AirShaper offers fixed-price options for aero testing
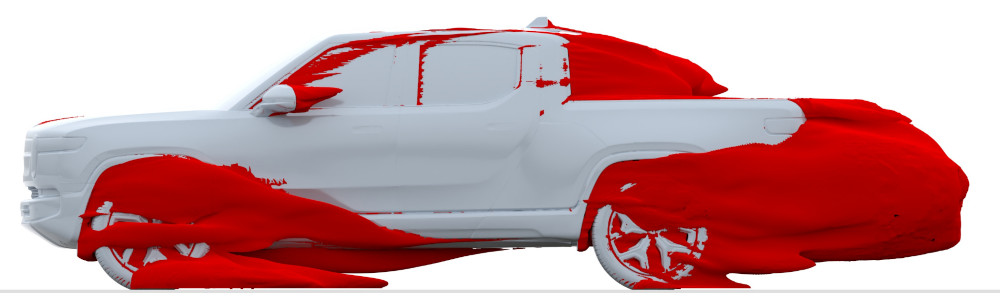
(Images courtesy of AirShaper)
Aerodynamic testing continues to shift away from wind tunnels and into the virtual world of computer models and CFD packages, but barriers to entry remain high because of five or six-figure prices for software licences and the need for very powerful computers to run the code (writes Peter Donaldson).
AirShaper is working to change all that by offering a range of less costly fixed-price simulations that run on Google Cloud and are accessible via a web browser.
The company recently assessed the Rivian R1T pick-up truck, which has a claimed drag coefficient (Cd) of just 0.3, something nearer 0.45 or 0.5 being more typical for this class of vehicle, according to AirShaper’s founder Wouter Remmerie.
Using a 3D model supplied by reverse engineering and benchmarking company A2MAC1, AirShaper confirmed that the actual Cd was very close to the claimed number, at 0.322, falling short by a small amount partly because of a rogue panel gap caused by an assembly fault in the scanned vehicle. The gap created a vortex around the windscreen pillar that generated some unanticipated drag, and AirShaper’s software found it.
Remmerie explains that customers don’t need much experience with simulation to use the service. All they need is a 3D model of the vehicle, which can be uploaded from the user’s own 3D environment. AirShaper uses the universal exchange file format .stl, so the software can work with any model from any software package.
“Often these models are very complex, consisting of many surfaces, and as soon as you have a gap between two panels or surfaces – no matter how small – normally the simulation software will crash,” he says.
“We have made it possible to work directly with very small gaps and holes in a model though, typically saving the designer days or weeks because they don’t have to go around the entire model to close every gap.”
Once uploaded to the cloud via the browser, the model can be dragged around to point into the wind, which is set to a reference speed appropriate to the vehicle, and the rotating wheels option is selected. The software will automatically detect the centre of rotation for each wheel, and match the rotation direction and speed to the vehicle’s velocity. There is also an option to add a radiator to assess its effect on performance.
Three levels of detail are available – a low-resolution simulation aimed at hobbyists priced at €50, a mid-level ‘regular’ simulation at €500, and the most detailed option with up to 100 million cells, at €2500. A regular run takes between 3 and 7 hours and, when it’s complete, the software produces a full report in PDF format.
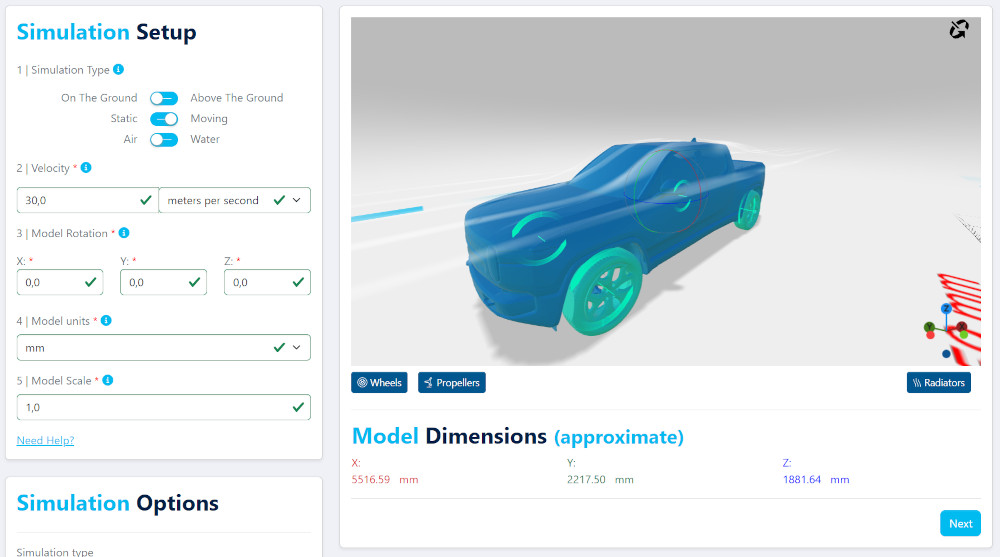
The set-up page is where you can upload your 3D model and set parameters such as the environment and speeds you want to investigate, wheel rotation and so on
“We calculate the frontal surface area of the car, which is used later on to calculate the Cd,” Remmerie says. “Then we calculate all the forces: we have a drag force along the wind direction, the vertical forces of lift/downforce – depending on the type of car – and we have lateral forces. We summarise them in a comprehensive table, and show how the calculation converged through time. All of this is done in an automated way.”
