BB Green ferry
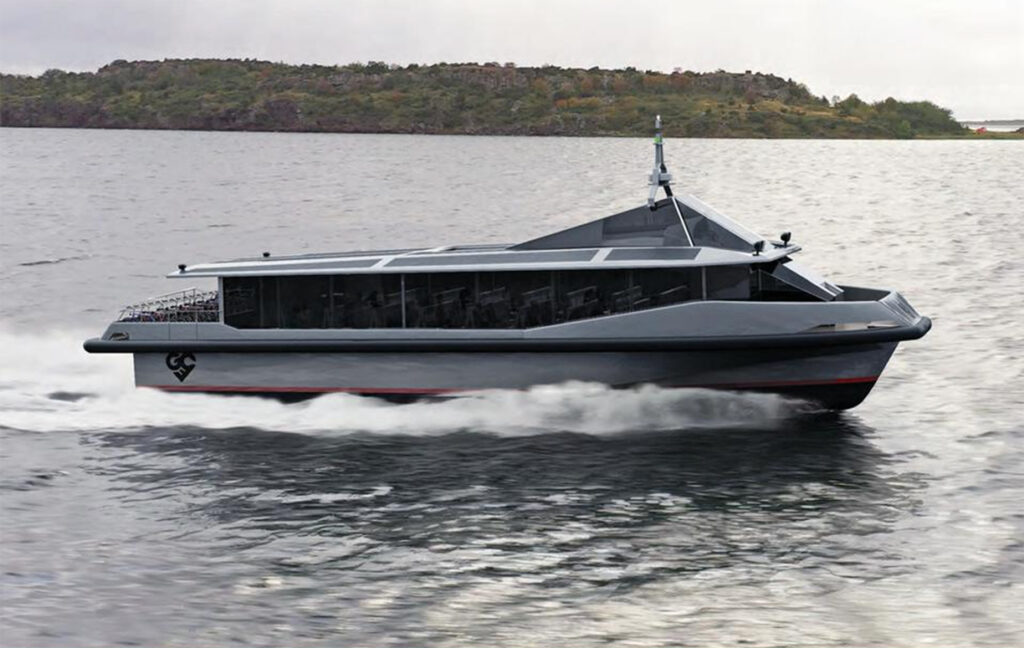
(Courtesy of Green City Ferries)
Rory Jackson looks at the development of this battery-powered ferry, which is aimed at shuttling workers to and from work.
Good news for commuters
As more and more people find work in the major urban centres of the world, traffic congestion continues to worsen. While road networks struggle to cope with an ever-growing number of commuters, levels of driver stress and greenhouse gas emissions are rising everywhere.
The BB Green ferry from Stockholm-based Green City Ferries (GCF) has been in development since 2013 as a cost-efficient, high-speed commuter vessel, with the immediate intention of incentivising workers of all classes to switch from using northern Europe’s congested intercity highways to a series of marine networks.
The new, standardised model, the BB Green 24 has a 24.8 m length overall (LOA), a beam of 7.5 m, and is designed to carry up to 147 seated passengers. The 28 t vessel integrates 500 kWh of lithium titanate oxide (LTO) battery cells, which can be fully charged from empty in just under 20 minutes at a C-rate of 3 (although a maximum of 6C is currently possible, which gives a charging time of just under 10 minutes).
These charging figures are important, as Hans Thornell, CEO of GCF, notes, “To be attractive, a commuter ferry must be able to offer more frequent departures, shorter travel time, pleasant experiences and no emissions, which will be possible with the BB Green 24.”
These supply the vehicle’s powertrain to consume 25 kWh per nautical mile at a cruising speed of 26 knots, and can travel at up to 35 knots.
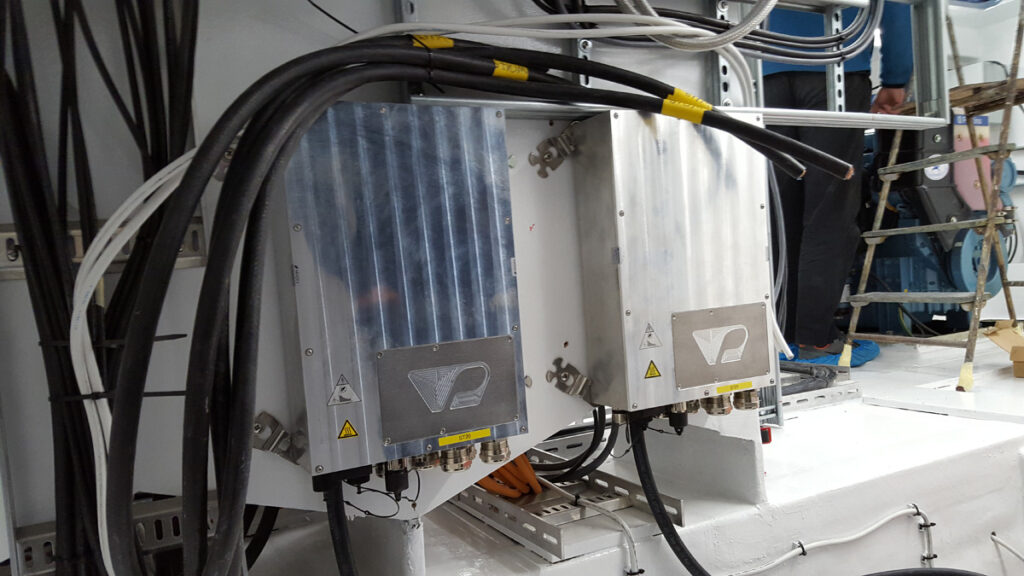
(Courtesy of Echandia Marine)
Project history
As Thornell recalls, 2013 was the first year that he and Magnus Eriksson, CEO of Echandia Marine, started pitching the idea for a battery-electric ferry, receiving €1m in r&d funding later that year from the Swedish Power Agency.
In 2014, GCF and Echandia unveiled their first proof-of-concept, the Movitz, which was the first serieshybrid passenger ferry to operate commercially.
“The Movitz project took about six months, in which we were the first company in the world to replace a ferry’s fuel powertrain with an electric one,” Thornell says.
“The charging station in the city centre of Stockholm could charge the battery in 10 minutes. That charging time was what first garnered huge attention for what we were trying to do: potential customers around the world finally saw that electric ferries really were commercially viable.”
The development of the BB Green itself began in earnest following a €2.2m grant from the 7th Framework Program of the European Commission to create a high-speed air-supported vessel.
That grant (and the consortium established around it) placed Echandia as the driveline systems integrator, working alongside such partners as Diab (who supplied foam cores for composite materials), SES Europe (who developed the air-supported hull technology), SSPA (who performed the tank testing) and others.
Another two years of development followed, with the first BB Green prototype unveiled in 2016. Nicknamed the AiriEl, that ship integrated several key technologies including an air-supported hull design, lightweight materials, LTO batteries, and more.
From these, the ferry derives advantages in such areas as top speed, charging time, energy efficiency, battery safety and cost-effective manufacture, compared with other electric commuter vessels.
The AiriEl was trialled in SSPA’s testing facilities for over 2000 hours (including running it up to speeds of 80 knots), before development began on a commercial version of the BB Green.
The commercially available iteration, the BB Green 24, integrates most of the same technologies and design points as on the AiriEl, while improving in key areas such as the motor and the cabin design.
A few initial routes along which the BB Green 24 might operate are anticipated. One is a 10 nautical mile route between the Swedish cities of Ockero and Gothenburg, with another between Stockholm and Varmdo – each of which would ideally have three ferries operating to minimise waiting times.
Further ahead, GCF also sees potential commuter routes across Norway, Denmark, the Netherlands, Britain, and several other nations where fast water commutes could be favoured over heavily congested roads.
GCF will handle the manufacturing, sales, and further development of the BB Green 24. Although the design of the production ferry is complete, the company anticipates that new technologies will periodically catch their collective eye as potentially worthwhile upgrades to the powertrain or hull.
Each different commute is also likely to merit some unique engineering to suit the exact ranges and routes to be undertaken on a day-to-day basis – presenting regular opportunities for GCF to update and optimise the powertrain by trying out new components. The company also expects eventually to design and build larger versions of the standard BB Green to handle busier commutes.
Echandia, on the other hand, is to focus on the energy storage and safety solutions innovated during the course of the BB Green project, conducting r&d on batteries, fuel cells and thermal management and safety systems that will be applicable to a range of heavy electric vehicles.
