Candela C-7 speedboat
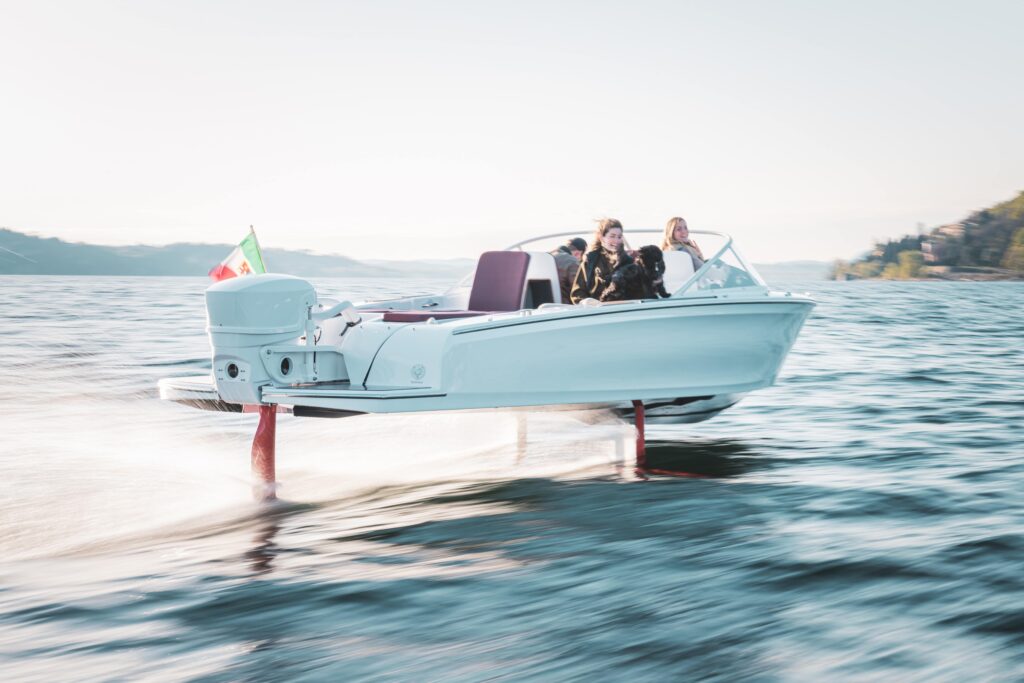
(Images courtesy of Candela Speed Boat)
Wing commander
Hydrofoiling gives this serial production boat high speed and long endurance. Rory Jackson examines the engineering decisions behind its design
When it comes to designing new kinds of boat hulls that will get as much power and endurance as possible out of battery-electric powertrains, one of the smartest things a maritime architect can do is simply lift the boat out of the water so that it doesn’t have to deal with all the drag and slamming that comes from propelling boats through waves.
We last featured such a solution in EME 6 (Spring 2020); as featured in that issue’s cover story, Green City Ferries and Echandia Marine had collaborated to create their BB Green all-electric boat. This Swedish commuter ferry used a 60 kW fan to generate a surface-effect air bubble beneath the centre of the hull, effectively raising about 80% of the boat’s ‘wet area’ out of the water.
That cut down the hefty energy bill induced by hydrodynamic drag, giving the companies’ vessel a considerable boost in energy efficiency not to mention side-benefits for commuting work, such as a much-reduced wake wash and a significant increase in speed.
It seems, however, that Swedish engineering is never quite ‘finished’ when it comes to pioneering new zero-emissions vehicles and maritime technologies. Rather than be content with pushing only 80% of the boat above the waterline, Stockholm County-based Candela Speed Boat has successfully engineered a hydrofoiling boat that works by using a wing beneath the keel to lift the entire hull out of the water.
Candela’s flagship product is its C-7 speedboat. In July, this two-seater, battery-electric craft competed (and came first) in the YCM International Speed Record race – the world’s biggest competition for electric and new energy boats – during the Monaco Energy Challenge. Among the competitors it beat were boats packing e-motors with 10 times the C-7’s horsepower.
Its electric motor produces up to 55 kW (73.7 bhp), which enables the 1300 kg, 7.7 m-long boat to move at a top speed of 30 knots. It cruises at 22 knots, at which speed it has a range of 50 nautical miles, or 92.6 km (not including an additional 14.8 km the system automatically ‘sets aside’ for limping home at 5 knots) between charges of its 40 kWh battery pack.
Its carbon fibre hull is 2.4 m wide, and its draft is 0.7 m when stationary or moving slowly. The draft extends to 1 m when moving at speed and foiling, and reaches a maximum of 1.5 m when the hydrofoil is extended but the boat is not foiling.
History of the C-7
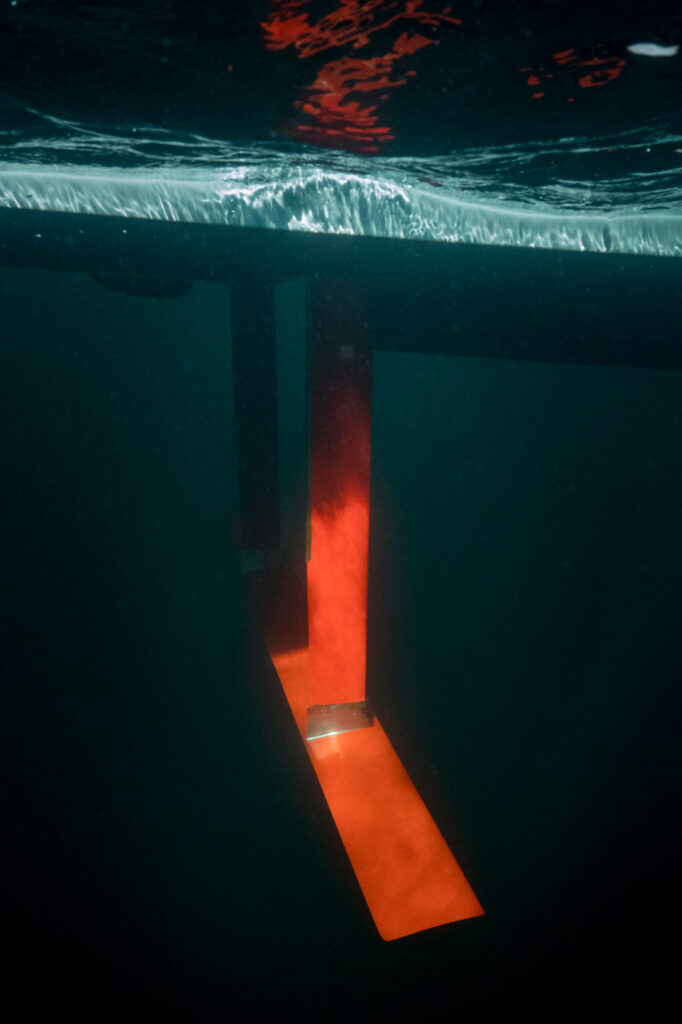
Candela was founded in 2014 by now-CEO Gustav Hasselskog after a holiday in the Stockholm Archipelago. While various factors motivated him to spearhead the development of a clean and energy-efficient speedboat, initially it was the high fuel costs incurred by repeated trips to and from the mainland during the holiday.
“Many people in northern Europe live either in island towns, island suburbs or similar, where regular commutes or other short trips are most conveniently made by boat,” explains Candela’s communications manager Mikael Mahlberg. “Gustav had looked into electric boats but found existing hulls consumed too much energy to get decent range at high speeds.
“For reference, a conventional 25 ft speedboat consumes about 15 times the energy per kilometre of a standard family car. And lithium-ion batteries contain just one fifteenth of the energy of gasoline.”
Anyone hoping to make an electric boat with a conventional hull hits something of an engineering wall. If they want high speeds, they get very short ranges, even with the highest-quality lithium-ion batteries currently available.
