Battery Show Europe 2023
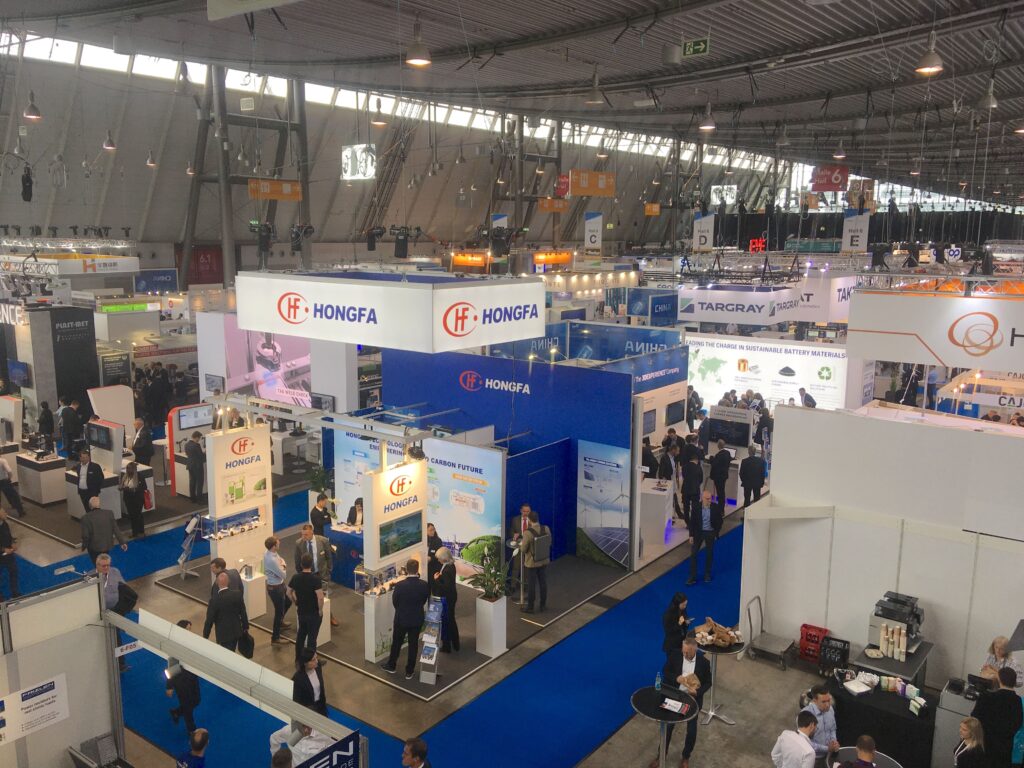
Circular motion
Peter Donaldson presents highlights from this year’s show, where a burgeoning theme was on meeting circular economy goals
Held at the Stuttgart Messe exhibition centre from 23 to 25 May, the Battery Show Europe 2023 was a lively and well-attended event that showcased advances in core battery and EV powertrain technology, materials, manufacturing and quality control processes. It also revealed a growing emphasis on repair, reuse, recycling and broader circular economy goals.
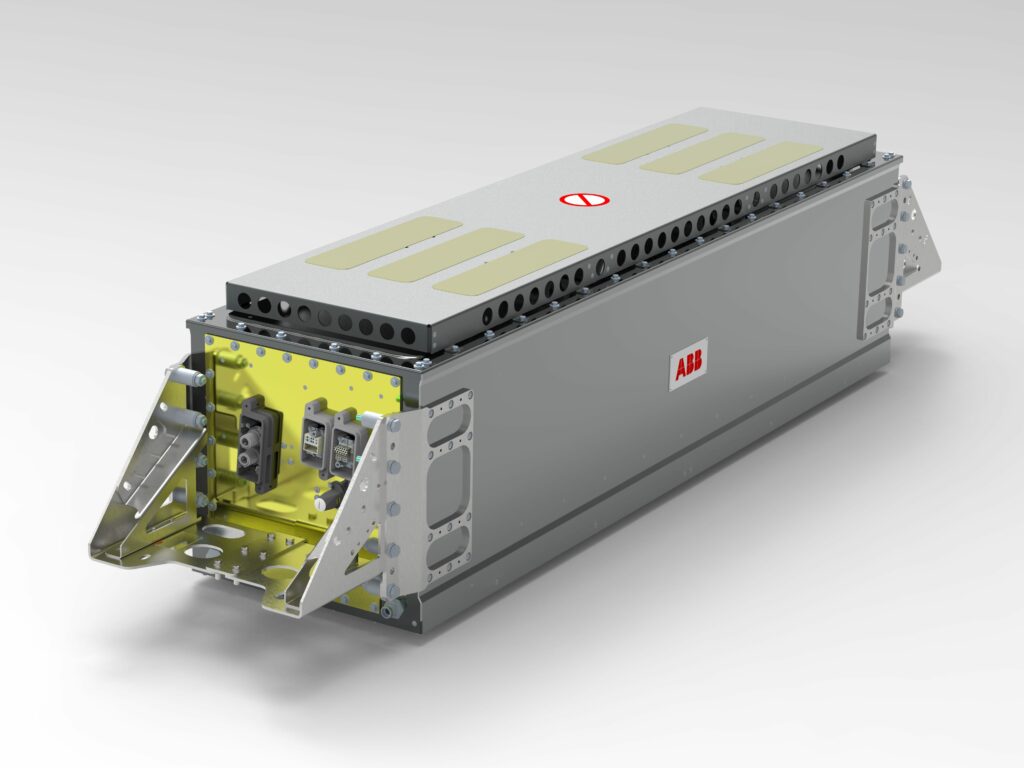
ABB featured its offering of complete powertrains for heavy-duty EVs, from mining vehicles to trucks and buses, with an example of an lithium titanate (LTO) battery pack, an inverter with a multi-purpose capability, and a large, 800 V permanent magnet motor from its AMXE family.
Designed for long service life, high performance and rapid cycling at the expense of energy density, the pack on display contains 11 modules of 48 LTO cells in prismatic format and offers a pack-level specific energy of 60-70 Wh/kg. The water-cooled pack also houses the BMS along with the contactors, protection circuits and fuses.
