Insulation
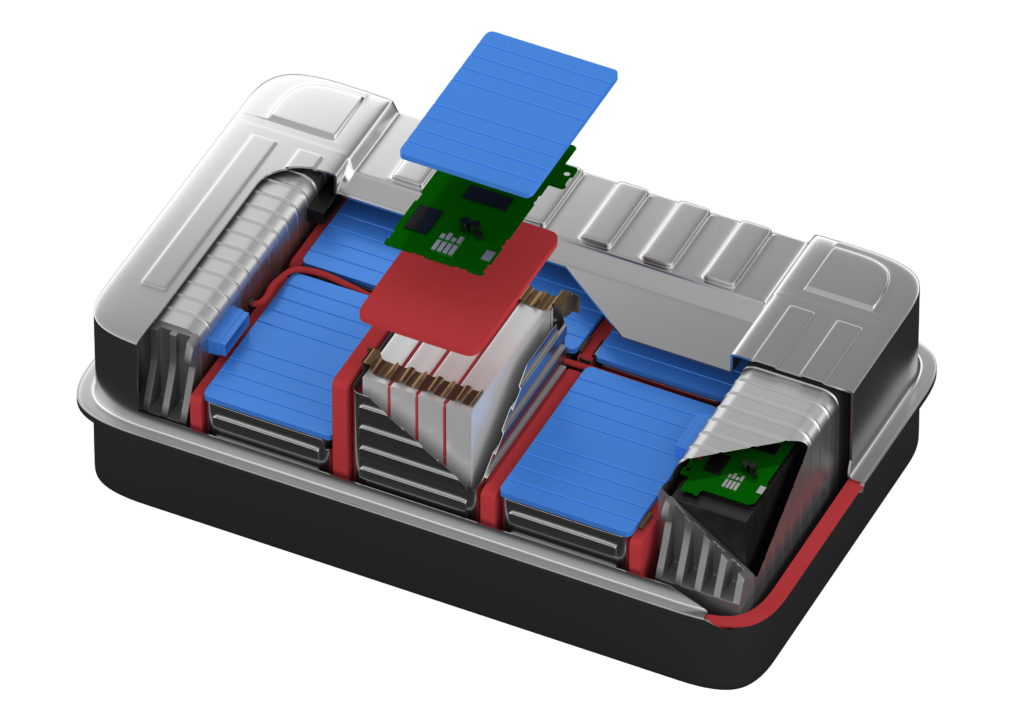
(Courtesy of ADDEV Materials)
Got it covered?
With the need for thermal and electrical insulation in electric vehicles set only to grow, Rory Jackson outlines the options available.
With EVs and HEVs being designed now for longer ranges and heavier loads, so batteries are emerging that provide increasing quantities of energy. Most often, that means larger or heavier battery packs that contain more cells, more modules, and higher energy densities than their predecessors.
However, as figures for energy storage, current draws and voltages go up, so does the need for thermal management. If a battery’s cell temperature rises above 80 C, the lithium in it can react exothermically with the solvent in the electrolyte layer on its anode, which generates further heat and harmful gases inside the battery.
Even higher cell temperatures can lead to internal short-circuits, cathode breakdowns and the release of gases, which when combined make thermal runaway highly probable. This self-sustaining process will lead to fires and eventually explosions within the battery.
Also, at every stage in the electric powertrain, excessive heat increases the vibration of conductor atoms, which disrupts the flow of electrons. That creates more resistance in the circuitry and less magnetic flux in the electric motors, and therefore leads directly to losses in power and energy efficiency throughout a vehicle.
In addition to active cooling systems that use air fans and liquid coolants, there are various passive thermal management systems available that need no power or software to provide critical insulation throughout electric powertrains.
And as well as straightforward thermal insulation, many components and junctions in an electric powertrain use thermally conductive materials. These provide electrical insulation while passively transferring excess heat out of the batteries, motors and other components. That heat can then be dissipated across such media as an aluminium cooling plate, under an air-cooling fan or via a liquid-cooling jacket.
These insulation systems can be installed on the outer level of components, or they can provide protection at lower levels such as among motor windings, or between the modules or individual cells of batteries. These latter configurations are typically more complicated, expensive and physically heavier than pack-level insulations, but they provide greater and longer-lasting protection for EV passengers against the effects of thermal runaway.
With Chinese, European and American regulators likely soon to require that EVs provide a minimum duration of protection for drivers following a thermal runaway alarm, it is critical that manufacturers assess the range of options available for thermal and electrical insulation throughout an e-powertrain.
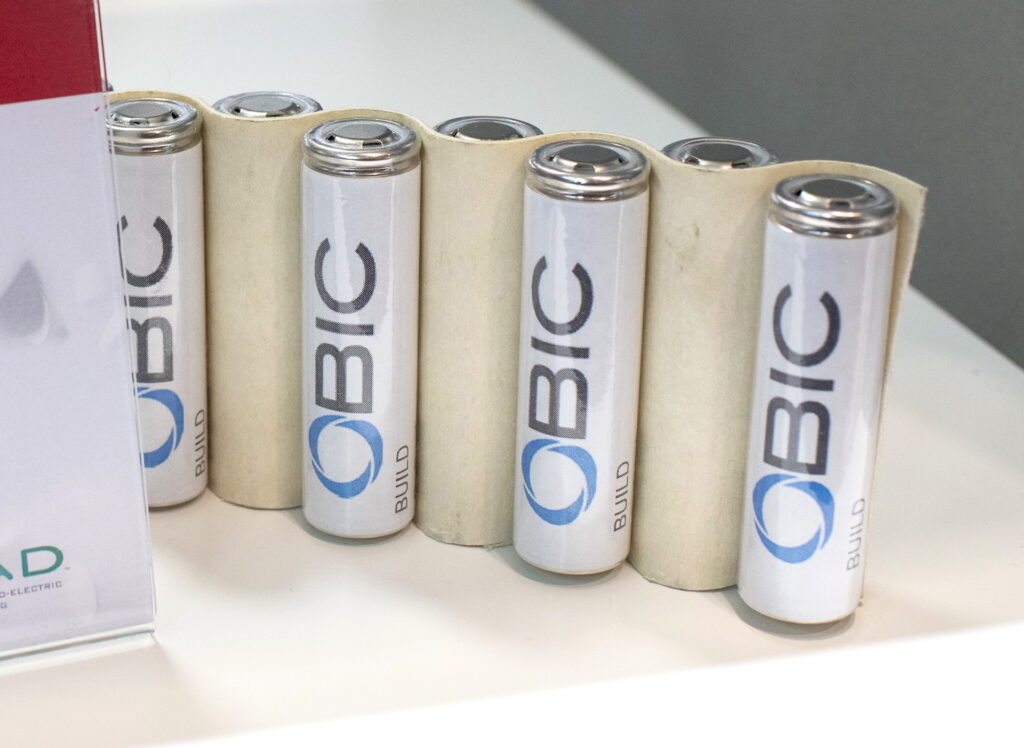
(Courtesy of DuPont)
Thermal insulation
Settling on one particular solution for any thermal or electrical junction can be daunting, given the array of choices available.
Polymers for example come in a range of forms to provide different levels of thermal protection for various parts. Silicone and Nomex, for instance, are well-established and widely used throughout EV and HEV components for their thermal, electrical and chemical resistance.
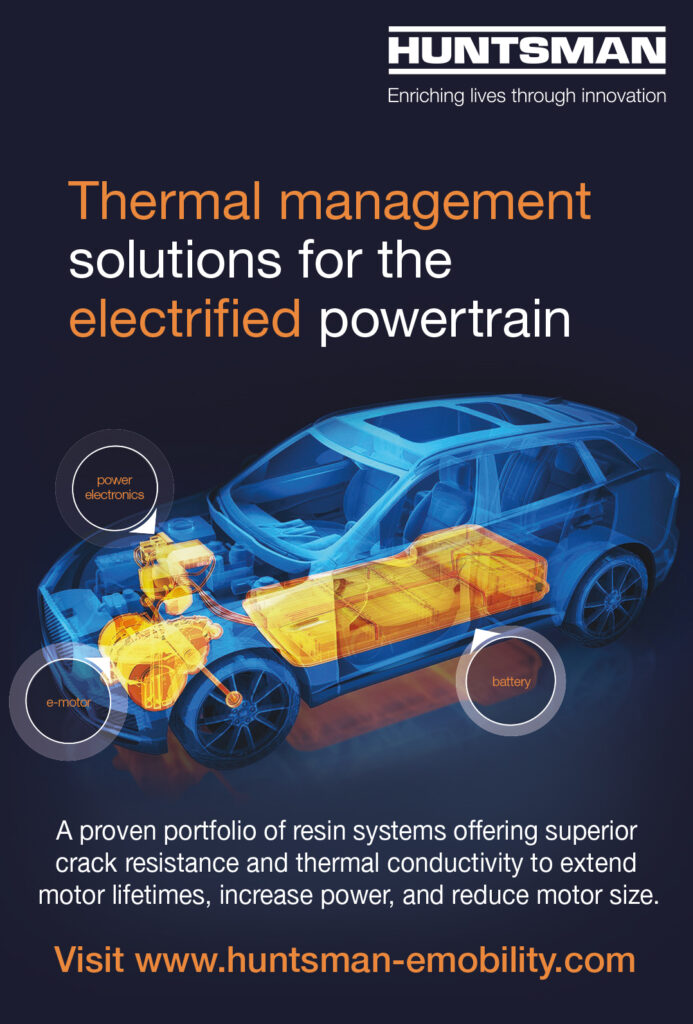
Silicone has strong silicon-oxygen atomic bonds that lend it towards high heat stability and resistance to oxidisation. With operating temperatures typically exceeding 200220 C, silicones are used as insulating sealants for electronic components and as jacket materials for high-voltage cables, for example.
