ZeroAvia hydrogen-electric aircraft
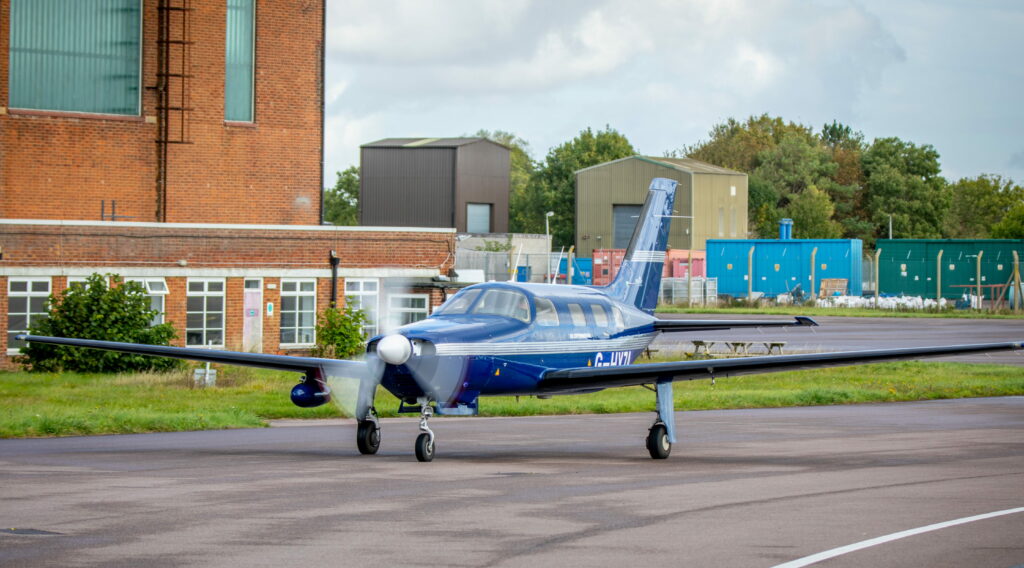
(Images courtesy of ZeroAvia)
Short haul from here
This hydrogen-electric aircraft powertrain developer has flights of less than 500 nautical miles – and their emissions – in its sights. Rory Jackson reports
As detailed in the first issue of this publication (Winter 2018) through our discussions with Pipistrel about its Alpha Electro aircraft, it is just as feasible to develop (and certify) a two-to-four seater plane to run on battery power as it is with a roadcar. While serious optimisation of the battery and overall system weight must be undertaken to make small battery-electric planes flightworthy, it is empirically achievable.
However, when trying to transport anything much heavier than four seated passengers, an aircraft manufacturer will run into the same problem as large truck or train manufacturers: the power density needed for very heavy vehicles cannot be supported simply by stringing together ever-higher numbers of packs in series. The gravimetric energy density of current battery technology simply isn’t high enough; eventually the powertrain ends up being so heavy that it cannot carry itself.
That is why hydrogen-electric power appeals greatly to vehicle developers looking to bring mass-transport or large-scale freight applications to e-mobility. The specific energy of hydrogen gas is around 33.3 kWh/kg, more than 200 times that of lithium-ion batteries (around 0.15 kWh/kg). And although arguments against investing r&d in hydrogen power are often circulated in the media, many companies continue developing and proving solutions oriented around hydrogen-electric mobility.
UK-based ZeroAvia has rapidly taken the lead in manned hydrogen-electric flight, having successfully flown its first test aircraft – a Piper Malibu Mirage six-seater – using a hydrogen PEM fuel cell configuration in September last year. It is now developing larger platforms for the powertrain.
With the aim of greater optimisation now in mind, ZeroAvia has announced partnerships with several other companies for r&d of specialised components to maximise the power and energy density in its powertrain. This will boost its capabilities beyond the aircraft used in its maiden flight towards the dozens and hundreds of seats it hopes to offer commercially in the future.
Aircraft roadmap
ZeroAvia’s research into aerospace emissions has determined that most CO2 is produced (during normal, pandemic-free operations) by narrow-body passenger aircraft: planes carrying 100-200 passengers, typically for 2-3 hours.
“Most flights in the 21st century took place under 500 nautical miles, so flying those aircraft without emissions is really our endgame, and we’re convinced hydrogen is how we get there,” says Julian Renz, head of partnerships and special projects at ZeroAvia.
“But there’s a lot of vapourware in electric aviation, a lot of lofty goals and ambitions, and our CEO Val Miftakhov wants to approach our ultimate goal with a practical strategy, which is why we started with fitting our prototype powertrain on a Piper Malibu Mirage. It’s a well-known and certified aircraft, and if we need to certify some of our powertrain components, doing so is easiest when flying an aircraft with under 20 seats.”
Flying a six-seater aircraft of that size typically satisfies regulators that a company is capable of transporting 10-20 passengers at a time. ZeroAvia therefore plans a stepping-stone approach to its technology demonstrators, both to prove their safety case to certification authorities and to gather real-world testing data on different powertrain components and how best to configure, arrange and run them.
The maiden flight (including taxiing, take-off and landing), around its UK headquarters in Cranfield, England, was part of the UK government-supported HyFlyer r&d project to decarbonise medium-range small passenger aircraft. The flight lasted about 8 minutes, reaching a peak altitude of 1000 ft and a top speed of 100 knots. Before successfully completing the HyFlyer I project in June 2021, ZeroAvia carried out a series of progressively longer and more advanced flight patterns that established the capability for long-distance flights using hydrogen-only propulsion.
“While we’re now working with a 250 kW powertrain, our next demonstrators will use a 600 kW electric engine – with one electric powertrain on the 10-seater aircraft, and two powertrains in wing-mounted nacelles on the 20-seater,” Renz says.
“Our powertrain is designed to be modularly scalable; hydrogen fuel cells are similar to batteries in that respect. If you want more energy in a battery, or more power from a fuel cell, you just add more cells until you reach your target capacity.”