Felix Traub explained that while this energy density is low compared with car and bus packs at 150-200 Wh/kg, that is offset by high charge and discharge rates relative to its capacity of 8C and 8E respectively. Also, a service life in excess of 20,000 cycles means the pack will typically last for 8 to 10 years in a demanding mining operation, or more than 15 years in other applications.
The inverter offered with the pack is a multi-purpose module that can also be configured to serve as a DC-DC converter or an onboard charger. “A large vehicle might have three or four, or even more of them, configured to do different jobs,” Traub said.
The inverter on display uses two-level technology, but ABB is working on the next-generation product, whose core power electronics are silicon IGBTs in a three-level topology, meaning it has three voltages to switch between to achieve the target average voltage. That will make it more accurate in achieving that target voltage, more energy-efficient and gentler on the motor when acting as an inverter than a faster switching two-level inverter based on SiC MOSFETs.
“Fast switching has advantages in some applications, but it can be quite stressful on the motor because the high switching gradients and dV/dt [voltage derivation over time] transients will degrade the insulation,” Traub said. “It’s like a mechanical stress reversal. With a three-level topology you have a much fewer stress reversals, and the amplitude of each reversal is smaller.”
Dow showed examples of the battery pack and power electronics applications for its Dowsil silicone and Voratron polyurethane products for thermal interface materials, gap fillers, thermal runaway, fire protection and potting developed in Dow’s multi-disciplinary, collaborative Mobility Science environment. Several of these products, including fire protection coatings and materials to contain heat in a bad cell, have been through qualification and are now commercialised,.
Luc Dusart said, “We listen to customers’ needs and try to identify the best solution and the best chemistry to meet those needs. If there’s no obvious winner then the customer will select one. That is important, because we can be pretty much technology-neutral, so there’s no pressure on a customer to select a certain chemistry”
He said Dow’s investment in application expertise is important here. “Our technical service people have a lot of application expertise, and being a materials science company we go very deeply into the chemistry. We look at how the chemistries can work together, including the potential for hybrid technologies.”
That is possible because the company is vertically integrated right back to the refining (cracking) of the feedstock into the polymer backbones. “We have direct access to the backbones, so it is easy to fine-tune them as we look for the best sustainable solutions,” said Esther Quintanilla.
“We have also found ways to use waste to replace fossil naptha in the feedstock.” To that end, the Dowsil and Voratron products now include recycled waste fed into the company’s electrically powered refining system, or ‘e-cracker’, she said.
Stora Enso, a Swedish-Finnish forestry company, showcased its development of a cell anode material from a more sustainable source than fossil graphite, which is ether mined or processed from petroleum coke, for example. The bio-based substitute, which Stora Enso calls Lignode, is a hard carbon made from lignin, a by-product in the production of cellulose fibre from wood.
“Our material is basically a drop-in in replacement for the anodes of 85-90% of rechargeable lithium-ion batteries that use fossil-based graphite,” explained Dr Stephan Walter. Lignode takes up and holds lithium ions when the cell is charged, releasing them during discharge to migrate back to the cathode through the electrolyte and across the separator, which electrons cannot cross and are therefore forced around the circuit as the current powers the load.
“Extracting lignin from the chemical pulping is a process that has been known for decades,” said Dr Walter. The lignin is refined and processed into a fine carbon powder; the powder is then used to produce electrode sheets and rolls for use in batteries. Stora Enso has the capacity to extract about 50,000 t of lignin annually.
The energy balance of the process is important to its sustainability. “If you look at the whole process, we are very energy-lean because we don’t need to go to very high temperatures compared with industrial graphite materials,” Dr Walter said.
Although Lignode is intended as a drop-in replacement for graphite, it requires a few (undisclosed) adaptations in electrolyte composition.
“We are through the pilot phase and are currently in the prototype demonstration and testing phase together with partners and selected industry players in the value chain, plus we are conducting a feasibility study for our first industrial production site,” he said.
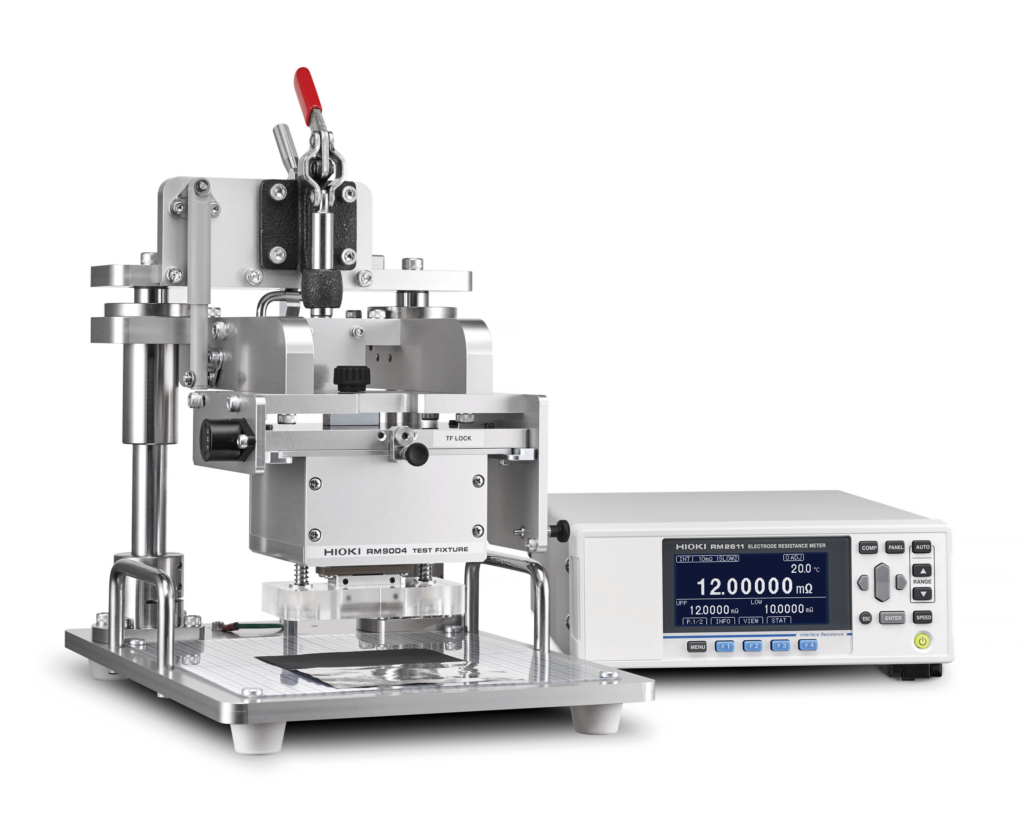
Hioki showed off an instrument that tests the quality of samples of newly calendared electrode sheets by measuring the resistance and calculating the resistivity of the coated surface on the production line before it goes into the cell. Variations in resistivity indicate quality problems and affect cell performance, so its RM2610 electrode resistance measurement system is designed to check that the values are consistent and within specification.
