling liquid in the vehicle,” Friedman added. “We are looking at both the passenger market and commercial vehicles but we assume the penetration will be for high end passenger vehicles.
“On the commercial side, we designed a module for Volvo where we showed we prevent thermal runaway in a 14 kWh module with over 700 cells. That’s a big module measuring 60 x 60 cm and they have 36 of these modules in the battery pack with one condenser and one compressor per pack.
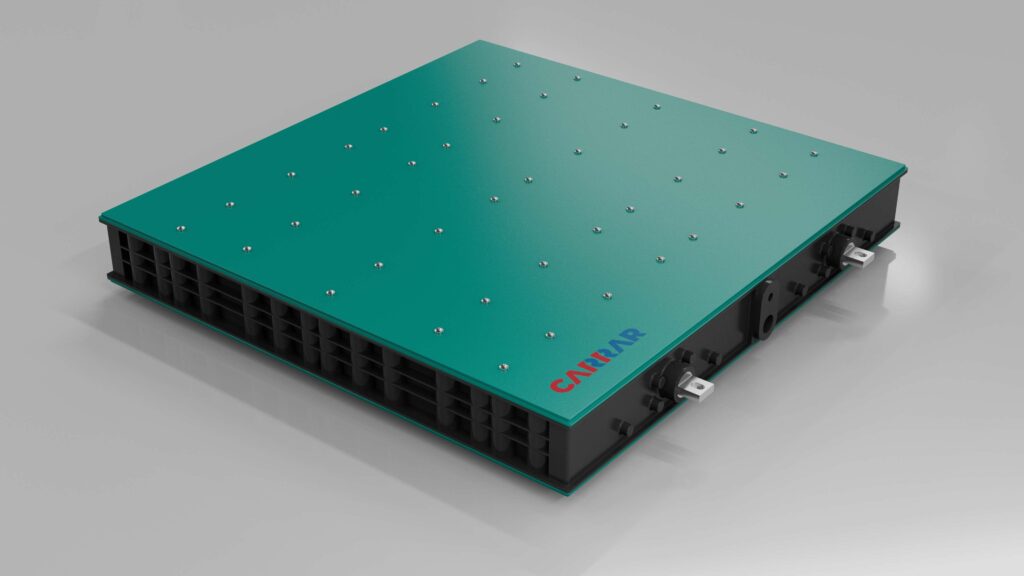
(Image courtesy of Carrar)
Test results
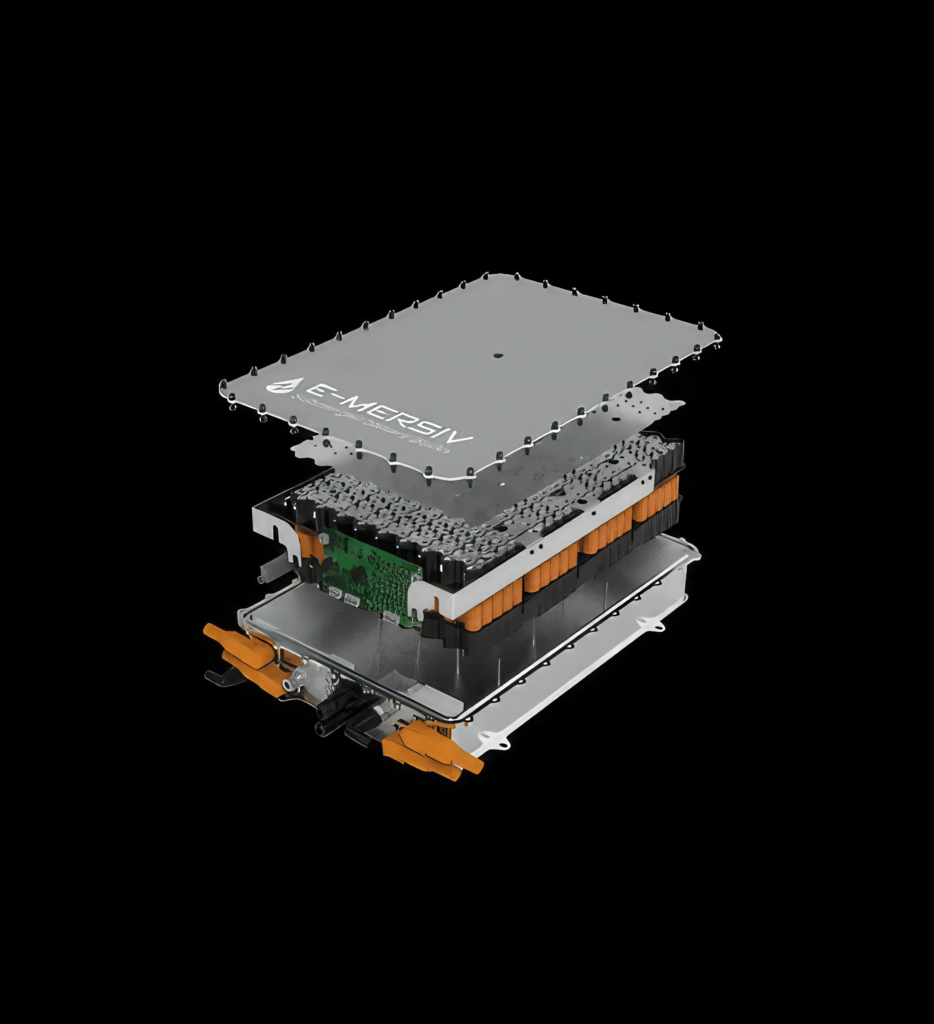
(Image courtesy of Mersiv)
Castrol worked with Virtual Vehicle Research [VVR] in Graz, Austria on the comparative performance of indirect and single phase immersion cooling technologies. This research compared battery cooling via indirect water-glycol baseplate cooling with immersion cooling. The majority of today’s battery packs are thermally managed using water-glycol-based coolants housed within channels in a baseplate that regulate the temperature of the cells.
The general belief in the industry is that immersion fluids are much more viscous than water-glycol. That was true for the first generation of Castrol’s ON EV thermal fluids. However this has evolved with the second-generation immersion fluids exhibiting similar viscosity to water-glycol fluids at 30 C at 2.9cSt compared with 2.7cSt for 50:50 water-glycol.
The SI unit for kinematic viscosity is one meter squared per second and is equivalent to 10,000 stoke (St). Usually, centistokes (cSt) is used, where 1 cSt = 1 mm2/s. This decrease in viscosity reduces the pump power required in an immersion-cooled battery system, increasing efficiency. Below 30 C, which is key for immersive cooling, the second-generation EV thermal fluid has even lower viscosity than water-glycol, for even higher pump efficiency.
