Battery recycling
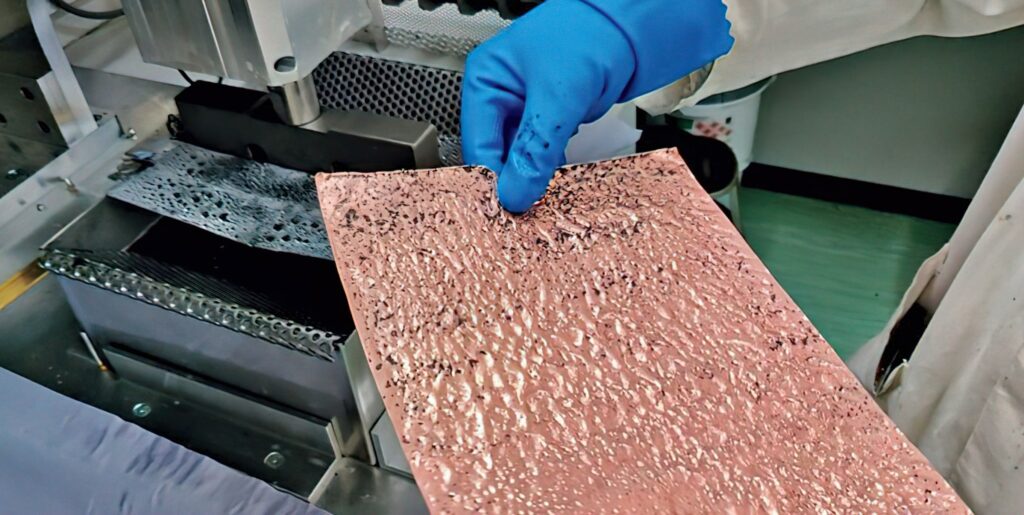
(Courtesy of University of Leicester/University of Birmingham/Faraday Institute)
Cell division
Nick Flaherty explains the various methods of recovering valuable battery materials, and why new processes are becoming necessary
Recycling batteries from e-mobility platforms, particularly lithium-ion and lithium iron phosphate (LFP) cells, is an area of increasing focus for the e-mobility industry.
Sourcing lithium, cobalt and manganese, even copper, for batteries from around the world leaves battery manufacturing companies vulnerable to geopolitical forces that can disrupt or limit the supply of these key materials, so battery makers are looking to recycling more of the existing batteries.
There are a number of very different approaches for recycling, some depending on the type of battery and others independent of format or battery chemistry. The coming generation of solid-state batteries could also lead to new approaches for recycling.
Before recovering the metals within them though, the packs can be re-used in a ‘second life’ application such as stationary power storage. When they are no longer reliable enough for vehicles they can be used to store power from wind turbines or solar farms, for example, or even in the home to store solar power.
For these applications, the battery management system (BMS) is a key factor. Wireless BMS connections on each pack give battery suppliers more options to re-use the packs, and the BMS nodes can be connected to different management software with machine learning algorithms that are optimised for stationary storage.
This can extend the life of an e-mobility battery pack from 5 years in a vehicle to 10 or even 15 years. Tesla for example re-uses the packs from it vehicles in its Powerwall system for home energy storage. Nissan will re-use the packs from its Leaf vehicles to store energy from solar farms and wind farms that power the battery plant alongside its car-making factory in Sunderland, UK.
But even these packs will need to be recycled, and different approaches are being adopted for this, with a focus on the speed of recycling. This is leading to changes in the design of the cell depending on the recycling approach, but it means that creating a universal recycling process is difficult.
The problem is exacerbated by the fact there are different formats for lithium-ion cells. Pouch cells are easier to dismantle, as they have flat sheets of electrodes and separators, while cylindrical cells need to be opened up and unrolled, and prismatic cells come in many shapes and forms. This is made even worse with structural batteries that can be in the sides or roof panels of vehicles, making disassembly costly and slow.
As a result, vehicle manufacturers are teaming up with recycling firms to optimise the design of cells and packs from their suppliers for their recycling partners. More than 1.3 Mt of battery cells are expected to be recycled each year by 2030, according to predictions of EV use and lifetimes, and this requires a considerable recycling infrastructure. This is up from just 100,000 t of batteries recycled in 2019, 70% of that in China.
There are currently only a few-large scale industrial process that can handle the growing amount of used lithium-ion batteries. Even the smaller pilot plants are still at the r&d stage and can’t process and purify all the different battery elements in an economical way. That means there is still a need for a process that can economically process all types of used lithium-ion batteries.
The recycling process
For the current recycling process, the first step is to discharge the pack completely, as there can still be significant amounts of charge inside. In the worst case, this can cause fires in recycling centres as the dismantling can cause short-circuits.
This takes time and requires specialist equipment to ensure safe discharging. Discharging a pack quickly for recycling means there are potentially large currents flowing, so any dismantling equipment has to be carefully isolated.
That has an impact on where the recycling is carried out. If, like Tesla, a car maker has control over the complete supply chain, then the pack recycling can be integrated into the production process and a specialist recycling plant with dedicated equipment can be built alongside the battery plant.
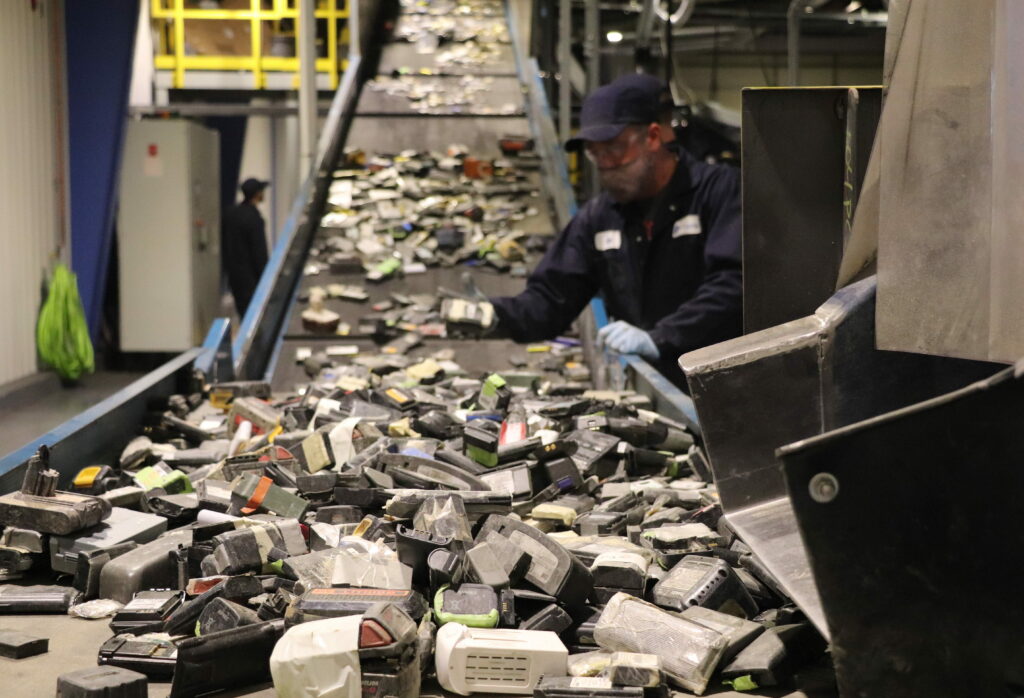
(Courtesy of Li-Cycle)
However, the trend towards battery ‘gigafactories’ means this can be a challenge, as the packs might have to be transported hundreds or even thousands of miles back to the recycling plant. There are also significant restrictions for safety reasons on transporting lithium-ion battery cells, especially exhausted cells that may be in an unknown condition.
