David Richards
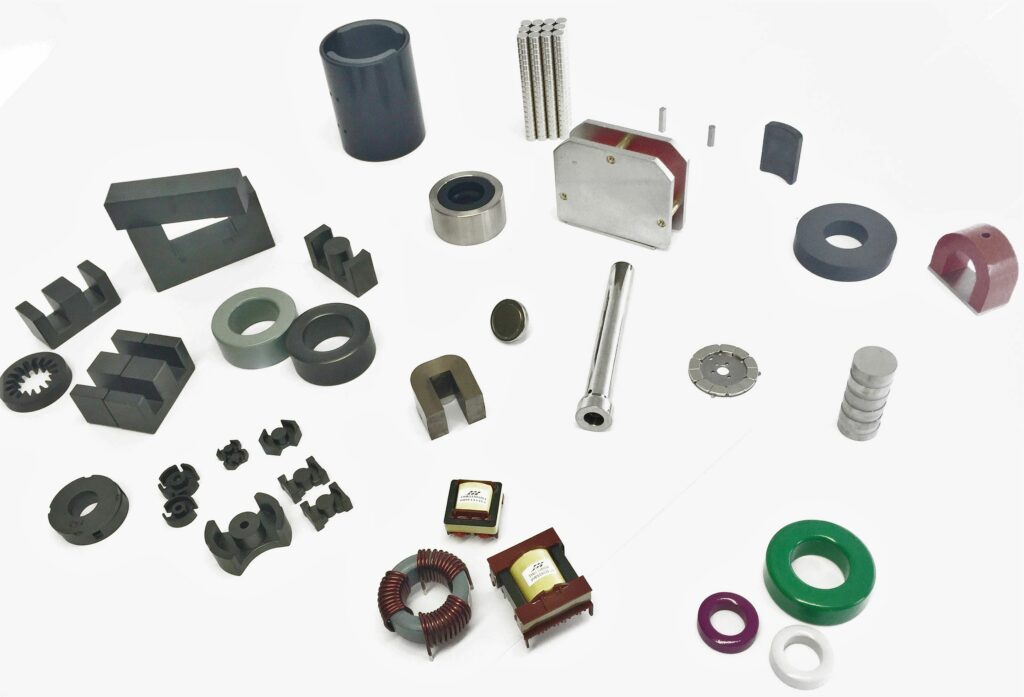
(Courtesy of MagDev)
Magnetic Compass
The technical manager at permanent magnet supplier MagDev gives Stewart Mitchell some pointers on their design and choice of materials for e-drive motors.
With the ever-increasing drive for e-mobility, the development of permanent magnet electric motors and their associated power electronics is now one of the most heavily investigated areas of engineering in the transport sector. The demand for high-performance versions of such motors has risen dramatically in all applications where high power density, high dynamic performance and high efficiency are of prime interest.
David Richards, technical manager at permanent magnet supplier MagDev, explains some of the science behind permanent magnets and some of the issues e-drive system manufacturers should consider when specifying permanent magnets for their application. He says, “For electric motor applications where high performance from a small packaging envelope, light weight and high efficiency are desired, rare earth permanent magnets such as samarium cobalt and neodymium iron boron are the most popular solutions. These rare earth magnets are typically 10 times stronger than the best ferrite magnets on the market today.
“The strength of a magnet influences the weight of the motor system. Because of its strength, you can use much less rare earth material than with other magnetic materials such as ferrites. If you like, it’s a magnetic power density of the material.
“However, rare earth magnets are more expensive than ferrite options, and have characteristics of their own that must be considered.”
We asked him: what defines the strength of a magnet? “That is what is known as the magnetic flux, which is measured in a unit called a gauss. Typically, electric motors use magnets with a gauss of between 4000 and 6000. You want that to be as high as possible for higher power density applications.
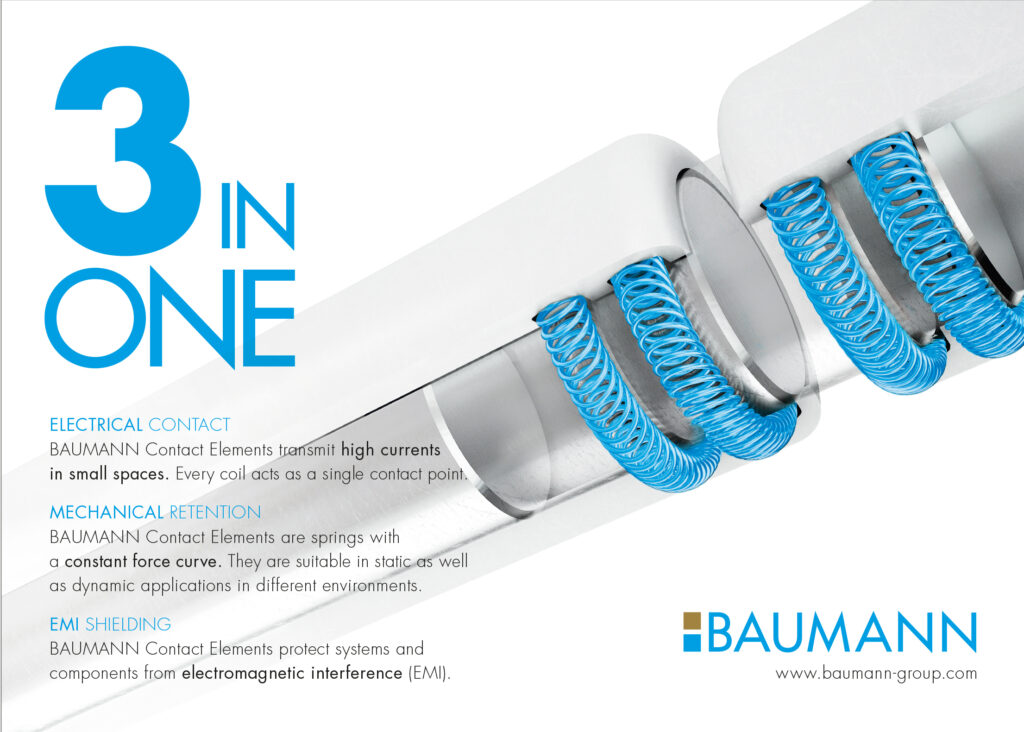
“To move something more efficiently with magnetics, you have to create a bigger force. For that, you generally want a higher field strength. Gauss is not a property that we adjust up and down; the material’s properties define the amount of gauss it has, and we saturate the material when we magnetise it to give it the most magnetic flux it can carry.
“The magnetic flux and surface area of the magnetic material have a linear relationship. If you double the area for a given material at full magnetic saturation, you will get double the flux.
“However, the strength throughout the depth of a magnet is slightly different. A magnet reaches a point where the increase in magnetic field strength over the depth plateaus out.