The optimum with present technology is around 120 kWh of energy for roughly 20-25 nautical miles of range, since integrating any additional battery packs will increase the vessel’s weight and drag to offset any potential gains in range, until eventually the boat simply sinks.
Faced with this hurdle, Hasselskog opted to create an electric hydrofoiling system that would lift a boat’s hull above the water and remove the problem of hydro drag altogether. He therefore began gathering a development team in 2014 that soon became Candela Speed Boat. Building the first prototype began in 2016, the final prototype followed in 2018, and serial production started in 2019.
With the boat and its unique technology now highly optimised and matured, Candela has now started manufacturing and selling the C-7, making it the first electric hydrofoiling vessel to enter serial production, with about 30 boats produced and sold each year. That is currently the maximum capacity of the 50-person company’s production capacity, but the company plans to scale up production, its next target being 400 units a year by 2024.
There is one last technology in the C-7 worth noting. Green City Ferries’ latest version of its fast commuter electric ferry design now does without the surface-effect air bubble technology in favour of a hydrofoil-assisted catamaran architecture, making the hydrofoil a de facto blueprint for the future of maritime e-mobility.
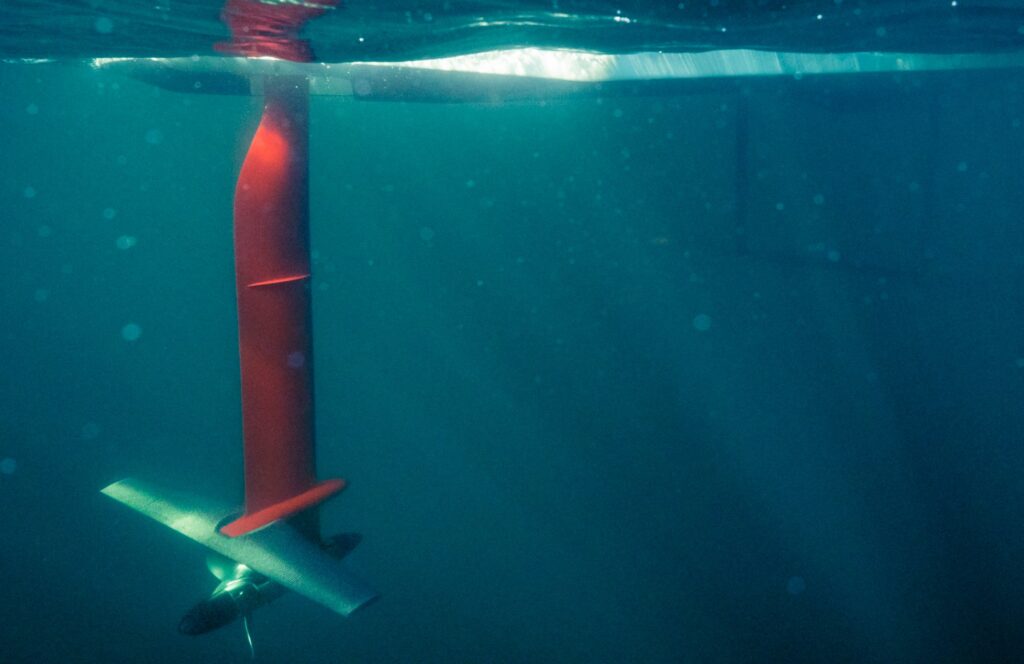
System overview
Compared with a conventional powerboat, the C-7 uses 80% less energy when in motion – around 0.85 kWh is consumed per nautical mile when cruising at 22 knots. As mentioned, almost all this energy efficiency comes from having lifted the boat out of the water, although not having to bear the mechanical and thermal losses of an IC engine helps too.
Foiling successfully relies on a few key points of the boat’s architecture. First, it needs to be light enough to be held above the waterline by the hydrofoil’s lift. The heavier the boat, the wider the foil must be, which increases the collision area and reduces drag efficiency and hence range.
The C-7’s hull design and engineering has been handled largely by structural engineer Olivier Philippot, who was chosen partly for his extensive experience of producing safe, lightweight, low-drag structures for attack helicopters with Eurocopter Group (now called Airbus Helicopters). The hull and structure have therefore been manufactured almost entirely from carbon fibre composite rather than fibreglass, the traditional hull material of most speedboats. It features thin outer carbon skins and decks, with spars and ribs glued throughout the interior for strengthening, like those inside the wings of passenger aircraft.
When it comes to piloting the boat, the key problem with submerged hydrofoil vessels is that they are inherently unstable: like a learner cyclist on a two-wheeled bike, they ‘want’ to fall to one side or the other. This imbalance must constantly be corrected – whether it be at high speed, cruise or turning – and it must be accomplished in a way that keeps the boat’s pilot and passenger(s) comfortable, or else no-one will want to sit in the resulting product.
The C-7”s hydrofoil is thus designed to be electromechanically shifted in order to rebalance the boat across the full range of motion it can perform, and in the pitch, roll, and yaw axes. It must also be able to maintain its height with great accuracy, or else risk repeatedly slamming or crashing into waves.
To enable the boat to understand its own dynamics and surroundings well enough to consistently keep the foil 50-60 cm beneath the surface of the water, given that piercing the surface will induce a loss of lift and cause the boat to settle on the water’s surface, a comprehensive suite of sensors has been arranged. This includes inertial sensors for measuring changes in the vehicle’s position and orientation, as well as barometers for gauging the altitude of the boat, and ultrasonics to give readings on the distance between the hull and the water.
Mahlberg notes that Candela is not the first to attempt a control system such as this. Before them, Boeing produces its 929 Jetfoil ferry, which was launched in 1974 and used a control architecture based on the aerospace giant’s jet aircraft to keep the large 115 t watercraft balanced.
“The development of Boeing’s system originated from their military technology,” Mahlberg says. “Their flight controller is actually pretty similar to ours in terms of its overall architectural concept, and I imagine it was picked from their jets.
“The dynamics of a hydrofoiling boat aren’t too dissimilar from a fighter jet. You have a lot of speed, a lot of imbalance, so you need a control system that keeps the craft from constantly rolling or dipping too far in one direction, and does so without overcompensating either.”
That vessel was powered by twin gas turbine engines and could achieve up to 45 knots. Boeing built a handful of them, although after 1985 it opted out of the hydrofoil industry and sold its licence for the 929 to Kawasaki Heavy Industries, who built only 16 of them between 1998 and 2020.
As mentioned however, Candela has been able to manufacture and sell far more boats than this, with many more on the way. Their production costs relative to the 929 have been helped in no small part by the massive availability of much smaller, cheaper and more lightweight electronics for making the kind of control architecture necessary for a hydrofoil. Also, the measurability and controllability using sensors and processors are helped by using an all-electric, fully digitalised powertrain, rather than a twin gas turbine arrangement.
“Advances in those components have helped us so much,” Mahlberg adds. “We’re selling a €300,000 pleasure boat, and the precision of driving and balancing from our electronics would have cost tens of millions of dollars just 20 years ago, I don’t want to think how much it must have cost Boeing in the 1970s.
“And we’ve refined the overall concept too, particularly for energy efficiency. If you look at the 929 Jetfoil, it’s actually a super-inefficient vessel, I think it consumes around 1600 litres/hour of fuel.”
In addition to needing various sensors and other electronics, the drive for energy saving and motion stability has spurred a lot of work on the propulsion mechanisms, both the hydrofoil and the thruster at the back. These systems comprise the three beams, or “struts” as they are called internally, that extend from below the C-7’s hull as it flies above the waves – that is, two forward struts attached to the foil, and one rear strut holding the thruster.
