EV dynamics
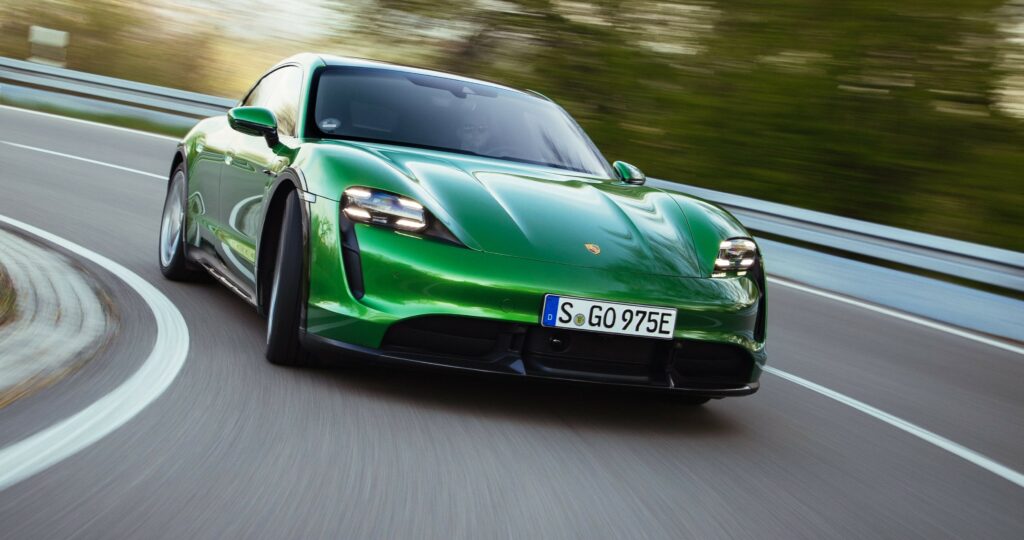
(Courtesy of Porsche Engineering)
Moving targets
Peter Donaldson reports on the steps EV engineers take to optimise the dynamic behaviour of their designs
How a car moves in response to the forces acting on it is a fundamental determinant of safety, comfort, energy efficiency and driver engagement, and electrification of the powertrain profoundly affects that dynamic behaviour. This influence results from differences in the vehicle’s overall mass and its distribution, when compared with IC-engined vehicles, along with the speed and precision of response inherent in electrical machines.
That presents engineers with problems as well as opportunities that differ from those associated with IC-engined vehicles and vary between different categories of EVs. The latter are far from homogenous, and in passenger cars there are architectural differences between those powered by hybrid systems, by batteries alone, and fuel cells. Even among pure battery EVs, there are differences in mass distribution between those derived from IC-engined vehicles or that share platforms in a manufacturer’s product range, and clean-sheet designs.
Like any object that moves, a car will pivot in the x, y and z axes, in movements known as roll, pitch and yaw, and surge, sway and heave. In addition to the movement of the vehicle as a whole, the wheels and tyres move in relation to the body, around and along their own x, y and z axes under the influence of forces from the road below, the body above and the powertrain, brakes, steering and suspension.
Key parameters
Weight, and weight distribution, affects all of these things, and therefore the amount of grip the tyres can generate and the predictability of that grip, the key parameters being the centre of gravity (CoG), the roll centre and the polar moment of inertia. The CoG is the point at which the weight appears to act, so an object supported at that point would be in balance.
The roll centre is determined by suspension geometry, and is the point about which the vehicle rolls under cornering forces. The front and rear suspension both have roll centres, and a vehicle effectively rolls about the axis defined by the line that joins them. If the CoG is a long way above the roll centre, the car will have a greater tendency to roll in corners, because the distance between the two points is effectively a moment arm, or lever.
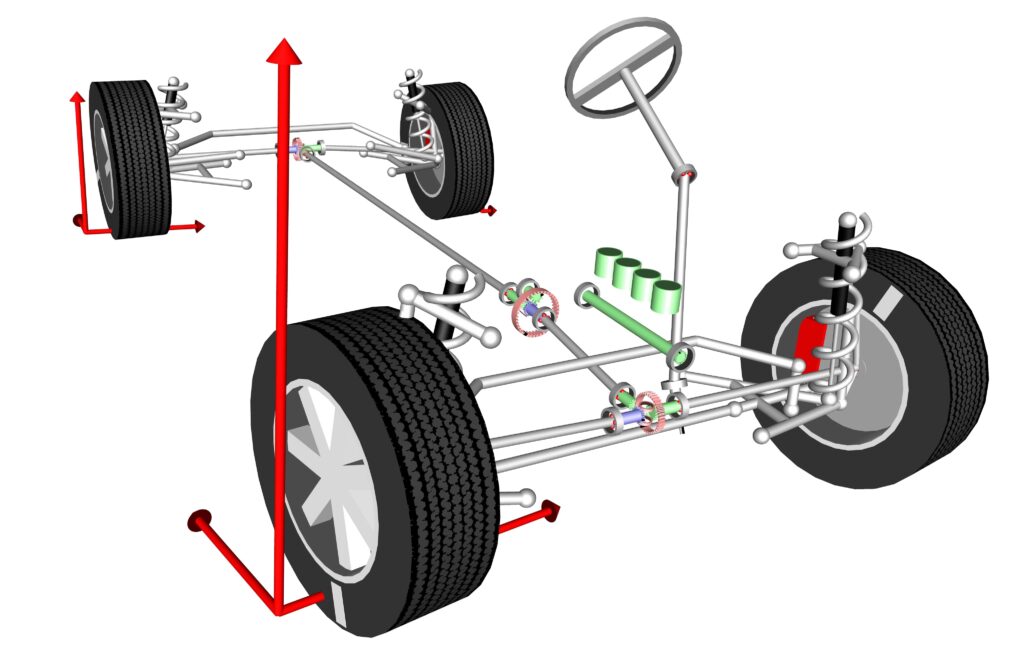
(Courtesy of Modelon)
Finally, the polar moment of inertia determines how quickly the car will accelerate in yaw, and it can be visualised with the aid of a dumbbell held in one hand. With the weights out at the ends of the bar, the polar moment of inertia is high and rotating the dumbbell by turning the wrist is difficult, but with the weights moved in towards the centre, the polar moment of inertia is lower and the dumbbell is much easier to turn.
According to Porsche Engineering, the CoG and the polar moment of inertia are two of the three most important criteria affecting an EV’s dynamic behaviour, the third being control of the drivetrain. The CoG tends to be lowest in battery EVs that use a skateboard-style architecture, while yaw inertia also tends to be low, as the largest mass – the battery – is concentrated in the centre of the vehicle.