“When the calendared electrode sheet is ready, you can take a sample and check whether the resistivity and interface resistance of the anode or cathode material is as you expected,” said Kai Scharrmann. “In the production environment, different pressures and temperatures, for example, in calendaring have a big impact on the electrode’s resistivity.”
The RM2610 consists of a manually operated mechanical tool that lowers a test head into contact with the surface of the electrode sample. Connected to a high-precision DC resistance meter calibrated in mΩ, the test head has 46 spring-loaded probe pins within a single square millimetre.
With the test head in contact under a precise pressure controlled by the tool, the mΩ meter runs a set of DC resistance tests between pairs of pins, forming a test network, and runs the values through an algorithm to calculate the resistivity of the electrode and the interface resistance between the active material and the electrode’s metal foil, Scharrmann explained.
“You need to know the resistivity and thickness of the foil,” he said. “And of course you have to tell the system what kind of active material is used so it can choose the right parameters.”
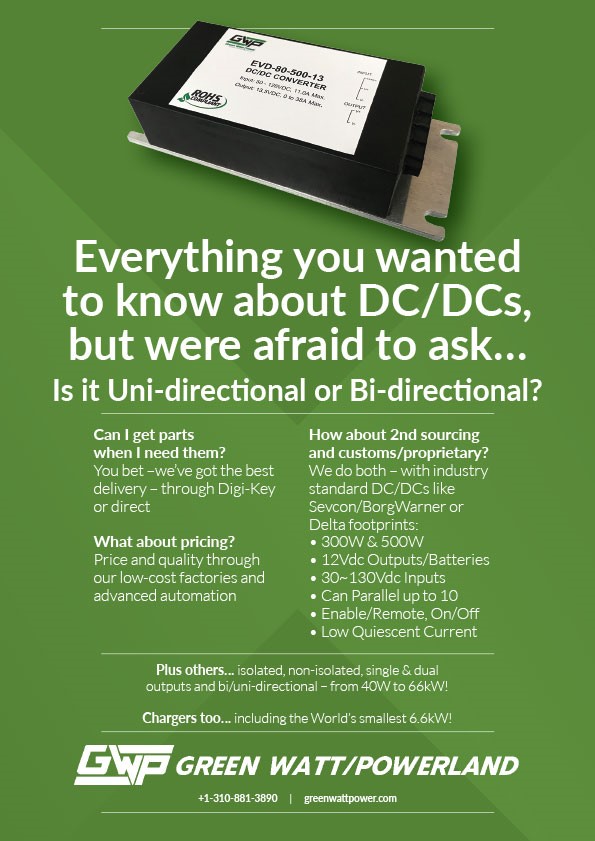
He emphasised that the RM2610 must be used in an environment in which temperature and humidity are tightly controlled, as in battery production environments.
The instrument is now used by all the major battery producers, Scharrmann said, with gigafactories using multiple units around the clock and typically conducting several hundred tests per day.
Carrar is working on a two-phase evaporative thermal management system for EVs with implementations of immersion two-phase cooling for batteries and direct contact evaporator cooling for power electronics and in-vehicle computers.
The company showed a working example of the battery cooling and heating system: a demonstration pack in which heating elements replaced the cells, and a transparent cover revealed the valve that controls the coolant’s flow into the module, along with the membrane through which the fluid evaporates before being fed to a condenser and pumped back around the system.
“Because we are taking advantage of latent heat and not specific heat, we can dissipate enormous amounts of heat from the batteries,” said Eitam Friedman. “In a vehicle with a normal-size radiator we can dissipate 25-30 kW of heat compared with 6 kW in a conventional system.”
The company has been testing the system with battery packs from several OEMs. The tests results showed that by keeping the temperature close to its ideal, Carrar doubled the cycle life achieved with its original cooling system and is on the way to tripling it. “The OEM battery, which achieved 600 cycles before reaching the end of its life at 80% capacity is now at 2000 cycles and still at 94% capacity,” Friedman said.
With evaporative cooling, most of the heat energy from the batteries goes into changing the state of the (dielectric) coolant instead of increasing its temperature. “This is also how we get the extreme uniformity in temperature, since the boiling point is constant,” he explained.
One key component of Carrar’s solution is a mechanical structure that, during boiling, increases the nucleation of vapour bubbles in the liquid. The measure of efficiency here is the difference in temperature between the liquid coming in and the vapour going out, which should be as small as possible.
“If we want the batteries to keep a stable 25 ºC, we need the temperature of the liquid coming in to be 23 ºC and the temperature of the vapor coming out to be 23.5 ºC. Carrar can do that,” Friedman said.
Carrar is in the process of ensuring the system meets all the relevant automotive requirements, and expects to reach Technology Readiness Level 6 during the first quarter of next year. It is working with several OEMs at different stages, including a leading truck OEM in a pre-development testing phase that, if successful, will lead to onsite testing of about 10 trucks.
