Dieseko Woltman pile-driller/driver
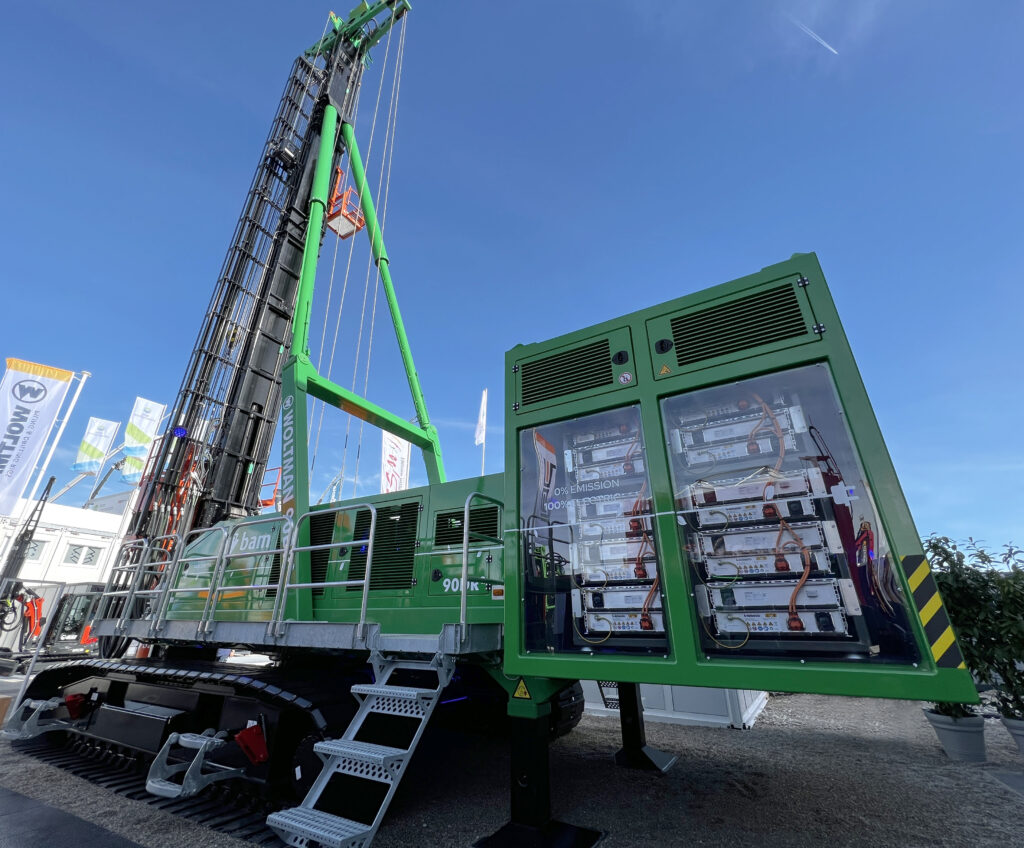
(Images courtesy of Dieseko)
Ground-breaker
Peter Donaldson reports on how this zero-emissions version of a diesel piling rig has been designed and developed
Drilling piles into the ground has been a crucial task in building for thousands of years. Whether they’re made from timber, reinforced concrete, steel or aluminium – and whether in column or sheet form – they help to stabilise the ground and make it more able to support heavy structures.
Against that backdrop, Dutch construction equipment manufacturer Dieseko has recently introduced an electrified version of its 90 t Woltman 90DR pile-drilling and driving rig, replacing its diesel engine and fuel system with an electric powertrain to create the Woltman 90Dre. It completed its first zero-emissions job at Amsterdam’s Schiphol airport in February this year, in the hands of launch customer BAM Infra Netherlands.
As the term suggests, pile drilling involves making a hole for the pile to go into, the pile often consisting of a framework of steel reinforcement that goes in first, followed by a pour of concrete or grout. In contrast, pile driving is the process of forcing a tubular or sheet pile directly into the ground using a hammer that works either by impact or vibrations.
Like its diesel forebear, the Woltman 90 DRe can be used for both, says Herman Legtenberg, director of technology and engineering at Dieseko Group.
The most prominent component of a piling rig is the leader, the vertical steel column that supports and guides both the drilling/driving tools and the pile itself. The 90DRe’s leader can be 30, 33 or 36 m high.
“We call it a leader-guided rig,” Legtenberg. “On the leader we can put the rotary head, which is most commonly used on this machine, and we can also put an impact or a vibratory hammer on it.”
The leader can also be fitted with a quattro piler, he adds, a tool that uses four clamps and cylinders to apply static downward pressure onto sections of sheet piling to press them into the ground without the use of impact or vibration.
Materials issues
The machine is made largely from steel, with the most widely used grade being S355, a structural steel with a minimum yield strength of 355 MPa. For the most highly stressed components, such as the leader, S690 high-tensile steel is used, which combines high strength with relatively low weight.
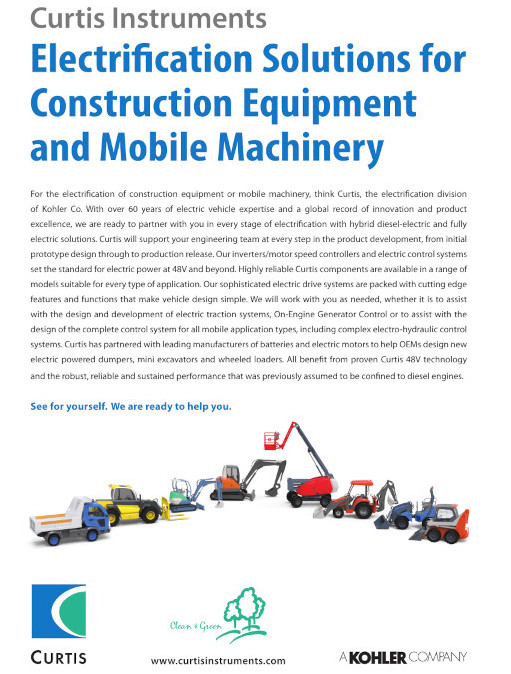
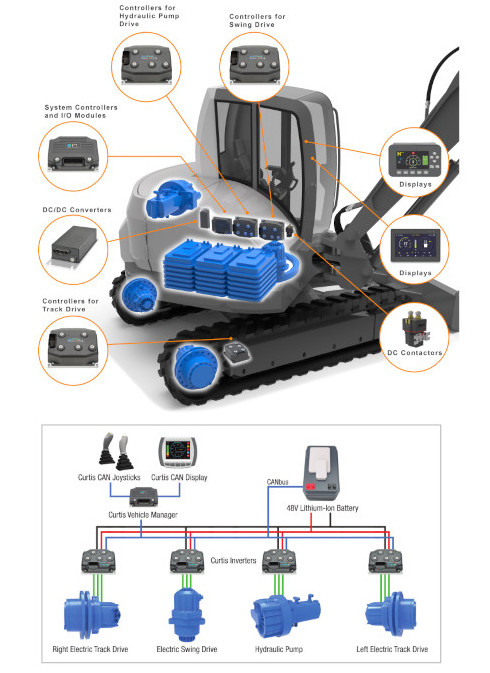
Legtenberg explains that the stresses on the leader are so high because it has be tall in order to install long piles and, while it usually works vertically, it also has to be able to tilt to install the angled piles used to anchor bridges, for example, multiplying the stresses.