All this means there is a demand for more local recycling plants, which requires more distributed specialist skills and equipment.
Many recycling systems work at the cell level, so the discharged pack also has to be dismantled. Again this has to be done by hand and can be time-consuming, but it does allow the plastics and some copper wiring to be removed. The sensors and wiring used for the BMS can also be removed, if they haven’t already.
However there is increasing interest in ‘all-in-one’ processes that can accept complete battery packs.
Currently, battery recyclers focus on the mechanical and physical separation of the different components of the batteries, such as the casing, current collector and the electrode materials. These processes usually involve crushing the batteries in a controlled inert atmosphere, and the crushed material is then separated by sieving, air and magnetic separation, then sent to other facilities for further processing.
After a mechanical separation of the plastic and/or metal of the pack, the cells are dismantled or shredded by powerful grinding machines, and the shredded materials can be recycled using one of two techniques.
The first, hydrometallurgical recycling, essentially uses a range of different acids as a solvent to recover the elements, which precipitate out of solution as salts. The exact solvents used tend to be proprietary information, in the same way as the formulation of the electrolytes in the cells.
The various active materials can be recovered using aqueous or organic solvents to dissolve the metal foil, the polymer binder, or the active material. The efficiency of this approach depends a lot on the shredding process.
The chemical process usually involves a leaching step to dissolve the metal oxides into the aqueous solution and different steps of precipitations and separations to obtain relatively pure metals. The processes are still in development and are expensive to operate because of steps such as liquid nitrogen immersion or the use of large quantities of chemicals.
Also, the treatment of any liquid waste has to be taken into consideration as the process can involve the use of strong acids, and any effluent can be toxic and difficult to dispose of safely. This drives the choice of chemicals used.
The other technique, pyrometallurgical recycling, uses temperatures of more than 1500 C to recover the materials, although at the expense of the plastics and graphite separator, which burn away. By heating at such high temperatures the organic polymers and the lithium burn away and the heavier metals such as cobalt, copper and nickel melt into an alloy, and any other materials end up as slag.
The metal alloys are sold to a metal smelter for separation but importantly the lithium is lost in the slag of those processes and can’t be recovered and sold, and the alloy sold possesses a fraction of the value of the separated and pure metals.
Another key point is that these alloys then re-enter the production process at the refining stage alongside virgin raw metal oxides. This process still requires significant amounts of energy for the refining process.

Ultrasound
Rather than shredding, another approach is to use ultrasonic sound waves in a liquid to dismantle the cells, which researchers say can speed up the recycling process by a factor of 100 and create a continuous process.
The ultrasound creates cavitation at the interface of the electrode and separator and enables rapid and selective breaking of the adhesive bond, enabling an electrode to be delaminated in a matter of seconds. This also produces a material of higher purity and value than the other recycling techniques that can potentially be directly recycled into new electrodes.
For recycling batteries, low-power ultrasound vibration at 50-100 W per gallon of liquid is used to assist the electrode delamination process in the cells. This process is slow, taking between about 5 and 90 minutes, depending on any electrode pre-treatment.
A more powerful method of ultrasonic agitation is to place an ultrasonic horn called a sonotrode in the liquid close to the electrode. The delamination of the electrode can take less than 10 seconds when the electrode is placed directly under a high-power sonotrode delivering 1000-2000 W, breaking the adhesive bonds between the active materials and current collectors. This could potentially lead to the recovery of the intact current collector.
The power needed depends on the strength of the adhesive bond between the current collector and the active material, and that depends on the particle size of the active material and the type of binder used.
This approach has been used on batteries from various Nissan Leaf cars, where the packs use a pouch cell. The cells were disassembled by hand and rinsed in dimethylcarbonate to remove their lithium hexafluorophosphate electrolyte.
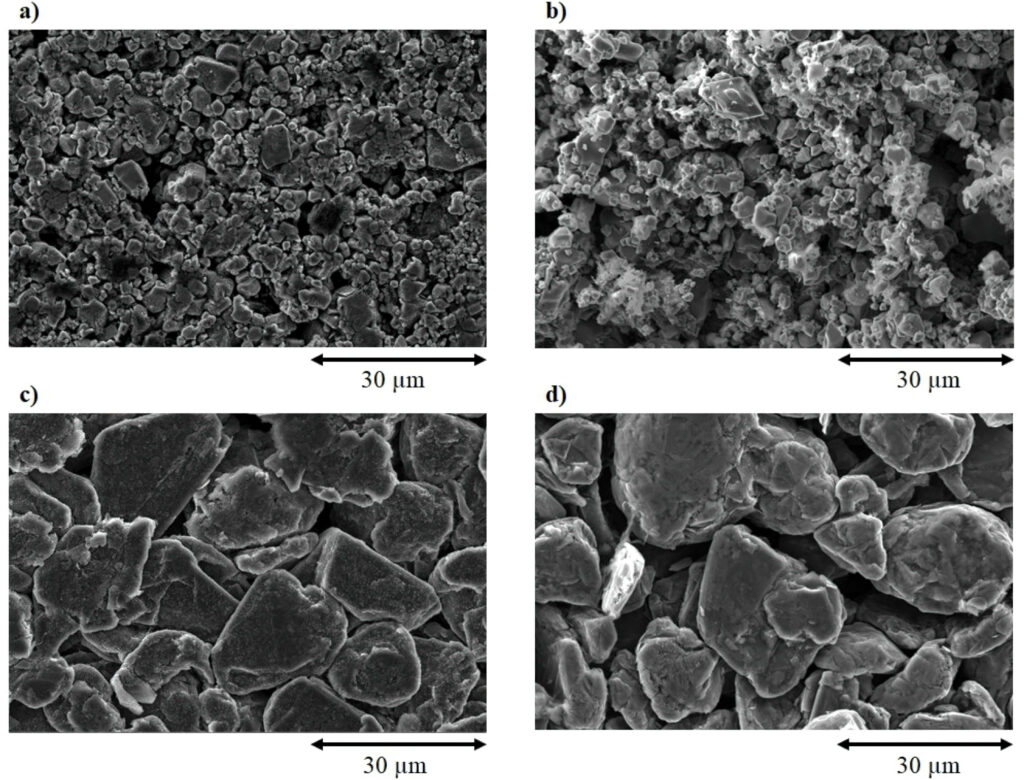
(Courtesy of University of Leicester)
Scaling up
A sonicator stack consisting of a converter, a booster and a sonotrode mounted on a frame is then used to separate the different parts of the pouch cells.
