Battery Show Europe 2022
Reading materials
Advances in coating and materials were some of the key takeaways from one of Europe’s largest battery trade fairs, reports Peter Donaldson
Held in Stuttgart as June became July, the Battery Show and Electric & Hybrid Vehicle Technology Expo had many highlights, including an advanced battery concept that boosts energy density using a physical architecture, new fire protection materials, dielectric coatings, a polymer crash structure unaffected by the heat of a coating process, plus silicone and polyurethane materials for use inside batteries.
Further advances that grabbed our attention were a custom interconnect scheme stamped from thin aluminium sheet, and advanced battery management approaches based on computer models, intelligent algorithms and power electronics.
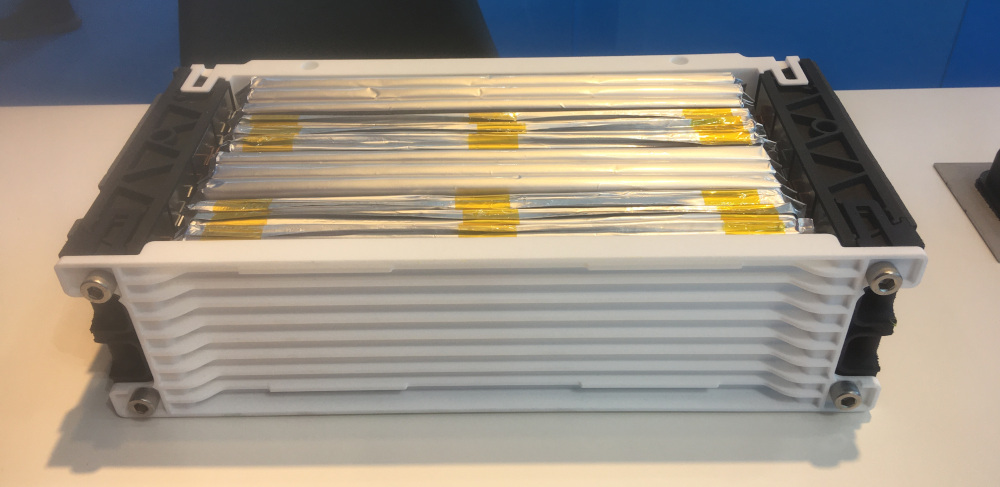
DuPont presented its three-in-one battery architecture concept at the show. Discussions of improvements to battery energy and power density often focus on advanced chemistries, but rethinking the physical architecture is a potentially very rewarding complementary approach.
The three-in-one moniker refers to the integration of structural, thermal and electrical connectivity functions in module components, explained Fabrice Giaume. “A typical battery pack today has four elements – cells, supporting structure, a separate cooling system and an independent electrical connection system,” he said. “We looked for ways to integrate functions better so that we could pack more cells into a given volume.”
Benchmarking packs already on the market showed that older ones typically have cell-to-pack ratios by volume of 25 to 30%, indicating poor packaging efficiency, while newer ones such as that for VW’s ID3 have ratios of around 35 to 37%. Cylindrical cells are at the lower end of that range, while prismatic cells are a bit better, and prismatics have a lower energy density because they contain voids.
“With a three-in-one construction, we are targeting ratios of up to 60% with pouch cells,” Giaume said.
The key idea was the creation of a plastic sandwich strong enough to form part of the module structure, through which a dielectric fluid can be circulated. The fluid provides direct cooling of the electrical connector plates, which are analogous to busbars inside the module and are connected at right angles to the current collector plates in each cell via the tabs. In many battery designs, the tabs are the parts that get the hottest.
“Cells are very anisotropic in terms of thermal conductivity,” Giaume said. “That’s because of the [metal] current collectors that run along the length and height of the cell, especially in pouch cells, but through the thickness there is very little, so we extract heat from these preferential directions to optimise thermal management.”
Using a 3D-printed electrically inert demonstrator, Giaume showed us how the basic ‘mini-module’ unit is assembled, in this case using pouch cells. The ends are formed as sandwich plates designed to be injection moulded from an aromatic polyamide material such as DuPont’s Zytel HTN, which has a very high glass-transition temperature that gives it very stable mechanical properties from -40 ºC to +80 ºC.
The sandwich structure is completed by aluminium outer skins, making the end piece a hybrid construction in material terms and a very stiff torsion box structurally.
A key enabler of the concept is the chemical bond that forms between the aluminium electrical connector plate and the polyamide on the end piece when the two components are welded together, which takes about 45 seconds, Giaume said.
