Battery Show North America 2022
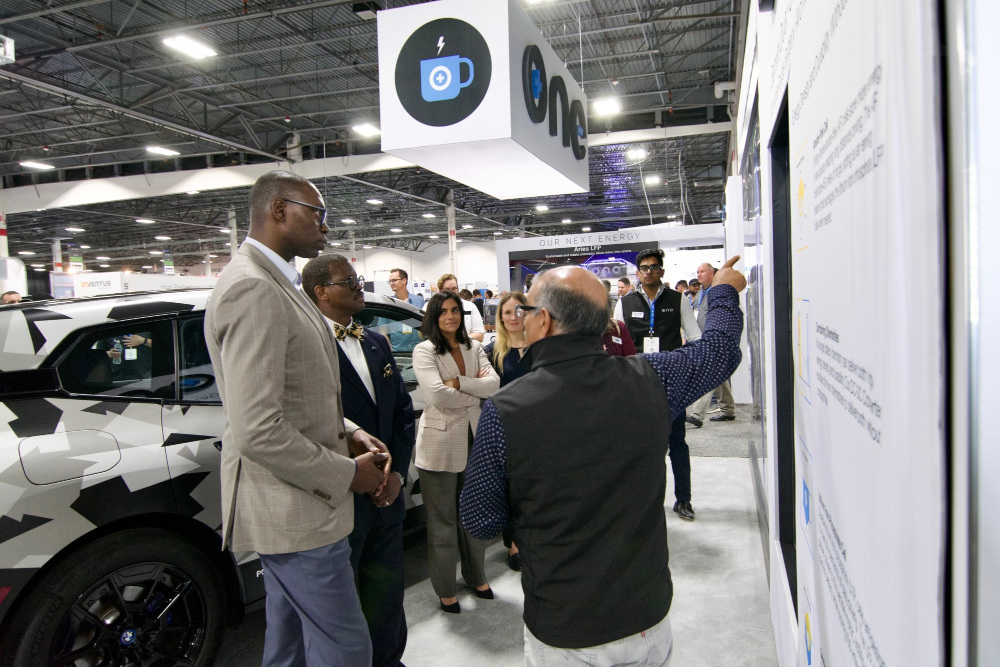
(Courtesy of the State of Michigan)
Supply and demand
Peter Donaldson provides some highlights of this key event, focusing on new products and technologies that offer solutions to pressing challenges
Held in Novi, Michigan, in mid-September, the Battery Show North America focused attention on numerous new products, from test equipment for battery development and manufacture to batteries, safety devices, power electronics and advanced sensing concepts.
Novonix supports battery development with ultra-high precision coulometry (UHPC), which the company describes as a vital tool in the development of new cell chemistries and designs. Novonix representatives presented their new 10A UHPC battery cycler module with eight channels at the show.
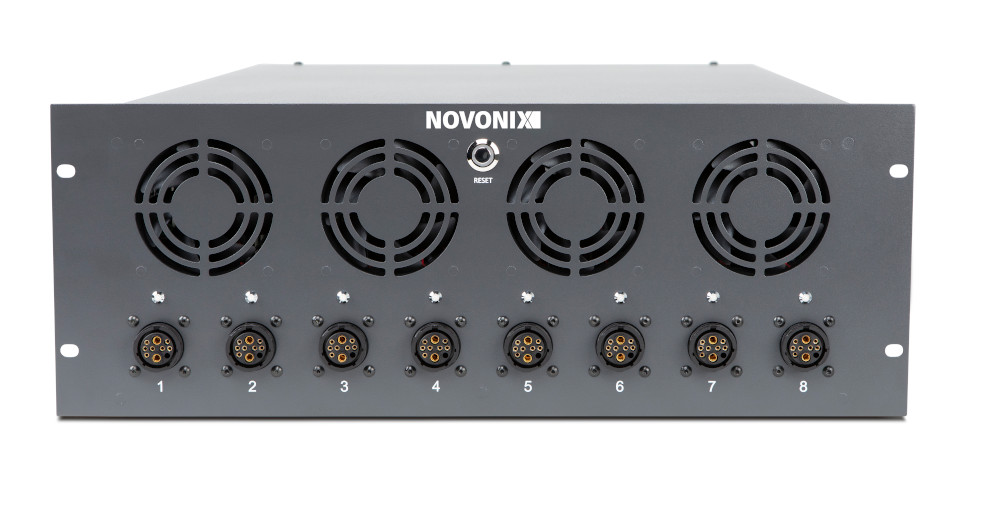
A coulomb is a fundamental unit of electric charge – the number of electrons that pass a given point in a second to produce a current of 1 A. In the battery field, however, capacity is typically measured in ampere hours (Ah). UHPC measures capacity by making extremely accurate and precise measurements of current, voltage and time through multiple charge and discharge cycles of cells under test, explained Alex Parkinson.
Traditionally, he said, testing a new cell involves connecting it to a battery cycler then charging and discharging it repeatedly, and analysing current, time and voltage data to draw inferences about what is happening in the cell and how it performs.
UHPC, he said, uses extreme accuracy and precision in measurement to “unlock a new class of high-resolution data” that can contribute to very high fidelity models, which can be used to understand a battery’s electrochemistry and the mechanisms by which it might fail. He was, however, keen to stress that UHPC alone does not predict cell life. “What UHPC can do is deliver very good data, including data you just can’t get otherwise.”
Parkinson noted that the accurate and precise measurement capabilities embodied in the company’s hardware comes from good circuit design, with great effort put into tackling all sources of error, including temperature fluctuations and vibration for example.
“We thought a lot about all those sources of error and designed our components in a way that minimises them,” he said. “We also highlighted those points in our recommendations for how the system should be used.”
Stephen Glazier chose measurements of coulombic efficiency – the discharge capacity divided by the charge capacity of a cell – to explain the difference between accuracy and precision in this context, and its importance. He showed a plot of eight cells being measured by other cyclers including Novonix’s new 10 A module.
“Some of those cyclers have good precision, cycle-to-cycle measurement being pretty consistent, but poor accuracy between cells when making the exact same measurements,” he said, contrasting this with the much more consistent performance of Novonix’ UHPC system.
“Its performance is identical in coulombic efficiency measured to the fourth decimal place, but on the other cyclers if you had a slight difference between two cells you wouldn’t be able to distinguish it from the noise.”