“The magnetic strength on the face of the magnet increases with the depth until the depth reaches three-quarters of the area of the face of the magnet, after which you’re not getting much more strength on the face.”
Which materials can rare earth magnetic materials interact with? “It will interact with anything ferric, like steel, but to an extent the magnetic field will also pass through other materials such as brass and aluminium.
“However, when you have a magnetic field passing through a partial conductor you get resistance, in the form of eddy current loses and back-EMF. If we want a magnet to interact with aluminium, because aluminium is a partial conductor a lot of eddy current losses can occur. As the magnet interacts, that interaction creates a back-EMF that acts like drag, and if it continues for a prolonged amount of time it can generate heat.”
How has rare earth permanent magnet technology developed in recent years? “The biggest developments have been in refining their ability to withstand temperature, which can be critical in a motor application. As they warm up, permanent magnet materials can lose some of their magnetic strength, and after a certain threshold they can become completely demagnetised.
“There are various grades of rare earth permanent magnet materials. Entry-level grades can deal with around 80 C, and you can get grades with a working temperature as high as 250 C.”
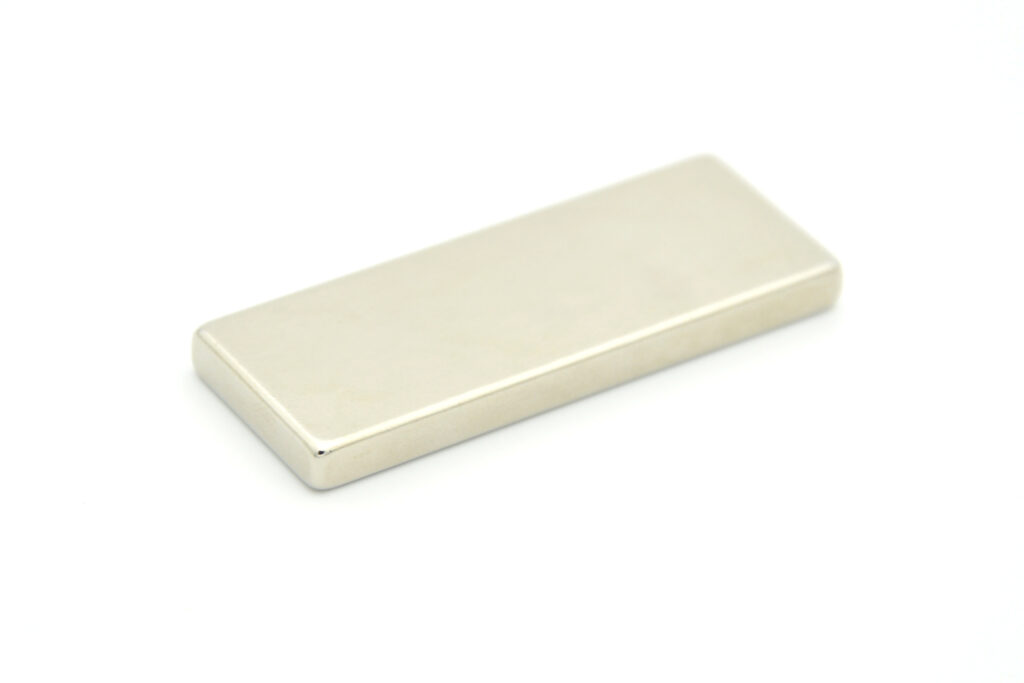
(Photo: Peter Matiss)
Manufacturing
How are rare earth permanent magnets manufactured? “They are sintered, which is a process of compacting and forming a solid mass of material by heat and pressure without melting them to the point of liquefaction. They are brought up to a given temperature for a regulated amount of time under a given pressure. After the sintering process, the material is often wire-eroded into the desired shape and then carefully ground for the desired surface finish.
“The manufacturing process has to be carefully controlled, because when the powder is being compressed, there is a risk of creating air pockets or voids in the part. That is unusual, but it does happen on the odd occasion, and it causes a weakness in the magnet.
“Also, many companies coat the magnets, using a nickel-copper-nickel layer for example, which is typically 10 to 15 microns thick. That protects the magnet from corrosion, and gives it some protection against chipping and other surface damage. For example, 70% of neodymium iron boron is iron, so it will rust if it is not coated against exposure to moisture.
“One consideration with respect to coatings is that, if you’re going to glue the magnets into position onto a rotor, the nickel-copper-nickel layer doesn’t provide a very good adhesion surface; you might want to go with a zinc coating instead. That said, most of the permanent magnets used on e-drive motors are located in a recess to prevent the magnet from moving.”
How does zinc compare to the nickel-copper-nickel layer regarding corrosion resistance? “It’s not as good. Anyone using zinc coatings must take that into account, and steps must be taken to further protect the rare earth or isolate it in some way.”
What are some of the factors that cause magnet-to-magnet variation? “That is caused by the same factors that cause variation in any material manufacturing process.
“In this case, the alloying elements can be different from batch to batch, and the quantity of ingredients can differ in small percentages too. Within a batch though, the material properties are often very consistent, because all the magnets in it went through the same process.
