New EV battery thermal runaway testing facility targets fire safety
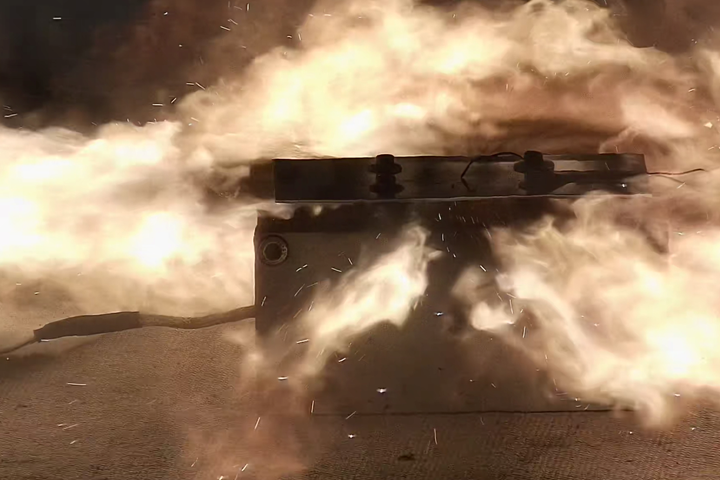
(Image courtesy of AZL Aachen)
A new collaborative project aimed at advancing fire safety testing for electric vehicle battery casings has been launched by AZL Aachen GmbH, responding to mounting industry demands for enhanced thermal management and fire protection in electromobility applications.
The initiative centers on developing a specialized test bench designed to replicate the extreme conditions that occur during thermal runaway events in both lithium iron phosphate and nickel manganese cobalt battery chemistries. This infrastructure enables controlled exposure of materials to high-temperature flames and hot particle impacts, creating a realistic platform for benchmarking structural and functional materials used in battery enclosures.
The testing methodology has been engineered to evaluate materials under conditions that closely simulate those encountered in automotive and aerospace applications. By enabling systematic comparison of thermal resistance and mechanical integrity, the project generates comprehensive data that supports material selection, development, and supplier qualification processes.
Participating companies will be able to submit their own material configurations for evaluation and receive detailed documentation including video records and thermal performance data. This process helps identify optimal solutions for battery housing safety while supporting the qualification of new materials against established industry benchmarks.
The project builds on previous collaborations with a consortium of 24 industry leaders including automotive OEMs, tier suppliers, and material producers. AZL has developed an instrumented testing protocol that quantifies material performance under varying flame temperatures while simultaneously assessing strength retention under fire load.
More than 50 materials have already been characterized through this established infrastructure. These include metals, polymers, fiber-reinforced composites, and multi-layered systems, all tested for survival under tensile load at 800°C, 1000°C, and 1200°C. The testing also evaluates failure modes, areal weight, and cost efficiency.
The current initiative leverages this knowledge base and test infrastructure, enabling partners to validate their own solutions and benchmark them against leading market alternatives.
The collaborative project will begin on July 15, 2025, with an initial meeting where partners will align on technical objectives and refine the testing agenda. The collaborative structure ensures resource pooling, transparency, and strategic insight, supporting technical advancement and market competitiveness in battery safety.
Companies interested in participating are encouraged to request further project details or arrange a consultation to discuss specific requirements.
The initiative comes at a time when battery thermal management and fire safety have become critical concerns for EV manufacturers, particularly as energy densities continue to increase and battery packs become more integrated into vehicle structures.
Click here to read the latest issue of E-Mobility Engineering.