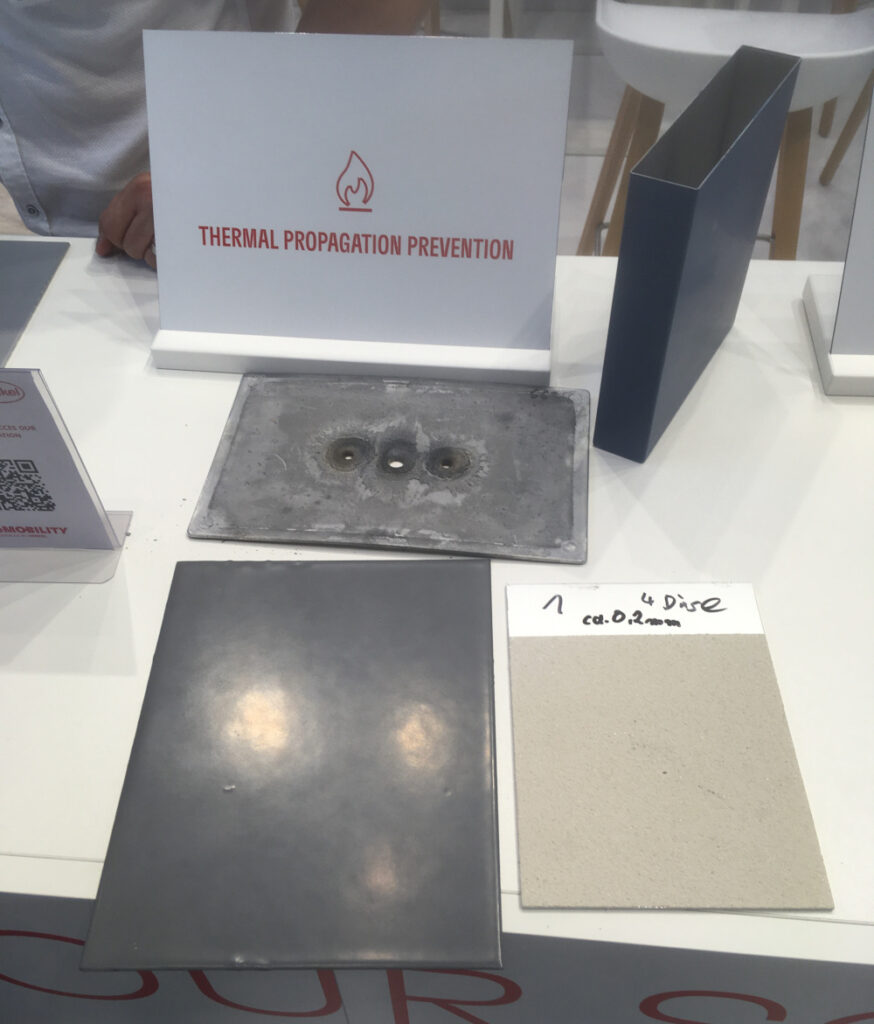
The bond is enabled by a water-based proprietary coating that activates the surface of the aluminium and allows it to ‘pick up’ the molecules of polyamide as it melts. “This can achieve around 60 MPa of lap shear strength, which is two to three times stronger than any adhesive,” he said.
The sides of the mini-module are formed by a pair of pressure plates that are bolted to the end pieces. These side plates compress the cells and also contain fluid passages and space for BMS circuit boards and sensors. A flexible foam between the cells allows for expansion and contraction as they charge and discharge. Aluminium top and bottom plates complete the mini-module, forming another very rigid torsion box.
The three-in-one modules can be stacked vertically, horizontally and end to end to forming mega-modules and complete packs. Where two modules meet end to end they share a single end piece, which handles structural loads, cooling and electrical connection for both.
“So in the volume of a conventional 60 kWh battery, you could pack almost 95 kWh. It’s all about packaging,” Giaume said.
Henkel revealed two new thermal coatings for battery packs at the show: the epoxy-based Loctite EA9400 and the water-based Loctite FPC5060. Both materials are designed to be applied to the inside of a battery pack lid. “If there is a thermal event, their job is to keep the heat and the fire inside the battery,” Asa Persson explained.
She told us that the epoxy material will keep the outside of the pack lid about 700 °C cooler than the inside, for example. “You have a lower temperature on the other side of the battery lid than with the water-based product, but in tests they have both shown the ability to withstand an 1100 °C fire for up to 10 minutes,” she said.
The single-component FPC5060 takes the form of a beige inorganic paste created by the aqueous synthetic resin dispersion method, and the cured coating does not produce smoke or fumes when exposed to heat.
FPC5060 is sprayed on to the part, and a 4 mm-thick coat cures at room temperature in 24 hours, or less if heat is applied. “We know short curing times are essential for OEMs, and we are looking at ways to reduce them,” Persson noted.
The two-component EA9400 is applied using a flat stream process, and after 60 minutes the battery lid is ready to be transported to the next station on the assembly line. After 120 minutes it can be loaded onto a carrier/truck, while after 180 minutes it is touch-dry.
Although initially intended for the inside of the battery pack lid, EA9400 can be used wherever heat needs to be kept away from critical parts. “Thinking of new applications, you could coat the corners near the tyres and wheels, and you can also coat surfaces vertically as well as horizontally,” Persson added.
Applied to the outside of the battery box, the epoxy material can also provide corrosion protection to the aluminium, while using it underneath could protect the battery from grass fires, for which all EV OEMs have a requirement, Persson pointed out.
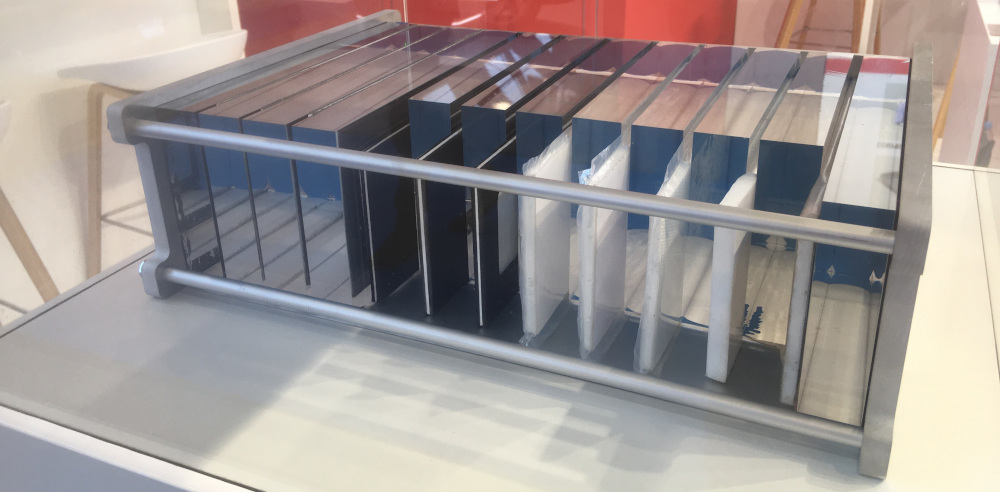
Henkel also introduced a new dielectric cell coating material based on acrylate 1K that is designed for rapid application.