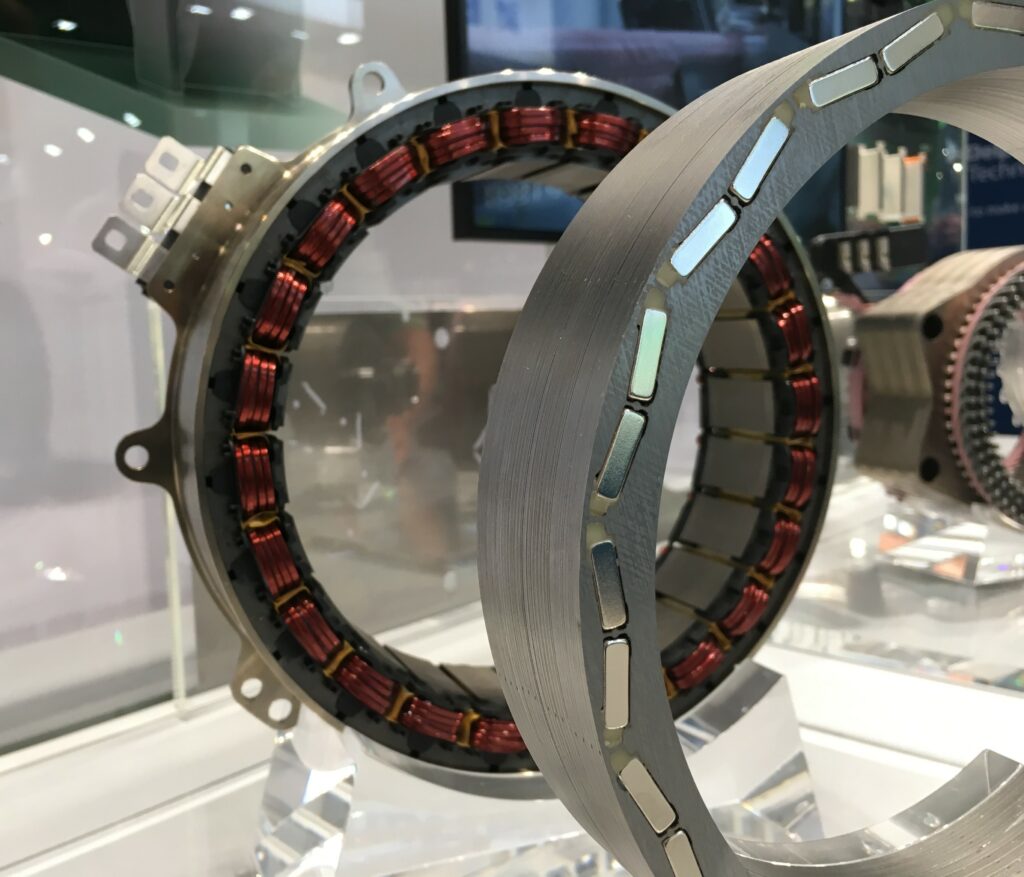
(Photo: Stewart Mitchell)
“However, batch to batch, you could see as much as 10% variation in the amount of a given element in the alloy. It is always important to choose a supplier with high quality control when it comes to the magnets used for e-drive motors, as a 10% difference in material properties in the rare earth material can directly correlate with a 10% loss in motor efficiency.”
What is involved in magnetising a rare earth magnet material? “We place the material we want to magnetise inside a coil that is close to the outside of the part. We then use a big capacitor that sends a huge charge through the coil. Our magnetiser uses 30,000 A for about a millisecond through the coil, effectively generating a very high magnetic field that lines the magnetised elements in the material north and south.
“The coil’s orientation determines the axis of the magnetic field inside the material; the material can only be magnetised in one direction. When discussing magnets for motors, they need to have very strong north and south poles. Generating a very strong north magnetic field next to a very strong south magnetic field is not easy however.
“Ferrite, which is a cheap magnetic material, is very easy to magnetise, you can create a jig to magnetise the rotor elements with the rotor components fully assembled. With rare earth magnetic materials though, if you want to get the north-south opposing fields, you have to magnetise the parts with the capacitor coil and assemble the magnets into the rotor in the desired orientation in that order.
“You need about 3 Tesla to magnetise most electric motor permanent magnets to saturated level. If it’s less than that, it isn’t stable and the field could break down or its orientation could move. That’s why you want to take it up to the full saturation level to fully magnetise it, and then you know how it’s going to perform.”
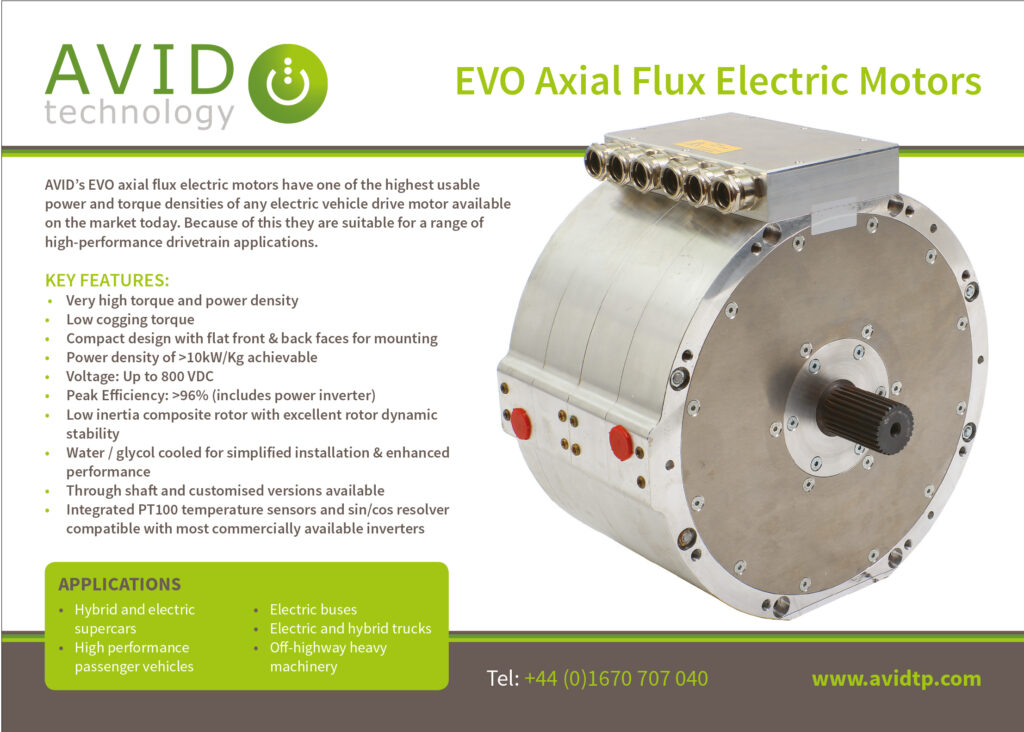
How do you measure the saturation? “Each rare earth magnet material has a demagnetisation curve. You can plot that parameter and check it using magnetic field measurement systems.”
Is the flux the same all the way through a magnet, or is the outer side or the very core of it stronger or weaker? “The strength of the magnetic flux is different in different sections of the magnet. There is a phenomenon called the edge effect, which means that at the edge of a magnet the flux is higher and so the magnetic strength is stronger than in the centre.
“That effect is not very dramatic on small magnets, but anything bigger than 1 cc and you’ll start noticing the difference between the centre and the outer edges. We call that the dish effect. That is important as far as designing motors is concerned, because you want the coils to be interacting with the magnets where the field is strongest.
“Because of the edge effect, if you increase the number of magnets for a given rotor size, there would be an increase in magnetic flux density. However, that is only true up to a point.
“It is most obvious when it comes to applications where a disc-shaped magnet is used. We worked with a customer who was using a disc-shaped magnet for their application, and we worked with them to provide a ring of similar geometry without a central core. After testing that ring shape, they found that compared to the disc magnet it provided a higher flux density for the amount of magnetic material they used.
“The flux is related to area which, in the case of the ring design, was higher on the surface than the disc, so it produced more flux. It was getting rid of the low field strength in the centre of the disc. Overall, there was less material with less cost and even more flux out of the magnet.
