Cell-to-pack batteries
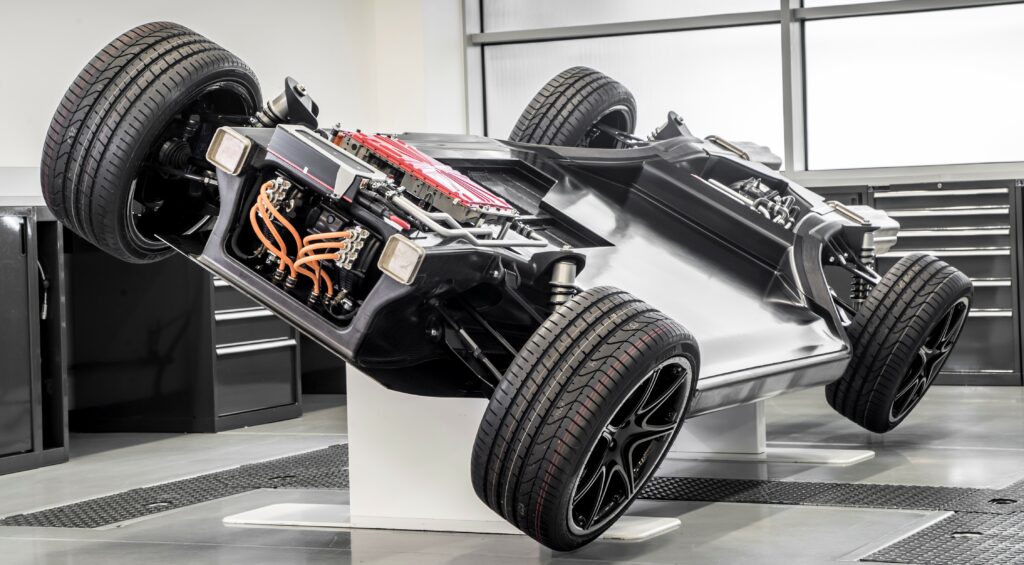
(Courtesy of Williams Advanced Engineering)
New connections
Peter Donaldson gauges the state of development of the various types of battery construction
Most EV battery packs are built from groups of cells housed in modules interconnected within a case that provides structural support, thermal management, environmental protection and connectivity with the rest of the drivetrain, but this is not the only way to do it. There are potential benefits to eliminating modules and building packs up from cells inside the case, in what has become known as the cell-to-pack arrangement.
A logical extension of this idea eliminates the dedicated case from the battery pack in the so-called cell-to-chassis concept. A third idea also discards the dedicated case but brings back the module, and is referred to as module-to-chassis construction. The point of all these is to improve the ratio of energy to weight and volume at pack level, and reduce the number of components in the pack and the manufacturing costs.
One major and immediate effect of moving to cell-to-pack construction of batteries is on the cells themselves. According to one EV consultant cum battery systems developer and manufacturer we spoke to as part of the research for this article, the cells used are likely to be in prismatic or pouch format and larger, in terms of physical size as well as energy capacity.
The main advantage of the cell-to-pack approach that flows from the use of fewer, larger cells is the smaller bill of materials and fewer interconnects, simplifying assembly and potentially increasing reliability. A Tesla battery pack might have 6000 cells, the consultant points out. “You break that down into maybe 16 modules on a Model S or four in a Model 3, and in either case that is a lot of interconnects, each of which is a potential point of failure. Going to cell-to-pack eradicates a lot of that, or at least minimises its impact.”
Eliminating modules through cell-to-pack construction gets rid of all the associated structure in their side walls, tops and bases. That frees up more volume inside the case for the cells, increasing the volumetric energy density (kWh/litre) at pack level. While the lower parts count probably cuts costs by itself, it can also lead to fewer production steps, and potentially reduces the overall engineering effort required.
Module-to-chassis could be seen as a stepping stone towards cell-to-chassis construction, the latter building individual cells directly into vehicle’s primary structure. The principal advantages are efficiency of packaging, structural performance and weight reduction in the resulting vehicle, says one specialised EV developer.
“Effectively, you are reducing the replication of structural performance,” a company expert says. “If you have a large standalone battery pack within any vehicle chassis, you effectively need a very large void to accommodate it, which is structurally inefficient. You end up building additional structural strength into the battery case itself and, you have to reinforce the chassis structure where the battery pack bolts into it.
“When you remove that large void from the chassis you can design the primary structure in a much more efficient way, using less material and with more direct control of load paths.”
A battery developer adds that cell-to-chassis construction also allows for better weight distribution. “If you’ve got a single mass pack effectively mounted into the chassis in a specific number of locations, you can’t really distribute the weight in the same way,” a company expert says. “Direct cell-to-chassis allows for optimisation of weight distribution.”
Inevitably, there are challenges with these approaches to battery design, and a senior engineer with a vehicle technology and engineering services company highlighted meeting safety requirements while delivering maximum performance with respect to cell-to-pack designs in particular. “From this perspective, moving the pack to be more of a structural part of the vehicle, and removing the modules, can remove certain failure mode mitigations around cell venting and propagation,” an expert from the company says.
Cooling also needs to be managed differently when taking this approach, and welding processes have to be reimagined for production solutions.
A battery sealing and thermal interface materials supplier notes that omitting battery module housings raises a number of issues, as they are important safety elements in battery packs. Additional safety measures are therefore required for cell-to-pack and cell-to-chassis pack designs that, for example, mitigate thermal propagation in case of a cell fire.
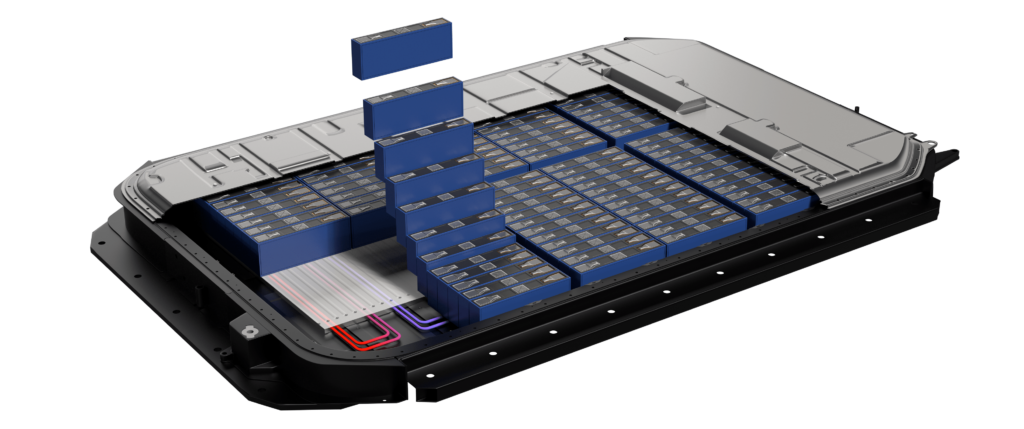
(Courtesy of Henkel)
“Battery modules are also important mechanical elements that ensure a stable position of battery cells, compensate for cell breathing and contribute to the overall mechanical integrity of the battery pack,” a company expert says. “Battery manufacturers have to develop new concepts that compensate for the omission of battery modules from a mechanical perspective.”
