ECE electric Doosan DX165W and DX300LC
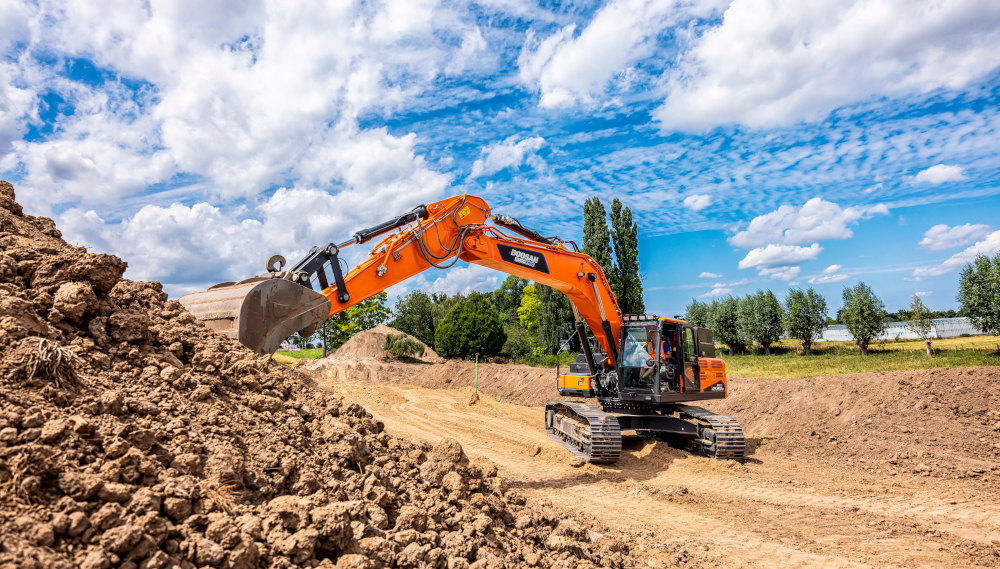
(Images courtesy of ECE unless otherwise stated)
Digging deep
Rory Jackson provides an in-depth report on how these heavy-duty excavators were converted to electric operation
The construction industry is a major focus for many parties intent on fighting pollution and climate change, and with good reason: studies over the past few years estimate that construction contributes just shy of 40% of the world’s output of greenhouse gases.
That figure, combined with the growing impetus to protect construction workers against the detrimental health effects of IC engine emissions, is shaping the industry’s demands and future regulations to favour low-carbon vehicles. While some responses to these changes take the form of LNG- and CNG-powered vehicles, which do lower emission outputs relative to diesel powertrains, electrifying construction equipment means eliminating all greenhouse gases at point of use, so it’s the ultimate way to stay ahead of tightening carbon restrictions.
While producing electric construction vehicles is challenging, given the heavy-duty applications for them, the market could be worth hundreds of billions once regulations begin coming into effect, making their ownership an urgent necessity for new building projects.
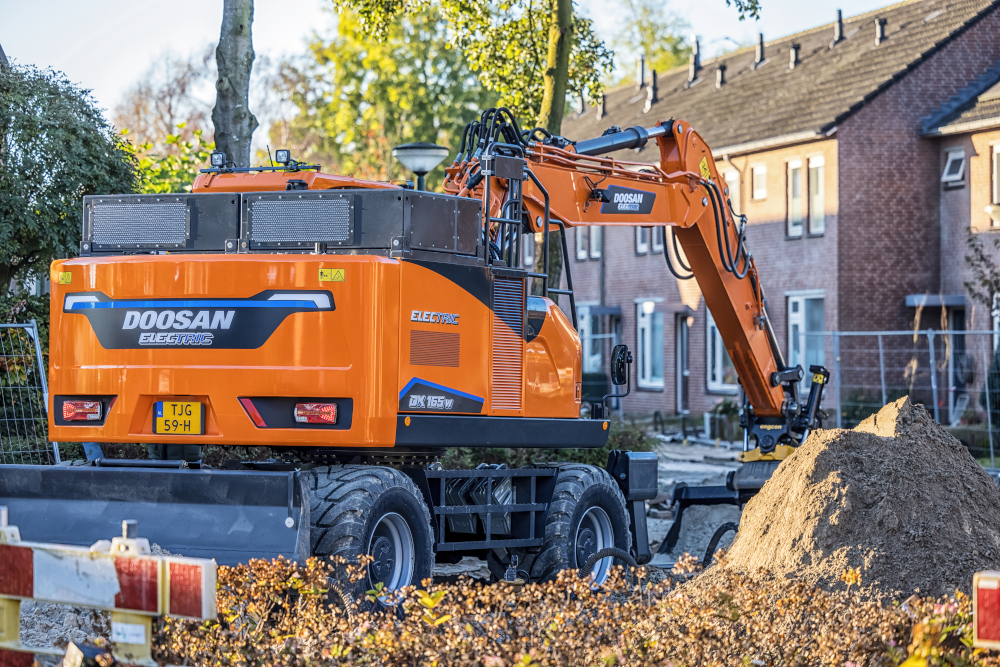
It also means an enormous reduction in part counts and hence ownership costs for vehicle owners by swapping out IC engines for electrified powertrains. Small wonder then that electric conversions of excavator systems are now commercially available, thanks in part to Netherlands-based Electric Construction Equipment (ECE).
ECE is a subsidiary of Staad Group, which imports and distributes diesel-powered Doosan earth-moving vehicles in the southern Netherlands. As ECE’s full name implies, it is responsible for providing electrified versions of the Doosan machinery, which are converted from IC engine power to battery-electric power in ECE’s facilities before being sold on to its clients. Some of these are large European construction companies, although ECE finds higher demand coming from the smaller subcontractors that work on behalf of the bigger firms.
Through rigorous r&d, both in-house and with key partners such as Webasto, ECE can now provide electric versions of different Doosan construction excavators. The two largest and most powerful of these are the DX165W Electric – which weighs roughly 17 t, has a bucket capacity of 0.64 m³, and can dig down to depths of 5.02 m – and the DX300LC Electric, a 34 t excavator with a 1.27 m³ bucket and a digging depth of 7.3 m.
ECE has re-engineered Doosan’s excavators to conform with all future limitations on point-of-use emissions as well as provide a fit with the operating and maintenance procedures on construction sites, in particular how batteries are used, managed and handled. The company’s engineering philosophy therefore begins with numerous application-critical end points in mind, making it a useful study in practical EV digger design and execution.
Electrifying Doosan’s excavators
ECE’s first work on an electrified excavator began in 2018, which soon after resulted in the all-electric Doosan DX19. This was a small excavator that allowed the Dutch company to begin gathering and gauging interest in emissions-free systems for demolition jobs in indoor spaces, where ventilation is insufficient for conventional diesel- or LNG-powered systems.
“It also meant we could start looking for partners and suppliers capable of shipping enough components for short production runs of the mini-excavator, in preparation for supplying larger quantities of more powerful excavators,” says Thijs Van Hal, COO of ECE.
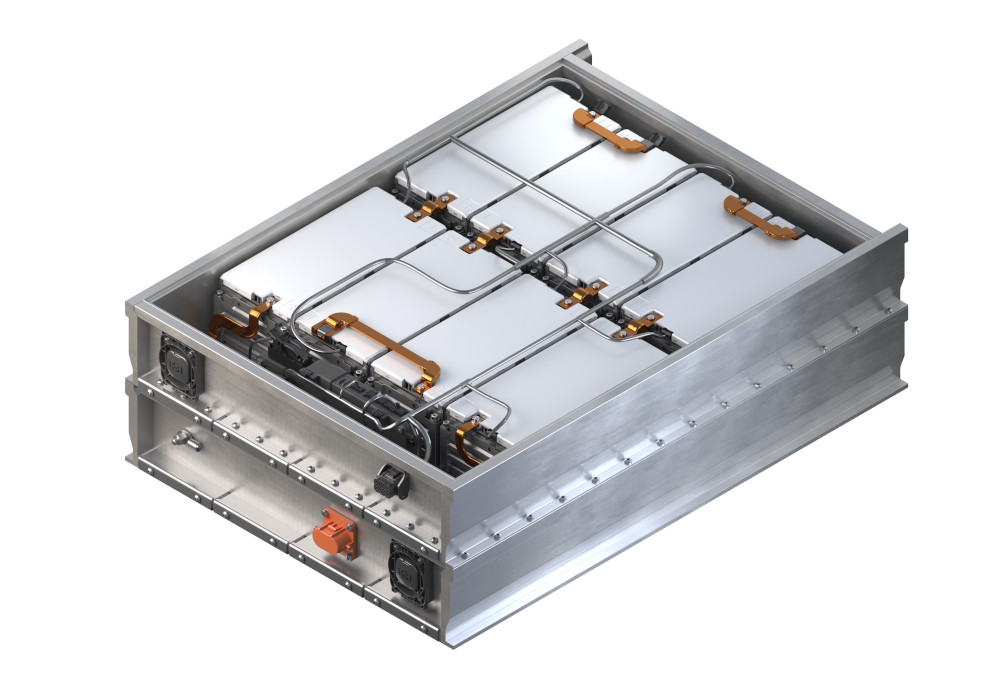
(Courtesy of Webasto)
“At the time, we didn’t think there was much of a market for larger excavators, but in 2019 customers started querying directly if we could electrify some of Doosan’s bigger models, principally because the emissions rules for construction projects looked like they were starting to change. For instance, by 2025, emissions-producing cars and trucks won’t be allowed in many European city centres, and by 2030 there will be widespread bans on diesel-powered excavators in city centres.”
