New chapter in the story of cork
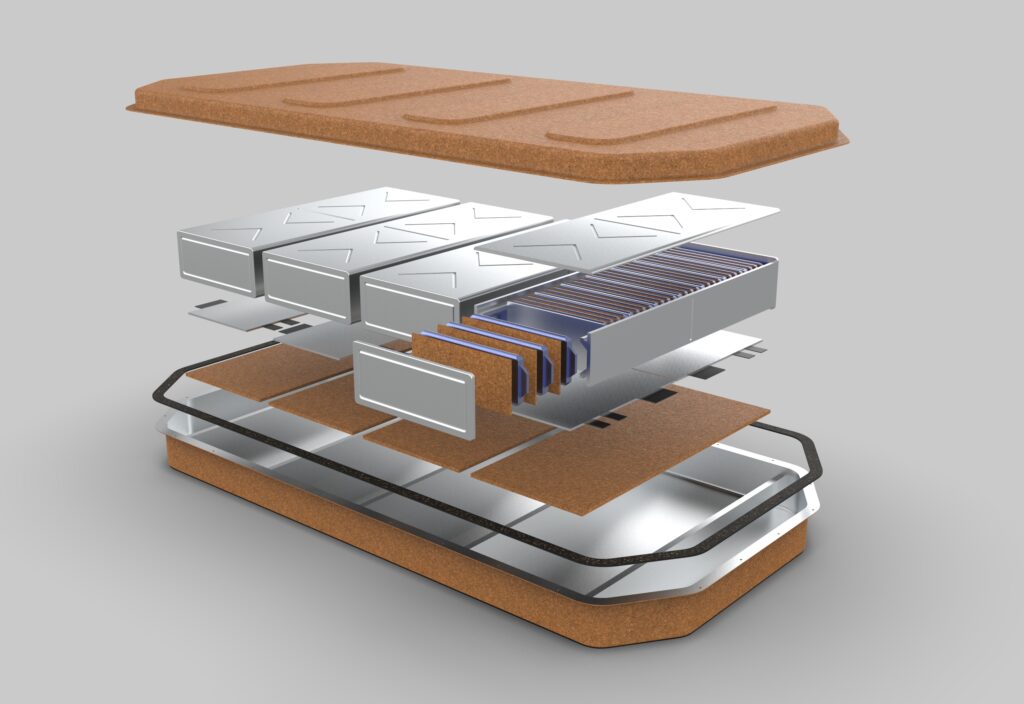
(Courtesy of Amorim Cork Composites);
Finding a material with several applications in state-of-the-art EV powertrains that literally grows on trees might seem unlikely, but that is exactly what Portuguese company Amorim Cork Composites is offering with cork (writes Peter Donaldson).
The raw material is the bark of the cork oak tree (Quercus suber), which in addition to its best-known application of sealing wine into bottles has a long history of engineering applications in the aerospace, defence, electricity and automotive industries. It is now being adapted to thermal protection, vibration and impact absorption in EV battery packs.
Early cars designed by Gottlieb Daimler and Carl Benz used cork gaskets to seal oil pans and valve gear covers, says Amorim’s mobility business manager Thomas Peroutka, and the material has been used in ablative and insulating thermal protection on rockets and satellites since the earliest days of spaceflight.
Its impact-absorbing capabilities have also been exploited for use in armour, and its vibration- and acoustic-damping properties have long been used in high-power electrical transformers, he adds.
Cork has a beehive-like microstructure of cells that take the form of tiny, gas-filled pentagonal and hexagonal prisms; a cubic centimetre of the material contains about 40 million cells. Amorim describes this as a mass of micro-balloons or micro-pillows gently pressing on each other, providing a unique combination of elasticity and compressibility that are at the heart of its damping and impact-absorbing properties.
It is also impermeable to gases and liquids, resistant to high temperatures, fire and friction as well as being strong and light.
In terms of its chemical composition, 45% is the complex bio-polyester suberin, with smaller amounts of lignin (27%), cellulose, waxes and other polysaccharides (12%), tannins (6%) and ceroids (6%).