The analysis in Graz focused on identifying the optimal cell cooling. That included whether it is better to have an increased cooling area but lower thermal properties of the fluid with immersion cooling, or a lower cooling area and higher fluid thermal properties with indirect cooling.
VVR also looked at the extra benefits that can be derived from cooling busbars and how the thermal environment affects the electrical performance and aging of the cells, and whether fluid flashpoint is related to safety performance.
To support this research, immersion and indirect mini-modules were designed and constructed with seven nickel-cobalt-aluminium (NCA) 21700 cylindrical cells. The immersion-cooled mini-module used direct busbar cooling and was designed and optimised with computational fluid dynamics (CFD) for heat transfer and minimised pressure drop.
The mini-modules were then put through performance and durability testing to analyse thermal and electrical behaviour, as well as being subjected to thermal propagation testing. Performance and durability test conditions were created to replicate realistic fast-charging scenarios, representing a 10-90% charge at a 3C charging rate, equivalent to just under 20 minutes of charge time.
The analysis found that immersion cooling improved the thermal gradient and peak temperature of cells under fast charging, minimising the surface cell thermal gradient to under 1.5 C.
Evaluation of durability identified that immersion cooling can extract more performance from cells. While the immersion-cooled module received 25% higher capacity through constant current charging than the indirectly cooled module, it had a 16% lower degradation rate despite the higher electrical stress. Significantly, Castrol and VVR expect this difference to increase alongside an increase in charge rate.