The anode sheets consist of a 15 µm-thick copper foil current collector, coated on both sides with 70 µm-thick active material that contains graphite and a binder material. The average particle size of the graphite is 15 µm diameter, and the total size of the anode is 20 cm x 23 cm.
The cathode sheets consist of a 25 µm-thick aluminium foil current collector that is coated on both sides with a 100 µm-thick active material that contains a mixture of lithium manganese oxide (LMO) that is typically 12 µm thick and lithium nickel manganese cobalt oxide (LiNiMnCoO2 or NMC) powder with carbon-black conductive additive and 5% PVDF binder. The average particle size of the NMC is 6 µm diameter, and the conductive additive 0.05-0.1 µm in diameter. The total size of the cathode is 19.5 x 22.5 cm.
A commercial 1250 W ultrasonic system with a 20 mm-diameter cylinder sonotrode delivers a power intensity up to 398 W/cm2 from the sonotrode’s front surface. At the frequency of 20 kHz, cavitation bubbles oscillate before growing larger and then collapsing.
For fast delamination of pouch cell-type batteries from an EV, a high-power ultrasonic unit operates at 20 kHz and at a maximum power of 2200 W. The sonotrode’s front face area is 1.5 x 21 cm2, and it can deliver a maximum power intensity of 70 W/cm2.
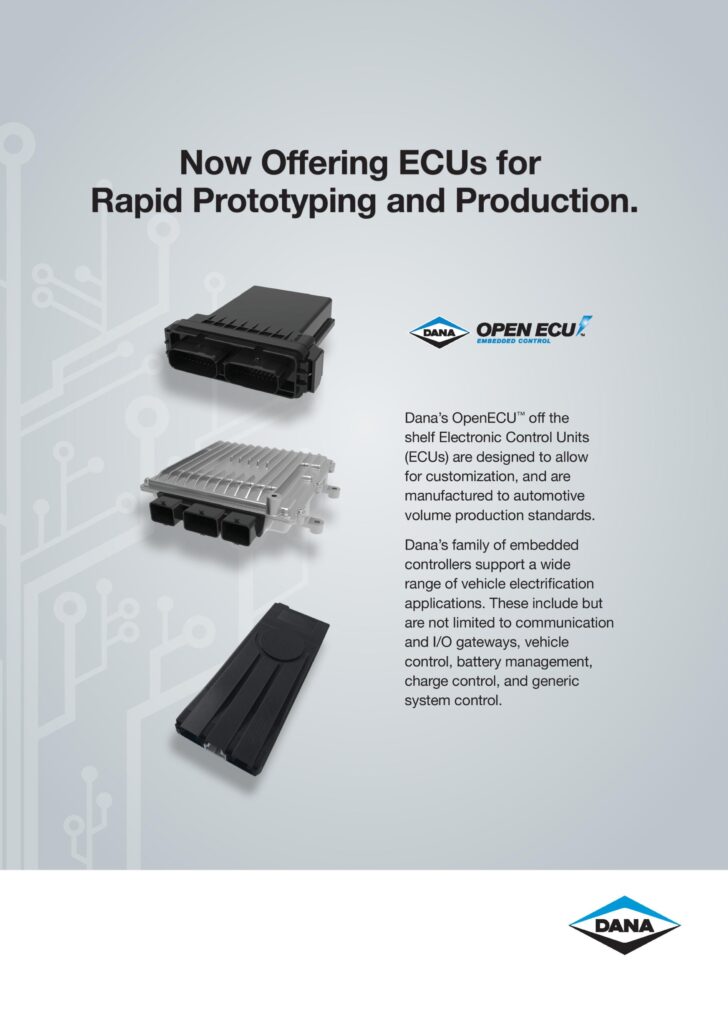
A bath consisting of a tank and basket is placed directly under the sonotrode, where the delamination takes place. In the delamination process, the electrode is fed into the 3 mm gap between the sonotrode and the sample tray at a rate of 2 to 3 cm/s and comes out on the other side of the sonotrode as delaminated metal foil. The active material coating disperses into the solvent tank and can be easily recovered via filtration of the solvent.
A high-speed camera operating at 20,000 frames/s monitors the dynamics of the sonotrode in water, showing a conical bubble structure created by vapour-filled cavities, which continuously and randomly generate and implode. The cone-like bubble structure formation is a combined effect of acoustic radiation and attraction forces between the bubbles, a so-called secondary Bjerknes force.
At a higher power intensity of 200 W/cm2, many more cavitation bubbles were generated, but without the conical bubble structure that formed at the lower power intensity. Instead, the bubbles can be seen moving swiftly away from the sonotrode, forming a chaotic jet that is strongly repelled by the large acoustic waves traveling from the front surface.
Using ultrasound at 120 W/cm2 on anode and cathode allowed delamination of a lithium-ion battery anode, where the graphite particles are bound to a 15 µm thick copper current collector using a binder. This is carried out in 0.05 M citric acid solution for 3 seconds. The citric acid was used as a wetting agent for the copper foil and increasing the citric acid concentration did not further aid the delamination process.
Rapid delamination on both the front and back sides of the electrode was achieved when the distance between the sonotrode and sample was 2.5 mm but the copper foil became wrinkled owing to the action of pressure waves.
The effectiveness of the technique also depends on the type of binder used. When PVDF was used, delamination in water was slower and less uniform. This is partially due to a mixture of surface wetting, polymer solubility and the presence of interfacial voids, which are important considerations in the delamination process.
Delamination of the NMC cathode with a binder was successful using an aqueous solution of 0.1 M sodium hydroxide. The same could also be achieved using an organic solvent, such as N-methyl-2-pyrrolidone (NMP). The 3 second experiment time was insufficient for chemical etching to delaminate but it clearly helps to break the interfacial adhesion.
The technique does not depend on the chemistry of the active material, and has been tested on a variety of cathode materials including NMC/NCA + LMO, NMC-532, and LFP from commercial cells as well as a range of end-of-line car cells with different chemistries. The technique worked equally well on all samples but is more dependent on the binder and its ageing.
The electrodes used in the Nissan Leaf pouch cells are typically of the order of 20 cm wide. To delaminate these, a high-power ultrasonic unit was built with a front face on the sonotrode with an area of 1.5 x 21 cm which operated at 20 kHz and a maximum power of 2200 W, and produces a maximum power intensity of 70 W/cm2.
Interestingly, delamination is easier and faster when the electrode material is moving under the sonotrode, as crack propagation aids delamination. These cracks will start at voids in the numerous interfacial boundaries of the layered structure of the electrode. For both cathode and anode, it can be seen that the aluminium and copper foil current collectors have been effectively delaminated on both sides, leaving the foil relatively free from active material.