Nomex is similar to Kevlar or Nylon, but with greater thermal and chemical resistance, and has long been used in a range of vehicles (from EVs to racecars) as a thermal and flame barrier, often as a sheet, although it is also available as a fibre. And when manufactured as long, thin sheets, it can be used as a slot insulator between the stator teeth of low-to-medium voltage motors, to reduce the aggregation of heat which might break down the enamelled insulation layer on the copper wires.
Polyester films such as Mylar, Lumirror and Hostphan also provide high thermal and mechanical resistance, and thus have similar versatility to Nomex, being applicable to batteries, motors and other electronic applications. Polyesters have found significant use as insulation for the busbars between battery modules.
As well as films, rubbers and aramids such as these, polyimide foams can maintain their structural integrity between -196 C and +300 C. These have a semi-open cell structure that minimises heat flow as well as sound vibration, making them useful for thermal as well as acoustic insulation.
The physical nature and manufacture of a polyimide foam will vary according to its application. The greater the need for thermal insulation, for example, the more the foam should be ‘densified’ under combined heat and pressure to enhance its thermally resistive properties (and to ruggedise it for harsher environments).
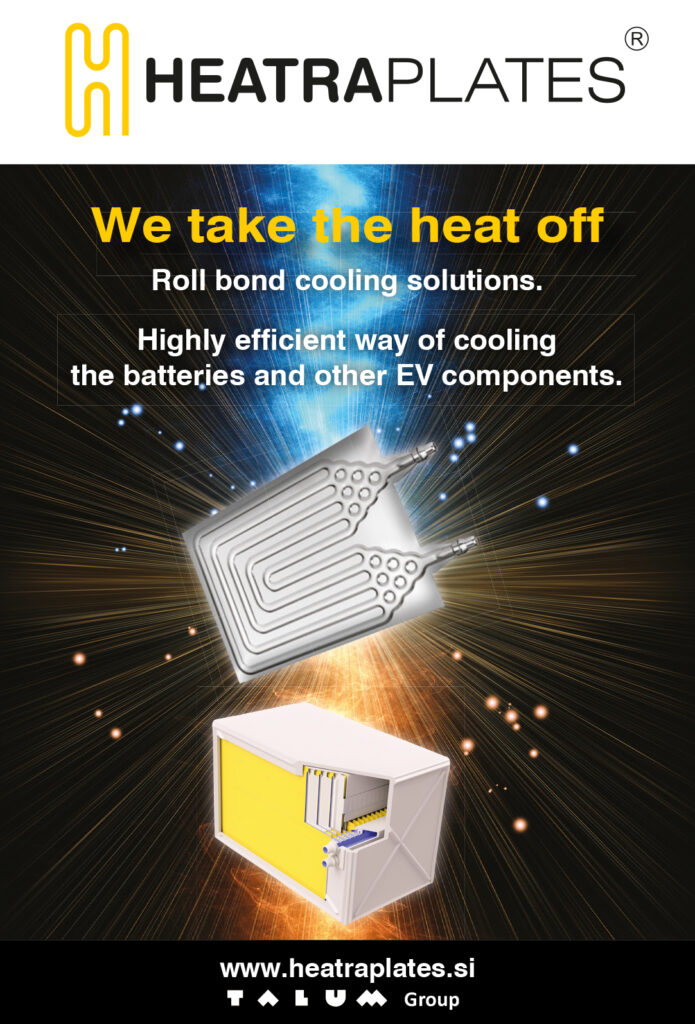
For example, if installed indoors or headliners to keep heat in and cold out of the car (or vice versa), some moderate densification may be useful, perhaps up to 5.4 kg/m3. But for more heavy-duty applications – such as installing it beneath the cabin floor to act as a thermal barrier against the heat coming from underfloor EV battery packs, or applying it near the turbocharger on an HEV engine to prevent heat melting soft components – a foam as dense as 6.4 kg/m3 or more could be necessary.
Acoustic insulation, such as that which might be installed between the cabin and any traction motors, can use less dense foams. Also, some varieties of polyimide foam are available that, if thermal runaway should occur, will generate no toxins and very little smoke when exposed to flames, contributing to the overall safety of passengers.
Phase-change materials (PCMs) have also been the subject of increasing development and have grown in popularity in the e-mobility industry. These are materials that react endothermically when battery cells get too hot, going from a solid-state to liquid and then gas.
These processes have the dual effect of dissipating heat throughout the PCM, and (eventually, after turning into a gas) helping to push the cell’s harmful gases out of the battery’s vents.
Both effects serve to stabilise the battery temperature and slow the rate of thermal runaway. The latter of these is particularly important, as tests have indicated that using PCMs (with an active cooling system) in batteries can provide up to 22 minutes between the start of thermal runaway and a cell exploding.
PCMs can be provided as a solid or flexible material, to account for the differing physical constraints between pouch cells and prismatic or cylindrical cells. Paper-like sheets can also be manufactured for use at the module or pack level.
Mica is also a major mainstay of thermal insulation and protection solutions in electric and hybrid vehicles. Unlike plastics and aramids, it is a naturally occurring silicate mineral – or more accurately, a group of such minerals – that is mined globally and therefore widely available.
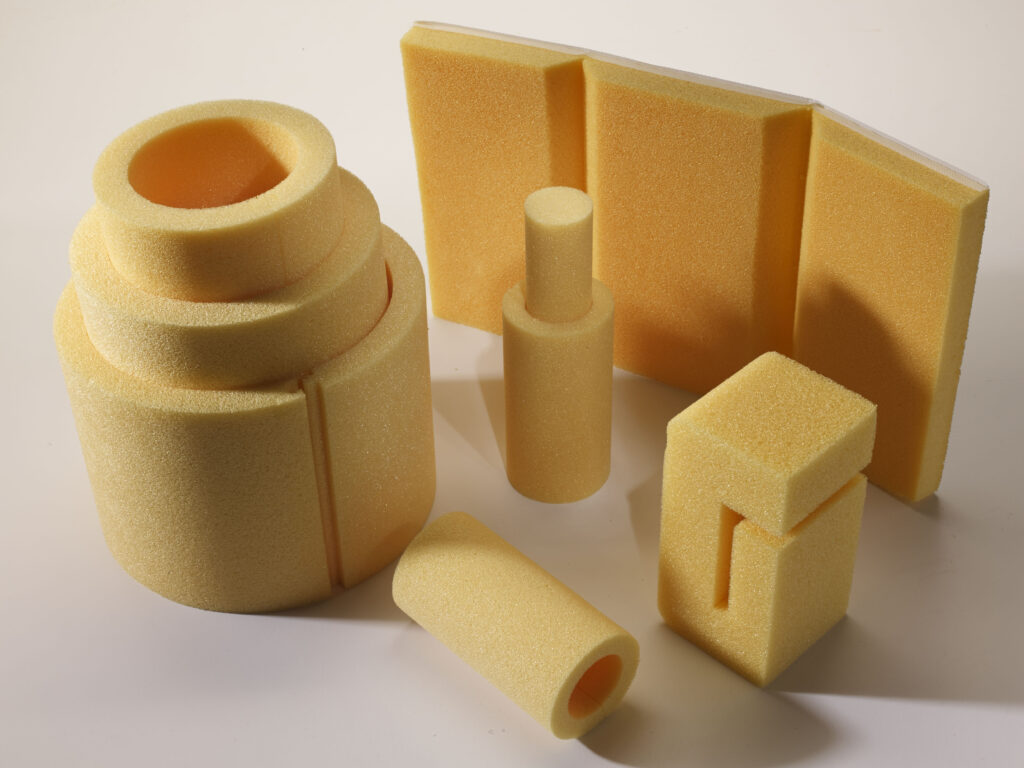
Micas have a sheet-like molecular structure made up of silica (SiO4) tetrahedrons, with sheets cross-linked by cations and minimal routes for electrons to pass freely between layers. That gives them two key qualities that make them vital as an insulating and protective barrier in EVs and HEVs.