“As most EVs use two electric machines, the control of the four-wheel drivetrain has a big influence on the dynamic behaviour,” says Martin Reichenecker, senior manager, chassis testing, at Porsche Engineering. “For both stability and handling, the linearity of the four-wheel drive [4WD] is important.”
Simulation specialist AVL notes that increased weight brings a need for better weight distribution. Lowering the CoG in relation to the roll centre, as a result of the battery’s layout and position, increases the car’s stability in roll, although the extra weight puts larger loads on the chassis components.
With the option to drive all four wheels independently, the company says, torque can be optimised at each one, and as the wheel torques are much higher in EVs than in comparable IC-engined vehicles, longitudinal acceleration tends to be much greater and spread over a wider speed range. That means other chassis components must be stronger to support the larger loads.
“Although they are not directly responsible for dynamic behaviour, regenerative systems such as brake/suspension energy recuperation need a trade-off between performance and recuperation, so the dynamics challenge is to optimise that trade-off,” AVL says.
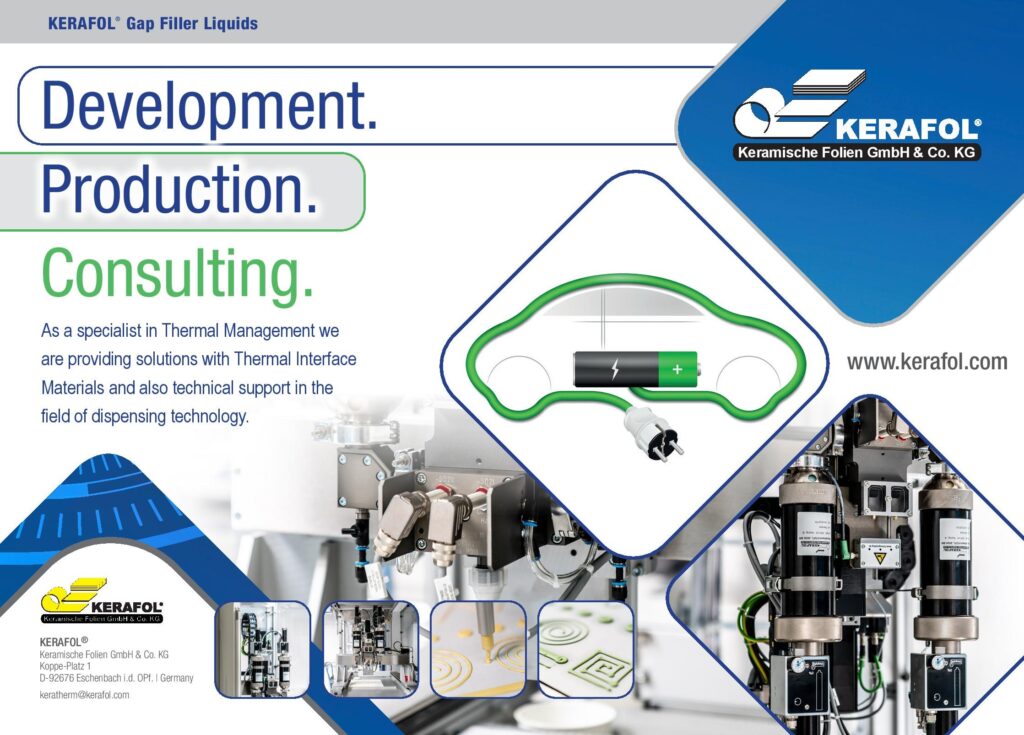
Piyush Karkare, director of global automotive solutions at Siemens Digital Industries Software, notes that the extra weight of the battery pack presents a challenge to ‘vertical dynamics’ – displacement and acceleration in heave. That affects comfort in particular, and drives different requirements for the tyres, particularly increased sidewall stiffness, and for the suspension in terms of spring and damper tuning.
He adds that traction control, along with control of suspension, brakes and steering, are all impacted significantly by the vehicle’s kerb weight and even more so by the distribution of both weight and propulsive power.
“Overall drivetrain performance and control strategies have a direct effect on the dynamics of EVs,” he says.
Peter Sundstrom, team leader for mechanics and vehicle dynamics at vehicle modelling specialist Modelon, agrees. He emphasises that as well as elevating family car acceleration to sportscar levels and pushing high-end EVs into supercar/hypercar territory, the rapid torque response available from electrical machines enables much more accurate slip control. That enhances traction and stability control and torque vectoring for further improvements in performance and active safety.
Sundstrom also highlights packaging differences, noting that electrical machines take up less space than an IC engine and its transmission and final drive components, and therefore provide more freedom to optimise suspension design. The active systems also have an impact in this area, he says, adding that the use of regenerative braking provides an opportunity to reduce the size of the components in the hydraulic braking system.
Mass distribution differences
When it comes to how much the nature of the drivetrain influences mass distribution by dictating where the major components must go, Sundstrom imagines a scale starting with IC-engined vehicles at the rigid end through hybrids and fuel cell EVs to battery EVs at the most flexible end. This is controlled by the size and weight of the components and the manner in which they are connected.
“With a combustion engine, you are pretty much locked down in terms of where you put your mass, but with a battery EV there is basically just cabling connecting them together, so you get more freedom to put the mass where you want it for the vehicle’s dynamic behaviour.”
Most IC vehicles are front-engined for convenience of packaging (mid- and rear-engined cars being a tiny minority) but in all cases the size, weight and cooling needs of the powerplant mean its position dominates the architecture of the car. The fuel tank, which is normally at the rear, is a mass that varies as it empties and is refilled, and that has to be accounted for, Siemens’ Karkare points out.
