Adhesives
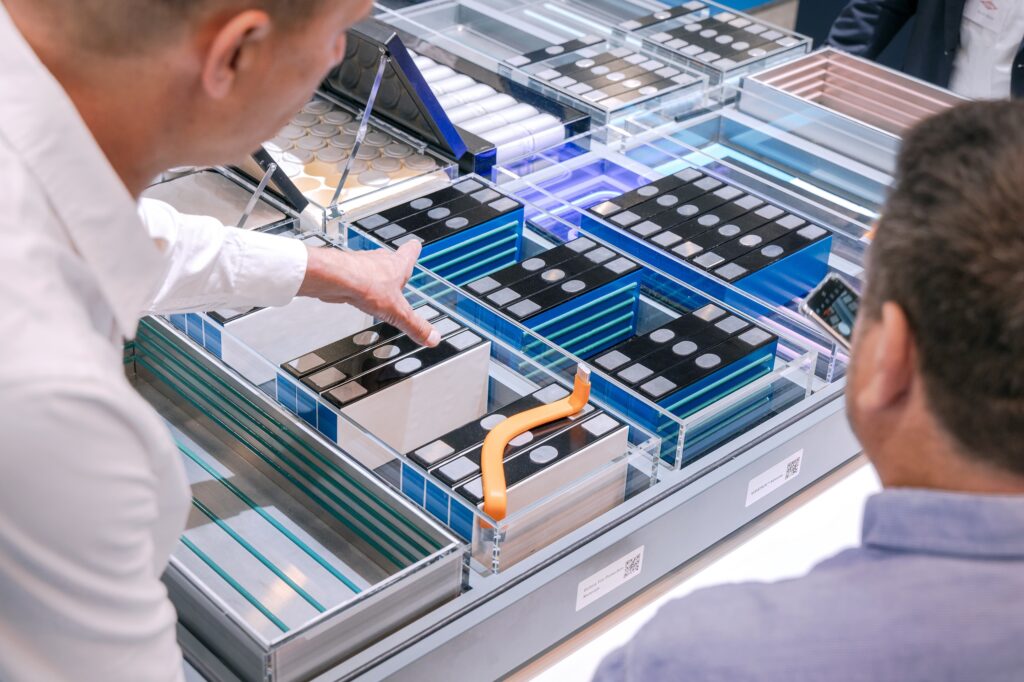
(Courtesy of Dow)
Pair bonding
The e-mobility sector is spurring fresh developments and creating new trends in adhesives technology, writes Peter Donaldson
Increasingly important in multiple applications in vehicles of all kinds, adhesives are central to the assembly of batteries, power electronics and motors used in EVs. Current development efforts are focused in areas such as ease of use in volume manufacturing as the EV industry gears up for mass production, and engineering in properties such as controlled de-bonding to support repair, reuse, repurposing and recycling, collectively known as re-X. At the same time, they have to meet stringent health & safety and environmental regulations.
That EVs are having an impact on the adhesives industry is beyond doubt. “We have seen a significant increase in adhesive content per vehicle,” says an expert from a major global chemicals company. “We are talking about thermal interface materials, reinforcement materials to increase the stiffness of the battery pack, and also integrating the cells directly into the pack. Compared with where we came from in IC-engined vehicle assembly, we have at least three or four times more adhesive content in each EV these days.”
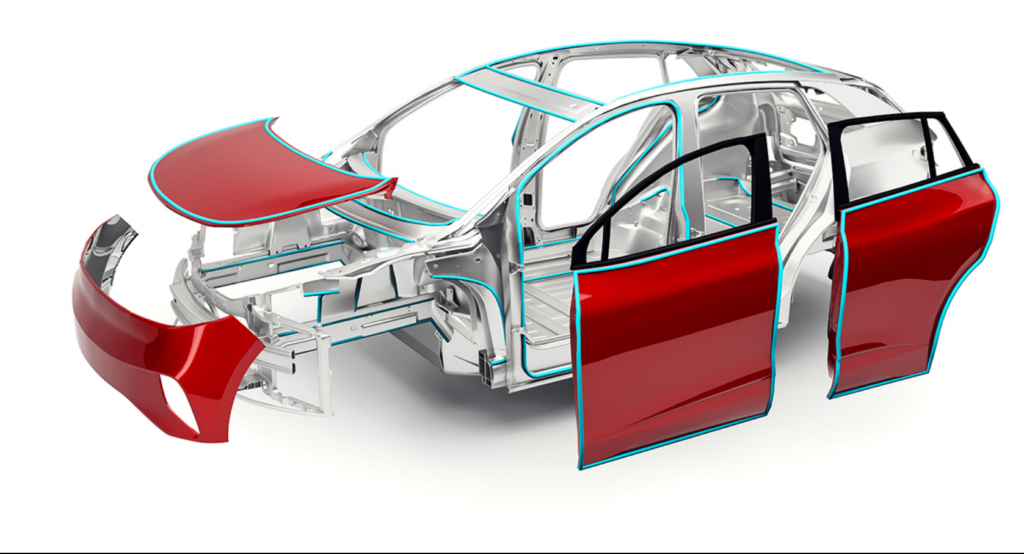
(Courtesy of Dupont)
Sticky pros and cons
Compared with alternatives such as mechanical fasteners and welding, the main advantages of adhesives are ease of use and weight reduction, according to an expert from a manufacturer and wholesaler of chemical products for the electronics industry.
There many further benefits – they also ease the joining of dissimilar materials, enable better stress distribution and support the integration of functions including corrosion protection and sealing, experts from a second major global chemical company add.
Dissimilar materials that can be successfully joined using adhesives include metals such as aluminium and steel, and various plastics and composites. In addition, they provide a more even stress distribution thanks to the continuous bond line, in contrast to the localised stress concentrations created by the use of screws, bolts, rivets or spot welds.
“That has two potential advantages,” experts at the first global chemicals company say. “One is that you can decrease the thickness of the substrates, which helps lighten the structure and, second, you get a much stiffer integrated part, contributing to better driveability, comfort and so on.”
Adhesives can also provide a bond that is often stronger than a joint created using mechanical fasteners or welding, adds an expert from a leading developer of rapid and light-curable materials, dispensing and curing equipment.
Distributing stress more evenly across bonded surfaces also reduces the risk of cracking or failure, this expert also notes, while also sealing against moisture and other environmental factors that can promote corrosion. Further, adhesives can exhibit specific properties such as flexibility, high-temperature resistance, chemical resistance and electrical conductivity to improve the performance of bonded components.
Finally, where aesthetics are important, they can create a ‘cleaner’, more pleasing appearance than mechanical fasteners or welding, which can leave visible marks or distortions on the surface of joined substrates, the expert says.
“Of course, there are also some disadvantages to using adhesives compared with mechanical fasteners or welding,” they add. “For example, adhesives can be more challenging to remove and repair, and may need longer curing times or specialised equipment. The choice between using adhesives, mechanical fasteners or welding will depend on the specific application’s requirements.”
An expert from an international provider of industrial UV adhesives, structural adhesives and conductive adhesives emphasises their versatility. “They can fit into the smallest places and bond the increasingly small electronic parts such as rear-view cameras and the smallest electronic surface mount devices; they are easy to handle and to dispense, even for complex geometries,” he says.
“In contrast to mechanical fasteners and welding, flexible adhesives offer the added benefit of being shock and vibration-resistant, and they compensate for the different thermal expansion rates of the materials in the connecting elements.”