“Dielectric protection is a pivotal challenge in EV battery pack design to protect cells from short-circuits that can cause cell failure and battery fires,” said Lucas Krahl. “Prismatic cell cans are typically be made from aluminium, and require special attention when it comes to dielectric protection, so they are commonly wrapped into thin polymer foils that feature a high dielectric breakdown voltage.”
In large-scale production of battery packs, the coating process from application to cure must take place quickly, he explained. “The important thing here is its fast curing under ultraviolet light, which takes seconds,” he said. In addition to its speed, UV curing also happens at room temperature.
“Its other key properties are a dielectric strength of more than 40 kV/mm, surface protection and compatibility with structural and thermal adhesives. If you want more from the cell, such as structural strength for the pack, our dielectric coating can provide strong adhesion.”
The coating is very thin, measuring less than 100 microns, so a thermal conductivity value of around 0.2 W/mK enables highly efficient cooling of the cells.
He added that the company is now looking into disruptive application options. “We can apply it using an automated spraying process, but there are also some new printing technologies we are investigating.”
Vehicle and battery OEMs are also looking for greater maintainability, and they particularly want to avoid having to scrap otherwise serviceable cells owing to a problem with the coating. “We are investigating laser cleaning so the coating can be completely stripped and a new one applied,” Krahl said.
Henkel is currently working on assembly and testing with customers, and Krahl expects the first to use the new coating in cell production from 2023.
Sabic discussed the progress in validating the fire-resisting performance of its Stamax fibreglass-filled polypropylene for battery cases, among other advances, according to Venkatakrishnan Umamaheswaran (known as UV).
Following the previous show in Stuttgart, we reported that a 2.6 mm-thick sample of Stamax had survived an 1100 °C burner test that blew right through a standard 1.5 mm-thick aluminium battery cover, protecting itself with intumescence and limiting the temperature on the non-exposed side to 85 °C. Since then, UV explained, it has survived a more representative test devised by Underwriters Laboratories (UL).
“We now have a lot more validated data from our work with UL, which is coming out with a more homogeneous way of testing,” he said. “Industry currently lacks standardised tests, and each car manufacturer uses its own.
“UL has more realistic test that involves building a module and forcing it into thermal runaway without applying an external flame, so the fire starts as it would in an EV in response to high temperature and pressure. Further, there are various tests for mechanical performance, thermal ageing and fatigue resistance, and Stamax has done well in those.”
Sabic’s battery crash protection material, Xenoy HTX, has been validated in crash testing that confirmed that its performance holds up in extremes of temperature after going through high-temperature manufacturing processes. It is a polyester-based resin that is formed into an impact-absorbing honeycomb structure.
“The primary concern is that the material must withstand high e-coat oven and paint line temperatures, then maintain its crash performance in very cold temperatures,” UV said. “We highlight the cold temperature impact to -20 °C and e-coat oven capability, which is unique for a plastic that isn’t a multi-component material. There are composites that will do that – some of them very exotic – but this is a regular solution that you don’t have to pay a king’s ransom for.”
The company also launched its Bluehero umbrella initiative for its automotive plastics expertise spanning the materials, application, design and manufacturing knowhow at the show.
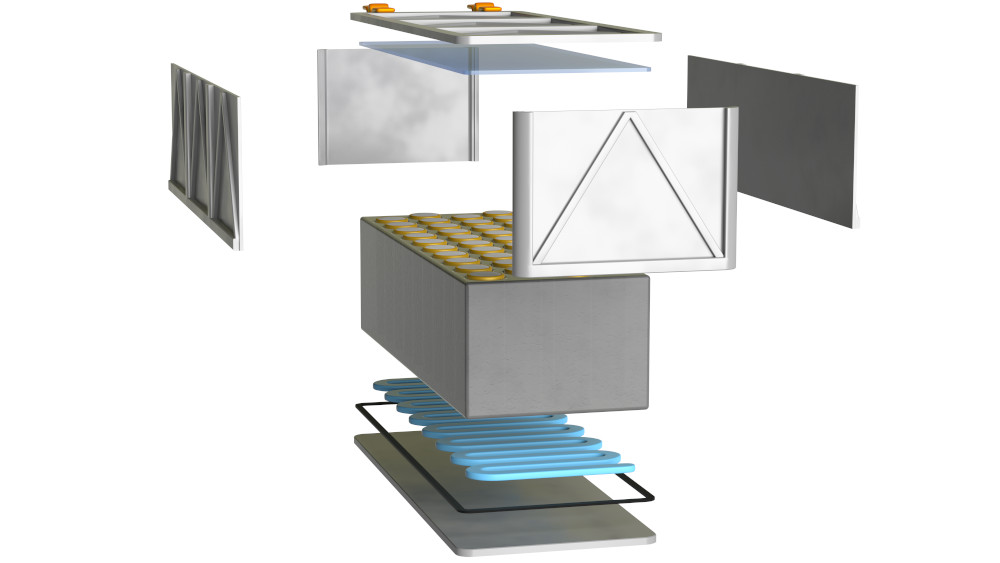
Dow presented new silicone– and polyurethane-based gap fillers, adhesives, pottants and battery enclosure materials at the show, which also provided the first opportunity for an insight into the company’s MobilityScience platform. This is intended to meet changing industry needs through materials science and support of customers’ development of applications, said Dr Esther Quintanilla.
“The idea is to bring the best combination of materials in our portfolio together and offer solutions using different technologies,” she added.
Among the Dowsil range of thermally and electrically conductive solutions, Dow introduced TC-5533 Gap, its silicone-based material for battery thermal management applications called Filler, along with polyurethane (PU) materials from the Voratron range.
A two-part, soft, thermally conductive material, Dowsil TC-5533 is designed to dissipate heat and relieve mechanical stresses between battery modules and cooling plates. With a thermal conductivity of 3 W/mK, it also has a low density of 2.6 g/millilitre.