“When it’s working at an angle, the forces on the leader are immense,” he says. “And of course the rotational bearing gets heavily loaded.”
The next major piece of structure is the machine deck, which houses the hydraulics and electronics along with the operator’s cabin. The deck rotates by means of a bearing on the chassis, called the undercarriage, to which caterpillar tracks are attached.
Among the hydraulically operated machines on the deck is a set of three winches, one that pulls downwards to assist installation, and two others that that pull upwards – one to raise the tooling, the other to extract piles or casings. The machine deck is also home to two pumps that feed pressurised oil to the hydraulic loads, the oil tank that serves as the hydraulic reservoir, and a dedicated hydraulic oil cooler.
All the pile installation and extraction tooling, as well as the automotive components on the Woltman 90DRe, remain hydraulic, as most customers have large investments in hydraulic tooling. However, the hydraulic pumps are driven by two permanent magnet (PM) electric motors from Danfoss.
Supplied by Webasto, the battery system is divided into two, Legtenberg explains The main, 1000 kWh pack in its container must be detached to allow the vehicle to fit on a low loader for transport. This is accomplished using a separate crane, as the pack weighs about 15 t.
Fortunately, the battery pack has next to no effect on the rig’s balance, as the diesel Woltman 90DR normally carries 15 t of ballast, which the battery replaces in the electrified version. “We got that one for free,” Legtenberg says.
With the main pack removed, the rig must still be capable of driving on and off the truck under its own power, so there is a smaller, 200 kWh pack that remains on the machine deck to power the tracks and raise the leader.
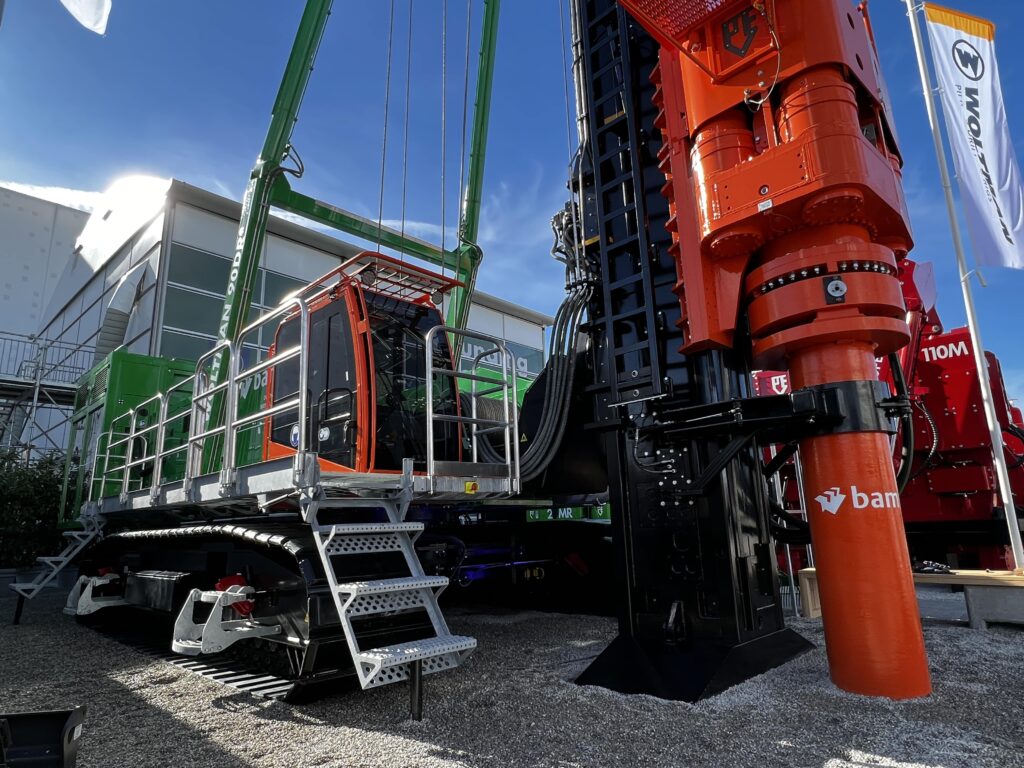
Energy and power
The total battery capacity is therefore 1200 kWh and the maximum power output is 613 kW, which is enough for a typical working day and is more power than the diesel rig on which the new machine is based. The maximum torque that the hydraulic drilling motor applies to the leader is 500 kNm, and the maximum pull-up force that can be generated by the winches is 80-100 t.
To determine how much battery capacity the Woltman 90DRe would need, Dieseko’s engineers analysed the performance and energy use of several comparable diesel machines during a typical working day with an energy reserve, which got them to the figure of 1200 kWh. Plotting that on a graph shows multiple power spikes through the day, each peaking at around 400 kW and representing the installation of one pile. This rig’s 613 kW provides it with a confidence-boosting margin.