ONLINE PARTNERS
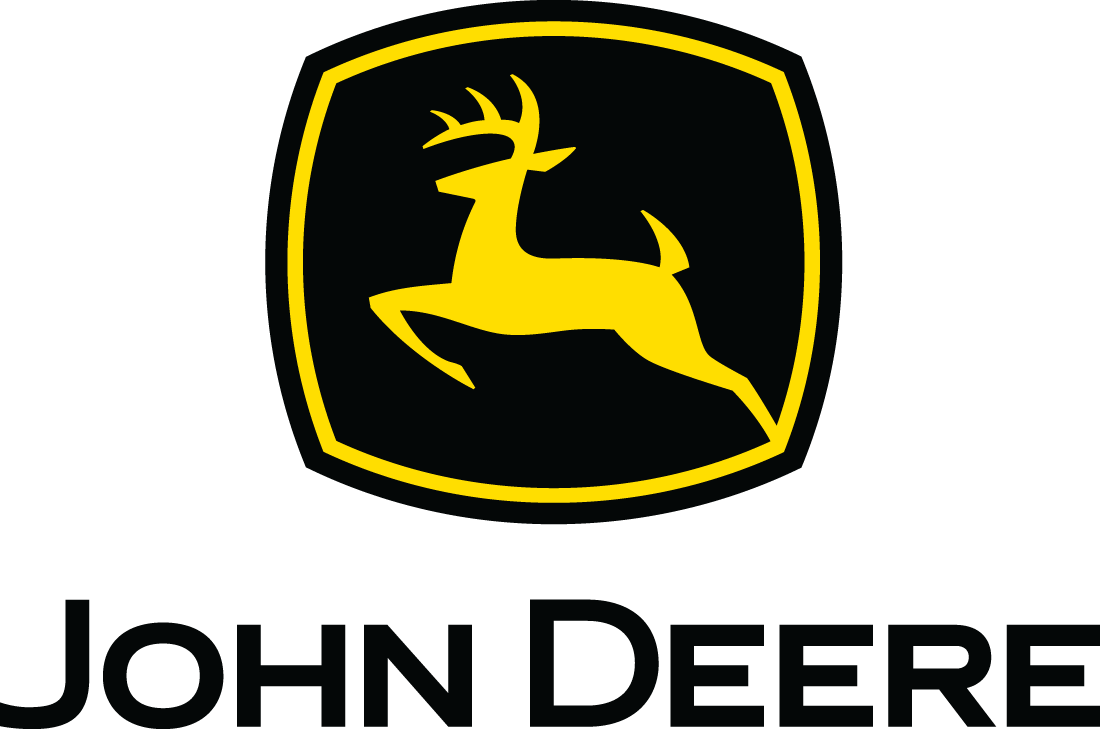
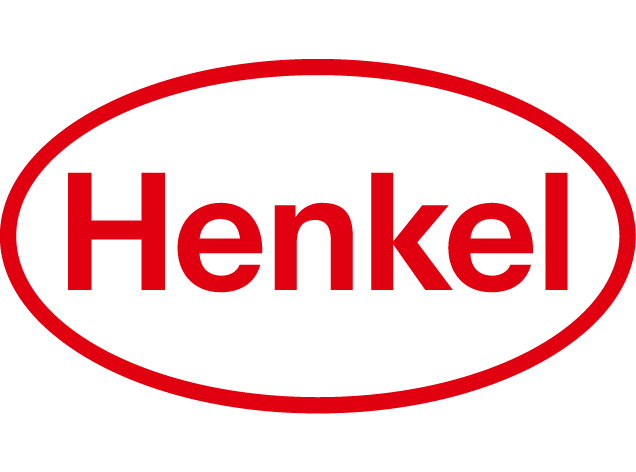
