Breakthrough for lithium-sulphur batteries
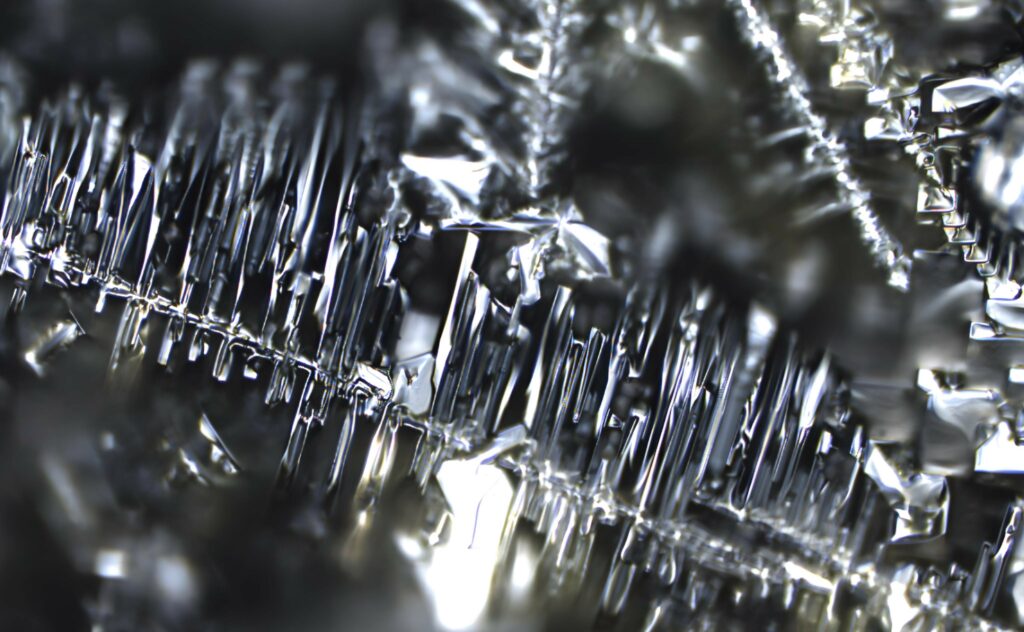
(Images courtesy of Theion)
A cell technology holding 900 Wh/kg – three times the energy density of state-of-the-art lithium-ion battery chemistries – that is safer and cheaper thanks to the use of abundant and easily accessible sulphur for the cathode in place of nickel manganese cobalt oxide (NMC) is an exciting prospect (writes Peter Donaldson).
Batteries that use sulphur in this way have been the subject of r&d for years, but have proved impractical for a number of reasons, primarily the ‘shuttling’ of polysulphide compounds that causing active material to be lost. This can be avoided by using electrolyte solvents based on ether rather than carbonate, but ether is highly volatile and has a low flash point, bringing its own safety and reliability problems.
However, German start-up Theion (ancient Greek for sulphur) is making r&d sample cells based on its new sulphur crystal wafer cathode technology that eliminates these problems, says its CEO Dr Ulrich Ehmes.
A sulphur atom has 16 electrons in total, six of which are valence electrons that can take part in chemical reactions, so it a good energy storage medium, but it is also a strong insulator with very low electrical conductivity. The sulphur on the cathode side therefore has to be processed in a special way to overcome this problem.
As Dr Ehmes explains, “We transform it from molten sulphur into a crystalline form, so we have a crystalline structure at the surface that is accessible to the electrons and ions.”
This is a two-step process, he adds. “First, we have to put in a network of highly electrically and thermally conductive material, in our case carbon nanotubes that are laid down on the molten sulphur. We orient these carbon nanotubes like a net, and around them we form the crystals. In the next step we cover this crystal structure with another highly conductive material.”
Dr Ehmes likens this process to doping a semiconductor, and Theion refers to the cathode as a sulphur crystal wafer, but he is keen to stress that the costs involved are nothing like as high as those associated with semiconductor production.
In both the first and the emerging second generation of Theion’s crystal battery, each cell has a thin lithium metal foil anode and the sulphur crystal wafer anode. While the first generation of the technology uses a liquid electrolyte, the second uses a solid polymer alternative.
“The big advantage of this solid electrolyte is that from Gen2 on we will have no inflammable parts in our cell, which makes the cell intrinsically very safe,” Dr Ehmes says.
Unlike a cell with an NMC cathode, there are no oxides in the cathode that could break down and release oxygen to feed a fire should the cell overheat, and there are no liquid hydrocarbons in the electrolyte to provide fuel.
