Dyno development
For ICE powertrain companies looking to transition into e-powertrain engineering, the construction of the new test cells poses on of the biggest cost-barrier to entry, writes Rory Jackson.
High-speed dynamometers and test benches capable of measuring the performances of e-motors are inevitably pricey, and many such companies already possess significant testing equipment for cycling combustion engines.
However, conventional ICE dynos are often designed for diesel- or gasoline-type engines running from 3000-to-10000 rpm, and are therefore ill-suited to the 20,000-25,000 rpm speed limits that e-motors may need to be operated to.
To bridge this gap and make the transition process easier for such companies, tectos GmbH has developed its new tGear solution.
The main part of this system packages a gearbox and torque meter together. It connects on its frontal input side to an e-motor’s output shaft, and to a conventional ICE dyno on its opposite interface via an assembly consisting of a constant-velocity (CV) shaft and mechanical adapter.
The tGear therefore translates the high input speeds of the e-motor being tested down to a slower output speed for compatibility with the ICE dyno’s comparably lower speed limits. It has a maximum input speed of up to 30,000 rpm, with its gearbox enabling reduction ratios from 2:1 up to 7:1.
The solution’s operational lifetime is rated to 20,000 hours, with oil and filter changes recommended every 2,000 hours, as well as routine checks of the clearances.
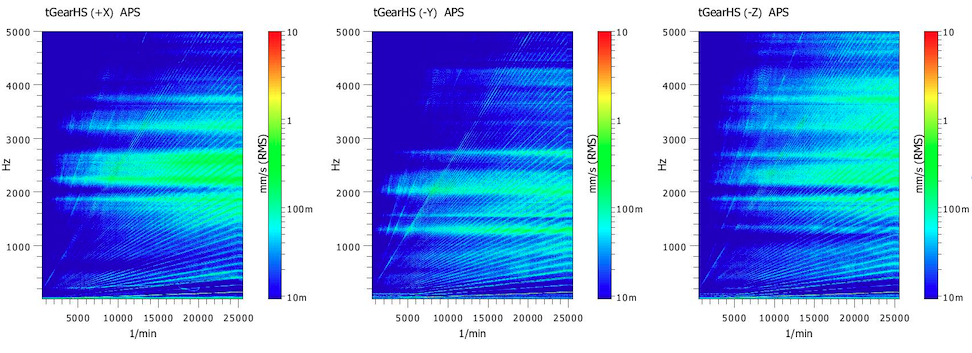
(courtesy of tectos GmbH)
As Dieter Höfler, CEO of tectos explains to EME, “Our engineers have made sure that tGear works independently of whatever dynamometer or e-motor the end-user is working with; it’s compatible with all dynos, because it connects through our CV shaft and adapter system instead of needing to connect directly to the dyno.”
Being a purely mechanical system – with no electrical interfacing required – it can also test both asynchronous and synchronous electric motors. Höfler adds however that they may add an Ether CAT/SPS interface for PT100 monitoring in the near future, based on requests from some customers.
The engineering and vibration-optimisation of the gearbox drew upon several years of experience and intensive development work by tectos’ NVH specialists across numerous different types of drives (the company declines to disclose details on exact arrangements of gears and vibration isolators used).
“The tGear is mounted on a base frame using a corresponding adapter plate; for the cooling of the interface, a domestic water supply with a water/glycol mix of 50:50 at about 20 C and with a flow rate of <20 L/min is used,” the CEO notes. “We have kept the mounting systems as simple and safe as possible.”
The cooling and lubrication system forms the secondary part of tGear. This section consists of a box containing oil, with a pump, filter, and heat exchanger.
From that box, oil is directed to the upper part of the gearbox and fed to its areas in need of lubrication. It is a closed-circuit system, fed with water from the domestic water supply for cooling, and can be mounted directly above the main gearbox, or elsewhere thanks to the flexible system of oil lines for feeding and return of oil to the secondary box.
