Condition monitoring
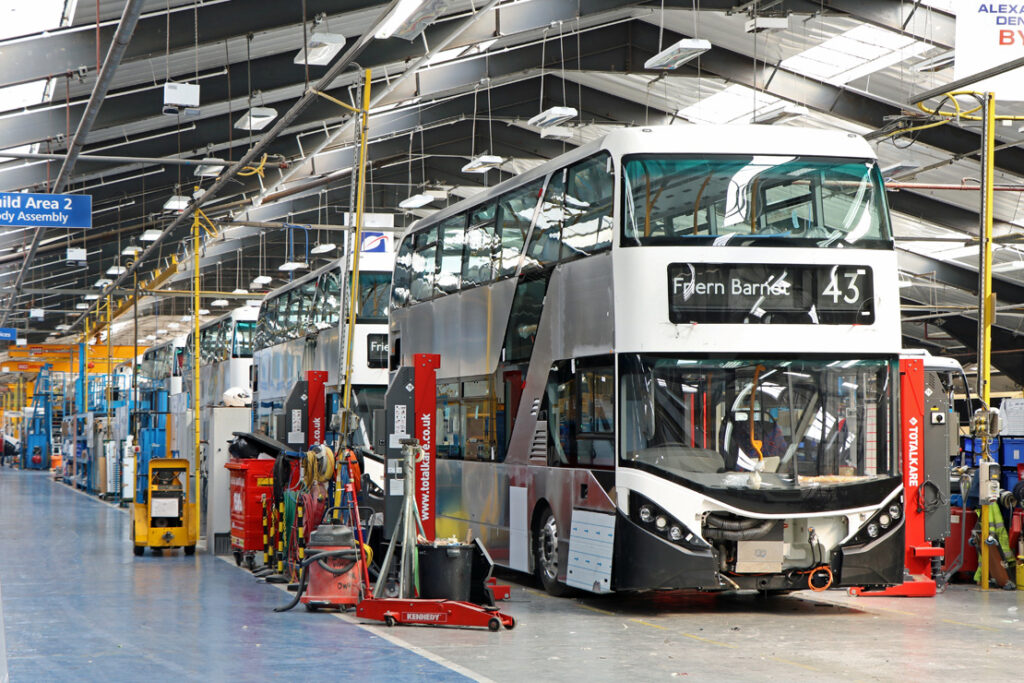
(Courtesy of Alexander Dennis)
Peter Donaldson examines the factors involved in keeping tabs on the health and performance of key EV components.
Health inspectors
While an EV’s most costly component is its battery, there are also many other subsystems – inverters, generators and so on – whose condition is critical to safety and efficiency. Machinery health and usage monitoring is well-established in industries such as aviation, but it is evolving and adapting to the technology of EVs in an era in which broadband connectivity and cloud computing are bringing huge processing power to bear. A vital step in monitoring any machine is measuring what key components are doing. Practically all modern vehicles have large numbers of embedded sensors, many of them essential to normal vehicle operation and some dedicated to condition monitoring. They provide signals that must be recorded and processed to detect developing faults, enable immediate mitigation and identify longer term health trends.
From diagnosis to prognosis
Most monitoring capability is devoted to timely detection and identification of faults, then executing immediate recovery strategies to ensure continued safe operation in ‘limp home’ mode, for example. The logical next step is to move into a full prognostics capability to predict failures as early as possible, evaluate remaining component life, and correlate vibration characteristics for example with component health.
In IC-engined commercial vehicles such as lorries and buses, the focus is on the diesel engine and its exhaust after-treatment system, and to a lesser extent on the transmission. With EVs, however, the primary focus is on the battery because it contains the greatest number of unknowns.
That is the view of an expert in commercial vehicle fleet telematics and condition monitoring, whose company serves bus operators encompassing IC-engined, hybrid and electric vehicles. He adds that operators are increasingly aware of the importance of battery performance and condition data to the assessment of ageing and preservation of warranties.
After the battery, priority goes to the inverter and onboard charger, followed by the motors. Centrally mounted motors powering conventional drivelines are not usually monitored, but electric portal axles or in-wheel motors are, largely because they are still relatively new technologies.
Additional challenges presented by EV powertrains are related to increased motor speeds. Although implemented in the pursuit of efficiency, spinning motors at high rpm can accelerate wear on the rotating components and create more vibration and consequent problems.
However, the EV industry can draw on extensive knowledge in the aircraft, shipping, railway and energy sectors regarding health and usage monitoring systems (HUMSs).
Cheap data transfer
Our telematics specialist confirms that cheap, high-bandwidth data transfer and practically unlimited cloud computing power now allow the bus and truck industries for example to benefit from condition monitoring systems that are directly comparable to HUMSs.
Data can be transferred at gigabytes per vehicle per month; volumes of this magnitude can easily be generated by sensors that sample at the millisecond level. Meanwhile, cloud computing allows almost any kind of complex analysis to be carried out.
This capability is embodied in algorithms that analyse vibration data, for example, which provides what one company with expertise in the area describes as an excellent opportunity to import prognostic condition monitoring knowledge from other applications. The company is working on several condition monitoring developments for cars and trucks using experience built up in other sectors, including wind turbines and industrial machinery in addition to railways.
Working in these areas has given the company’s engineers expertise in gathering, interpreting and postprocessing data from noise, vibration, temperature and rotational speed, allowing them to create model-based algorithms and other software that can be applied to the EV sector.
