Lithium-sulphur batteries
Shuttle systems
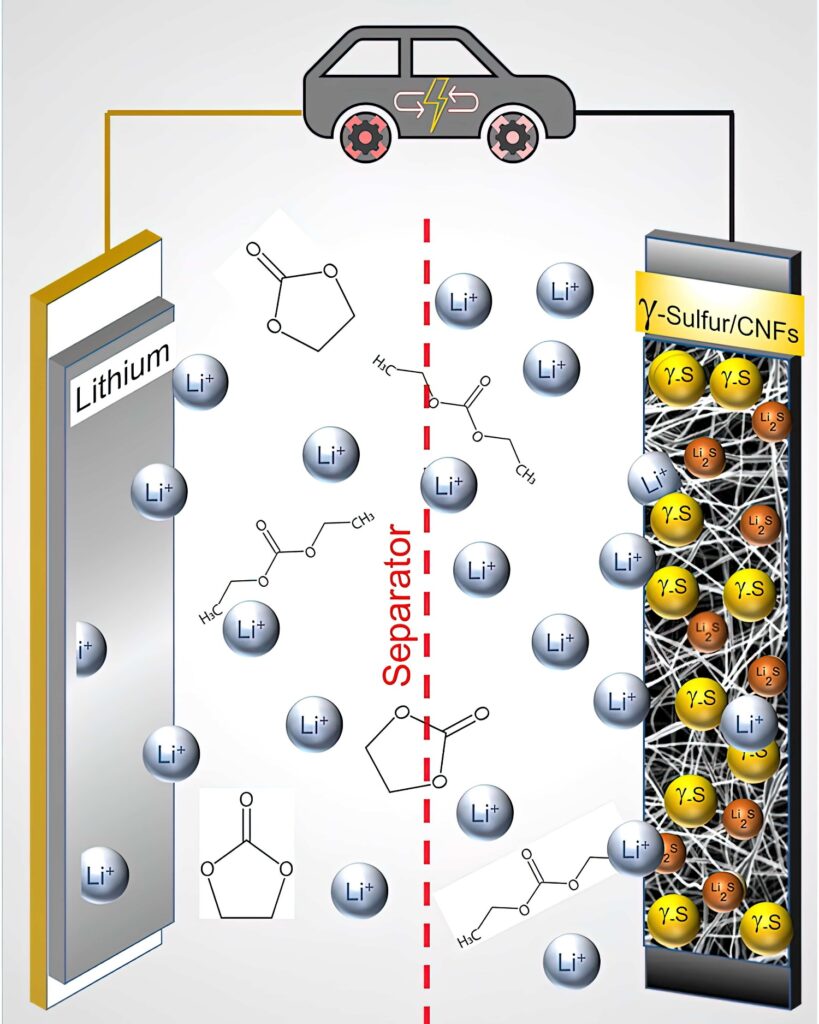
(Courtesy of Drexel University)
Lithium-sulphur batteries suffer from short lifetimes from the polysulphide shuttle effect. Nick Flaherty reports on attempts to reduce this
The most significant advantage that lithium-sulphur (LiS) batteries offer over rival battery technologies is their substantially higher energy density per unit weight. LiS cells with lithium metal anodes have a theoretical energy density of 2700 Wh/kg, dramatically higher than lithium-ion cells that with silicon anodes are reaching 470 Wh/kg.
This is naturally of interest to vehicle makers to reduce the weight of battery packs while boosting the range. It also avoids the use of nickel and cobalt, which have jumped in price and come from unsustainable sources.
LiS cells in comparison can use low-cost sulphur and carbon materials and still tap into the lithium supply chain supplying the industry, producing cells with the same energy density as lithium-ion for half the cost.
They also offer major safety benefits over other battery types thanks to their operating mechanism. The conversion reaction, which forms new materials during charge and discharge, eliminates the need to host lithium ions in materials, and reduces the risk of catastrophic failure of batteries. Alongside that, the highly reactive lithium metal anode is passivated with sulphide materials during operation, further reducing the risk of a dangerous failure.
As the cells still use lithium, thermal runaway remains a possibility, but research has shown that the magnitude of this failure is far lower than with lithium-ion cells.
LiS technology is also a prime candidate for solid-state batteries. A protective solid-state layer at the anode mitigates the risk of short-circuiting of cells, and the conversion mechanism also enables LiS cells to be stored safely for extended durations and shipped in a fully discharged state, enabling transportation via air freight as the cell is not unstable at low discharge states, unlike lithium-ion batteries.
The high energy density means the technology is also of vital interest to electric aircraft designers. Studies by NASA for example see LiS cells as a candidate for large single-aisle passenger aircraft that can carry 150 people.
While the energy density reduces as a result of the practicalities of producing a battery cell, prototype LiS technology has already been demonstrated at 470 Wh/kg, the same as the leading edge lithium-ion cells. Projects around the world are finding ingenious ways to boost the capacity and the performance of LiS cells.
Development projects
In an LiS cell, elemental sulphur (S8) is converted to Li2S, with each sulphur atom reacting with two lithium ions during the conversion reaction. In comparison, traditional lithium-ion battery cathodes accommodate only an average of 0.5-0.7 lithium ions per host atom.
Most LiS batteries use lithium metal anodes and a cheaper plating/stripping chemistry compared to the graphite anodes and intercalation chemistry of traditional lithium-ion batteries. Aside from these differences, LiS batteries’ other components (current collectors, electrolyte, separator) are similar to those used in traditional lithium-ion batteries, although their chemistries are often tuned to interact more optimally with sulphur.
A pure sulphur cathode does not conduct electricity, so carbon is typically added in relatively high quantities to improve the performance, and there is a focus on different types of carbon used. This varies from highly processed nanotube carbon for high performance to carbon generated from waste fruit or plastic for low cost.
One of the main challenges of LiS cells is the lifetime. A phenomenon called the polysulphide shuttle effect causes a loss of active sulphur from the cathode. Polysulphides formed during cell operation shuttle back and forth between the electrodes, reducing the lifetime of the cell to less than 100 cycles.
While the simplified chemical conversion during discharge is 16 Li + 8 S -> 8 Li2S, the actual conversion is more complex, and includes intermediate conversions to various polysulphides (Li2S8, Li2S6 and so on). As the cell cycles, some amount of lithium and sulphur are lost to polysulphide molecules that fail to complete the conversion, eventually causing the battery to fail.