In batteries in particular, electrically conductive adhesives often replace soldering, the expert adds, noting that high-voltage EV batteries are typically assembled from hundreds or even thousands of individual lithium-ion cells and have to meet exacting performance, durability and safety criteria. In replacing soldered connections, electrically conductive adhesives have to ensure loss-free energy transmission while also being flexible enough to accommodate differential thermal expansion.
Electric motors contain components that either cannot be joined using mechanical fasteners or welds, or work less efficiently if they are, according to an expert in the use of adhesives in motors and generators. Permanent magnets fall into the first category, as they tend to be made from brittle, sensitive materials and are often protected by coatings, so it is essential to bond them without damaging the surface, he says.
While the thin electrical steel laminations in rotors and stators can be welded, it makes it harder to minimise the eddy currents that reduce efficiency. “You try to insulate the steel layers from each other, but with joining methods such as welding you make connections between them,” he adds. “However, adhesives can provide both insulation and strong bonding.”
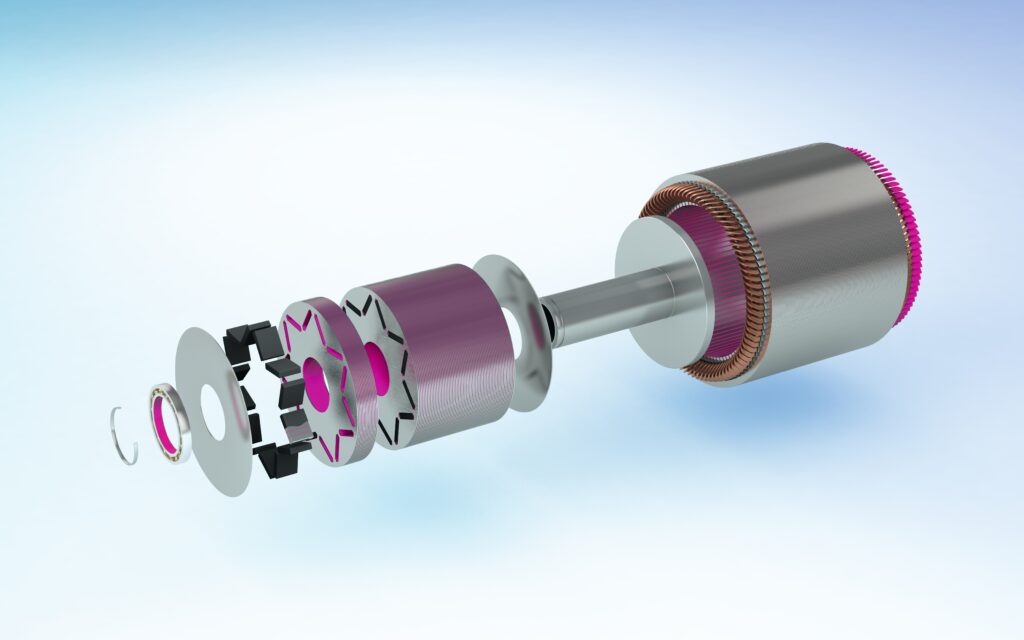
(Courtesy of Delo)
Basic chemistry
The key chemical bases for adhesives include epoxies, polyurethanes and silyl modified polymers, silicones, acrylics and acrylates. Each has their pros and cons that have to be taken into account when selecting them for particular applications and in component and bond design.
Most adhesives used in motors are epoxies because they offer good resistance against high temperatures (up to 180 ºC is typical) and against chemicals such as oils while offering high mechanical strength and robustness to impact, which make epoxy-based adhesives important in a various other applications.
They can offer a range of different material characteristics that range from flexible and soft with high elongation at breakage to hard and scratch-resistant with extremely high bond strength, according to the international UV curing and electrically conductive adhesives provider.
“Cured epoxy adhesives usually have low shrinkage and dry, non-tacky surfaces, making them suitable as one-sided protective coatings as well as for bonding,” the UV adhesives expert explains. “Some epoxies exhibit very good optical properties and diffraction indexes, making them useful for applications in precision optics and lens bonding. Epoxy adhesives also have an extremely low ionic and alkaline and halogen content, down to less than 10 ppm, making them a good choice for use in electronics and in applications where corrosion must be prevented.”
Broadly, the cons associated with most epoxies come from their high rigidity, which makes them susceptible to cracking under aggressive thermal cycling, the manufacturer of chemicals for electronics notes, and they can be slow to cure.
Polyurethanes are flexible at low temperatures and cure quickly, which helps in high-throughput manufacturing, and they bond well to many substrates including metals, plastics and composites. On the minus side, they are usually limited to a maximum operating temperature of 125 ºC, and chemical resistance is not as high as that of other adhesive types. Further, aluminium usually requires special pre-treatment for a polyurethane adhesive to stick to it.
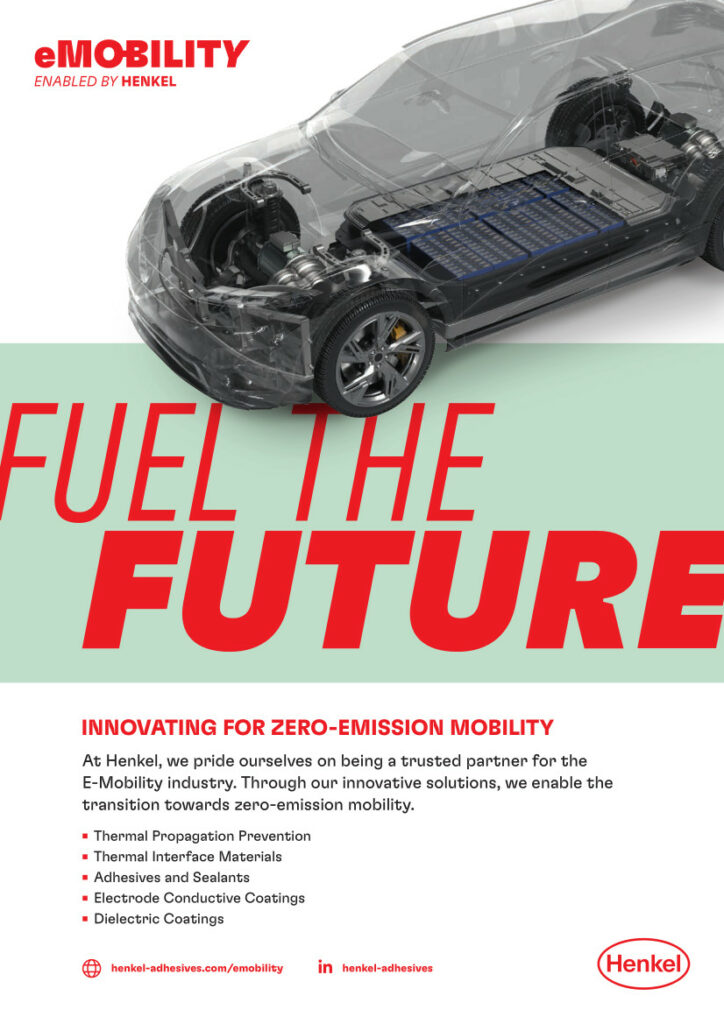
Silicones also bond well to many substrates, while also exerting low stresses on parts and providing good temperature resistance, making them highly tolerant of thermal cycling, and they are good electrical insulators. However, silicones are poor in terms of chemical resistance, and their bond strength is inferior to that of other chemistries such as epoxy, polyurethane and acrylic. They are also slow to cure and leave residues that can hinder other bonding steps and contaminate painting processes.
Silyl modified polymer adhesives are flexible, free of known hazardous materials (‘label-free’) and silicone, and provide moderate strength and excellent adhesion. Their downsides include relatively poor resistance to extremes of temperature and aggressive chemicals, the experts from our second global chemical company note.