Fuel and reactant management
While the exact configuration of the powertrain is at present fitted to the specifications of the Piper Malibu aircraft, the concept is scalable to the bodies and nacelles of larger planes.
Energy on board the aircraft is stored as gaseous hydrogen, pressurised to 350 bar and kept in cylindrical tanks. For test operations, the tanks are stored inside the cabin, but in future they are expected to be stored on hardpoints under or over the wings, to minimise the number of modifications to the actual airframe.
Customisations of the tanks have been minimal, with most focus here having been on achieving the dimensions needed for the tanks ZeroAvia wanted to meet the needs of its airframe, with a Type 4 tank used in the Piper aircraft. Such tanks combine a carbon composite outer layer (principally providing strength) with a plastic liner that largely serves to prevent leakage. These materials enable a satisfactory gravimetric energy density in terms of how much hydrogen can be stored per kilo of tank weight.
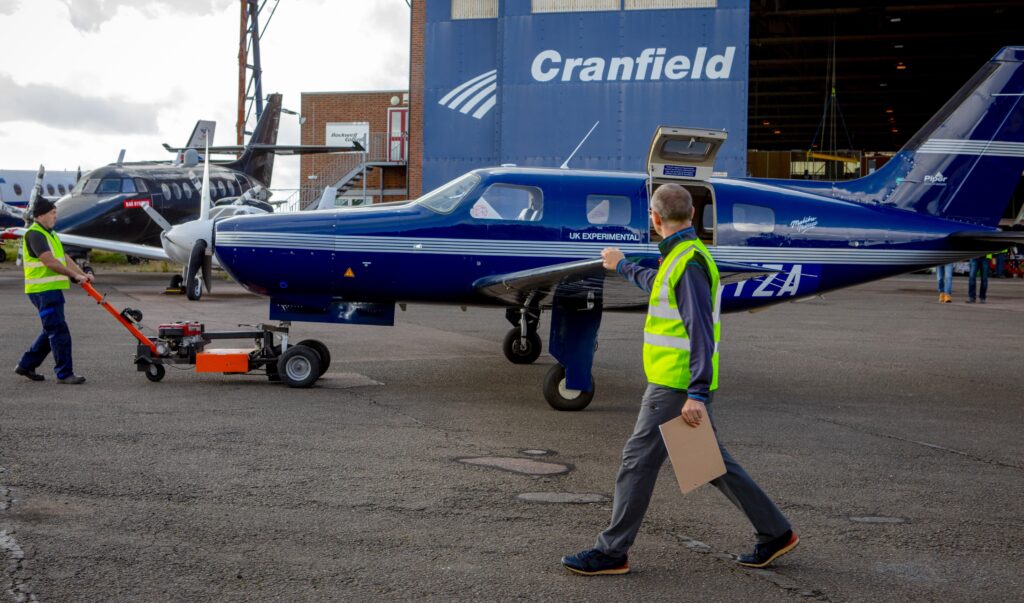
“In our first test flight, we had about 1.5 kg of hydrogen on board, of which we used roughly half,” Renz notes. “Ultimately though, on the six-seater plane we’d like to have up to 15-20 kg of hydrogen, which will enable us to fly 200-300 miles.”
He adds however that this topic is something the company is discussing with regulators, as the standardised types of hydrogen tanks available were established with automotive safety requirements in mind, which could mean needing different designs and certifications.
For the hydrogen gas to be used by the PEM fuel cell, its pressure needs to be lowered from 350 bar. During cruise, the required pressure is typically just under 10 bar, although over the cell’s range of operation, 8-12 bar might be needed. To enable this, the gas leaving the tank passes through a pressure regulator to achieve accurate depressurisation, before running through flexible steel tubing towards the cell’s anode.
“There are quite a few other systems throughout the hydrogen manifold to ensure safe and accurate pressure regulation,” Renz says. “We have solenoid valves on the fuel tank to control the flow of hydrogen into the pressure regulator, as well as pressure sensors on either side of the regulator.”
Placing a sensor after the regulator in the manifold allows the cell’s management system to confirm that the regulator is working correctly. If hydrogen is heading towards the cell at excess pressure, a check valve can shut off the flow from the lines, or a safety valve on the cell stack can purge any pressure build-up inside the system.
Meanwhile, a pressure sensor in the tank gauges how much fuel is left inside the hydrogen tank, or detects if the pressure drops too quickly, as this can indicate a leak.
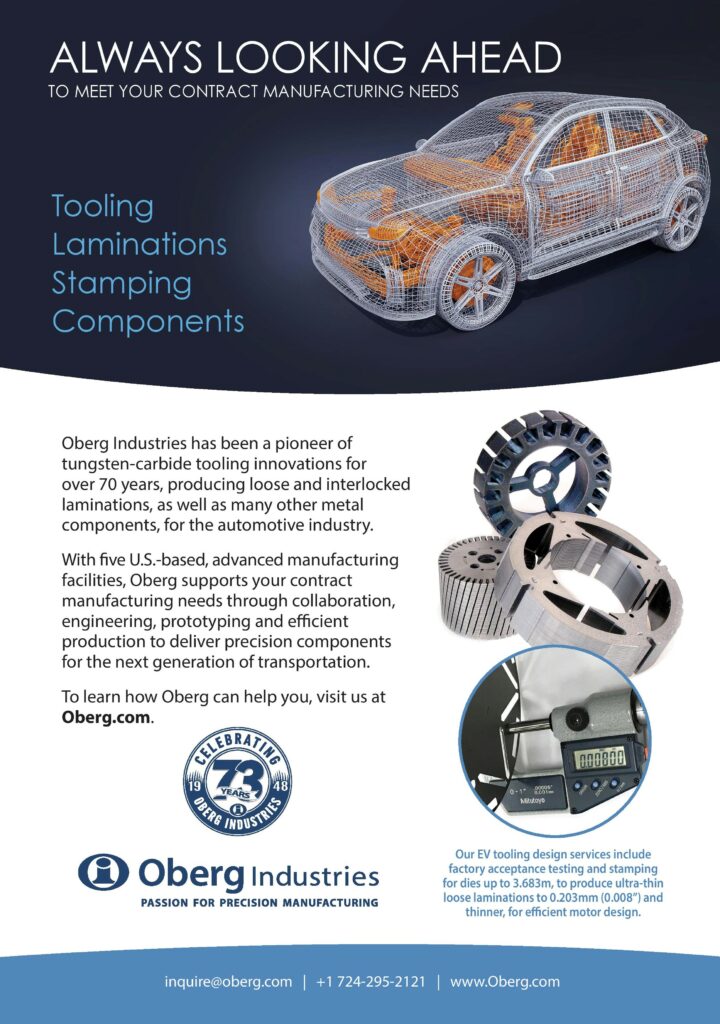
“We also have a vent line for the tank and hydrogen manifold section,” Renz adds. “That’s there to ensure that if there ever was a leak, it gets vented in a dedicated spot, to safely lead the hydrogen outside the aircraft and prevent an unsafe build-up of gas from occurring inside the fuselage or nacelle.”
