Autocraft battery re-manufacturing
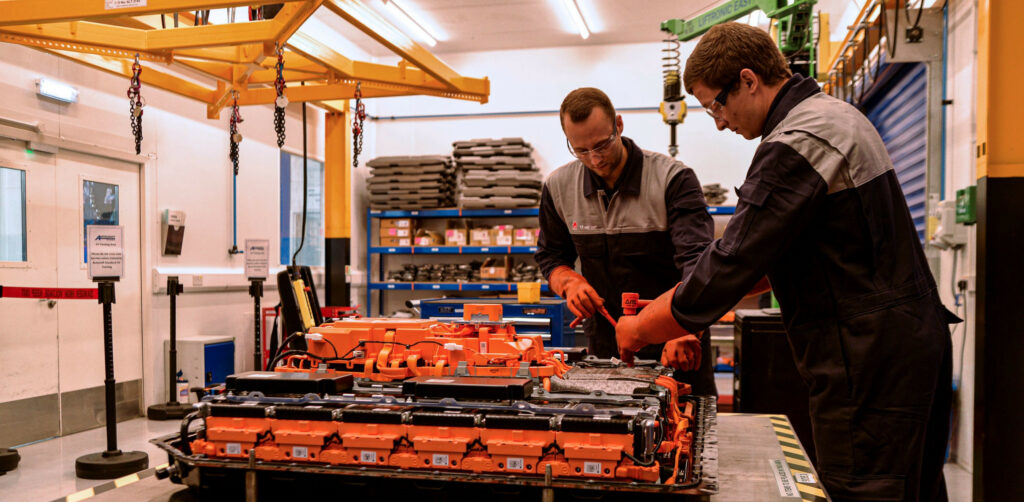
(Courtesy of Autocraft)
With 40 years of experience re-manufacturing internal combustion engines and transmissions for automotive OEMs, Autocraft Solutions Group has turned its attention to EVs in recent years and has developed both fixed and mobile battery re-manufacturing systems to meet a growing need, as CTO Simon Warburton explains to Peter Donaldson.
That need is to match battery life to expected vehicle service life while making them ready to go into second life applications such as energy storage, he argues
“If you service a battery pack and replace the cells that are degrading, you may have to do this once or twice over the lifetime of the vehicle. For most vehicles in the UK, the average age at which they are sold for scrap is around about 15 years, and the average age of a car in the UK is about eight, while battery packs in EVs are warranted to 150,000 km or seven or eight years, so what are you going to do, scrap it at that point?” he asks.
“This is an important consideration given that, typically, the manufacture of an EV produces nearly double carbon emissions of the production of an ICE vehicle. Depending on the EV in question it will take between 32,000 km and 88,000 km of usage to break even on the carbon emissions generated in production. This is largely due to the environmental impact of the extraction and refining of raw materials for lithium-ion batteries. Two repairs to replace degrading cells, using the Autocraft system, produces less than 6% of the CO2 emissions of a new pack,” he emphasises.
“That’s not going to get us to net zero, but if you service a pack you can extend its useful life in the vehicle to 12 or 13 years and, when the battery has degraded to the point where it is unsuitable for automotive use, we can repurpose its modules and cells for second life applications. This is vital for owners as, currently, the second-hand market doesn’t understand the value of used EVs.”
The re-manufacturing process does not return the battery to as new condition, he explains, instead replacing any failed cells with others whose state of health matches the remaining cells to bring it back onto the expected degradation curve.
“If a customer has a problem at five years when the pack was at, say, 90% capacity but one failed cell has brought it down to 65%, we could restore it to 90% capacity and extend its life. We estimate that by utilising this technology, we can extend typical battery pack life from 7-8 years to about 12 years.”
In the long term, the typical source of the replacement cells would be donor packs, he says. “Now, at the beginning we use brand new cells, but as the programme goes on, as with a project we completed for a UK OEM, we will harvest. There are 36 modules in the pack that we re-manufactured, so a donor pack can repair 30 or more others.”
This is also important, he adds, given the constant development of cell chemistry, as manufacturers will not be producing equivalent cells several years after their production runs end.