Adhesives based on acrylics bond well to metal, glass, plastic and dissimilar substrates. They are highly resistant to chemical attack and cure quickly, speeding up assembly times, the developer of rapid and light curable adhesives says.
Acrylics are available in a wide range of viscosities, so they can easily be adapted to individual needs, and they feature a wide range of characteristics, from soft and flexible to hard, from unfilled to filled, or from mobile to gel-like, the UV adhesives provider adds. In terms of cons, they may not be able to withstand high temperatures, and their limited flexibility makes them unsuitable for applications in which there may be movement or vibration. Further, acrylics release an odour and special ventilation is required to get rid of it.
The cure
Curing time is a very important attribute of an adhesive, particularly in highly automated mass-production environments. As a rule of thumb, rapid curing has to be traded off against structural properties, according to our e-motor adhesive specialist.
Epoxies, for example, generally consist of a resin and a hardener that come pre-mixed in single-component (1K) adhesives or are supplied separately and mixed immediately before application in two-component (2K) formulations. The 2K adhesives usually cure at room temperature, with the process triggered by mixing the components, while curing their 1K counterparts normally requires them to be heated to a trigger temperature.
However, for products and manufacturing concepts requiring high-speed curing to accommodate large production volumes, UV adhesives are typically used because they cure in seconds. They can be either epoxy or acrylic formulations, and contain photo-initiator molecules that create reactive species such as free radicals (acrylates), cations or anions (epoxies) when exposed to visible or ultraviolet (UV) light.
UV light sources include conventional mercury vapour lamps and, increasingly, LED lights operating in a different part of the UV spectrum, usually at wavelengths of 365 or 405 nm. Modern adhesives can also contain photo-initiators to react to both, says the international UV adhesives provider, which has developed new epoxide resin adhesives that do this.
Curing is also affected by the substrates that the adhesive is being asked to bond, and there are multi-substrate adhesives as well as more specialised ones with different curing parameters, the company’s expert says.
“Substrates that are not permeable to light should be bonded with adhesives that cure with heat,” he says. “There are also plastic substrates that are permeable to light but not to UV light, so here a light curing adhesive that cures at wavelengths of 405 nm or longer, should be the choice.”
Application areas
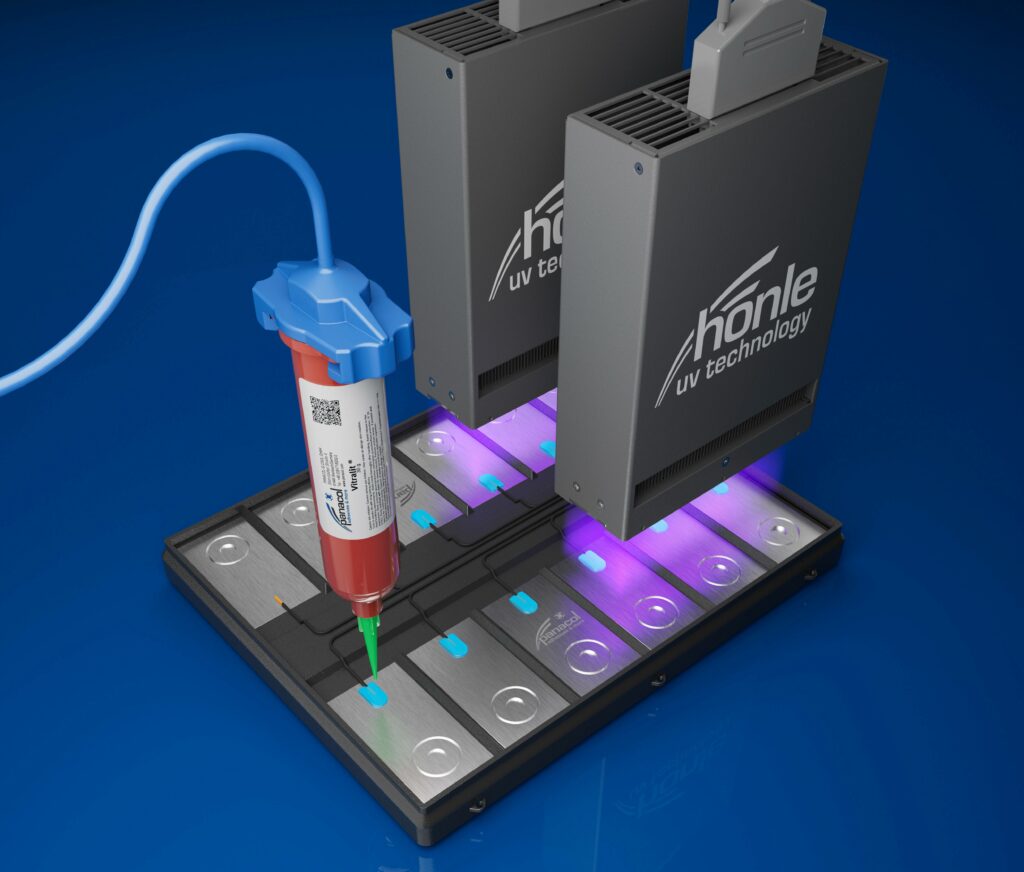
(Courtesy of Panacol)
The demands placed on adhesives used in EVs differ between the main application areas, namely the body/chassis, battery, powertrain, electronics and the cabin interior, although there are also commonalities.
In structural applications, strength of adhesion is naturally prioritised. The focus here is on structural and crash-resistant adhesives to optimise body stiffness, passenger safety and lightweight construction, and with EVs there is even more emphasis on light weight to compensate for the heavy battery, say the experts from the second global chemicals company.
In the battery, while this structural strength is important, there is an emphasis on secondary features such as flame retardancy and thermal conductivity, according to the manufacturer of chemicals for electronics. The same is true with most electrical components, where electrically conductive adhesives are used for cold soldering, the company’s expert notes.
Thermal management is a key factor in battery, power conversion and electronics applications, with thermally conductive adhesives providing a critical connection between the cells and the cooling system, for example, to transfer heat quickly and efficiently, to optimise performance as well as prevent thermal runaway.
Here, preventing unwanted thermal propagation between cells is also critical, the experts from the second global chemicals company explain. For electric drive system applications, thermal potting and gasketing is important, they add.
Inside batteries, electrically conductive adhesives are used in cell contact systems. These adhesives, says the expert from the provider of industrial UV cured adhesives, must be specially formulated to ensure loss-free energy transmission while remaining flexible enough to compensate for the different thermal expansion rates of the materials used in the connecting elements.
One of the most important developments affecting battery assembly is the need for both thermal interface materials and thermally conductive adhesives, notes an expert from the first global chemicals company. “These are clearly new within the battery space, and the latest trends are around foams and potting,” he says. “This is coming into play with cylindrical cells, and we also have a couple of applications around prismatics that involve potting materials.”
Challenges in this area centre on weight and cost, he explains. “Our customers are moving towards cost parity with IC-engined vehicles, so the lower the cost of the overall battery pack the better, and light weight is a key need. However, they also want thermal insulation to avoid heat going from one cell to another, they want electrical insulation to avoid short-circuits and then they want structural integrity for the module or the pack. So they need to make compromises. If you go to super-lightweight with foams then your structural integrity is going to be compromised, and vice versa.”