The physical structure of both cathode and bulk anode materials were unaffected by the delamination process. However, the larger particles of graphite in the anode appeared to have been ‘cleaned’ of smaller particles, most likely a carbon-black conductive additive. While the delamination will occur in deionised water, the efficiency of separation can be improved by adjusting the pH to etch the substrate, or by adding wetting agents to aid the collapse of the cavitation bubbles.
While binder-specific solvents such as NMP also enable rapid delamination, by partially dissolving the binder, this is probably not a viable practical option owing to its cost and toxicity. Volatile solvents such as ethanol are unsuitable because of their volatility, lack of polymer solubility and inability to support suitable cavitation.
Depending on the choice of delaminating solvent, the delaminated active material will also contain the polymer binder. A significant proportion of battery waste material originates from production scrap with various polymers. These can be recovered with acetone to rebind the active materials to a substrate.
This approach had shown recovery of 99.5% of active material for both the anode and cathode. At under 3 µm, the unrecovered 0.5% of active material comprises particles that are too small to easily be recovered via filtration techniques; an example here is additive called carbon-black, which has particle sizes of 0.05-0.1 µm.
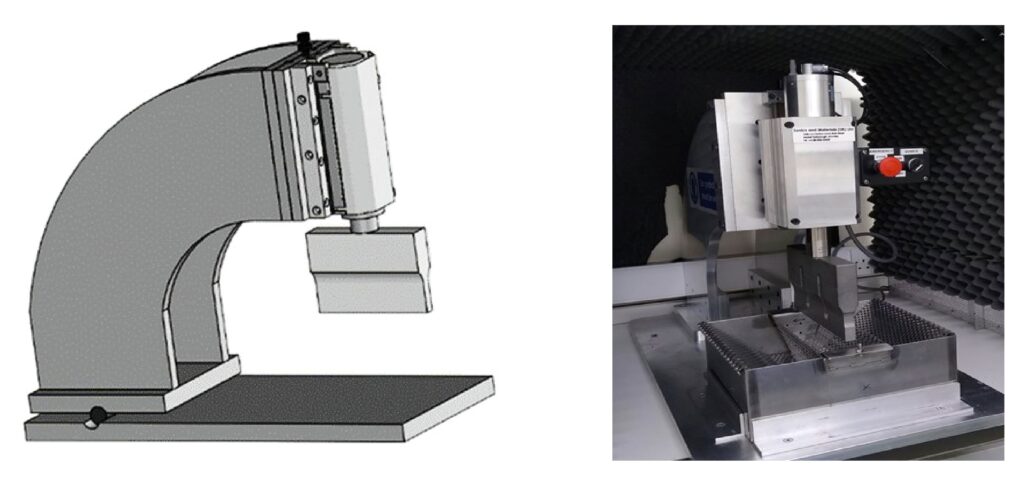
(Courtesy of University of Leicester)
This compares with about 67% efficiency when recovering cathode material using a stirred sulphuric acid solution.
The delamination rate for both electrodes with ultrasound was 44 cm2/s, so the prototype unit is capable of processing 350 of the 20 x 20 cm electrodes per hour at a cost of $0.10 to 0.15/kg of electrode material.
The ultrasonic delamination technique is designed to work on whole rather than shredded electrodes, which makes it particularly suitable for production scrap and quality control reject material, which accounts for about 5-20% of production.
The challenge is that existing cell designs do not lend themselves to disassembly. However, this could be financially preferable to shredding, and produces higher purity products with a lower chemical and energy requirement. Many manufacturers are also designing cells that are easier to disassemble and recycle.
This ultrasonic technique will become more significant when solid-state batteries need to be recycled, in about 10 years’ time. As the name suggests, the battery cells do not use a liquid electrolyte, instead they have a ceramic layer. An ultrasonic process may well be a key tool in separating these layers for quicker and more reliable recycling.
All-in-one shredding
New approaches are overcoming the challenges of having to disassemble a pack and even the cells by hand to get at the electrodes.
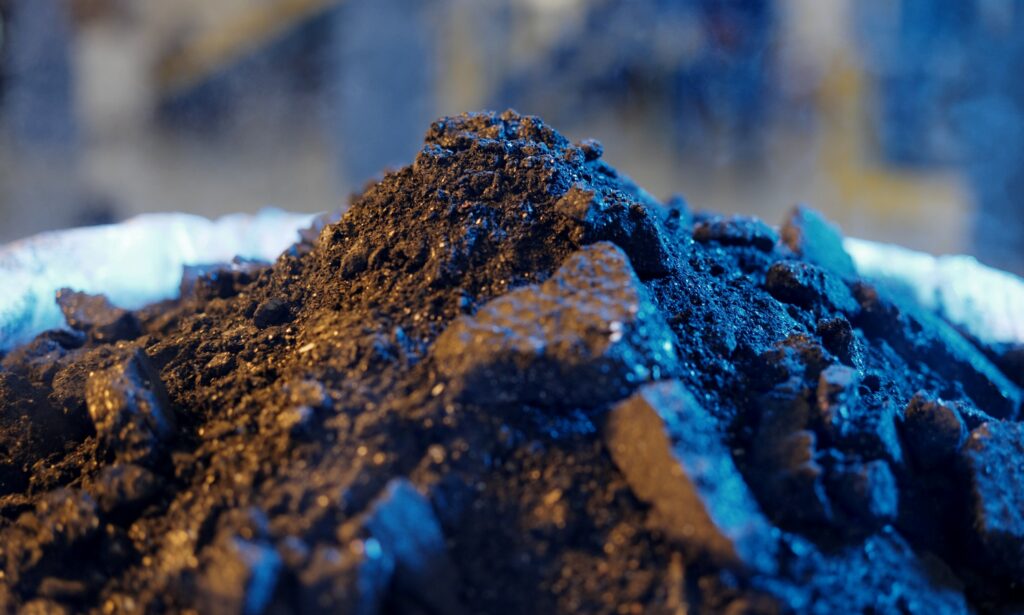
(Courtesy of Li-Cycle)
Packs can be recycled directly, using a powerful shredding machine submerged in an ionic fluid. The packs are shredded in the fluid that discharges the pack as it is destroyed. The plastic shreds and copper foil float to the surface for recovery, while the rest sinks to the bottom. This creates a ‘black mass’ of all the different elements.
The lithium can be recovered as lithium carbonate, while the cobalt and manganese are recovered as sulphates. These can be 97% pure and fed back as a cathode material precursor for building cells.
With this all-in-one approach, a spoke-and-hub model with an all-in-one shredding technique allows all kinds of batteries – not just EV cells – to be easily recycled, as no disassembly is required. It takes all kinds of lithium-ion batteries from packs used in power tools to EV packs and produces the black mass that can be more easily shipped to the purification plants alongside those developing the precursor materials.