Oxygen is supplied to the cathode using the ambient air outside the aircraft. A compressor is used to draw in the air and pressurise it to provide a mass flow about twice that of the hydrogen going to the anode sidebefore it enters the fuel cell.
Given that at the cruising altitude of 10,000 ft the ambient air pressure drops to 0.7 atmospheres, it could be assumed that the air compressor needs to work harder to provide the same mass of airflow. However, given that the power requirement (and hence the required amount of oxygen) at altitude during cruise is also about 70% of that needed during take-off, the compressor tends to work fairly similarly across the aircraft’s full range of operations.
Hydrogen-electric powertrain
ZeroAvia has partnered with Swedish company PowerCell for the supply of hydrogen fuel cells for this project. In the case of the Piper Malibu test aircraft, the powerplant used was a PowerCell MS-100 cell (a product since rebranded as the Power Generation System 100), which has an expected lifetime of 20,000 hours and can be operated in temperatures from -30 to +45 C.
This standard fuel cell system outputs up to 100 kW net power, weighs 170 kg and measures 696 x 674 x 606 mm. Power is typically supplied over a 300 V bus (up to a maximum of 570 V DC, and down to a minimum of 250 V) at a rated current of 375 A, with 420 A as the maximum current and 60 A as the minimum.
The cell’s rated efficiency at 100 kW output is 45%. At this power output, roughly 122 kW of heat is produced. System efficiency at between 40 and 60 kW power output reaches about 58%.
“There were many reasons for choosing this fuel cell, but most important was the power density, particularly the ramp rate – how quickly it can react to a change in load,” Renz says.
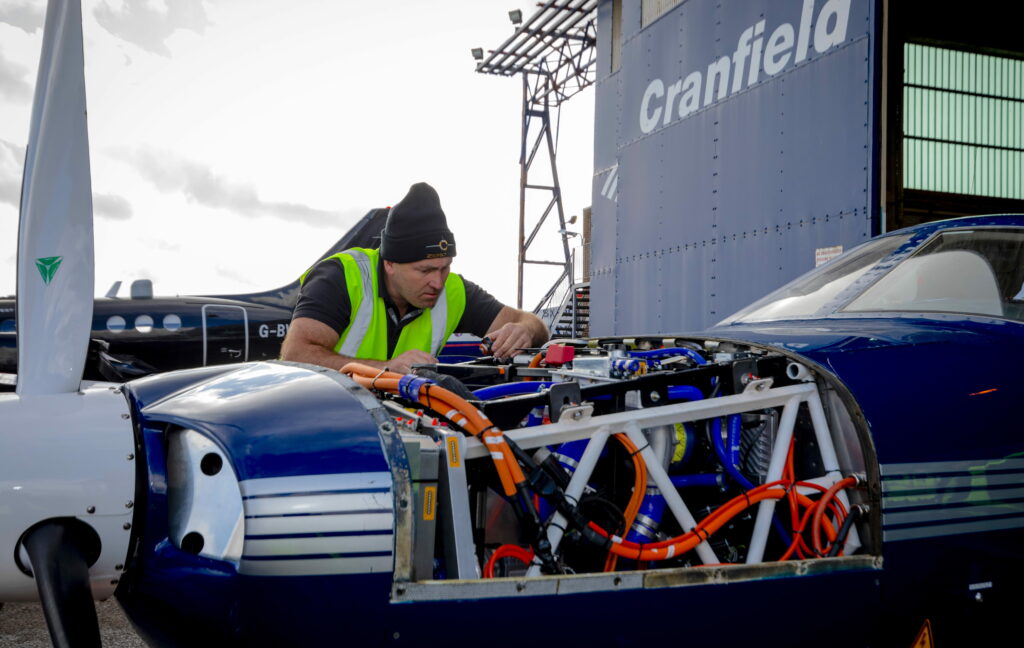
“Most hydrogen-electric vehicles carry a battery or supercapacitor, as that allows a much faster power response than fuel cells, which are relatively sluggish because they depend on a chemical process to output current. We need to be able to replicate the power curves and ramp rates of turboprops if we’re going to achieve stable hydrogen-electric flight, in particular during take-off.”
For thermal management of the cell, a liquid-cooling loop is integrated to enable piping of heat to the end-user’s preferred heat sink (with the cell’s coolant typically exiting the outlet at around 80 C). In ZeroAvia’s case, this was a radiator installed behind the propeller, with the prop’s downwash of air being used to create additional airflow for cooling the radiator.
As Renz explains, “Thermal management was something we worked on extensively to ensure we reject as much waste heat as possible. A number of liquid-cooling loops were used to cool the motors, inverters and the cell stack. A water-glycol mix was used for all electronics except for the cell stack, for which a special low-conductivity cooling liquid recommended by the fuel cell manufacturer was used.”