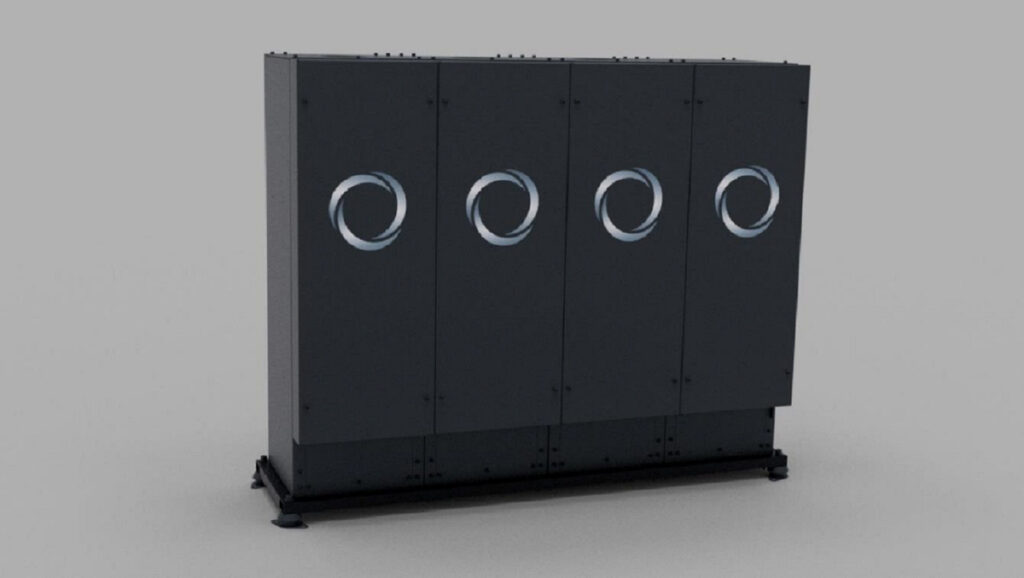
(Courtesy of Echandia Marine)
Power overview
“Cost-effectiveness is critical to the wider adoption of EVs; the initial reluctance from customers is always cost-related. To that end, our ferry has been designed to use just 25% of the energy typically used by commuter vessels of similar passenger capacities,” Thornell adds. “And that’s not even accounting for the speed and low maintenance costs of our system compared with ICE and hybrid ferries.”
While speed is not necessarily a vital target for most electric vehicles, the BB Green’s speed has a direct effect on its convenience and thus its commercial viability. As Thornell suggests, the average urban-coastal commuter will need to choose between their car and the ferry. If the latter takes far longer than 40 minutes, and arrives only every 30 minutes, they simply won’t choose to take the ferry.
The needs of the commuter must be balanced with the combined load of all the onboard systems. A simulation of the 48-minute Stockholm-to-Varmdo route suggests that the ferry would require roughly 372 kWh. The simulation consisted of several operating stages: at the start and finish, about two-and-a-half minutes were spent at 5 knots, carefully navigating the 0.2 nautical miles closest to either city’s seaport, during which the ferry consumed around 65 kW, for a total energy usage of 3 kWh.
In the approach to or departure from those relatively congested waters, the ferry moved at around 10 knots, running on 160 kW, and expended around 50 kWh across these two stages, which combined lasted about 11.5 minutes to cover the 2.3 nautical miles between the urban waters and transit waters.
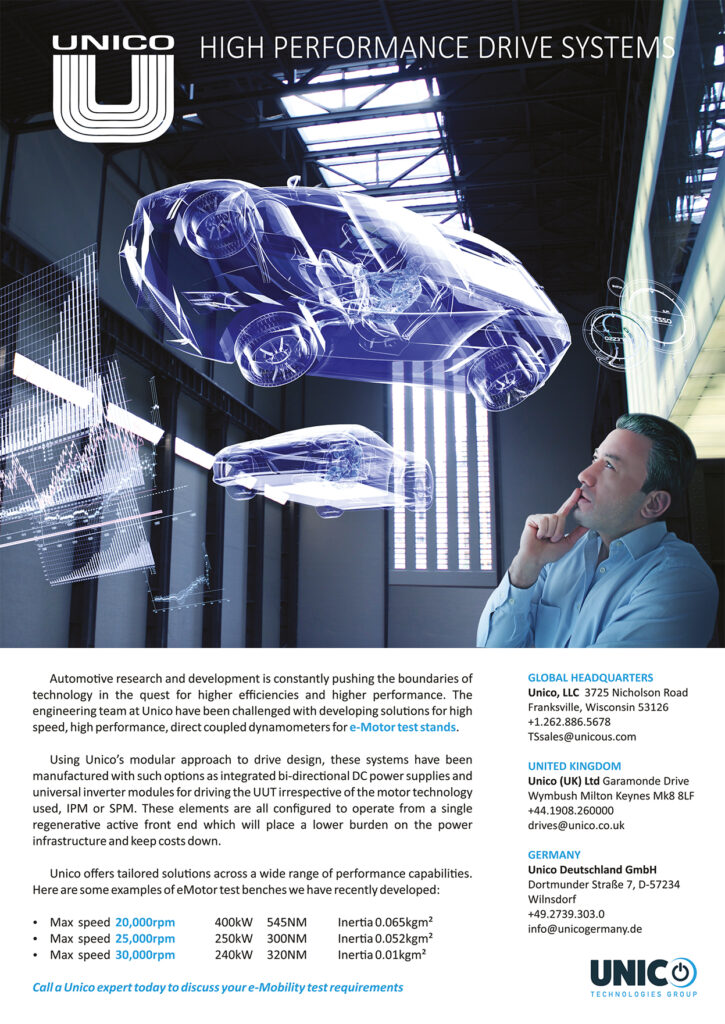
The main fast-transit portion of the simulated commute took 30 minutes, during which the ferry travelled at 25 knots, covering 12 nautical miles, and pulling 650 kW from the battery (meaning 322 kWh was used).
The BB Green 24’s 500 kWh of batteries in the centre of the boat connect to a switchboard in a back room, which directs power through a series of flexible bus bars to five liquid-cooled inverters distributed across the ferry. The inverters are largely designed around silicon IGBT power semiconductors and FPGAbased control algorithms, and were selected because of familiarity with their integration requirements and performance.
Each of the two propulsion systems at the back has two 160 kW drive inverters, arranged in a master-slave configuration. Additionally, an 80 kW inverter supplies AC power to the fan used to generate the air-support cushion beneath the craft.
Furthermore, a 90 kW AFE inverter serves as the low-power, slow-speed onboard charger, converting a 400 V, three-phase AC power supply from onshore charging stations into a DC voltage for the batteries. The fast ‘super-charging’ uses an input of up to 850 V DC and 2 MW, in order to fully recharge the batteries in potentially 1520 minutes.
Lastly, considerable energy storage must be allocated to cabin use, as Thornell and his team anticipate that almost every commuter will want to charge their personal electronics from their seat. Also, a number of cabin systems for environmental control, entertainment and other purposes will be available at each seat.
To that end, a number of smaller inverters are also installed to convert the batteries’ voltage to 230 and 400 V AC, and 24 DC outputs for the various cabin systems.
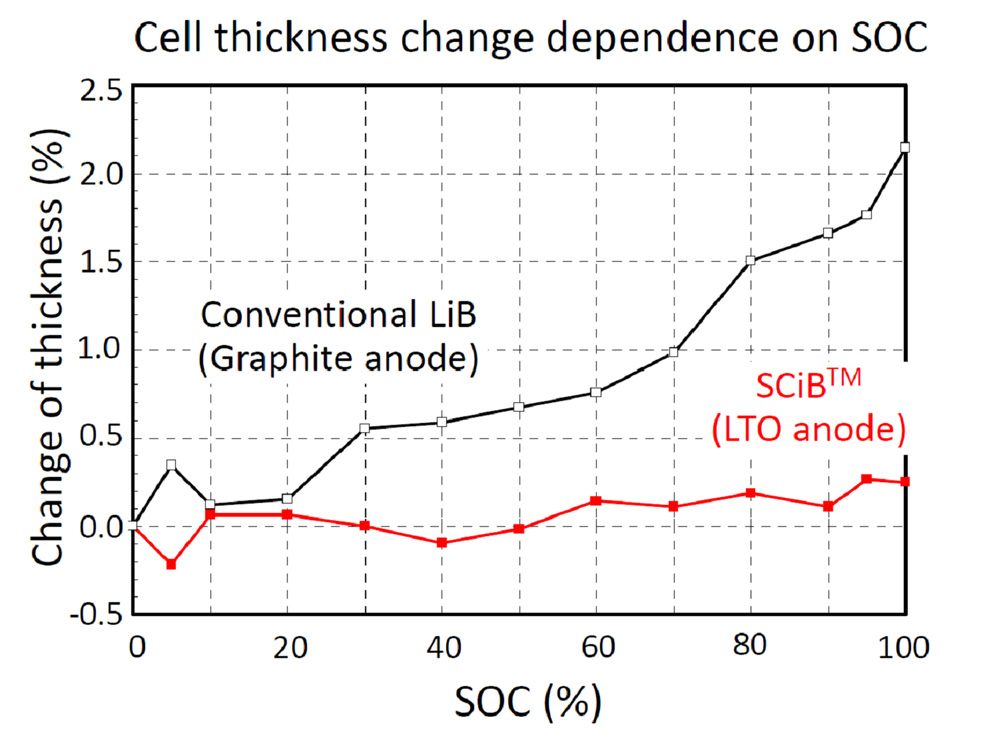
(Courtesy of Toshiba)
Battery integration
An array of novel technological systems has been assembled to provide for the BB Green 24’s energy storage needs. The battery and its surrounding subsystems (as well as the rest of the ferry’s powertrain) were designed and developed by Magnus Eriksson, the present CEO (and founder) of Echandia Marine.
