High-voltage breakout module needs no power meters or current transformers
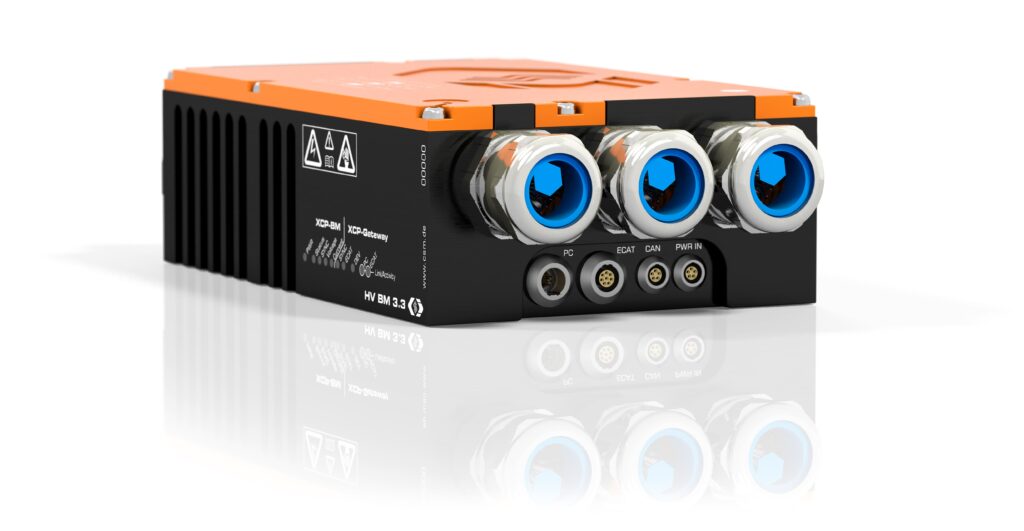
(Courtesy of CSM)
Measurement and data technology company CSM has unveiled a new HV breakout module designed to meet the international safety standards required for the use of equipment in HV applications on EVs. The company says it simplifies the instrumentation, improves accuracy and reduces costs compared with systems that have not designed for in-vehicle use. When combined with Vector Informatik’s eMobility Analyzer, real-time power analysis can performed on the test bench and in a test vehicle.
The module, HV BM 3.3, enables for the first time the electrical power analysis of vehicle engines without the use of classical power meters and current transformers. It is suitable for use in powertrain test benches as well as for mobile, real-time measurement in the HV electrical system of test vehicles.
It samples current and voltage signals at 2 MS/s and sends the sampled values via XCP-on-Ethernet to Vector Informatik, vMeasure exp or CANape software. The measured raw data is stored, and power values are calculated in real time using the integrated eMobility Analyzer function library.
The eMobility Analyzer calculates motor power values such as active power, apparent and reactive power, power factor, harmonics, total energy or the effective power of the motor windings. At the same time, a graphical online display of all the measured values and power parameters is available.