As indicated, electricity from the fuel cell and a battery pack (rated for up to 250 kW power output) runs to the inverters and electrical motors for achieving the necessary ramp rate for flight operations. It also helps to stabilise the supply voltage coming from the fuel cell stack, and some open-cathode PEM fuel cells will periodically be disconnected from their load so that a process called ‘current pulsing’ can be carried out. This consists largely of carrying out short-circuits inside the stack to rejuvenate its humidity and maintain its conductivity and power output during lengthy operations.
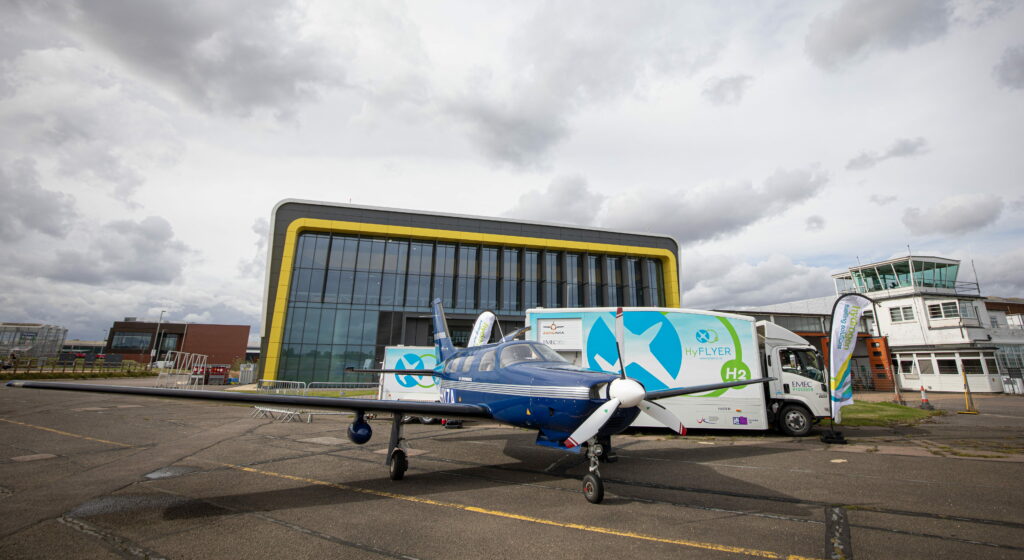
The inverters were selected to match the power performance of the electric motor system and for compatibility with the input voltage from the battery and the output voltage needed for the motor (the latter of which runs from 400 to 800 V AC). The drive system consists of two motors driving a single output shaft for the propeller; each is rated to 130 kW maximum power, and combined these produce up to 250 kW.
Each e-motor is a COTS product supplied by an undisclosed company, although ZeroAvia comments that the company traditionally produces systems for the automotive sector, and chose this motor for its reliability, input voltage, weight and by extension its power-to-weight ratio. It is a permanent magnet synchronous motor, configured as a radial-flux machine with an internal rotor and external stator for power density.
“The power of the electric motors directly determines how large of an aircraft you can lift, as well as how many passengers you can transport, while the energy density of the fuel tank is key for how long and how far you can transport them,” Renz says. “Again, that is why a hydrogen-electric powertrain makes so much sense to us for aviation – you’re matching the high energy density of hydrogen gas with the high power of electric machines.”
The powertrain (encompassing the fuel cell, battery, inverters and electric motors) is installed inside the nose of the Piper aircraft. The propeller is mounted on the motor shaft, but rather than use the stock propeller, ZeroAvia has installed a COTS electrically actuated variable-pitch system, to maximise the aerodynamic efficiency of the prop blades’ angles of attack across the test aircraft’s flight envelope, through taxiing, take-off, cruise and descent.
Hydrogen infrastructure
While one of the biggest criticisms laid at proponents of hydrogen-electric power is the lack of availability of hydrogen gas compared with, say, access to electricity for recharging from the grid, ZeroAvia is quick to point out that all the technology needed to make hydrogen gas is available to anyone who actually wants it.
Internally, however, Renz acknowledges a key problem for scaling up commercial hydrogen-electric flight: most airports in a short timeframe would be unlikely to have any hydrogen gas to offer aircraft driven by ZeroAvia’s powertrain if they were to land there.
To that end, the company is also undertaking r&d for ‘green’ hydrogen production, storage and dispensing infrastructure. The primary demonstrator for this currently sits at Cranfield airport, near ZeroAvia’s facilities.
Water is dispensed into an electrolyser, which produces hydrogen from water using a reversed version of the electrochemical reaction by which PEM fuel cells produce electricity. The electrolyser is powered using electricity from Cranfield University’s own grid, which is partially supplied by solar panel arrays.
Dispensing this hydrogen is then carried out by a mobile fuelling truck, which is largely identical to the trucks ferrying jet fuel around most airports. The truck carries Type 4 tanks that are refilled at the electrolyser before it drives over to ZeroAvia’s aircraft. A nozzle is attached to the plane from its storage tanks, and upon opening the valves at either end, hydrogen flows out until 350 bar is reached at either end, typically after just a few minutes.
“As we see it, producing hydrogen on-site at airports by using renewable energy and feeding that directly into electrolysis is the cheapest way to access hydrogen gas, as well as the greenest,” Renz says. “Britain has widespread access to wind and wave power, and parts of Oxfordshire provide almost perfect conditions for solar array fields.
“There are further practical reasons to turn airports into hubs for a national hydrogen grid. Airports are major transport and logistics hubs, with huge trucks, buses and coaches constantly running to and from them – electrifying these types of vehicles with hydrogen makes much more sense than batteries in terms of weight , cost and range efficiency, so why not gear up airports to act as hydrogen refuelling stations?”