The steps the software takes to build the simulation start with the creation of a virtual wind tunnel in the 3D domain around the car, Remmerie explains. The domain is then divided into 3D cells, each of which has a velocity of flow and a pressure value. Analogous to the pattern of pixels in a 2D digital photograph, the cells depict a 3D flow pattern around the object, and they are smallest and most numerous close to the car where the airflow is most complex.
“At the inlet of the virtual tunnel there is a certain air velocity, which will develop a flow around the car,” Remmerie says. “This process takes many iterations to converge on a stable flow pattern that matches reality as closely as possible.
“Once we have calculated the Cd, we estimate the aerodynamic power required to maintain a certain constant speed. Drag scales with the second power of velocity, assuming a constant Cd, meaning that drag goes up by a factor of four if you double the velocity.
“In terms of the power the electric motor needs to provide though – which in turn shows how much energy is drained – you have to multiply it again by the velocity, because power is a product of force and velocity. The required aerodynamic power to maintain a certain speed is therefore proportional to the third power of velocity, which means that if you double the velocity the aerodynamic power you need goes up by factor of eight.”
Clearly there is a lot to be gained for EV designers in getting the aerodynamics right, starting with basic decisions about shape. Remmerie says, “Are we going to give the aerodynamics priority in terms of the basic shape of the car, or will you go for a conventional-looking car and tweak it as much as possible?”