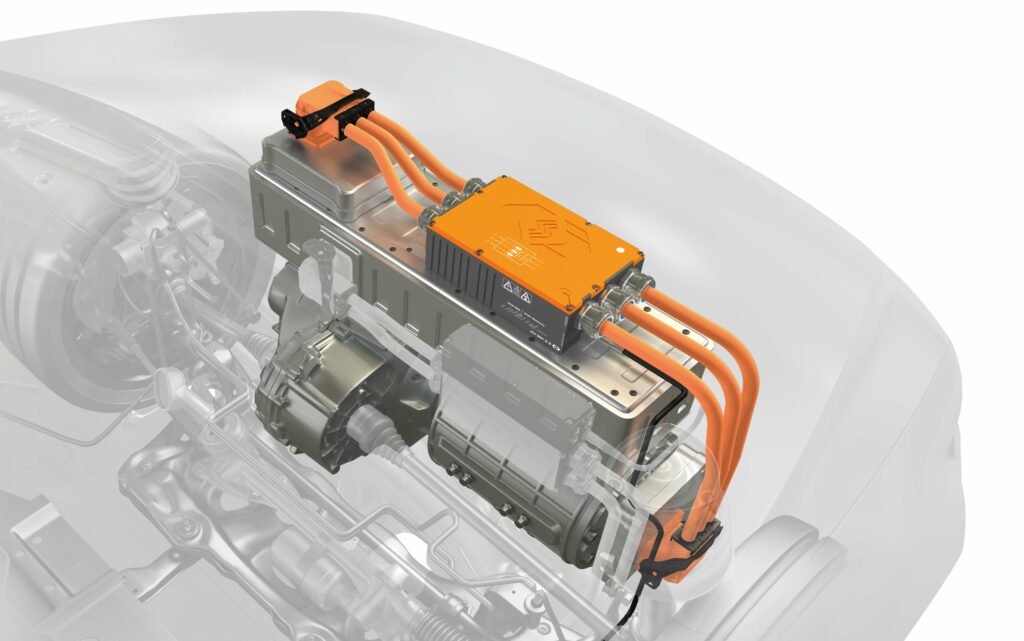
The module allows HV cables of up to 95 mm2 to be connected directly. The cables are fed into the module via suitable PG cable glands and connected with appropriately sized ring terminals.
Alternatively, the HV BM 3.3 can also be supplied with three-phase PowerLog connectors. This allows easy connection of DUTs, especially in powertrain test benches, to reduce changeover times. These connections, and the module itself, provide a system that meets EN 61010:1 requirements for using electronic equipment in HV environments.
For three-phase power measurement, the measurement circuit for currents and voltages is already installed in the module. This eliminates the need for cumbersome cabling, and eliminates the associated interference.
Phase currents and voltages up to 1400 A and 2000 V are sampled synchronously within 1 µs by the module. Complex phase correction for power measurement, as was previously common, is no longer necessary. The direct A-D conversion in the module and transmission of digital samples avoids electromagnetic interference in the environment of high-speed traction inverters.
The number of channels for power analysis can be easily expanded. The measurement data of further HV Breakout Modules, for example those between the battery (-ies) and inverter(s) or other vehicle components, are synchronously integrated in the measurement chain via an EtherCAT interface. This enables power efficiency analysis of the components in the powertrain with minimal effort.
Additional HV-safe and conventional CSM MiniModules for measuring temperatures, vibration, torque and speed can be added via a CAN interface in order to approach load points with temperature accuracy and to record efficiency maps.
Time synchronisation with other data sources, such as ECU data, is performed using PTP synchronisation according to the IEEE1588 standard.
The HV BM 3.3 can operate in ambient temperatures from -40 C to +125 C. A high-voltage and interference-proof encapsulated design with temperature-compensated shunt modules ensures very high accuracy over the entire temperature range.
