Hyundai Mobis develops pulsating heat pipes for ultrafast charging
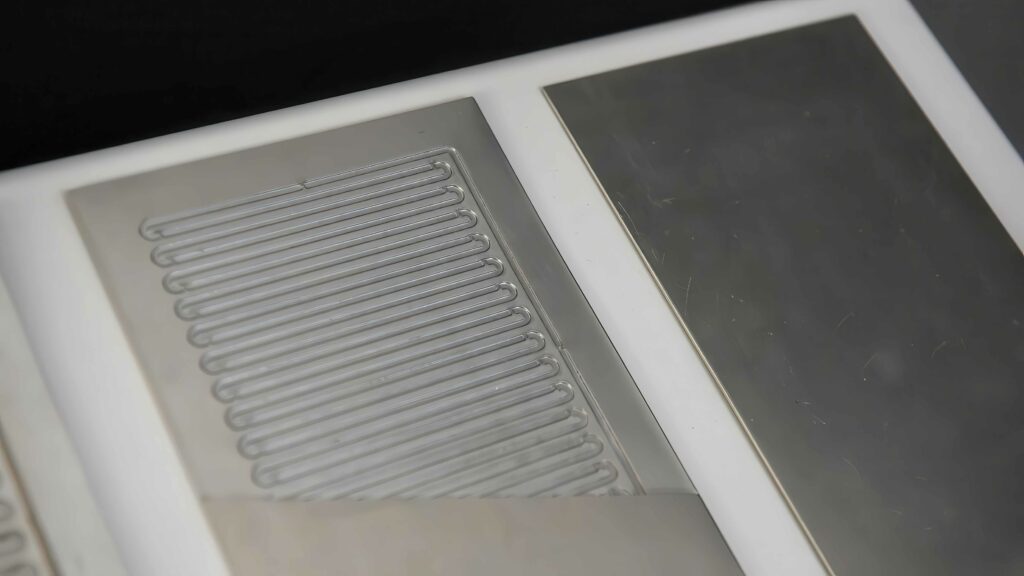
(Image courtesy of Hyundai Mobis)
Hyundai Mobis has developed a ‘pulsating’ heat-pipe (PHP) material to improve the thermal performance of battery packs during fast charging. It aims to prevent overheating during the ultra-fast charging of EVs, writes Nick Flaherty.
Heat pipes are metal tubes that act as thermal conductors to boost the efficiency of heat transfer.
PHPs diffuse heat through the vibration and circulation of refrigerant internally. The volatile liquid in the capillary tube turns to vapour and moves through the pipe, cooling and creating a series of bubbles that transfer the heat.
This can result in over 10 times the heat-transfer performance than standard aluminium, rapidly moving the heat from overheated battery cells to the exterior.
The European Space Agency (ESA) is developing and testing a direct chip-to-baseplate thermal concept based on PHPs that reduces design complexity, yet widens the operating temperature range and boosts thermal transport performance.
This aims to transfer at least 60 W for cooling controller chips with a thin, meandering, two-phase capillary tube of less than 5 mm thick, which can be densely packed to provide high thermal performance with high heat-flux density.
Using PHPs for direct cooling reduces the size of radiators and lets the batteries operate at a higher temperature.
Hyundai Mobis has adapted the technology for EVs using an aluminium alloy and a refrigerant, and it is placed between battery cells to lower the internal battery temperature that spikes during rapid charging.
Even when battery heat generation increases during ultra-fast charging, it is expected to significantly reduce EV charging time by implementing a stable thermal-management system capable of withstanding the heat.
Hyundai Mobis placed the heat pipes between each battery cell in a pack. They quickly transferred the heat generated in each cell to cooling blocks, controlling the internal temperature at module level.
In a comparison test of the heat dissipation performance between the PHP and a standard aluminium cooling plate, the heat pipe showed a temperature difference of nearly 20o.