He also emphasised two other important metrics on which UHPC produces accurate data. The first is capacity fade, or how much capacity is lost during every cycle, a figure that is used in estimating cell lifetime in terms of cycles to 80% of original capacity.
The other is charge endpoint capacity slippage, which is hard to measure accurately but provides information on how much excess charge from reactions other than those that lead to capacity fade are happening in the cell. The reactions generate current and can indicate the presence of hidden mechanisms that can lead to sudden cell failure, such as oxidation of electrolyte at the cathode, which leads to electrolyte loss and dissolution of transition metals from the cathode.
“Some of these things lead to the rollover failure that you can’t really predict when you just look at the capacity fade plot over a few hundred cycles, as capacity then drops off suddenly,” he said. “With UHPC you can start to see these trends.”
The 10 A UHPC channel module is designed to complement and integrate with the existing 20 A and 2 A modules, offering eight independent channels each with six high-precision current ranges (100 µA, 1 mA, 10 mA, 100 mA, 1 A and 10 A).
Parkinson said Novonix re-engineered the hardware and circuitry to provide a more robust platform for future growth in capability. “We used a single reference chip to tie all eight channels together,” he said. “This architecture means we can get tighter calibration from channel to channel, and if there is any drift on an individual channel, it can be quickly detected.”
Glazier described the 10 A module as a multi-purpose device that offers a lot of flexibility in a 4U enclosure. “Imagine taking a big, 50 Ah cell and running a charge/discharge protocol that involves a C5 charge and a C500,000 charge on one device, all automatically, all while measuring current with a precision of better than 20 ppm.”
In terms of software, the focus is on ease of use and intuitiveness, so that scientists and engineers using the equipment don’t have to think much about setting the equipment up, but can concentrate on their data.
Glazier added that the new hardware development opens up the opportunity for more flexibility in operation, and that the company is exploring future software releases that could unlock more capabilities and features for UHPC systems.
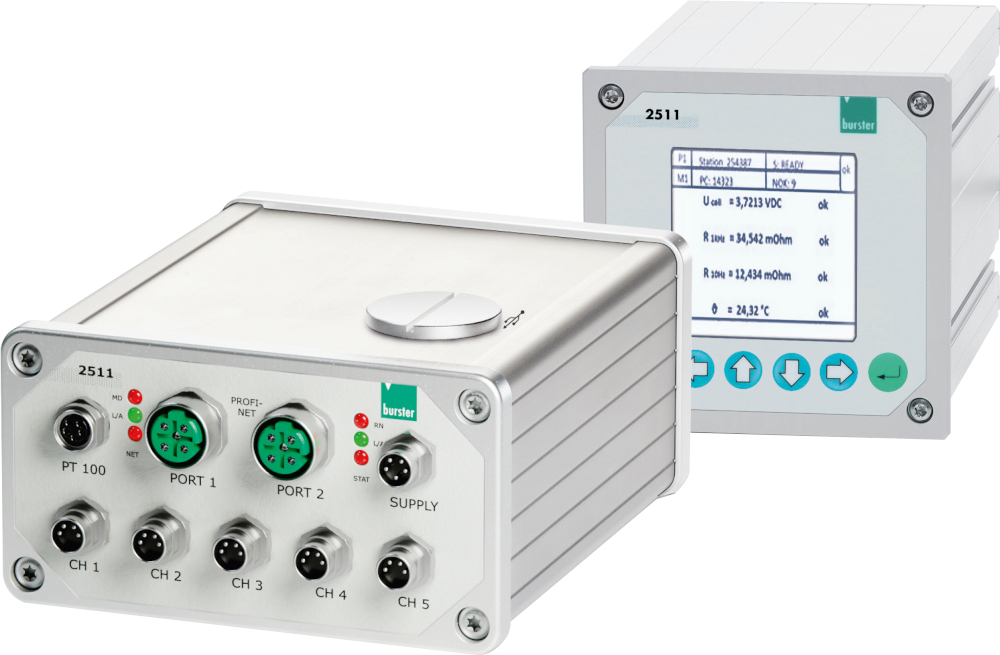
Burster showcased its new model 2511 measuring module designed for fast and complete checking of cells and modules in automated battery production facilities, including gigafactories, as a replacement for measuring systems originally designed for laboratory use.
Adam Giorgione said such systems are large and lavishly equipped in terms of functions, but tend to have partially outdated comms and control interfaces.
Giorgione described the 2511 as an innovative, fast and extremely compact measuring module that can be networked using several Fieldbus comms standards.
He said it is aimed primarily at applications in fully automated assembly systems in pack and module production for e-mobility, power tools, industrial vehicles, comms electronics and energy storage. In these environments, compactness, easy integration into modern control concepts and recording of key battery parameters are essential, he added.
The demands on battery testing in such production facilities are high, and among them are interfaces that are easy to integrate and control, and provide fast, reliable and precise measurements and evaluations, he said. Also essential are compactness and ease of installation, along with reliably reproducible contacting of cells, and options for multi-channel measurement on very large pack, module and cell-to-pack applications.
“Another aspect is the regular checking of the measuring systems, an important factor in achieving reliable, correct and reproducible results,” Bodemer said.
Giorgione also emphasised that the 2511 series is easy to integrate into existing or planned control concepts through Fieldbus, supporting both cyclic and acyclic measuring options via the Profinet industrial Ethernet comms standard. It is also possible to transmit measured values and evaluation results, and product- or order-related data via Fieldbus, and the system also enables parametrisation and complete back-up at the control level, he said.
“Measurement of the open-circuit voltage is still widespread, but not always meaningful as a unique criterion,” he said. “Only the determination and evaluation of the AC/DC impedance values (at 10 Hz and 1 kHz) provide information about battery quality and allow conclusions to be drawn about electrode and electrolyte properties, as these have a significant influence on the ageing process, state of charge (SoC), capacity and service life.”
With up to five channels, the Burster 2511 measures open-circuit voltage and pack voltage as well as the real impedance value with configurable measurement frequencies. Made from aluminium, Burster 2511 modules weigh about 500 g, have dimensions of 104 x 54.6 x 120 mm, and meet the IP54 ingress protection standard.
The core component is what Giorgione described as a fast and powerful microcontroller that includes a synchronous 24-bit double analogue-to-digital converter with switchable pre-amplification, and an ARM Cortex processor for internal control.
