Battery inspection for EV manufacturing
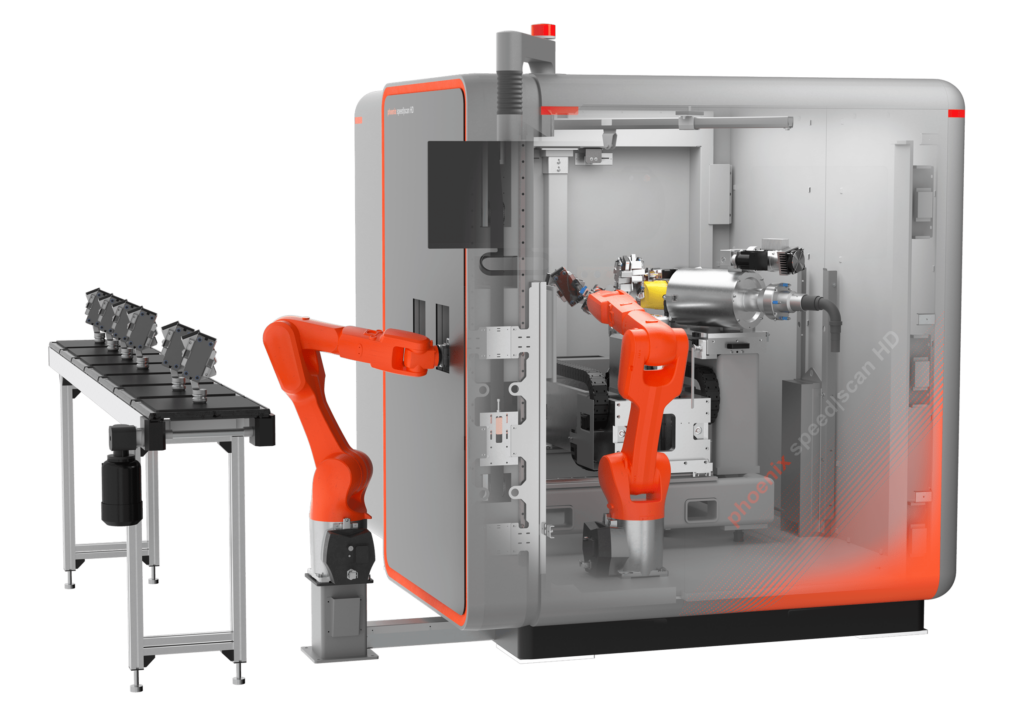
(Image courtesy of Baker Hughes Waygate Technologies)
Battery sleuthing
Getting inside a battery to check its integrity or to trace a fault in a non-destructive manner is technologically challenging, as Peter Donaldson explains
Mass producing large capacity lithium-ion batteries to meet the anticipated demand for EVs while ensuring that they are as safe, dependable and long-lived as possible is driving the need for faster, more thorough and more reliable inspection systems. Such inspection technologies must keep pace with volume manufacturing processes without missing any defects that could cause embarrassing, expensive or even life-threatening problems during a service life that could extend over decades.
Some idea of the scale of the developing challenge can be gleaned from market forecasts that predict that the global EV fleet will grow to between 240 million and 380 million by 2030, roughly an order of magnitude more than the 26 million reported to exist in 2022, notes an expert from a global supplier of X-ray, computed tomography (CT) and ultrasonic industrial inspection systems.
“Ensuring a high-speed yet meticulous industrial inspection is crucial not only for meeting demand but also for minimising the risk of quality escapes,” this expert adds. “Given the potential catastrophic consequences on both health and finances, there is an imperative to enhance inspection processes to detect and rectify any deviations promptly.”
Inspection from inception
Right at the beginning, raw materials are inspected to ensure the quality and integrity of components before they are integrated into the manufacturing process. During cell manufacture, inspection technologies are used to assess the quality of individual cells, identify defects, and ensure uniformity in production.
At the module assembly stage, inspection systems are used to check that components are properly connected and aligned for optimal performance. And in pack assembly, inspection technologies are crucial in ensuring the integrity of the overall structure, the proper arrangement of cells, and the overall safety and quality of the complete pack.
The manufacturing process finishes with end-of-line testing, which encompasses both functional checks and a final comprehensive inspection aimed at guaranteeing that each battery meets the required quality standards before reaching the customer.
The most common manufacturing defects are electrode overhang, metal contaminants, delamination, deflected anodes, voids/porosity, bad welds, critical structural changes, cycling induced particle cracking or ageing mechanisms such as electrode particle composition degradation, mechanical deformation and assembly glue issues.
A broad and expanding range of technologies is applied at all stages of the manufacturing process, with an emphasis on non-destructive methods followed by destructive ones if it is necessary to investigate a detected defect in more depth in a lab environment rather than on the production line.
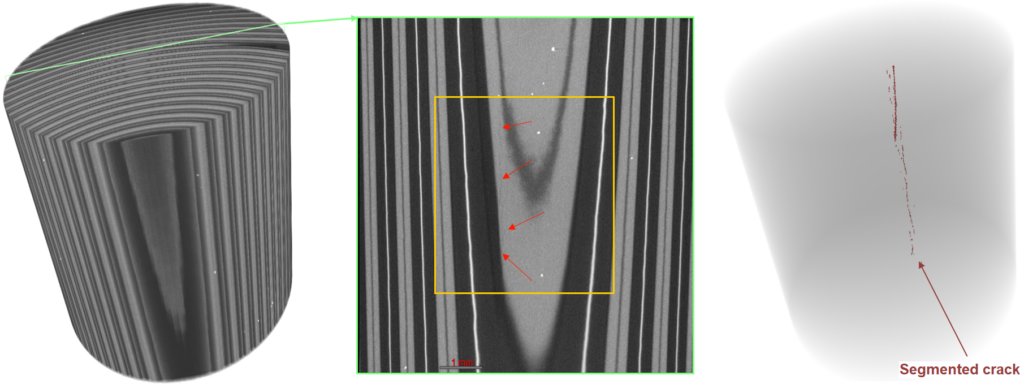
(Image courtesy of Zeiss)
Key inspection technologies
Cameras feeding imagery to computer vision systems are employed for visual inspections of surfaces of electrodes and assemblies to look for defects ranging from anomalies in active material to misalignment of components, leakage, and external defects.
Techniques such as ultrasound and X-ray technologies including CT scanners are used to examine the internal structure of cells, modules and packs, identifying defects and anomalies without causing damage.
Typical, CT scanners consist of an X-ray source and a detector that are positioned on opposite sides of the part being scanned. The source emits a narrow beam of X-rays that passes through the part. Both source and detector are mounted on a circular rotating gantry that surrounds the part and completes a rotation in a matter of seconds.
