Motor cooling
Cool motive force
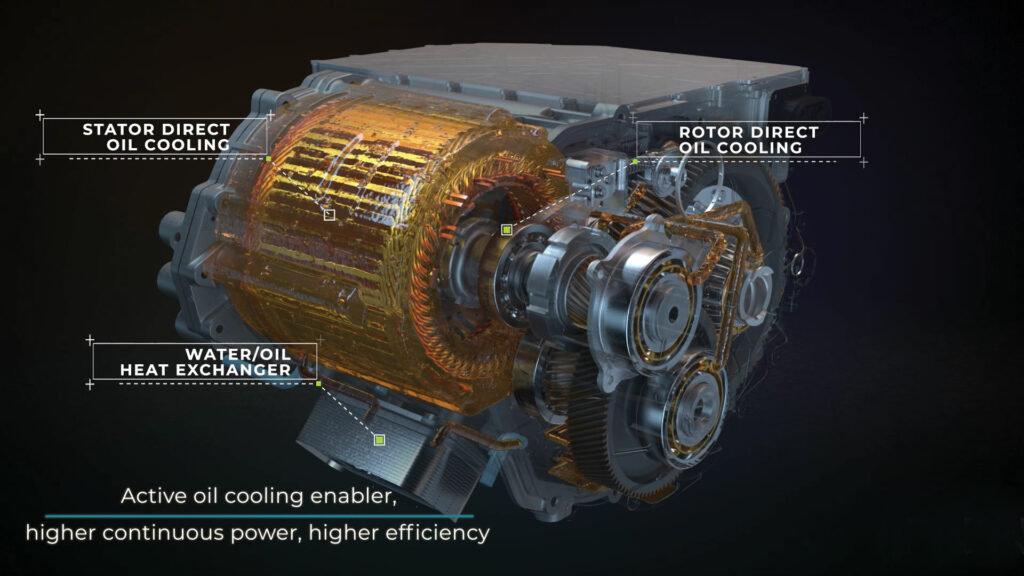
(Image courtesy of Valeo)
E-motor cooling technology is evolving rapidly, as Peter Donaldson finds out
Discussions on thermal management in electric vehicles (EVs) usually focus on the battery because of the risk and potential consequences of thermal runaway. However, keeping motors comfortable in terms of temperature is also crucial to the performance, reliability, efficiency and longevity of an EV’s powertrain. E-motors generate significant heat from resistive losses in the windings, hysteresis and eddy current losses in the stator and rotor cores, and friction in the bearings. Furthermore, power and torque outputs, duty cycles, environmental conditions and location within the vehicle can also combine to make the process of removal of unwanted heat surprisingly complex. Over the past five years, however, the landscape of e-motor cooling technologies has witnessed significant advances.
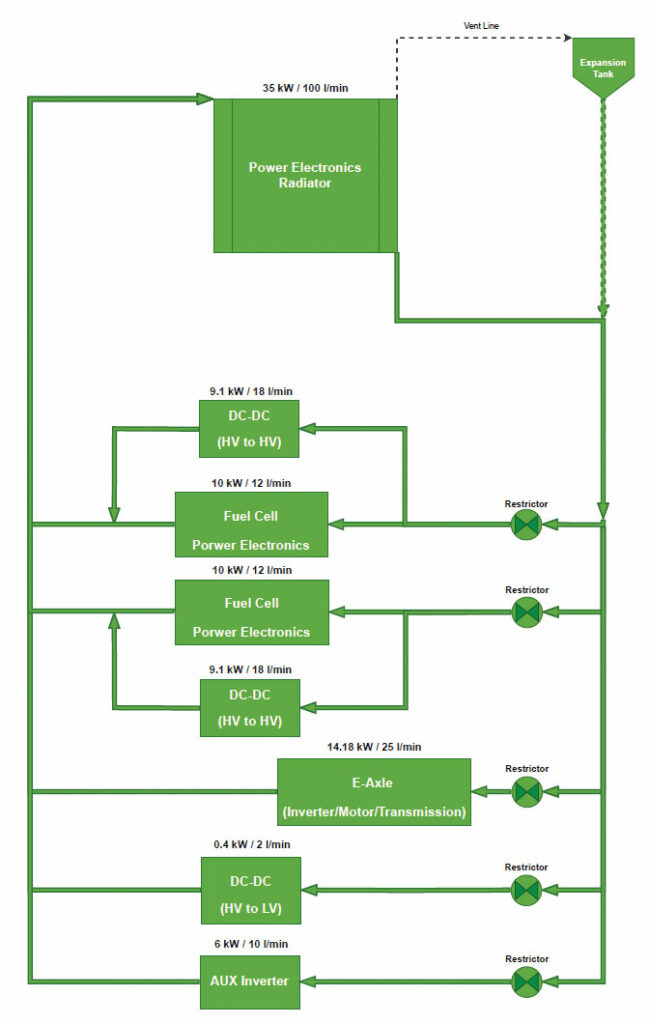
(Image courtesy of Grayson Thermal Systems)
Cool trends
One of the most notable trends is the integration of multiple coolant circuits. Nathan Stephens, chief engineer and head of technology at Grayson Thermal Systems, emphasises that, “The drive to connect EV motor coolant circuits to other coolant loops such as those for power electronics and power distribution into a complete thermal management system is one of the most significant advancements for increasing efficiency and performance.” This integrated approach allows for intelligent heat management, where waste heat can be employed strategically for other purposes. Stephens highlights that such systems “can now harvest the heat generated from EV traction motors and redirect it to the inside of a vehicle to improve passenger comfort.” This reduces reliance on energy-intensive auxiliary heating systems such as heat pumps or electrical heaters, leading to improved energy efficiency and extended driving range, particularly in colder climates.
Parker Lord has focused on enhancing heat transfer at the component level through innovative material science. Business development manager Eric Wyman, points to the significant impact of “end-winding potting with thermally conductive two-component pottants.” This technique involves encapsulating the motor’s end windings with a specialized material that exhibits high thermal conductivity, facilitating a more efficient pathway for dissipation of heat from the windings to the stator housing. Wyman explains that “ensuring efficient cooling of the motor can allow for smaller motors with higher output, saving weight and expense,” because effective thermal management permits higher power densities without exceeding critical temperature limits. This reduction in the size and weight of the motor directly contributes to improved vehicle efficiency and handling.