The first is a high degree of thermal resistance. For example, phlogopite mica can maintain its structural integrity up to 1200 C, while for muscovite mica it is up to 950-1000 C. In addition, mica can withstand extremely high electrical forces, insulating against up to 22 kV/mm.
These two properties make them useful to engineers in different sectors. For example, domestic bread toasters often have sheets of mica behind their filaments, and other applications have been found for mica over the past 100 years. In the e-mobility space, mica has garnered interest among researchers looking for optimal thermal runaway solutions for battery packs.
Since thermal runaway in one cell or pack can quickly spread and transfer the runaway throughout a vehicle’s batteries, one solution to preventing that heat transfer has been to use a combination of mica and a bio-soluble insulation paper. It is worth noting that this was deliberately developed without the use of ceramic paper which, while highly useful for electrical and thermal insulation, can be carcinogenic, so many manufacturers take the bio-soluble option.
Although layers for protecting against thermal runaway can be installed at the cell, module or pack level, the end result of the chosen solution must be to protect passengers as the battery is burning, so that they can park and exit the vehicle in such a way as to minimise damage to themselves and the surroundings.
To that end, an increasingly popular solution involves installing a layer of mica between the battery layer and the vehicle’s cabin floor. The thickness of the layer will vary depending on the vehicle’s battery power, its potential for heat production, and the time delay the manufacturer aims to give the end-user in the event of a runaway.
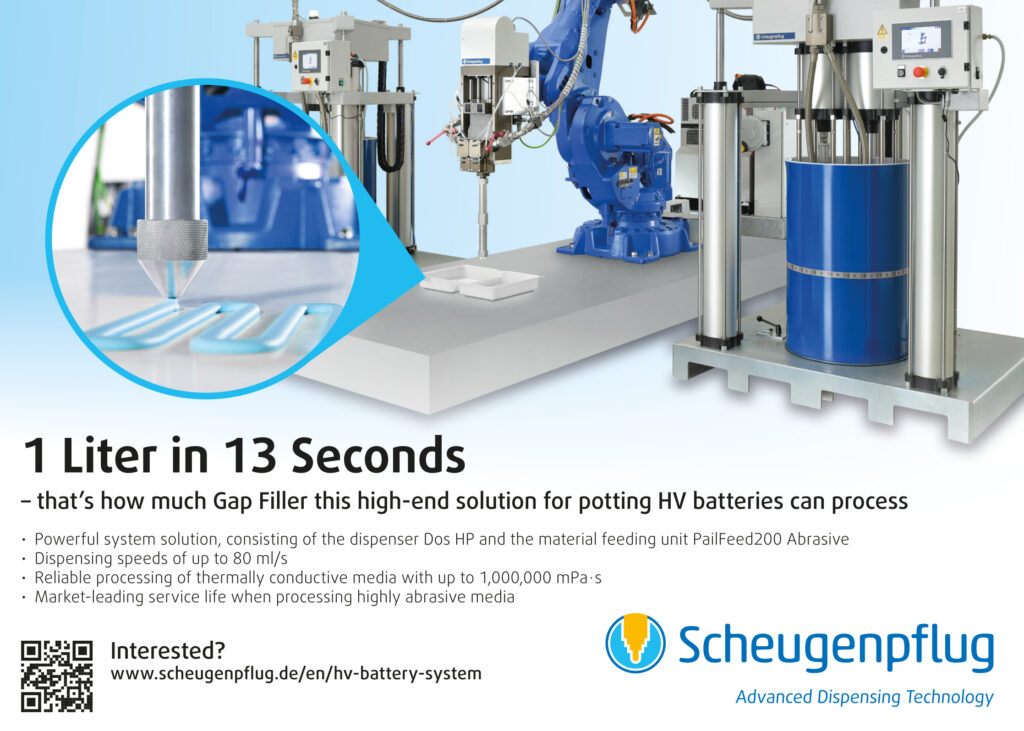
Generally, the industry is moving towards providing vehicles with a 10-minute window, during which the ‘cold phase’ of a thermal runaway must be maintained while an alarm has notified passengers of the need to park safely and make their escape.
Mica’s mechanical properties lend it to further ways of protecting EV passengers. For example, layers of insulation must also provide a dielectric barrier between the individual battery packs and the batteries and chassis components; this property will grow in importance as EV battery voltages increase from 400 to 800 V and beyond. Using thicker mica layers will help ensure there are no short-circuits between the chassis and battery.
Also, when battery cells explode, shards of metal can be propelled outwards, at speeds of up to Mach 5. Tests indicate that mica is sufficiently mechanically rigid to just about withstand and contain such impacts, and in some cases, manufacturers have opted for simply thickening the mica layer in their vehicles rather than use aluminium impact protection sheets.
The question of weight must arise when using thicker sheets of mica, however, particularly regarding the amount of weight the manufacturer is willing to allocate to this protective layer. The density of raw mica is typically 2.4 t/m3, but when enriched with an epoxy or silicone resin, that can fall to between 1.8 and 2.2 t/m3.
A typical EV might contain up to 120 pieces of mica, over and around its battery packs (as well as its connectors, wire harnesses, motor coils and other parts that need thermal and electrical insulation). As an EV manufacturer goes through design iterations, adding weight for thermal insulation, each next iteration might end up weighing 2.4 kg more than the last as they repeatedly add 20 g to each piece of mica.
Fortunately, mica can be very easily cut and shaped to a desired thickness, down to 0.1 mm at a time. At the smallest level, a 0.1 mm piece of mica paper can fit between individual cells and block up to 2.3 kV, enabling engineers to design for exact balances between thermal, dielectric and weight targets.
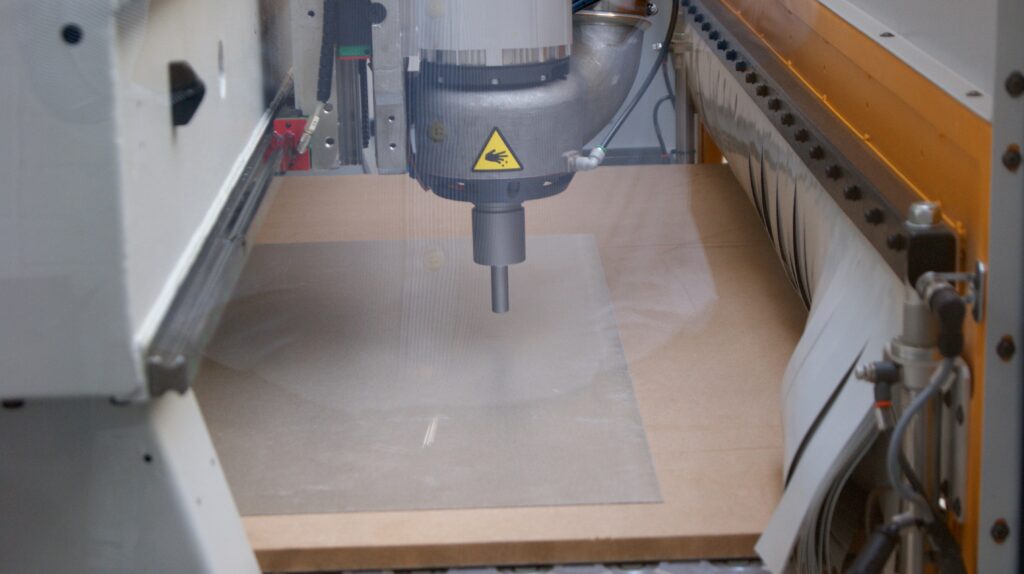
(Courtesy of Elmelin)
Thermal transfer
As mentioned, it is often critical throughout an electric powertrain to provide insulation against heat and thermal transfer to enable the heat to pass out of sensitive componentry and towards a cooling medium. Materials for that must be formulated to exhibit high thermal conductivity, as well as other factors depending on their specific application.
As an example of one such factor, applying thermally conductive epoxies around connectors and circuitry will need to double as strong electrical insulation, with both factors being key to preventing loss of current through the material.
As well as providing an interface between heat-generating electronics and cooling systems, thermally conductive materials are also routinely used as structural components throughout electrical powertrain parts. In a high-voltage battery, for example, there are thermally conductive sealants, gaskets and structural and semi-structural adhesives, most often made from a cure-in-place polymer extruded in fluid form.
Thermal interface gap-fillers typically come as solid pre-cured sheets or fluids, and both can be produced as single- or two-component materials. The latter work in a similar principle to composite materials such as carbon fibre, and by incorporating a second component, some qualities can be enhanced.
For example, blending in particles of aluminium oxide is commonly carried out to improve the thermal conductivity of the gap-filler, as is the use of boron nitride. Meanwhile, fibreglass matting is sometimes used in thermal pads for added mechanical strength while retaining thermal performance, but the qualities of the two components must be balanced carefully to prevent one hampering the benefits of the other.