The company has consistently used LTO cells from Toshiba’s SCiB (Super Charge ion Battery) series as the core of its battery packs and powertrain integrations, for the range of advantages this chemistry provides over their more widely used counterparts such as lead-acid or NMC batteries.
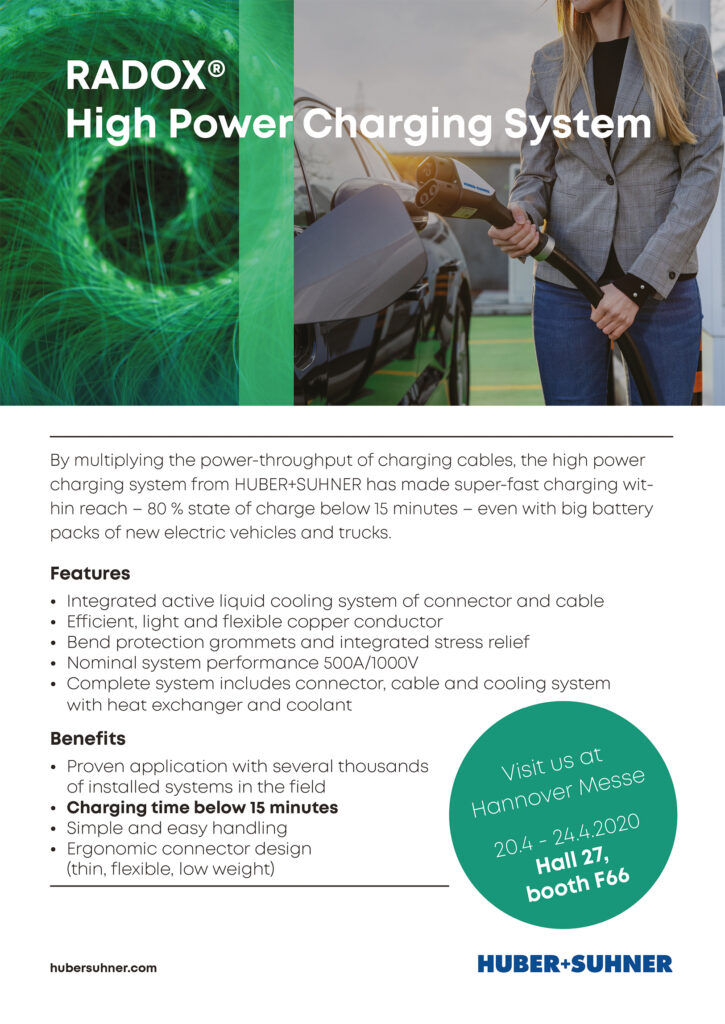
At the centre of the BB Green 24’s energy storage is Toshiba’s Type 3-23 module. Each module is made up of two strings of 12 cells (2P12S), and each cell holds 23 Ah of energy capacity with an energy-to-weight ratio of 96 Wh/kg, with an energy-to-volume of 202 Wh/litre.
This means that, at a size of 119 x 106 x 22 mm and a weight of 550 g per cell, each contains a maximum of around 52.9 Wh of usable energy.
Each cell operates at between 1.5 and 2.7 V DC (with 2.3 V as the nominal supply rate), with a nominal capacity of 23 Ah, and a continuous charging (and discharging) current of 160 A, although 350 A can be sustained for up to 10 s.
Eriksson explains, “Each battery module contains two sets of 23 Ah SCiB cells; each set is made up of 12 cells connected in series, and the two sets are connected to each other in parallel. And so the module’s nominal voltage of 27.6 V comes from that series connection.”
Overall, the BB Green 24’s battery room (a common feature on electric vessels) is set up in the centre of the boat with 14 strings of modules connected in parallel, and each string consists of 32 modules in series. That gives the aforementioned nominal 500 kWh of energy. The batteries are arranged in two racks running the length of the room, and have a bulkhead dividing them.
“For as long as Echandia existed we’d wanted to work with LTO cells, but for a long time they were too heavy and expensive to be viable – until around the time we started the BB Green project, that is,” Eriksson says. “We worked with a number of vendors before deciding to go with Toshiba’s LTO cell.
“And when we moved on from the Movitz to developing the prototype AirEl BB Green, we asked quite a few vendors to make a DNV-GL certified battery system for us, but they were all either too expensive or the vendors were too busy, so that’s what motivated us to make it ourselves and be our own battery system supplier.”
Echandia’s internal r&d resulted in a battery rack assembly with 50% less weight compared to that used on the Movitz. Eriksson also notes that the initial cost of LTO can be higher than NMC cells, but the former’s total cost of ownership (over their lifetime) can be far lower than the latter’s.
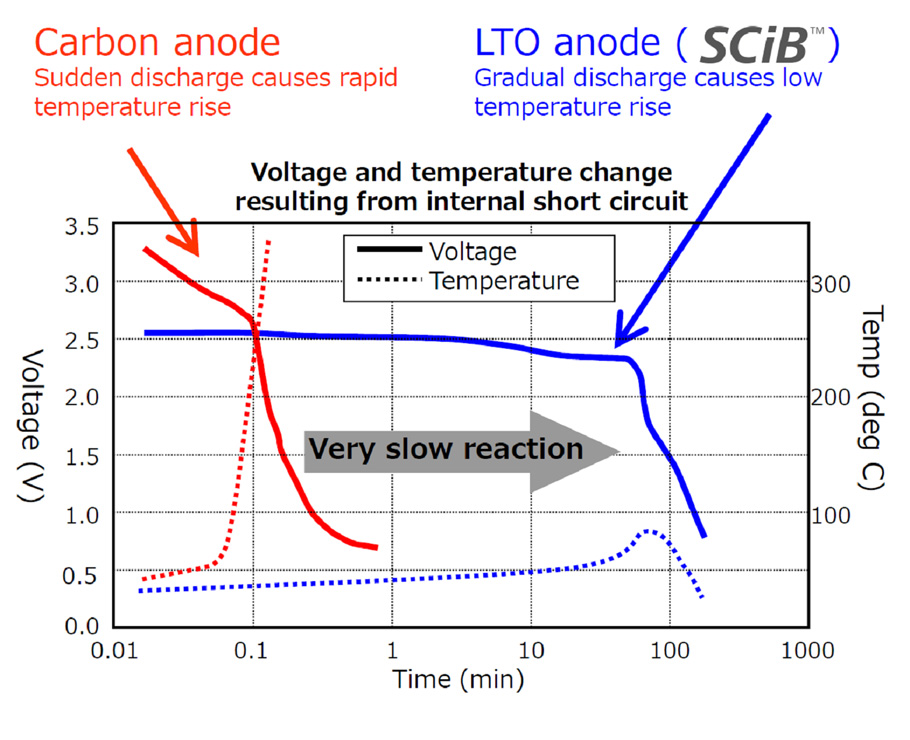
(Courtesy of Toshiba)
Lithium titanate oxide
In principle, the packs installed on the BB Green prototype and BB Green 24 are intended to power each ferry for 10 years, and they can be charged at a C-rate of up to 6 without significantly impacting their lifetime. After those 10 years, and the capacity of the LTO cells has dropped below 80% – the standard definition for ‘end of life’ in most batteries – GCF and Echandia anticipate selling them for reuse (without needing recycling) as stationary energy storage in solar or wind power stations.
LTO batteries also have certain safety characteristics that differentiate them from NMC packs.
In the former, lithium titanate (Li2TiO3) coats the anodes of the cells, as opposed to the carbon-graphite coatings used in those with the latter chemistry. Perhaps the foremost difference between the two is that Li2TiO3 molecules have a crystal structure that remains relatively stable in terms of how its volume changes with each cell’s SoC.
NMC and other carbon-graphite anode cells tend to change thickness by up to 2.1% at 100% SoC; LTO, on the other hand, is rarely (if ever) observed to change thickness by more than 0.25%.
“These constant volumetric changes inside the cell cause mechanical stress throughout them as they charge, whether they are pouch-type or prismatic, so it’s critical that those changes are reduced,” Eriksson notes.
“Furthermore, one of the reasons we’re able to resell our LTO packs after they’ve dropped to 80% capacity is that there’s little to no tendency for dendrite build-up in the cells over the long-term. That isn’t something we can do with any other chemistry, really.”