Manufacturing the PHPs can be a challenge, so the company developed a press process for large-scale continuous production. These pipes have a thickness of only 0.8 mm, significantly thinner than standard heat pipes, which are about 6 mm.
Click here to read the latest issue of E-Mobility Engineering.
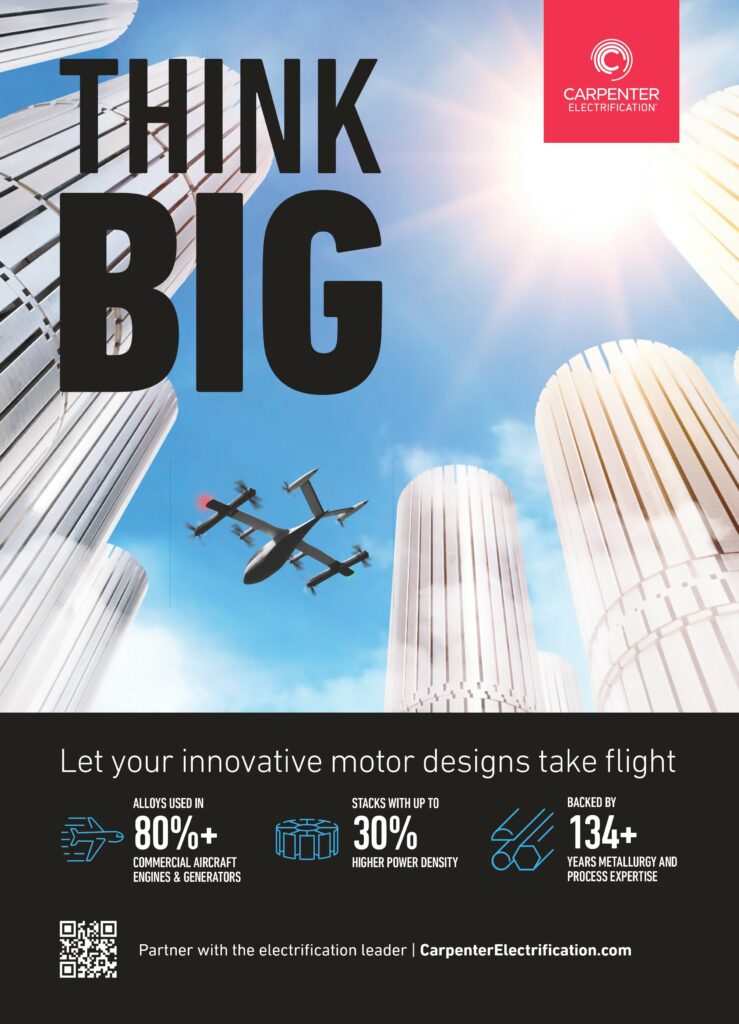
ONLINE PARTNERS
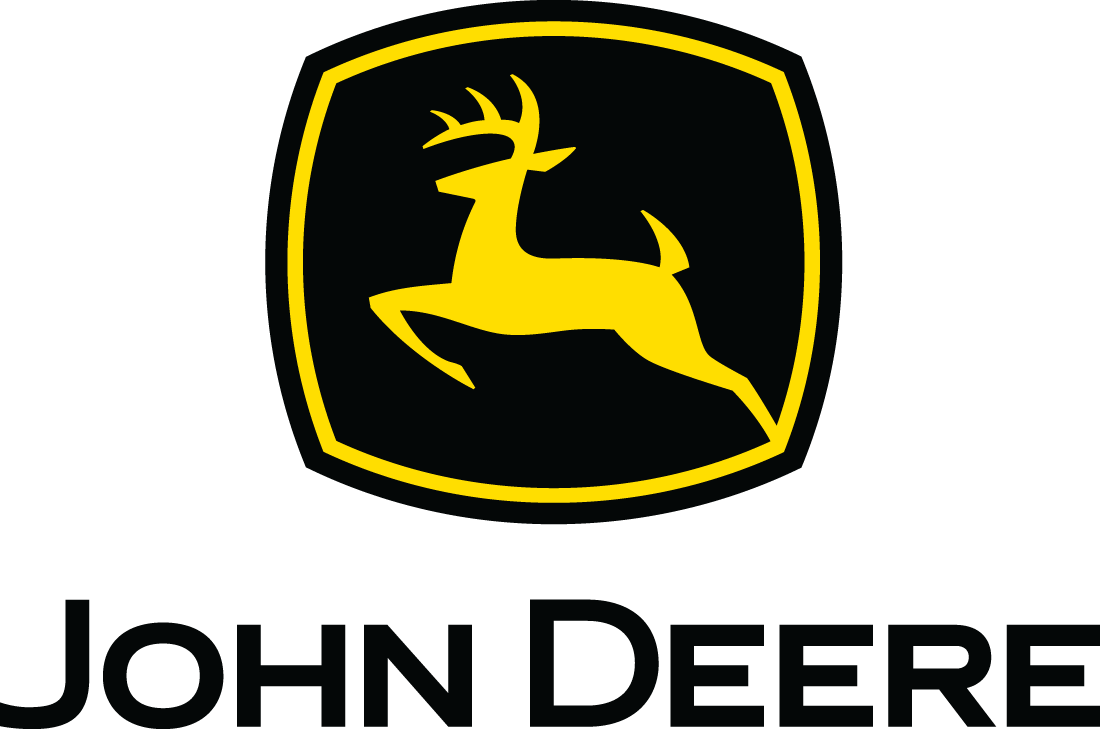
