How Camfil cleans up the battery production process
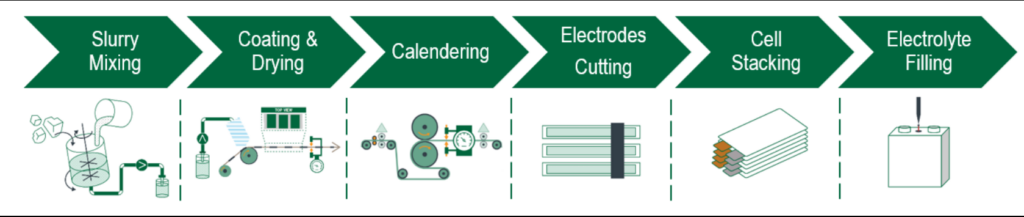
(Images courtesy of Camfil)
Battery anodes and cathodes are typically made from slurries of active chemical powders and supporting substances such as binders and solvents applied to foil substrates, before being dried, cut and combined into ‘jelly rolls’ or laminates to form the core components of cells (writes Peter Donaldson).
The process inevitably generates dust and vapours that are variously toxic, explosive or polluting. Along with other contaminants, they can also degrade battery safety, performance, reliability and cycle life.
When laying out and equipping gigafactories, it is essential to understand the production process and the emissions it generates. This is so that solutions for heating, ventilation and air conditioning, dust extraction and molecular filtration can be tailored to the facilities to optimise efficiency and minimise the total cost of operation, argues Gabriele Schenetti, EMEA sales director for the Air Pollution Control business area of filtration specialist Camfil.
One of the key decisions that has to be made early on is where to put the extraction and filtration equipment. Schenetti explains that location is always a compromise because it is rarely practical to put the dust collector next to the process that is usually the source of the dust and vapour.
“Capturing close to the source is beneficial to the negative pressure we need in the piping, as the pressure decay over the extraction and the transport line will be less,” he says. “Typically, the source of dust is inside the clean room, so it’s not easy to place a dust collector near the source.”
A key constraint, he explains, is that the dust in a battery production plant is potentially explosive, so the dust collector has to be equipped safety measures. (Camfil’s solutions for dealing with explosive dusts will be covered in a subsequent story soon.)
Because dust particles and vapour molecules are of different sizes, they require different filtration technologies to remove them from the air. However, the two can be combined in stages, with dust filtration followed by molecular filtration, Schenetti says.
Typically, Camfil’s dust filters are made either from a blend of cellulose and polyester impregnated with carbon, or polyester. Vapours are removed from the air by molecular filters usually based on activated carbon.
Clean air to a defined standard is important both for the production process, especially as process air is recirculated to save energy, and for protecting the wider environment. For the battery manufacturing process, that standard is normally specified by the battery maker and the consulting engineers tasked with designing the factory, while governments set the environmental standards.
Confirming that those standards are being met relies on measuring the numbers of particles in a given volume of air. The challenge here is that the emitted particles are not uniformly distributed around a workspace, Schenetti notes.
However, Camfil guarantees the performance of its filters in terms of parts per million of dust in filtered air, and has software that estimates initial filtration efficiency and the lifetime of the molecular filtration solutions. “We can give you the exact percentage it is expected to return,” Schenetti says.
An extraction and filtration system must not only remove dust and vapours from the air efficiently, it must also be efficient with the energy and other consumables it uses.