“The impedance is measured according to the galvanostatic principle, the current is applied in a discharging manner, and the test object serves as the current source,” he explained. “The test object is subjected to a medium direct current using a complex process, which does not represent a load on the cell owing to the very short measurement time. Digital signal processing, various filters and arithmetic algorithms enable the real impedance value of a cell to be calculated.”
Available now, the 2511 modules can be connected into a multi-channel measurement system, both physically through a DIN mounting rail or wall mounting and at the control level through Profinet and EtherCat.
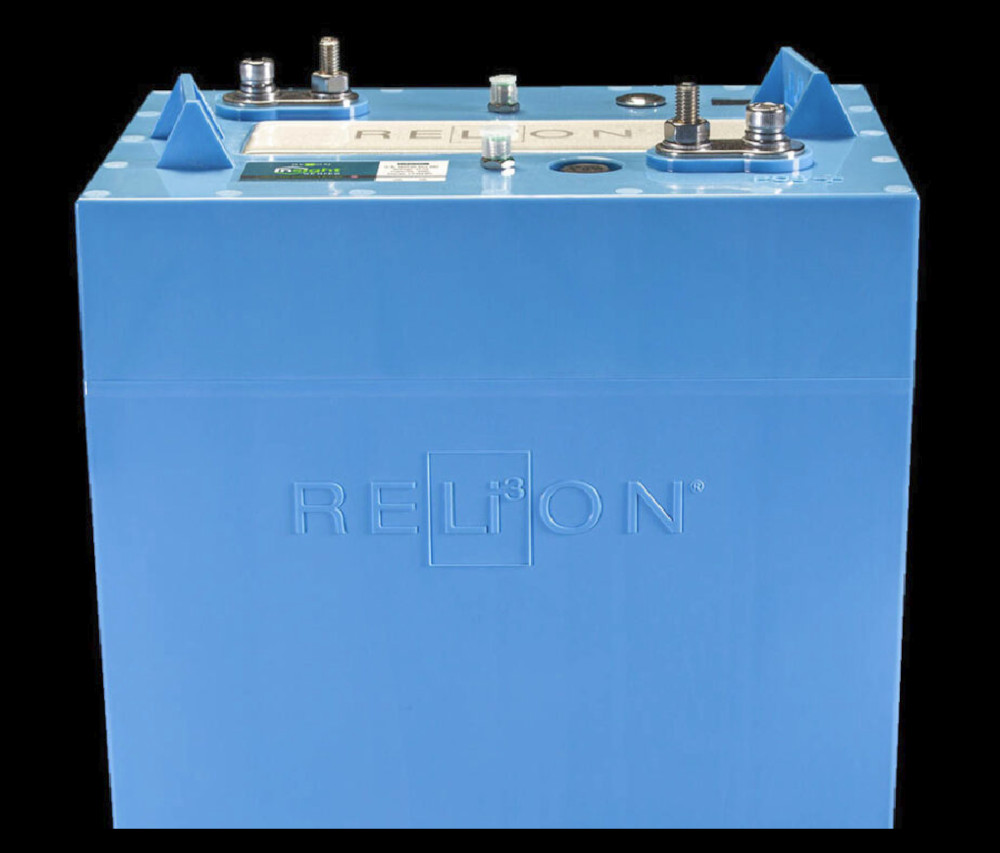
Lithium Power presented its new GC2/GC8 battery range, which is designed for drop-in replacement of lead-acid batteries in light EVs, materials handling equipment, marine applications, recreational vehicles, back-up power and solar energy storage systems. It comes in 12, 24, 36 and 48 V forms.
With drop-in replacements, it is very important that the new lithium iron phosphate batteries are fully compatible with the lead-acid applications and chargers, so the proprietary BMS works with existing controllers and a variety of chargers, Stan Chan said. He added that a parallel connection capability allows the battery packs to remain small and easy to maintain and transport.
“Traditional lead-acid packs are connected in series to reach a certain voltage: for example, eight 6 V batteries create a 48V system,” he said. “However, the overall capacity is limited, and a failure of any battery reduces the overall voltage, causing the whole system to fail.”
That, he explained can be solved by connecting batteries in parallel, with two 48 V, 30 Ah batteries connected this way offering 48 V and 60 Ah. “We have an EV customer who connects thirty-six 48 V 30 Ah batteries in parallel. If any of the batteries fail, the capacity is reduced but the overall system maintains 48 V,” he said.
This parallel connection capability is facilitated by the comms protocols the company offers, including CAN bus, SM bus and Bluetooth. “When they are connected in parallel, they communicate with each other and work together. When you turn one battery on, all will turn on,” Chan said.
He added that while some competitors’ systems can also connect batteries in parallel, they require them to be at the same SoC or voltage before connection, and that, after a few cycles the batteries become increasingly unbalanced.
Lithium Power has also addressed this issue through its BMS. Chan explained that the GC2/GC8 can be connected at different SOCs, such as 20% and 100%, and the battery with the higher voltage will not charge the ones at lower voltages.
“If batteries were to charge each other it would be a major safety hazard, as there would be a large in-rush current. Our pack balancing means we can connect a brand new battery with a set of old batteries that have experienced numerous cycles.”
Rather than using a third-party product, the company owns its BMS technology and therefore has full control of the batteries, enabling it to provide adjustable protection parameters to accommodate different applications and operating conditions, he said.
“Our batteries can be set to different sleep mode timers,” he noted. “User settings can be customised, battery status information and history data log are accessible, and batteries can be programmed to pre-heat before charging in below-freezing environments.”