Dendrites of lithium are deposited as ‘plating’, and grow between battery electrodes – typically from the anode and towards either the cathode or the cell’s insulation.
A dendrite penetrating either of those can cause short-circuits and fire hazards in the long term.
The presence of dendrites and their growth rates are extremely difficult to measure when the battery is in operation. It can be attempted, for example by monitoring the deterioration in energy capacity or changes in internal resistance. However, these do not correlate directly with dendrite formation, and so will not accurately capture the long-term risks posed by lithium plating in a given cell.
One of the main reasons for dendrite formation are the high charging currents that can occur when a battery’s electrode potential falls to the lower end of its voltage range – below 1 V, for example. But LTO notably cannot form lithium dendrites, as its electrode potential cannot drop below 1.5 V. As a result, the ‘real’ working lifespan of the battery can run to 30 or 40 years.
“That’s important, because shortcircuits inside the cell can’t be controlled. It’s not like you can open up the cell and disconnect the terminals inside, that’s impossible,” Eriksson notes.
“And for similar reasons they work well in cold weather – tests indicate that they retain 80% of their capacity when running at -30 C. Overall, if you have a heavy-duty application with a very high frequency of charging and discharging, our battery works out much cheaper than NMC packs of equivalent power because it will last much longer for our application than NMC would.”
An additional safety feature inherent to the cell itself is observable by way of penetration testing, as piercing can also cause internal cell short-circuits. When pierced, carbon anode cells will suddenly discharge, which causes a rapid temperature increase in the cell, breaching 300 C in a little over 6 s, probably sending the cell into thermal runaway.
LTO cells, however, react far more slowly to such damage, taking nearly 10 minutes before showing any signs of discharge, and the internal temperature takes around 80-90 minutes to reach 80 C before gradually dropping back down to room temperature.
“The reason is that LTO goes through an internal phase transformation – it has a built-in current-limiting function,” Eriksson explains. “If there’s a penetration, the ohmic resistance increases so much that the current draw is reduced, preventing it from discharging quickly.”
The company makes a pointed comparison of its system with a ‘typical’ fuel-powered ferry, which consumes between 300 and 400 litres of diesel (generating around 1 t of CO2 and 10 kg of NOx and other small particles) per hour.
They also note that the widely used NMC-type batteries have been found to suffer adverse effects on their lifespan and a higher risk of thermal runaway when repeatedly charged or discharged at rates above 2C.
“The configuration of LTO battery cell we’re installing in the BB Green 24 can be charged at rates up to 6C continuously without affecting its lifespan,” Eriksson reminds us. “Their charging times will be determined far less by the limitations of the cell technology and far more by the spare energy capacity in their host city’s grid.”
As of January 2020, the final approval tests – EMC testing – of the BB Green 24’s batteries had been completed, and certification is expected shortly.
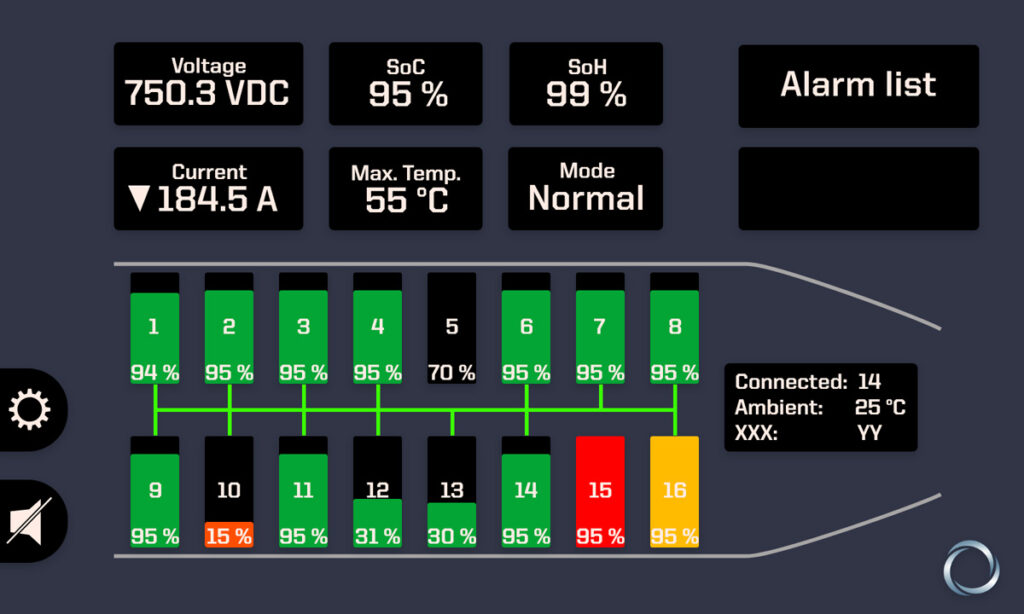
(Courtesy of Echandia Marine)
Thermal management and safety
“A fire broke out on a hybrid-powered car ferry in October 2019, which was caused by a leak in its battery’s liquidcooling system,” Eriksson recounts. “A gasket leaked water-glycol, which short-circuited a busbar, starting a fire that spread to the battery, causing the battery to start emitting gas.
“The gas wasn’t extracted properly, and during this event they used completely the wrong fire extinguishing media, as well as a salt-water sprinkler system, which caused several more short-circuits.”
The Echandia CEO brings up this point of reference, as the BB Green is designed with a comprehensive suite of safety systems that are different from those used in that incident. They are arranged as three system layers: cooling, gas sensors and firefighting.
The ferry’s battery packs are entirely air-cooled, even at 6C charging, having been successfully tested to keep the modules well within their operating boundaries of -30 to +55 C. Preliminary tests of the battery at a 9C charging rate are being conducted to determine whether air-cooling is still sufficient or if liquid-cooling may be necessary.
In the standard cooling configuration, a series of fans are installed beneath the battery racks to blow air up through the spaces between the modules, using convection to keep them within operating temperature.
“Next, we’ve integrated gas and smoke sensors in the ventilation ducts that run above the battery racks,” Eriksson explains. “Those ducts serve partially to recirculate cooling air but also, in the event of off-gassing we can detect battery gases the moment they pass through the ducts and vent them outside.”
Echandia selected the Li-Ion Tamer sensor model for gas detection, which is designed to provide at least 6.4 minutes (and potentially as much as 11 minutes) of warning before a thermal runaway can occur. It does so by detecting initial signature levels of carbon monoxide, ethane, and other components of lowlevel early battery off-gassing.
This deviates from many typical configurations that focus on smoke detection, despite many smoke sensors being unable to detect smoke until after a fire has already started.
And if a fire should still break out, the onboard firefighting system is configured to inject each compartment of the battery racks separately (as needed) with a direct-cooling foam.
A fully automated system for creating the foam (by mixing a stored foam premix with air from 300 bar pressurised air bottles) and distributing it where needed was co-developed by Echandia and Netherlands-based FiFi4Marine.
This foam is a water-based, biodegradable, non-toxic and noncorrosive mixture, thus helping to minimise damage and the risks posed to people in and around the battery room, or entering it afterwards.
“Remarkably few automated or manual firefighting systems – including for aircraft and land vehicles – use extinguishers with all of these qualities. Too many vehicles, biomes and personnel suffer serious harm during fire-countering efforts as a result of chemical foams being used,” Eriksson adds.
After mixture, it is automatically piped at 6-8 bar through a network of pipes and valves, filling the affected rack with foam and keeping the remaining battery system in operation. In the event of an external fire, the complete battery system can be filled with the protective foam without causing any long-term damage, or cooling it below its -30 C environmental operating limit.
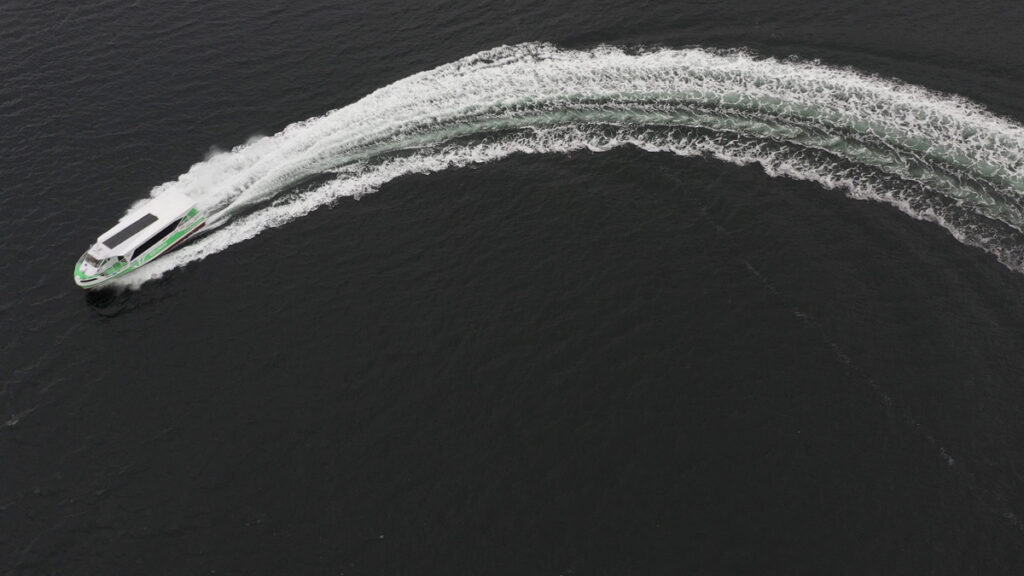
(Courtesy of Green City Ferries)
EMS
The power management architecture has been developed in-house from a blank sheet, with simplicity and redundancy in mind. For the latter of these, the ferry’s automated energy management system (EMS) software connects to two separate BMSs, both of which are connected to every string of battery modules.