Our specialist EV developer stresses that challenges present themselves in the design of the vehicle itself and in manufacture at different volumes. “From a design perspective, every vehicle has differing requirements, whether it’s a passenger vehicle, sportscar, last-mile delivery van or larger commercial truck, and the set of challenges vary depending on the application and the performance requirements,” the EV developer says.
“You have to consider the volumes of vehicles you are looking to produce, how many batteries you are looking to build, and what the processes for those builds will be in a battery environment,” the developer adds. “At low volumes, for example with specialist sportscars or some commercial vehicles that undergo body conversions, you typically have a very labour-intensive build process, so a more complicated battery build process is acceptable because the assembly methodology allows for that.
“If you are producing vehicles in the hundreds, thousands or tens of thousands of units per year you need a heavily automated solution. You need a very clear understanding of the requirements, not just from a technical and performance perspective but also from a commercial point of view.”
A developer of lithium metal batteries argues that the biggest challenge that has to be overcome is traditional thinking about how vehicles, including their battery packs, are manufactured, from raw materials through to just-in-time delivery of major subsystems.
“To be viable, cell-to-pack and cell-to-chassis systems must be more productive across several metrics, including development effort, safety, total cost, assembly time and performance,” a company expert says.
“With that in mind, the cost-benefit analysis should be holistic and include stakeholders from battery cell engineering, battery pack engineering, vehicle assembly, purchasing and logistics. The analysis should study the entire EV production process rather than being limited to a direct one-to-one comparison of cell-to-pack or cell-to-chassis versus module-to-pack assembly construction.”
Physical integration impacts
In terms of physical integration of the battery into the vehicle, the cell-to-pack approach may seem very similar to traditional cell-to-module-to-pack construction, but it still requires careful consideration.
“Much of our activity in this area is looking at how we can use the cells to give structure to the overall vehicle performance, through a detailed, virtual characterisation from the cells to the systems,” notes one vehicle technology and engineering services specialist. “Through physical testing to correlate the models, we are able to analyse various scenarios to provide the best solution for a given application.”
He emphasises that with one fewer barrier – the module structure – to protect the cells in crash scenarios, there has to be much more focus on the interaction between the cells, the battery case and the vehicle structure to ensure a safe and practical solution. “ It would be wasteful to create additional volume for cells, if only to allocate it to larger walls around the battery enclosure due to poor understanding of how the impact deforms the structure. Again, this can be managed through strong modelling techniques.”
Further challenges, he adds, are encountered as the battery system enclosure interacts with more of the chassis and vehicle system elements, such as seating anchors in the Tesla Model Y, for example.
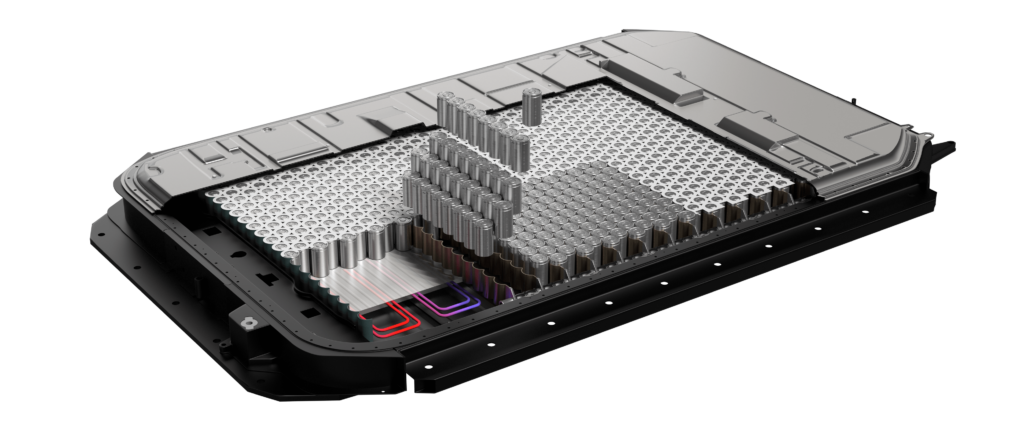
(Courtesy of Henkel)
The structural impact of the cell-to-chassis approach is much greater. “New solutions must be developed that ensure a safe placement of the battery cells inside the vehicle chassis over the full lifetime,” an adhesives, sealants and thermal interface materials expert notes.
“Current design concepts range from using special cell carriers to hold the cells in place, mechanical elements at the side, bottom or top of the battery pack, and most important new adhesives to allow a strong and reliable connection of battery cells to the bottom or cooling plate in the vehicle,” the expert adds. “Further developments address novel insulating coatings for prismatic cell cans that can be used instead of conventional polymer foils and improve the bonding between the cell and the cooling plate.”
The structural battery pack in Tesla’s Model Y can be seen as an example of the cell-to-chassis philosophy because, as the name suggests, the pack is a key load bearing member of the vehicle’s chassis, and it can be configured with or without modules.
Cell-to-pack construction also has implications for the shape of battery packs, argues the EV consultant and battery systems manufacturer, which is a consequence of using much larger cells.
“The downside of that is that the lowest common denominator is a fixed shape, a problem that does not exist with 21700 cylindrical cells, for example, as you can make the pack any shape you like because they are quite small cells,” the consultant says. “When you jump up to modules, there are again quite a lot of ways in which you can change their layout, so you have some flexibility, but when you go to cell-to-pack – if you use very large cells – you lose most of that flexibility.”
While this is not really a problem for vehicles whose battery packs are large rectangular slabs, he says, for EVs derived from IC engine platforms the structure can be very restrictive, as it forces designers to shape the pack to fit the available space. However, EVs based on IC engine-powered platforms are likely to be rare in future.
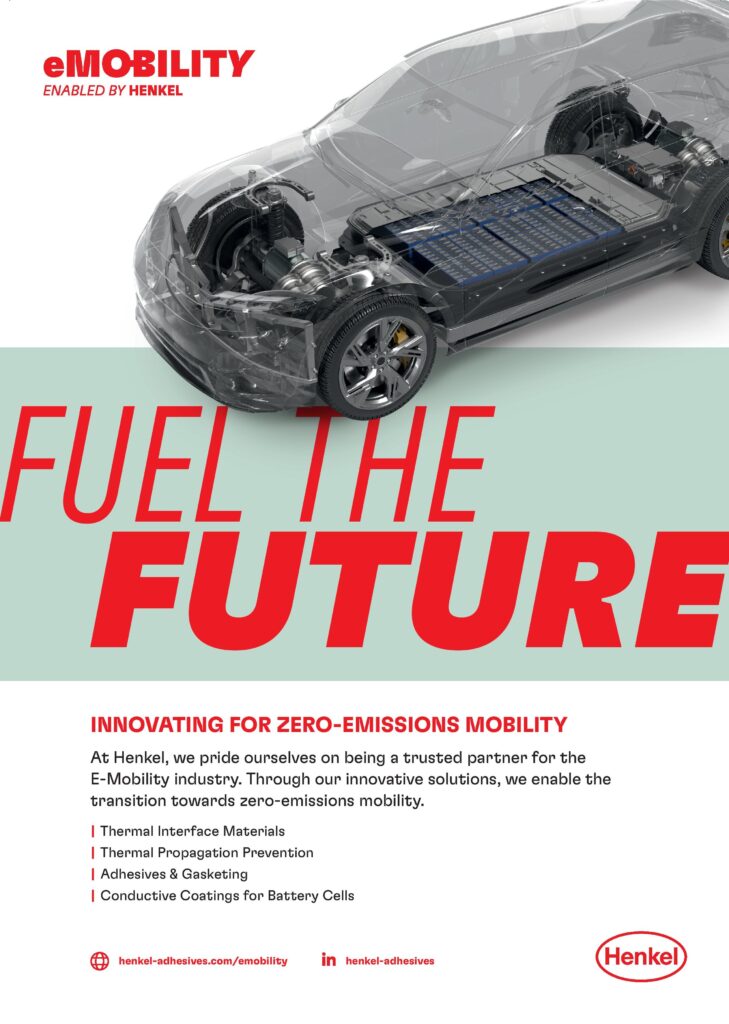
One approach to cell-to-chassis construction implies the need for cells whose construction can add to the structural strength of the vehicle, the EV consultant adds. “My interpretation is that you literally don’t have any other supporting structure.”
