Dust busters
Risk management requires using dust collectors and isolation equipment certified for the materials, says Camfil’s Gabriele Schenetti
Dust explosions are a major hazard in many industries, and there are about 2,000 occurrences in factories and refineries across Europe per year. Battery electrode manufacturing is exposed to this type of risk and must take precautions that comply with explosive atmosphere (ATEX) directives. This means facilities must be designed to reduce the risk of dust explosions and mitigate them if they happen, Gabriele Schenetti, EMEA sales director for the Air Pollution Control business area of filtration specialist Camfil, explains to Peter Donaldson.
Many kinds of dust can explode, from foodstuffs such as flour, baking powder, sugar and tea to dusts created by the processing of plastics, powder paints and detergent, to dusts created by the cutting and machining of metals, such as aluminium, titanium, magnesium, chromium and even iron.
In lithium-ion battery anode manufacture, for example, the slurry mixing, coating and drying, calendering (compression and consolidation) and cutting processes all release such delights as lithium nickel manganese cobalt oxide dust, which explodes as readily as the more innocuous substances listed above.
Dust explosions have a particular anatomy and progression. When a combustible material is dispersed as fine dust, the surface area exposed to the air is thousands of times larger than it would be as a solid mass. Such a huge contact area means that when ignited, the dust will burn very rapidly and release big amounts of energy in a short time, resulting in large and rapid increases in temperature and pressure that create shockwaves – and there are many potential sources of ignition in industrial settings. This primary explosion can trigger secondary explosions in other areas as the pressure waves travel through pipes, culverts and corridors, and these can be larger than the primary ones.
Prevention and mitigation