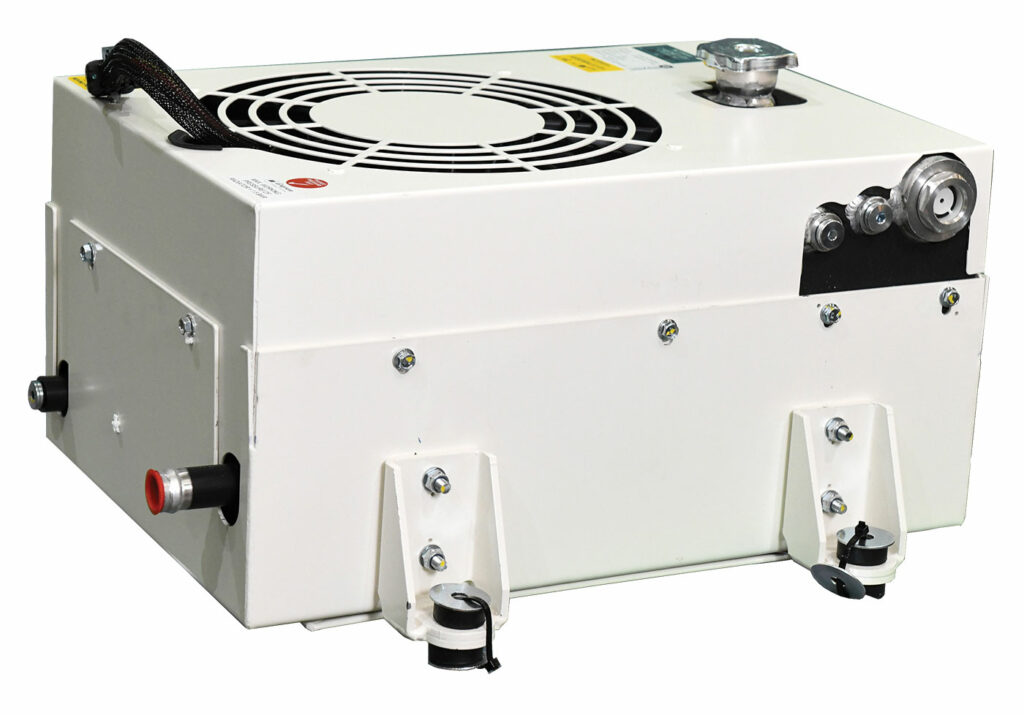
(Image courtesy of Grayson Thermal Systems)
Smaller fluid measures
Sudhi Uppuluri, director of automotive and transportation industry strategy, simulation and testing at Siemens, notes progress in the sparing use of coolants: “One of the key advances that I’ve seen is that the industry has gotten a lot more efficient at cooling the motor with less oil.” A crucial aspect of this involves precise identification and targeting of high-temperature areas within the motor. Uppuluri elaborates on the efforts to “identify where these hot spots are, where we need oil nozzles to spray so that we don’t have temperature disparities that are large enough to cause distortion, all done with a minimum of oil.”
In addition to minimising the amount of coolant and oil within the system, development looks to reduce the complexity of the delivery system through optimising the design, the number and location of nozzles, and the quantity of oil that should be sprayed to ensure sufficient cooling. This meticulous approach is intended to provide effective cooling without unnecessary energy expenditure and while minimising the weight of the cooling fluid.
Targeted cooling
Valeo’s Pascale Herman, director of product planning at the company’s power division, provides a broader perspective on the evolution of motor cooling, highlighting the transition from air and water-jacket cooling toward more direct and efficient methods. She emphasises that “with e-motor speed and power getting higher and higher, cooling becomes more important and challenging for performance.” She adds that getting the cooling medium closer to the hottest areas and shortening heat transfer paths are important trends in motor thermal management, citing slot cooling as an example.
Furthermore, direct oil cooling, where the coolant is in direct contact with the stator windings and even the rotor, has emerged as a significant advancement. Herman explains that this “enables higher power density and continuous power output without overheating” and “reduces motor size and weight by improving thermal management,” ultimately leading to increased efficiency by maintaining optimal operating temperatures. The adoption of direct oil cooling by manufacturers such as Lucid Motors in their compact drive units underscores its effectiveness in achieving high power output in a compact form factor, she notes.
The development and application of advanced coolant materials and nanofluids also represent significant strides forward in motor cooling technology. Herman highlights that the development of high-performance coolants with nanoparticles (such as graphene or alumina) improves thermal conductivity significantly over conventional coolants. This allows for more effective heat dissipation without the need for increased pump size or flow rates, facilitating more aggressive driving without derating, and potentially increasing motor lifespan owing to more stable thermal environments.
Furthermore, the integration of 3D printed cooling channels directly into motor housings or components offers unprecedented design flexibility for thermal management. Herman notes that additive manufacturing enables complex internal geometries for directing cooling channels straight into motor housings or components, which improves surface area contact with the coolant and enables custom-designed flow paths to eliminate hot spots. While challenges related to serial manufacturing costs and mechanical strength – you don’t want too many holes though the material – are still being addressed, this technology holds immense promise for creating highly optimised cooling solutions.