“This ensures you can break literally any connection on the ferry, and all vital systems will still function. There’s no power or data link that isn’t doubled, and if one goes missing the EMS will detect it,” Eriksson notes.
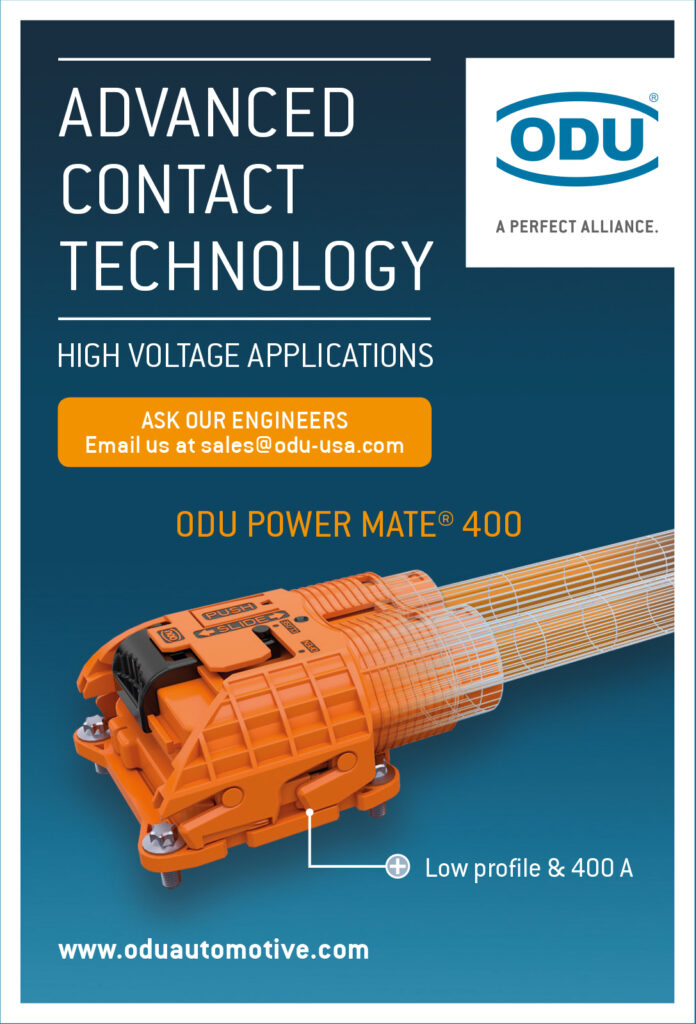
Via the Toshiba Type 3-23 modules’ voltage and current monitoring sensors, the EMS tracks all typical failure modes such as overcharge and overdischarge, providing corresponding alert signals and opening the offending contactor if a sign of excessive charge or discharge is detected.
The EMS also takes all command inputs from the operator. Two electronic control units process throttle, joystick and steering commands from the bridge before communicating them by CAN J1939 to the EMS, which then transmits the control inputs to the propulsion systems via CAN 2.0B.
Charging options
The ferry is being designed with shorebased plug-in charging in mind, and Swedish company Vattenfall will be supplying and integrating the charging stations.
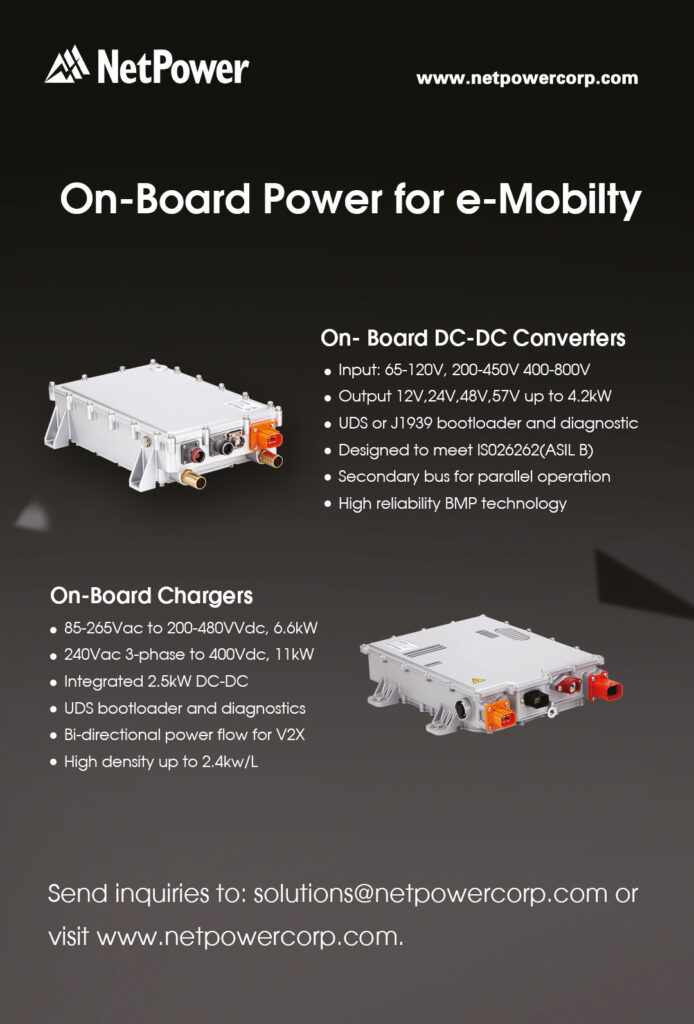
However, in the interest of reducing the burden on the ferry crew, automated charging systems remain a point of interest for the company. This is a challenge owing to the different dynamics between the stationary shore side and the boat moving around in the waves. Even gentle waves can make it hard to design an automated extendable arm or similar system for intelligently and accurately plugging in the charger.
One possible approach it is studying is the use of wireless inductive charging by way of a floating pontoon that would contain the primary charger coil.
That pontoon would be connected to the dock (and therefore the grid), but float parallel with the ferry’s hull on the water, perhaps a metre or less away from it. This would keep it lined up with the secondary (receiving) charger coil installed in the ferry’s chine, to replenish the battery capacity without needing a crew member to carry a charging cable dockside and back again (or ensuring that neither the passengers nor anyone else tamper with it during charging).
“And different cities will want us to use different methods of charging. Exploring every possible architecture makes sense, so we can be flexible with the different demands that different users will have,” Thornell adds.
Propulsion
As mentioned, the propulsion system at the back is split across two units, each of which has two 160 kW drive inverters.
Each half of the system is made from a single mechanical drivetrain and two electrical machines: a motor that converts electricity into rotary motion, and a propeller unit that provides propulsion and steering.
The motor configuration to be used in the BB Green 24 is a recent development from an unnamed Italian manufacturer. It is an axial flux permanent magnet dual-rotor design, rated to 330 kW at 2600 rpm operating speed, weighing 210 kg (including bearings) and measuring 620 mm across and 230 mm in length.
Also, each of the motors is designed with dual windings owing to a class requirement, hence the need for two inverters for each set of windings.
The initial propulsion pod units are custom Volvo Penta IPS (Integrated Propulsion System) units, which have been modified to be powered purely electrically (without hydraulics). However, these are part of a limited-series production, and Volvo Penta is unlikely to produce them in large quantities for another two or three years.
To that end, GCF is considering integrating electric propulsion pod units from a range of other potential suppliers, including Rolls-Royce, Hydrosta, Servogear and Voith. Waterjets are also being considered for routes with very few stops and a high cruising speed, owing to their propulsion efficiency being highest when above 25 knots.
Air-supported hull
The air cushion generated under the BB Green’s enclosed-catamaran hull reduces the ‘wet area’ (compared with a planing boat hull design) by around 80%. This lowest area of the hull is a major source of friction and drag.
