Baknor reveals revolutionary advance in liquid cold plate casting process
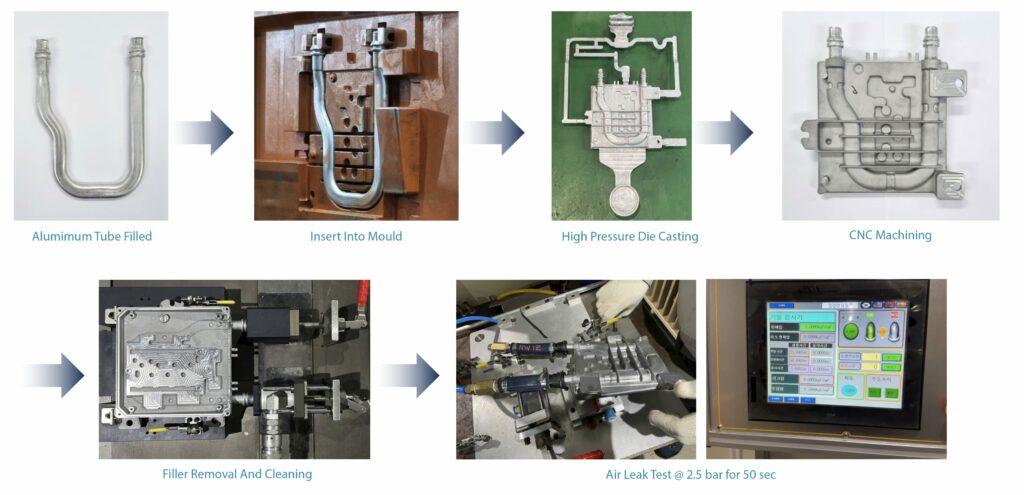
A new leak-free casting process that could revolutionise the efficiency of liquid cold plates has been introduced by leading thermal management solution innovator Baknor. The ‘Zero Zleak’ method promises to enhance the performance and reliability of cooling systems for high-power batteries and power electronics and set new industry standards.
Liquid cold plates are high-tech heat sinks that move heat from electronics to a coolant and carry that heat away to prevent overheating and damage. In EVs, they are used to efficiently cool down the battery pack by removing heat generated from the cells, significantly reducing battery life and improving performance.
Their effectiveness depends on their heat conduction capabilities and the efficiency of the coolant’s path and it is essential that the entire plate is completely sealed and does not leak, to maintain proper cooling and avoid potential safety hazards associated with the expulsion of coolant within the vehicle’s electrical system.
Baknor’s latest advancement combines the strength of cast aluminium with the precision of Zero Zleak Tubes to eliminate the risks of fluid leakage whilst also improving structural integrity and optimising thermal performance – making it ideal not only for EVs but also renewable energy storage, data centres and industrial power systems.
“As industries demand more efficient and reliable thermal management solutions, this breakthrough manufacturing process using Zero Zleak Tube in casting technology provides unmatched performance and durability, offering high-efficiency cooling for power-dense applications,” said Baknor co-founder Michael Ruscigno.
There are currently seven different manufacturing techniques for cold plates – stamping and brazing or roll-bonding, used for high volumes and low cost; machining, friction stir welding or die-casting, for high precision and strength; 3D-printing or CNC machining, for custom designs and prototyping; and extrusion, for lightweight and scalable plates.
Each of these processes has trade-offs in cost, complexity, thermal performance and manufacturing scalability, and the appropriate selection is typically dependent on the specific cooling requirements and production volume. However, Baknor’s Zero Zleak Tubes method offers a completely different and innovative approach to manufacturing.
Traditional methods often involve joints or interfaces where leaks can occur, but this technique eliminates such vulnerabilities by integrating a single, continuous tube – typically made of copper or stainless steel – into the cold plate without any joints, ensuring a seamless coolant pathway and significantly reducing the potential for leaks.
