Challenge of batteries for heavy-duty EVs
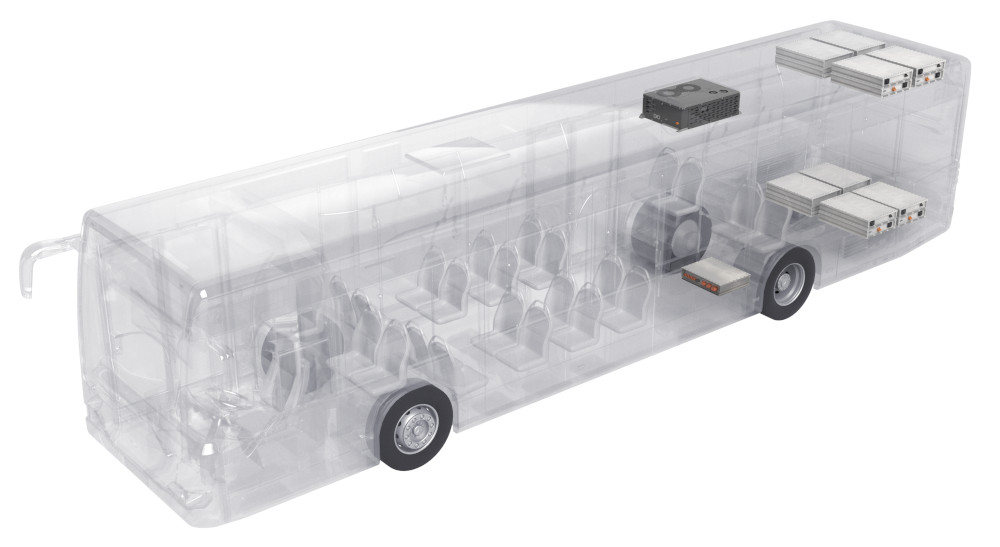
Big business
High-voltage batteries are indispensable for the electrification and decarbonisation of vehicles worldwide, but the specific energy and energy density limitations of current battery technology bring challenges to the forefront when optimising different kinds of EVs. Take heavy-duty commercial EVs, for example. Whether electrifying an 18-wheel truck, a coach, a city bus or some similar sort of long-endurance fleet vehicle, hundreds of kilowatt-hours of energy need to be stored onboard.
The problem here is that commercially available lithium-ion cells typically contain only 0.015 kWh/kg; even the very best, from r&d labs, rarely hold more than 400 Wh/kg. Furthermore, given the amount of weight to be carried and the levels of vibrational and environmental harshness likely to be endured, the cells must be housed in packs large enough to house extensive protection systems to prevent any damage to them.
That piles on the weight though, forcing EV engineers to add more and more packs to ensure their vehicles have enough onboard energy to satisfy their range conditions. It also implies that high-voltage buses must be installed in order to deliver enough power to physically move such hefty EVs without severe current losses.
None of this is really feasible. To force a way to a high-energy target in this manner would add up to thousands of kilos’ worth of battery packs – potentially as much weight in the battery as in the EV and its payload combined. And finding certified components at the desired voltages presents supply chain issues that can make the endeavour cost-ineffective or downright impossible.
To understand how these challenging trade-offs can be resolved, we interviewed battery manufacturers to understand what their vision of the perfect pack for heavy-duty commercial EV applications would look like.
Pack design and specification
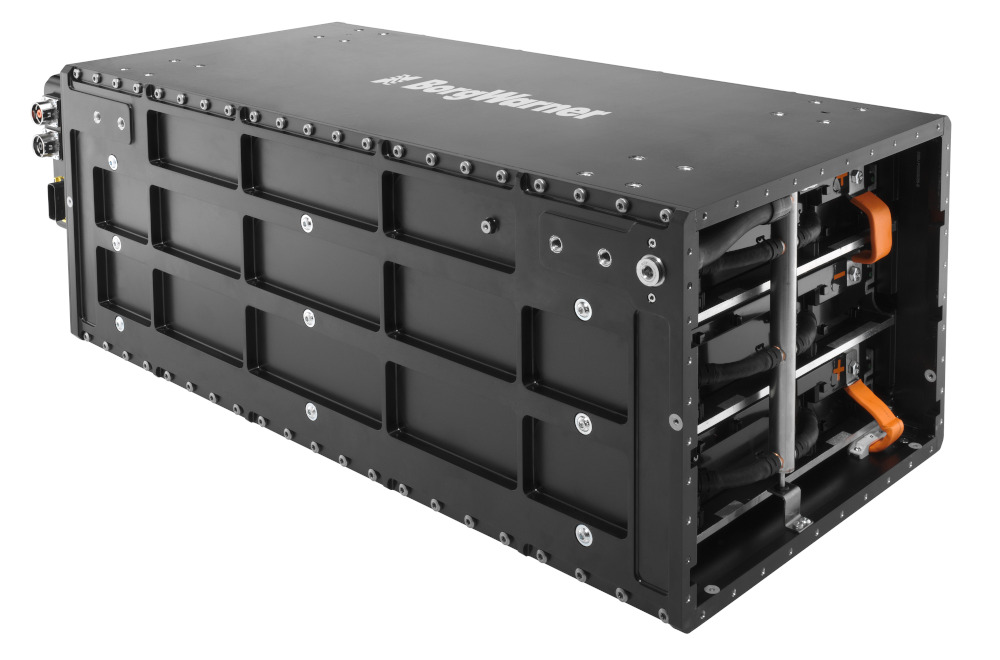
(Courtesy of Akasol)
The initial steps for battery pack development vary between suppliers. For some, setting maximum constraints on collective pack weight or dimensions as well as minimum targets on collective battery energy can be useful for optimising pack parameters around the end-user’s application.
With high-level targets fixed in this way, engineers can be freed up to test and simulate ways to remove weight at every level of integration, from pack to module and cell.
The extent to which each of these will change over the course of the design process also varies. For instance, Mike Ukabam, application engineering manager at Leclanche, notes, “Battery modules account for around 75% of the weight of a battery pack. They are usually of a standardised design and made as light as possible right from the outset, so as not to be modified when being integrated into a pack.”