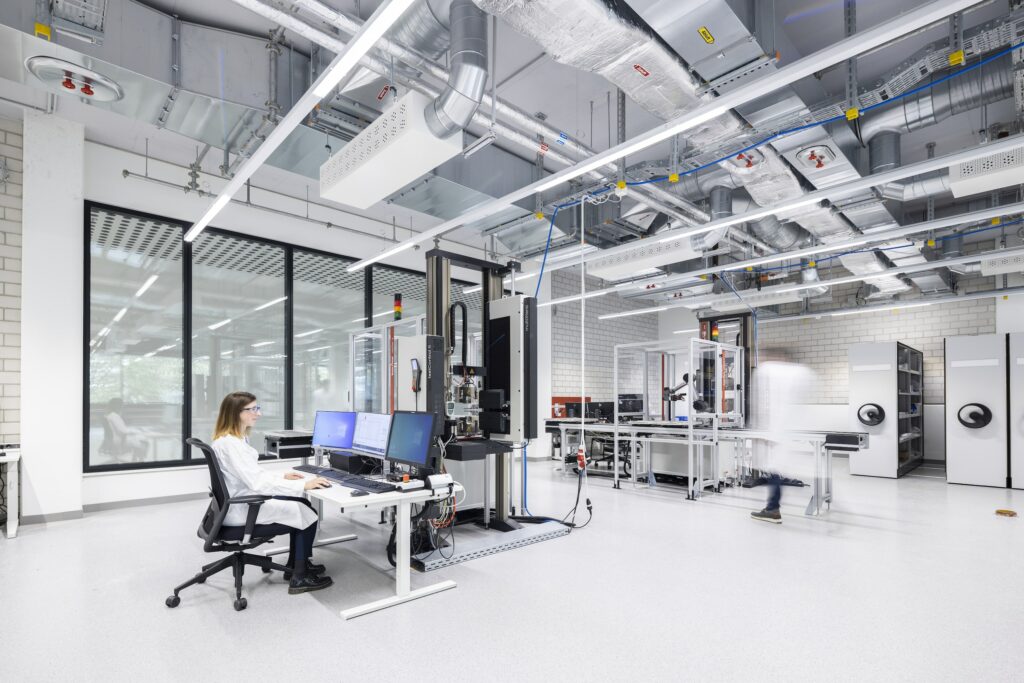
Henkel had news of its evolving capability in virtual development of materials, eventually to be assisted by AI, to develop new formulations that are near-perfect for the application first time, having predicted their performance in the final application, Keon Lee explained.
“Every formulation ends up with different properties,” he said. “The first step is to understand the linkage of the material, meaning the combination of raw materials and consequences as their properties change. Understanding that, we can then create a digital twin of the material through the simulation.
“Based on that, we can create the material cards, which are sets of information about the physical properties of the materials as tested under a range of conditions. That information can then be fed into the designs, enabling the simulation of materials, components and complete battery packs.”
Traditionally, development of a new material starts with a customer requirement and initial development based on institutional knowledge, followed by a time-consuming iterative testing and reformulation loop.
“With the database and the simulation package, we can very much shorten the process and find something really close to the best formulation first time, then decrease the optimisation loop,” Lee said.
The overall ambition goes further, in seeking to create new material cards through simulation only, without prior requirements. “We can create whole battery system models in simulation with different combinations of our materials,” Lee said. “With this capability, we hope to participate in the very initial phase of battery system design.”
Eventually, AI is expected to significantly improve the speed and accuracy of this virtual development process, but first it has to learn from taking in material cards and simulation results. Once trained though, the AI should be able to estimate the formulations that will perform best in particular applications, and also create its own material cards.
The initial simulation capability is due to be launched later this year and become operational early next, while the AI will need a couple more years. “We will probably have the first set of AI-based results by the middle of 2025,” Lee said.
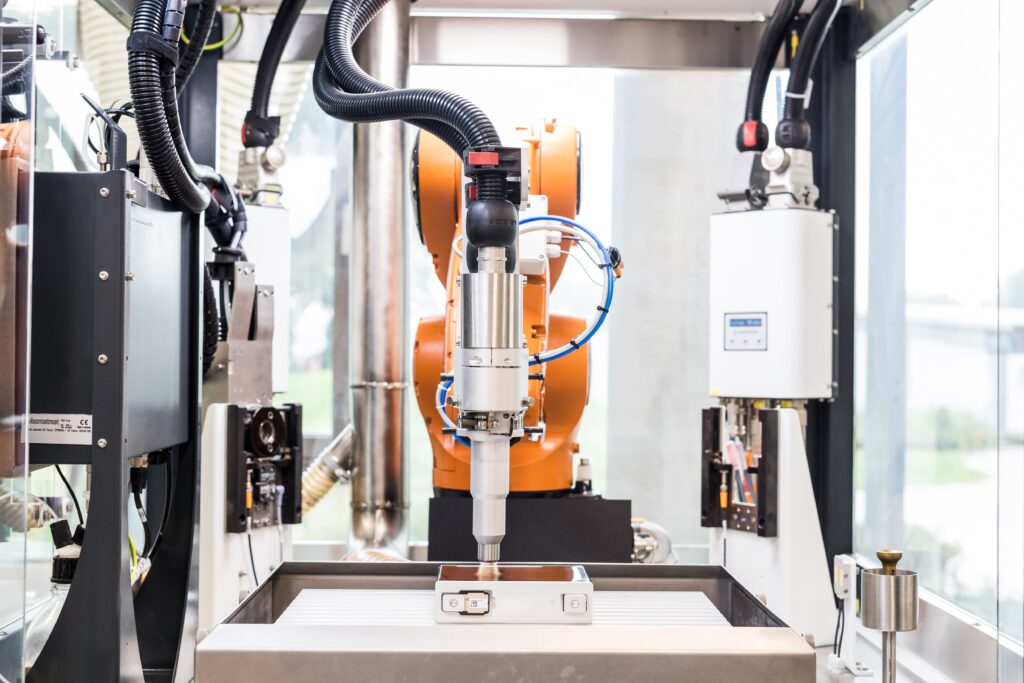
Plasmatreat demonstrated its ability to clean battery cells using atmospheric pressure (AP) plasma to remove any organic contaminants and, in some cases, activate surfaces to aid subsequent pack assembly steps.
“Our Openair-Plasma is used for activating and cleaning surfaces to increase the wettability and adhesion for paints and any adhesive,” Tanja Pawlenko explained. “One major benefit is the ability to get rid of primer or mechanical pre-treatments.”
Plasmatreat’s equipment needs only electric current and, usually, compressed dry air. The plasma consists of molecules split into their constituent atoms, changing their chemical behaviour. The active substance in this case is free oxygen released by splitting the O2 molecule. The free oxygen reacts with the carbon and any hydrogen in organic substances to convert them to CO2 and H2O gas that is then blown from the component’s surface.
“If you have any organic residues – dust, release agents or other thin oils, for example – the plasma will react with it,” Pawlenko said. “In the case of plastic we activate the surface. The plasma opens the carbon-hydrogen chains and brings oxygen in.