Given Staad Group’s experience and inventory of the larger diesel-powered Doosan machines that customers wanted electrified, ECE had easy access to copious data on key powertrain constraints, such as the kinds of duties the vehicles performed and the rates of fuel consumption they exhibited during such duties.
By analysing such metrics over the 200-or-so Doosan DX165Ws and DX300LCs that Staad has in operation, ECE was able to set targets that the two vehicles’ electric powertrains would need to achieve in areas such as voltage, current, onboard stored energy, and e-motor shaft speed and power.
“Important goals included both machines needing to run for eight hours between charges, they needed to have swappable batteries, and in general they needed to be safe,” Van Hal says.
“There were some physical constraints and targets too. For instance, we were quite sure the battery packs would need to sit where the diesel engines had previously been installed, with some additional modifications to ensure sufficient counterweighting against the movements of the digger arms, and to keep the centre of gravity the same as in the IC engine-powered excavators.
“While running simulations in AutoCAD to determine the kinds of components we’d need to hit these targets, we started looking for suppliers for batteries and electric motors. We agreed the sale of the first units in late 2019, which were to be supplied in 2020.”
The first half of 2020 was spent largely on selecting battery and electric drive systems, as well as integrating them into the two excavators. The summer and autumn through to December were spent running tests to analyse their performance and determine how to optimise them, in terms of hardware configurations and software tuning.
“Most important among our test objectives was getting practical comparisons of how our electric conversions performed in comparison with the original diesel-powered excavators,” Van Hal explains. “So to ensure those comparisons were accurate, we’d run drills of movements and digs with diesel vehicles we had in-house, then repeat them as closely as possible with our electrified prototypes.
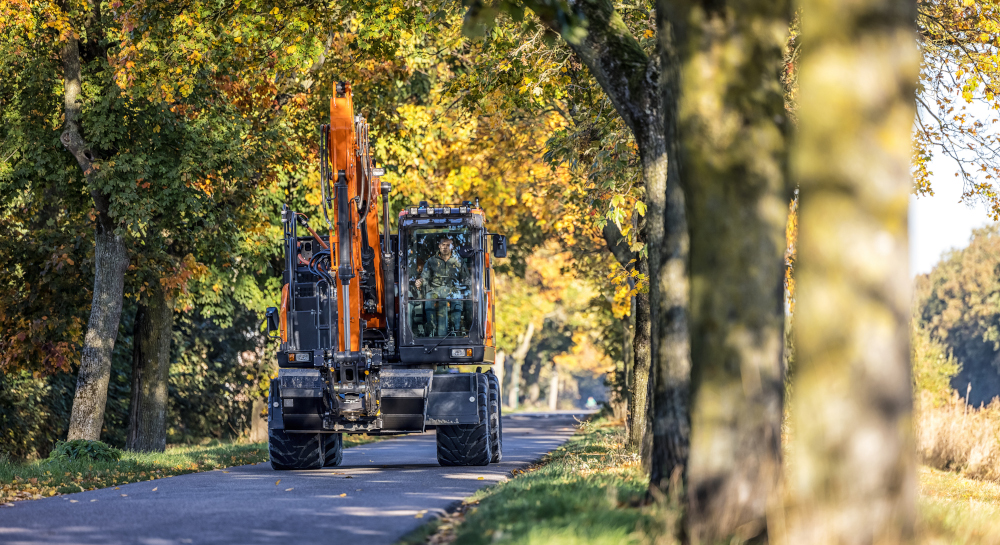
“Efficiency and endurance are of paramount importance to our customers, so first and foremost we’d look at diesel fuel consumption, and contrast that with the rates of battery energy consumption, to optimise that latter parameter wherever we could from pack to motor.”
Before the first commercial deliveries, ECE also loaned the DX165W and DX300LC Electric prototypes to customers’ building sites for beta testing for a fortnight. That verified first-hand that the heavy-duty EVs could execute the sorts of digging, earth-moving and demolition tasks that end-users would require.
Again, diesel-powered Doosan excavators were available at these sites whenever the beta testers wanted direct comparisons of the high-carbon and zero-carbon machines.
Even after the first DX165W and DX300LC EVs were supplied to their customer (a construction subcontractor in Norway), talks between the end-user and ECE continued, and yielded invaluable feedback on key operational considerations, for instance on the best approaches for handling or storing battery packs.
To date, 20 units are working with commercial partners, and Van Hal notes that five have gone to large construction firms, with the other 15 being used by subcontractors. A further 56 Doosan vehicles have been bought and were going through the production process at time of writing.
Specification and anatomy
We previously covered the John Deere 944K Hybrid Wheel Loader (EME 03, Summer 2019), which required holistic re-engineering to transform from a diesel system into a hybrid-electric one, owing largely to the torque and regeneration requirements associated with how loaders drive directly into earth (or other material) to scoop it into their buckets.
By contrast, however, the two large Doosan excavators are consistently stationary when lifting, and spend very little time driving around construction yards. That, combined with r&d revealing that the hydraulics used for traction and lifting were far more suitable for efficient movements of the heavy vehicles and arms than electro-mechanical ones, mean the electric powertrain is largely separate from the hydraulics; that meant the latter required effectively no modifications whether driven by a diesel engine’s shaft or an e-motor’s. As a result, ECE found that engineering the electric DX165W and DX300LC posed largely similar challenges to electrifying cars, trucks and buses.
“The main challenge was fitting enough energy on either machine to make sure they could run for eight hours at a time,” Van Hal says. “For reference, a litre of diesel contains about 10 kWh of energy, whereas the volume of a 10 kWh battery pack is much larger than a litre.
“So we spent a lot of time calculating the dimensions of the batteries for different cell and module types, to then understand how much space or counterweighting we’d need to accommodate the packs.”
Part of this simplicity comes from the fact that, as mentioned, the traction and lifting systems on the electric DX165W and DX300LC have been left largely unchanged, leading ECE’s engineers to the principle of “if it ain’t broke, don’t fix it”. On both EVs, the battery pack sits at the back behind the cabin, and a heating and cooling system for the batteries is installed above (which functions independently of the vehicles) along with the BMS and a 24 V ancillary battery for cabin, control and other low-voltage systems.