The tube is pressed into a channelled aluminium extrusion in a process that not only secures the tube firmly within the plate but also eliminates the need for the use of performance-limiting epoxies or adhesives for fixing. This results in superior thermal performance and a reliable, leak-free operation.
The innovation lies in the combined use of the single, continuous joint-free tubing; the precise press-fit technique in which the continuous tube is pressed into milled grooves within the aluminium plate to firmly secure the tube; and the elimination of adhesives through the use of mechanical bonding to maintain integrity and thermal performance.
Fluid flow and heat transfer is optimised within the part by the use of high thermal conductivity materials for the tubes and plates and the addition of surface enhancements that incorporate internal grooves or textured surfaces within the tubes to increase surface area and add turbulence, further improving heat transfer efficiency.
The use of fin structures, added through pressing after bending, further increases surface area, improves heat transfer and enhances thermal performance by improving conduction from the tube walls to the coolant, disrupting laminar flow and promoting better mixing and thermal contact between the coolant and the tube walls.
The absence of brazing or welded joints also means the structure can better withstand thermal expansion and contraction while the press-fit process prevents micro-gaps that could lead to coolant leakage or mechanical failure and the need for fewer fittings, seals or connectors reduces risks of failure due to vibration, pressure fluctuations or long-term wear.
Crucially, the process also offers more flexibility for designers to optimise their cooling designs as unlike traditional machined or stamped cold plates, which have fixed flat internal channels, the continuous tubing can be bent into complex serpentine, spiral or multi-directional paths before being pressed into the aluminium plate.