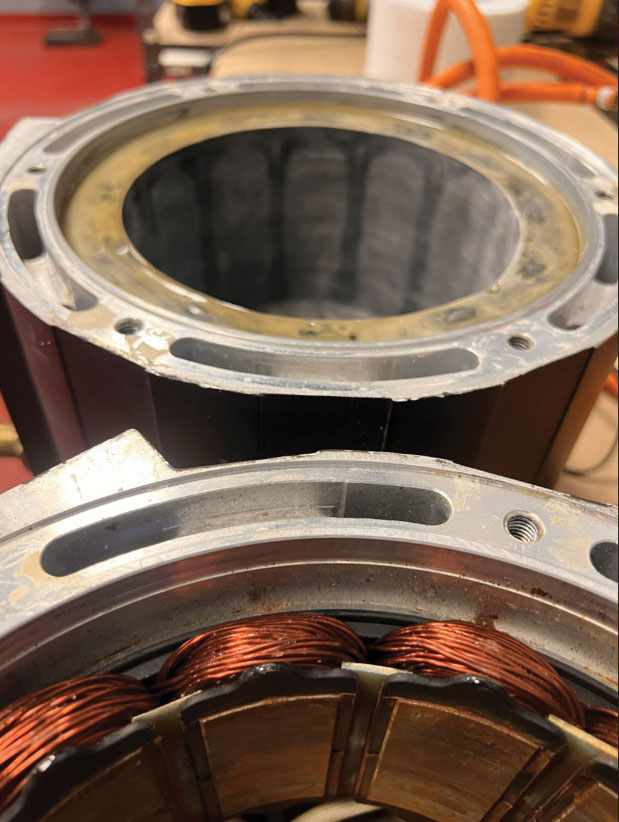
(Image courtesy of Parker Lord)
Hello TIM
Thermal interface materials (TIMs) have also played a crucial role in enhancing heat transfer within e-motors. Herman explains that TIMs “fill microscopic air gaps between two solid surfaces, such as the copper windings and aluminium housings.” By replacing air, a poor thermal conductor, with materials exhibiting higher thermal conductivity, TIMs “help create a smooth thermal path,” thereby improving the overall efficiency of heat dissipation from the motor’s internal components to the cooling system.
Simon Odling, chief of new technology at YASA, details the company’s specific approach to liquid cooling, focusing on an ‘oil-flooded stator’ design. In this configuration, the copper windings are fully immersed in oil within a sealed polymer structure. Odling emphasizes that “it’s all about maximising surface area and contact between, primarily, the copper and the oil, which means we get a very fast cooling effect. So, we can have a very low time constant in terms of thermal mass in the stator and we can get the stator hot or cool very quickly.” The continuous circulation of oil within the stator, facilitated by strategically placed ‘blockers and diverters’ and optimized through computational fluid dynamics analysis, ensures efficient and even temperature distribution, allowing YASA motors to operate at high-performance levels with rapid thermal response.
Achieving optimal performance in EVs hinges significantly on the effective integration of motor cooling systems with the thermal management of other critical components, most notably the battery and the power electronics. This holistic approach presents both substantial benefits and considerable engineering challenges.
Integration pros and cons
Grayson Thermal Systems’ Stephens underscores the economic and weight advantages of integrating cooling circuits: “Integrating motor cooling with other circuits really makes a better cost/weight trade, as there are fewer systems to control.” He points out that the non-constant nature of heat rejection from various components allows for system sizing based on average usage, optimising efficiency. However, a key challenge lies in accurately understanding diverse vehicle use cases to strike the right balance in system capacity, avoiding both undersizing and unnecessary oversizing.
A fundamental hurdle in integration arises from the disparate temperature requirements of different components. As Stephens notes, “power electronics coolant can run at hotter temperatures of up to approximately 60 C; battery coolant requires colder temperatures of up to approximately 30 C.” This temperature differential prohibits direct connection of these circuits. Nevertheless, innovative integration strategies, such as Grayson’s chassis-mounted complete thermal management system (CTMS), do offer solutions. The CTMS intelligently manages heat transfer across power electronics, the traction motor, battery coolant, and cabin HVAC system, optimizing energy flow and reducing refrigerant usage, Stephens says.
Parker Lord’s Wyman emphasises the synergistic benefits of including the motor in a shared cooling loop, particularly when utilizing potting techniques to connect end windings to a liquid-cooled housing. This integration “allows the motor to get maximum cooling from the same cooling system, which may reduce weight and complexity versus a non-integrated system,” he says.
Uppuluri highlights the complexities of physical integration, especially the tightly packaged arrangement of the inverter, motor, and gearbox. Heat transfer occurs bidirectionally between these components, necessitating careful thermal management considerations. Furthermore, the heat extracted from the motor by the coolant needs to be managed effectively within the broader vehicle thermal architecture, the expert from Siemens says. He explains that the existence of multiple cooling systems with distinct temperature ranges in hybrid vehicles−a hot loop for the engine, a medium-temperature loop for the motor, and a very low-temperature loop for the battery−often mandates the integration of a chiller. While these loops operate at different temperatures, the capacity for strategic exchange of heat between them is crucial for overall system efficiency, such as warming a cold battery using waste heat from the motor or engine, he says. This necessitates sophisticated valving and control systems to direct heat flow based on operating conditions.
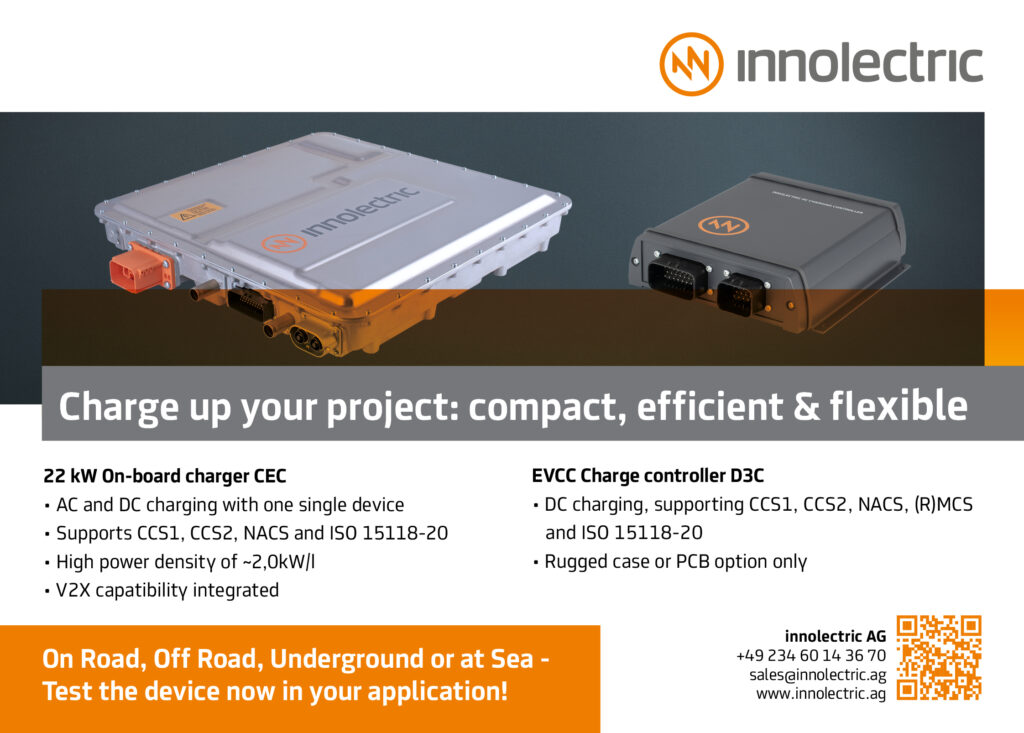
“Thermal management has to be considered at vehicle level, encompassing the battery, e-motor and power electronics as well as the air conditioning needs for cabin comfort,” according to Valeo’s Herman. What she terms global optimisation yields several crucial benefits, including enhanced system efficiency and energy optimisation by ensuring all heat-generating components operate within their ideal temperature ranges, preventing wasteful overcooling or undercooling. Integrated thermal management also contributes to improved component lifespan and reliability by preventing hotspots and enabling predictive thermal control. Furthermore, combining cooling loops can lead to packaging and weight efficiencies by removing redundant parts and reducing space usage. During high-demand scenarios like fast charging or hard acceleration, an integrated approach avoids thermal bottlenecks that could limit performance or trigger safety shutdowns, she adds.