Silicone is a widely used base for thermal pads and gap-fillers. Its pliability is useful for structural and manufacturing purposes, and it will perform across a wide range of temperatures (typically -50 C to +200 C, although these limits can be pushed).
Some manufacturers and users of thermal interface materials prefer to avoid silicone, however, largely owing to fears about outgassing, so a number of single- and two-component silicone-free solutions have been developed in recent years.
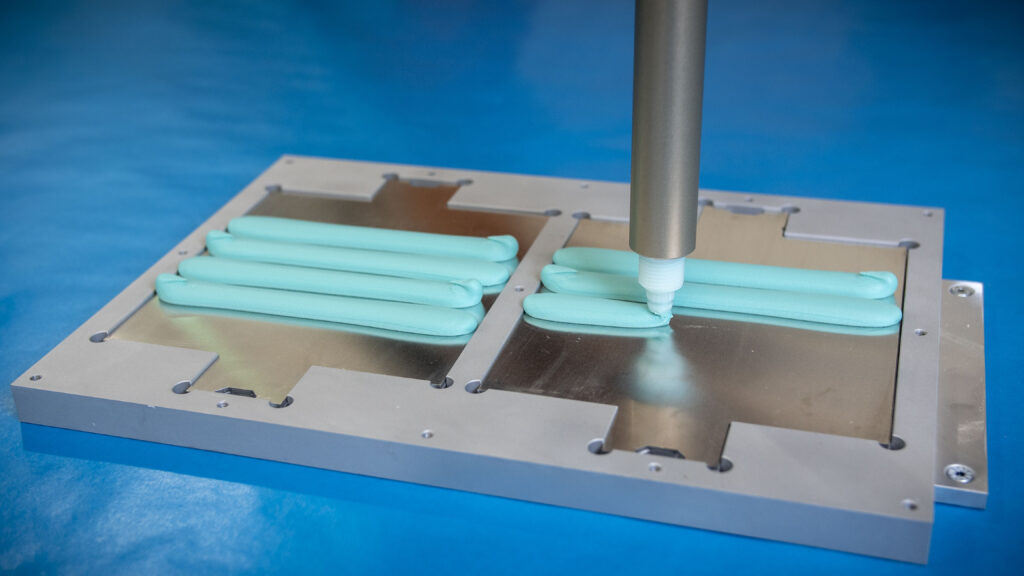
(Courtesy of DuPont)
Application processes
To select the right insulation materials and apply them in the required locations and quantities, significant thermal modelling and analysis should be carried out.
Since heat increases the conductive resistance throughout an e-powertrain and reduces the magnetic flux in electric motors, the power losses derived using electrical analysis and calculation can be used to effectively model the thermal distribution throughout batteries, motors and other parts.
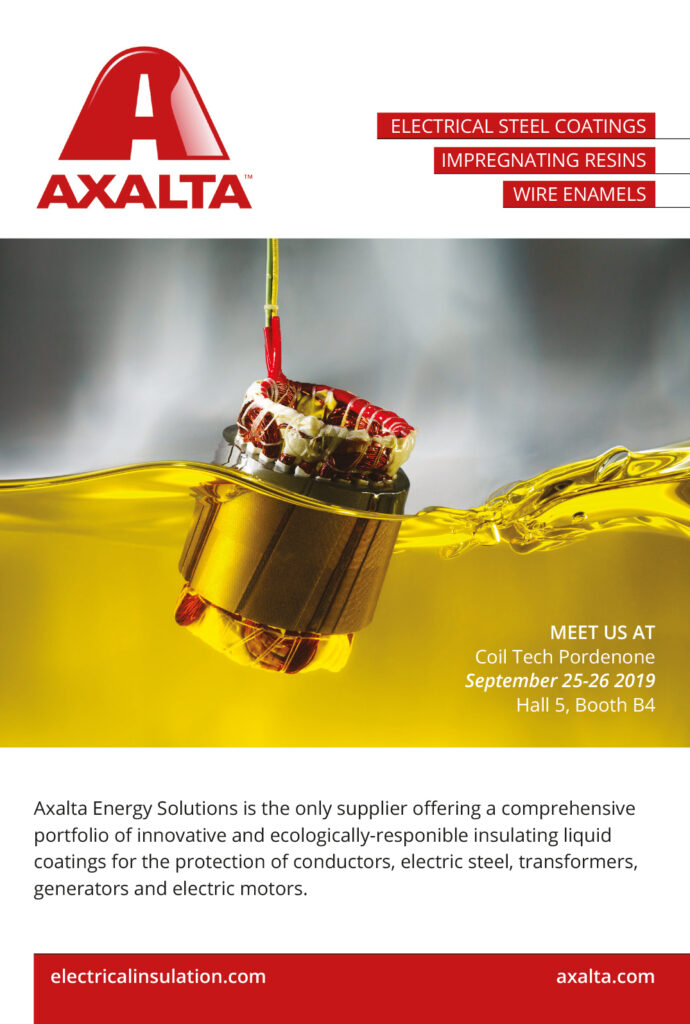
For an electric motor, for example, electrical losses can be combined with mechanical and ventilation-driven heat losses to generate a 3D model of how power dissipation is distributed throughout it (including the densities of it in different motor sections). That then serves as a reliable thermal distribution model for analysing and determining which insulation materials need to be used, where to apply them and in what quantities.
Thermal interface materials must be extruded into place with precision to ensure material consistency, and thus effective thermal transfer and electrical insulation.
Similar modelling can be performed for EMI by using any preexisting models of the circuitry and components. After that, the circuitry can be modified, components exchanged, or EMI filters developed to resolve any issues that arise.
Solid thermal insulators that come in sheets, slots and other such shapes can be manufactured to specified dimensions and installed without too much complexity, depending on the material in question.
However, impregnating motors, batteries and inverters with single- or two-component gap-filler resins, sealants, adhesives, liquid foams or pastes is a much more complex issue, with many different factors to consider.
For instance, the impregnation process must as far as possible avoid leaving any air gaps or bubbles in the extruded material, as pockets of air will reduce the quality of thermal conductivity, causing damage to batteries in the long run through insufficient heat dissipation.
Such gaps would also weaken the structural integrity of insulating seals, allowing heat and potentially moisture and chemicals into component enclosures. Weakening the structure of other gap-fillers would also mean there is less protection for electrical parts against mechanical or electromagnetic vibrations and impacts from dust or gravel.
There are a number of means of thermal material installation. For example, applying thermally conductive and electrically insulative resins to electric motors or generators can be accomplished by ‘potting’.
To do that, the rotor or stator is first pre-heated and a mould is prepared. The motor part is then pressed into the bore of the mould (or vice versa, depending on the motor’s configuration), and the resin is injected into it from the bottom using a vacuum to pull it through. The mould ensures the shape of the potting, and is removed after the resin cures.
Potting is perhaps the most popular impregnation process, probably because it achieves better heat transfer and environmental protection than other methods.
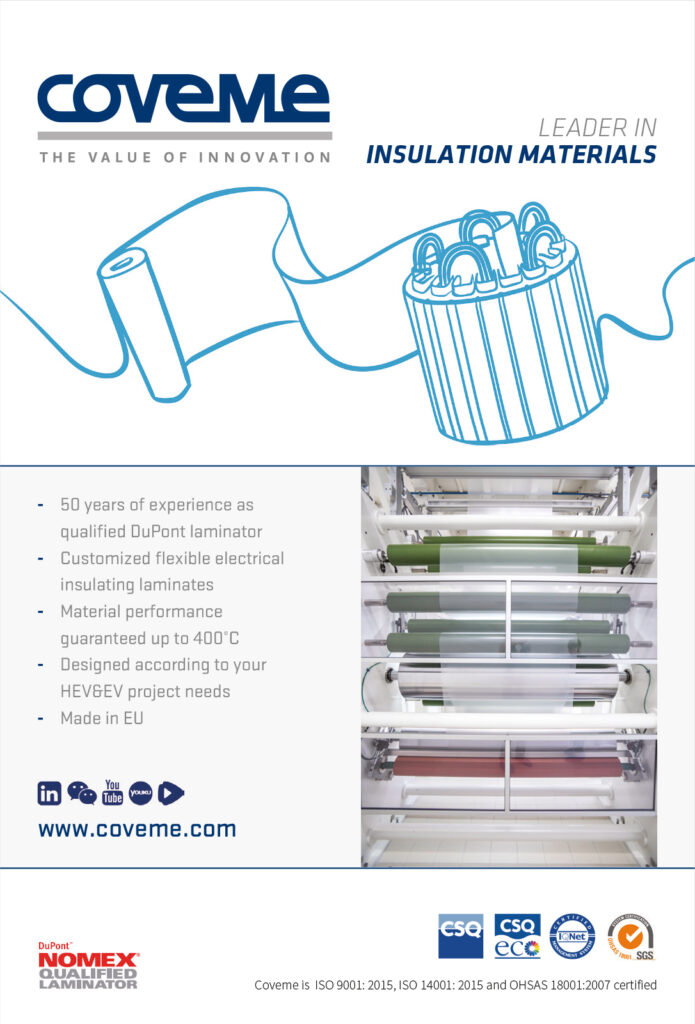
Alternatively, the pre-heated rotor or stator can be mounted on a rotating fixture, with the resin trickled onto the windings at a carefully controlled rate, or the motor component might be dipped into a resin bath as it rotates. Both methods are very useful for conserving the consumption of resin while achieving a very high filling grade in the motor windings, although some cleaning of excess resin across other parts of the stator or rotor may be needed during or immediately after impregnation.
