Heraeus reduces gap in stacked rare-earth magnets in ‘game-changer’ for motor design
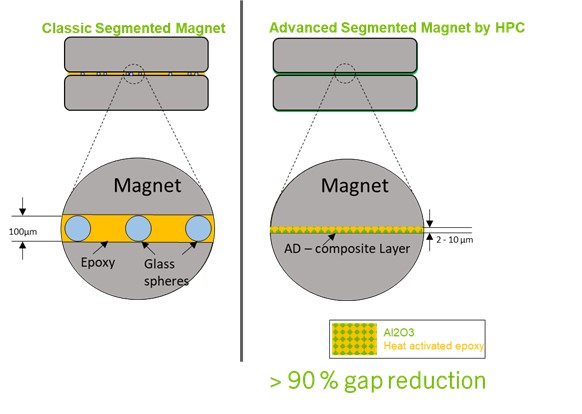
Heraeus High Performance Coatings has launched an innovative process for laminated rare-earth metal magnets that boosts performance and manufacturing efficiency, which is crucial for high-power electric motors.
Upon thermal activation, the Aerosol Deposition (AD) method ensures robust adhesion while maintaining exceptionally narrow gaps, surpassing the capabilities of conventional manufacturing methods such as Glass Sphere Spacer, Thick Epoxy Coating and Spray Paint Coating.