Furthermore, as the vessel rises by about 40 cm during operation, the decrease in water displaced means the ferry needs to move less water to travel. Together, these two factors reduce the overall energy consumption by around 40% compared with a carbon fibre catamaran of the same size.
It also reduces the wake wash generated behind the ferry, to a maximum of no more than 16 cm either side of the beam on the prototype vessel. This means a much lower overall disruption of the water, enabling greater use of boats with this design quality in potentially congested harbours and coasts.
A 60 kW fan is the focal point of the air-support system. When active, the fan draws in air from the two inlet vents on the BB Green’s bow, compressing and blowing 15 m3/s of air (at 4.5 kPa pressure) through a single outlet into the gap beneath the hull.
On average, about 55 kW is consumed during normal fan operation, and a number of pressure sensors are connected to a pneumatic flap at the lower aft of the hull. Those sensors’ readings are used by an ‘automated ride control’ system to sustain the pressure, volume and smooth operation of the airsupport cushion.
“If you’re trying to build a fast ferry, cutting resistance – and by extension energy consumption – is so important, otherwise you’ll need to keep adding extra battery packs to supply all the energy you need, which adds more weight and charging time, and you get into a loop of bad engineering,” Thornell notes.
Lightweight material construction
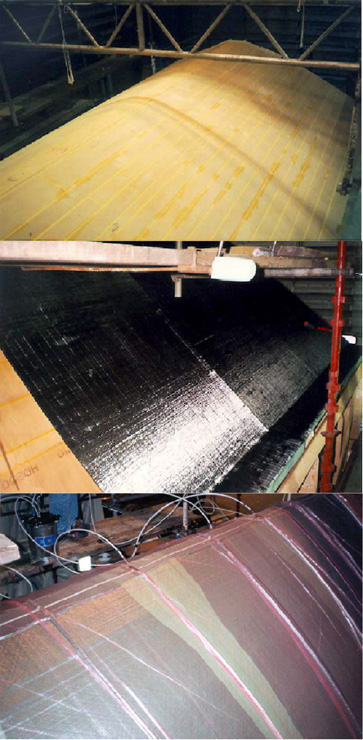
(Courtesy of Green City Ferries)
In order to make the most of its electric powertrain and air-cushion support (as well as reaching the kinds of speeds needed for high-speed marine commuting), the BB Green needed a hull that maximised strength while minimising weight. Materials engineering was therefore vital.
Design and engineering of the hull fell under the responsibilities of Anders Lonno, CTO at GCF. Much like Thornell and Eriksson, he is a qualified naval architect, who gained all his earlier experience working on military applications with the Swedish Royal Institute of Technology, with particular emphasis on r&d using composite materials in the maritime domain.
“My first major project – one of the first serious studies in composites for ships – was looking into ways we could use carbon fibre instead of glass fibre for Sweden’s Visby-class corvettes,” he recalls.
“And although that was a military application, and 25 years ago, the commercial BB Green is being built using an essentially identical set of materials and structures to that which we’d developed for the Visby class – it remains a state-of-the-art approach to naval material engineering.”
A ‘sandwich’ of two carbon fibre laminates with PVC foam filling between them forms the basis of this approach. They consist of a high-strength carbon fibre (T700 or equivalent), a matrix of vinyl ester resin and a foam material called Divinycell H as the core. This combination is commonly used in marine applications.
“Using polyester or epoxy resins were options we could have gone with,” Lonno notes. “Vinyl ester is like polyester, but modified to be mechanically stronger and not as complicated to work with as epoxies – particularly in the sense that many epoxies can cause allergic reactions or other health problems, especially on contact with human skin. That makes vinyl ester a far better choice for costeffectively manufacturing large, strong vessel hulls.”
Construction of the hull was performed through a large-scale vacuum infusion. This is a closed process that starts with dry carbon fibre fabrics combined with the PVC foam core in a female mould. The fabric is then laid out across the shape of the hull, all of which is wrapped in a huge shroud of plastic film before the air beneath that film is sucked out. When all the air under the vacuum bag has been evacuated, the vinyl ester is sucked in and impregnates the fibre and the core.
A side effect of this is that the carbonPVC sandwich structure is challenging to construct in curved forms, so the BB Green’s hull design emphasises long, straight planes with minimal rounded areas. Notably, this long, thin shape also contributes to reduced impacts from waves and a smoother journey for those onboard.
Lonno notes, “The effect of the vacuuming distributes the vinyl ester tightly and evenly across the film, impregnating the fibres thoroughly and evenly throughout the fabric, ensuring uniformity in material density and strength across the vessel hull, and without needing to add too much weight in the form of extra resin.
“That’s not always guaranteed with composite constructions, especially when the resin is first applied to the fabric by hand, which can lead to spots with air bubbles, under-impregnations and other flaws that can lead to structural weaknesses.”
Precision in the vacuum infusion process is critical, as a single mistake can mean having to start the entire process again from scratch, and Lonno stresses the importance of copious training, experience and concentration to ensure no part of the fabric, its film covering, or its exposure to the vacuum is left unchecked before the infusion starts.
“The infusion of the BB Green 24’s outer hull takes maybe up to five hours, which is very rapid when you compare it to wet layup or hand layup, on top of leading to a far more consistent finish. But you absolutely cannot do it without an extremely well-trained team of materials engineers.
“Internal structural stiffeners and beams are added afterwards, followed by upper decks and bulkheads; including those in the initial infusion would be far too complicated.
“All of those are also made with the carbon-PVC sandwich structure. Carbon composite is thinner and lighter than fibreglass for the same mechanical strength, stiffness and robustness, and the foam core separates the two layers and greatly aids strength and stiffness – it’s harder to reap the benefits of carbon fibre with a single-skin design.
“Choosing T700, or an equivalent, was key as well, because it’s much tougher than typical low-cost carbon fibres and up to three times less brittle.
“When subjected to piercing, and impact and elongation tests, it always performs very highly. We’re going to be speeding along in busy waters with debris floating around, so it’s imperative that the material is still very strong while minimising weight.”
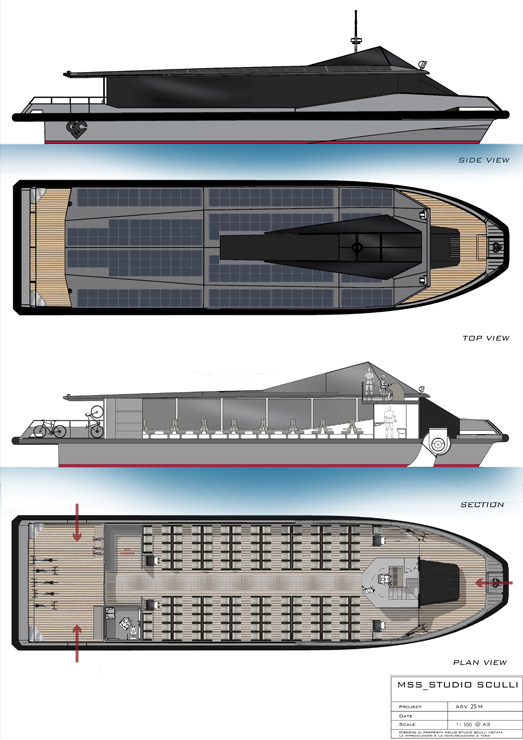
(Courtesy of Green City Ferries)
The future
GCF will soon turn its eyes towards leasing BB Green 24s to operators and transport authorities across international markets, with particular emphasis on local manufacturing of ferries and parts for costeffective and competitive production.
As mentioned, GCF intends to stay abreast of new technologies and components that improve the ferry on each route it takes.
Soon after the first production vessel is completed, the company’s engineers plan to integrate and test rooftop solar panels on the ferry, which they hope will supply a passive power boost of around 5%, reducing charge times and energy costs in the long run.
Also, Echandia is working on a maritime fuel cell system, potentially to be used on larger, longer-range journeys, with one prospective route operating over 90 nautical miles and potentially using a vessel ferrying 300 passengers.
With an eye on constant evolution and reinvention, the BB Green is well-suited to serving coasts and waterways the world over.
