Elaphe’s approach to in-wheel motor development
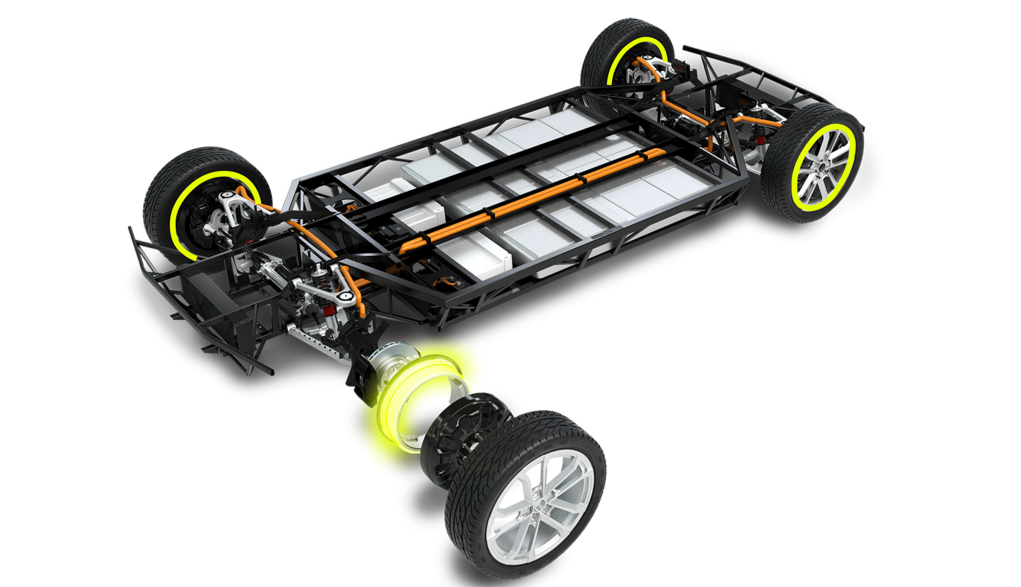
(Images courtesy of Elaphe)
Specialising in complete in-wheel electric powertrains, Elaphe’s development roots go back to the late 1980s (writes Peter Donaldson). However, the company was only officially founded 16 years ago, to pioneer in-wheel motors and multiple-wheel drive control systems, which it has evolved into a complete technology platform.
“One of the most important things for us in this are our relationships with legacy and newcomer OEMs, because closely working with vehicle innovators such as solar EV developer Lightyear help us to optimise the efficiency of the powertrain,” says CTO Gorazd Gotovac.
The principal challenges Elaphe solved in the development of its motors centred on weight and durability. “The weight issue was basically one of torque density, providing the required torque within a very tight space,” says Gotovac. “By torque density, I mean both gravimetric density, because of the importance of unsprung weight, and volumetric density: torque per kilo and torque per unit volume.”
He adds that the durability challenge arose because of the harsh environment in which the wheel operates. “Contrary to common belief though, it is not as bad as it might seem, because the motors are protected by the rim and the tyre,” he stresses.
The question of unsprung mass always comes up when discussing in-wheel motors, Gotovac acknowledges, but the problem is essentially a thing of the past. “There is a body of literature discussing the range of sprung-to-unsprung weight ratios that are acceptable for comfort,” he says.
He emphasises that, in tests, most drivers do not experience any issues that could be related to unsprung mass. “If you have a professional driver in the vehicle then they will notice a heavier wheel in particular situations, but not always,” he says. “However, for ‘normal’ people who do not study vehicle dynamics and handling, unsprung mass effects go unnoticed.”
The key, he adds, is to remain within the range of acceptable sprung-to-unsprung-mass ratios, which is best achieved by developing vehicles from the ground up, around the powertrain and user requirements.
