Freedom from rare earth magnets?
A good alternative to magnets made from rare earth elements such as neodymium, dysprosium and samarium – which are expensive, volatile in price and supply and polluting in their extraction – is something of a holy grail for the electrical industry in general and EVs in particular.
Enter Niron Magnetics with its Clean Earth iron nitride magnets. These have attracted interest from organisations including General Motors and Marquette University, in the US, with whom Niron has partnered for the development of EV drivetrains, starting with a demonstrator for the Chevrolet Bolt. Niron CEO Andy Blackburn talks exclusively to Peter Donaldson about the technology.
The neodymium used in the most popular rare earth magnets (NdFeB, for example) costs about $120 per kilo, while the iron and nitrogen used in Niron magnets are tens of cents per kilo.
Saturation refers to the point at which a material can hold no more magnetisation, regardless of the strength of the magnetising field to which it is exposed. When the field is removed, the remaining flux density, known as the remanence, is a better indicator of the magnet’s inherent strength. Blackburn explains that the remanence of the pure materials falls as other substances are added, for example to stabilise the magnet’s performance with temperature.
“The top-performing neodymium magnets are around 1.3 T,” he says. “When you put dysprosium in to make the higher temperature grades the remanence falls to about 1 T, while samarium cobalt magnets are in a similar range but with better temperature performance.”
A practical iron nitride magnet would be in the 1-1.5 T range, but would retain that strength at higher temperatures, such as those in an EV motor, at which only the most expensive rare earth magnets can compete, he adds.
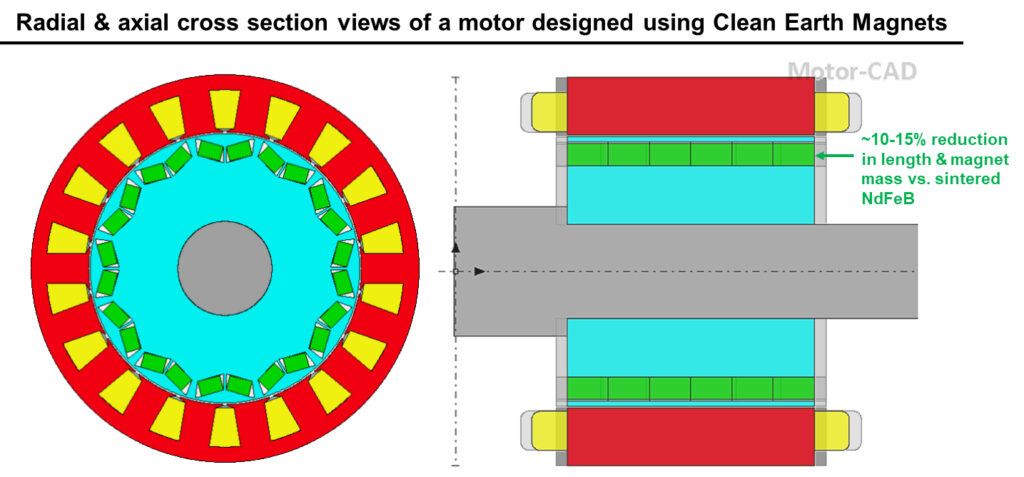
(Courtesy of Niron Magnetics)
One apparent disadvantage of iron nitride magnets is that their coercivity is less than that of neodymium. Coercivity is a measure of the magnet’s ability to resist having the polarity of its field flipped when exposed to a strong opposing field. Without coercivity, the magnetic fields in a motor would rotate without turning the shaft.
“We think the maximum possible coercivity is between 4000 and 5000 oersteds, compared with around 12,000 oersteds or more for neodymium. However, their coercivity drops off as temperature rises, so at typical operating temperatures we are pretty competitive.”
Niron is working to perfect its magnet production using a powder metallurgy process in which nitrogen gas is diffused into the metal in a precisely controlled process designed to yield Fe16N2 powder. This is then consolidated into the required shapes using a polymer binder for the first-generation magnets, which is intended to be replaced by what Blackburn calls cold sintering in the “fully dense” second generation.
