Tropos Motors ABLE-XR
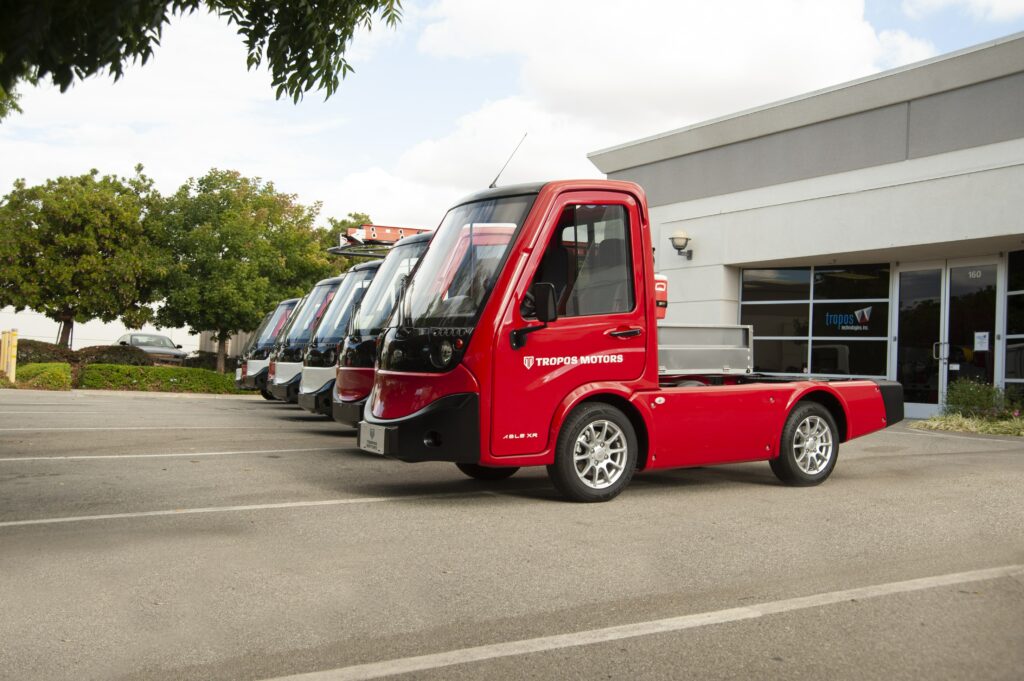
Eyes on the size
Matching the size of vehicle to the size of job was the inspiration behind developing this utility vehicle. Rory Jackson reports.
The ABLE-XR from Tropos Motors is an electric compact utility vehicle (eCUV) designed for carrying loads over short distances, for delivery applications that would normally be reserved for low-speed trucks. This battery-electric two-seater truck was originally conceived and developed by SITL-Brandt Motors, an automotive manufacturer based in Lyon, France.
In 2014, SITL-Brandt and its IP were bought by Cenntro Motors, a Nevada-based developer of all-electric vehicles. California-based Tropos Technologies supported Cenntro’s efforts to develop the truck further, and the design eventually matured into the ABLE series of eCUVs now being produced by Tropos Motors (an electric automotive subsidiary of Tropos Technologies).
Much of the impetus behind developing the ABLE series came from Tropos Motors’ founder and CEO John Bautista, who had spotted a key emerging market for all-electric vehicles around that time.
As he explains, “Rather than buying a full-sized petrol or diesel truck to do jobs that don’t actually require that much capability or capacity – or buying a modified golf cart or utility task vehicle that would be fine for some jobs but too small for others – you can do it with a vehicle that’s sized appropriately for the job.”
The ABLE-XR is the latest in the series. It is powered primarily by a 26 kWh lithium-ion battery pack, which enables a maximum range of up to 257 km (160 miles) – four times that of the typical ABLE-series vehicles and close to three times more than many typical eCUVs.
The vehicle measures 3.81 m long, 1.905 m tall, and 1.4 m wide, and is currently rated to carry up to 2000 lb (907 kg) in private grounds or facilities, although for legal reasons it is limited to 1100 lb (499 kg) on US public roads, or 565 kg in the EU.
If the XR is carrying a full load, the extent to which its maximum range is reduced depends on how much acceleration and hill-climbing is undertaken (as the energy consumed by these tasks is affected more by the payload than the job of sustaining constant speed). On average, the effect might be a reduction of 20-30% in range if working at payload capacity.
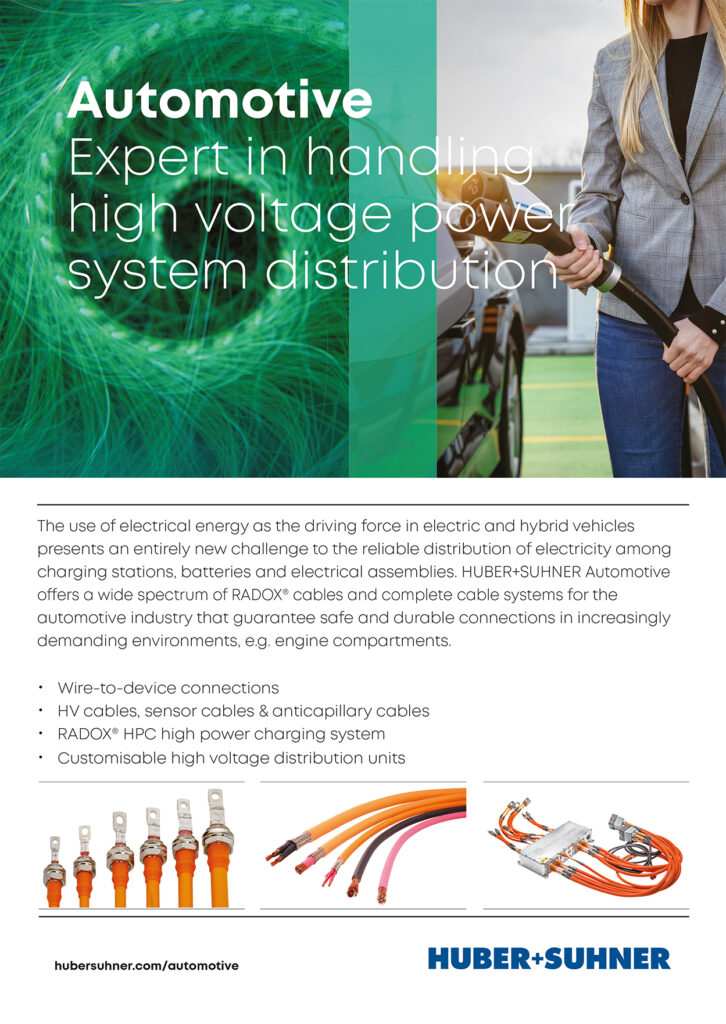
“Having a 26 kWh pack gives five hours of drive time at 40 kph,” Bautista notes. “And that amount of energy means you can carry loads that are close to the maximum vehicle weight ratings as defined by US and EU road authorities, and still transport them smoothly through even the most challenging uphill routes and driving conditions.
