Cake Kalk OR

(Images courtesy of Cake)
Keeping it clean
Rory Jackson charts the development of this e-bike, whose entire manufacturing process is geared towards producing zero emissions
Supporters of e-mobility as a means of reducing carbon emissions and mitigating climate change ned to remind themselves that battery-electric vehicles are only zero-emissions machinery at the point of use. The extraction, refinement, fabrication and assembly of essentially all parts throughout an EV can still produce enormous quantities of harmful emissions, and exactly how much CO2 or other gases are emitted per process or component remains a mystery to the overwhelming majority of EV companies.
Swedish two-wheeler manufacturer Cake is attracting attention for taking a lead against that, by aiming to produce the world’s first electric bike to produce zero emissions from its material extraction ‘from cradle to gate’ – that is, from the moment it starts being produced to the moment it exits the factory – a project it calls The Cleanest Dirt Bike Ever.
Although Cake already designs and manufactures numerous models of EV, the focal point and test subject for this truly zero-emissions ambition is the Kalk, a battery-electric dirt bike that comes in off-road as well as street-legal variants. For the most part, this article will focus on the off-road version, the Kalk OR.
The bike has a top speed of 90 kph and a peak torque of 280 Nm at the wheel, with power coming from a centrally mounted motor via a chain transmission with a 12:80 reduction. Its lithium-ion battery carries 2.6 kWh (or 50 Ah) of energy, discharges at a nominal voltage of 51.8 V DC up to a peak of 58.5 V, and sits within a frame made almost entirely from aluminium.
Inside the frame is the battery pack, inverter, motor and controller. Ahead of those are the handlebars, rider display, forward lights and an upside-down air fork suspension, specially designed for Cake by Ohlins, with 38 mm stanchion tubes, three-stage air springs and 204 mm of travel. On top of the frame is the vinyl seat, and behind the frame is a swing-arm that is attached to the rear wheel, with a 205 mm Ohlins TTX22 Shock integrating internal parts and springs from Cake.
Although the lifespan of the Kalk is still being defined in hours, kilometres and battery cycles, the company points to Sinje Gottwald, motorcycle adventurer and Cake B2B account manager who recently completed a 124-day, 13,000 km journey on a Kalk bike, as evidence of its real-world capabilities. Notably, it was a solo, unassisted journey from Spain to South Africa, and showed that the bike could survive travelling through some of the world’s hottest and dustiest environments.
Electrifying an off-road dirt bike represents a challenge from an environmental and shock-proofing perspective, but it makes sense for more reasons than just reducing emissions. “For instance, dirt bike applications such as motocross or wilderness exploration require a lot of torque and acceleration, and electric motors naturally have sharp torque and acceleration from stationary, along with almost instantaneous power delivery compared with two and four-stroke engines,” explains Avinash Kumar, Cake’s specialist for LCA (life cycle assessment) standardised according to ISO 14040: 2006 and ISO 14044: 2006.
“On top of that, the greater efficiency of electric powertrains versus IC-engined powertrains means you get more power to the wheel with fewer losses, and the much reduced noise compared to the typically very noisy conventional dirt bikes means less disturbance to other wilderness trekkers, less noise pollution in nature, and our street-legal models don’t bother people in towns and cities.
“It is a challenging balance to strike, however, since a bigger motor gets you more power but also more bulk and weight in the frame; it’s a similar trade-off for battery energy. Overall though, our team has worked to reach a sweet spot that balances the different performance and physical goals that are key to the riding experience, while also making our job of carbon reduction achievable.”
Central to this balance has been a focus on lightweight construction in order to meet the bike’s performance targets, as well as using as small a number of battery cells as achievable to lighten the bike even more.
Company history
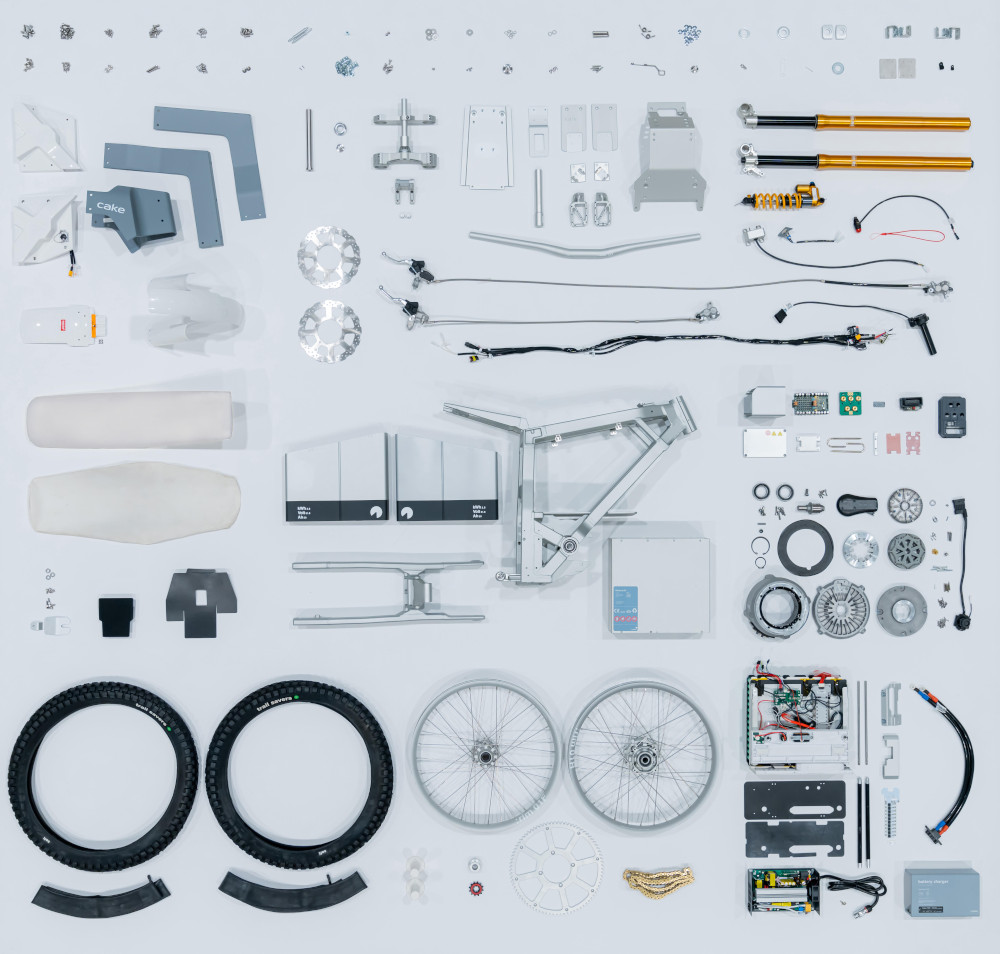
After Cake’s founding in 2016 by CEO Stefan Ytterborn and his sons, the first commercial delivery of 50 hand-made Kalk bikes followed in summer 2018, with series production of the Kalk starting in late spring 2019. Although the development period was short, considerable r&d was fitted into this time, and more has followed during the company’s continual efforts to fine-tune their vehicle models.
“Most of our componentry was engineered, designed and tooled from scratch, the only standard parts being foot pegs, brake levers, rubber handles and the rear shock,” says Ytterborn. “Even the tyres were specifically developed to minimise the physical footprint while riding trails.”
“It might sound a bit of a cliche, like a corporate mantra, but we really do nurture our three big goals equally seriously in the course of our engineering: that’s the industrial-looking design aesthetic, the performance of the dirt bike mechanically and electrically, and the sustainability of it and all its parts and development processes from conception to recycling,” explains Krister Thour, CTO of Cake.
Much of the pre-production research from 2015 to 2017 consisted of test-riding existing and commercially available dirt bikes and motorbikes to identify what qualities (if any) were desirable in each one, in order to cherry-pick the positive aspects of the aesthetics and performance that would be targeted later in the Kalk’s development.
Some experiences during this time heavily influenced Cake to start with a blank sheet for the first concept designs of the Kalk. Ytterborn and his collaborators were for instance strongly motivated not to follow in the path of companies that had electrified existing IC-engined motorbike chassis, as they’d found such EVs to be grievously sub-optimal in many ways. These included poor use of internal space for subsystems, incorrect centres of gravity and weight distributions, and vibrations and resonances of mechanical and electrical components.
“Even some well-known motorcycle OEMs had gone down the electric conversion route, and Ytterborn found a great many respected reviewers across social media echoing his concerns that electrified IC-engined bikes just felt weird, uncomfortable and wrong, so we started with two wheels and two handlebars, but everything in between had to be reinvented at some level,” Thour says.