These cells might be very large and strong enough to form a structural element of the frame, in the way some motorcycle engines are. “I don’t think that’s ever going to happen, and I don’t know any cell manufacturers or designers who ever want that to happen,” the consultant says.
Crash safety implications
Crash safety affects all aspects of battery design, and the cell-to-pack and cell-to-chassis concepts provide the opportunity to get the battery components into a better place than can usually be achieved when working with a single large battery pack mass, the specialist EV builder notes. “You are able to get the batteries lower in the vehicle, typically, improving the weight distribution, the inertia of the battery system in impact, and you are getting away from the extremities of the vehicle,” he says.
Whether a module-to-chassis or cell-to-chassis design will perform better in a crash than a standalone battery pack – in a skateboard configuration, for example – depends on the details of the design.
“As with module-to-pack designs, the cells must be packaged away from any crash or impact zones,” the lithium metal battery manufacturer says. “Vehicle development engineers can assess the intrusion of a crash into the battery enclosure space, which is a limiting factor on the available space to package the batteries, especially in the y axis or the width of the battery pack,” the expert says.
“The worst crash generally is the side pole impact. That is a very difficult test to pass, from a legislative perspective, because you have a high level of intrusion through a sill section and into the battery enclosure,” the specialist EV builder says.
“When you have a standalone battery pack bolted into a chassis, typically you will end up with the mounting structure being relatively close to the extremity of the vehicle, and it therefore comes into the impact fairly early.
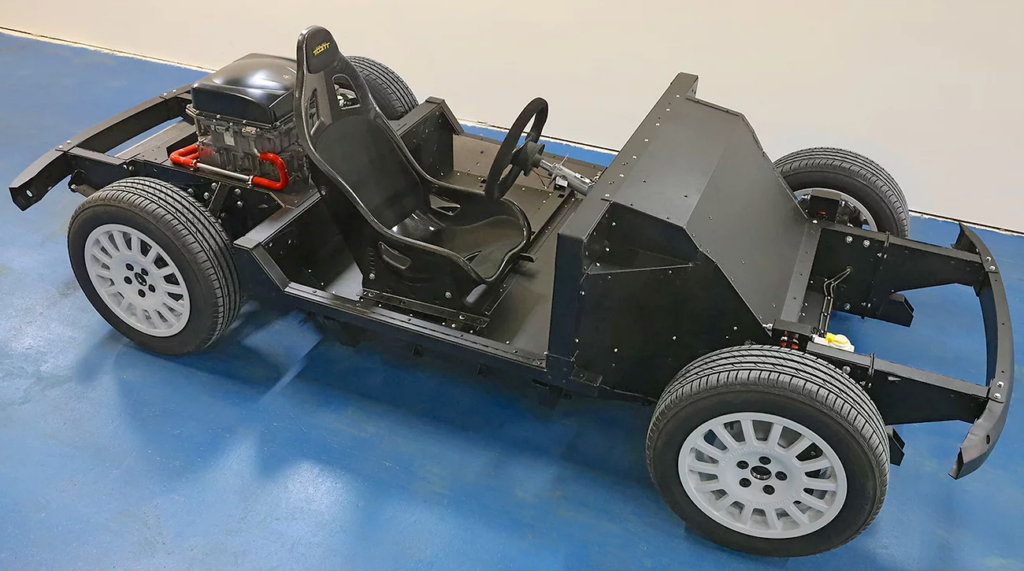
(Courtesy of Watt EV)
“When you are building an integrated module- or cell-to-chassis solution you have the opportunity for a much greater deformation area before you get into battery deformation.”
That said, the elimination of battery housings and module components call for new developments of structural elements, notes the adhesives and thermal management materials expert. “Even if the vehicle chassis itself remains undamaged, the crash impact can affect the cells, causing damage to interfaces or in-cell structures and potentially leading to severe thermal runaway events. Additional safety measures will be necessary to protect battery cells in vehicle-to-chassis concepts,” the adhesives and materials expert says.
The EV consultant and battery maker concurs. In addition to fuses and interconnects that break when certain mechanical stress levels are exceeded, advanced materials will play even more important parts than they do now.
“We are getting to a point where over the next few years you will start seeing materials that break down under thermal stress and release phase-change materials that could extinguish a fire,” he says. “Certainly the F500 additive used in fire extinguishers in Formula E is promising. Progressive chemicals like that are very capable, but you have to have some really serious damage to a battery for them to come into their own.”
Cell format impacts
Not all cell formats are well-suited to either cell-to-pack or cell-to-chassis battery construction, with pouch cells in particular lacking inherent structural strength and requiring additional support that also allows for their expansion and contraction during charging and discharging. Prismatic and cylindrical cells feature a robust aluminium or steel alloy housing, respectively, whereas the housing of pouch cells is made of less stable composite foils.
Larger cylindrical or prismatic cells will be better suited to the application, the vehicle technology and engineering services specialist says. “Our initial analysis with the 21700 cylindrical cell is that stacked tolerances could become a significant barrier to reliable repeatability in manufacturing.”
While cylindrical format cells can be made in large energy capacities and large physical sizes, most are small, and as the technology for mass producing the jellyroll anode, separator and cathode structure is very well understood, the other formats are playing catch-up when it comes to economies of scale, our EV consultant and battery manufacturer points out.
“If you are churning out a vehicle every 5 minutes, that means you have 5 minutes to make the battery… and you have a few seconds to make each cell,” he says.