He adds that the customer’s expected integration method is one of the biggest factors affecting the design of the pack housing. “In some cases, the vehicle structure is designed to support the weight of the pack evenly across the underside of the pack; in other cases the pack needs to be self-supported, as when it’s attached at only the end plates of the pack.
“A pack designed to be installed in the first case can be made lighter, because it is not supporting its own weight, while a pack designed to be supported at the end plates will need to be reinforced and hence will weigh more. And the choice of enclosure material will be dictated primarily by the cost and application.”
Ukabam notes in particular that integration requirements will generally drive significant design differences between packs for trucks and those for buses. “Battery packs for trucks are usually fitted between the chassis rails or outside them,” he says. “They will have fewer fixing points compared to a car pack, and will therefore require a more robust construction. The packs will also be subject to higher levels of torsion than car packs.
“Battery packs for buses meanwhile are usually roof-mounted or fitted at the rear, and roof mounted packs can be made to be ‘self-supporting’, which means the pack weight is supported by the vehicle side structure and not the roof itself.”
Dr Lena Beckmann, head of battery product management at Webasto Group, concurs on matters of standardisation and integration, noting, “Standardised battery packs give the advantage that you don’t need to take the full investment as a customer.
“All customers need is a reasonable size of pack to make good use of the installation space and to achieve an appropriate energy density in Wh/kg as well as in costs, that is, €/kWh. Each vehicle has individual requirements of course, but we see similarities between fitting it between the ladder frame, on the roof, in the former IC engine area, and on the side of the vehicle.”
Given these variables, it can be challenging to pinpoint what the specifications for the ideal heavy commercial EV pack might be.
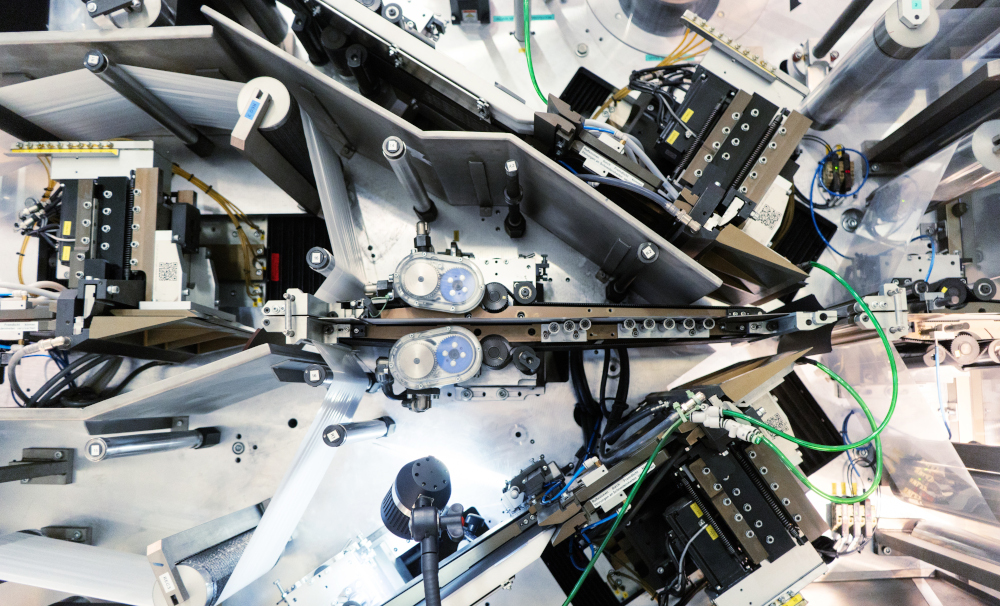
(Courtesy of Leclanche)
Akasol for instance suggests that a pack weight of 500-600 kg with a length of up to 2 m, a width from 0.5 to 0.75 m, and a height of 0.3 to 0.4 m is optimal, with a pack voltage range of about 500-800 V maximum, 150-250 A, and an energy storage of around 500 kWh for powering something such as a solo or articulated bus, or an EV of equivalent weight and duty.
Given the often time-critical nature of such vehicles’ use cases, Akasol also aims to implement fast DC charging systems in its future energy systems. The company also typically designs for IP67- or IP6K9K-level protection in its packs for ruggedness against dust and water ingress, with short-term tolerance of temperatures from -30 C to +60 C.
Dr Beckmann meanwhile points towards Webasto’s CV Standard Battery System as having been optimised around dimensions of 960 x 687 x 302 mm, for which the group offers its customers different installation options. For instance, it can be modularly connected in series and parallel in groups of up to 10 packs, with an output voltage bus of either 400 or 800 V. Each Webasto CV pack contains 35 kWh, weighs up to 295 kg, and is IP67-rated.
Leclanche meanwhile sees packs weighing 260 to 550 kg being strung together for total battery weights of 2000-3300 kg in commercial EVs, targeting 350-500 kWh of energy for 12 m EVs and up to 650 kWh for 18 m trucks (or 100-300 Ah in terms of general energy capacity). At present these would deliver power over a 600-660 V supply, although the company is working on 800 V buses for its future solutions.
A typical commercial vehicle pack measures 1700 to 2000 mm in length, is 700 to 900 mm wide and 300 mm in height, and charges at between 0.9 and 3.0 C. In terms of enclosure ruggedness, Leclanche’s executive VP for eTransport Phil Broad comments, “IP67 is the most realistic rating that will be required. The batteries will be operating at voltages close to 1000 V, and at those levels the isolation of the single components from the grounding is extremely important.
“Also, any humidity – be it from condensation or water ingress – or foreign particles that might enter the battery enclosure could reduce the isolation value, and that could lead to safety issues with the potential of arcing happening in the battery.”
Cell considerations
With these pack specifications in mind, the question arises of how the battery manufacturers achieve them. Many will anticipate (correctly) that the creation of the ideal battery pack starts at the cell level: pack suppliers nowadays have a wealth of cell materials and configurations to choose from, so there is much to consider when settling on the optimal cell type.
Right now, one of the most pressing questions among battery manufacturers is whether to continue using lithium nickel manganese cobalt oxide (NMC) cells or to switch to lithium iron phosphate (LFP) as the cathode material.