“There is a trade-off with this phenomenon at a certain point where if the magnet is too small, the amount of magnetic flux it can carry isn’t enough to be useful in an electric motor application, and it is more susceptible to demagnetisation. That occurs when the geometry of each magnet doesn’t have a depth of one-third of the surface for optimum flux density. However, for the most part, the larger area will produce better performance.”
Can rare earth magnet materials be used as stressed components? “Absolutely not. These alloys are very brittle and would fail if they were loaded. They are even susceptible to cracking under vibration. There are bonded alloys that have neodymium iron boron elements in them that can be manufactured into load-bearing components, but they have half the strength of a full neodymium iron boron magnet because the rare earth elements are diluted in this type of alloy.
“Also, the magnetic flux in these bonded alloys isn’t easily orientated; it’s just neodymium flake that is tipped into an alloy pot, so making a useful magnet from them isn’t very easy. For e-drive motor applications, the magnetic flux that could be generated from the bonded alloy would probably not be acceptable.
“However, you are stuck somewhat with a catalogue size and shape of these neodymium iron boron magnets because they are not easy to manipulate during post-production. You need diamond-impregnated tools to grind rare earth magnets because they are so brittle and hard. Many neodymium iron boron magnets are manufactured using wire eroding, and motor manufacturers typically don’t have that kind of capability.”
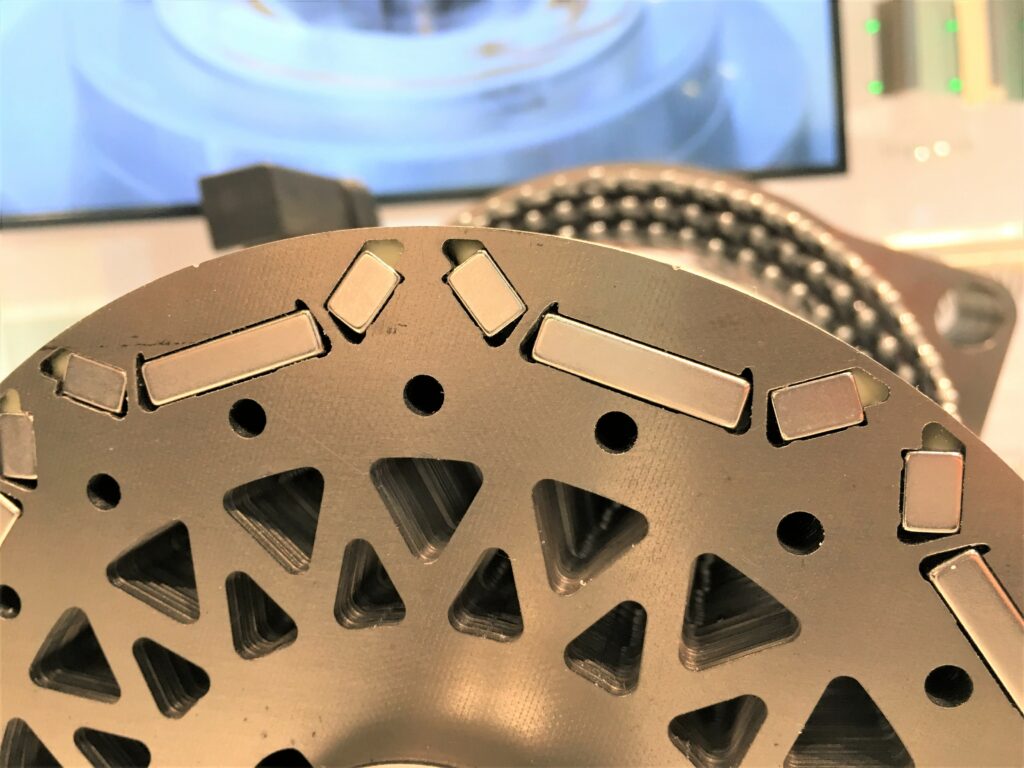
(Photo: Stewart Mitchell)
Temperature considerations
How do you define the temperature within which a magnet can operate? “The temperature window for a magnet is defined by the material alloy it is made from, the size of the magnet and its magnetic flux. There are many different grades of magnets on the market, and there is magnet standard that defines these properties from every supplier.
“In general, as the required magnetic flux and temperature resistance go up, so does the cost for each unit. For traction drive motors, for example, one of the biggest considerations is a magnet’s temperature resistance, because for automotive applications the motor must operate efficiently in a wide range of environments and applications.
“In general, the cooler you can keep a magnet the better, as it means you can use more of its flux. The more you heat it up, the less effective flux you have.
“If a rare earth magnet is operated above its specified peak working temperature, you can quickly get to a point where the magnetic flux begins to break down. After long exposure to temperatures above the specified working limit, the magnetic flux can completely dissolve, and you would need to re-magnetise the material.
“That phenomenon is similar to elastic and plastic physical deformation in a material, in that up to a certain threshold the magnetism will return, but above that it won’t ever come back and the property is gone.”
What generates heat in electric motors? “A number of things. The first is just the physical movement. Some automotive motors spin at tens of thousands of rpm, which generates friction in the airgaps between the rotor and the stator, and that heats up the components. You also have eddy current heating as well, which is produced by a magnet spinning in a magnetic field near a conductor.”
How close can you run a permanent magnet to its upper temperature threshold? “For an application that requires a 120 C working temperature, we would specify a magnet with a 150 C upper temperature limit or, more precisely, a 25% buffer. That buffer will ensure that the magnet won’t become demagnetised.
“In general, samarium cobalt magnets have a higher temperature threshold per unit magnetic flux strength than neodymium iron boron, but they only have a certain amount of maximum magnetic flux. Neodymium iron boron rare earth magnets have far wider magnetic flux options.
“As for where one would use samarium cobalt over neodymium iron boron, that would come down to the temperature window the magnet is going to operate in. If it is anything over 150 C, we would suggest running a test with both neodymium iron boron and samarium cobalt to measure the losses with both alloys.