Besides essentials such as knowing the specific explosion risks of the dust in question and minimising potential sources of ignition, risk management requires using dust collectors and isolation equipment certified for these materials, as well as ensuring personnel are well trained and have a thorough understanding of ATEX regulations, Schenetti says.
In an electrode-manufacturing facility, the most likely site of a dust explosion is the dust collector itself, so it needs integrated prevention and mitigation measures, he explains. These can include a system that exhausts the pressure wave to the outside, so the dust collector should ideally be placed close to a location where it is possible to vent the pressure wave.
“When outdoor venting is not possible, flameless venting can be used for indoor pressure release. Alternatively, chemical explosion suppressants that interfere with the combustion process injecting inert, dry chemical powders can be an option,” Schenetti says. “Venting is used in combination with additional equipment such as fast-acting mechanical isolation valves or, again, chemical explosion suppressants to avoid explosion propagation back into the process.”
Flame barriers
The downstream air coming out of dust collectors and being recirculated also requires protection, so Camfil offers them with integrated HEPA filters, which act as flame barriers.
As new battery chemistries emerge, explosion protection will need to adapt, Schenetti concludes.
“New chemistries and better technology will change the manufacturing machinery, and factors such as the explosive properties of the dust to be handled, dust loads and airflows can all change, and will have an impact on the filtration systems.”
Click here to read the latest issue of E-Mobility Engineering.
ONLINE PARTNERS
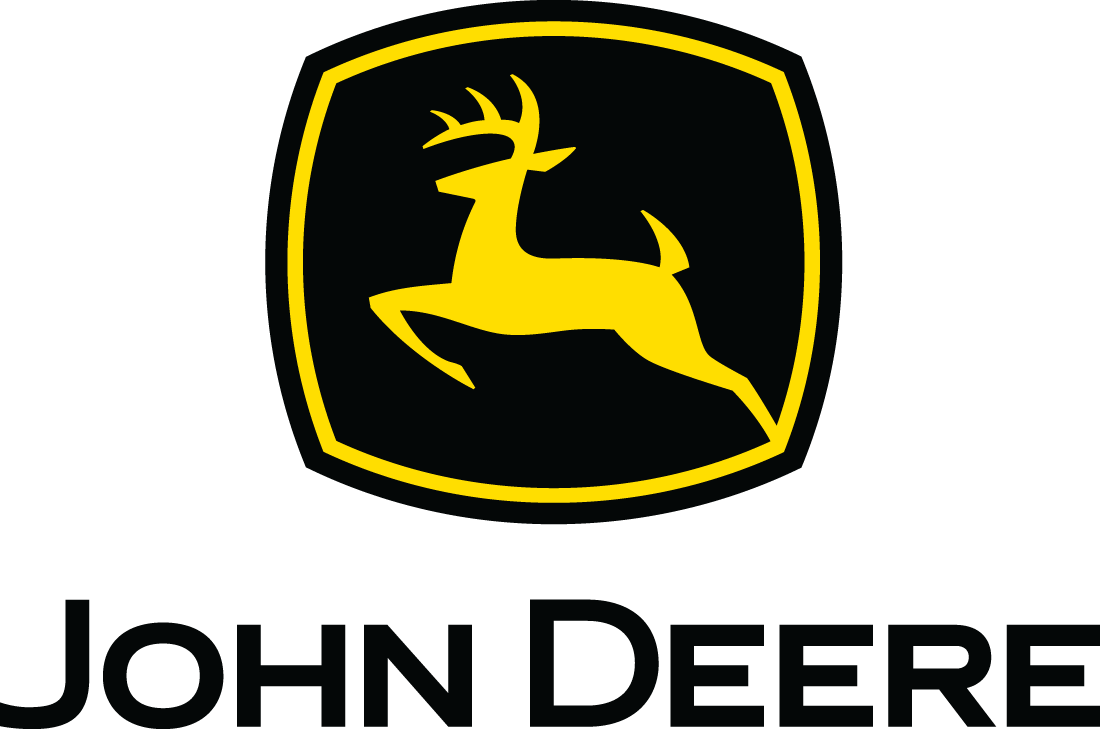
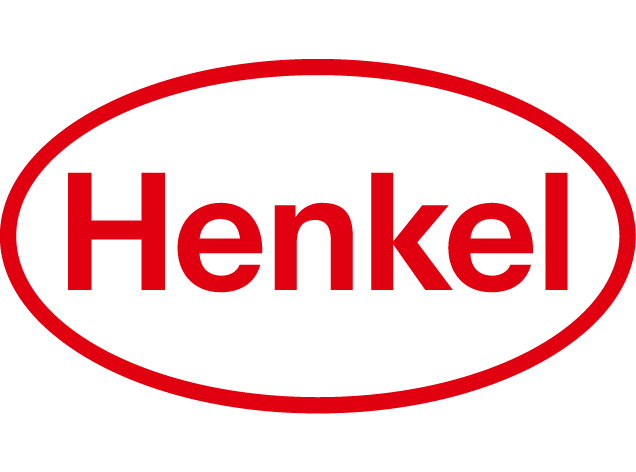
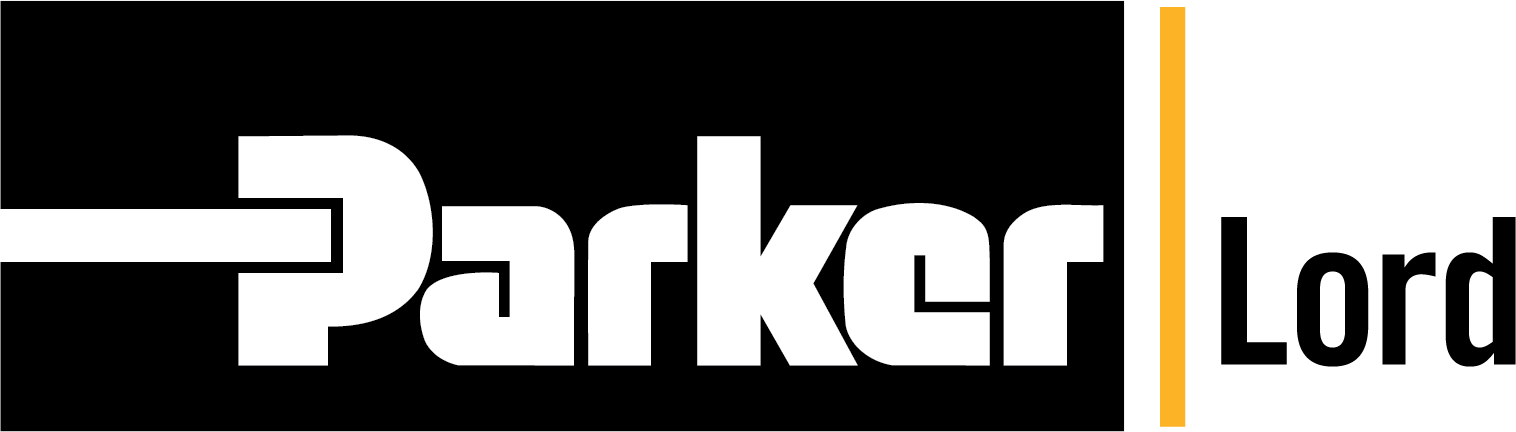
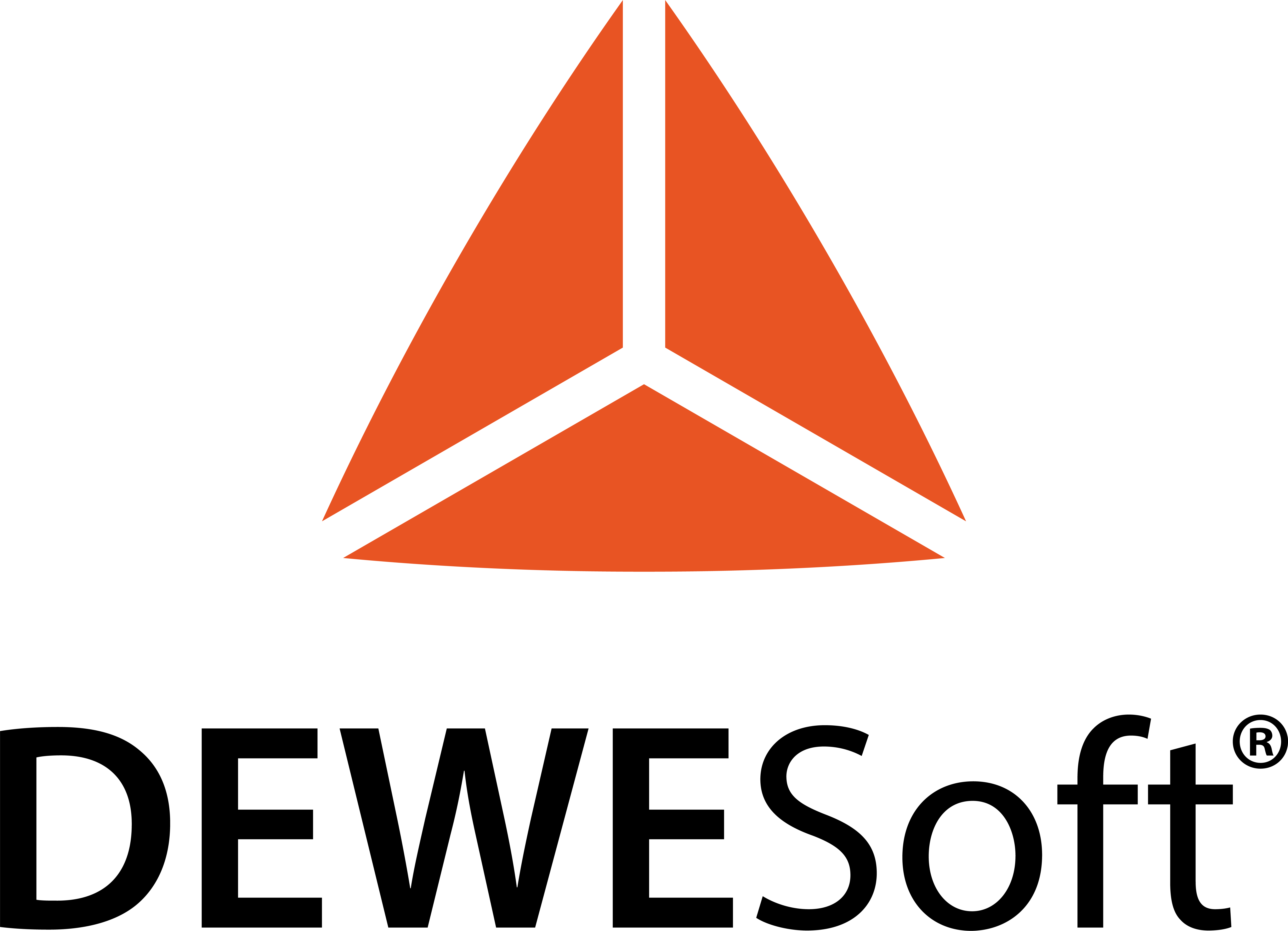
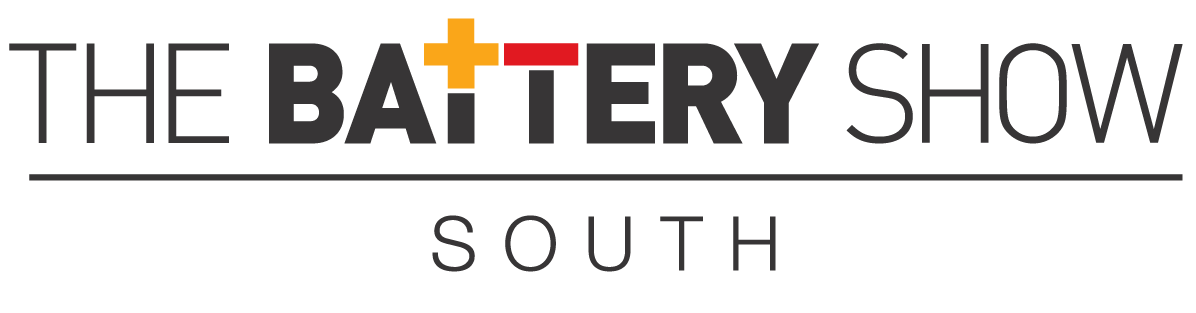
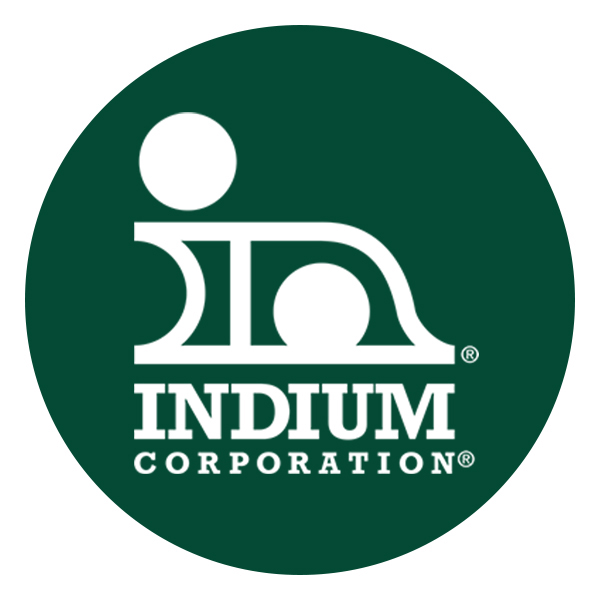
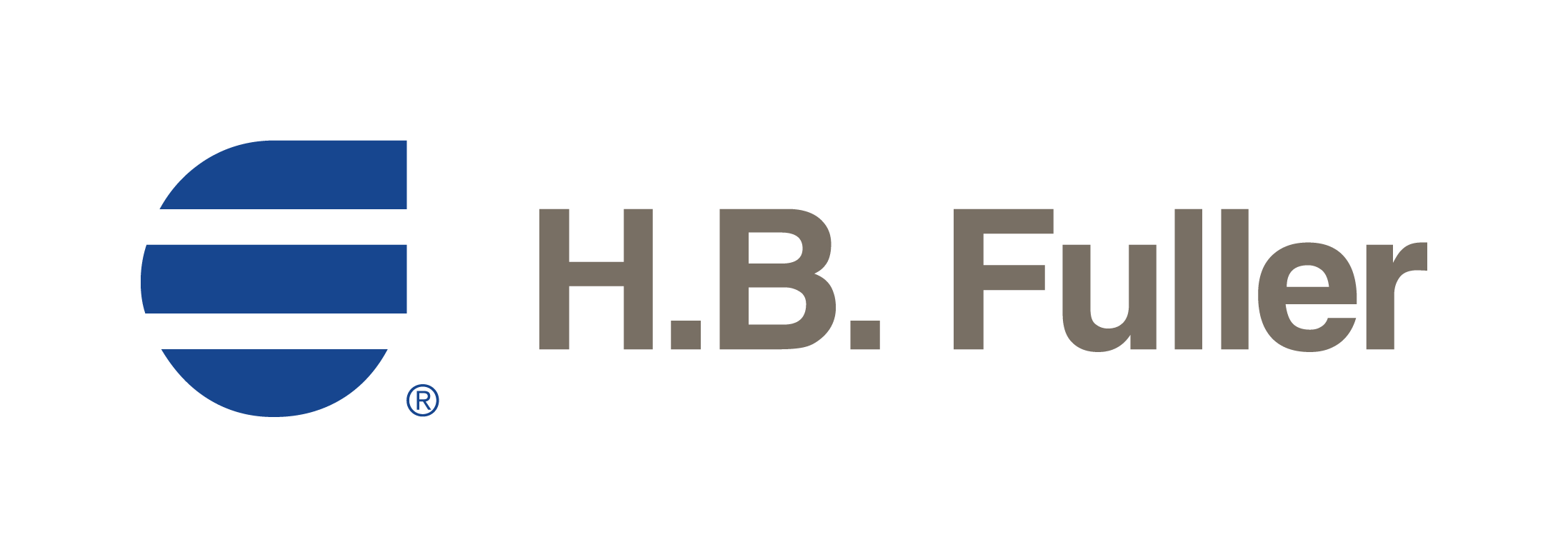