“After the activation, the OH groups generated on the surface react better with a coating or adhesive. For example, if you apply a pressure-sensitive adhesive tape on the cleaned surface you will have much better adhesion.”
Battery applications include preparation of cell surfaces to receive PET foils and gap fillers. Plasmatreat is also using its PlasmaPlus process to apply anti-corrosion coatings to battery cases to prepare surfaces for sealing compounds.
Openair-Plasma and PlasmaPlus enable AP plasma to treats materials including metals, glass, textiles and plastics. The company said creating new material combinations is also possible in a cost-effective, clean and sustainable way.
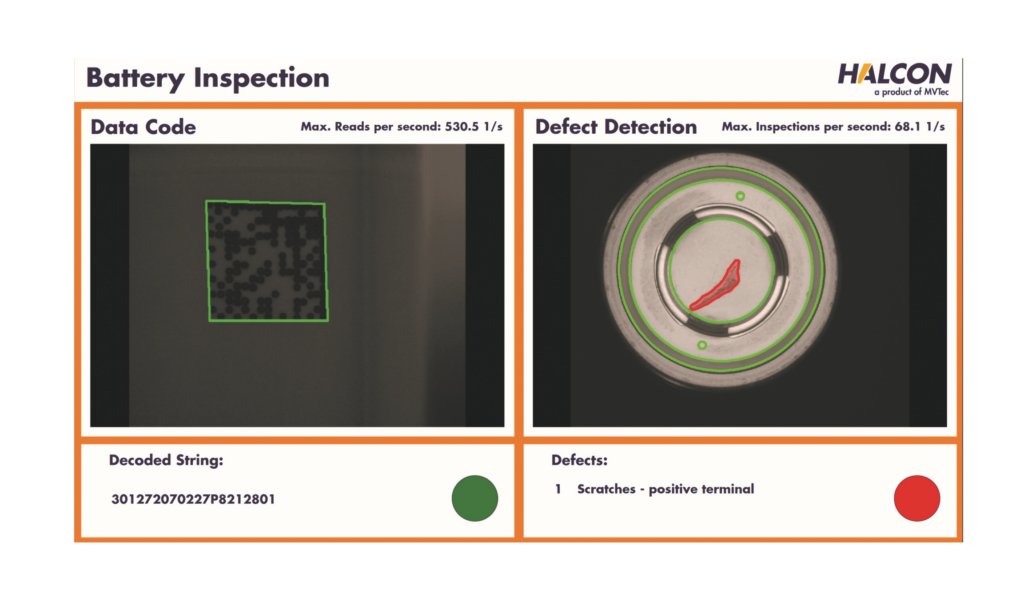
MVTec presented its machine vision software, MVTec Halcon, and its associated deep learning tool.
MVTec’s software is designed to solve complex industrial imaging applications in battery production processes. Such applications include surface inspecting electrode foils after the coating process or, as shown in the demo application on the stand, inspecting the surface of cylindrical cells on a production line.
The latter was using a rule-based approach to look for defects such as scratches, which in this case had been applied to some of the cells for the demonstration. In the demonstration, a set of cells were spinning on a turntable with a lateral camera reading data codes on the sheathing while a second, vertical, camera looked down at the cylindrical cell tops.
“What we inspect is the cap on these cylindrical cells,” Klaus Schrenker said. “First we determine how the battery is positioned, and then we perform a blob analysis, which is one of the basic techniques in machine vision.
“Blob analysis is the extraction of features from connected pixels that share the same logical state. The technology enables the identification of small defects in a very robust way, for example scratches or contaminations that might create a short-circuit.”
Paraphrasing, the rule says that if the difference in the grey values between certain areas is higher than some threshold level, and it extends over a given number of contiguous pixels, that indicates a defect.
“In terms of defect size, the round cell is not the most challenging case, but if we look at a coated surface the granularity of the different grey values can be very small between coated and uncoated material,” Schrenker said.
Using a deep learning approach for inspection tasks requires feeding the software with images to teach it what to look for. “When using anomaly detection, you can potentially do it with only ‘good’ images, but it is more robust if you also have a subset showing defects,” he explained.
Rule-based machine vision can be faster and more robust than deep learning approaches, depending on the production line and the application, but combining them often provides the best results. “MVTec’s software enables users to apply and combine both methods seamlessly,” Schrenker said.
Elinta Motors presented a pair of new asynchronous induction motors for commercial EVs, one for trucks and buses of 12 to 18 t, the other for smaller machines of around 3.5 to 5 t. In both, the design emphasis is on robustness and longevity in high mileage commercial operation, according to Jokuzis, the Lithuanian company’s CEO.
The larger of the two is the EPM 32.200, a 450-800 V motor rated at 320 kW and 800-1250 Nm, and weighing 134 kg. A radial flux machine with a high current density cast-copper rotor, it is driven by Elinta’s 280 kW, 450 A, 800 V inverter/motor controller, which is based on SiC power electronics and weighs 7.4 kg.
The motor has a cooling system that uses a standard water-glycol mix only, eliminating the need for separate oil cooling thanks to the very low thermal conductivity of the epoxy adhesive used in the core components.
“The motor is a simple design, but has an efficiency of within 1 or 2% of synchronous motors without using any rare earth materials, and with silicon carbide you gain around 1% in the drive,” Laurynas Jokuzis said. “If you compare that to a normal synchronous system, the efficiency would be exactly the same because of the SiC inverter, and you could use a field-weakening mode much more efficiently than a synchronous machine could.”
Both are available in four and six-pole versions, the four-pole configuration being for high-speed drives while the six-pole versions generate high levels of torque at lower speeds. The four-pole motors are usually combined with reduction gearing, while the six-pole motors are more often used in a direct-drive system turning a differential.
The motors are radial flux rather than axial flux machines, even though the latter are increasingly popular in high-torque applications. “Basically, our goal is not to over-engineer the motor,” Jokuzis said. “Axial flux and motors are small and light, but in case of damage or very high usage, you might have a bearing failure and lose the air gap.
“We have had some of our motors run for 500,000 km, had a failed bearing replaced and run for another 500,000. With an axial flux motor that would not be achievable in a normal workshop.”