ONLINE PARTNERS
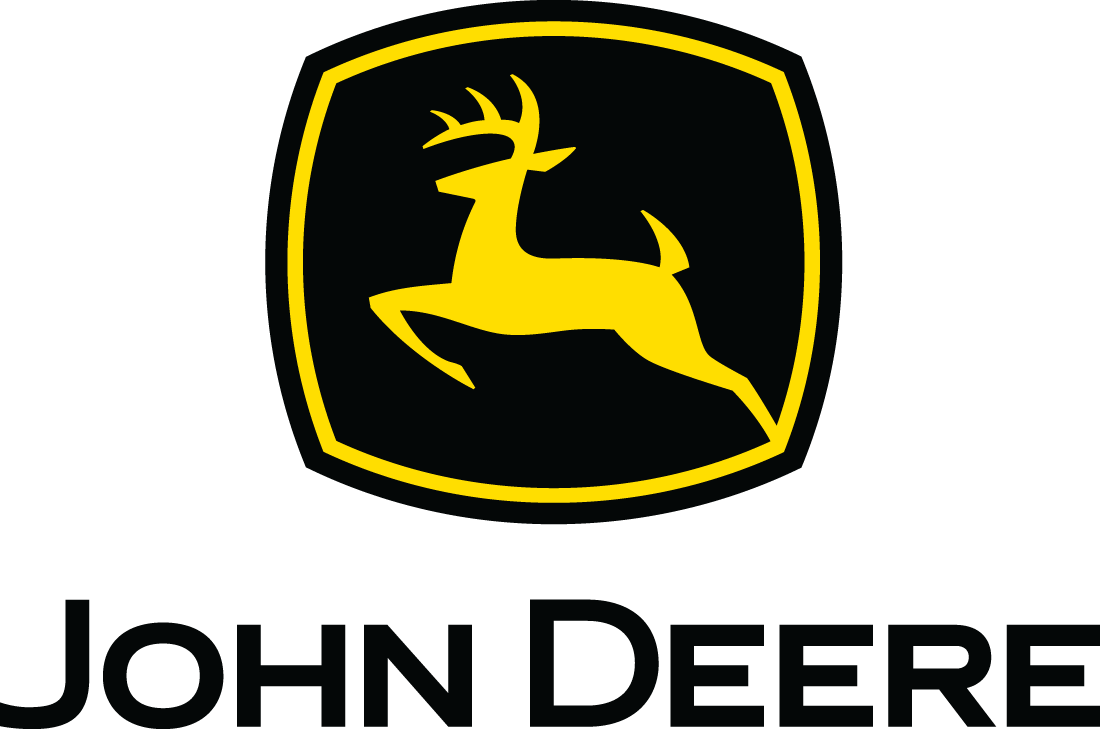
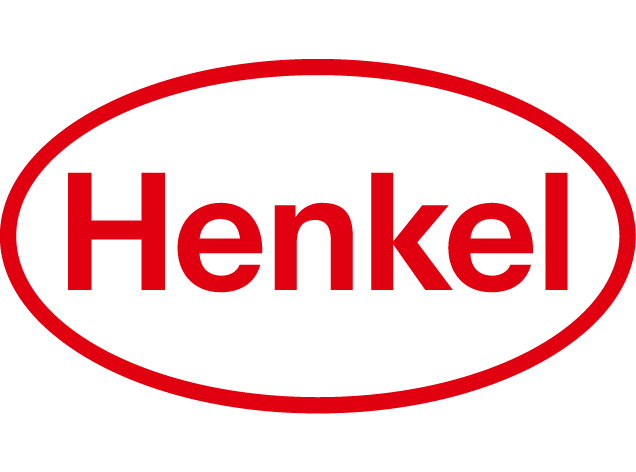