Characteristics that ease its use in battery manufacture include low and stable dispensing pressures from drums, low abrasion and very low stresses during assembly. It is also formulated for a long working time of more than 90 minutes at 25 °C, with a cure time of less than 18 hours at that temperature, and for low emission of siloxane volatiles, with less than 100 ppm. It is also designed to be reworkable, with low pull-off forces to ease repair and recycling.
Other silicone materials have been designed to enable long-term module/pack operational stability, while also providing fire protection in the case of a thermal runaway.
The Voratron brand is a range of PU systems that enable the development of thermally conductive and non-thermally conductive adhesives, gap fillers and pottants/encapsulants for a broad range of battery types, including those based on prismatic, pouch and cylindrical cells.
Dow displayed materials from both its silicon and PU ranges in a case reminiscent of a car battery pack. “We’re showing high-strength adhesives used to assemble battery cells or install them into modules to provide structural strength as required,” said John McKeen.
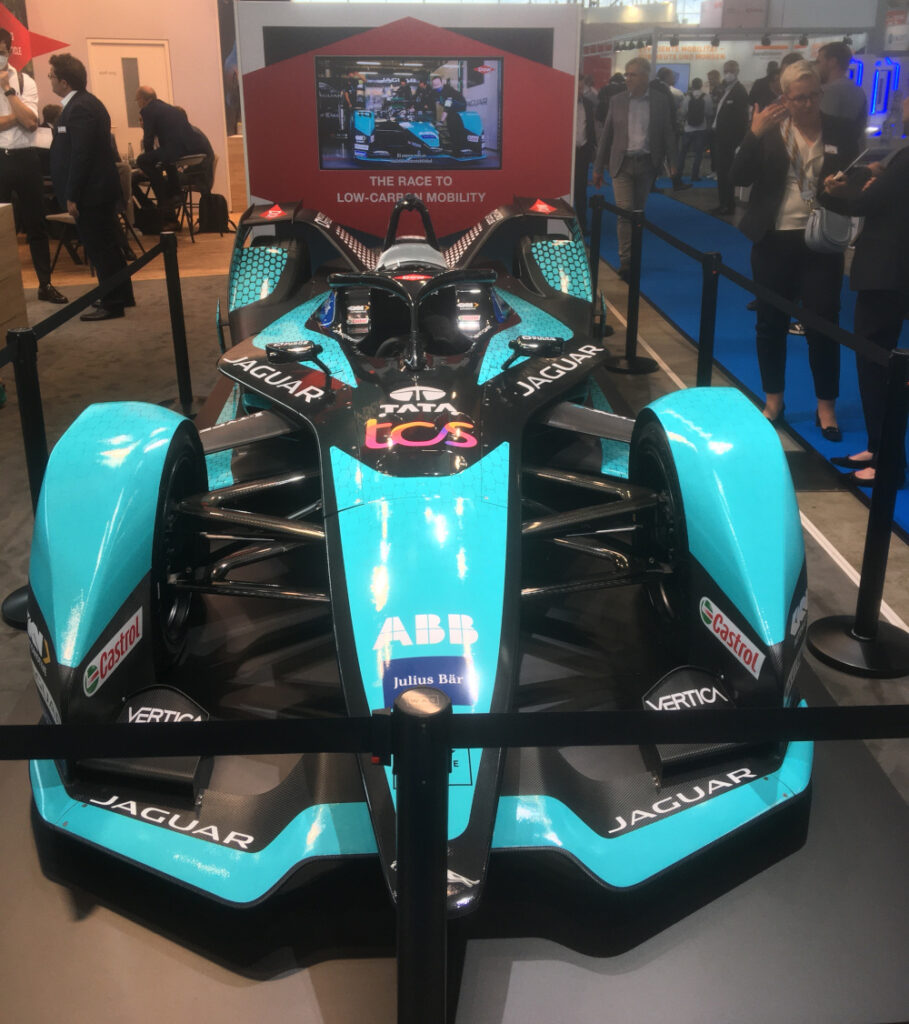
“Both PU and silicone foams can be used to help deal with mechanical stress and thermal runaway,” he added, “and both PU and silicone gap fillers are available with a range of thermal conductivities of 1 to 1.5 lower end and from 3 up to 6 with the silicone at the higher end.”
An example of the latter is the new Dowsil TC4060 thermal gel for power electronics applications.
Paulo Diena noted a growing interest in the use of composite materials and foams in battery pack lids. PU foams have been used for decades between composite layers.
“The foam is used to keep the composite skins at the right distance apart for the desired mechanical properties in the sandwich structure,” he explained. “We also have a PU fibreglass composite. Weight will be a bit higher, but stiffness is 10 times higher than with the foam.”
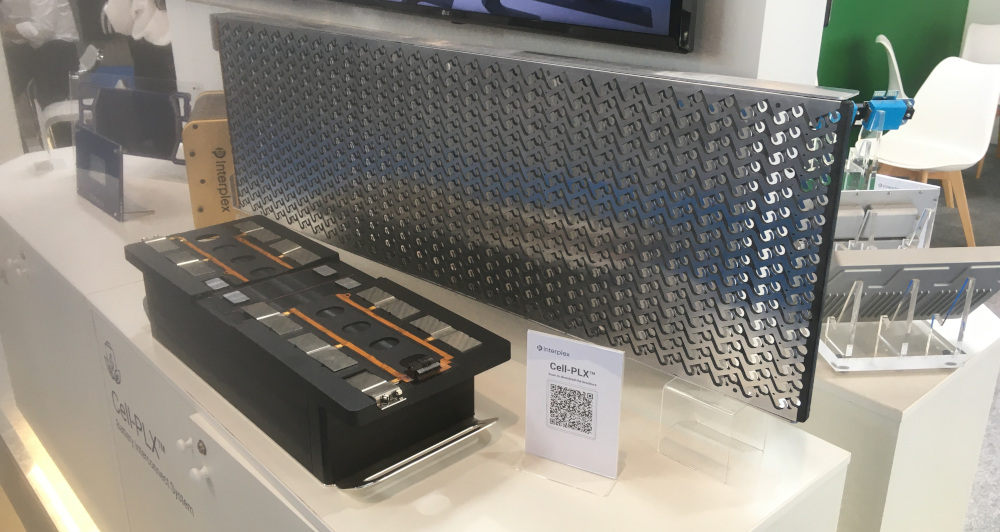
Interplex showcased its Cell PLX battery interconnect solution at Stuttgart. Large battery packs can have huge numbers of cells, particularly when the smaller cylindrical types are used, so speeding up the process of connecting them to each other and to the pack’s busbars though automation is important, something that that the company has addressed.