X-rays are partially absorbed by the different materials they encounter as they pass through the part, with dense materials absorbing more X-ray energy and appearing white on a monochrome image, with less dense materials showing up as shades of grey, while air and the least dense materials appear black as most X-rays pass right through.
However, ‘false’ colours can be applied to highlight materials of interest with different densities. Because the part is scanned from all around, algorithms can process the recorded data to produce highly detailed 3D slices through the part. To create these images quickly enough for production line use requires powerful computers, while AI helps rapid interpretation.
Thermal imaging uses cameras sensitive to infrared wavelengths to identify temperature variations and potential hotspots within battery modules and packs. Ultrasonic inspection systems use high-frequency sound waves to find defects such as voids in battery components by analysing the echoes returned from interfaces between materials.
These are complemented by other techniques such as Electrochemical impedance spectroscopy (EIS), which analyses the electrical behaviour of cells and batteries to assess performance and detect anomalies, while pressure decay and helium leak testing, for example, check for gas leaks at cell, module and pack level.
The performance of both established and emerging inspection technologies is benefiting from the application of artificial intelligence (AI) techniques such as machine learning to improve speed and accuracy in processing and interpreting sensor data.
Principal challenges
Inspecting EV battery systems throughout their manufacture speedily and reliably is particularly challenging, because cycle time is crucial and manufacturers demand quick turnarounds for efficient production.
“The need to test 100% of batteries in line adds complexity to the task of maintaining a swift manufacturing pace while maintaining quality control,” stresses an expert from a non-destructive testing (NDT) company employing X-ray and CT technologies including 3D-Inline CT systems.
Reliability of inspection and measurement is governed by standards such as the German VDA5, and meeting them adds an additional layer of complexity, the expert adds. “Striking a balance between meeting these standards and maintaining an efficient manufacturing process is a challenge, as rigorous testing may increase cycle times.”
Catching defects as early as possible in the manufacturing process is crucial to improving the yield achieved by a facility such as a megafactory. This is because bringing the reject and rework rates to a minimum will bring down battery costs, emphasises an expert from a camera-based inspection system provider.
Large facilities also present the problem of round-the-clock monitoring of newly manufactured batteries in storage and the recognition of defects that are not yet visible, a specialist from a developer of infrared cameras and thermographic solutions notes.
More broadly, the main challenge with inspection of batteries through the manufacturing process stems from the industry’s relative youth, comments an expert from a provider of inspection systems that use a variety of technologies.
“In more mature manufacturing processes, there is greater understanding of failure modes and more consensus on tolerances and inspection approaches. With EV battery inspection, many manufacturers are still learning about what constitutes a relevant defect,” he says. “The exciting thing is that we get to help the battery industry develop that understanding to push the limits as the technology expands and grows.”
This company’s inspection technologies include optical microscopy, X-ray microscopy, digital radiography, CF, traditional coordinate measuring machines (CMM), optical scanning, and structured light measurement.
Staged inspections
Different stages of battery manufacture require different inspection technologies. One of the earliest stages is electrode production, which involves the application of active anode and cathode compounds and binding agents in slurry form to sheets of substrates fed from a roll. These are then dried, compressed (“calendared”) and cut to size ready for assembly into cells, and this stage is well suited to inspection with specialised camera systems.
While this can be done with area scanning cameras that capture discrete frames, these frames then have to be electronically stitched together before processing, which is not a natural fit for a continuous roll-to-roll process such as electrode production, notes our camera-based inspection expert. Wide, high-speed linescan cameras provide a better solution, he says, running at rates of around 100 kHz to expose 100,000 lines per second.
This company uses time delay integration (TDI) technology in its linescan cameras that feature multiple rows of sensors covering every part of the surface being inspected. The TDI technology then combines all the exposures for each line – there can be 100 of them – to maximise the signal-to-noise ratio in the final image, he explains.
TDI is particularly helpful in what he terms “light-starved” situations often encountered when inspecting dark materials or those that should not be exposed to high intensity lights for various reasons. “Using TDI means you can collect more photons but you don’t need to shine a bright light,” he adds. The TDI camera is an enabler for high speed imaging to meet the demanding requirement of high throughput production lines, he emphasises.
Later in the manufacturing process, X-ray and CT allow thorough examination without compromising the integrity of the components being inspected, which is crucial to quality control. The latest systems also provide very high-resolution images, ensuring precise and detailed visualisation of internal structures. This contributes to accurate defect identification and analysis. The latest systems also feature increasingly accurate AI-based automatic defect recognition capabilities.
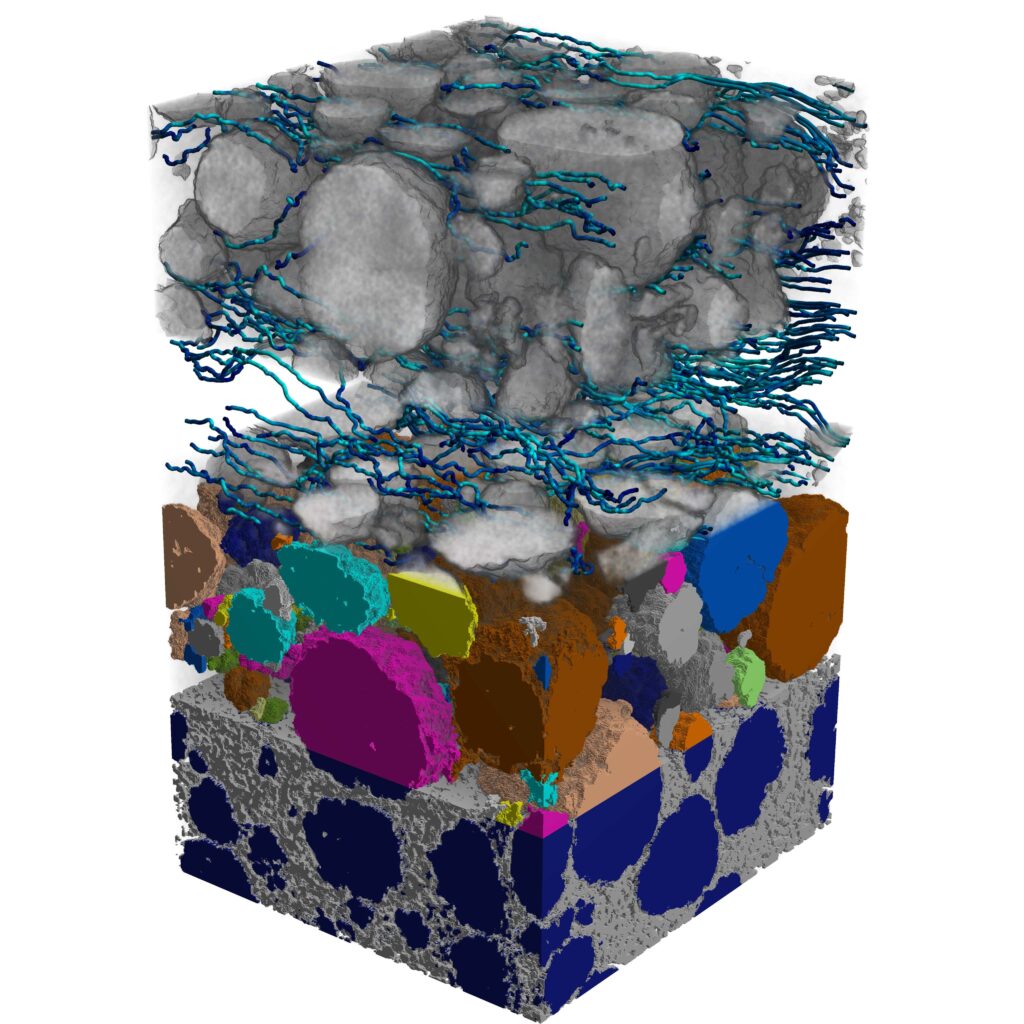
(Image courtesy of ZEISS)
Combining processes
Combining different inspection technologies can be particularly useful. “Each inspection technology has inherent benefits and limitations. Batteries are notoriously difficult to tear down, and the process of doing so can destroy much of the pertinent information,” our multi-technology inspection system expert says. He emphasises that X-rays can inspect internal features of complex parts across multiple scale lengths from centimetres to sub-millimetre volumes and capture relevant structural details with spatial resolutions ranging from microns to nanometres. This range of scales encompasses battery packs and cell-level analysis and material microstructure-level analysis.