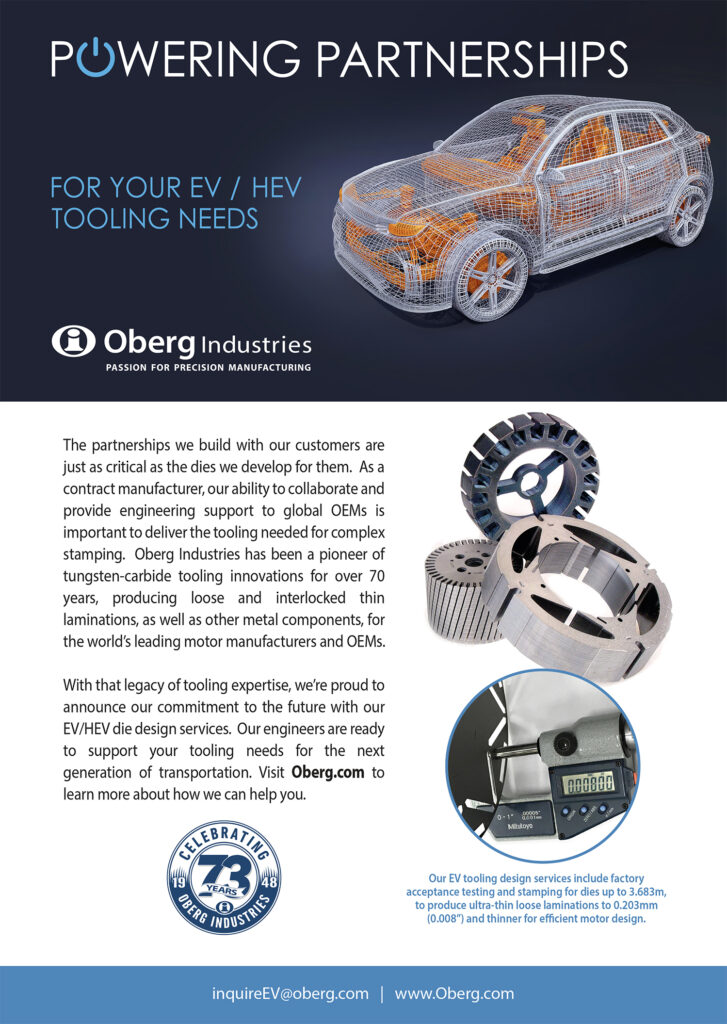
One example of this knowledge transfer involves an electrified bogie for a train, a component whose architectural layout, vibration characteristics and failure modes are very similar to those of e-axles for EVs. Sensing, signal acquisition and conditioning electronics must, however, be specific to each new application, and must comply with automotive environmental specifications and quality standards, the company says.
One of the main challenges with achieving reliable early prediction of failure and calculation of the life remaining in such complex systems is that architectures capable of doing so without dramatically increasing the number of sensors required are still evolving. A promising approach here though is to make the most of the information that’s readily available on the vehicle, typically on the CAN bus.
While an e-axle for example might seem like a relatively simple system from a mechanical point of view, the combination of gears and bearings operating in different conditions and subject to multiple potential failure modes actually qualifies them as complex systems. When the aim is to achieve reliable condition monitoring with diagnostic and prognostic capabilities at an acceptable cost, selecting sensors with the right characteristics and putting them in the right positions demands deep knowledge of both the component to be monitored and the application.
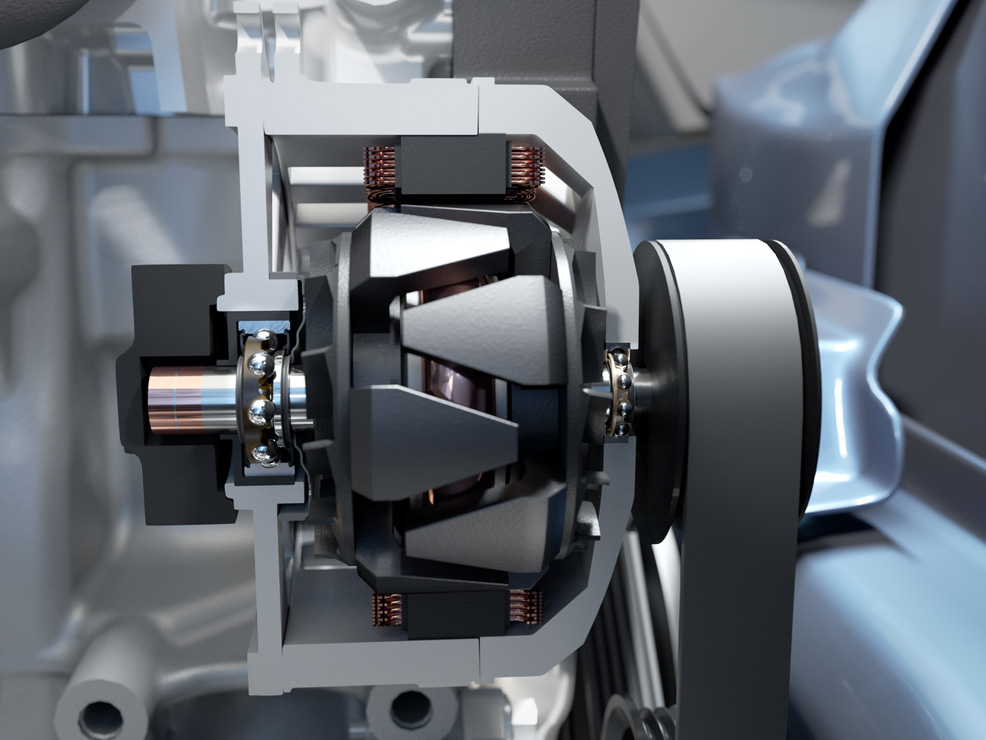
(Courtesy of SKF)
Because transmissions and e-axles are designed to last for the full service life of the vehicle with minimal maintenance, and because of the reduced driver/operator involvement with shared and autonomous vehicles, it has become increasingly important to design the component and the monitoring system together with the application in mind.
Many parameters affect component ageing, and combine to determine the maintenance costs and service life of the EV as a whole, the vibration analysis expert says. Temperature and vibration affect everything, and friction is a factor in all rotating, sliding and meshing components.
Meanwhile, electric current peaks such as in-rush currents during regenerative braking impact the battery. Parasitic currents inside electrical machines can also affect bearings and gears, while electrical noise and voltage spikes stress power electronics and can damage control electronics.
Informative trends
With the battery, our telematics specialist emphasises, the key is to build an overall understanding by measuring current and voltages at pack level, and diving deeper with individual cell-level measurements, looking particularly at maxima and minima in current, voltage and temperature.
The trends in voltage and temperature measurements are crucial, he adds, for assessing battery ageing. While currents tend to stay the same through time, quicker voltage drops indicate deterioration, and are affected by cell temperatures. Other useful parameters are the technical and operational states of charge, the first being the full installed battery capacity and the second the useable capacity remaining.
The battery management system (BMS) uses all these measurements to calculate the health of the battery, publishing it on the CAN bus and enabling the telematics to upload it to the cloud. In some cases, however, vehicle OEMs choose to connect the telematics system upstream of the BMS, so that the cloud-based monitoring system takes its data directly from the battery sensors and does its own health calculations.