Specifications Green City Ferries BB Green 24
Air-supported, carbon composite hull 147 passengers Dimensions: 24.8 x 7.5 m Displacement: 28 t Energy storage: 500 kWh Maximum continuous speed: 35 knots Operating speed: 26 knots Operating power consumption: 25 kWh/nautical mile
Maximum power output: 660 kW Maximum charge rate: 6C Fastest full charging time: 11 minutes
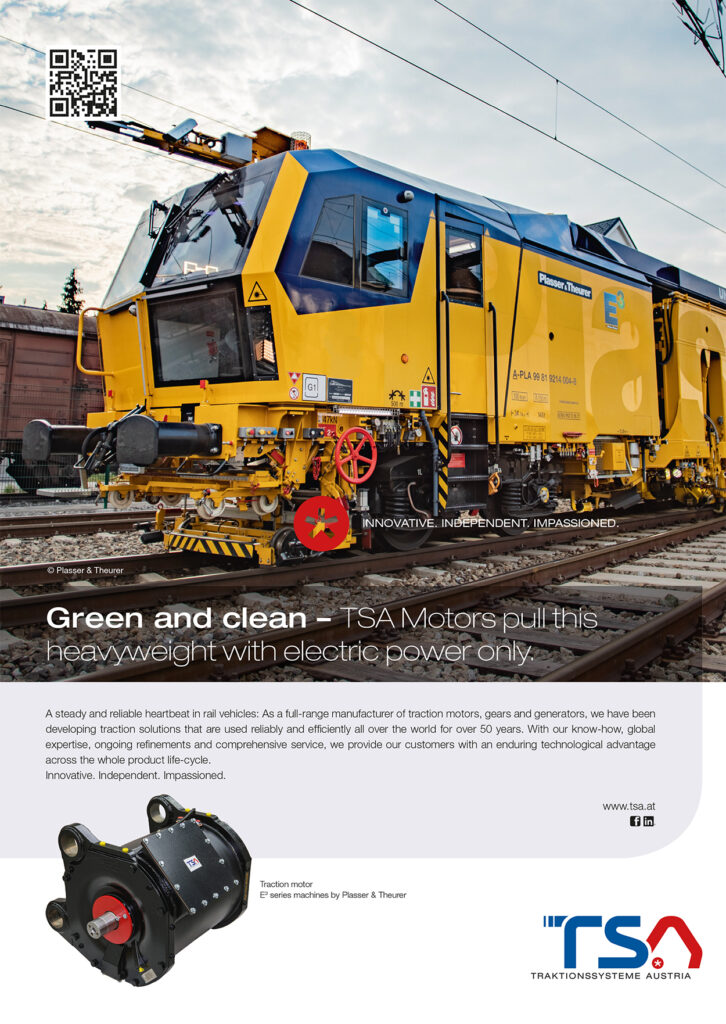
Some key suppliers
System integration: Echandia Marine
Battery cells and modules: Toshiba
Traction motor: undisclosed
Motor inverter: Aradex
Onboard charger: Aradex
Fan inverter: Keb
All other power converters: Aradex