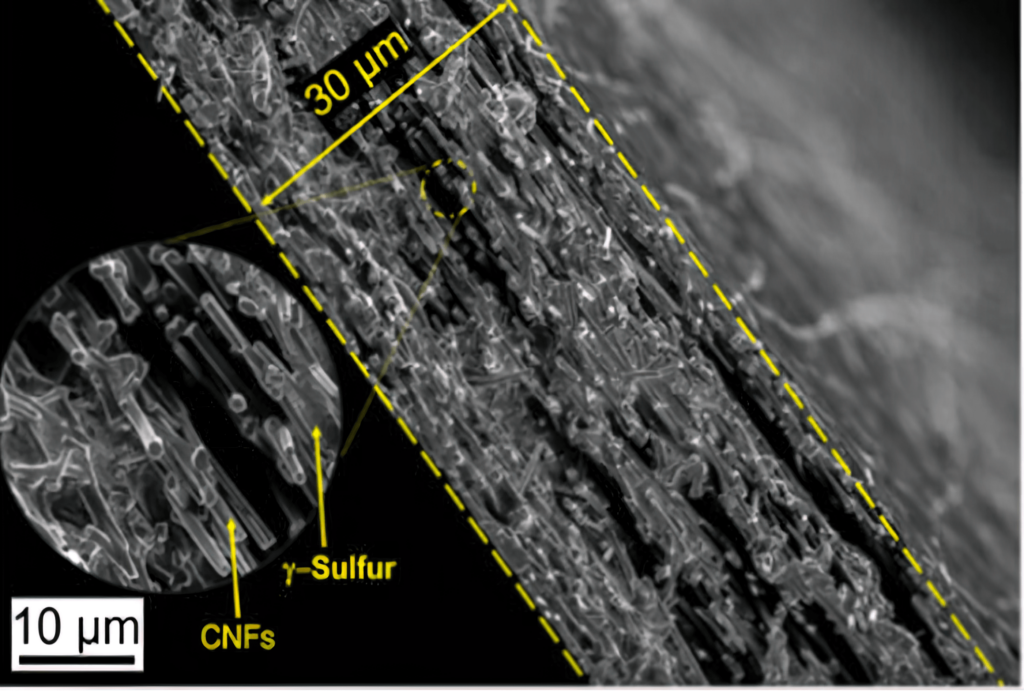
(Courtesy of Drexel University)
Various attempts have been made to mitigate the polysulphide shuttle effect. Most efforts focus on adding separators or cathode coatings that keep the polysulphides localised on or near the cathode. Using a solid layer to protect the lithium anode and adding materials to trap polysulphides and reduce the shuttle effect are among the most promising ongoing research areas.
The sulphur used at the cathode also undergoes significant expansion as it reacts during discharge. This can result in fracturing of the cathode and a loss of electrical connectivity in it, again reducing the number of charge-discharge cycles. An expansion-tolerant electrode avoids these problems and increases the amount of sulphur in the cathode, giving a performance closer to the theoretical maximum.
Further challenges comes from the low solubility of polysulphides in the electrolyte and the rate at which the polysulphide products react during cell discharge. To overcome these issues, materials that increase the rate of the reactions can be incorporated into the cathode to promote improved performance, while extensive research is underway to improve the electrolytes used.
The challenge in the development of the technology comes from delivering enough power from the cell to take advantage of the energy density.
Historically, most LiS research has focused on developing new materials to improve the sulphur cathode. However, in recent years it has been recognised that developments are needed across the cell to improve the performance of LiS batteries.
The Faraday Institution’s Lithium-Sulphur Technology Accelerator (LiSTAR) project, led by University College London with six other universities and seven leading industrial partners, is researching the development of LiS batteries.
The project has four work packages focused on improving the critical areas to accelerate the commercialisation of these devices.
The first is to design cathodes that maximise the sulphur content and accommodate swelling during operation while including catalytic components to improve the performance of cells. The second is to develop safer electrolytes and incorporate new materials that can improve the efficiency of the battery and mitigate the polysulphide shuttling effect.
Advanced computational techniques are also being developed in the third work package to speed up the design of the materials and understand the key degradation pathways in LiS cells. The fourth work package is concerned with the design of the lithium metal anode in commercial cell formats.
The project sees the possibility of producing a cell with an energy density of 600 Wh/kg and a 500-cycle life at a charging rate of 1 C in the near future.
Elsewhere, researchers at Drexel University in the US have developed a way to stabilise a rare form of sulphur in a cathode. This would allow it to be used in the carbonate electrolyte used in commercial lithium-ion batteries. Previous attempts to use a sulphur cathode in a battery with a carbonate electrolyte solution resulted in nearly immediate shutdown and a complete failure of the battery after only one cycle.
The researchers say this could provide three times the capacity of lithium-ion batteries and last more than 4000 recharges – the equivalent of 10 years of use.
“Sulphur has been highly desirable for use in batteries for a number of years, because it is abundant and can be collected in a way that is safe and environmentally friendly,” says Dr Vibha Kalra, a professor in Drexel’s Department of Chemical and Biological Engineering, who led the research. “And as we have now demonstrated, it also has the potential to improve the performance of batteries in EVs and mobile devices in a commercially viable way.
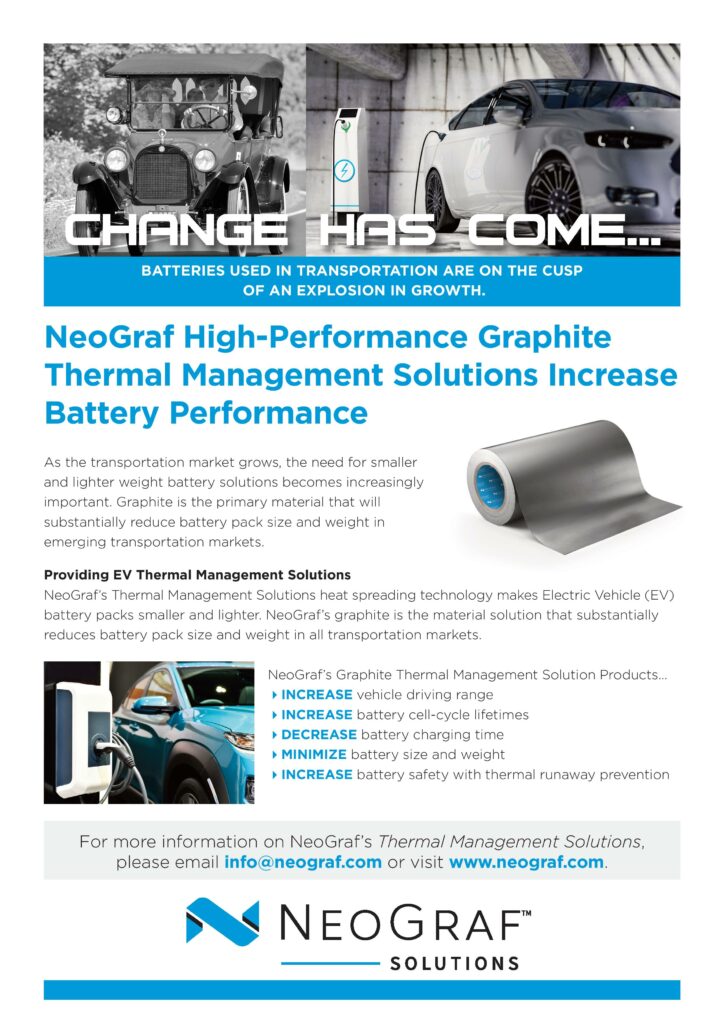
“Most LiS systems have adopted ether electrolytes to avoid the adverse reactions with carbonate,” he adds. “Then, over the years, the researchers deep-dived into enhancing performances in ether-based sulphur batteries by mitigating polysulphide shuttle. But the field completely overlooked the fact that the ether electrolyte itself is a problem.