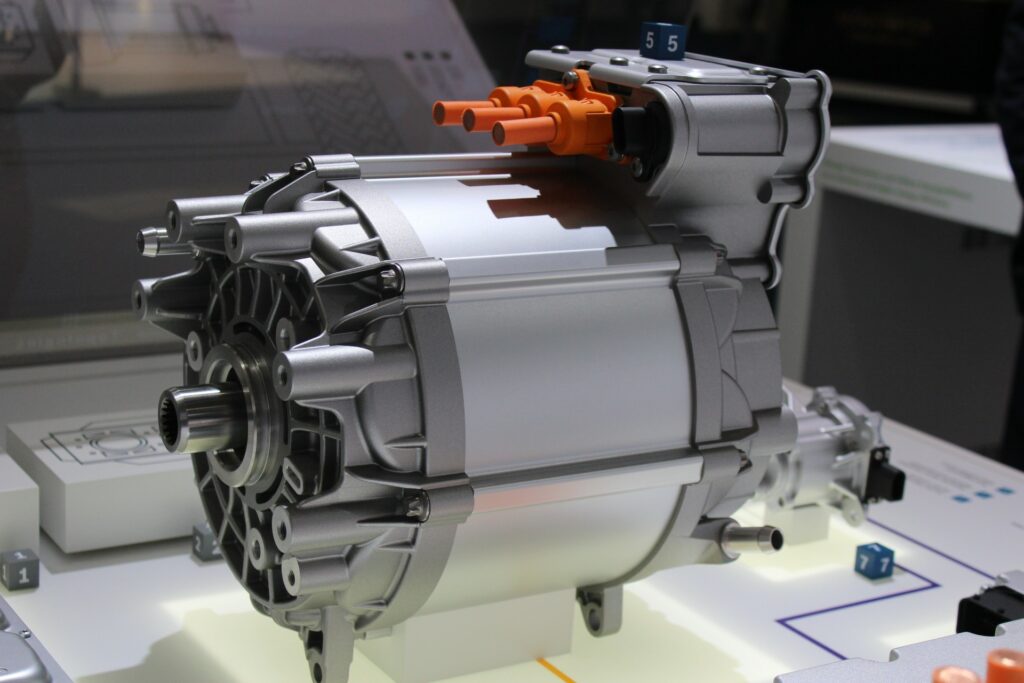
(Photo: Stewart Mitchell)
“The temperature is a difficult thing to characterise. If the high temperature lasts for just an instant and then falls, that can be fine for both alloys. In most cases, the magnetism comes back strong again after just a short burst of high-temperature exposure, but if the part is to be operated above 150 C for an extended period, you need to consider samarium cobalt as an option, simply because of its stability under prolonged exposure to this kind of temperature.
“If the magnetic parts need to run in even more extreme temperature environments, such as in a high-performance hybrid system – particularly one with energy recovery – there are even higher temperature resistant alloys than neodymium iron boron and samarium cobalt. Dysprosium for example is a ceramic-metal composite that is currently used to give rare earth alloys even higher temperature range. It is very expensive, however, and its supply market is very volatile, so the less dependent you are on such materials, the less exposed you will be to these markets and the more consistent the cost of manufacturing your motors will be.”
How much of the magnetic strength of a material remains at its upper temperature limit? “Most of the neodymium iron boron alloys have 80% of their magnetic flux strength at their specified temperature threshold; above that the drop-off is very dramatic. The operating conditions have to be carefully characterised, and all rare earth magnetic materials must be considered to find the optimum for a given application.”
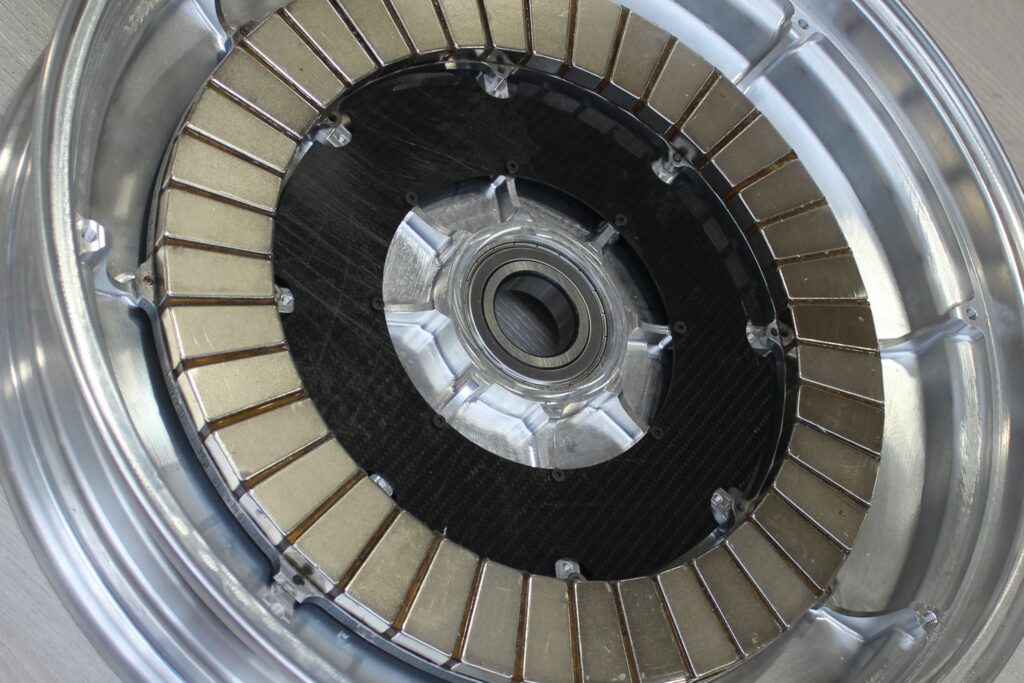
(Courtesy of Cambridge University)
Magnet selection
Are there any differences between the magnet type that someone would pick for a radial flux motor compared to that for an axial flux motor? “For axial flux motors, we typically specify neodymium iron boron blocks, some of which are as big as business cards. This solution is fairly expensive in this form though because of the size of these magnets.
“A radial motor often uses much smaller neodymium iron boron magnets embedded inside laminated rotor stacks. The radial flux design allows you to use much less rare earth material, which can be a huge proportion of the cost of the motor.
“Comparing the material for a radial flux motor to that for an axial flux motor is rarely about the grade. You could use any grade of rare earth magnet in either axial flux or radial flux motors, although for the same material, if you’re using less it will be cheaper.
“The target for both motor designs, especially in automotive applications, is power density within a given packaging envelope, and power density is quite a complex subject when it comes to the magnet. For the same grade of rare earth, the more concentrated the magnetic flux at each pole of the rotor, the more effective the potential of that magnet array.
“Therefore, creating a stronger magnetic field is not just about the volume of magnetic material. The more sophisticated the design and layout of the magnetic material, the more effectively the magnetic flux can be used to drive the motor, and therefore the fewer the losses and the higher the power density of the motor.
“A well-designed rotor can produce a higher power output per unit volume of magnetic material used and a given magnetic field than one simply with a lot of magnetic material inside. For a given power level, a well-designed rotor can use less magnetic material that has a lower magnetic flux and will therefore be cheaper than a badly designed counterpart.
“As such, the design of each pole and its orientation to the rotating magnetic field in the motor is more critical than the specific magnetic flux strength of the magnets you use. The vast majority of field strength is a function of the area of the magnet exposed to the rotating magnetic field.
“The more exposed the magnet, the more effectively the rotating magnetic field can act on the permanent magnet. You want the magnet to interact with as many coils as possible, so if you have a greater area of magnet exposed to the coils, you can get better interaction.”