To gauge the safety of immersion and indirectly cooled systems, Castrol and VVR designed a series of thermal runaway tests. These tests were performed in a sealed chamber with limited oxygen to enable the observation of any failure, as well as to ensure that the module was not fully destroyed.
A nail penetration method was used to initiate the thermal runaway of the central cell. Thermal runaway can lead to thermal propagation, where heat from a damaged cell is transferred via convection and conduction to adjacent cells, a process that can potentially lead to catastrophic failure of the entire battery pack.
The immersion-cooled module proved effective in mitigating thermal propagation even though it was not optimised for safety. Heat dissipation and not the flashpoint of the fluid determines safety in immersion-cooled systems. The effective heat dissipation comes from a combination of vent-gas management and the fluid conducting heat away from the damaged cell.
The higher performance enabled by the immersion cooling does not come at the cost of capacity. The research suggests that in extrapolating the data to higher energy density cells and higher charging rates, the differences would become even more pronounced between immersion and indirect systems.
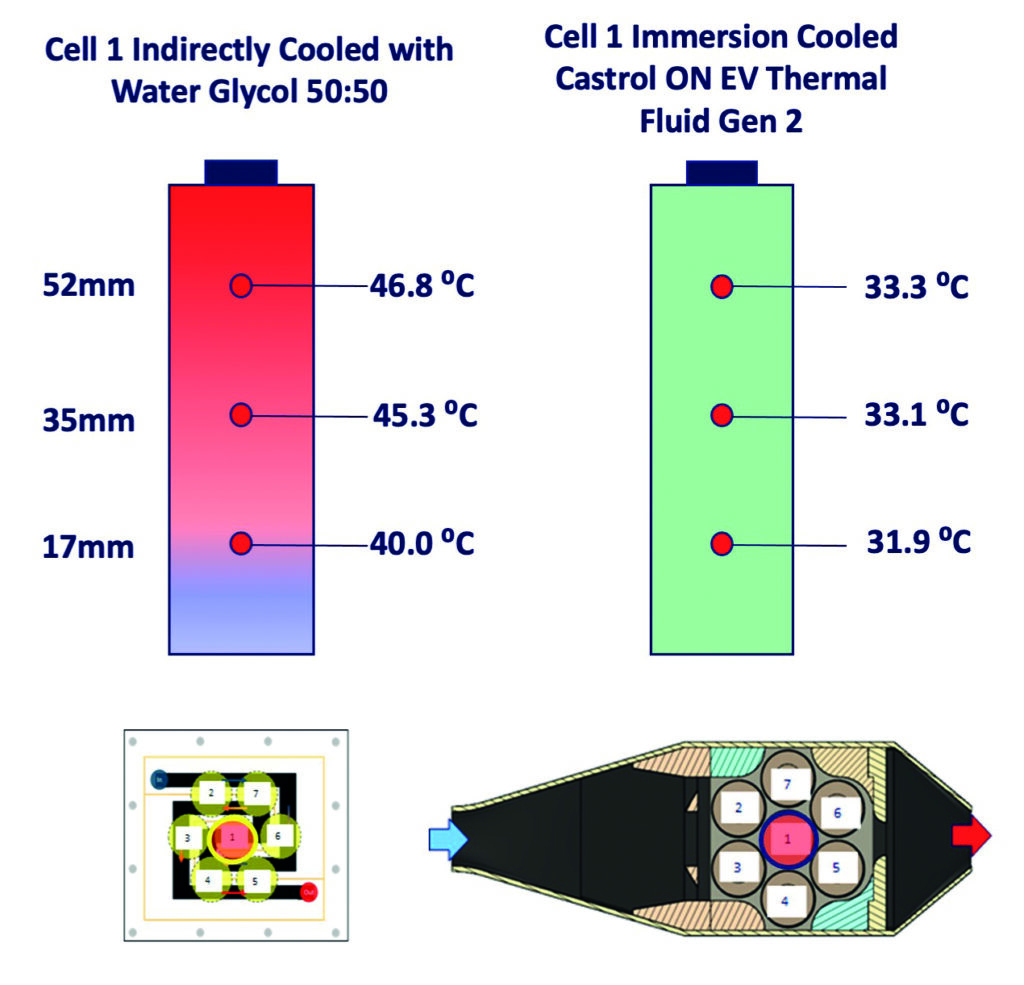
(Image courtesy of Castrol)
Dual phase immersive cooling tests
Tests at the Technical University of Munich with cylindrical NMC lithium ion battery cells with 2C charging and discharging rates (2C/2C) showed that the dual phase immersive cooling system developed by Carrar allowed the pack to operate for 2400 cycles until it reached the 80% of capacity that is usually regarded as the end of life for such a pack. This compares to 600 cycles for the NMC cells using liquid cooling.