“In our work, the primary objective was to replace the ether with carbonate, but in doing so we also eliminated the polysulphides. That meant no shuttling, so the battery could perform exceptionally well through thousands of cycles.”
The team had previously developed a cathode using carbon nanofibres that slowed the shuttle effect in ether-based cells by reducing the movement of intermediate polysulphides. But to improve the commercial path of the cathodes, the group realised it needed to make them function with a commercially viable carbonate electrolyte.
“Having a cathode that works with the carbonate electrolyte that they are already using is the path of least resistance for commercial manufacturers,” says Dr Kalra. “So rather than pushing for industry adoption of a new electrolyte, our goal was to make a cathode that could work in the pre-existing lithium-ion electrolyte system.”
A new form of sulphur
The team tried to confine the sulphur in the carbon nanofibre cathode substrate using a vapour deposition technique. While this process did not succeed in embedding the sulphur within the nanofibre mesh, the sulphur crystallised in an unexpected way, forming a slight variation of it called monoclinic gamma-phase sulphur. This chemical phase of sulphur, which is not reactive with the carbonate electrolyte, had previously only been created at high temperatures in labs, and has only been observed in nature in the extreme environment of oil wells.
“As we began the test, it started running beautifully – something we did not expect,” says Dr Kalra. “In fact, we tested it over and over again – more than 100 times – to ensure we were really seeing what we thought we were seeing. The sulphur cathode, which we suspected would cause the reaction to grind to a halt, actually performed amazingly well, and it did so again and again without causing shuttling.”
Rahul Pai, a doctoral student in the department and co-author of the research, says, “At first it was hard to believe that this was what we were detecting, because in all previous research monoclinic sulphur has been unstable under 95 C.
“In the past century there have been only a handful of studies that produced monoclinic gamma sulphur, and it has only been stable for 20 to 30 minutes at most. But we had created it in a cathode that was undergoing thousands of charge-discharge cycles without diminished performance – and a year later, our examination of it shows that the chemical phase has remained the same.”
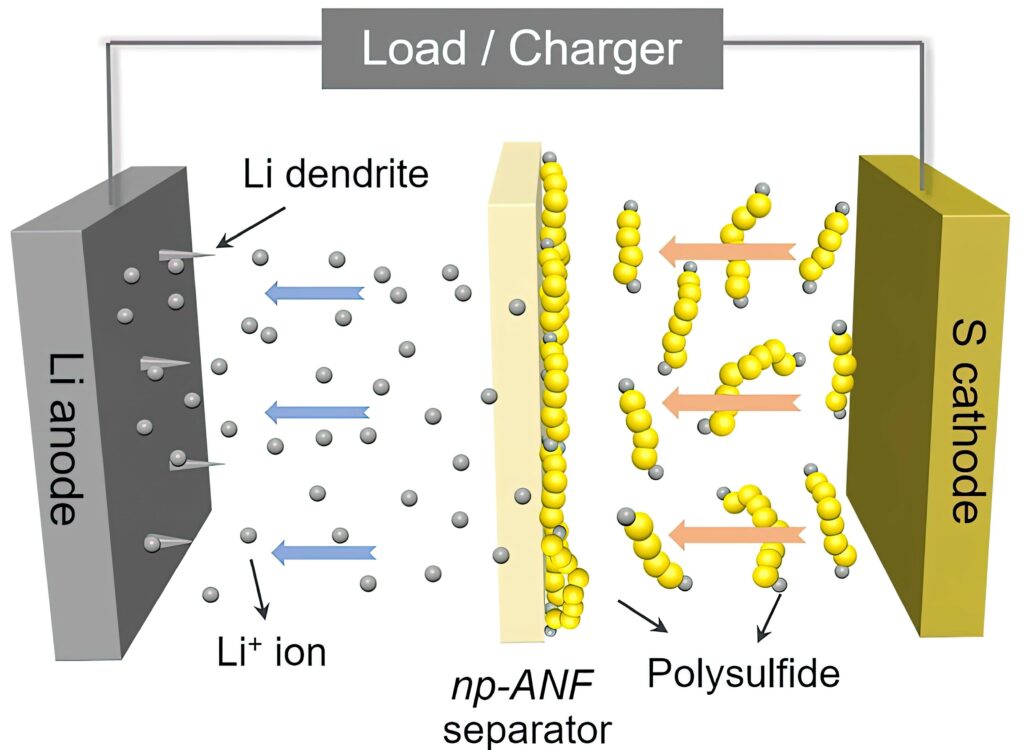
(Courtesy of University of Michigan)
The cathode was tested for over a year and remains stable after more than 4000 charge-discharge cycles.
Dr Kalra says, “While we are still working to understand the exact mechanism behind the creation of this stable monoclinic sulphur at room temperature, this remains an exciting discovery and one that could open a number of doors for developing more sustainable and affordable battery technology.”
Having a stable sulphur cathode that works with a carbonate electrolyte also opens up the use of materials such as sodium for the anode.
“Getting away from a dependence on lithium and other materials that are expensive and difficult to extract from the ground is a vital step for developing batteries and expanding our ability to use renewable energy sources,” says Dr Kalra. “Developing a viable LiS battery opens a number of pathways to replacing these materials.”
Meanwhile, researchers in Australia have developed a nanoporous interlayer that sits between the two electrodes to reduce the shuttling of the polysulphides.
These Porous Aromatic Frameworks have uniform 13 Å pores and internal surface areas that can be readily chemically functionalised. Appropriate sulphonation levels within these pores can deliver high lithium-ion transport rates, giving high capacity retention above 1000 mAh/g after 500 cycles at practical charge rates.
“A lithium battery interlayer sits in the middle of the battery and keeps the electrodes apart, and helps lithium get from one side of the battery to the other faster,” says Professor Matthew Hill at Monash University’s Faculty of Engineering, who led the research. “The new interlayer overcomes the slower charge and discharge rates of previous generation lithium-sulphur batteries.