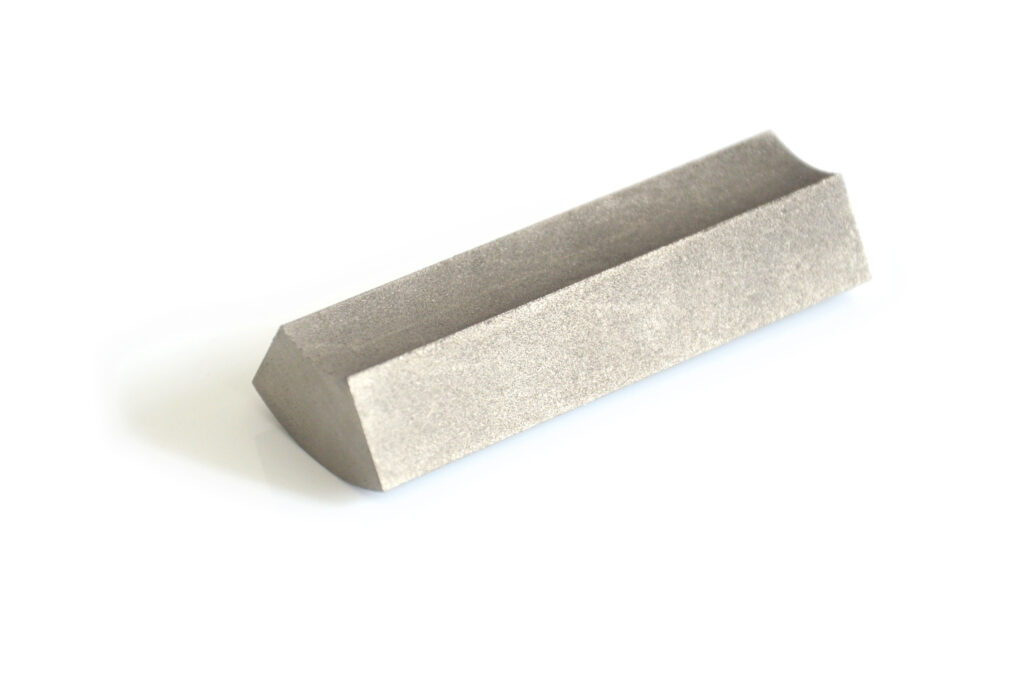
(Photo: Peter Matiss)
Rotor design
What are the benefits of having magnets embedded in the rotor, otherwise known as internal permanent magnet rotor design? “The primary function of the internal permanent magnet rotor design is to reduce the amount of magnetic material required in the rotor.
“Many automotive manufacturers use electrical steel lamination stacks to build up the rotor and locate the stator and coils around the outside of the rotor lamination stack. The lamination sits on the shaft that rotates to create drive. The benefits of this are obvious from a magnet point of view, as there is much less magnet material, which is a large part of the cost of the motor.
“It is also far simpler to assemble compared to surface permanent magnet rotors, because it uses much smaller magnets compared to the often rather large trapezoidal magnetic material chunks that many surface permanent magnet rotors use.”
How do you define how many poles you want in an electric motor? “For the most part, that’s based on the target speed of the motor and inverter technology rather than the magnetics. However, from a magnet perspective, the more poles you have over a given surface area of a rotor, the higher the number of magnets you need and the smaller the magnets are.
“That means the motor’s operation is more complex in the way that the coils in the stator are set up and how the rotating magnetic field interacts with the permanent magnets.
“The number of poles on the rotor must be even, because each magnet has a north and south orientation and they must be alternating around the rotor. The windings can be tailored in a number of ways, however, and that is to do with the number of phases in the motor and its maximum speed.
“For example, a six-phase motor can be programmed to run as two, three-phase systems within the control protocol. That set-up means the motor can be run in different ways – as a six-phase motor for high-power scenarios, or three phases to lower the load on the control system in steady-state or low-load conditions.
“That’s down to the control unit; it’s the switching between north and south that generates the power. It is only when the polarity changes from north to south do you get the change in flux, which causes the motion of the rotor, and the number of magnetic poles you have on the rotor determines the required switching frequency for a given rpm. The control technology defines the maximum number of poles more so than the magnet technology.”
MagDev
MagDev is a UK-based custom magnets and industrial magnet manufacturer specialising in supplying permanent magnets, magnetic assemblies and soft ferrite cores with magnetic properties tuned to specific applications.
It was founded in 1943, and in 1986 it became part of the MMG group of companies trading as Neosid. In August 2003, MMG MagDev was formed by the merger of MMG GB and Magnet Developments, operating from a group facility in Swindon, England.
At that time, the production of the Neosid range of soft ferrites was moved to another company in the MMG group, MMG India, based in Chennai. In June 2010, MMG MagDev and MMG India were acquired by Delta Magnets, and are now part of the DMG group of companies.
In March 2011 the company bought its present facility in Swindon as part of an expansion strategy following the acquisition of the company by Delta Magnets. In July 2012 the company changed its name to MagDev, as it remains today.