However, achieving effective thermal system integration presents significant challenges. Conflicting thermal needs, with batteries preferring temperatures cooler than those suitable for motors and inverters, necessitate careful management through multi-zone or staged cooling strategies. Increased system complexity, involving more valves, sensors, pumps and control logic raises the risk of failure and demands sophisticated thermal controllers. Eliminating heat transfer imbalances, where one component might experience rapid heat spikes while others remain cool, requires dynamic cooling management. Packaging constraints within the tight confines of the vehicle architecture pose a significant design problem. Finally, coordinating thermal control across multiple electronic control units requires complex algorithms that respond to various driving conditions and load profiles. Herman cites Tesla and Chery (with Valeo’s thermal management module) as examples of effective integration, using central thermal control units and active valves to manage coolant flow and temperature across different components.
YASA’s Odling reinforces the criticality of vehicle-level integration for efficient EVs and hybrids. He notes that vehicle manufacturers typically employ a water–glycol system as a single thermal management solution for battery, power electronics, and the entire electric drive unit (EDU), including the motor. This creates a two-way interaction, where the motor’s inlet coolant conditions are defined by the vehicle’s thermal management system, while the heat rejected by the motor significantly impacts the vehicle’s overall thermal load.
In many modern EDU designs, particularly for axle and hybrid applications, fluids are shared between systems, such as the motor oil also lubricating the gearbox. This necessitates comprehensive understanding of the thermal loads from both the motor and the transmission losses to effectively manage the heat rejection back to the vehicle’s heat exchanger and, consequently, the cooling strategy for the battery, cabin and other systems.
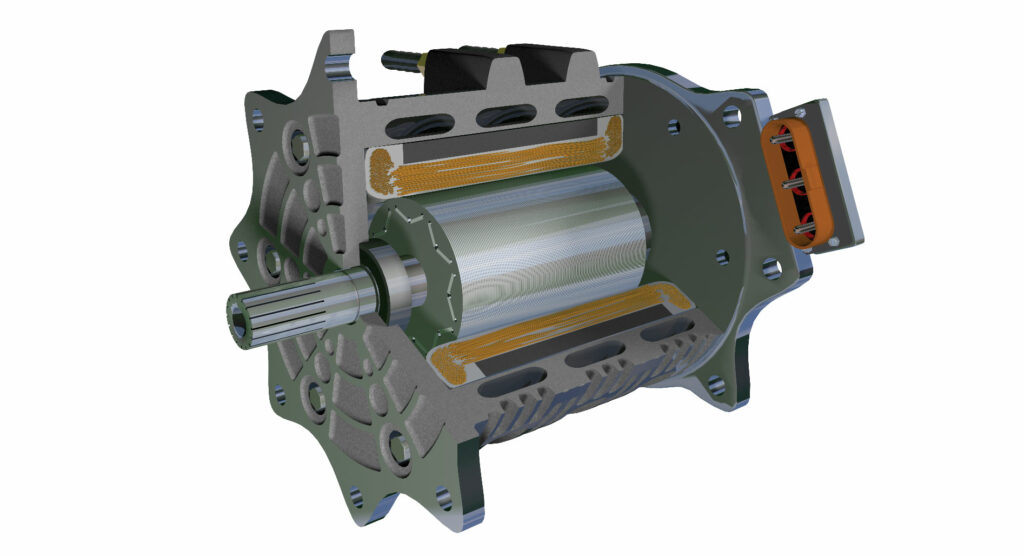
(Image courtesy of Parker Lord)
TIMs in motors
Albeit often unnoticed, TIMs play a crucial role in the efficient operation of EV motor cooling systems. These materials are placed strategically between surfaces that need to transfer heat, such as between the motor windings and the stator housing, or between the power electronics and their heat sinks. Their primary function is to fill the microscopic air gaps that exist between even seemingly smooth surfaces. Air is a poor conductor of heat and so replacing it with a thermally conductive TIM significantly enhances the rate at which heat can be dissipated away from heat-generating components.
Grayson’s Stephens highlights the dual functionality that some advanced TIMs, particularly phase change materials, can offer: “Phase change materials that can do solid to liquid perform the dual role of absorbing and rejecting heat, thus being both the heat exchanger and coolant transfer liquid.” This ability to absorb heat during periods of high load and then release it as the system cools can help buffer temperature fluctuations and maintain more stable operating conditions.
Advances in TIMs focus on balancing acts such as achieving high thermal conductivity without compromising other key properties. Parker Lord has developed products with high thermal conductivity combined with relatively low viscosity that allow better heat rejection without sacrificing end-winding fill, Wyman explains. This is particularly important in areas with complex geometries, ensuring that the TIM can effectively penetrate and fill all the necessary spaces to maximise thermal contact.
A critical characteristic of TIMs is the heat transfer coefficient, which dictates how effectively heat moves from the motor to the cooling fluid. A higher heat transfer coefficient means that less coolant flow is required to remove the same amount of heat. This, in turn, leads to a lighter system with reduced consumption of energy by the coolant pump and lower windage losses within the motor.