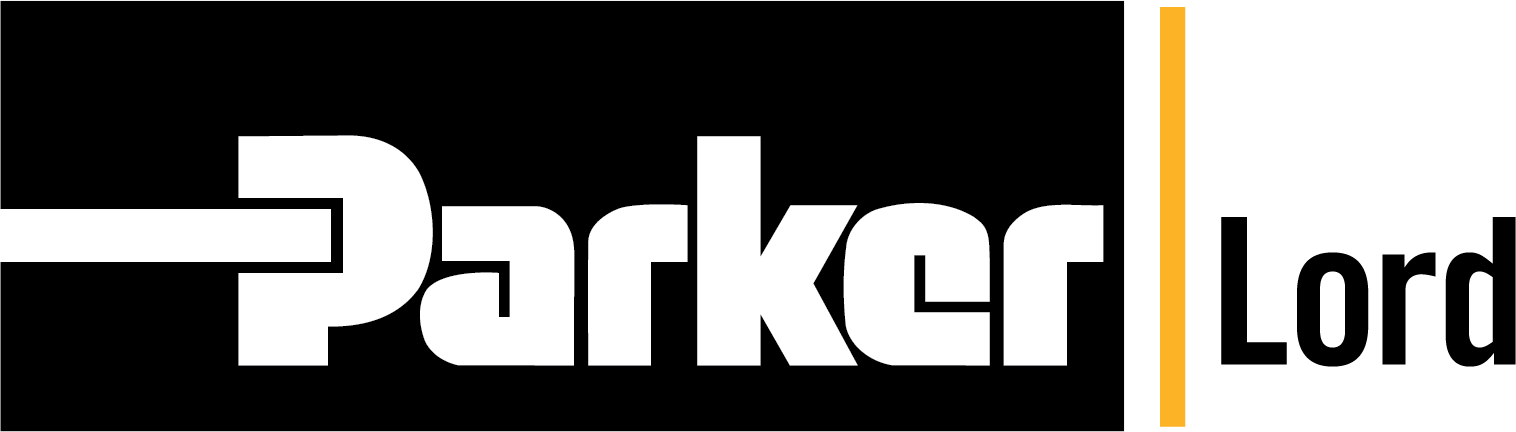
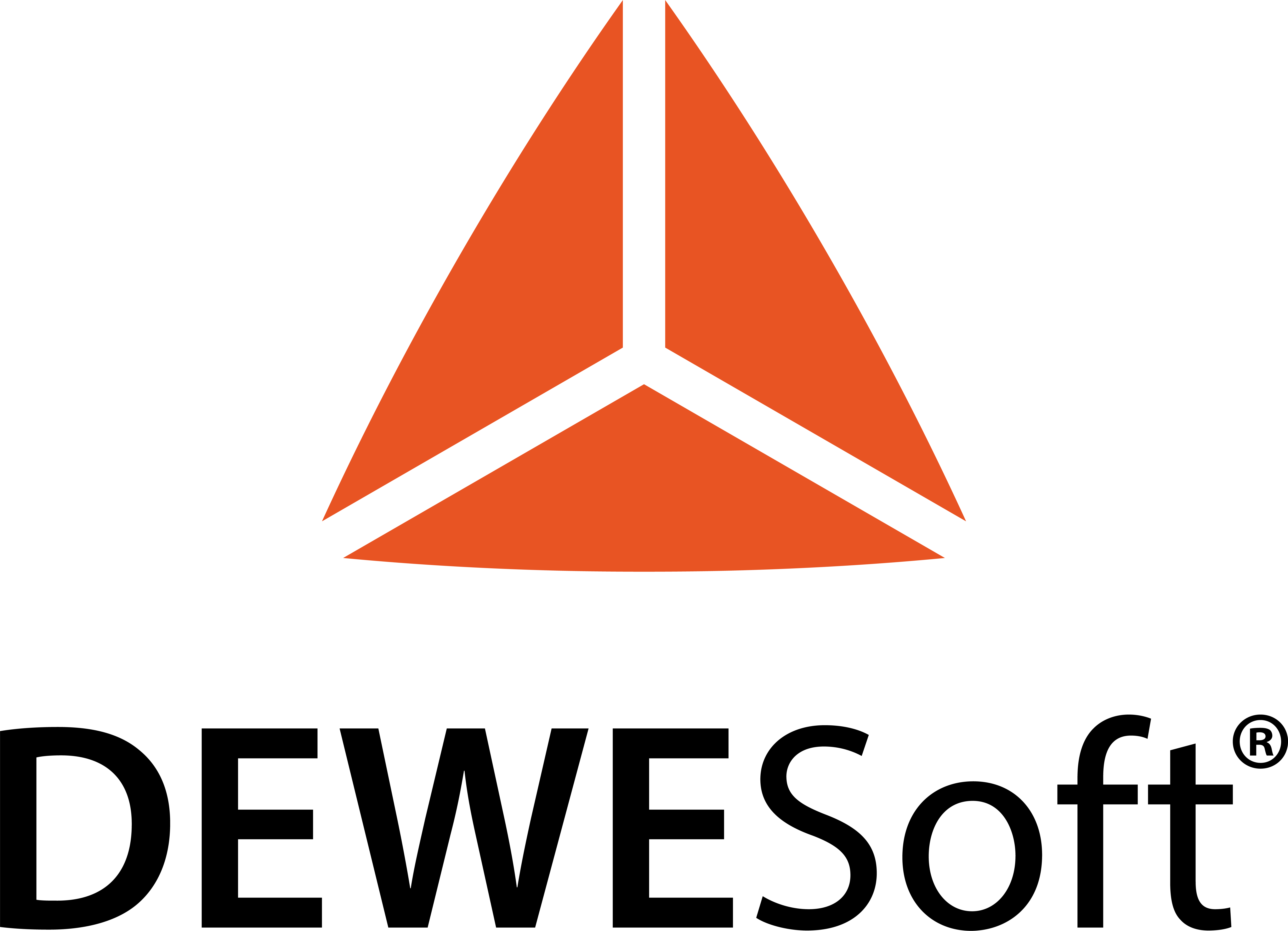