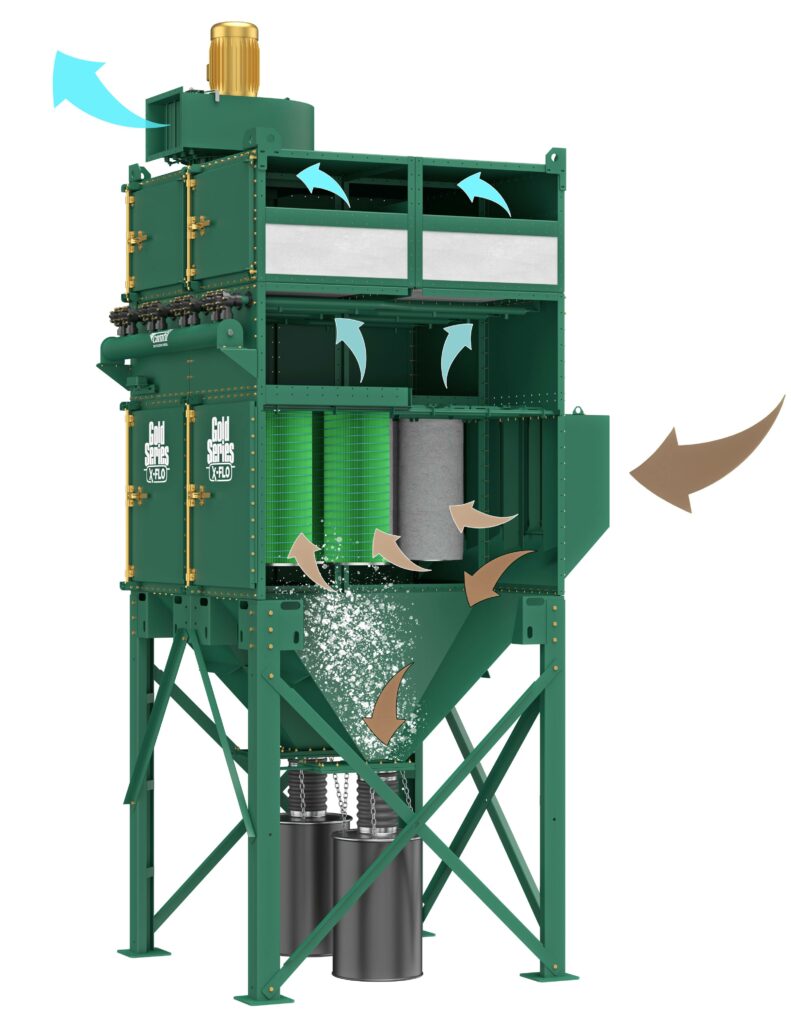
“One of the main concerns is to recirculate as much air as possible,” he says. “The air we extract from the process is usually dry, and to generate that you need to spend money, so you want to reuse as much of the air as you can and do it in the safest and most efficient way.”
Running extraction fans incurs energy costs, as does providing compressed air to clean filters, and then there is the cost of consumables such as the filter elements themselves. Camfil’s product range includes static filters that are replaced rather than cleaned, and dust collectors that include cleanable filters.
“We can advise on the proper mix, depending on the dust load to be extracted, to optimise the total cost of ownership of the air filtration system,” Schenetti says.
While static filters are relatively inexpensive, they have shorter service lives when dust loads are higher, so cleanable filters provide a lower total cost of ownership in these circumstances. However, the optimal system might be one that combines the two, he explains.
“The cleanable filter is only the first stage; there will always be a second or even a third stage, to ensure that the quality of the recirculated air is good enough to meet the requirements,” he says. “With the first, cleanable filter, we collect the highest dust load so that the filters in the later stages have longer lives.”
The cleaning systems are automatic, measuring the pressures where dirty air enters the filter and where clean air leaves it, triggering the cleaning process when the difference between them reaches a preset value. Compressed air blows the dust out of the filter, and the dust falls into a hopper that is emptied into a bin, where the dust is sealed inside.
To ensure worker safety as well, a ‘bag-in bag-out’ system is often used for filter changes and dust disposal, so that the operator can replace the old filters and empty bins without coming into contact with the dust.
Schenetti regards extraction and filtration technologies as mature, but believes that a deeper understanding of specific applications will enable further optimisation. This, he says, requires close monitoring of the evolution in battery chemistries and the manufacturing processes and machinery.
