Going electric gives classic off-roader new abilities
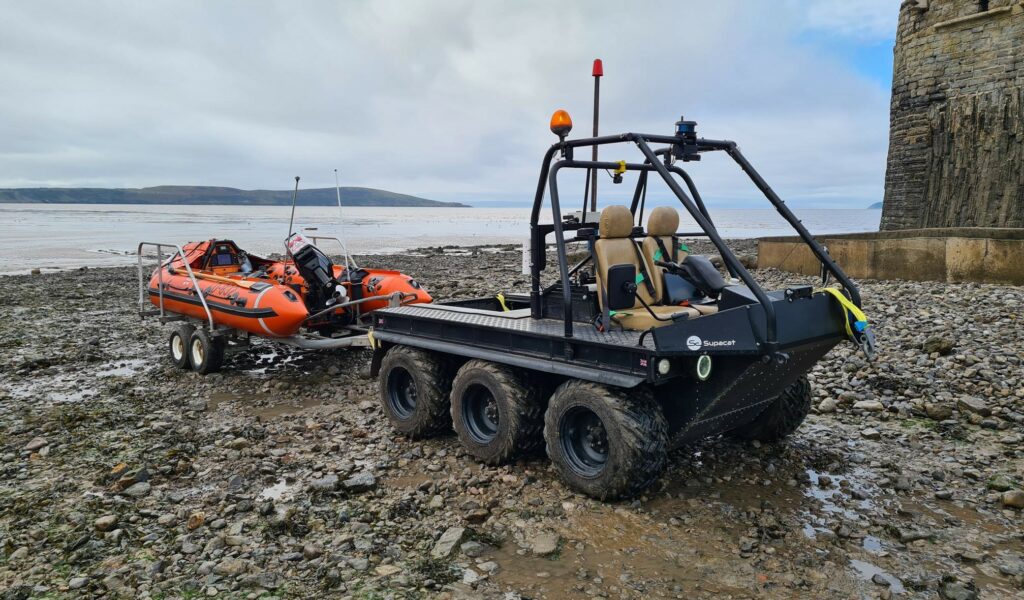
(Courtesy of SC Innovation)
Examples of classic vehicles converted to electric power abound, but SC Innovation’s reworking of the rugged skid-steered 6 x 6 All-Terrain Mobility Platform (ATMP) is remarkable because, rather than adding a high-tech twist to an exercise in nostalgia, it brings new capabilities to a machine that has filled niches in military, agricultural and other utility applications since the early 1980s (writes Peter Donaldson).
The diesel-powered machine on which the e-ATMP is based has three axles, each of which is different, and electrification provided the opportunity to simplify the system and bring some modularity, says design engineer Matt Harvey, who led the engineering effort.
“With the e-ATMP, we have assembled every axle from common parts as we worked through the vehicle design, reducing the parts count and using commercial off-the-shelf items wherever possible,” he explains. “Overall, it is a simpler design with a lot more packaging space inside the vehicle.”
Six Dana Ashwoods IPM motors drive a wheel each via belts and Dana Brevini planetary reduction gearboxes. The belt drives provide a 2:1 reduction between the motors and the gearboxes, with the desired speed and torque provided in a single ratio. This architecture was chosen over in-wheel motors to minimise changes to the original, with the belt drives allowing easy changes to the initial reduction during development.
The control architecture also evolved during development. Harvey says it was originally configured with one primary inverter/controller from Curtis Instruments, two secondary and three tertiary controllers, but was soon simplified to a single primary controller with a lot more processing power managing individual controllers for each wheel.
A lot of subsequent work has gone into the control software to optimise the drive for different conditions. “Two different driving modes are built into the controllers,” Harvey says.
“We have a torque mode for on-road driving, which makes the vehicle act like a normal car. In this mode the wheel motors take the energy they require to meet a certain torque demand from the operator or the control system.
“Then we have speed mode, in which all the wheels try to achieve the same rotational speed. That works well off-road because when you are trying to cross obstacles you don’t have one wheel trying to spin the power away. In more mechanical terms, torque mode is like an open differential, while speed mode replicates a locked differential.”
He adds that the team has also created what amounts to a virtual ‘e-differential’ to help with steering, particularly off-road in speed mode where making all the wheels turn at the same speed would hinder steering.
