Brandon Fisher
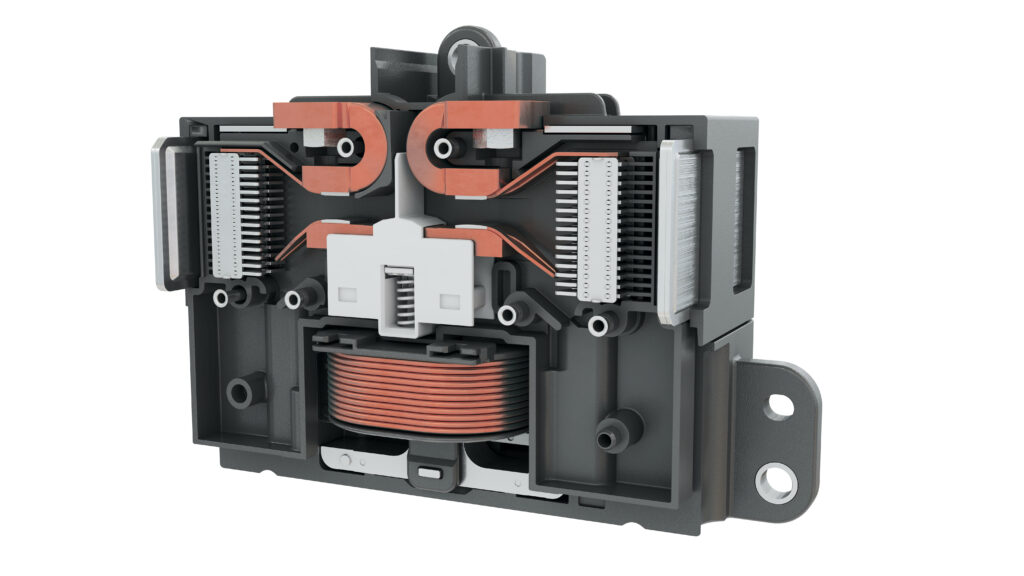
(Images courtesy of Eaton)
Safe pair of hands
Eaton’s head of HV safety systems talks to Rory Jackson about his career so far and the company’s work in the EV sector
As electric powertrains move from 400 V architectures up to 800-1000 V and higher still, innovations around ensuring the safety of power distribution systems are critical to protecting drivers and passengers, and instilling long-term faith in the viability of e-mobility en masse around the world.
Brandon Fisher knows this well. As engineering product line manager for HV power distribution and protection systems at Eaton, he wields considerable resources in devising novel solutions to ensuring the safety of the countless potentially hazardous connections in the most advanced electric powertrains across the EV industry.
Early life and university
“My father was an engineer, and when I was 5 he bought a ‘basket case’ motorbike for us to put together, and for the rest of my youth I’d get really excited about anything to do with the anatomy of vehicles and machinery,” he says.
“He and I would work on cars together a lot, and at one point my mother got us one of those Teddy Ruxpin animatronic bears. Within a week my brother and I had taken it apart, and identified every aspect of how its electrical and mechanical parts worked.”
Following his youth and early education in Oregon, he moved to California to study in the Mechanical Engineering programme at the California Polytechnic State University in San Luis Obispo. Known colloquially as Cal Poly, it combined a strong educational philosophy of ‘learning by doing’, with a practical, lab-based focus on mechatronics that drew Fisher’s particular interest.
“I’m a kinaesthetic learner – I’ve always picked things up by working with my hands and experiencing new forms of engineering directly,” he says. “And I had a tight budget there – I was the first in my family to go to university – so I was really motivated to get my money’s worth of education, and Cal Poly’s programmes were a perfect fit.”
His mechatronics focus guided him into a number of automotive and robotics projects, from FEA simulations to vehicular assembly work, culminating in a robotics competition in 2004 which he entered as part of a team composed largely of fellow mechanical engineers.
“For that, we were given a microprocessor and the objective of making a robotic solution that could speed around a table tennis board, picking up balls around a white line and dropping them into a box at the end of the room,” he recalls.
“We had to define the batteries, the frame, the chassis, how to collect and deliver the balls, all the electrical and mechanical connections between everything, and so on. We focused on making a robot that performed well, ran quickly and looked good; our entry broke the school record and the instructor asked to buy the robot to use a the demonstrator for future competitions.”
Saleen and MillenWorks
The success of this competition, along with other projects in electromechanics and engines across Cal Poly’s courses’ caught the eye of high-performance sportscar and automotive components producer Saleen, which brought Fisher in as an intern in 2004. Its aim was to put his mind to a supercharger being developed by its powertrain group.