For example, it is possible to identify regions of interest using X-ray or optical microscopy scanning and then relocate that region of interest in a focused ion beam scanning electron microscope (FIB-SEM) for further high-resolution imaging and chemical analysis. The high-resolution imaging capabilities of FIB-SEM allow for an in-depth examination of the microstructure and composition of materials, offering a more granular understanding of the root causes of defects. However, FIB-SEM isn’t a non-destructive process because it requires extraction and preparation of small samples that must then be placed in a vacuum chamber.
Described as a disruptive technology, 3D inline CT is designed to provide a more comprehensive and detailed inspection of batteries during the manufacturing process. This while operating at speeds high enough to keep up with modern battery production lines and minimising the likelihood of faulty batteries passing through the manufacturing process undetected. “By providing detailed insights into the internal structure and components of batteries, we enhance the overall safety standards, identifying potential issues before they can compromise the integrity of the product,” the X-ray and CT company’s expert says.
The company’s new 3D inline CT technology, the expert says, can replace conventional techniques that require extraction of samples and embedding them in resin or grinding them. “This substitution not only preserves the integrity of the batteries but also streamlines the inspection process by eliminating the need for time-consuming and potentially damaging procedures.”
The technology provides improved accuracy in both quantifying and qualifying defects, he adds. This enables more detailed analysis of internal structure and capturing measurements of hidden features that conventional methods may struggle to evaluate.
“In certain applications, CT technology can serve as a holistic testing method, consolidating multiple inspection steps into one comprehensive scan” he notes. “This integration not only enhances the thoroughness of the inspection but also reduces the overall effort and tooling required.”
Electrode overhangs
Technologies such as X-ray, CT and ultrasonics are effective at detecting electrode overhang errors, which is crucial to ensuring precise electrode positioning within the cell, and at identifying broken tab welds. They are also good for electrode bend-angle verification, checking for the proper alignment of electrodes for optimal performance, for locating any inclusions and contaminants within the cell, and for finding damage to electrodes. Beyond cell-level defects, they can also spot problems in electronics within modules, and with module assembly, the X-ray, CT and ultrasonic systems provider points out.
Advanced solutions, including 3D inline CT systems, automate analysis of cathode/anode overhang, bending and exit angles, and the location, identification and assessment of contaminants and delaminations that separate layers of materials that should be in close contact.
“With hundreds of features inside a battery that can be measured, our technologies provide a comprehensive assessment. This includes dimensional measurements, structural evaluations, and other critical parameters,” according to an expert from a 3D inline CT systems provider.
Thermal imaging also helps to detect faults in production at an early stage in order to avoid rejects and minimise rework, a thermographic specialist notes. The company’s infrared cameras can be flexibly adapted to a wide variety of inspection and measurement tasks. They can also be individually integrated into existing quality assurance and surveillance systems, enabling the merging of live visual and thermographic video imagery.
For monitoring stored batteries, thermographic cameras that provide detailed and colour-coded images based on temperature are integrated into customised systems that operate continuously without supervision, automatically triggering an alarm when temperature values exceed critical thresholds. These cameras enable the early detection of increasing temperatures and the localisation of heat sources that are not detectable by visual sensors. Supporting computer systems process the data to display temperature-time profiles in all areas of battery storage facilities.
Companies with large portfolios of inspection products are in a good position to provide tools for correlative workflows that integrate inspections across different technologies. With batteries this makes it possible, for example, to inspect the chemical compositions of raw materials with high-resolution microscopy. Once these are converted into active materials, optical imaging can be used to inspect for tears or foreign material in the electrodes.
After cell assembly, CT can be employed to check for alignment and overhang defects. With the digitisation of all this data, if a failure occurs in the field, engineers can look back at all levels in the manufacturing process to determine the root cause.
Technological limitations

(Image courtesy of Teledyne DALSA)
All these technologies have their limitations, which tend to be highly dependent on specific use cases. The efficiency of the inspection process can be influenced by the characteristics of the defects being targeted and the intricacies of the production workflow, another expert notes.
“Certain defects or manufacturing steps may require more time for a thorough and accurate scan, impacting the overall speed of the inspection process,” this expert says. “Balancing the need for precision with the demand for a timely assessment is a challenge that may be encountered in CT industrial inspection of batteries.”
The limitations of CT technology are imposed by the laws of physics, and are principally associated with the penetration of samples based on their density; high density samples that hinder penetration can compromise the inspection process.
Further, high spatial resolution requirements tend to limit the size of the sample that can be scanned given that X-rays strongly attenuate as the thickness increases, a factor that also strongly depends on material composition.
“There is always a trade-off between data quality and time investment, says an expert from our multi-technology inspection provider. “To achieve high resolution CT images, cycle time can be a barrier for some inline inspection requirements. X-ray based imaging also can struggle with inspections of samples with multiple materials of different density. Batteries are sometimes difficult to image due to the mixed materials inherent in their design.”