“We have coded it so that when you steer, the inner wheels slow down and the outer wheels speed up, to achieve enhanced steering and reduced tyre scrub. That helps the e-ATMP feel and act more like a conventional vehicle.”
Electrification has also allowed the engineering team to increase the vehicle’s mobility. The original had skid-steer capability, in which pulling on one handlebar applied a mechanical brake to the output of the gearbox on that side, with enough authority to make the ATMP pivot around the inside centre wheel, which the e-ATMP can replicate and improve upon.
“Basically, we regen the inside wheels so they lock up,” Harvey explains. “Then, with independent wheels on each side, we can set them to rotate in the opposite directions so it will spin on the spot.”
SC Innovation was also keen to match the diesel ATMP’s towing performance, as the ability to tow things much heavier than itself has long been one of the vehicle’s key selling points. A static drawbar pull test, in which the vehicle is shackled to a post and the tractive effort it generates in pulling on the post is measured, enabled the company to verify that and to determine the motors’ maximum current draw at the same time.
This was part of the process that helped refine the electric power system in preparation for specifying a lithium-ion battery pack to replace the lead-acid pack used in development.
This is more complex than might be expected because of the diversity in the duty cycles that suit different potential customers. With short missions with easy access to recharging, lead-acid batteries remain attractive because of their far lower cost.
In a recent demonstration for the UK’s Royal National Lifeboat Institution, the e-ATMP towed a trailered lifeboat, pulling the boat-trailer combination (weighing just under a ton) over rocky and silty terrain, providing a good example of such a mission. In contrast, military customers are likely to want more range and endurance, as well as the ability to