“My original internship was meant to be 3 months, but they requested that I extend it to 6, because we were on a launch platform and they really wanted us to keep doing what we were doing,” he explains.
“I still had two quarters of courses I needed to complete at Cal Poly, but then they asked if I wanted to do my senior project with them too. That project was all about making a new kind of brake calliper, and Saleen provided a lot of the funding and materials that I needed, as well as the test platform.”
This momentum from electromechanics into vehicle and structural dynamics motivated Saleen’s management to put Fisher into r&d in chassis systems dynamics as a full-time engineer, particularly in developing new suspension systems, brakes and anti-roll bars through intensive road- and shock-testing of vehicle platforms.
“There was a lot of subsystem-level fine tuning to see how that would benefit system-level performance, with a lot of really cutting-edge electronics and data acquisition tech for the time,” he recounts. “We would develop those parts in the lab, rush out to the proving ground, and test them to see if we were making Saleen’s sportscars perform faster and better.”
Fisher’s work as a chassis systems engineer at Saleen lasted for about 18 months, during which he gained extensive experience in the design, building and testing of numerous Saleen Mustangs as well as the Saleen S7 supercar, originally built from the ground up as a racecar before being spun out into a production roadcar.
“That was a great learning ground, because I worked for some of the best-known engineers in the industry, and I got to work on car designs that had stemmed from numerous race winners, including winners of the 24 Hours of Le Mans’ GT class,” he adds.
“You got to see first-hand how racing drives automotive innovations within strict timelines, so when the opportunity came to move over to MillenWorks, which had been founded by the famous rally car driver Rod Millen and was a really sought-after place to work, I couldn’t pass up the opportunity.”
MillenWorks’ engineers were known as the ‘suspension gurus’ for the US military, and indeed Fisher soon found himself working on a new kind of vehicle demonstrator: a hybrid-electric military transport vehicle that soon became known as the MillenWorks Light Utility Vehicle.
“At the time, there really wasn’t anything to base that powertrain on,” he says. “Sure, the Toyota Prius had just come out, but this was a military product, so we built it from the ground up, and it was later used by Textron as a contender for the Joint Light Tactical Vehicle contract for the US military.
“We built the battery modules, battery pack and vehicle structure all from blank sheets. We even rented a plot of land and built some test courses that mimicked proving grounds such as the Aberdeen military test course in Maryland, so that we could run tests and provide data to the DoD.
“That was a 14-month project in which we designed, prototyped and tested a vehicle with all sorts of new technologies. It was a never-before-seen type of electric drivetrain, with a couple of 150 kW UQM motor and inverter pairings for traction, integrated at the front and rear in an all-wheel-drive configuration, which led us to call it a road-coupled series parallel-hybrid.”
Its powertrain incorporated a Steyr turbodiesel and generator as its range extender, mounted in line with a hybrid transaxle assembly (which happened to be built around an Eaton automated manual transmission system) to the rear wheels. The pack was constructed around 18650 cells from A123 Systems, traditionally used in power tools, and independent semi-active damping suspension systems were integrated at the front and rear.
Into Eaton
After a year working as an independent engineering consultant, largely on projects alongside his former employers and teammates across Saleen and MillenWorks, Fisher began working as a project design engineer for Cooper-Bussman, with a similar focus to where he had left off at MillenWorks – on electrical engineering work for vehicles.
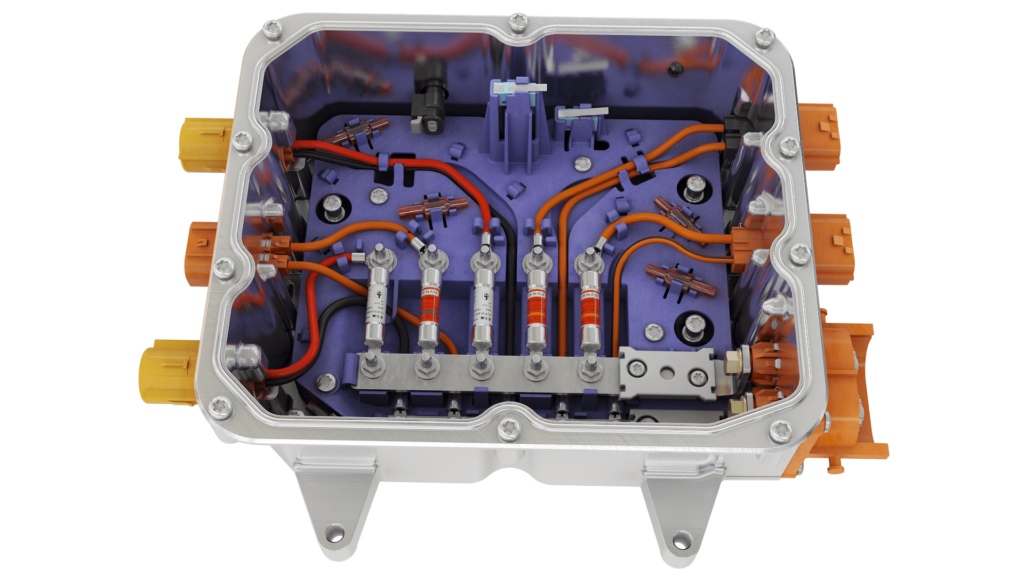
“I joined them in 2010, and soon found myself specialising in their power distribution systems, and then in 2011 they were acquired by Eaton,” he says. “Soon after their product manager for power distribution left, as the leading engineer in that department I stepped into the role to start handling some of the business side of things for Eaton’s power systems product line. It also allowed me to start coordinating some of the strategy of how the line was going to develop based on where customers – that is, vehicle manufacturers – were taking their designs.”