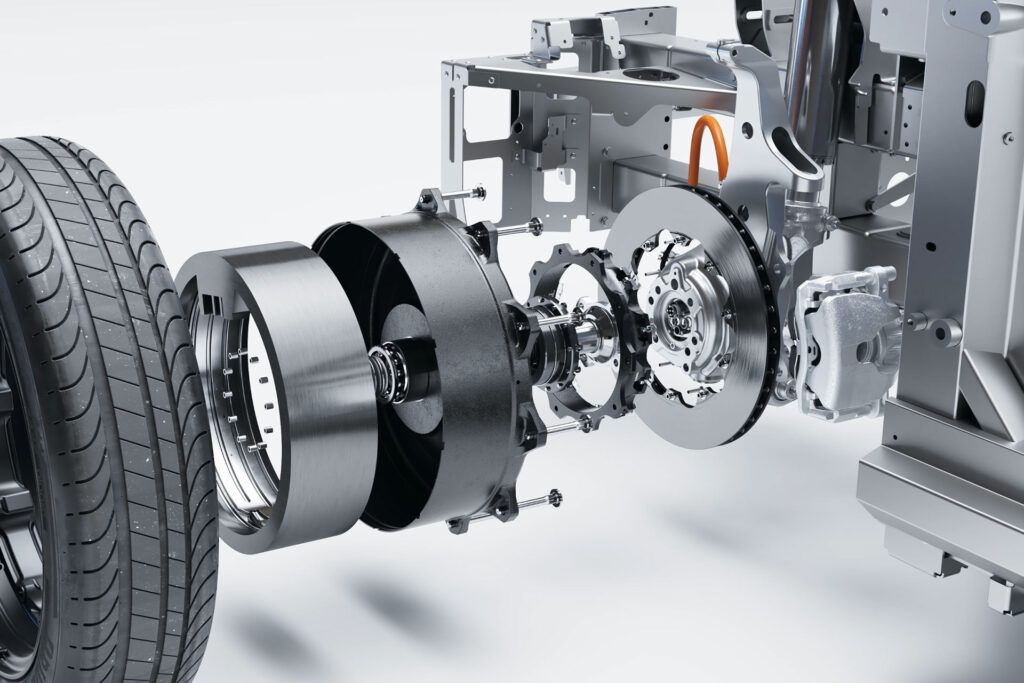
Elaphe’s approach is to rely primarily on design to keep its wheels within that range, using standard, relatively inexpensive materials such as aluminium, steel sheet and copper, while minimising the use of costly rare earth materials in its permanent magnets.
The basis of its approach to minimising the use of rare earths was to design motors with large numbers of pole pairs, which presents issues of its own. “Achieving a large number of pole pairs reliably while still getting good efficiency from the motor was the challenge,” Gotovac says.
Overcoming that involved co-optimisation with key elements of the wider system – particularly the inverter – and developing winding technologies to create large numbers of pole pairs, for which the company holds several patents. The result is a very high torque achieved at an acceptable cost, Gotovac adds, pointing to a volumetric torque density of more than 460 Nm/litre.
“It was clear to us from the beginning that the material cost and the weight of the motor are actually going in the same direction through optimisation, and that we should focus on that in design,” he says.
“We always looked at the e-axle as the competition. Looking at the permanent magnet mass in those, we wanted to keep two in-wheel motors the same or very close to one e-axle, so that we wouldn’t be much heavier at the system level, and from a cost perspective we would remain quite close.”
In terms of efficiency, in-wheel motors gain over IC-engined vehicles and more conventional EVs because they eliminate even more of the losses generated through its joints, bearings and lubricating oil. While modern transmissions don’t contain large quantities of oil, it still causes viscous losses that multiply in cold weather as the oil thickens.
“Fundamentally, that is the biggest thing,” Gotovac says. “If you put an electric car in neutral and coast, you get a feeling of just how good EVs with conventional e-axles already are, losing speed relatively slowly. If you do that in a vehicle with in-wheel motors, that happens even more slowly.”
Efficiency is particularly important for the Lightyear 0, which is designed to use integral solar panels to provide up to 70 km of range from solar power alone, depending on the climate. That is supplemented by charging the battery from a home socket to minimise reliance on fast-charging infrastructure.
That puts a premium on very close cooperation between Elaphe and Lightyear. “You cannot develop an in-wheel motor system in isolation from the vehicle,” Gotovac explains. “Yes, you can develop and mature the core technology, but you have to work very closely with the OEM to make the right trade-offs at the motor and vehicle levels to optimise the efficiency of all the vehicle’s systems.”