ONLINE PARTNERS
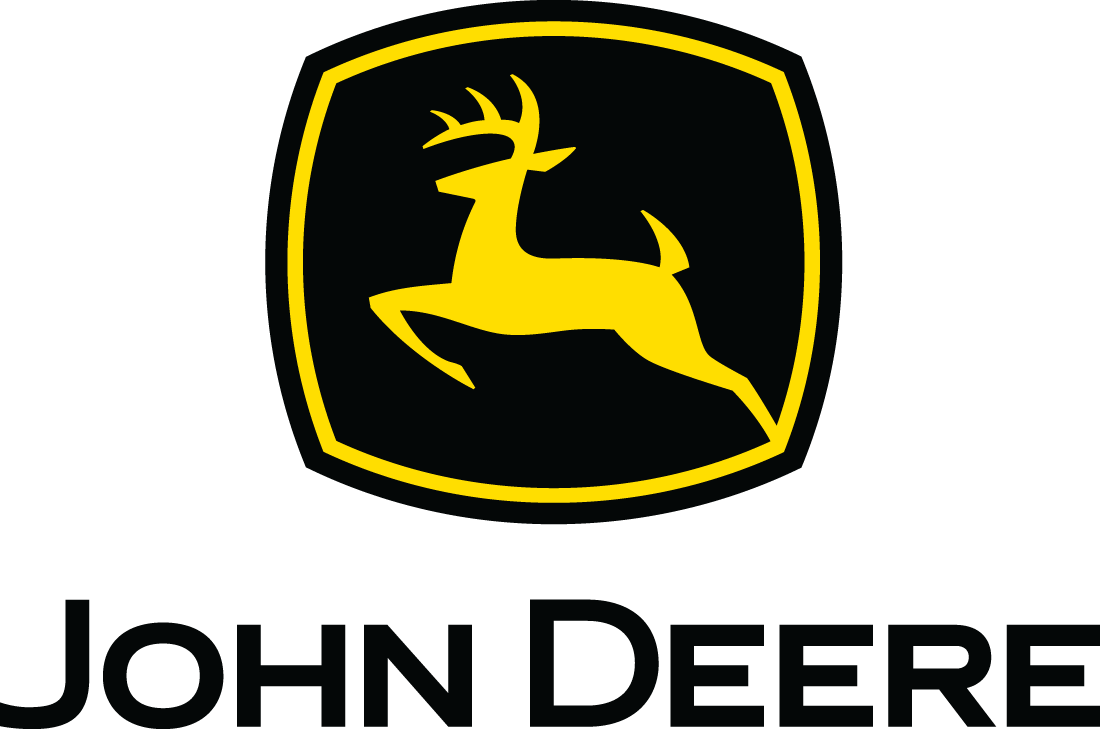
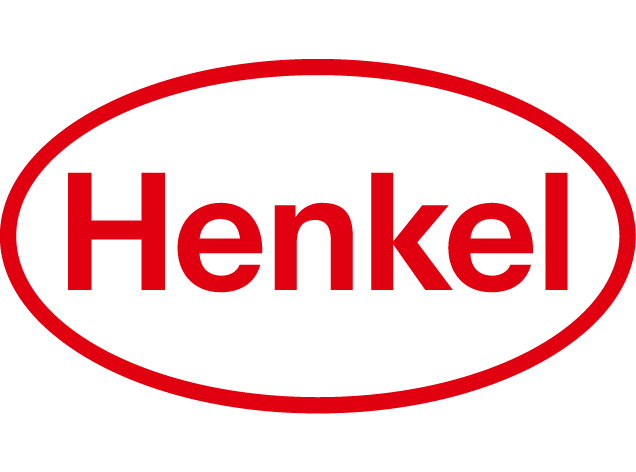