Another patented approach is to immerse the shredded lithium-ion batteries in an organic solvent and then fed into a dryer producing a gaseous organic phase and dried battery residue. The resulting powder is fed into a magnetic separator to remove magnetic particles such as steel and iron from the pack, and then an eddy-current separator can be used to extract the aluminium and copper.
Grinding the non-magnetic residue and mixing the fine particles with an acid produces a metal oxides slurry. Leaching this slurry and then filtering the leachate removes the non-leachable metals before feeding this into a sulphide precipitation tank. Mixing this leachate with an organic extraction solvent separates the cobalt and manganese using solvents and electrolysis, then crystallising sodium sulphate from the aqueous phase and adding sodium carbonate to the liquor and heating up the sodium carbonate to produce a precipitate of lithium carbonate.
When dried, the lithium carbonate has a purity of 99% and is suitable as the starting point for new battery cells.
As a final stage, the graphite can be purified from the non-leachable materials in a furnace operating at up to 800 C and combining the two recycling techniques. This also reduces the amount of effluent, but has an issue with power consumption for the furnace. This opens up new models for recycling the batteries.
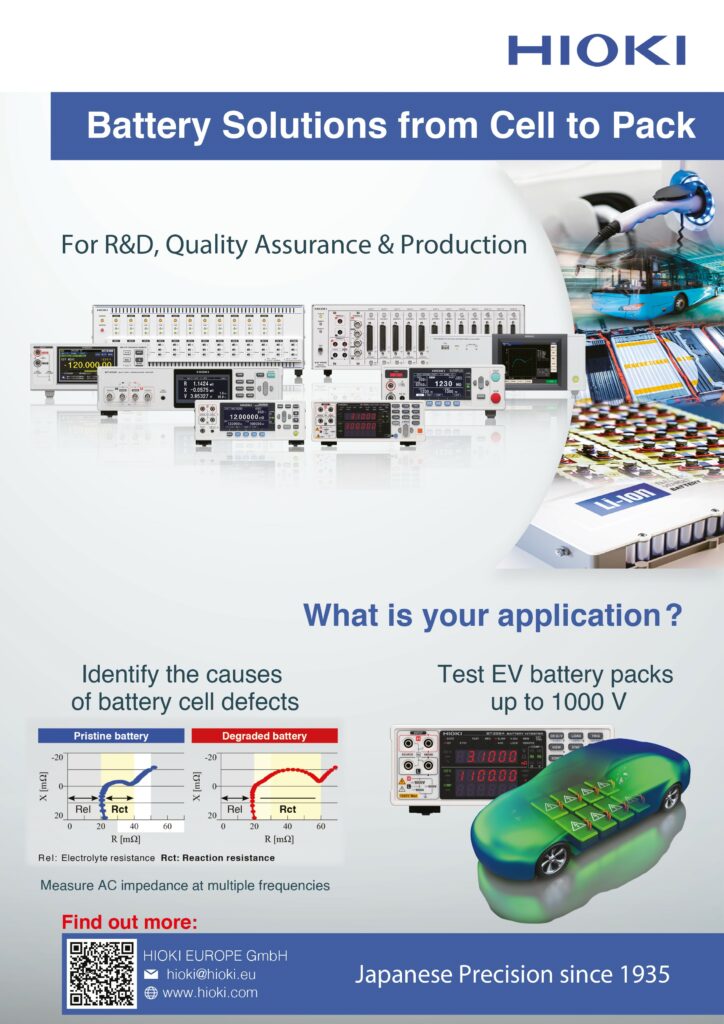
Conclusion
Battery recycling has a wide range of challenges, not just in the process to recover the precious lithium and other elements. Re-using the cells in other applications leads to additional requirements for BMSs, and spreads out the packs across wider areas in homes, offices and wind and solar farms.
This also presents challenges for how the battery packs are eventually recycled. While car makers may have more of a closed-loop approach to taking exhausted packs from vehicles and recycling them, the increased adoption of second-use applications presents more transport challenges for the packs.
This is leading to recycling firms to develop hub-and-spoke models, where the shredding of packs can be performed more locally, avoiding the challenges and safety issues of transporting exhausted packs. This means the ‘black mass’ of recycled material can be easily and safely shipped to the cathode-making plants as a precursor material.
However, the focus on new recycling processes such as ultrasonic dismantling may well be become more significant with the advent of solid-state batteries that need to be recycled.
Acknowledgements
The author would like to thank Kunal Phalpher at Li-Cycle and Chunhong Lei at the University of Leicester and the Faraday Institution for their help with the research for this article.
Recycling other EV battery chemistries
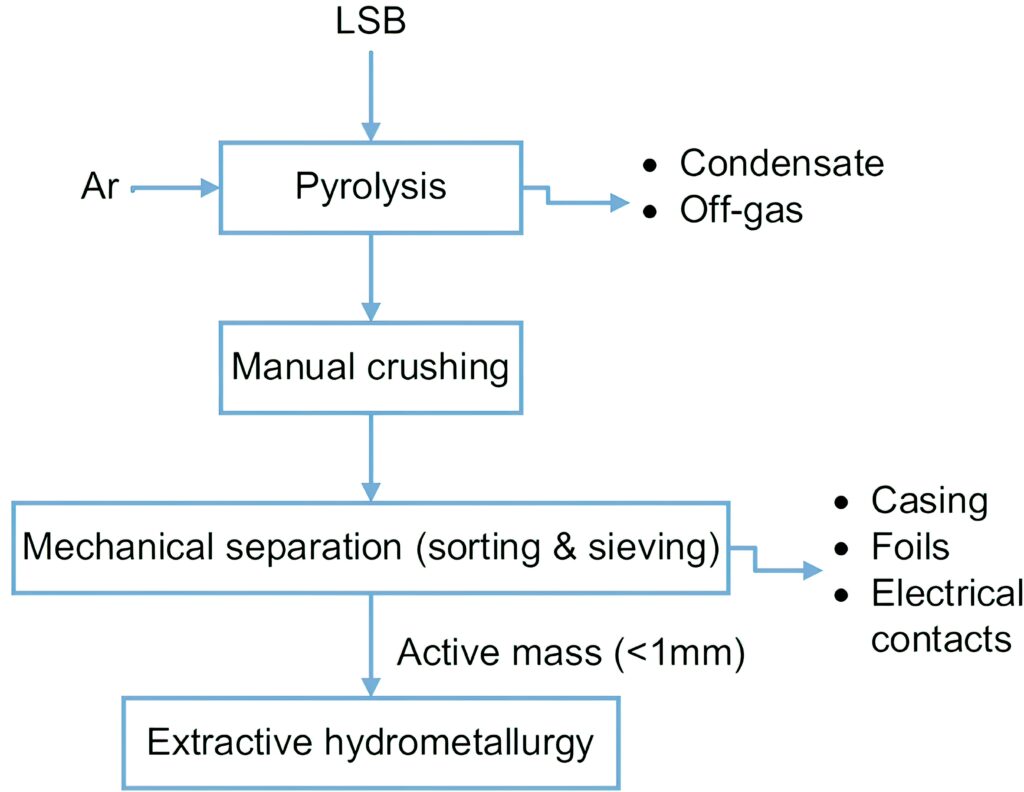
(Courtesy of University of Aachen)
The challenges of recycling lithium-ion batteries is at the forefront of the industry as a result of the millions of cells that will be produced every year for EVs. But there are other battery chemistries used for e-mobility platforms with a lot fewer recycling issues.
