Henkel explains its battery fire-resistant coatings process
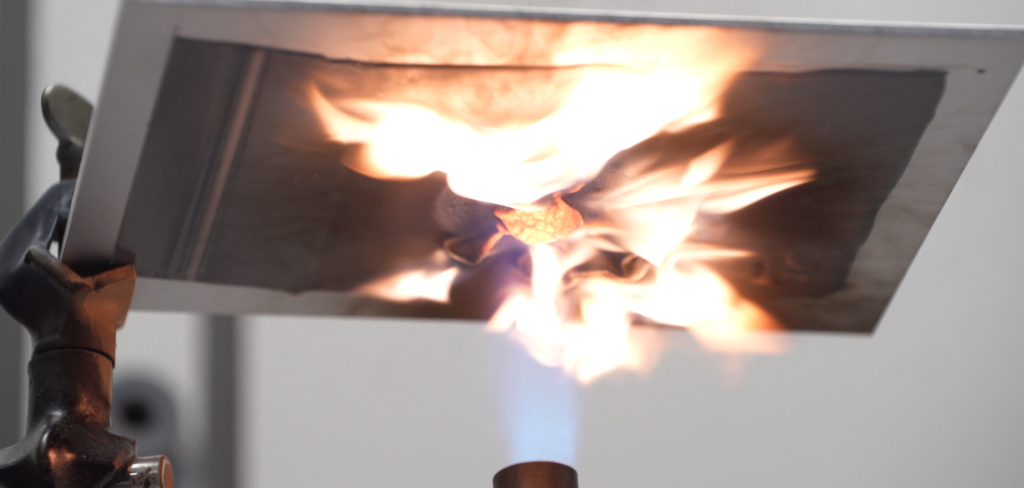
(Images courtesy of Henkel)
Whether EVs are more likely to catch fire than IC-engined vehicles is uncertain, as small sample sizes make reliable statistical comparisons difficult (writes Peter Donaldson). Nonetheless, lithium-ion battery fires are difficult to extinguish because they release oxygen and hydrocarbons from the thermal breakdown of compounds in their cathodes and liquid electrolytes.
A major focus for the EV’s industry’s safety efforts is therefore on giving vehicle occupants more time to get out before the fire penetrates the cabin. That is what drove Henkel to launch two fire-resistant coatings, Loctite EA 9400 and Loctite FPC 5060, for the inside of battery pack lids, in 2021.
EA 9400 is a two-component epoxy-based intumescent material for use as a heat shield, electrical insulation and mechanical protection. FPC 5060 is based on an aqueous dispersion with inorganic fillers made from low-toxicity materials and free from halogens, heavy metals and asbestos. EA 9400 cures and FPC 5060 dries at room temperature.
Dr Kim Kreiskoether, Henkel battery and cell system specialist, says, “Many companies in the battery value chain are showing strong interest in the coatings.”
She adds that Henkel’s customers now include many of the world’s vehicle OEMs and battery manufacturers, which it supports by talking to their battery development teams, preparing samples and supporting or carrying out tests to meet design-specific requirements, such as the flame test.
The company has also worked with partners to develop spray-coating and flat-streaming equipment for applying the materials. “The equipment is designed for fast process times, with no masking or low overspray, and no or minimal aerosol development,” Dr Kreiskoether says.
She explains that Henkel checks that the materials meet adhesion and processability requirements using characterisation methods such as the bending test, before putting them through a standard series of fire protection tests.
“For an application-oriented test methodology, it is always important to keep the requirements of the battery system in mind,” she says. “We therefore start with the open flame test, where the sample is placed over a Bunsen burner at a defined distance for 10 minutes; the temperatures acting on the sample are 1100 ºC. The temperature on the other side of the sample is measured using temperature sensors.”
If the tests are passed, Henkel then works with partners to expose the material to a simulated thermal runaway using a pyrotechnic device or a particle gun, or a real thermal runaway triggered in a cell in front of the sample.
