Better eVTOL landings
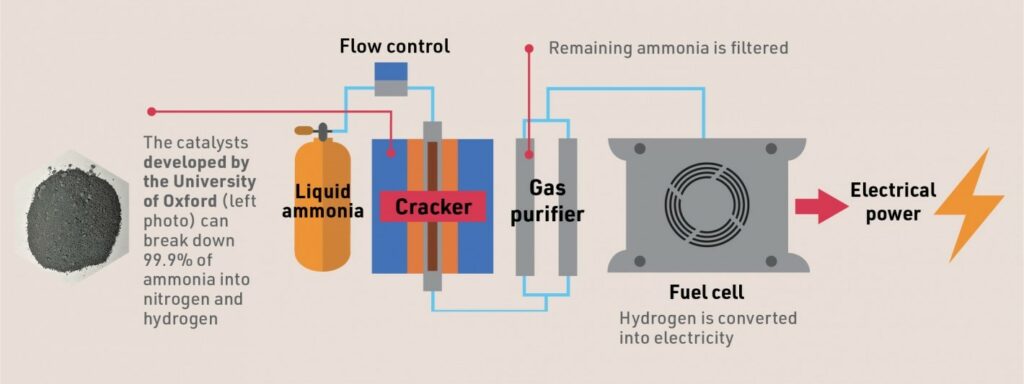
Battery-powered manned eVTOL aircraft intended to operate to and from urban vertiports have a sharply limited energy budget, so designing energy-efficient flight profiles for them is obviously important – and if those profiles can also improve passenger comfort and safety at the same time, so much the better (writes Peter Donaldson).
That is what a team of Chinese engineers set out to do for the Commercial Aircraft Corporation of China (COMAC) ET120, a half-scale demonstrator for a lift/cruise eVTOL machine intended to carry four people or so, focusing on a new energy-efficient landing profile.
The ET120 has eight lift rotors in four pairs on two longitudinal booms above the high aspect-ratio wing, and a pusher propeller mounted behind the cabin and above the low set tail boom, which ends in a T-tail.
The team, from the School of Aerospace Engineering at the Nanjing University of Aeronautics & Astronautics, the COMAC Beijing Aircraft Technology Research Institute and the School of Aerospace Engineering in Shenyang Aerospace University, came up with an alternative to the climb-to-decelerate and stall-to-decelerate manoeuvres that immediately precede the vertical approach to touchdown in many eVTOL landing profiles.
The profiles were originally developed for use in small uncrewed aircraft, to which they are well-suited. For manned eVTOL machines however, they are too energy-hungry, uncomfortable for passengers and potentially dangerous. The new profile the team developed replaces the climb-to-decelerate manoeuvre used by the ET120 with a rolling manoeuvre in the horizontal plane.
In the original profile, the landing process starts from the cruise in level flight. When the auto-land function is engaged, the system switches off the propulsion motor and pitches up to convert speed into altitude, then switches on the lift motors before entering a hover above the touchdown point and making a vertical descent.
That however occupies a lot of airspace in high-traffic areas, while gaining altitude before landing goes against common sense, and the climb consumes energy unnecessarily and gives the rotors more work to do in the descent. It is also uncomfortable for passengers.
Instead, the new profile uses a five-stage spiral approach, with banked turns to bleed off the speed while suppressing the tendency to climb.
Stage 1 brings the aircraft close to the pad and turns it into a loiter circle at constant airspeed and altitude.
In stage 2 it starts to decelerate, switching off the thrust motor and briefly entering a wing-borne glide while maintaining altitude. It uses drag to reduce airspeed and a fixed bank angle to spiral in towards the landing pad.
At the start of stage 3 the craft is still at medium airspeed, and wing efficiency is much greater than rotor efficiency when the rotors are switched on and brought up to 30% of maximum rpm. It continues to maintain altitude while losing airspeed in its banked turn, ending the stage when the pitch angle reaches a predetermined value.