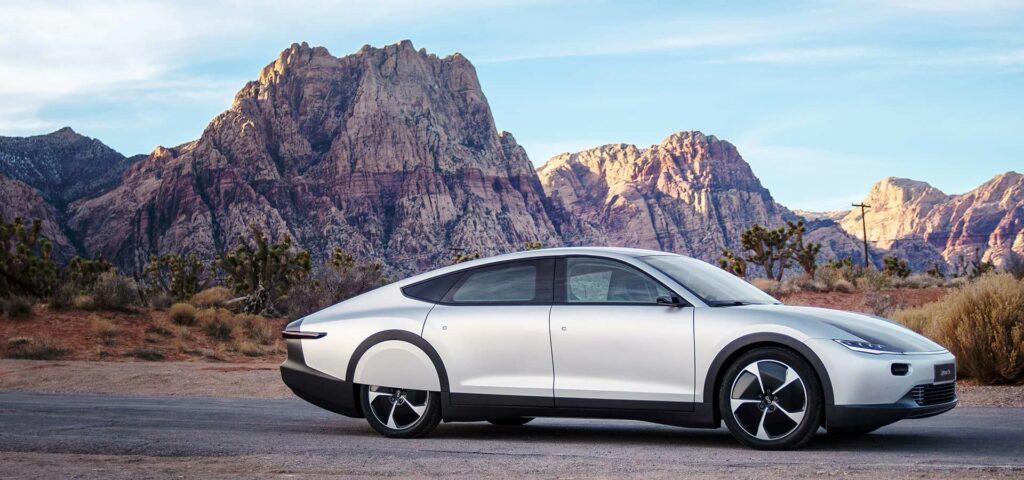
ONLINE PARTNERS
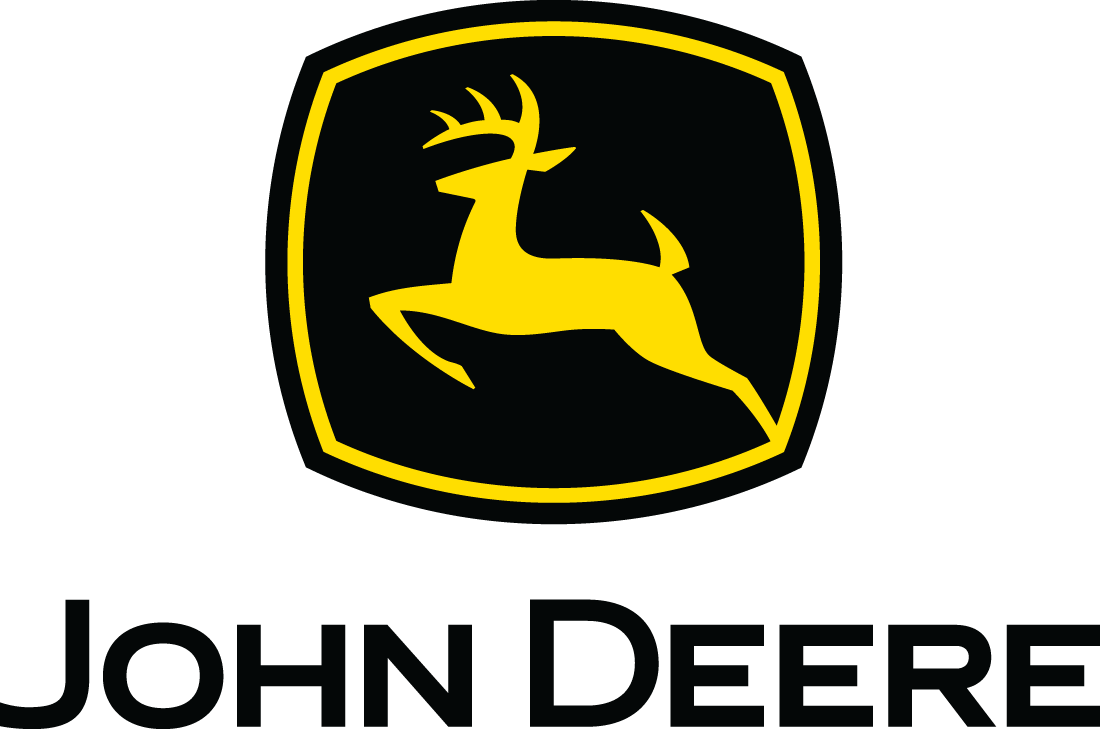