The main engineering challenges Dieseko faced in developing the electrified rig were centred on knowing the domains of electric powertrains, electronic controls, time, space and systems integration. “We are a mechanical company with a lot of hydraulic knowledge, but limited electrical knowledge,” Legtenberg says. “So we had to find expert partners – that was very important.”
Dieseko therefore chose Webasto to provide the complete battery system, including its thermal management and power distribution subsystems, and Danfoss to supply the electric motors and power electronics. IFM supplied the overall control system for the rig, while for electronic management of the valves in the hydraulic system as well as the operator’s controls in the cabin and system integration, it turned to VSE Industrial Automation, a specialist in electrical control systems for heavy machines.
“Time was an issue,” Legtenberg says. “We had a year to build this machine, which is only a little longer than the regular production time for a diesel-powered rig.” The compressed timeline resulted from BAM’s requirement to be ready for zero-emissions operations by the start of 2023 and Dieseko’s desire to present the machine at Bauma in November 2022.
“And space was also a challenge because these batteries are very large. The electric motors are very compact, but the amount of electronics you need to control everything is amazing, almost doubling the space you think you need.”
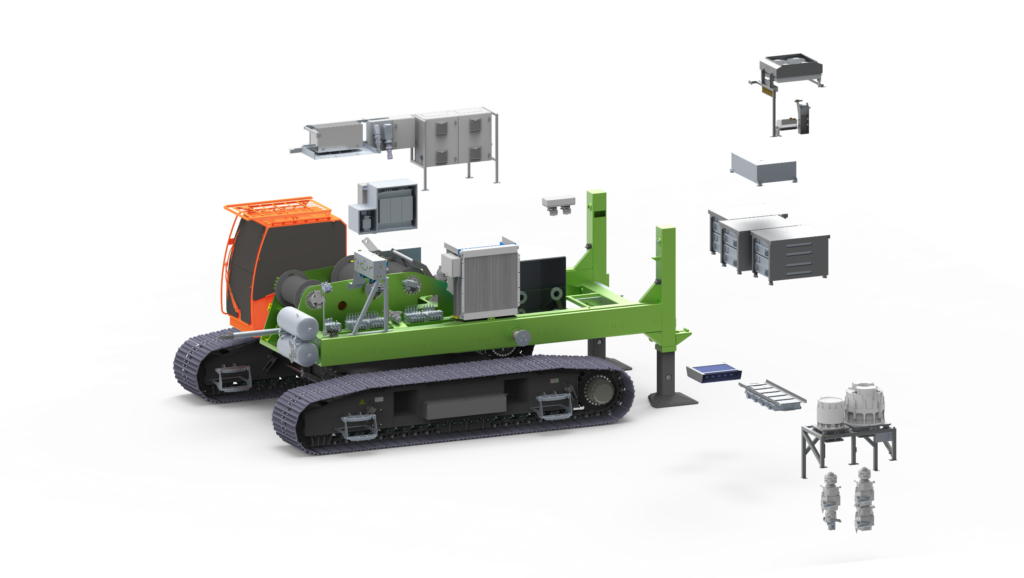
Mobile versus industrial batteries
Legtenberg reports that the team initially looked at suppliers of industrial-quality batteries, but soon changed tack.
“Industrial quality sounds good, but what we need is mobile quality,” he emphasises.
“Mobile quality means the batteries can withstand off-road use, high g-forces and rough environmental conditions, while industrial quality is more for stationary applications in factories. Even in this market there are not many companies that know the difference.”
Integration was also challenging, he says, with five companies with different areas of expertise all having to understand one another to work together. “Our project manager Stephan Reedijk did a very good job in this, but not everything went smoothly, as supply chain issues affected the newest electronic control platform hardware that IFM would deliver for the 90DRe.
“All the programming was done on that new platform, but in the summer of 2022 we got the bad news that the market introduction of the platform was delayed till 2024,” Legtenberg recalls. “So then I had VSE reprogram all the hardware for an existing, IFM platform. That was a real setback.”
The end result was positive, however, as VSE created a complete new control system for the machine that will also be used on all the other rigs that Dieseko builds from now on.
Regarding the battery system’s development, Legtenberg admits to some early scepticism about Webasto’s ability to deliver on time, but that soon passed. “I got the feeling from their top management that they put a high priority on our project,” he notes. “They put a good team together for us and we got all the cooperation we needed.
“VSE also had weekly Teams meetings with the Webasto guys. It was excellent, and it was a critical factor in the project’s success.”
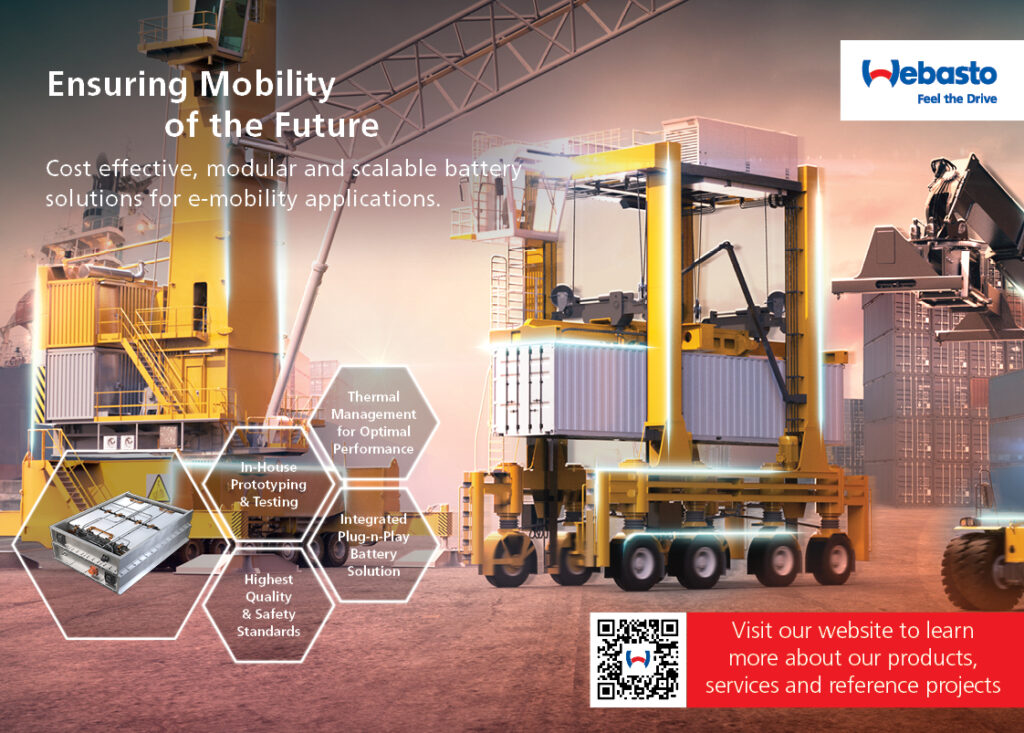
Powertrain team building
The project benefited from an established working relationship between Webasto and Danfoss on integration of the batteries with the power electronics and the motors, adds Rainer Beckert, Webasto’s senior sales manager for e-mobility. “The system was already partly pre-aligned and pre-tested with some of the Danfoss components, as we had already done a lot of projects together,” he says.