Dr Beckmann comments, “In terms of total cost of ownership, LFP might seem like the logical choice at first glance. However, both trucks and buses have to take into account that the maximum vehicle payload is reduced by increases in the weight of the battery system. As nickel-rich NMC – and NCA [lithium nickel cobalt aluminium oxide] – chemistries offer higher gravimetric energy densities at both the cell and system levels, they enable higher payloads and therefore more cost-efficient use of the entire vehicle.”
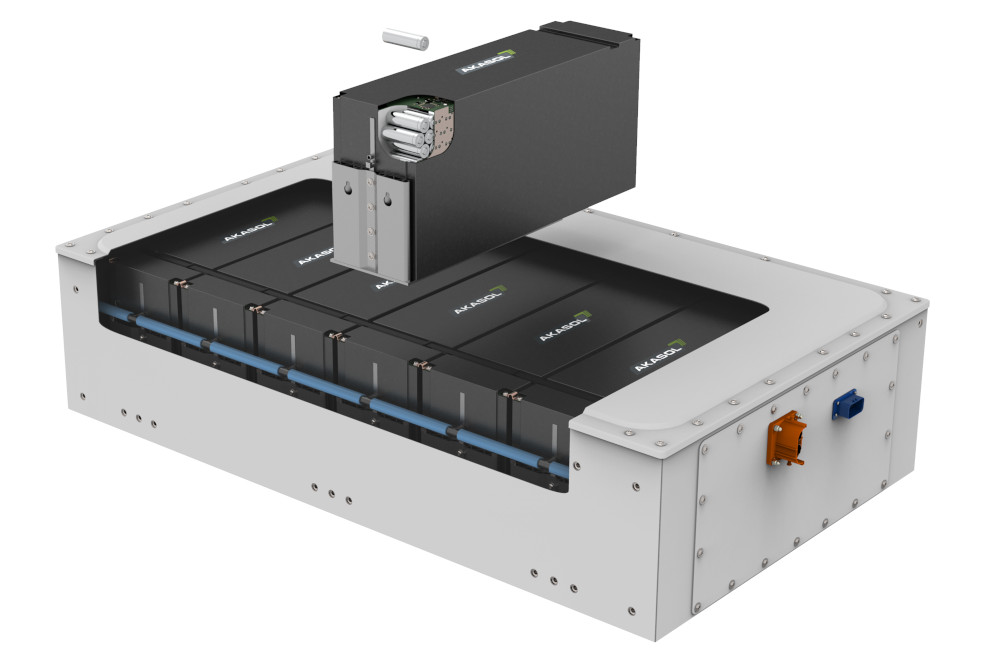
Pierre Blanc, chief technology and industrial officer at Leclanche, concurs, adding, “Graphite anode cells are best suited for battery-electric vehicles and are typically used with an oxide cathode such as NMC or NCA, or with an olivine structure such as LFP.
“NMC has the advantage of higher energy density – typically 30% higher than comparable LFP cells – whereas LFP might have the advantage of reduced dependency on some critical metals. Since both technologies tend to use graphite anode, the initial safety concerns are very similar, such as the kinds of reactions that initiate on the anode, or the potential for burning the electrolyte, with cathode contributions only occurring later in the thermal runaway process.”
Dr Martin Busche, VP of r&d for Akasol, adds that silicon-carbon composite anode chemistries can be ideal for enhancing the energy densities and charging speeds of NMC batteries. However, he cautions further on the costs of these materials, noting that the supply chain instabilities and price fluctuations of nickel, manganese and cobalt in particular can present financial risks.
“Current geopolitical events pose a multitude of risks for mined materials such as cobalt,” he says. “Furthermore, raw material price increases and upcoming shortages in nickel, manganese, graphite and so on will severely exaggerate supply gaps and price risks throughout the supply chain. LFP is a little less affected, but it is not a 1:1 replacement for NMC-based chemistries.
“Certainly, LFP offers cost benefits and the possibilities of bigger cells and lower labour-intensiveness in pack integrations, as it is inherently safer. However, it suffers from lower specific and volumetric energy density than NMC, and – at least from an active material perspective – lower electronic and lithium ionic conductivity, which contribute to lower performance.”
Within these electrolyte families, companies must also consider which are the best specific combinations of cathode and anode materials for their application. While laboratories and gigafactories experiment constantly with new material combinations, with the aim of identifying new competitive cell technologies, some material properties are well-understood.
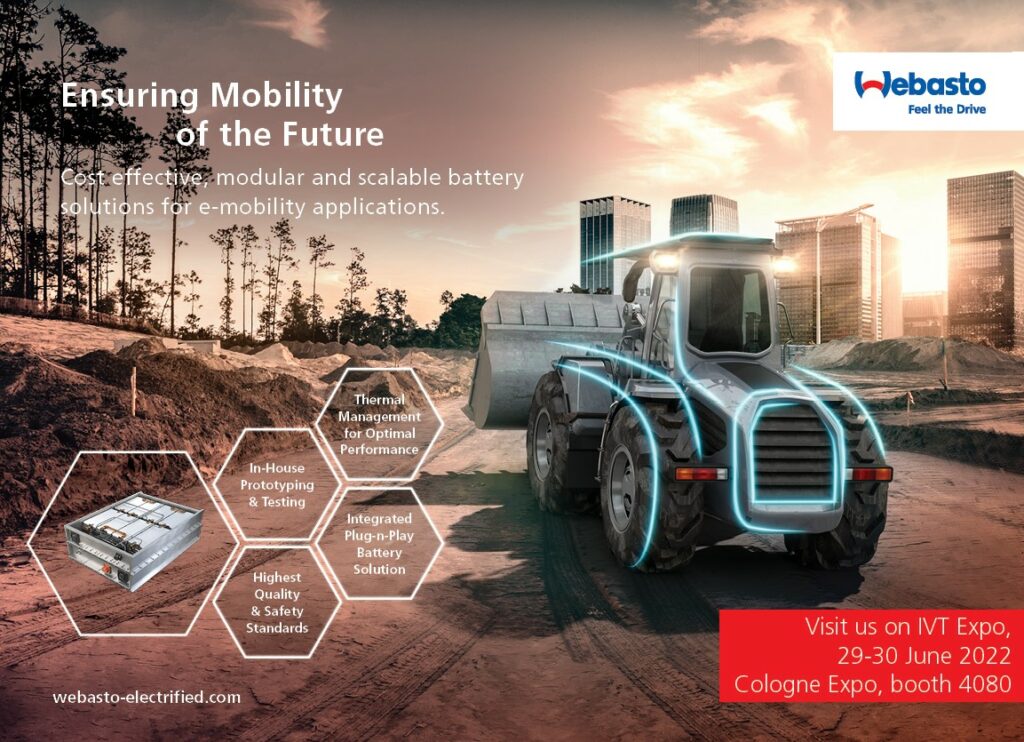
As Dr Beckmann says, “Nickel content on the cathode side is the most obvious lever for energy density, whereas silicon content on the anode side is the most obvious one for fast-charging capability.