In the first case, very aerodynamic overall shapes such as the teardrop can force compromises on practicality, by restricting rear headroom, for example. More fundamentally, for a given Cd, small cars generate less drag than large ones.
In the latter case, small details take on great importance, such as smoothing sharp edges, making door handles flush-fitting, replacing door mirrors with cameras, and ensuring that the underside of the floor is flat so that the airflow is not disturbed by suspension components.
As its name suggests, AirShaper software can automatically morph the shape of a design to reduce drag or increase downforce and so on. With the solar-powered Aptera, for example, the software was given a virtual box around the front wheel covers within which to reduce drag, which it did by curving the front of each cover to point inwards, towards the car’s nose, to align with the local airflow instead of with the driving direction.
“If you have already eked out most of the performance using manual iterations and simulations, you can use this technology to further refine your design,” Remmerie concludes.
To try out the AirShaper software go to: https://app.airshaper.com/projects/tesla-semi
ONLINE PARTNERS
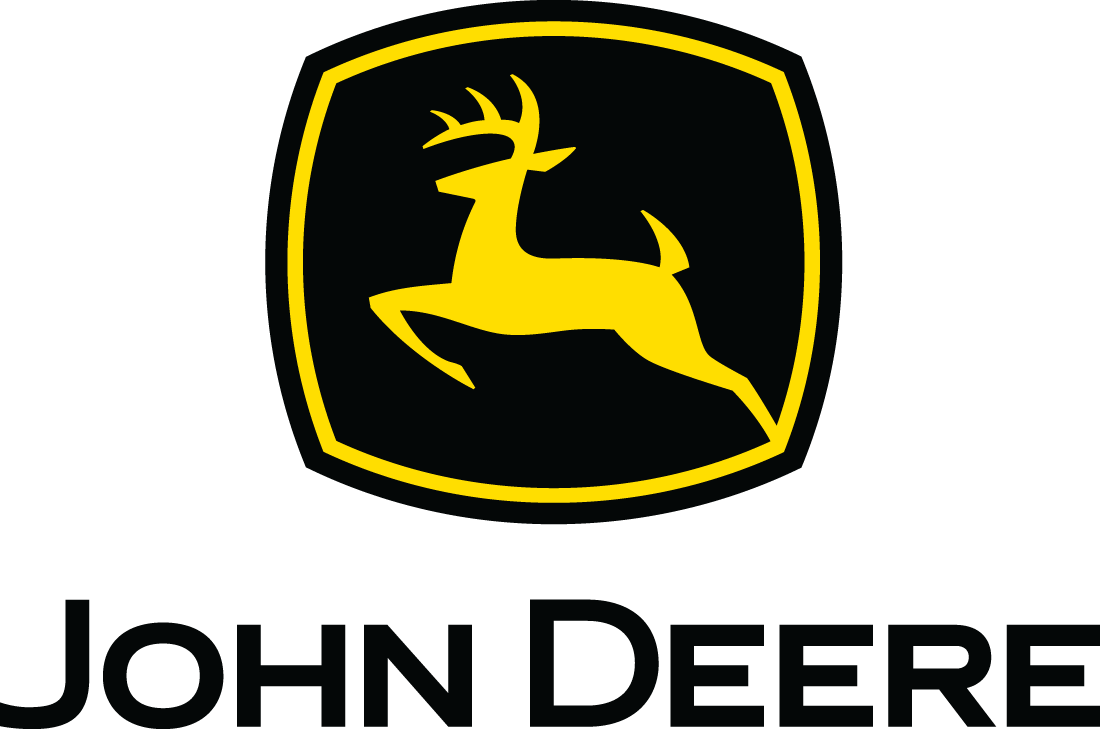
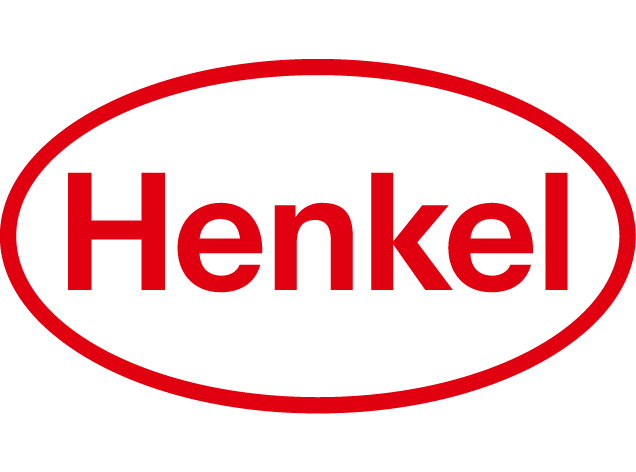
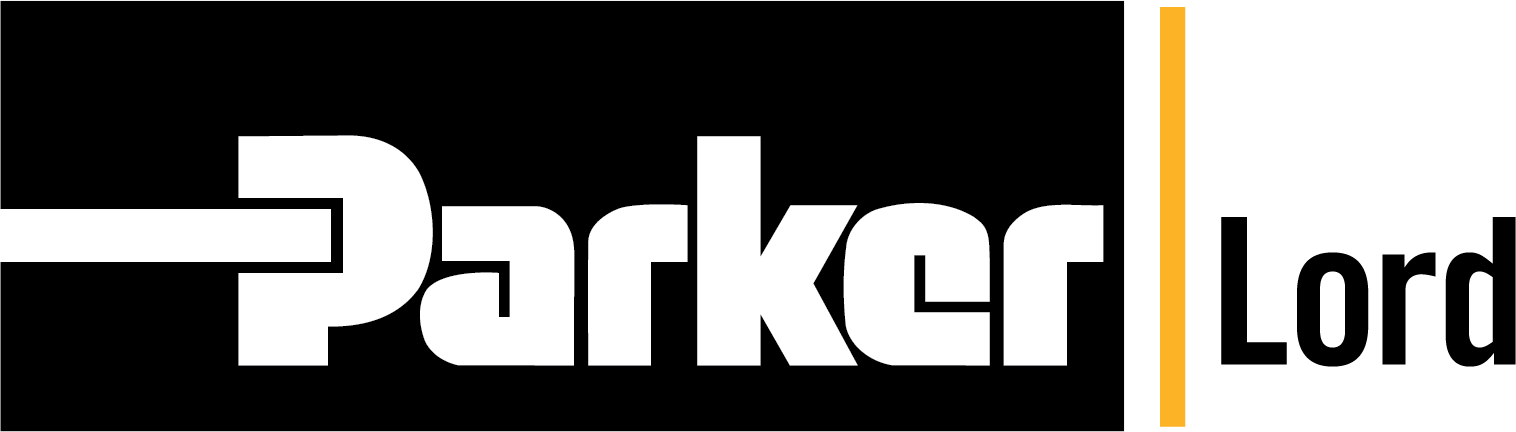
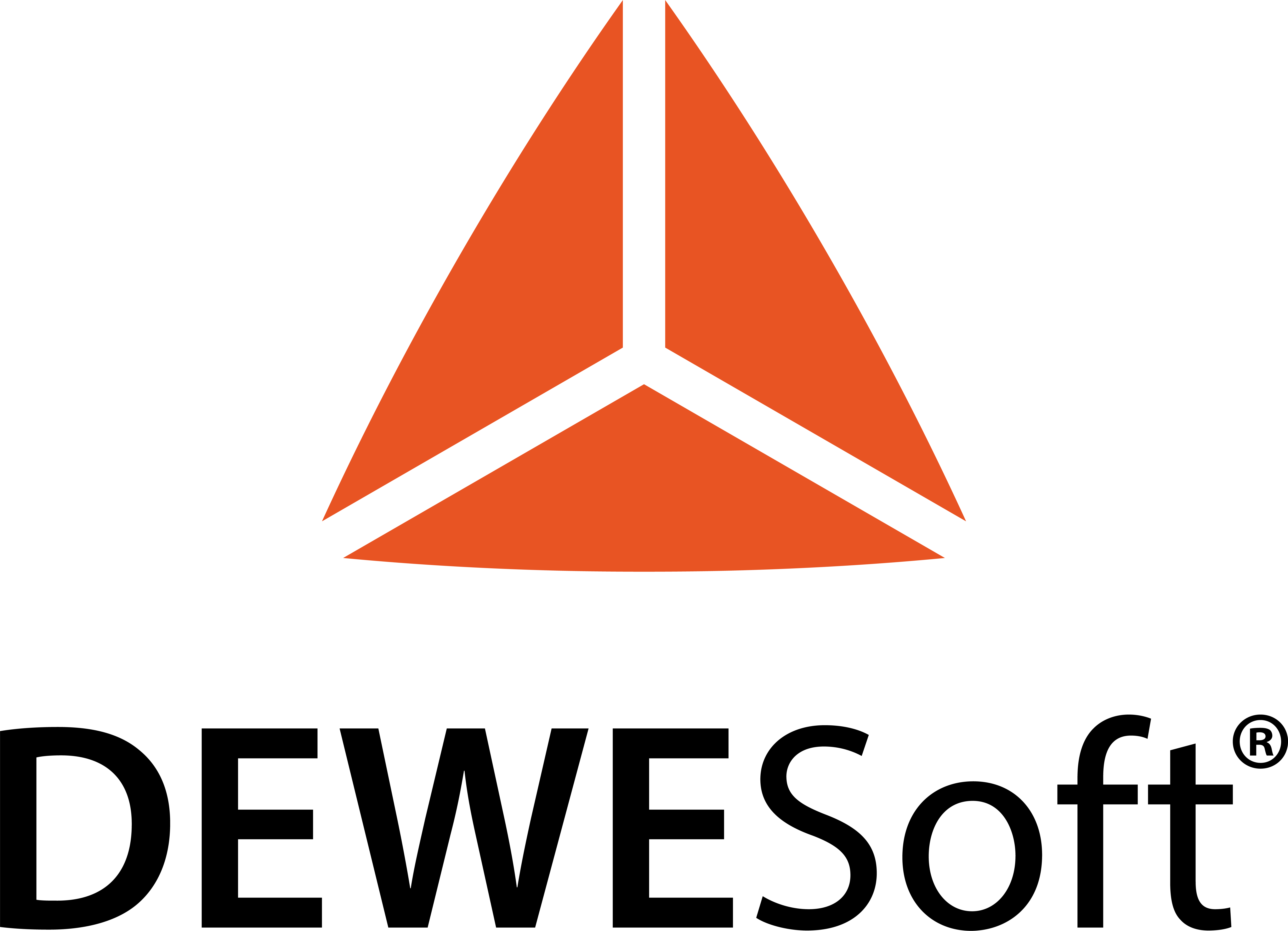
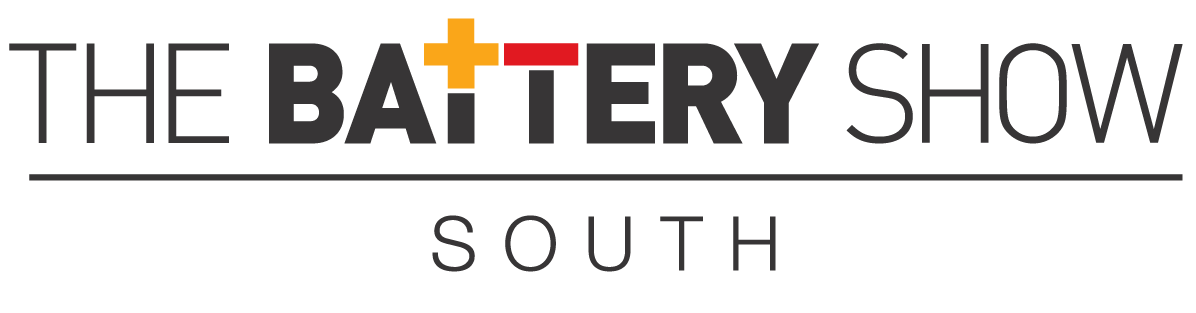
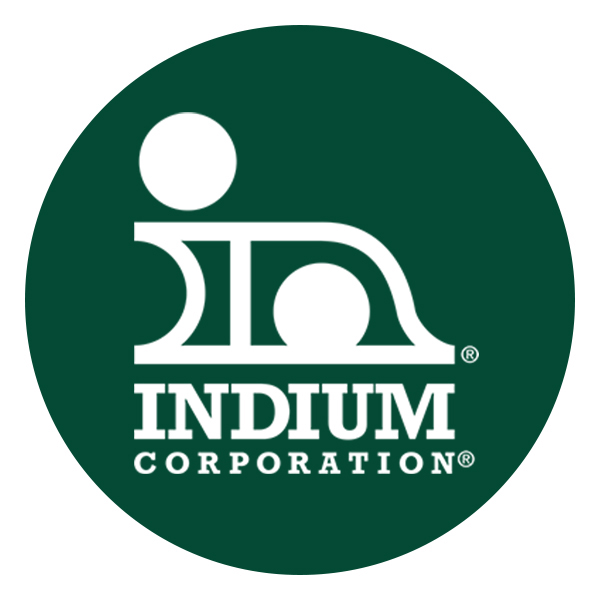
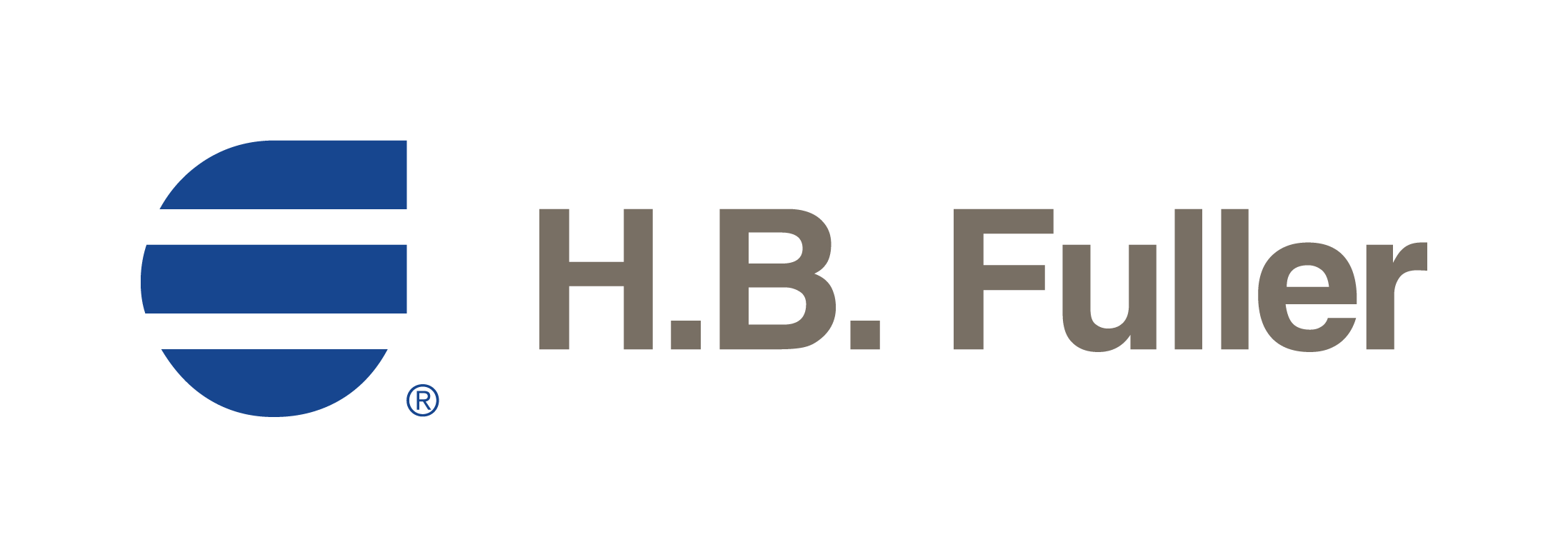