The battery system Webasto supplied is modular and based on the company’s Commercial Vehicle (CV) Standard packs, which come with its vehicle interface box (VIB) and electrical battery thermal management (eBTM) system.
The VIB serves as an interface between multiple battery packs and the vehicle while also fulfilling the functions of a power distribution unit, a master BMS and fuse box. The eBTM provides up to 10 kW of heating power and 8 kW of cooling power to keep water-cooled battery packs at their optimum temperature, despite any extremes of ambient heat or cold.
“Webasto provided a nice, rounded package and we did not have to do a lot of shopping to find additional components,” Legtenberg says.
Getting into a technology so new to the company, and still evolving, brought what Legtenberg calls a forest of uncertainty regarding the standards and norms they would have to comply with. This is another area in which working with Webasto was helpful, he says, as its battery systems already complied with a lot of standards relevant to electric powertrains for mobile machinery and road vehicles.
He also points to the extensive environmental testing that Webasto carried out on the battery system, particularly shock and vibration tests using shaker rigs.
Christian Kiemer, e-mobility application engineering manager at Webasto, points out that the company’s facility in Hengersberg, Bavaria, has a very large shaker rig that can generate accelerations up to 50 g. “The shaker is in a climatic chamber, so you are not only shaking test items but doing so in harsh conditions such as very low and very high temperatures, so you can simulate a lot of use cases,” he says.
“There are not many of these shakers in Europe, maybe two or three, and one is in our facility. This helps a lot to make the batteries as robust as possible, especially for the off-highway market.”
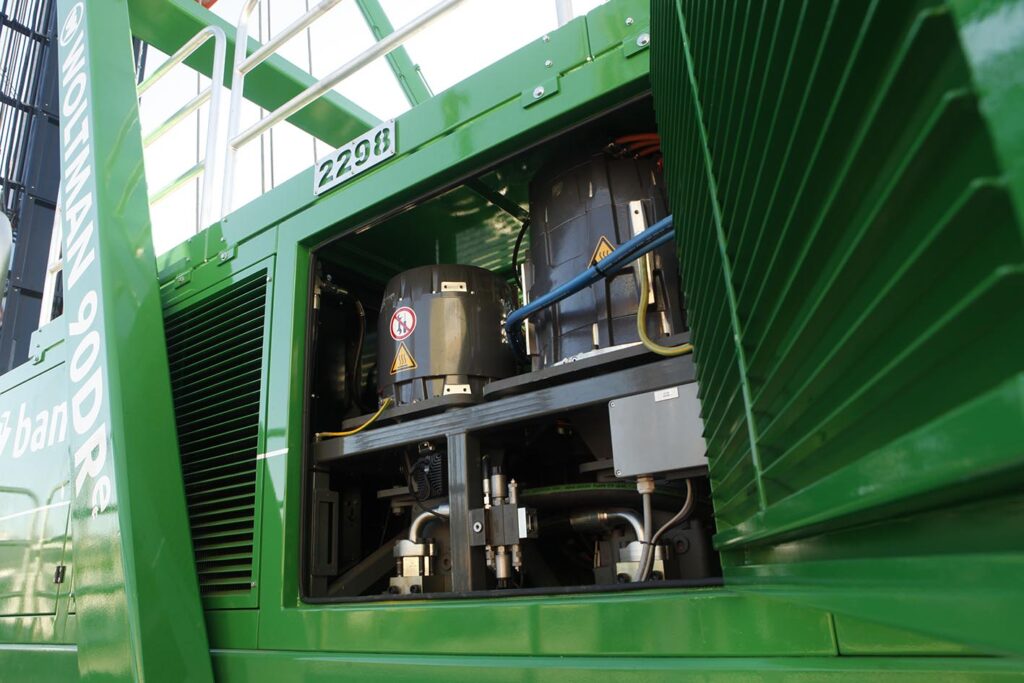
NMC over LFP
Legtenberg emphases the importance of cooling the battery pack, which is based on lithium nickel manganese cobalt oxide (NMC) cell chemistry and is inherently more vulnerable to thermal runway than lithium iron phosphate (LFP).
“There was a lot of discussion about whether we should use LFP or NMC batteries,” he says. “We decided that the Webasto NMC batteries would be best for off-road applications because they have a high energy density, are highly certified [including for control of thermal runaway] and can also run in freezing temperatures. On the construction site, you need robustness and high energy density, and in winter you need to start in the morning after a cold night.”
The only part of the battery system not supplied by Webasto is the 2 x 12 V battery used during start-up for the high-voltage system, powering the BMS and closing the contactors on the 800 V packs.
As the whole system runs on DC, the power electronics boxes perform the DC-DC conversion and voltage regulation. Nominally rated at 800 V, the battery supplies the DC bus with 790-670 V over the course of the working day.
Legtenberg explains, “This DC bus voltage is converted to 840-890 VDC by the DC-DC converter to a central DC bus voltage. The voltage drops more than an LFP battery would, so we need the converter. With this set-up, we can still use the maximum power of 613 kW at the end of a heavy working day, even when the batteries are quite empty.”