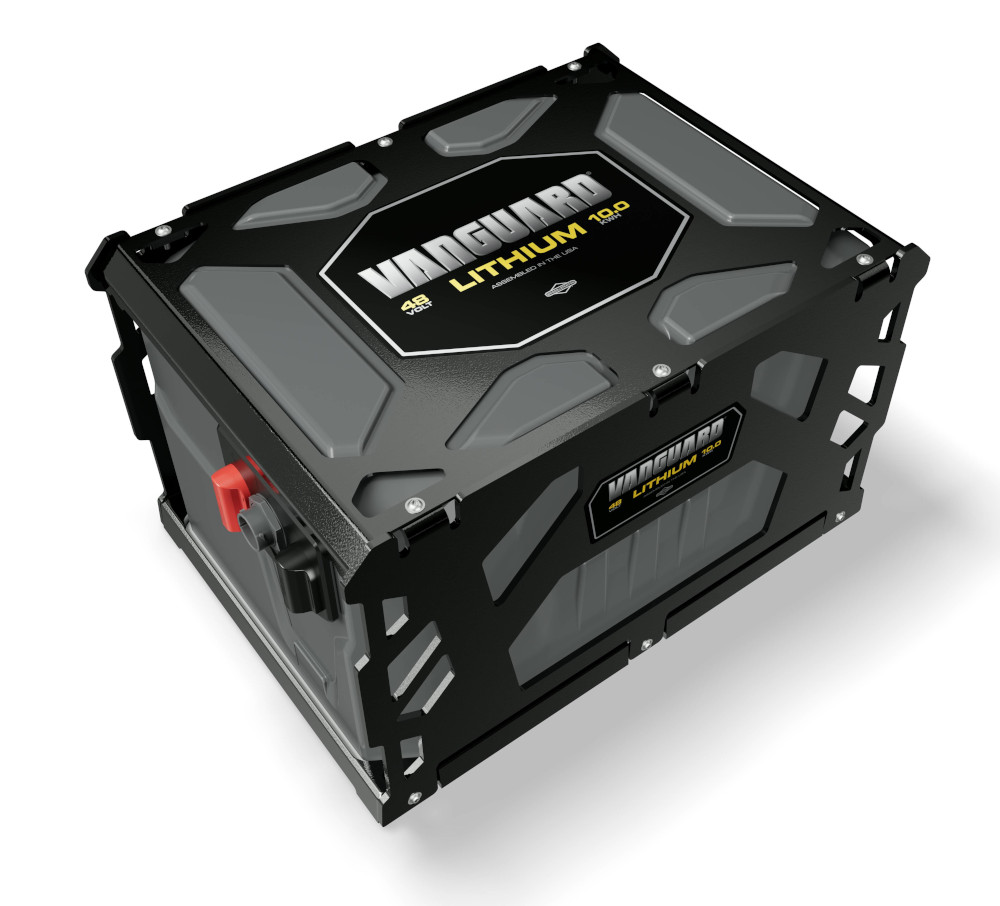
Briggs & Stratton showcased its new Vanguard 48 V, 10 kWh commercial lithium-ion battery pack designed for autonomous vehicles, utility vehicles, light duty zero-emissions construction equipment and outdoor power equipment. Its 10 kWh capacity represents the total energy measured using a 0.2C discharge according to the IEC 61960-3:2017 standard.
The pack comes with an integrated BMS and charger, along with a steel roll cage for impact protection. The company said the Vanguard pack has been tested and validated to operate in any environment that the vehicles and equipment it powers are intended to encounter.
Michael Marshall explained that the main development challenge was balancing power output with runtime.
“Everyone wants high power and long runtime,” he said. “Our 10 kWh battery capitalises on the power output of our 5 kWh battery while providing twice the runtime. We decided not to pursue double the power output of this pack but instead to focus on range extension while being more cost-effective.
“The hardest part was proving to ourselves that this is what the industry was asking for,” he added. “We found that none of our current or prospective partners required sustained high-power output, but rather more runtime at a nominal rate.”
The two 5 kWh batteries that form the 10 kWh pack are connected in parallel, and the company has applied for patents covering a ‘communication-less’ paralleling strategy. “That was developed for military-grade applications where compromised comms environments will still allow battery packs to be paralleled and power a machine. For safety, however, we always require comms for charging, but not for discharging.”
The battery is based on Briggs & Stratton’s cell module assembly (CMA) design, which is focused on ease of manufacturing. It is based on cylindrical cells but is agnostic regarding cell chemistry. Marshall explained that CMA enables the company to switch seamlessly between cells optimised for energy density, power density or for a good compromise between them, and it can also use cells from different manufacturers.
He also pointed out that the battery is designed to be serviceable. “Unlike foam-filled automotive batteries, each battery module is 100% replaceable,” he said.
The new 10 kWh pack is also designed to withstand a wide range of temperatures during both charge and discharge, enabled by a function in the BMS called PowerMap.
“It’s obvious that lithium-ion doesn’t like being too warm or cold, and we can’t fight physics,” Marshall said. “What we capitalise on is the fact that our BMS performs real-time calculations to provide applications with knowledge of how current can be delivered and accepted at any time.
“That allows applications to ‘deplete the tank’ or discharge to empty without overheating. Similarly, we can charge without faulting, even in high ambient temperatures.”
The company chose a combination of convective and conductive cooling as the basis of its thermal management approach to the pack. “Our packs are used in applications where Briggs & Stratton doesn’t control the end product, so we rely on free and forced-air convection for heat transfer,” Marshall said. “Our die-cast packs use higher levels of conductive thermal management.”
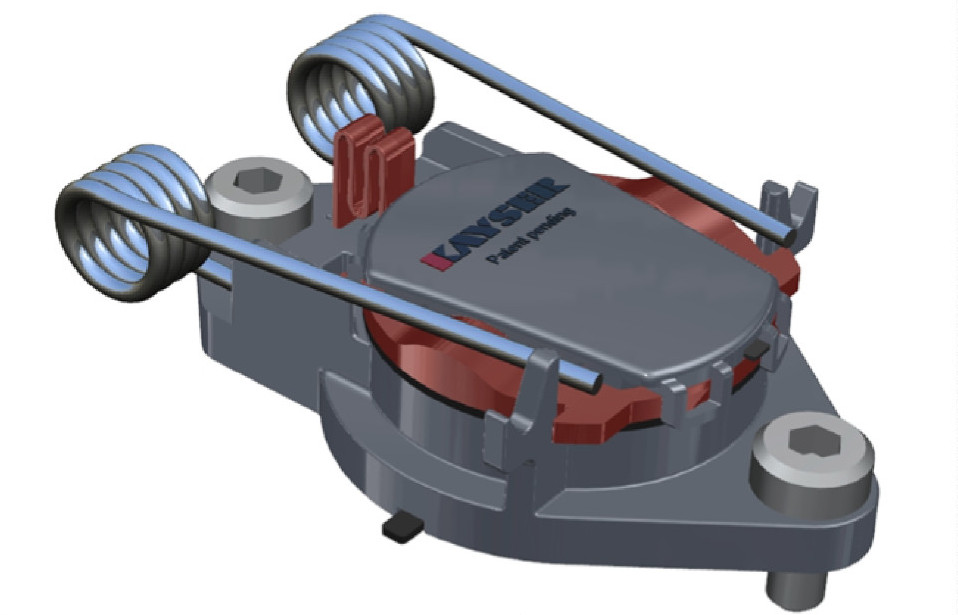
Kayser Automotive gave us details of its Kayser Guard safety valve system for hermetically sealed battery housings. The system is designed to be able to accommodate moderate pressure differences that occur during normal operation using a low-rate equalisation mechanism, while providing a rapid means of safely relieving any pressure spike in an emergency.
