BorgWarner’s plans for high-voltage commercial vehicle power systems
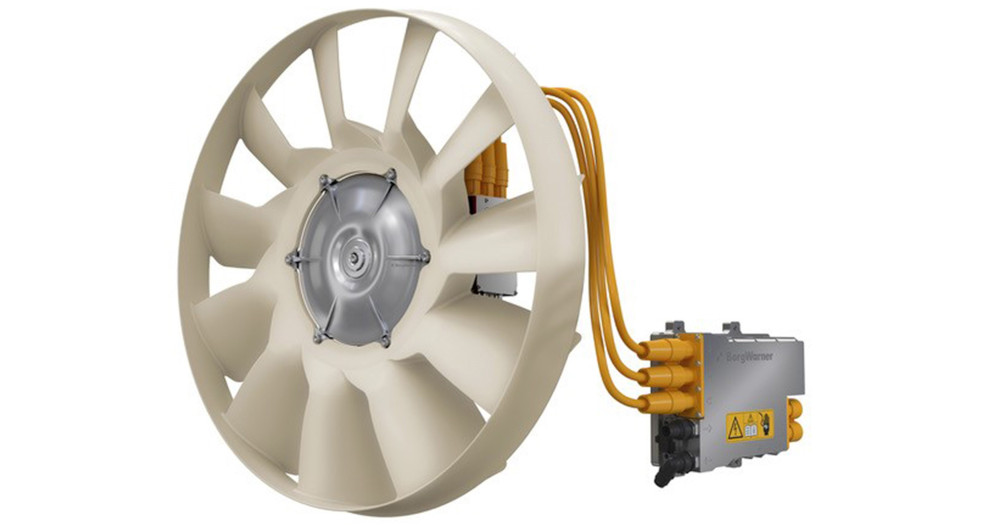
Total cost of ownership, long service life and packaging efficiency that frees mass and volume for cargo and passengers are essential requirements for all commercial vehicles (CVs) – and meeting all those needs is a challenge as the sector transitions to electric power, according to Harry Husted, BorgWarner’s vice-president and CTO (writes Peter Donaldson).
Speaking at the IAA Transportation 2022 event in Hanover in connection with the 800 V battery, inverter, motor, cooling and charging system the company is evolving for electrified CVs, he said the vehicles benefit from 800 V systems because they can operate at the high continuous powers they need without running into constraints connected with the sizing of busbars and cables.
“At a certain power level the 400 V class becomes unmanageable, and the 800 V class is much better matched to the power levels that we see,” he said. “When you double that voltage you cut the current in half, and it keeps the currents and the sizes of the cabling and the busbars manageable.”
Small ∆T, big e-fan
The company’s headline product is a new electric fan for cooling the kind of high-powered fuel cell stacks now going into large, long-range trucks and buses. Because of their size and power output, these systems have to reject large amounts of heat, Husted explained.
“Fuel cell vehicles have significant thermal management needs, even though the temperature of the liquid water coming out of the fuel cell stack is fairly low,” he said. “So the ∆T – the difference in temperatures – between the cell coolant and the ambient air is quite small, which means you need to move a lot of air through large heat exchangers.
“The hot water coming out of a fuel cell is at about 80 ºC, and if you are in a high ambient environment in certain parts of the world, the air you are using to cool it might be at 40 ºC, so you have only 40 ºC of ∆T.”
Another application for which Husted reported a strong pull from the industry is cooling for braking resistors. Typically, a large vehicle will rely on its traction motors in regenerative braking mode to slow it down, but in long hill descents with a heavy load and the battery in a high state of charge the regen will put out more energy into the battery than it can take up.
“For this situation, trucks are being fitted with very large braking resistors,” he said. “Instead of pushing that energy into the battery pack, we will be pushing it into the braking resistors. Those resistor systems need to be cooled, which means that again we have to move a lot of air.”
To meet these needs, BorgWarner is developing an e-fan module equipped with a large fan driven by an 800 V electric motor rated at 40 kW continuous power output. The fan is undergoing tests in preparation for production, and there was a working example on display at the show.