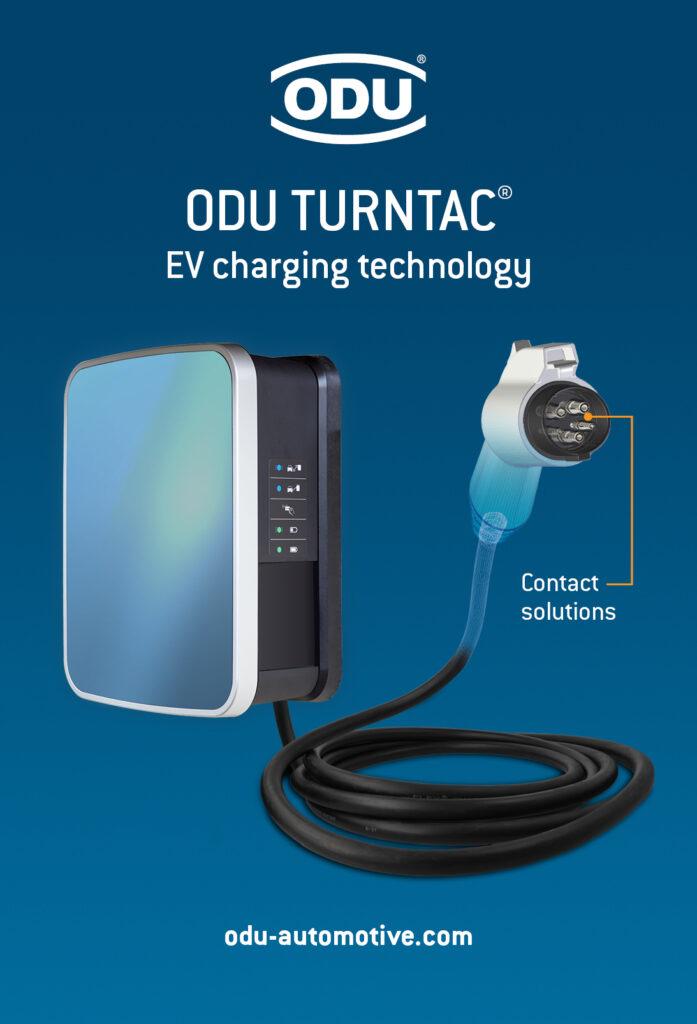
Adhesives used in powertrains and batteries also need to stand up to oils in transmissions, for example, and the harsh chemistries inside the batteries, while adhesives used in electronics need appreciable vibration and moisture protection to prevent components from shifting and shorting, the expert from the developer of rapid and light curable adhesives explains.
For electronic parts, adhesives must also fulfil other criteria such as low ion content and electrical or thermal conductivity. To protect sensitive components, adhesives are applied to PCBs as ‘glob tops’ – coatings or underfills for chips – says the UV curable and conductive adhesives expert.
In mini cameras for reversing etc, they are used for sealing, holding and joining lenses. Specially formulated photoconducting and highly transparent adhesives are the best choice for securing glass lenses or plastic camera housing parts, the expert adds.
“So as not to impair the quality of the optics, these special cements must be optically clear adhesives with low shrinkage to prevent stress on the glass lenses,” he says. “Low shrinkage is often achieved by the addition of nano-sized filler materials. Because the optical components must be secured quickly after their precision adjustment, rapidly curing UV adhesives are commonly used here.”
Cabin interior adhesives are used for many things, including bonding interior lighting, sealing displays and securing the latest in-mould electronics. Adhesives used in the interior must cure completely, with little to no outgassing to avoid any chemical odour and/or deposition of unreacted components.
When used on the vehicle exterior, adhesives have to tolerate extreme environmental conditions such as wide temperature differences, weather, pollution and UV exposure, according to the light curable adhesives developer. In some exterior applications, while strong bonds are required, there is no need to use the strongest adhesives to form them.
For example, although the windscreen is heavy it is also large, as is the area to be bonded. “With adhesives, mostly you have tiny areas with high strength requirements, but for the windscreen you don’t have those requirements because the area of the bond is so big,” the expert in e-motor adhesives says. “You need flexibility of course, and some resistance, but it is mostly just resistance to sun, rain and UV. It’s not like you need the strength of something like an epoxy, as you would for an electric motor.”
Multiple properties
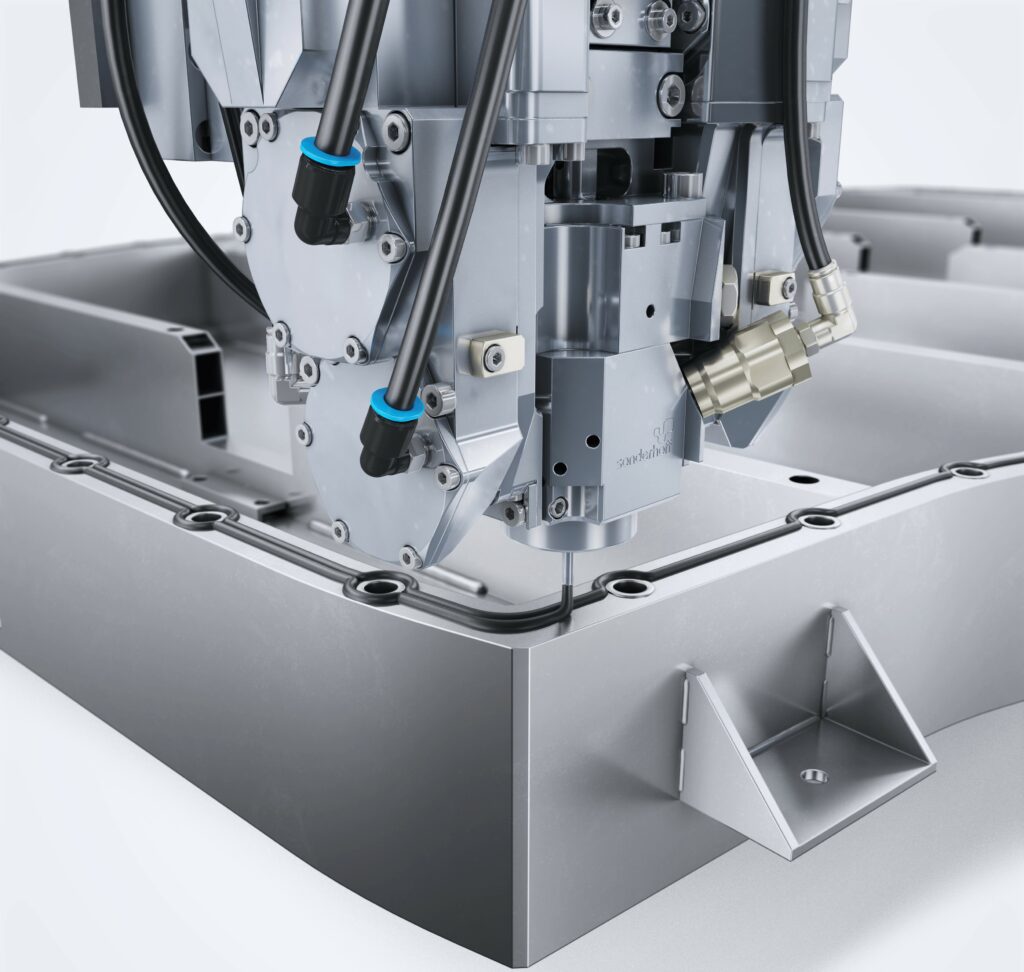
(Courtesy of Henkel)
Increasingly, adhesives have to provide a range of important properties such as thermal or electrical conductivity or insulation, sealing, compatibility with safety standards such as UL 94 for flammability and more, in addition to forming strong bonds.
Further, demands for ease of processing in high-volume production environments are added to the more complex performance requirements. For example, where room temperature curing is required it is not possible to use 1K heat-curing products, and new raw materials are sometimes required.