The cells also stayed above 90% for 2200 cycles. That compares to dropping below at 400 cycles with a liquid cooled system, which is important for the second hand market notes Friedman. He is less concerned about outgassing from the cells.
“If we have outgassing from the cell it’s an extreme event and you need to take the car to the garage. We have shown in tests we can prevent thermal runaway as we can dissipate more heat than the cell is generating. And if there is runaway we don’t get thermal propagation. That data comes from the voltage data from the BMS.”
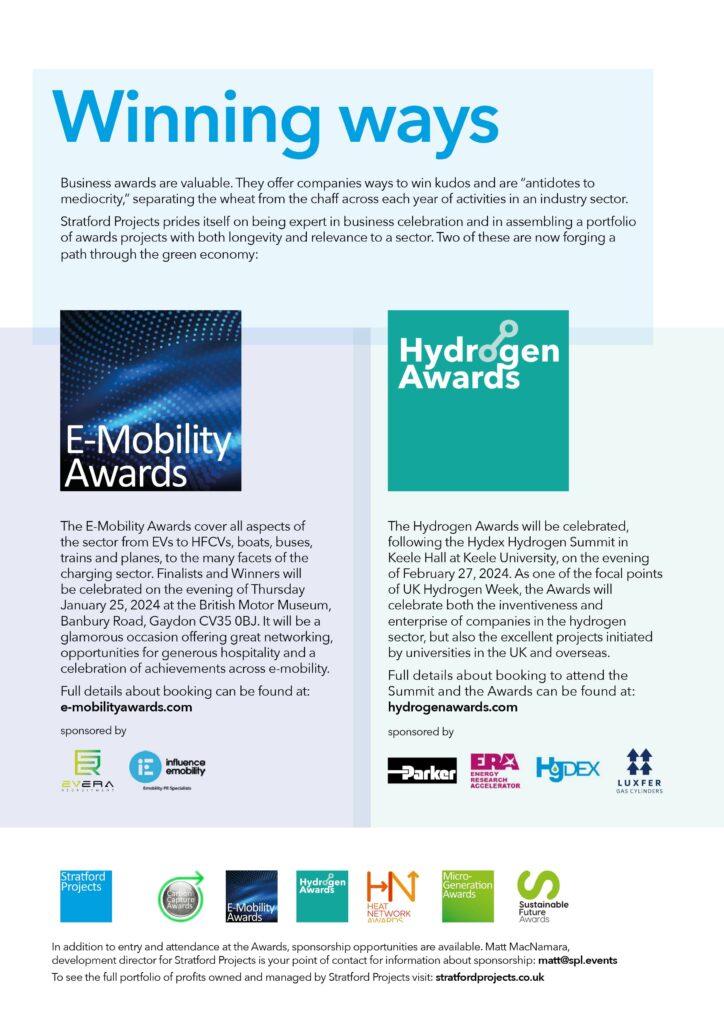
Hydrogen
The use of hydrogen for power systems also opens up opportunities for more integrated cooling systems. The cryogenically cooled hydrogen can be used as a coolant for the power electronics, the battery pack and the motor before being used in a fuel cell to generate power.
Ricardo also has a research project on cryogenic cooling. “We see the opportunity of using this as a way to achieve high efficiency in component performance,” said Ennever.