“However, maximising these performance points means compromising on cycle life and therefore total cost of ownership. Moreover, the chosen cell chemistry has to be in harmony with other, often overlooked, factors in cell design to strike the perfect balance for heavy-duty applications.
“The interplay between cell chemistry and cell form factor is key. Cylindrical cells enable the highest nickel contents and accordingly energy densities, while maintaining the highest safety standards. Moreover, they allow the highest flexibility for modular systems and their use of installation space.
“On the other hand, the use of big prismatic cells is essential for competitive LFP batteries, thus limiting their application to large packs with limited flexibility. Finally, pouch cells are very cost-competitive at the cell level but require more complex system integration.”
The relationships between cell chemistries and form factors has noteworthy implications for the ideal types of cells to use in electrified trucks, buses and coaches. Heavy-duty commercial EVs generally require large battery capacities as well as relatively high power (compared with packs for cars and light utility vehicles) for the energy density configuration of the cell design.
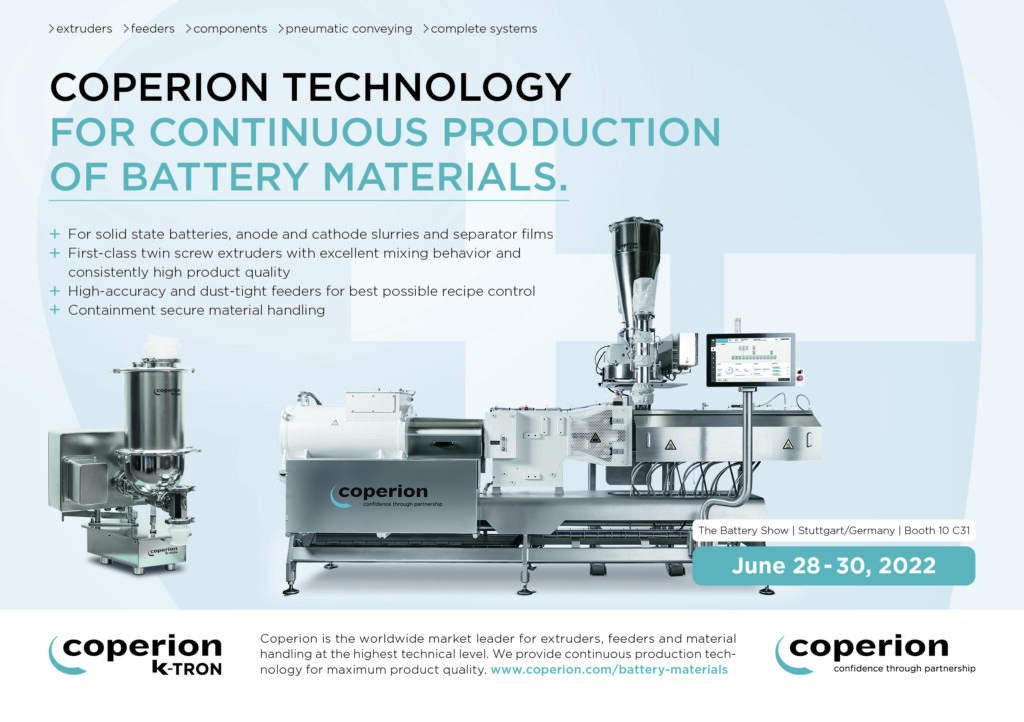
“With these in mind, the ability to extract heat from the battery packs is very important, so optimising the internal resistance of the cells is critical,” says Blanc. “From a design point of view, cylindrical cells have a rather high internal resistance, resulting in more heat needing to be removed. Their surface area-to-capacity ratio is also much lower than in other cell formats, meaning a smaller area for heat exchanges to take place and extract that heat.
“As with pouch cells, prismatic cells have a much lower internal resistance than cylindrical cells. However, prismatic cells tend to be thicker than pouch cells, meaning that the centre of the cell will see higher temperatures than those in pouch cells, and with a higher temperature gradient.
“This will have an impact on cell ageing, as in a more asymmetric ageing within the cell. Pouch cells meanwhile require more complex mechanical structures for integration in battery packs, as they do not have any mechanical structure for supporting themselves. Other considerations will come into play, such as the internal structure of the electrode layering, but the main focus for heavy-duty EV packs moving forward will be mostly on prismatic and pouch formats.”
Dr Busche notes however that commercial EV customers are among the most sensitive to safety concerns, so integrated safety features typical of cylindrical cells such as overpressure current interrupt devices and rupture valves could still make them highly desirable in such contexts (adding also that prismatic cells often feature these too).
Also, being highly standardised makes them easily ‘exchangeable’ between different suppliers and packs without mechanical incompatibilities arising.