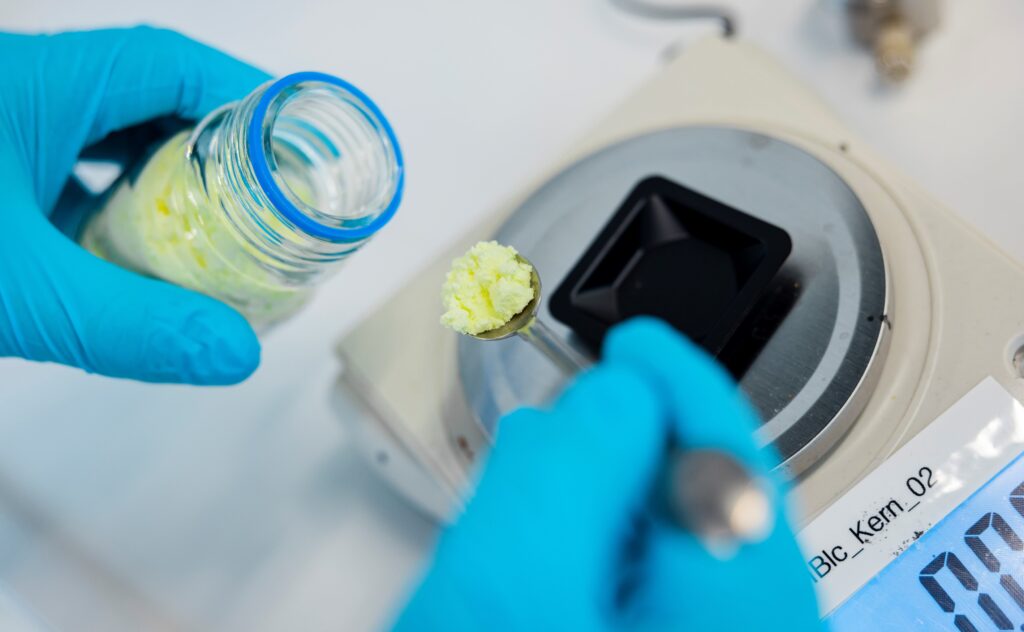
To prevent dendrite formation in the lithium metal anode, Dr Ehmes explains, the energy loading expressed in mAh/cm2 is around 20% higher on the anode than on the cathode. “For example, if we had 20 mAh/cm2 on the cathode side, we would have 24 or 25 mAh/cm2 on the anode.”