“When the processes and machines change, we need to be involved to be able to design the extraction and filtration systems for our customers,” he says. “We are happy to do that and assist battery makers from the outset.”
Click here to read the latest issue of E-Mobility Engineering.
ONLINE PARTNERS
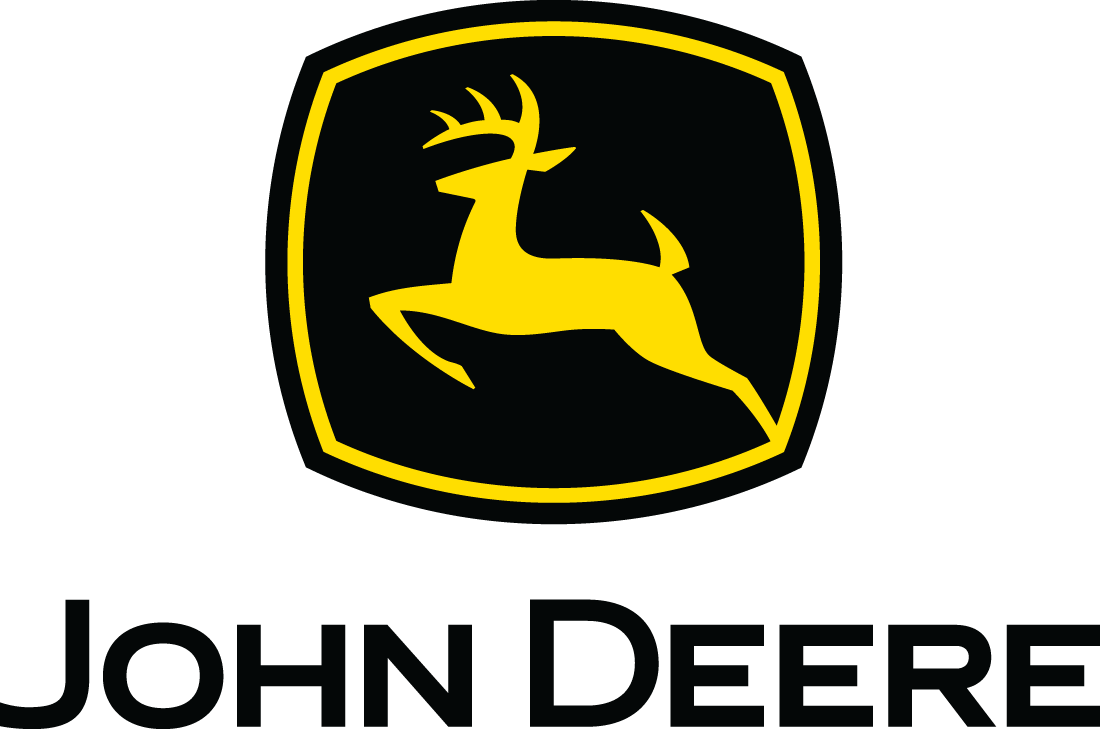
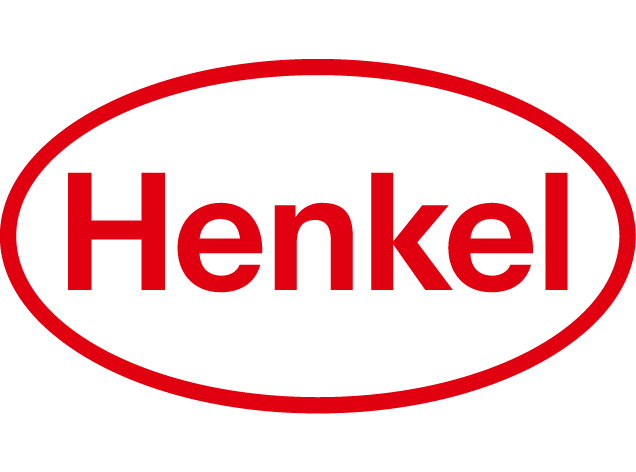
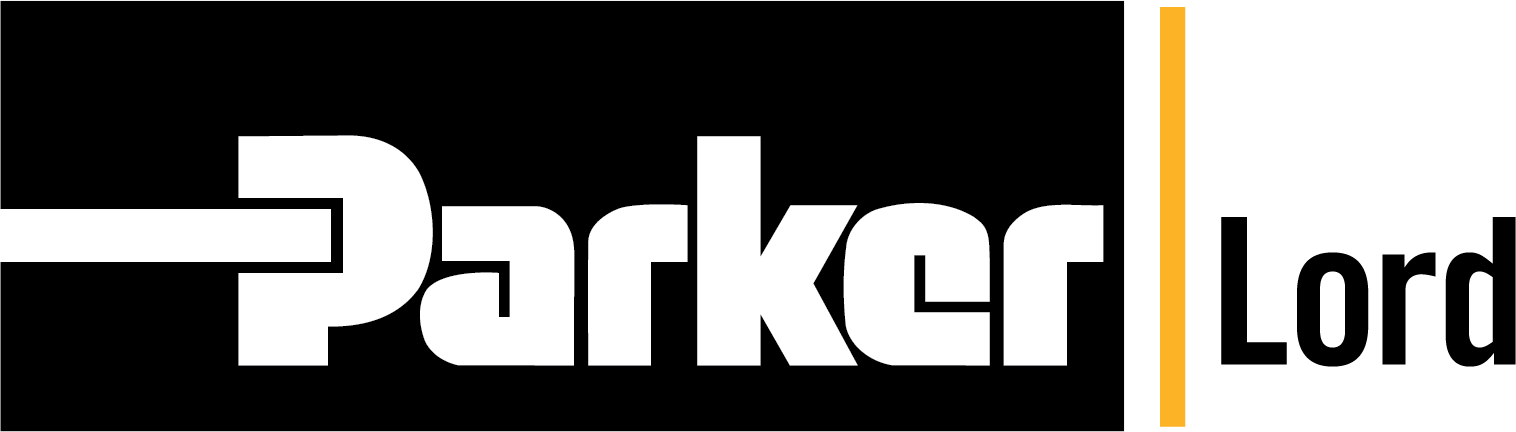