“Most eCUVs offer maybe 96 km of range at best, and if you factor in some road incline, cold weather and a 500 kg load, say, that range drops to between 30 and 50 km or less very quickly. That doesn’t make much commercial sense, yet we can probably still achieve at least 207-232 km.”
The ABLE-XR is based on the company’s ABLE-ST electric truck, which is the prior vehicle to the XR, although the XR improves on the ST’s maximum range of 193 km. And feeling that many electric vehicle manufacturers use heavy and poorly balanced chassis that were designed originally for fuel engines, Tropos has used a combination of CFD and CAD software to design and simulate a chassis structure that is lighter, more modular and better balanced than other offerings.
Much of the interest in the XR is coming from companies operating last-mile delivery vehicles, and public fleets ferrying engineers and equipment for municipality work such as fixing street lights and changing refuse containers. To that end, it is also fitted with safety features such as ABS brakes and can be configured for left- or right-hand driving.
Energy storage

Although the onboard energy storage for traction is fixed at 26 kWh, two different battery types are available.
The standard option is a lithium-ion battery (specifically NMC chemistry). “We typically offer a five-year warranty on the battery, but our trials and use cases have indicated a high likelihood of the battery lasting up to 10 years, which means replacing them only once or twice over the 20-year or more lifespan of the XR,” Bautista says.
“And even as you approach the end of a battery’s life, with maybe 25% of energy storage and vehicle range having been lost due to degradation of the cathode, we’ve found that you can still get 175-185 km out of the nominal 257 km, which is plenty for the XR’s applications.”
Beneath the payload bed, the NMC batteries are split into two 13 kWh, 96 V packs, one near the rear of the vehicle and the other about 1.5 m further forward, behind the XR’s cabin. This aspect of the design is due to space management throughout the chassis, and because the engineering team could not fit all 26 kWh worth of cells into their normal in-house battery box, so two smaller boxes were used rather than one bigger one.
“It also offers a convenient route towards offering a 13 kWh version of the XR, for users looking at below-average journey lengths and payloads,” says Bautista.
Each battery pack has a nominal voltage of 86.4 V, a rated capacity of 150 Ah, a rated operating discharge current of 140 A, and weighs about 118 kg.
As an alternative to the NMC packs, end-users can opt for an absorbent glass mat (AGM) battery, which has been chosen for its low maintenance requirements and safety relative to typical flooded-cell lead-acid types.
“Although our vehicles are designed for very high torque, the amount of current needed by the drivetrain is not high, so the limitations on current delivery that AGM batteries are typically subject to don’t pose an issue,” Bautista says.
“AGMs are quite a bit safer than flooded cells, which tend to continually release hydrogen gas, which builds up and can then of course explode in the event of an accidental spark.”
NMC batteries are lighter and take up less volume in the vehicle than AGM types, and typically deliver higher current (if needed); their expected lifespan also tends to be up to six times that of AGM batteries. However, AGMs may still be preferable for users seeking to lower their initial cost of investment, given that they are far cheaper to produce than lithium-ion batteries.

As Bautista explains, “For the XR’s most common end-users – those delivering supplies around closed campuses and other private facilities – the initial cost is generally a much more important factor than the running or operating costs. While the weight of an AGM battery of equivalent energy content is about three times that of the lithium version, and the AGM battery takes up about three times more space, the cost of lithium is still about three times that of AGM.”
The XR’s onboard charger is a 3 kW system that operates at 220 V AC. This is the most powerful onboard charger the company has used to date, and is a step-change from the 1.5 kW inverter on the ST model. As a result, both vehicles reach a full charge after about six to eight hours on a Level Two 120 V AC socket.
“We want to ensure our charging is kept as simple as possible, by plugging into a wall socket, without needing specialised charging infrastructure,” Bautista adds.
The power from the charger is regulated by a battery control box that sits between the cabin and the forward battery pack. The control box contains the switching electronics, enabling either battery to be isolated if there is a problem with it. The battery management system (BMS) and power comms processor are also integrated.
The BMS serves mainly to feed battery information via CAN bus to a display inside the cabin, with most of the XR’s powertrain control coming from a controller unit located behind the forward battery pack and in front of the traction motor. The BMS measures all the cell groups in each pack – their state of charge, the current being consumed, and monitoring for faults that would disable the vehicle for safety reasons.
Cabin systems
Aside from the two 13 kWh packs, the battery control box has another feed connected to a separate onboard battery, which supplies power to the various cabin systems.