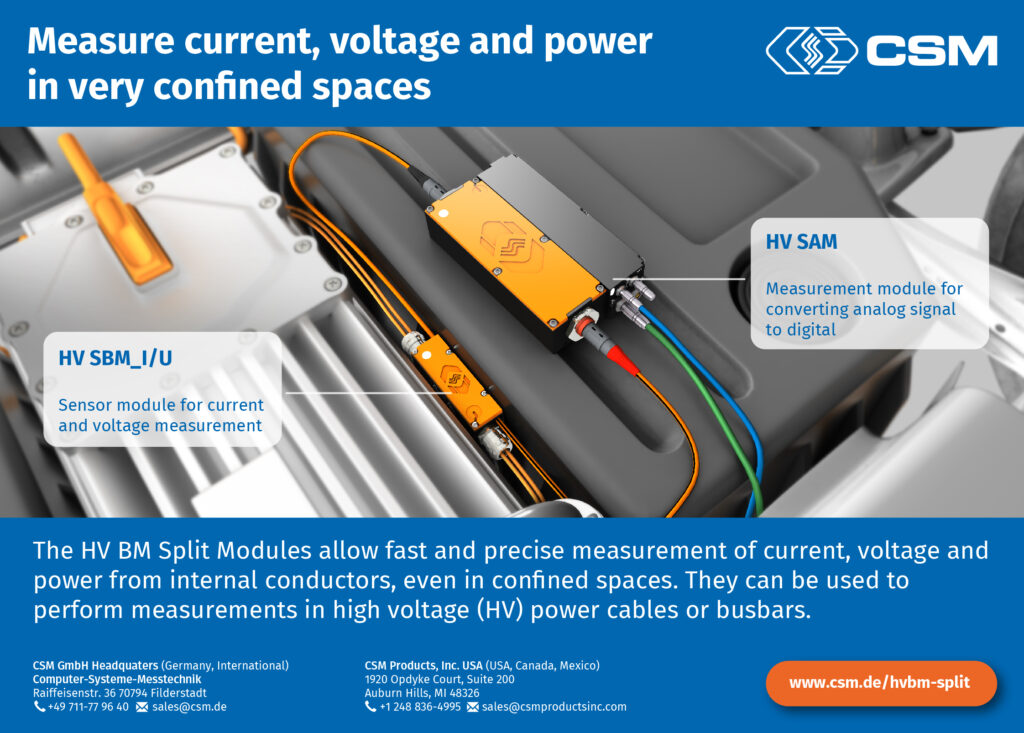
Although the 90DRe is a very large machine, space and weight are at a premium because of packaging and transport constraints, and the high voltage allows the size and weight of the conductors to be reduced for a given power draw, Kiemer says.
The battery system also supports charging from the mains during operation. While not needed to provide maximum power, this simultaneous charging and discharging provides the ability to top up the battery pack if the machine has to use more energy because of heavy ground conditions.
Electro-hydraulics
Each of the two Danfoss PM motors drives its own hydraulic pump. When the rig needs to move under its own power between piles, the smaller of the two motors draws power from the smaller battery pack installed on the machine deck to power the hydraulic motors that drive the tracks and the smaller winches.
When the rig is in position, the larger motor draws from the main pack in its container attached to the back of the machine deck to power the big winch and whichever tool is fitted to the leader.
When maximum power is required, however, both motors draw from both sections of the battery pack, and all the hydraulic flow from both pumps can be directed to the winches and the tooling. Together, the low and high-pressure pumps can deliver hydraulic fluid at up to 350 bar.
Dieseko has a patent pending on this system, which improves overall energy efficiency. “We could have chosen to go with one big motor,” Legtenberg says. “Not only is this a zero-emissions machine, we also want to optimise it so it consumes less energy.”
The hydraulic pumps feed manifolds that supply all the winches, motors and numerous cylinders. The leader is folded down and laid flat on the machine deck for transport, so it is raised into its operating position hydraulically. The pins that secure the battery container to the rear of the machine deck, and open to allow it to be removed for transport and maintenance, are also hydraulic.
The electro-hydraulic management system also includes a suite of sensors to measure parameters, such as pressure and flow and motor speeds that indicate how much power is required at any given moment, along with sensors that monitor the condition of the machinery.
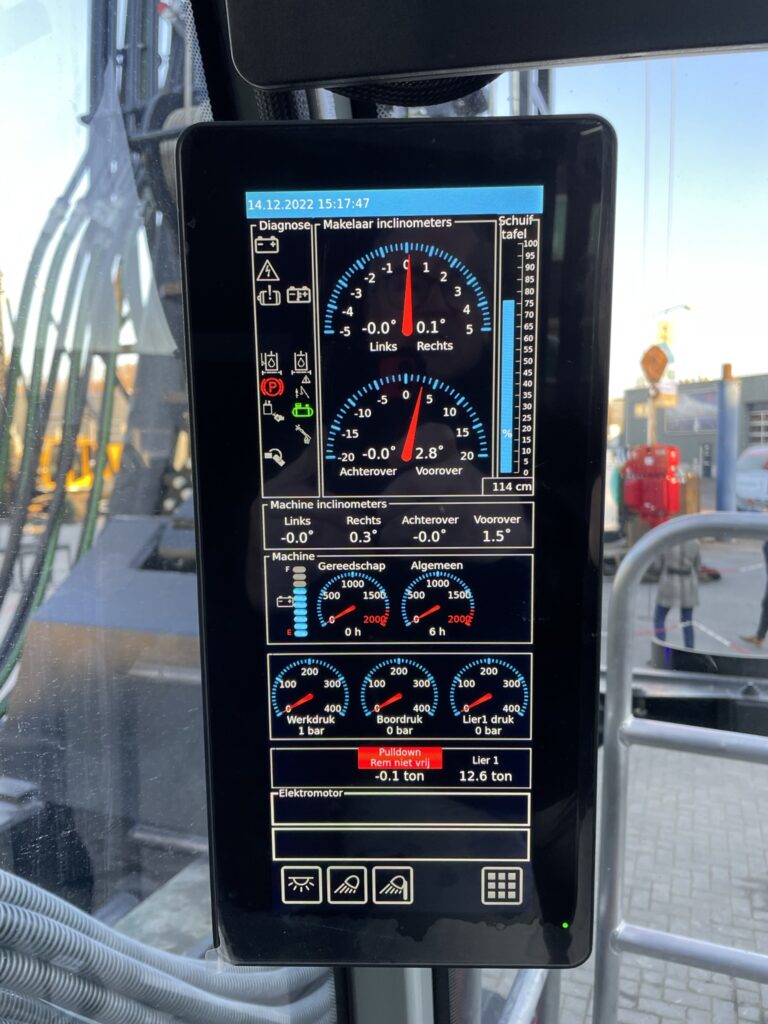
Operator controls and displays
In terms of control, the 90DRe is essentially a drive-by-wire machine, with everything from the joysticks in the operator’s cabin to the hydraulic control valves in the manifolds generating or responding to signals processed in ECUs.