Fellow researcher Ehsan Ghasemiestabanati says, “The interlayer stops polysulphides from moving across the battery; polysulfides interfere with the anode and shorten the battery life. It means the battery can be charged and discharged as many as 2000 times without failing.”
The team had previously used sugar to stabilise the sulphur in the cathode, preventing it from moving. A test cell built by the team has a life of at least 1000 cycles, while still holding more capacity than equivalent lithium-ion batteries.
The LiS work at Monash has been supported by CleanFuture Energy, an Australian subsidiary of the Enserv Group of Thailand, to develop and manufacture LiS batteries for e-mobility applications. Mark Gustowski, managing director of Enserv Australia, says, “We would be looking to use the technology to enter the growing market for EVs and electronic devices. We plan to make the first lithium-sulphur batteries in Australia using Australian lithium within about 5 years.”
Kevlar nanofibres
Researchers from the University of Michigan in the US have used a network of aramid nanofibres, recycled from Kevlar, to boost the cycle life of a LiS cell.
“There are a number of reports claiming several hundred cycles for lithium-sulphur batteries, but it is achieved at the expense of other parameters – capacity, charging rate, resilience and safety,” says Nicholas Kotov, Professor of Chemical Sciences and Engineering at the university, who led the research. “The challenge nowadays is to make a battery that increases the cycling rate from the former 10 cycles to hundreds of cycles and satisfies multiple other requirements including cost.”
The team had previously used networks of aramid nanofibres infused with an electrolyte gel in a lithium-ion cell to stop the dendrites that can grow from one electrode to the other and cause a short-circuit. The toughness of aramid fibres stops the dendrites.
But LiS batteries have another problem: that polysulfide shuttle effect. The membrane in the cell needs to allow lithium ions to flow from the lithium to the sulphur and back but also has to block the polysulfides. This ability is called ion selectivity.
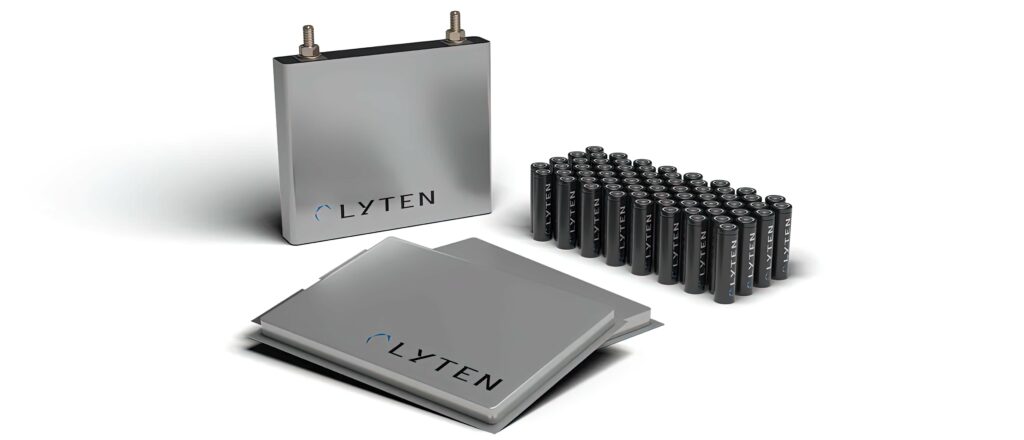
(Courtesy of Lyten)
The lithium ions and lithium polysulphides are similar in size, so it wasn’t enough to block the polysulphides by making small channels. Mimicking pores in biological membranes, the researchers added an electrical charge to the pores in the membrane.
They did that by harnessing the lithium polysulphides themselves. The polysulphides stuck to the aramid nanofibres, and their negative charges repelled the other lithium polysulphide ions that continued to form at the sulphur electrode. Positively charged lithium ions, however, could pass freely.
The team has designed a cell with a capacity and efficiency approaching the theoretical limits. It can also handle the temperature extremes of automotive designs and supports 1000 cycles of fast charging.
But commercial LiS cells are already becoming available for testing by developers ahead of volume production.
For example, the LytCell, from Lyten, in the US, uses a form of graphene with an innate, 3D structure that can ‘cage’ the sulphur within highly reactive orthogonal graphene layers. This is far more effective in driving full conversions to Li2S during discharge and to S8 during charging within the cathode. It also mitigates the polysulphide shuttle effect.
Lyten also uses an engineered coating on the lithium metal anode to mitigate the formation of dendrites. This has achieved lifetimes of over 1400 cycles in prototypes of its designs that have an energy density of 900 Wh/kg, and it plans to start volume commercial production in 2025.
The 3D graphene platform can be tuned at the molecular level to specific battery application requirements to improve energy density, provide better temperature performance and enable faster charging in 20 minutes with improved safety. Unlike lithium-ion batteries, it can operate from -30 C to +60 C, reducing the system’s cost by reducing the need for heat sinks and the amount of thermal management required.
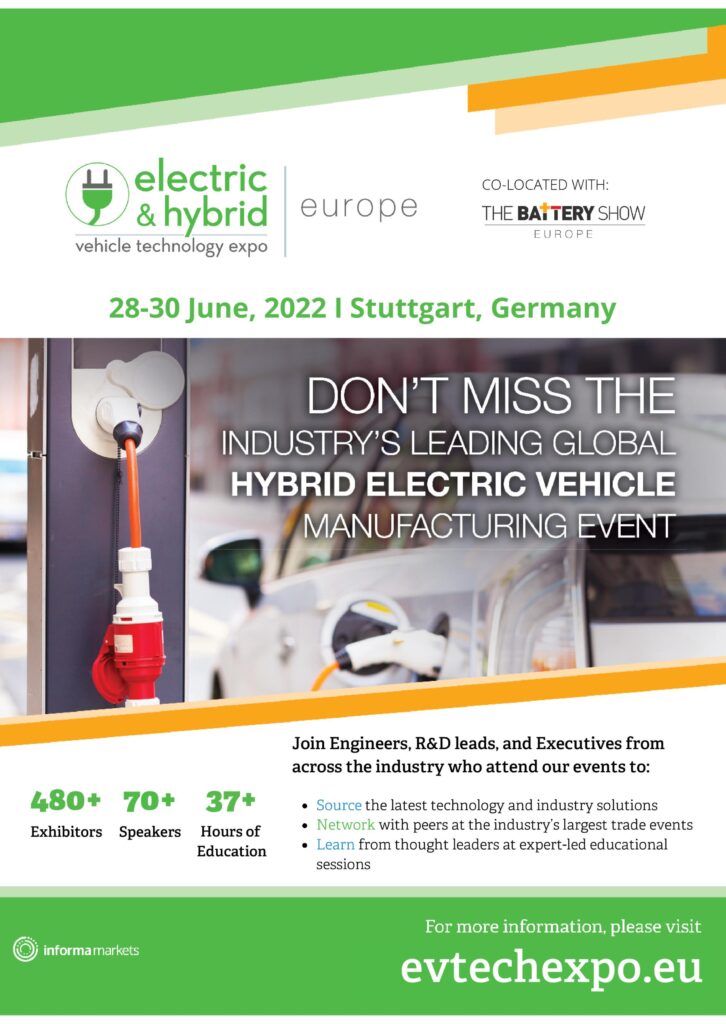
Testing LiS cells
One of the major challenges however is testing LiS cells. In order to distinguish the electrochemical responses from the anode and cathode, a third reference electrode has to be introduced. This technique is widely used for lithium-ion batteries, but there are few reports of three-electrode LiS cells, and those that are used are mostly for electrochemical impedance spectroscopy to measure an electrode, rather than the performance of a cell at different states of charge.
