Meeting the challenges of developing e-VTOL air taxis
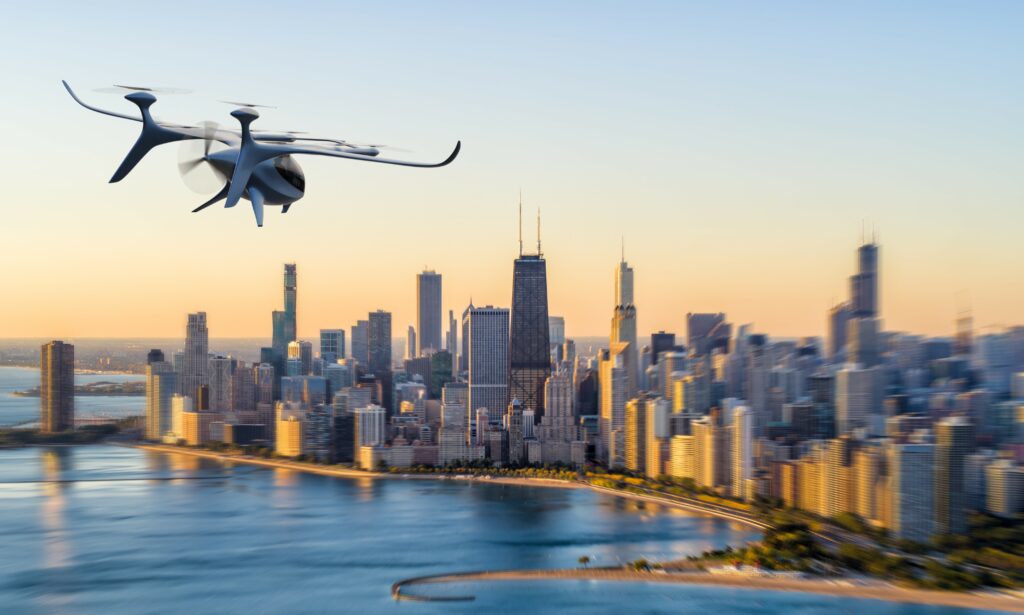
(Images courtesy of AutoFlight)
AutoFlight’s Prosperity I, a Chinese-designed e-VTOL air taxi sized to accommodate a pilot and three passengers, is intended to meet the rigorous safety standards that apply to transport-category aircraft including the largest airliners, and the company is aiming for certification and service entry in 2025 (writes Peter Donaldson).
Invited by electric aviation pioneer and AutoFlight’s founder, chairman and CEO Tian Yu, Mark Robert Henning joined the company last year as managing director of AutoFlight Europe to guide Prosperity I through European certification. This came after a long engineering career at Airbus and its predecessors, where he worked on combat jets and managed helicopter development programmes.
Henning says there are three main engineering challenges facing everyone developing e-VTOL aircraft. The first is propulsion, in which engineers have to work with the existing battery technologies and configure the motors and motor controllers to use the available energy as efficiently as possible.
The battery system has to be fully customised for the application, he emphasises. “We have to fit it into our aerodynamic design and optimise it,” he says.
Deciding where to put the battery so that it is not too far from the inverter and the motors is part of the optimisation process, because cabling adds weight and brings electromagnetic compatibility issues. Also, the battery cannot be configured as a monolithic pack because no single point of failure is allowed by the regulations.
“That means creating a very close relationship with the battery supplier,” he says.
The second challenge lies in flight control. “In vertical flight and in transition, the aircraft is inherently unstable aerodynamically, so we have to fully control that.”
EASA regulations demand a 10-9 safety factor, meaning that the probability of a technical failure causing a crash is one in a billion flight hours. This is driving intense debate and analysis within AutoFlight about the level of redundancy the flight control system needs. “Whether we will need to go triplex or even quadruplex I cannot tell you yet, but this is a critical discussion,” Henning says.