ONLINE PARTNERS
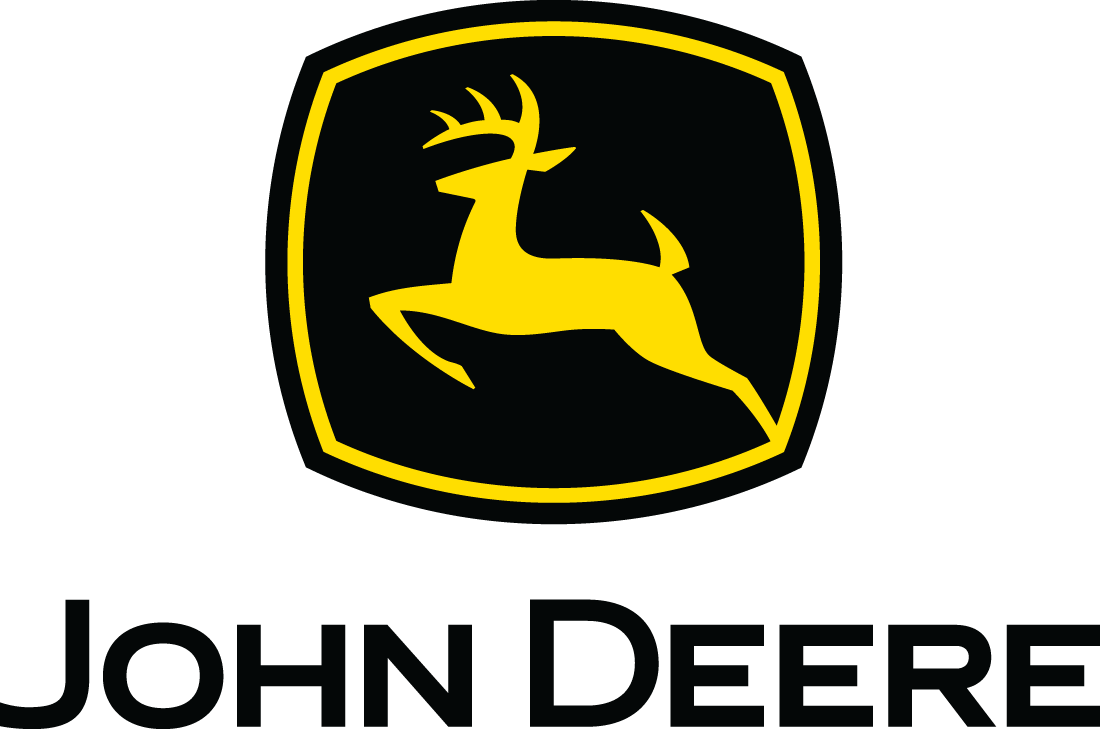
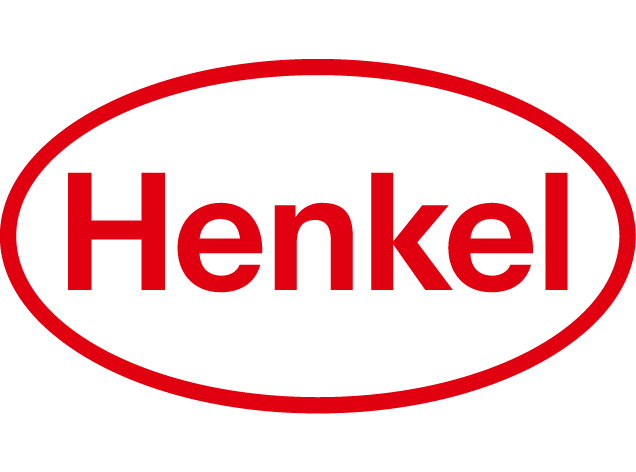
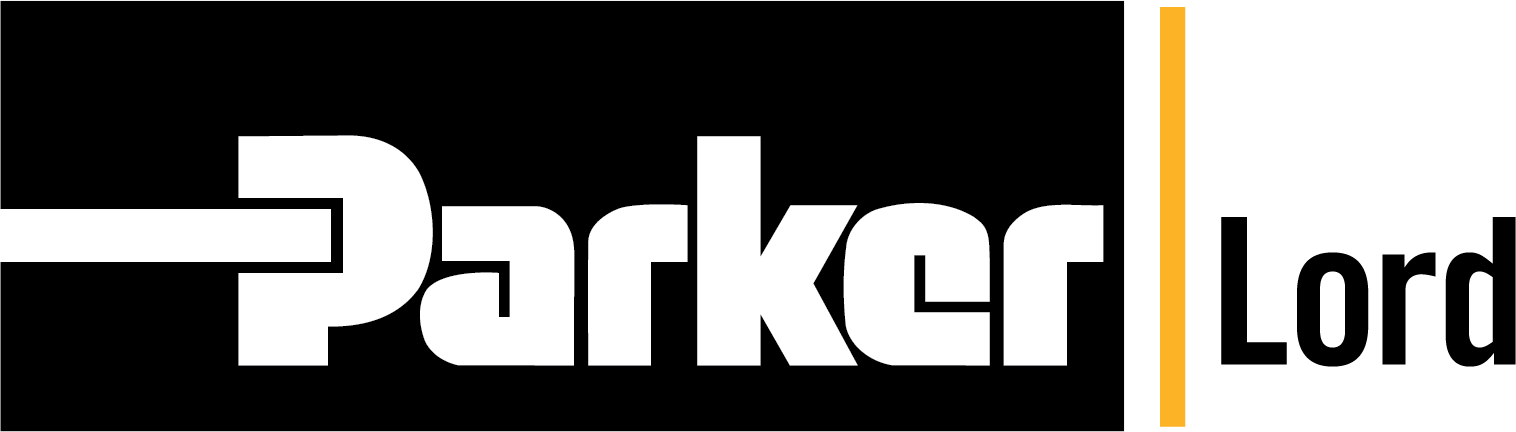