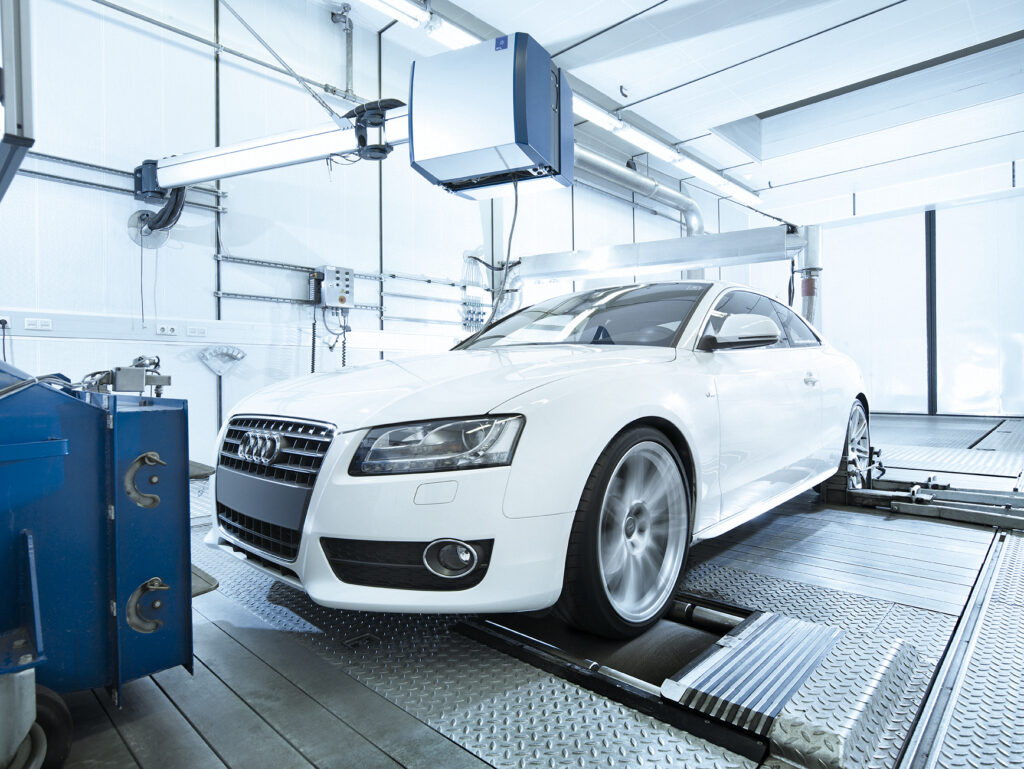
While hybrids must pack even more machinery into the available volume, there are differences among them in terms of mass distribution that stem from powertrain layout, according to AVL. Some place the additional weight of an electric motor between the IC engine and the gearbox, for example, while others use an e-axle at the rear and turn a front-wheel-drive IC car into a 4WD hybrid.
They also need space for the battery, usually within a vehicle architecture conceived for an IC engine, so the modules are usually fitted into the ‘transmission tunnel’ or in the rear compartment. Sometimes they are positioned above the CoG, Porsche Engineering notes, reducing agility and performance.
A series hybrid, however, is usually more like an EV fitted with a range extending generator than an IC-engined vehicle with electrical machines integrated into its powertrain. As the range extender is likely to be small and to deliver its power entirely electrically, there are more options for positioning it.
The layout and mass distribution of fuel cell EVs are similar to those of hybrids, in AVL’s view. Both need smaller batteries than battery EVs, and they are usually located behind the rear axle. Both also need fuel tanks, with a fuel cell EV needing to store hydrogen gas at high pressure, often just in front of the rear axle. Also, in a fuel cell EV the under-bonnet space is typically occupied by the fuel cell stack, power conversion electronics and the electric motor.
With battery EVs, the electric motor and simple transmission are outweighed – literally – by their massive battery packs, which makes them the heaviest category of all but at the same time brings the CoG lower and closer to the roll centre, shortening the effective moment arm and reducing the tendency to roll.
While battery EVs benefit from a lower CoG, their mass distribution is often oriented toward the rear because of the location of the battery and electric drivetrain components, Porsche Engineering says.
Clean-sheet advantage
Among battery EVs, there is a distinction between those based on a conventional IC-engine platforms (or one available in both IC and battery EV variants) and clean-sheet battery EV designs.
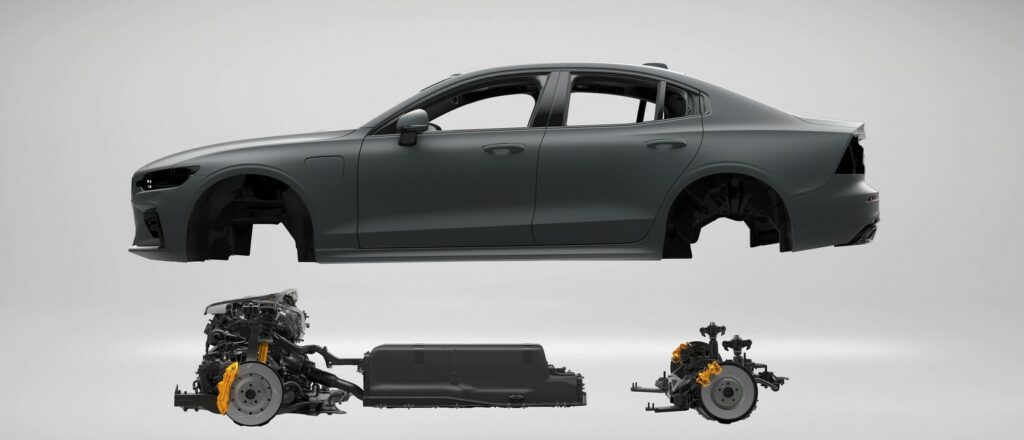
(Courtesy of Volvo)
“If you base an EV on a traditional platform, you tend to just place the motor where the IC engine was and the battery probably somewhere around where the fuel tank was,” says Sundstrom. “So you essentially get the same mass distribution but probably a heavier car.”
That is because battery EVs based on IC-engine layouts suffer from packaging obstacles owing to an architecture conceived for another powertrain concept,. The spaces left for the IC engine components such as exhaust systems are no longer fitted, causing difficulties in positioning batteries and e-axles because of complex underbody topology.
AVL says, “That means very expensive and complex battery layouts have to be adopted, and a massive variation of the CoG occurs, which moves further to the rear. If the e-motor then sits in the front and the battery mainly in the back, this causes a major limitation in performance.”
Typically, therefore, it is more common for IC-engined and hybrid vehicles to share platforms with battery EVs that increasingly are built on dedicated architectures. Karkare says, “Clean-sheet designs allow to engineers to package battery packs more optimally and permits better structural stability from both the vehicle dynamics and manufacturing perspectives.”
Unsurprisingly, clean-sheet designs offer the best opportunities to optimise a vehicle’s weight distribution and packaging with its dynamic performance in mind. As well as much greater freedom in positioning the heavy energy storage and drivetrain components, says Porsche Engineering, it also allows the design team to find the best chassis kinematic points.
Kinematics is the study of the motion of points, objects and groups of objects – suspension mechanisms, for example – in isolation from the motion’s causes. With the goal of keeping the tyres in contact with the ground as consistently as possible, it is essential to optimise the motions of the suspension linkages in the volume available.
The suspension pick-up points influence the geometry and orientation of basic components such as control arms and linkages that constrain the movement of the wheels. Pick-up points are therefore key kinematic points and must be located on nodes on the chassis; these are points that remain stationary as the chassis flexes and vibrates, which even the strongest and stiffest do to a degree.
