Flextem’s PTC heating films for batteries
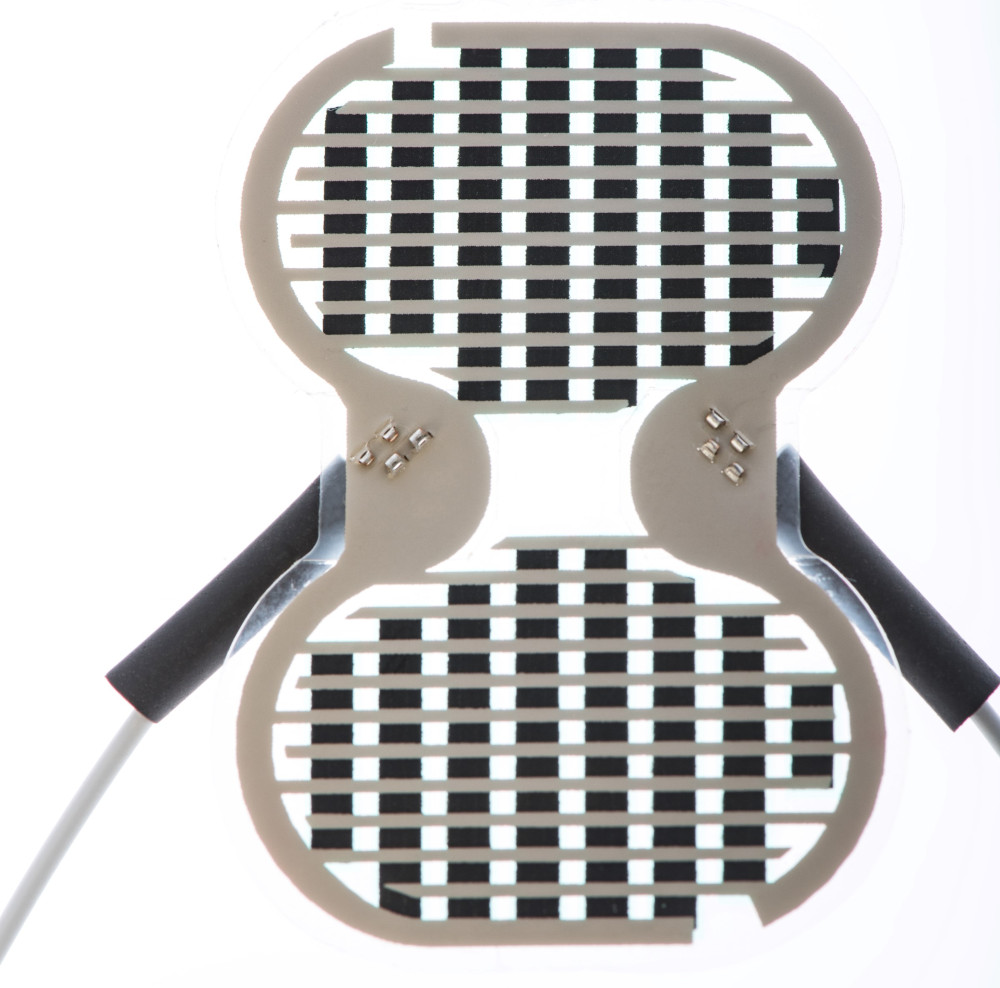
Heating is as important as cooling in the thermal management of battery packs, since lithium-ion batteries need to be held within the temperature range specified by the cell manufacturer if they are to operate safely and efficiently, and achieve their maximum service life (writes Peter Donaldson).
Efficient, self-regulating positive temperature coefficient (PTC) heaters constitute an established technology in this area, and to get the best of them they must be custom designed for each application.
The heaters themselves consist of polyester films typically made from polyethylene terephthalate or polyethylene napthalate, or from polyimide materials such as Kapton. The heating elements are screen-printed onto them as dots of carbon-based PTC ink, with a silver substrate electrically connected to the dots by a carbon layer.
In all PTC materials, resistance increases with temperature, in a process that is naturally self-limiting so that the heating element will not exceed a certain temperature, which can be engineered for each cell type and battery application.
“PTC ink is combined with carbon,” Lars Keiz of insulation and heating technology developer Flextem explains. “As the material heats up it expands, so the resistance increases.