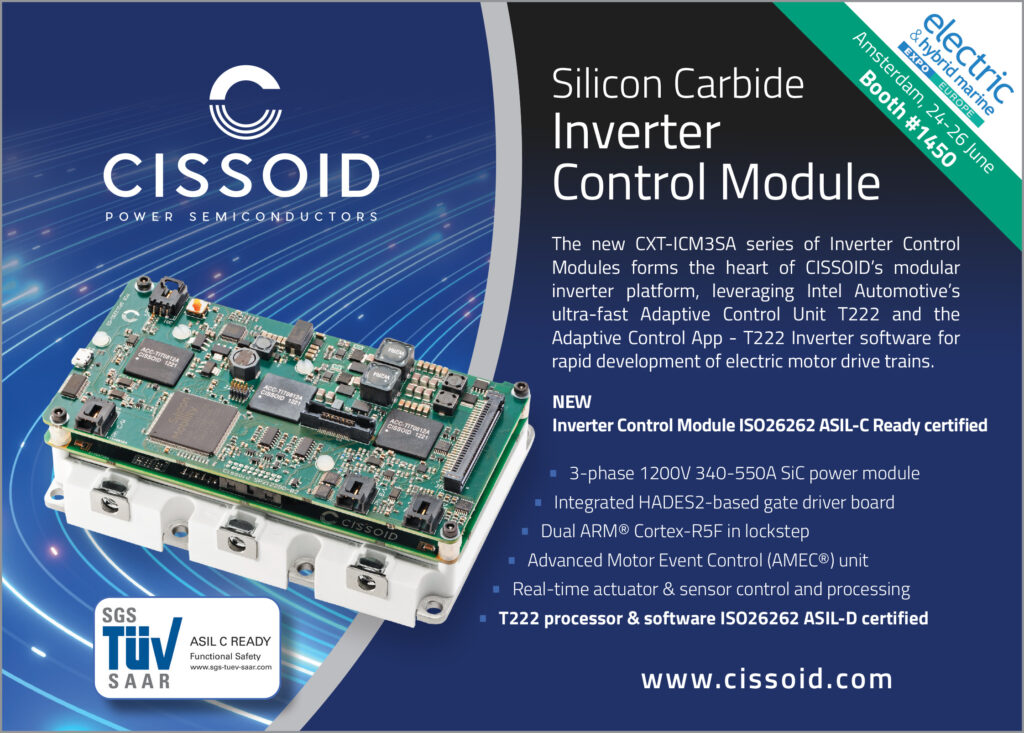
Herman describes advanced TIMs as “the thermal glue that keeps everything running cool and smooth,” emphasising that “better TIMs mean better heat flow, better performance and longer-lasting EV motors – all without major changes to system architecture.” Valeo’s expert outlines several common types of TIMs used in EV motors, including thermal greases and pastes for tight surfaces, gap fillers for uneven surfaces, phase change materials, thermal adhesives for bonding, and thermally conductive foams or pads for larger interfaces.
The benefits of advanced TIMs are manifold. Firstly, they offer higher thermal conductivity. She notes that new TIMs incorporating advanced fillers like boron nitride, graphene, carbon nanotubes and ceramic nanoparticles can achieve thermal conductivities of 10 W/m·K or higher; a significant improvement over older compounds. This enhanced heat flow leads to lower operating temperatures and higher power output. Secondly, they provide improved mechanical properties, such as being softer, more compliant, or electrically insulating, thereby allowing them to withstand vibration, expansion and contraction without degrading thermal performance. Thirdly, modern TIMs offer easier application in manufacturing through pre-formed pads, dispensable pastes or curing compounds that are compatible with automated processes, reducing production time and defects, she explains. Finally, many advanced TIMs offer electrical isolation with thermal conductivity, which is crucial in high-voltage EV systems, enabling compact motor–inverter integration without compromising safety.
Herman also highlights the adoption of advanced TIMs by leading EV manufacturers such as Tesla, Lucid Motors and BMW in their motor housings to enhance thermal management. Tesla utilizes high-performance gap fillers and thermal pastes to optimize heat dissipation from the stator to the housing. Lucid Motors, with its power-dense drive units, likely employs custom-designed TIMs, potentially including phase change materials or liquid-dispensed thermal gels, to manage the high heat loads generated by high-speed operation. BMW incorporates thermally conductive adhesives and gap pads in their motors, emphasizing durability for modular motor construction.
Odling connects the benefits of TIMs to the challenges of heat transfer in conventional radial flux motors. He explains that in such motors, heat must travel through multiple interfaces – from the copper windings to the stator iron and then to the cooling jacket – with each interface presenting thermal resistance. By using a thermal medium such as a high thermal conductivity polymer to intimately fill the space around the copper windings, heat can be transferred to the stator more quickly, YASA’s expert notes. Similarly, a good thermal interface between the stator iron and the cooling jacket can further reduce the overall thermal resistance, leading to lower operating temperatures in the core of the motor that, in turn, enable improved performance. While axial-flux specialist YASA’s current market motors do not require TIMs owing to their direct cooling approach, they are actively exploring the use of TIMs between the copper and iron in future high-power density designs to further enhance thermal management within the stator.
In a potted motor, heat flows from the stator core toward the end windings and out through the potting and housing, not into the back iron as is often assumed. Since stator slots already contain thermally conductive copper, fully potting them is unnecessary for effective cooling, says Parker Lord’s Wyman.
Stephens explains that electric motors operate most efficiently at their nominal rpm range. During high-speed driving, however, motors often run closer to their maximum rpm, leading to reduced efficiency and a greater proportion of the electrical energy being converted to heat. Using the example of a 100 kW motor operating at 85% efficiency, Grayson’s expert points out that a significant 15 kW of heat is generated. To effectively dissipate this heat, it is crucial to specify coolant flow rates that are high enough to transfer the heat without excessive temperature differentials within the coolant, but not so high as to cause significant pressure drops across the motor’s cooling channels.