Building the first prototype took less than 6 months, thanks partly to the EV’s small size, but more so towards the clear agreements that the team reached over the design, materials choices, assembly processes and all other factors of production before beginning to lay out components in the workshop. There were therefore no unanswered questions that could hinder the dirt bike’s assembly, or cause misuse of what was then still very little funding and a company of fewer than 10 people.
When it came to specifying the electric drivetrain during the course of product development, there was very little in terms of pre-existing industry standards for Cake’s engineers to draw on, even in verifying the durability and ruggedness of parts against the conditions the bike would have to endure.
“There were some UN directives for transport, and a little on shock testing, but that didn’t really go any further than rudimentary safety guidelines,” Thour notes. “So a huge amount of trial and error was needed to test, iterate and validate our design.
“For instance, we have a docking connector at the bottom of the battery, so you push the battery down from above and it connects to the drivetrain. In order to find the correct connector, and make sure we got the guiding pins and required contact pressure exactly right for the dirt bike to work consistently in customers’ hands, we had to do so many physical acts of testing the bike and its parts.”
Beyond workshop and bench tests, many hours were spent at motocross tracks, on streets viable for testing, and on dynamometers belonging to local motocross garages, to validate and tune them in ideal settings, sub-optimal settings and industry-standard conditions respectively.
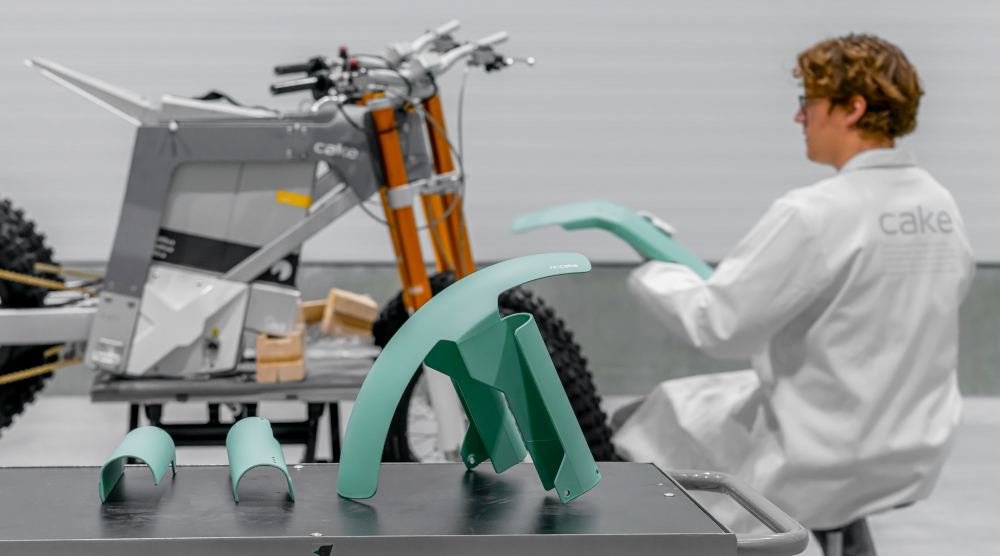
The Cleanest Dirt Bike Ever
At the time of writing, making the Kalk the world’s cleanest dirt bike was a work in progress, but Cake has completed some critical steps towards it.
These began in 2021, when Cake and its primary partner on the project, Swedish renewable energy company (and one of the largest energy companies in Sweden and Europe) Vattenfall first started discussing mutual interests that would eventually come together as The Cleanest Dirt Bike Ever project. Soon after, they selected the Kalk to be the model for the project, although the public announcement of the plans came in June 2021, and initial research started in September that year.
“In January 2022, we started calculating the exact amount of CO2 emissions created by manufacturing one Kalk bike, down to the very materials for each part,” recounts Isabella Pehrsson, sustainability manager at Cake and leader of the project.
“That was a tactile exercise as much as a mathematical one, in which we first took apart a complete Kalk and laid out every part flat across a workshop floor, to feel out the scope of the challenge and divide up the calculation tasks for inventory analysis and environmental impact assessments based on subsystem and material categories. By spring 2022, we had an official number.
“What was helpful was that we’d already aimed to save weight, emissions and recycling burden wherever possible by reducing material usage when the Kalk was first designed. We’ve also designed our dirt bikes the be as modular as possible, because that enables us to swap new parts in and out as cleaner or more efficient alternatives are developed.
“We’ve found that the biggest cause of emissions across the different production stages of the Kalk’s parts – and one of the most straightforward to resolve – is the absence of green energy powering the machines producing the Kalk.”
Vattenfall has been Cake’s foremost partner in the project, partly owing to its focus on decarbonising industry and hence the compatibility of the two companies’ goals. As Jacques Pellis, industry partnerships at Vattenfall Communications, comments, “Decarbonising the energy supply is a first prerequisite for The Cleanest Dirt Bike Ever. However, electricity is not only a power source, it is also a source of innovation, both directly and indirectly through fossil-free hydrogen, which can be used as a feedstock and energy for industrial processes in order to decarbonise the production of for example steel, cement, ammonia and chemicals such as plastics or glue.
“While research has already shown that a fossil-free industry is possible, both technically and economically, this project will show real results that will hopefully inspire more industries to decarbonise.”
Kumar emphasises however that the process of calculating the Kalk’s CO2 emissions during production was very complex. Although the LCA standards specify frameworks and methodologies for breaking down parts and identifying how to calculate required CO2 emissions, lengthy discussions with suppliers were needed to uncover every CO2-generating stage of every production process and method used for every material, along with shipping methods.
These could then be modelled in standardised LCA software to output raw figures for CO2 emissions, which then had to be validated by checking against further real-world consultations and data, and gaining assurance that any assumptions made regarding data averages, aggregates and regressions made sense.
“The kind of LCA databases we use, like ecoinvent or GaBi, have different emissions figures associated with materials extraction and processing, production processes, and energy emission factors,” says Kumar. That has allowed us to cross-reference all the figures that were being put out and to compare those contrasting emissions values, to gauge how much we could trust the estimates of CO2 outputs we were getting, until we came up with a figure that we were sure was an accurate reflection of the Kalk’s emissions from cradle to gate.”
Calculating that figure has shown the scale of the challenge being undertaken by investigating and compiling the exact amount of CO2 emitted in the bike’s manufacture, and percentages for how much CO2 is emitted per component.
Specifically, 1186 kg of CO2 are generated throughout production of the bike and all its parts. For reference, Cake notes that around 25-30 t of CO2 is produced in the course of manufacturing an average electric car, and consuming a standard 60 litre tank of gasoline emits 182 kg.
The drivetrain occupies the lion’s share of this – collectively, the e-motor, battery, main controller, suspension and brakes comprise 57%, or around 676 kg of CO2, while the aluminium in the frame represents 24%, the non-drivetrain electronics contribute 7%, steel parts 4%, plastic components 3% and rubber 1%. From these figures, Cake is about to begin shrinking that amount by targeting different sources of emissions one by one, as zero-carbon options for electric dirt bike parts become available, either from outside suppliers or Cake’s other partners.
Body and structural materials
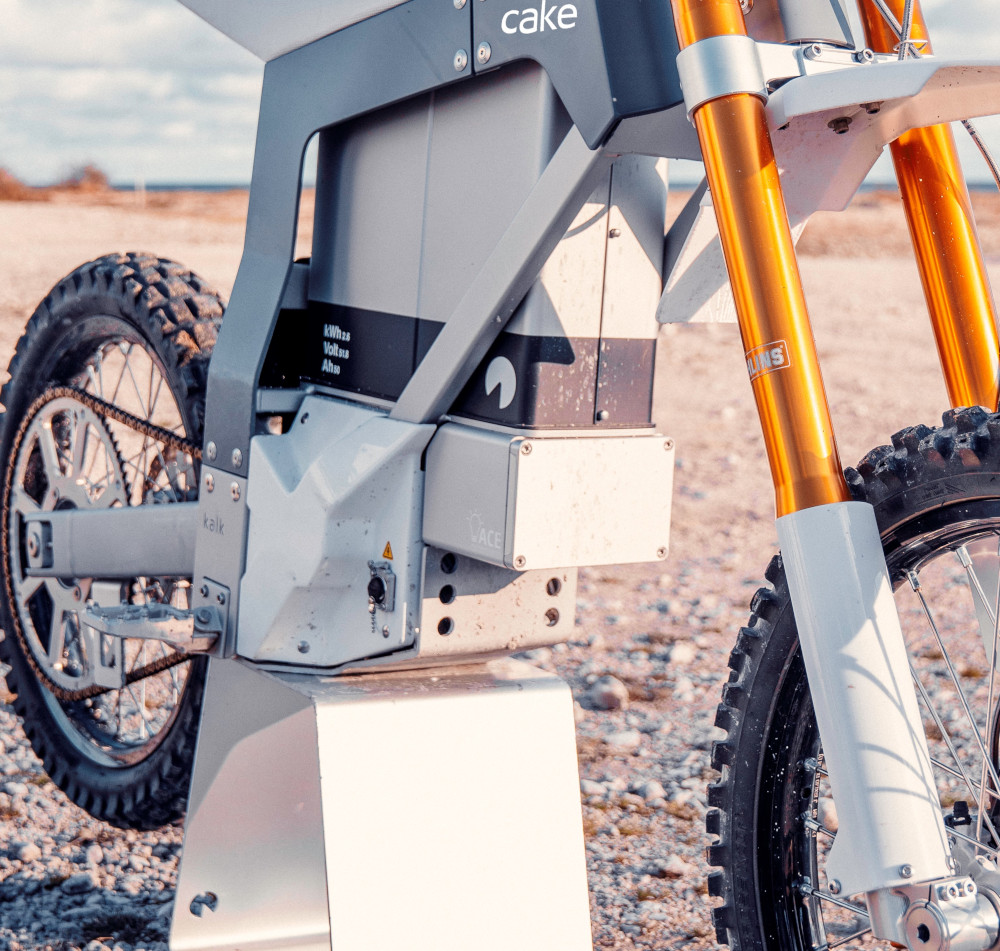
Much of the field testing during the Kalk’s development was aimed at zeroing in on the optimal choices for structural and subsystem housing materials, by accumulating reliable data on the bike, cross-referenced with LCA databases and information gleaned from metals suppliers.