This feed uses a DC-DC converter to step the voltage from 30-100 V down to 12 V for the cabin battery, as all the cabin’s electronics are 12 V systems. These include the cabin heater, air conditioning, dashboard lights, windshield wipers and defroster, and Bluetooth systems.
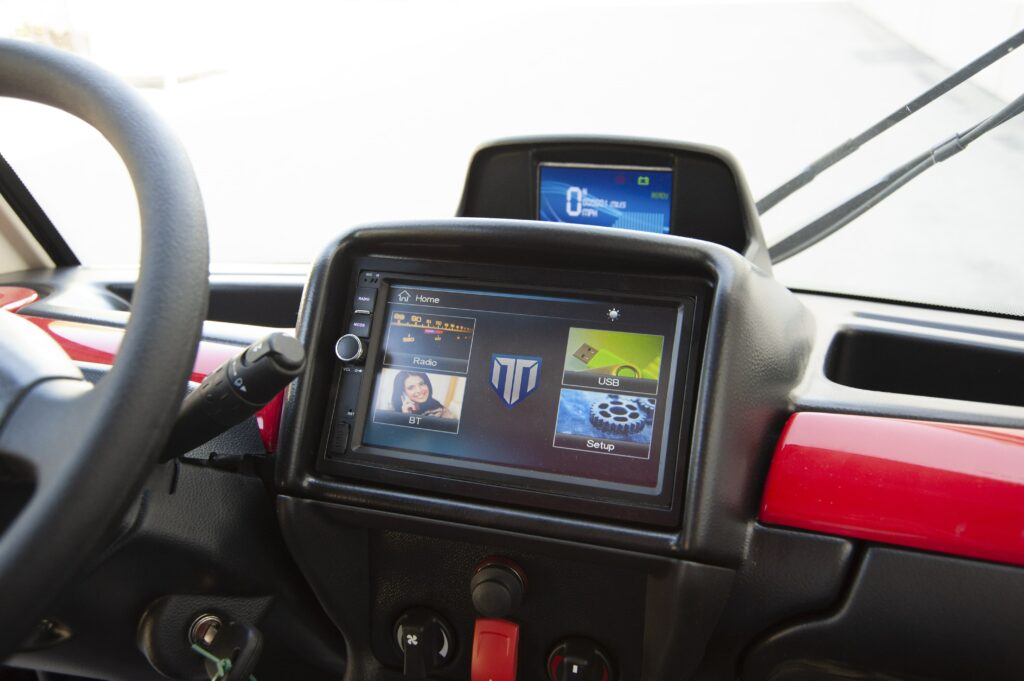
“The extra battery’s there because of the DC-DC,” Bautista says. “If you have a battery, you can get away with a lower current-carrying capacity for that power converter, so you don’t have to find a DC-DC with a high amperage because the battery provides that necessary current.”
The cabin battery has a maximum output current of 50 A, is protected in an IP67-rated enclosure, and kept within an operating temperature range of -40 to +60 C.
Motor and drivetrain
The company has opted to use a single-motor drive system, rather than a dual-drive set-up which would see each of the two rear wheels being driven by its own, less powerful motor. By extension, each motor needs its own controller.
As Bautista explains, “Down the years I’ve noticed that the cost of building an electric motor doesn’t change much, regardless of whether it’s 2-4 kW up to 10, 15, maybe even 20 kW. Most of that cost is in the machining process – making the endplates, the stator and so on. It just scales up, so most of the actual machining and assembly work is about the same in that broad range, so for the XR, I figured: why not go for one bigger motor rather than two smaller ones?”
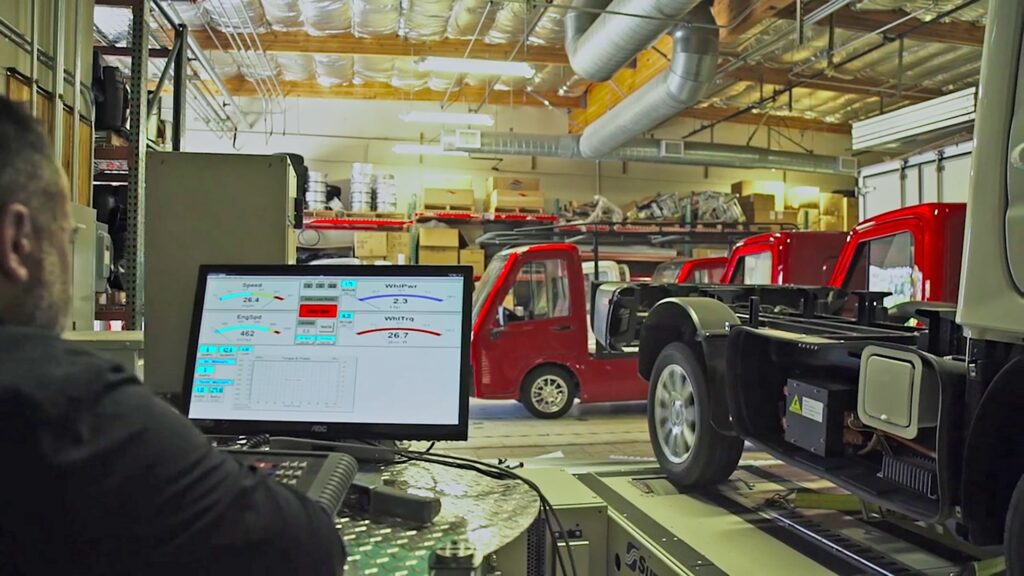
The motor is a permanent magnet AC type, with 10 kW (13 hp) of traction produced at normal operation, up to a peak of 18 kW (24 hp). The design is centred on a radial flux configuration, with an internal rotor, an external stator and four pole pairs.
Its operating voltage is 72 V (up to a maximum of 96 V) and it has a top speed of 3000 rpm, although it is rated to 2500 rpm (and 167 Hz) for normal operation. The system has a maximum current draw of 400 A, and produces up to 120 Nm of torque.