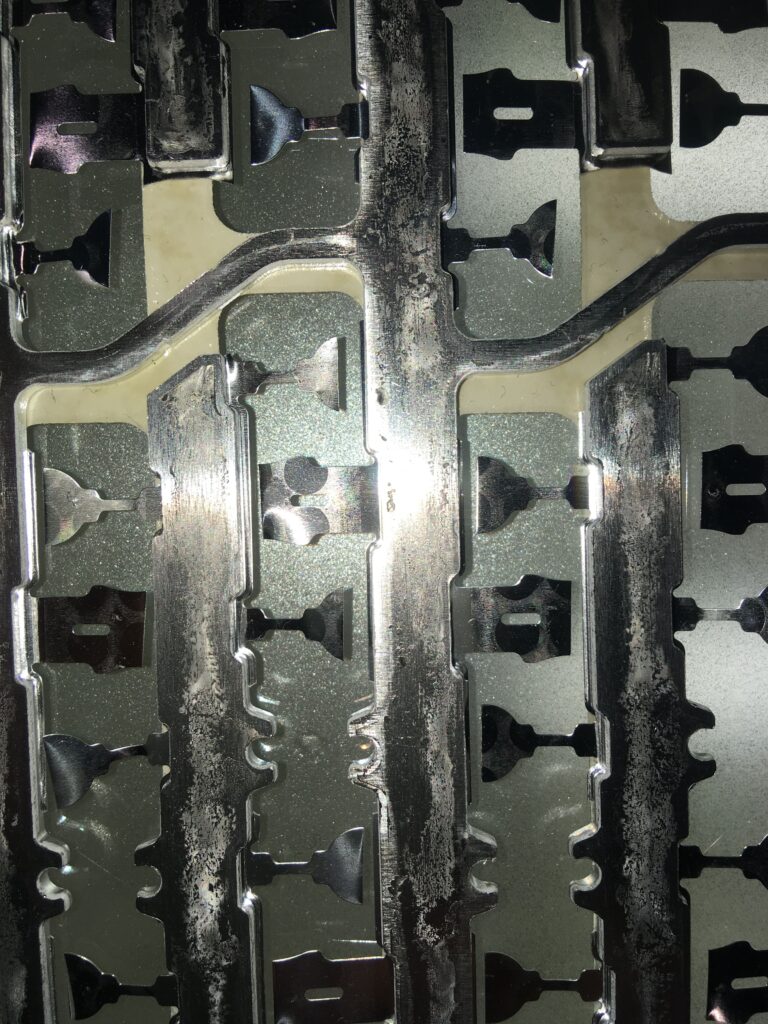
Wiegel showed its newly patented welding and stamping technique for making busbars of variable thickness for battery current collectors in large numbers at low cost.
“We use a continuous ultrasonic welding process that allows us to marry an aluminium foil to an aluminium bus bar, although it can be used for dissimilar metals such as aluminium and copper,” Mark Lakis said.
The foil is less than 0.15 mm thick, while the busbar is over 2 mm. Lakis explained that the company is welding the foil to the busbar because