At stage 4 the aircraft is in the mid-to-low-airspeed regime, and wing and rotor efficiency are equal. The lift rotors are brought up to 60%, giving them control of the altitude, and the stage ends when airspeed drops below 5 m/s.
In stage 5 the vehicle is in the hover to prepare for a vertical descent to touchdown.
To ensure stability through the manoeuvre, the autopilot logic uses L1 adaptive control to cope with the uncertainties occasioned by the aircraft’s complex transitional aerodynamics.
As well as a smooth, comfortable flight that avoids potentially dangerous attitudes, the team says this landing profile also reduces the rotors’ workload in the hover by 64% – a worthwhile energy saving in an electric aircraft.
ONLINE PARTNERS
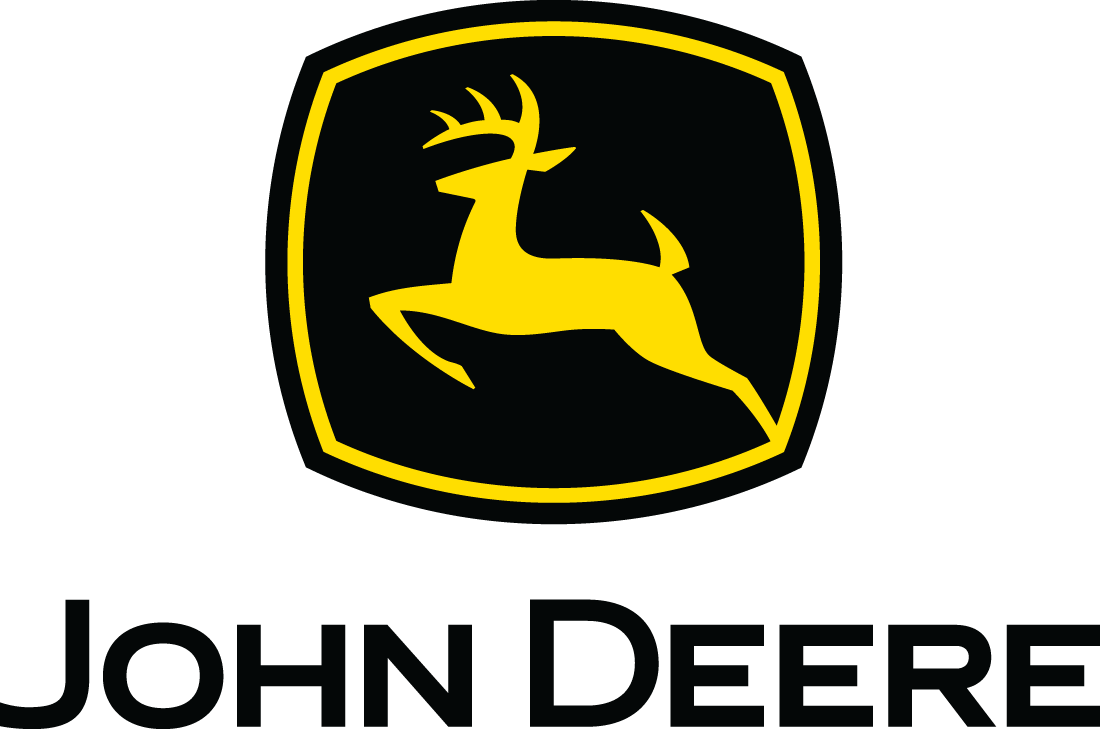