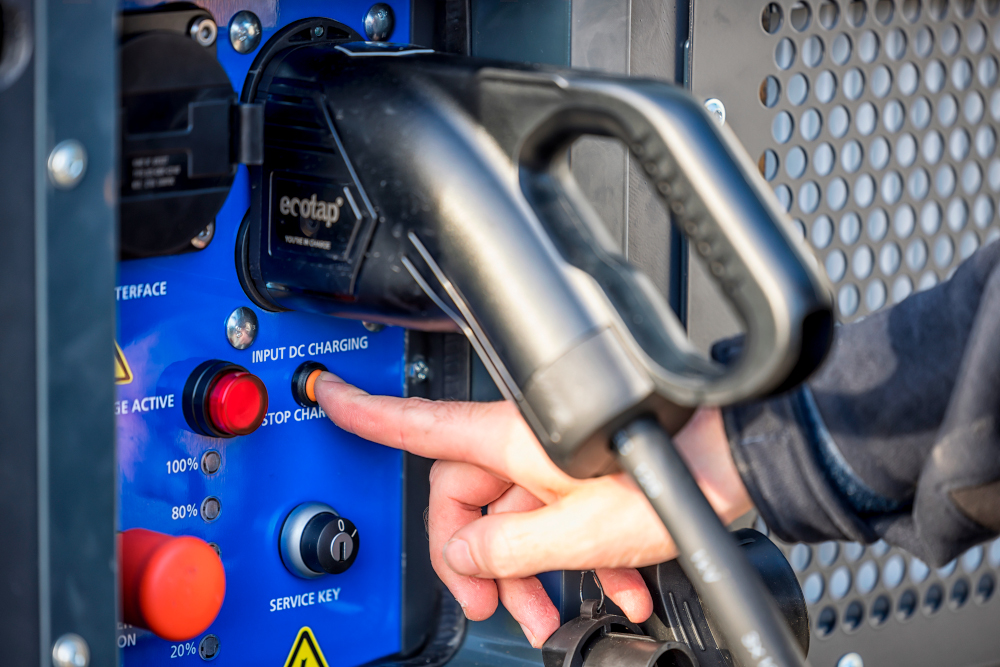
Some HV cabling connects the packs to a high-voltage power distribution unit (referred to in-house as the ‘roundabout’) which delivers power at 800 V to the motor-inverter, electric fans, the LV DC-DC, onboard charger and other HV components. These sit between the batteries and the counterweight.
Power from the electric machine directly drives two hydraulic pumps for digging. One is for the lifting boom and arm, the other for the excavator bucket and wheels.
Van Hal comments, “800 V is high, and it’s still not that easy to find components for 800 V batteries, powertrains and HVACs, but to efficiently achieve the torque needed by the hydraulics in our machines, it’s important that we go for higher voltage and hence lower currents.”
He notes that both lifting and traction consume huge amounts of energy on excavators. He estimates that when driving at around 40 kph, the electric DX165W and DX300LC consume about 60 kW and 70 kW of energy respectively, although the vehicles will rarely exceed 35 kph, and drive mainly just at the start and finish of typical workdays.
When lifting and digging, an average of 25 kWh is used per hour, so with up to two hours of driving and eight hours of work potentially expected per day, onboard energy storage of at least 200 kWh is needed.
“And on top of making enough space for eight hours’ worth of batteries, we needed to install them where they were low enough to be manually removed and replaced. This takes place while the excavators’ cabins are stationary,” Van Hal adds.
“We’ve put a lot of componentry and software intelligence into the battery packs to ensure they can charge from a wide range of inputs.”
At 17 t, the DX165W Electric weighs around 1-1.5 t more than its diesel-powered equivalent. While weight reduction is an advantage for most EVs, construction excavators must be extremely rugged, so minimal structural changes have been made, and those that have still use mainly steel for robustness.
Replacing the IC engine with battery packs has for instance widened the lower chassis of the DX165W such that its widest point is now 2.5 m, rather than the original 2.45 m. The DX300LC Electric has been similarly increased in size and weight, with the original weighing just 30 t to the EV’s 34 t.
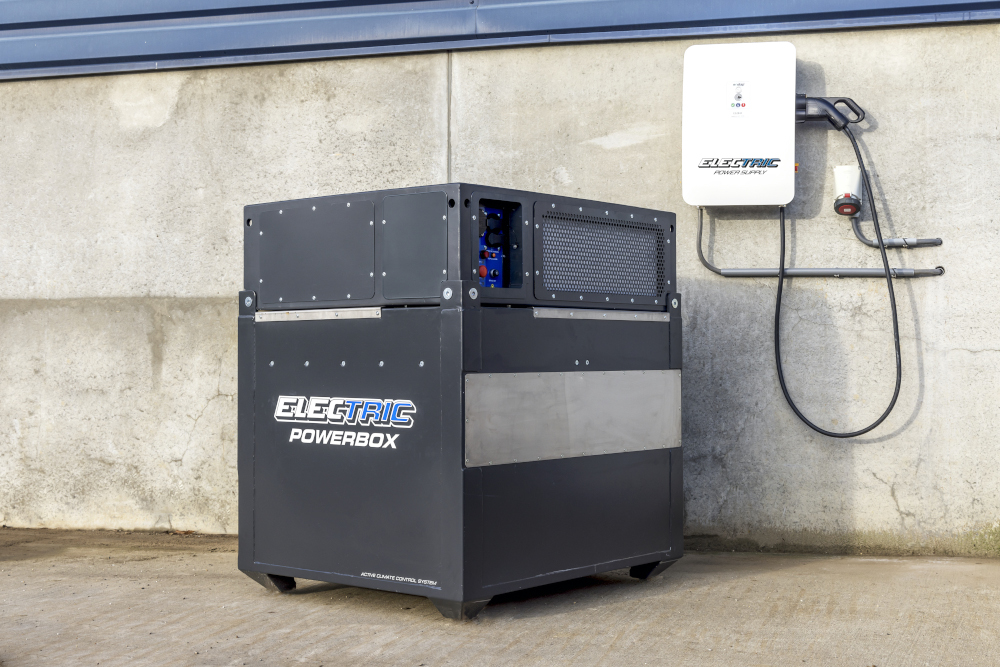
“We made quite a few other structural changes to prevent the electrification resulting in too much of a weight increase,” Van Hal says. “For instance, most of the ballast in the original two excavator models was replaced by battery weight.
“Weight distribution is an indispensable foundation of how excavators move and operate safely. So a lot of practical measurement and CAD simulation was performed to understand the weight of the engine, the ballast, all the other heavy components, and how each contributed to the overall weight distribution, in order to understand what we had to recreate when choosing where to place all the electric powertrain systems.
“We eventually came to the conclusion that we didn’t really need any of the original counterweighting thanks to the mass of the batteries. So out of the original 3.5 t of ballast on each vehicle, there’s only a 600 kg steel plate left.”
Swappable battery packs
As mentioned, the HV buses in the electric DX165W and DX300LC operate at 800 V. That is achieved through the design of the proprietary battery system known as the PowerBox. Developed by ECE, each PowerBox contains four CV Standard battery packs supplied by Webasto – two in series, two in parallel, each pack containing 35 kWh.
The DX165W Electric contains two PowerBoxes and hence stores up to 280 kWh onboard, while the DX300LC Electric carries three of them for a total of 420 kWh. Each PowerBox is roughly 135 cm wide, 107 cm long and 130 cm tall, and weighs about 2.2 t.
“When we were looking for a battery supplier, we wanted one that had good experience in heating and cooling, because these vehicles needed to function in the Norwegian winter as well as the southern European summer,” Van Hal says.
“We also wanted a supplier in Europe, to ensure our supply chain resilience. A lot of our r&d took place not just during the Covid-19 worldwide lockdowns, and also when the Evergreen container ship blocked the Suez Canal and much of the international shipping. So we couldn’t entrust our future to the potentially onerous shipping times from China, not to mention the lack of face-to-face support from working with partners outside of Europe.”
This r&d was also performed with key assistance from Webasto. The Germany company customised the design of the packs to the specifications given by ECE to suit the construction vehicle environment and swappability that the latter sought to tackle in the PowerBox architecture.
Charging systems
Some readers may be familiar with swappable battery concepts from their use in e-scooters, e-motorbikes and e-tricycles around the world: the packs interface and fit into conformal slots as cartridges.
The PowerBox architecture is much the same, but at a larger scale for the electric DX165W and DX300LC. As excavation jobs can sometimes run in excess of eight hours, and such jobs are far apart from each other with only a driver and a construction worker present, ECE’s customers needed an approach by which packs could be replaced by one person with no electrical engineering knowledge, to enable a digger to continue working.
The electric DX165W’s eight packs and the DX300LC’s 12 are accessible via a panel at the back. A system of HV interlocks across the packs is engaged while a given digger is working, to prevent hazardous removals. Once the digger stops working and is turned off (and thus rendering the HV networks, LV networks and HV interlocks inactive) a worker can physically unplug each pack as they so choose, and slide them out of the PowerBox’s racks via lifting points atop the packs.