Dipping the entire component into a resin bath (without a mould) is also the simplest way of impregnating motors, but it leads to the highest resin consumption of all the methods and requires the most cleaning-up afterwards.
The quality of the pre-heating is also important, as a stator that has been thoroughly heated with an equal distribution across its body will provide for a more balanced penetration and quantity of resin across its windings.
For drawing fluidic thermal transfer materials from their storage drums and depositing them into battery interface gaps, single-component materials are conveyed directly from a nozzle or needle, but materials using two components must first be injected into a mixing head, in order to combine them and produce a composite of the two before extrusion.
The nozzles must also be mechanically optimised to provide a volumetrically consistent and continuous dosage of the filler material, whether it be from a few microlitres to a litre per minute, as deviations in the dosing rate can create air bubbles in the resins.
For example, one approach uses a pump incorporating a rotor with eccentric motion (the mechanism of which resembles a corkscrew) to convey a constant volume of material. It can also reverse the motion to ‘break off’ the extruded material cleanly and without dripping, enabling a dosing precision of ±1%, even for quantities as low as a microlitre.
As many thermal transfer materials are abrasive, dispenser parts ought to be made from resistant materials such as stainless steel or a ceramic to prevent damage or breakdowns during dosing. While making parts such as pump rotors out of a ceramic is more expensive than using stainless steel, owing to their higher manufacturing complexity, the former also offers greater durability.
Once the method of dispensing the resin has been decided, one of various automation systems can be adopted to precisely plot and control the angle and pattern that the dispenser nozzle takes through the thermal interface gap. These systems ensure that the gap-filler is injected at a controlled speed.
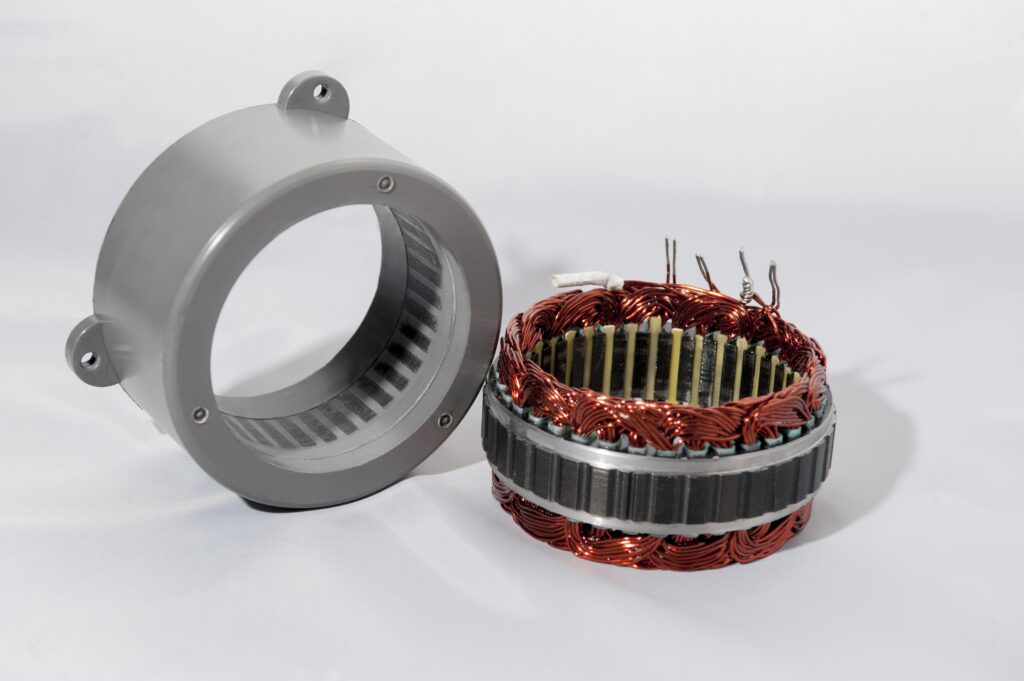
(Courtesy of Huntsman)
Cable insulation
As mentioned, silicone is used in various thermal applications throughout electric powertrains, both as a base for thermal interface materials and as cable jackets.
As the primary conduits for increasingly high voltages throughout EVs and HEVs – upwards of 400 V, and likely to routinely exceed 1000 V soon – HV cables have seen perhaps the most alternatives to silicone developed, owing to concerns regarding outgassing, temperature or mechanical factors.
A number of industry standards have been set for cable insulation materials to ensure a common minimum level of safety between all of them. For example, the Automotive ISO 6722-1 standard for cables in road vehicles (and the ISO 19642 standard which is due to replace it) defines a ‘Class 4’ material as one that functions over a lifetime of 3000 h at 150 C.
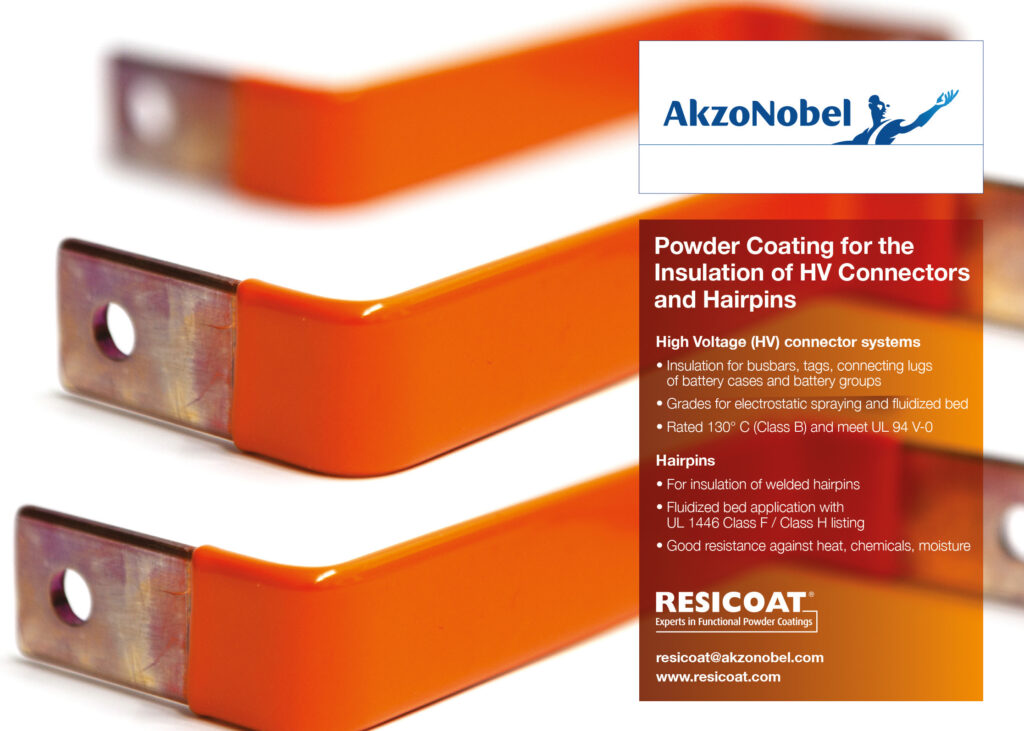
Beyond temperature and lifespan, however, cable insulation materials can differ across a range of other physical and operational qualities, which bear consideration. Irradiated crosslinked polyolefin (XPLO) for example can provide similar thermal and dielectric performance to silicone, but at a much-reduced material thickness.
Its high mechanical, thermal and electrical resistance comes from being formed through the heat and pressure of electron beam cross-linking processes. It is also a halogen-free material, so it will not outgas or emit toxins of any kind when exposed to fire, thus circumventing one of the primary concerns some manufacturers have towards silicone.
At the same time, XPLO resists corrosion from battery acids and other chemicals, which would otherwise present serious problems to many rubbers and other insulation materials for battery cables (including silicones).
The flexibility of cable insulation is important for routing them through the powertrain, to avoid areas with excess heat or other hazards and without leading to wear and tear of the thermally resistant material against the enclosures of power components.