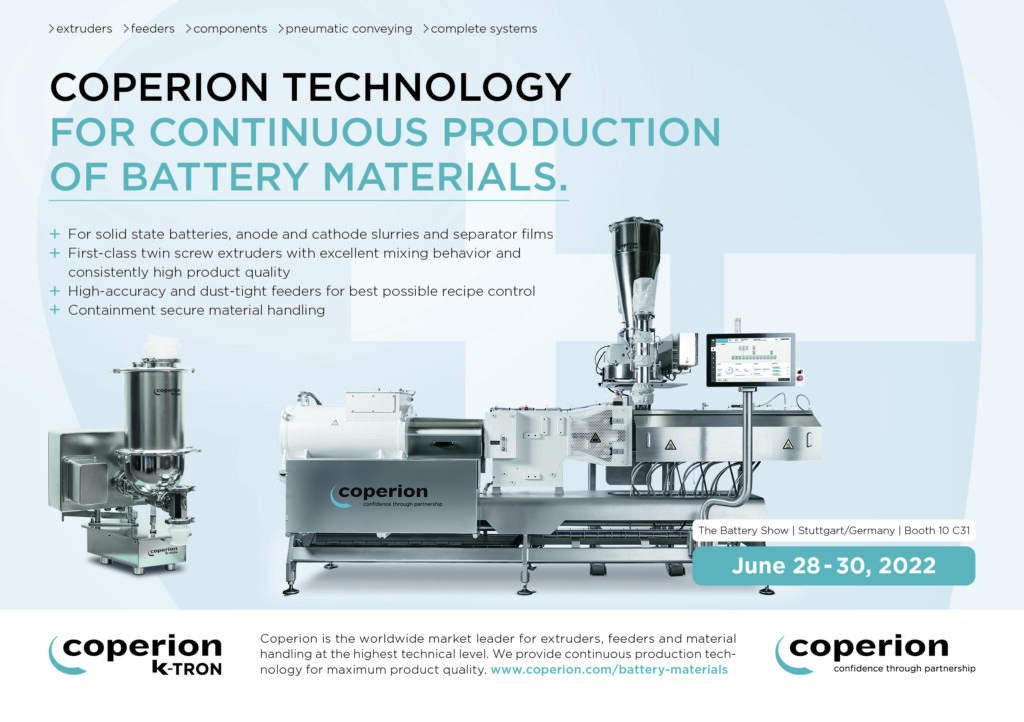
“For cell-to-pack and cell-to-chassis construction you need a large capacity cell, and certainly large pouch and prismatic cells are available, and in certain chemistries you can get some very large cylindrical cells, but not in the hundreds of amp-hours you would need for the average car,” he says.
Physical size, energy capacity and structural strength are not the only important factors, however, as electrical connectivity also has to be taken into consideration, the lithium metal battery developer emphasises.
“Prismatic cans are best suited for cell-to-pack and cell-to-chassis battery designs owing to the presence of both electrical terminals on the top of the cell, allowing for access to make the electrical connections to build up the voltage and battery as well as installing and connecting the battery management system [BMS],” he says. “Cylindrical cells typically have a terminal at each end of the cell and will be problematic to access the bottom terminal for cell-to-cell electrical connections.”
Cell size is also important for assembly, the specialist EV builder says. “As a general rule of thumb, a larger cell format will reduce the number of connections needed, and will be better suited to high-volume applications where are you are looking at reducing manufacturing time.”
Battery case design
While the loss of internal module structure in cell-to-pack designs has to be taken into consideration, the pack case does not have to very different from one enclosing a conventional module-to-pack battery, the lithium metal battery specialist argues.
“Tesla dramatically improved the Model 3 battery pack design over the Model S by decreasing the number of modules in the battery pack from 16 to four. At the same time, Tesla was able to communise the modules resulting in only two variants, a 23S and 25S module,” he says. (Communisation is the practice of using the same components across several vehicle models.)
“To be successful in the EV battery pack business; communisation leads to greater efficiencies of scale.”
The vehicle technology and engineering services specialist emphasises that it is not necessary to reinforce the enclosure in all cell-to-pack designs. “The important consideration in this design philosophy is to take a holistic view of the vehicle as a whole,” he says.
“Larger format cells could play in role in providing some structure to the vehicle if you can design the systems to transfer load in a safe, controlled way. The trade-offs should be viewed at a vehicle level.”
For all battery designs the pack housing structure, or case, makes a vital contribution to the overall mechanical integrity of the battery pack, the adhesives, sealants and thermal interface materials expert says. “The loss of internal structure provided by the module can increase requirements on the housing, although this effect is considered moderate.
“Some battery manufacturers aim for a cell-to-pack design that also omits the use of extrusion profiles and cross-struts to maximise volume use and packing efficiency of the cells. In this case structural support through, for example, reinforced battery housings with strengthened bottom or top plates that act as a rigid outer skeleton can be required to improve overall stiffness and crash resistance.”
The EV consultant and battery manufacturer emphasises that battery case design, whatever the kind of architecture used, the same fundamentals apply. “As a consultant, a lot of my time is spent explaining the principles of battery design to good mechanical engineers because, really; it’s a mechanical engineering job and you just need to know the rules,” he says. “You give plenty of space around the high-voltage interconnects, and you follow an architecture that has safety principles built in.”
Thermal management effects
While the cell-to-pack concept has some impacts on thermal management, they are not fundamental. “In general, most modules are loaded onto a cold plate, and cell-to-pack would be no different,” the lithium metal battery developer notes. “In the case of prismatic can cells, they can be placed directly onto a cold plate and held in place with a thermally conductive adhesive.
The vehicle technology and engineering services specialist says, “I would add that by removing the module, it’s clear that failure to design a safe cell-to-cell propagation prevention method will probably cause a more severe failure, without the module to provide containment, particularly when coupled with larger format cells.
“Therefore, our thermal strategies have been designed from the ground up to ensure we go back to first engineering principles. We then accelerate our deployment of a given solution by using our strong intellectual property in this space. Now more than ever, we also leverage our control systems capability to ensure we are able to detect potential failures far in advance of a physical event.”
While the impact on thermal management cannot be clearly generalised, says the adhesives, sealants and thermal interface materials expert, the effect on overall cooling requirements is expected to be low, and on cooling plate design it is expected to be moderate. However, the effect on the use of thermal interface materials could be more significant, particularly with prismatic cell designs.
“As the cells are required to provide enhanced structural stability within the battery pack, conventional thermal gap fillers can be replaced by thermally conductive adhesives,” he says.
With the omission of modules, the propagation of a thermal runway can be faster and more severe in cell-to-pack batteries, and needs to be addressed by additional safety measures, he adds. Further, larger cell designs are often seen in cell-to-pack concepts that can also lead to more severe thermal runaway events as more energy can be released. Thermal runaway prevention is expected to become more important in cell-to-pack designs by means of cell-to-cell heat shield materials, for example.
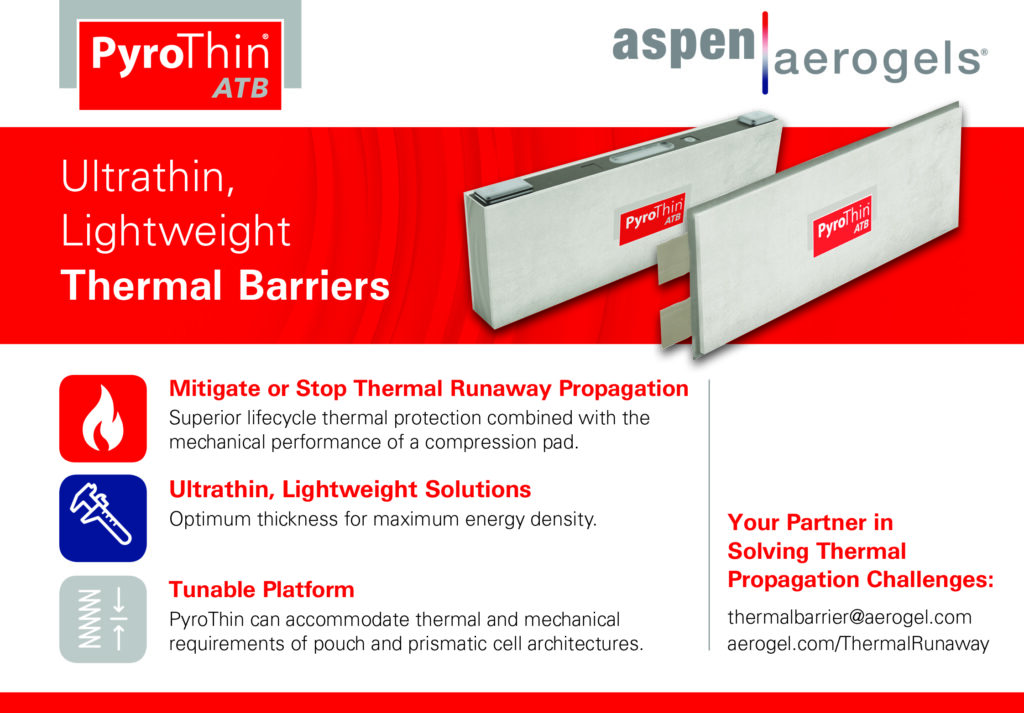
The specialist EV builder notes that the effects of module-to-chassis and cell-to-chassis construction on thermal management can be application-specific. The company has developed a low-volume sports coupe with a module-to-chassis battery system with air cooling, for example.