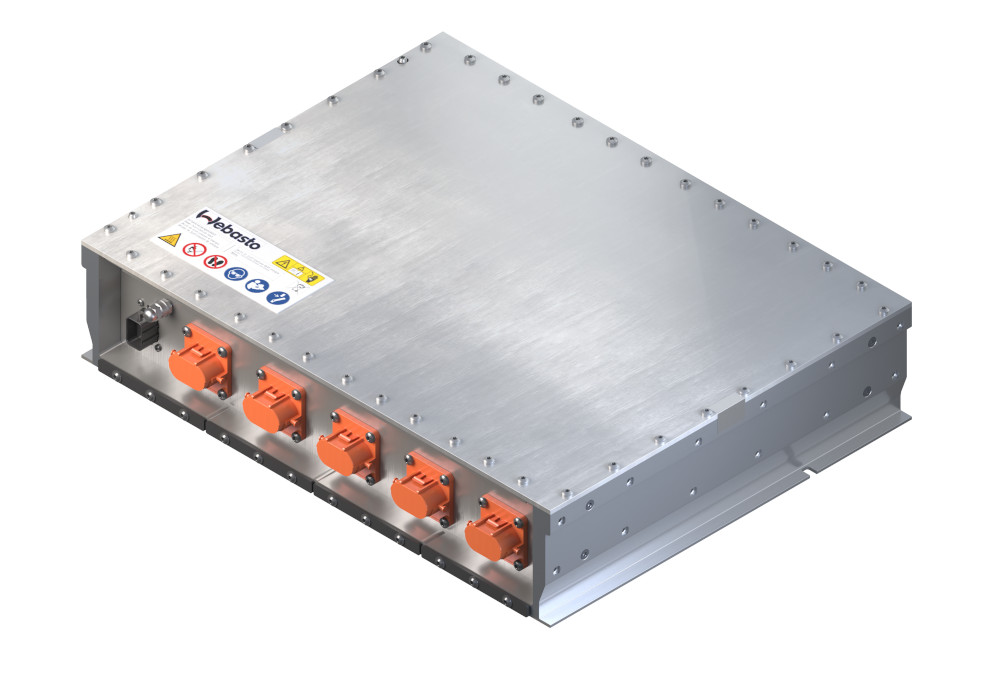
(Courtesy of Webasto)
Given the weight of each PowerBox, ECE plans to provide a trailer for carrying packs to and from the customer’s charging station. It will feature a mobile, electrically powered, manually operated crane for lifting and moving the batteries.
“Designing and engineering this swappable battery approach took weekly videoconference meetings between Webasto’s engineers and ours,” Van Hal says. “We did the primary drawings and software, while they performed important tunings and changes from their side to make sure the solution worked and was practical.
“They continue to provide good development support alongside a regular supply of batteries and related components. And it was a useful partnership for them too: they now know a lot about what it takes to make batteries that work for construction sites, particularly in terms of charging systems and battery behaviours.”
The swappable nature of the excavators’ battery packs means that construction yards can develop their own charging areas using whatever HV or LV outlets are available on site, theoretically close to or inside a designated battery storage warehouse.
“There are also two 22 kW AC charging ports behind the cabin of each excavator, near where the counterweight plate is, so we can also recharge the packs at up to 44 kW while they’re installed on a machine in a lifespan-preserving way overnight,” Val Hal adds. “Meanwhile, there are CCS2 ports on the individual packs that allow them to be fast-charged at 140-150 kW via DC during lunch breaks.”
Each AC charging port is controlled by an onboard charger from Stercom, which was selected because it is based nearby, in Germany, and hence easily contacted, as well as for its 800 V architecture – a rare quality among OBCs, ECE notes – and agile liquid cooling.
The OBCs connect to the PowerBoxes, which notably control the charging and discharging of the packs such that each 35 kWh pack is either replenished or depleted one at a time, rather than all packs across all PowerBoxes being consistently balanced for SoC. That ensures workers can swap completely empty packs for fully charged ones.
“So theoretically, each excavator can be kept working 24 hours per day, save for the few minutes it takes to replace a pack,” Van Hal says. “The software in the BMS controls the requests for charging to the OBC and the discharging to the roundabout.”
Battery modules and cells
The packs in ECE’s vehicles are made from automotive battery modules supplied by Samsung SDI. Inside the modules are prismatic, NMC-811 cells, with laser-welded compression, retention, and busbar components for the cells to ensure consistent long-term performance.
While the SDI modules come with a range of differently optimised cells, those in the ECE vehicles incorporate the HEV-type cells, which contain 5.2-5.9 Ah each and have been optimised for power density.
As Webasto explains, the excavators will often go from lifting no weight to suddenly lifting up 2 t of earth and swinging it around. That creates intermittent, sharp spikes in the loads on the batteries, and without cell technology formulated with high power discharges in mind, either the EVs’ lifting capabilities or the lifespans of the cells (or both) would suffer.
Each pack therefore contains 16 SDI modules, connected together for 400 V per pack, hence the 800 V output per PowerBox, when two pairs of packs are connected in series.
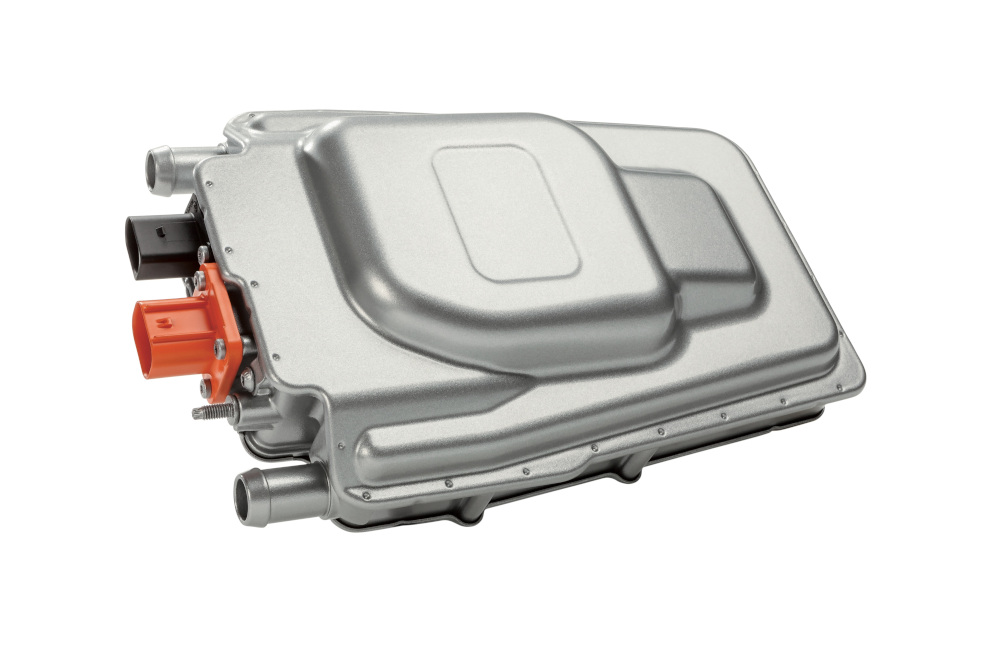
(Courtesy of Webasto)
Battery thermal management
While the packs contain these modules, also inside the main housing of each pack are two plates for water-glycol thermal management circuits for combined heating and cooling.
The plates are integrated as standard with each 35 kWh pack, as it is widely known that lithium-ion batteries are at their safest and most efficient when operating in environments of 25-30 ºC, a temperature range that is particularly challenging for ECE’s northern European customers to offer easily.
The plates are therefore installed in the tops and bottoms of the modules and cells of each pack, and when installed in the PowerBox they conduct heat to and from an onboard heating circuit as well as a refrigerant circuit. The heat circuit uses an 800 V heater combined with a heating pump, while the cooling loop uses 800 V e-compressors with a radiator for cooling. The high voltage design of these heating and cooling components minimises parasitic losses from thermal management.
Vehicle Interface Box
The BMS is housed in Webasto’s Vehicle Interface Box (VIB), which uses an automotive controller for functions relating to battery management as well as sharing key performance and health information with the vehicle control unit and ECE’s fleet management systems. It is also contained in an IP65-rated enclosure for ruggedness in the harsh construction yard environments.
The VIB tracks and manages battery temperatures, with sensors taking readings at 32 positions per pack, shutting off the packs if excess cold or heat is detected. It also balances power and energy across the cells, using Webasto’s Vehicle Gateway, the BMS software package provided as standard with the VIB. Also inside the BMS is a range of safety hardware features, including circuit breakers, overcurrent protectors and pre-charge resistors.
Cabin systems
Van Hal comments that the 800 V architecture was not only important for the PowerBoxes and e-motor, it also has had a significant impact on the development of the HVAC system. That’s because ECE wanted to use an 800 V compressor for the HVAC in the excavators’ cabins to minimise the part count and energy inefficiency of using a lower-voltage system with a DC-DC converter.