Hydrogen fuel cells are more particular about leakage in the hose portion, so hard tubing tends to be used, says St John at Danfoss. “Again, for hydrogen it is cleanliness that is the issue and that means we will use stainless steel.”
Conclusion
Single and dual phase immersive cooling can provide advantages for e-mobility powertrain designs in many ways. With a similar level of complexity as today’s liquid cooled systems, immersive cooling can keep battery cells within one or two degrees of the optimum operating temperature of 25 C. This enables faster charging – at 3C and above – removing the heat generated and ensuring the charging does not damage the cells. This also supports higher discharge rates to provide more power for construction and mining equipment.
The stable temperature of immersive cooling supports safer operation, eliminating the issue of thermal runaway. It also leads to a significantly longer lifetime for the cells, boosting the secondhand value of vehicles, while reducing the number and weight of the components for the cooling system.
Click here to read the latest issue of E-Mobility Engineering.
ONLINE PARTNERS
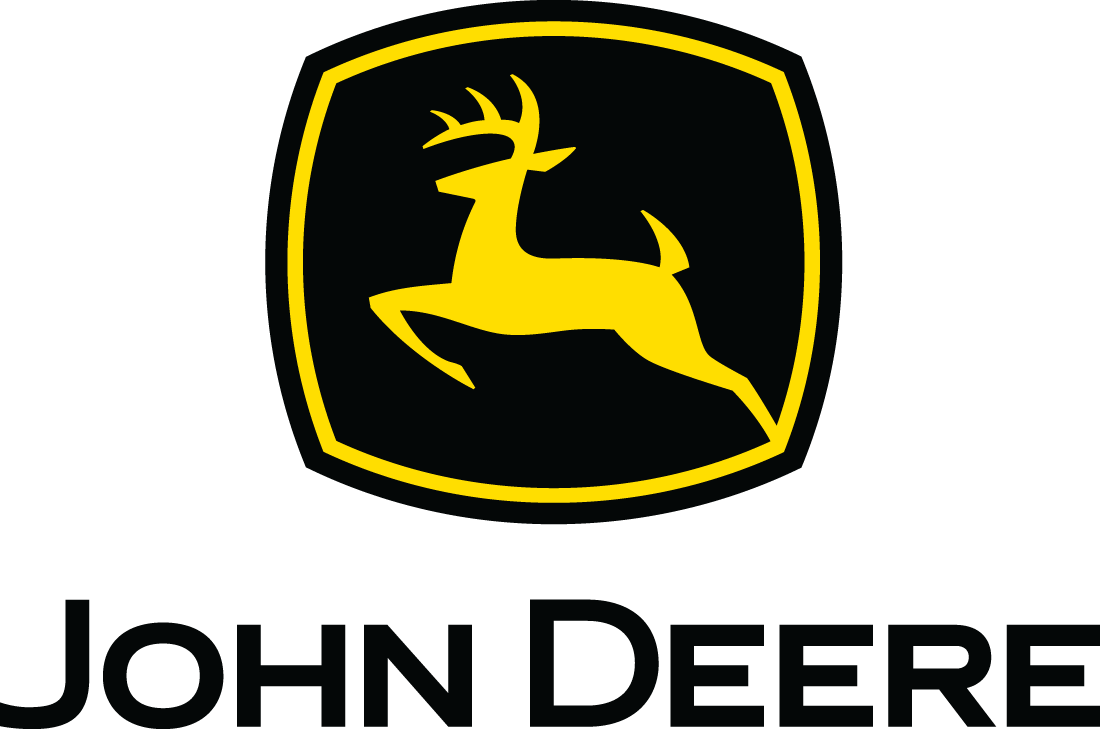
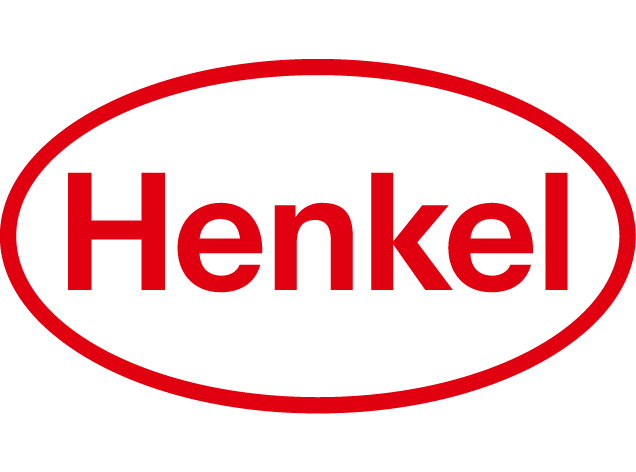
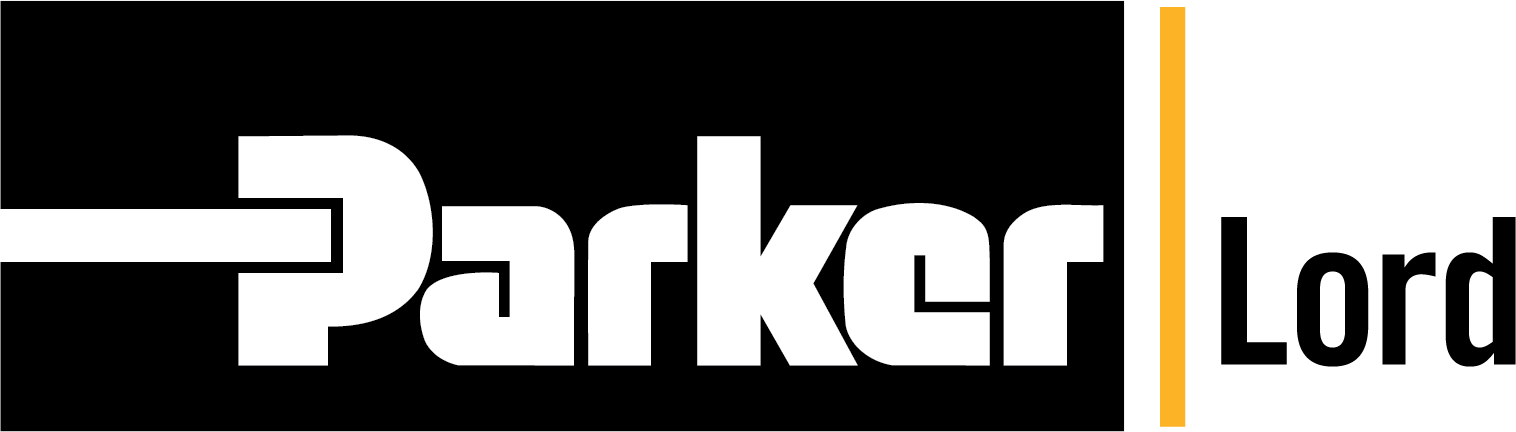
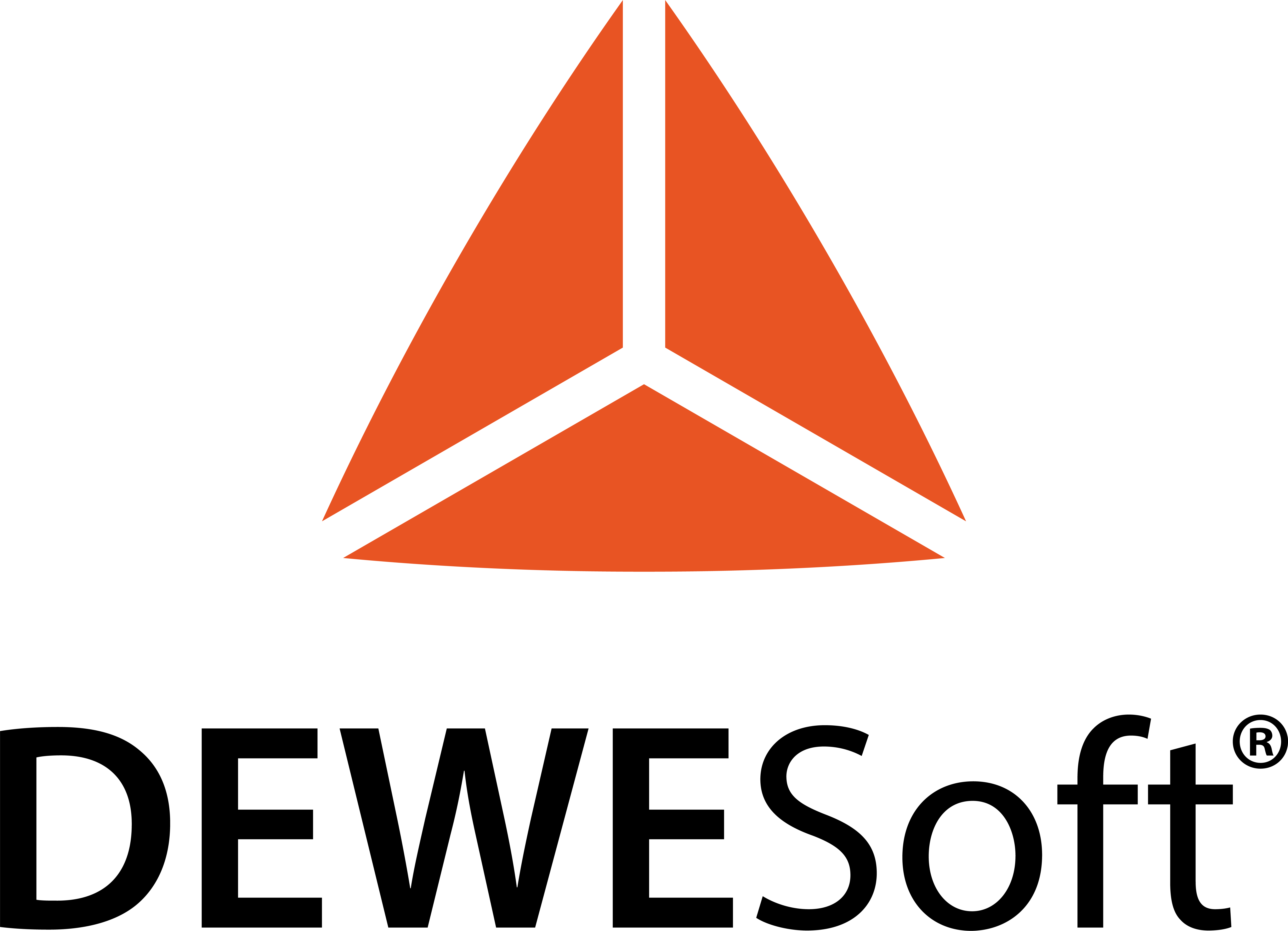
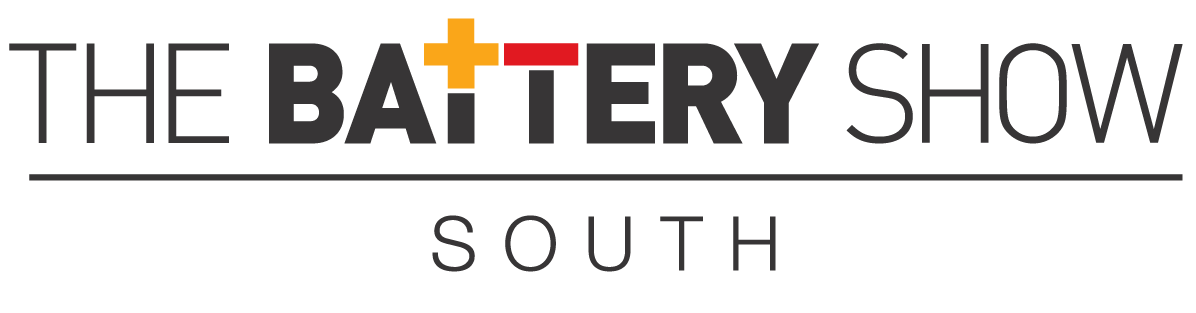
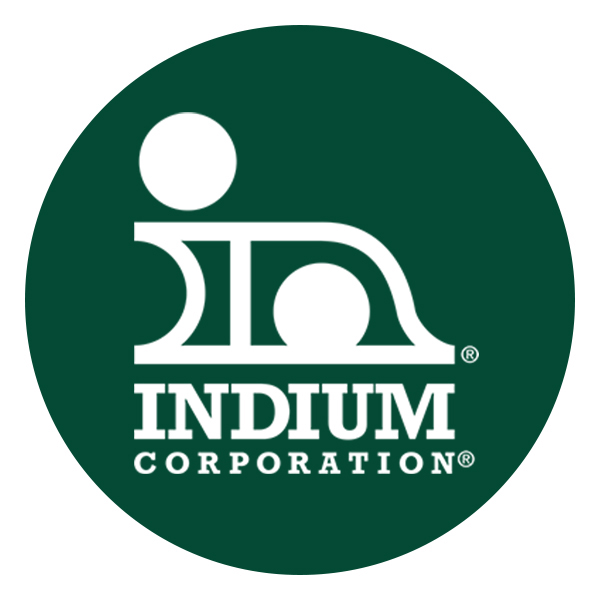
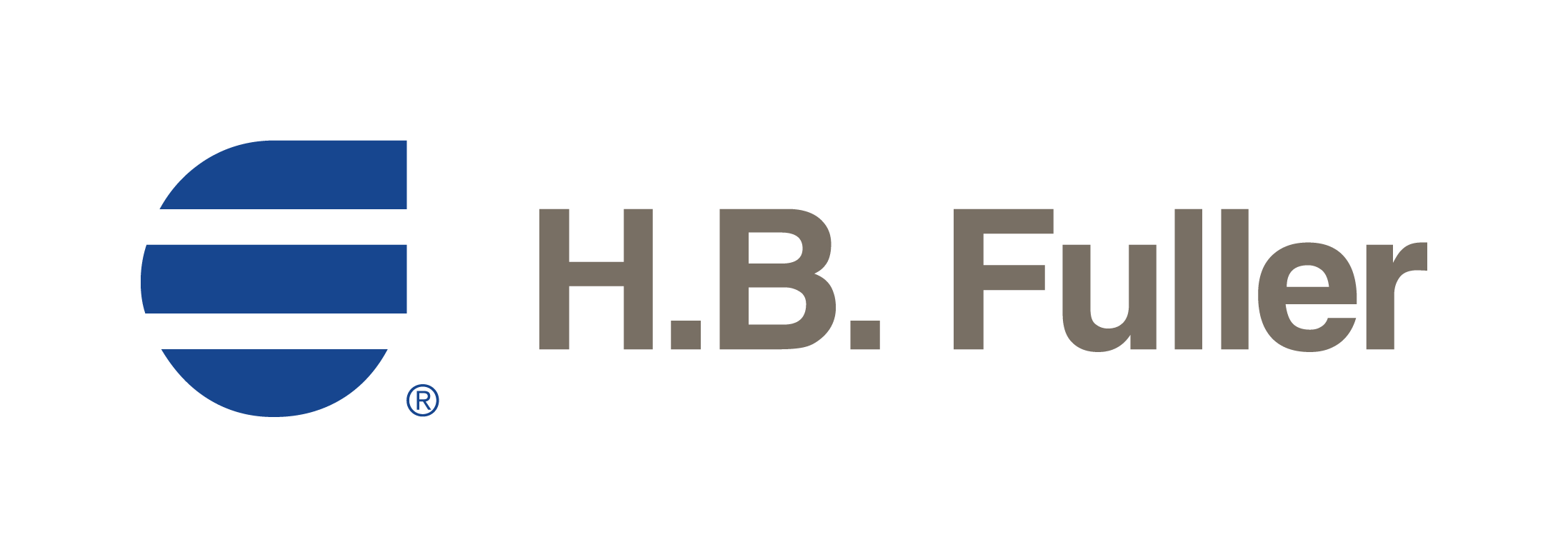