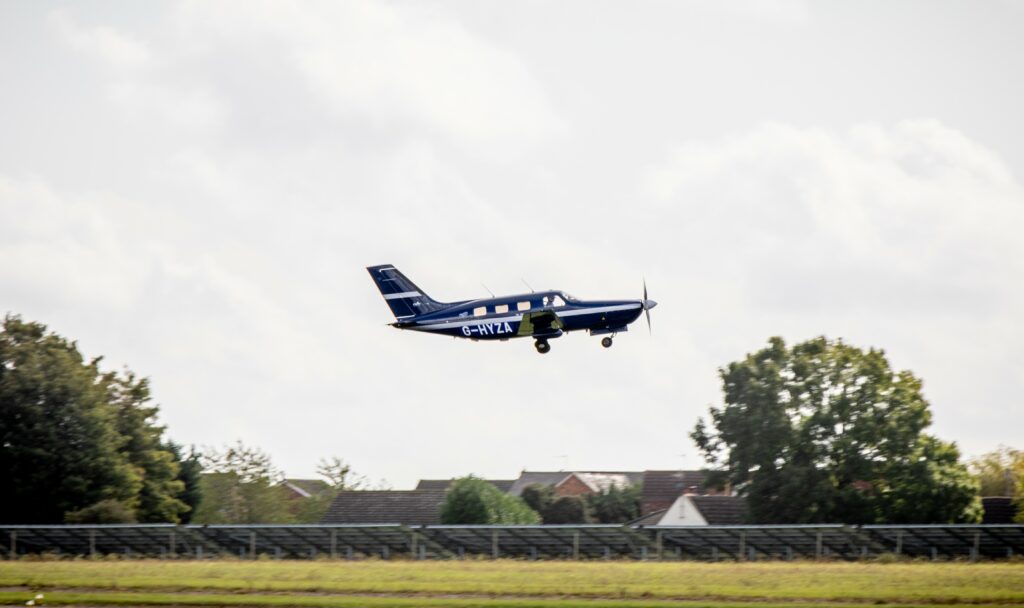
Future plans
Now forging ahead with developing its 600 kW powertrain for commercial use-cases, ZeroAvia has signed an order for a number of 100 kW fuel cells for its 10- and 20-seat demonstrators. Deliveries of these will start later this year.
The company is also now working with high-speed electric air compressor developer Aeristech, whose patented motor and control technology is expected to help significantly with improving the power-to-weight and power-to-volume ratios of the overall powertrain.
Development of the powertrain for 10-20 seater planes is included in the next phase of the HyFlyer project, HyFlyer II, which is aiming to create a market-ready hydrogen-electric powertrain by 2024.
“If we want to see hydrogen-electric commercial flights within the next few years, we have to be practical, which means working with components that are widely available,” Renz says. “We have to fly well-established aircraft models, and fuel them with gaseous hydrogen stored at 350 bar.
“But as we move into the future, for the much larger aircraft we might need to design airframes around our powertrain, which will open up opportunities for things like storing fuel in the wings and using liquid hydrogen, which is stored cryogenically but can provide 3-10 times the energy density of hydrogen gas – in fact, it’s more energy-dense than jet fuel. That’s really where aviation has to go, once the technology allows it at a large scale.”
PEM fuel cell operation
Electricity in the ZeroAvia powertrain is generated via a proton exchange membrane or polymer electrolyte membrane (PEM) fuel cell. Current is produced following an electrochemical reaction of hydrogen and oxygen, which takes place inside the membrane electrode assembly (MEA) at the core of each cell structure.
The MEA consists of a semi-permeable PEM layer, sandwiched between an anode and a cathode layer, which serve to diffuse the reactant gases. Each of the latter two layers also has a catalyst layer embedded in it, typically platinum or a similar substance, which plays a key role in the electrochemical reaction.
Hydrogen gas flows into the PEM’s anode sides, while oxygen flows into the cathode sides, each typically being distributed via a flow field installed into two plates that enclose each cell to maintain pressure.
The catalyst layer splits the hydrogen gas molecules at the anode into protons and electrons. The protons pass through the central semi-permeable membrane before reacting with the oxygen molecules on the cathode side to form water that leaves the cell via the exhaust. The electrons flow along a circuit, which produced an electric current from the cell stack.
Also installed around the cell are a number of sensors and other systems to ensure the balance of heat and humidity (for ionic conductivity of the membrane) as well as reactant flow rate and pressure (corresponding to the required current) inside the stack of cells are correct. There are additional control systems for managing the power output and by extension the rate at which reactants are consumed; collectively these systems are referred to as the balance of plant.