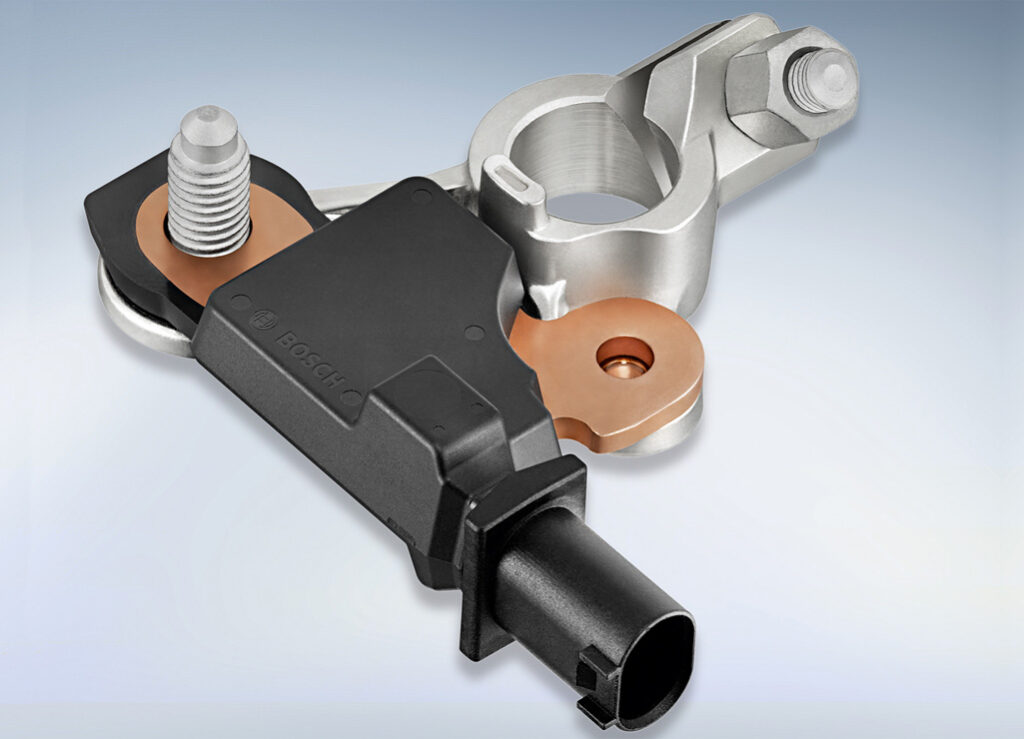
(Courtesy of Bosch)
With inverters and converters, the key parameters to measure are current in/out, voltage in/out and temperature, with statistical analysis revealing trends that might indicate problems.
In addition to temperature, voltage and current draw, torque and speed are monitored in motors, but the telematics specialist notes that issues with motors are rare.
As regards ECUs, he says his company is sometimes asked to transmit temperatures to ensure they are within safe working limits. However, ECUs run their own internal diagnostics in addition to the monitoring they do on the systems they control, generating fault codes under the OBD2 protocol, for example, which are therefore available to the condition monitoring system.
While cloud computing can take cues from these codes and analyse an inservice system, that is not the normal approach as customers tend to want what our expert refers to as “a single source of truth”. Detecting a developing problem early though allows the service provider to warn the operator that a particular system is likely to generate a fault code before long.
Sensor advances
Sensors have improved significantly in recent years, and now offer much greater sensitivity, accuracy and bandwidth for example, enabling them to detect fainter signals over a broader range of frequencies.
Despite these advances though, installing them in the optimum positions is often difficult. Challenges include space constraints in tightly packed assemblies, sourcing competitively priced sensors that can withstand harsh automotive environments over long vehicle service lives and connecting them to power supplies and data buses.
However, the maturing of MEMS technologies and the miniaturisation of transducing elements are making physical integration easier. Very small sensors are much easier to package with local signal conditioning and even pre-processing electronics. The associated reduction in their power consumption also eases and improves their integration, particularly when they have to be installed on rotating parts, according to the vibration analysis expert.
Such installations can make it impractical to power them from the vehicle’s battery though. However, energy harvesting techniques can convert mechanical vibrations, for example, into enough electrical power to run very small sensors independently.
For example, a prominent French research institute has recently published work (1) that examines a harvesting method that would be well suited to EV applications. It is based on a tiny piezoelectric transducer fixed to a resonating beam.
The lead researcher notes that a major issue is that the bandwidth of the harvester is especially narrow around its resonant frequency. He adds that vibration frequency can vary with time, which is a problem for harvesters that operate at fixed resonant frequencies.
As a solution, the team made an adaptive interface that collects the energy from the harvester and dynamically adjusts its resonant frequency. The result is a claimed 446% increase in harvesting bandwidth, the largest yet achieved. Between 100 μW and 1 mW can be generated from vibration in the environment, while the system consumes only about 1 μW, the paper says.
Better battery sensing
Inside battery packs it is naturally easier to power sensors, and most cells have their own voltage measurement chips. Currents are measured using shunt resistors or open-loop Hall effect sensors, while thermistors – semiconductor sensors that exhibit large changes in resistance in response to small changes in temperature – are used for thermal measurements. However, new sensor technologies are needed to identify changes inside batteries that lead to degradation and failure.
This is the mission of an EU r&d effort entitled ‘Spatially resolved acoustic, mechanical and ultrasonic sensing for smart batteries’ or Spartacus for short. Funded under the EU’s Horizon 2020 programme, it began in September last year and is due to finish in August 2023.
As well as mechanical and acoustic sensors, the project also aims to develop temperature sensors and electrochemical impedance measurement systems, and correlate sensor data with battery performance. The technology is intended to monitor the state of different parameters continuously, so that a battery can be cycled on an age dependent optimum level.
Earlier work with ultrasonics, for example, has confirmed the ability of such sensors to detect electrical arcing inside battery packs, while strain gauges have proved capable of detecting mechanical changes such as deformation of pouch cells.
Condition monitoring is about more than identifying long-term battery health trends, however, and has played a crucial role in the rapid and reliable detection of thermal runaway – arguably the biggest safety issue facing the EV industry.
A thermal runaway is a hazard in many lithium-ion battery chemistries, and starts with a failure in a cell that, if uncontrolled, can cascade throughout the battery pack, resulting in the release of hazardous gases and leading to a fire that can consume the pack. Causes of thermal runaways include internal and external short-circuits, overcharging, overheating, an impact or mechanical damage to the cell, and separator failure.