Peak heat
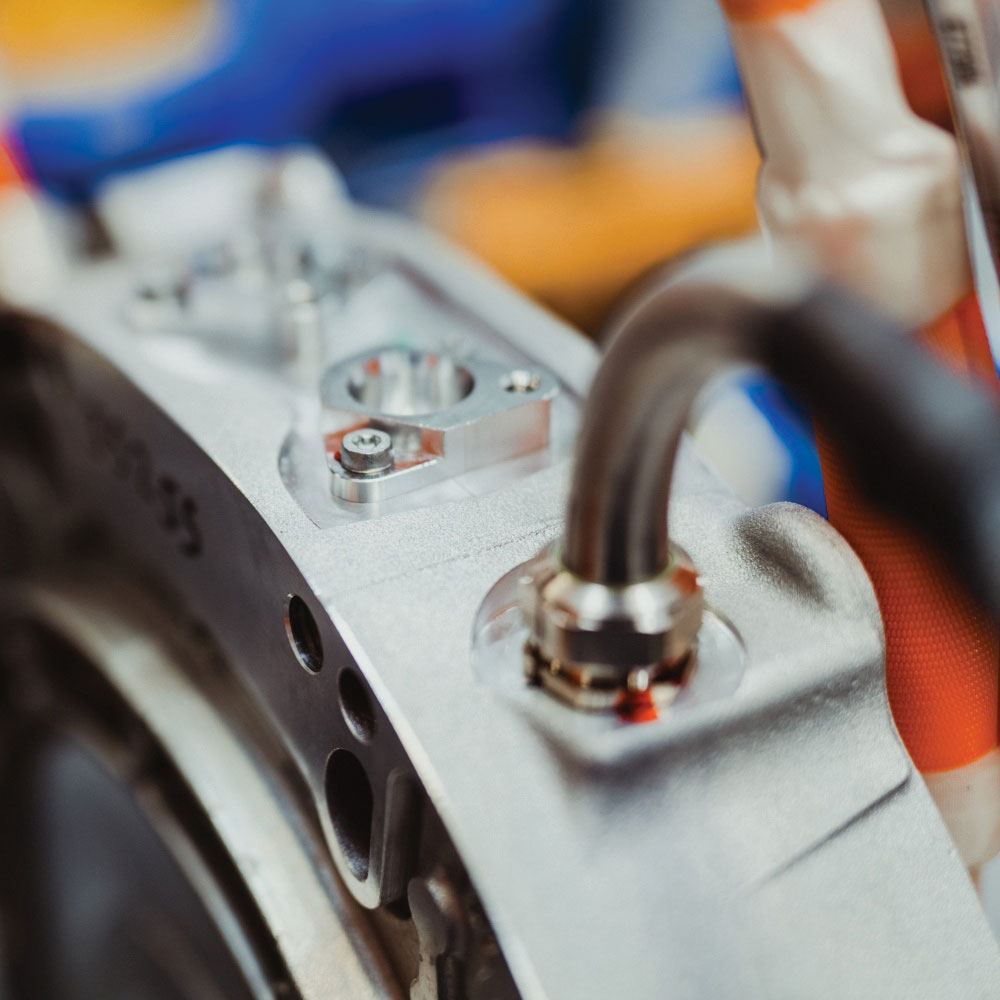
(Image courtesy of YASA)
While fast charging is primarily a thermal challenge for the battery system, as Siemens’ Uppuluri notes, it can indirectly impact motor performance, particularly during regenerative braking. Although regenerative braking events are typically short cycles, they can generate substantial heat within the motor. However, Uppuluri suggests that the transient nature of this heat generation might not always necessitate immediate intensive cooling, because the coolant temperature might experience only a temporary rise. The more critical thermal challenge for batteries during fast charging lies in the sustained high level of power input over extended periods, leading to significant heat build-up that requires robust cooling solutions to prevent derating and prolonged charging times.
For high-performance motors themselves, Uppuluri revisits the fundamental choice between air and liquid cooling. While lower-powered motors can often be adequately air-cooled, high-performance applications invariably require more sophisticated liquid cooling systems, potentially even incorporating air-conditioning chillers to maintain optimal operating temperatures. In this realm, performance takes precedence, often in lower-volume, high-margin vehicles such as sports cars or luxury models. This allows for implementation of more intricate and costly cooling systems with complex cooling channel geometries and additional heat exchangers to ensure uniform temperature distribution.
Valeo’s expert outlines specific challenges in high-performance EV cooling. Heat accumulation during continuous high-speed driving in the motor and power electronics, coupled with heat generation in the battery during fast charging, can push the entire system toward critical temperature thresholds. Furthermore, component interaction poses another challenge because the thermal loads of the motor, power electronics and battery can influence each other, making it difficult to optimise cooling for each component individually. For instance, a hot motor can negatively impact the cooling efficiency of the battery if they share thermal management resources.
To address these challenges, Herman emphasises holistic thermal management, employing integrated systems with multi-loop cooling circuits dedicated to the motor, battery and power electronics. These advanced systems often feature adaptive cooling, where coolant flow rates and temperatures are adjusted dynamically based on real-time data from thermal sensors. Cooling system integration, where cooling channels are shared strategically between components like the motor and the inverter can also improve overall system efficiency. Finally, advanced heat exchangers, such as multi-layered or hybrid air–liquid systems, can more effectively manage heat from diverse sources.
Odling focuses on the perspective of the motor in high-performance scenarios, emphasizing the challenges posed by repeated acceleration cycles and long-duration high-speed runs, especially when followed by rapid charging without an adequate cool-down time. These continuous operating demands are critical performance metrics for high-performance vehicles.