Over the following few years, Eaton gradually began changing its power distribution technologies from copper and plastic wiring-based systems towards printed circuit boards, in essence going from classic bulky fuse boxes to slimmer, smart fuse boxes with microcontrollers running CAN buses and exporting diagnostic data before and after a fuse had blown or other incidents occurring.
“It was also when we began looking at HV power distribution opportunities,” Fisher says. “Some of the projects we have now were envisioned back then, in a ‘hybrid group’ within Eaton that had previously launched an electric hybrid drive unit by procuring parts and working as the systems integrator.
“We’d sold that platform to some big customers, including Daimler and Navistar. I looked at its powertrain from a power distribution perspective and told the team I saw some opportunities there. For instance, there was a project with the US Department of Energy at the time called Supertruck where they were trying to drastically reduce the emissions and boost the efficiency on older freight vehicles, and after talking with potential customers there we started giving technology demonstrations and prototyping HV distribution systems for them.”
Safety at high voltage
By this time, the consensus had grown within Eaton that HV powertrain technologies were going to become a critical area of business; less clear was when it would happen, and hence when the right time to ramp up investment into e-mobility would be.
It was around 2014, soon after Fisher started moving back from business-related decision making into engineering team leadership, that Caterpillar – one of Eaton’s key customers – formulated a strategy to electrify all 135 of its platforms.
“At the time, we were working on their second HV inverter solution for an electrified paver – both the main powertrain inverter and an auxiliary inverter for powering lights, coffee machines and so on for night-time jobs,” he says.
“That was really our first production e-mobility solution. And things really took off soon after, in a side project [still at Eaton] where our team was evaluating HV power distribution for passenger cars, both as internal r&d and also for some companies. Some Ford engineers for instance sent us a specification for some HV vehicle systems to query what we could make in line with them.
“That drove us to start prototyping HV fuse boxes, starting with industrial fuses that traditionally didn’t get more than five thermal cycles in a day, but when you put those on an EV, a single acceleration and deceleration counts as one cycle.
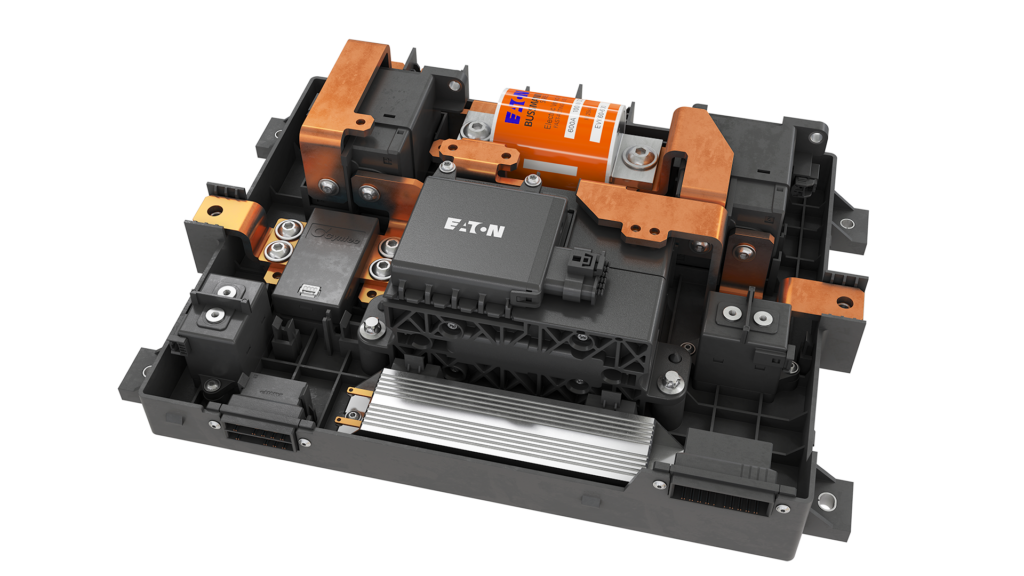
“So now they were being cycled hundreds of times per day, and hence they were failing far earlier than they usually did. So we quickly devised technologies for diagnosing when fuses were close to failure, and worked to educate the automotive industry about the importance of simulating for the lifetime of fuses in EV applications before determining fuse sizings.”