ECUs: Volvo Penta
Onshore charging stations: Vattenfall
Carbon fibre: Toray
Composite foams: Diab
Vinyl ester: Reichhold
Gas sensors: Nexceris
Firefighting system: FiFi4Marine
Air-support fan: undisclosed
Cables: Scankab
Busbars: Mericon
Connectors: various
Software interface: Siemens
Testing facilities and consultation: SSPA
ONLINE PARTNERS
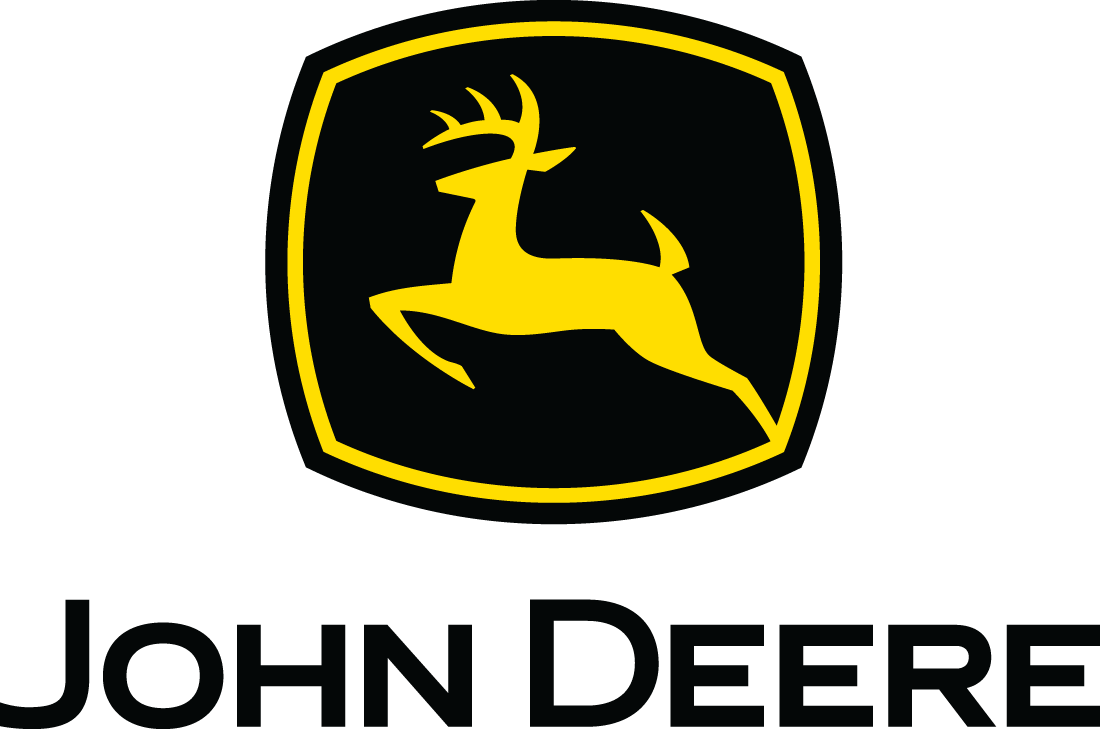
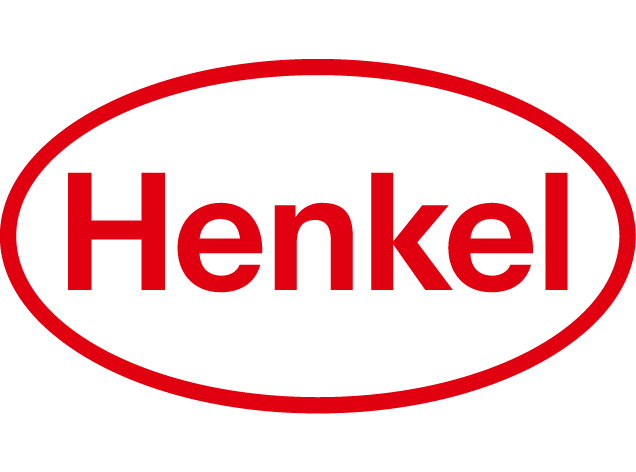
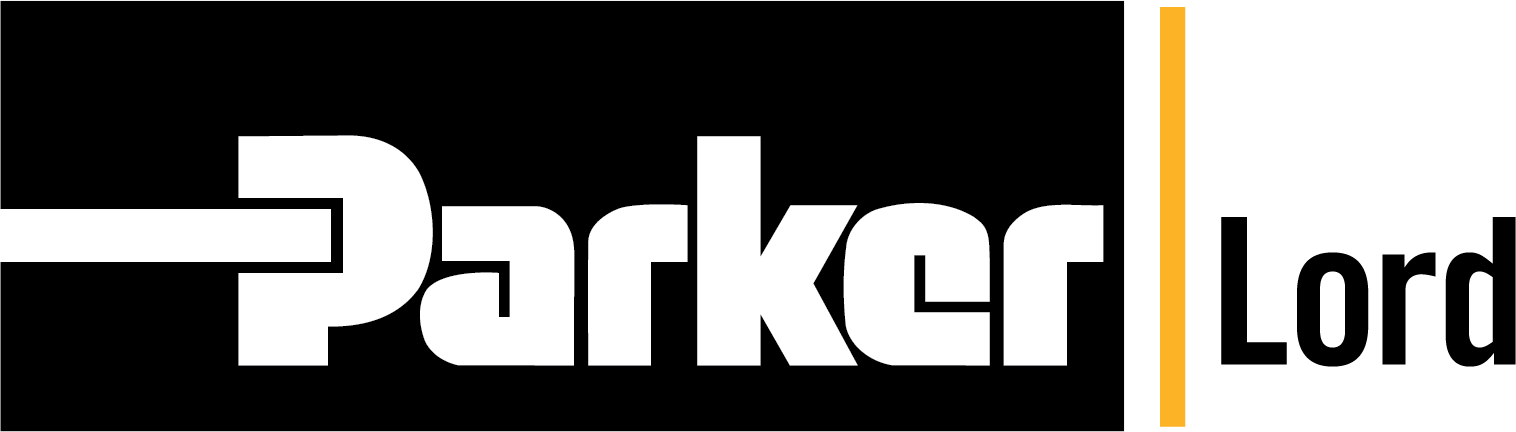
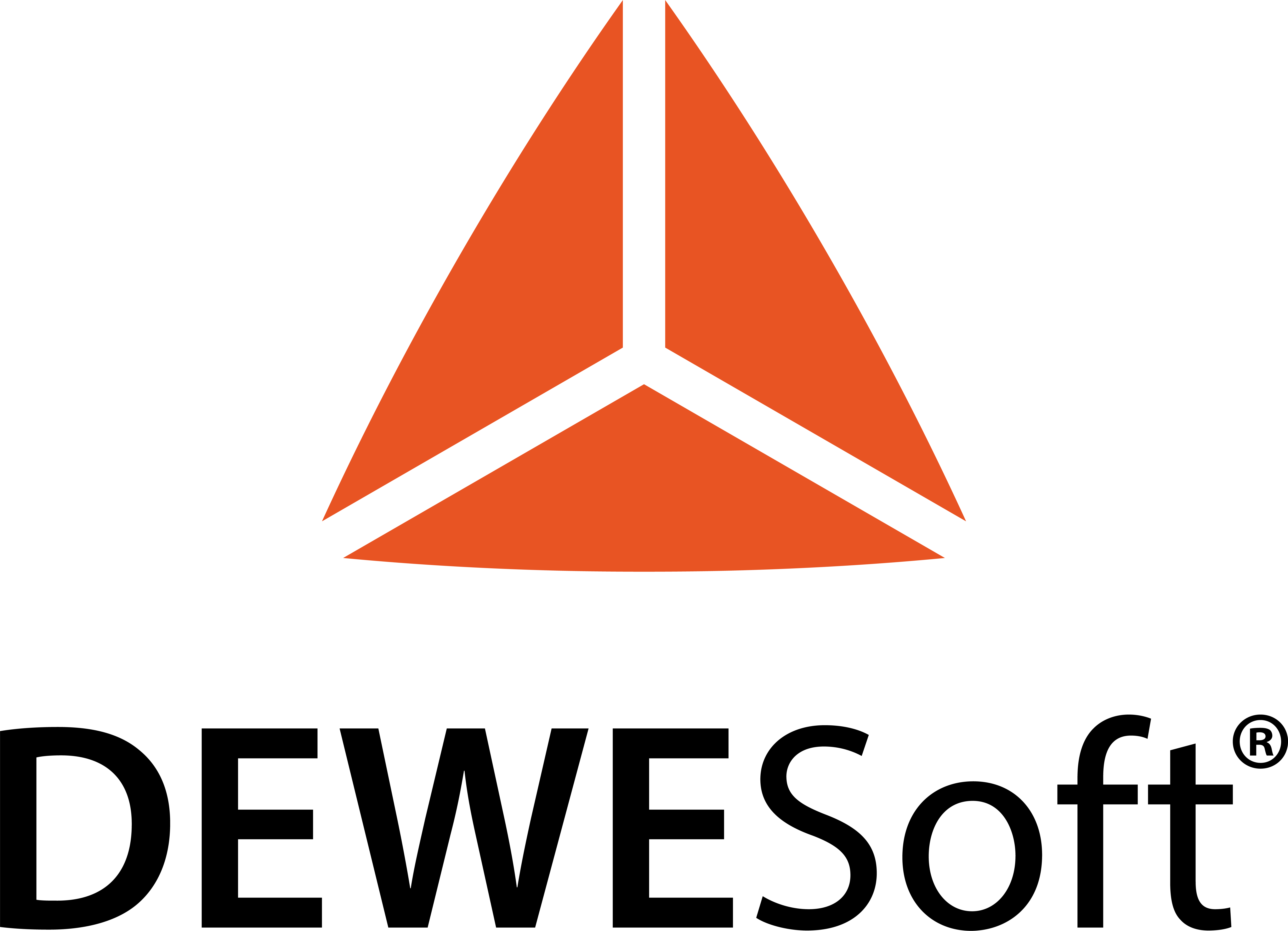
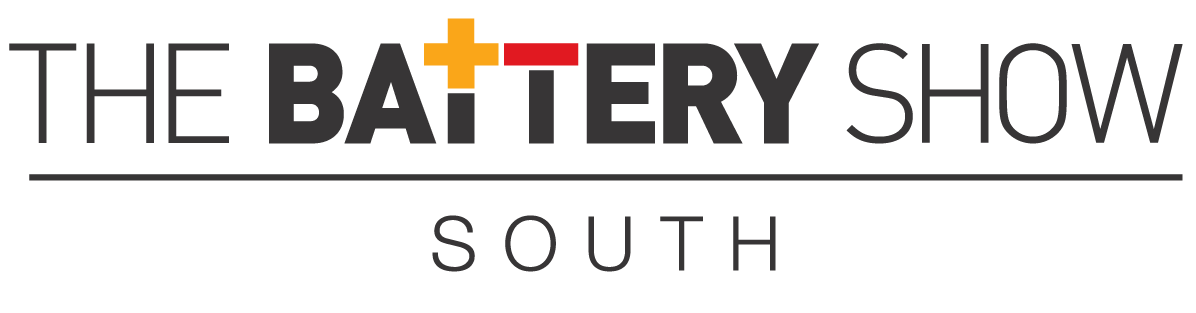
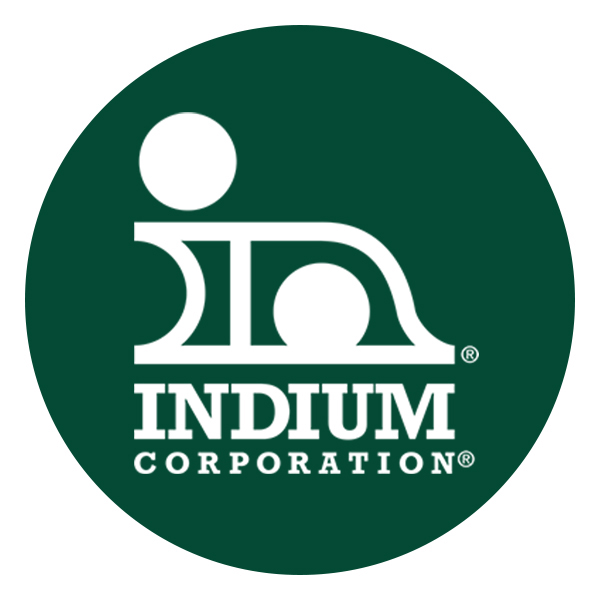
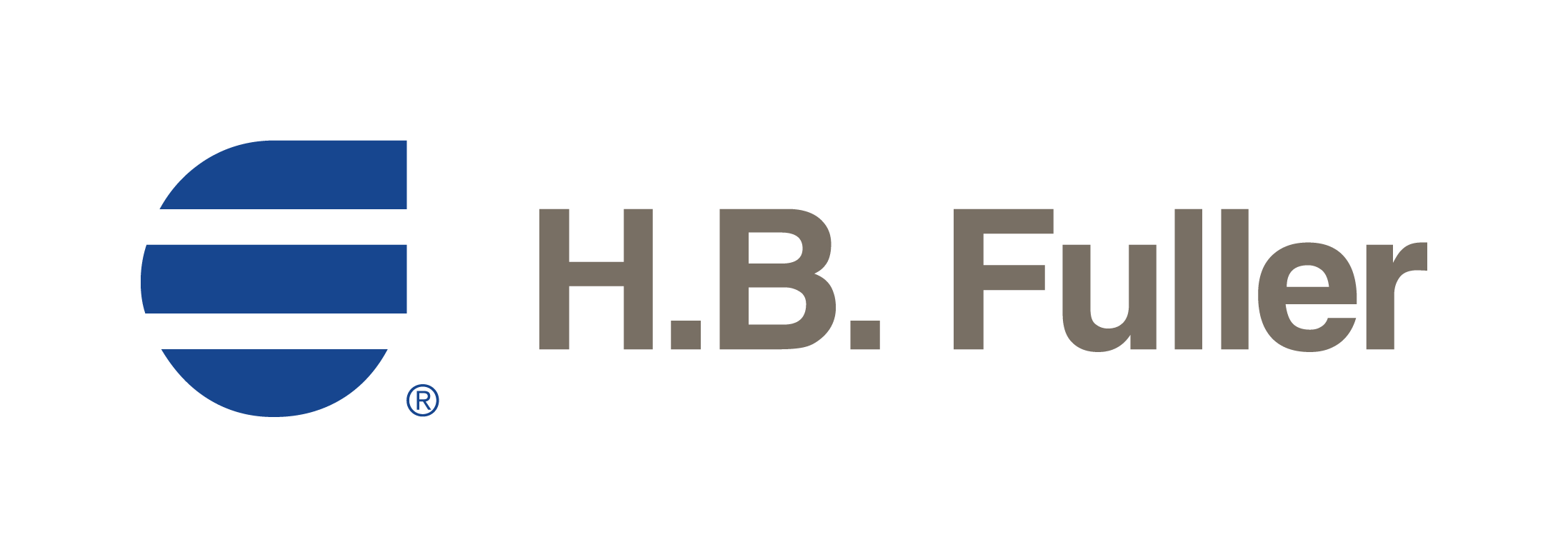