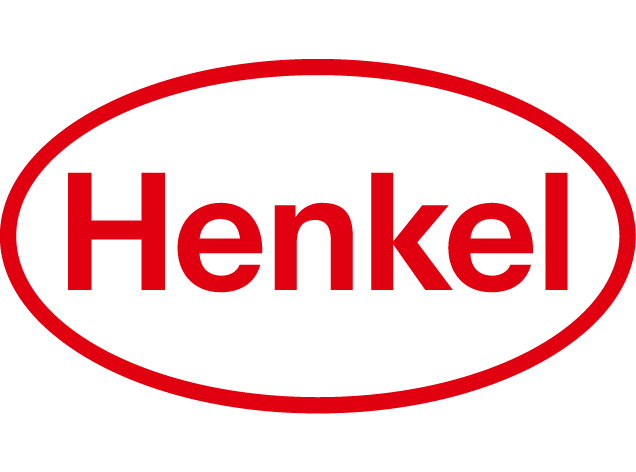
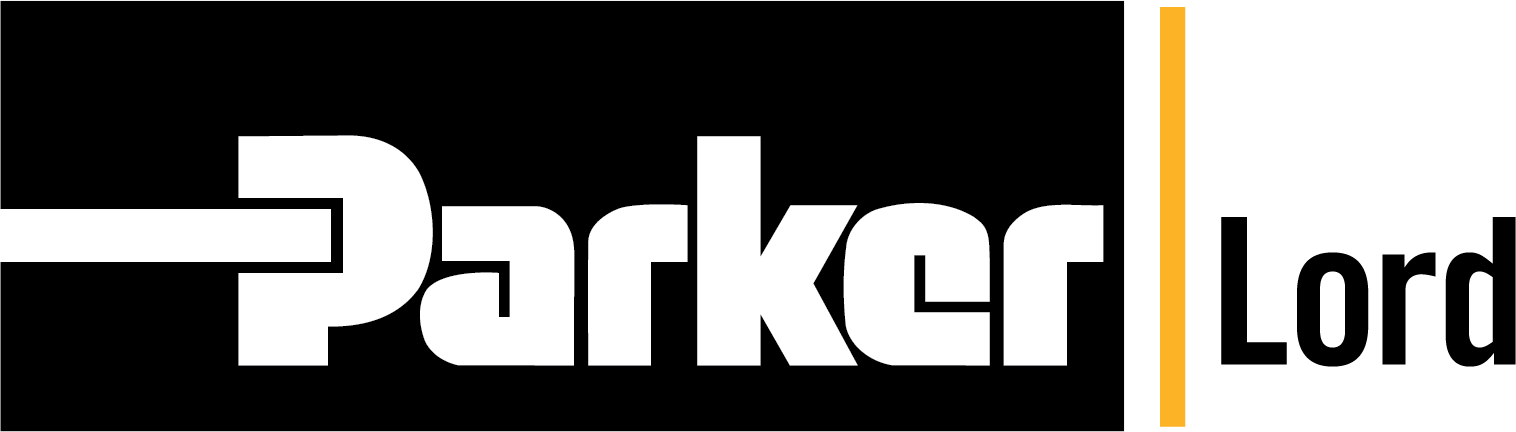