Each Cell PLX system is custom designed and stamped out of sheet metal for every application. “Our core capabilities are interconnects; we connect power systems together,” Randy Tan explained. “With Cell PLX, we design an interconnect system on top of the array of cells, and can optimise it for whatever is needed in terms of power, current or even thermal distribution, and design it to the customer’s specification.”
On display at the show was a 1.5 m-long example designed to connect up to 1000 cylindrical cells in series or parallel and made from a tough aluminium plate. The stamped sheets for Cell PLX systems are usually 0.3 or 0.5 mm thick.
The example system was designed for cells with both the positive and negative terminals on the top, and included two return busbars that also form the module’s positive and negative terminals. “We also include a signal path to collect voltages and temperatures from battery modules and send the data to the BMS,” Tan explained.
This example was also designed for a vehicle with four large battery modules under its chassis. “The customer takes our product, puts it on top of their modules and sends it into an automatic machine that completes the welding within 2 minutes. To complete an EV battery with four modules you need about 10 minutes,” Tan said.
Tan pointed out that as EV battery modules are getting larger, so demand for Interplex’s ability to stamp thin aluminium components in large formats of up to 2 x 0.5 m is increasing.
The company’s development roadmap includes allowing individual cells to be replaced if customers ask for that capability, as well as accommodating cell-to-pack and cell-to-chassis battery architectures.
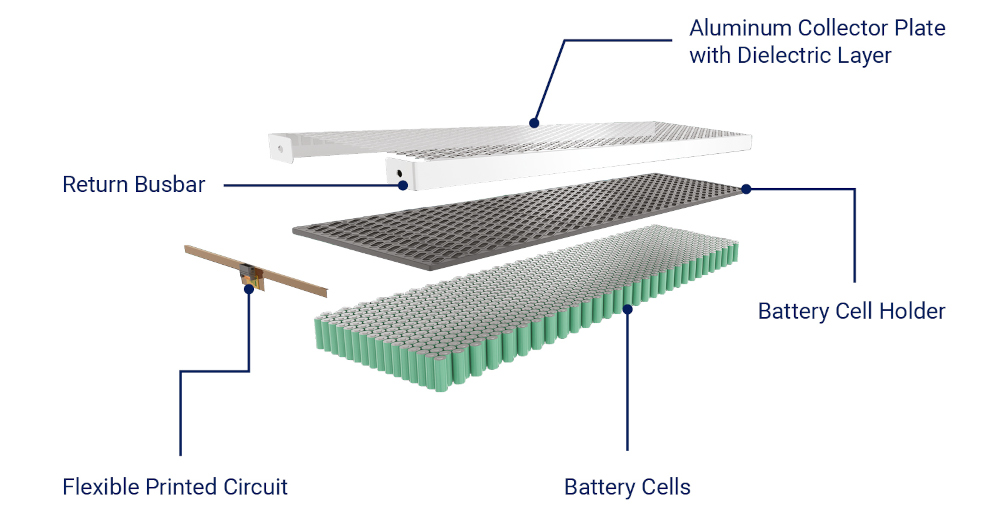
Breathe Battery Technologies exhibited its system for optimising the control of battery charging and discharging to safely reduce charge time, improve performance and extend service life. Breathe is a member of a new generation of specialised companies that is emerging to offer intelligent software for batteries in applications ranging from consumer electronics to EVs.
“We work with OEMs and their suppliers to put a small fraction of the total software on their BMS,” Dr Ian Campbell said. “Our software usually influences the charging process and either makes it much faster in the case of our Breathe Charge product or much healthier in the case of our Breathe Life product.
“Cycle life is significantly enhanced, capacity retention is better, OEMs face less warranty risk, there’s a better experience for the user from day one to the end of the battery’s life, and the battery is better prepared for its second-life application.”
While that might seem to be a key area for battery and vehicle OEMs, Dr Campbell emphasised that Breathe Technology is focused solely on these intelligent software functions.
“That means we can put a lot more time, energy and investment into that one specific area to extract the most performance from the battery system,” he said. “We currently have ten PhDs in the company, and a lot of those are in the battery algorithm development area.”
Breathe Charge and Breathe Life are off-the-shelf products, he said, although there is some preparatory work to do for each customer application. “Companies send us their battery system or cells, we do a little calibration for them, our software team works with theirs on the integration, and the application drops into their existing hardware and software architectures,” Dr Campbell explained.
“Our software is a very lightweight battery model that runs in real time on the BMS, and understands what’s happening electrochemically in the cells across the pack, and there’s an algorithm that’s making intelligent control decisions,” he added.
“It effectively says, ‘OK, now the charging current should be at this level’ to balance the performance with the health of the battery based on the model and the insight we have into the battery’s health at a given moment. It does this in real time as you are charging the battery and as the battery is ageing as well, so the software always treats it as it needs to be treated.”
Breathe Charge, for example, has been applied to Varta’s Easy Blade 48 V lithium-ion battery, which is used primarily in small and medium-sized vehicles such as industrial automated guided vehicles and forklifts. In this battery, Varta reported, it reduced charging time by 27%, saving 23 minutes, and enabled 3% more energy to be stored in the cells without affecting service life.