Candela emphasises that the real revolution with the C-7 is the foil system rather than the electric motor and battery pack, but the way the latter are packaged and used are still worth noting, particularly in terms of the thruster’s hydrodynamics. Both the thruster and the hydrofoil have been engineered to minimise drag along with any potential points of failure that could harm ride quality.
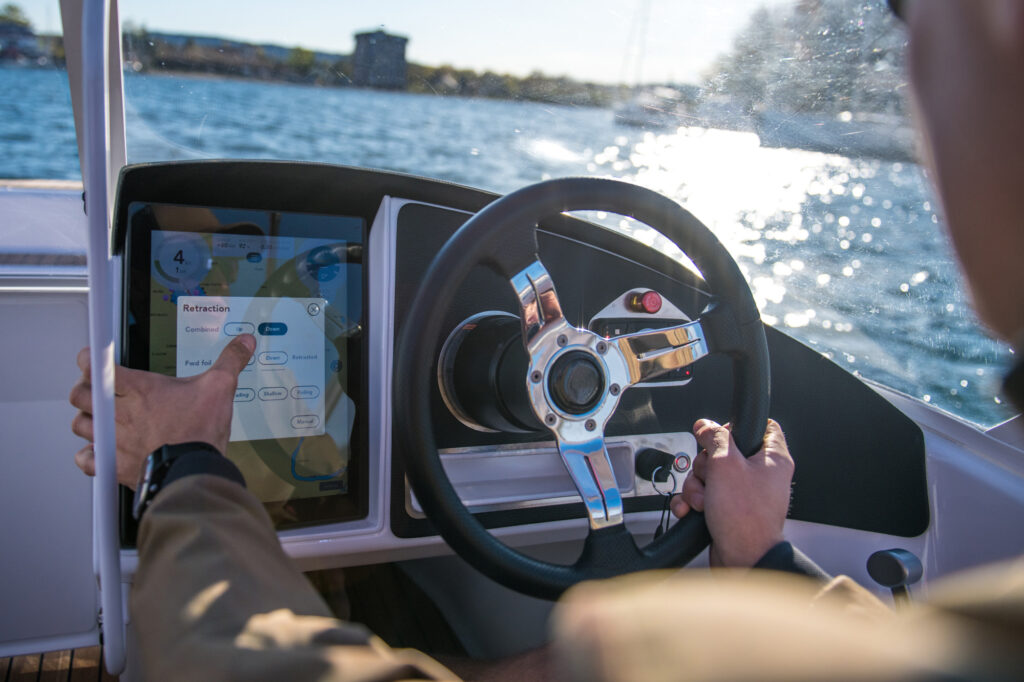
Developing the hydrofoil
The first version of the C-7 featured a vee-shaped hydrofoil, whose design was based on extensive computer simulations.
Nonetheless, when it came to real-world testing it proved to be insufficiently stable at speed. That was not unexpected: the C-7 has to deal with airflow around its hull as well as the flow of water around its foil and thruster as it moves, and Candela’s engineers were acutely aware that not many software programs were capable of accurately simulating the dynamics of both air and sea at once.
That meant much of 2016 and part of 2017 was spent redesigning the foil and developing the software. The foil’s width is close to that of the beam, with the hydrodynamic optimisation of the cross-section (and the rest of the foil shape) being a trade-off between multiple conflicting factors.
“For example, if you want more lift you could just make the wing much longer, but if the foil protrudes past the draft of the hull, it’ll become a pain when you’re trying to dock,” Mahlberg says. “We didn’t want any compromises in how the C-7 compared with a normal IC-engined boat; it had to be able to dock normally, traverse shallow waters, be transportable on a road trailer, and so on.”
To ensure these latter two capabilities, the wing is held in place by two retractable struts that mount vertically into the boat hull via two holding shafts. Each strut is connected to an electric motor that serves to either lower the foil about 80 cm below the keel line or raise the foil about 20 cm above it (where it tucks in safely behind the keel).
From start-up to about 16 knots, the C-7 operates like a normal speedboat, using just its outboard thruster; when commanded via the throttle lever to go faster, the hull starts to fly, foilborne. When dropping below 16 knots, the foil will not produce enough lift to sustain flight, so conventional operations are resumed.
When flying, the foil struts are locked in their most extended position by a robust bronze lock-pin. In flight, hydraulic actuators push on the struts to make them pivot around the lock-pins. When the struts pivot back and forth, they cause the foil to change its angle of attack.
“Engineering the system for banked turns proved to be a challenge that nobody had solved before on a foiling leisure boat,” Mahlberg says. “Most hydrofoils in the past were built such that when they turned, it really felt like a go-kart: the passengers would feel as if they were being pushed to one side from the g-forces, because the boats weren’t engineered to bank when turning.
“Performing a banked turn, in which the whole vessel leans into the curves like a motorcyclist, is really important not just for a comfortable ride but to minimise the mechanical stresses that the boat puts onto the foil and its beams.”
And although perfecting the dynamics and timing of the foil’s actuators via the control algorithms has been a key part of the C-7’s turning ability, its success has also come from designing the wing to physically twist during the boat’s turns.
There is no actuator inside the wing, the carbon composite from which it is made has been selected because it can be twisted back and forth without cracking. Earlier versions used aluminium, but the stress imparted on them from turning proved unsustainable.
There are a few mechanisms included in the hydrofoil’s design to enable banked turning. The first are the lock-pins, one in each of the foil’s two struts, which are activated electromechanically to enable the actuators pushing on the struts to make them swing back and forth.
To steer left, for example, the left strut is pointed backwards, the right strut is pointed forwards, and the wing twists accordingly. The foil system shares similar traits with the Wright brothers’ first aircraft, the Flyer, which relied on a twisting wing rather than ailerons. Also, a proprietary holding device joins each strut to the foil to allow some limited axial freedom of movement, and to ensure no structural stress is imparted to the joints that could cause either of them to break.
“The middle of the carbon fibre foil flexes and bends, which makes the foil function much as an aileron to roll the boat, with the rudder at the rear assisting in steering,” Mahlberg says. “We didn’t want to use flaps underwater, as they would just create more potential points of failure and also the potential risks of biofouling or similar.”
The foil is by design not indestructible – if it hits a submerged rock at cruising speed or above, for example, it will break off for safety reasons, rather than breaking the whole boat. This is a big advantage compared with non-hydrofoil boats, says Mahlberg.
The shafts that hold the struts are designed to function as the strongest points in the hull, so despite the loss of the foil, the rest of the boat will still function normally, enabling a safe (albeit less energy-efficient) return to port. The foil can then be easily replaced.
“I had the opportunity to try this in my first week on the job,” Mahlberg recalls. “When foiling into a harbour, I hit a submerged chain strapped across the entrance. The landing was totally undramatic, but when I looked down I couldn’t see the foil – it had come off. We replaced it in less than an hour and were out foiling soon after,” says Mahlberg.