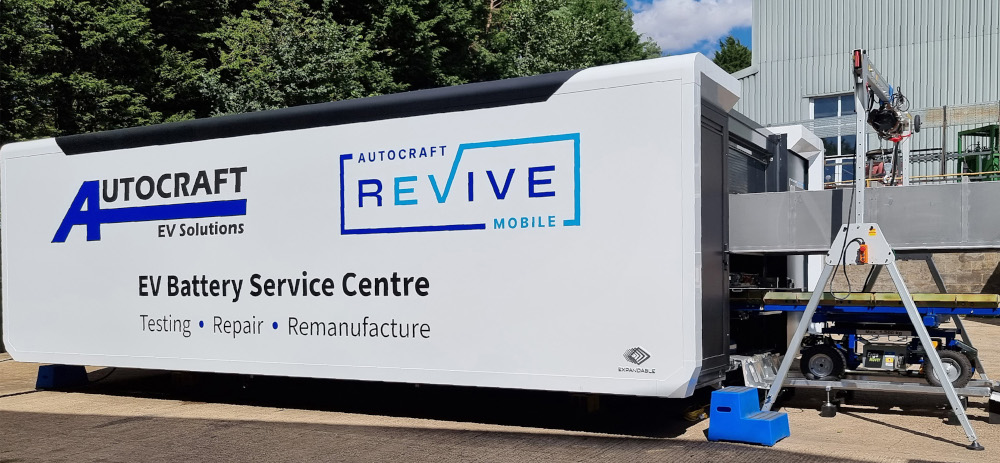
(Courtesy of Autocraft)
Integrated into the dimensional equivalent of one 30 ft ISO container, Autocraft’s Revive Mobile battery service centre deploys on site by folding itself out from the bed of a truck and includes its own power source so it can operate independently of or connected to the grid, Warburton says. During pack discharge, for example, it can return the battery’s energy to the grid.