The traction motor consumes an average of 315 W/mile (197 W/km) when carrying a 650 lb (295 kg) payload. That performance figure was revealed during a trial of the XR alongside two electric vehicles in use on the campus of a university in California.
“The vehicles were carrying the same loads and driving up to their maximum speeds, over a very uneven route; the university’s two vehicles used 458 and 600 W/mile,” Bautista recalls.
“There are higher-end motors for even greater energy efficiency, and higher-grade components, but with the extra cost they’d add, I don’t know that our end-users would derive extra value out of them in the medium to long term.”
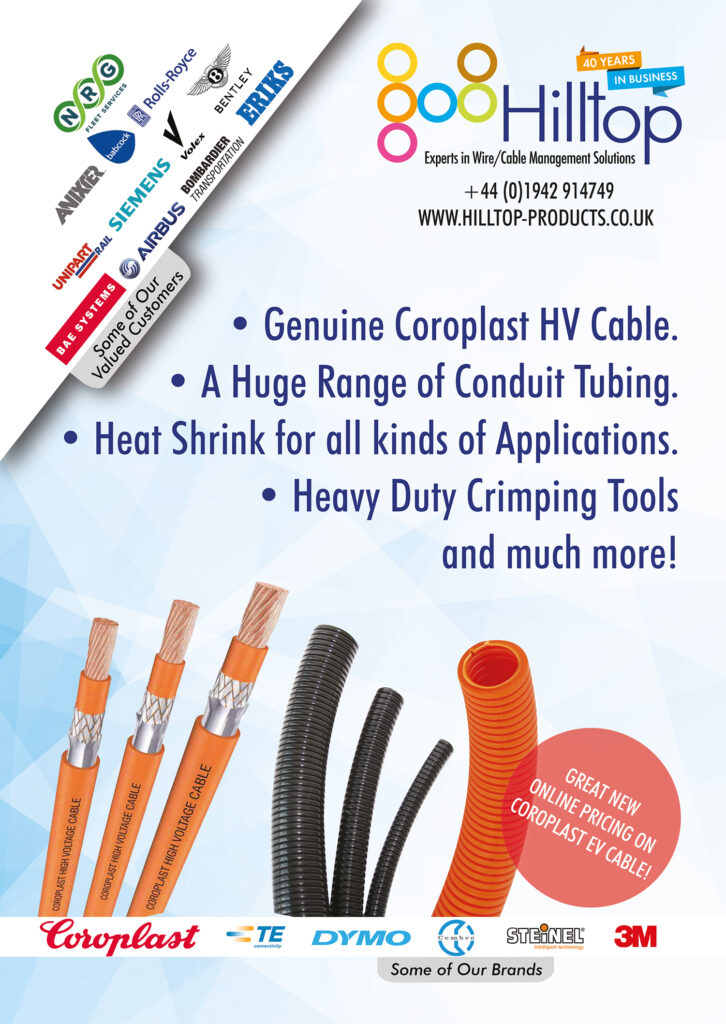
The motor assembly is largely automated, for mechanical consistency and to keep the air gap tolerances as tight as possible. The same supplier provides the XR’s differential, and neither has suffered a failure so far.
“It’s the same with the inverter and motor controller,” Bautista adds. “The only issues we’ve had with that have been software-related, so they were easily solved. I’ve always seen higher consistency and efficiency from a complete drivetrain system, with all the parts designed by one supplier to match each other and work together.”
The size of motor and the operating voltage were selected to provide the torque – up to 1020 Nm at the rear wheels – for the XR’s anticipated duties. The operating voltage has been kept to less than 100 V for safety reasons and because increases in voltage would only increase motor speed, which is irrelevant to the XR’s intended use.
“We’re also testing a 48 V drive motor now,” Bautista comments. “We’ve been able to run it on our dyno to up to 96 kph, which is quite fast for a 48 V system.
“It’s largely a question of being able to produce a good peak torque that, coupled with our gear reduction – which is a limited-split style differential with an 8.5:1 drive ratio – will give the kind of operation in any range of speeds that users need it to operate in. It doesn’t do any good to produce a huge amount of torque but to only have that just off zero rpm and then have it diminish rapidly after that. Or have it give very little torque just off zero rpm and have it peak somewhere else along the curve that’s not practical. We’ve seen both of these happen in electric motors before.”
The motor uses direct torque control (DTC) to target particular levels of torque starting at zero rpm and above. “When you don’t need as much torque but you do need more horsepower, such as travelling to a pick-up location at short notice, you need more power to sustain speed,” Bautista says.
The XR’s suspension is a transverse leaf spring arrangement at the front and torsion beam at the rear. “The rear suspension has added lateral shock absorbers, and was chosen for compactness, to keep the suspension from encroaching into the cargo space,” Bautista notes.
“The front suspension configuration was similarly chosen for compactness as well as reduced weight and cost compared with the alternatives out there.
“For example, a Macpherson strut would have been much taller, and would have interfered with the seating platform, while a double A-arm suspension would have added more parts and thus more complexity, manufacturing cost and weight.”