Initially, Amorim is working on are thermal protection pads for the inside of battery packs, anti-vibration pads, and structural parts. In structural applications, the cork is combined with carbon fibres, glass fibres and/or metals such as aluminium to produce housings and covers with inherent thermal insulation, noise and vibration reduction and impact safety properties in addition to structural strength.
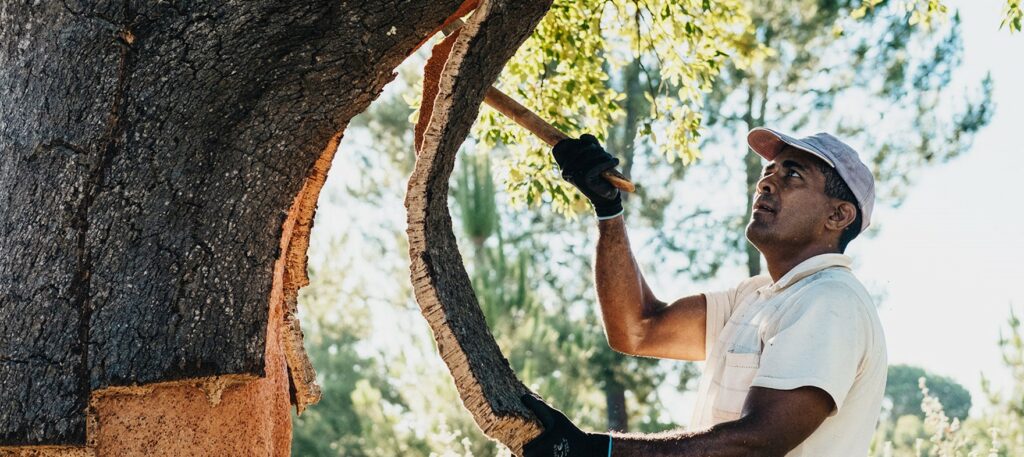
Amorim has developed different materials and solutions in various formats for different applications in the e-mobility sector, Peroutka says, and is talking with OEMs and Tier One suppliers about innovative ways of applying the material.
One of these is injection moulding, for which the cork first has to be granulated and mixed with other materials. “This allows us to use a huge variety of process parameters, from extrusion to lamination, thermo-forming and thermo-moulding,” he says.
Peroutka also emphasises that cork is not just carbon-neutral but effectively carbon-negative. “Studies indicate that for each ton of cork produced, a cork oak forest can sequester up to 73 tons of CO2,” he says.
The trees are not cut down to harvest the cork; the bark itself is left to regrow for nine years before being harvested again. Each tree can be harvested about 17 times over its lifetime, which on average is 200 years.
In addition, cork oak forests are part of the world’s biodiversity hotspots, have a recognised protection status, contribute to climate regulation, are a driving force for sustainable development and play a crucial role in the world’s ecological balance.
The first battery pack applications will emerge this year from cooperation with three European companies, Peroutka notes. “We are running the final tests and if, as we expect, everything works out well, we will start the scaling-up process for pre-series production.”