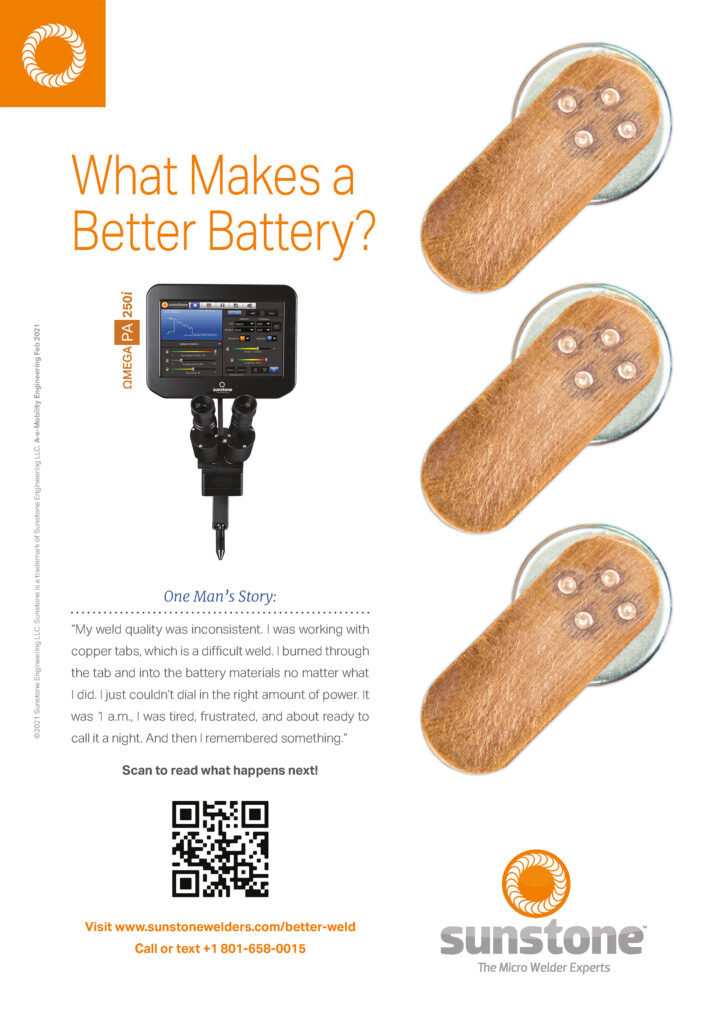
Fires in vehicle battery packs are hard to get at with conventional firefighting equipment. Also, they cannot be fought effectively with the water and foam used on fuel, brake fluid and other fires by depriving them of oxygen and reducing the temperature of the reactants. That’s because burning lithium-ion cells produce their own oxygen as the cathode and solid electrolyte interface layer decompose.
Compounding the problem, liquid electrolytes are usually volatile hydrocarbons that, when released inside the pack, provide extra fuel. Even when extinguished, lithium-ion batteries can reignite later if damage to the pack has resulted in ‘stranded energy’ – the energy remaining in a cell after efforts to discharge it safely – posing a long-term hazard.
New regulations mandate the installation of alarm systems that can warn of a developing thermal runaway 5 minutes before it poses a hazard to anyone in the vehicle’s passenger compartment.
Monitoring for thermal runaways
A major supplier of advanced sensor technologies to the industrial, aviation and transport industries has developed a set of general requirements for detecting a thermal runaway (2).
Any such system must perform just as well at the end of a battery pack’s life of 20 years or more as it does when the pack is brand new, a senior engineer from the company says. It must also operate reliably when the battery is charging or discharging and there is plenty of power available, as well as when the battery is inactive for a long time. In this ‘quiet’ mode there is a compromise between response time and power consumption, to ensure that the sensor does not drain the 12 V battery below useable levels.
Because a single cell can undergo thermal runaway in a matter of seconds, the sensor must have a high sampling rate, of at least 10 Hz in quiet mode and around 1 kHz while the vehicle is operating. It must also be agnostic to a wide range of parameters including cell, module and pack configuration, electrochemistry formulation and cell capacities, while neither missing detections nor generating false alarms.
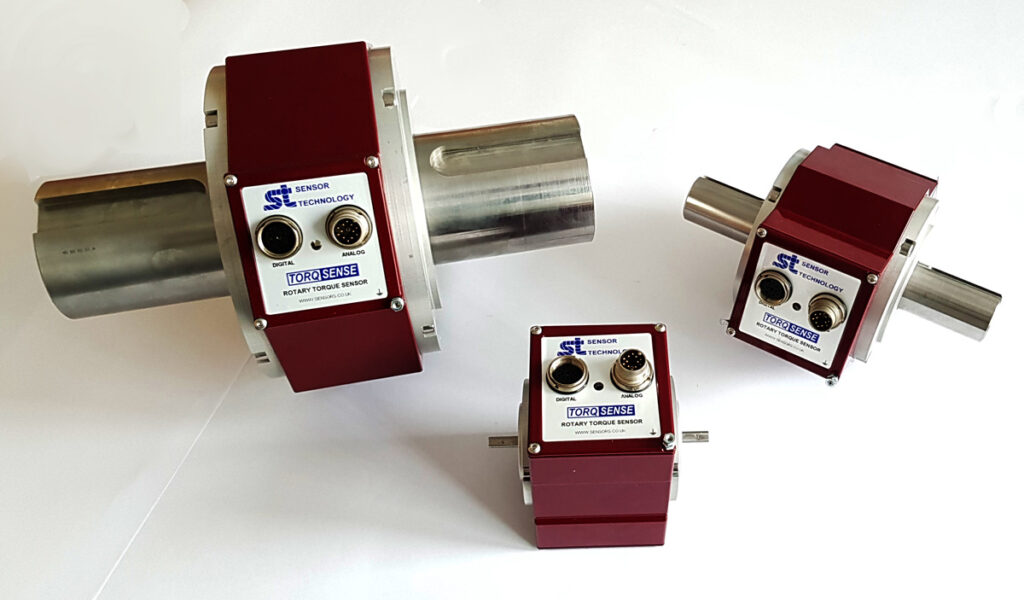
(Courtesy of Sensor Technology)
He adds that detection options for thermal runaway are limited. He describes temperature monitoring as impractical unless the fault occurs very close to the sensor, while voltage and current measurements are useful but more challenging in module configurations with parallel cells.