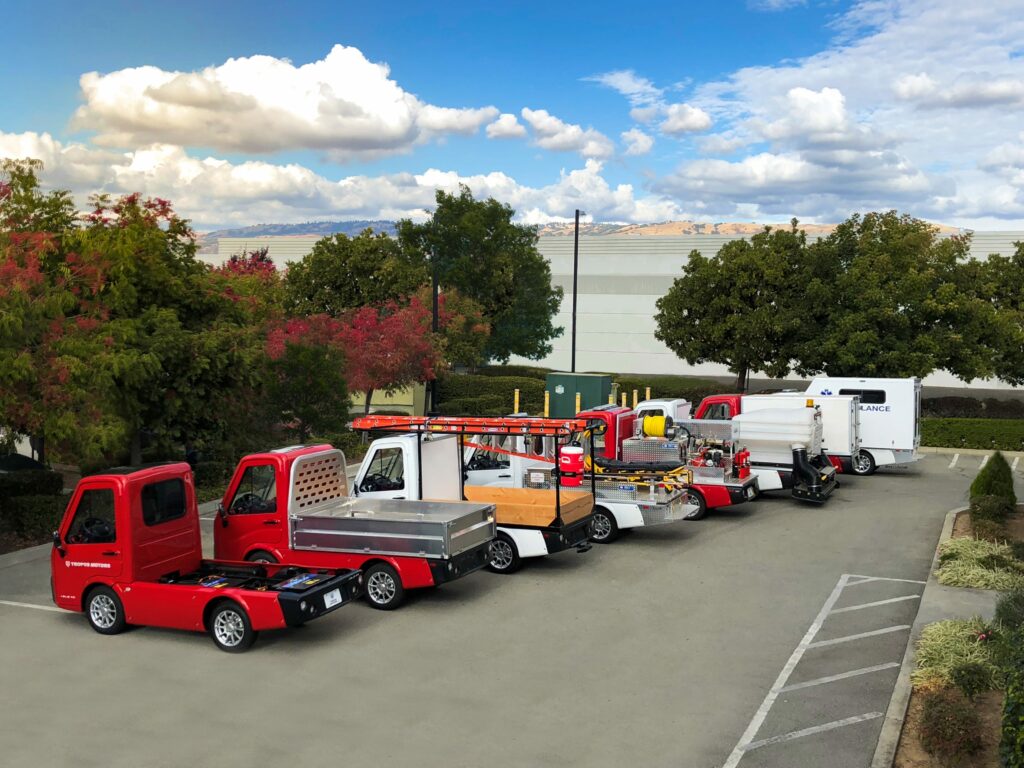
Thermal management
Most of the XR’s customers will be operating the vehicle on public roads, where their payloads will be capped at 499 kg and their speeds limited to 35 mph (56 kph).
That means its powertrain will not usually operate under heavy current loads, even when driving uphill. It can carry a small payload going up a small hill while drawing 200 A, or it can carry the maximum payload on a relatively flat surface and still use 200 A.
With so little current needed relative to most EVs, the XR’s components do not produce a level of heat that would require a lot of cooling or a particularly complex thermal management system. “We can get away with air cooling our motor,” Bautista says.
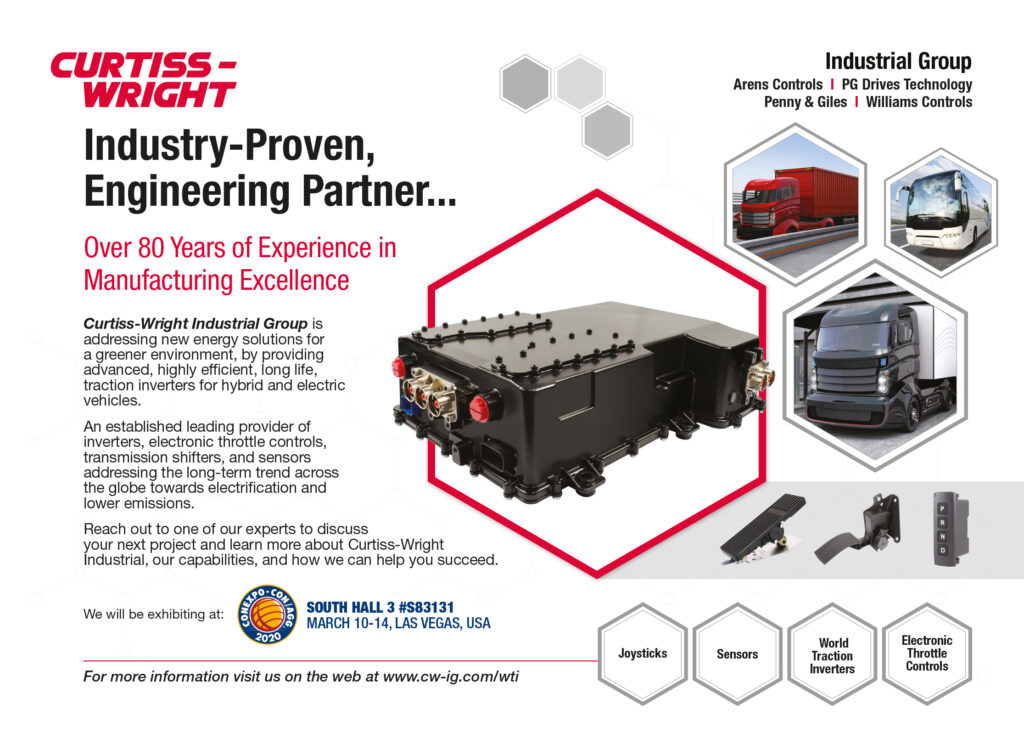
“The motor casing has aluminium fins, with a similar sort of heat sink on the controller, and both have forced-air fans for when extra cooling is needed. The battery packs have thermal interface materials to dissipate their heat to the outer casings, and that’s it.”
That keeps the XR’s lithium/NMC batteries within their optimal operating temperature range of -20 to +60 C. Similarly, for the AGM batteries, the optimal operating temperature levels are maintained at between -15 and +50 C.
Payloads
For most XR operators working in municipal duties and last-mile deliveries, there are currently three general options for payload bed packages. The ABLE Cargo is a box that has 3.5 m3 of internal storage and is built using a combination of aluminium and honeycomb fibreglass.
It has rear-hinged swing double doors, and another kerbside hinged swing door, with stainless steel door latches and hinges. All the doors are fully gasketed, and all the seams have been caulked and sealed.