ONLINE PARTNERS
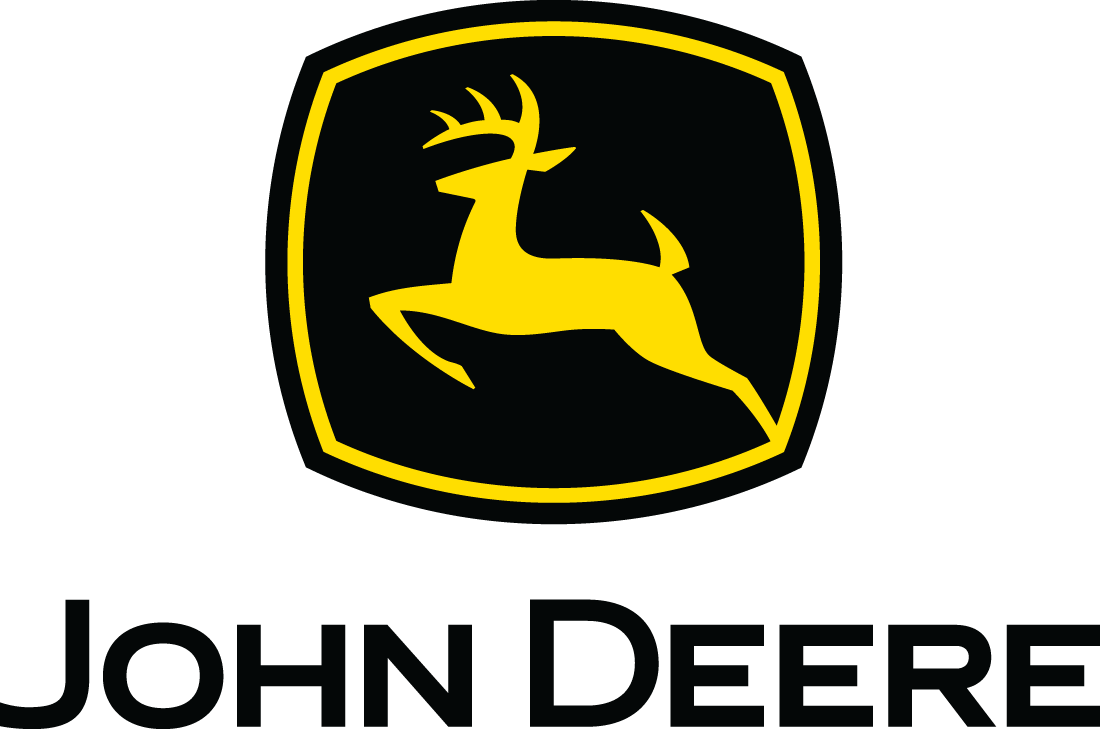
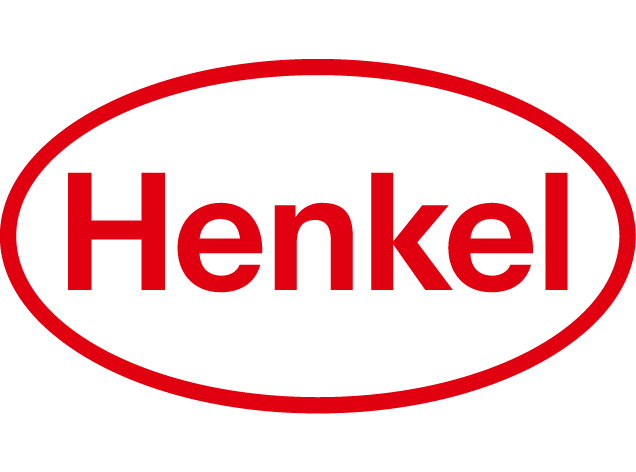