Monitoring air pressure inside the pack’s void space has been attempted, he notes, but pressure rise is highly dependent on enclosure design and is not useful for detecting events in cells with very low states of charge or health. Cell swelling can be an indication of thermal runaway, but it is difficult to monitor in individual cells and impractical in large-format packs. Also, the signal-to-noise ratio (SNR) for this fault tends to be small and needs to be distinguished from normal thermal and inflation swelling, he adds.
Such swelling affects pouch cells in particular, because of their flexible walls.
Detecting gas holds far more promise, offering both speed of response and a high SNR, as the cells quickly vent large volumes of gases, including carbon dioxide and hydrogen, in high concentrations relative to background levels. Even in the most polluted environments, background CO2 concentrations rarely exceed 2600 parts per million (ppm), while in the first few seconds of a thermal runaway the concentration in the battery enclosure generally exceeds 65,000 ppm, and will rise to more than 200,000 ppm.
Hydrogen turns out to be an even better indicator, as background levels are usually less than 6 ppm but concentrations in the battery case easily exceed 40,000 ppm in the first few seconds of venting.
This specialist sensor company tested a number of sensing technologies, and found that CMOS based hydrogen sensors provided rapid response, usually sounding the alarm in less than 3 seconds. They do not need a catalyst, and come with a record of reliability over more than 30,000 hours of use in mine safety applications.
Abundant cloud computing
Condition monitoring systems, particularly those that aspire to accurate prognostics, require considerable computing power, as they will have to rely on a number of data elaboration techniques and the application of advanced concepts such as virtual sensing and sensor fusion.
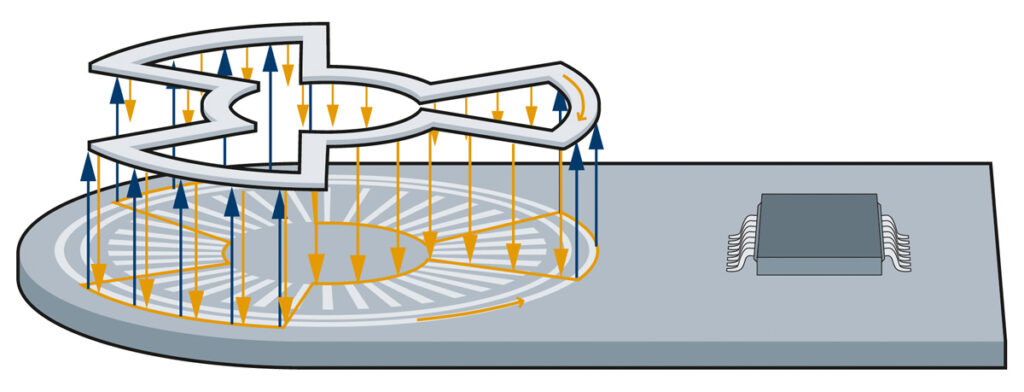
(Courtesy of Hella)
When applied to data, particularly data that a computer has interpreted as information, elaboration can be thought of as a secondary interpretation process that improves understanding of the information and derives new information from it. For example, predictive algorithms could elaborate on data from one sensor by associating it with data from another, with earlier data from the same sensor, with something that the vehicle was doing when the data was recorded, or all three, to draw inferences.
Sensor fusion algorithms can create a greater understanding of the situation than could be achieved through reliance on any single source. Virtual sensing emerges from sensor fusion, as it uses information provided by sensors and process parameters to estimate the value of some other parameter that cannot be measured directly.
These techniques can also be used with model-based approaches to prediction, and contribute to capabilities that come into the realm of AI and machine learning, together creating the ability to detect changes in data patterns that signify developing faults and impending failures.
Our expert emphasises that knowledge of system operating conditions and behaviour over its service life is crucial to effective and reliable prognostics. He stresses that machine learning algorithms linked to deep and extensive knowledge of realworld vehicle applications are essential.
All of this implies the need for a major step up in computing capabilities. The vibration analysis expert notes that vehicle electrical and electronic architectures are evolving from large numbers of distributed and separated ECUs with low computing power to so-called domain control units with sufficient computing power for multiple functions, including prognostics.
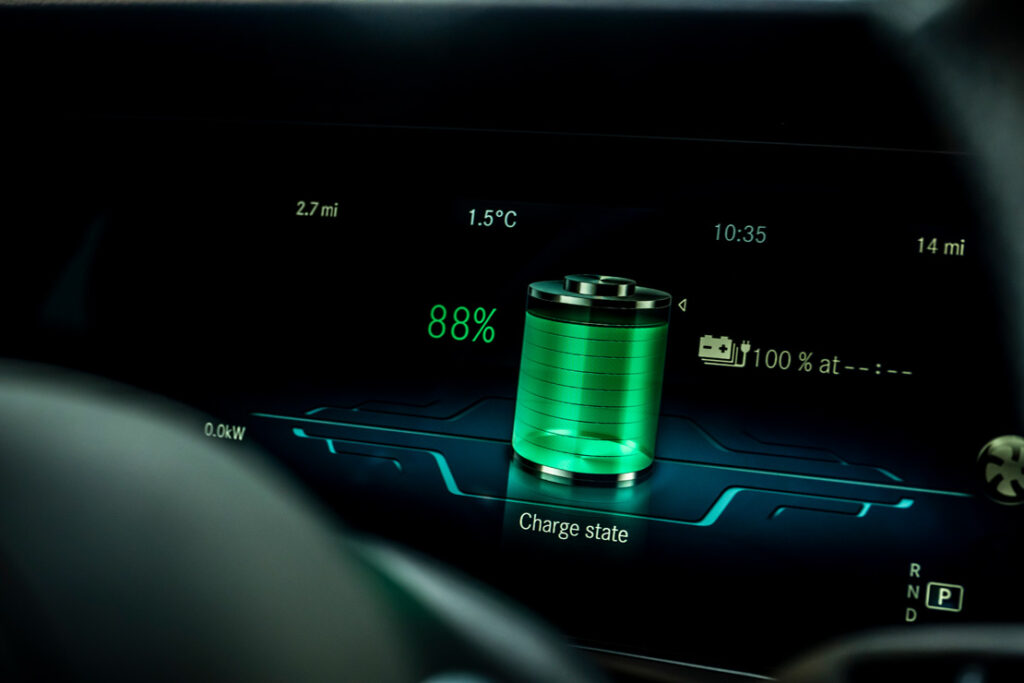
(Courtesy of Mercedes-Benz)
While cloud computing has really freed condition monitoring from the limitations in processing power and storage that it used to face, providers’ own costs are heavily infl uenced by the computing resources they have to devote to customers’ data. Our expert says that optimising algorithms has saved up to 50% of the processing power required for some analyses.