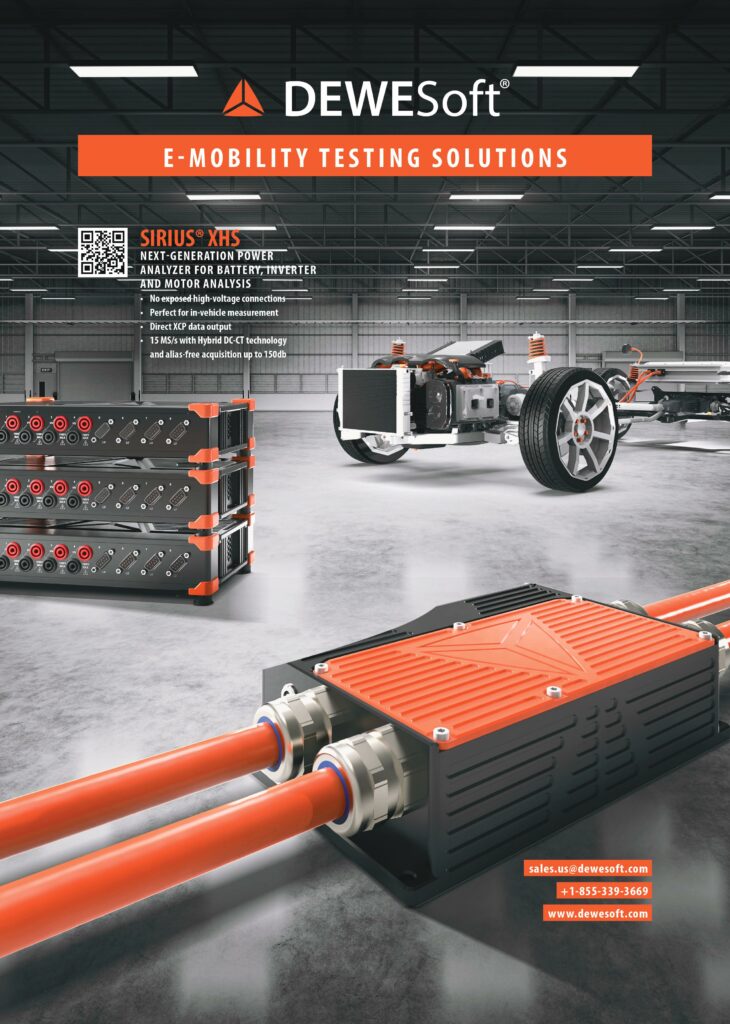
Cooling with AI
Rapidly becoming ubiquitous, artificial intelligence (AI) is beginning to impact motor cooling with, for example, generative AI now creating elaborate and very efficient paths for fluid channels within motor housings and cooling plates, Uppuluri notes, cautioning that ensuring they are manufacturable at a cost appropriate to the application is crucial.
Also, he expects that AI will help significantly with overall motor design, particularly in optimising a system with several variables, such as the number of windings, the size of the air gap between rotor and stator, the number and position of nozzles for directing cooling oil flow. “Optimising across all of this without the acceleration from AI takes a very long time,” Siemens’ expert says.
Herman adds that AI will support multi-physics coupled simulation tools for generative design, taking magnetic, mechanical, noise–vibration–harshness and thermal behaviour into account. Ultimately, AI and machine learning, she says, will revolutionise EV motor thermal management by offering predictive cooling strategies, in addition to predictive diagnostics and optimisation of energy use.
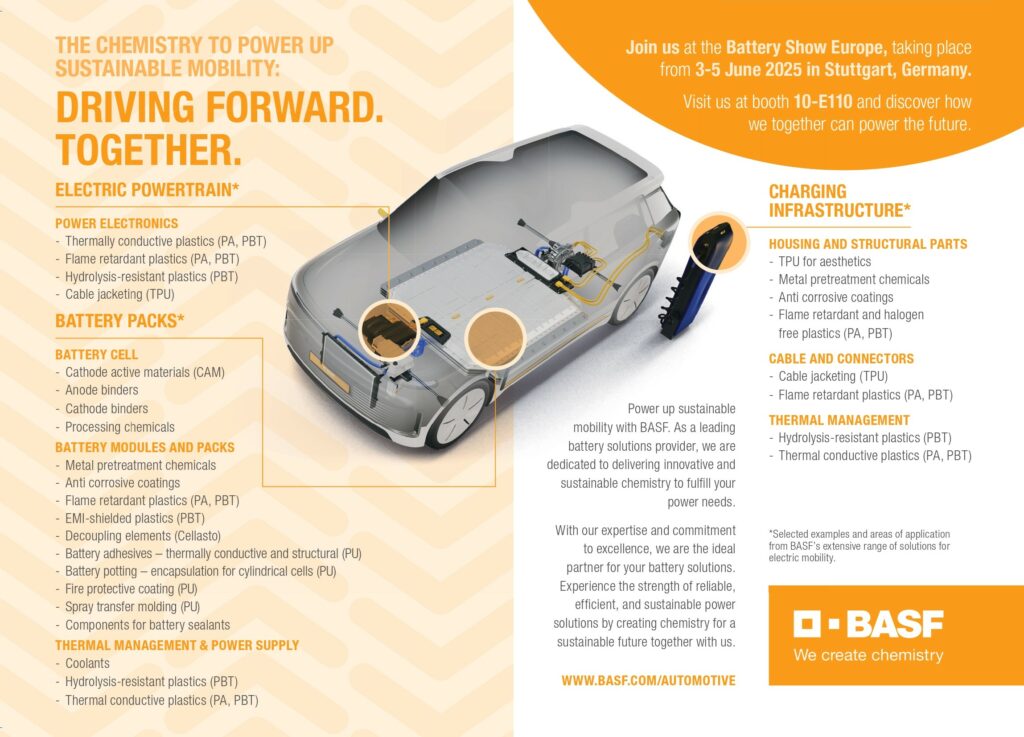
Electrohydrodynamics and ‘superconductivity’
More broadly, Herman anticipates that the next decade or so will be shaped by the emergence and maturing of new technologies. One of these is electrohydrodynamic (EHD) cooling, which uses electric fields to drive the flow of fluids or gases at the microscopic level, thereby enhancing heat transfer, particularly in motors and power electronics. Developed to cool electronics, EHD cooling does not need mechanical pumps, meaning that it could enable simpler and more reliable systems capable of highly targeted cooling in areas with concentrated heat generation, such as motor windings. Without mechanical parts, EHD cooling could also reduce the overall energy consumption of thermal management systems.
However, significant challenges remain, notably the current low efficiency of EHD cooling when scaled up for larger systems such as EV motors and batteries. Moreover, the technology is still in the early stages of r&d, requiring further maturation before it can be considered viable for mass-market applications, Herman cautions.
Another emerging technology is thermally ‘superconductive’ cooling systems based on graphene and/or carbon nanotubes. Both offer disruptive potential for EV thermal management by virtue of their exceptionally high intrinsic thermal conductivities, she emphasises. Their superior mechanical strength and flexibility compared with established heat transfer materials allow for integration into complex geometries, and provide enhanced durability under vibration and thermal cycling. Furthermore, the ultra-thin and lightweight nature of graphene could lead to highly efficient and compact coolers for use in space-constrained motor housings.