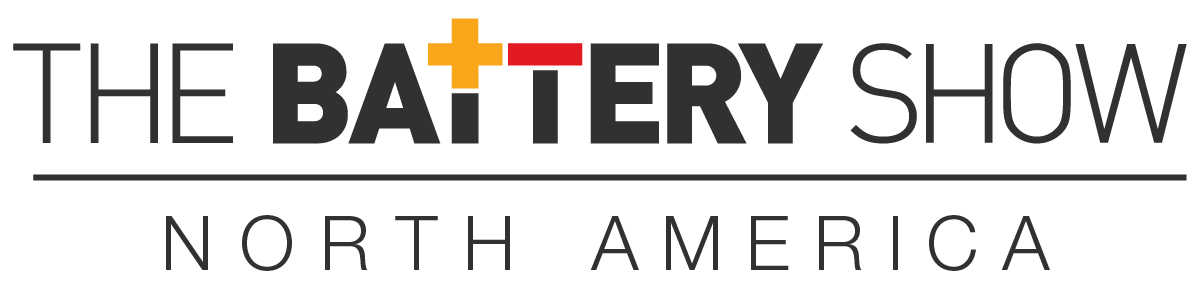
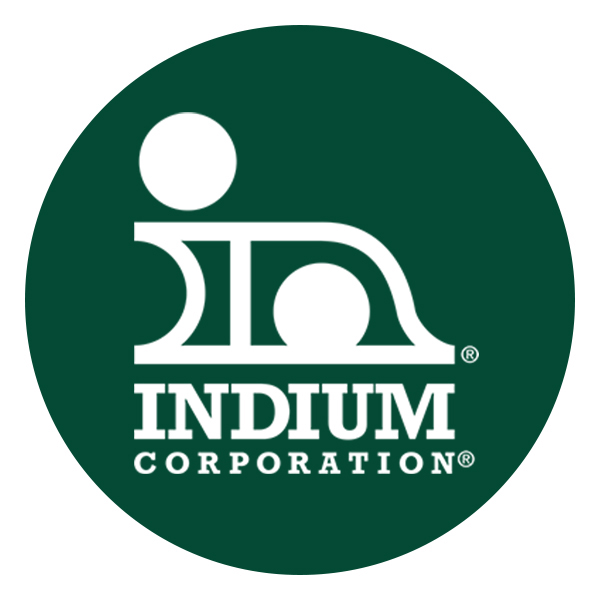