Spun out of Imperial College London in 2019, Dr Campbell the company is building up a portfolio of software functions to get the most out of a battery in all respects.
He added that there is a massive amount more to get out of batteries just by understanding them better. “All the automotive OEMs are acknowledging how important intelligent software functions will be for the differentiation of their brands over the next decade,” he said.
Brill Power has patented a novel approach to battery management that incorporates power electronics at the level of connections between cells and groups of cells within the pack, said Stuart Grondel.
“It allows the power electronics to actively manage the load between the series connections, ensuring that every battery cell is used to its full potential during the pack’s life,” he explained. “By varying the load between cells in proportion to their health, we enable the cell degradation curves to converge instead of diverge. That way you end up with a battery pack that lasts far longer.”
Basic functions of a BMS include protection from overcharging and over-discharging, and passive balancing of the cells. Cell balancing in a passive system relies on the dissipation of excess energy in certain cell groups at the top or bottom of charge, which is inherently inefficient because the energy is dissipated as heat using resistors, Grondel said.
A little more advanced is active balancing, he added. This involves shifting a small amount of current (usually less than 1 A) between cell groups in the pack, effectively shifting the charge around rather than dissipating it as heat.
Brill Power calls its approach ‘active loading. “Basically, we can divide up the full battery current and send it in different proportions to different cell groups, and we do that in proportion to that particular cell group’s health,” Grondel said.
This is where the power electronics come in, as the key switching technology the system relies on are transistors, specifically MOSFETs. “The MOSFETs can switch cell groups in and out at a very high frequency, ultimately creating a form of pseudo duty cycle or load profile for a given cell group,” Grondel explained.
The complete system includes power electronics, control electronics hardware with embedded firmware, and software. Most of the control at pack level is done by the main control board, with subordinate power and control boards at cell/cell group level. The main controller sends data via a web gateway to the cloud, where, for example, a fleet operator or owner can access it.