As a result, the resistance of the contribution of the lithium anode over extended cycling in the LiS system has not yet been well-investigated. A team of researchers in the Department of Chemistry at Uppsala University, in Sweden, has therefore looked into this.
A major challenge in building three-electrode LiS cells arises from the sensitivity of the cell response to the volume of the electrolyte. As an example, the Uppsala team initially looked at the construction of three-electrode cells in a vacuum-sealed pouch cell and in a reusable three-electrode cell housing from a commercial supplier.
Cells built in each format showed shorter cycle life and higher cell resistance than expected. This was a result of the vacuum sealing process of the pouch cells, which removes an uncontrolled amount of electrolyte, while the O-rings of the customised cells appeared not to provide a sufficient seal.
So the team used a gold microwire coated with a polyimide material to create a three-electrode cell that behaves in a comparable manner to a two-electrode equivalent. The polyimide insulates the microwire throughout the cell, leaving only a small cross-section between the two main electrodes, and makes it easy to ensure good electrode alignment. Crucially for the LiS system, the microwire electrode provides a valuable function when lithiated as a conventional third reference electrode, or as an unlithiated pseudo-reference electrode with the same performance.
This is the first effective three-electrode system for measuring the performance of LiS cells.
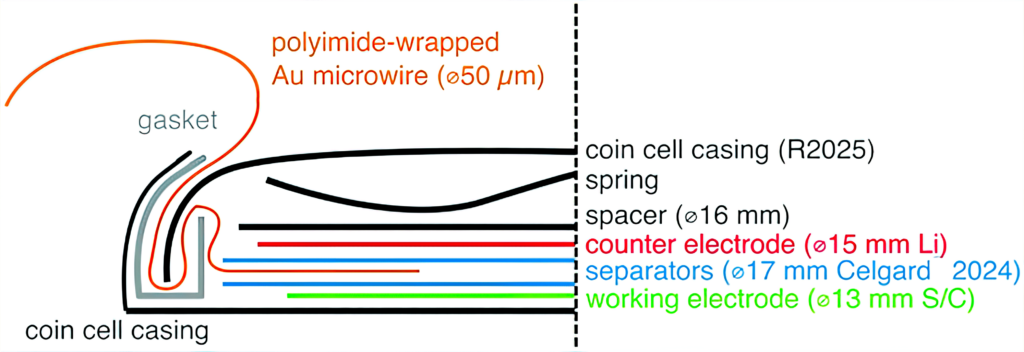
(Courtesy of Uppsala University)
Eliminating lithium
Another project, led by Chalmers University, in Sweden, aims to eliminate the lithium metal in the anode for a LiS cell.
The Lithium Sulphur Superbattery Exploiting Nanotechnology (LISSEN) project aims to create a cell with a lithiated silicon anode instead and a nanostructured sulphur-carbon composite as the cathode. This would offer an energy density of at least three times that available from present lithium battery technology, a comparatively long cycle life, a much lower cost by replacing cobalt with sulphur and a high safety degree by eliminating the lithium metal.
The researchers have previously developed a 3D sponge, or aerogel, made from graphene, for LiS batteries. This acts as a free-standing electrode in the cell and allows more effective use of the sulphur. Combining the cathode and electrolyte into one liquid, called a catholyte, can help save weight in the battery, as well as offer faster charging and better power capabilities.
“You take the aerogel, which is a long thin tube, and then you slice it,” says Carmen Cavallo of the Department of Physics at Chalmers, and lead researcher on the study. “You take that slice, and compress it, to fit into the battery. Then a sulphur-rich solution, the catholyte, is added and the porous aerogel acts as the support.
“The aerogel’s porous structure is key. It soaks up a lot of the catholyte, giving you a high enough sulphur loading to make the catholyte concept worthwhile.
“This kind of semi-liquid catholyte is really essential here. It allows the sulphur to cycle back and forth without any losses. It is not lost through dissolution, because it is already dissolved into the catholyte solution.”
Some of the catholyte solution is applied to the separator as well, to maximise the battery’s sulphur content. The resulting cell showed 85% capacity retention after 350 cycles, but the challenge is to improve the capacity and the cycle life.
The project includes Volkswagen as well as materials company Johnson Matthey, which acquired the technology developed by LiS cell pioneer Oxis Energy. The research aims to develop all the steps for producing a commercial battery cell, starting from material synthesis and characterisation, and using nanotechnology for improving the charging rate before building and testing large-scale prototypes, with scaling up the manufacturing process with industrial partners. It will also make sure that the cells can be recycled.