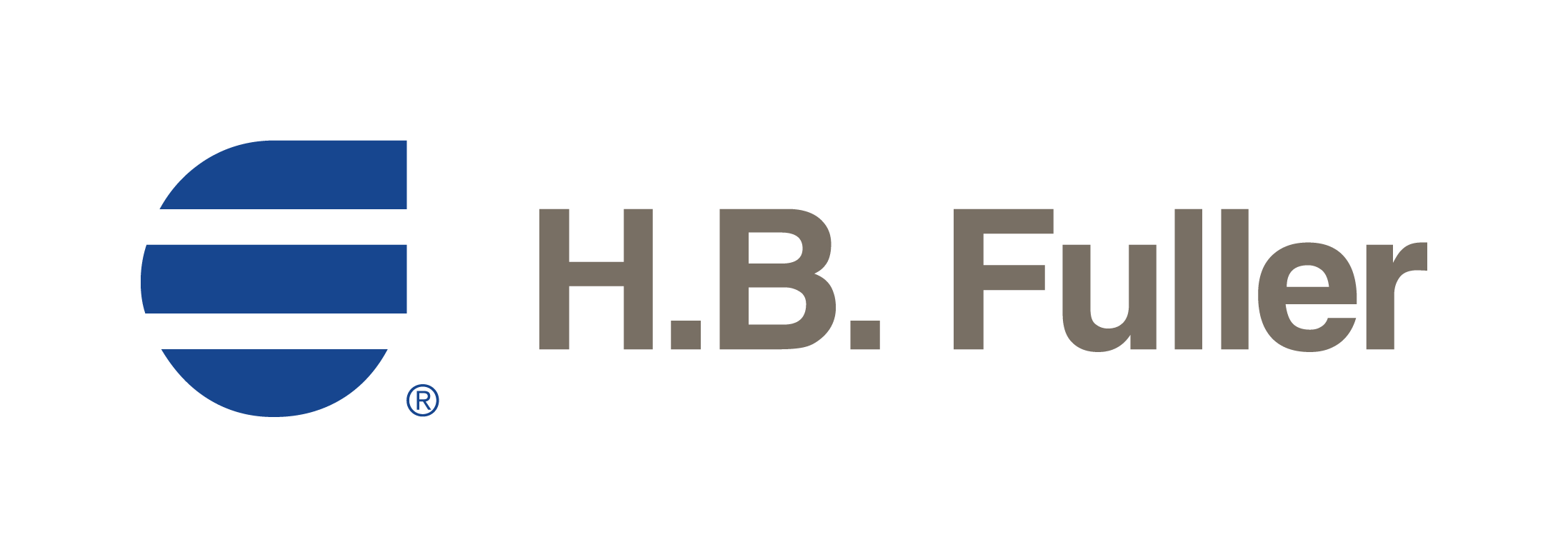
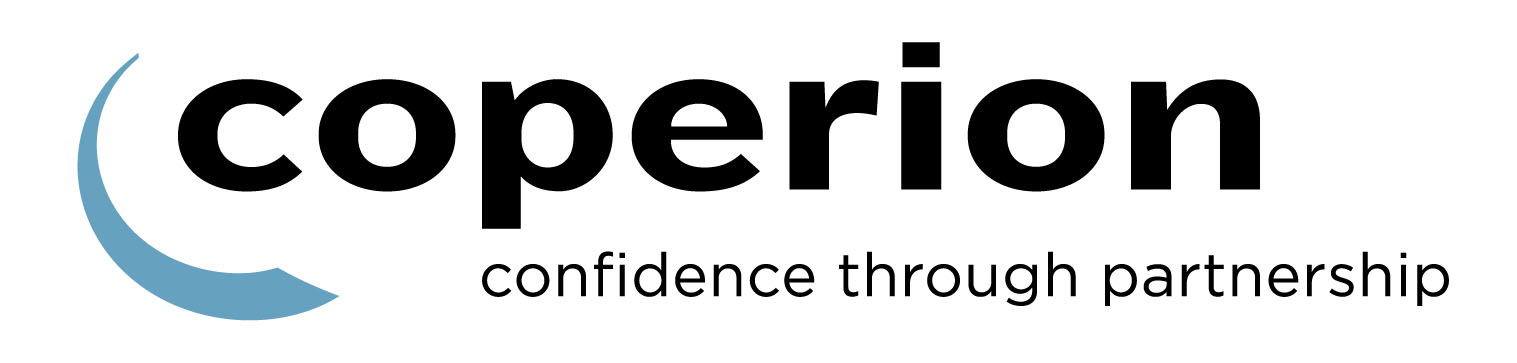