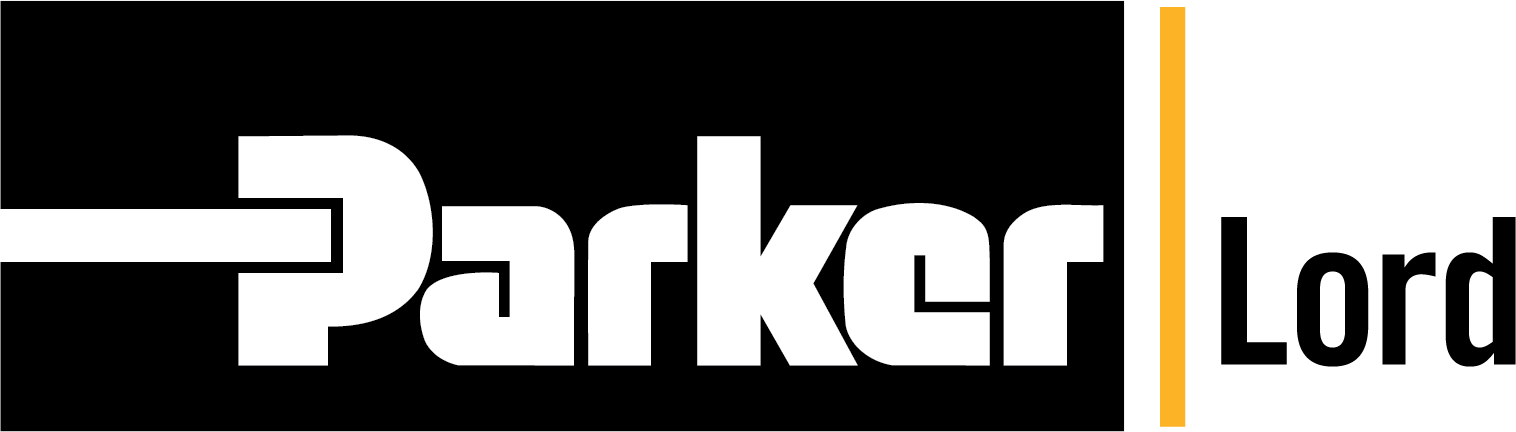
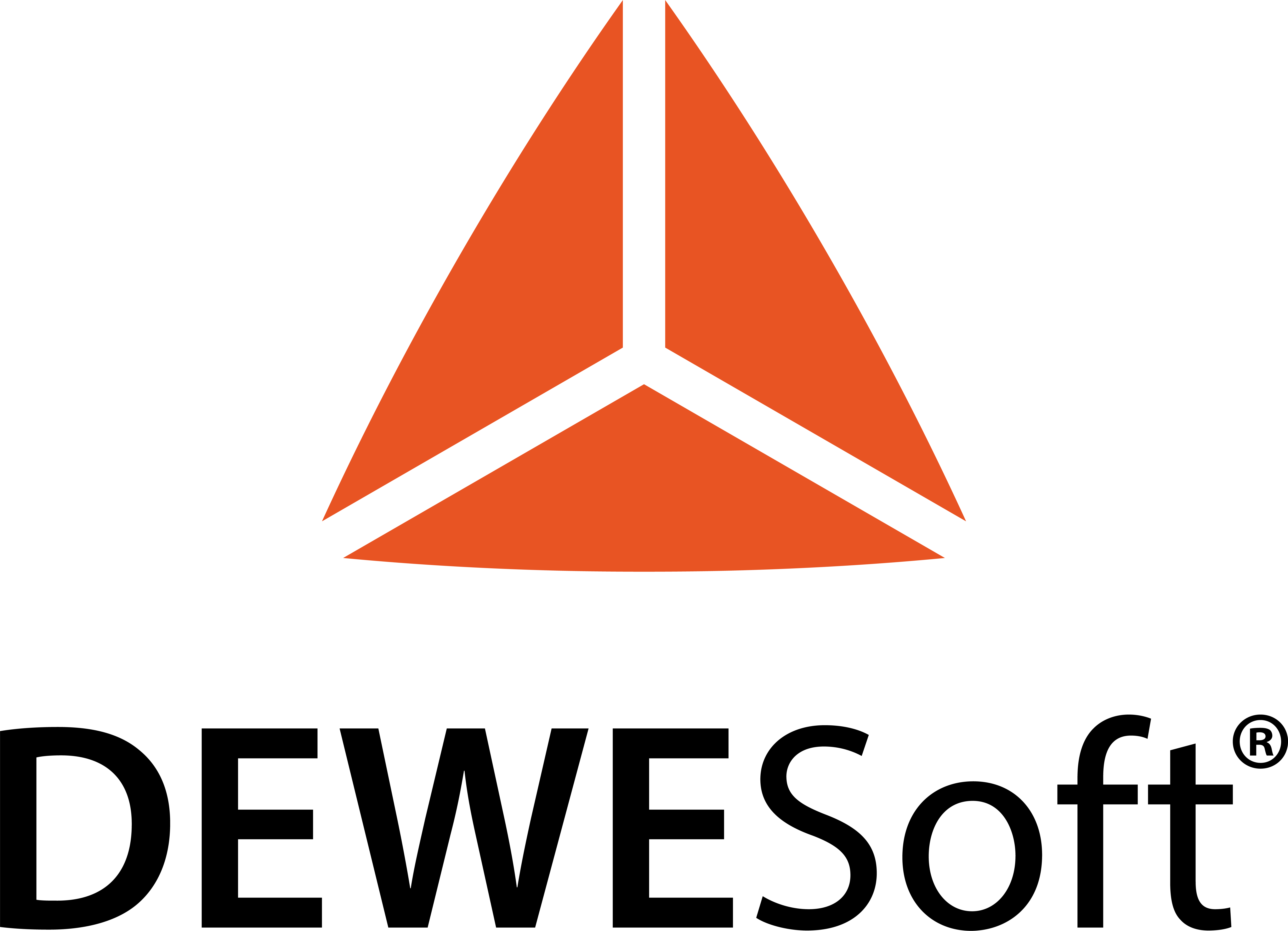