However, there tends to be a tradeoff between an insulation material’s flexibility and the ease with which it can be cut and stripped during manufacturing – and the faster the cable insulation can be cut to the ordered lengths, the lower its price will be. Silicone and other rubbers will provide higher flexibility than XPLO, whereas XPLO will strip and snap off more quickly and cleanly, reducing that aspect of the manufacturing cost.
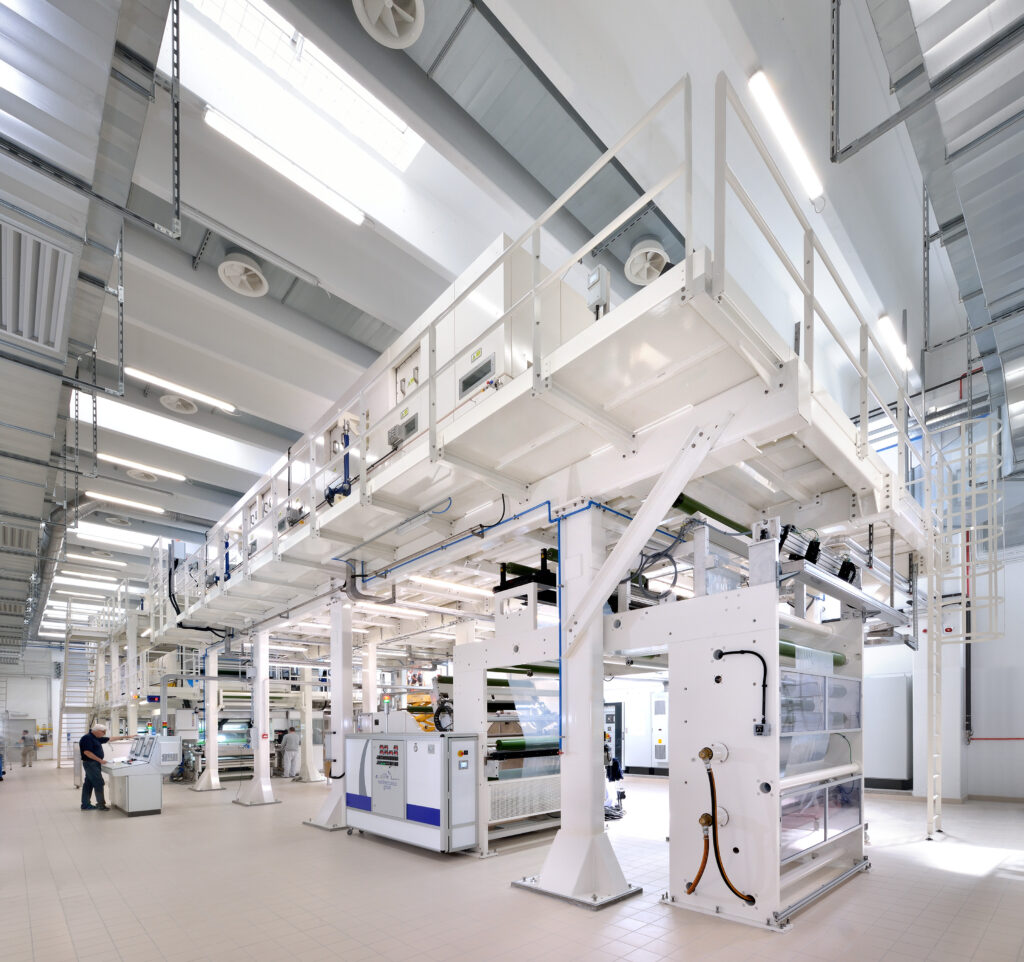
(Courtesy of Coveme)
Conclusion
EV manufacturers are well-placed to track and manage the countless points of thermal and electric imbalance across their vehicles, and can fall back on an enormous range of materials and formats for insulation that have been developed down the years across many industries. Advances in simulation and design will further aid the ability of manufacturers to optimise the thermal requirements and provide long-lasting lifespans and performance capabilities for their end-users.
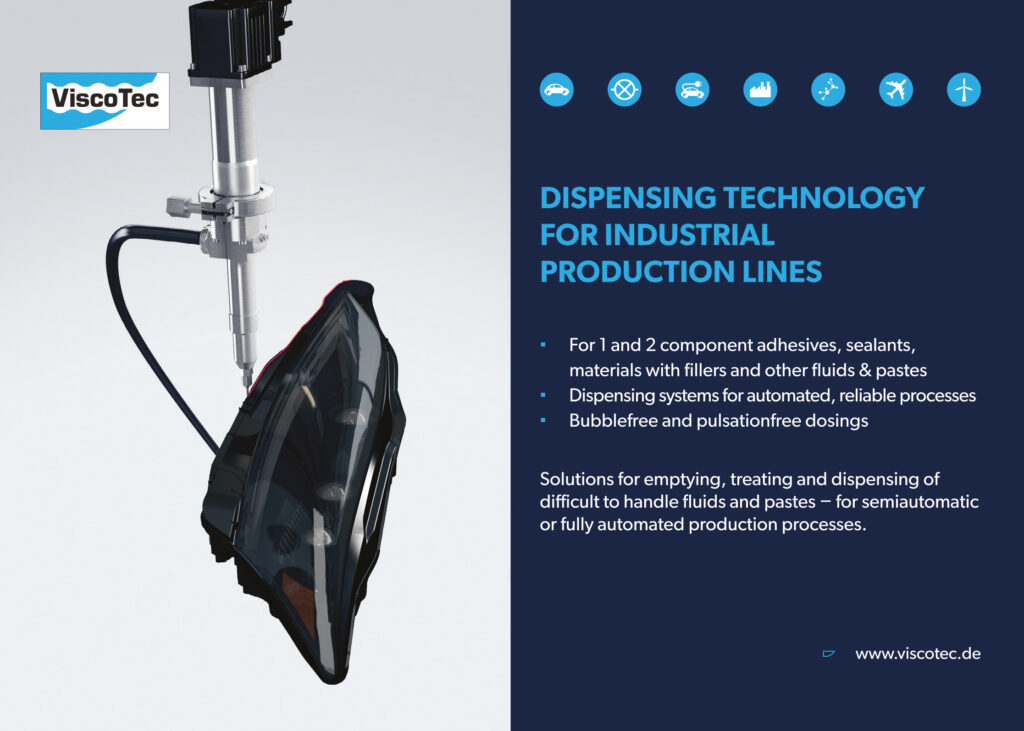
Acknowledgements
The author would like to thank Richard Clarke at Morgan Advanced Materials, Alessandro Piroli at Coveme, Sertac Tekin at Huber+Suhner, Josef Donislreiter at Viscotec, Holger Schuh at Henkel, Michel Moiny and Nicholas Ziapkoff at ADDEV Materials, Isabella Knauder at AVL, Richard Montgomery at Boyd Corporation, Andreas Lutz and Richard Trammell at DuPont, Terry Hughes and Christian Krauss at Elmelin, Carlo Motta at bdtronic, and Werner Hollstein and Florian Gnadinger at Huntsman for their help with researching this article.