Developing adhesives with combinations of properties, some of which conflict, is a challenge and involves compromises. “Secondary features require powder fillers in relatively high amounts, which subsequently increases viscosity and lower adhesive strength,” an expert from the manufacturer of chemicals for electronics says. “It can be a challenge to balance viscosity and adhesive strength with the performance of secondary features.”
Striking this balance is essential if a new adhesive is going to be commercially successful. “For example, one component might provide superior electrical insulation, but it might also increase the adhesive’s viscosity to a point that makes it impractical to use or dispense,” the expert from the rapid and light-curable materials developer says. “The viscosity then needs to be adjusted without diluting the efficiency of the electronic insulating material to a point where it will not provide any benefit.”
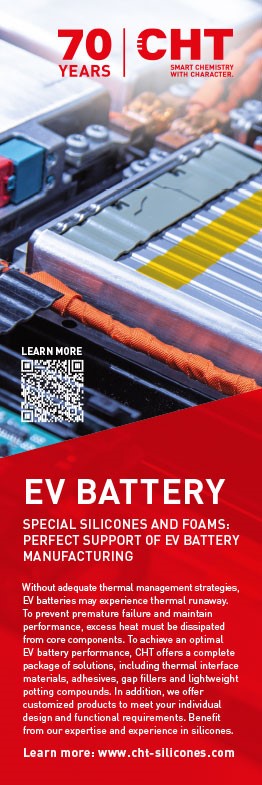
The specialist in e-motor adhesives notes that the challenge can be different for each property. The first major task for the r&d team is to check which raw materials are available, and then look into the chemistry to find fillers that can be combined with them.
“With thermal conductivity, for example, you need thermally conductive particles to use in a filler, which can bring its own challenges, depending on the adhesive system,” he says. “If you have, for example, a light-curing system and you add filler for thermal conductivity it could block the light.
“The filler could also be heavy, undergo sedimentation and make the product unstable. So you have to do a lot of testing to check that the properties are right – making a product stable is a major challenge.”
Unmodified epoxy adhesives have low thermal conductivity, which is usually increased by using fillers based on ceramic or metallic particles, and although metallic fillers can be used they are also electrically conductive, a property that rules them out for many applications.
“Ideally, thermally conductive fillers should have a high thermal conductivity, low thermal expansion, low abrasiveness and good chemical resistance,” says the expert from the industrial UV curing and electrically conductive adhesives supplier. “The development of thermally conductive adhesives focuses mainly on the effects of different fillers.
“The filler material also affects its flow behaviour – an important point to bear in mind, as the right viscosity is important in later application. While too low a viscosity can impair edge stability or cause the adhesive to run, excessive viscosity often leads to incorrect application of the material, for example because a rough surface is not fully wetted to yield a positive fit. Too high a viscosity can also cause problems in dosing.”
The story with electrically conductive adhesives is similar, the expert adds. They are usually thermally curing epoxies augmented with metallic fillers such as silver.
“Grade, shape, grain size and grain distribution of the filling material are critical for optimising adhesive conductivity, and silver flakes are especially effective in creating efficient energy flow and therefore high conductivity,” he says. “As a general rule, the higher the degree of filling the better the conductivity, but that leads to high costs for silver epoxies.”
Conventional fillers often bring problems in dispensing though. As well as making the adhesive too viscous and prone to clogging, they tend to result in bubbling or bleeding from delicate bead lines.
“With an appropriate selection of silver flakes the flow behaviour of conductive adhesives can now be crucially improved,” the expert adds. “Thanks to innovative silver fillers, newly developed conductive adhesives are now very well suited for jetting and screen printing, without clogging dispenser nozzles.”
The chemical engineering task therefore involves developing not only the adhesives but also the other components. “We develop special polymers, which you include in the formulation, and we develop special filler packages and special curing accelerators,” says an expert from the first global chemicals company. “The development of the component is as important as developing the formulation itself, and the cost has to be attractive to the customer.”
Another expert from the company outlines some of the challenges with thermal interface materials. In addition to their main heat transfer function, customers also insist that they stay where they are put, and if battery cells are to be placed on the TIM during assembly the cells have to go into position quickly, so the required pressing force is very important, he says.
Similarly, if the ability to pull out cells to repair the pack is required, the pull-out force is also important. At the same time, they must not sag in any way and they must not burn. “This goes on and on in order to come to a final specification,” the expert says.
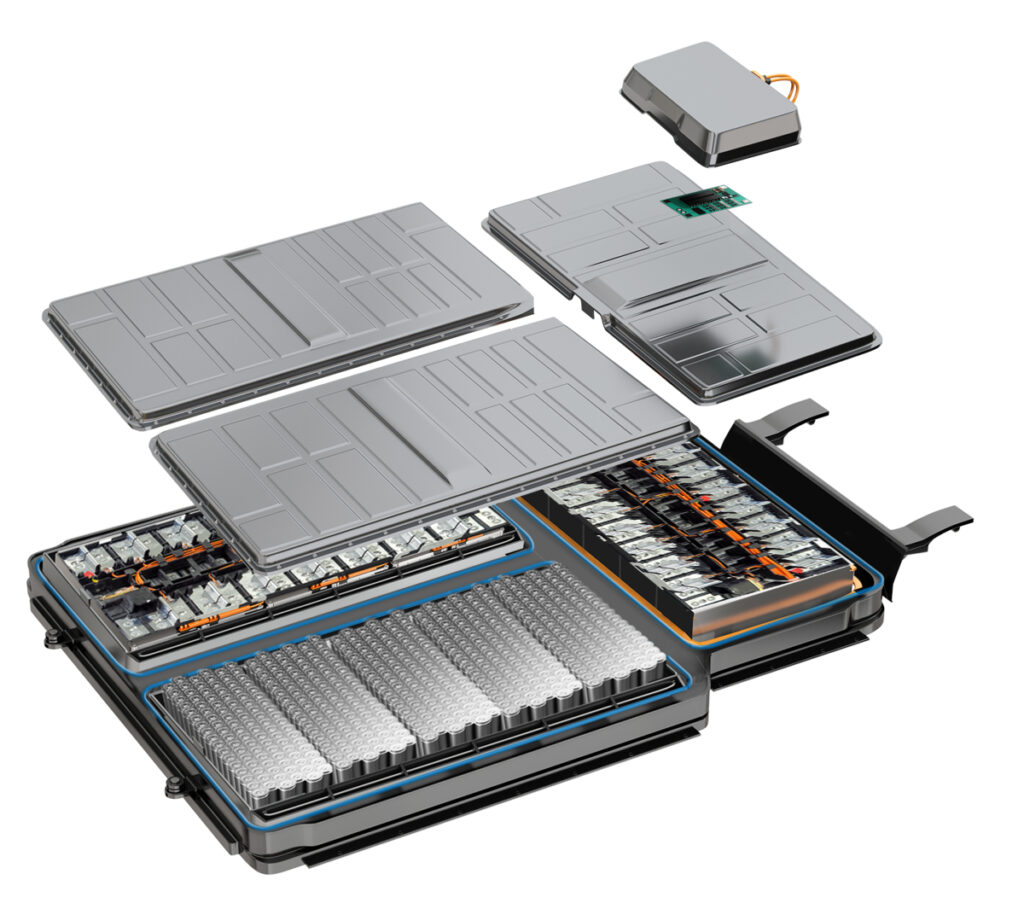
(Courtesy of Dymax)
Unsticking on demand
Among the many additional demands on adhesives is the need for de-bonding on demand to support re-X requirements, while maintaining their other qualities. These are fundamentally conflicting requirements, and it is generally understood that adhesive curing is not something that can be easily reversed on demand, but there are methods that can be applied.