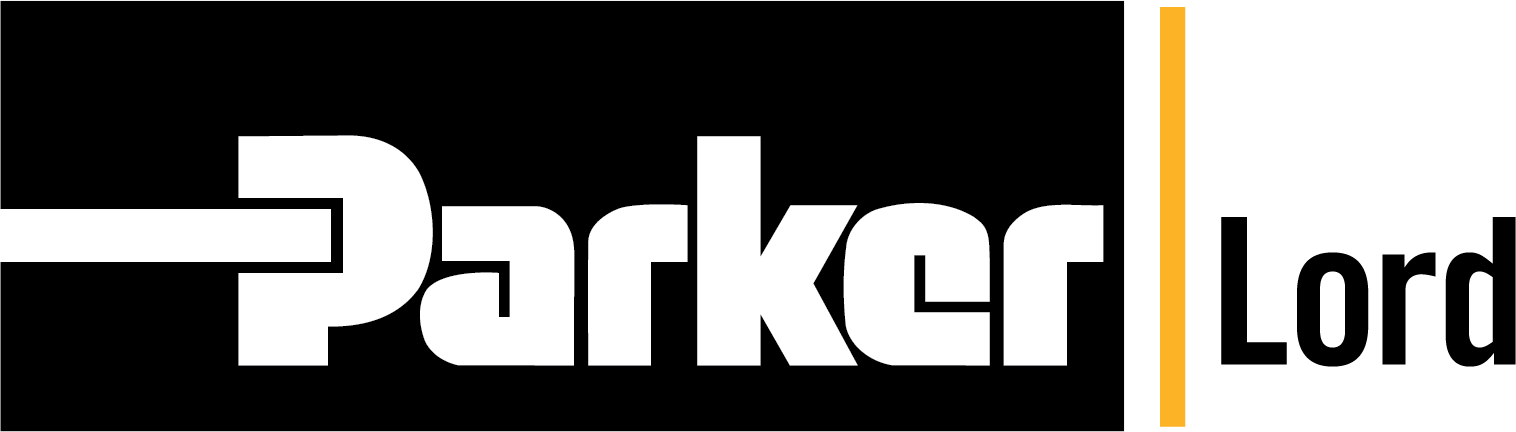
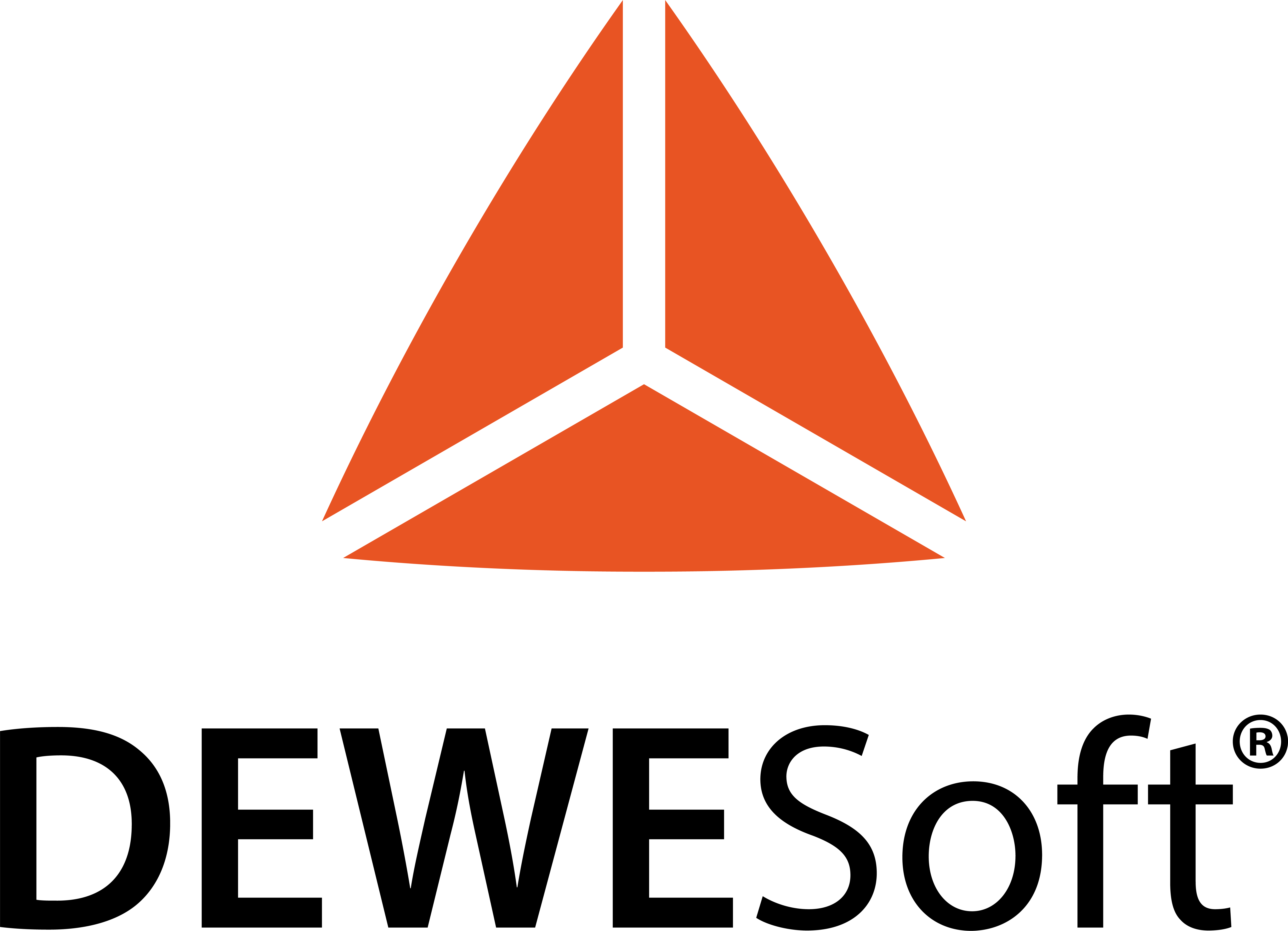