However, it is not enough simply to put more computing power on the vehicle to ensure these systems deliver actionable information to drivers, operators and so on in a timely manner as part of what is becoming known as full digital business management. That will require fast and reliable connections between databases, data sources and processing algorithms.
That is a major challenge, the vibration analysis expert notes, and is compounded by the anticipated need for further standardisation in terms of data creation, storage and communication to put the data into an easily exchangeable and portable format.
Translation challenge
Here, translation is critical. CAN bus data is in hexadecimal code, which needs to be translated into standard engineering units.
Unfortunately, there is no industrywide standard for encoding the data, so different manufacturers use different codes, and there are even major differences within manufacturers’ own vehicle ranges. That opens up opportunities for companies that can translate and process data from different OEMs’ vehicles to provide services to operators with mixed fleets.
It is extremely important therefore to be flexible when dealing with different vehicles, and to adapt to changes quickly, our expert stresses, as well as to be able to read and translate as much data as possible. When the data from each vehicle has been translated, the diverse inputs have to be mapped onto standard parameters so that the same analyses can be carried out on all of them, he says.
Although it has taken a long time, parameters relevant to EVs that were not immediately brought into the J1939 standard that governs CAN bus comms are now in there, including those for most of the high-voltage batteries and inverters. Nevertheless, the process is not complete, our expert reports, as his company sees many vehicle OEMs still using their own proprietary interpretations and are therefore not linking their EV powertrain data to the J1939 standard.
Prognostic condition monitoring algorithms could also make an important contribution to the achievement of the Automotive Safety Integrity Levels in ISO 26262, the standard that governs the functional safety of electrical and electronic systems in production road vehicles, particularly for EVs with autonomous features. When they comply with ISO 26262, the software and overall data acquisition systems for prognostics will be suitable for integration within automotive software architectures such as AutoSar.
Artificially intelligent web-based condition monitoring applications also promise to make life easier for maintenance technicians tasked with keeping EVs on the road. For example, they could automatically trigger orders for spare parts ahead of time so that they will be in the workshop when the vehicle arrives. Our expert notes that the system could also use the workshop visit as an opportunity to complete the diagnostic and prognostic cycles, and to gather data on the procedures for improving the overall reliability of its diagnoses and predictions.
User-friendliness is also key to the acceptance of these systems. Our telematics specialist says it should be possible for someone with little or no training, or engineering or technical background, to be able to use them easily. His company’s applications reside in the cloud and be accessed through a browser.