“Using the pyrotechnic device, the test duration is 20 seconds at a temperature of about 1400 ºC, which corresponds to the thermal runaway of a cylindrical cell,” Dr Kreiskoether says. “With the particle gun, temperatures of up to 1500 ºC can be reached using alumina particles with various diameters.
“The temperature and duration of the test with real cells depends on the cell used. One of our testing partners offers prismatic cells with 50 Ah, for instance.”
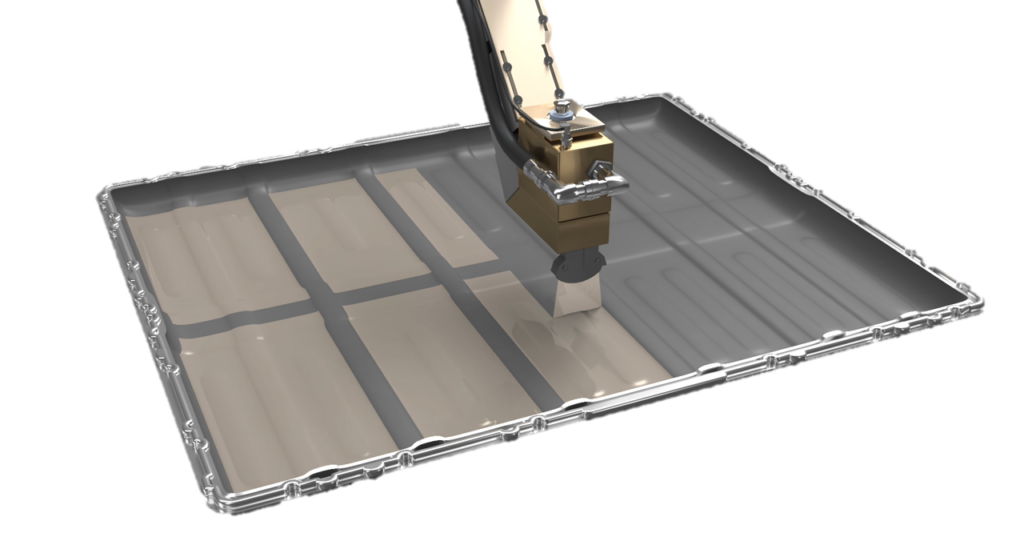
After these tests come pack-level tests of each material. Usual industry practice is to conduct the tests in cooperation with the battery manufacturer, but Henkel will soon be able to do this itself to support material development and more precise characterisation of a material’s performance.
This capability is embodied in a test stand now under development. It represents a customer-independent battery design at system level, Dr Kreiskoether explains, and will accommodate both cylindrical and prismatic cells. The company plans to make the system available later this year.
“In the battery test stand, we can apply materials such as the fire protection coating but also fire protection pads, thermal gap-filler and thermally conductive adhesives, and investigate their influence on the thermal event,” she says.
In formulating the materials themselves, Henkel has to balance requirements such as heat shielding and electrical insulation properties, mechanical stability, the thinnest possible coating to save installation space, cost-effectiveness, environmental friendliness and processability.
For example, using FPC 5060 requires a higher coating thicknesses compared to EA 9400, she says.
“We are also more limited in terms of the application process due to the fibres in FPC 5060, which is why we currently recommend spray-coating,” Dr Kreiskoether says. “The drying times of a water-based system are also higher compared to a cross-linking system. However, we have a higher environmental compatibility due to the use of water as a solvent, and as there is no chemical reaction it maintains a consistently thick coating even during a thermal event.”
She notes that the epoxy-based material’s intumescent reaction allows it to be applied in a thinner coating. As it is exposed to a high-temperature flame, the coating begins to foam, increasing the distance between the flame and the substrate, and forming a heat shield.
“Since this material does not contain long fibres, it can be sprayed on as well as flat-streamed. For almost 2D components such as battery lids, the flat-streaming process means no masking is necessary and no aerosol formation takes place.”