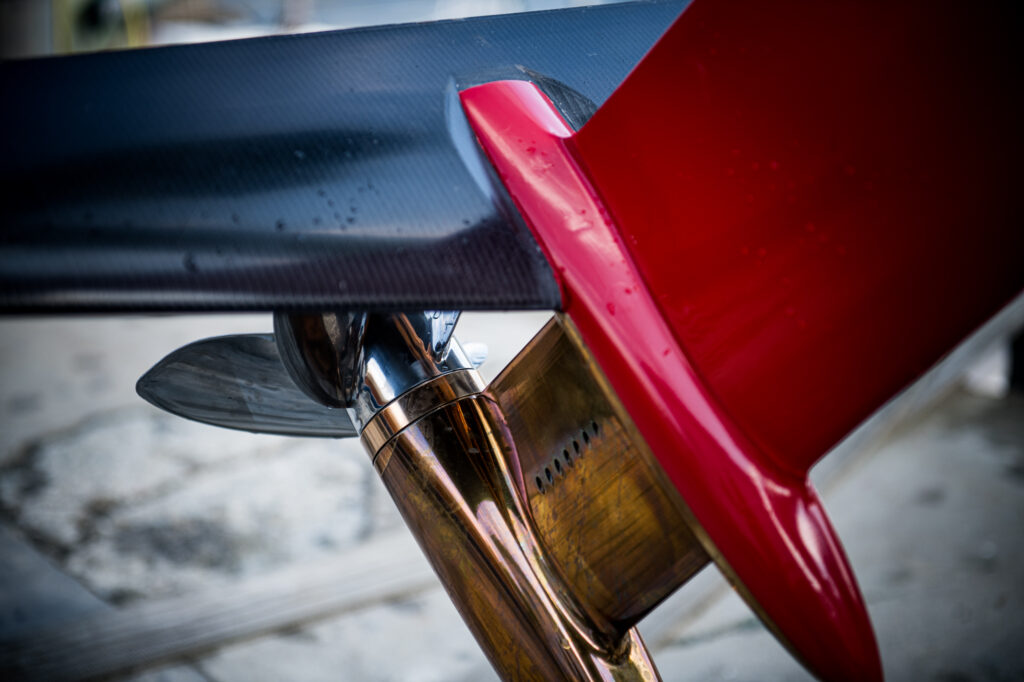
Powertrain
The core of the thruster used to propel the C-7 is a Deep Blue 50 R from Torqeedo. This is an 80 bhp electrically powered outboard thruster weighing 139 kg, with a top propeller output speed of 2400 rpm and a maximum torque of 198 Nm.
The shaft running down from the electric motor and gearbox to the propeller is 51 cm long. Its tilting and trimming surfaces are designed without hydraulics, and its structure is cooled using seawater. The thruster is lifted in and out of the water by hydraulic actuators, in a movement resembling that for a normal IC outboard engine, but with an added pitching movement that eases access to the motor and gearbox for maintenance.
In the C-7, however, the mechanics and electronics of the Deep Blue 50 R have been repackaged into a design with similar dimensions to the foil and forward struts, to achieve comparable hydrodynamics. Its beams, vertical rudder and horizontal rudder – which resembles a wing, sitting above the prop and extending about 35 cm either side of it – are therefore about 2 cm thick, far thinner than a conventional outboard and about 5-6 times more drag-efficient.
Once repackaged into the C-7’s architecture, the 400 V e-motor and inverter combination produces up to 55 kW. It consumes about 17-18 kW when the boat is moving from 5 to 20 knots, and its efficiency peaks at around 22 knots. By contrast, an equivalent traditional IC-hydraulic outboard would consume around 100 kW to produce the same net power output.
During operation, a pump in the motor-gearbox assembly draws seawater up through a hose-like channel to directly cool the motor and battery pack. When the C-7 isn’t moving, the thruster can be hoisted out of the water much like any outboard system. The hydraulic actuators serve to raise it at slower speeds in shallow waters – although this ‘shallow mode’ must be activated via the pilot’s interface – and to lower it during foiling.
As a result of foiling, the maximum the wake wash from the C-7 produces waves of between 7.5 and 10 cm in height during cruise, meaning minimal disruption to other boats in busy waters.
The battery pack used is a 40 kWh BMW i3 system, bought off the shelf and selected largely for its 8-year service guarantee and for being a widely used, well-proven battery using energy-dense lithium-ion NMC prismatic cells.
The popularity of the battery (styled by Torqeedo as the Deep Blue Battery) among maritime users comes in no small part from the various safety elements in its engineering. For example, if excess pressure should accumulate in its cells, a pressure valve disc opens to release any build-up of gases, minimising the chances of explosions or water ingress in the IP67-rated pack.
Also, its BMS is rated to the ASIL-C automotive safety standard, which Torqeedo cites as being a more rigorous level of safety compliance than is typical in boating, and a compressor is integrated to enable uniform air-based cooling throughout the pack without needing the weight of a liquid-cooling circuit.
Internally, the pack’s cells have laser-welded cell connections for consistency and reduced complexity in their manufacture. It is charged at a maximum rate of 9.9 kW, with charging managed by the standard-issue BMW i3 BMS, although future Candela boats will have fast DC charging.
When the foil is retracted and the C-7 is operating in normal displacement mode, the battery also helps by acting as ballast, its 350 kg of weight keeping the centre of balance in the approximate dead centre of the boat. Therefore, if the user chooses to drive slowly through heavy waves or to allow seven or eight people on board, the boat’s weight distribution remains largely the same.
“Conventional, planing motorboats built for the open sea tend to be rather unstable at slow speeds if you load them unevenly, owing to their sharp vee-hulls. By contrast, the C-7 has a totally flat aft hull, since it relies on foils for seakeeping. So the whole crew – up to seven – can stand on the railing and it won’t heel over that much.
The flight controller
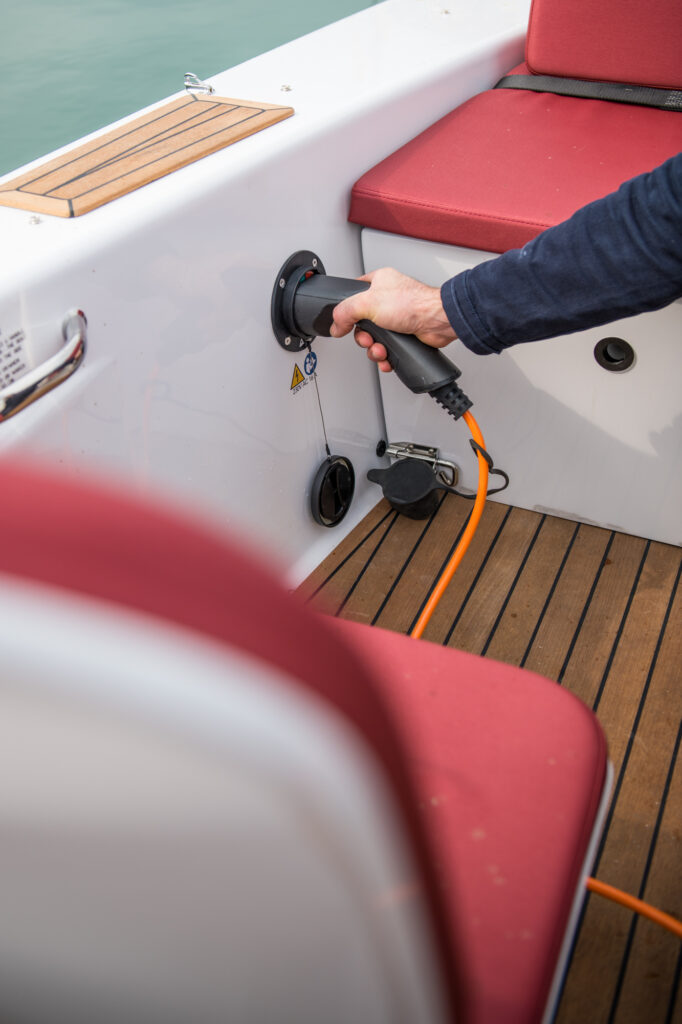
The control system by which the C-7 successfully foils and balances works in a similar principle to a self-driving car or quadcopter UAV. A series of motion reference sensors feed various data on position and attitude to a computer, which adjusts the vehicle’s actuators as needed to maintain balance.
This is no coincidence. Candela’s engineer Kristian Sloth Lauszus previously worked on UAV flight controllers before designing and building the control system for the C-7, and the dynamics of the latter are not wholly different from the former, especially given that above 16 knots the boat does indeed fly above the water. Small wonder then that the speedboat’s control system is referred to in-house as the “flight controller”.