Condition monitoring technologies could also have an impact on the comms architectures used aboard vehicles as they come to deal with more data on more components and subsystems; some of that data is likely to be safety-critical. Protocols such as CAN, and the flexible data rate variant CAN-FD developed to deal with high data volumes, will probably evolve to meet these needs, according to our vibration analysis expert.
In parallel, wireless comms protocols will grow in importance to reduce the complexity, weight and cost of wiring harnesses while enabling point-to-point collection of data from embedded sensors and the exchange of data that is not safety-critical.
With the introduction of big data into the automotive environment, accurate information from condition monitoring applications will be increasingly important as a market differentiator for vehicle manufacturers.
Acknowledgements
The author would like to thank Alberto Carlevaris at SKF and Alexander Schabert at Viriciti for their help with researching this article.
References
1. Morel, A., Quelen, A., Berlitz, C., Gibus, D., Gasnier, P., Badel, A., and Pillonnet, G., “Self-Tunable Phase-Shifted SECE Piezoelectric Energy-Harvesting IC with a 30nW MPPT Achieving 446% Energy- Bandwidth Improvement and 94% Eiciency”, 10.1109/ ISSCC 19947.2020.9062972
2. Engle, B., “Amphenol Advanced Sensors’ Robust Early Detection of Battery Thermal Runaway”, The Battery Show & EV Tech, November 2020
ONLINE PARTNERS
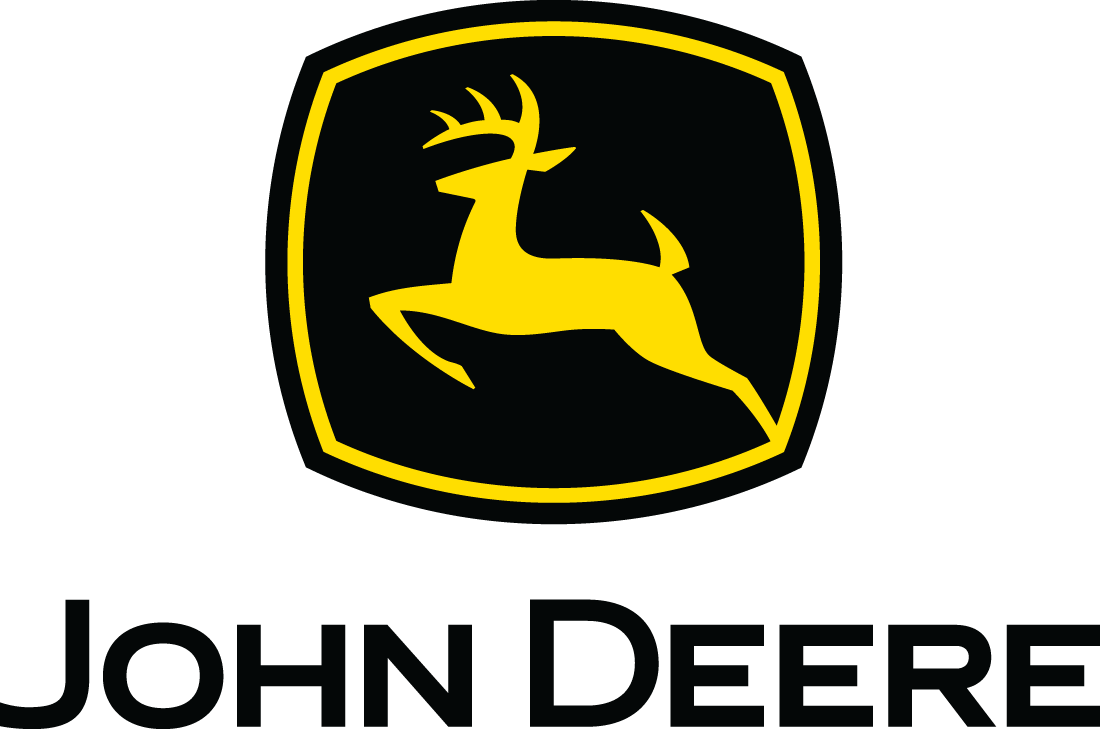
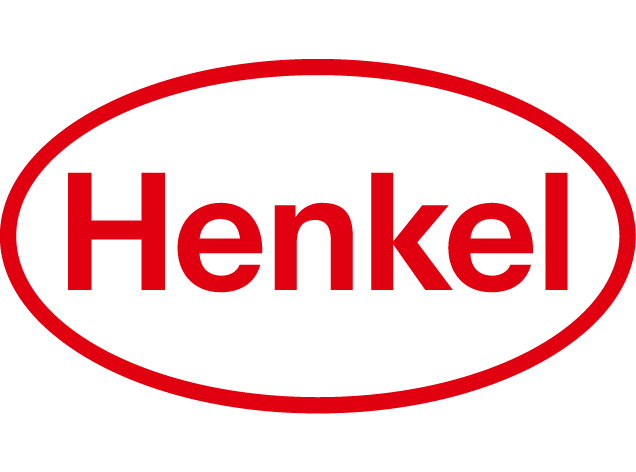
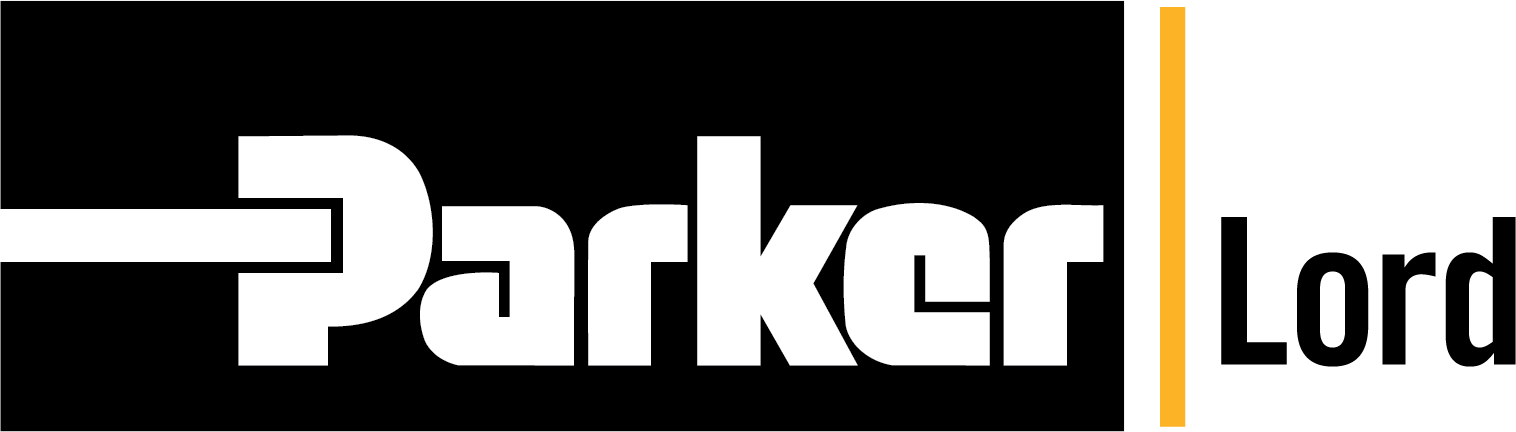
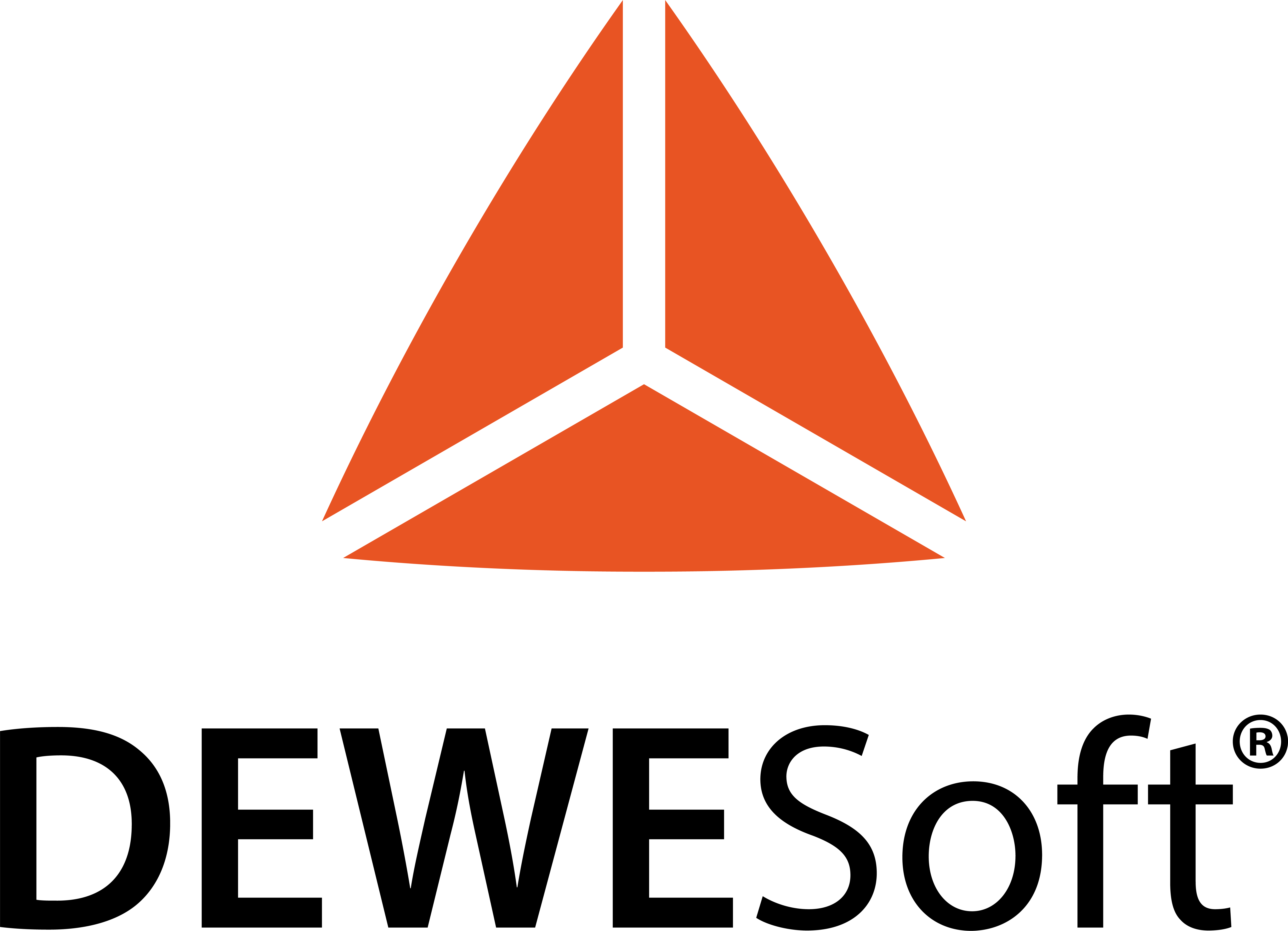
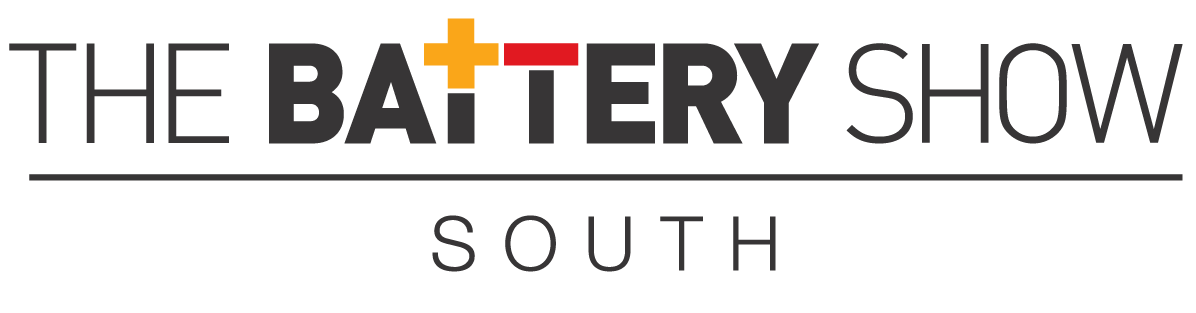
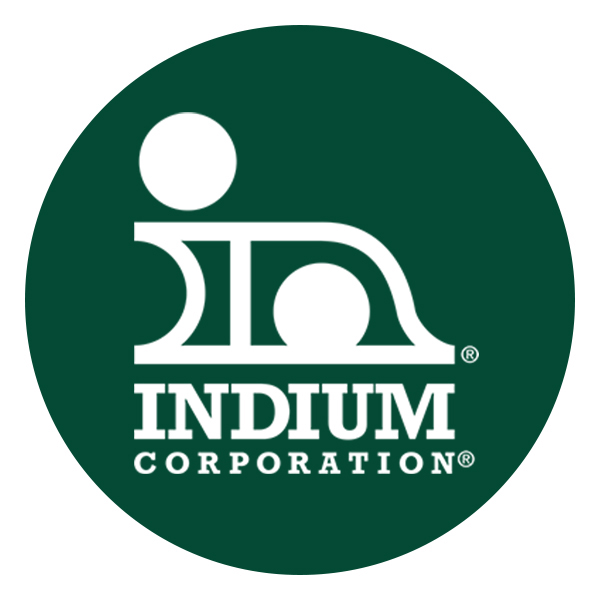
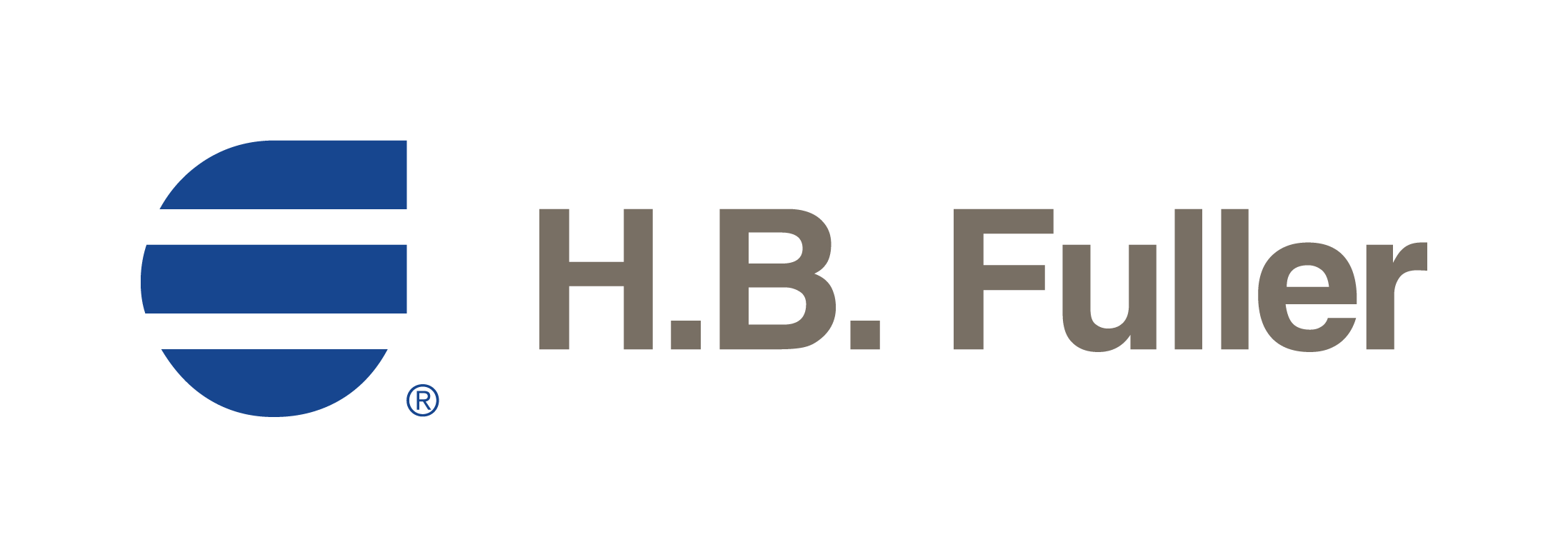