it can create a geometry in the foil that eliminates the need for a wire bond or ribbon bond, removing a step from the customer’s production process. The customer simply has to laser weld the foil tabs to the cells’ positive and negative terminals, whether they have both terminals on the top, or one on top and one on the bottom, as Wiegel’s technique can handle both types of cell carrier.

Ultrasonic welding is a cold technique that vibrates the materials to be joined against one another in a manner that scrubs off the oxide layers, bringing ‘virgin’ metal into direct contact and forming a strong bond without melting the metal. “The weld extends across the entire width of the busbar so you are getting the maximum cross-sectional area in your weld, which is very efficient thermally and electrically.”
ONLINE PARTNERS
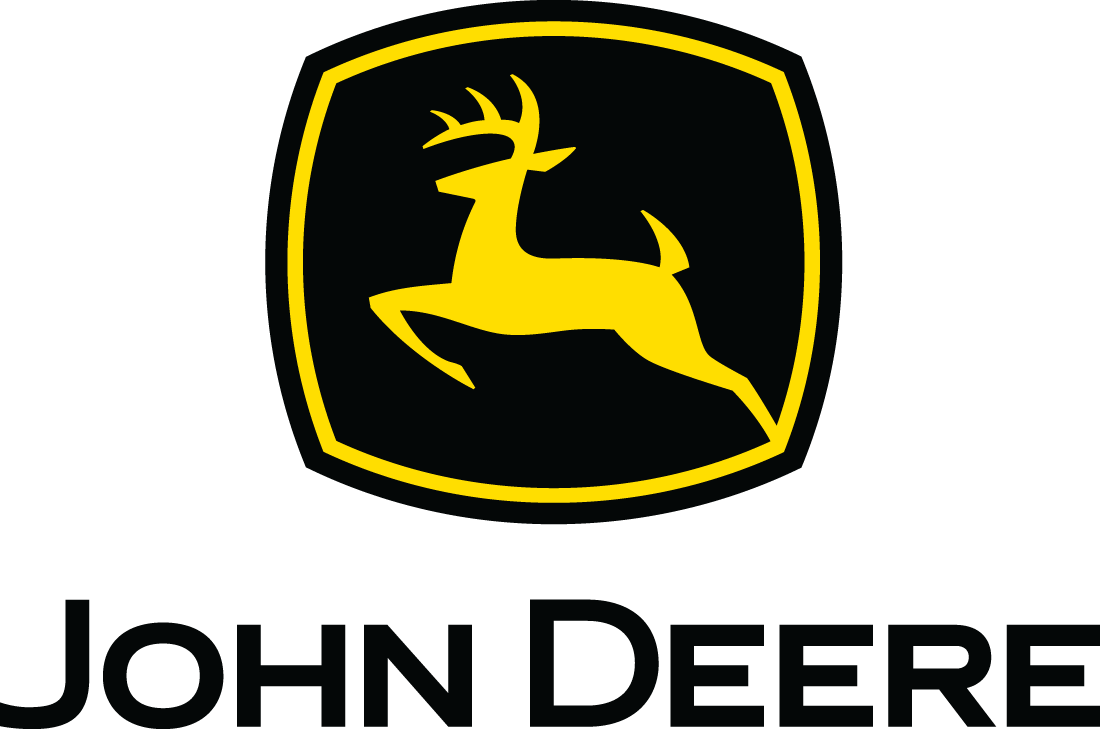
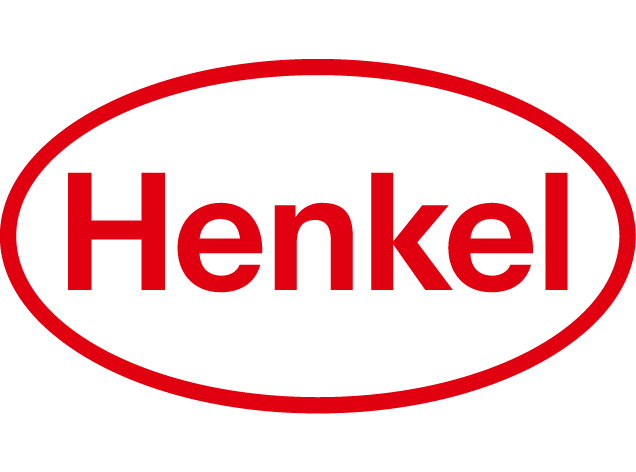
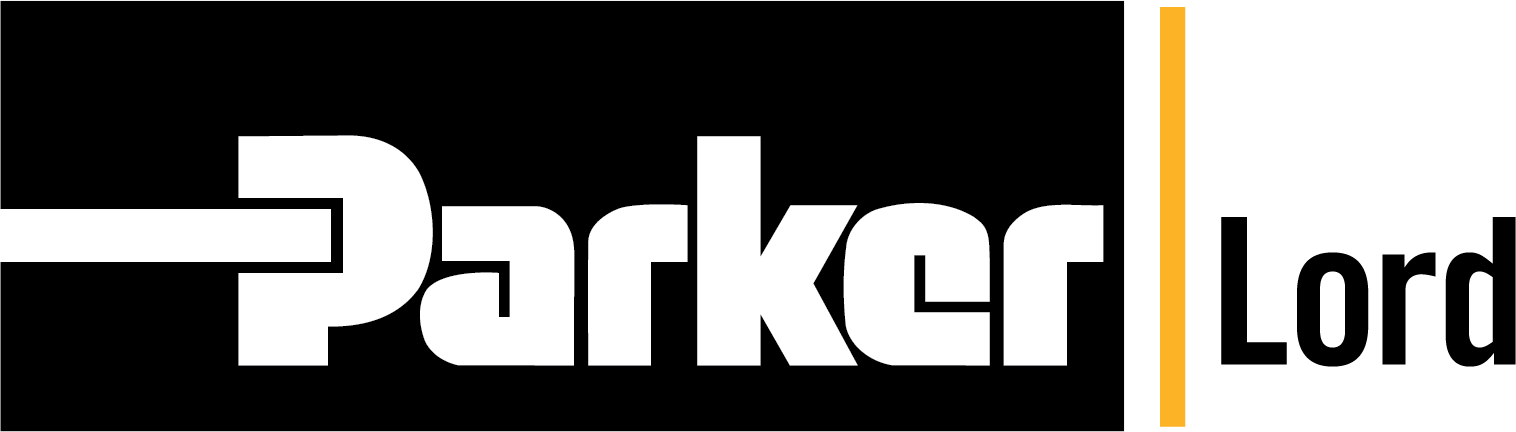
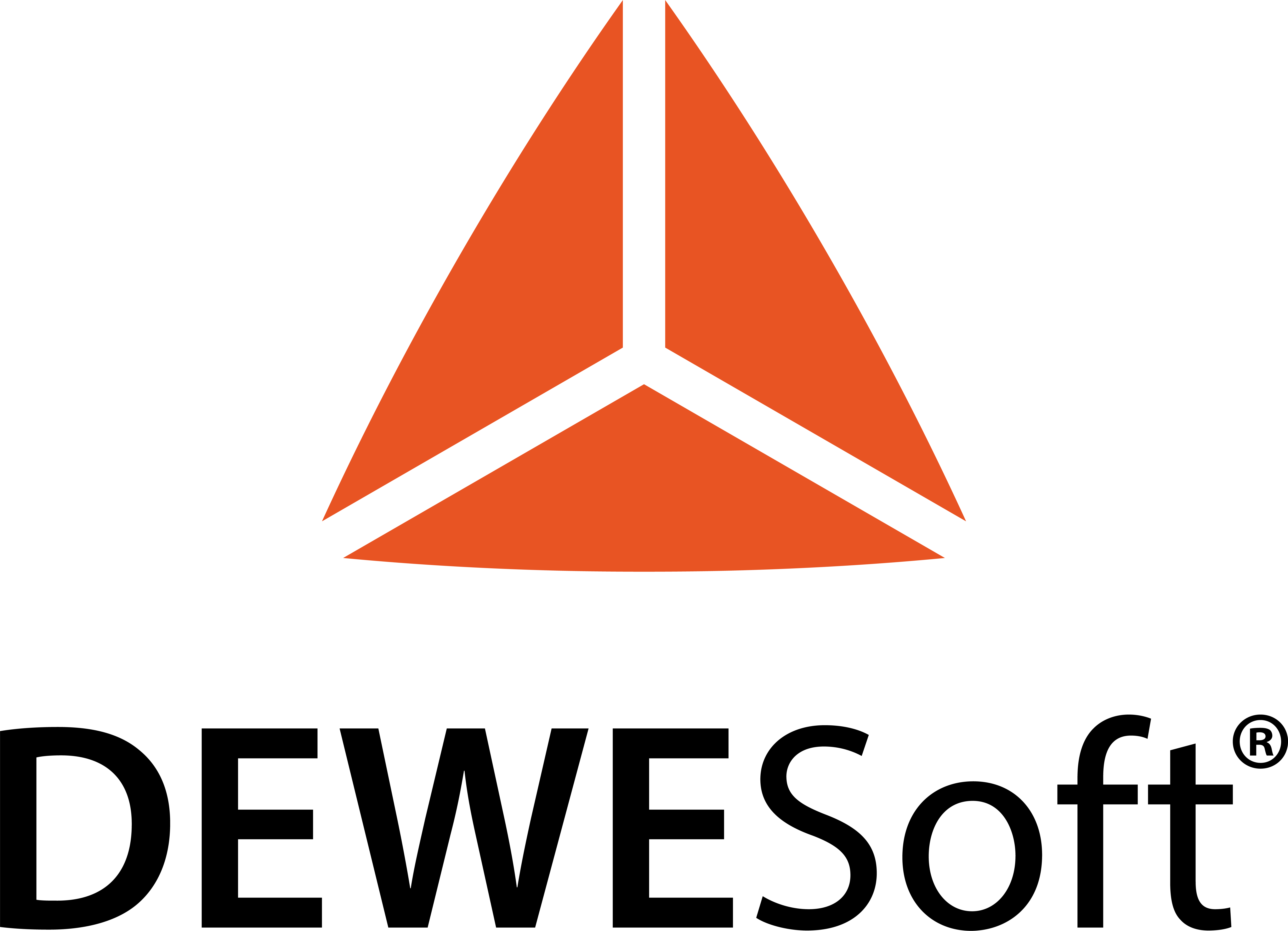
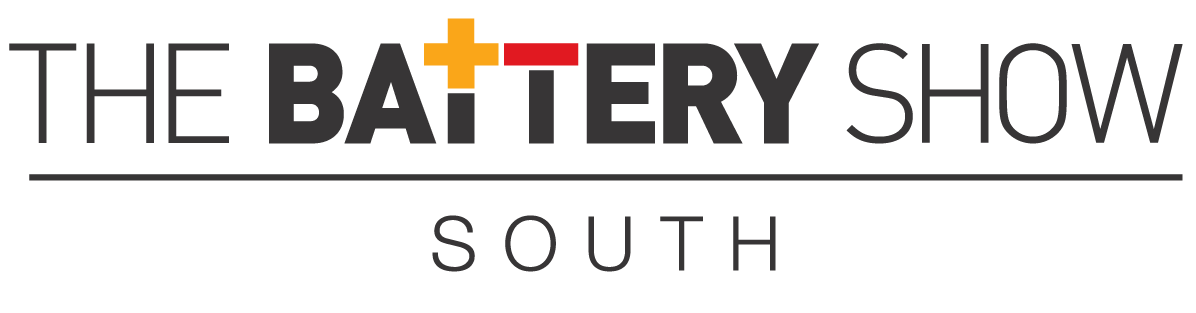
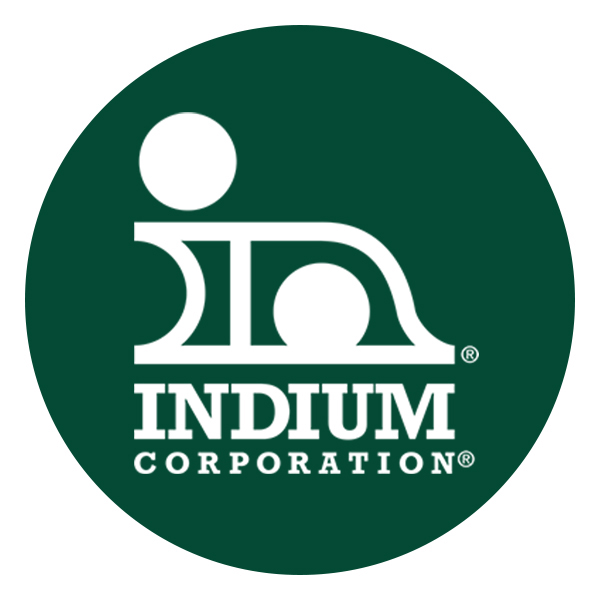
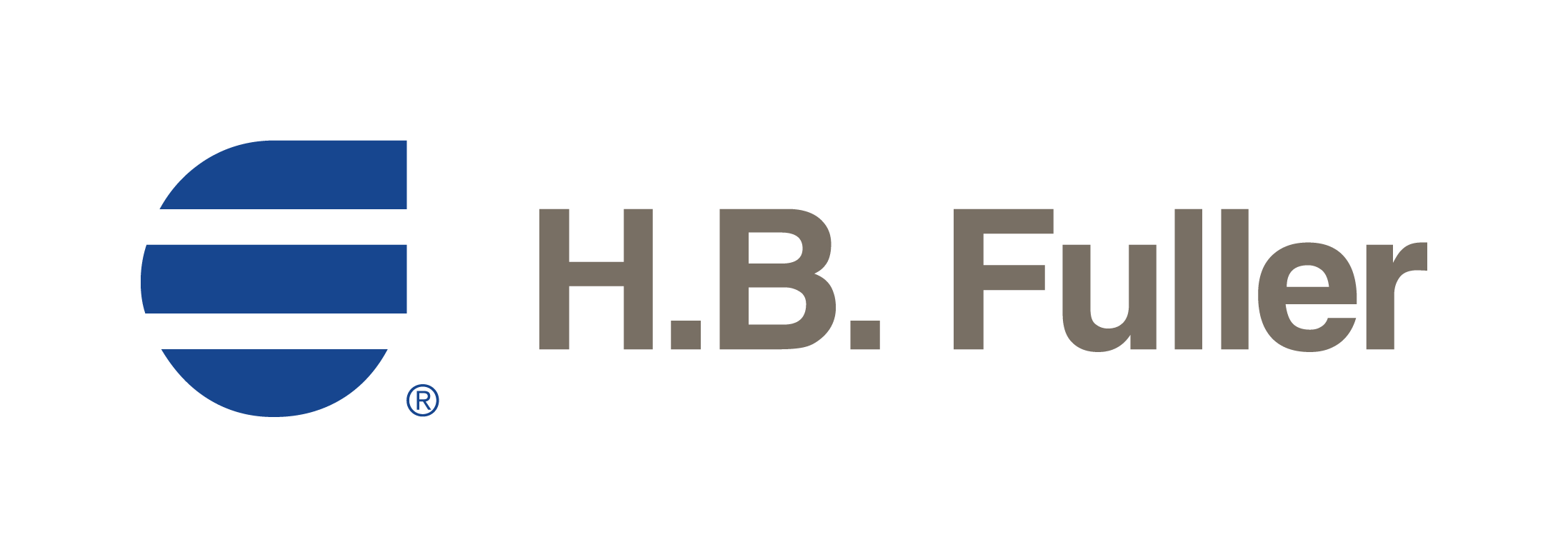