While the e-fan is the company’s latest 800 V accessory system, it is already supplying an 800 V, 300 bhp motor and inverter module to drive the hydraulic pumps in waste management vehicles. “Garbage trucks have a lot of moving parts, and they all exploit the power and size economy of hydraulics,” Husted said.
While direct electric actuation will be selectively applied where it makes sense, he sees the use of an efficient motor to drive a hydraulic pump as a great transitional solution. “It allows you to take a lot of proven, durable technology, make a simple system change to the drive unit, and electrify that truck,” he explained.
‘Ultra-flat’ battery modules
BorgWarner also showcased its ‘ultra-flat’ battery module concept that brings the pack height down to less than 120 mm; it is aimed at lightweight CVs and buses.
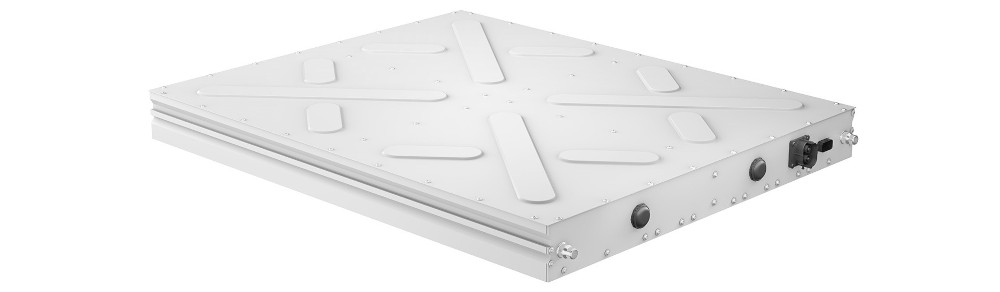
“This is partly about creating more room for people and goods, but it’s also about offering packaging options,” Husted said. “We are seeing a need to put the battery in the bottom of the vehicle underneath the load floor while maintaining ground clearance.
“We are also offering a second variant that is more prismatic in shape, so that batteries can fit into available spaces around the vehicle.”