“Most of the structure is aluminium alloys, and we started with a lot of 6061, as well as a lot in the 70 series – the highest grades of aluminium you can get – particularly for the steering heads and other parts of the frame that take most of the torque and physical abuse,” Thour says.
“We could have ‘gone down’ to aviation-grade metals in some parts between those stressed areas, and in the first versions of the Kalk we may have over-dimensioned some structural parts because of the rapid nature of our development process and the dearth of information on how to optimise the mechanics of an electric dirt bike, but we engineered by feel so as not to fall short of necessary durability limits, say by accidentally under-dimensioning anything.”
Thour adds that not only does Ohlins provide the Kalk’s front fork and shock absorber, but the company helped Cake in designing and developing the forks to be as light as possible. In pursuit of material lightness, Cake has sought to optimise the weight of every other component, including the drivetrain, electronics and battery.
Also, the frame is at present largely 6061 aluminium, extruded and forged before being CNC-machined, while the handlebars are 7050 Al. The steel is largely stainless, sitting in the brake disc (a 220 mm-diameter, 3.2 mm-thick part), and the fenders are largely PC or ABS plastic. Owing to carbon composite’s poor recyclability, it is used in only one specialist variant of the Kalk, the AP, in order to give extra strength and hard riding tolerance for its intended user base of wildlife conservation agents.
“Across all these parts, we’ve been investigating how we might use recycled materials, from aluminium to plastics and their substitutes – not just their availability but whether they come with the mechanical strengths and other qualities we need to maintain the lifetime of the Kalk,” Pehrsson says.
In addition to researching recycled high-strength aluminium, Cake keeps a close eye on the progress by steel manufacturer SSAB on fossil-free steel, based on HYBRIT technology.
“HYBRIT is a joint venture between SSAB, mining company LKAB and Vattenfall which began in 2016 to explore the opportunities of fossil-free steel. That resulted in the first hydrogen reduced iron in May 2021, first fossil free steel delivery by SSAB in August and the first product produced in October – a truck trailer together with Volvo. Actually in June 2022 the first construction machine made with fossil free steel was delivered by Volvo to a customer,” Pellis explains.
He adds, “Every percentage reduction in carbon matters, so in addition to HYBRIT steel potentially replacing some of our aluminium in the future, we’re also looking into other materials that could potentially replace plastics throughout the bike.”
For example, Cake has already announced a partnership with PaperShell, whose eponymous material is a natural fibre composite that is stronger than plastic but with a far lower carbon footprint – less than 1/7th that of polyproplene and less than 3% of that of fibreglass.
Energy
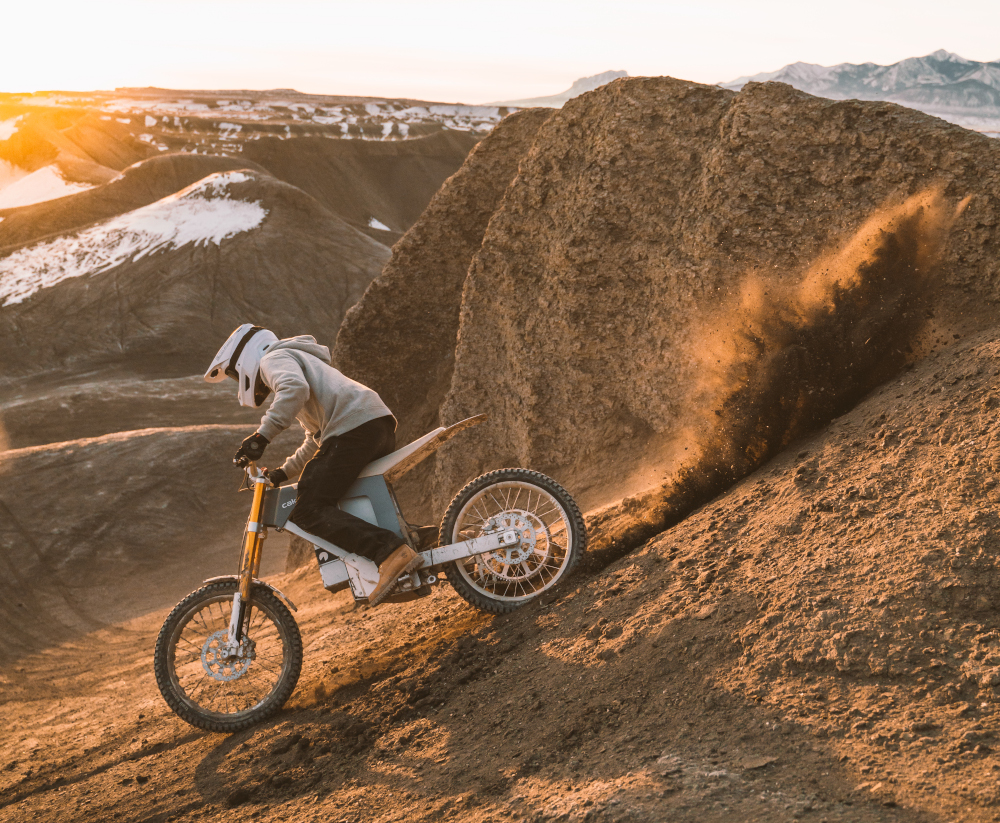
Thour notes that one area where there was already a lot of literature and standards to draw on was the battery. Guidelines for developing BMSs, balancing lithium-ion cells, and assembling safe modules and packs were already available, particularly for harsh environments such as military use.
Naturally, some requirements in military-grade battery standards, such as designing for temperature limits of 250 ºC, would have been unnecessarily challenging to achieve in a dirt bike, but other areas such as EMC, shock and vibration provided useful pointers on mechanical and material choices throughout the battery.
“We paid close attention to what the customer would experience with this bike,” Thour says. “For instance, there’d be no sense in packing 30 kWh worth of cells inside it, because that would be incredibly heavy and the rider would not get particularly far when riding it for motocross, stunt riding, exploration or what have you.
“Making an electric dirt bike creates different issues from many other EVs, because of this very fact that you need to optimise it for high performance. Whether you’re riding an off-road Kalk or a street-legal one, the ride quality will define whether our project was successful or not.”
Accordingly, when it came to choosing between high-energy cells and high-power cells, Cake opted for more power and less energy, enabling the explosive delivery of electric power necessary for the high throttle responses and torque outputs characteristic of dirt bikes.
The current cell of choice in the Kalk bikes is therefore an 18650 cylindrical NCA cell from Samsung. Both Panasonic and Samsung cells had been used early in development to rapidly prototype the bike, and Thour says both companies’ cells provided consistent and reliable performance during every one of Cake’s battery cycling and track riding tests.
On balance though, the cylindrical cell form factor has allowed a high packing rate and hence specific energy in the 17 kg battery pack. However, some later Cake models have incorporated more energy-optimised NMC cells, for instance in use cases where maximising range is more important than a sharp acceleration curve.