Safely minimising weight is the third challenge, he says. “With this 1500 kg aircraft you cannot allow 2 kg for a sensor or say it doesn’t matter if the passenger seat is a little heavy, and the challenge is even greater in electric aircraft because you lose payload and range more dramatically than when you have a gas turbine powerplant.”
Prosperity I has a high-aspect ratio wing plus a canard foreplane as a horizontal stabiliser. This configuration makes for a more aerodynamically efficient aircraft, because canards contribute to lift rather than creating downforce that would have to be countered with extra lift and the induced drag that comes with it. The wing is attached to two slim longitudinal beams, with the cabin pod beneath and the canard foreplane between them.
Eight lift motors rated at 100 kW each are arranged in two rows of three along the longitudinal beams, with another atop each of the vertical tails. The beams and vertical tails are slim to minimise parasitic drag from rotor wash impingement in vertical flight. A single 150 kW motor in pusher configuration is mounted at the rear of the fuselage and is used in forward flight to enable cruise speeds of between 180 and 230 kph.
The basic concept is used in AutoFlight’s cargo UAVs, the 50 kg V50 White Shark and the 400 kg V400 Albatross.
“I don’t need all 800 kW for continuous lift, but I do need it for controllability in the vertical, in the acceleration and transition phases, and I need it for the failure case,” Henning says. “That means if I lose two motors the remaining six have to lift all 1500 kg.
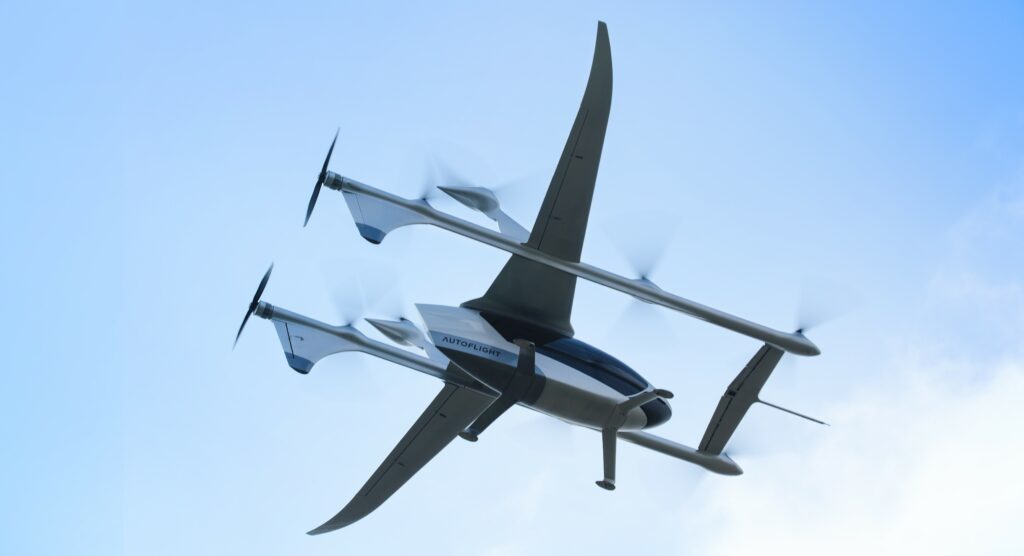
“We can lose two motors and still maintain control in the vertical and transition modes, even the front or rear pair, so long as the failed units are on different sides of the aircraft.”
The motors drive fixed-pitch propellers, chosen for reliability through simplicity, with thrust changes made by varying the rpm, and the drive is direct to avoid the use of gears for the same reason. “The fewer mechanical parts we have, the higher the inherent safety of the design,” Henning says.
For thermal management, he is also determined to avoid liquid cooling, for similar reasons, as the coolant and the pipes, pumps and tanks would add weight, complexity, cost and maintenance requirements.
He reveals that AutoFlight is designing its own motors and motor controllers. “We are protecting that IP, and as we move to serial production later those vital components will be 100% under our control,” he says.