At the time, Eaton had also grown its capabilities in HV DC-DC converters and industrial controls. These, combined with its inverter and fuse box capabilities, were crystallised as the Eaton eMobility business, for which Fisher was named manager of new product introductions across HV power distribution and production systems in 2018, when Eaton formally launched the eMobility business, and then engineering product line manager for such solutions in 2021.
Although Fisher started alone in the role, he has since grown his team to 53 engineers, and leads them in r&d for commercial EVs and electric production passenger cars.
“Our automotive products typically fall into two categories: HV auxiliary fuse boxes, and what a lot of OEMs might call a ‘battery junction box’ or ‘battery electrical centre’ – essentially the main distribution and protection point out of the battery pack,” he explains. “Also, we leverage technologies being developed in other parts of the business, which has contributed hugely to our newest and perhaps most successful product, the Breaktor.”
The Breaktor is an HV circuit-breaker developed specifically for automotive use, and is designed as a replacement for traditional contactor-and-fuse junctions in EVs. While fuses must be replaced after shorting, the Breaktor’s mechanical contactor linkages can close or open to connect or disconnect (respectively) HV power to or from the drivetrain, based on the turn of the driver’s ignition key. Most critically, it can rapidly open within 4 ms of a short-circuit or overcurrent to break an HV connection, and then be closed later to reconnect the HV network, without needing fuses.
Fisher also mentions an isolation measurement system, now available for reporting the resistance between HV battery packs and the chassis, and hence detecting when isolation systems are starting to break down and when shutting off the HV power delivery might become a safety-critical need.
“The early years of EVs were fraught with fears over their safety, not only from passengers but from first responders, technicians who had to work on them, and others, so we’re constantly focusing on designing our power management and safety systems really well,” he says.
“We’ve taken lessons from Eaton’s existing HV distribution technologies across the aerospace, industrial and residential sectors and worked to apply them in the automotive space, changing our simulation and validation approaches where necessary to produce something that will ensure OEMs can make vehicles that are fully protected.”
Future plans
Although the Breaktor is rapidly becoming Eaton eMobility’s star product, Fisher and his colleagues maintain an eye towards the future, and what HV safety systems for EVs might look like in the next 5-10 years.
“Everything in EVs is moving towards more solid-state solutions, so instead of mechanical switching devices, I think we’re going to see distribution systems built around IGBTs and FETs made from advanced semiconductor materials in the future,” he says.
“The Breaktor is an order of magnitude faster than fuses, and IGBTs are an order of magnitude faster than the Breaktor. They’re too expensive to use in HV distribution and protection right now, but volume production will drive that down.
“We already have LV systems in that regard that are solid-state, designed around FETs. The level of control you gain, and the amount of packaging volume you reduce are too beneficial to ignore as HV technologies advance, and new microcontrollers and diagnostics algorithms mean that connected, software-defined EVs can become safer as they get smarter.
“And as battery cells gain more energy capacity, that’s naturally going to drive higher requirements in safety system. I think that’s going to be a healthy progression that will make EVs more usable and accessible for everybody.”