For even more optimisation between a satisfactory riding time and comfortable packing in terms of the centre of gravity, weight distribution and body shape, the Kalk incorporates 2.6 kWh of battery energy, which in typical operation is discharged at a rate between 3C and 5C, while outputting around 7 kW (up to a peak of 12 kW) over a 48 V bus. Not only does the battery cable output 48 V, but everything in the bike operates on this voltage, simplifying powertrain assembly and parts count.
Battery stability
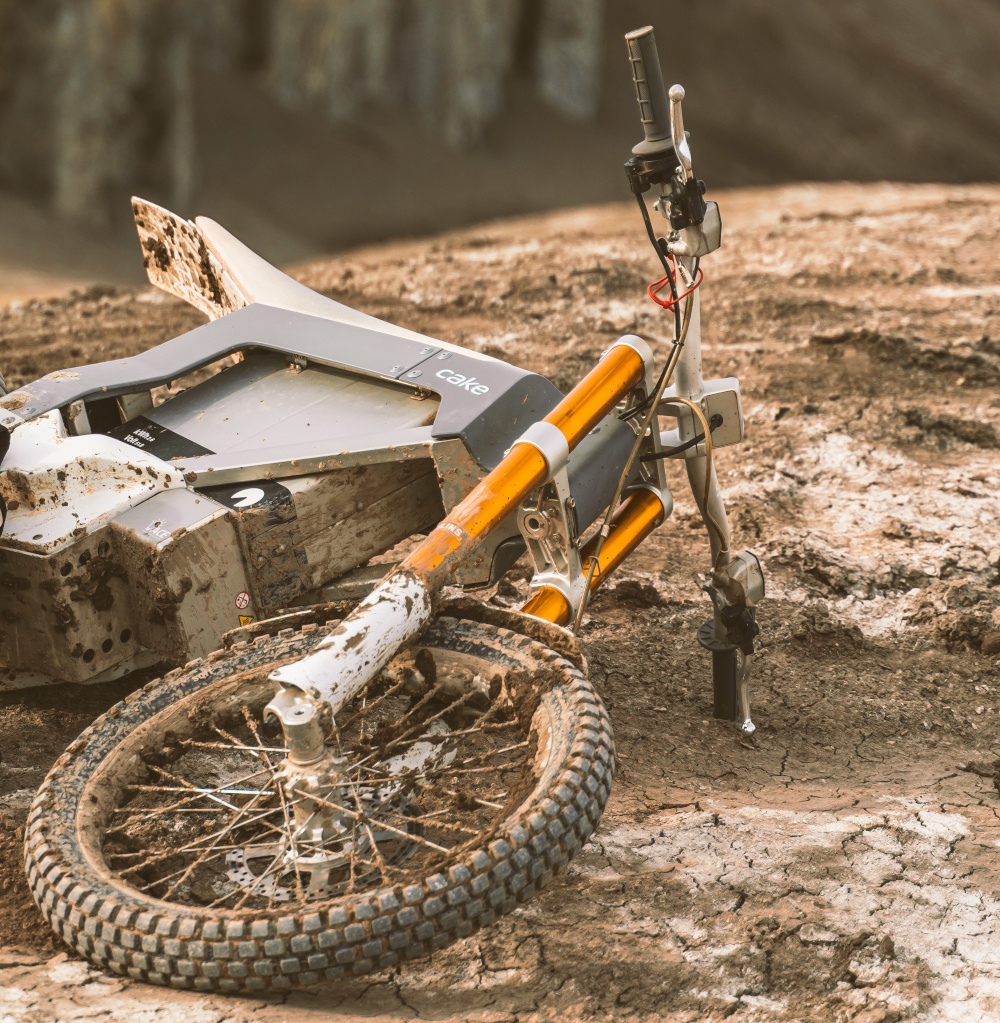
The lower energy capacity also means the Kalk has shorter recharge times – about 2 hours to go from 0% to 80% SoC, with a further hour to reach 100%. And while Cake notes that the Samsung cells discharge at up to 5C, and are perfectly capable of being recharged safely at up to 2.5C, the company’s wariness of stressing the battery during charges means its engineers limit the charging rates to between 0.3 and 0.5C over the curve of charge time through the BMS and charger software.
“Most of the BMS r&d targeted safety-critical and somewhat obvious capabilities, in particular cell balancing with constant and precise measuring of cell voltages, temperatures, currents and so on,” Thour says.
“Programming a high degree of autonomy into the BMS was also very important from our perspective. Although we worked initially with a partner and used a BMS based on one of their reference designs but tweaked towards our preferred safety levels and balancing behaviours, by 2019 we’d switched to a BMS made entirely in-house.”
In our previous features on electric motorcycles, such as the Lightning Strike (EME 4, Autumn 2019) and Energica Eva Ribelle (EME 9, Spring 2021), battery cooling is achieved largely by mounting the pack uncovered behind the front wheel. This allows the rush of air flowing over the pack walls at speed to dissipate the heat generated by the cells as it is transferred to the outer enclosure, and to do so in a way that scales with power output.
However, the off-road version of the Kalk is not intended for lengthy driving on straightaways as they are. As a dirt bike, its main areas of use will be in forests, motocross circuits and stunt courses. Impact protection of the battery thus takes precedence over leaving it exposed to the air, so it is fitted beneath the seat (where it can be removed and replaced) inside the aluminium frame walls.
Indeed, Thour comments, “The worst case for the efficiency and well-being of the Kalk is full throttle on a highway. That’s where you have the highest torque, owing to the current from the battery and the drag across the body reaching their real-world maximums, so you’re discharging the battery as hard as it can really be pushed.
“We’ve not had many complaints, but possibly the most severe was from someone who was a heavy customer, who’d opted to use a Kalk on California State Route 1 in the middle of summer. Basically it t was the perfect recipe for an overtemperature condition. But in all cases of high-end motocross customers driving the Kalk on the harshest circuits, or through severe environments in Africa with our Kalk AP for anti-poaching workers, we’ve never had an issue.”
Rather than equip a large and complex system of radiators, pipes, and pastes for thermal management into the dirt bike’s small frame to compensate for the lack of air, Cake has optimised the designs of its battery systems and structure around maintaining thermal stability at the cell and module levels.
“First, we maintain a thin air gap between the frame’s aluminium outer walls and the battery pack’s housing, which helps in hot as well as cold conditions to maintain the battery’s thermal stability. That wasn’t an intentional function of the design, but a lucky engineering accident,” Thour explains.
“And as well as reducing the amount of free air inside the battery, with the air gap but also by maxing the cell packing density, we’ve connected the cells with a higher number of parallel strings than what you might typically see in a battery of this size. That means we decrease the current that has to pass through each individual parallel string, meaning less current lost as heat, and less thermal build-up in the pack.”
Battery development
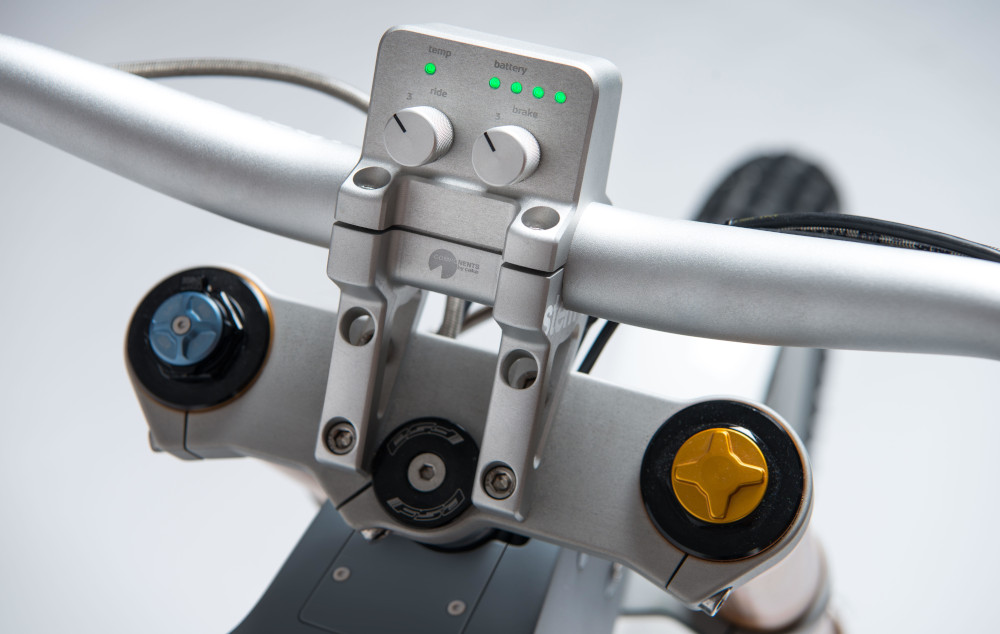
At the moment, AC charging through a 110/220 V input is the only available option for replenishing the battery, but a fast DC charging system is in development.