“Two years ago it was still very difficult to find 800 V air conditioner compressors, so at the moment our active excavators are using 24 V compressors with DC-DCs for the air conditioning, as well as the original HVAC interface panels as on the fuel-powered DX165W and DX300LC,” Van Hal says.
“That’s a different 24 V DC-DC to the one connecting to the cabin systems battery,” he adds. “That battery was also used on the original Doosan machines to provide a stable low-voltage power output of up to 3 kW – more than enough for the operator’s panels, lighting systems, controllers, and connectivity systems.
“But if we’d added the compressor alongside all those systems it would have brought us close to the discharge limit of that small pack. That’s why the compressor has its own dedicated converter and pack, identical to those of the operator systems.”
And while the fuel-powered excavators would use the heat from their diesel engines to warm their cabins, ECE uses electric heaters from Webasto (one per EV) to pipe heat in a liquid circuit around the operator’s station. Unlike the current compressor, that is an 800 V system.
Here, however, Webasto adds that it has now developed and certified an 800 V air-conditioning compressor for ECE’s Doosans, and that these will be integrated in 2023, replacing the 24 V systems and hence eliminating the associated DC-DC and its power efficiency losses. Webasto also notes that future architectures of the construction EVs might use the heat of the battery packs to warm the cabin, thereby replacing the electric heater or allowing the use of a smaller one instead.
“It is far easier to find 800 V compressors these days,” Val Hal adds. “They’re not as widely available as 300-400 V systems, but judging by the market trends we think 800 V HVACs will soon be the norm in heavy-duty EVs.”
Powertrain
While the electric DX165W and DX300LC can use the same compressors and heaters, since both house a single operator in their cabins with identical environmental requirements, the latter has a larger lifting arm and digging capacity as well as a greater overall mass, so it needs a much more powerful e-motor.
Both machines use motors and inverters from Danish industrial group Danfoss. As well as being a European supplier, the company specialises in designing electric motors for battery-electric or hybrid powertrains in mobile work machines, buses and marine vessels operating in harsh environments and demanding applications.
“Danfoss has its factory in Finland, and service partners across the continent, which means we and our customers can easily get maintenance or repairs done on the motors and inverters either face to face or by fast shipping,” Van Hal says. “Not only would it take far longer with a US or Asian supplier but even getting feedback would be limited by the time difference.”
The DX165W Electric is powered by an EM-PMI375-T500 motor, which provides power ranging from 66 kW up to 158 kW at operating speeds from 1100 rpm up to 4000 rpm respectively. It weighs 172 kg, measures 368 mm long and 450 mm in diameter, and outputs up to 3400 Nm of static torque or 2500 Nm of dynamic torque.
“On the DX165W we’re able to do all our lifting and traction with no more than 104 kW from the T500, with no difference for the operator in terms of the feel they get from their levers,” Van Hal says. “We could use more power to do jobs faster but for now customers are fine with it.”
The DX300LC Electric meanwhile uses Danfoss’ EM-PMI375-T800. This is a 428 mm-long, 450 mm-diameter, 210 kg machine that supplies 85 kW when running at 900 rpm and peak continuous power of 251 kW at 4000 rpm.
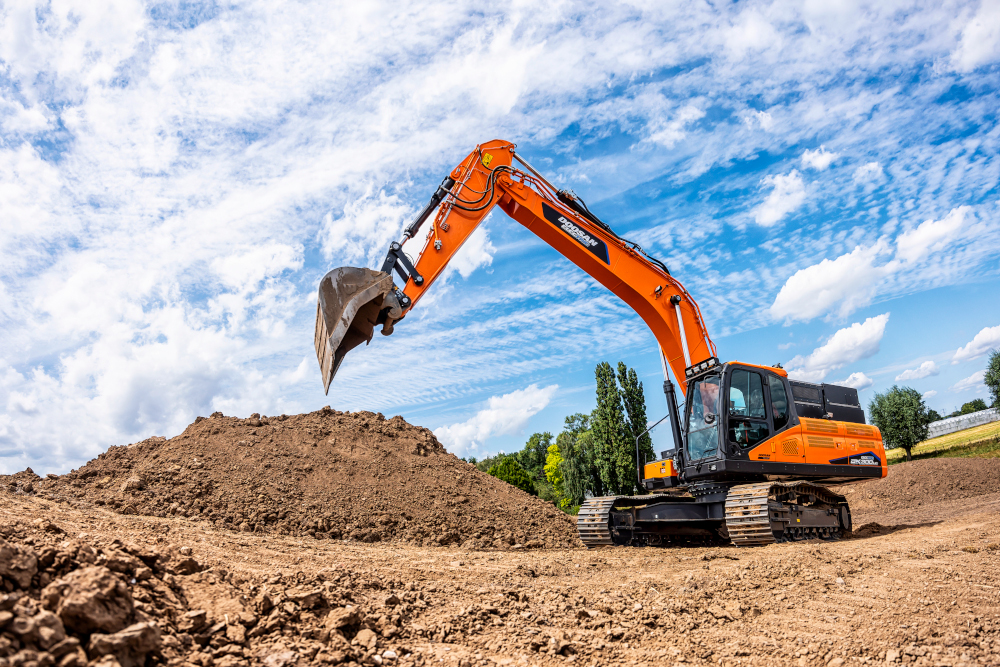
Both e-motors are reluctance-assisted synchronous permanent magnet AC machines with six pole pairs in their stators and internally mounted rotor magnets, capable of up to 96% power efficiency, built using aluminium frames and ruggedised to IP65.
Each motor’s shaft comes with an SAE-standard flange mounting to match the kind of connections typical of diesel engine shafts, which helps keep their integration into the Doosans straightforward.
The motors are also paired with Danfoss inverters, with common coolant loops running between the motor and inverter. A water-glycol mixture is pumped at a minimum flow rate of 20 litres/minute and at a maximum pressure of 3 bar, with a specified operating temperature range of -20 to +70 ºC for the liquid. The powertrain risks becoming derated if either extreme is surpassed.
Transmission and controls
As mentioned, the downstream parts of the excavators’ drivetrains – their lifting arms, booms, and buckets, as well as their traction systems – have been left largely untouched, with the electric powertrain and cabin systems generally being closer to drop-in replacements than requiring general overhauls of the machines, save for the aforementioned changes to the chassis and counterweights to accommodate the PowerBoxes.
However, there is an area of interplay between the powertrain’s electrical systems and the mechanical systems for use on the roads and at construction sites. There are also reasons why an e-motor can provide the same capabilities as a diesel engine without the need for a lot of new and thus expensive and heavy gearboxes to account for differences in speed, torque and acceleration.
It is also important to understand where hydraulic systems still have an advantage over existing electric and electromechanical technologies. ECE retained much of the hydraulics because its r&d found the hydraulics to be superior over electromechanics for applying force responsively at low cyclic frequencies.
The flange on the Danfoss motors means their shafts can be directly connected to and drive the hydraulic pumps just as the diesel engines would. These load-sensing pumps were developed by Bosch Rexroth, and in the DX300LC they are tandem variable displacement axial piston types with a maximum flow rate of 248 litres/minute each at 1800 rpm. The DX165W uses a pair of bent-axis axial piston pumps with maximum flow rates of 176 litres/minute each at 2200 rpm.
In addition to being the same models as on the original Doosan architectures, the means by which they transmit power to the digging and traction system works is also the same. As the operator pulls the control levers in their cabin, the hydraulic pump controller (also from Bosch Rexroth) sends requests for power to the EPOS (electronic power optimising system), which is the central computer that processes all the control inputs and functional outputs of each excavator.