The operator is provided with a comprehensive set of displays dealing with start-up and shutdown procedures, pile drilling and driving operations, performance and health of the batteries, inverters and motors, battery charging and system diagnostics, for the moment all labelled in Dutch. Among the most important displays for pile drilling and installation, for example, are two inclinometers that show the angle of the leader from the vertical in left/right and fore/aft terms.
Despite the time constraints, and the electronics hardware supply problem, development was completed in good time, Legtenberg says. Dieseko signed the contract with BAM in November 2021, and the 90DRe was presented at the Bauma event in November 2022. When the machine returned from the show, there was still some final testing to be done, so its first job at Schiphol Airport effectively served as an operational trial.
“BAM did an extremely good job,” Legtenberg says. “It was not a big job; it was to drill 30 piles in, but it was a perfect test.
“We were concerned that, every day, service engineers, software engineers and mechanical engineers from the development team should go there or log in to the machine remotely to solve any bugs. I expected that to take 2 or 3 months, which would have been reasonable, but there was practically nothing, only a few minor things they had to adjust.
“I was amazed, because normally Murphy’s law is on your case, but it was just one filter that had to be upgraded because it was getting a little too hot, and one cable connector proved a little weak, so we had to find a new connector.”
The filter was a power electronics component in the charging circuit, essentially a transformer that serves to smooth out the ripples in the charging voltage. “We went one size bigger, and that solved it. I was really impressed with the machine’s reliability because there were so many new components involved,” Legtenberg says.
The Schiphol job attracted a lot of interest from potential customers and competitors. “It is a slow-moving market defined by Dutch rules,” Legtenberg says. “We see that the government and the four big cities are tightening their zero-emissions requirements and, based on that, we expect to sell more soon.”
Development paths