In terms of the effect on handling, a 50/50 weight distribution is favourable but not mandatory for a well-balanced vehicle, according to Porsche Engineering. That is because the dimensions of the front and rear tyres can usually be adjusted to compensate for differences in load between the axles.
AVL agrees, adding that the best solution often emerges from considering the application and permissible additional load. Rear-biased distributions of 45/55 or even 40/60 might prove better for traction and agility in rear-wheel-drive sportscars in particular, enabling them to brake later on the approach to corners because the rear wheels lock later. Also, the load transfer from rear to front under braking can bring the distribution to 50/50 dynamically.
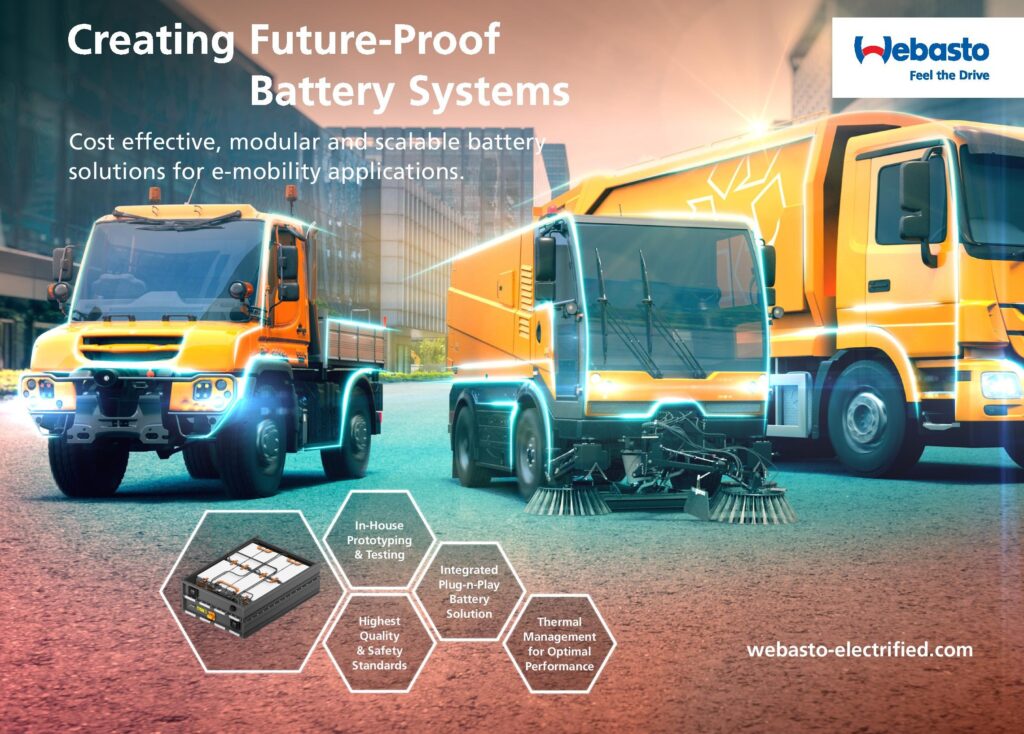
Load transfer
More important though than the distribution of load between axles, Porsche Engineering adds, is the fore/aft location of the large masses and the height of the CoG. With a low CoG and a centralised mass, there is less load transfer laterally across the vehicle when cornering, and that allows the car to make better use of the available grip to generate more lateral g-force, which translates into higher corner speeds.
The lower roll gradient allows softer anti-roll bars to be fitted, improving comfort, as do the reduced oscillations in pitch and roll in normal street driving. Also, inherently better agility and steering response permits a softer, more comfortable spring and damper set-up to be used without sacrificing performance.
The greater weight of an EV can be an advantage in terms of comfort, AVL points out, because the extra weight of the battery is supported by the springs, suspension, wheels and tyres. These are relatively light, leading to a higher sprung-to-unsprung mass ratio and a smoother ride, principally because it increases the separation between the natural frequencies at which the body and the tyre/wheel/suspension system oscillate.
Karkare adds, however, that greater weight also requires stiffer tyres, different shock absorber tuning and demands more from the braking system, which together can make the desired ride plushness and comfort a challenge to realise. Higher overall weight also puts greater demands on the tyres, which is an important safety consideration that impacts tyre performance specifications.
Apart from the flexibility to engineer in favourable weight distribution, eliminating the IC engine also brings the opportunity to improve crash safety, Sundstrom says, because the design of the crumple zones is not constrained by the large, rigid block of the engine in front of the driver.
Striking the right balance between handling, comfort and safety for passenger cars presents a number of engineering challenges; AVL points to the rearward shift in the CoG. In some front-wheel-drive (FWD) configurations, for example, this can present traction problems, particularly if the vehicle is fully loaded, which are exacerbated by the high torque and rapid torque response characteristic of electric motors.
This can also exacerbate tendencies towards torque steer in FWD cars. Adding a large battery to an EV derived from an IC engine platform also often results in a longer wheelbase and consequent larger turning circle, even in smaller vehicles.
AVL also says the rearward placement of a large battery pack can bring severe packaging problems in vehicles that use simpler rear suspension designs such as those based on a twist-beam axle, forcing a trade-off between battery capacity and range against the cost and complexity of a more compact suspension.
With multiple variables such as weight, driveline layout, CoG, tyres, spring/damper tuning and brake design, optimally balancing the lateral, longitudinal and vertical dynamics is a complex task, Karkare, emphasises, particularly when it comes to comfort. This is especially true for EVs, he says, as all these factors affect range.
“Range is one of the biggest differentiators between EVs,” says Sundstrom. “Most people who don’t want an EV are worried about range, so you need good numbers. The trade-off for that is that you need more battery capacity, and that makes the cars heavier and more expensive, which is the other worry people have.”
Packaging suspension
Differences in mass distribution affect the suspension designers approach to key parameters such as roll centres, pick-up points, geometry and spring/damper rates, anti-roll bar stiffness and wheel sizes, for example.
The biggest change in vehicle architecture is due to the 110-140 mm added in the vertical direction by the flat-floor battery, which also moves the steering wheel centre higher, AVL comments. EVs also tend to have larger diameter wheels and suspension top mounts that sit higher. In the longitudinal direction, the distance between the centre of the steering wheel and the centre of each front wheel tends to be shorter, making the cabin larger and the wheelbase longer compared with IC-engined vehicles of the same length.
To maximise space for the battery, AVL continues, the lower suspension link (also known as the comfort link) is oriented towards the front of the vehicle, and the steering rack is positioned in front of the axle rather than behind it.
“The generally lower centre of gravity needs to be reflected in the roll centre height as well, influencing the suspension’s hardpoint definition,” AVL says. “Also, in the rear the target is to maximise the space for the battery, so axle types that do not affect battery length tend to be chosen.”