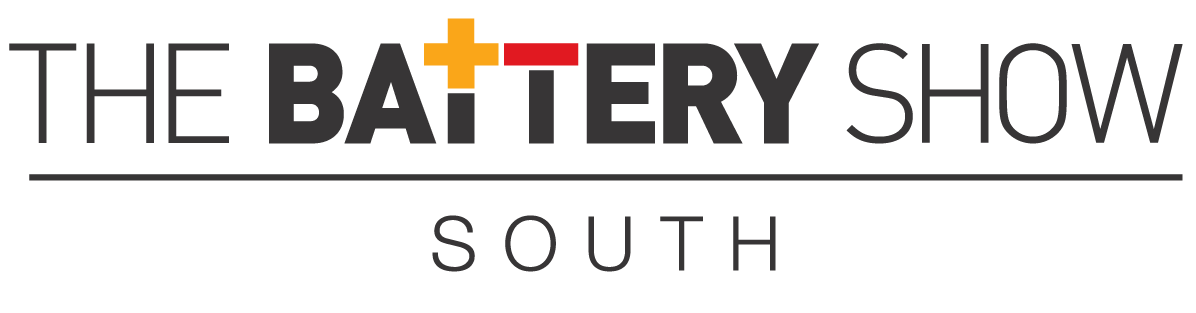
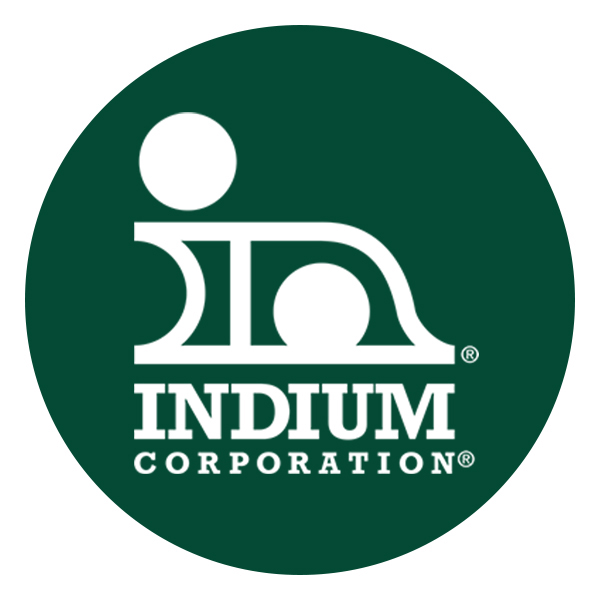