The gap between magnets >50µm is minimized to a precise range of 2-8µm. This smaller gap results in more magnetic material per volume, enhancing the intrinsic efficiency of the magnets.
The ultra-thin composite layer is approximately 3µm, combining insulation and gluing in one step. Costs are potentially lowered by reducing material usage and shortening production time.
Various magnet shapes and sizes are accommodated, increasing design flexibility and application in different motor types and sizes. The technique can be easily scaled to meet production volumes.
The ceramic part of the coating is highly stable at elevated temperatures, broadening the application range of the magnets. There is also enhanced electrical insulation between the laminated layers, suppressing eddy current losses and boosting effective magnetic flux density. The process is also eco-friendly due to the absence of wet chemical processes and VOC emissions.
“This innovative coating technique by Heraeus opens up new horizons in e-mobility, significantly enhancing the efficiency and performance of electric motors. The reduced gap in stacked rare-earth magnets is a game-changer in motor design, aligning perfectly with our industry’s goal for higher motor efficiency and sustainability,” says Ilka Luck, head of Heraeus High Performance Coatings.
Click here to read the latest issue of E-Mobility Engineering.
ONLINE PARTNERS
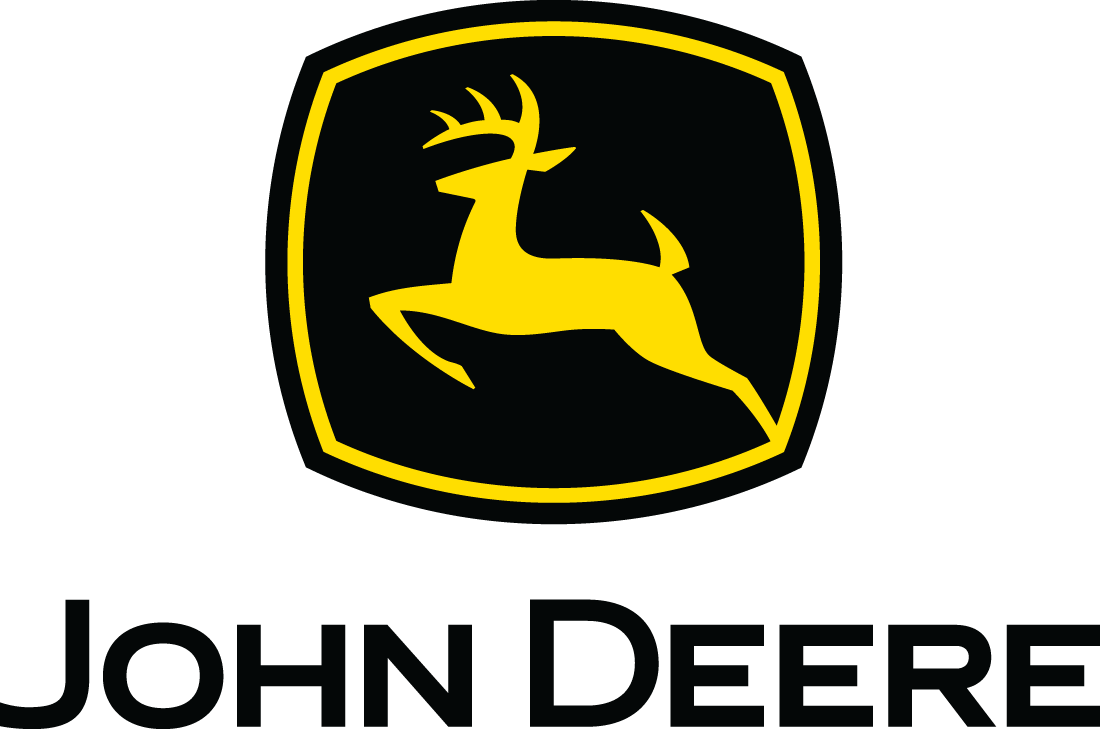
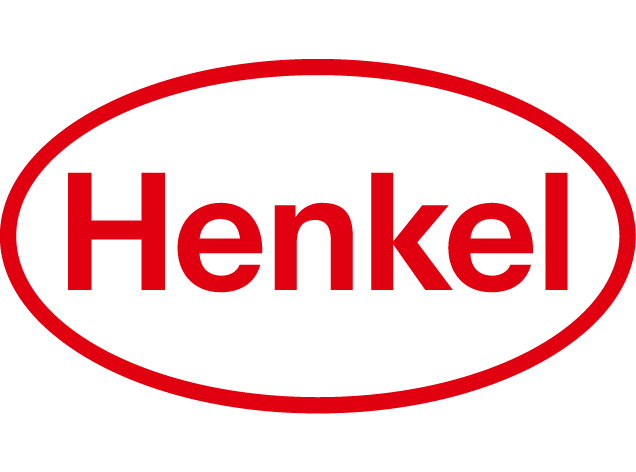
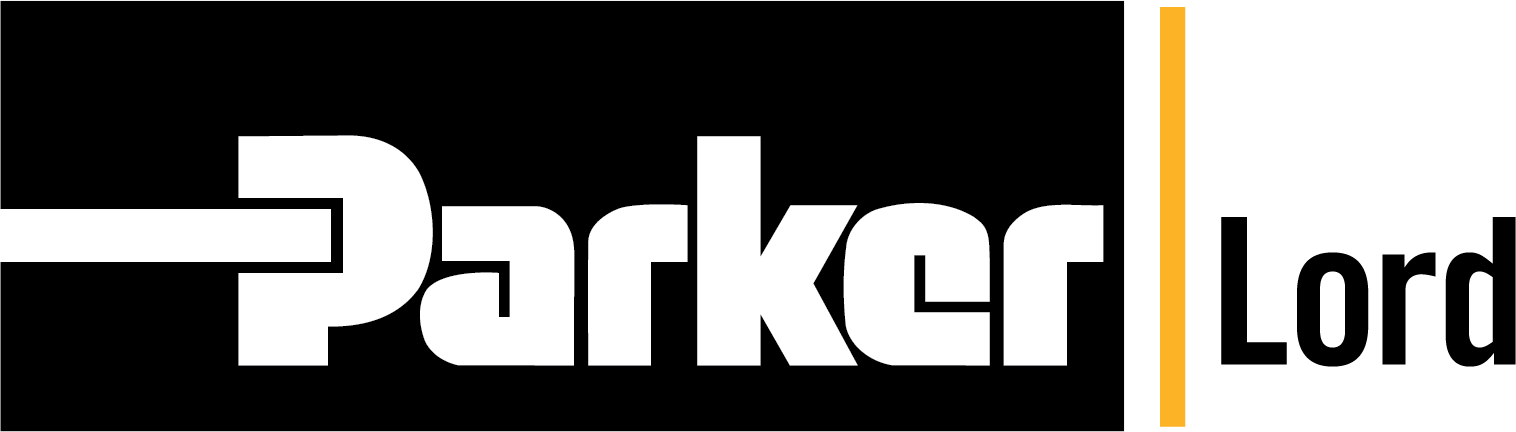
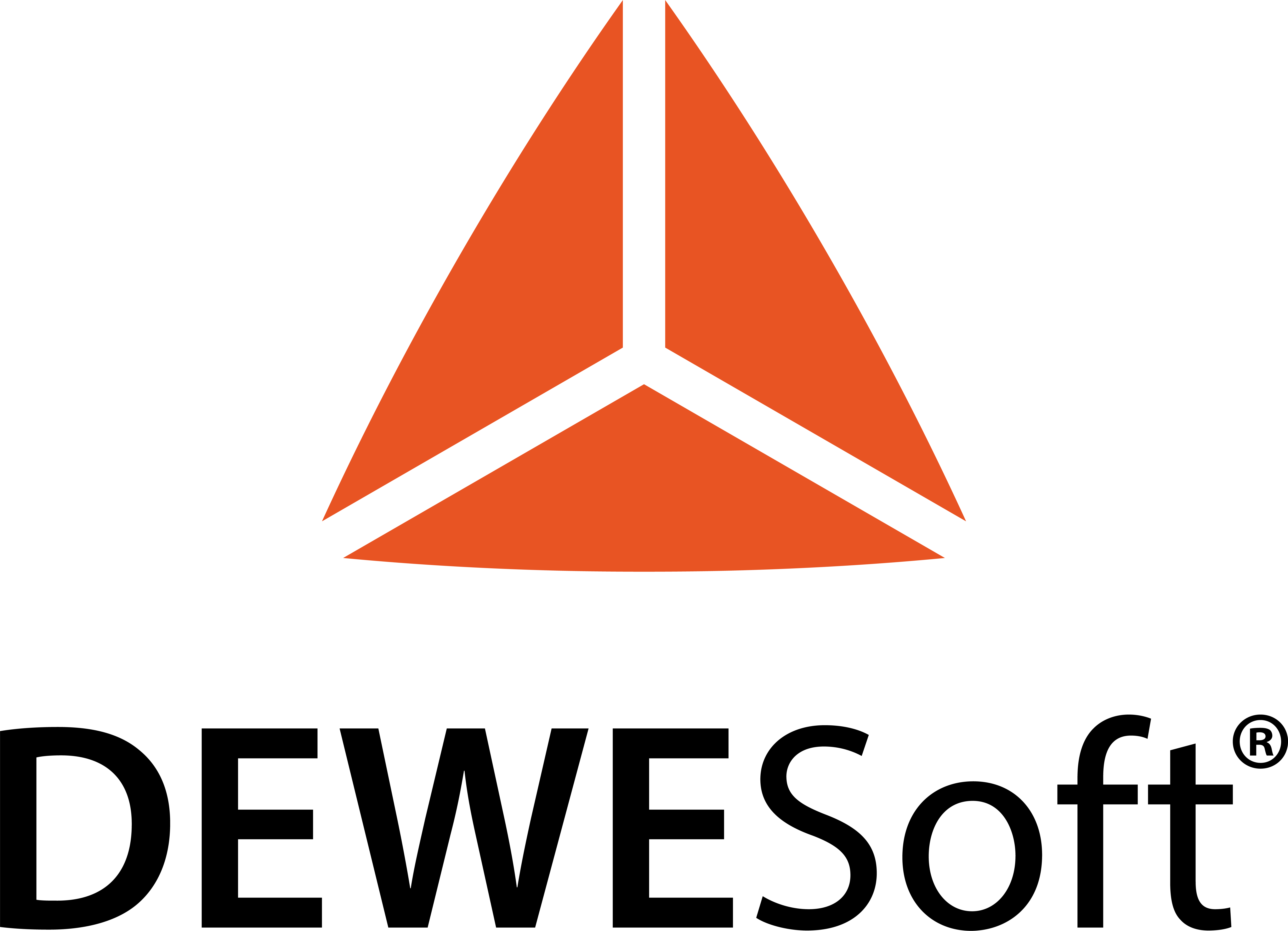
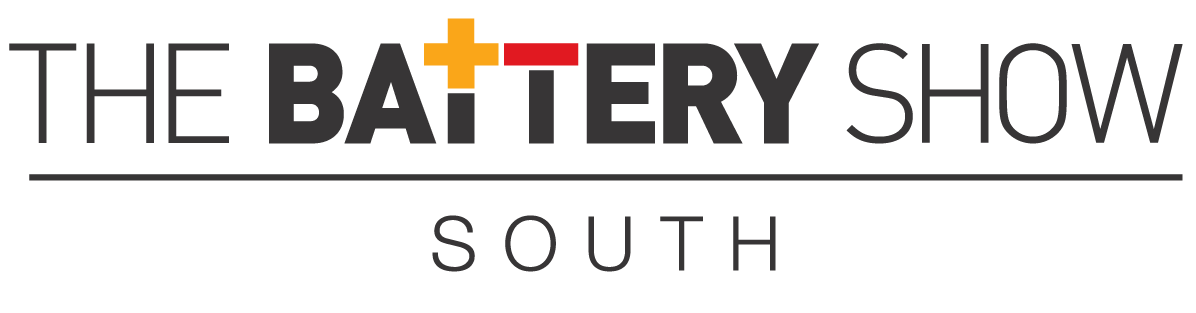
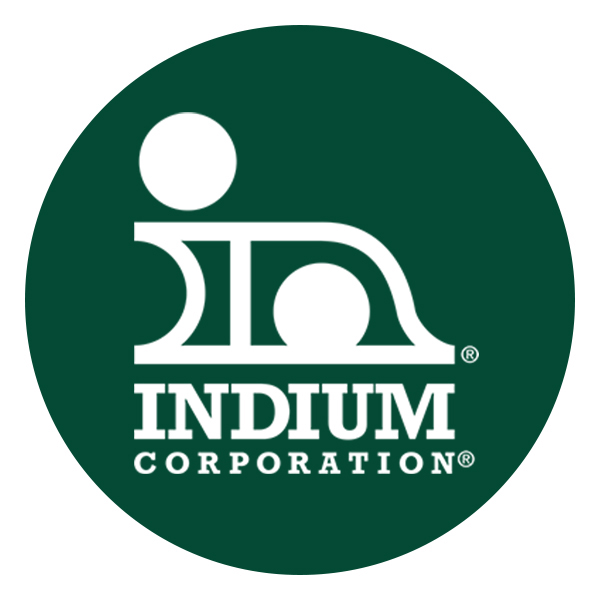
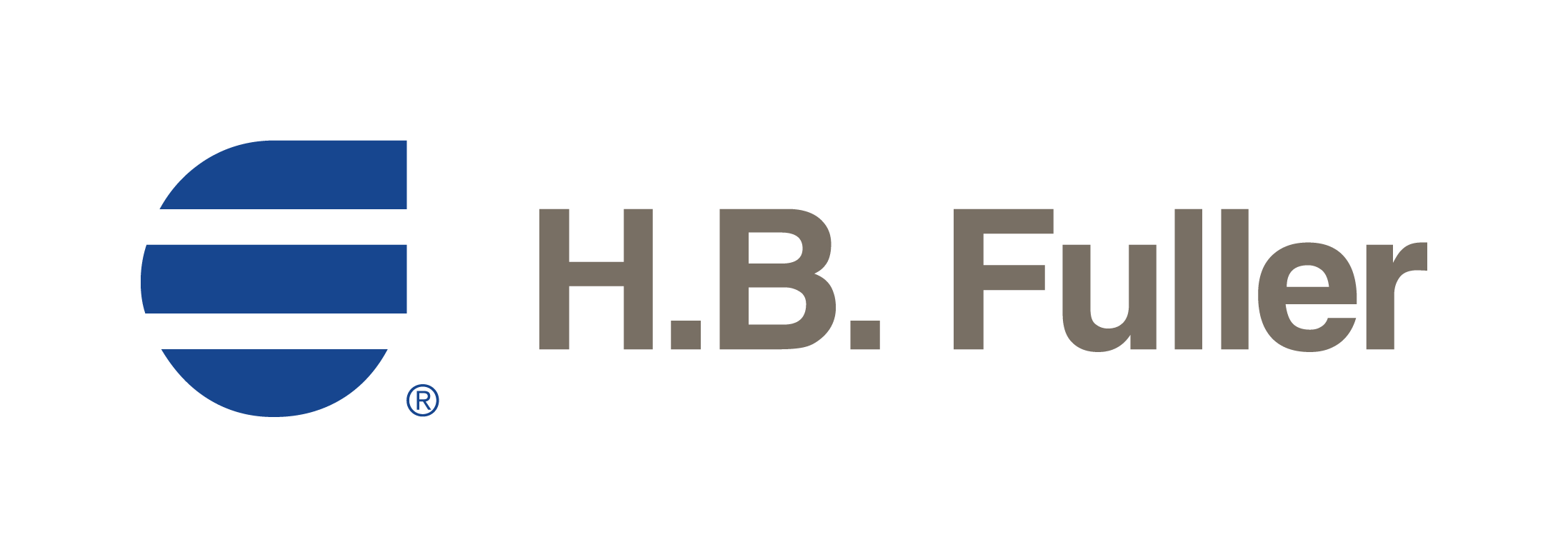