Air-based thermal management is sufficient when performance requirements are low, he says, while there are several ways of providing thermal management with liquid heat transfer media. These include hard-piped solutions, expanding enclosures that fully encapsulate individual modules or by immersion.
“From a design point of view, how you integrate those will depend on the type of cell or module you’re using and the thermal challenges you’re presented with,” he adds.
“There is some really interesting work being done around the immersed solutions at the moment. One of the significant issues with them, however, is that you end up with a very high-mass dielectric fluid.
“The reality is that some of these technologies are well-developed. In our case, a module-to-chassis approach is proven in the coupe we have developed, and the platform can be used as the basis for a wide range of alternative applications, be they passenger or commercial. Full immersion of a pack, however, is still at a relatively low technical and manufacturing readiness level and needs significant work to understand the real-world benefits.
Air cooling for the coupe’s module-to-chassis battery was chosen because it chimes well with the company’s philosophy. “What we are trying to do is ‘lightweight’ the EV,” its builder says. “The bonded aluminium and multi-material structure mean that we end up with a very light vehicle platform.
“In the case of the coupe, we have a full vehicle that weighs under 1000 kg with a 40 kWh battery capacity. By reducing mass, we are seeing benefits at system levels throughout the vehicle. For example, the thermal loading of moving something weighing 1000 kg is much smaller than that generated by moving something that weighs 2000 kg.”
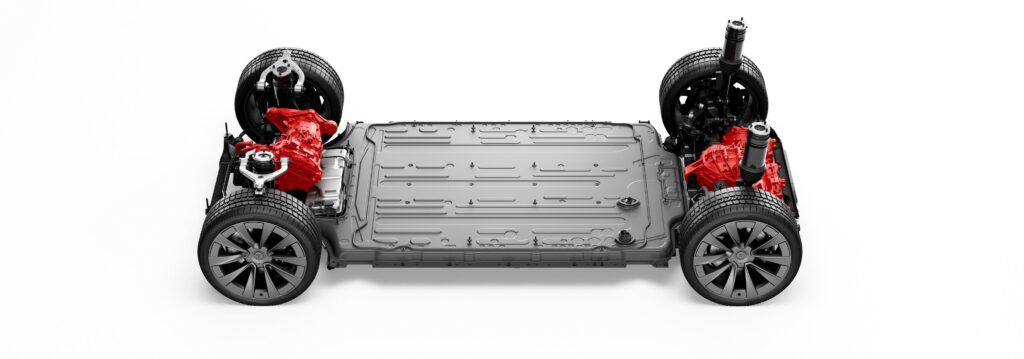
(Courtesy of Tesla)
Interconnects and the BMS
The battery developer working with the EV builder stresses that in any battery pack there are really two interconnects to consider, the first being the high-voltage, high-power system for the traction motors, the second being the sensing and control network for the BMS.
“When you have a system based on modules, the monitoring aspect can be effectively distributed through the module,” he says. “You might have a circuit board in each module for the temperature and voltage measurement, and that has a single Can bus connection that talks back to the master part of the BMS.
“The high-power connections will be made via bolted connections or via a large pin on the connector. Those modules are typically identical, so they can be easily assembled in manufacturing and can be replaced during a refurbishment or repair of the pack.
“In a cell-to-pack or cell-to-chassis design, the interconnects for the cells are either welded or bolted, depending on the cell format. They might be connected in groups if they are small cylindrical cells, groups of cells in parallel, fitted into the chassis or pack. The BMS will have its own ‘octopus’ of cables running out to the individual cells.
“If you look at it from a logical perspective, the wiring diagrams would look the same but the physical implementation would be different between the systems.”
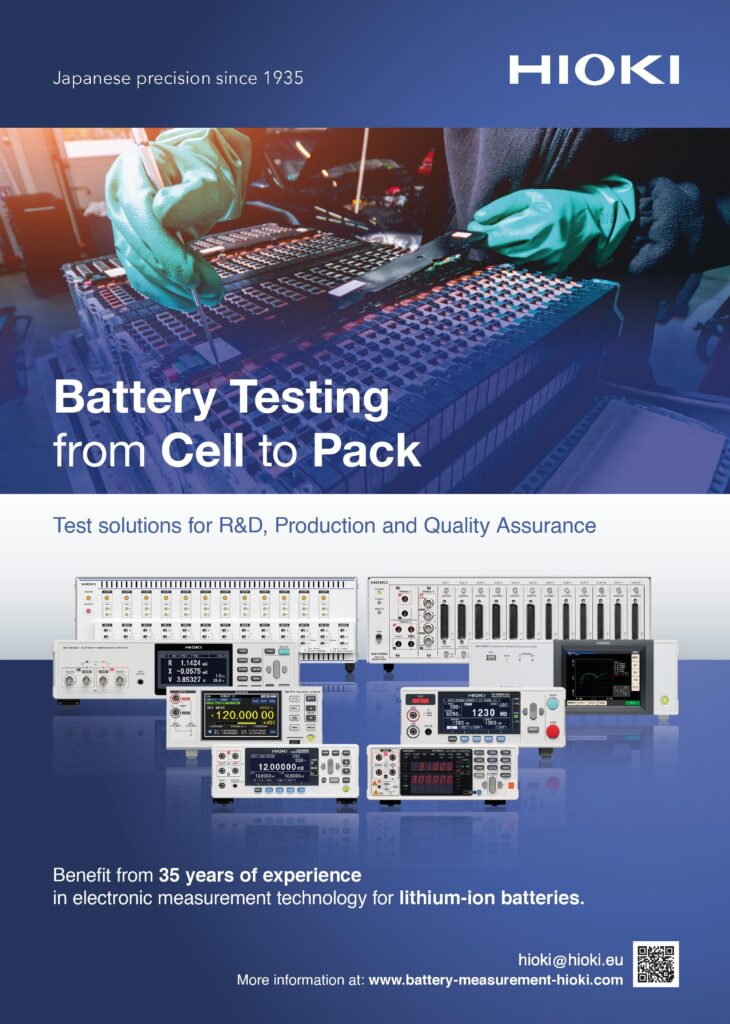
Serviceability and replacement
The lithium metal battery maker cautions that cell-to-chassis designs can make battery servicing difficult. “The battery enclosure portion of the vehicle chassis must be removable to be able to access and service the battery pack, and having an easily removable battery also facilitates battery swapping,” the company expert says.