One proof-of-concept aircraft is flying now, with a second set to join the programme soon. “Later this year we will freeze the configuration and go into detail design. In 18 months we will start to build prototypes, and these will be representative of the final configuration,” he says.
“We are still investigating how many prototypes we will need for the certification programme, three or perhaps four. They are going to fly for 2 years, as the EASA will want a lot of testing.”
Serial production will begin during the certification process, he adds, the idea being to be ready for service entry immediately after certification.
ONLINE PARTNERS
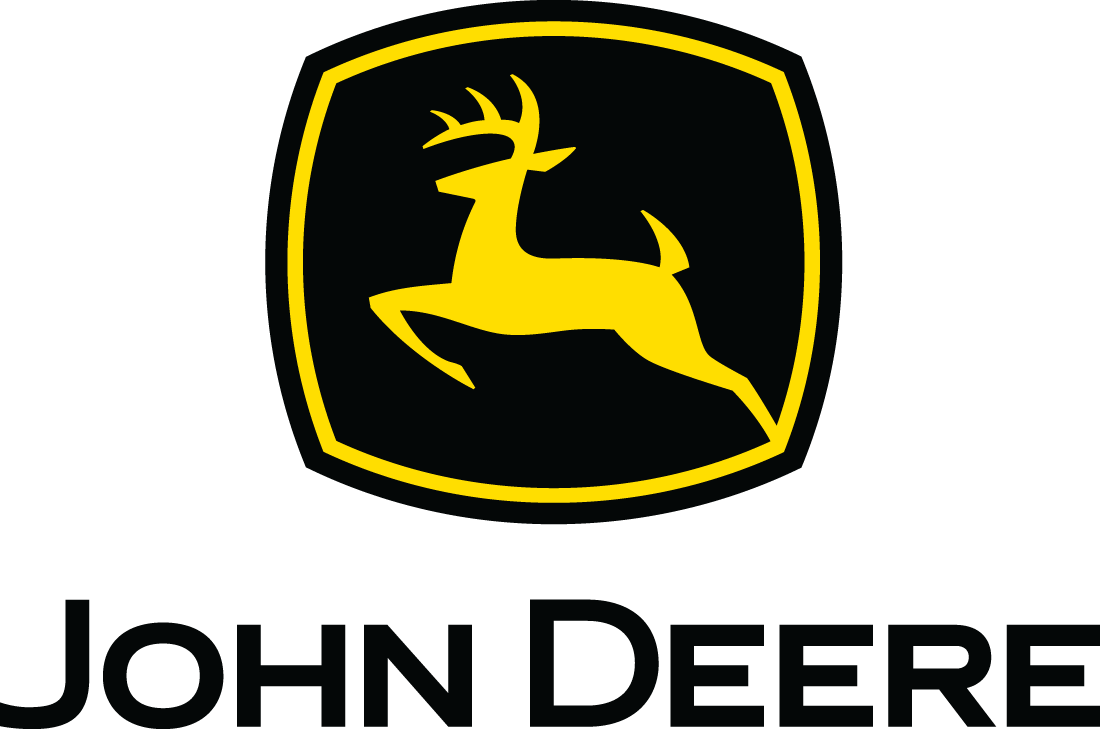