Its capabilities include pack integrity safety checking with state-of-health (SoH) test equipment, fault identification, repair planning, pack discharge and disassembly, module replacement and pack reassembly, post-repair charge, discharge, and SoH testing. All these capabilities are supported by cloud computing, Warburton notes.
Warburton describes the system as semi-automated, explaining that for those procedures that require a human operator it provides detailed step-by-step instructions, in many cases using virtual reality technology to project the instructions onto the precise areas of the pack to be worked on.
The safety systems also track the tools ensuring that none are left in packs by mistake. Camera based systems monitor whether all PPE is being worn correctly, for example, and will shut down the electrical systems until it is.
The safety of the system itself has been independently verified by the UK Fire Brigade and insurance companies, Warburton notes. “Further consultation with the UK Health & Safety Executive and Environment Agency have been arranged to help shape new regulation in DC current, as there has been a great deal of interest in how Autocraft is implementing its own safety systems.”
ONLINE PARTNERS
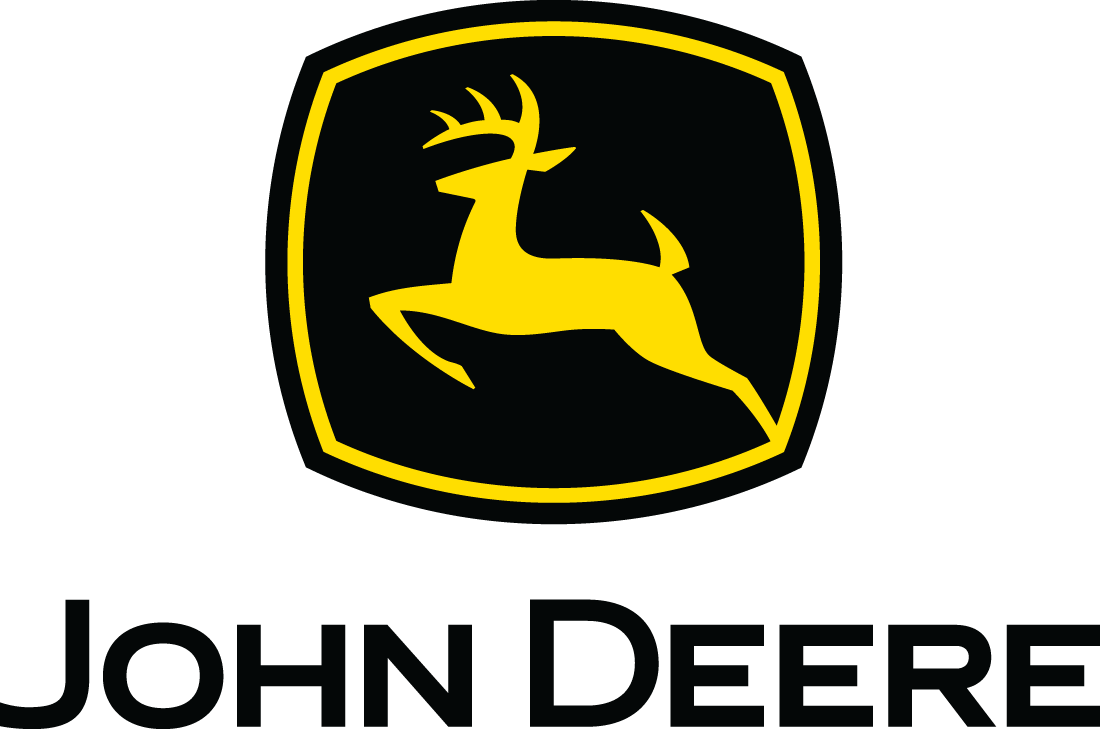
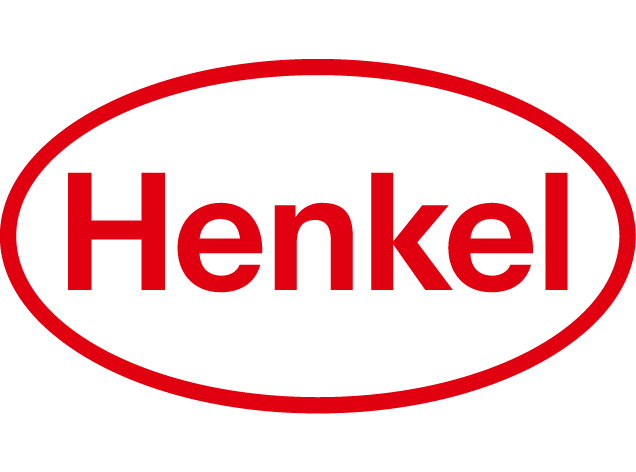
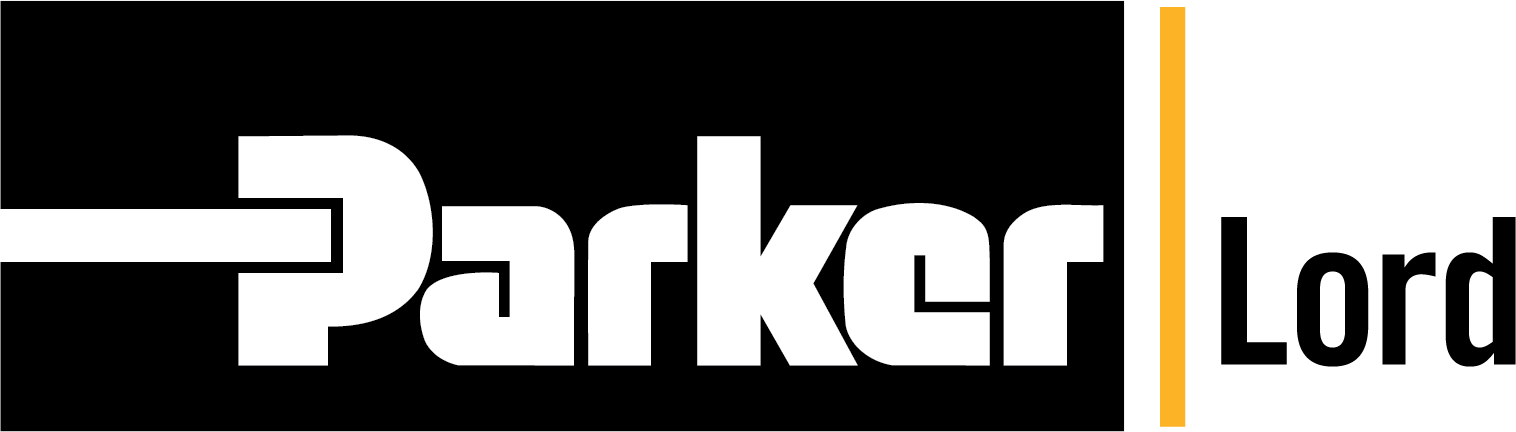
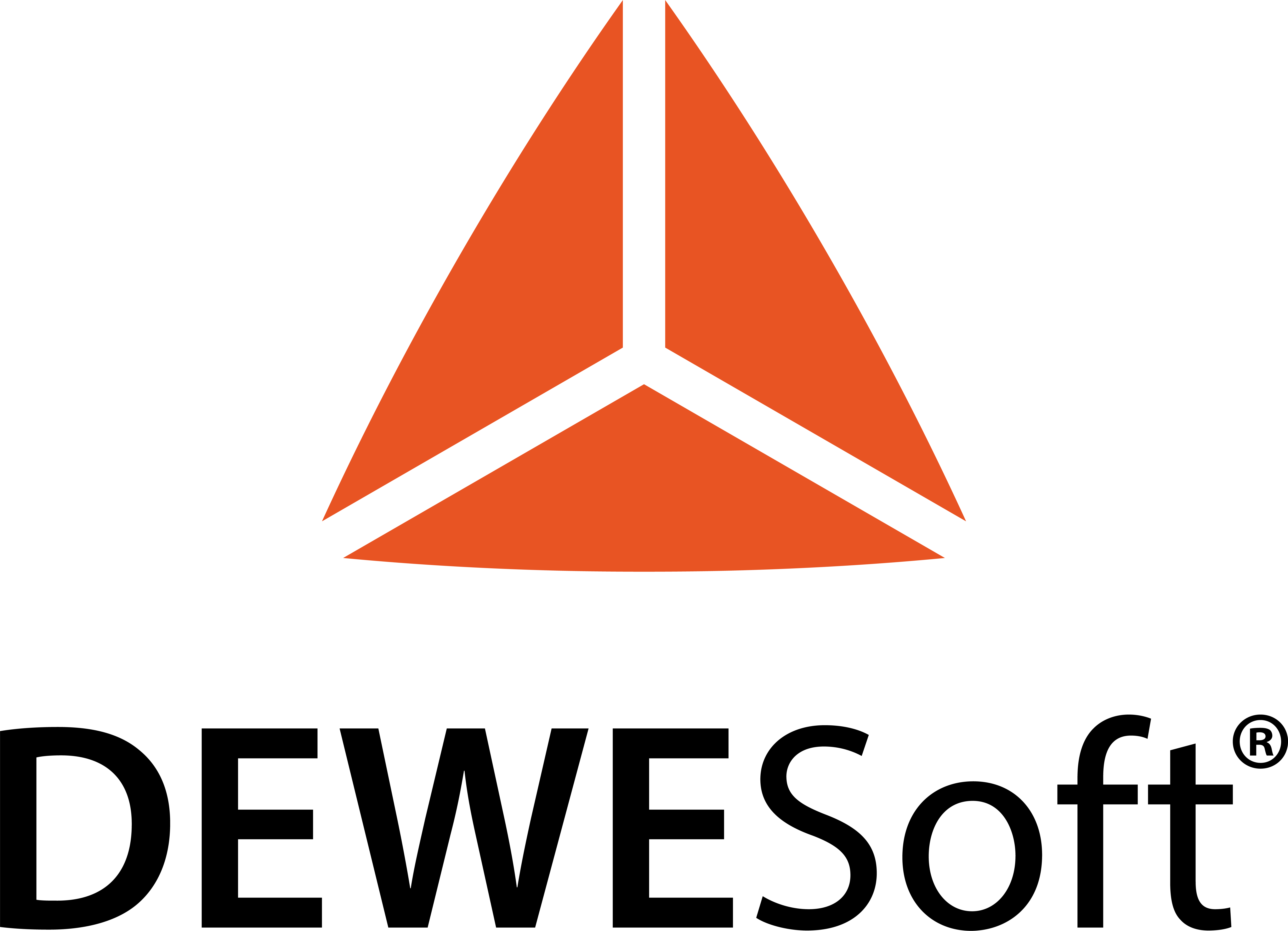
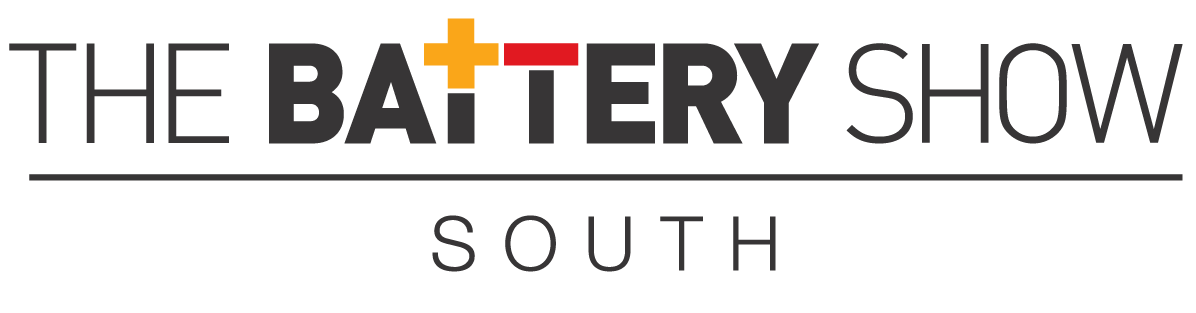
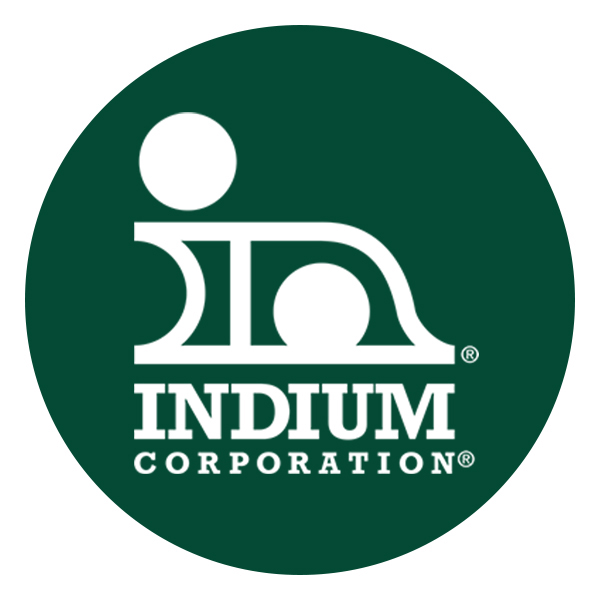

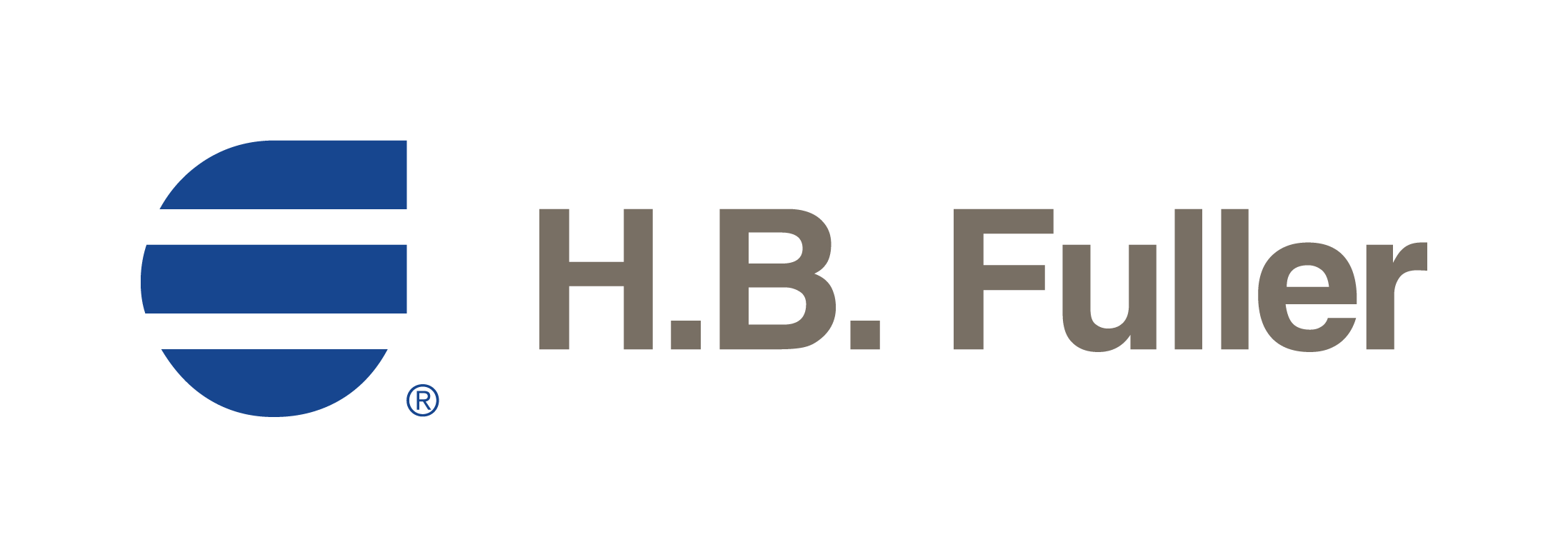
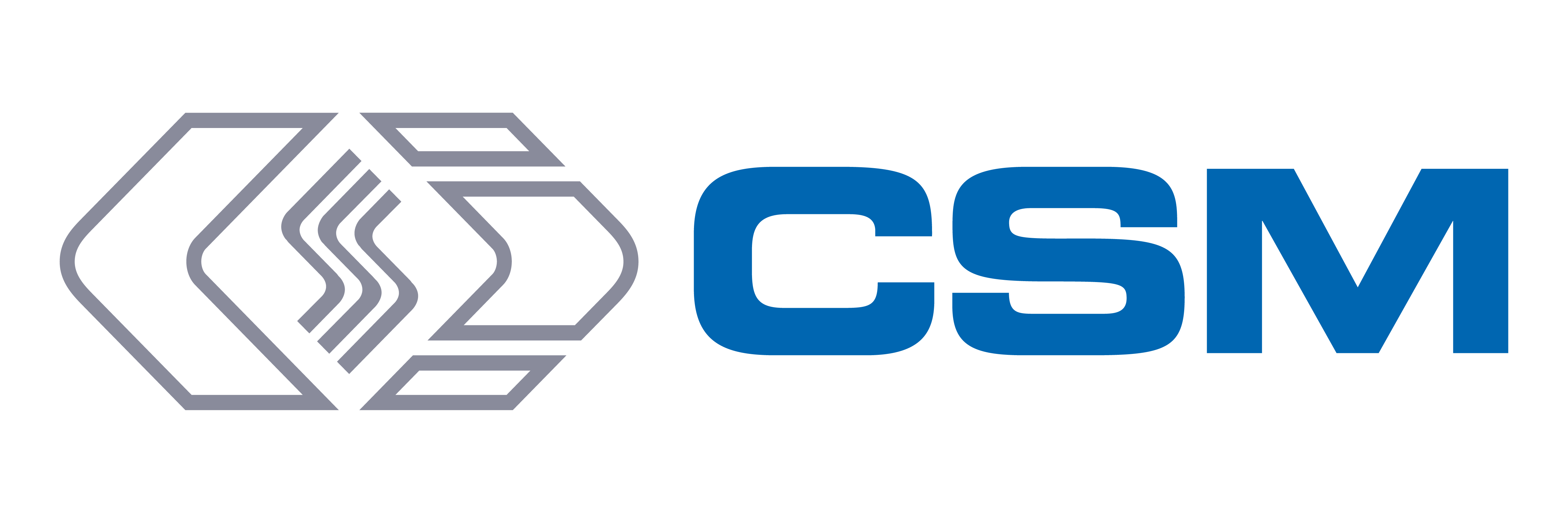
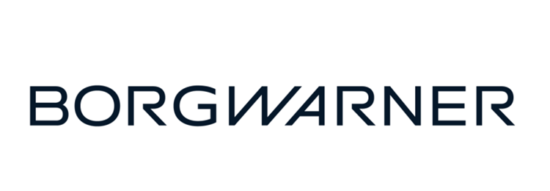