Also in the works are a few changes to the battery technology for the Kalk and Cake’s other bikes. For example, of the newer platforms powered by NMC cells for enhanced range (at the cost of power availability), several use 21700-type cylindrical cells.
This is aimed at future-proofing their pack designs. Cake’s engineers are confident that all new cell chemistries – from alternative formulations of NMC, NCA, LFP and so on to cathode and anode formulations not yet commercially available – will come in 21700 form factors, so they see designing a pack around 21700-type cells as enabling drop-in replacements of them cells with newer, superior technologies.
“Naturally, we’re not so naive as to think it’ll be a seamless process to replace the old cells with those containing newer chemistries, but cutting down the physical integration hurdles and providing some mechanical backwards-compatibility in cell form factors will allow us to get cutting-edge products to market more easily and take advantage of more advanced and hopefully cleaner generations of batteries,” Thour says.
Although the Samsung cells have performed well to date, Cake plans to switch to Northvolt cells in the future, for a number of reasons.
“For a start, if we want to make the cleanest dirt bike ever, the fact that Northvolt’s gigafactory is powered by clean electricity means that we cut 60% of the carbon associated with the battery in one fell swoop,” Thour says. “As Isabella says, the easiest, lowest-hanging fruit you can go for when cutting emissions is to pick a solution powered by clean energy.”
Pehrsson adds, “We have signed a letter of intent with Northvolt, and their CEO is on our board. The only reason they’re not in the Kalk yet is because they haven’t started production of their 21700-type cylindrical cells.
“As stated, we want all our future battery packs built around these cell types, for packing density and future-proofing, but their sustainable power, short shipping distances – given that they’re a fellow Sweden-based group – and their high usage of recycled battery materials makes them ideal for The Cleanest Dirt Bike Ever.”
Controls and modes
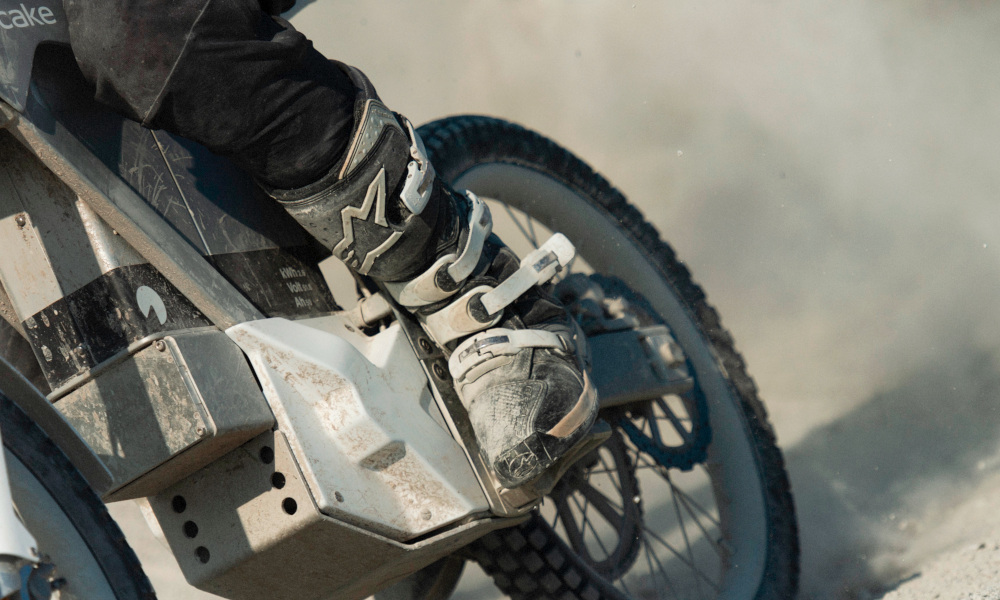
As mentioned, the voltage architecture running throughout the Kalk is designed with a 48 V system (51.8 V nominal), although the company is not above designing for higher voltages where necessary. Its limited-edition Bukk dirt bike for example – now sold out – uses a 16 kW e-motor, and this higher power prompted Cake to design a 72 V bus to avoid high current losses from the battery to the inverter and motor.
Thour comments, “Our present voltage is high for a bike, even though it’s not the ‘high voltage’ you see in bigger EVs, like 400-800 V for cars and trucks. But we wanted the simplicity and efficiency of a single voltage architecture from the beginning, with no pronounced junctions for power conversion.
“This was another quite experimental area, in that we weren’t sure that 51.8 V was necessarily going to work for an electric dirt bike, if it might turn out to be wrong for the powertrain from a current and torque perspective. But through a lot of trial and error we validated that it was safe and effective.”
He also notes that the street-legal version of the Kalk was required by law to have a 12 V parallel system for the headlights, blinkers, manual controls and some other safety-critical subsystems. Supplied initially by COTS providers, these are now produced in-house.
At the heart of the power management, control and comms is a proprietary control unit responsible for executing manual as well as automatic command signals for lights and indicators, and for generating signals corresponding to the correct motor frequency based on the throttle position.
“To give our customers their ideal experience, the control system is programmed with the necessary performance allowances or limitations typical of the different riding modes and braking modes,” Thour says “Engineering this main control unit in-house was therefore key to having complete, fine-grain control over the throttle response, the regenerative braking and similar parameters.
“And even after we were satisfied with our proprietary hardware system, we iterated the software through many versions using input from well-experienced test riders, including motocross riders who understood what quality feels like in high-end dirt bikes, and less experienced ones to see if the automation in our battery management and control systems still felt intuitive to the uninitiated.”
The Kalk’s three riding modes include an exploration mode that caps the top speed to 45 kph and enables 3-4 hours of range on a full charge, an enduro or active trail mode with a 70 kph speed limit and 1-2 hours of estimated riding time, and a full power mode that allows the bike’s maximum nominal speed of 90 kph.
Meanwhile, the braking modes run from a freewheel mode to a mode with regeneration programmed to simulate the feel of two-stroke braking, and another, harder regenerative mode aimed at recreating a four-stroke engine brake.
“It might sound like over-engineering, but perfecting the throttle response and retardation curves is essential to the feel and enjoyment of a dirt bike, regardless of the rider’s skill level,” Thour says.
“So it took a lot of time and revisions from our software engineers to get the motor control and battery management perfect, and every time we changed a line of code, we had to test the bike again in real-world conditions. This was still all very untried and untested territory, as everything from traction over the ground to the geometries of the structural metals needs to be validated against differences in how the software flexes the powertrain.
“Even now, although we’re very happy with the CAD and FEA simulation package we acquired about a year ago – which certainly helps us to iterate faster – we still do just as much real-world track testing, because ultimately that’s the only way to be 100% sure of the safety and fine control of our bikes.”
Traction
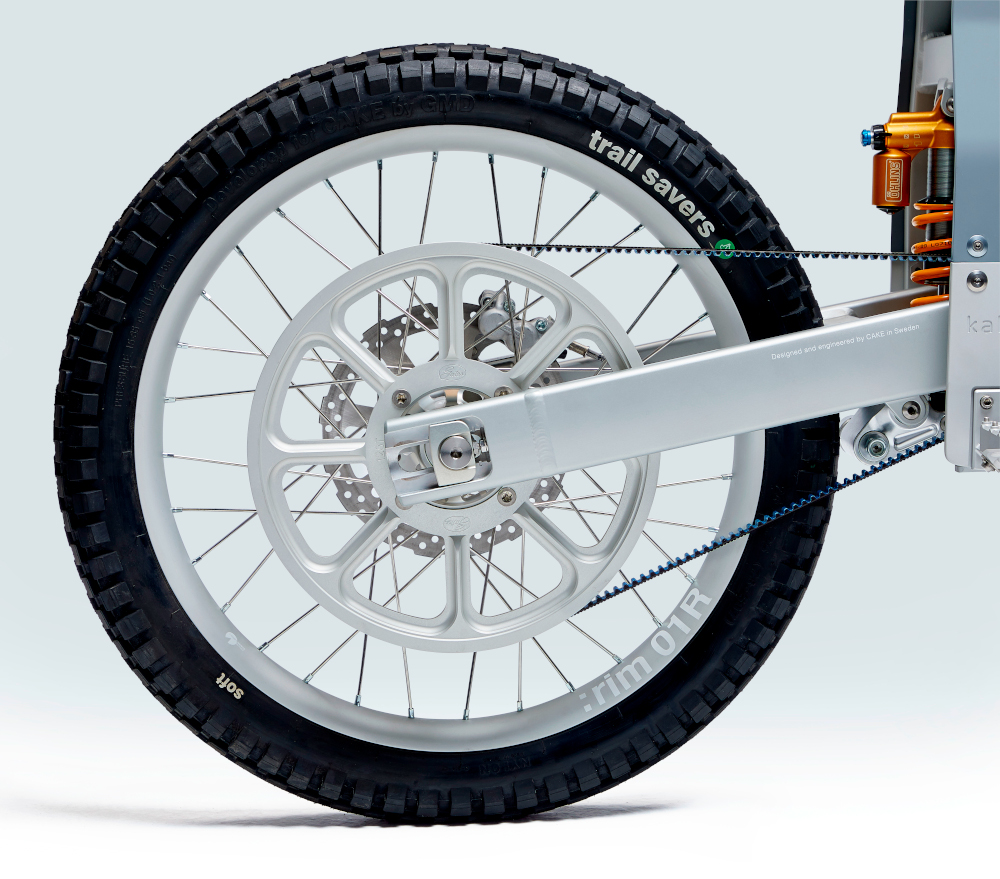
As discussed, designing a dirt bike around an electric motor is advantageous from an end-use perspective, as its standard driving profile consists of rapidly oscillating changes between high-torque acceleration and hard braking (possibly with impacts).