Essentially, the de-bonding process must be made as easy as possible without having to use harsh or costly methods such as chemical soaking, embrittlement using cold temperatures, or extreme heat. The adhesive’s strength also has to be balanced against ease of de-bonding.
“It is essential to develop a formulation with an appreciable bond strength while offering the ability to remove the cured adhesive by hand at room temperature or with low localised heat,” the expert from the developer of rapid and light-curable materials says.
“The challenge is to provide the high strength, mechanical performance and adhesion requirements of an adhesive in terms of overall reliability, while having a trigger for debonding purposes incorporated,” an expert from the second global chemicals company adds. “This trigger – whether it responds to, for example, temperature, soaking, an electric current, a magnetic field, or radiation – has to be stable and inactive over the vehicle’s service life until it is needed, and must not be activated by chance or environmental conditions.”
They emphasise that the trigger must not influence the adhesive’s performance, but must activate very reliably to enable a re-X process. “The strict separation of a typical adhesive’s function in service and the requirement for de-bonding in one product needs to be controlled,” the experts from the second major chemical company add.
As noted, there are several possible approaches to de-bonding, and the second global chemicals company is pursuing five, four of which an expert from the company was willing to discuss briefly.
The first is an adhesive that degrades when it reaches a given temperature, or uses some other principle that causes a weakening of the bond line through temperature. Given that lithium-ion cells are generally stable up to 60 or 70 ºC and enter thermal runaway at around 120-130 ºC, there is quite a narrow window in which the de-bonding trigger can safely operate, he says.
The second is electrical, and involves polymers that change the shape of their crystalline structure when a voltage is applied. Again, it is critical to make sure de-bonding can’t be triggered in normal operation. “The number one priority is eliminating the risk of short-circuits,” the expert says.
The third type is mechanical de-bonding, which could involve a simple purpose-designed tool such as a wire saw or an adhesive designed to unstick in response to a calibrated peel force, for example.
Chemical de-bonding is the fourth option under consideration. This could involve an adhesive developed to dissolve easily in a solvent that is not present in the battery pack, whether in the electrolyte or any coolants or refrigerants. The solvent would soak into the bulk adhesive or the bond line to weaken it.
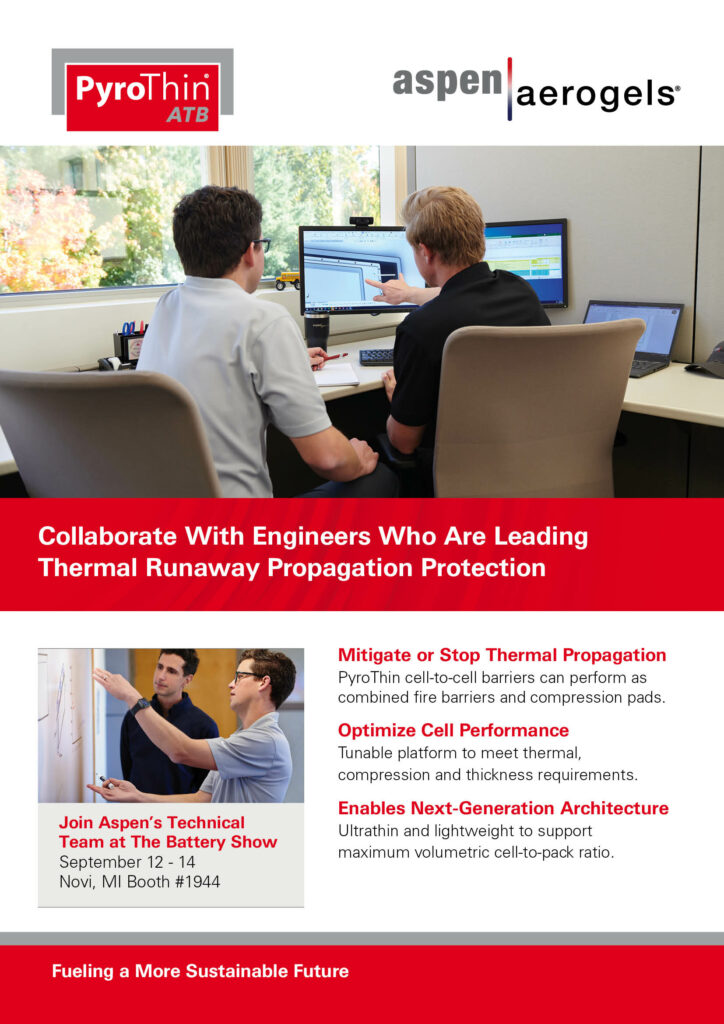
In all these cases, he argues, the entire battery pack will have to be designed with disassembly in mind, with injection points for solvents or contact points for applying a voltage for example.
An expert from the first global chemicals company, which is also working on de-bonding solutions, stresses the need for an economical basis for what is inevitably a time-consuming technical process. “I believe there is an economical model within battery manufacturing if we can increase the yield,” he says. “If there’s a defect in the manufacturing process and you can pull out the affected cells and replace them, then it makes a lot of sense.”
In electronics, the ability to rework and repair individual modules on PCBs is increasingly important, according to the UV curing adhesives specialist, which supplies several underfill and edge-bonding adhesives that do this.
“For easy identification, the removable adhesives fluoresce yellow under UV light, despite their black colouration,” he says. “The adhesive can then be easily removed without damaging the bonded components when the cured adhesive receives thermal exposure above its glass transition temperature of 150 ºC. The adhesive softens, and can be manually scraped away using a small spatula or similar instrument.”
In support of re-X approaches, de-bonding also feeds into much-needed improvements in overall sustainability for EVs by reducing waste and the need for virgin raw materials. Other approaches are focused on reducing energy consumption in manufacturing through, for example, the use of 2K adhesives that don’t need heat for curing (UV LED curing lamps help here), and producing the adhesives on machines powered from green energy sources, while others centre on more sustainable feedstocks.
Such feedstocks can include recycled material or biologically based materials including natural oils, starches, and proteins, which have a lower environmental impact than petroleum-based adhesives and can decompose more quickly. In using biologically based adhesives though, an expert from the first global chemical company cautions that it is important to avoid competing with foodstuffs.
Other desirable characteristics for sustainability include the recyclability of the adhesives themselves, and automated dispensing systems with high placement accuracy to reduce the amount of adhesive needed.
Like the e-mobility industry itself, the adhesives that enable them to perform as required are undergoing a rapid and profound evolution, challenging the chemicals industry, Tier 1 suppliers and OEMs to work together from the earliest stages of product development.
Acknowledgements
The author would like to thank Christophe Van Herreweghe and Andreas Lutz at DuPont, Rainer Kohlstrung and Pascal Moch at Henkel, Roman Schilcher at Delo, and He-Qun Zhu at Panacol-Elosol GmbH for their help with researching this article.