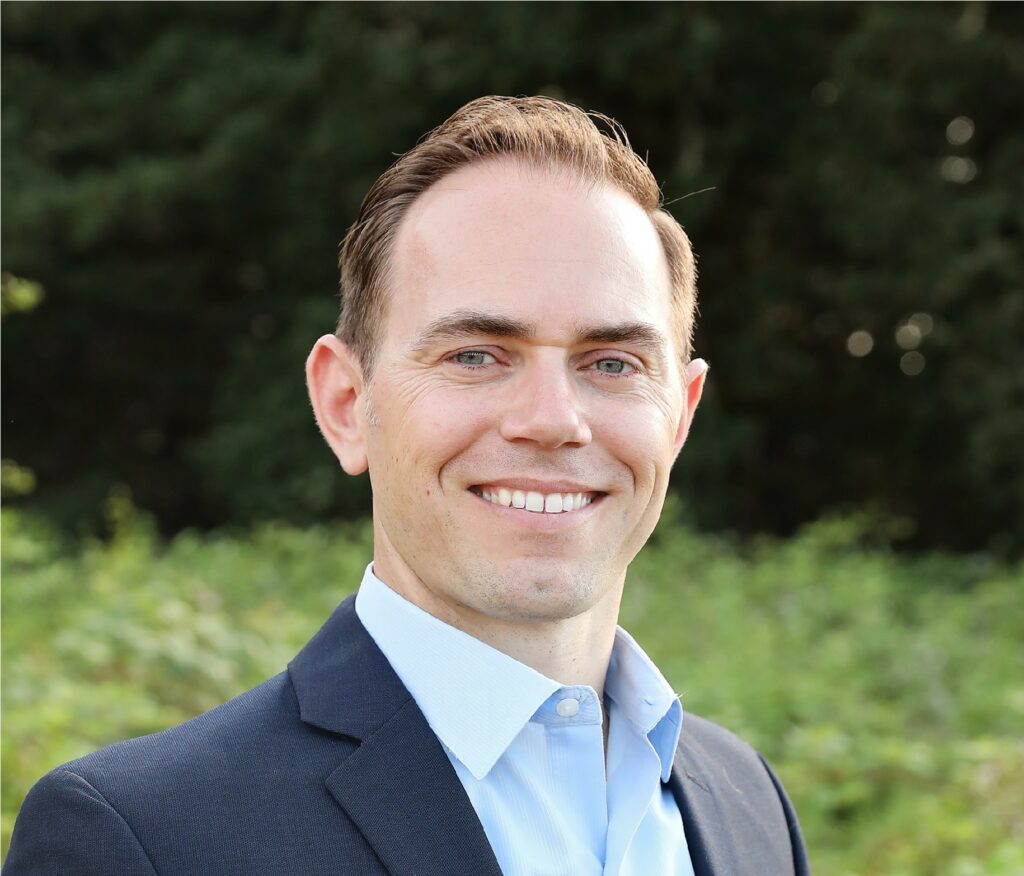
Brandon Fisher
Brandon Fisher was born and raised in Oregon, attending Oregon City High School before starting a Bachelor’s Degree in Mechanical Engineering at the California Polytechnic State University which lasted 5 years.
In the final year of his degree programme he began an engineering