He stresses that the vehicle OEM must develop a strategy and requirements for servicing. For example, this would involve determining which components are serviceable, identifying the least replaceable unit, and deciding what the training requirements for technicians are. Another key decision is whether each dealership services the battery, or whether it should go to a regional repair facility.
While adhesives can ensure strong, reliable fixing of cells to the chassis, repair, replacement and recycling are major challenges with this kind of battery architecture, the sealants and adhesives expert says. “The development of adhesive and mechanical concepts that allow a simple disassembly of the battery after reaching end-of-life or battery failure is a pivotal task.”
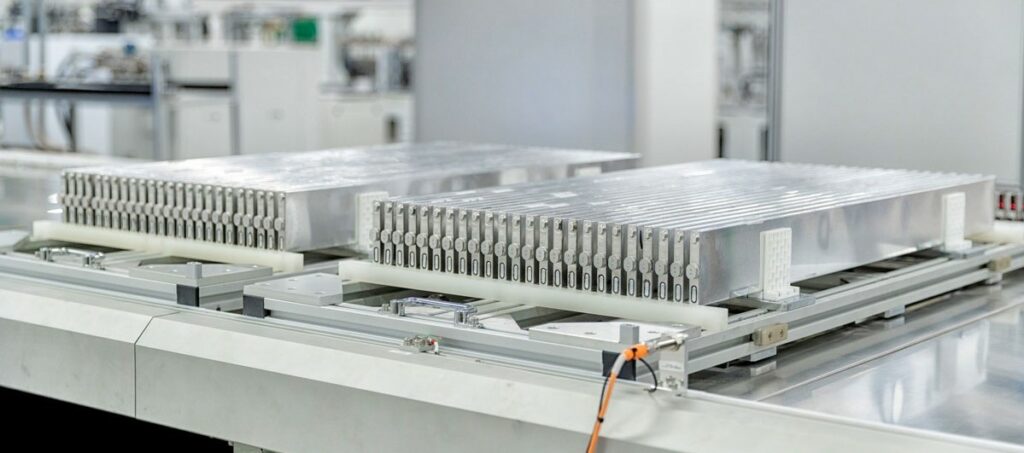
(Courtesy of BYD)
Growing maturity
The technical maturity of these architectures is progressing quickly, with cell-to-pack much further along. Multiple automotive OEMs and cell manufacturers