“A lot of the data analysis is done at the cell level by the boards themselves, while some of it is done at the cloud level and could be done retrospectively for analysis,” Grondel noted.
Brill power has commercialised the technology for stationary energy storage batteries, and is at the prototyping stage in the development of an EV application,. The company is working with vehicle OEMs to develop the technology into a product that can go into a vehicle, an effort that has so far involved lab-scale tests with Aston Martin and Delta Motorsport, and with which the Advanced Propulsion Centre UK and Innovate UK have been “hugely supportive”.
The system could be deployed on a vehicle at a meaningful scale within 2 years, according to Grondel.
ONLINE PARTNERS
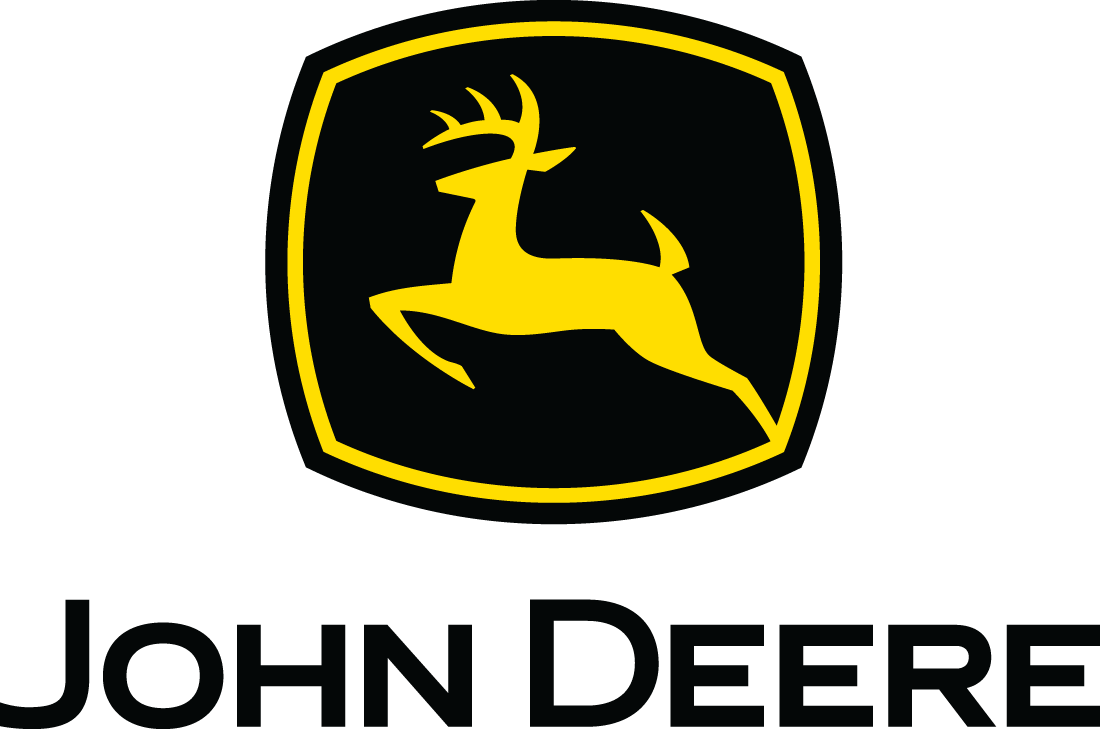
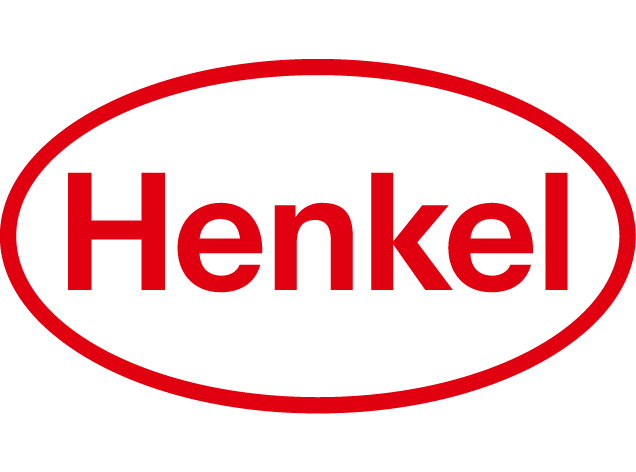
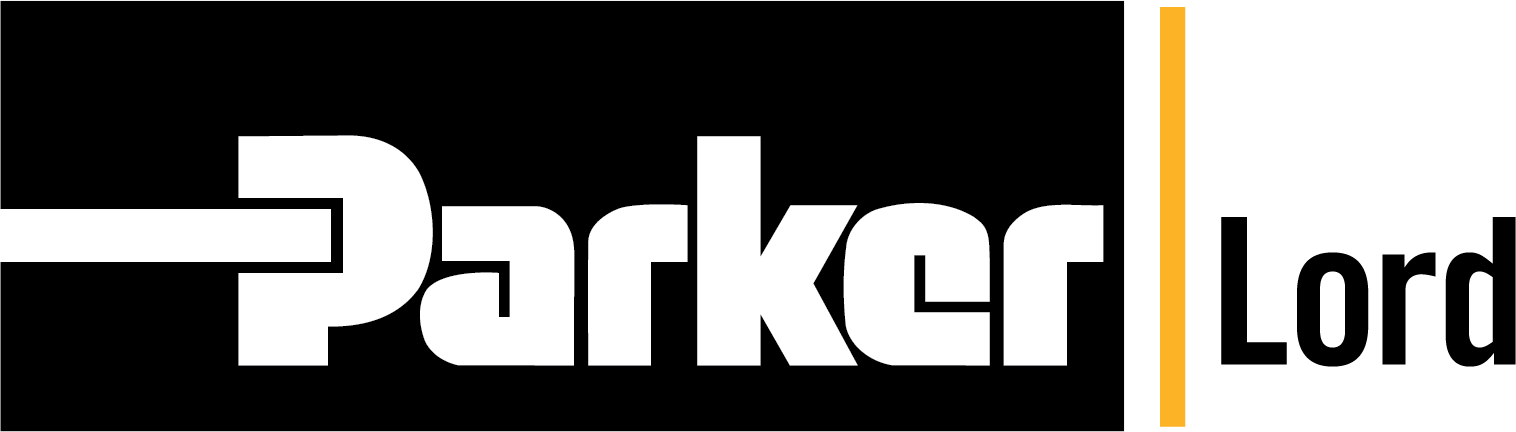
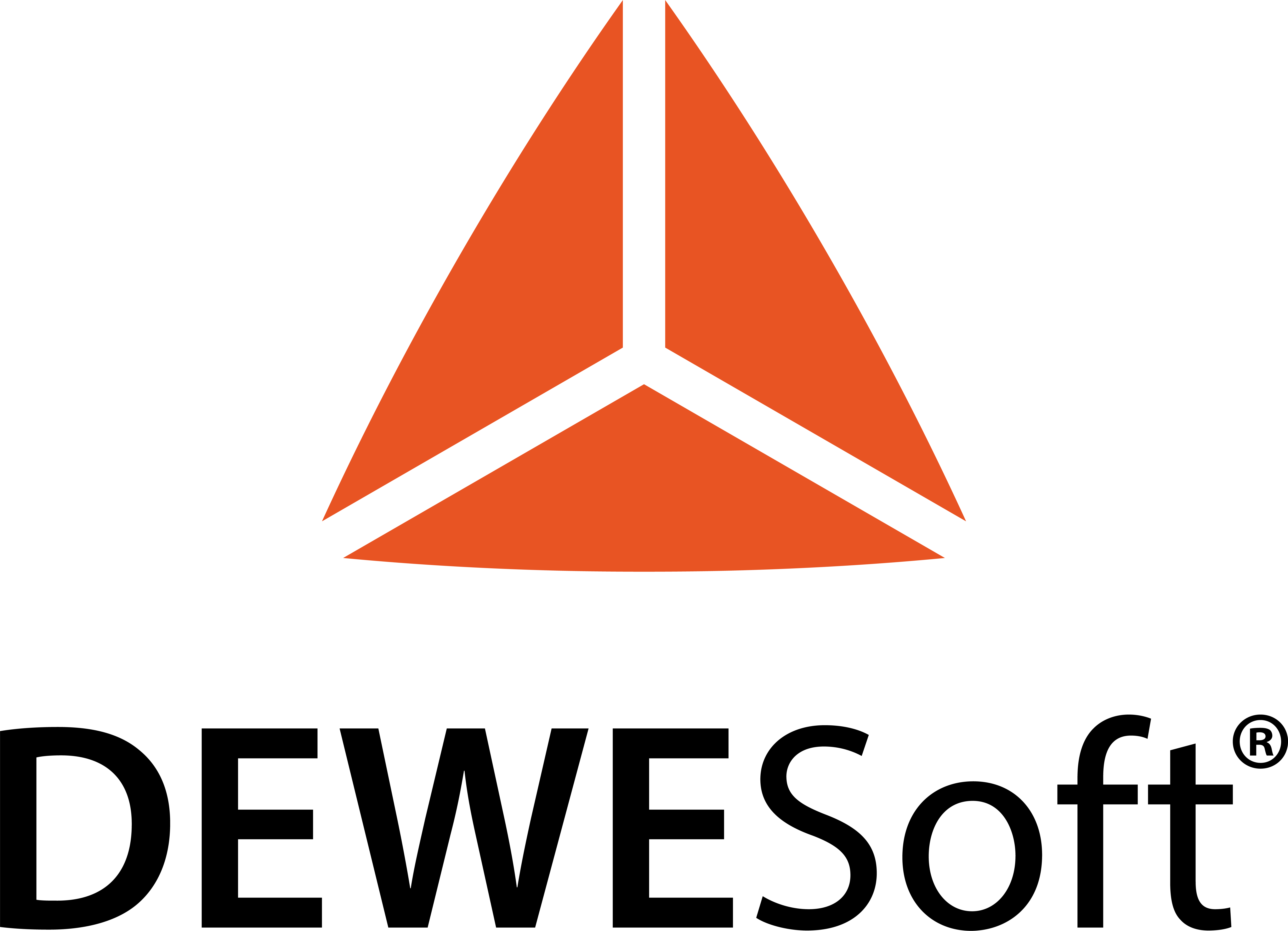
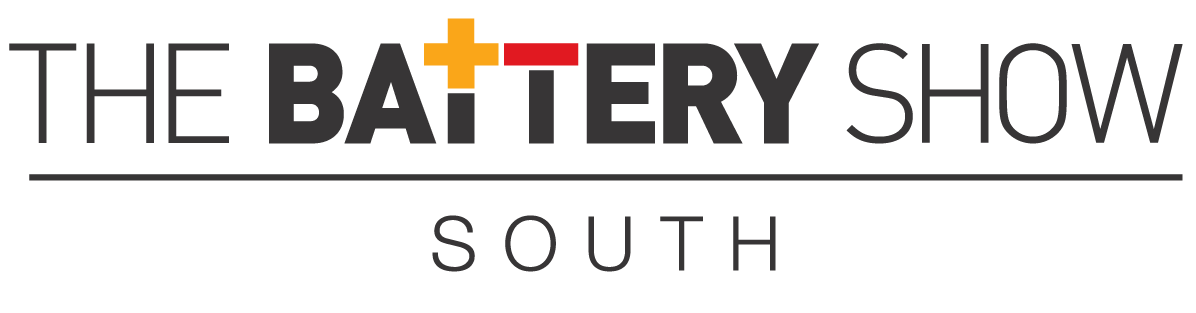
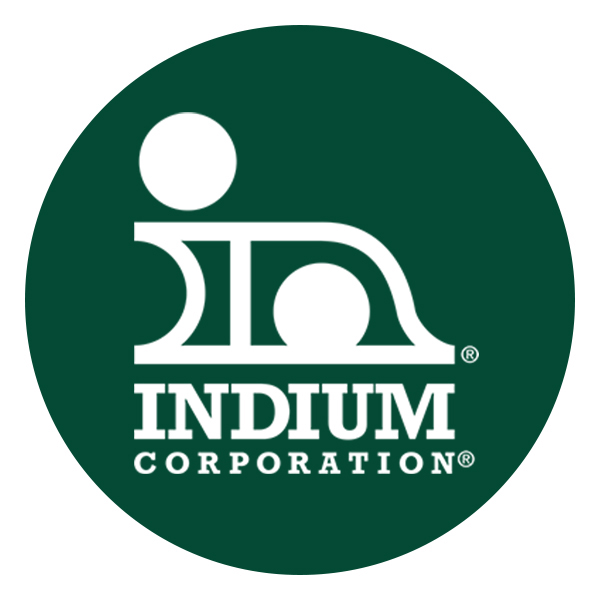
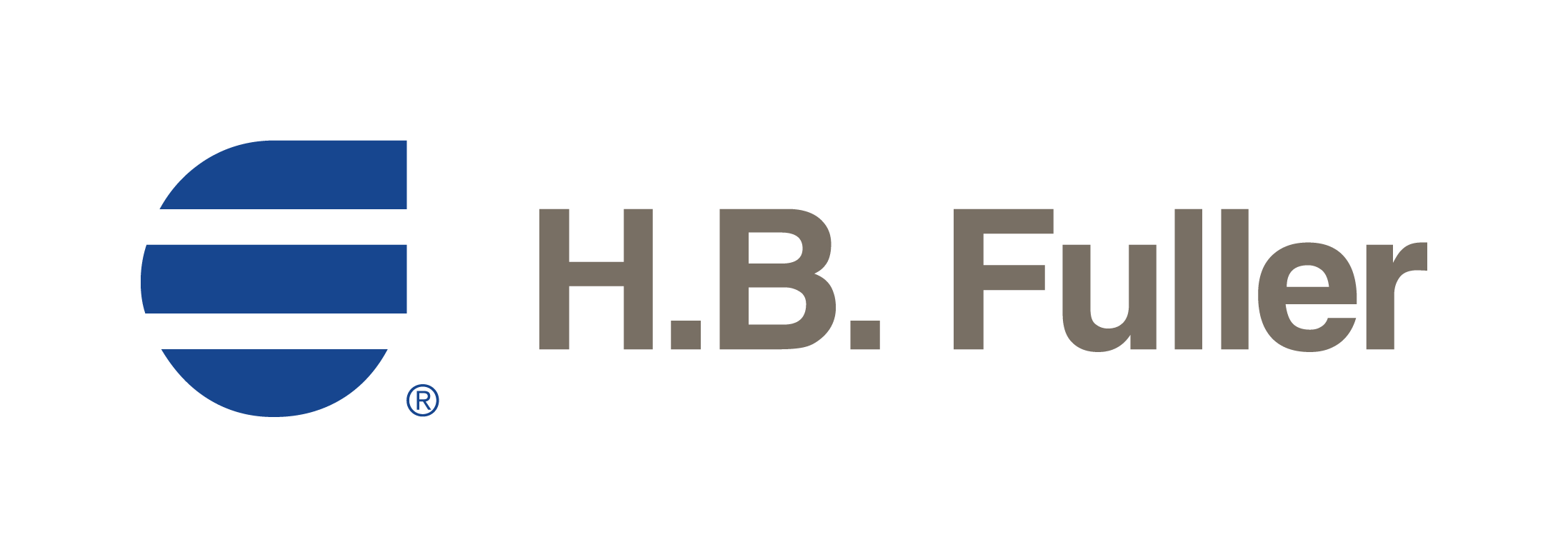