Some examples of insulation suppliers
Austria
AVL
Germany
+43 316 787 0
www.avl.com
AkzoNobel
Axalta Coating Systems
bdtronic
Henkel
Poppe+Potthoff
Parker Hannifin
Scheugenpflug
Wevo-Chemie
+49 7121 519 0
+49 202 529 0
+49 7934 1040
+49 211 797 0
+49 5203 9166 0
+49 7142 351 0
+49 9445 9564 0
+49 7111 6761 0
www.resicoat.com
www.axalta.com
www.bdtronic.com
www.henkel.com
www.poppe-potthoff.de
www.parker.com
www.scheugenpflug.de
www.wevo-chemie.de
Italy
Coveme
+39 051 6226111
www.coveme.com
France
ADDEV Materials
+33 472 668440
www.addevmaterials.eu
Slovenia
Talum Izparilniki
+386 2 7995 633
www.talum.izparilniki.si
UK
Avid Technology
Elmelin
Fujipoly Europe
Morgan Advanced Materials
+44 1670 707 040
+44 208 520 2248
+44 1908 277800
+44 1753 837000
www.avidtp.com
www.elmelin.com
www.fujipoly.eu
www.morganadvancedmaterials.com
USA
Boyd Corporation
DuPont
Huntsman Corporation
+1 888 244 6931
+1 302 774 1000
+1 281 719 6000
www.boydcorp.com
www.dupont.com
www.huntsman.com
ONLINE PARTNERS
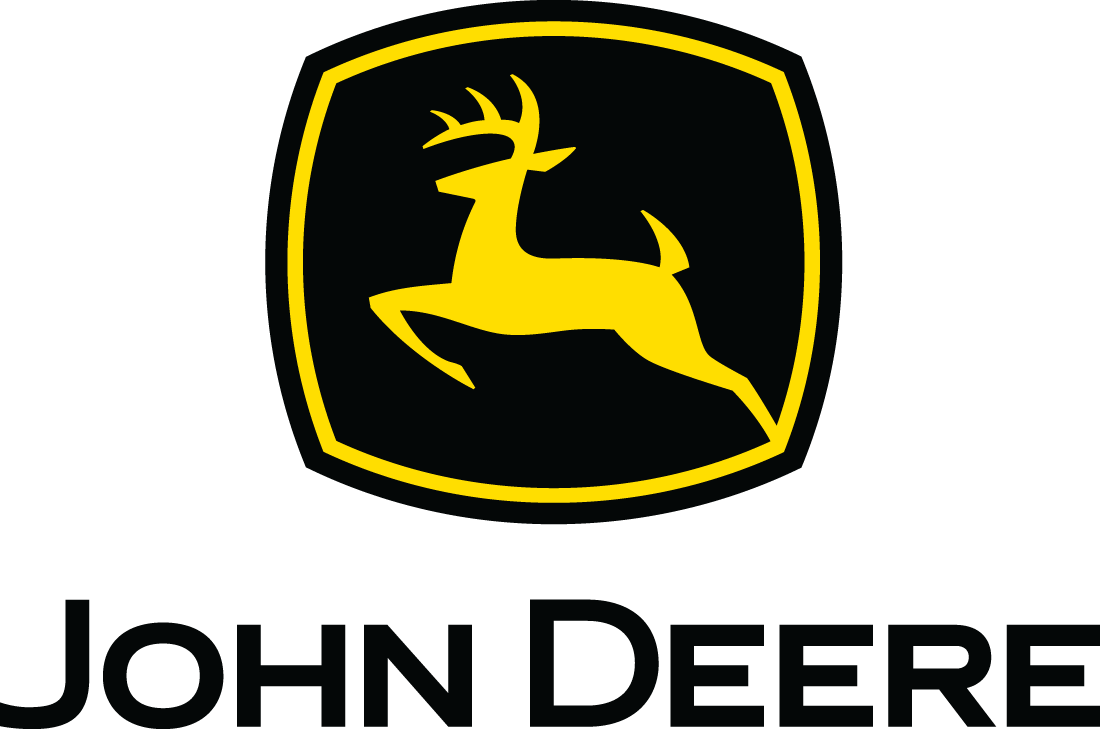
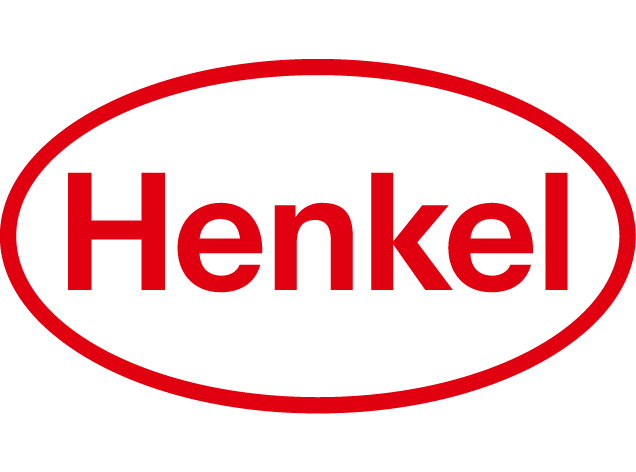
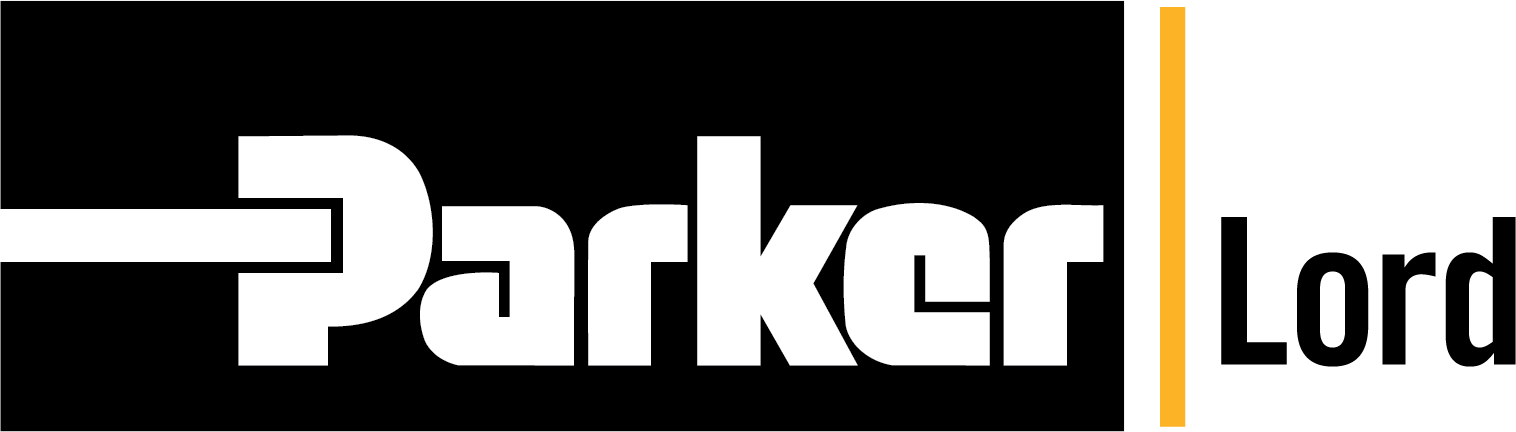
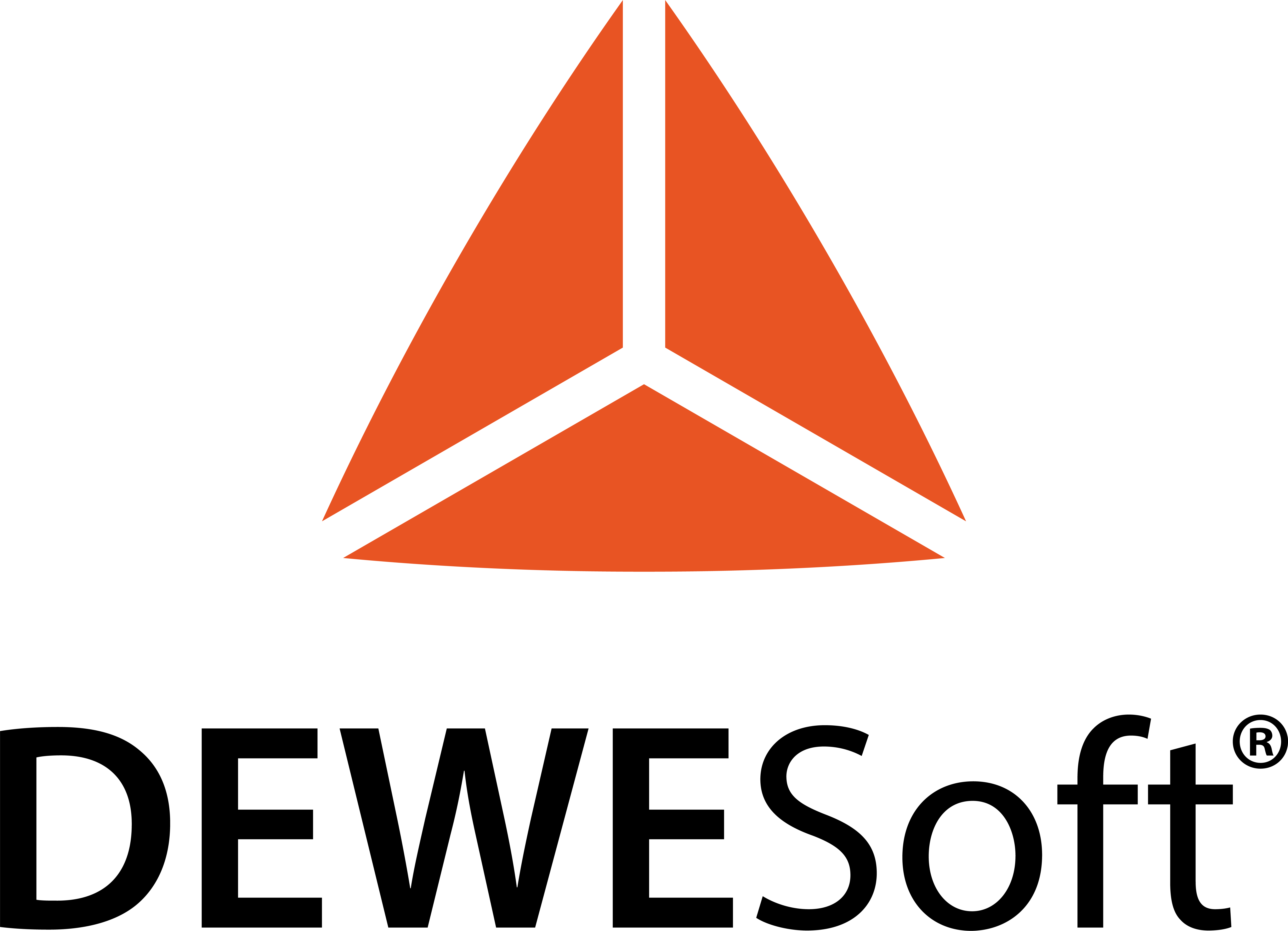
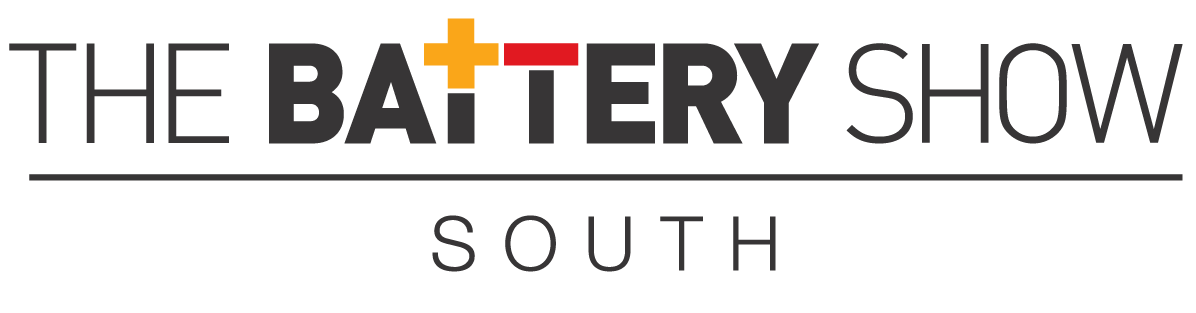
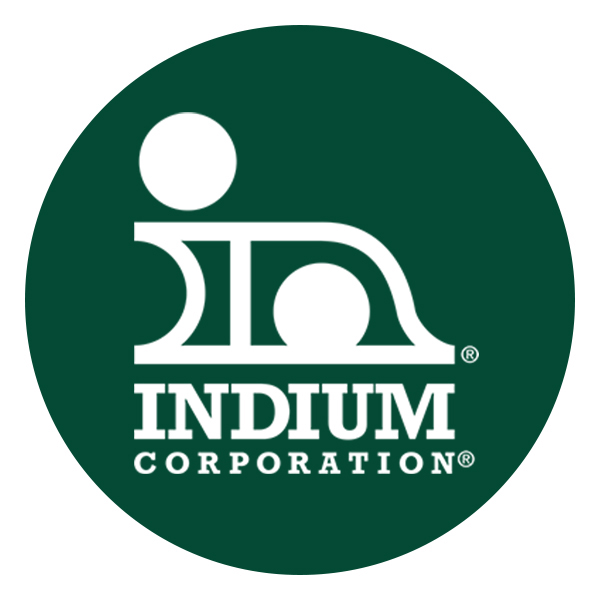

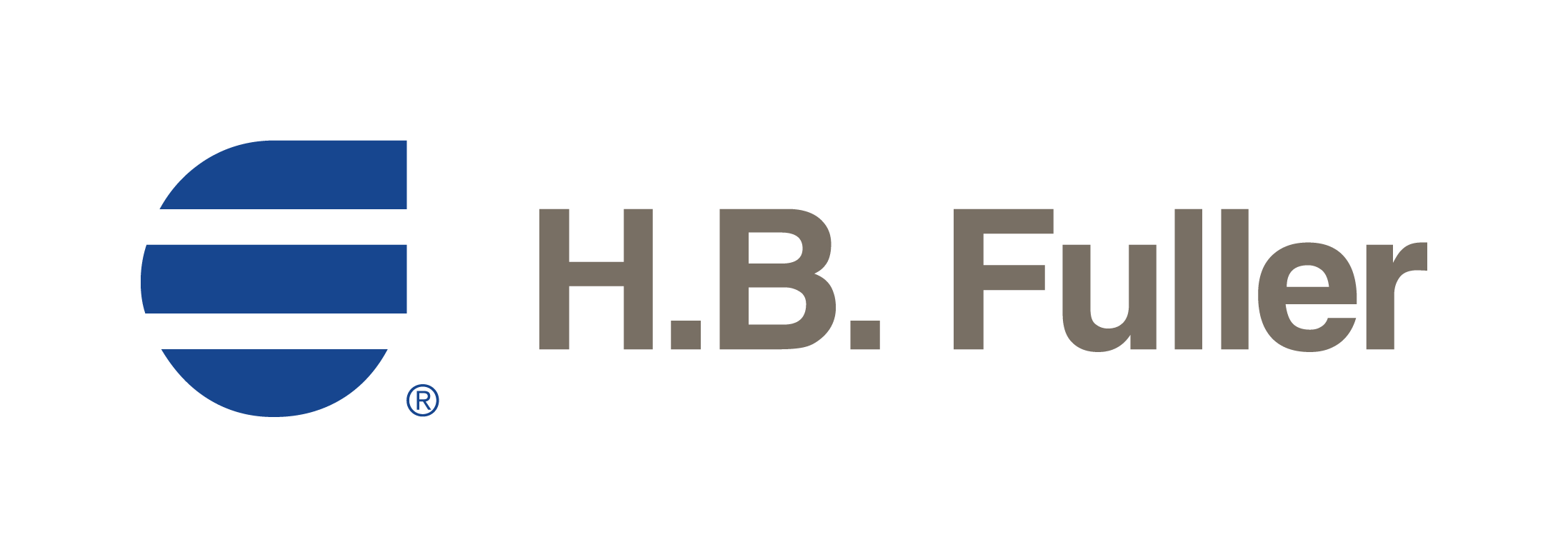
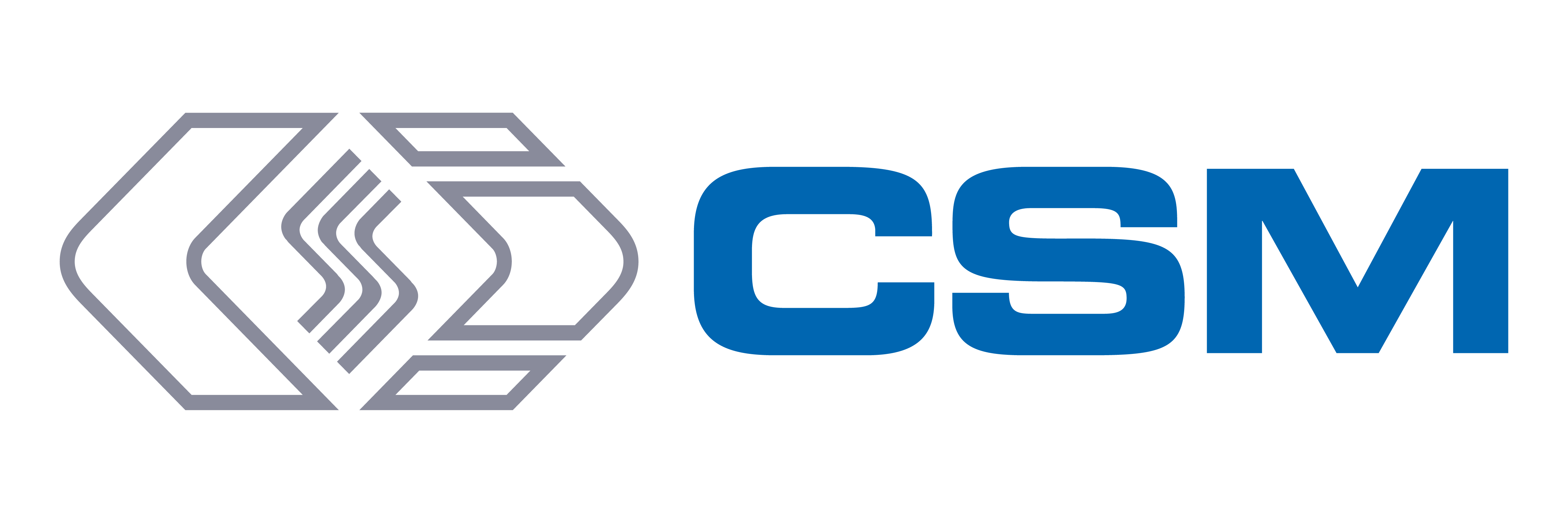
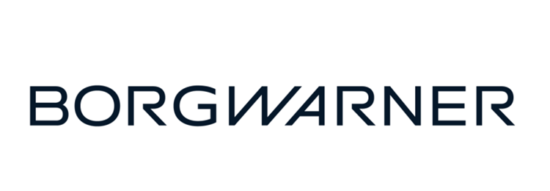