“This required very fine motor control, and so the three-phase variable frequency drive in the inverter is designed both for that and to integrate seamlessly into the 48 V bus. The actual loads run a bit higher than that, maybe to our peaks of 58.5 V,” Thour says.
“That comes with some advantages in manufacturing as well. Since it’s a much lower voltage system than, say, a car or truck EV, our engineers can assemble the powertrains quickly and without taking extra pains over safety.”
The inverter is harder to heat-manage internally than the battery, so a network of copper heat pipes run through the inverter across the power MOSFETs to a thick aluminium plate typically mounted on the outside the frame, usually either on the front or bottom depending on the product or application. The aluminium also inherently provides some additional thermal transference and heat dissipation during current spikes to the motor.
“We’re currently using some COTS, medium-end MOSFETs but we’re always looking for ways to improve in terms of the components we use and what they bring to our bikes,” Thour says. “During the Covid pandemic, for example, we looked at suppliers across Europe and beyond to cover shortages and see what combinations of carbon reduction, cost efficiency and performance we could get. As one result of that, we’re now in a joint venture with a company that can dedicate more manpower to inverter r&d than us, to help accelerate developments in that respect.”
The electric motor is a radial flux, IPM machine. A key reason for choosing this configuration was to minimise the Kalk’s parts count. Also, the maturity and low maintenance of IPM systems gave Cake the confidence that using them was in the best interest of the bike’s longevity and emissions.
“Some would counter that it’s hard to get a dirt bike level of horsepower out of the bike with an IPM machine, and I would agree, but we’re doing optimised performance, not performance competitive with full-size motocross motorcycles,” Thour says. “Someone else might have the fastest electric dirt bike in the world, but that’s not what we’re aiming for; we’re aiming for zero-emissions over lifetime, and exploring forests with respect, not tearing up habitats or parks.”
The motor is now in its third generation of design, and Cake is planning a fourth one, particularly for weight reduction through more efficient use of material in the stator. “Much of these are materials we’ve already discussed, like aluminium and steel, as well as iron, but the big item of concern is the permanent magnets,” Kumar says.
“As a rare earth material, these represent something that’s difficult to decarbonise, particularly in terms of their extraction, and that keeps us investigating the viability of things like AC induction motors to see if there are any that can achieve the torque and efficiency at the kind of weight and lifetime we need.”
In its present design, the motor outputs up to 42 Nm of torque, and as mentioned up to 12 kW of power. Mounted on the motor shaft is a sprocket with 12 teeth, which drives a 420 chain with an O-ring. The chain runs to a sprocket with 80 teeth at the rear wheel, and this reduction makes for up to 280 Nm of wheel torque.
“We do have a hub wheel motor drive in one of our other bikes, but obviously it’s a much slower vehicle, so for the Kalk we’re happy with a central motor powertrain configuration. It’s easy to play around with the sprockets and chains to get different combinations of torque and speed,” Thour adds.
Rider systems
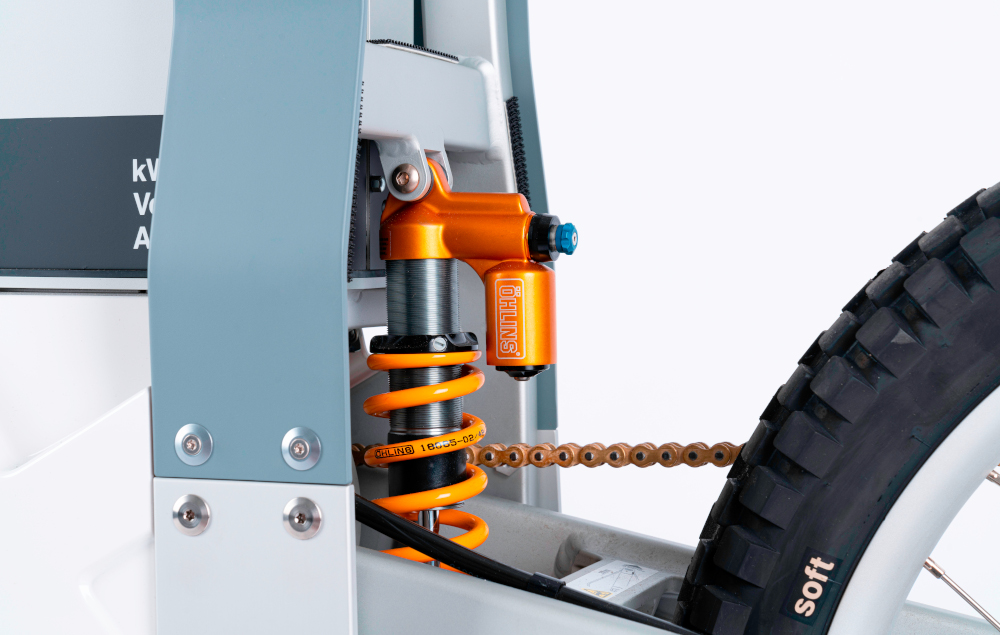
Although Cake’s personnel see the mechanical aspects of the Kalk as highly important, they re-emphasise that the bulk of a customer’s experience comes from the software. That includes the rider’s display, an app for tracking and managing a Kalk, and connectivity systems. The display is a simple, industrial-style colour display screen with an adaptive interface that displays key stats such as speed and SoC, and they can also be viewed on a smartphone using the app or via Cake’s website.
“That’s useful for the Kalk, and even more so for our street-legal, business-oriented bikes, whose customers are running delivery fleets and want to analyse how their Cake EVs are being driven, when a service is due, when batteries need to be changed or refurbished, where they are and so on,” Thour notes.
“We’ve worked with a lot of software engineering partners on this, but we’re gradually bringing the core competencies in-house, from front end to back, including the cloud for seamless connectivity between the app, the bikes and our web portal for managing the bikes. Within that is a digital twin of the dirt bike, which visualises all the data on performance, state of health, and upcoming maintenance dates.”
Currently under development are some improvements to the adaptive display for automating predictive selections of information intuitively during riding. That might include graphs or numbers for speed and charge/discharge rates during high acceleration or deceleration, or the SoC and estimated remaining range indicators when the battery capacity drops.
Cake anticipates all EV manufacturers tending towards these types of predictive UI systems, especially faster off-road vehicles such as the Kalk, as well as electric snowmobiles or SUVs for instance.
“To ensure consistent delivery of data between users’ vehicles, displays, smartphones and the cloud, we have three wireless comms protocols operating constantly,” Thour says. “One is a 4G cellular link using a COTS IoT device, which also has a secondary 2G link as a back-up, and we also have a Bluetooth radio on each Kalk for short-range comms with the rider’s phone. The third is an NFC sensor to enable the smartphone or fob to be used as a key for locking and unlocking the bike.
“We haven’t moved into 5G yet; that’ll happen once the chips are updated, made cost-effective and are widely available. As it stands, we don’t have an urgent need for such data bandwidth, but once enough bikes are operating in congested areas, such as our commercial fleet designs, than 5G could be a real benefit.”