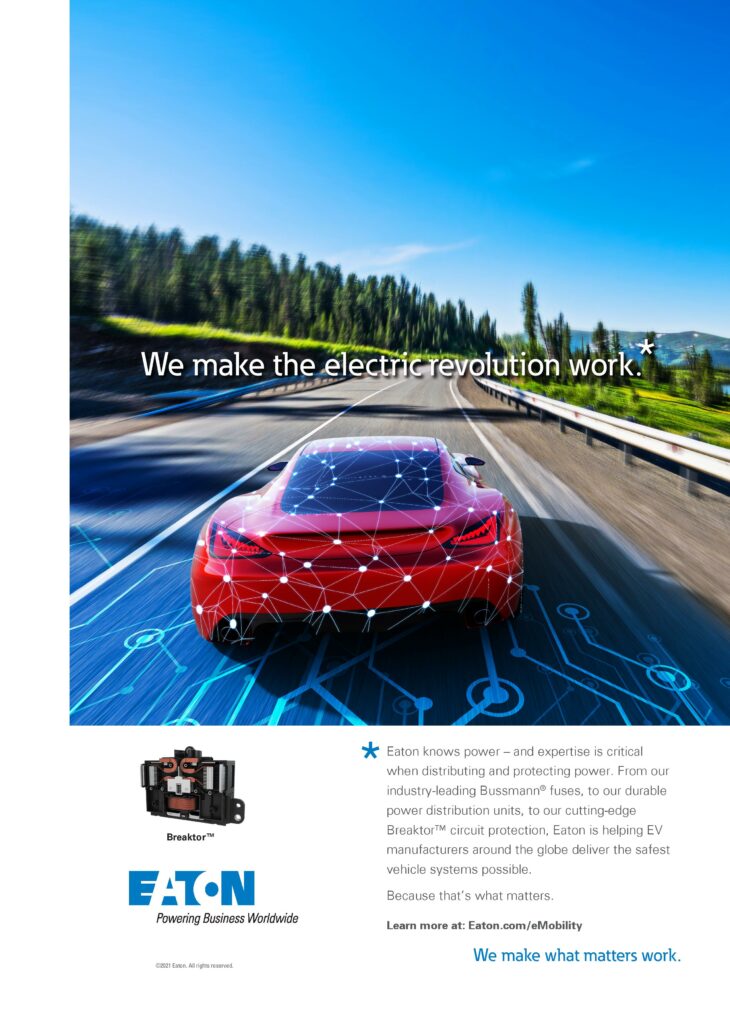
ZeroAvia’s origins
ZeroAvia was founded in November 2017 by Val Miftakhov, who became its CEO in May 2019. He had previously founded eMotorwerks, a company focused on developing EV charging infrastructure, and had served as CEO there for 7 years before taking the reins at ZeroAvia.
Outside his work life, Miftakhov has piloted fixed-wing and rotary aircraft, and is familiar with the engineering of such vehicles, including their power and energy density needs. This experience, combined with his professional background and experience, convinced him