power comms equipment and recharge soldiers’ personal mission electronics, so a high-energy pack would be a better fit.
A modular, easily reconfigurable pack with the option of different battery chemistries and a range extender – for which diesel generators and even fuel cells remain under consideration – is therefore likely to be the preferred solution, Harvey says.
ONLINE PARTNERS
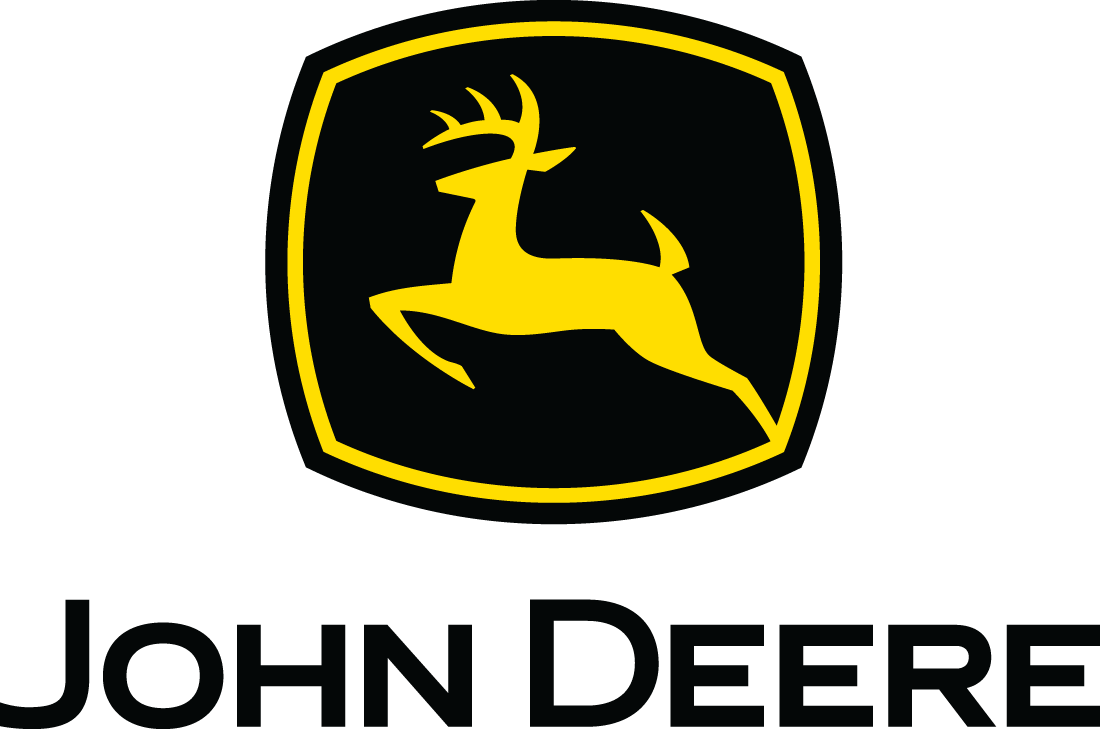
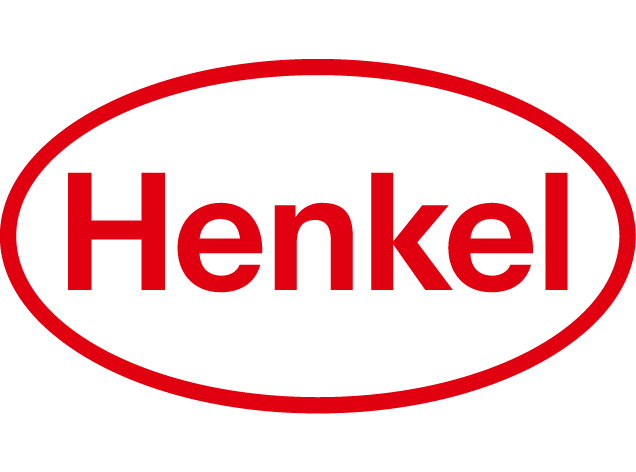
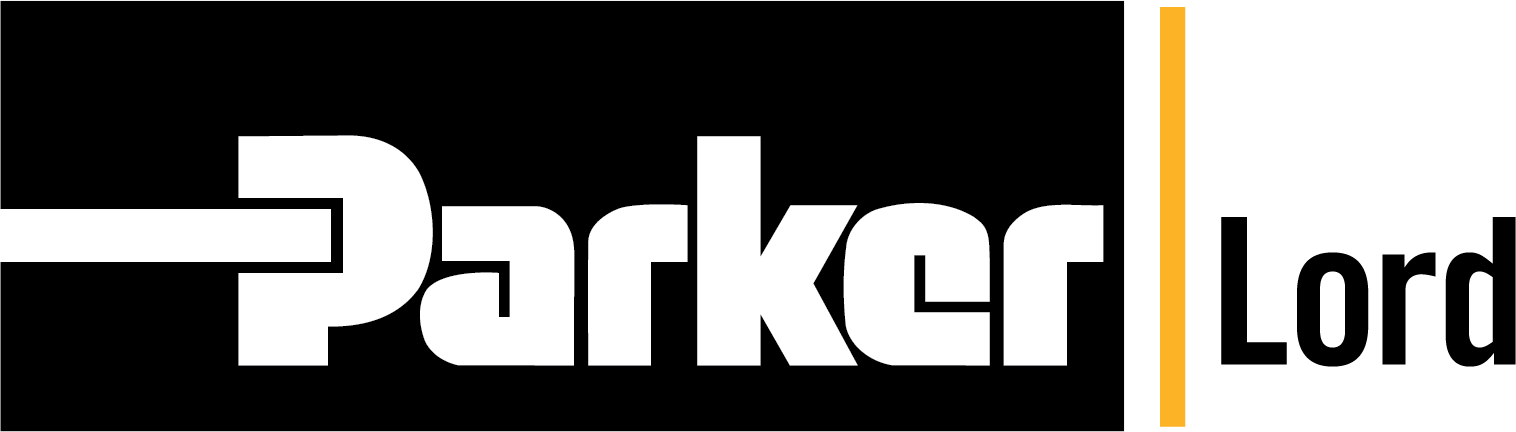
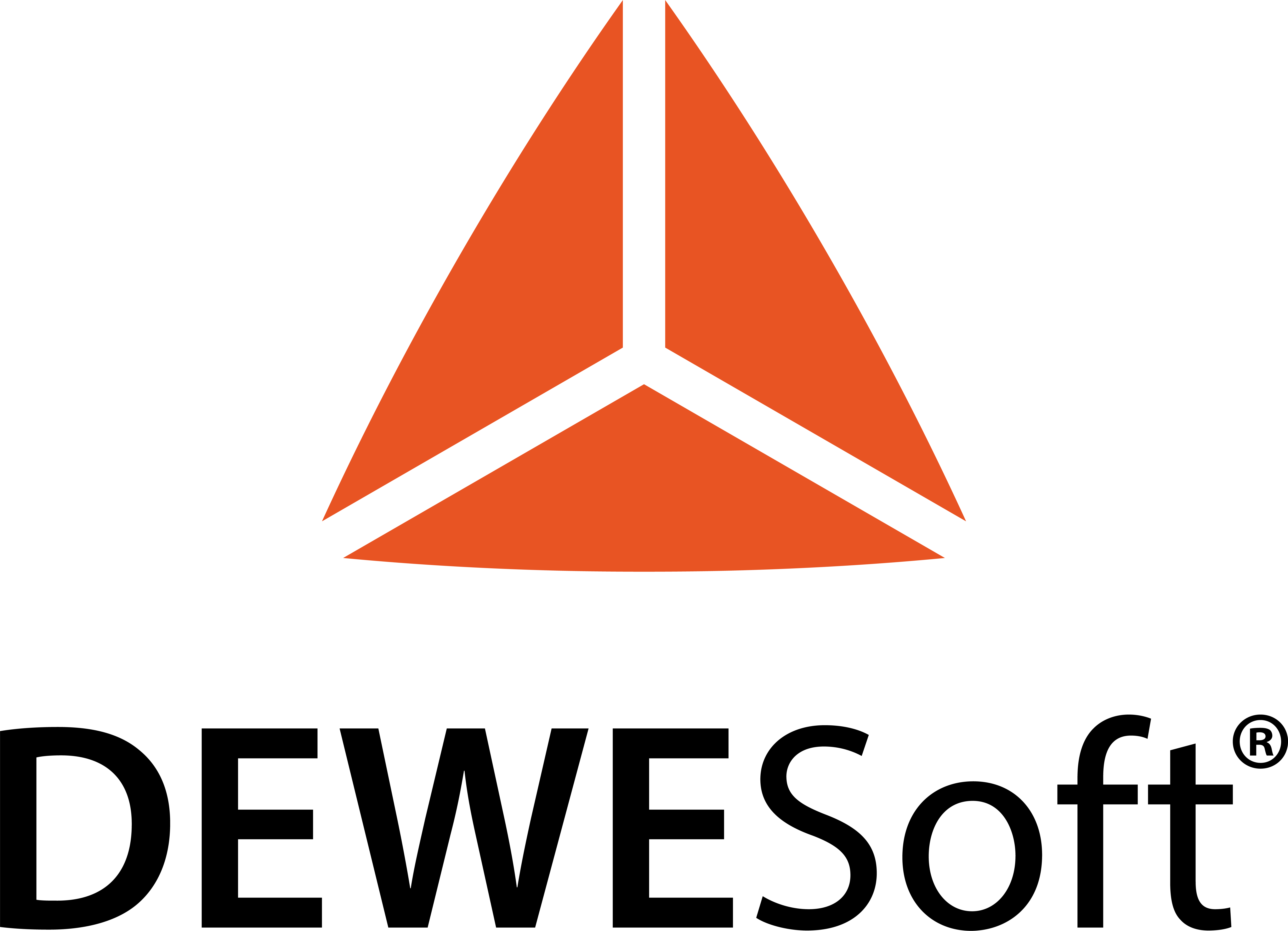
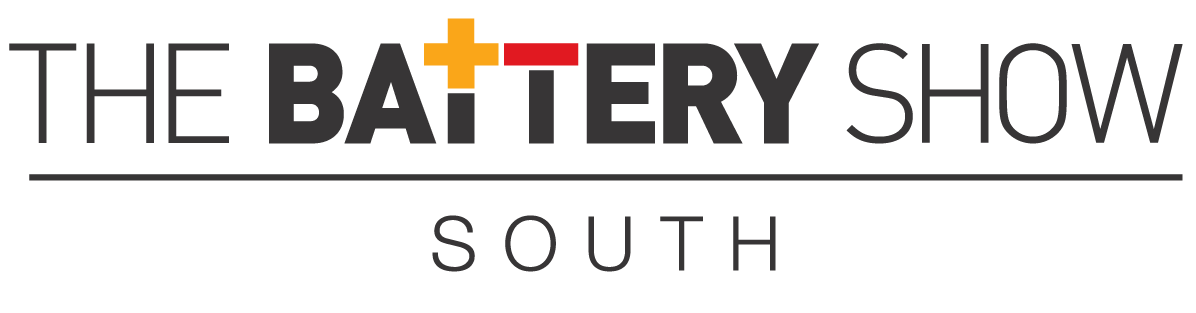
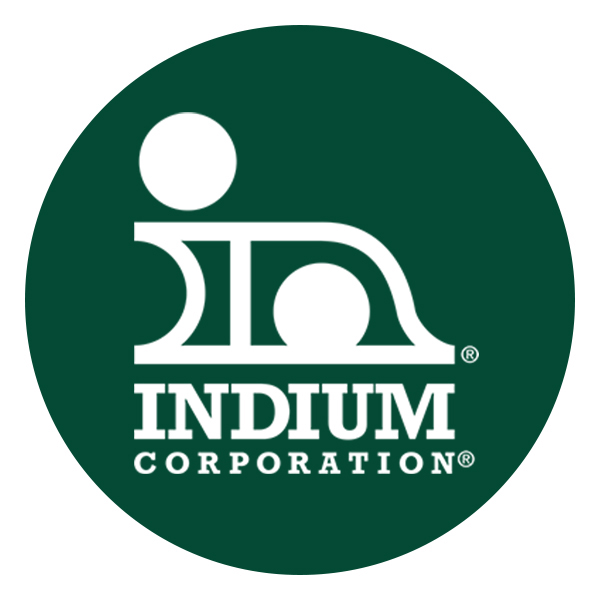
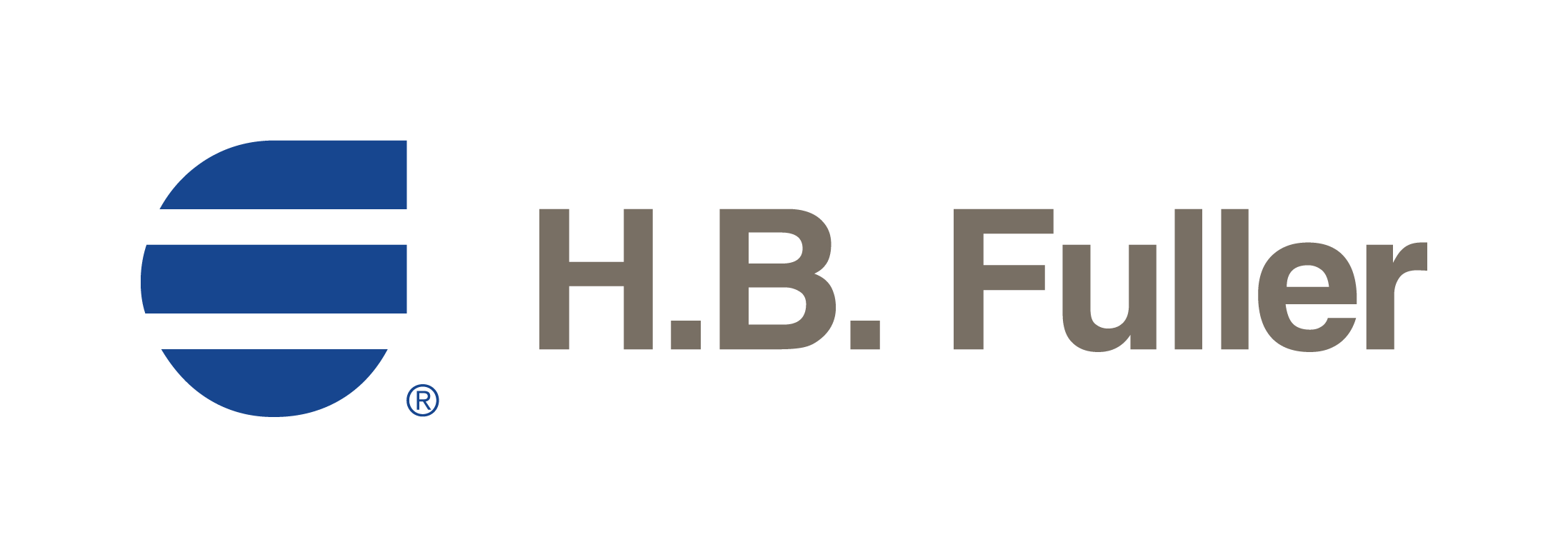