Sustainable future
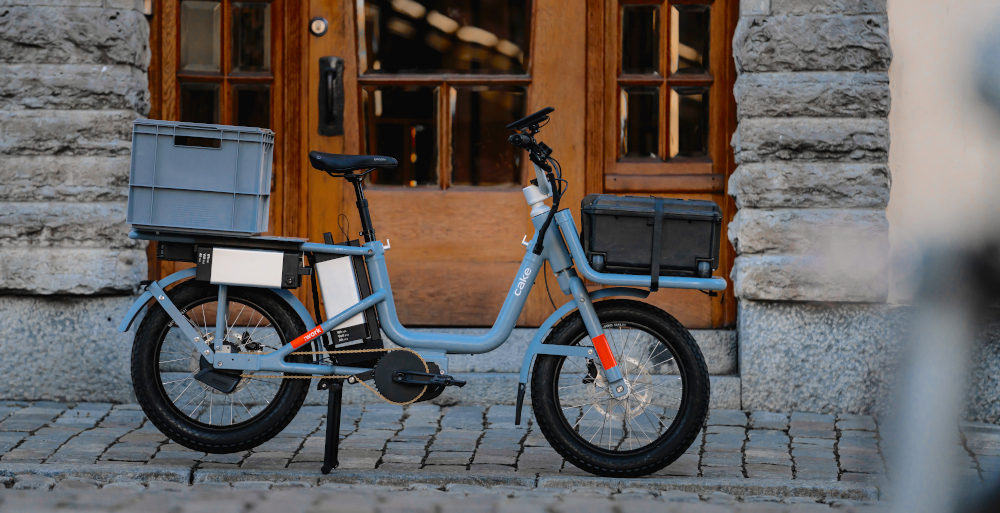
Cake continues to develop and release new products in its portfolio of electric motorbikes, its latest being the Aik platform aimed at users such as delivery riders in cities.
Much like the Kalk, it features an aluminium frame and a central motor drive, although it also has a modular battery system that gives users the flexibility to integrate as much or as little battery power as they need for their jobs. Up to three packs can be installed on the Aik to enable 360 km of range between charges or swaps.
In the meantime, Cake and its partners will continue to explore and exploit the use of fossil-free materials and practices in future versions of the Kalk and its other EVs, and support r&d into technological innovations beyond e-mobility with a view to decarbonising industries around the world.