internship with US sportscar company Saleen, which was first extended and then transitioned into a full-time role as a chassis systems engineer. In December 2006 he became a project engineer at MillenWorks (known as Rod Millen Motorsports until 2005 and acquired by Textron in 2011), a position he held until February 2009.
After a year of independent engineering consultancy, Fisher moved to work as a project design engineer for Cooper-Bussman, which was acquired by Eaton. In the years following the acquisition, he moved up the ladder of Eaton’s engineering management until becoming engineering product line manager for power distribution and protection systems for Eaton’s e-mobility business in January 2021.
ONLINE PARTNERS
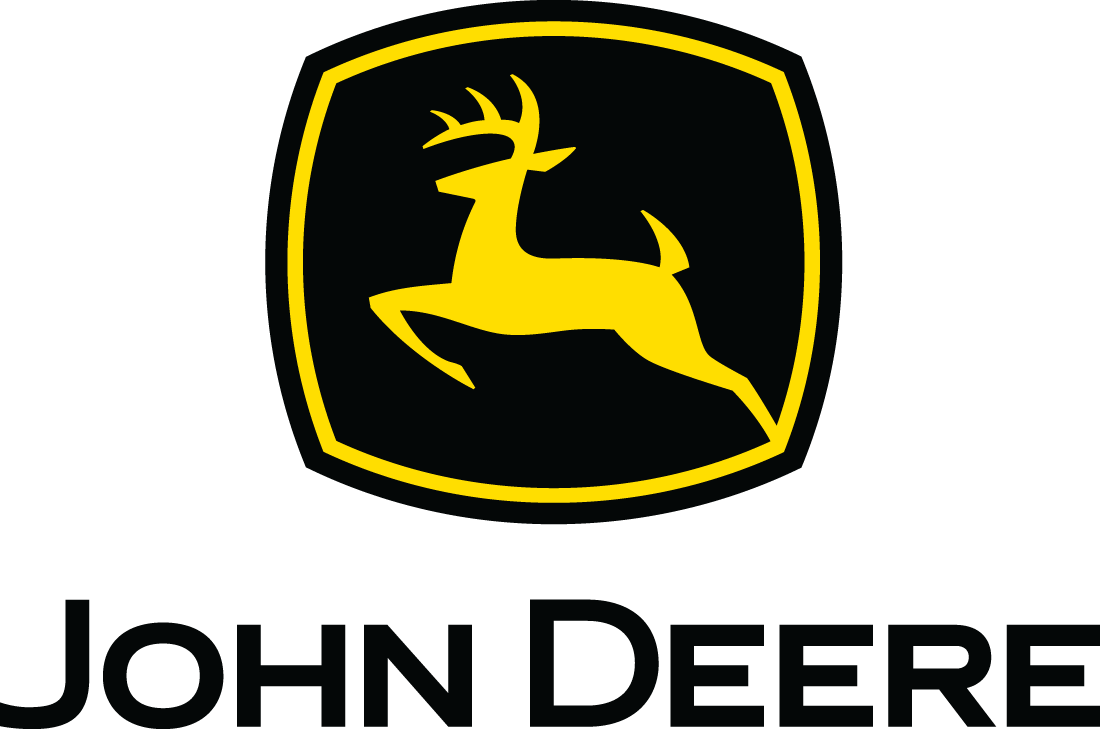
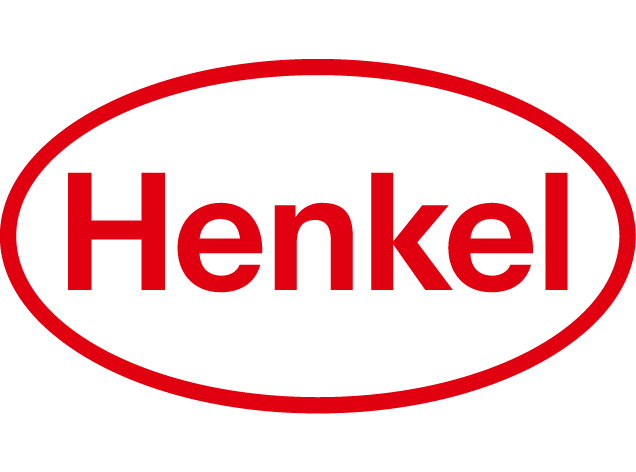
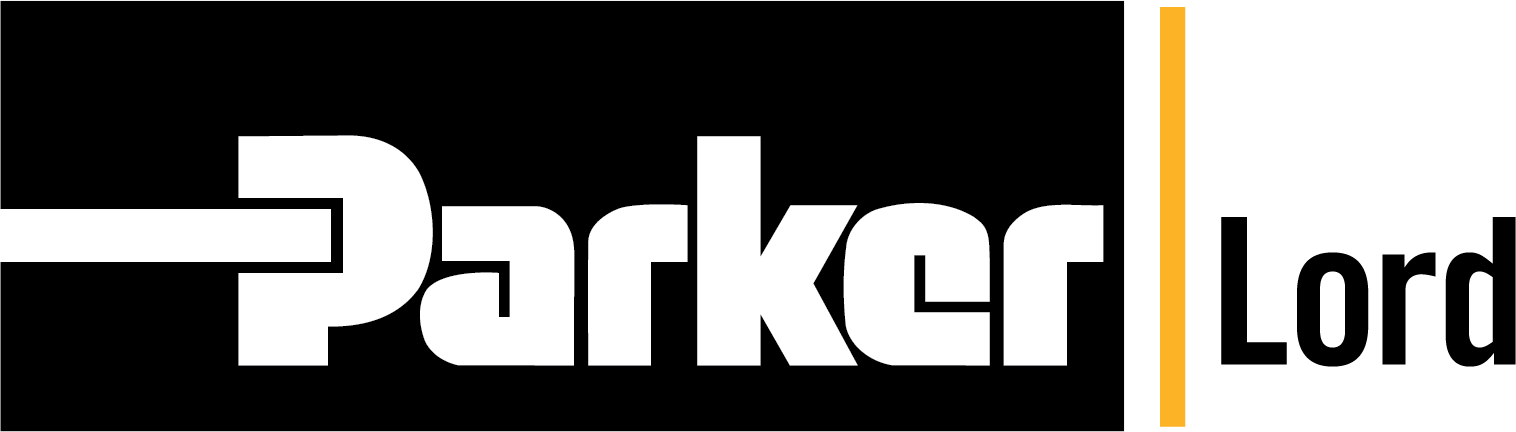
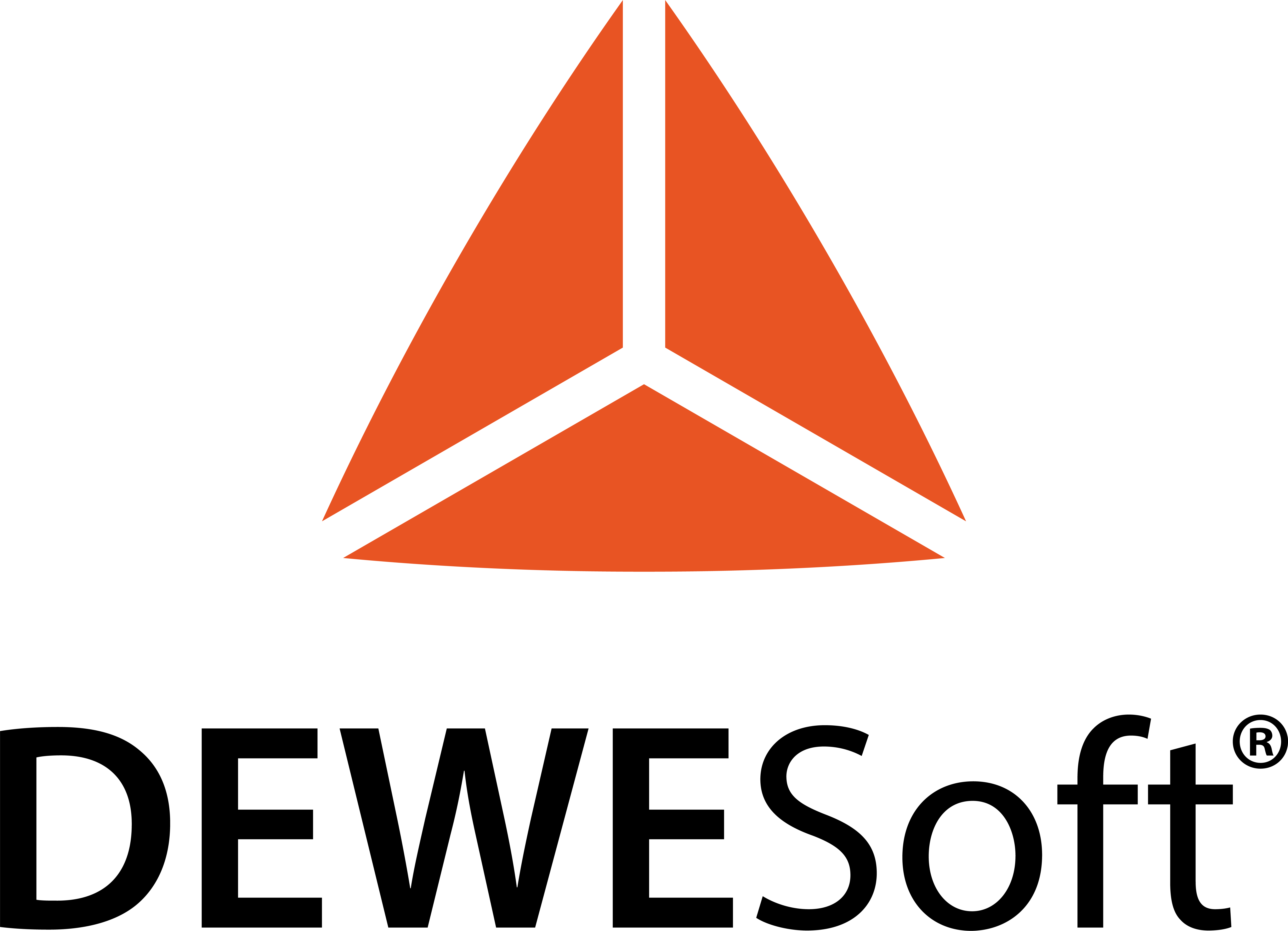
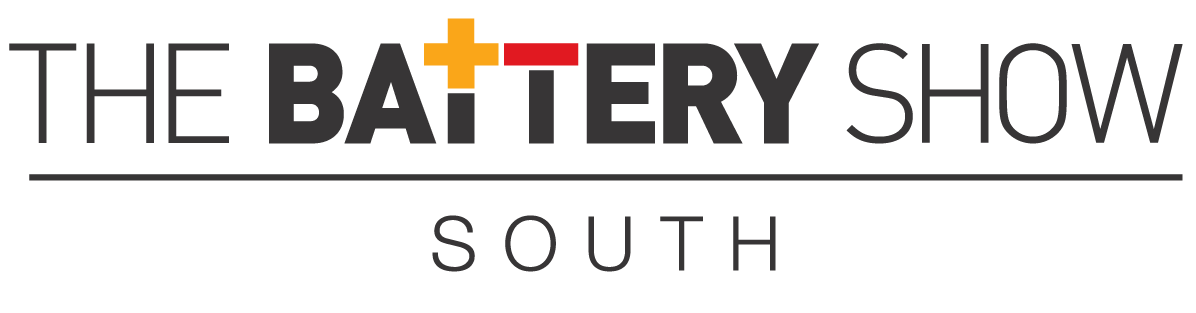
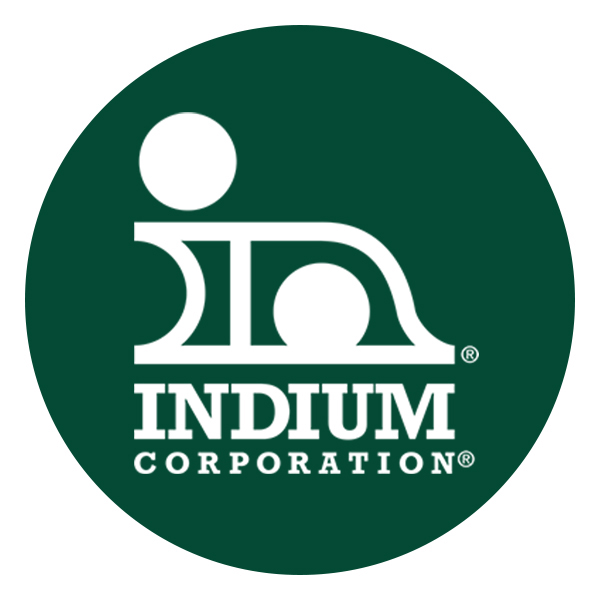
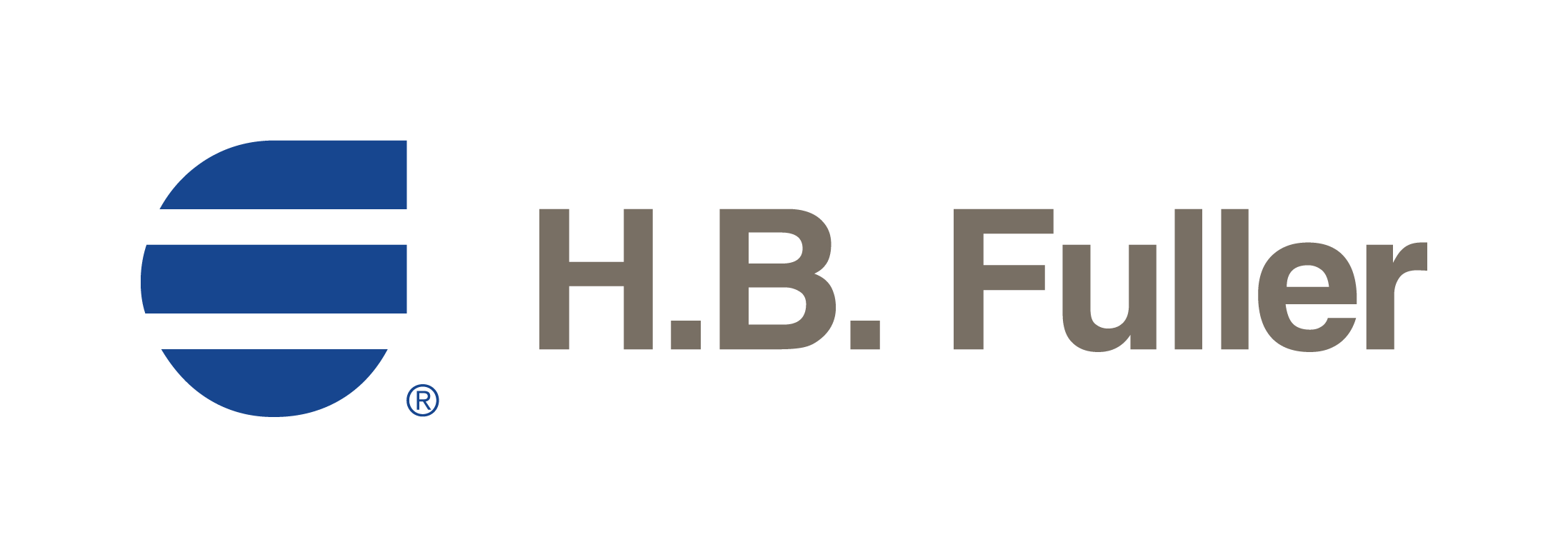