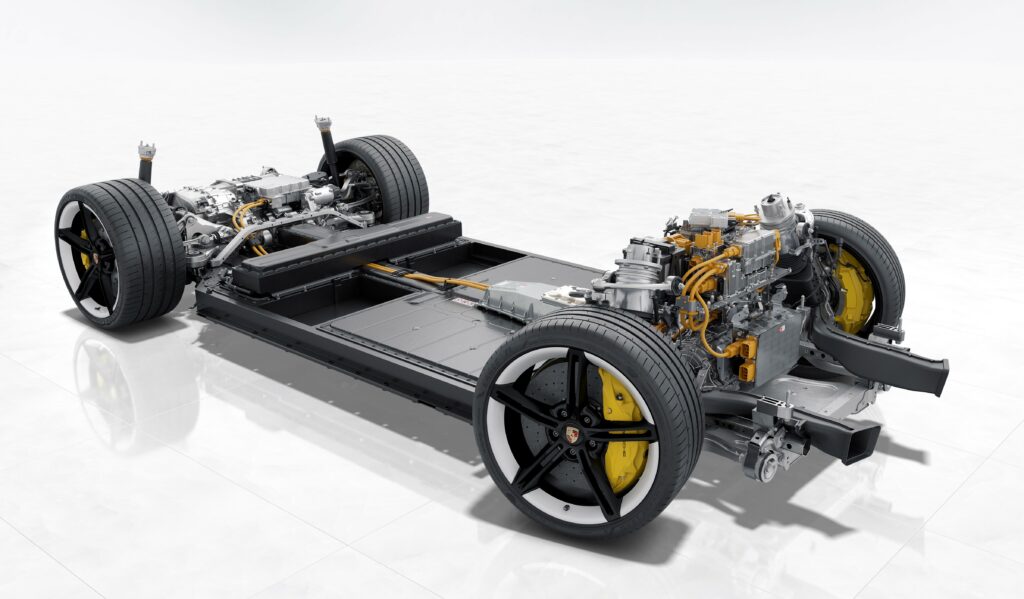
(Courtesy of Porsche Engineering)
Porsche Engineering emphasises that better boundary conditions such as a low CoG and low yaw inertia influence many factors. For example, spring rates, sway bar rates and damping ratios can be set lower than on a comparable vehicle with a higher CoG to achieve the same handling characteristics. Also, roll centres and anti-dive/anti squat geometry must be adapted to the lower CoG height, otherwise the vehicle could suffer extreme roll or pitch stiffness. “The remaining hardpoints are vehicle- and target-dependent, and not necessarily battery EV-dependent,” Reichenecker says.
To some extent, these advantages can compensate for the greater overall mass, which requires increased stiffness in the tyres and/or in terms of higher spring, damper and anti-roll bar rates to handle the extra weight and inertia, Karkare says. He adds that more compact EV driveline components offer designers more flexibility in the choice of suspension geometry and layout, as well as the points at which the suspension connects to the body in order to place the roll centre in the desired position and create the desired anti-squat and anti-dive characteristics.
“However, to maximise space for the battery pack, the tyres are pushed as far as possible into the vehicle’s corners,” he says. “Those limitations in packaging space can create additional challenges in achieving the desired suspension geometry.”
Skateboard pros and cons
The increasingly prominent skateboard architecture is close to ideal in terms of lowering the CoG, centralising mass and allowing maximum flexibility in suspension design. It also allows manufacturers to put any style or configuration of body (‘top hat’) on it, just as the ladder frame chassis did in the early days of the car.
Examples include Rivian, which offers a pick-up and an SUV on the same skateboard, and Tesla whose Model S and Model X also share a platform, Sundstrom says. “You have all this freedom to place the rest of the parts, seats and bodywork and so on where they make the most sense, because you have a flat floor inside the vehicle.”
This architecture allows for what Karkare calls “parallel but decoupled business models”, in which top hat innovations and skateboard innovations (in the battery and electric powertrain) can be decoupled, perhaps also shifting innovation costs onto skateboard suppliers.
However, the architecture also throws up some dynamic challenges, he cautions, principally in coupling the top hat to the skateboard in a way that achieves the desired overall static and dynamic stiffness targets, both in the low-frequency domain that affects driving dynamics and its high frequency counterpart that impacts noise, vibration and harshness.
Another, perhaps less than obvious potential limitation is in packaging efficiency and flexibility when it comes to differentiating products that share the platform, AVL says. If one fixed-design battery module is used, it’s likely that there won’t be a wide spread in track width among the vehicles built on a single platform, limiting seat position options in the lateral direction. More broadly, it makes it more difficult to optimise individual models, not only in terms of internal layout but also of driving dynamics.
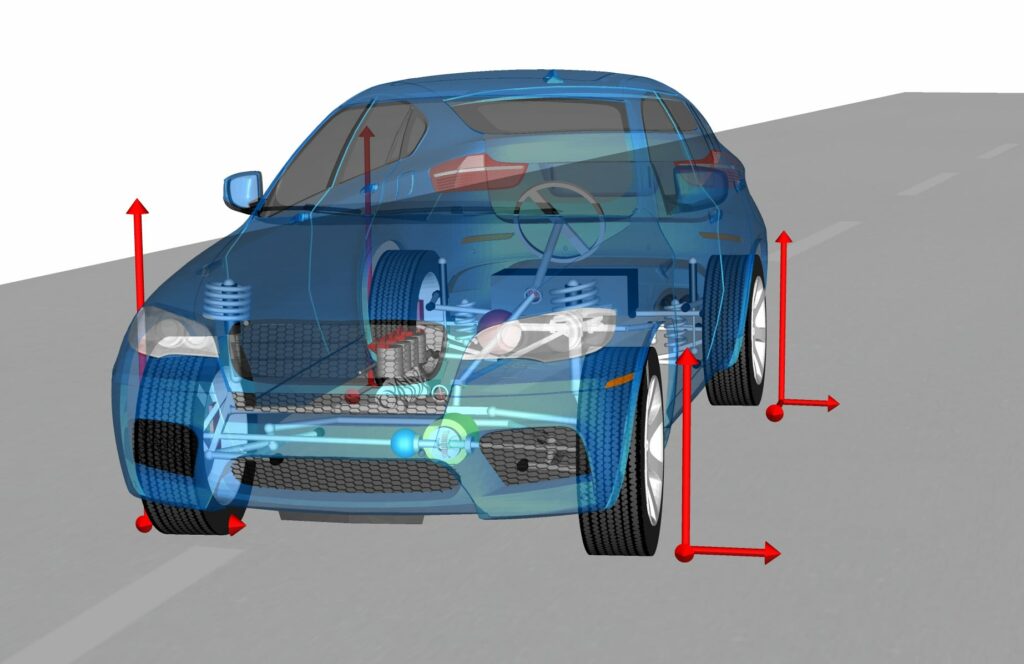
(Courtesy of Modelon)
Future directions
However, Porsche Engineering anticipates more development of different vehicle types, such as saloons/sedans, SUVs and crossovers, based on a common platform. “Different heights could be managed with different kinematic hardpoints, while the positions of electric motors and batteries can vary to achieve the best result for each vehicle type,” says Reichenecker.