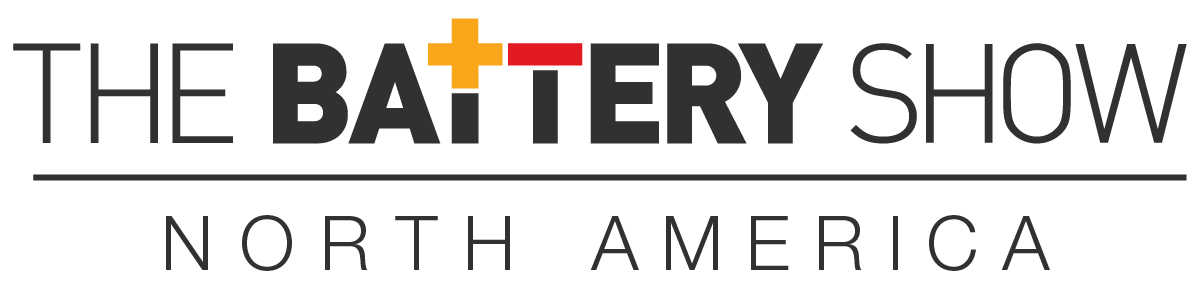
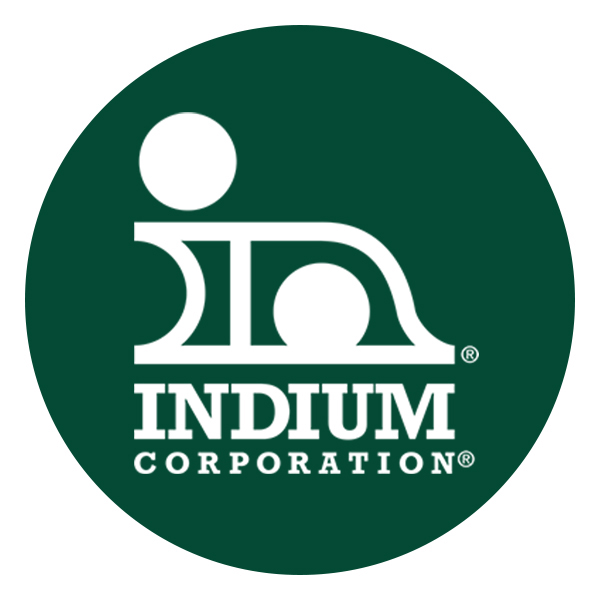
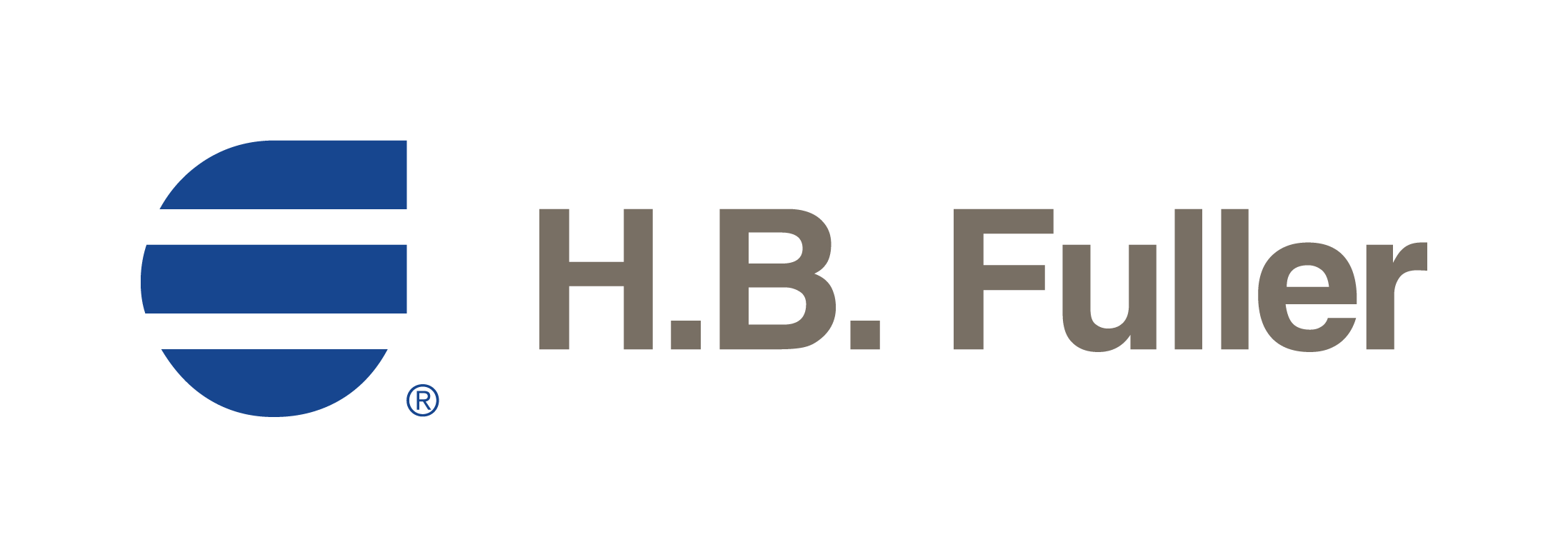