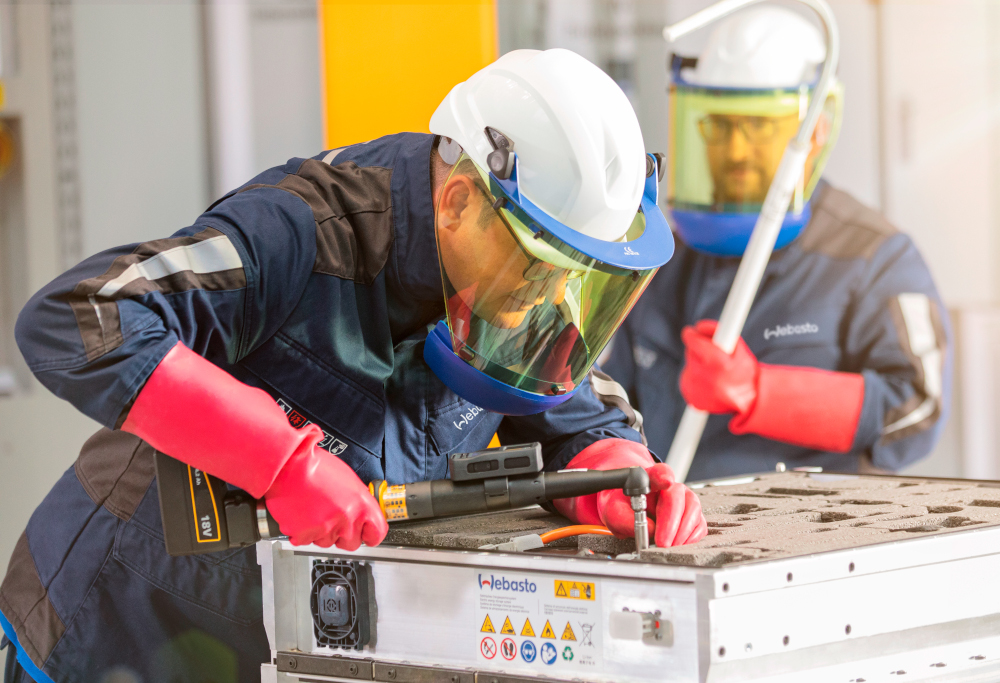
(Courtesy of Webasto)
Battery management
The high volume and maintenance costs associated with electrifying a fleet of heavy commercial vehicles have certain impacts on how the battery management systems (BMSs) for such systems should be designed. For instance, end-users typically demand very high lifetime and ruggedness in their battery packs.
“That is especially true for trucks, and will probably drive high requirements on the quality and thus cost of the microcontrollers and internal data storage systems chosen,” says Dr Busche.
Dr Beckmann adds, “The testing for the BMS is sometimes even more extensive compared to those of passenger EV BMSs. Another main difference is that we need to control a multi-pack system most of the time since most of our customers use several battery packs. We have also therefore developed options for the multi-pack with our Vehicle Interface Box [VIB] and Vehicle Interface Gateway [VIG].”
Both are designed for master BMS functionality with central CAN comms interfaces between an EV and its battery systems, as well as 12-14 V inputs and 400 or 800 V compatibility. The VIB is configurable for managing up to 10 packs, while the VIG can manage up to 18.
It is also critical that BMSs and EV comms networks comply with all the internationally accepted standards for safety and performance.
“Both roadcar EVs and heavy-duty commercial buses and trucks must comply with ISO 26262,” says Sylvain Chonavel, Leclanche’s chief engineer for on/off highway and rail vehicles. “And we use CAN bus on truck packs and Modbus on marine and stationary projects.”
Manufacturing
Generally, the manufacturing of battery packs for heavy-duty commercial applications will be similar to those intended for light-duty or consumer EV packs.
“The two main differences will be the size and weight of the packs, and the production volumes. These will have an impact on the manufacturing equipment used to produce the packs,” comments John Lewis, eTransport product manager for Leclanche.
“We have seen in the past that heavy-duty applications would tend to use larger batteries with higher voltages, but we find that consumer EV batteries are also going in that direction now.
“Because the battery packs tend to be larger in heavy-duty applications, the materials handling equipment needs to be adapted to such heavier batteries. And with production volumes lower than in the consumer EV space, the choice of such equipment will also be adapted to the volume requirements.”
That means solutions for automated assembly lines might be less applicable in production lines for heavy-duty commercial EV batteries than for consumer EVs, although Webasto has developed a sizeable assembly line for its CV Standard packs that is optimised to produce high-end batteries in lower volumes than in the passenger car space.
Lewis also notes that manual skill requirements will remain largely unchanged from one case to the other.
These similarities in manufacturing requirements means that keeping assembly lines flexible, scalable and product independent could be critical for the sustainable growth of production capabilities.
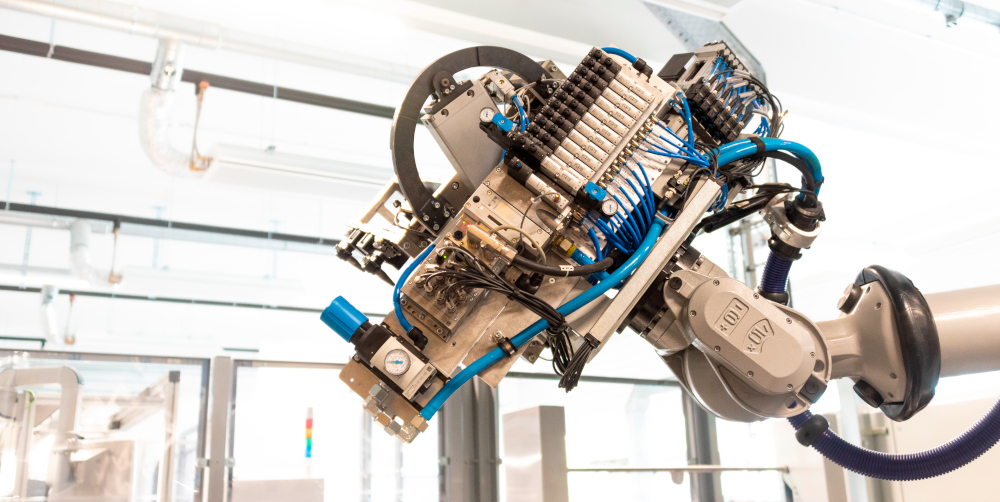
(Courtesy of Leclanche)
Dr Busche comments that at Akasol, “In a highly efficient production environment with a significant level of automation it is always important to have skilled operators who are able to control the lines. With our strategy, to have product-independent assembly lines, the processes and skills are not influenced by the types of products.”