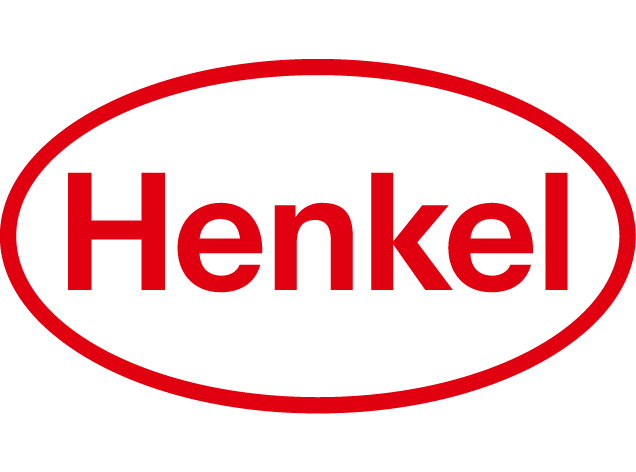
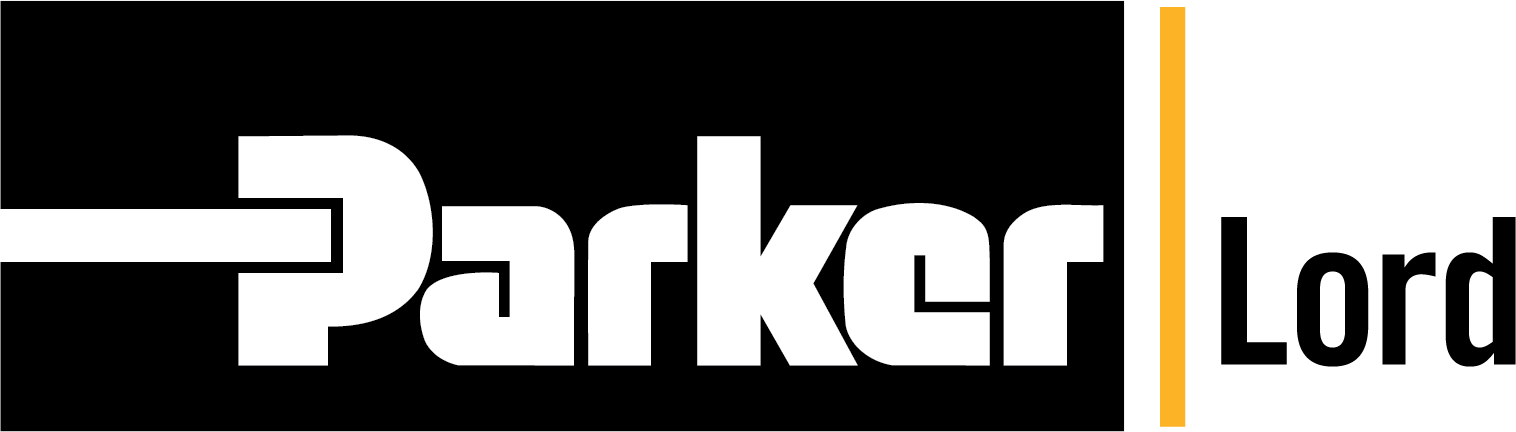
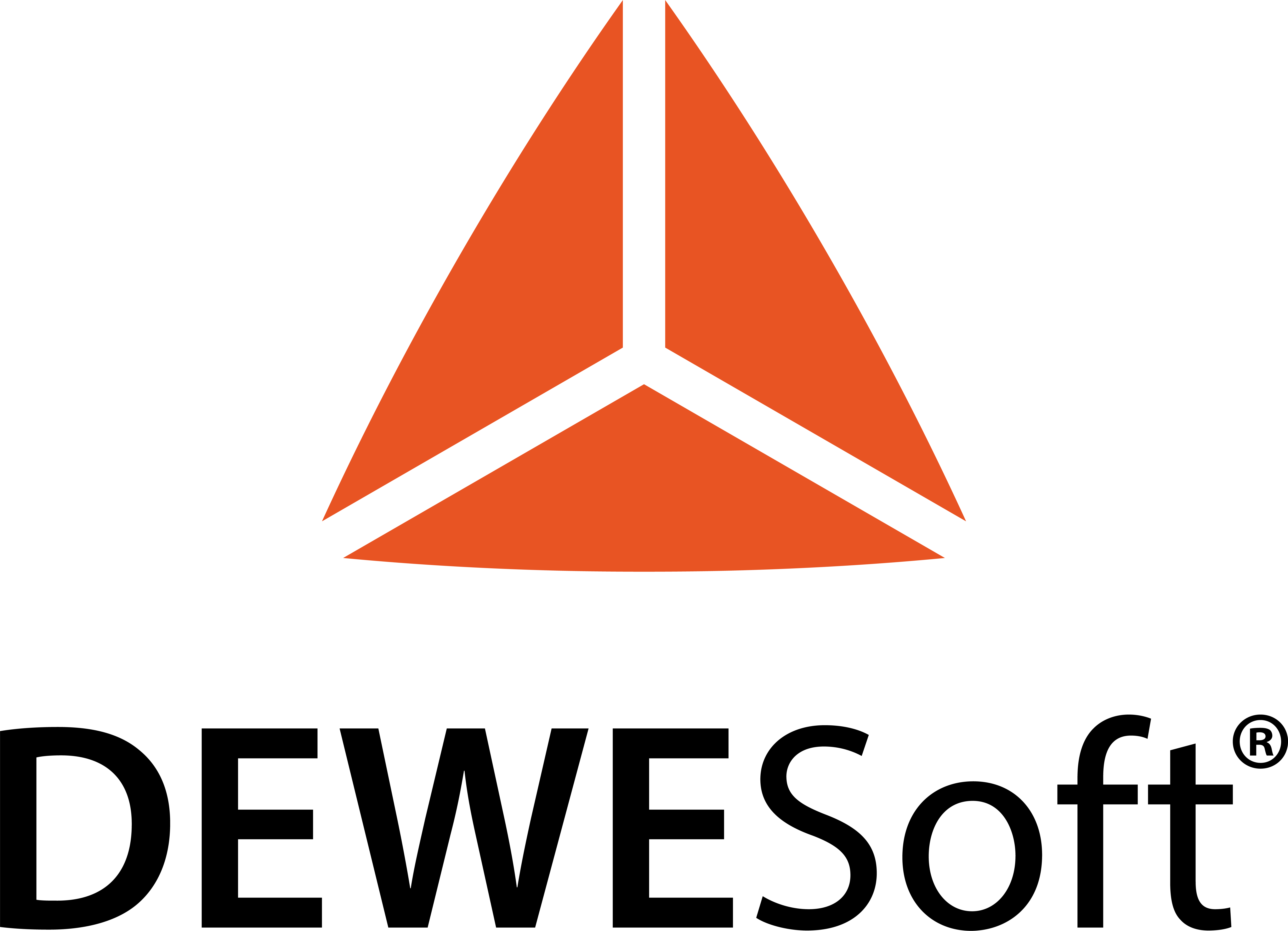
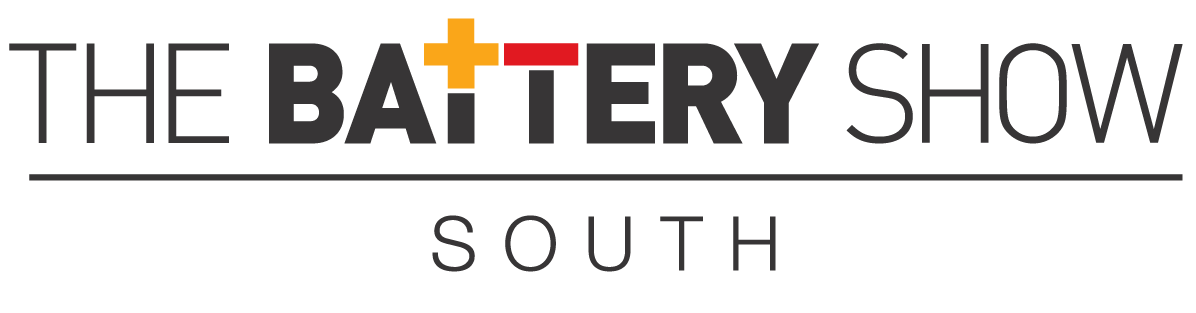
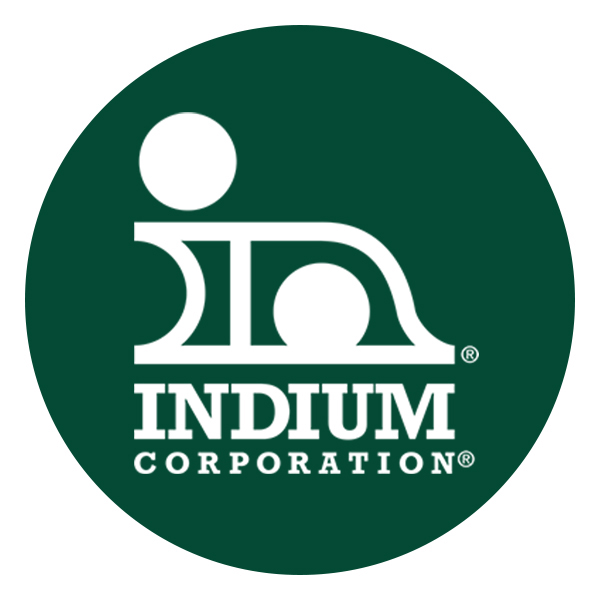
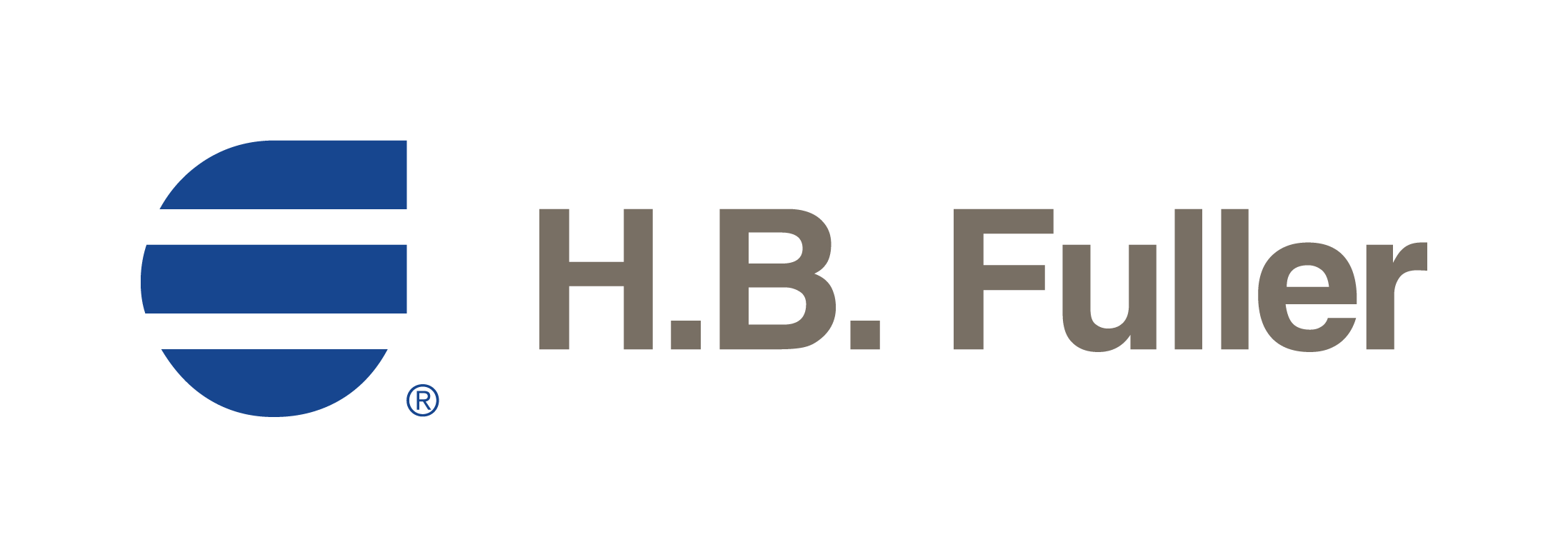