that commercial aviation could not be decarbonised through batteries alone, and that developing battery-electric planes while waiting for cell technology to advance to the necessary energy density levels was impractical.
Through early discussions with his team at ZeroAvia, hydrogen was put forward as the most practical means of realising zero-emissions long-haul flights, especially in terms of the technological readiness and commercial availability of powertrain components, and how easily a hydrogen-electric powertrain could be scaled up from a six-seater aircraft to fit something akin to an Airbus A320.
Specifications
PA-46-350P Malibu Mirage demonstrator
Six-seater fixed-wing aircraft
Hydrogen-electric powertrain
PEM fuel cell
MTOW: 1969 kg
Wingspan: 13.11 m
Length: 8.6 m
Fuel capacity: 1.5-15 kg of hydrogen
Fuel storage pressure: 350 bar
Maximum power output: 250 kW
ONLINE PARTNERS
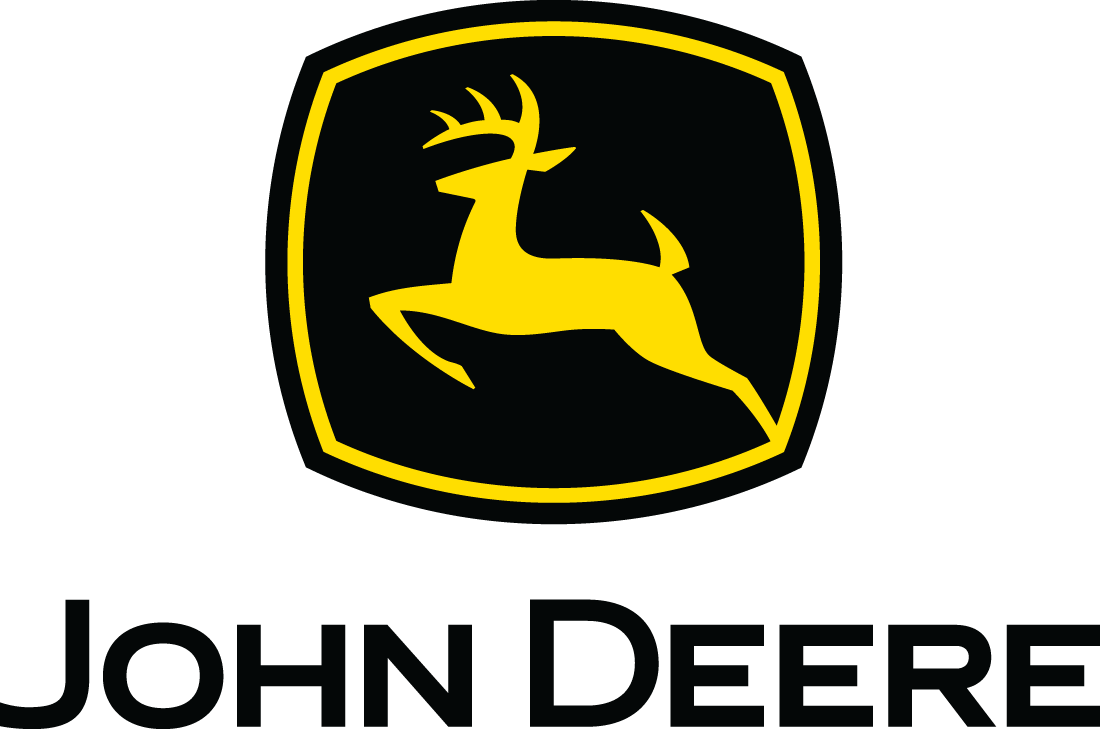
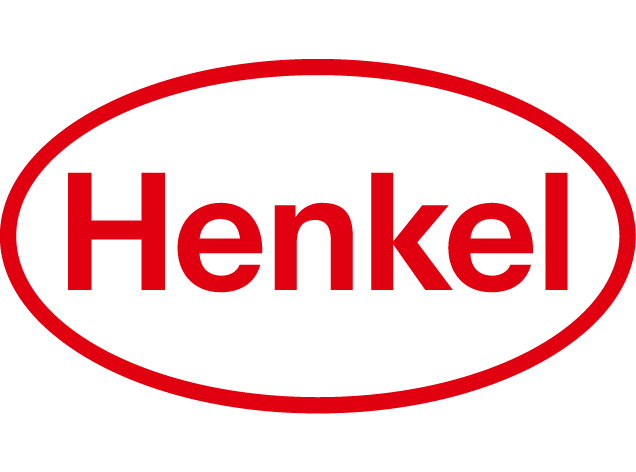
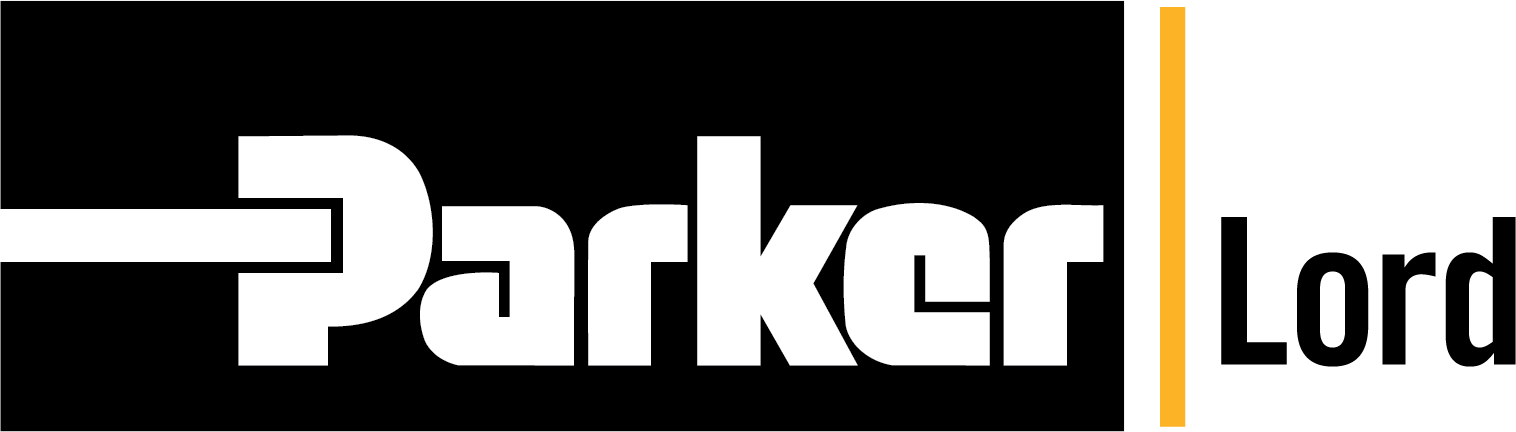
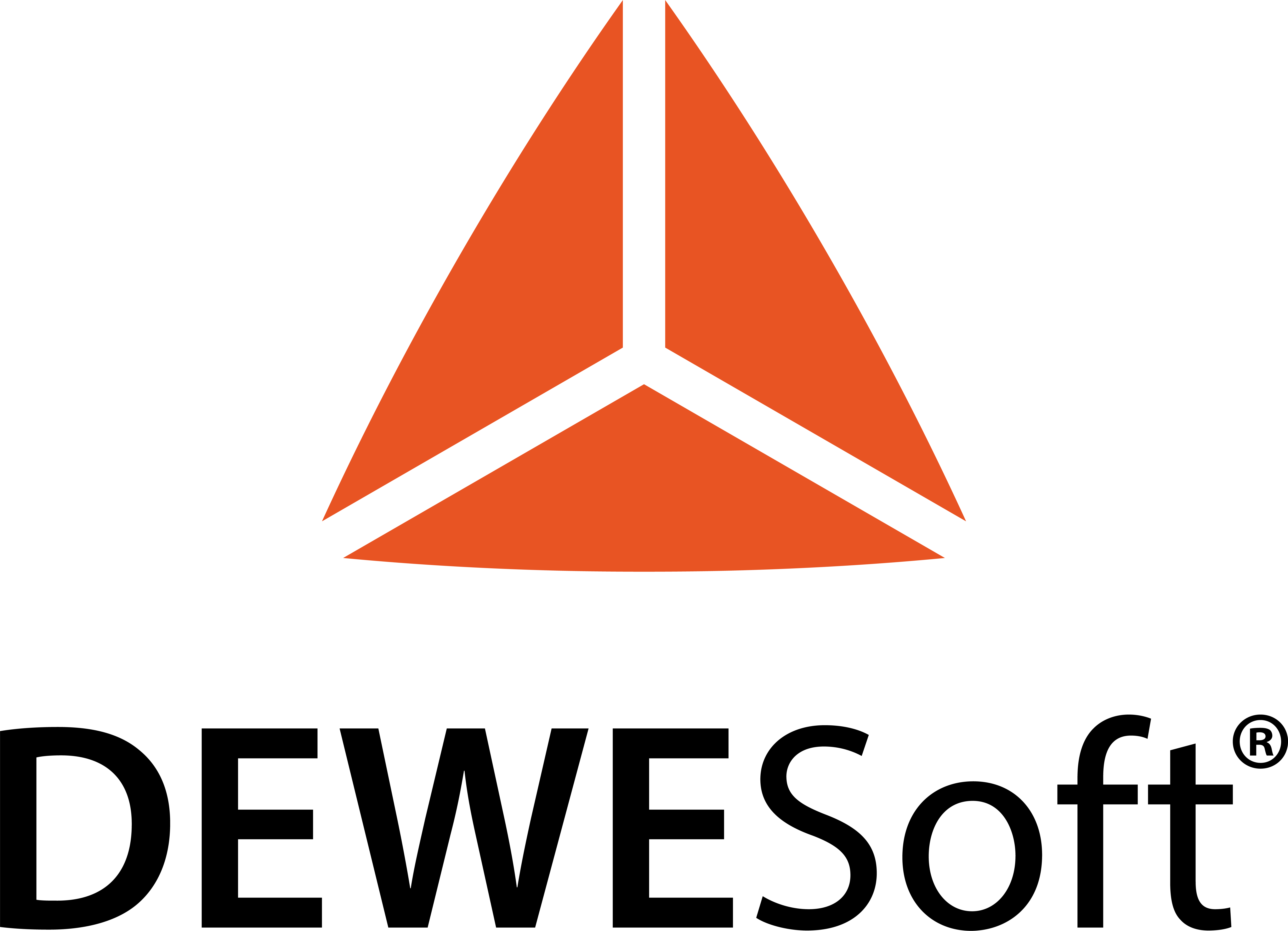
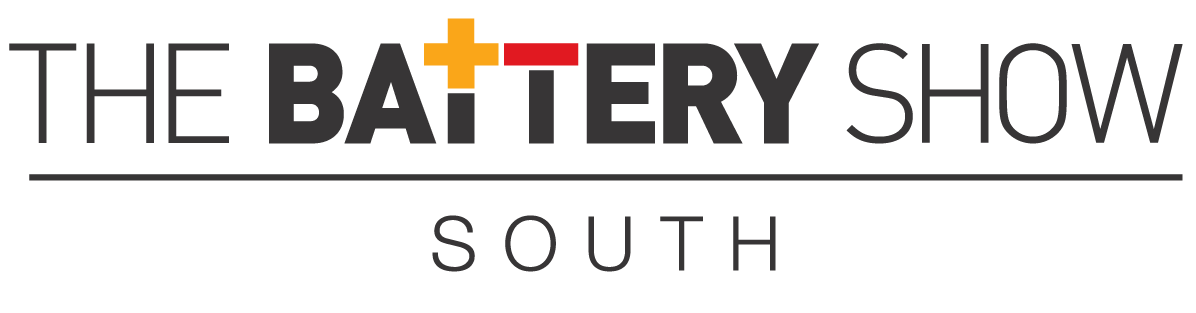
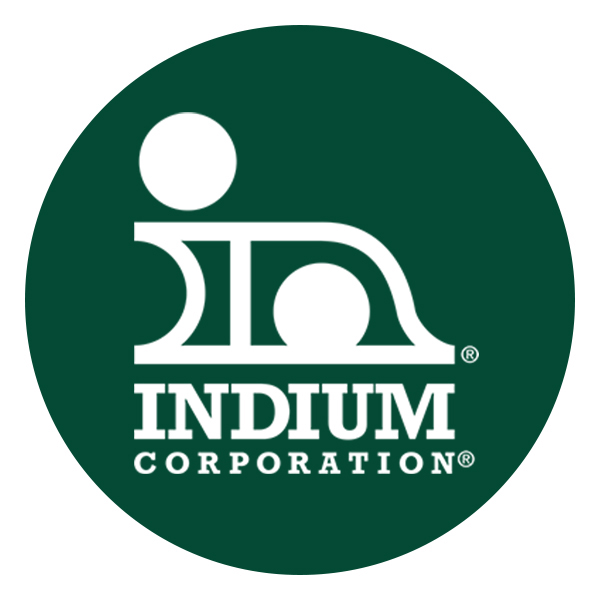
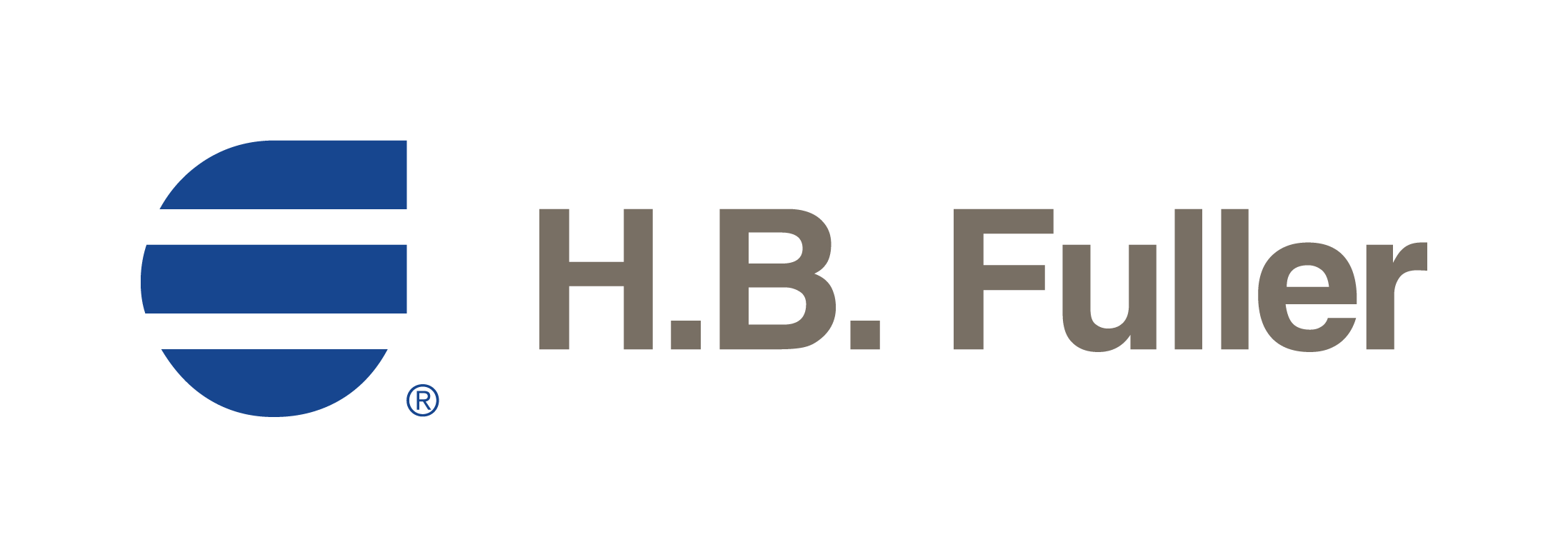