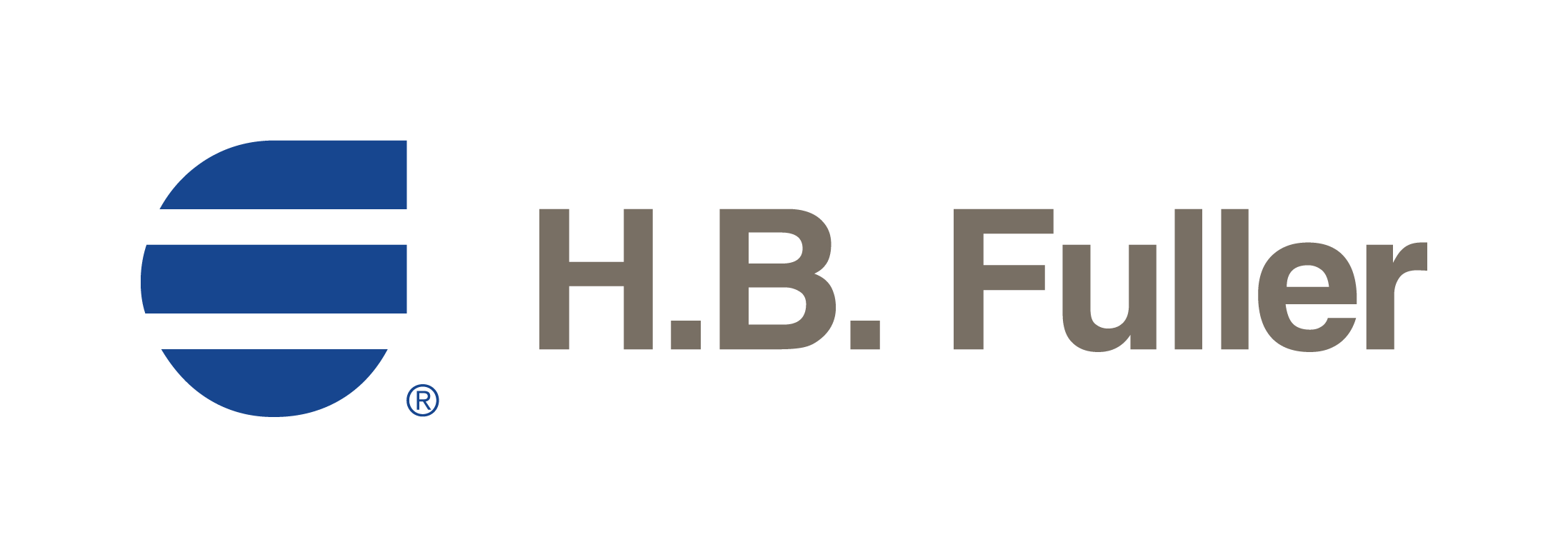
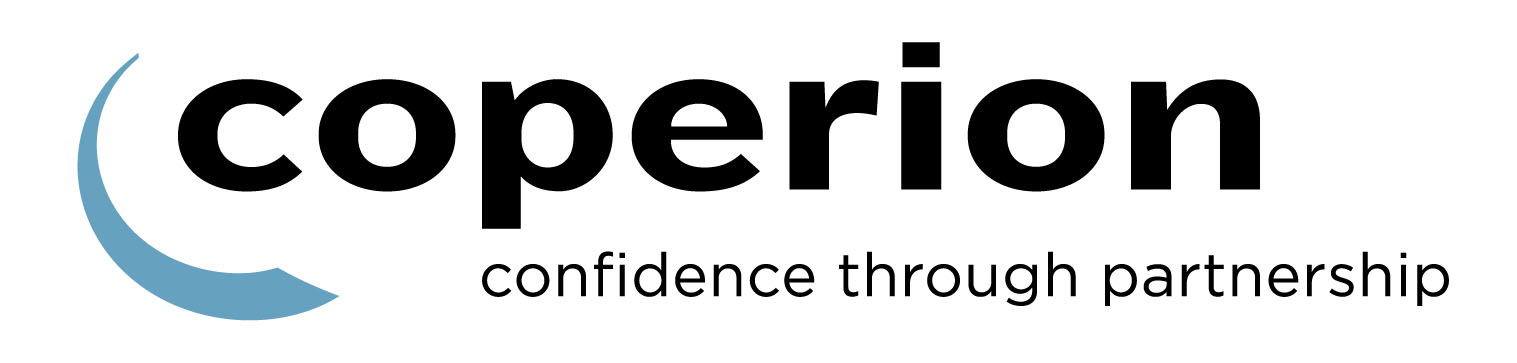