Sodium batteries do not use lithium or cobalt, and so are free from the cost and recycling imperative, The sodium and the graphite used in the electrodes are some of the most common elements on Earth, so there is no need to recover them. The value for recycling is in the plastics and metals in the cells and packs, and there is no risk with dismantling these. That is why this technology has been increasingly popular in areas such as India for three-wheeler and electric trucks.
Lithium sulphur is an increasingly popular battery technology for electric aircraft, as it has a higher energy density than lithium-ion and without many of the safety issues. Recycling the lithium, sulphur, carbon and aluminium from these cells uses both thermal and hydrometallurgical steps.
A thermal treatment at 500 C with a holding time of 1 hour reduces the mass by 27%, which is then shredded to a ‘black mass’ powder containing all the recoverable resources from the metal casing. The black mass is then further treated in an aqueous solution, followed by an acid process. Nitric acid and sodium hydroxide provide the highest lithium yields – much better than with sulphuric and hydrochloric acids.
Using this process, up to 93% of lithium could be transferred to a solid lithium carbonate product.
With thanks to Lilian Schwich at IME Aachen.
Flow batteries
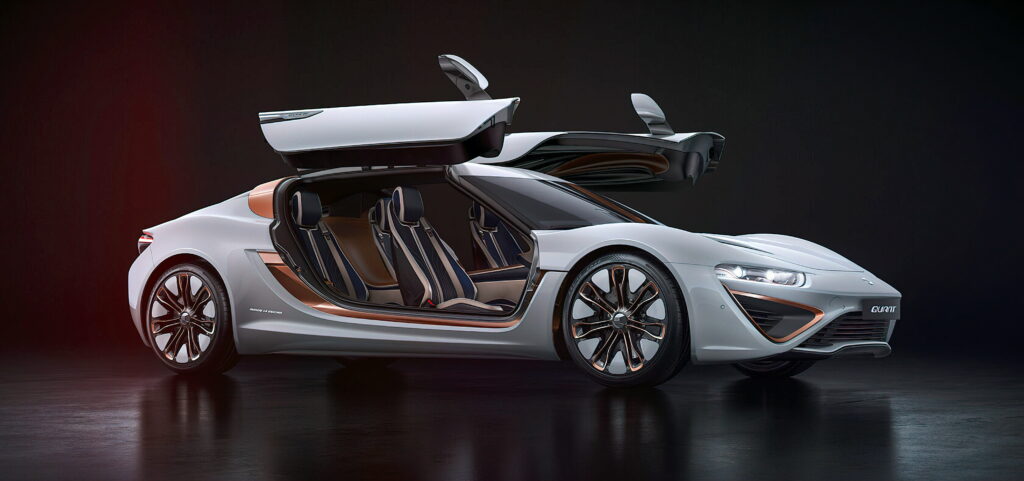
(Courtesy of Nanoflowcell)
Flow batteries have a very different structure for e-mobility platforms, with more focus on avoiding the problems of lithium batteries.
Flow batteries use two liquid electrolytes, an anolyte and a catholyte, which often contain the highly toxic element vanadium, and a membrane. The electrolytes are stored as a liquid in a tank and flow through the membrane to another tank to generate the electricity.
The tank of fresh electrolyte can be topped up in the same way as gasoline or diesel, and the tank of used electrolyte easily drained at the same time. This dramatically simplifies the structure of an electric powertrain, and has been used for powering electric cars and providing power through a charging point as well as for shipping.
This used electrolyte can then be recycled, often by the vanadium producer, with 97% purity.
One of the issues with reprocessing the electrolyte are the shipping costs. If the electrolyte can be treated on-site to produce a vanadium precipitate, it would cut the cost of shipping the material to a vanadium producer for recovering the precipitate.
Alternatively, the electrolyte can be shipped to a vanadium producer to be recovered as a commercial product. This can be achieved by oxidation in a sodium hypochlorite (bleach) or sodium chlorate solution at temperatures of around 65 C.
The electrolyte can also be added to the furnace that generates the vanadium from ore feedstock. However, this approach has challenges owing to the corrosive nature of the electrolyte.
One advantage of recycling spent electrolyte is that the vanadium is already in solution, as the largest losses for any vanadium producer come from dissolving the element.
Another approach, which is being used in the Quant 48 V prototype electric car developed by Nanoflowcell, uses positively and negatively charged electrolyte liquids that are stored separately in two tanks and then, as with a traditional flow cell or fuel cell, pumped through a cell in separate circuits.
Here, the two electrolyte circuits are separated only by a permeable membrane. An exchange of ions takes place as soon as the positive and negative electrolyte solutions pass one another on either side of the converter membrane.
Both electrolytes are non-toxic and sourced sustainably, with the resulting exhausted fluid being pH-neutral and easy to dispose of.
A different flow battery approach, developed by IFbattery in the US, removes the membrane and instead uses a single fluid that oxidises an anode to produce electrons, and through a reduction at the cathode, generates current. The oxidant is a macro-molecule that lives in the electrolyte, but it is reduced only at the cathode. The spent battery fluids or electrolytes can be collected and taken to a solar farm, wind turbine installation or hydroelectric plant for recharging electrically.
With thanks to Prof John Cushman at Purdue University, and Mike Woolery at Rensselaer Polytechnic Institute.