With sulphur costing €0.20 per kilo compared with around €20.00 for NMC 811, and materials accounting for 70% of the total, lithium-sulphur batteries promise to be far cheaper, Dr Ehmes emphasises.
These batteries should also be easier to recycle, he says, as there are only four materials in the cell rather than eight in the case of an NMC cell, for example.
The first customer samples for niche markets, such as spacecraft and launch vehicles, will be delivered this year, he says, with other applications such as airborne, mobile and wearable technologies following in 2023 and automotive and electric flight in 2024, with production scaling up through 2027.
Theion’s plan is to hand over the first EV-ready samples to customers by 2024.
ONLINE PARTNERS
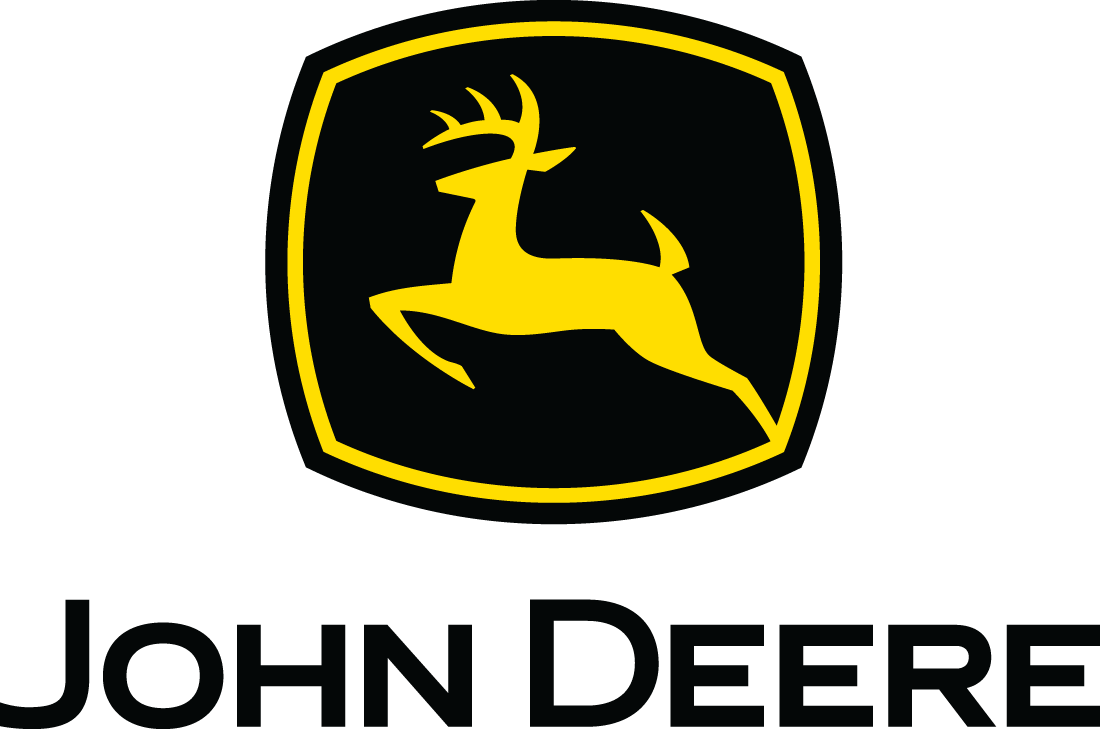
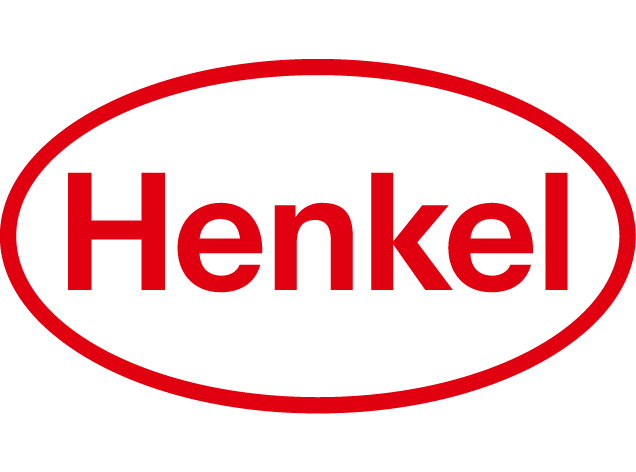
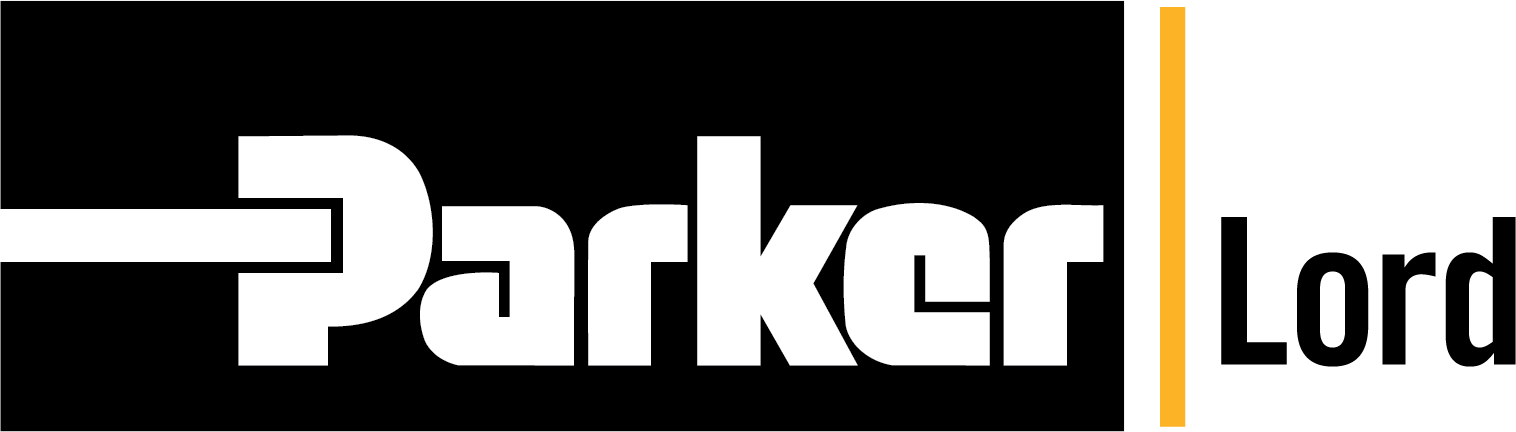
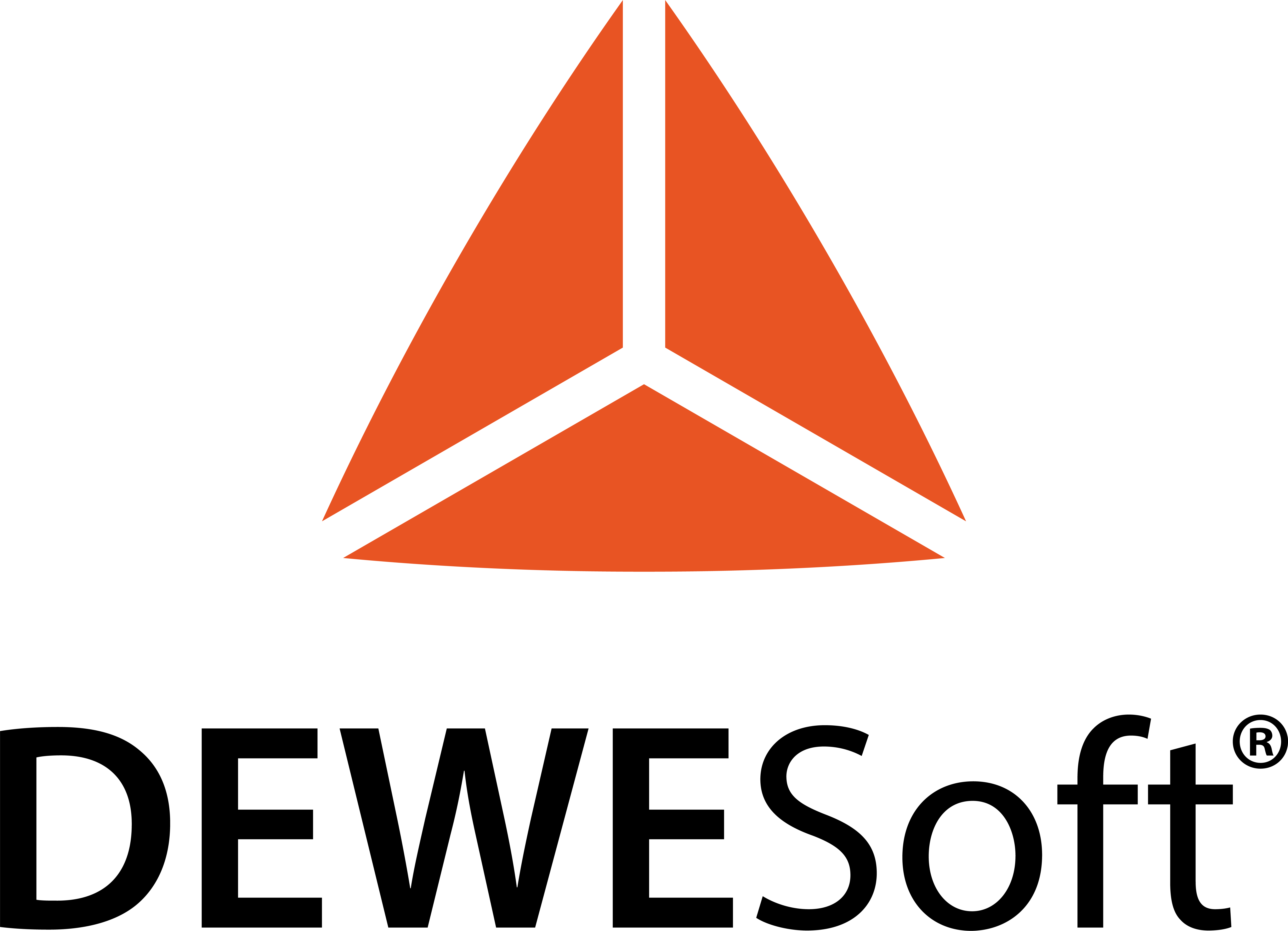
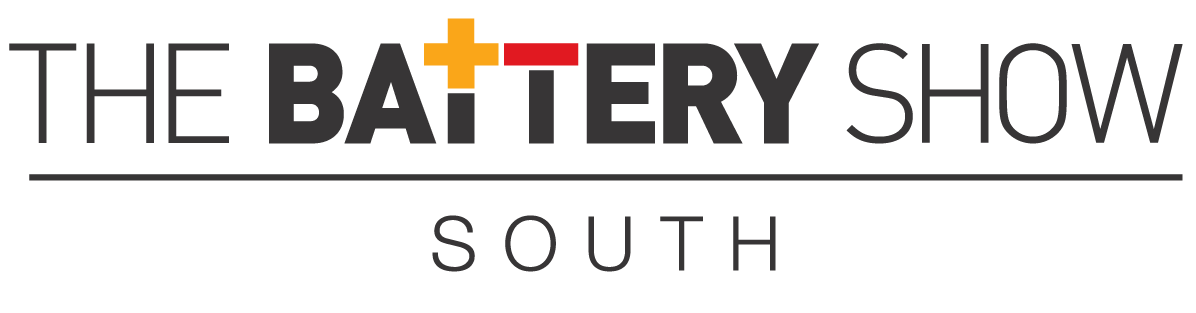
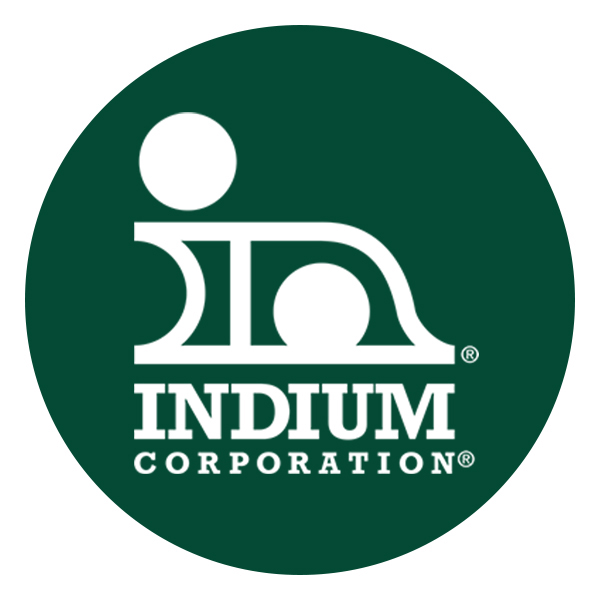
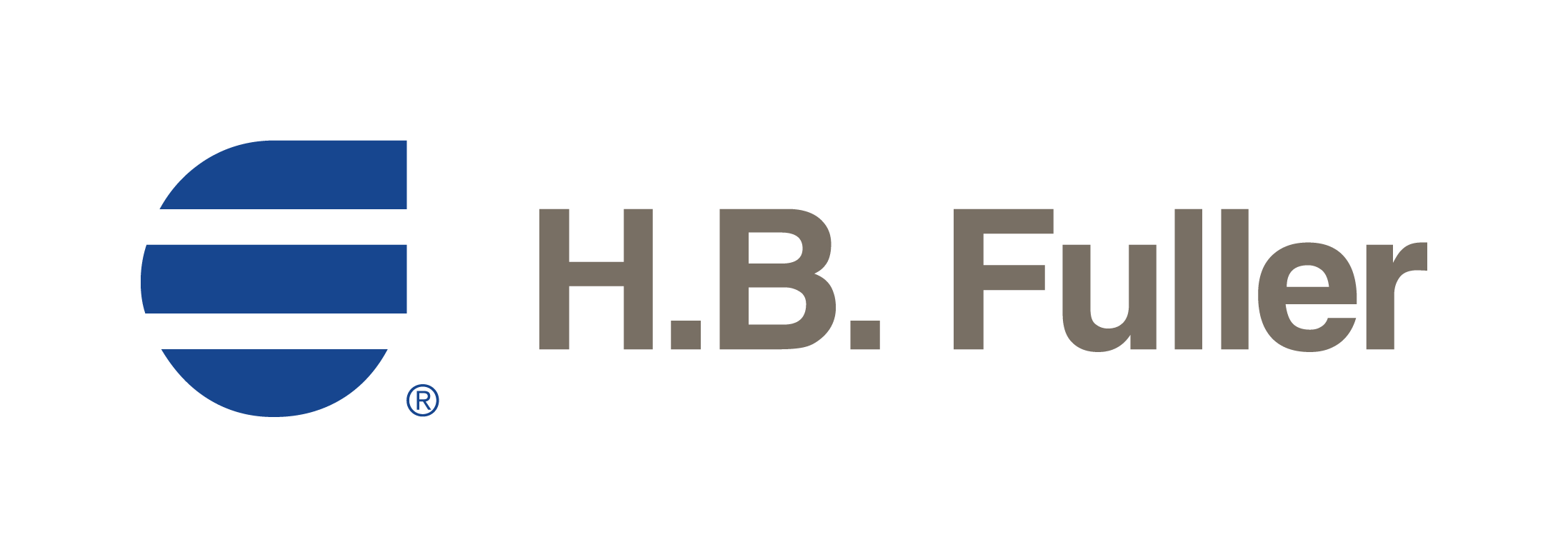