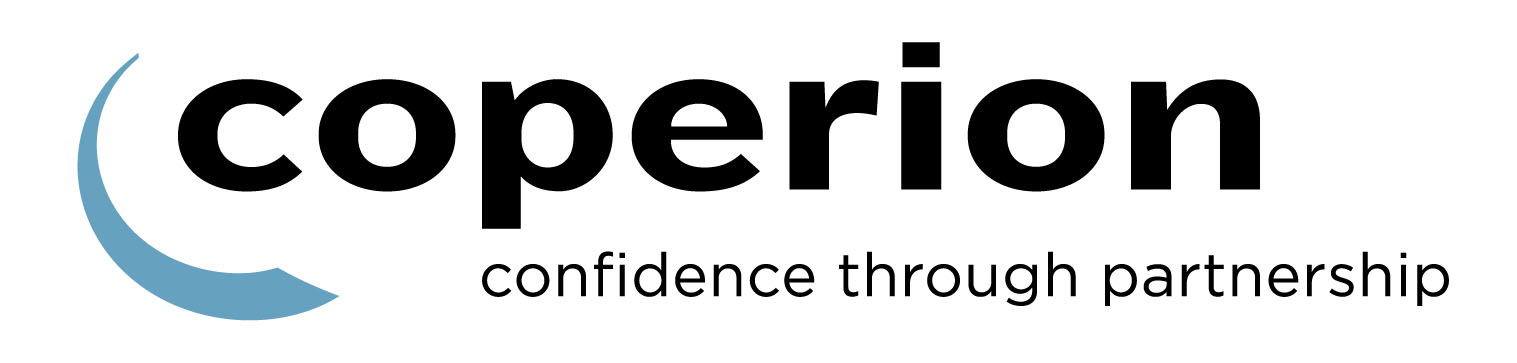
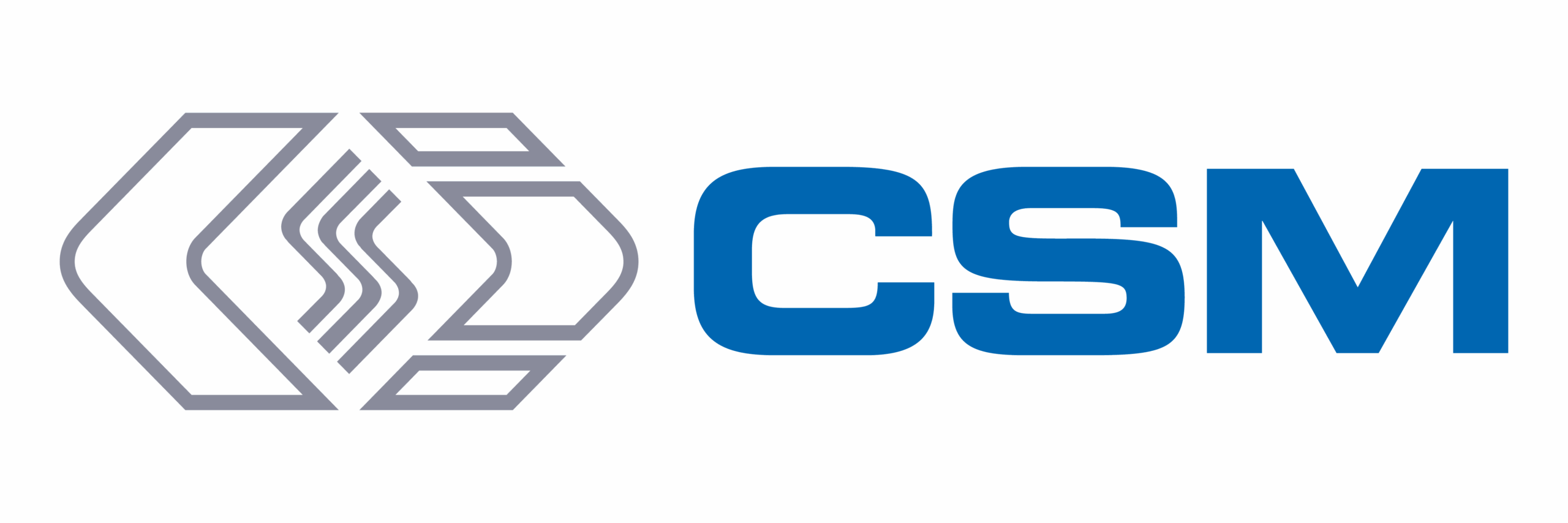