The core part of the first stage of the control process – the sensor inputs – are acceleration readings from an accelerometer, along with measurements from a gyroscope, while speed and position are calculated using GPS.
“The accelerometer and gyro comprise our inertial measurement unit, which integrates with the GNSS receiver directly onto the board of the flight control computer,” says Lauszus.
Both the accelerometer and gyroscope are similar to those used in smartphones or UAVs, being low-cost, free of moving parts, and widely available. “Many of these types of sensors were originally designed for UAVs, which can rapidly flip in the air, and so they can measure changes in movement of up to 300°/s,” Lauszus explains.
He adds that the inertial estimates are calculated at a rate exceeding 100 Hz, ensuring more than enough actionable data inputs for the control loop, which sends commands to the foil actuators at 100 Hz.
“Speed readings from the GNSS are also important, because the lifting force generated by the foil is proportional to the square of the boat’s speed, so if you double the speed you get four times the force; hence the faster you move. It’s therefore critical that the control system has a good speed estimate to keep the boat stable.”
At the very front of the C-7 are two ultrasonic sensors, each measuring the distance between the hull and the water; two are installed for redundancy.
“The power used by the pilot and flight control systems is really low,” Lauszus says. “Of course, the main bus from the battery is 400 V, and that’s great for the motor, but a DC-DC converter steps that down to 12 V for the control system.
“So-called ‘take-off’ is handled by the flight controller. Initially, the angle of attack of the aft and front foil is set in such a way as to pitch up the boat in order to lift it out of the water. Once the correct altitude is reached, the pitch is normalised to balance the boat parallel to the water. The process is performed in reverse during ‘landing’, with the nose pitching up just before landing; similar to when an aircraft flares as it lands.”
State observer systems on the flight controller serve to verify the integrity of data, and the boat is programmed to land and operate in slow mode for safety purposes in case of any errors.
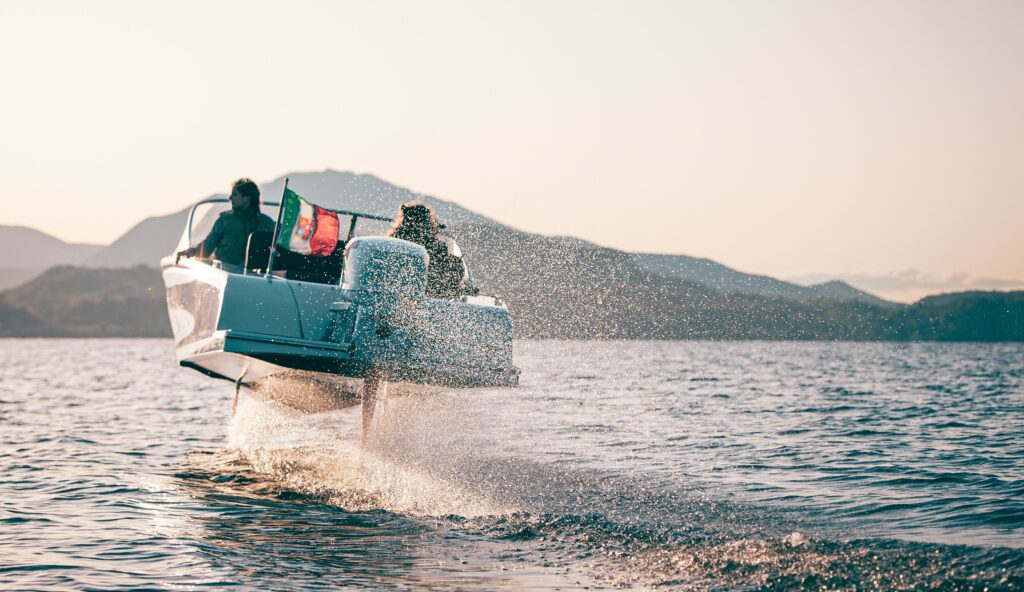
Hull materials and hydrodynamics
In the earliest design stages for the C-7’s hull, very little was defined – only that it had to fly, and would therefore need to be as light as possible. The first prototype was built in an aerospace carbon fibre factory, made entirely from the best composite material Candela could find.
Philippot says, “The only downside with a carbon fibre hull is in fact the expense of building it, to make the boat affordable for serial production. Carbon composite is around half the weight of fibreglass composite while being stronger and stiffer. Every gram added would mean we’d need a more powerful, heavy and expensive powertrain, which would risk reducing our range.”
Although carbon composite is pricier than fibreglass, Candela has striven to use thin carbon parts to reduce the overall bill of materials in the structure. Philippot points out that the labour cost of carbon fibre is a bigger concern than the material cost.
To optimise the value for money in the factory processes, vacuum infusion is used to embed the resins into the carbon fibres for the larger hull sections. The advantages of this process were also espoused by Green City Ferries: by enclosing the fibre and resin within airtight soft plastic bagging, and forcing the latter through the former at -1 bar, it ensures a uniform spread and density of resin.
This is used for the large hull and deck sections, while the struts and rudders (each being around 2 cm thick) were made using a different carbon composite and an undisclosed manufacturing process to ensure they could handle the loads and stresses coming from the waves, from turning, and from carrying the 1.3 t boat, as was the foil to ensure it could twist and deform as needed for turning the boat.
“We searched for a long time for suppliers who could produce the parts with the strengths we needed at a reasonable price, and we did a lot of testing to make sure those thin, lightweight parts could safely handle and transmit huge loads while maintaining the stability of the boat, to be certain we were choosing the right manufacturers,” Philippot notes.
The deck is also topped with teak for aesthetic reasons, and is manufactured with hatches for maintenance workers to access the battery pack, flight controller, and other parts. Beneath the deck is a network of aerospace-style ribs and spars, to maximise the structural strength of the boat while minimising weight.
“If you look inside an Airbus or Boeing aircraft structure, you have a rib, spar or string every 10 cm or so, and the outer skin is just 2 mm thick,” Philippot explains. “Their engineers know from impact tests that this arrangement works, and we know that having a similar system in our boat is key for minimising weight while maintaining safety.
“Most speedboats opt for a sandwich-type outer skin instead, but not only is that too heavy for the C-7, it also isn’t strong enough to help with distributing the loads that concentrate around the three ‘legs’ of the boat.”
To simulate the load distributions, CAD and FEA were used extensively to closely predict the behaviour of the carbon composite, although as mentioned, a lot of real-world tests were needed to get the foil to twist without breaking or being too pliable.
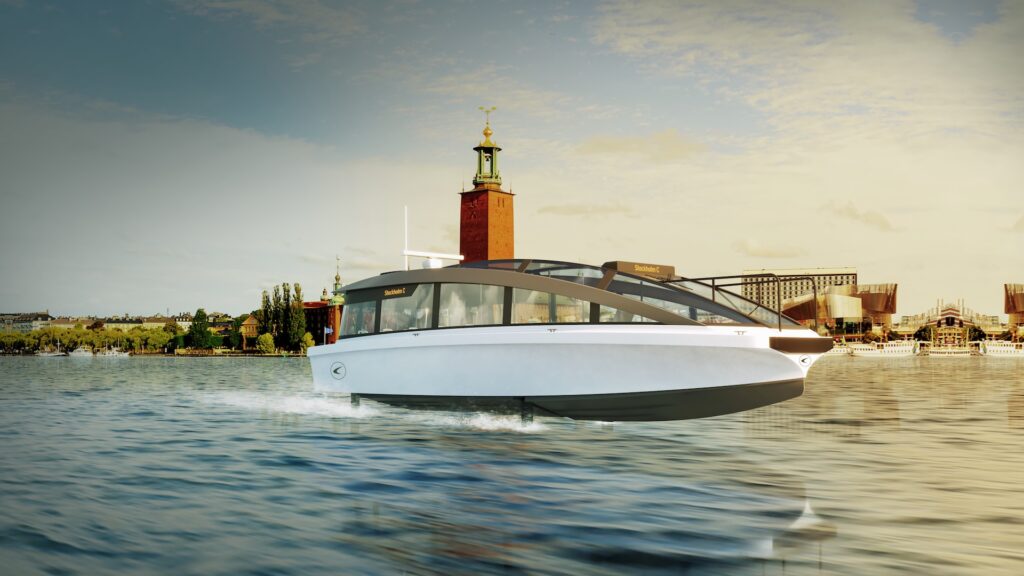
Future plans
The C-7 is now the best-selling premium electric boat in Europe, thanks in no small part to its foiling-based powertrain that offers its owners 95-97% lower operating costs compared with a traditional diesel- or gasoline-powered speedboat.