ONLINE PARTNERS
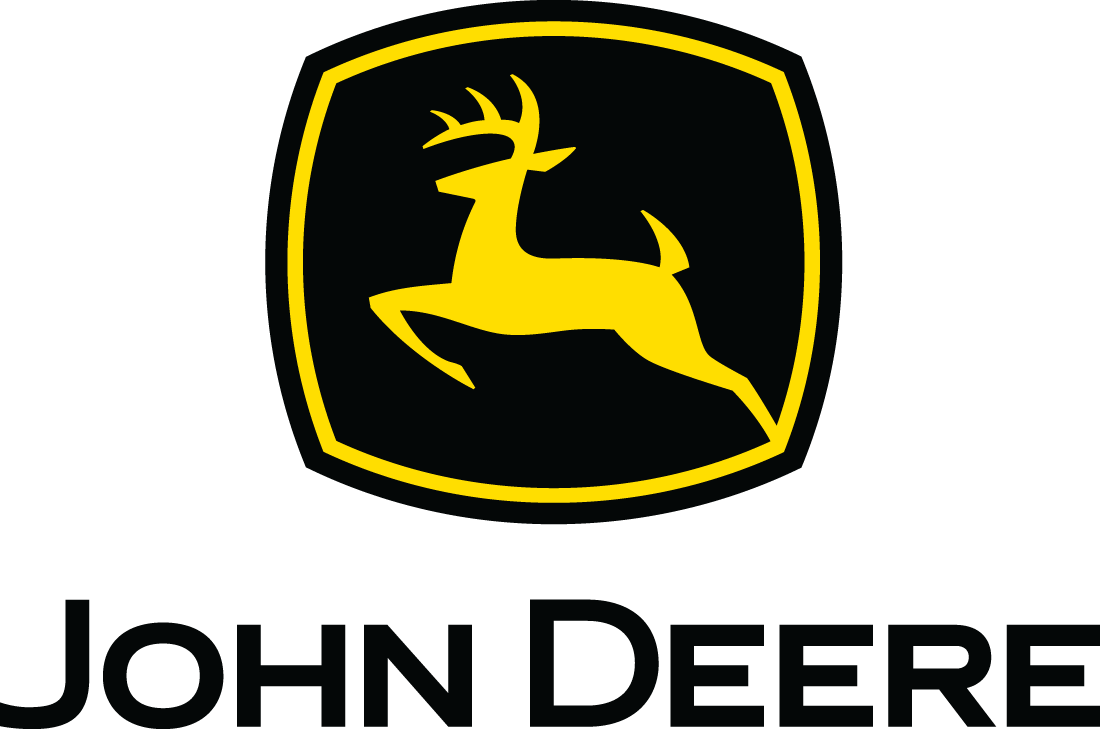
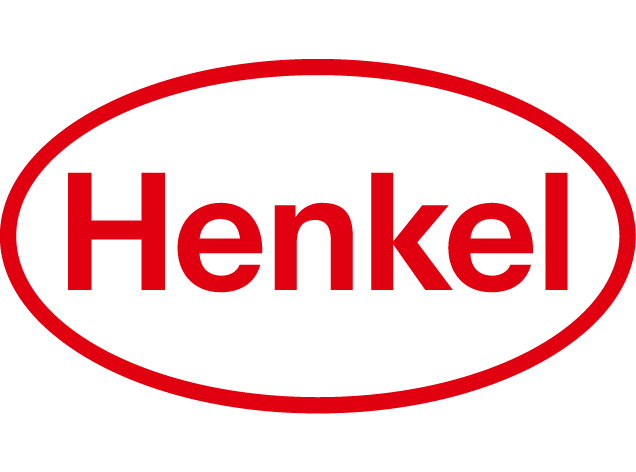
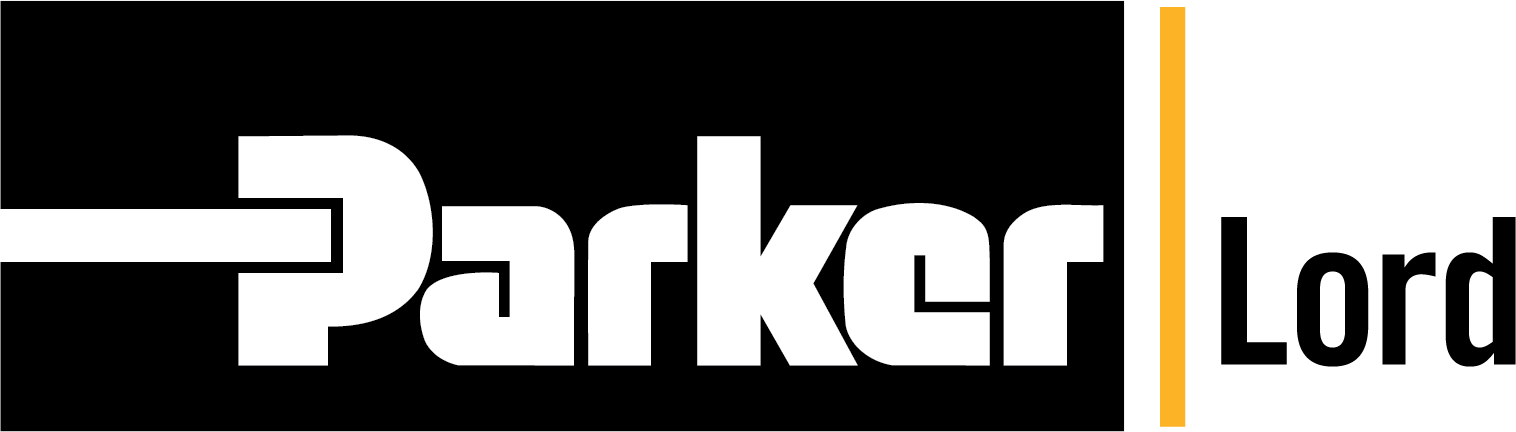