have announced the introduction of their cell-to-pack and cell-to-chassis battery concepts to the market, with Tesla’s structural battery pack, BYD’s Blade battery and CATL’s cell-to-pack designs being the most prominent examples, the sealants and adhesives expert notes.
“While early examples focused mostly on the safer LFP cell chemistry, recent announcements also include nickel-rich layered oxides that are considered harder to handle,” he says. “That clearly indicates the rising maturity of cell-to-pack technology. Following BYD’s cell-to-pack market introduction in its Han [luxury saloon] in 2020, more automotive OEMs are expected to announce development of novel cell-to-pack concepts.”
Acknowledgements
The author would like to thank Ian Goodman at Goodman Wolfe Consulting, Dr Tobias Knecht at Henkel Neil Yates at Watt Electric Vehicle Company, Pete Bishop at Silver Power Systems, James Hoxey at Williams Advanced Engineering, and Mark Niedzwiecki at Sion Power for their help with researching this article.
Some suppliers of cell-to-pack and cell-to-chassis batteries
Germany
Henkel+49 211 7970 www.henkel.com/company
Japan
Panasonic +81 6 6908 1121 www.industrial.panasonic.com/ww/products/pt/lithium-ion
Korea
LG Energy Solution +82 2 3777 1114 www.lgensol.com/en/index
Samsung SDI +82 55 380 2334 www.samsungsdi.com/automotive-battery/index.html
SK Innovation +82 2 2121 5114 eng.skinnovation.com/http://eng.skinnovation.com/
UK
Silver Power Systems www.silverpowersystems.com
USA
BYD North America +1 213 748 3980 www.en.byd.com
C4V +1 607 224 2225 www.chargecccv.com
Sion Power +1 520 799 7500 www.sionpower.com
ONLINE PARTNERS
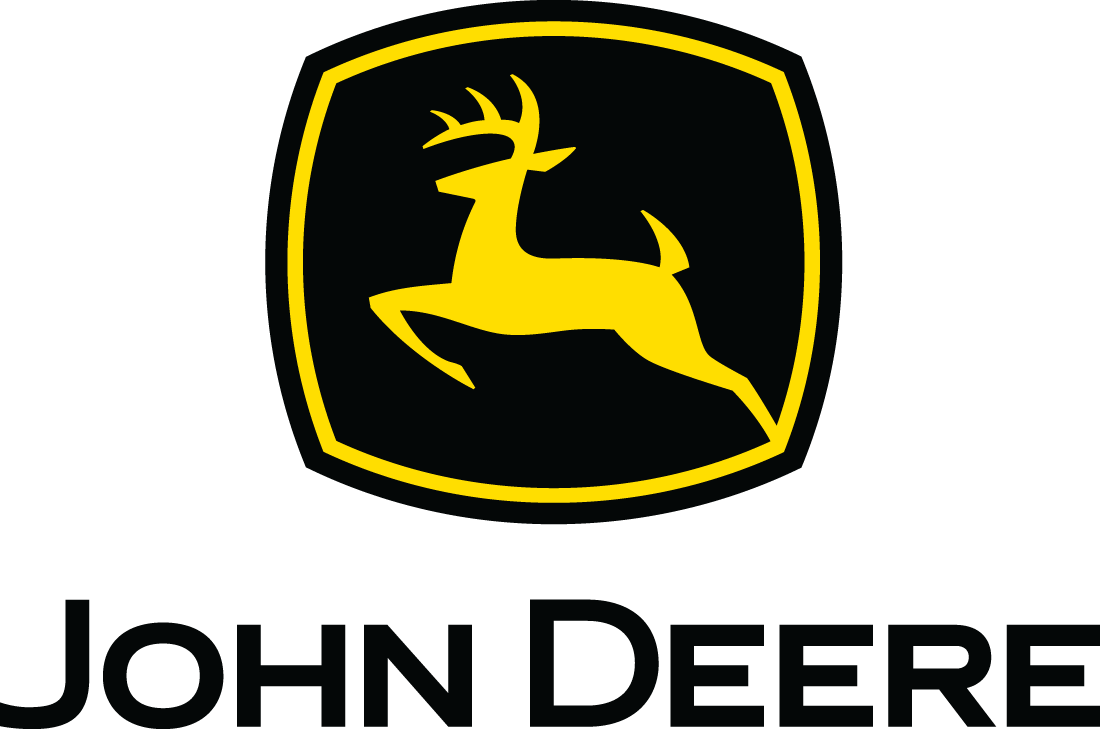
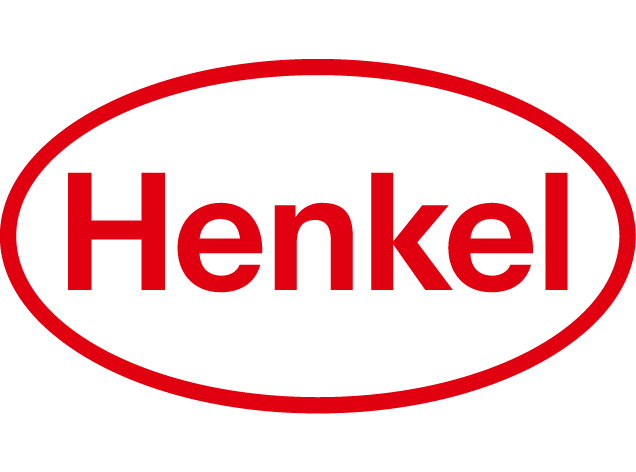
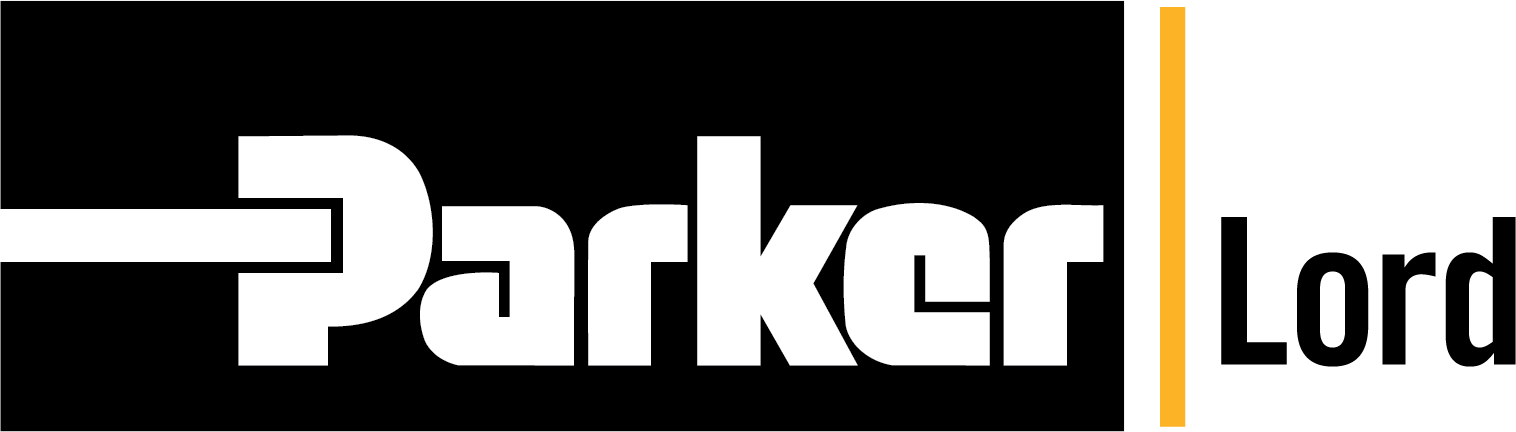
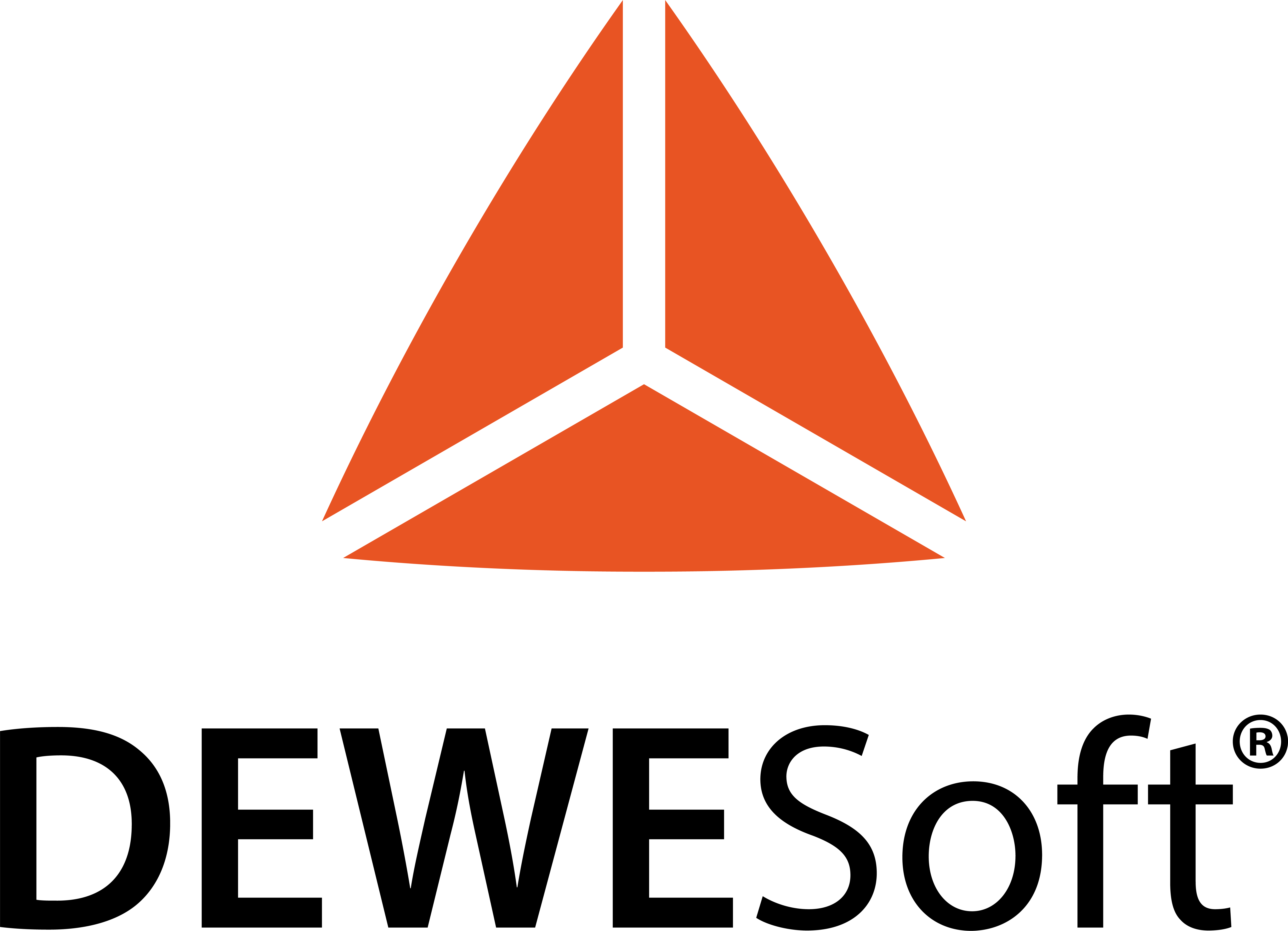
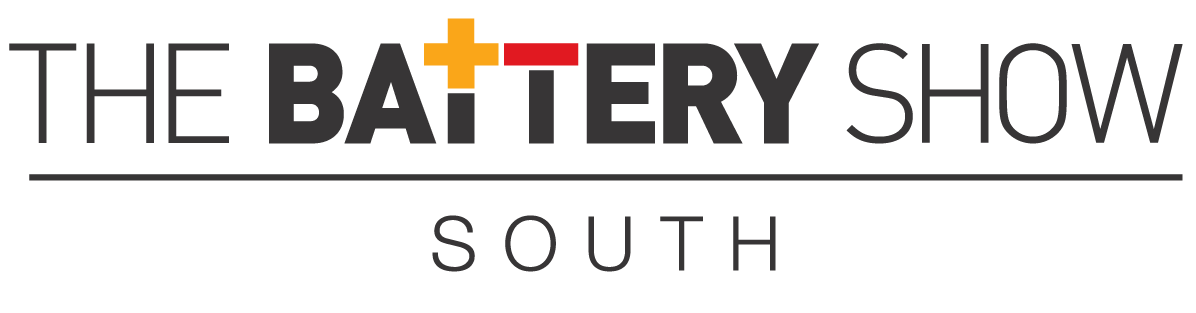
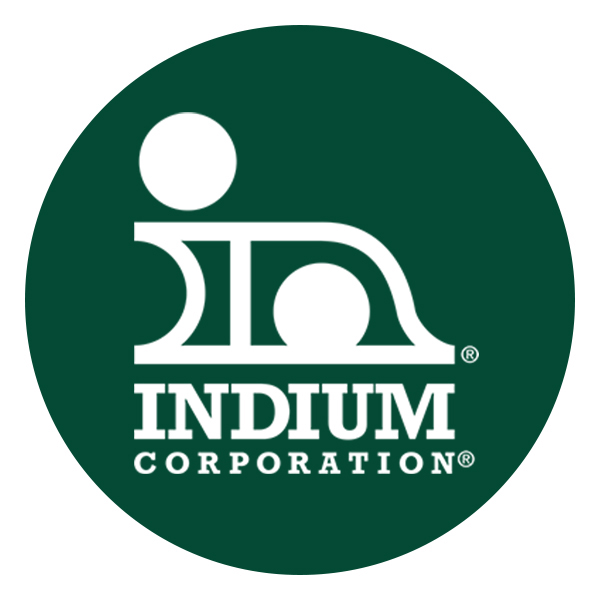

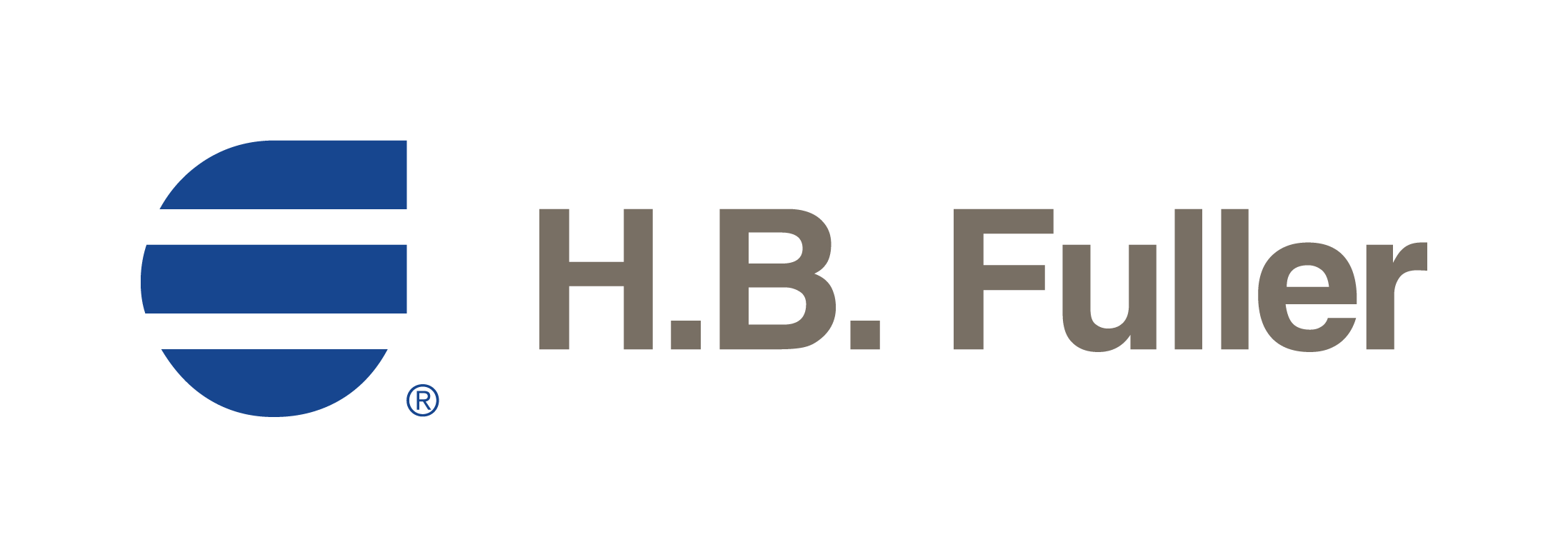
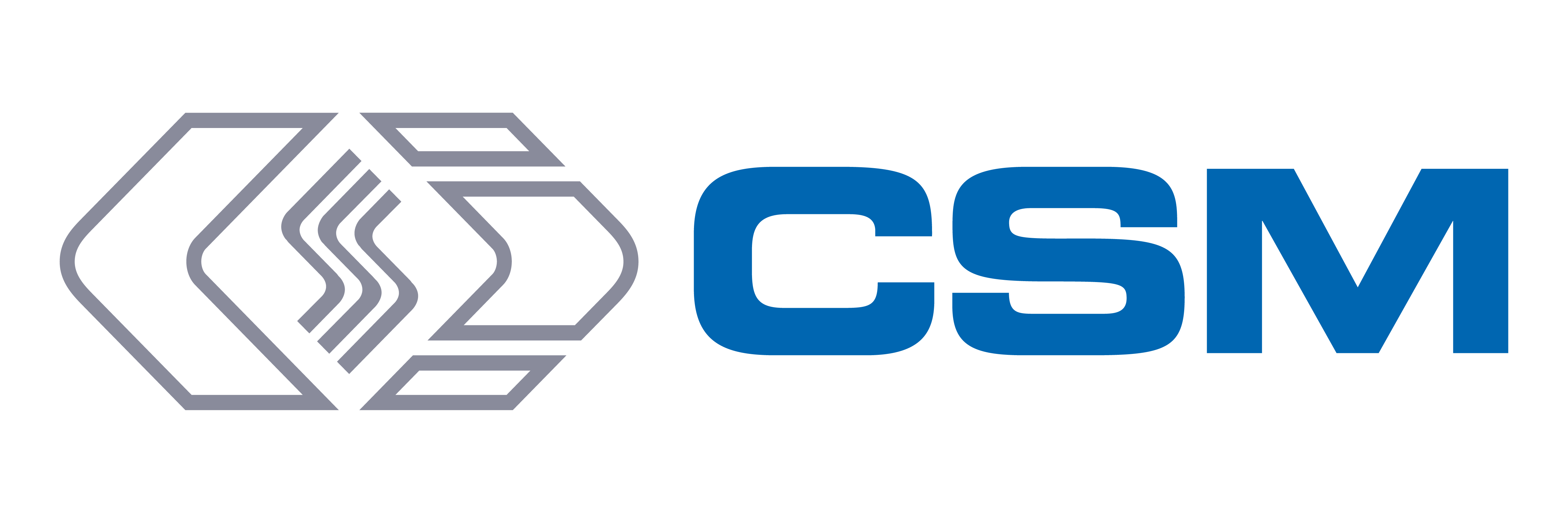
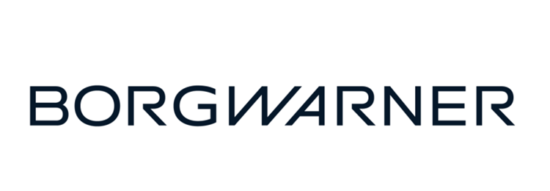