Testing
Standards such as UN-ECE R100 and R10 among other, comparable regional norms, detail the kinds of test regimens that are most important for validating battery packs.
“The main tests to be conducted include vibration, fire resistance, thermal shock, mechanical shock, mechanical integrity – that is, crash testing – as well as pack sealing, pack capacity, cycling capability, overcharge protection, over-temperature protection and BMS comms,” says Chonavel.
Procedures and equipment for some of these are well-established in the automotive world, such as for mechanical integrity and vibration testing. Webasto for instance points towards its multi-axial swing table as being key in this regard. Such systems typically apply force and motion in six degrees of freedom to components to evaluate their behaviour across a broad array of real-world movements and shocks.
Other equipment such as oscilloscopes, power analysers and signal generators are critical for cell cycling, overcharge, overcurrent, and many other electrical validations, across both high-voltage power delivery and low-voltage data integrity.
Akasol and Leclanche also point towards pressure testing and leak testing of batteries as being key to heavy-duty commercial EVs, given the lengthy and sometimes poorly maintained highways that such vehicles must endure for logistics or transport work.
Future prospects
In the pursuit of lower maintenance costs and emissions, battery recycling is likely to be important for future generations of heavy-duty commercial EV fleets, although predictions vary as to when the first major recycling efforts for lithium-ion packs will begin.
Packs designed with high cycle numbers for their lifetimes are expected to reach 80% of their nominal capacities – a figure widely accepted as their ‘end of life’ in the e-mobility world – between 4 and 10 years after their initial delivery. At this time, Broad notes, “The customer can decide to replace it with a new battery, and the old battery can be then reused in a stationary application, such as for grid services or for energy shifting.
“Thanks to the IoT capability of our product, we can perform remote pack diagnostics in real time to decide in advance whether the battery is suitable for a second life. If not, we’ll send it directly for recycling.”
Dr Busche comments that Akasol generally agrees with this timeframe. “We anticipate a ramp-up for heavy-duty EV packs starting with medium volumes from 2025, increasing to high volumes in 2030.”
In general terms, Akasol sees the recycling process as following several steps. First, all removable parts in an old pack will be dismantled to stockpile a pre-sorted set of materials. Many metal and electronic components in these sets can then be recycled using well-established, conventional techniques.