“All the black dots are effectively different heating elements on a bigger heater that might have 100 dots, each of which regulates itself individually. So the heater adapts itself to the needs of the battery – if one cell still needs heat it will get it, if its neighbour doesn’t it won’t, because the element will be at its limit,” he adds.
In this way, the technology automatically adapts to the surrounding thermal conditions and can ensure homogeneous heat distribution, even when some areas of the battery experience different heating loads, so that both hotspots and general overheating are avoided.
Keiz explains that because the limiting effect is a fundamental property of the material, it does not require computer control. “A lot of customers also control it externally, but you really don’t have to,” he says.
He emphasises that Flextem makes no standard products, as everything is customised, including the size and shape of the heater film and each individual element.
Although the polyester carrier films are the most common for EV applications, Flextem often uses polyamide in aircraft and satellite applications, because it tolerates higher temperatures. Polyamide will work up to 200 °C while polyester is limited to 150 °C, Keiz says.
In addition to the PTC ink and conductive silver layer, an insulating layer is also printed onto the carrier to prevent short-circuits. The company can also laminate the heater to provide better thermal insulation, Keiz notes. “We can laminate aluminium foil and/or foam – aluminium foil for a better heat distribution, foam as a thermal insulation,” he says.
Flextem’s PTC heaters work at between 1 and 900 V DC and AC, and can deliver more than 2 W/cm2, with power consumption depending on temperature. They can be made in sizes of up to 970 x 650 mm and can use Fast Flexible Cable or Micro Quadlok System crimp connections.
ONLINE PARTNERS
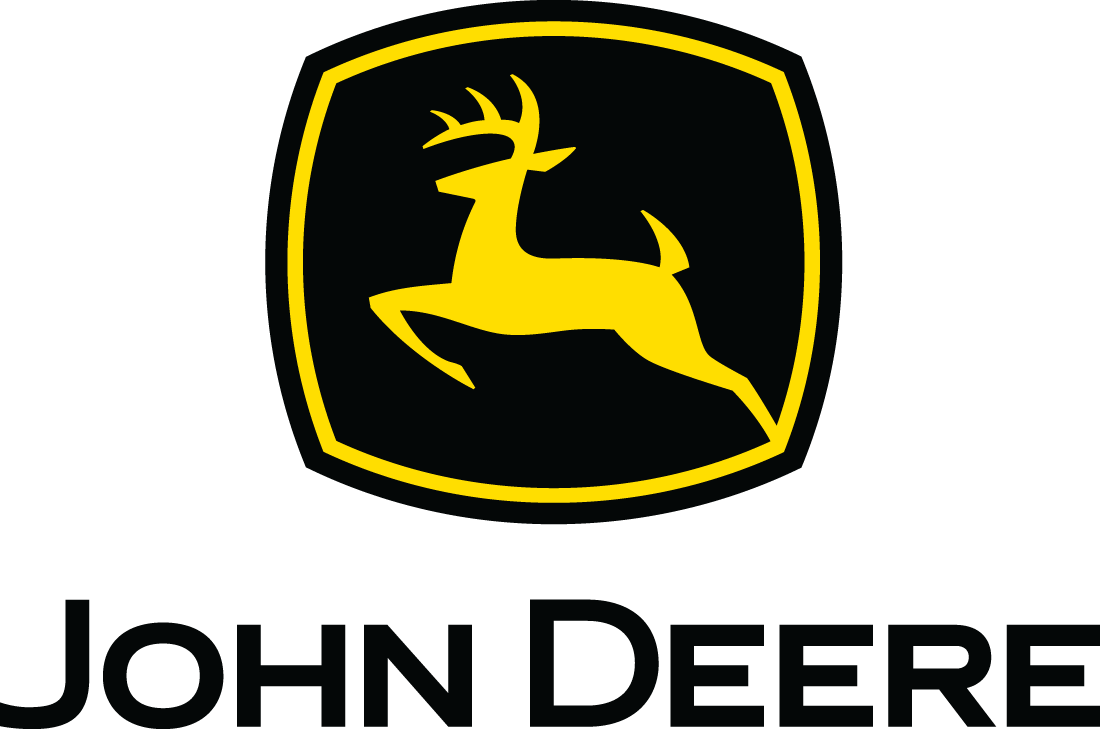
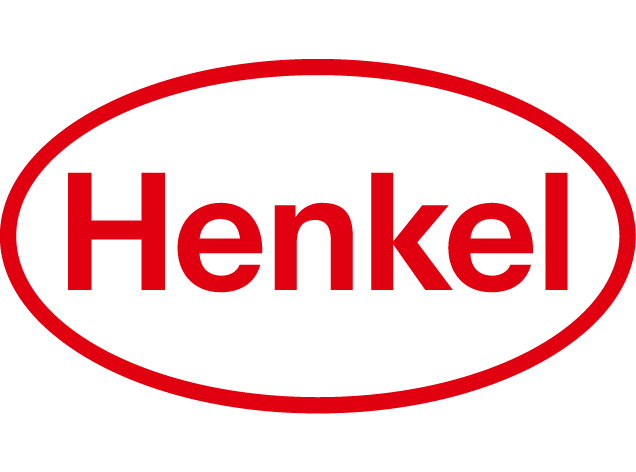
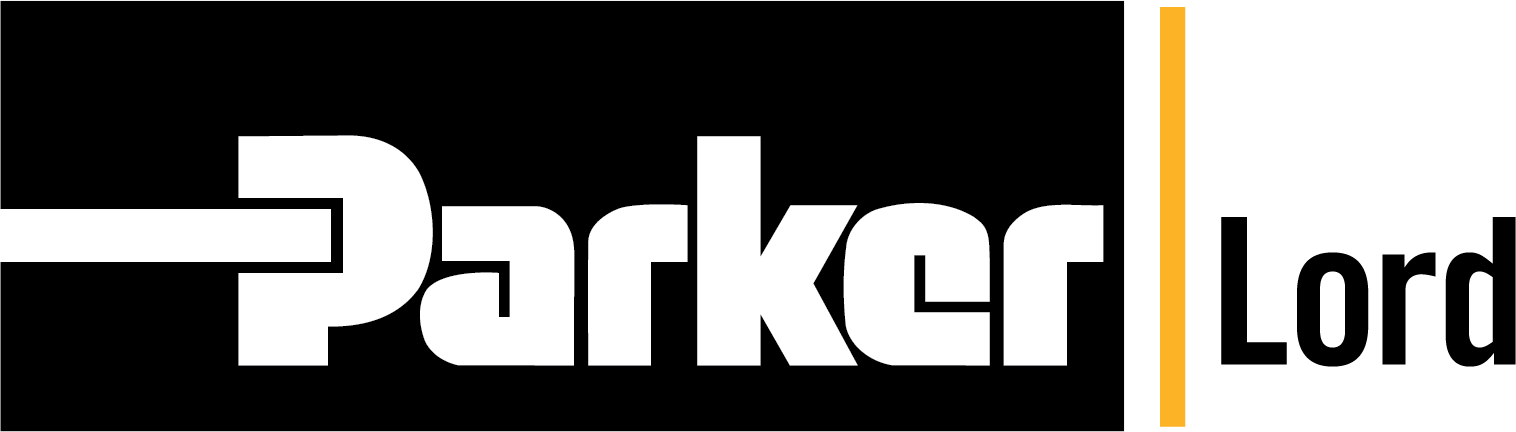
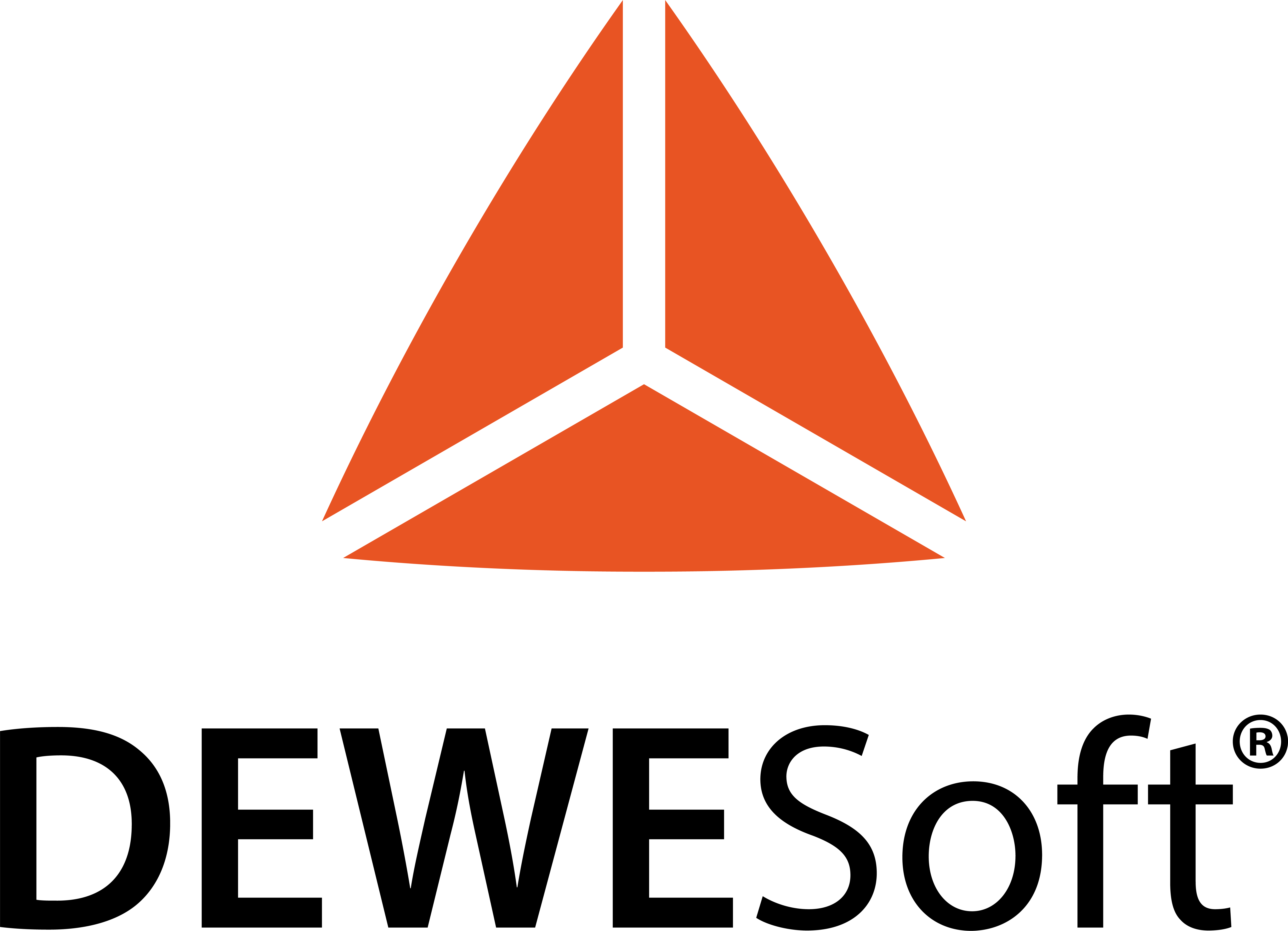
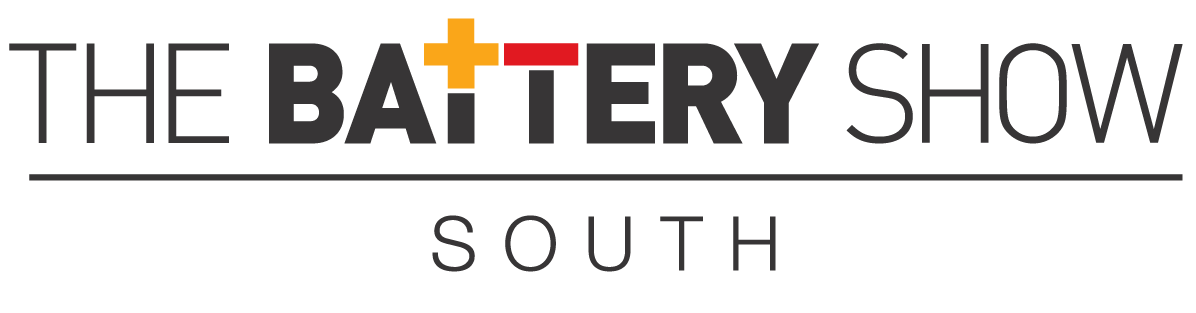
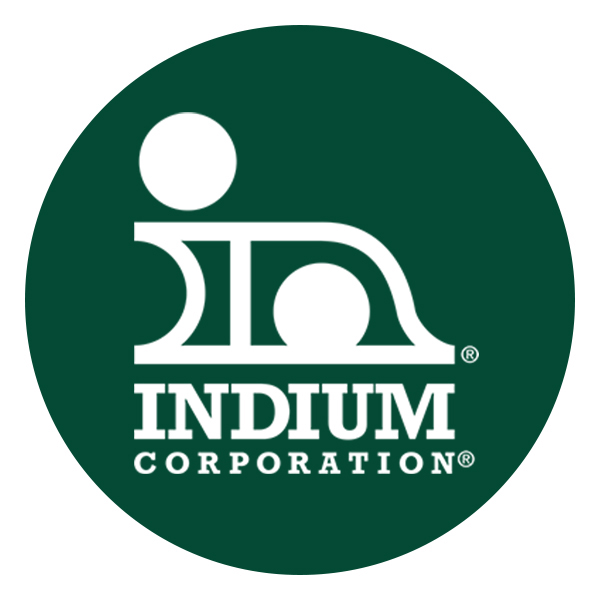
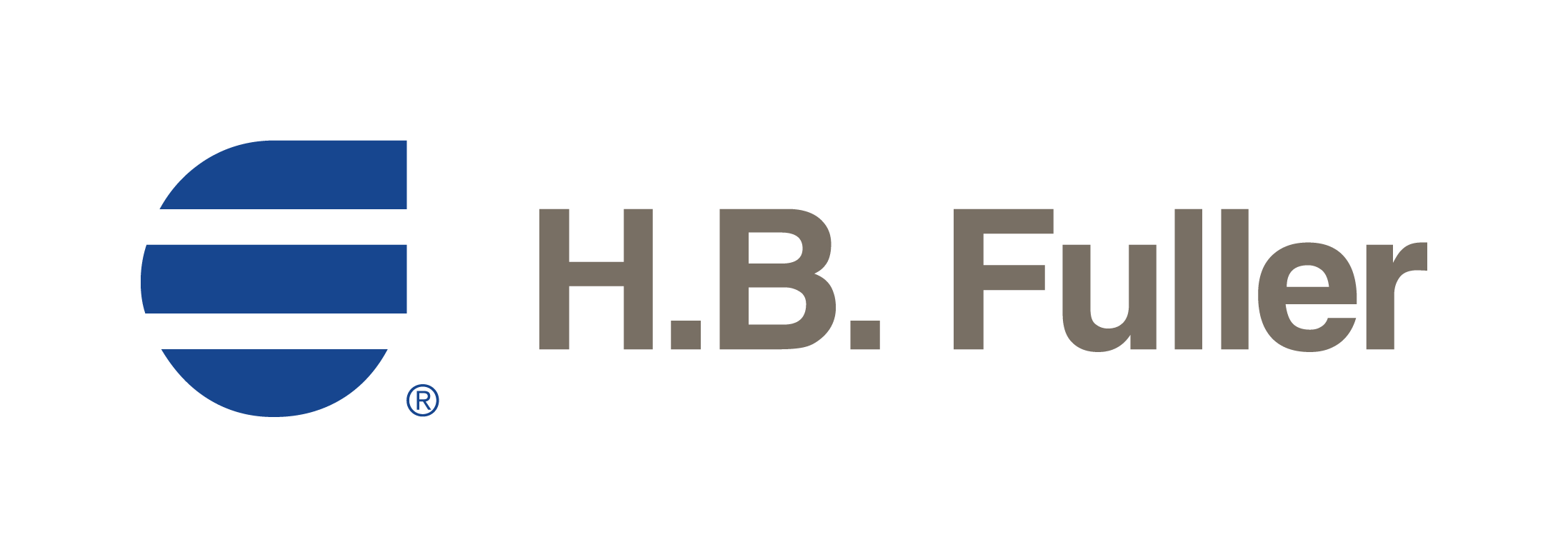