Radiation safety is always a concern, she adds, so X-ray inspections are conducted within an enclosed cabinet. This provides safe working conditions but also can limit the size of samples that can be imaged. For example, cells are easily imaged, but large modules can be problematic, and while complete EV packs can be imaged, they require the extremely expensive solutions based on linear accelerators.
Cameras, including infrared thermographic sensors, always need a line of sight to the item being inspected, and all optical systems depend on lighting. Most optical systems today use visible light sensors, including red-green-blue (RGB) cameras, according to the expert from a camera-based inspection system provider, but this is changing.
“We see more applications moving to other sensors such as NIR (near infrared) or ultraviolet (UV) in different wavelengths,” he says. He adds that the company has developed what he terms a multispectral camera/light that provides illumination in and detection of RGB and near infrared (NIR) light at the same time, initially for inspection of printed circuit boards (PCB). “NIR has a longer wavelength and it penetrates into silicon or other materials. Visually, you cannot see the defect because of the paint, but the NIR can penetrate that paint and detect the defect underneath.”
Evolving inspection ecosystem
The integration of these technologies into the processes of battery manufacture varies among manufacturers, and is currently limited. However, another expert reports a discernible uptick in interest and is discussing the implementation of an “ecosystem” for management and archiving of inspection data. This is a software suite designed to facilitate a streamlined and organised integration of inspection technologies into the broader battery manufacturing processes.
They remark: “the evolving interest in integration indicates a growing recognition of the importance of seamless incorporation of inspection technologies into the manufacturing workflow.”
Physical integration of optical inspection systems, for example, involves the installation of cameras and lighting systems on or near the production machinery, so the systems have to be very flexible and customisable, according to our optical inspection systems expert. He says most current systems are general in nature rather than specific to battery inspection.
He adds that a one-size-fits-all inspection system would be ideal, but is very difficult to achieve. “Different applications have different requirements for speeds, resolutions and lighting, based on the material under inspection.”
Many of the 3D inline CT provider’s solutions are used in labs or as close as possible to the production line, and current applications are fully integrated into the line, typically located after hot pressing or canning stages in the manufacturing process. The company is working with customers to integrate CT technology as early as possible into the production line. “This signifies a shift towards more proactive and pre-emptive inspection methodologies,” this expert says.
Essential to this process is the provision of interfaces to different customers’ manufacturing execution systems (MES). “This facilitates the exchange of information and enables fast interactions at scale, allowing for immediate adjustments and responses based on inspection results,” he adds.
With cross-platform software and data storage solutions, the instrument status and resulting data can be shared, processed, traced, and archived.
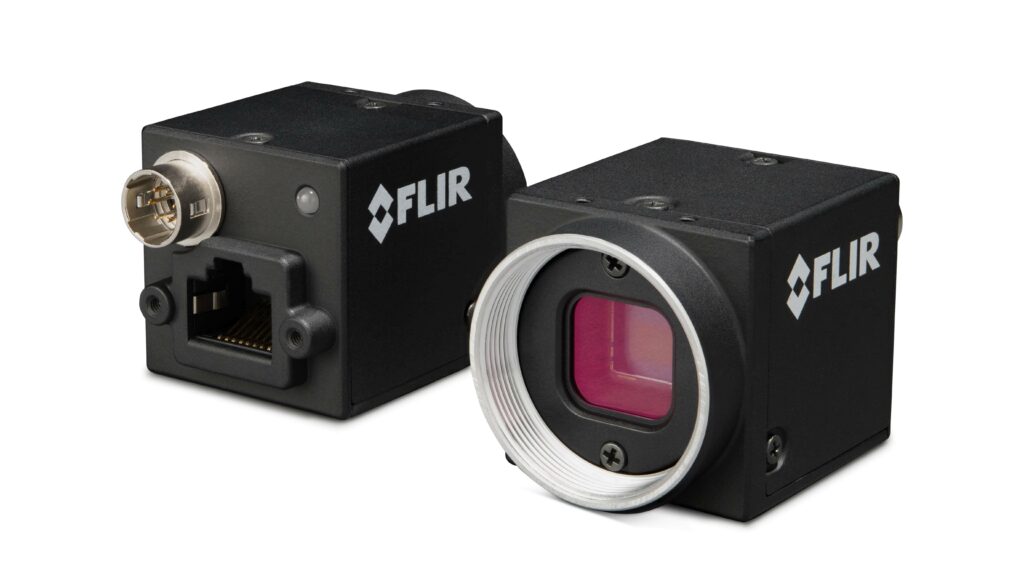
(Image courtesy of Teledyne FLIR)
Finding root causes
Information generated by inspection technologies plays a pivotal role in addressing and rectifying issues within the manufacturing process. “When defects are identified, this information often serves as a key indicator of the root cause, or significantly contributes to the root cause analysis,” says one expert.
“Subsequently, the manufacturing process or materials can be adjusted based on the insights gleaned from the inspection results. This iterative approach to problem-solving ensures that corrective actions are targeted and effective.”
More than just the number of defects, battery manufacturers need to know what kinds of defects they are and their root causes, another expert notes. “This is the key information you are looking for from the vision system, and we categorise them using AI. Once you know the root cause of a defect such as a pinhole or a scratch, engineers can find a solution to fix it. Unfortunately, manufacturers don’t want to disclose the detail because this is their IP.”
Feedback from inspection systems provides insights into manufacturing processes at scale, our visual inspection expert says. Automated scan upload and feature extraction allow for rapid collection and interpretation of data. Automated defect detection ensures that process problems are promptly identified, while automated alerts warn of deviations from quality standards, cueing immediate corrective actions, he explains.
He adds that his company’s systems enable download of cell scans and metrology with a click, so that data is readily available for analysis and decision-making in support of problem-solving. “Information generated during inspection is stored at scale for extended periods, preserving the history of each cell. This allows for post-hoc metrology analysis, enabling detailed examinations of past production cycles and facilitating comparisons between gigafactories, cell designs, production time periods, and shifts,” he says.
“The data supports r&d efforts by providing information for continuous improvement and innovation. It is also instrumental in upholding product safety standards, identifying potential risks, and proactively addressing safety concerns.”