Low-rate pressure equalisation is handled by a semi-permeable PTFE membrane, while the emergency device is a spring-loaded safety valve. The development team said the system is flexible, in that the valve can be installed with or without the membrane, and that the company specialises in customised solutions for different battery pack designs.
This custom tailoring extends, for example, to the size of the pores in the membrane, a team spokesperson said. “Kayser has different membranes available to allow the right one to be chosen in terms of breathability and available space,” they explained.
The valve is opened when the pressure inside a pack reaches a threshold level, which can be adjusted to a customer’s specification simply by changing the spring pre-load. In production, this pressure can be tested to 100% at the end of the line before delivery.
Triggering is purely mechanical and does not depend on a signal from a sensor. “The pressure acts on the piston surface, and the piston is held by a spring load, so if force on the piston overcomes the spring load, the piston pops out,” the spokesperson explained.
“After the triggering, a resistance-free section is opened for gas release,” they added. “Only the piston diameter limits the flow according to the pressure inside the battery pack.”
In larger packs, more than one Kayser Guard can be used, and the company also offers the option of bigger devices.
The development team reported that the concept has garnered “huge interest” and cites its accuracy, independence from environmental influences such as temperature and humidity, and even from assembly issues.
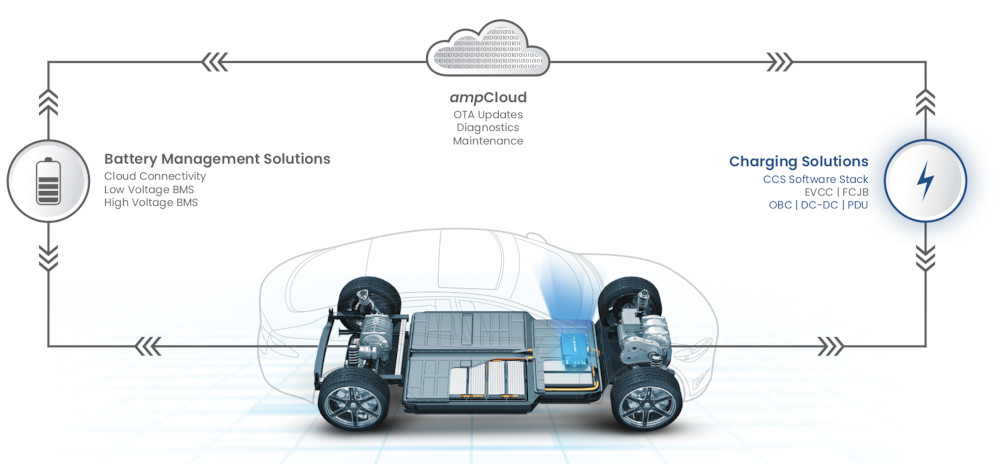
AMP showcased its Energy Management Unit (EMU), which it describes as a comprehensive solution to all an electric vehicle’s energy needs as it combines the functions of a DC-DC converter, on-board charger (OBC) and power distribution system with 500 A fast charge capabilities in a single enclosure, saving both space and weight, Anil Paryani explained.
“EMU uses the latest silicon carbide and magnetics technologies to reduce the power electronics packaging volume drastically, “he added.
Combining these three systems into one relies on deep expertise in several technologies including wide band gap power semiconductors and high-frequency magnetics, along with a multi-physics understanding of electrical, electromagnetic, thermal and mechanical systems, enabling engineers to co-design them. Understanding of advanced digital control and scalable embedded software systems is also critical, Paryani said.
“The use of silicon carbide unlocks higher power density and efficiency, better platform scalability, and precise charging control.”
One result is a reduction in volume of more than 65% over comparable available solutions. This increase in power density brings cooling challenges, so the EMU is liquid cooled and capable of accepting a wide range of flow rates. The unit can be housed within the battery pack, forming an energy subsystem, an approach that AMP engineers refer to as a power wall on wheels.
As a charger it can accept three-phase AC at 320 V to 415 V or single phase AC at 97 to 265 V at the input, and currents of 48 A and 24 A respectively, with output power of up to 11 kW at 270 to 465 VDC. Efficiency at full load is quoted at more than 92%, and it can deliver its maximum 500 A fast charge current for 10 minutes, says the company.
In DC-DC converter mode it can accept 270 to 465 VDC and put out 9 to 16 VDC and up to 3 kW at more than 94% efficiency.
Connected to the company’s ampCloud, the EMU forms and end-to-end system for energy management, charging and cloud-based analytics, diagnostics and maintenance.
In production and deployed on more than 11,000 road vehicles, the EMU is also scalable for different platforms, he said, adding that it can be integrated into applications as diverse as passenger cars, large commercial vehicles and even hypersonic air vehicles.
“Efficient, intelligent and connected” are characteristics Paryani expects of future energy management technology as applied to EVs, mobility and beyond into many other aspects of life, particularly clean energy.
“Engineers at AMP have developed an operating system for e-mobility to harness this energy on the vehicle and through the vehicle to the grid.”