The second option is the ABLE Pickup, an open bed with just under 3 m2 of space. The structure is all-aluminium, with three drop-down sides and corrugated flooring for extra loadbearing strength.
Third is the ABLE Trades, which consists of a frame made from aluminium, honeycomb fibreglass and wood. It is designed for carrying utility work equipment such as ladders or electric tools.
With similar dimensions to the ABLE Pickup, the Trades package also comes with a specialised safety beacon mount for warning oncoming cars or cyclists to keep their distance, in case of work being conducted on a road or streetlights for example.
In addition to these payload options, Tropos is also developing a range of others for whatever users might want. For example, the XR has been customised for fire response, medical services, refuse disposal, street sweeping and as mobile beer dispensaries.

The Cargo, Pickup and Trades options are designed to fit the Tropos Easy-Swap architecture, which enables the XR to change from one-bed package to another using just a flathead screwdriver and a 19 mm wrench.
Changeovers take a maximum of 30 minutes, and the basic packages with the Easy-Swap architecture can be swapped in less than 10 minutes.
The future
Given that the XR’s missions are largely uncomplicated delivery routes, Tropos has fitted the vehicle with drive-by-wire controls in order to make it autonomous-ready for end-users who would prefer eventually to automate its operation, for reducing the burden on the driver or enabling them to focus on other tasks.
The control configuration includes steering actuation, braking actuation and the aforementioned CAN interface with the vehicle controller for changing direction, speed and so on.
Development of the drive-by-wire architecture began about a year ago, with a particular focus going into the steering wheel position sensing. However, the company itself has not developed