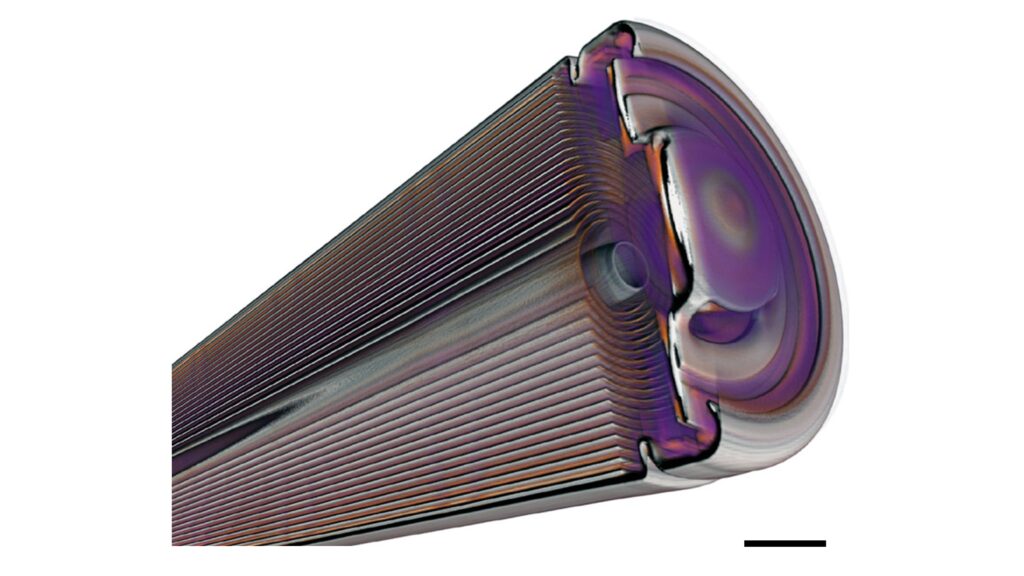
(Image courtesy of ZEISS)
Inspection advances
As a totem of progress in inspection technology, the most important thing for customers is detectability – how to detect a defect, another expert explains. “That is not just the camera, the customer solution also depends on the system design including the light source and the lens.
“Detectability is a big issue in many industries, and in future with cameras and other sensors we want to improve signal-to-noise ratio because that is the most important element of detecting a defect,” he says.”
Another area for improvement is exploiting light beyond the visible, he adds, emphasising the need to move to both UV and IR, including IR wavebands beyond the thermal.
Traditionally, many cell manufacturers relied on 2D X-ray methods for inline inspection, but the shift to 3D inline CT systems provides a more comprehensive view of battery components, enabling more accurate, reliable and repeatable measurements and consequent identification of defects and reducing the likelihood of false positives.
Preloaded and customised job routines, automation, and AI powered data analysis make CT inspection systems easier to use and yield results more quickly, while CT technology itself is continuously advancing. As parts have grown larger and more complex, more powerful systems have become available. Additionally, new and faster techniques for scanning have been developed. Arguably, the largest push in the field has been integrating advanced AI into reconstruction and image analysis.
The principal way in which AI is now making its way into the heart of inspection is through automatic defect recognition (ADR), enabling manufacturers to automate defect analysis workflows. For example, a new system from a leading provider offers AI-based, on-premises ADR software with teachable algorithms that evaluate the quality of a wide range of parts and exploit automated detection of microstructural defects in CT images.
“This software provides specific feature analysis with ADR for pass/fail decisions and fully automated CT workflows. And we are planning to expand the range of this offering,” this company’s expert says.
One important thread of development in processing X-ray images involves dealing with the effects of scatter. X-ray scatter artefacts are unwanted signals or disturbances that can appear in an X-ray image due to the scattering of X-ray photons as they interact with the object being imaged.
Essentially, photons can change direction after interacting with the atoms in the material, deviating from the primary path intended for imaging, degrading the image by creating background noise or reducing contrast. Our multi-technology inspection system provider offers a hardware-and-software-based system to control scatter that dramatically improves image clarity when scanning large, dense objects such as batteries.
This company has also introduced a new 450kV CT system coupled with proprietary X-ray software optimised for non-destructive inspection of cylindrical and pouch cell batteries. The company works to fine tune its systems with as many interconnected technologies, including optical inspection systems, as possible.
In infrared inspection systems, cameras with higher spatial resolution allow for wider monitoring areas to be covered by a single camera without losing the ability to resolve small details. In thermographic cameras, higher thermal resolution means the ability to distinguish smaller differences and changes in temperature, which translates into early detection of developing problems such as thermal runaway.
Contact image sensor (CIS) technology is of increasing importance in visual inspection. Simple, low cost examples of these cameras are widely used in office scanning and copying machines, but our camera-based inspection system provider recently introduced high-speed, high-resolution versions coupled with advanced machine vision software.
CIS cameras also have telecentric lenses, which means that the images they generate contain no distortion. This makes them very good in metrology applications, including margin inspection in which the edges of components are measured to ensure they have the correct dimensions.
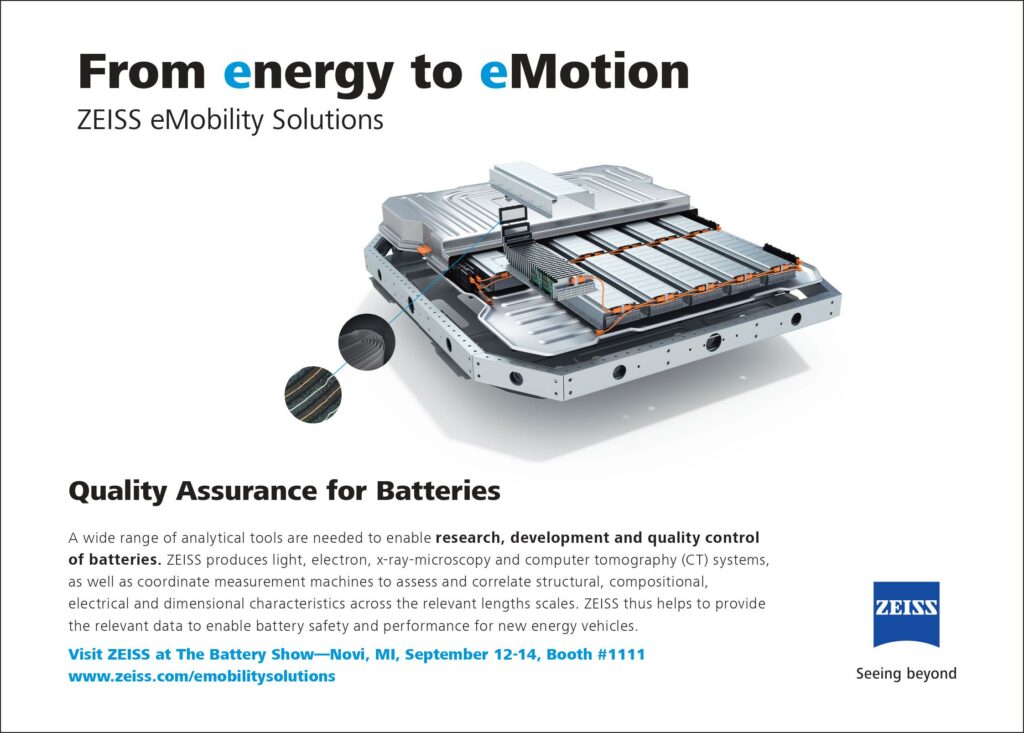
Bigger components, higher resolutions
Near term improvements in these inspection technologies centre on the ability to handle bigger components, higher resolution and through-life condition assessment. The camera-based inspection technology provider plans to develop more advanced linescan and CIS cameras in the next few years.