These battery modules are now in development, and to achieve the pack-level energy density they want, BorgWarner’s engineering team is addressing the packaging, routing and structural challenges.
“A battery pack is not just a collection of cells in a box,” Husted said. “We need a strong thermal aspect to manage the temperature, we need a BMS that monitors the cells and helps with control, and the other crucial element is structural.
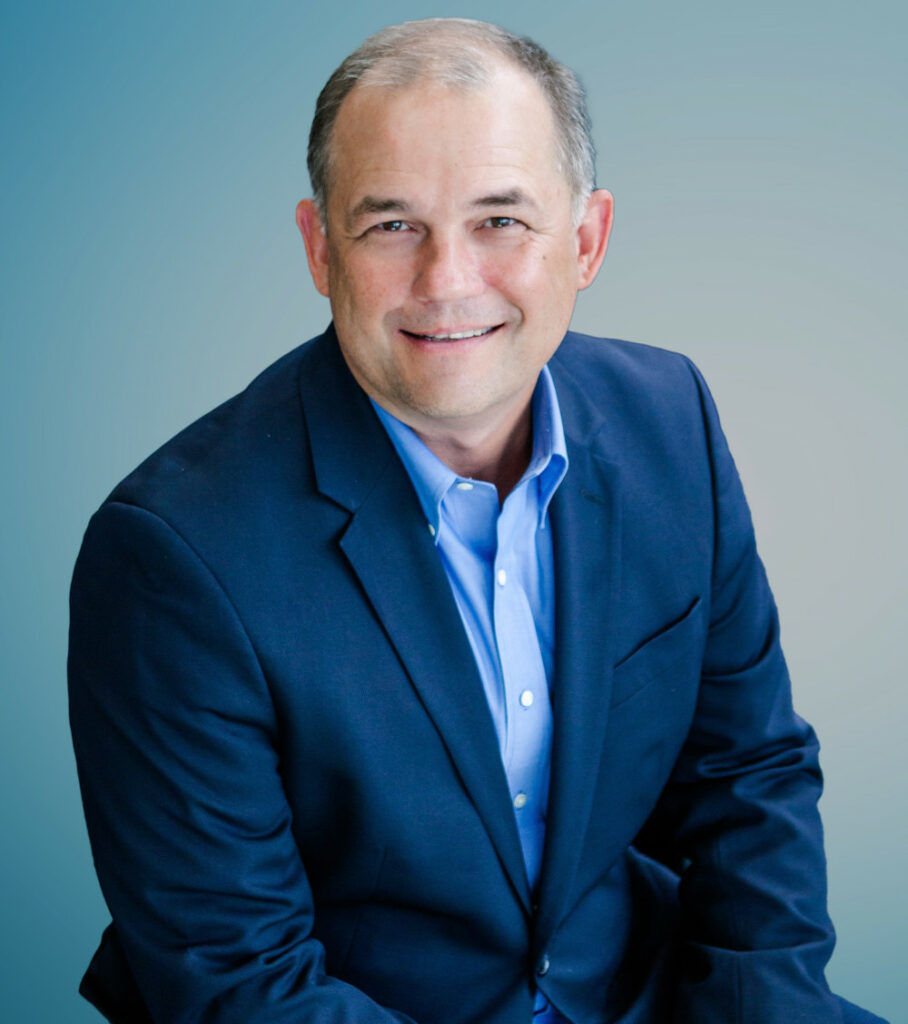
(Images courtesy of BorgWarner)
“Cells are still fairly heavy, and when you concentrate that much mass you need a strong structure so that it will handle the long-term stresses of the application, including vibration.