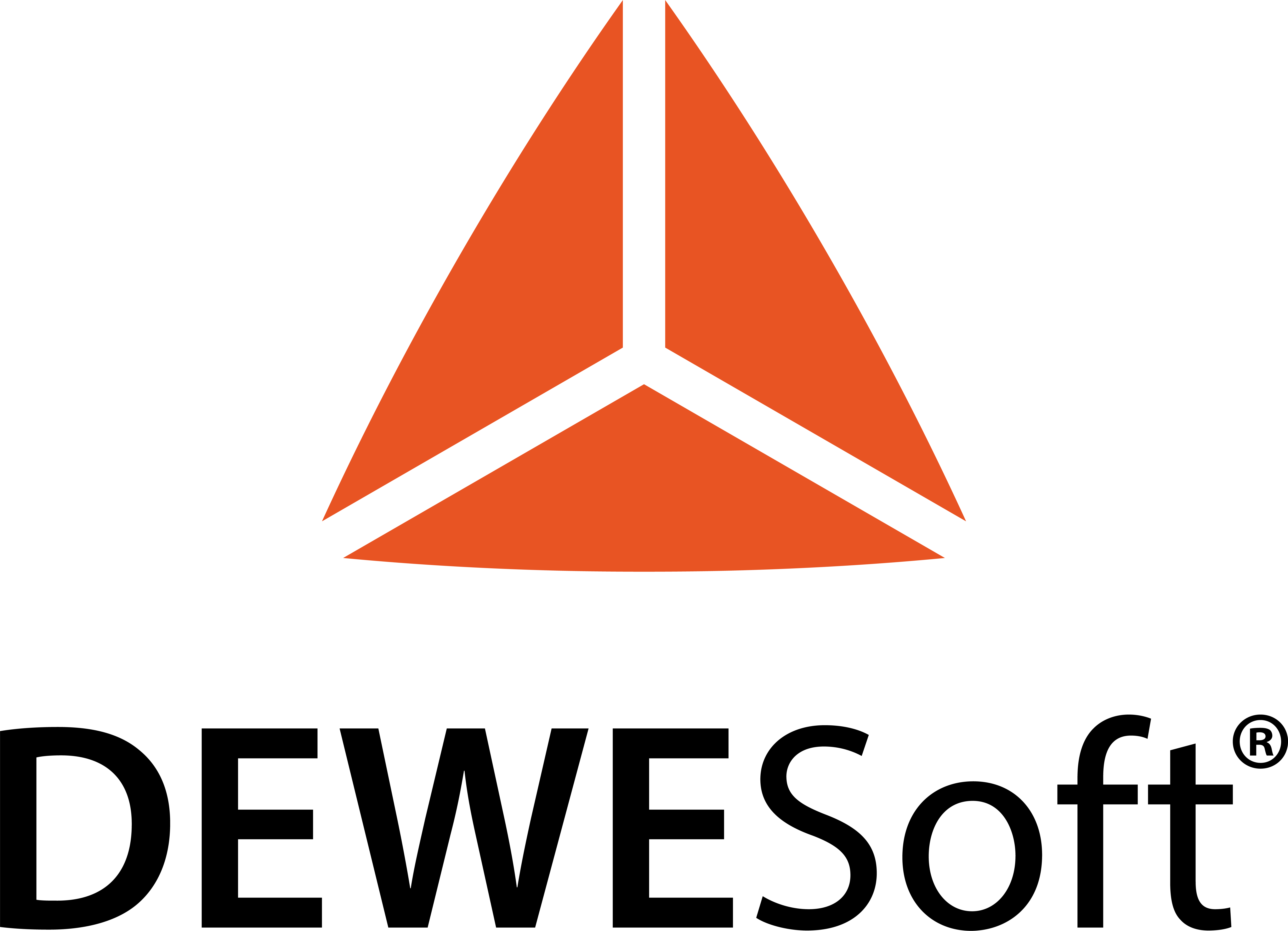
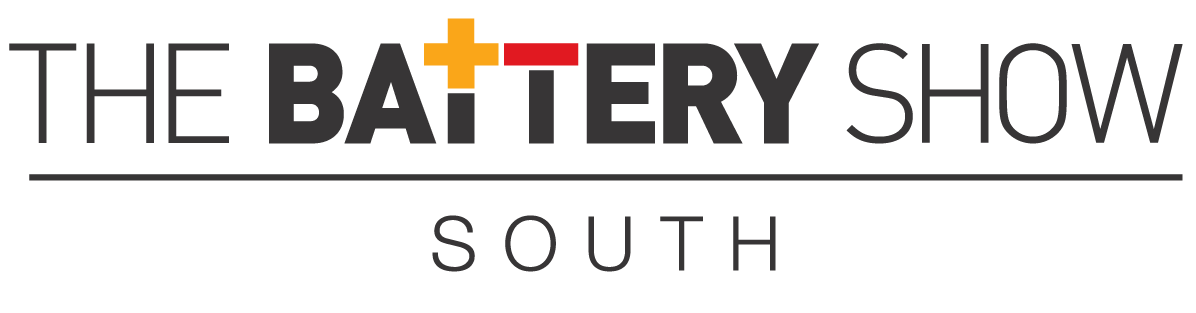