Anticipating the growing importance of cell- and module-level inspections, our 3D inline CT provider is working to develop more detailed, accurate, and comprehensive evaluations of individual cells and assembled modules during manufacture. Additionally, in response to the need to support sustainability and circular economy goals, the company has committed itself to advancing inspection technologies to assess batteries scheduled for second-use applications and recycling, gauging their condition, quality, and viability at various stages of their lifecycles.
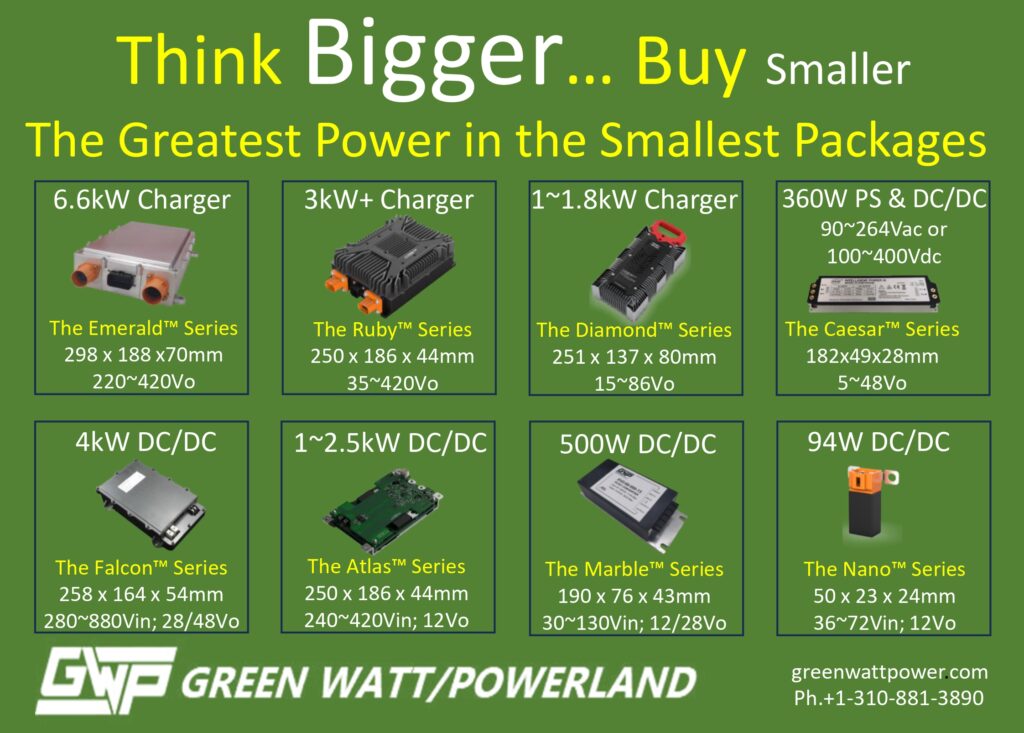
Future directions
Applications of other technologies are emerging. For example optical and Raman spectroscopy provide insights into the chemical composition of battery materials, while nuclear magnetic resonance (NMR) spectroscopy is used to analyse the structure and performance of solid-state electrolytes for a potential new generation of batteries. Also, imaging with electromagnetic wavelengths in the terahertz band is being explored for battery inspection, offering high-resolution imaging and analysis of internal components.
Acknowledgements
The author would like to thank the following for their help with this article: Dipl.-Ing. Steffen Sturm, Project Manager Thermography Solutions, InfraTec GmbH Infrarotsensorik und Messtechnik, Dr Xing-Fei He, Senior Product Manager, Teledyne Imaging Inc, Dana Begun, Shannon Bollin, Herminso Gomez Villarraga, Trevor Campbell, Kyle Crosby, Kevin Legacy, and David Wick from ZEISS Industrial Quality Solutions, and experts from Baker Hughes Waygate Technologies and VCbattery.
Some suppliers of battery inspection services
Canada
Baker Hughes Waygate Technologies
Basler
Hitachi High-Tec
InfraTec
VCbattery
Japan
+49 2233 6010
+49 4102 463 0
+49 2151 643 50
+49 351 828760
+49 451 290 2860
Carl Zeiss Industrial metrology
Cognex
Nikon Industrial Metrology
Nordson Technologies
Thermofisher Scientific
+1 800 327 9735
+1 508 650 3000
+1 810 220 4360
+1 440 892 1580
+1 781 622 1000
Click here to read the latest issue of E-Mobility Engineering.