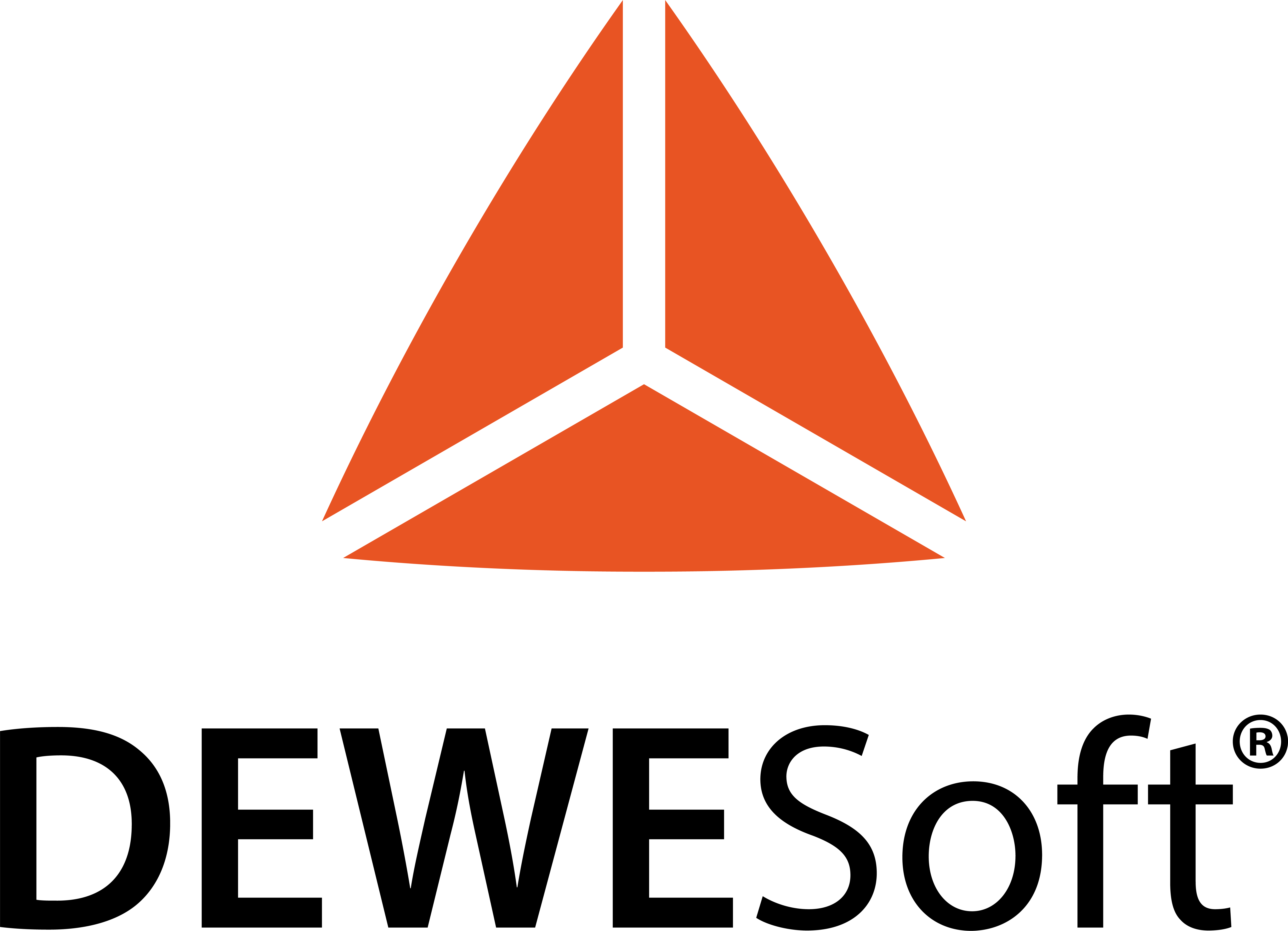
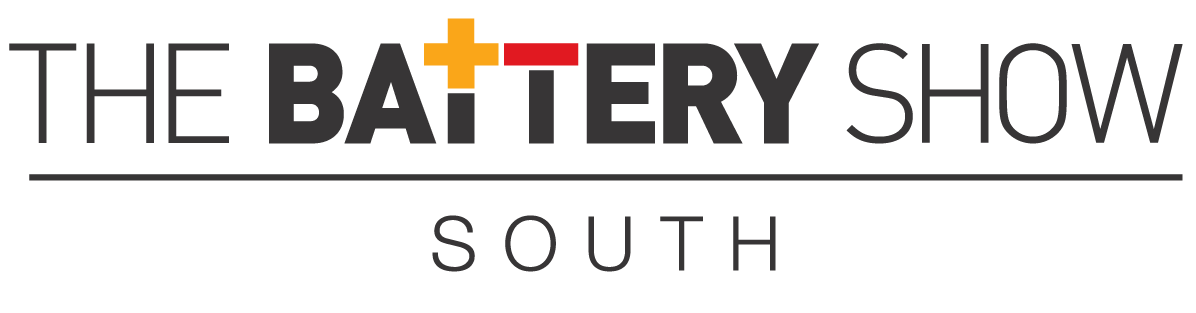
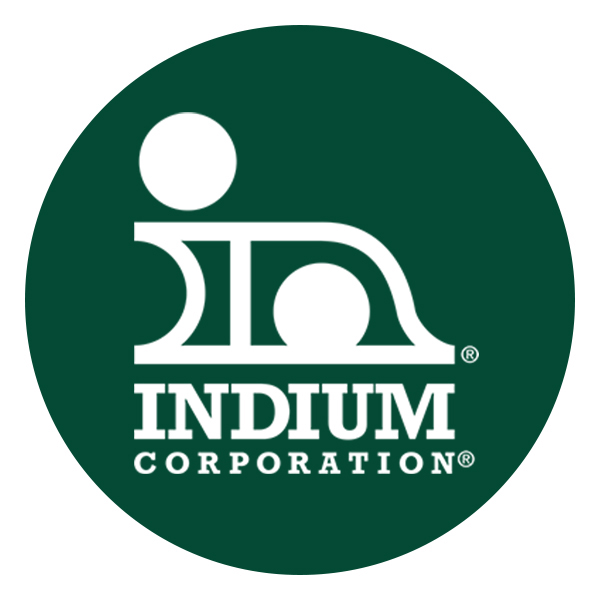
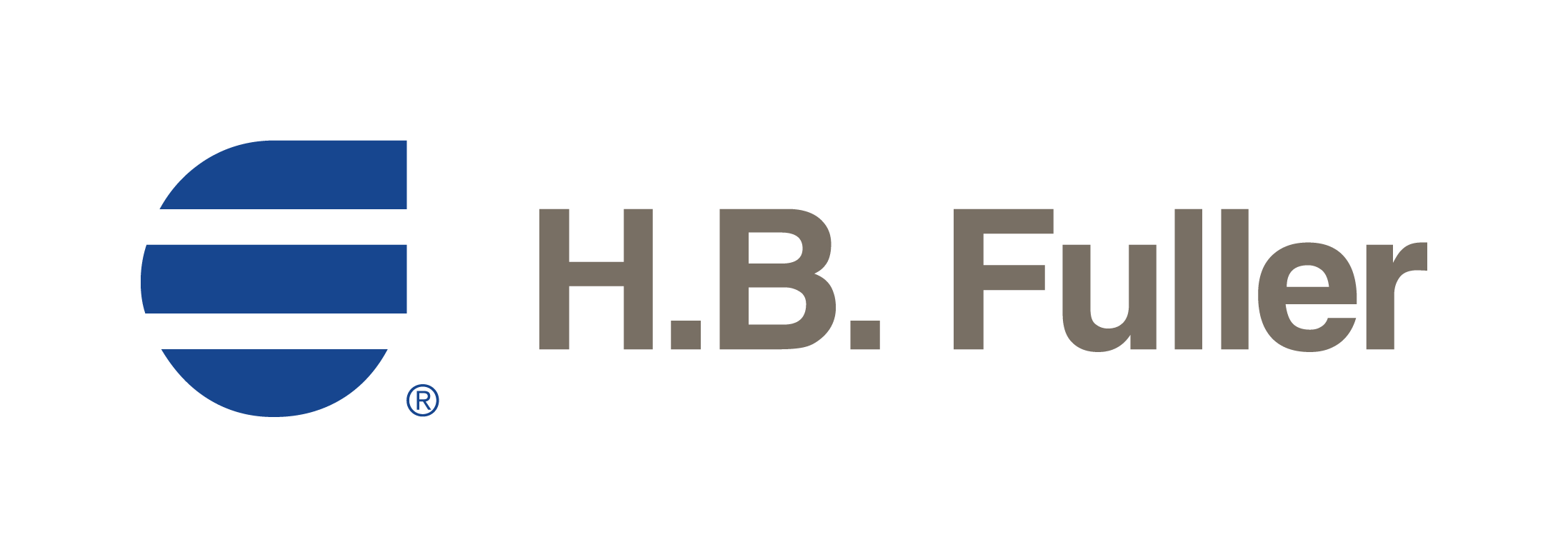