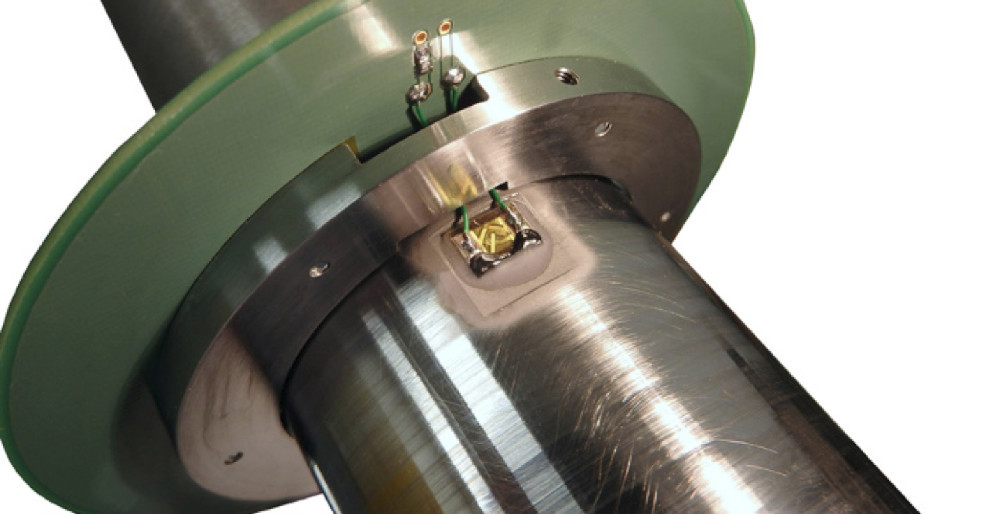
Transense Technologies discussed how to improve the performance, efficiency and safety of electric motors through embedded sensing of critical parameters such as torque and temperature using patented Surface Acoustic Wave (SAW) sensors, which Ryan Maughan said is a radical departure from current practice.
“It is now possible to fit a real-time dynamometer to every electric motor,” he said.
He explained that motors are normally characterised and controlled by, for example, calculating torque from the relationship between the B field current and the motor torque constant.
He said this is complicated by the motor’s properties and various loss mechanisms, which leads to the need for a laborious means of calculating the torque output of a new motor design by characterising it over many operating points and creating parameter look-up tables and control variables.
Current is measured using Hall effect sensors in the inverter, forming a control loop inside the inverter for torque estimation, he added.
Further, the loss mechanisms are dynamic, signal filtering is essential in current sensors, and manufacturing tolerances have to be taken into account, so motor control is complex.