The development of polymer battery cases for EVs brings its own complications that stem from the fact that they can be made from different polymers, such as PA6, SMC and PP, and can have different fillers. Henkel is evaluating and developing its fire protection coatings for those though, she explains.
The evolution of battery pack architectures is also set to increase demands on coatings by making them multi-functional. “For example, a fire protection and electrical insulation coating thinner than 1 mm that is suitable for cell-to-pack designs with large cell formats will be required,” Dr Kreiskoether says. “At the same time, cell-to-chassis designs might need added functions such as panel reinforcement or noise, vibration and harshness management.”
ONLINE PARTNERS
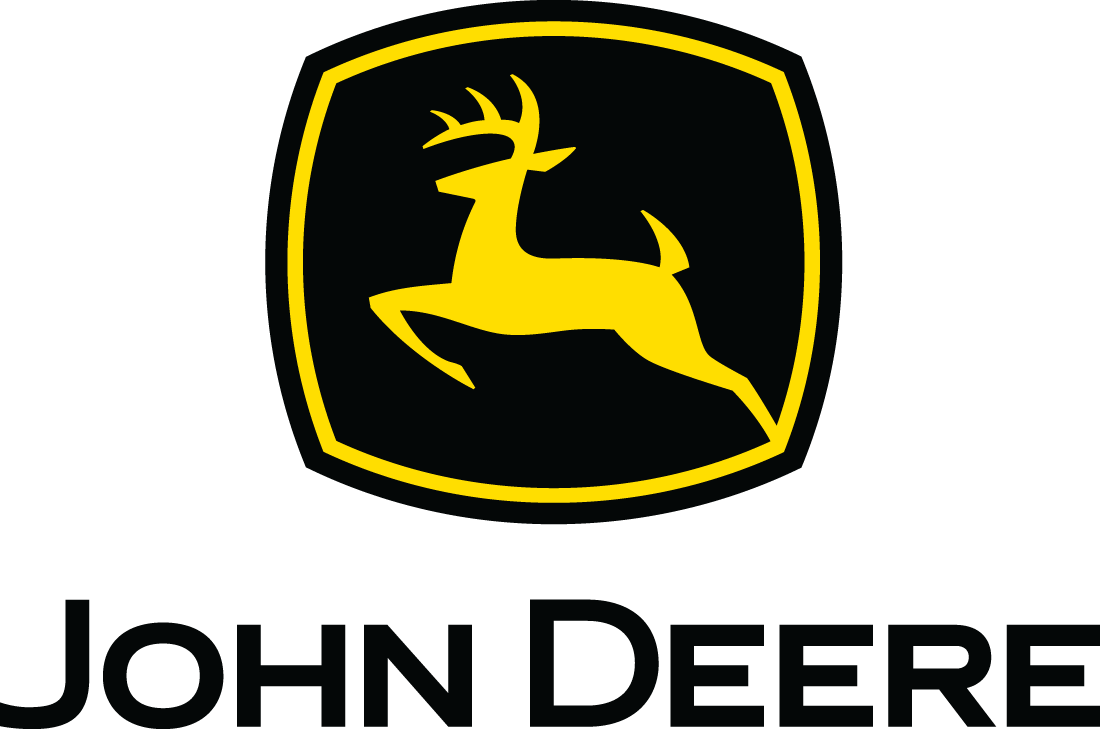
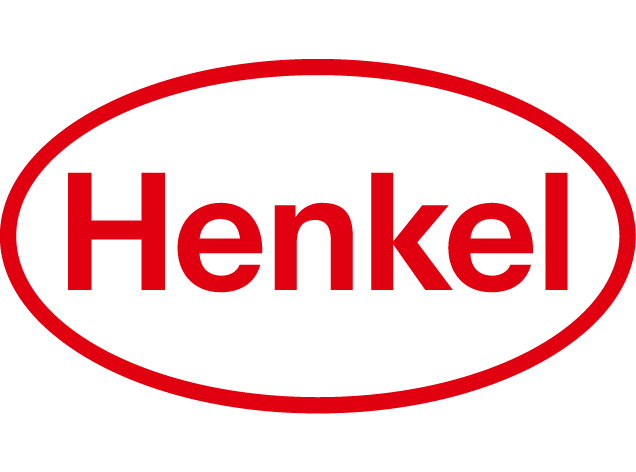
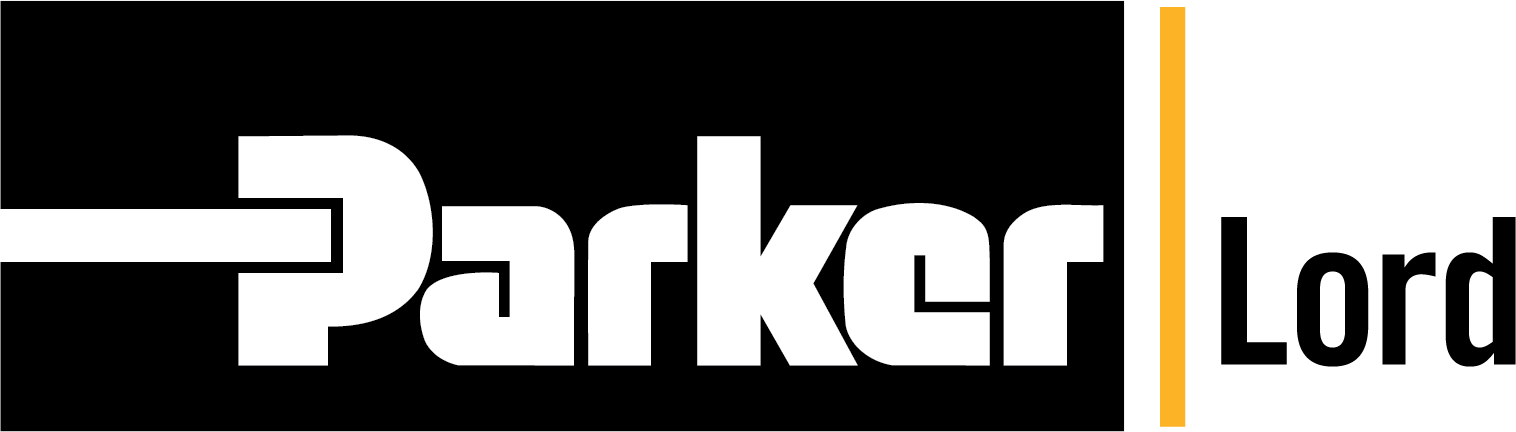
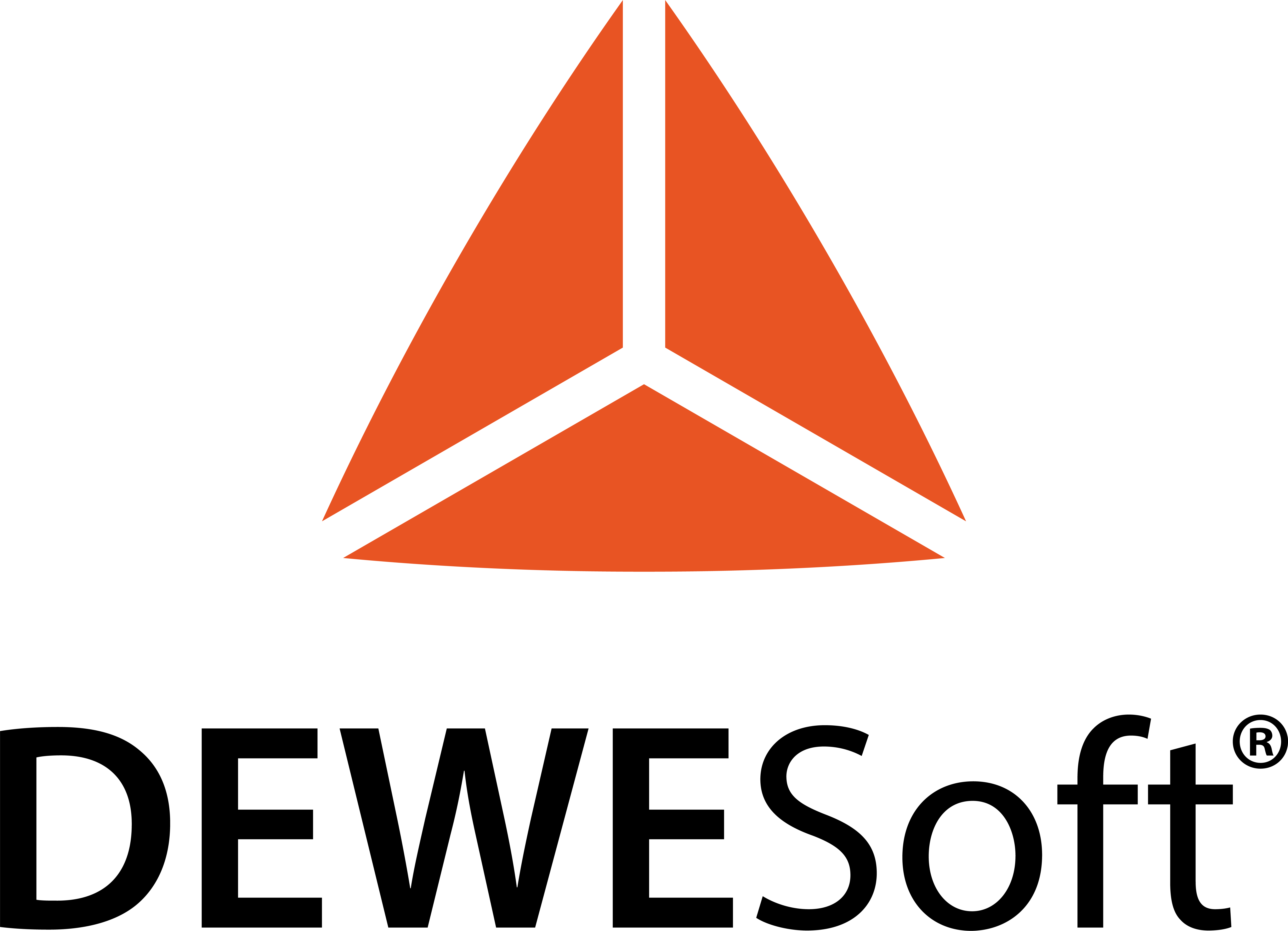
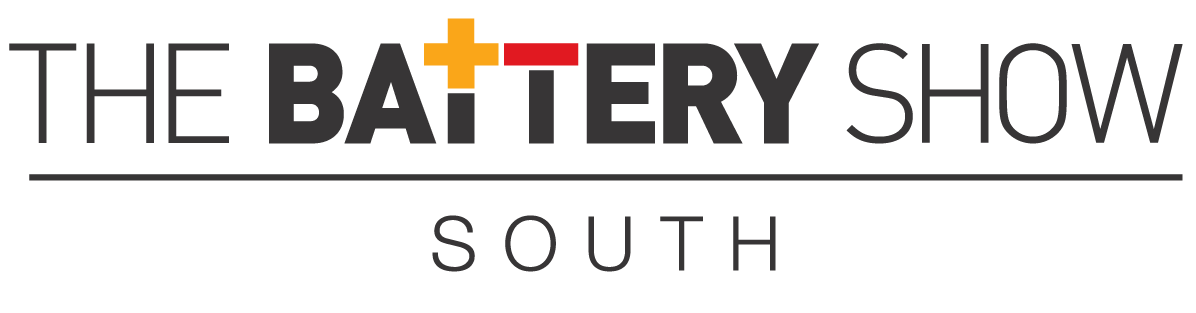
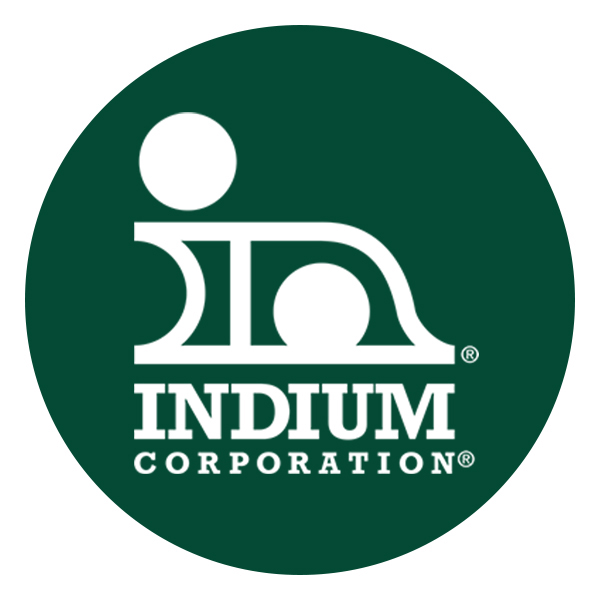
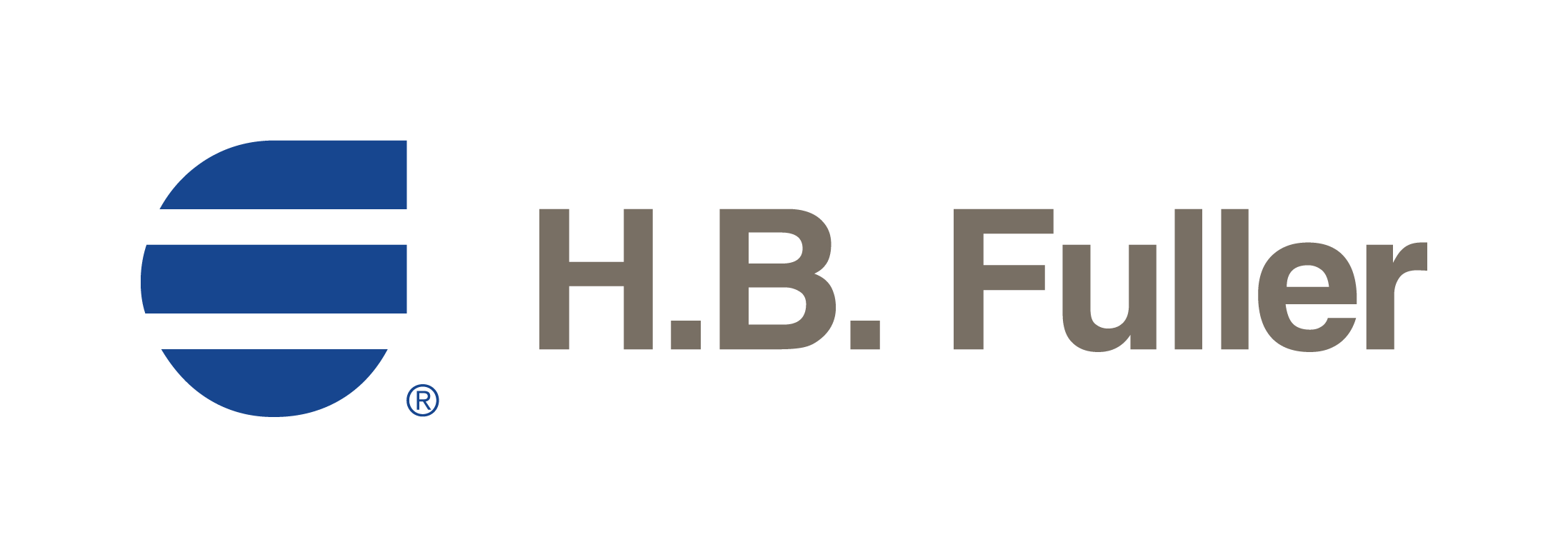