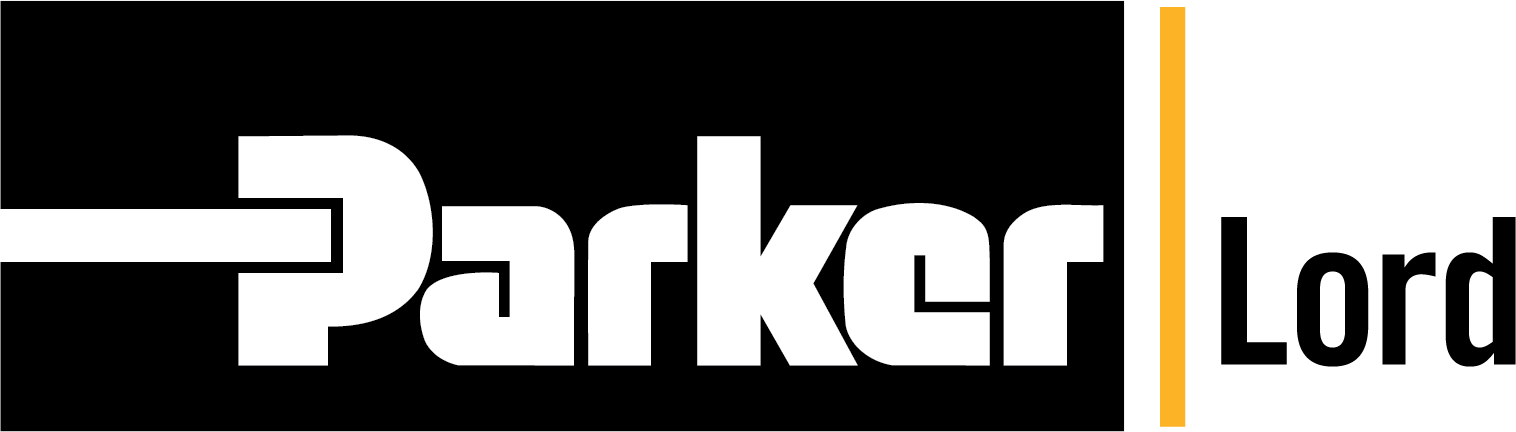
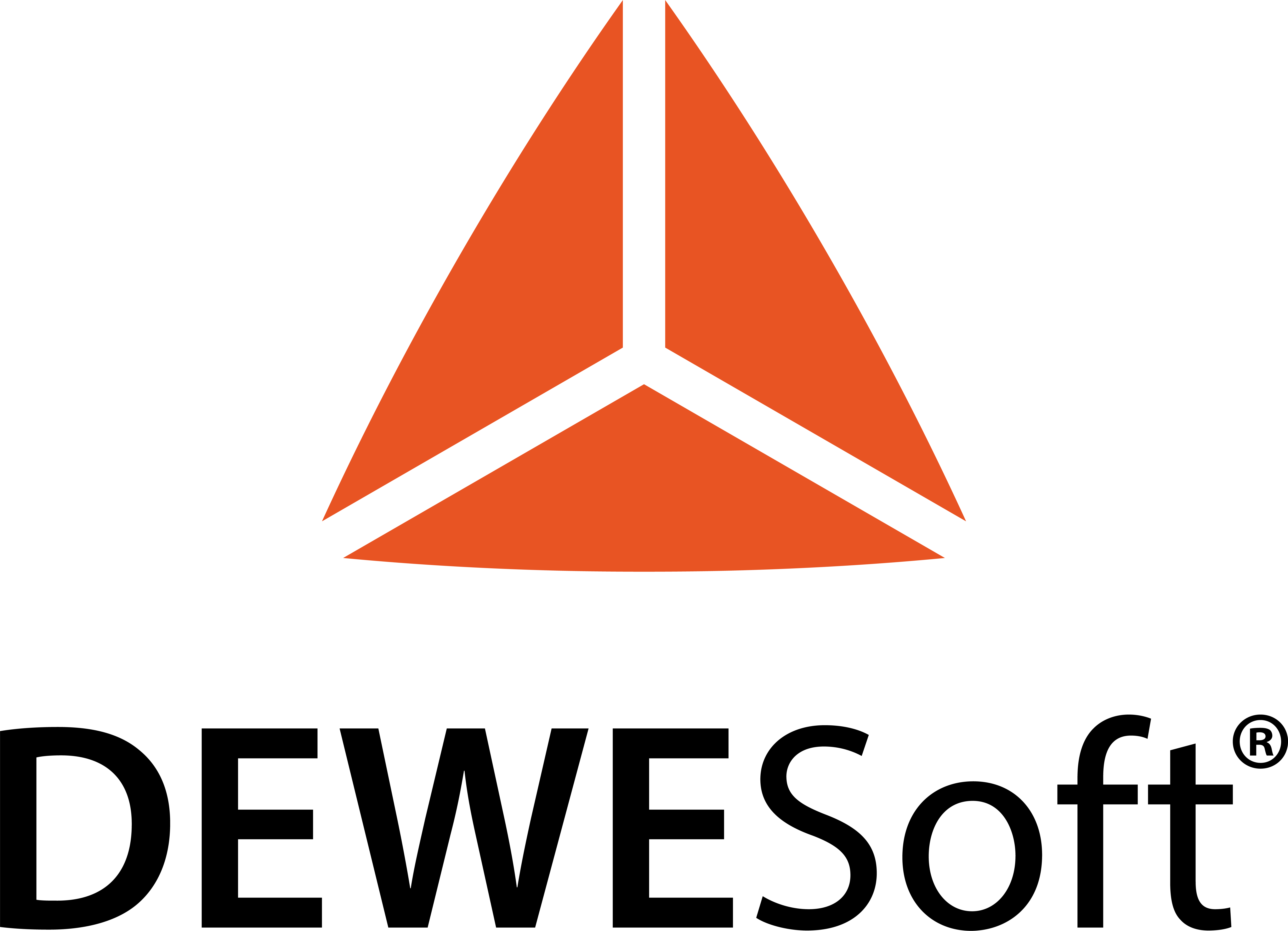