“So getting that multi-disciplinary work done to form that pack into what is essentially a high-power electrical product is a challenging engineering exercise, but our team are experts who have done it many times before.”
In choosing the chemistry for the cells, BorgWarner has focused on energy density to help customers with packaging and range, while balancing that against recharging time and cycle life, Husted said.
On the inverter side, the company has built on the capabilities it acquired when it bought Delphi Technologies, particularly regarding its compact Viper power switches, which are liquid-cooled on both sides. Husted explained that this has enabled BorgWarner to get more electrical performance from the switches without exceeding their thermal limits.
Staying with that principle, BorgWarner has replaced the original silicon IGBTs with silicon carbide MOSFETs, which has enabled higher switching frequencies and a doubling of the voltage to 800 V.
Grid to wheels and back
The final area of technology that allows BorgWarner to offer grid-to-wheels electrification is stationary charging. In addition to its Iperion 120 charger we reported on some time ago, the company has acquired Rhombus Energy Solutions and its bidirectional chargers, which were the first to be certified to the US standard UL1741 for vehicle-to-grid capability.
“We are setting ourselves up to provide support to local electrical systems and to expand into supplying power back to the grid when the time is right,” Husted said.
ONLINE PARTNERS
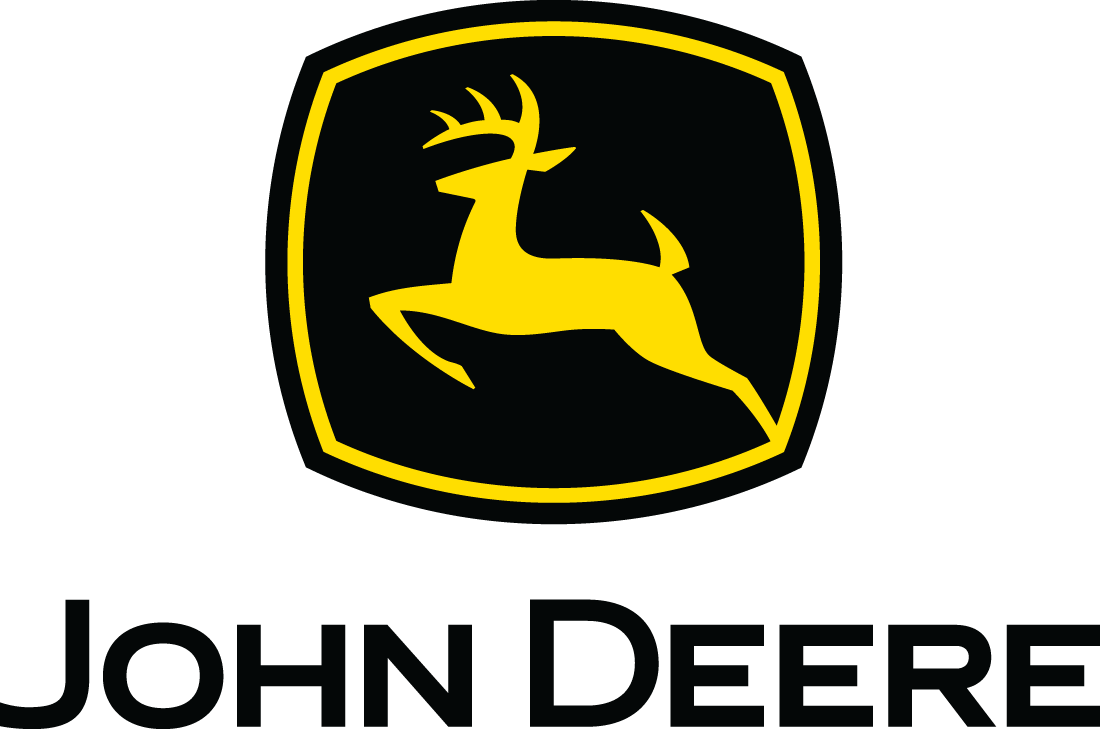
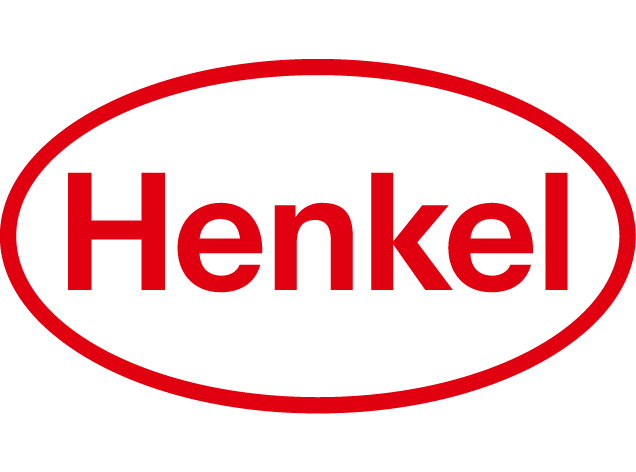
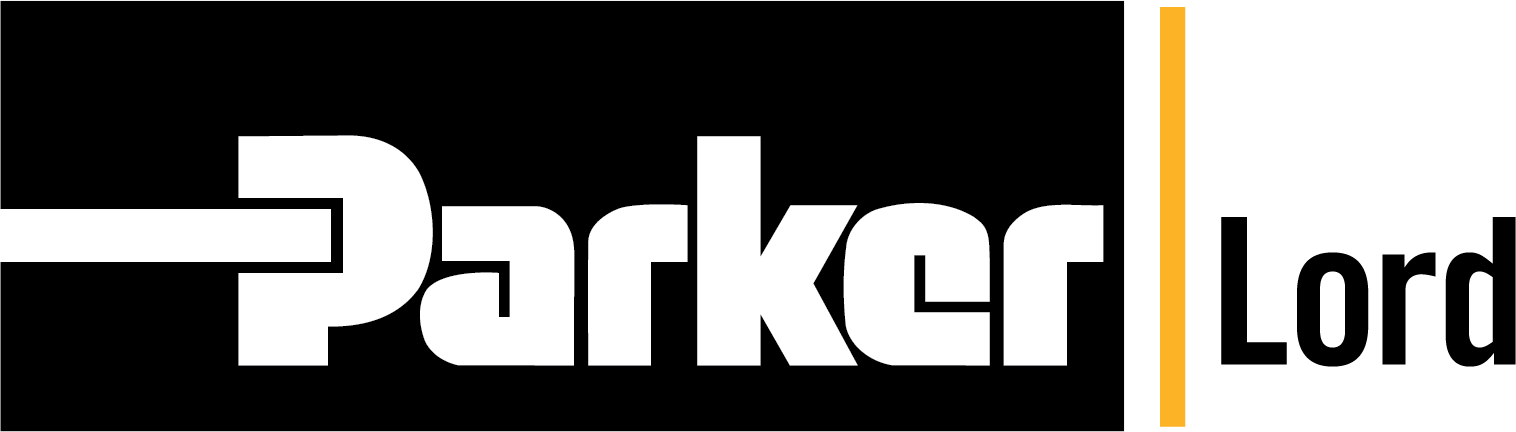
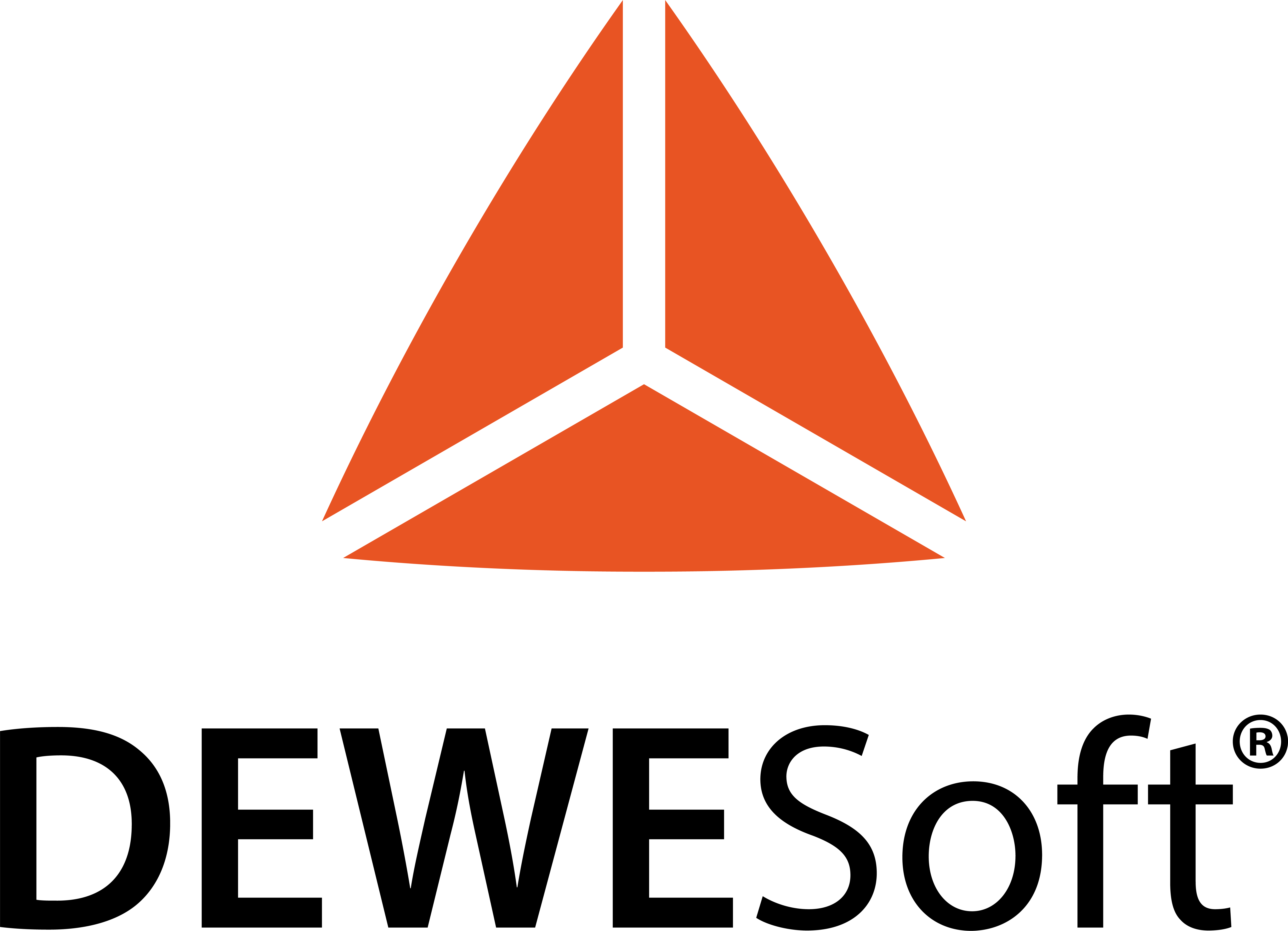
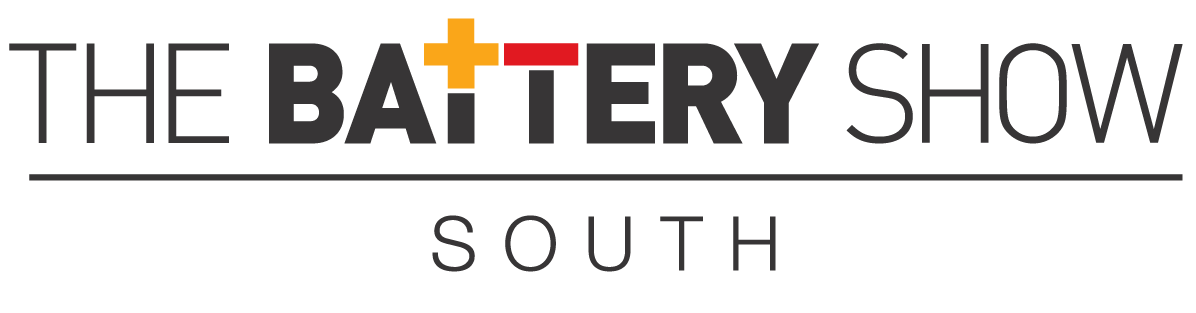
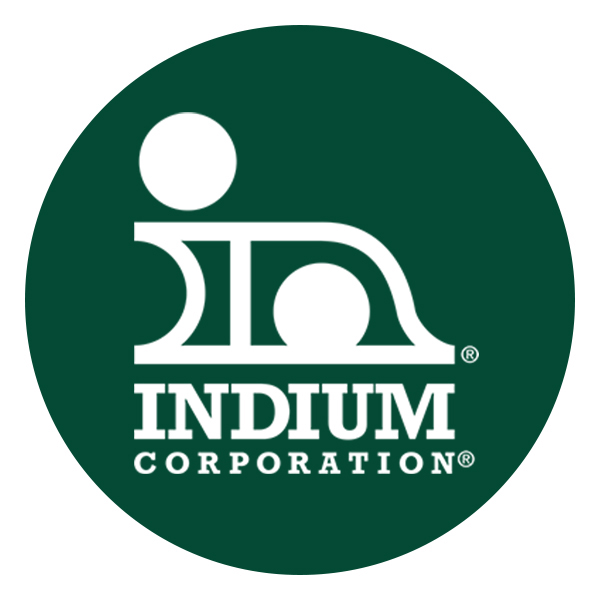

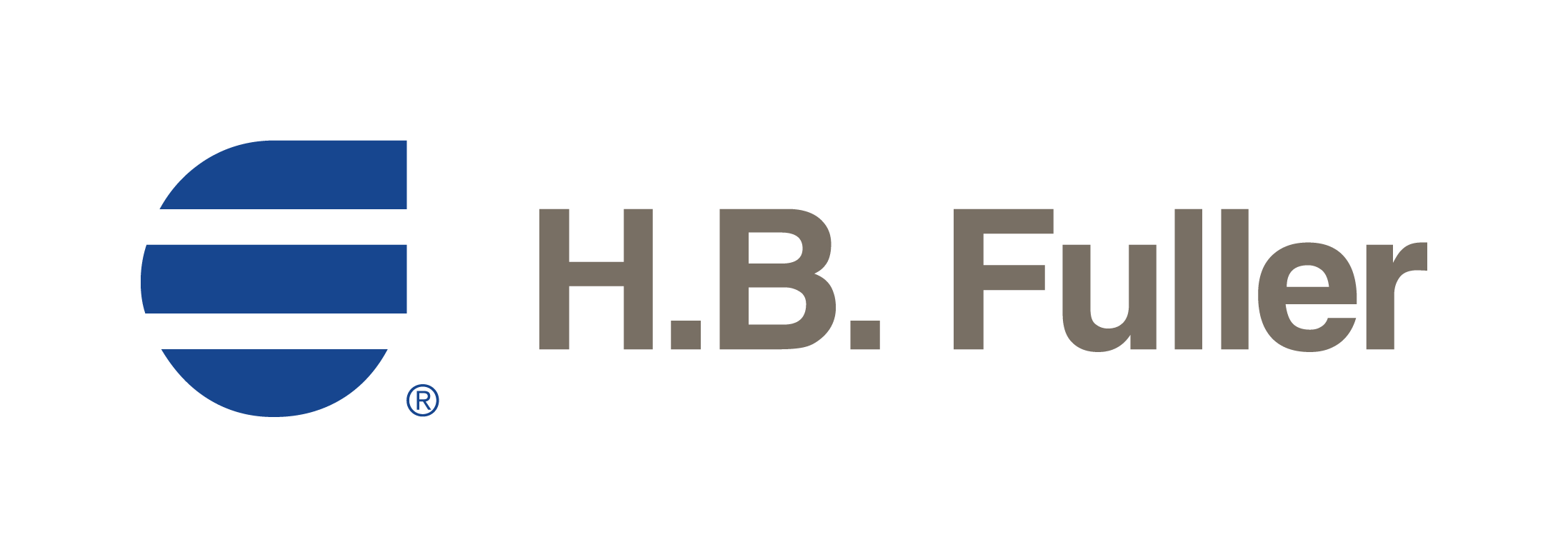
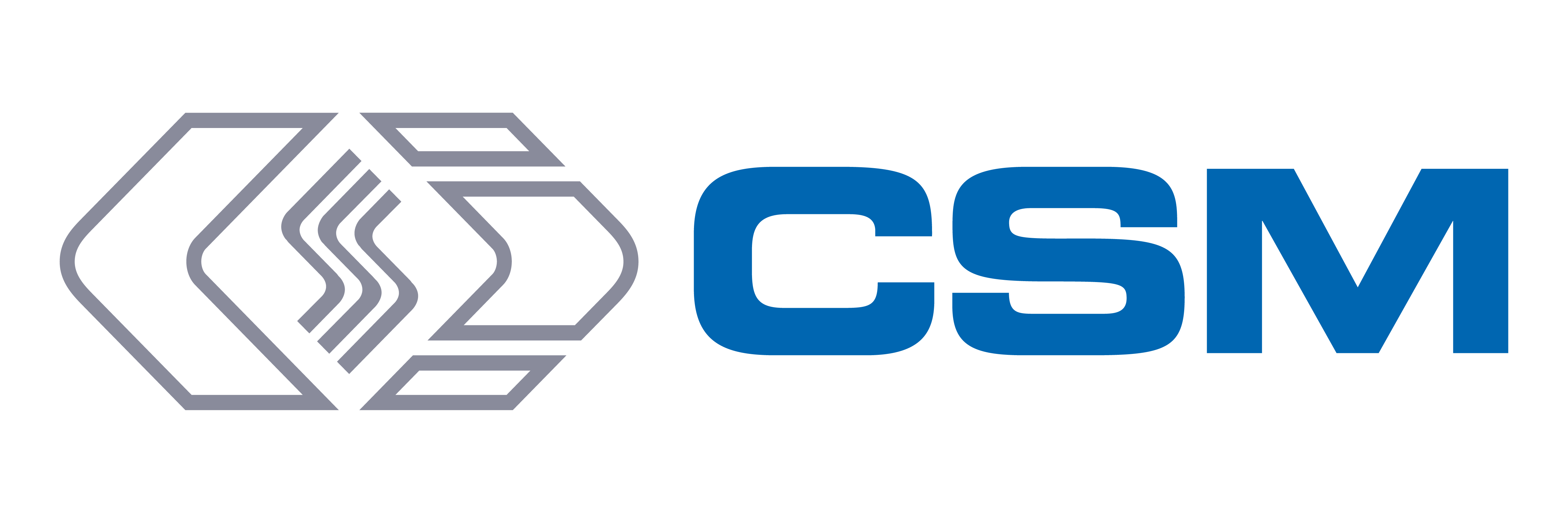
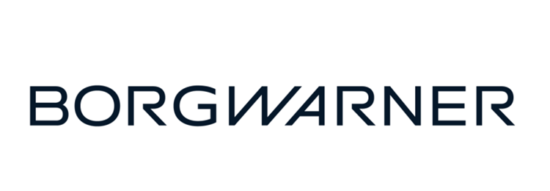