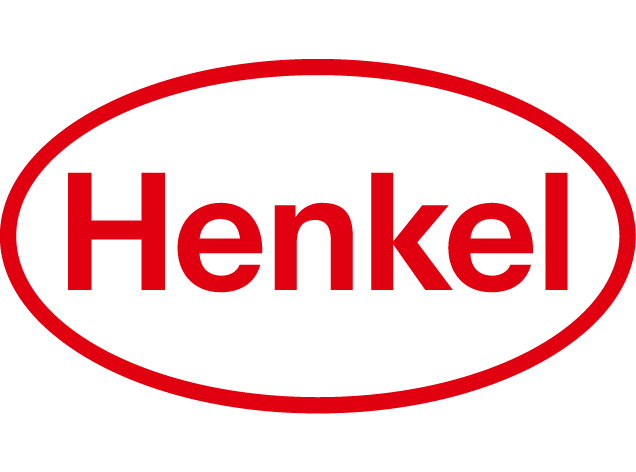
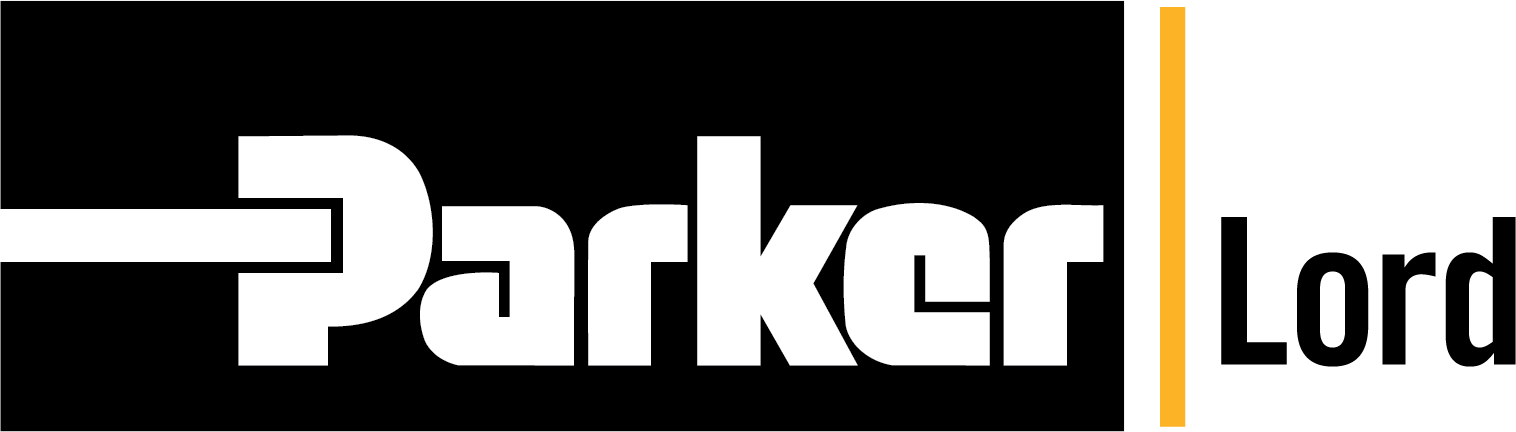
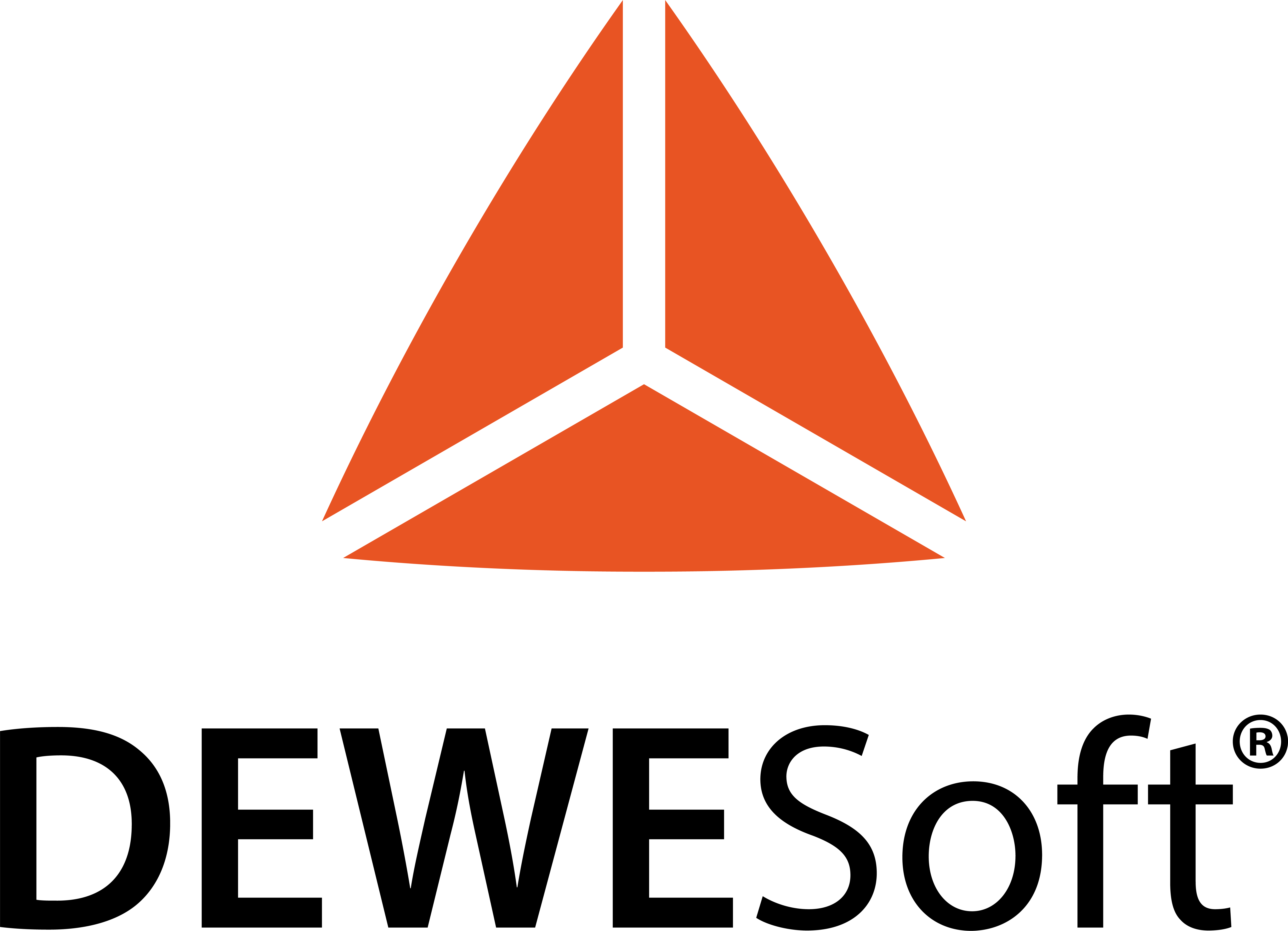
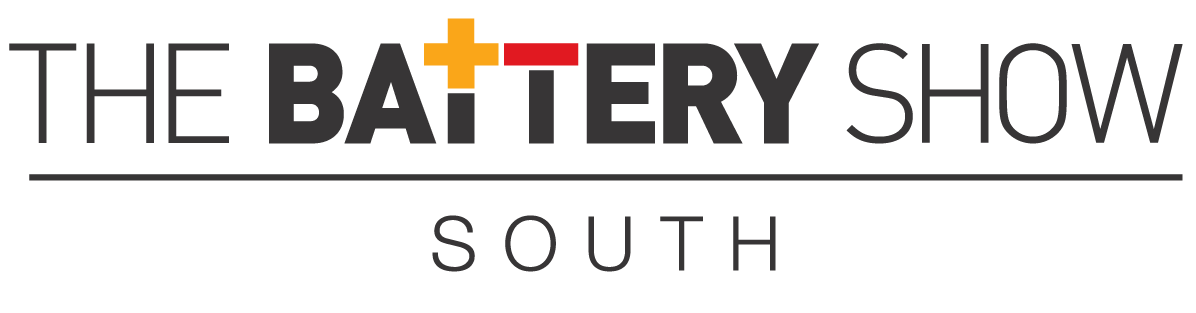