The channels can be denser or wider, allowing engineers to implement localised cooling optimisation, and by customising the height, spacing and orientation of the fins, it also offers more control over thermal performance. Finally, the elimination of brazing moulds or CNC machining means that creative new layouts can be tested and modified with ease.
As well as this increased design flexibility, the process is also more cost-effective, due to efficient use of materials, elimination of bonding materials and a simplified manufacturing process, eliminating labour-intensive and time-consuming brazing and welding and reducing energy consumption by avoiding high-temperature processes.
The improved heat transfer efficiency achieved through this manufacturing process should, ultimately, enable smaller and lighter designs to achieve the same cooling performance, while the mechanical bonding will provide greater shock and vibration resistance, making it ideal for demanding applications like EVs.
Click here to read the latest issue of E-Mobility Engineering.
ONLINE PARTNERS
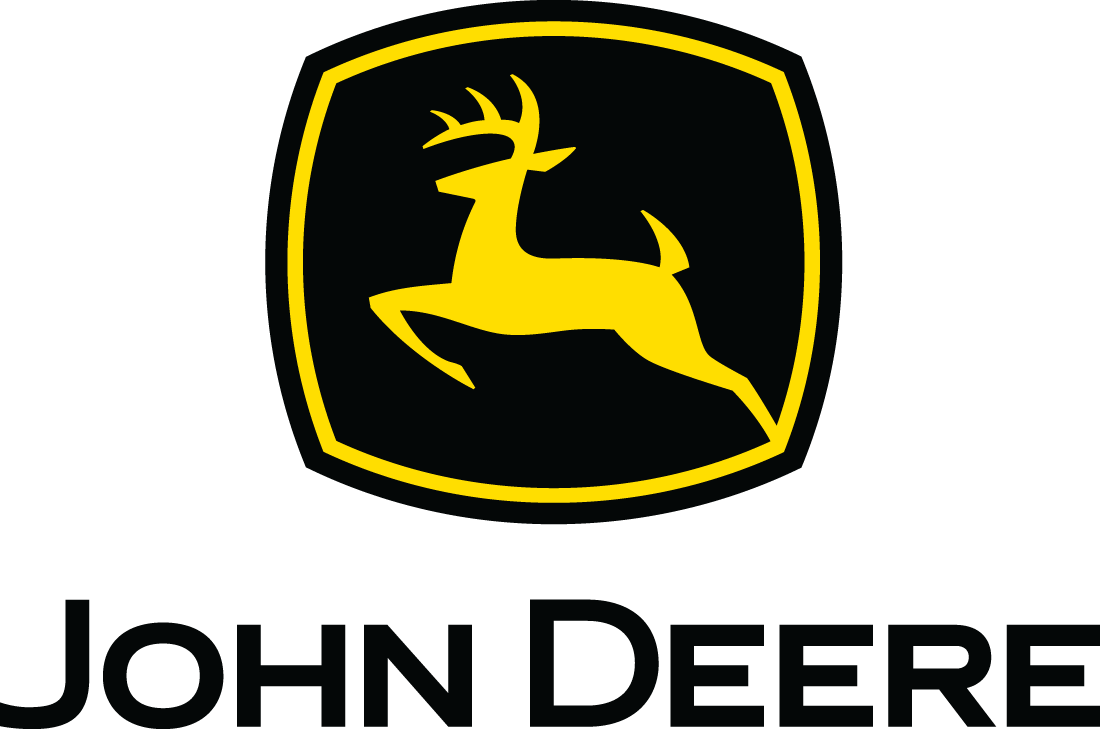
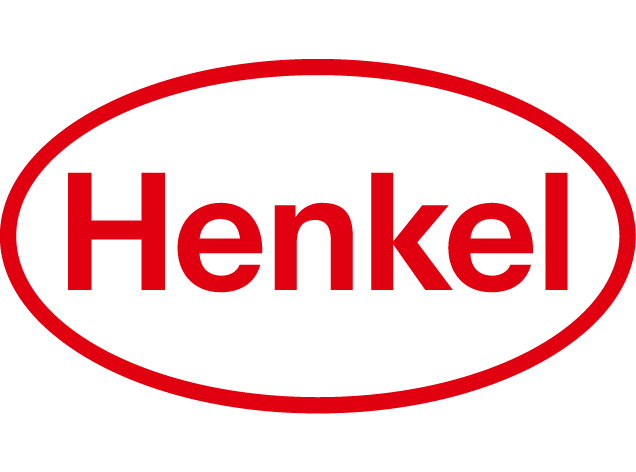
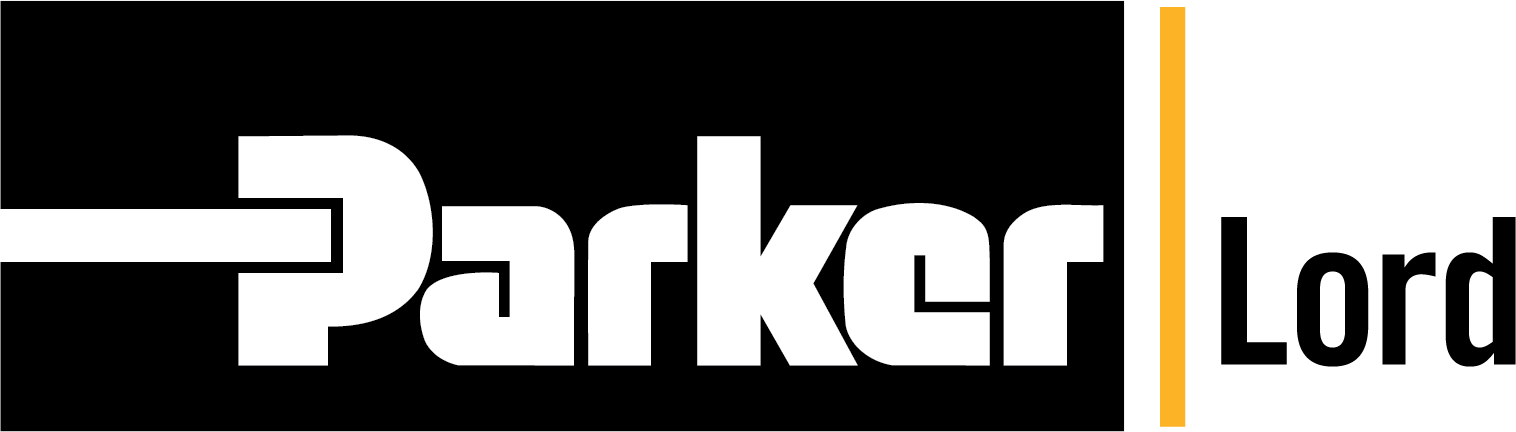
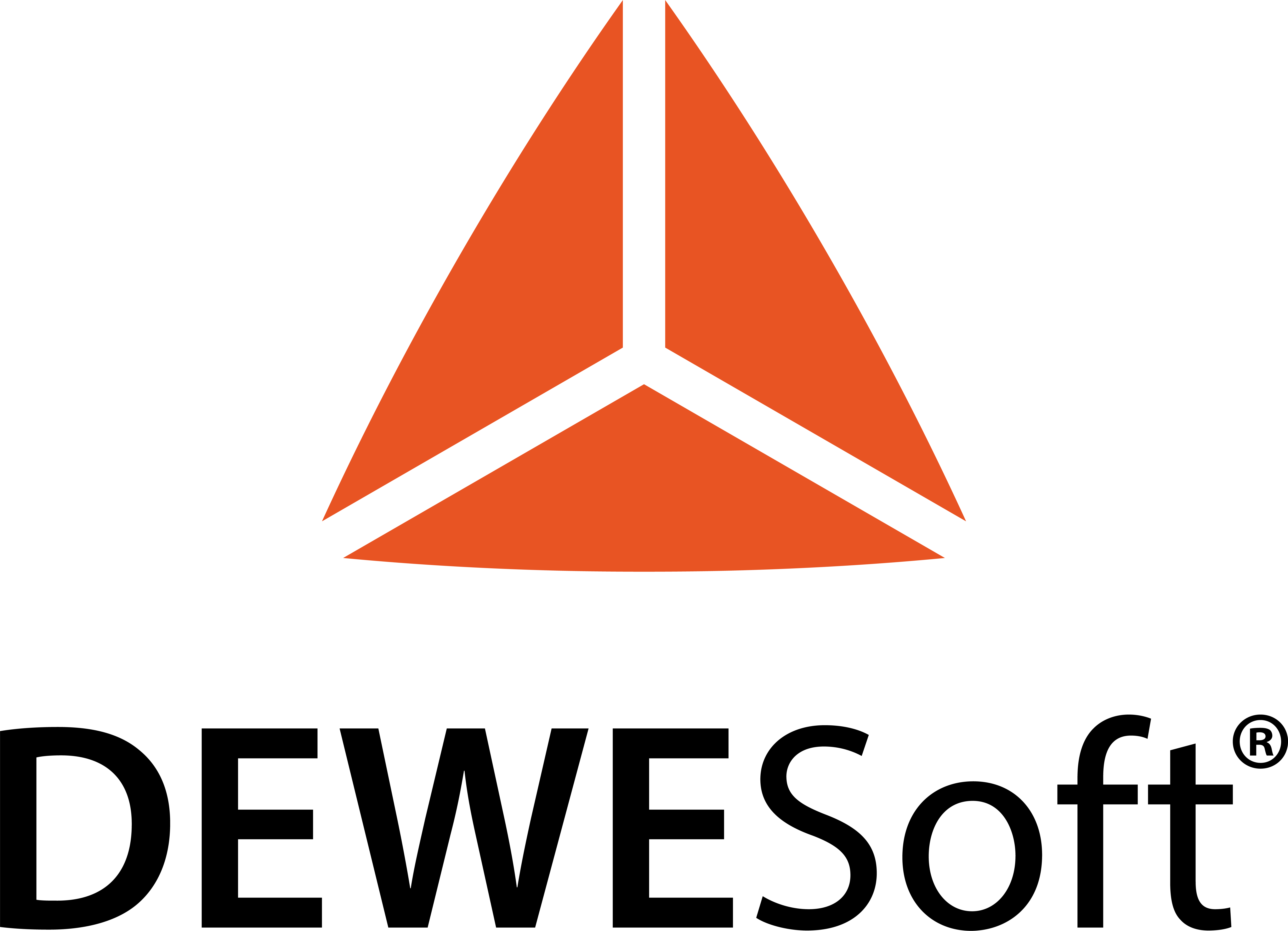
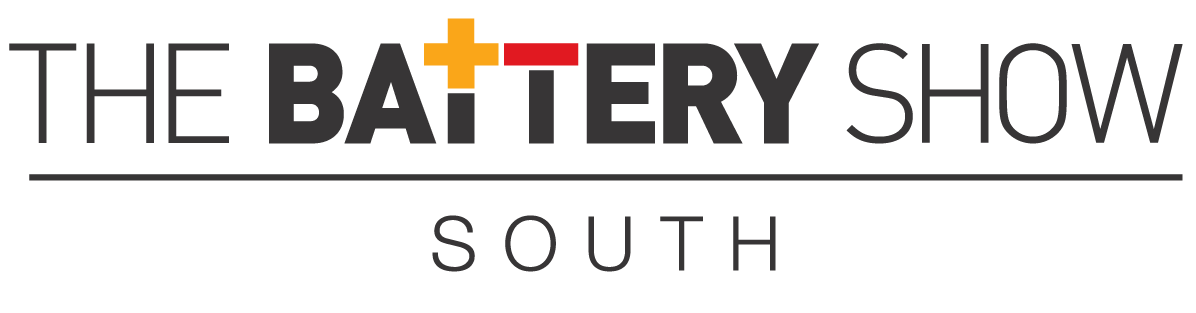
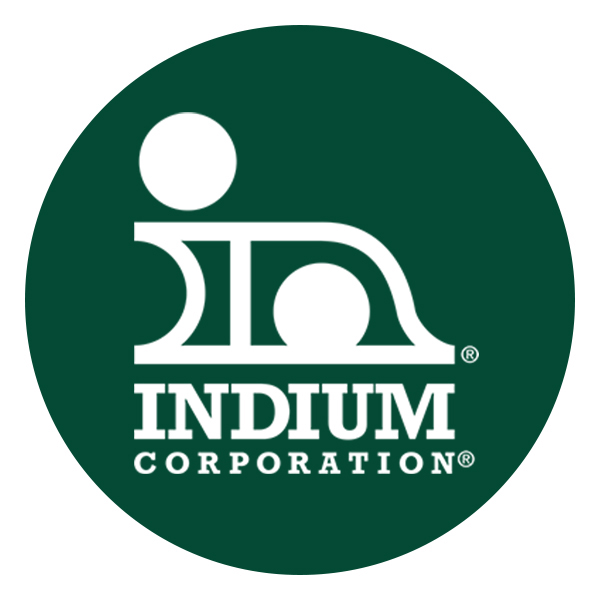
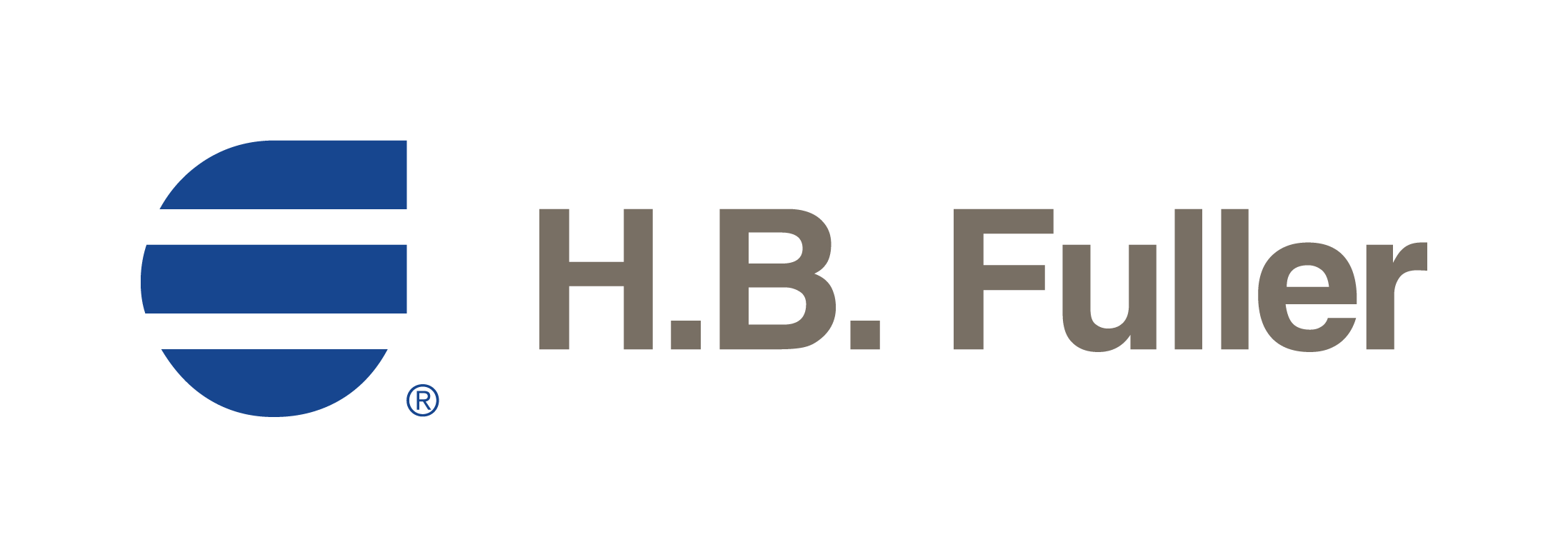
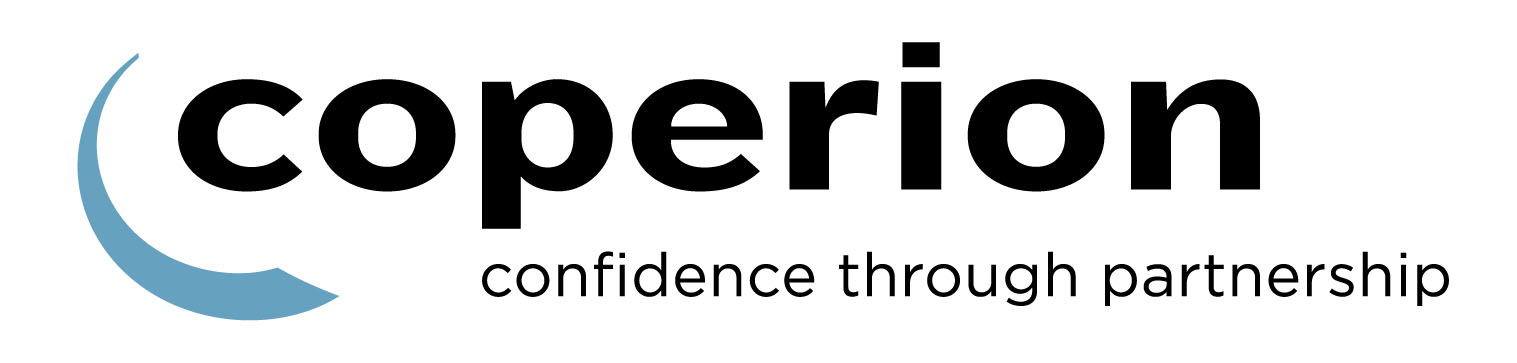