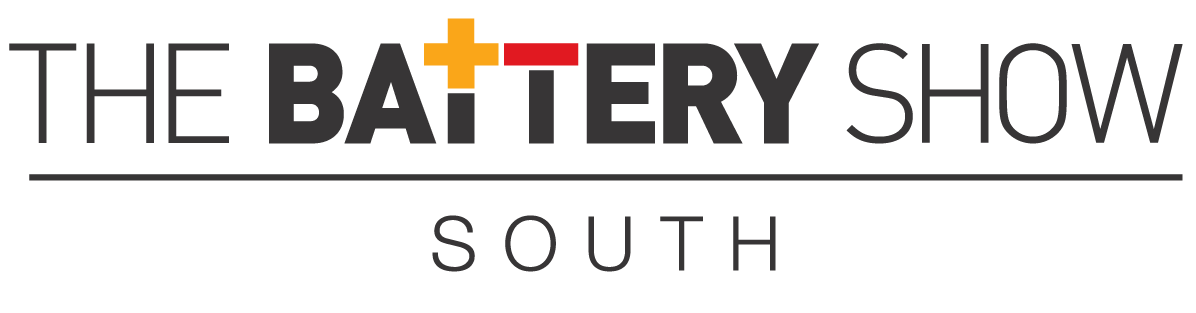
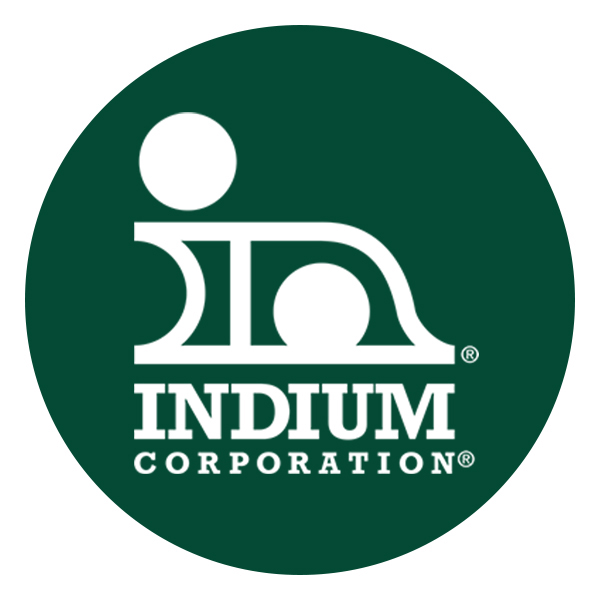

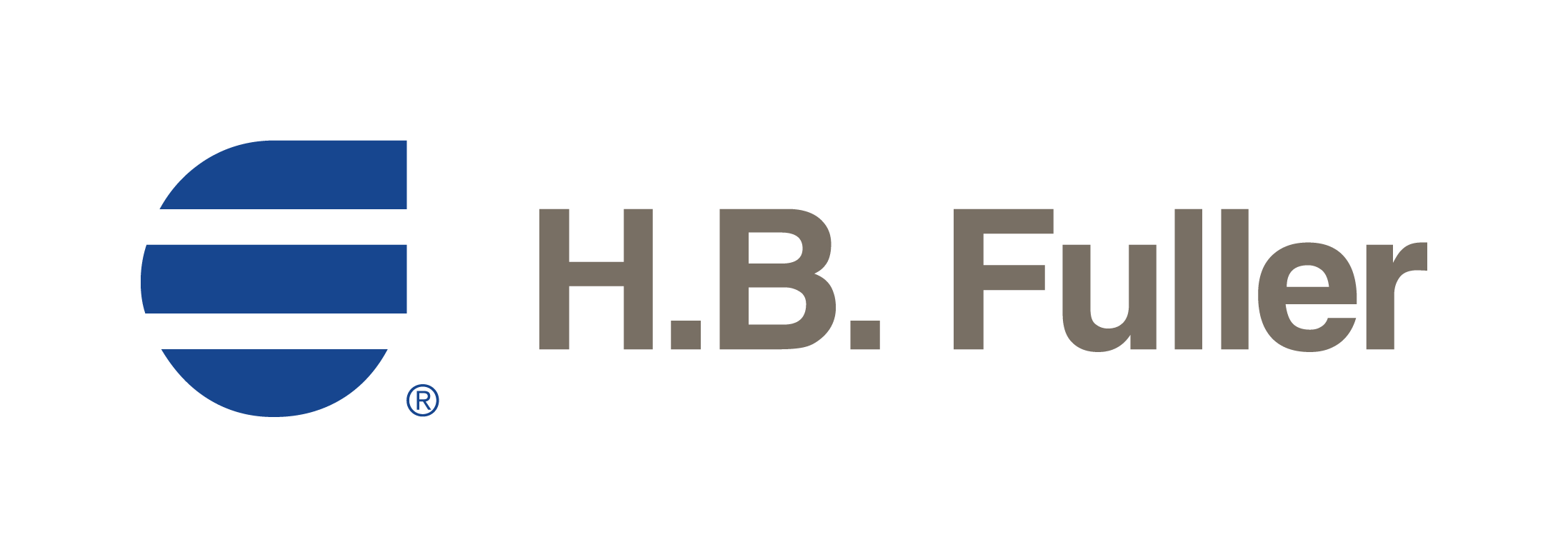