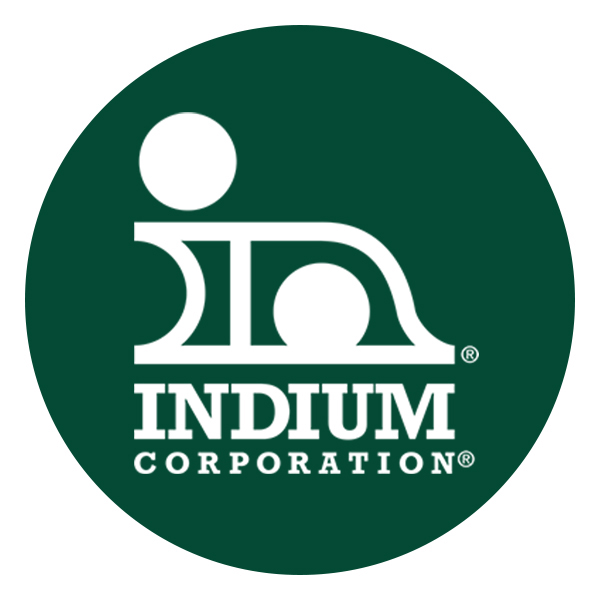
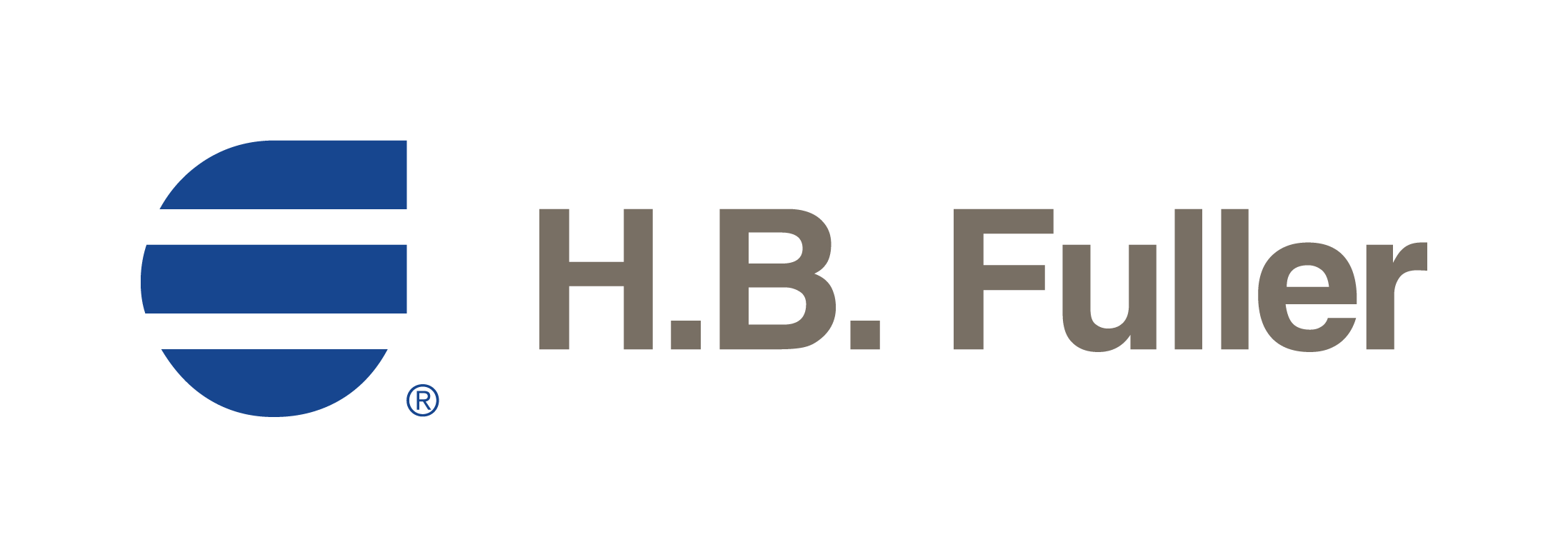
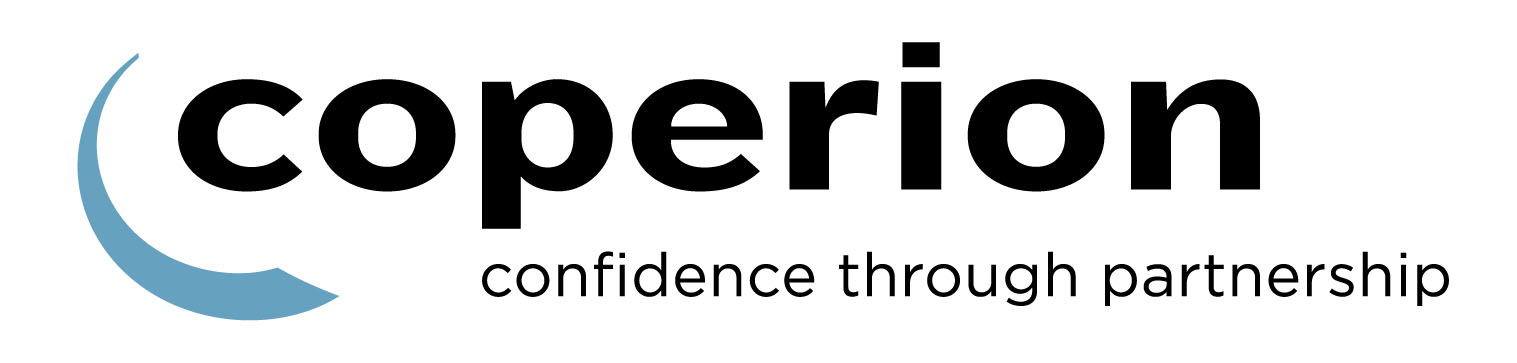