ONLINE PARTNERS
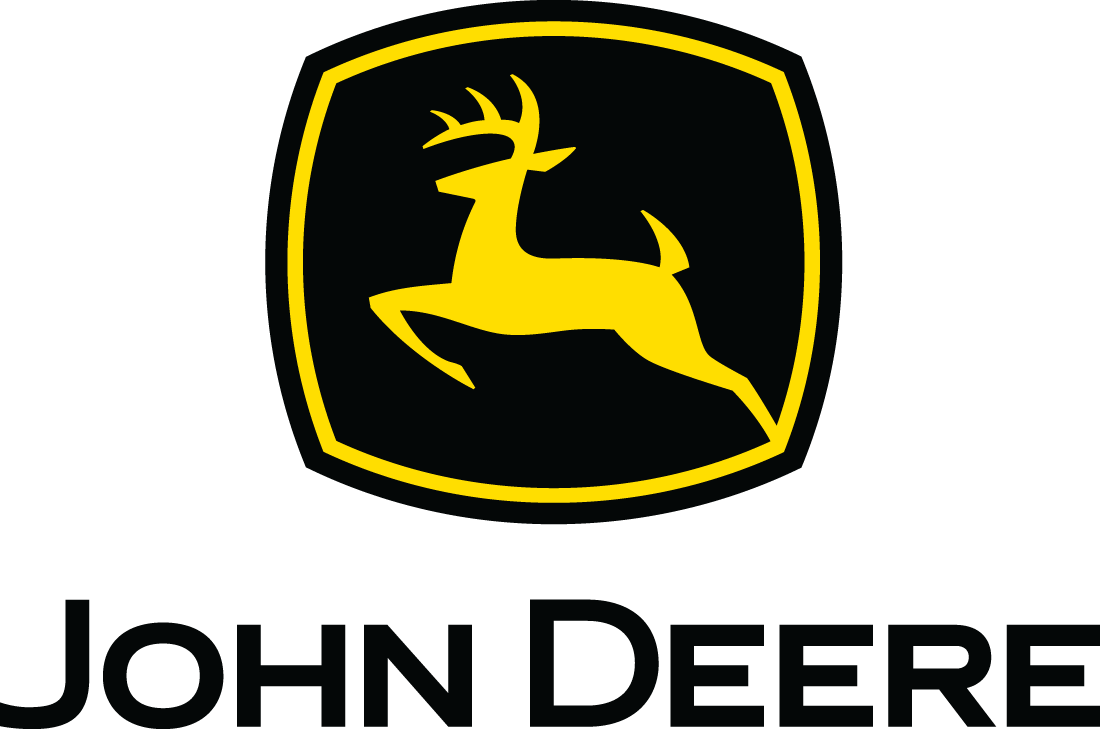
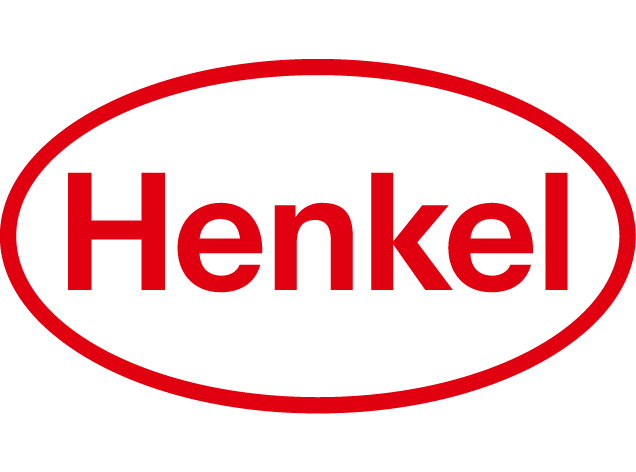
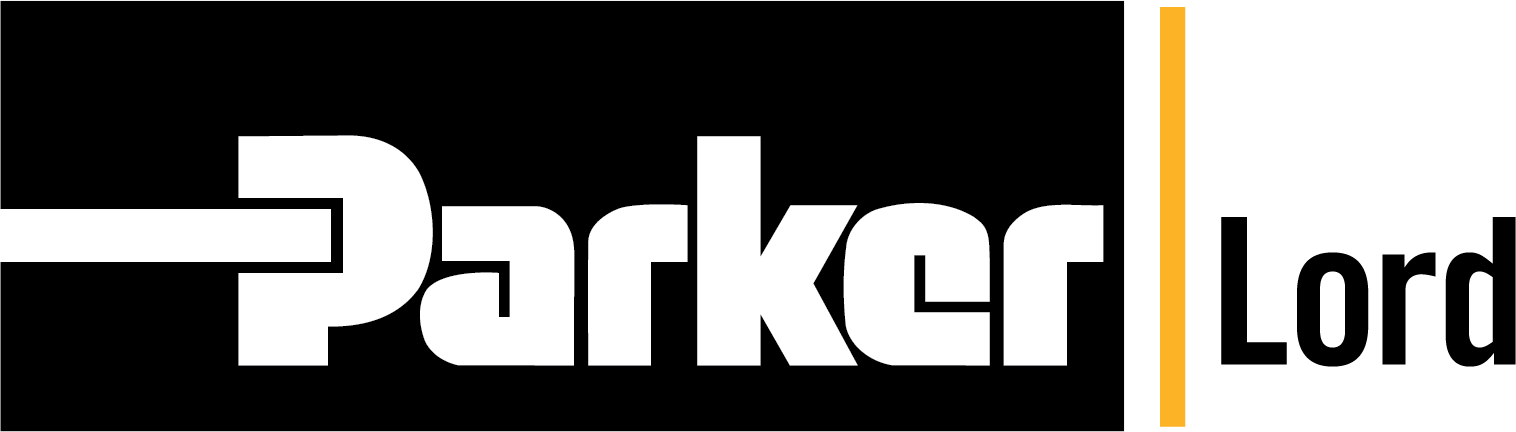