From a commercial perspective, such low operating costs and the greater profitability they could bring, naturally appeal to maritime fleet operators. To that end, in addition to expanding its productive output of C-7s, Candela is growing its portfolio to develop and produce larger boats for use as water taxis and commuter ferries – an immense market across not only northern Europe, but also the Gulf States, East Asia and realistically any coastal city with large waterways.
At the time of writing, the Candela P-12 water taxi had been officially launched, and will be delivered to its first customers soon. This 8.5 m-long vessel carries up to 12 passengers (hence its name) and consumes 1 kWh/nautical mile, which the company estimates as a twelfth of the energy consumption of standard IC-engined water taxis.
The Candela P-30 is still in development. Its dimensions are less clear – a 30-passenger initial version is the target – but the concept is scalable up to 300 passengers. In addition to a top speed of 30 knots and a cruise of 20-plus knots, with minimal wake disturbances for other ships and 95% less g-force disturbance for customers, Candela sees this boat being a game-changer for waterborne commuting and urban transport in general.
“Waterways these days are mostly seen as obstacles that have to be overcome: you build a bridge over them, or a tunnel under them,” Mahlberg says. “What if we could use them for low-cost, high-speed electric transport instead? In many cities, waterways offer excellent cross-traffic connections but are mostly unused.”
Data gathered on these new vessels and the new electric components they use can be expected to inform the engineering on future versions of the C-7 and other vessels that Candela is likely to build.
Hydrofoiling
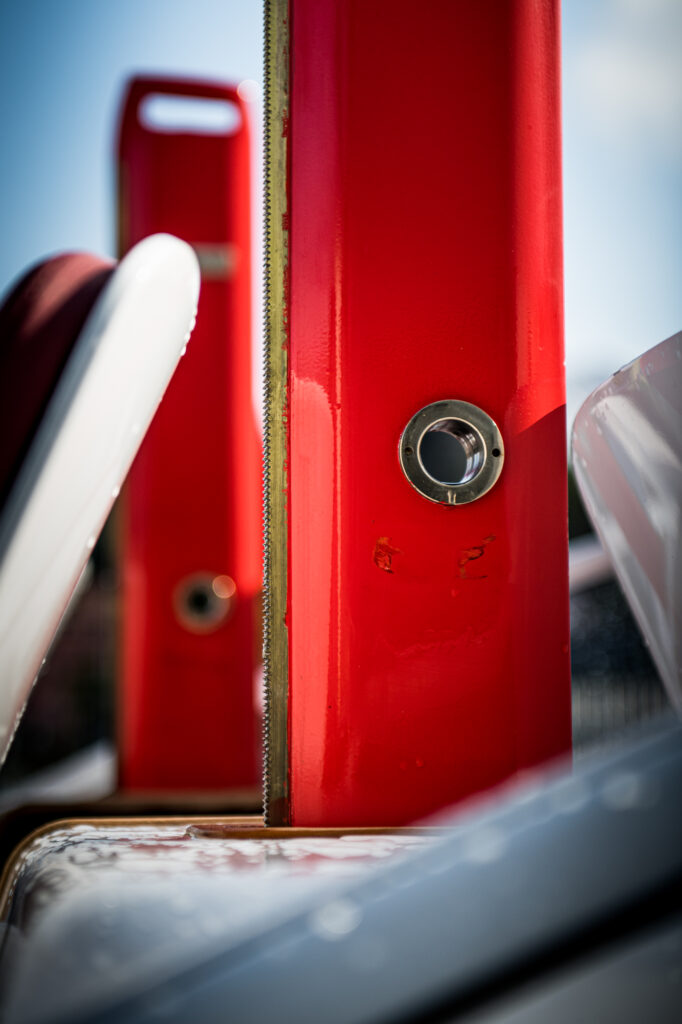
A hydrofoil is a system or shape that works below the waves much as an aerofoil does in air. It is akin to a wing, generating lift when it moves through water; a vessel designed to use a hydrofoil can also be referred to as a hydrofoil, or simply as a ‘hydrofoiling boat’.
Hydrofoils were first patented in the late 1800s, with prototype designs developed and tested starting around the beginning of the 20th century.
There are broadly two types of hydrofoil. One is the surface-piercing hydrofoil, which has a vee-like shape (part of which protrudes above the surface of the water during foiling) and acts rather like water skis to produce lift. It has been used successfully for many years, for example in the Voskhod-type river ferries manufactured first in the former Soviet Union and now in Ukraine.
The other is the fully submerged hydrofoil, which as its name suggests keeps its entire foil beneath the water. Comparatively fewer of these have been made, but those that have often take an inverted-T shape, with beams extending vertically down from the hull to mount two separate – or one collective – flat horizontal hydrofoil surfaces.
Surface-piercing hydrofoils have to contend with the shapes and forces of waves, so boats that use them move with less stability and energy efficiency compared with those using fully submerged hydrofoils. However, the latter are not self-stabilising, unlike surface-piercing hydrofoils, and therefore need an accurate control system capable of constantly adjusting and rebalancing their vessels. That has made the design and scale production of such systems far more challenging.
The C-Pod
As well as developing the C-7 and additional, larger vessels for public transport applications, Candela has unveiled a new electric pod thruster, the C-Pod, which will be used on its new water taxis, ferries and other future vessels. At the time of writing, the C-Pod was intended solely for use on Candela’s future craft.
Pod thrusters such as the C-Pod are inherently more efficient than outboards, as they have no gears or transmission shaft. By directly driving the propeller, they require no oil and greatly reduce parasitic losses.
They will be mounted in line on Candela’s upcoming P-12 water taxi and P-30 ferry – one drive on the former and two on the latter, sitting and operating beneath the water without emitting any noise noticeable to passengers or people on the shore, and without needing gear boxes or z-drive azimuth thrusters.
Each C-Pod is built around two permanent magnet synchronous motors that together produce a cumulative 60 kW at peak. This will enable the P-12 to cruise at 20 knots over a range of 45 nautical miles, and the P-30 to cruise at the same speed over 60 nautical miles.
Candela’s communications manager Mikael Mahlberg says, “As the first obstacle encountered by any new, small e-motor design is heat losses, the packaging of the C-Pod has been designed to get the flow of seawater as close to the stator as possible.”
At time of writing, the size of the C-Pod had not been publicly released, but Mahlberg estimates that its output (enabled through its high heat tolerance) gives its motor a power-to-volume ratio several times that of the best COTS motor.
As output power is a function of speed and torque, and torque is limited by the size of the motor, the C-Pod’s engineers needed a way of increasing the system’s power without encroaching on the limitations that propeller tip speeds encounter in water. At around 45 m/s, the pressure in the water flow around each prop tip drops to the point of cavitation, leading to inefficiencies and potential damage.
To avoid that, two counter-rotating props are used to push overall propeller efficiency to more than 80%. “That gives the C-Pod several times the power density compared with the best available COTS pod thrusters,” Mahlberg adds.