Some suppliers of battery case materials
France
Germany
Bdtronic
CHT
Delo
Henkel
Panacol
Tesa Tape
+49 7934 104 0
+49 7071 154 0
+49 8193 99000
+49 211 797 0
+49 6171 62020
+49 40 888 99 0
Switzerland
UK
USA
3M
Atlas Copco
Avery Dennison
Dow
DuPont
Dymax
HB Fuller
Hunstman
ITW
MG Chemicals
Nordson Adhesive Systems
+1 888 364 3577
+1 651 290 0000
+1 440 534 6000
+1 989 636 1000
+1 302 774 1000
+1 860 482 1010
+1 651 236 5900
+1 888 564 9318
+1 978 774 0516
+1 800 340 0772
+1 440 892 1580
ONLINE PARTNERS
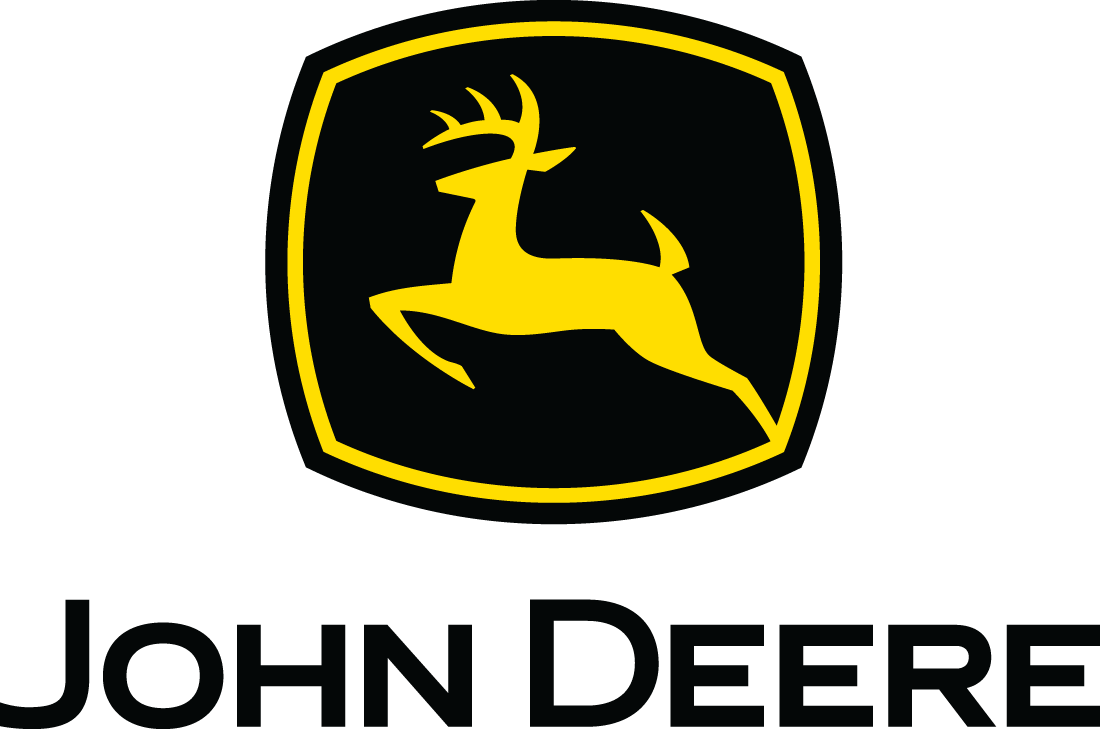
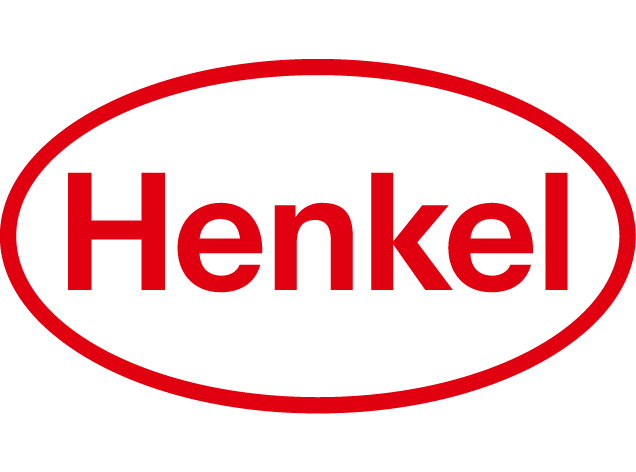
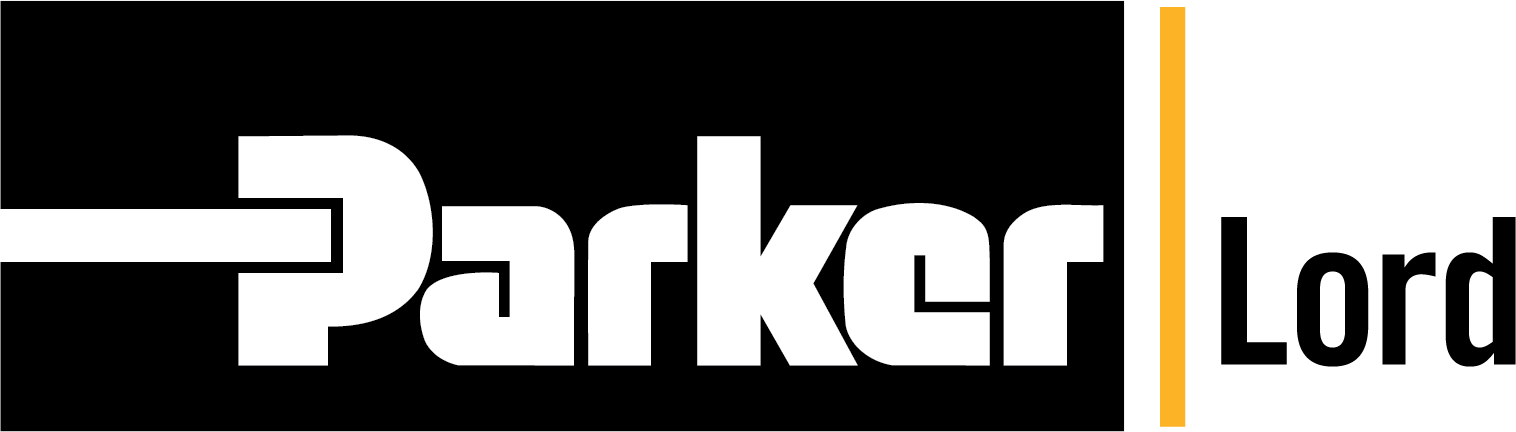
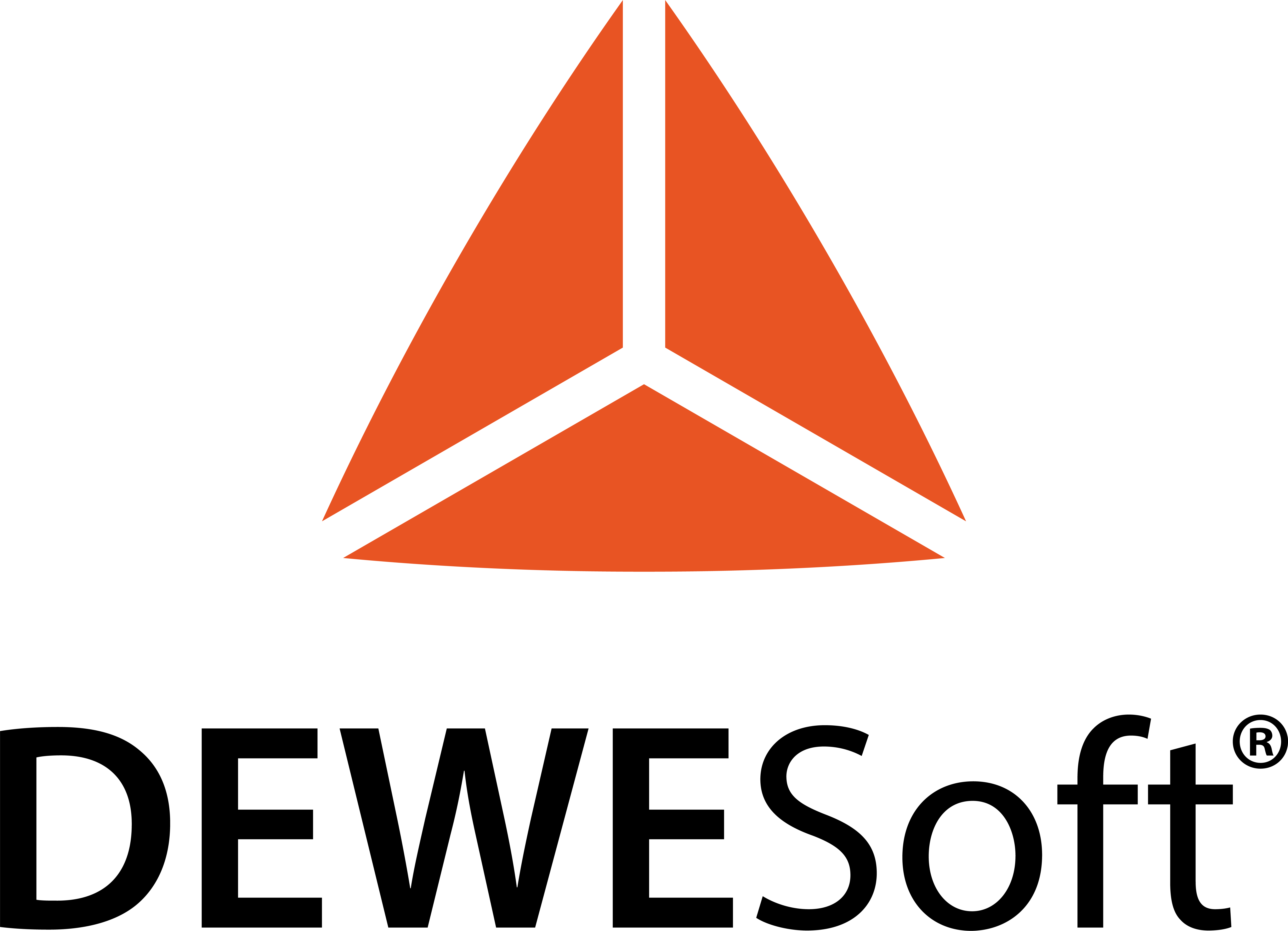
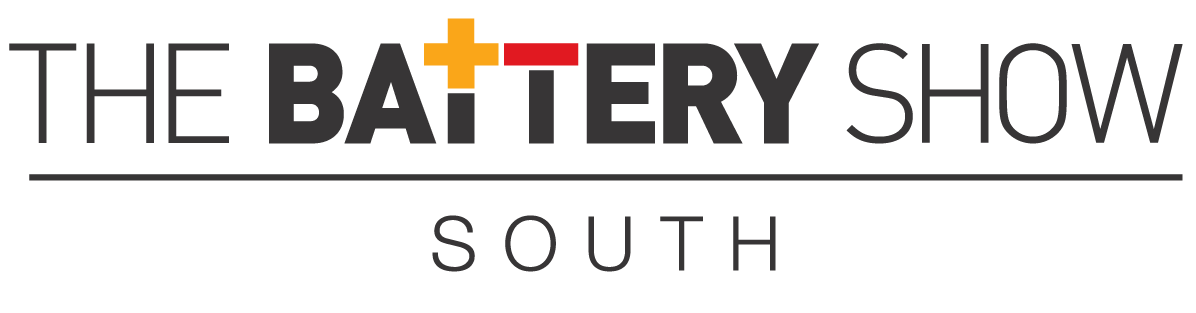
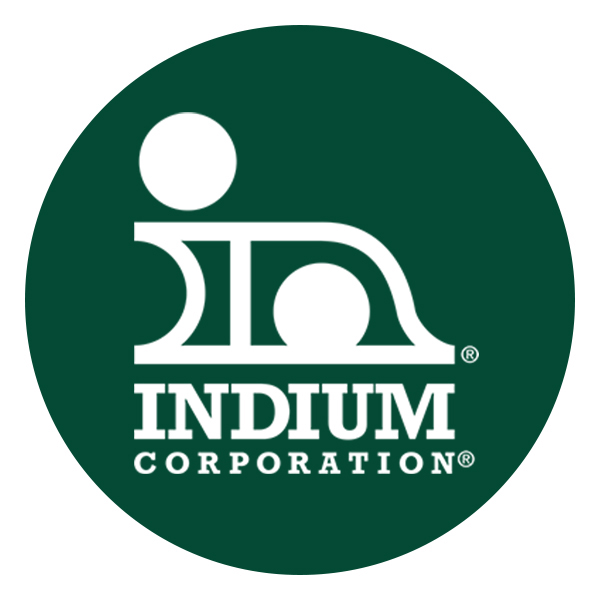
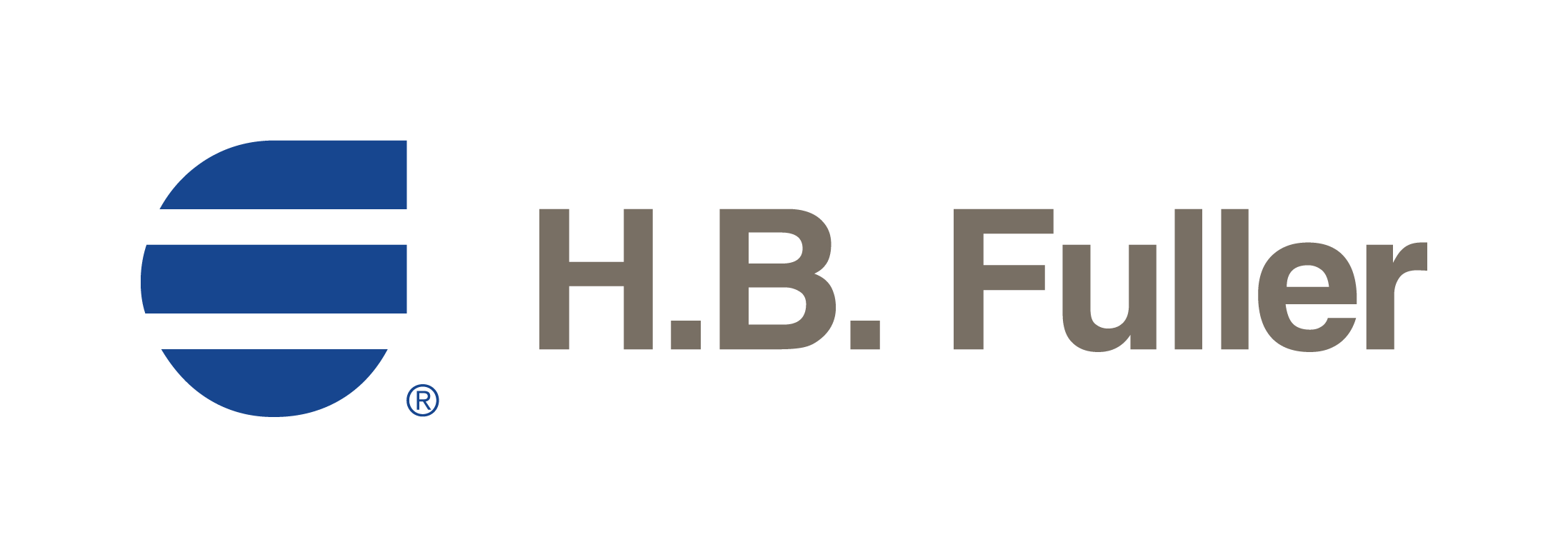