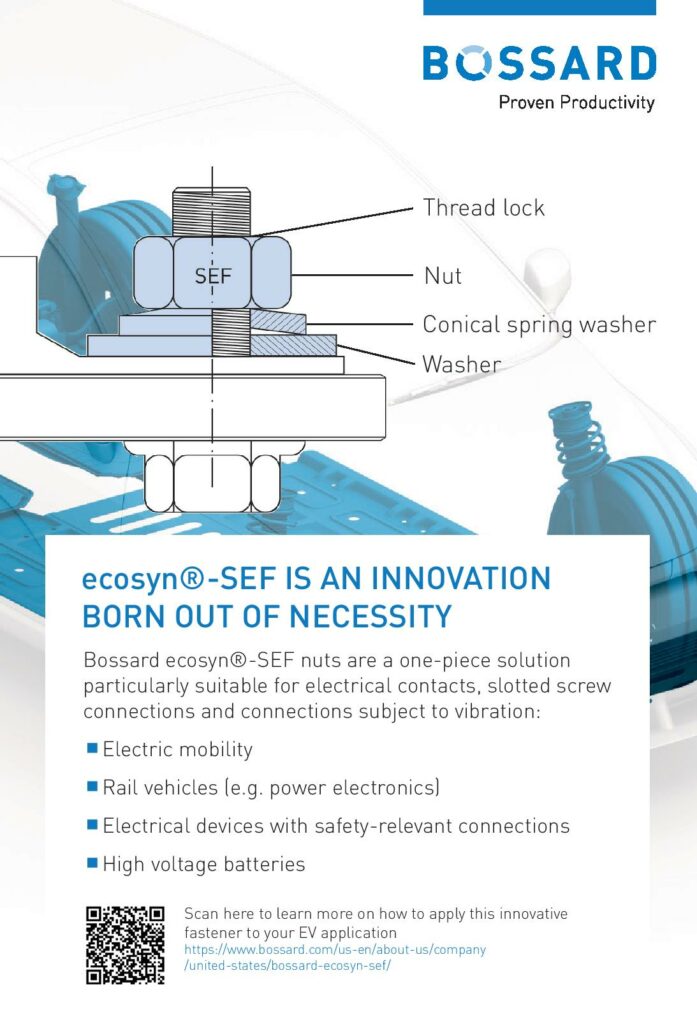
“The EPOS would calculate and request the necessary rpm from the diesel engine’s ECU to satisfy the power request from the hydraulics controller, and now we do the same, only we request the rpm from the ECU (also from Danfoss) on the inverter instead,” Van Hal explains.
“Feedback from the ECU goes then to the hydraulics controller, which sends signals as to whether the e-motor should speed up or slow down to get the right flow and pressure of hydraulic fluid going through the arm, bucket or travel systems. So essentially, the Bosch Rexroth hydraulic controller is the master and the Danfoss ECU is the slave; the latter listens to the former and adjusts its speed according to the command signals it receives.
“And remember that the hydraulic pumps are limited to speeds of 1800 and 2200 rpm, which is why we don’t run the e-machines at their peak power outputs just yet. It’s a limitation in terms of speed, but the power at which hydraulic fluid is pumped doesn’t affect the downstream power with which the arm and bucket lift, or the power used for movement.”
“The outward flow from the pumps is controlled by valves that split the fluids going to the arm, boom, bucket and drivetrain. Each valve has an integrated pressure sensor to tell the controller whether it should be requesting higher or lower speeds from the e-motor.
“They can also be configured to open simultaneously or for one to shut when a conflicting system is in use. For instance the bucket’s valve typically shuts off fluid flow to that system, hence restricting its movement, when the traction system is in use.
“And in addition to the high-pressure hydraulics for all those systems, a low-pressure hydraulic network runs from the operator’s levers, pedals and steering wheel for sending manual control signals to the different systems’ valves via the hydraulics controller,” Van Hal says.
With hydraulic force governed via these valves, the DX165W’s pumps allow for up to 34.3 MPa of liquid pressure, which translates to 350 kgf/cm2, during lifting work and 36.3 MPa during traction. The DX300LC’s pumps are configured for the same pressure and force despite their design difference, so it follows that the smaller excavator is less likely to require the maximum possible hydraulic force while working or being driven.
As mentioned, both EVs’ motors drive a pair of hydraulic pumps: while the first covers the lifting actions, as discussed above, the second is for travel and bucket actuation. The second pump driven by the DX300LC’s T800 motor directly propels three hydraulic axial piston motors. The first of these is used for rotating the cabin, and hence also the lifting arm. It also drives an oil-immersed two-stage planetary reduction gear, in order to rotate the cabin at up to 9.88 rpm, with up to 12,137 kgf/m applied.
The other two axial piston motors each work one of the drive tracks for the DX300LC’s traction through a planetary reduction gearbox. Each is an independent, high-torque motor, whose controllers respond to CAN signals coming from a pair of foot pedals in the cabin. They and the gearboxes are protected by the track frames, as are multi-disc track brakes, which are applied via springs and released via the hydraulics.
On the DX165W, the second of its two hydraulic pumps drives a hydraulic motor that connects to a pair of ZF axles: a rear axle upon which the hydraulic transmission mounts for optimal protection and ground clearance, and a front axle designed to achieve wide oscillating and steering. And like on the DX300LC, this pump also drives an axial piston motor with a two-stage planetary gearbox, at up to 14.6 rpm with 3608 kgf/m.
Braking is achieved through disc plates engineered for working on wheels rather than treads. Initial actuation of the brake and steering systems is performed by dedicated gear pumps, with valve-controlled auxiliary circuits connecting the hydraulic fluid to these systems.
Despite the parasitic losses inherent in hydraulics, ECE plans to continue using them for the foreseeable future, not only for their greater practicality over electromechanics but also because replacing them would drive up the total cost of ownership. However, a lot of room for improvement is still possible through the control software, Van Hal notes.
“For instance, the hydraulics controller by default still requests 900 rpm of the e-motor when idle, because that’s the speed the diesel engine idles at,” he explains. “Soon we’ll be testing a patch that changes this command to request just 100 rpm or maybe 0 rpm of the electric machine, because the pumps only ask for idle when they don’t need any power.”
Computation and connectivity
As discussed, the main vehicle computer executing the operator’s commands for excavation and movement is the Doosan EPOS, which holds the intermediary algorithms between the hydraulics controllers and the e-motor.
“It’s through that original Doosan EPOS that the operator is also able to control key safety-critical functions such as braking and steering, and it also manages the display screen,” Van Hal says.
“The EPOS connects via an SAE-J1939 standard CAN 2.0 bus to the Rexroth controllers managing the lifting and traction drivetrains. Based on what the Rexroth systems communicate, the EPOS sends rpm requests to the powertrain ECU, and the ECU communicates with our main controller for the electric conversion-related systems, overseeing the power distribution, the onboard charger’s controller, the BMS, and our low-voltage subsystem controllers for the cabin and the HVAC.”
The main controller is a Danfoss Plus+1 MC050 machine management system, designed principally to function as part of a distributed network of intelligent control nodes such as that in the electrified Doosan excavators. The M050 is powered by a 32-bit ARM Cortex-M3 processor, which has 512 kbytes of internal flash memory and features a nested vectored interrupt controller (NVIC) for processing up to 240 interrupt signals with low latency.
The NVIC can also be used for assigning priority levels to signals within the bus coming from different sections of the electric powertrain based on user configurations, with the possibility for dynamic reprioritisation, which might be critical during safety-hazardous scenarios such as motor failures or battery packs running excessively hot or cold.
Also, as can be inferred from the name, the MC050 comes with Danfoss’ Plus+1 guide software, which is designed as an assistive graphical tool for machine application software development, without its end-user needing to be experienced in programming. It is designed to allow modular dragging and dropping of function blocks into algorithmic flow diagrams, enabling rapid addition or exchange of modules for managing sensors, valves, pumps and motors, as well as allowing for PID control, ramp rates, and filters, all the while generating source code directly from the end-user’s graphical drawings to minimise program errors.
“There’s also some remote connectivity and control systems worth mentioning,” Van Hal adds. “For instance, operators working in winter environments will want to preheat the cabin so they don’t freeze in the early hours of their work. That’s possible through the Webasto remote app, which connects to the excavator via 4G to activate the electric heater and HVAC system.
“We’re also adding further connectivity systems ourselves for remote tracking of system health parameters, such as for the state of the battery packs and motor. We’re developing a cloud-based monitoring and analytics module in-house, since it’s important for users’ long-term costs of ownership to record and evaluate trends in battery SoH, SoC and temperatures.
“Users also want to be able to track such trends throughout the night and in the morning before they arrive at a site, that any packs or machines left to slow-charge overnight have in fact been replenished. More fundamentally, they want to track the locations of their machines, error codes, stationary time spent charging, current consumed, and other work efficiency-related metrics. We’ve therefore also installed GPS and 4G antennas atop the cabins to make all that possible.”
The connectivity system is also being developed for bidirectional comms, so that owners of the electric excavators will in future receive texts or e-mails alerting them of such matters as safety-related issues, charging progress updates, and energy efficiency reports.