Specifications
C-7 Hydrofoiling speedboat
Battery-electric powertrain
Hull: carbon composite
Power source: 400 V lithium-NMC battery, 40 kWh
Dimensions: 7.7 x 2.4 m
Maximum draft: 1.5 m
Weight: 1300 kg
Maximum speed: 30 knots
Cruising speed: 22 knots
Maximum power: 55 kW
Maximum range between charges: 50 nautical miles at 22 knots; 8 nautical miles at 5 knots in ‘limp-home mode’
Maximum wave handling: 1.2 m
ONLINE PARTNERS
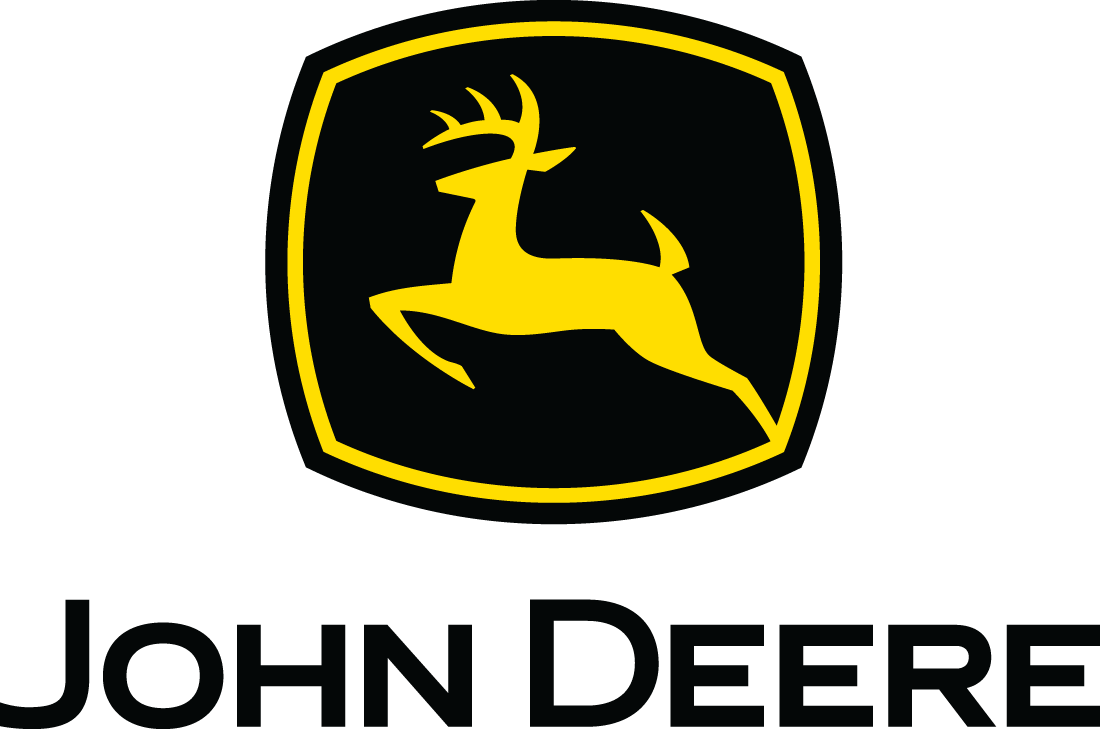
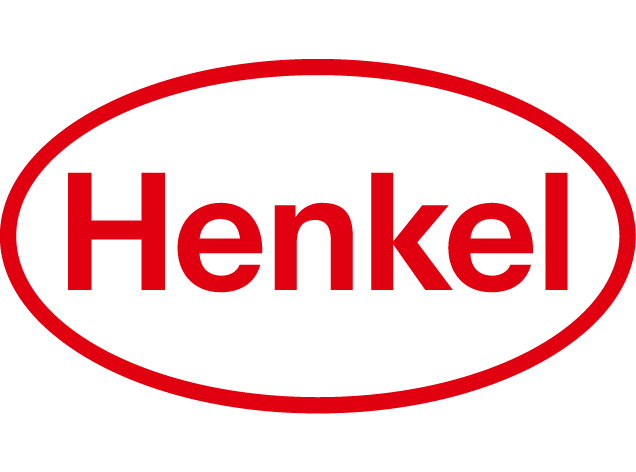
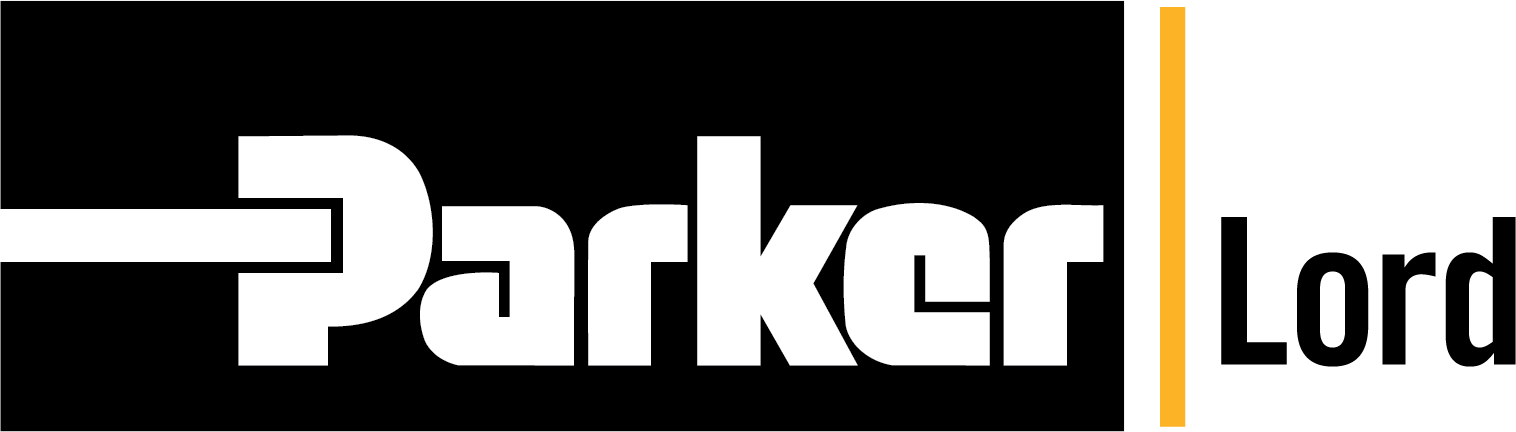
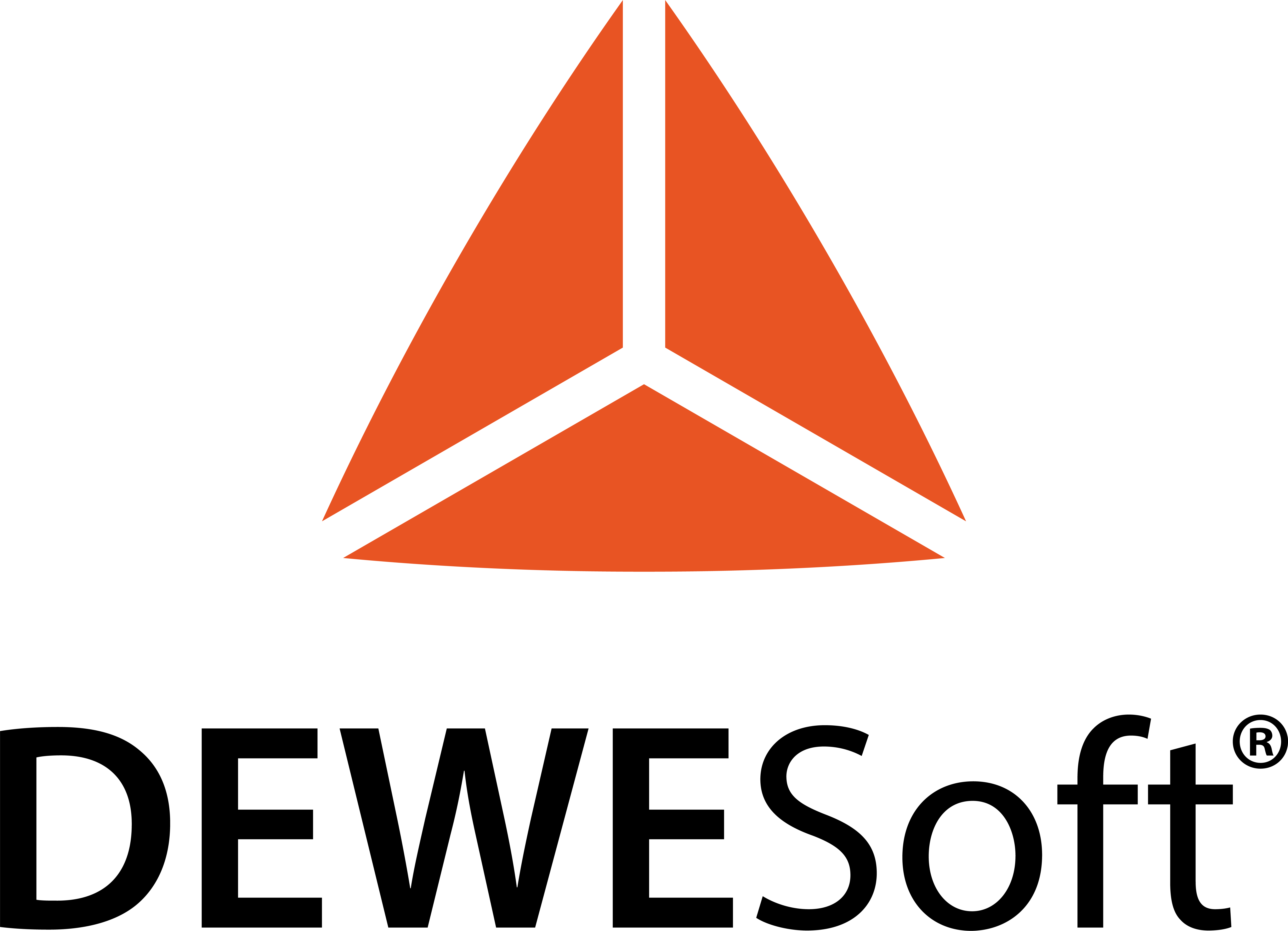
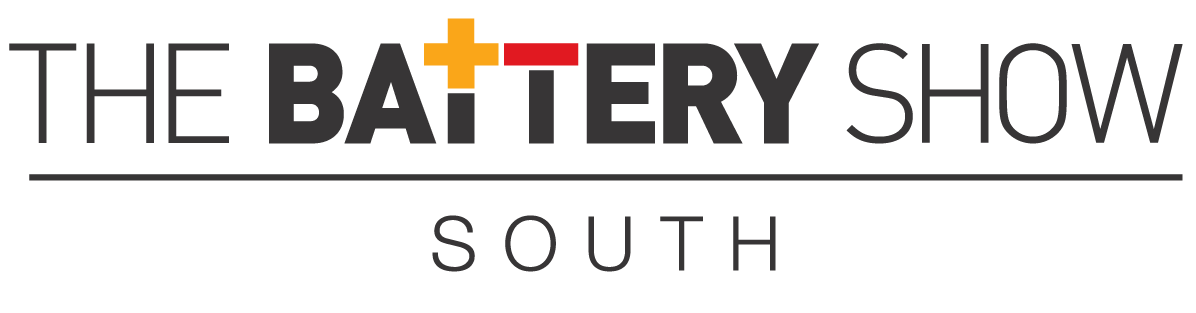
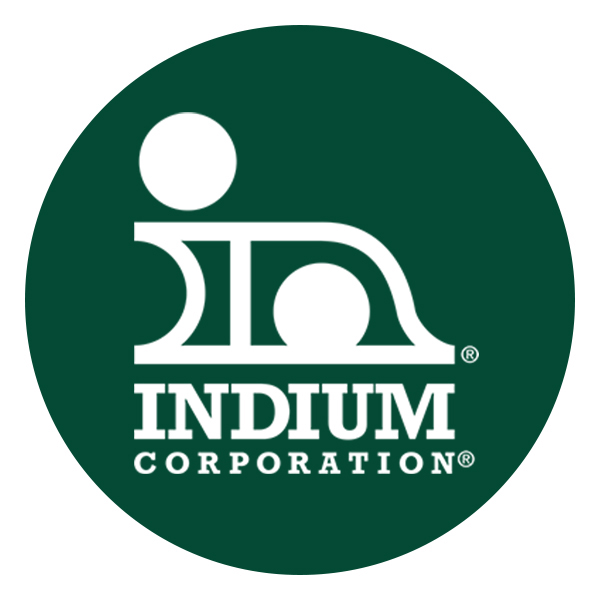
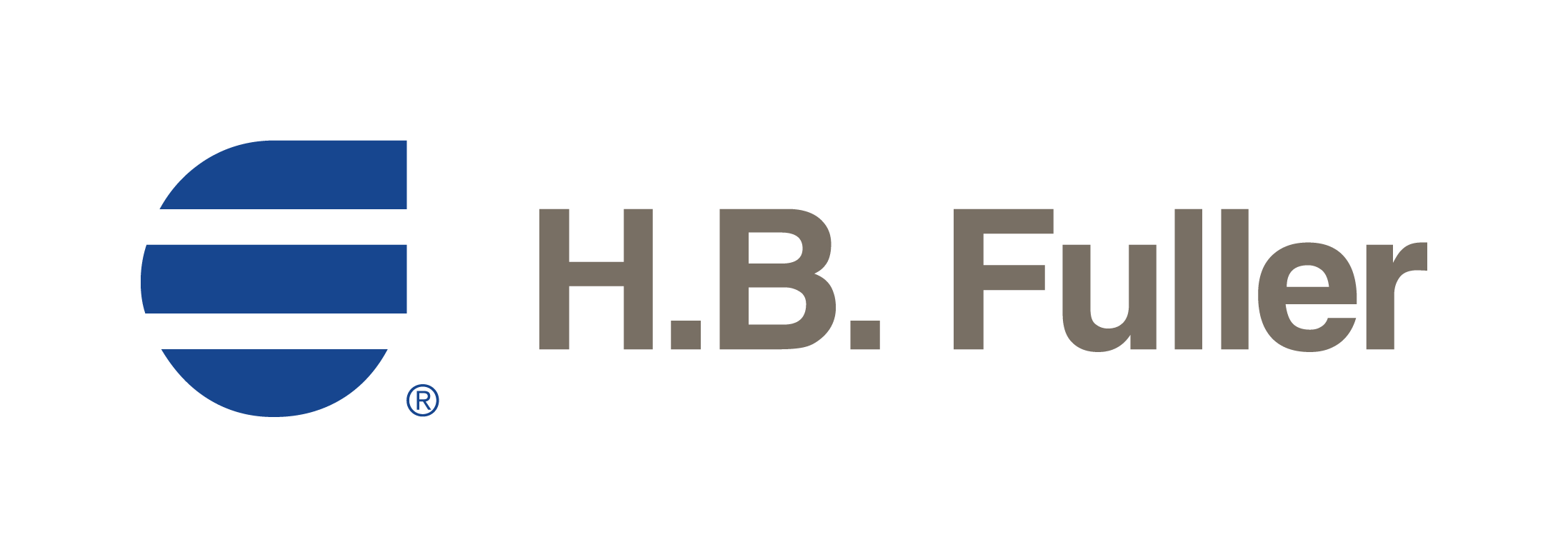