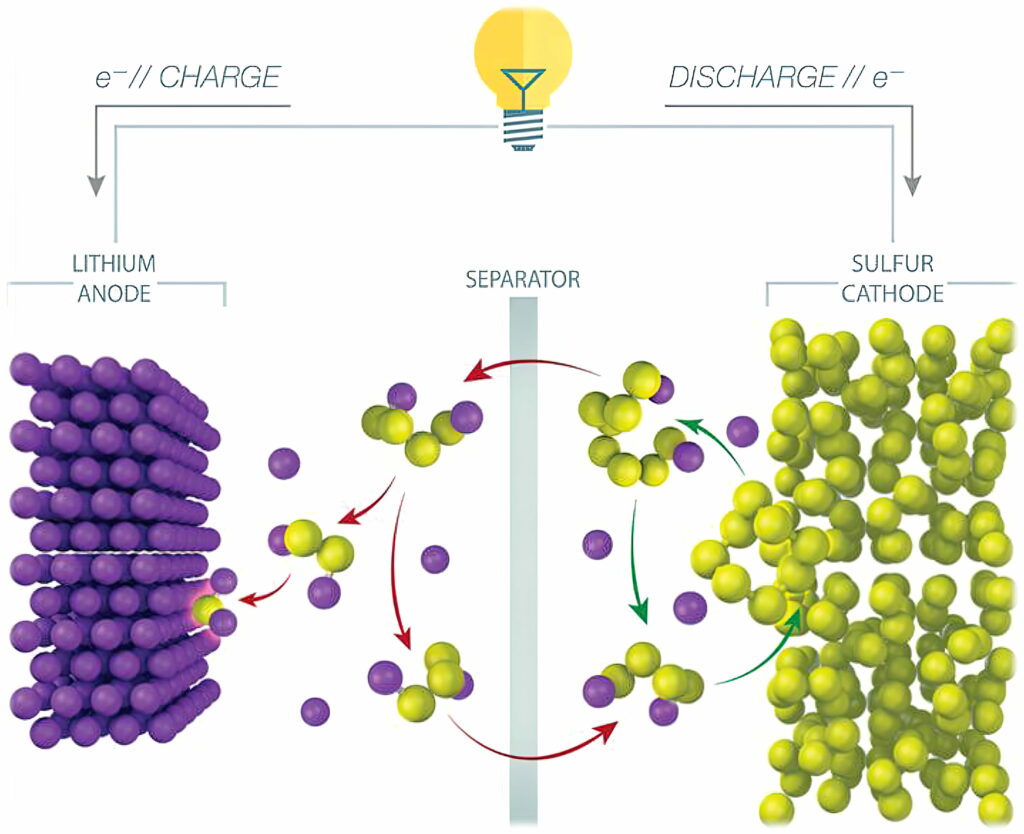
(Courtesy of Chalmers University)
Conclusion
Sulphur is an intriguing material for e-mobility batteries. Combined with a lithium metal anode, it has the potential to provide lightweight, high-capacity battery packs at half the cost of present lithium-ion packs without the safety risks, even with liquid electrolytes. With solid electrolytes the risks are reduced even further, and this reduces the need for many of the safety-related aspects of a battery pack that are designed to limit the impact of thermal runaway, making packs lighter still.
The high energy density makes it a strong candidate for powering the motors of electric aircraft, but the challenges of the relatively short cycle life remain.