Specifications
Kalk
Electric off-road dirt bike
NCA 18650 cylindrical cells
Radial-flux PMAC IPM motor
Weight: 69 kg
Handle height: 1135 mm
Seat height: 926 mm
Width: 810 mm
Wheelbase: 1309 mm
Nominal voltage: 51.8 V
Peak voltage: 58.5 V
Battery energy: 2.6 kWh
Battery capacity: 50 Ah
Maximum continuous power: 7 kW
Peak power: 12 kW
Charging voltage: 110/220 V DC
Estimated charging time: 3 hours
ONLINE PARTNERS
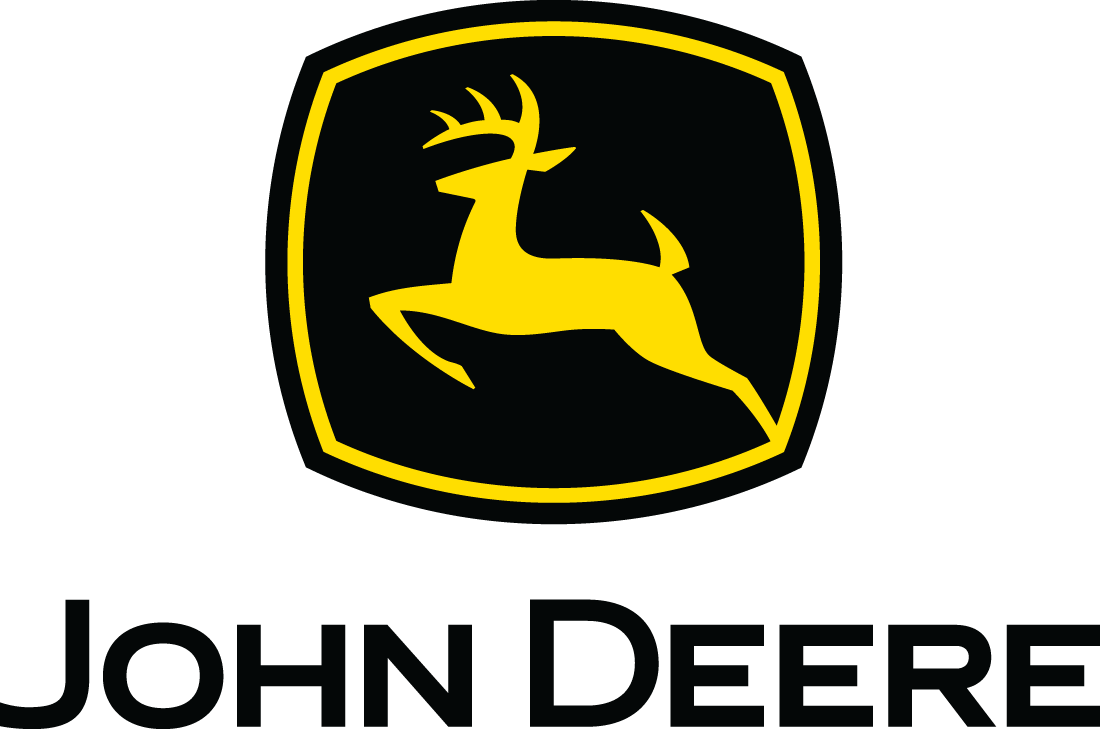
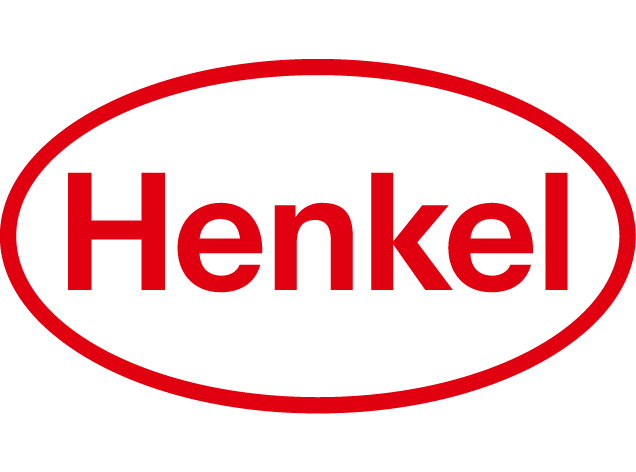
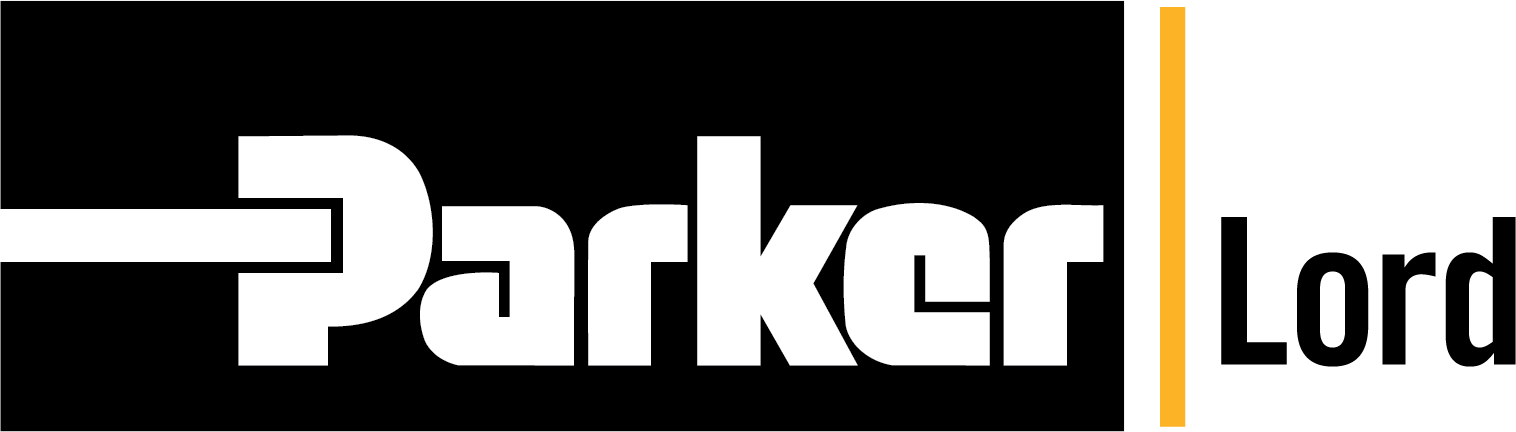
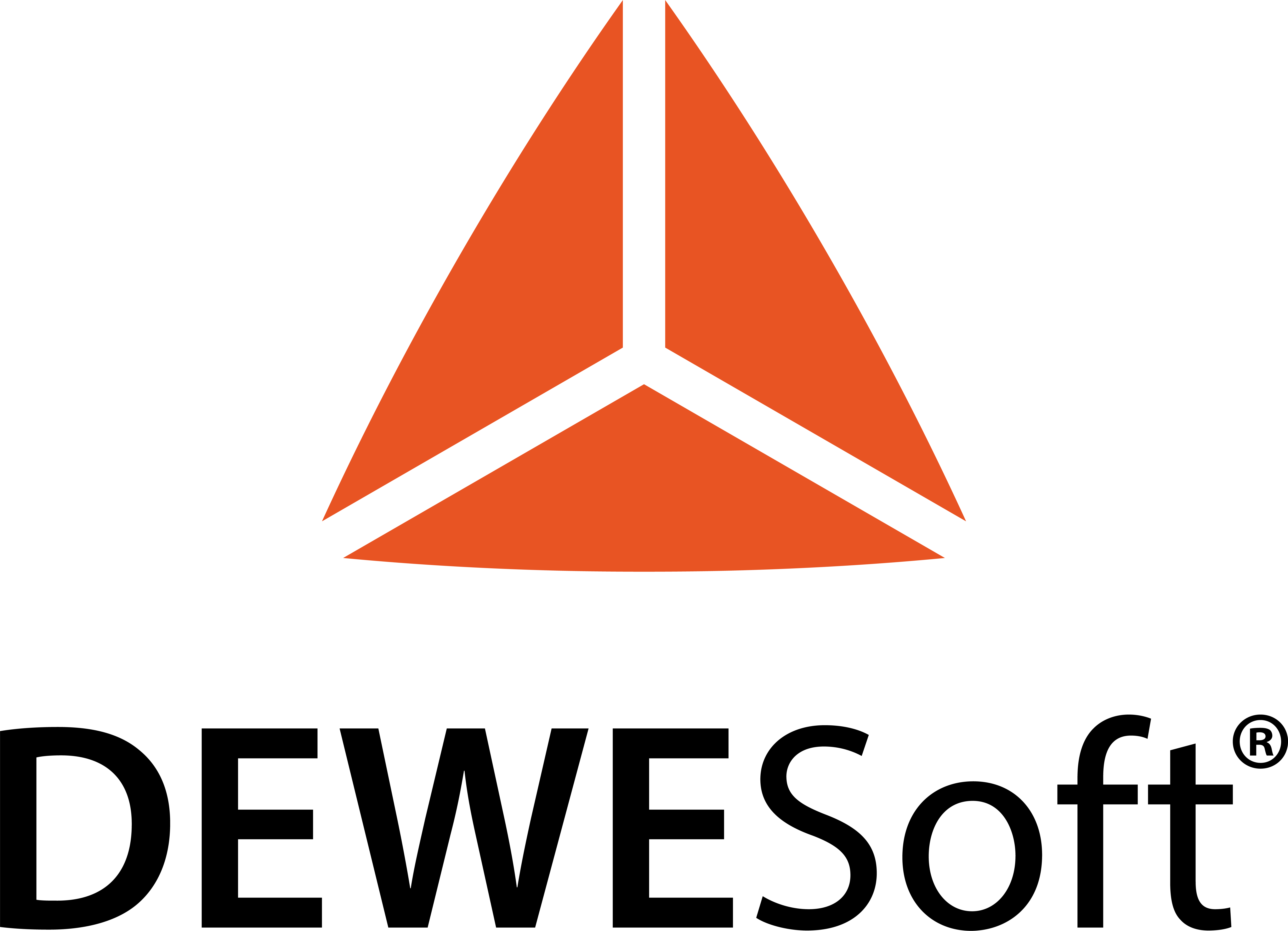
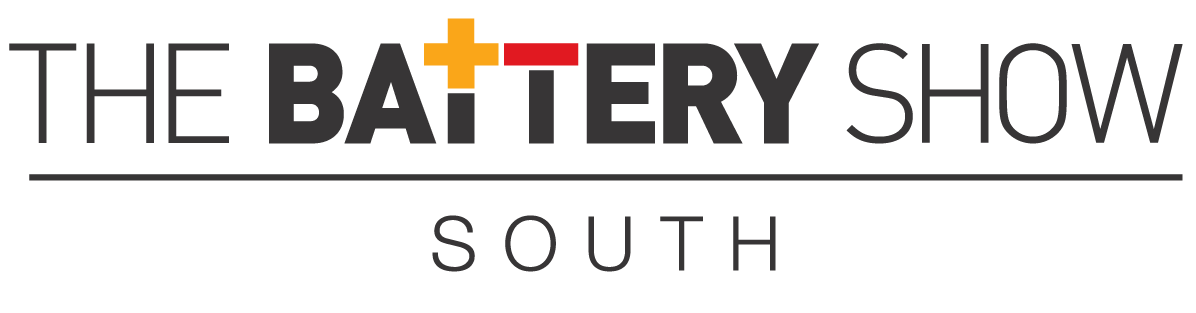
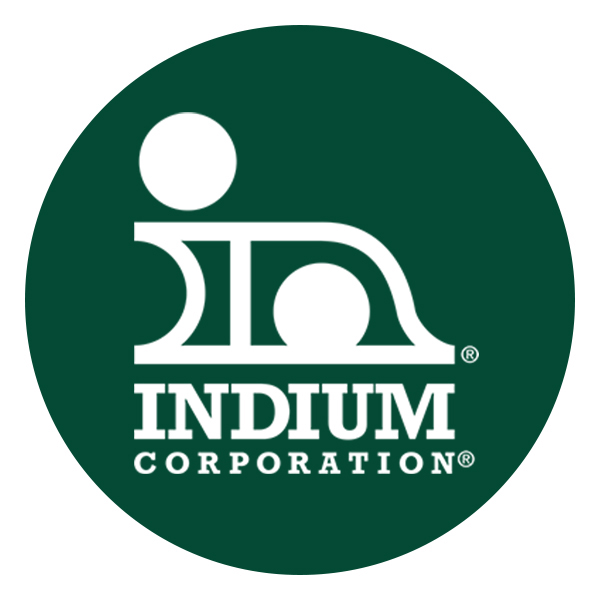
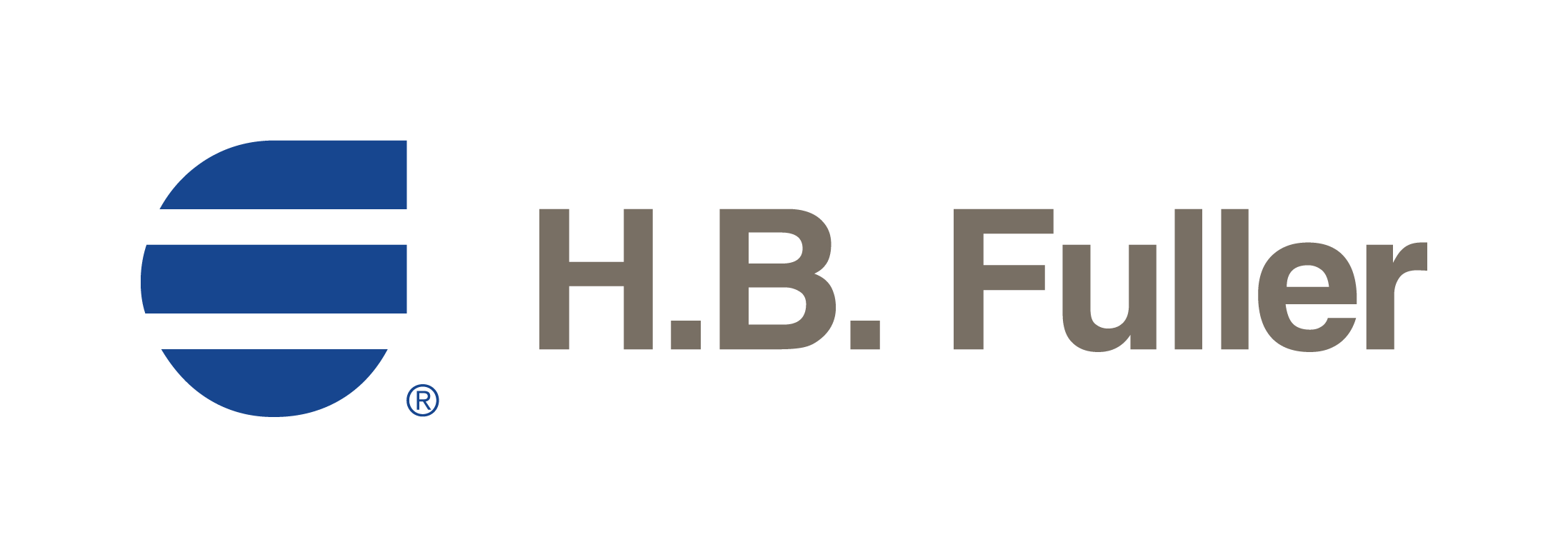