any AI or autonomy, instead opting to leave it up to end-users as to what manner or choices of algorithms and awareness sensors they would choose for their XRs.
“If a user wants to install an AI stack and sensor architecture, they just need to apply it to our vehicle, and the XR will respond to the commands as programmed in their algorithms,” Bautista says.
Further projects aimed at optimising the connectivity and performance of the XR (and Tropos’ other right-sizing vehicles) are being developed through a partnership with Panasonic. That tie-up was announced in May earlier this year, although further details could not be disclosed at the time of writing.
ONLINE PARTNERS
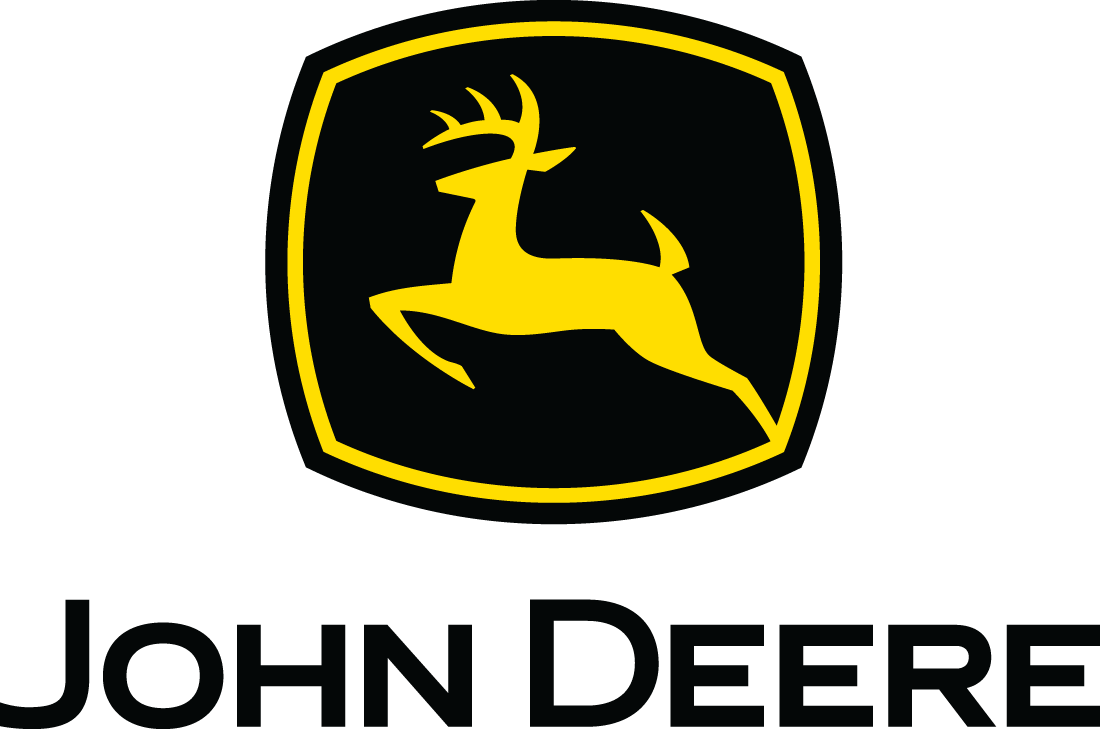
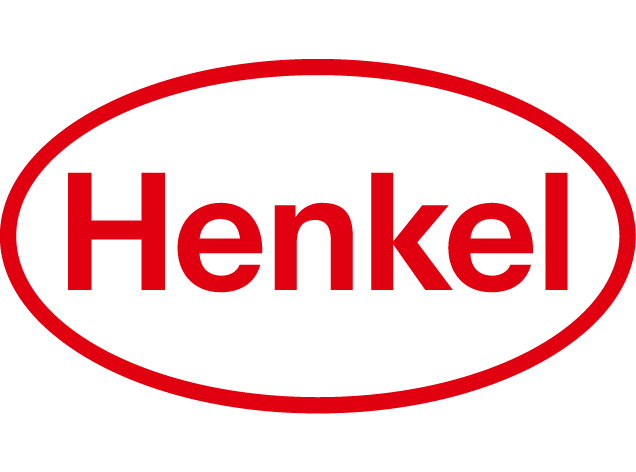
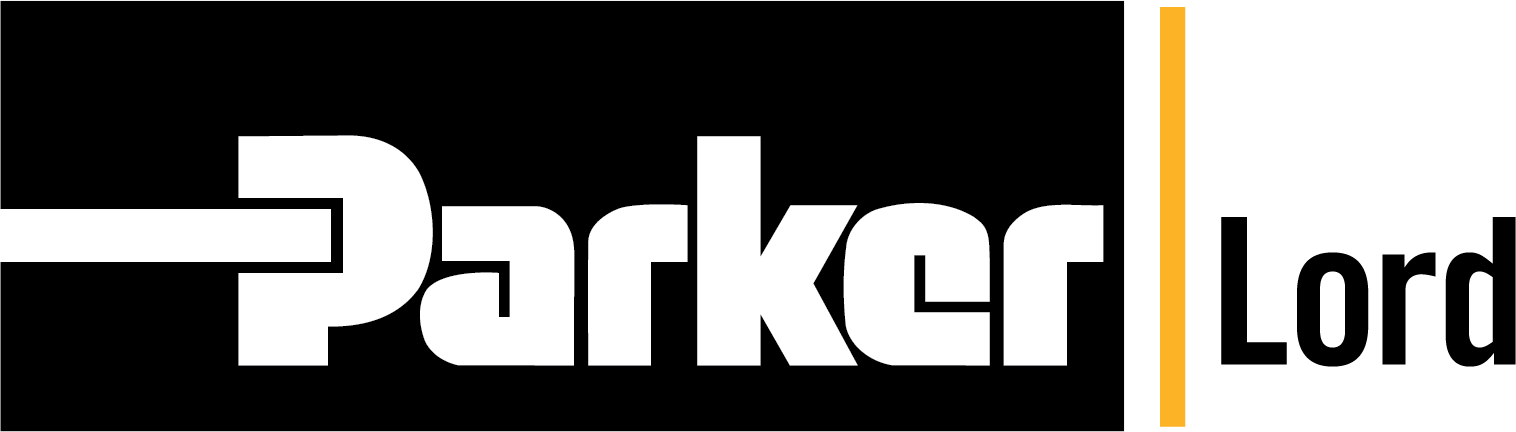
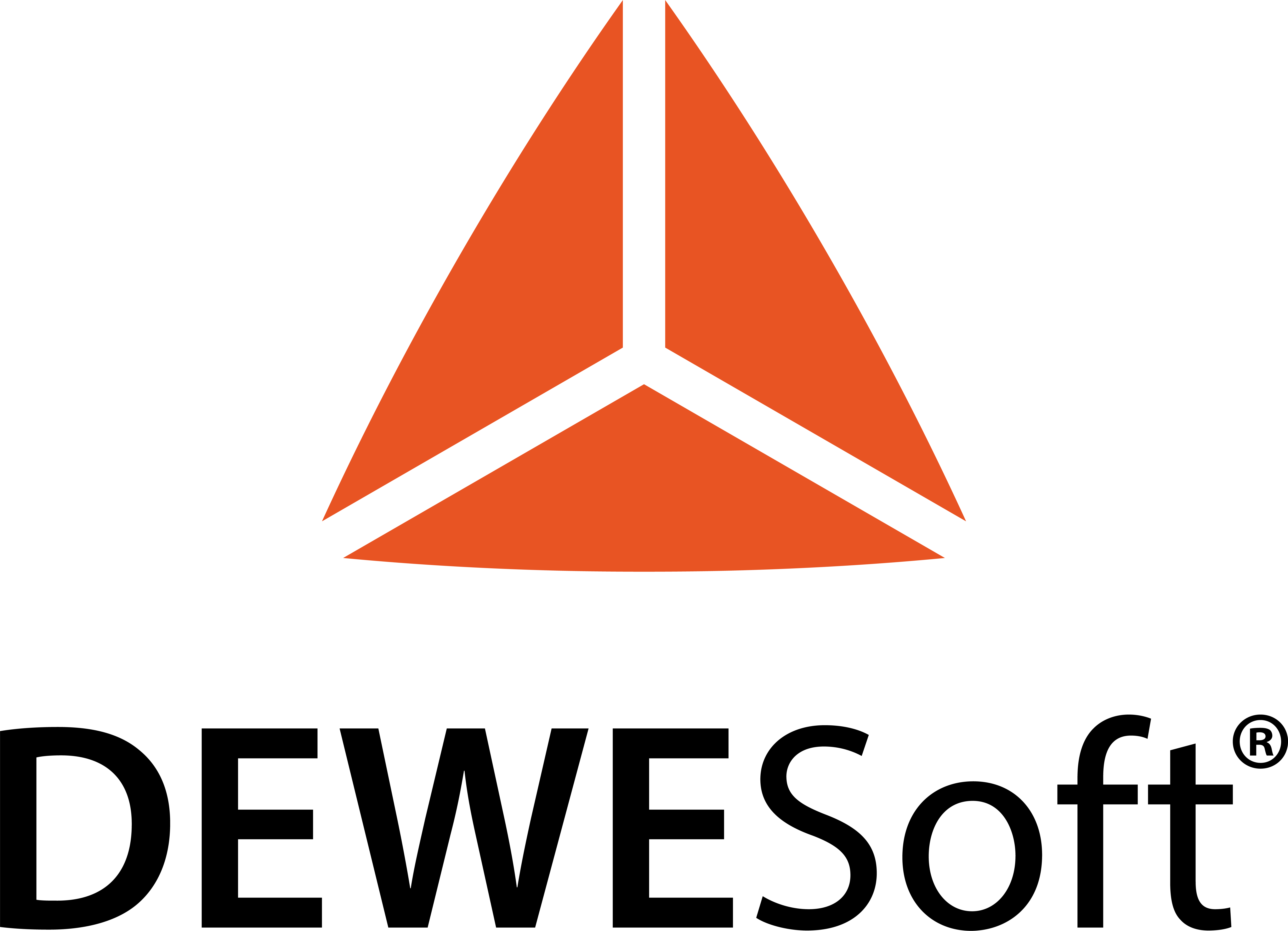
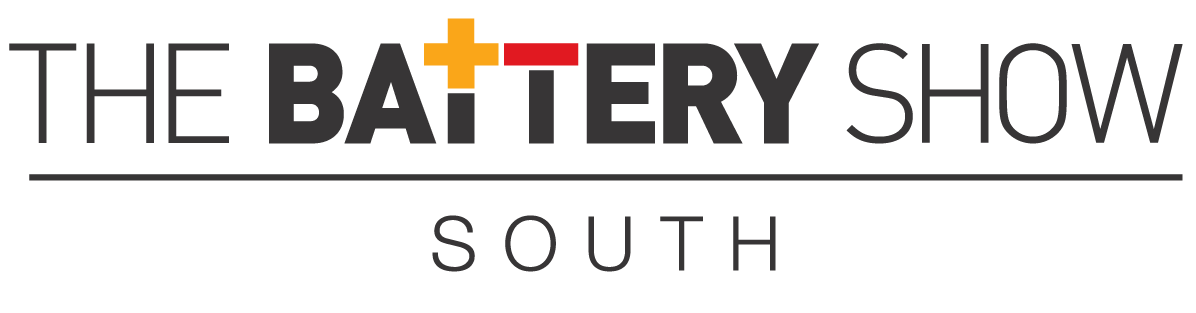
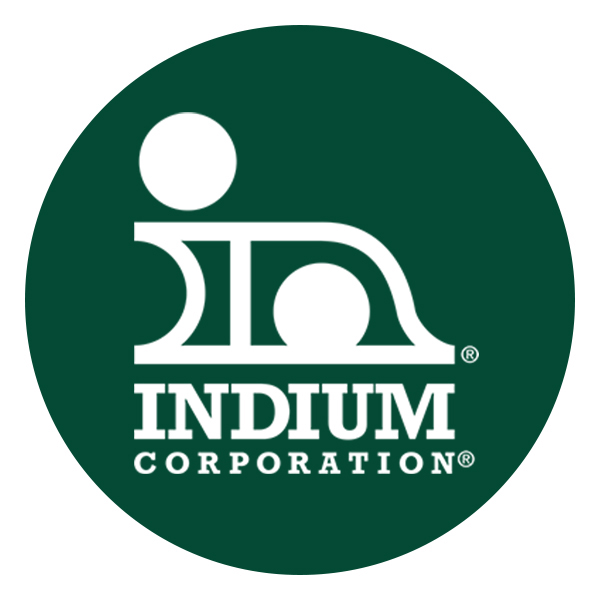
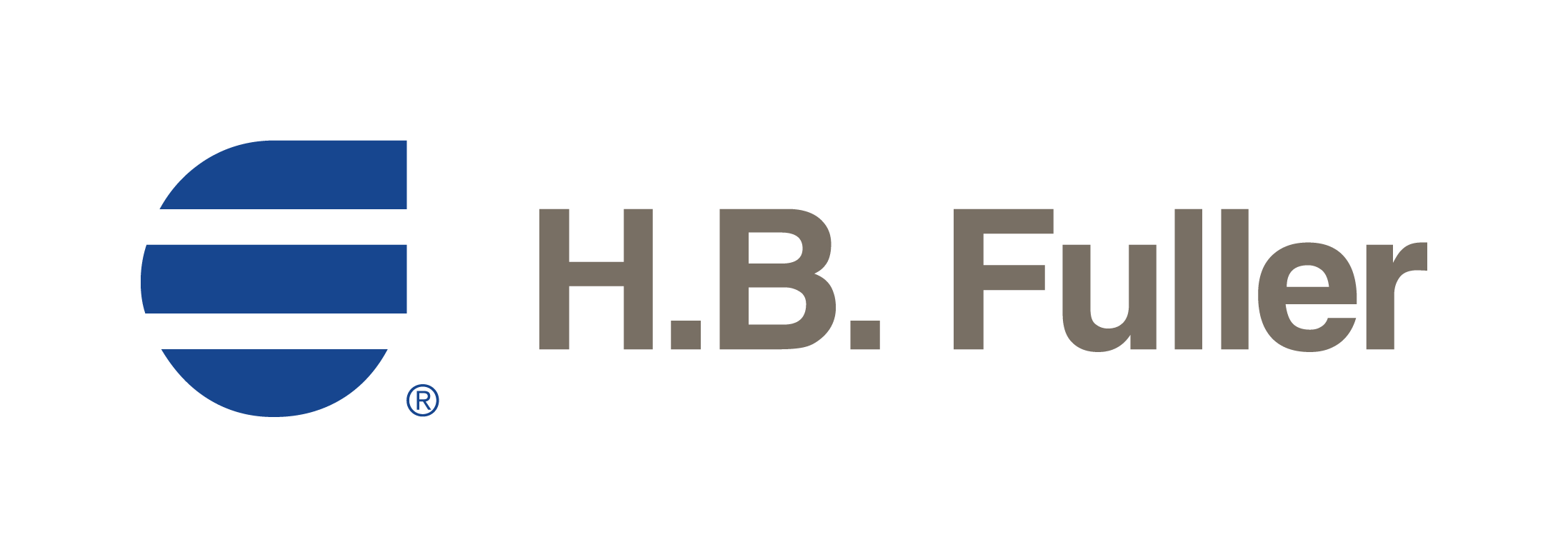