As with all vehicles, the dynamic behaviours of EVs can be shaped and assessed virtually using design software, models and simulations, and Karkare expects virtualisation of the design process to increase. He also anticipates maximal use of data from tests and simulations to feed machine learning algorithms, with the aim of speeding up the development process.
He links this with growing centralisation of control systems, to which electrification lends itself. “Whereas at this stage there are multiple different active systems and controllers, this is expected to move to a ‘whole vehicle control’ concept,” he says.
It has been common practice to manage lateral and longitudinal dynamics separately, AVL notes. In contrast, new EV-related technologies need strong coupling of all degrees of freedom all the time and on all roads, particularly as advanced driver assistance systems (ADAS) become more common. The e-chassis as a ‘feature enabler’ has to be robust in all conditions, comfort-oriented in motion control, failsafe and energy saving, the company adds.
The large number of ADAS functions, each of which needs several actuators, leads to increased complexity, as well as greater overlap and interdependence between functions, says the company. The pay-off for that is higher levels of safety through redundancy. For example, the steering can be carried out using the normal steering components with a steer-by-brake (differential braking) system and with a steer-by-torque (torque vectoring) system, the latter two being fallback options for the first.
This high level of integration also enables energy efficiency and vehicle dynamics, which have traditionally been engineered separately, to be brought together. “Optimally distributing propulsive and brake torque allows a better trade-off,” says AVL.