Beyond the 90DRe, Dieseko is looking to electrify a smaller machine such as the Woltman 55DR. With an eye on reducing the price of electrification, the company has started developing a battery-powered electro-hydraulic powerpack that can be connected to the hydraulic system of existing diesel-powered machines to enable them to operate in zero-emissions mode when required.
Another line of development is the electrification of pile drills and vibratory hammers, which could yield an energy saving of around 20-25% over hydraulics, Legtenberg says. Of these, the vibratory hammer is the more challenging, because the motor will have to be mounted on the moving part and will therefore have to withstand sustained high-frequency 20 g accelerations, with peaks of 40 g during rebound. Pile drivers work hard.
Some key suppliers
Battery system: Webasto
Motors and power electronics: Danfoss
Vehicle control system: IFM
Electro-hydraulic valves, operator controls and system integration: VSE Industrial Automation
ONLINE PARTNERS
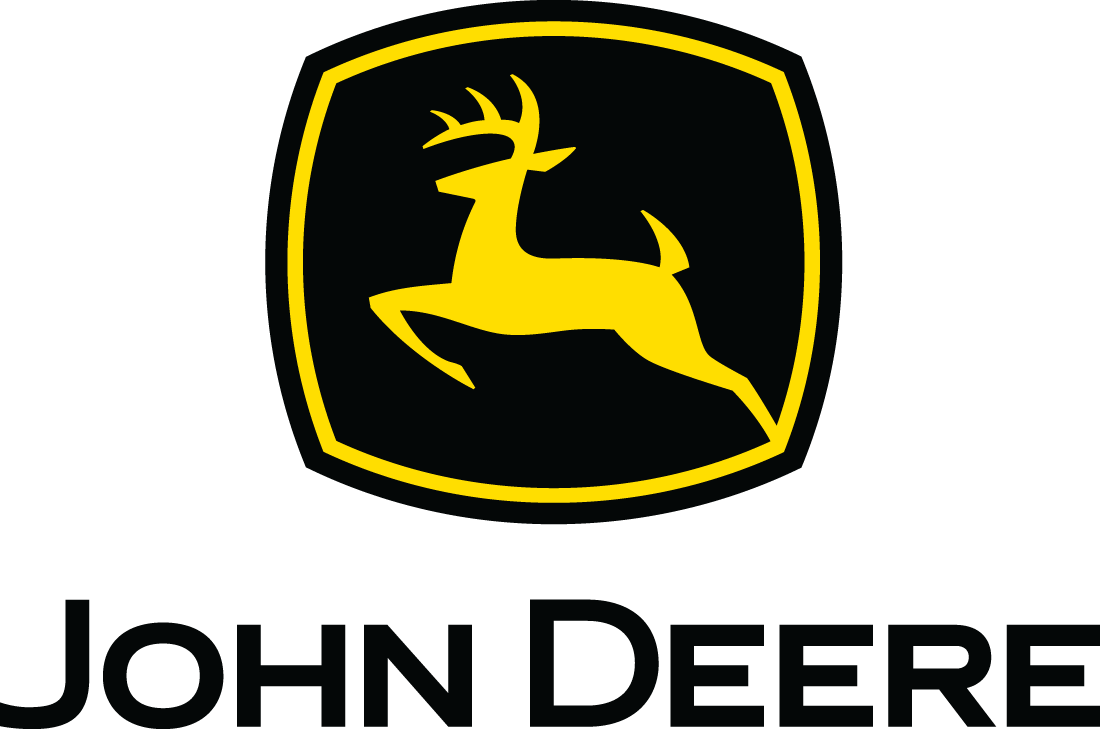
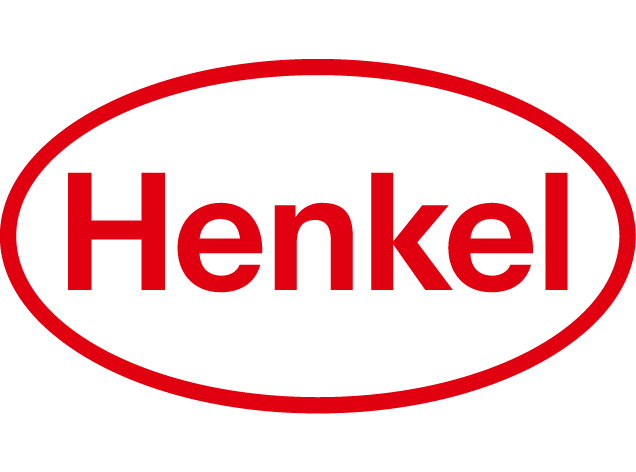
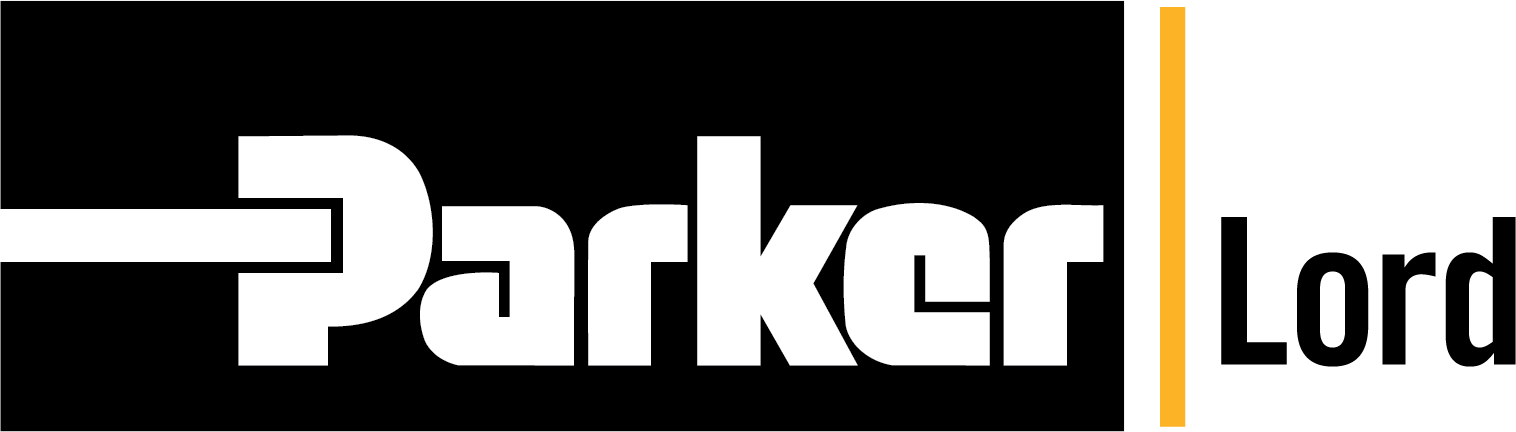
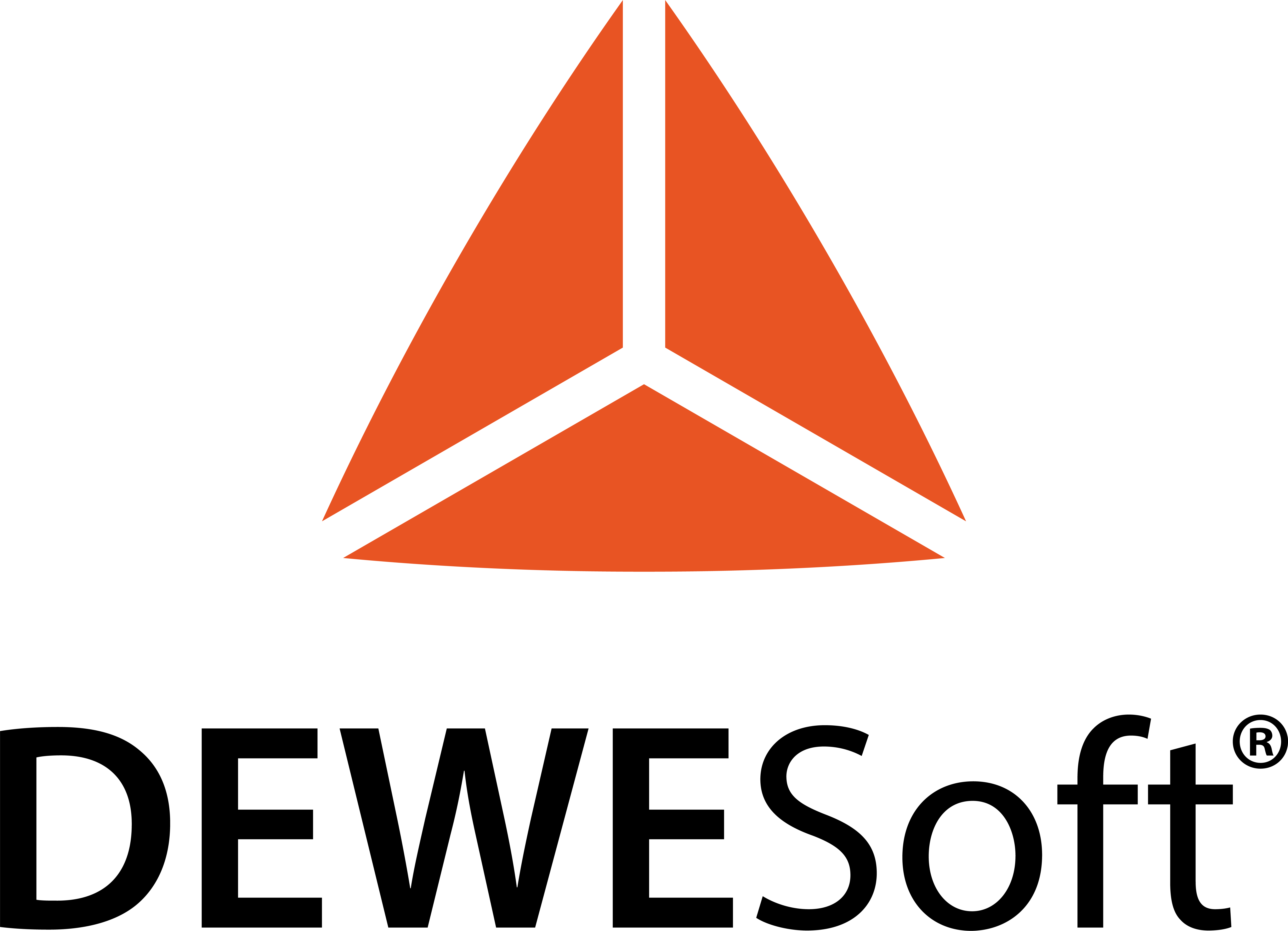
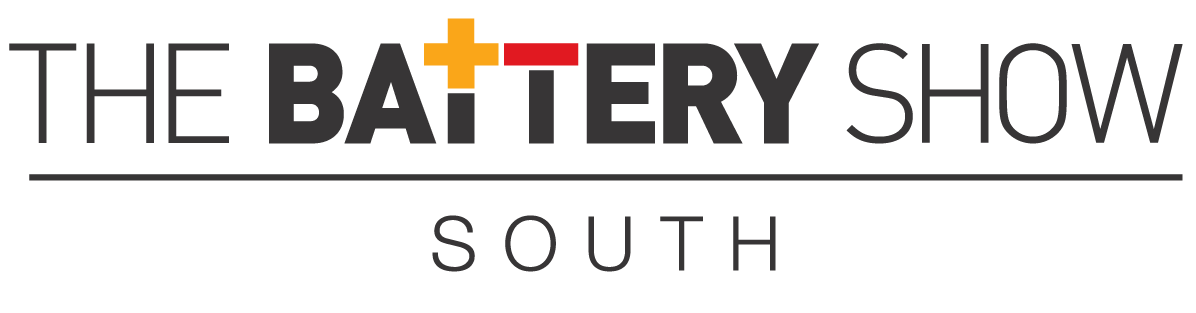
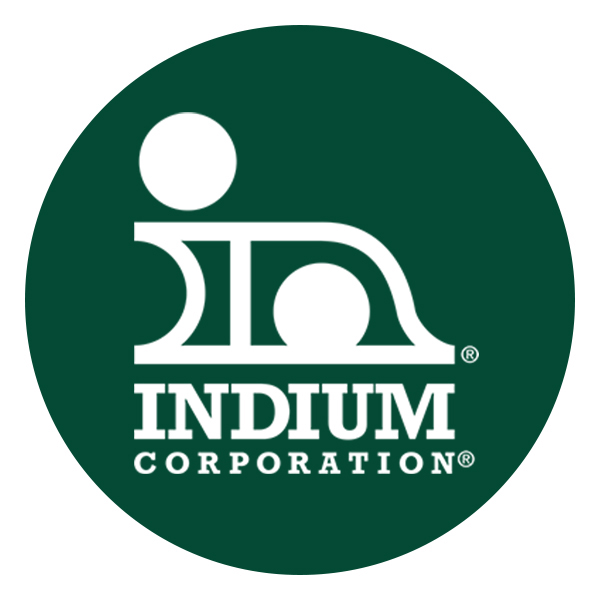
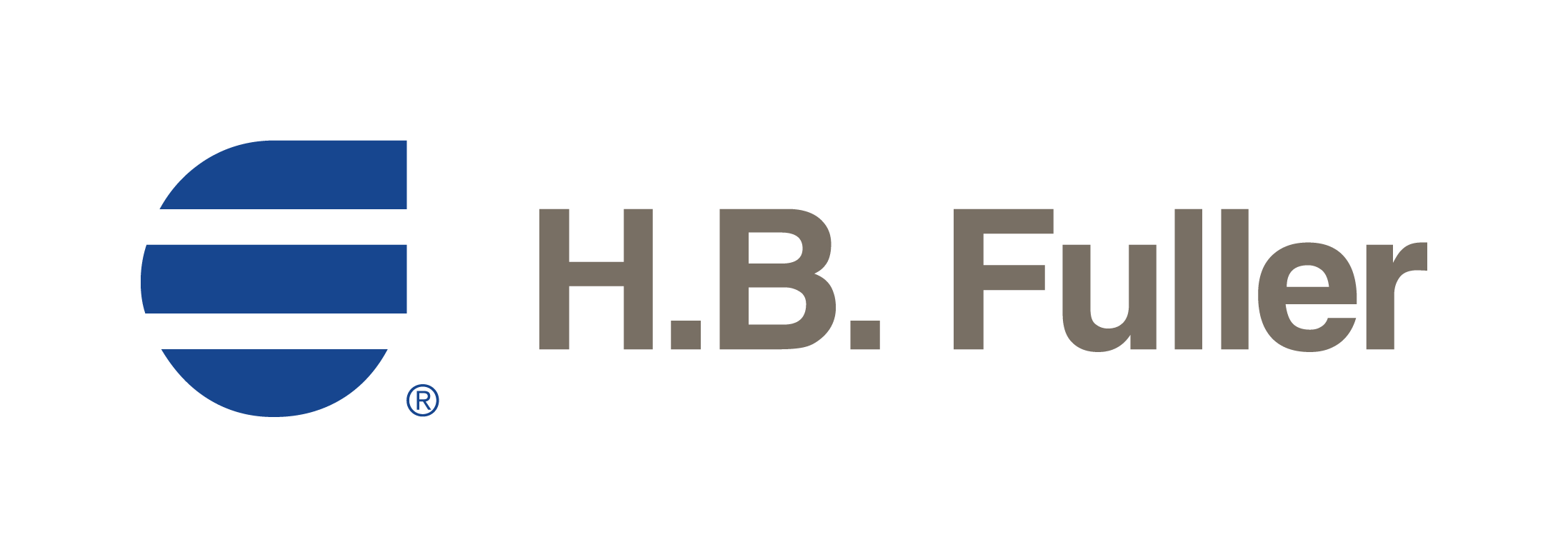