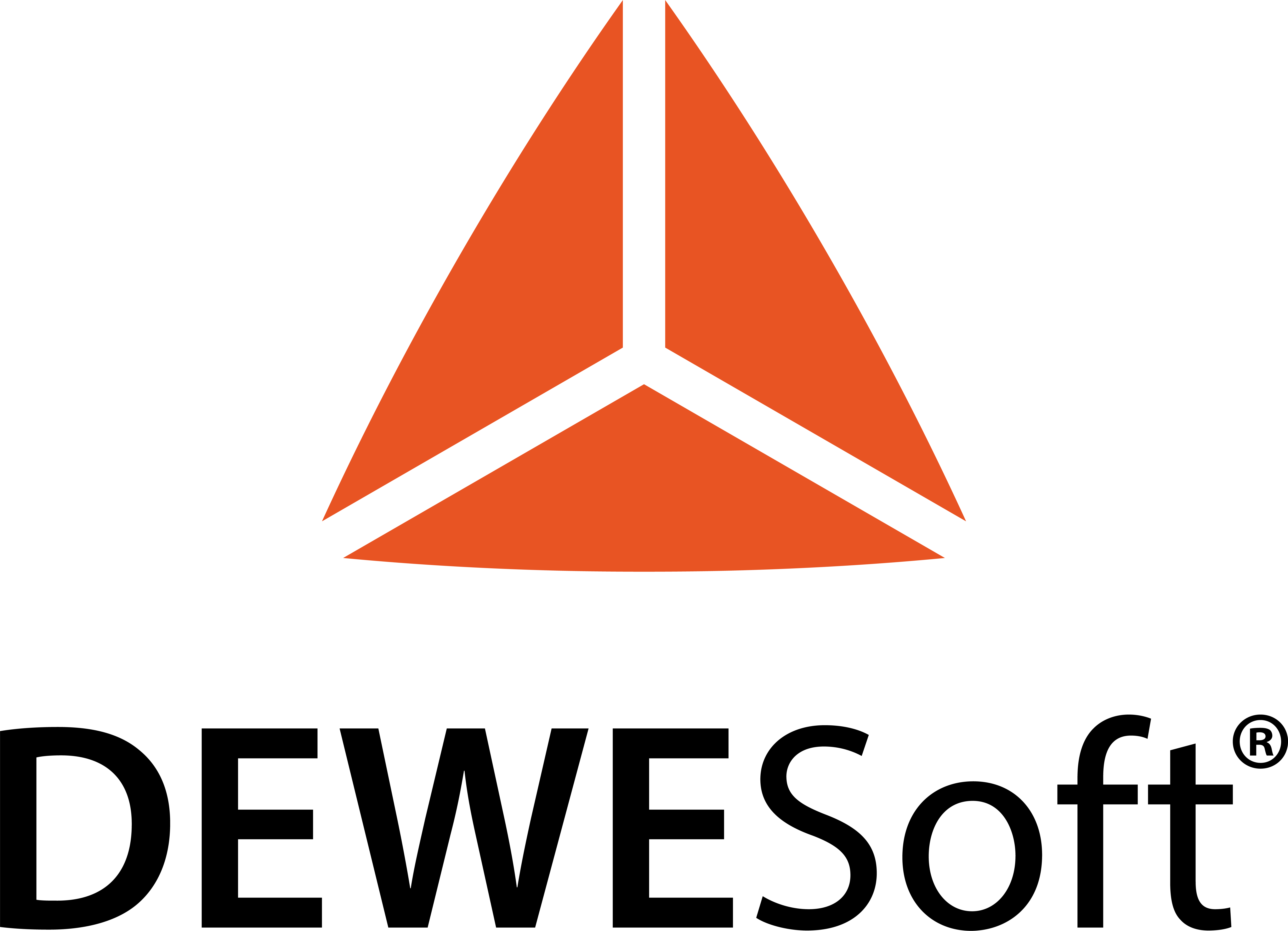
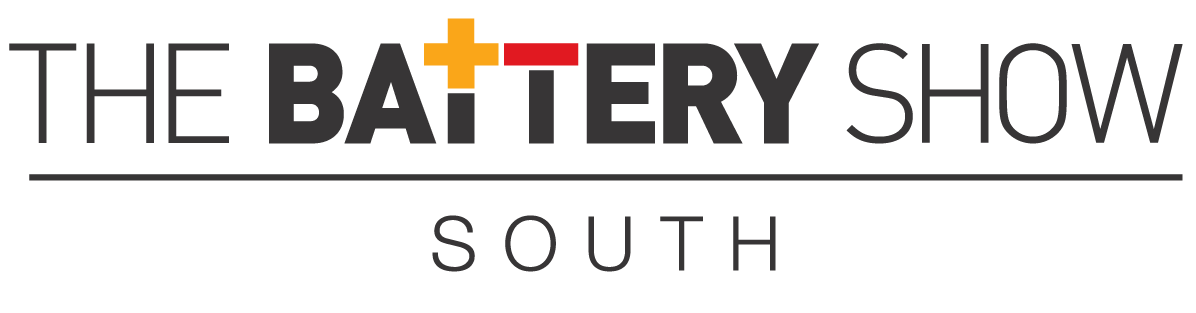
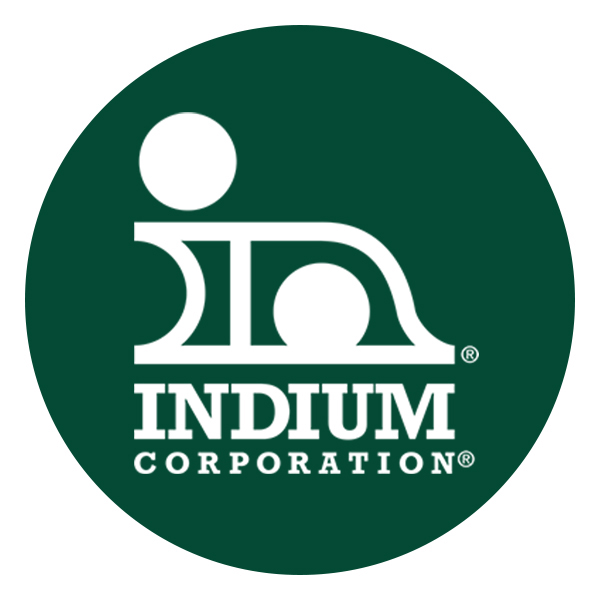
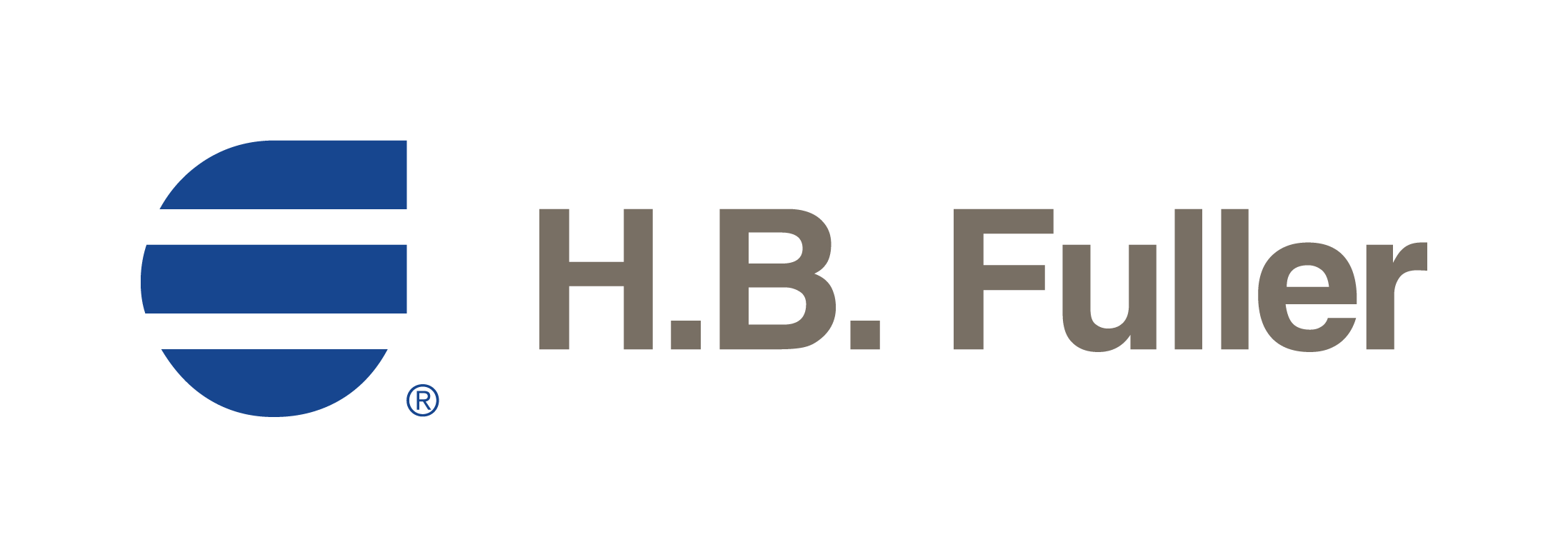