Less well-established is how best to recycle the modules and cells. “Leclanche is continuously working with different partners to follow the latest technical recycling solutions,” Broad adds. “In our plants in Germany and Switzerland, we collect already partially assembled or final products that didn’t pass the quality test required to ensure the highest quality of our battery.
“That gives us unique opportunities to experiment with and benchmarking different recycling processes. We also consider the location of the recycling facilities, as they will need to be built close to the end-of-life locations of heavy commercial EVs.
“And for both the recycling processes and facility constructions, CO2 emissions must be minimised and challenged as far as possible, since end-of-life emissions form part of the total CO2 emissions of our company.”
The future success of battery recycling also depends on the rate at which materials can be recovered for cell and module remanufacturing. To that end, Akasol aims by 2030 to have advanced its special recycling processes to make up to 95% material regain achievable.
“Such targets are key to creating a circular economy for battery materials,” Dr Busche concludes.
ONLINE PARTNERS
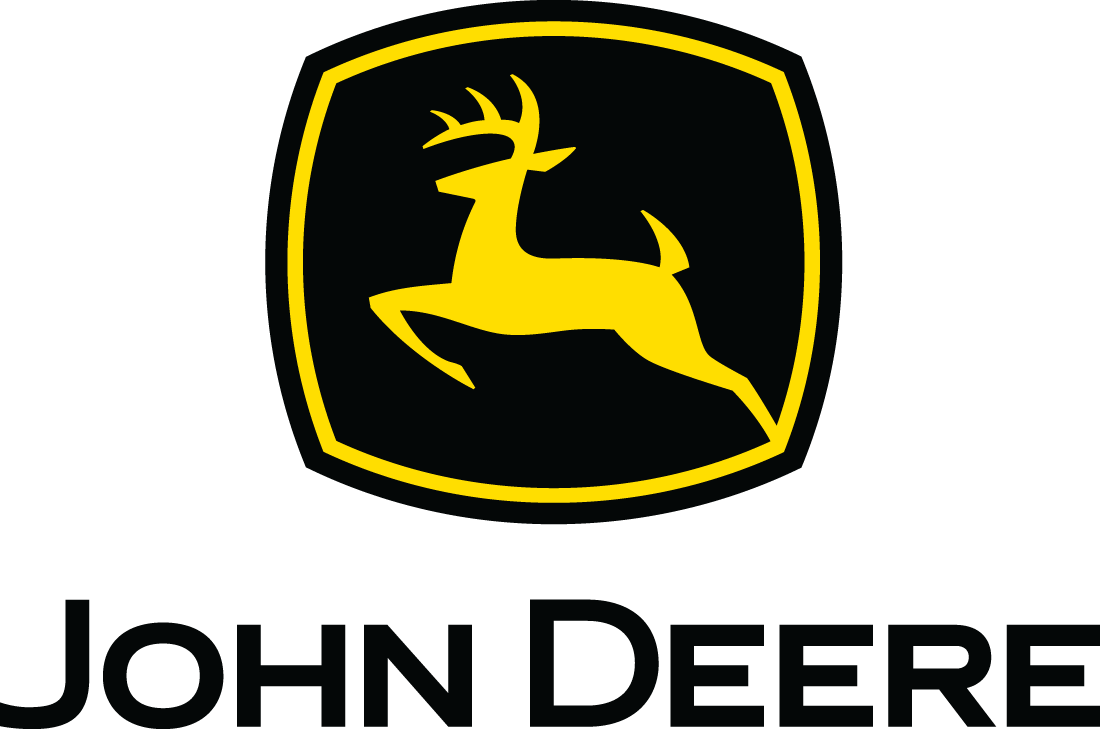
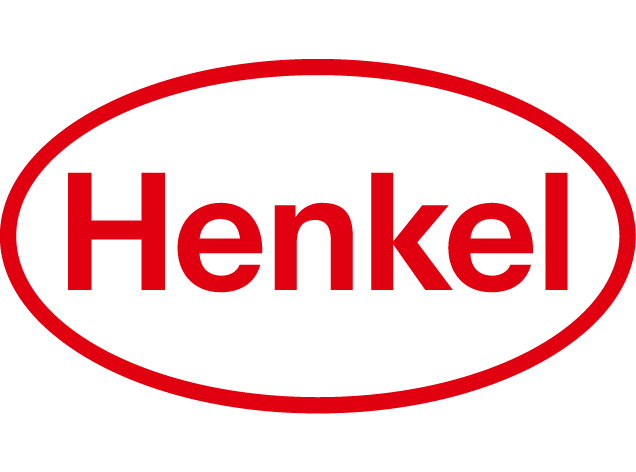
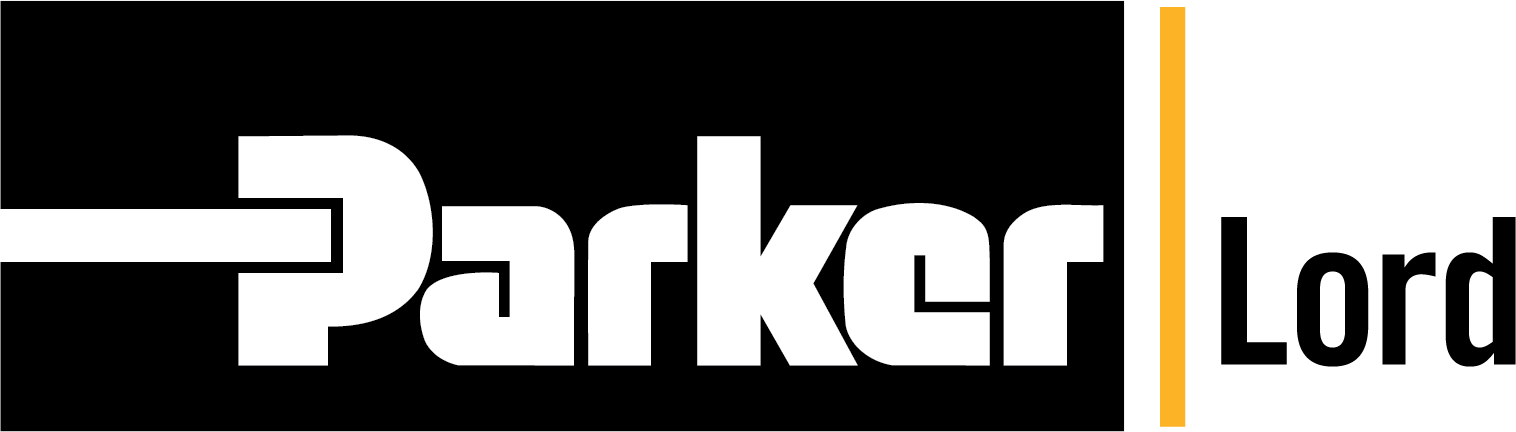
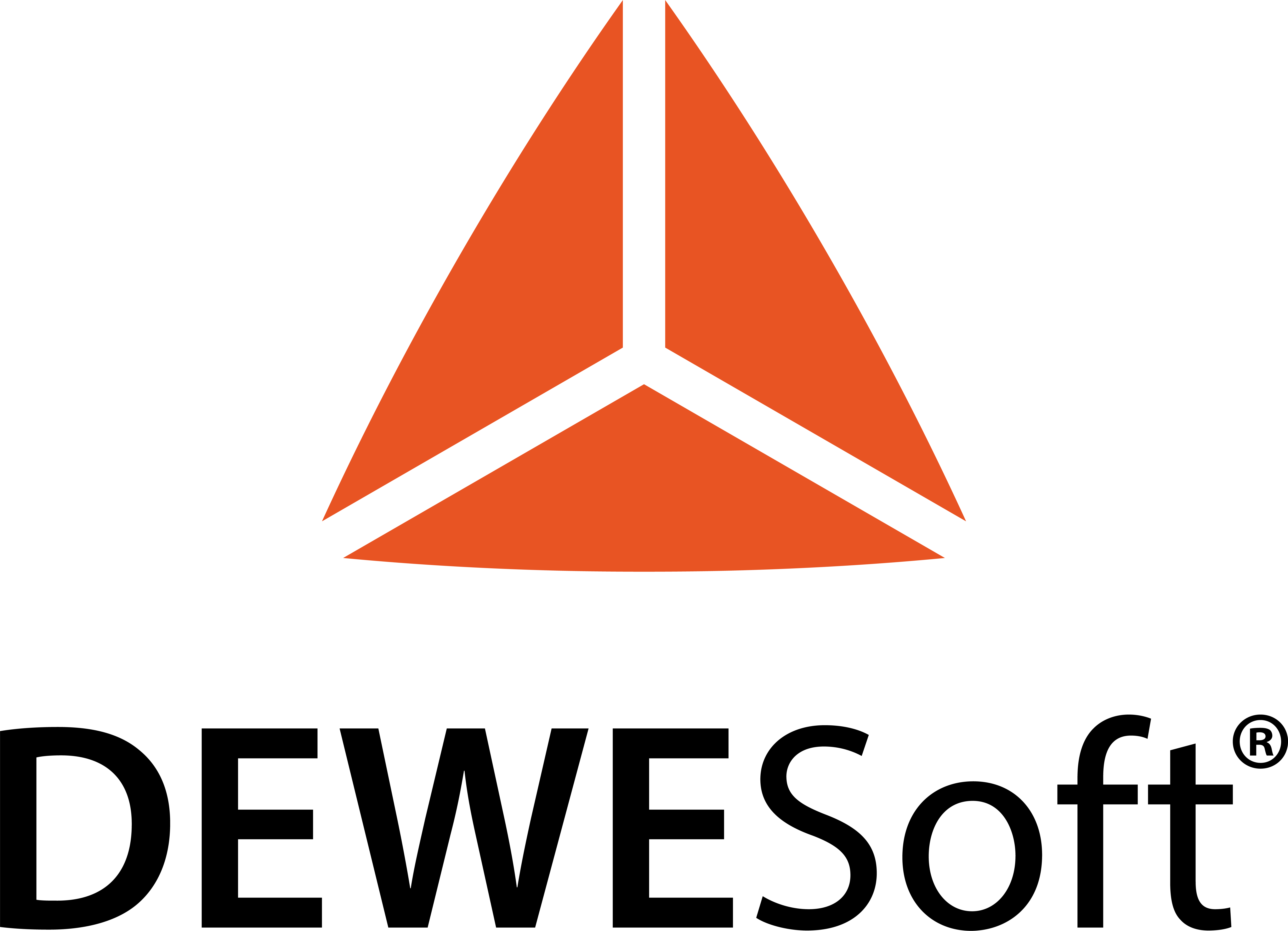
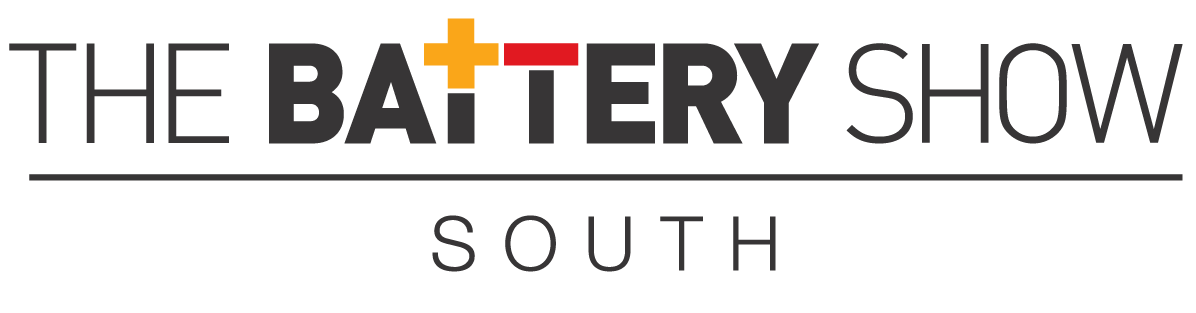
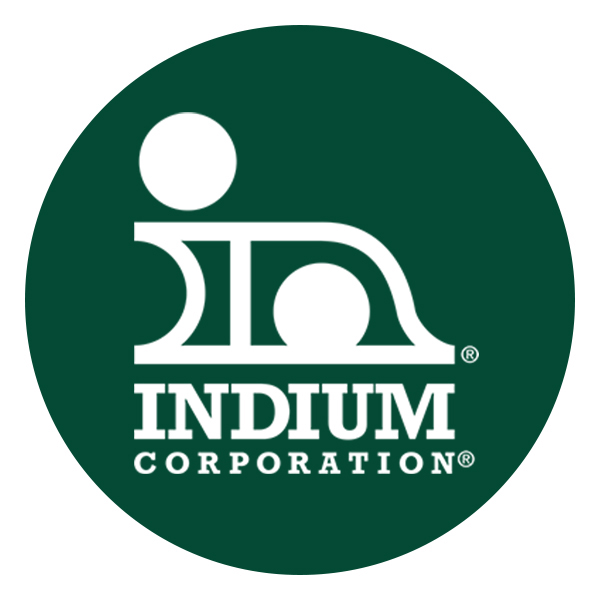
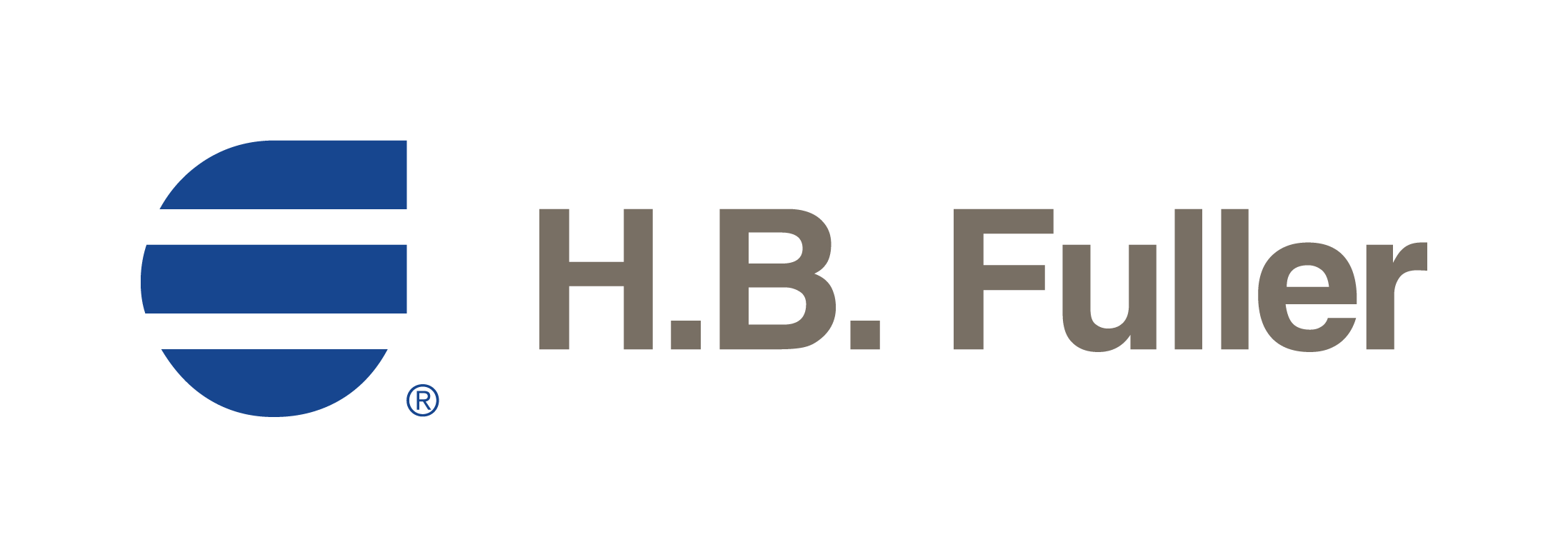