Systems with multiple interdependencies are complex by definition, so computer simulations that can work through multiple combinations and permutations very rapidly are vital for optimising EV platforms that allow more design freedom.
“Simulations have been around for a long time,” Sundstrom says. “What is interesting now though is that we are getting new ways to use the models. Simulations allow you to explore a very wide design space compared with building physical prototypes, and if you apply these new optimisation methods and machine learning you can make that design space even wider and cover even more ground.”
With more design space and faster means of exploring it, EV capabilities can only grow.
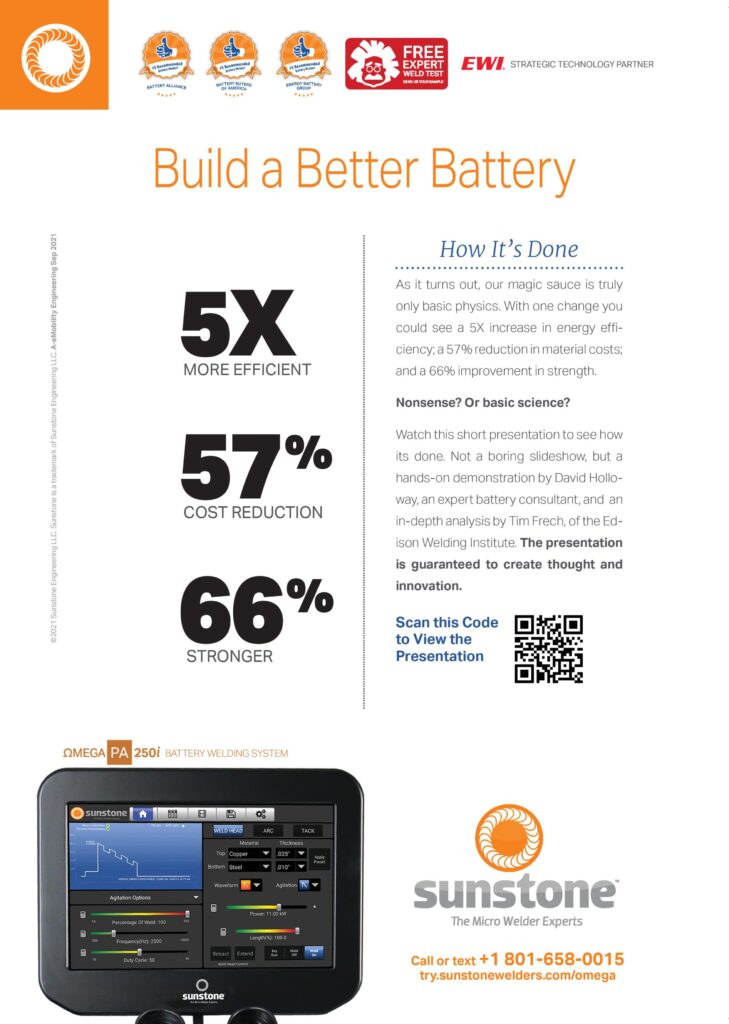
ONLINE PARTNERS
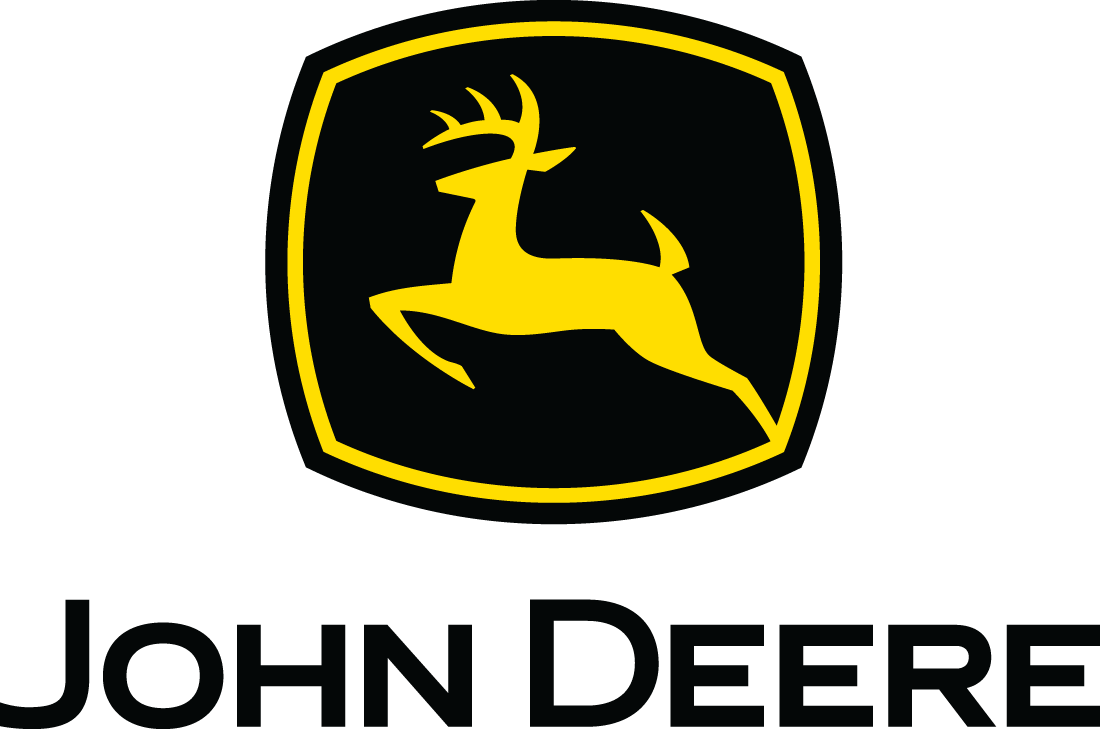
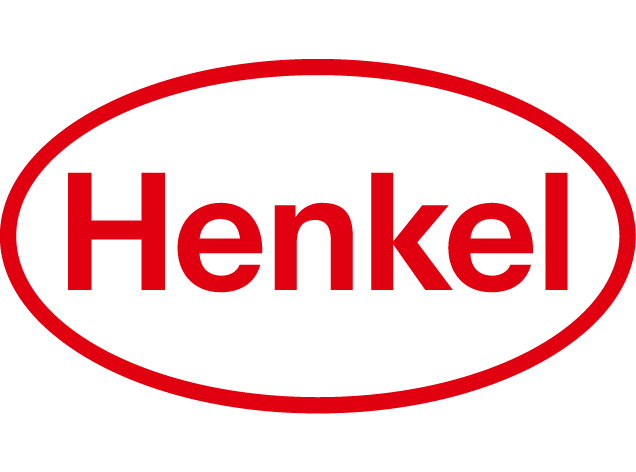
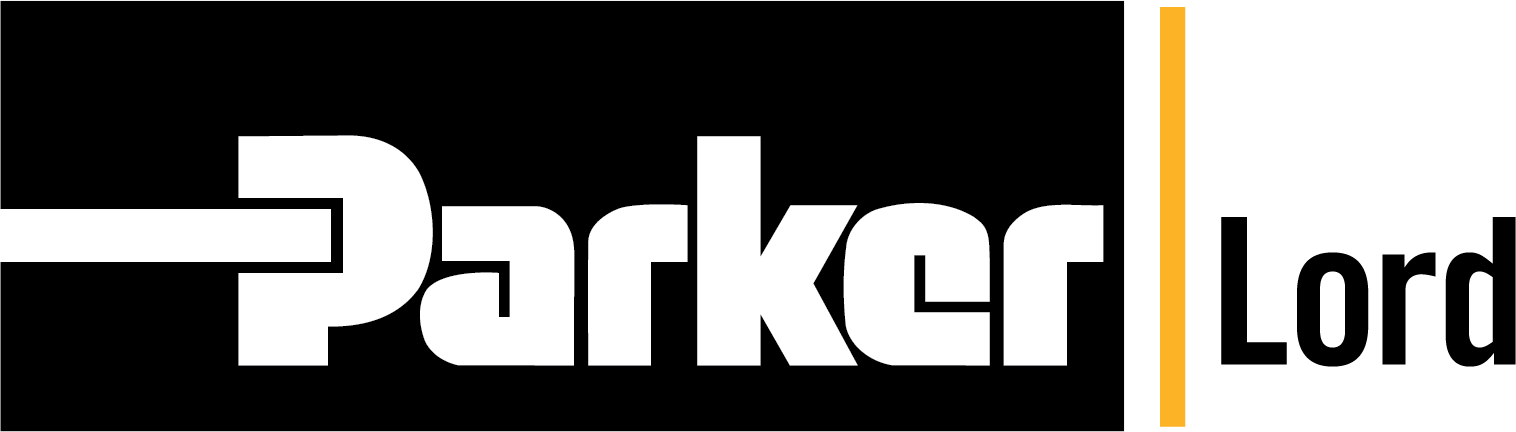
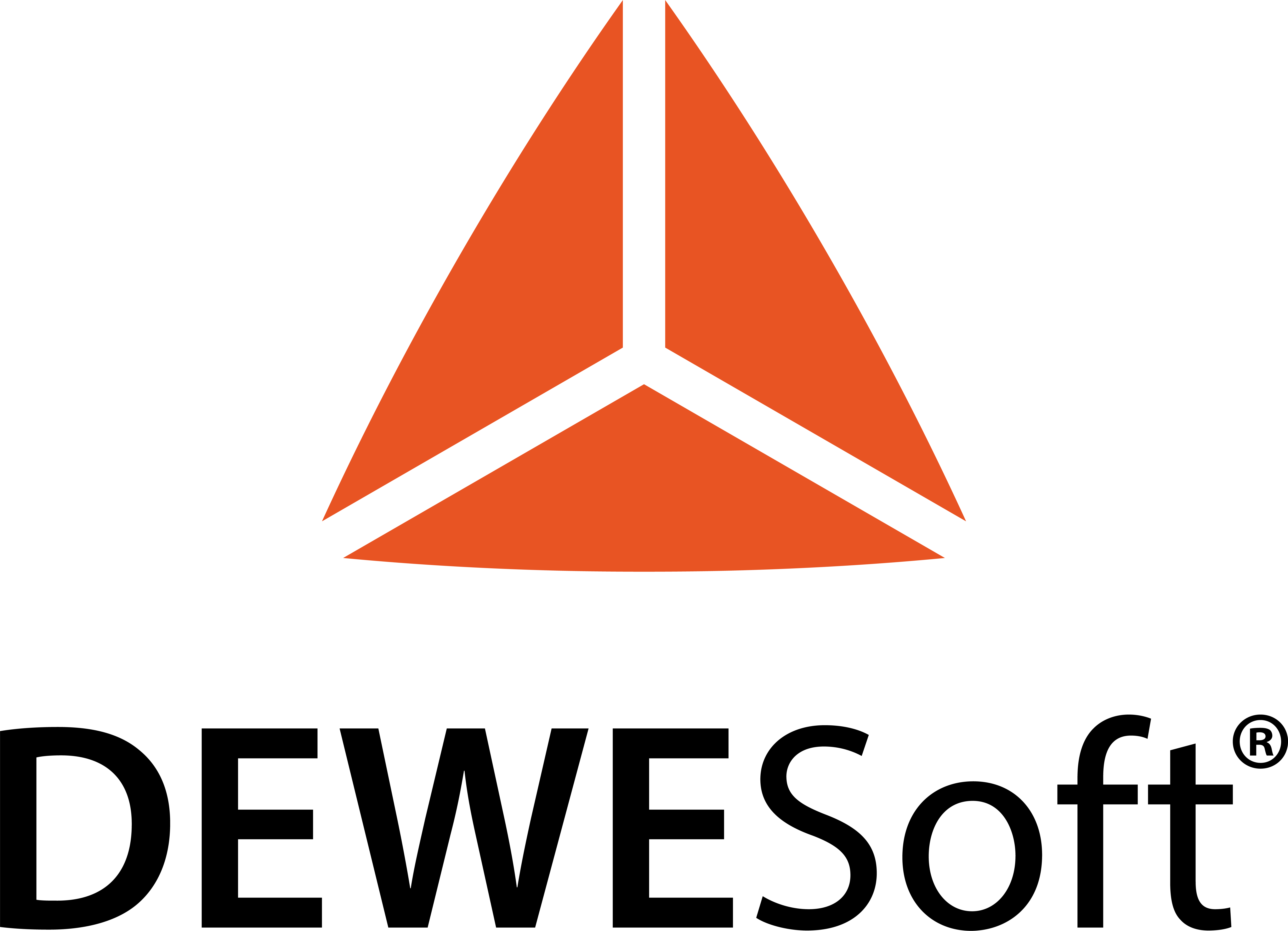
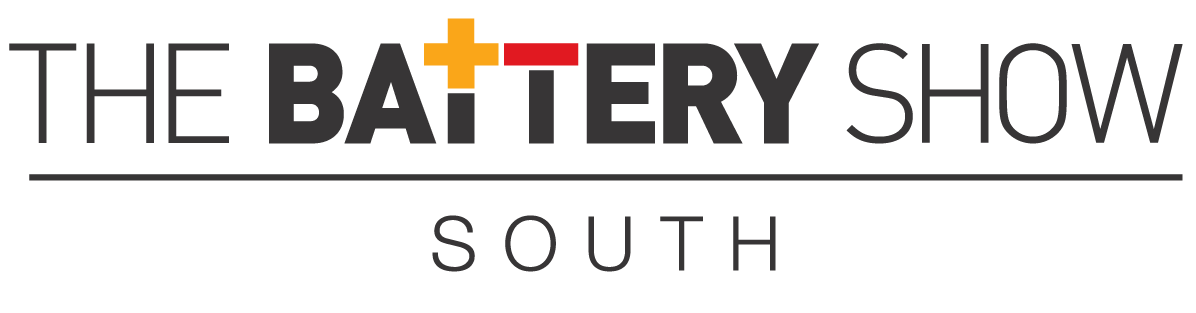
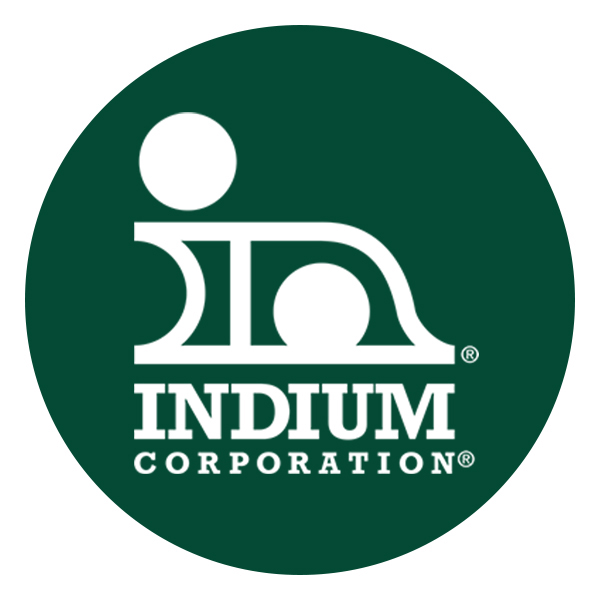
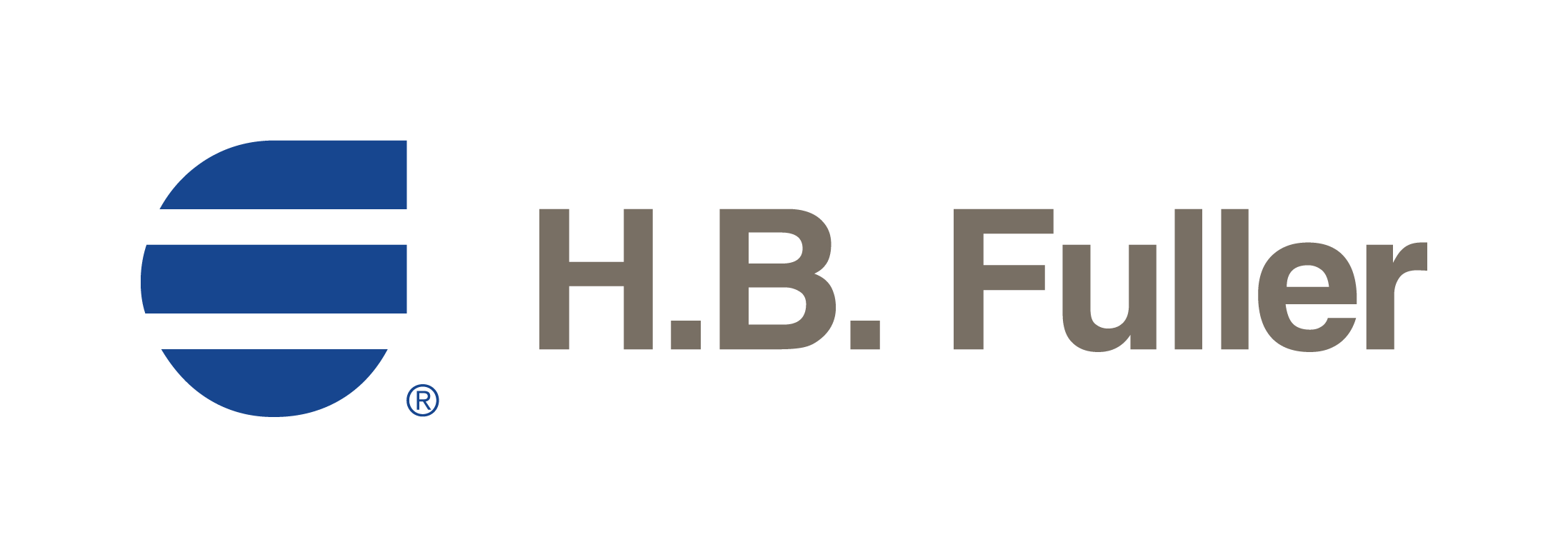