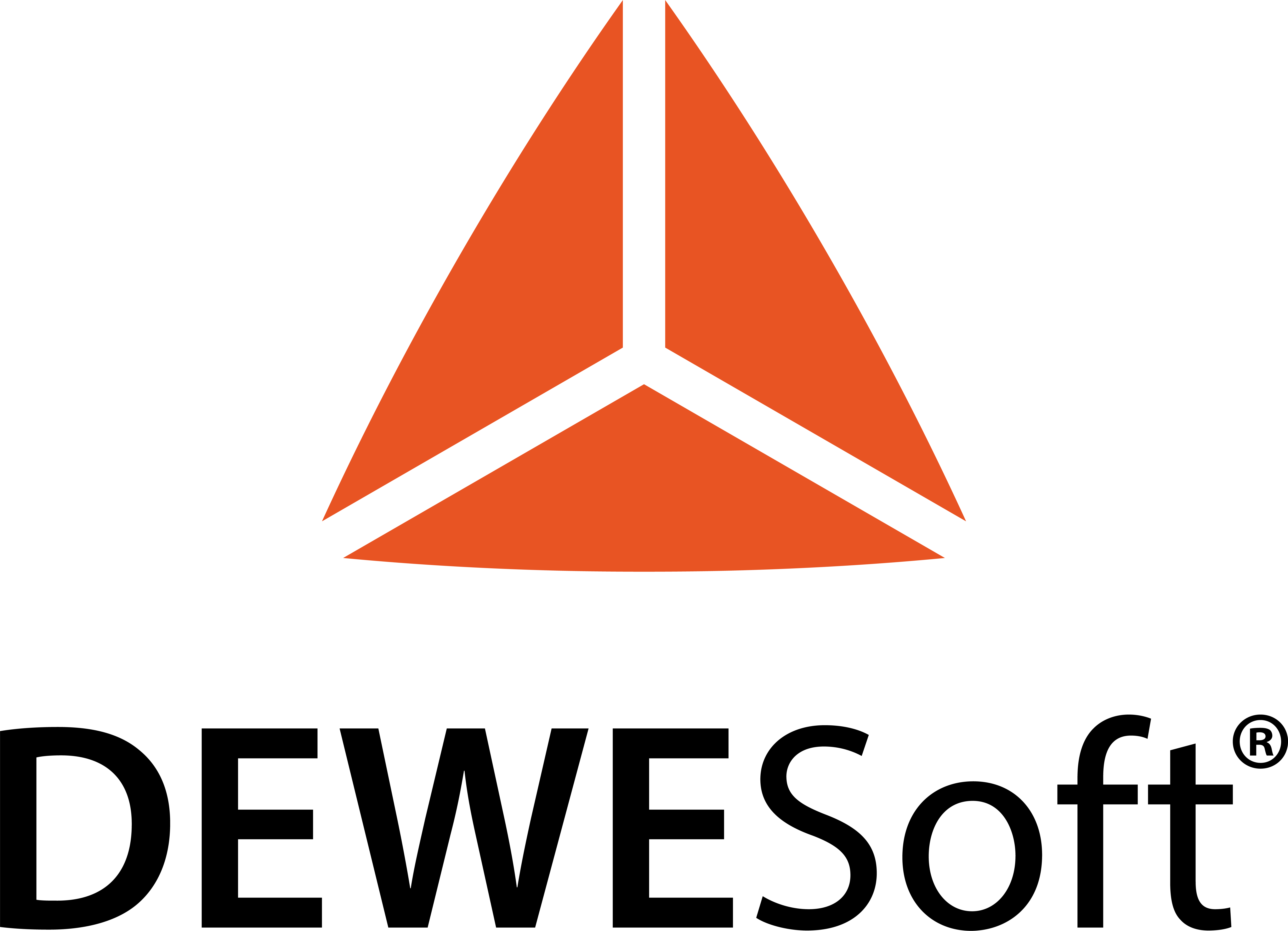
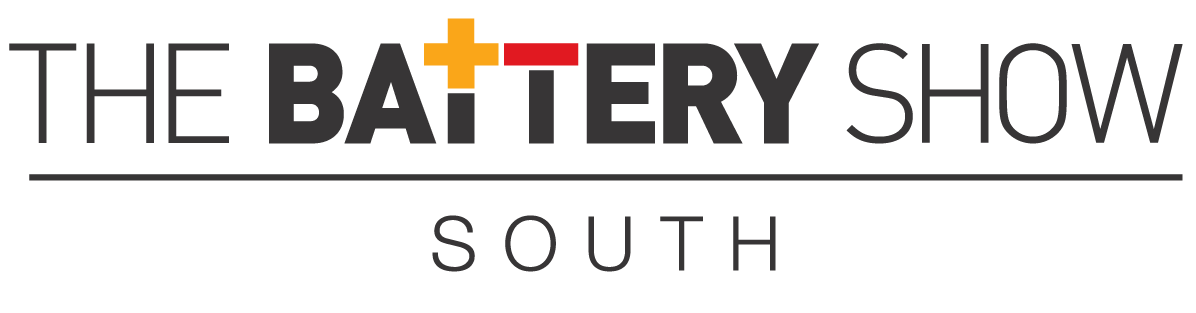
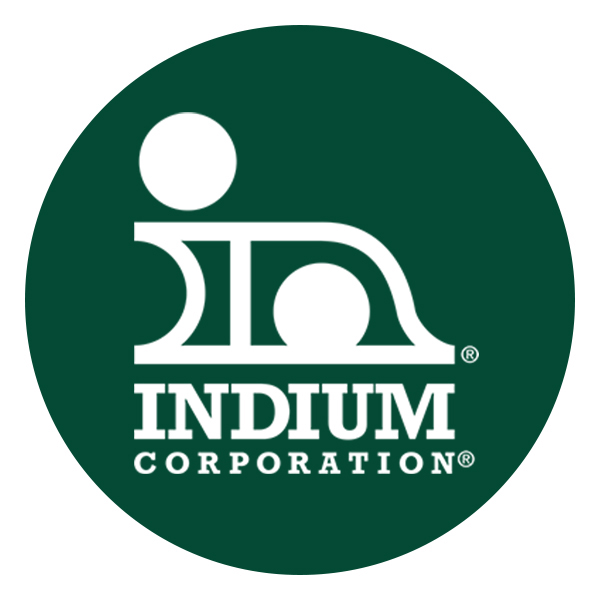
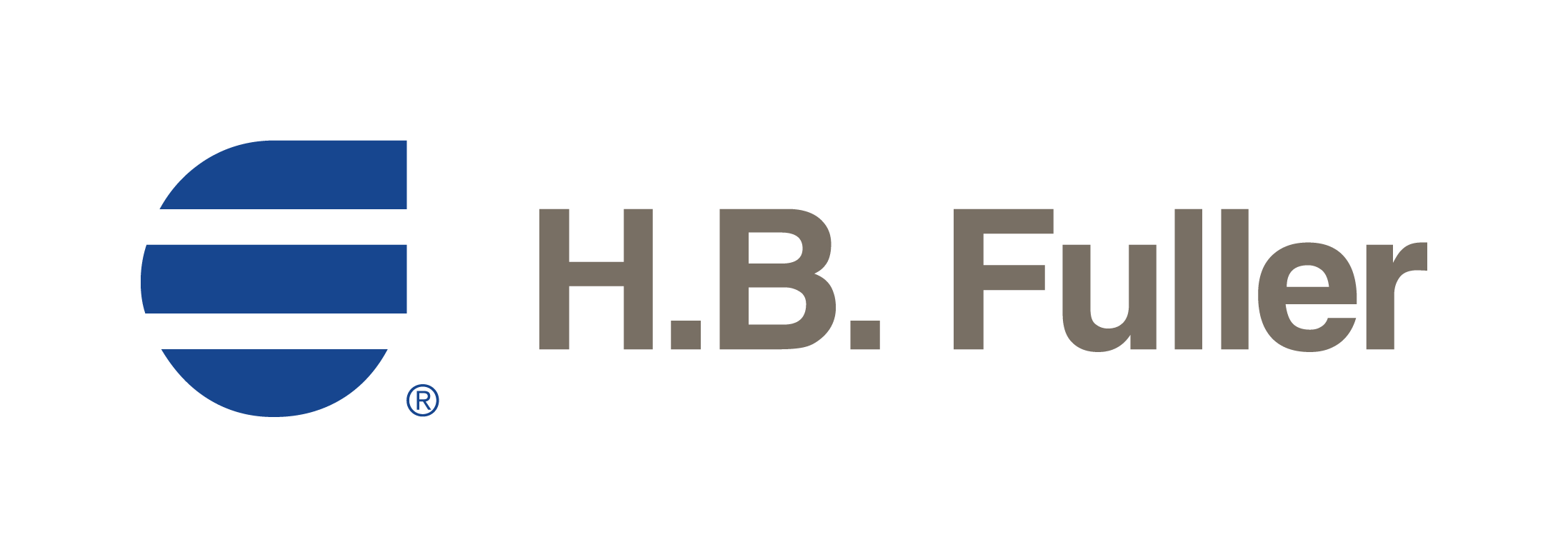