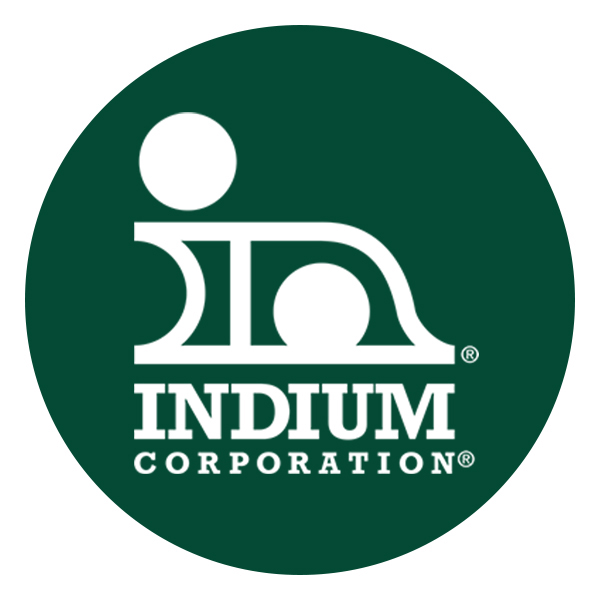
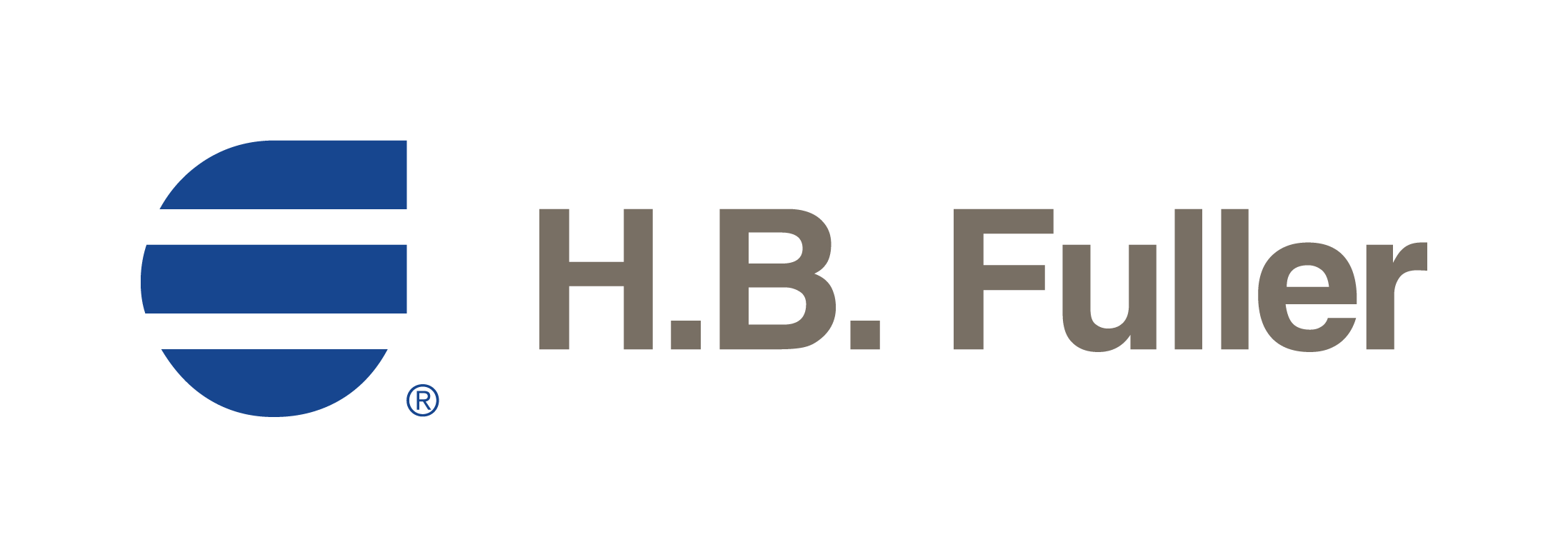