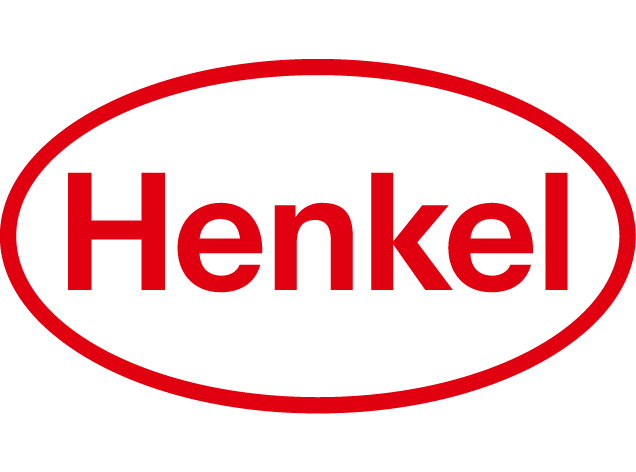
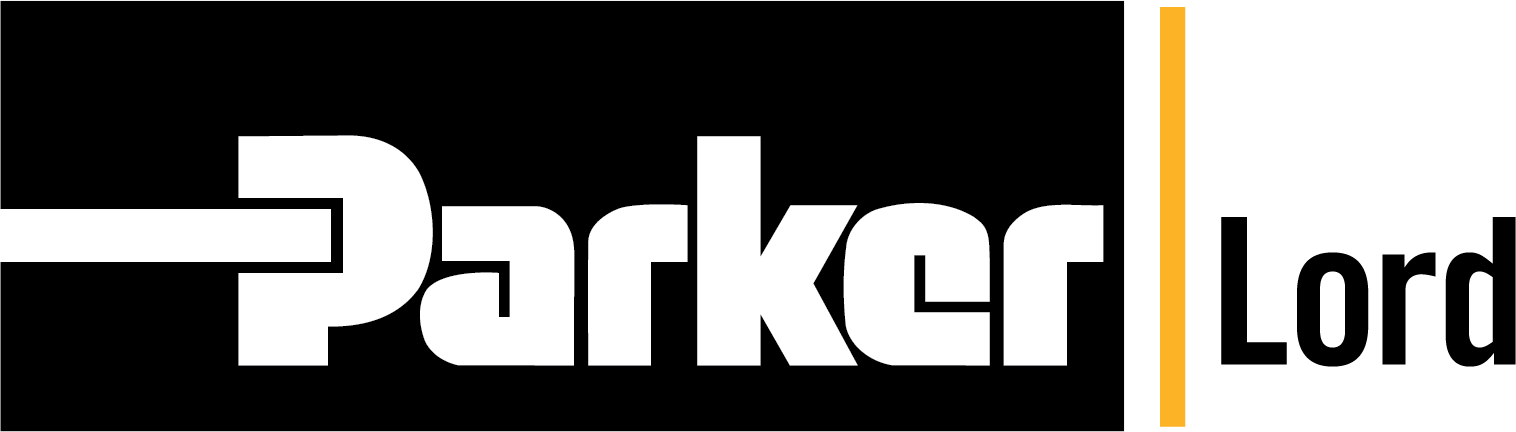
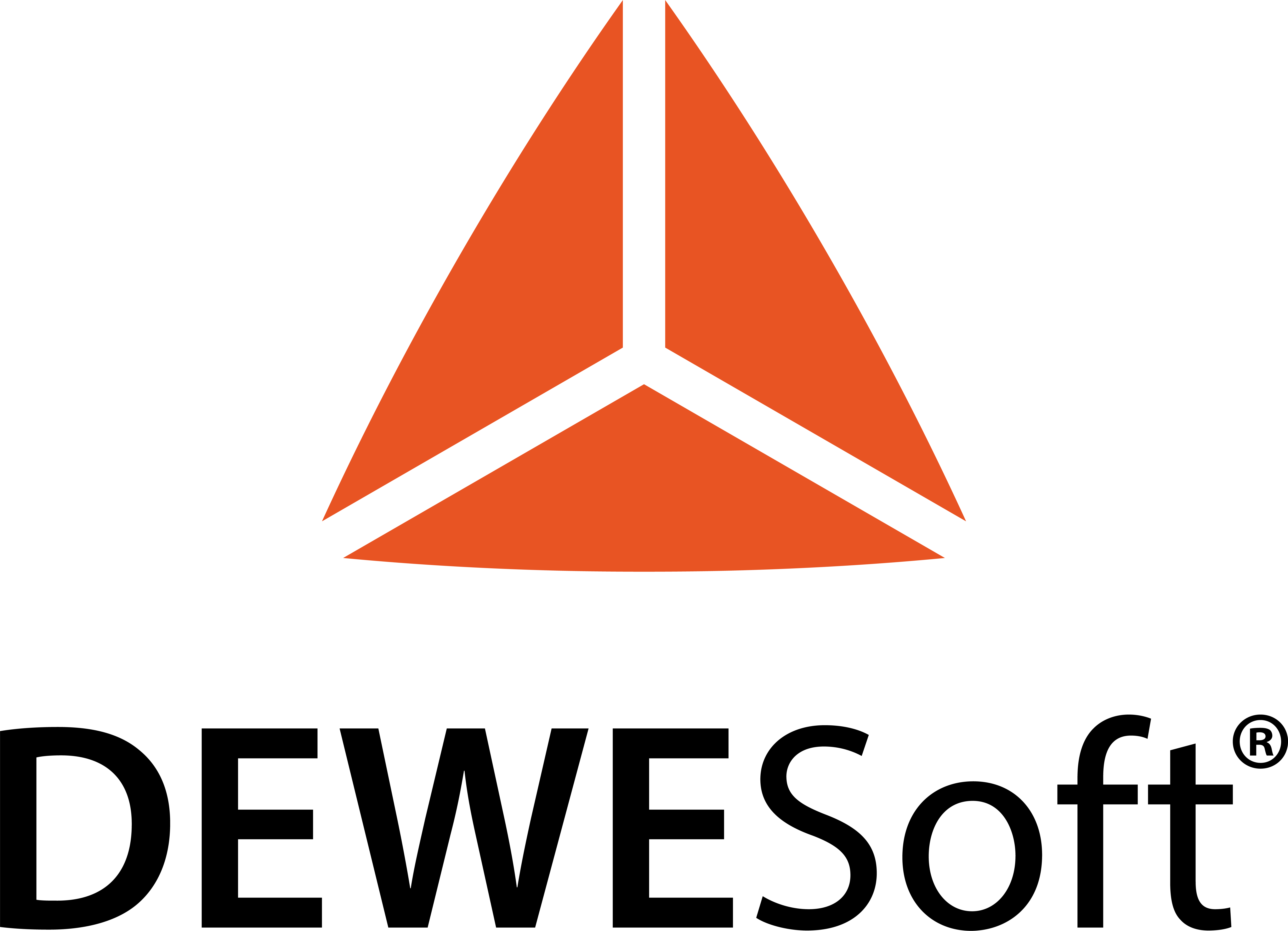
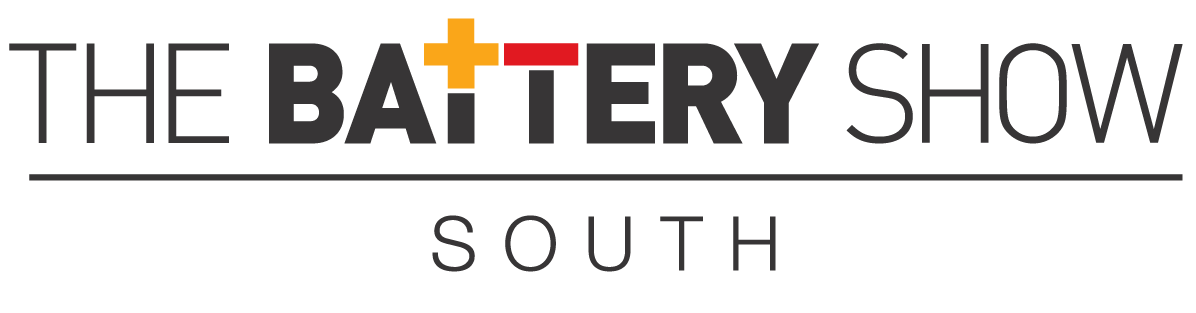
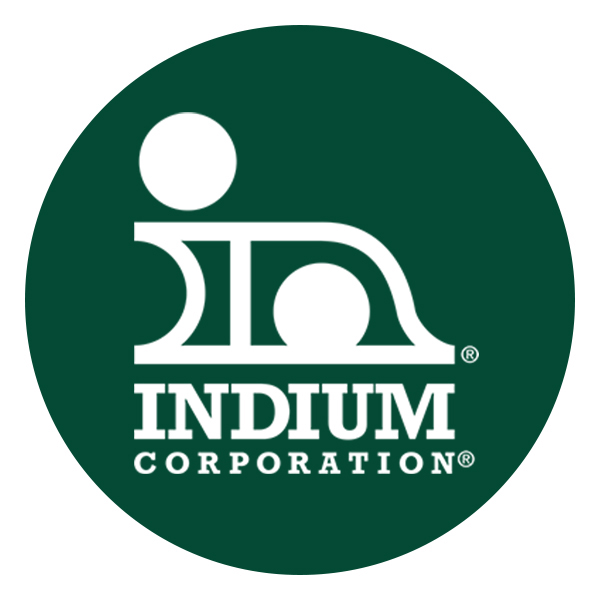
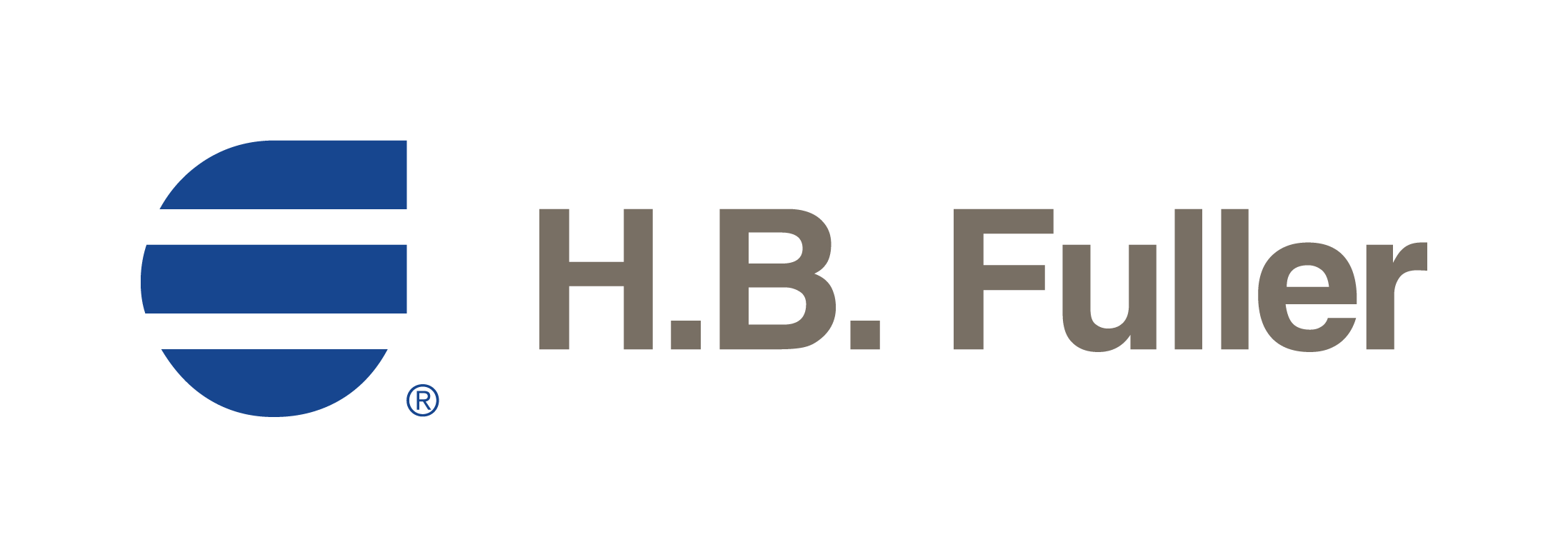