Many research projects around the world are looking to overcome the challenge of the polysulphide shuttle problem, with different architectures and materials such as graphene aerogels and Kevlar nanoparticles. These are showing highly promising results, boosting the lifetime of LiS cells from under 50 to over 4000 charge-discharge cycles.
The challenge being addressed now is to commercialise the technology for volume production. The lower cost of sulphur, and the elimination of nickel and cobalt gives battery makers more headroom for reducing costs even with smaller manufacturing volumes.
Some manufacturers are now emerging form years of quiet development with high-capacity prototype LiS battery packs with long lifetimes that are now being tested by lead customers in the US. As these gain traction in niche applications, e-mobility designers will be able to adopt the technology in existing lithium-ion manufacturing lines, boosting the range and operating time of vehicles.
That then leads to the potential for high-performance battery cells that eliminate the use of lithium metal anodes. Cells with silicon or magnesium anodes and sulphur cathodes offer the potential for more rugged battery packs with even higher energy densities that sidestep the challenges of thermal runaway entirely.
ONLINE PARTNERS
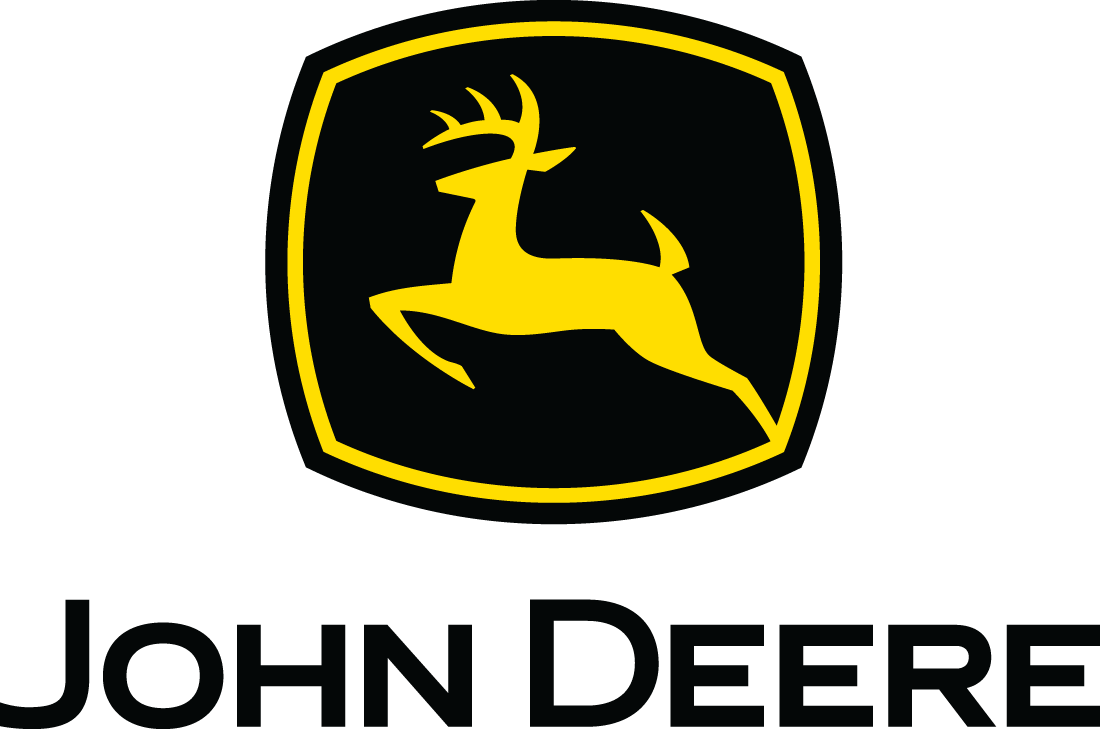
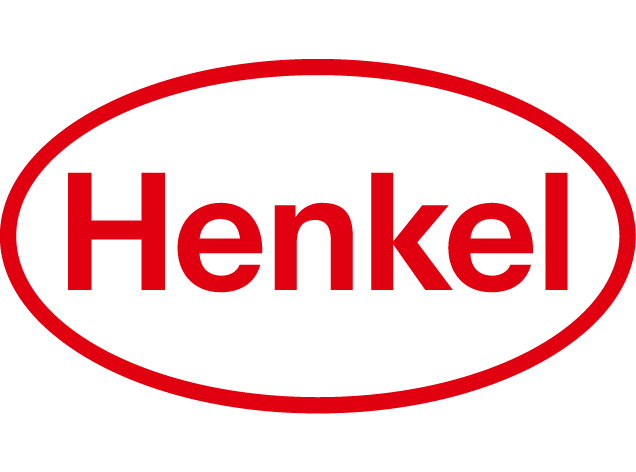
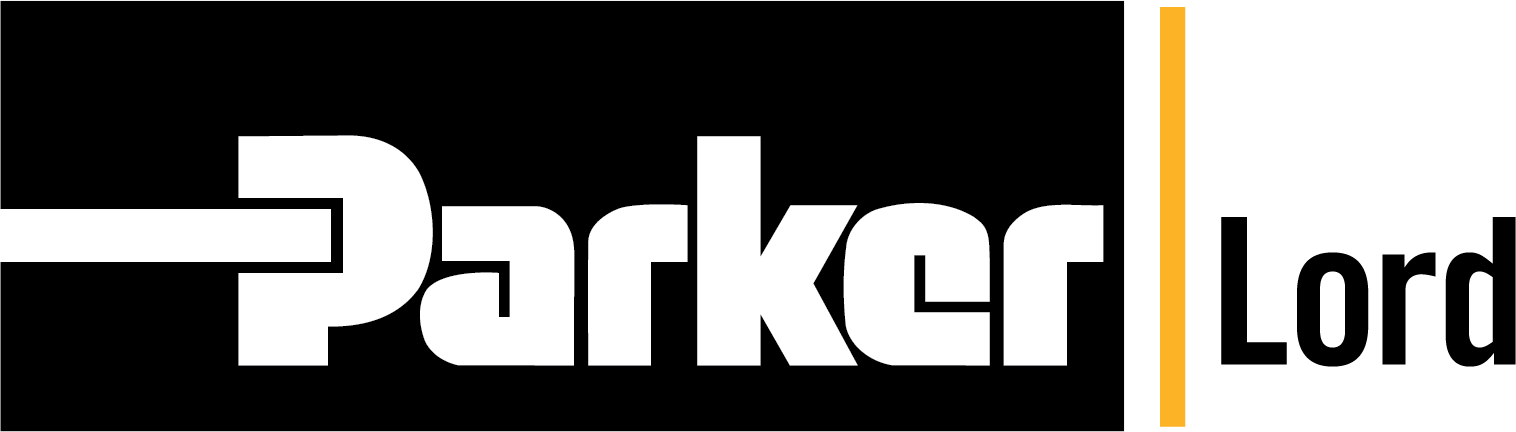
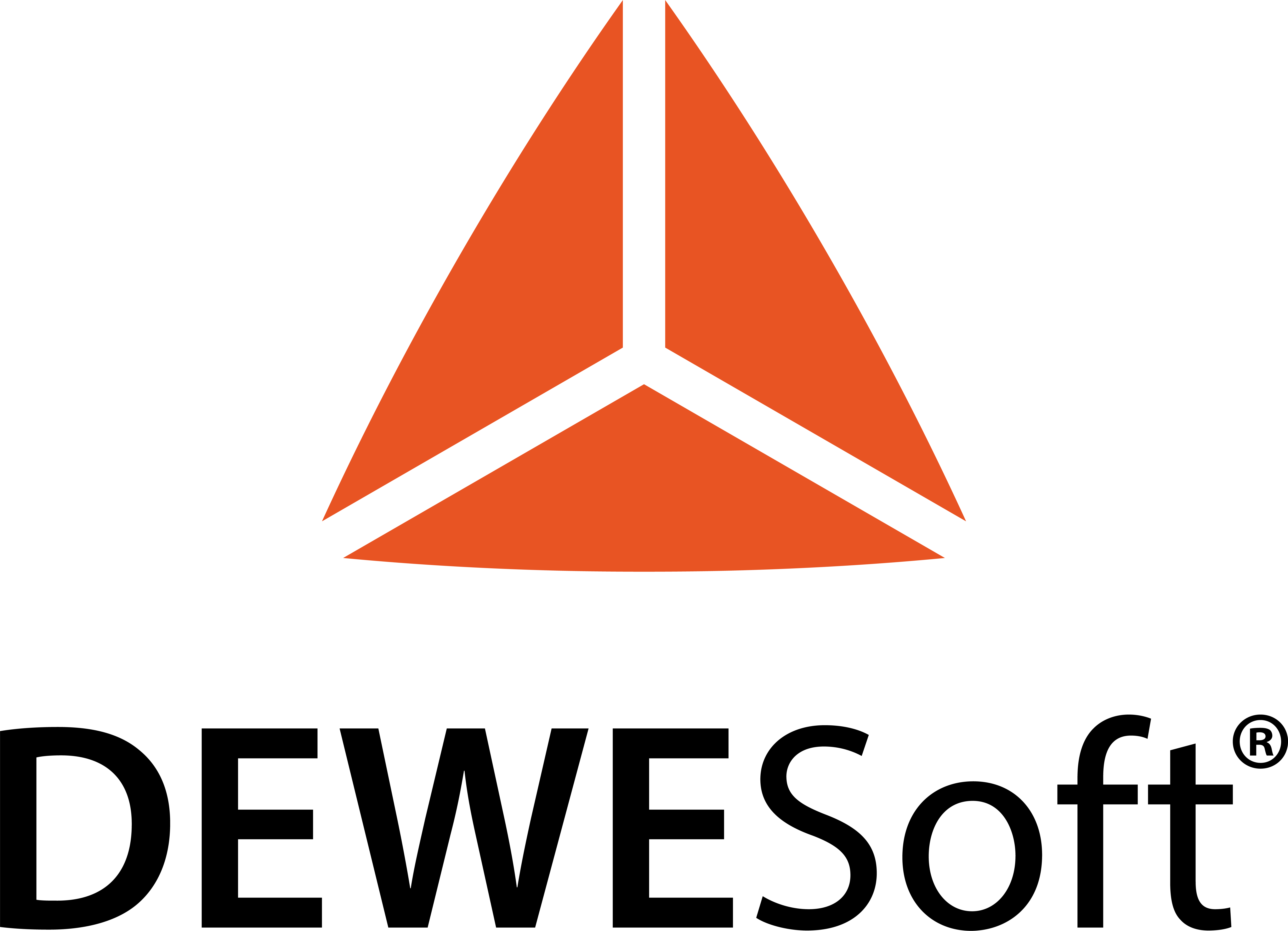
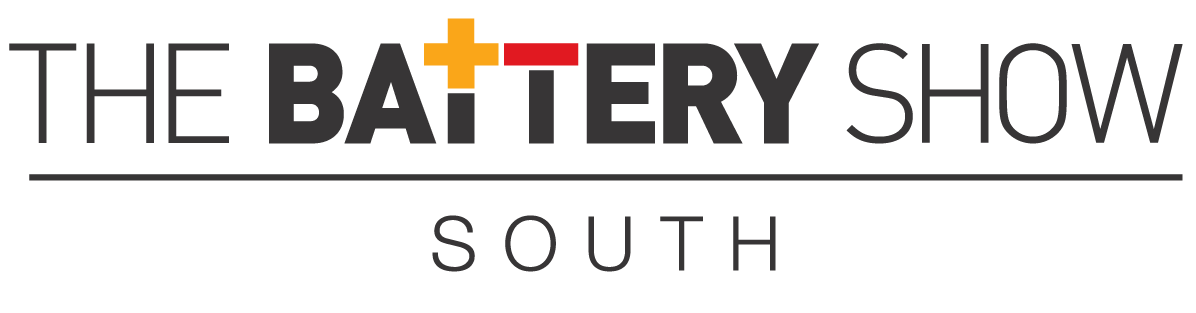
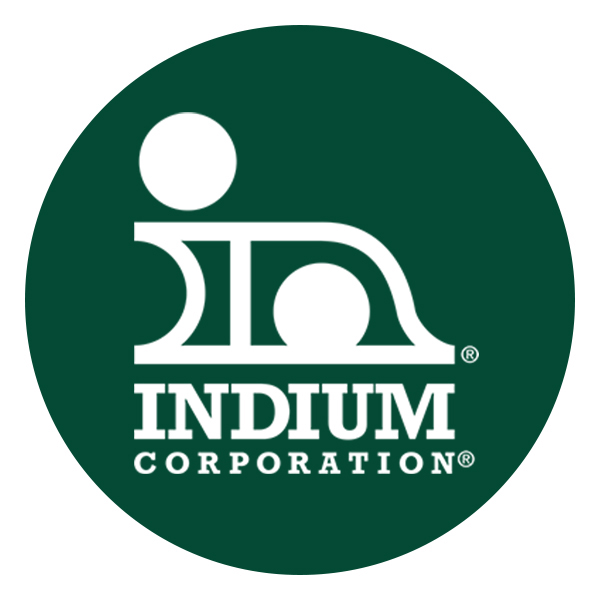
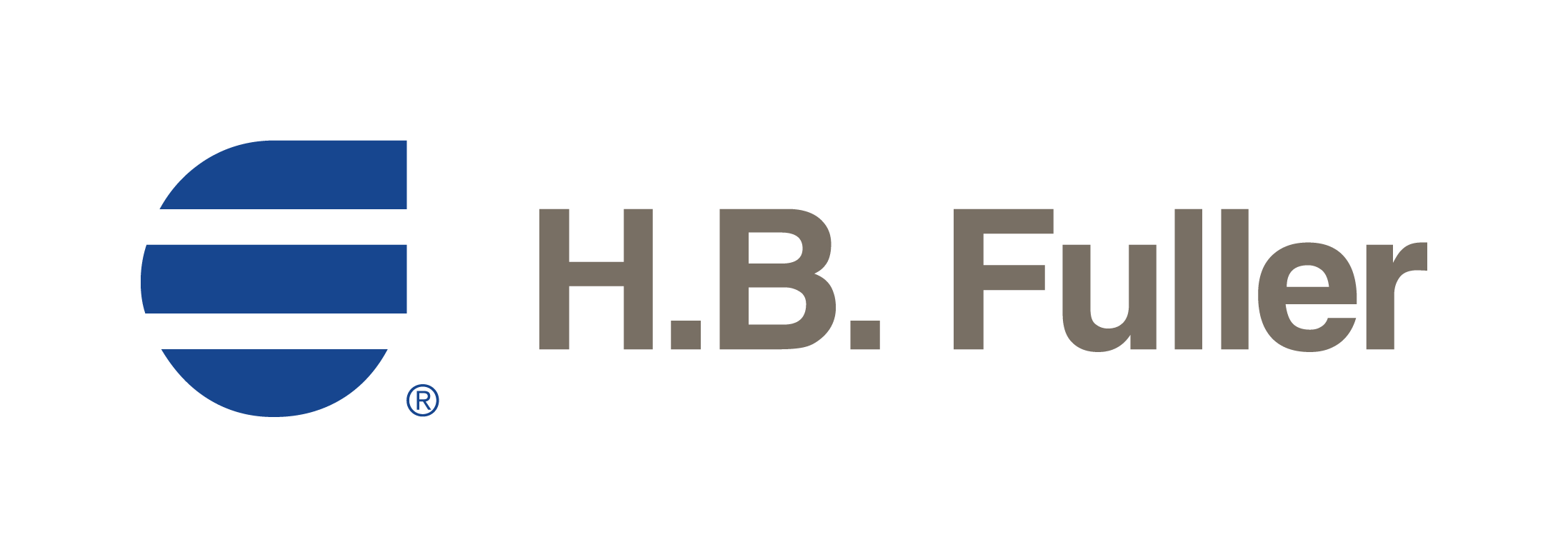
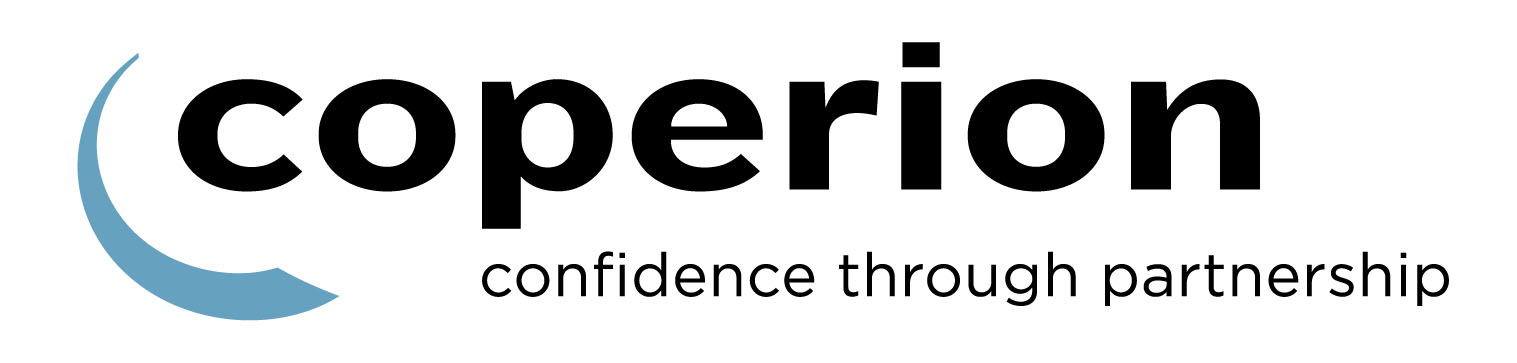