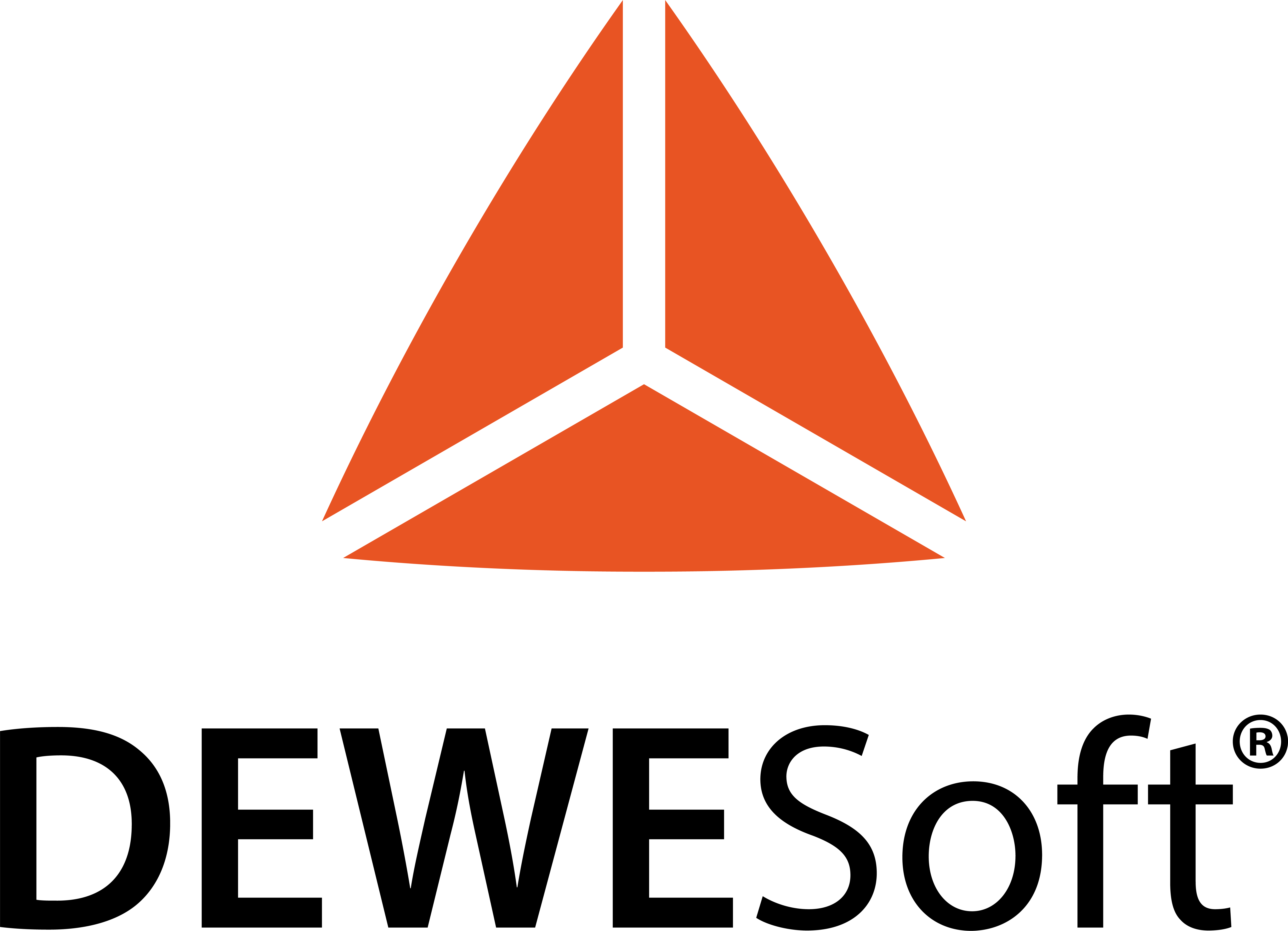
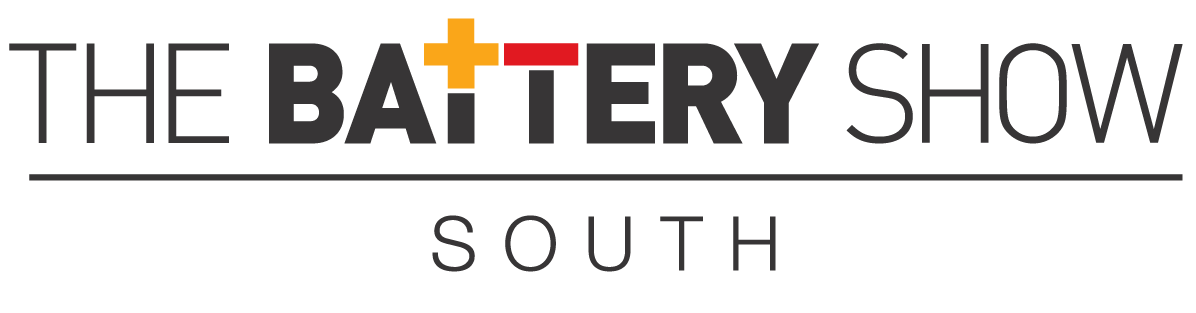
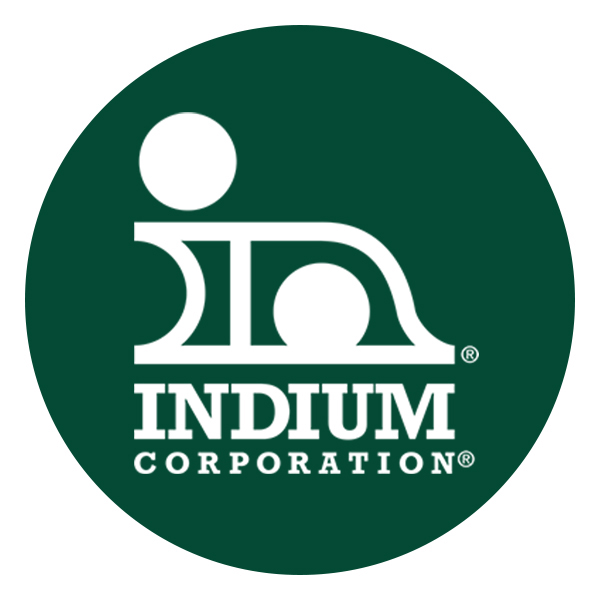
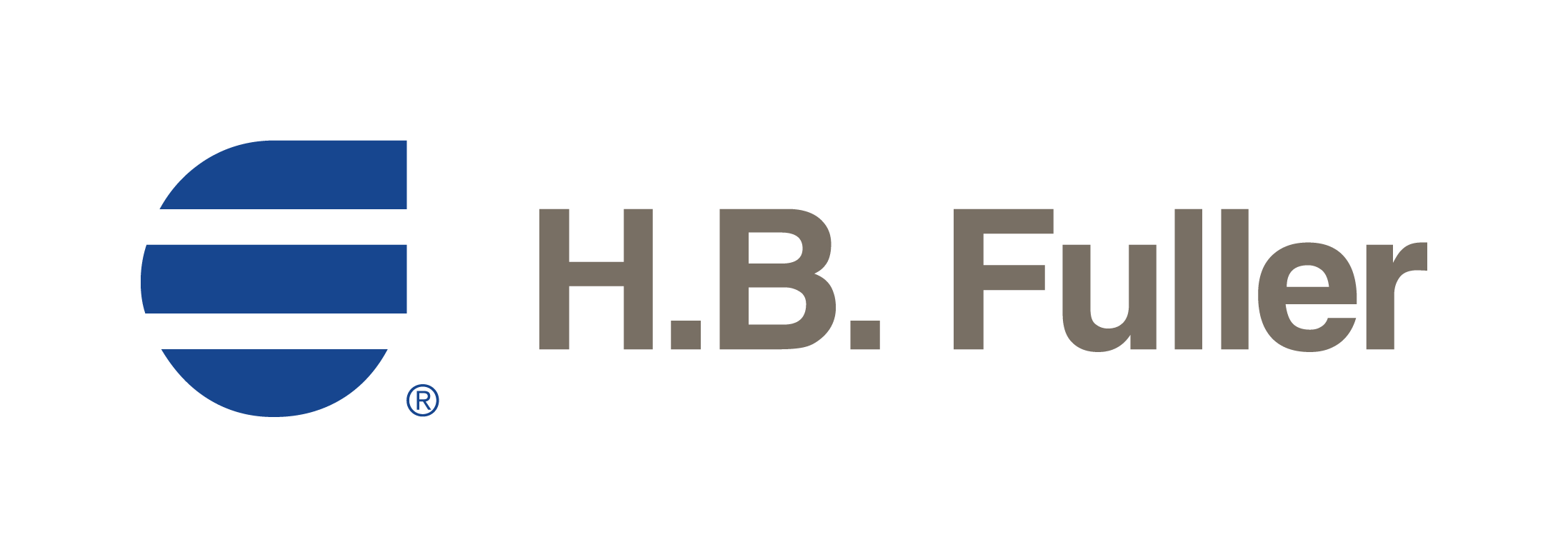