Iron nitride magnets should not be thought of as simple drop-in replacements for rare earth magnets though, he cautions. The differences in flux density, coercivity and temperature stability of performance affect how electrical machines using them should be designed, he emphasises. Based on simulations, UK company Motor Design has designed two Prius-class 30 kW, 125 Nm motors, one using each generation of iron nitride magnets, with a motor using N42UH neodymium magnets for comparison.
“You end up with a motor certified at 10% smaller and lighter, with less steel and copper and 15-30% less magnet material because of the higher flux,” Blackburn says. “You get somewhere between two-and-a-half and three times as much power per dollar of magnet cost.”
Funded in part by the US Department of Energy, the Chevrolet Bolt drivetrain demonstrator will use Niron’s second-generation magnet material, and should be ready by the end of 2023. However, the company should be ready to provide samples of this material to other interested parties by late 2022.
ONLINE PARTNERS
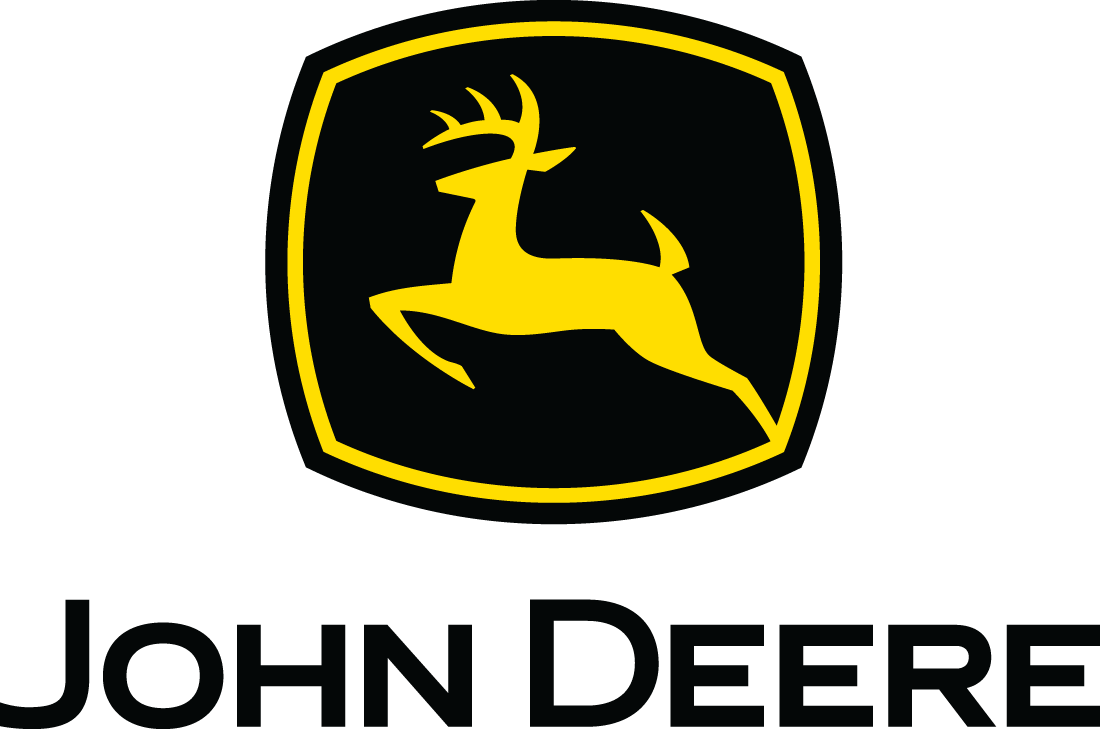
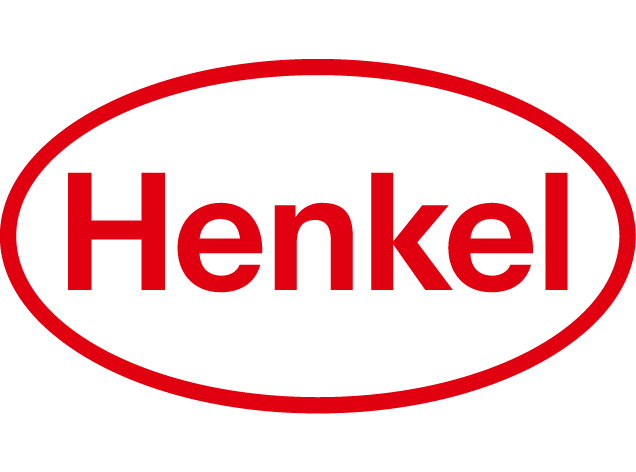
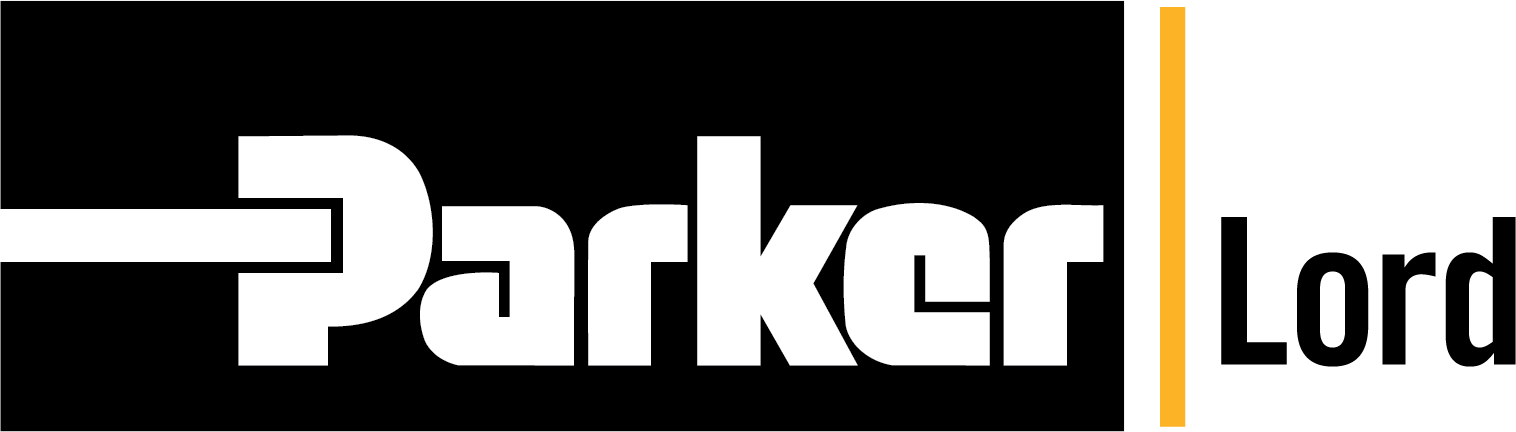
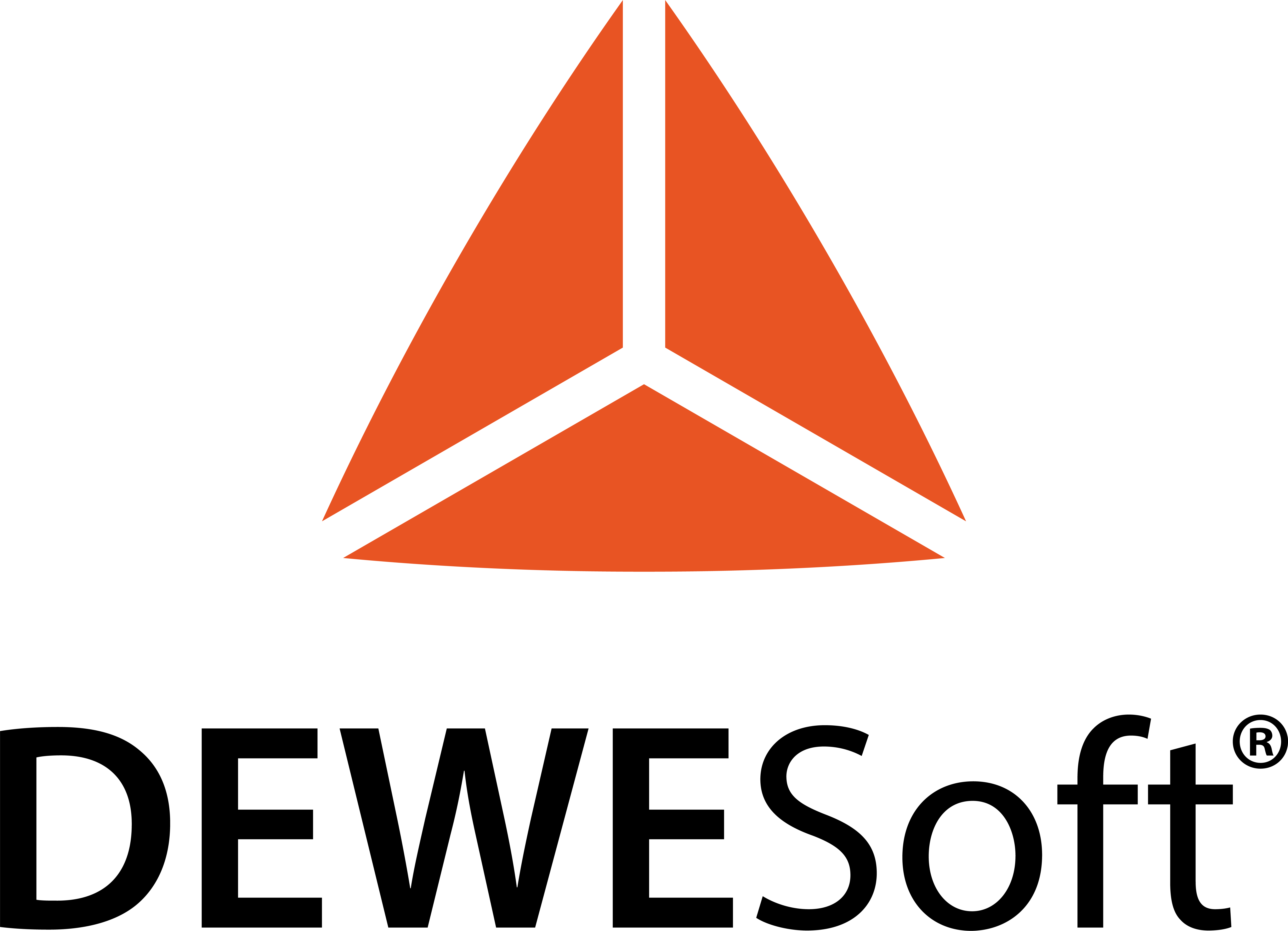
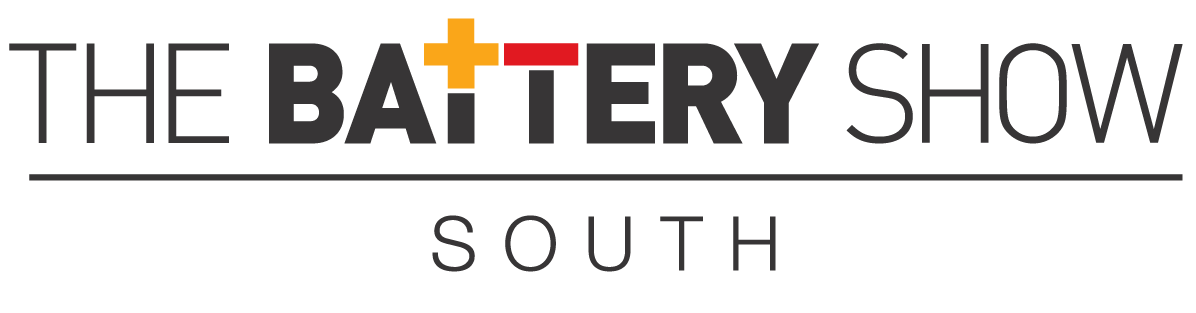
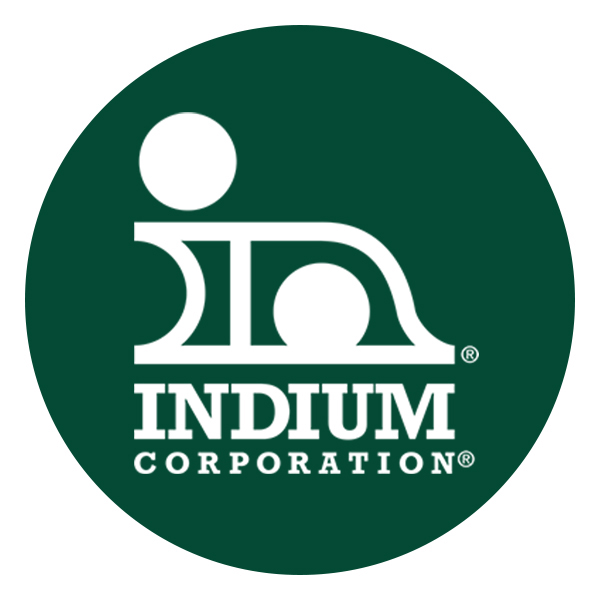
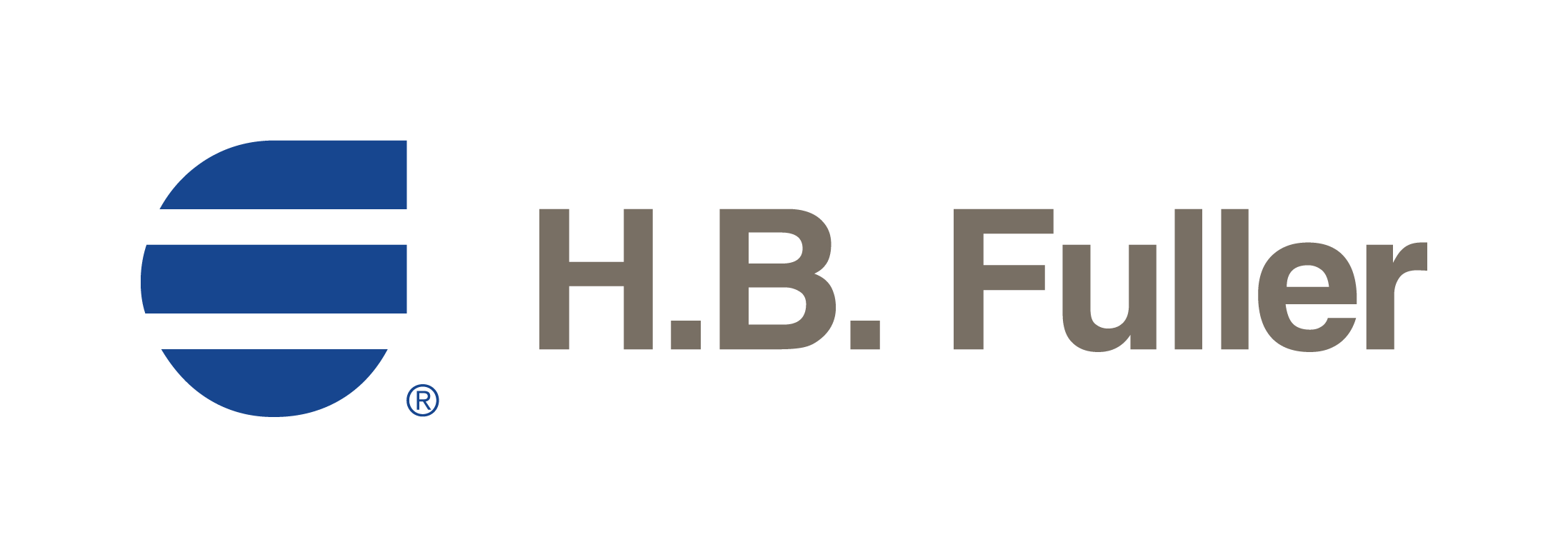