Future construction EVs
In addition to continued development and improvement of the electric DX165W and DX300LC, ECE is now working on electrifying other construction vehicles.
“One of these is a tractor, and the first prototype is now in its fifth week of trials for commercial work in the field,” Van Hal says. “We’re using the same components and drivetrain engineering philosophy as in the Doosans, and we expect to continue using them as we take the tractor from testing through to production.”
The tractor is likely to be used for transporting goods and materials in bulk to, from or across construction sites, including the aforementioned trailer for battery swapping.
“We’re also working now on electrifying a wheel loader. Converting a loader is more complex, but construction companies need to move earth over greater distances than is possible with the DX165W or DX300LC,” Van Hal says.
“Because of all these different heavy-duty jobs with different machinery requirements, customers need a lot more than what is available commercially right now. It’s going to take electrifying the full ecosystem of construction vehicles to decarbonise building sites, and it’s important that we continue using common battery packs, controllers and other electric components between them to make maintenance and ownership convenient for new adopters.”
Specifications
DX165W Electric
Weight: 17 t
Bucket capacity: 0.64 m³
Maximum digging depth: 5.02 m
Voltage: 800 V
Battery capacity: 280 kWh
Peak power: 158 kW
Maximum speed: 40 kph
Typical speed: 35 kph
DX300LC Electric
Weight: 34 t
Bucket capacity: 1.27 m³
Maximum digging depth: 7.3 m
Voltage: 800 V
Battery capacity: 420 kWh
Peak power: 251 kW
Maximum speed: 5.5 kph
Minimum speed: 3 kph
Some key suppliers
Battery packs: Webasto
Battery modules: Samsung SDI
Active thermal management systems: Webasto
BMS: Webasto
Onboard charger: Stercom
Motors: Danfoss
Inverters: Danfoss
Hydraulics: Bosch Rexroth
Axle: ZF
ONLINE PARTNERS
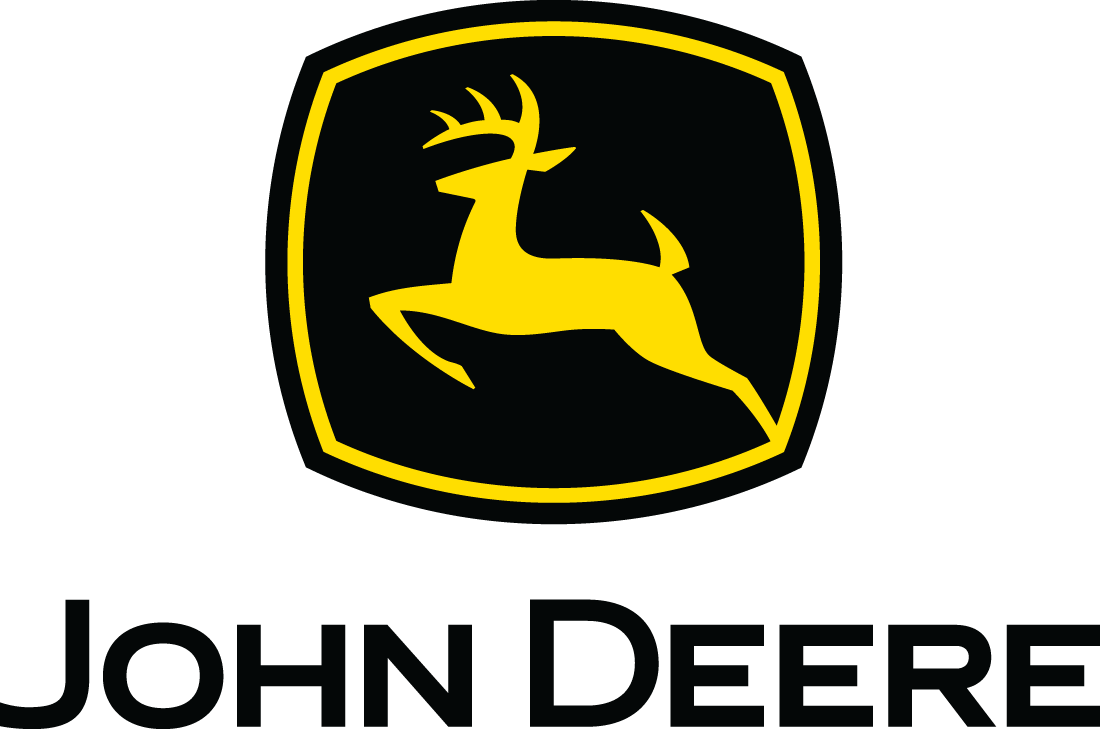
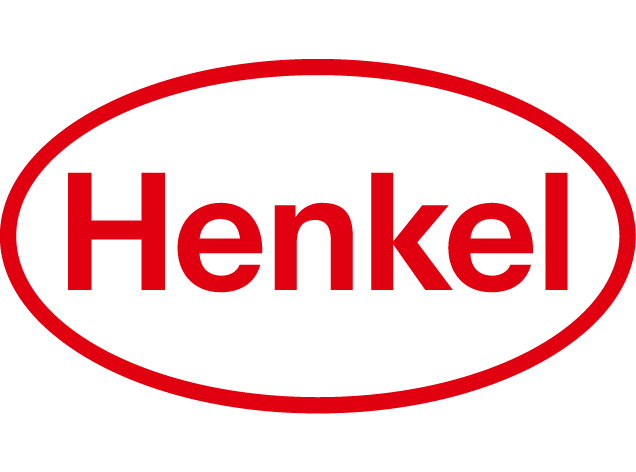
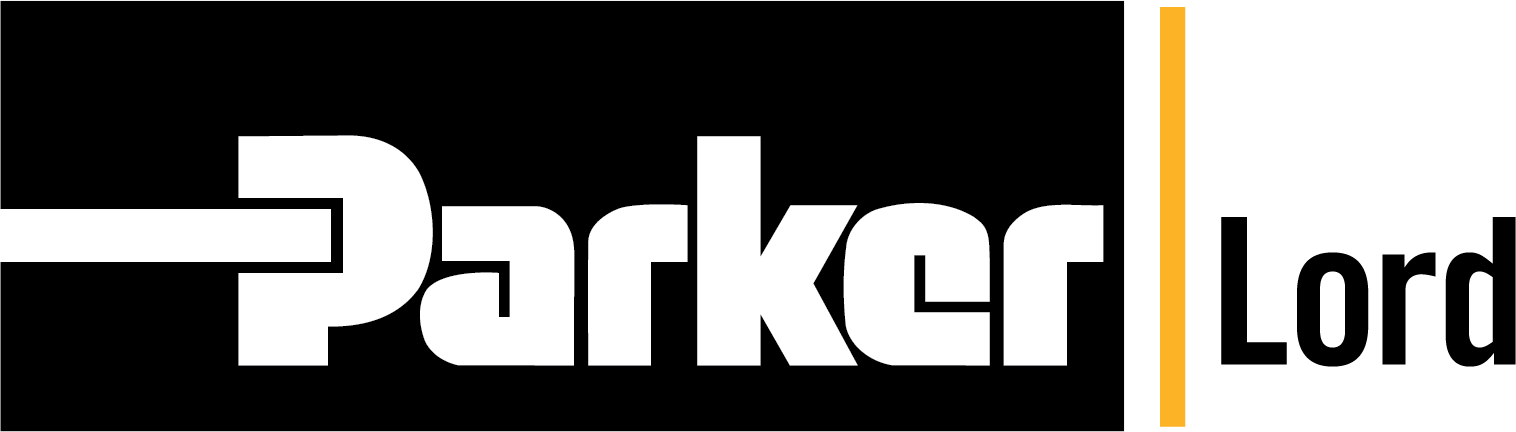
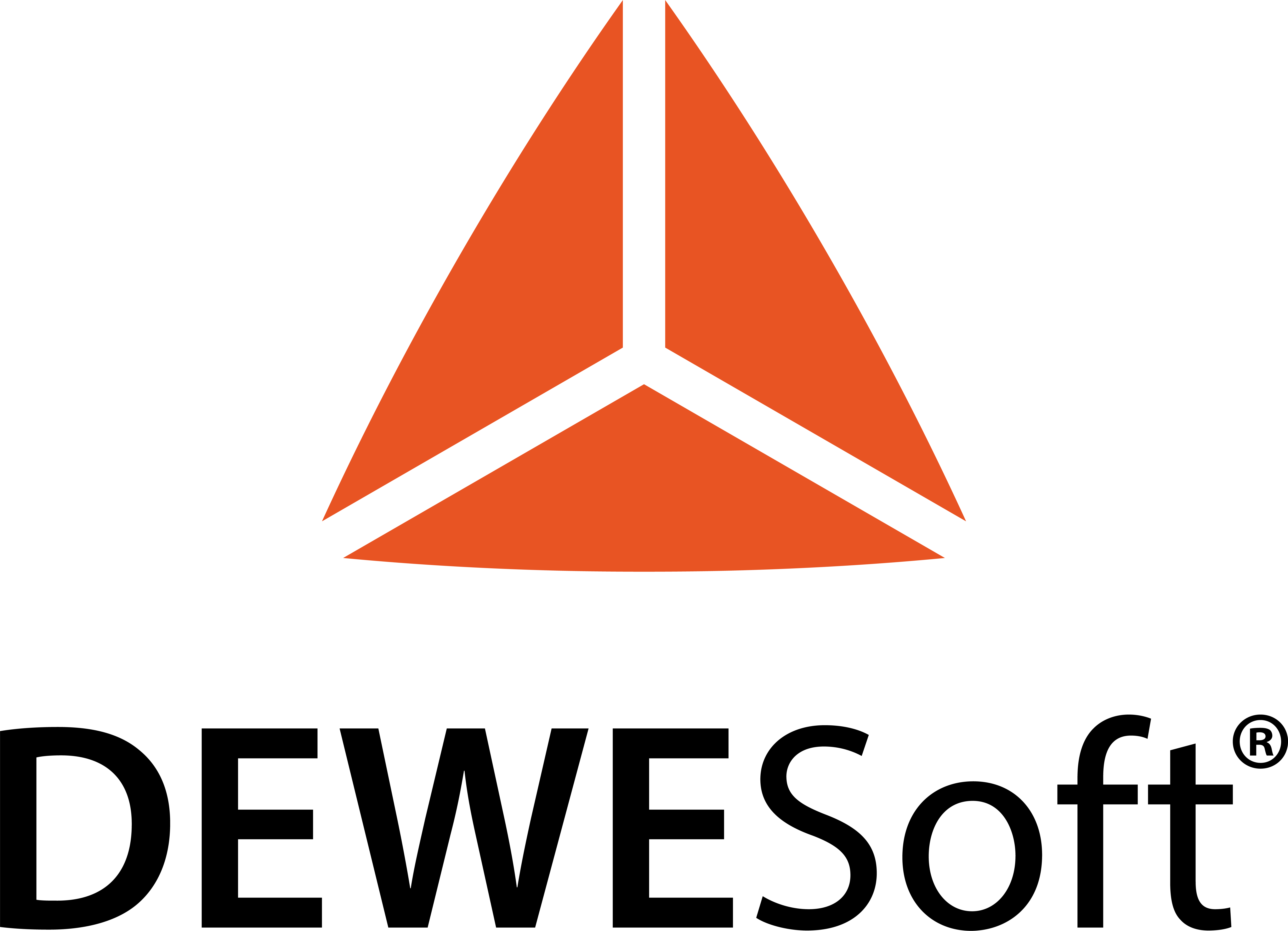
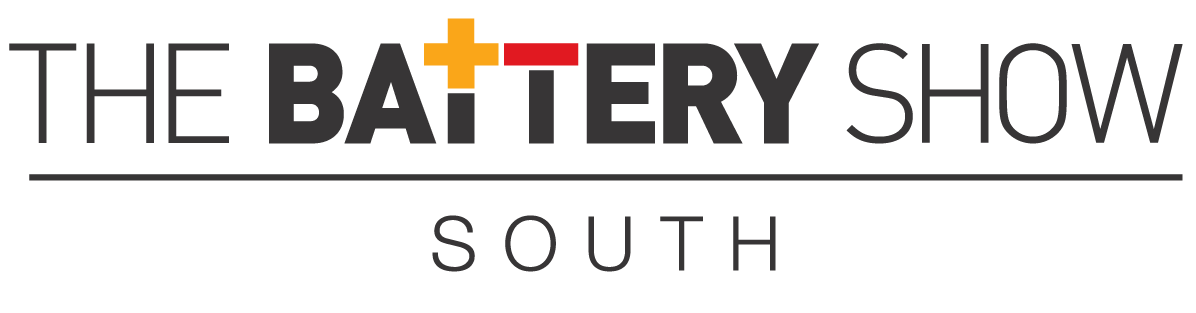
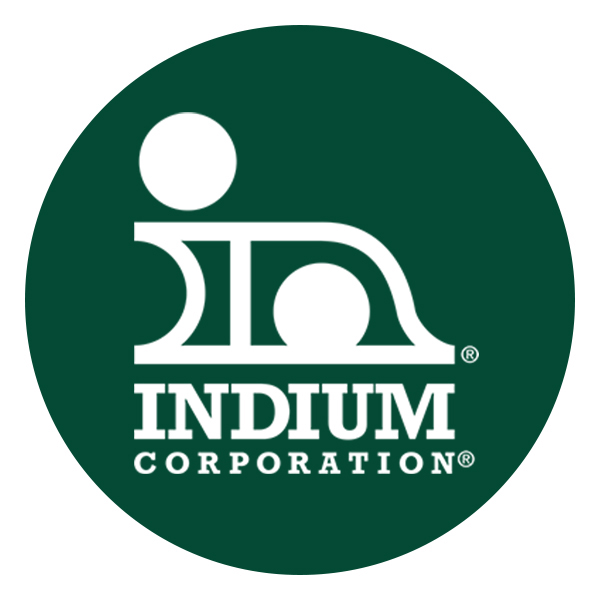
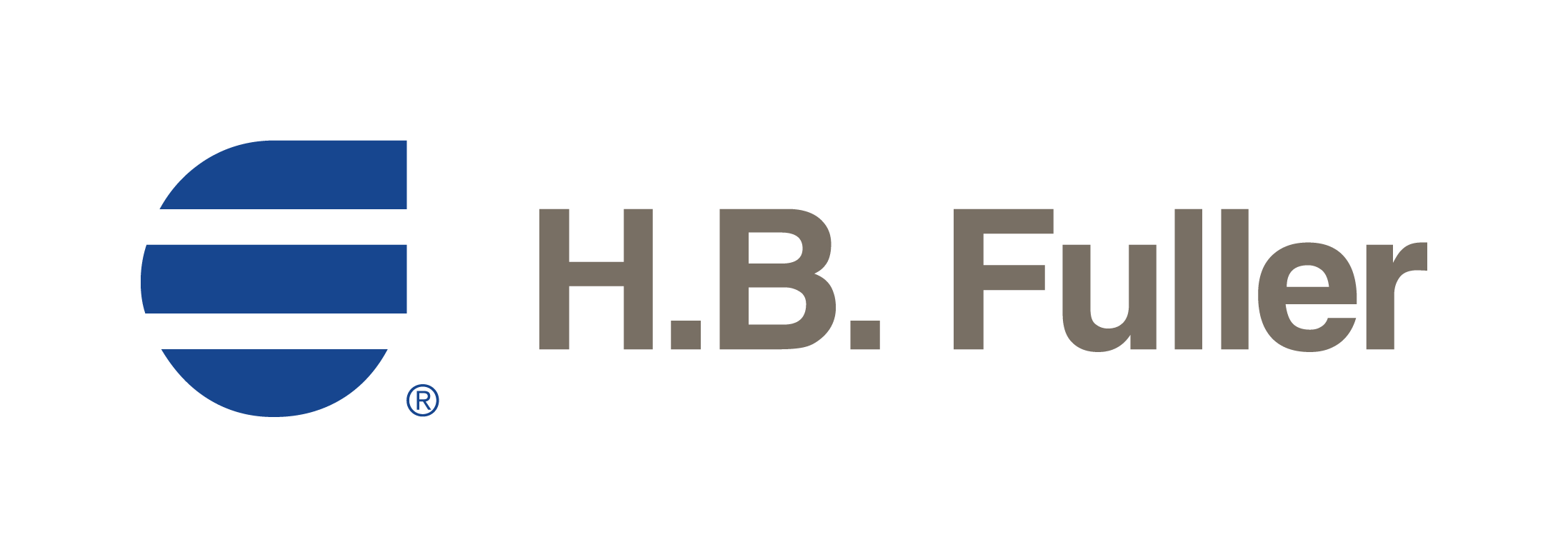