Torque sensors, for example, have not been embedded in every electric motor yet for many reasons. Maughan said these include cost, the need to make shafts flex enough to create a measurable strain in torsion, poor accuracy of available sensing technologies, the space available in the motor for the sensor and its control electronics, and the limited durability of these items.
SAW technology, he argued, is set to change that by providing robust, accurate, real-time measurement of torque, pressure, strain and temperature. As well as improving efficiency and performance, it also leads to better safety through redundant and dissimilar verification of the torque delivered, real-time monitoring of machine performance, load and condition – things that normally require a dynamometer, he pointed out.
The sensors themselves are small, wireless non-contact devices that don’t need batteries. They are also unaffected by magnetic fields and are relatively inexpensive.
Essentially, they are resonating piezoelectric devices built on carefully selected quartz substrates that, for example, allow the deflection of a shaft in response to torque to alter the resonant frequency. The sensor is connected to a small RF antenna that receives an interrogation signal and reflects it back in altered form through the antenna to reader electronics, which derive a torque figure from it.
In practice, Maughan said, torque applied to the shaft changes two SAW resonances in two sensing devices on opposite sides of the shaft – one high frequency, one low – in opposite directions because they are strained differently. Using HF and LF sensors enables compensation for axial forces and bending moments.
The technology is already in use in high-end motorsport and aerospace applications, as well as electric power assisted steering system in an automotive application. It is also being applied to an automotive electric drive unit in which it will provide real-time measurement of shaft torque and temperature, Maughan said.
“Their greatest potential impact is on larger vehicles and high performance vehicles, such as trucks and buses, off-highway machinery, SUVs and high-powered passenger cars,” he added.
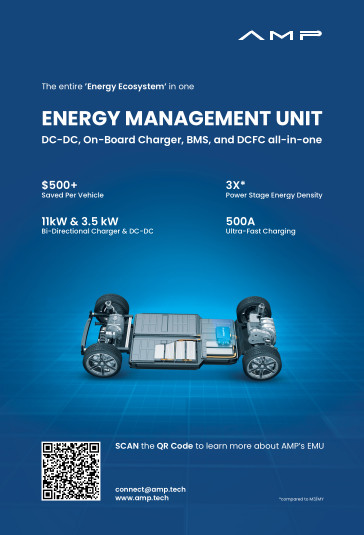

ONLINE PARTNERS
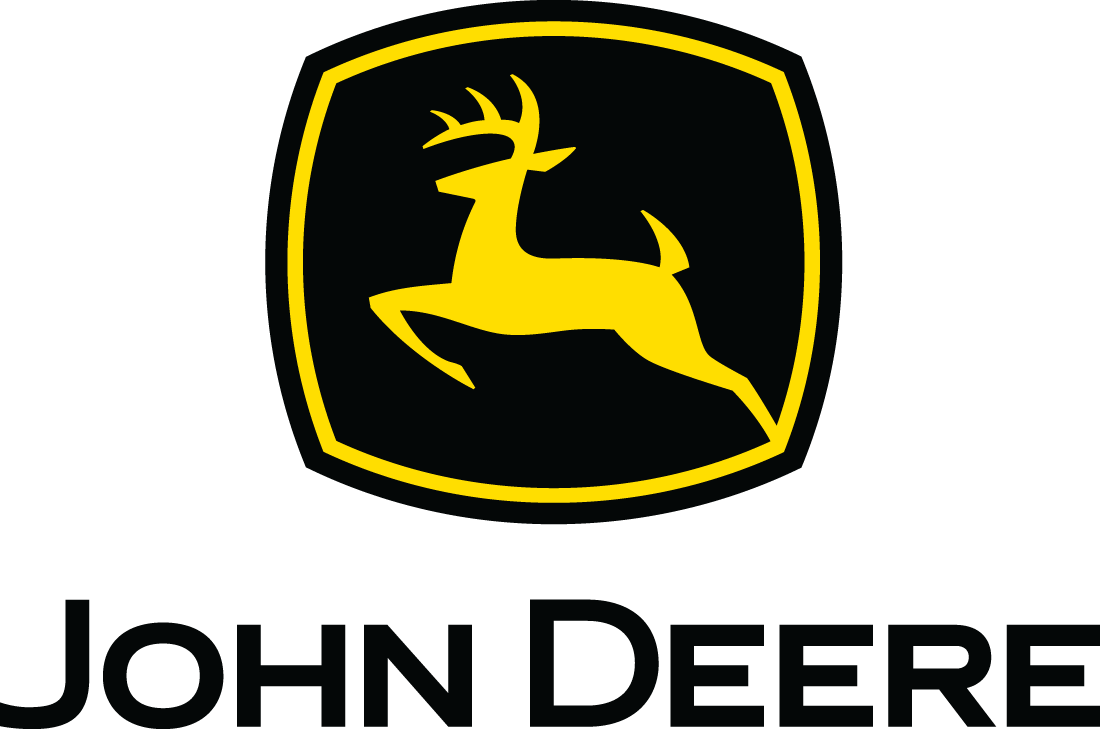
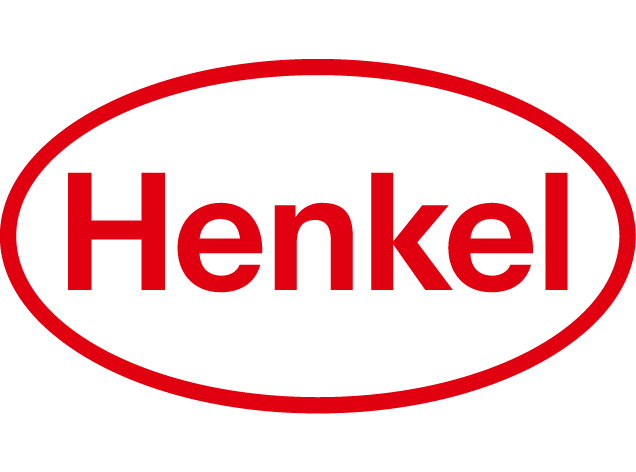
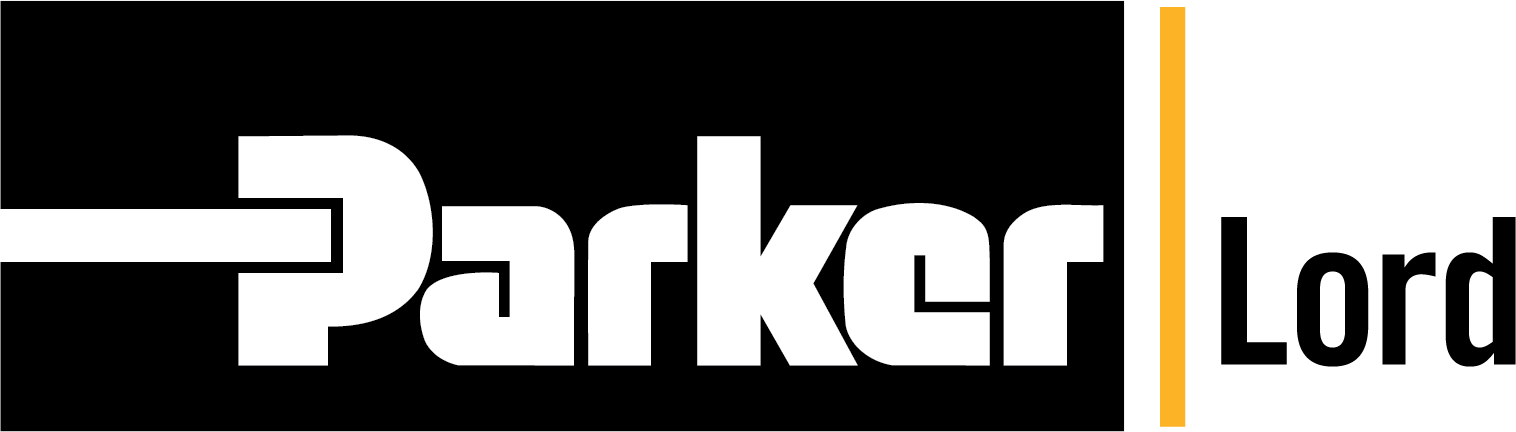
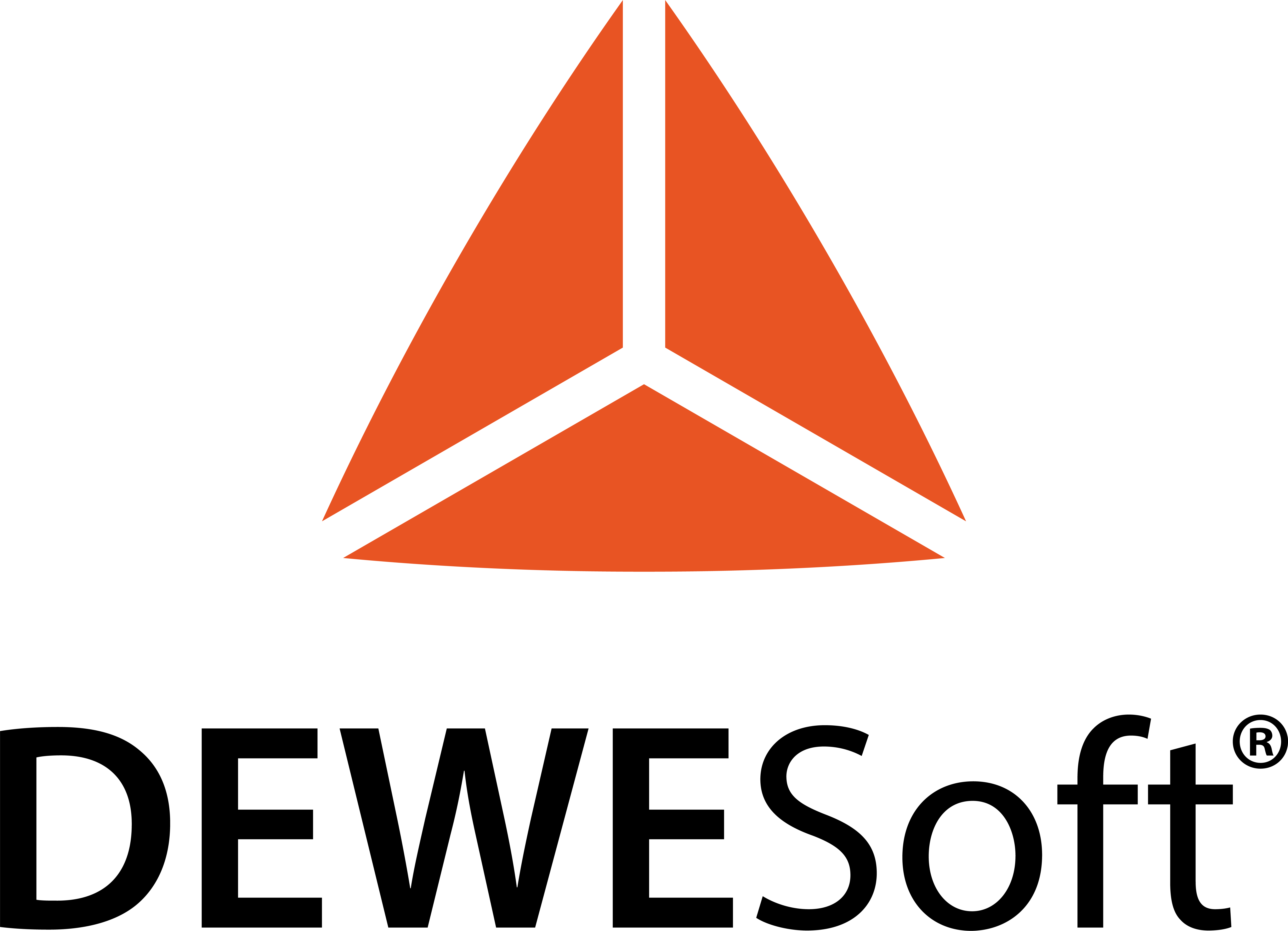
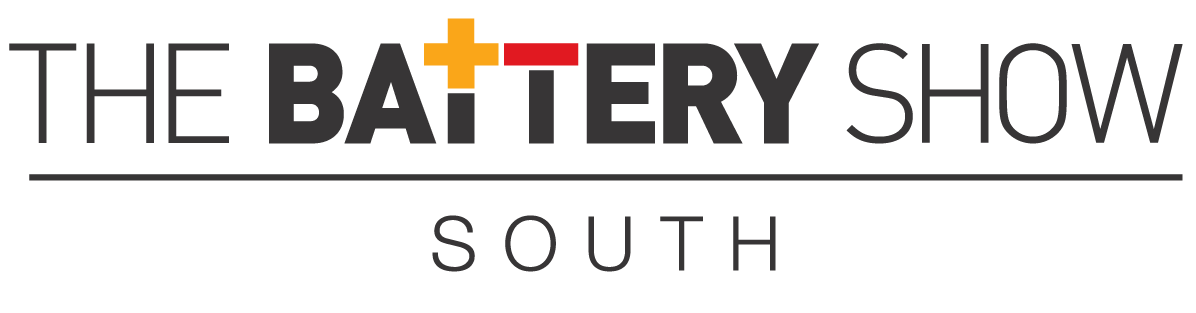
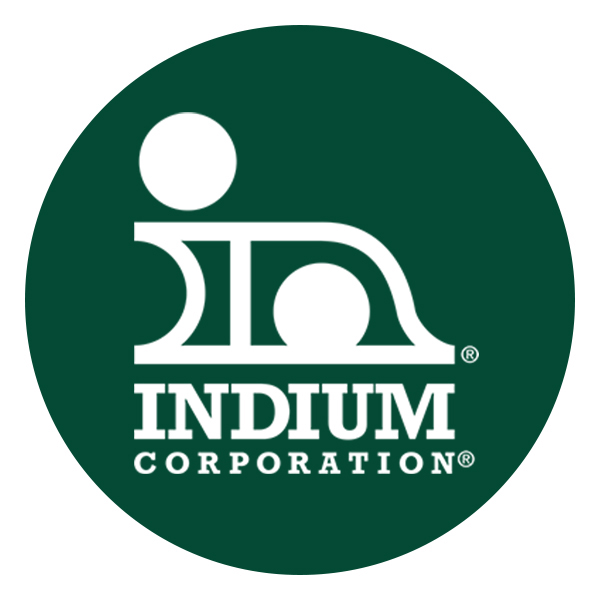
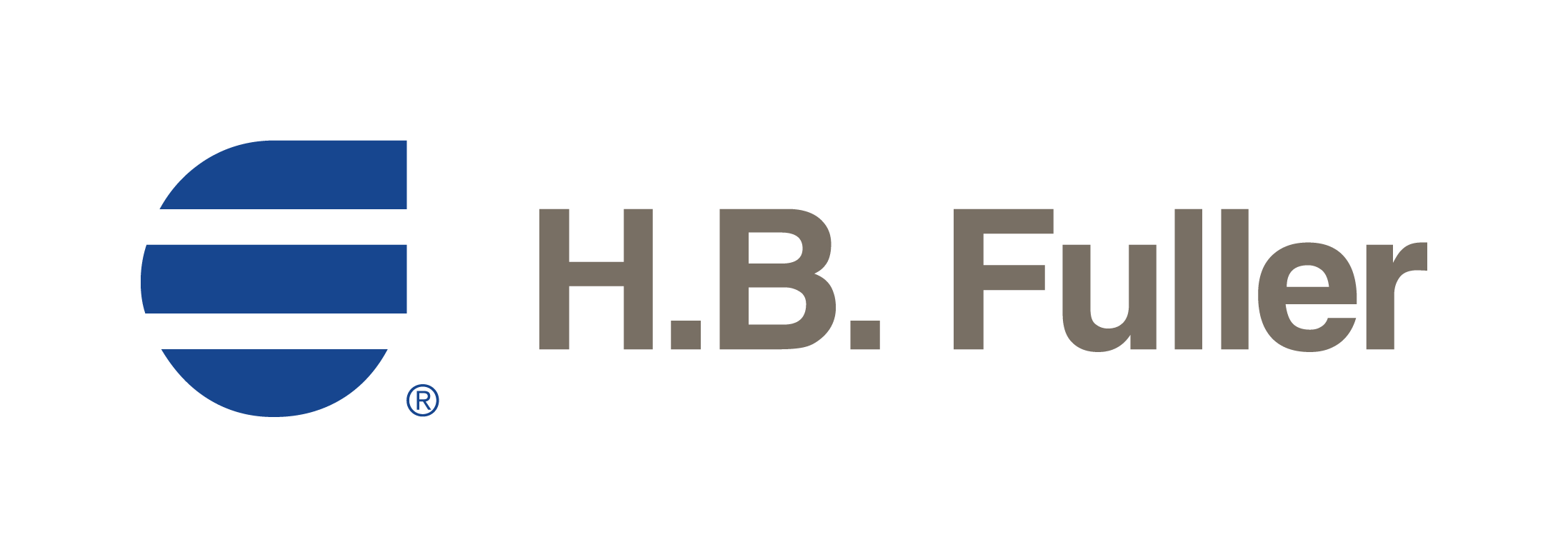