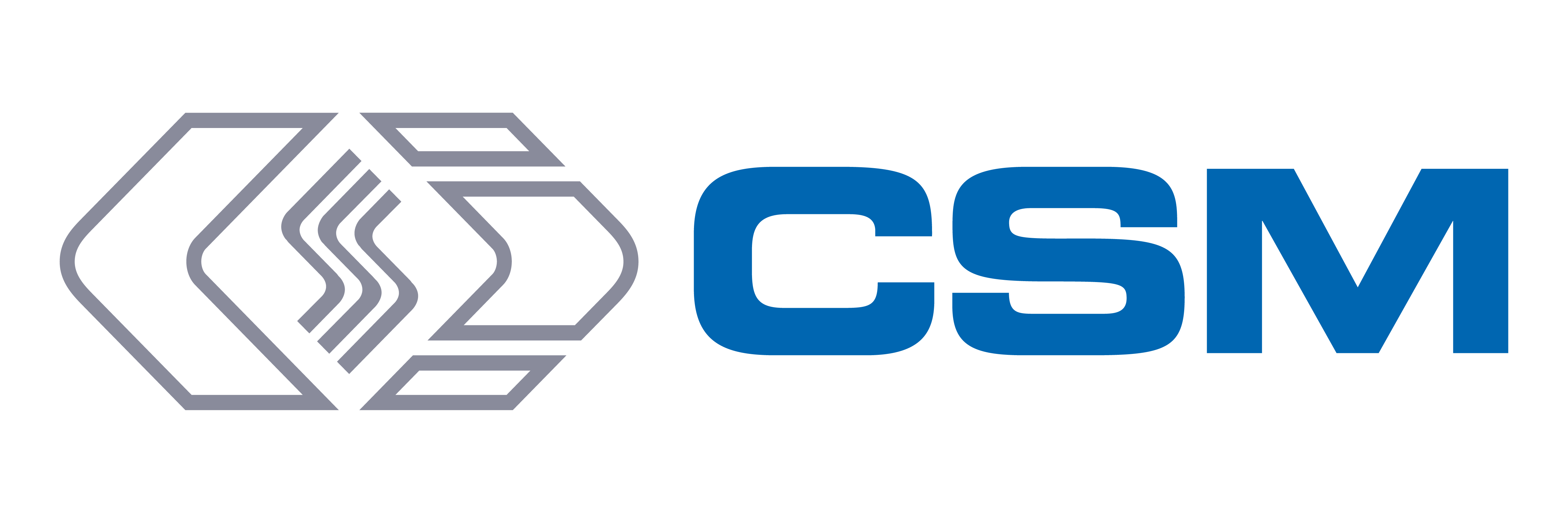
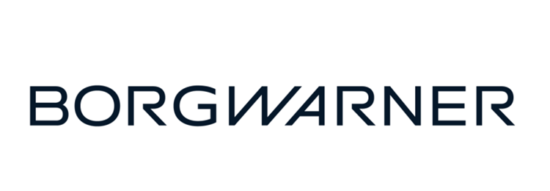