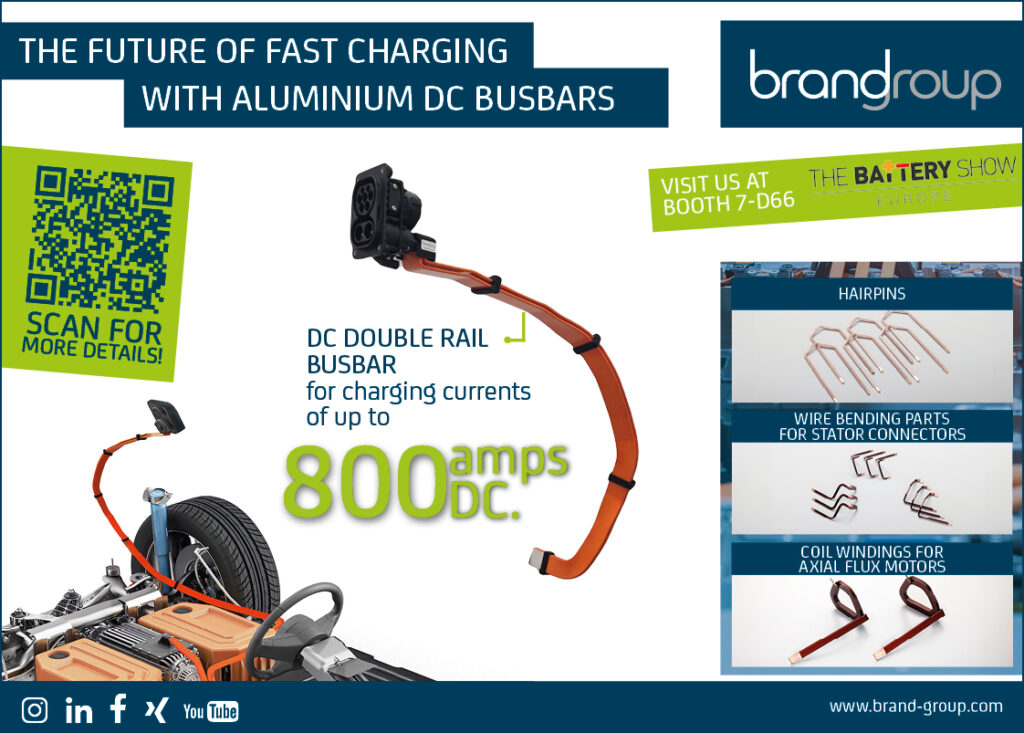
Click here to read the latest issue of E-Mobility Engineering.
ONLINE PARTNERS
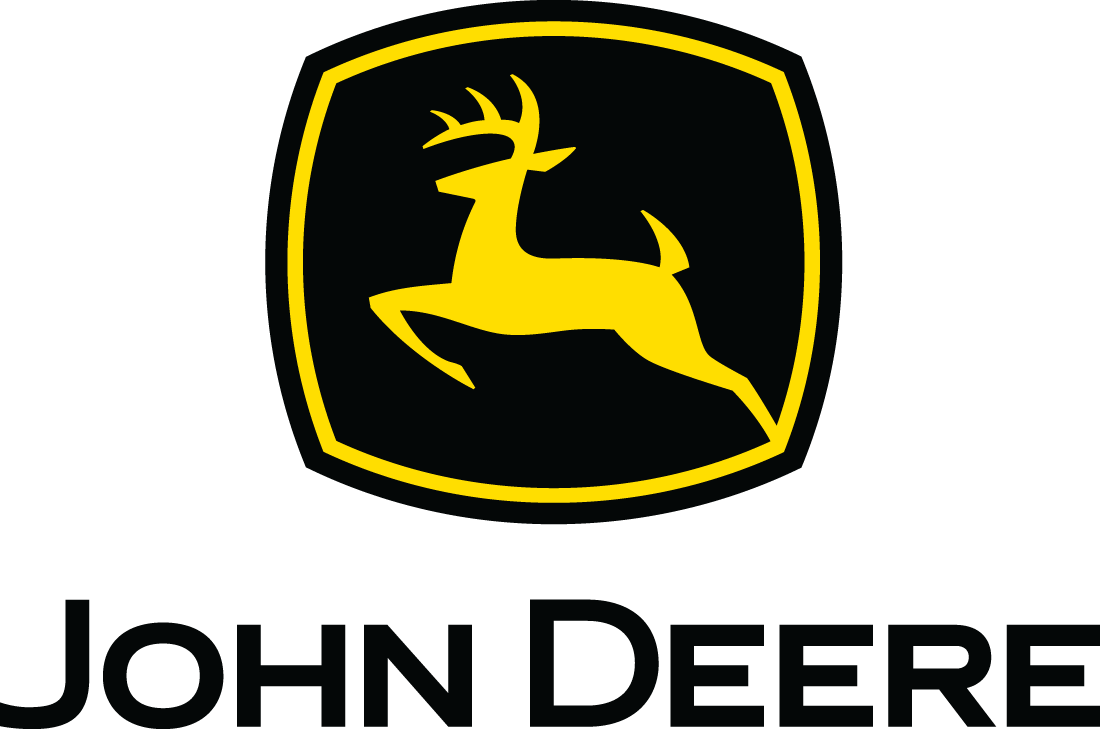
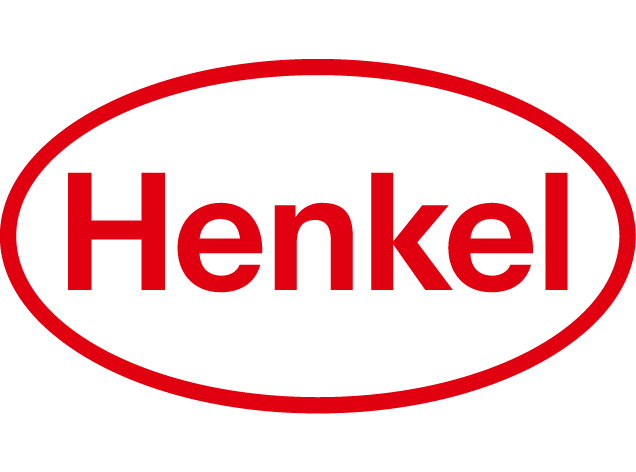
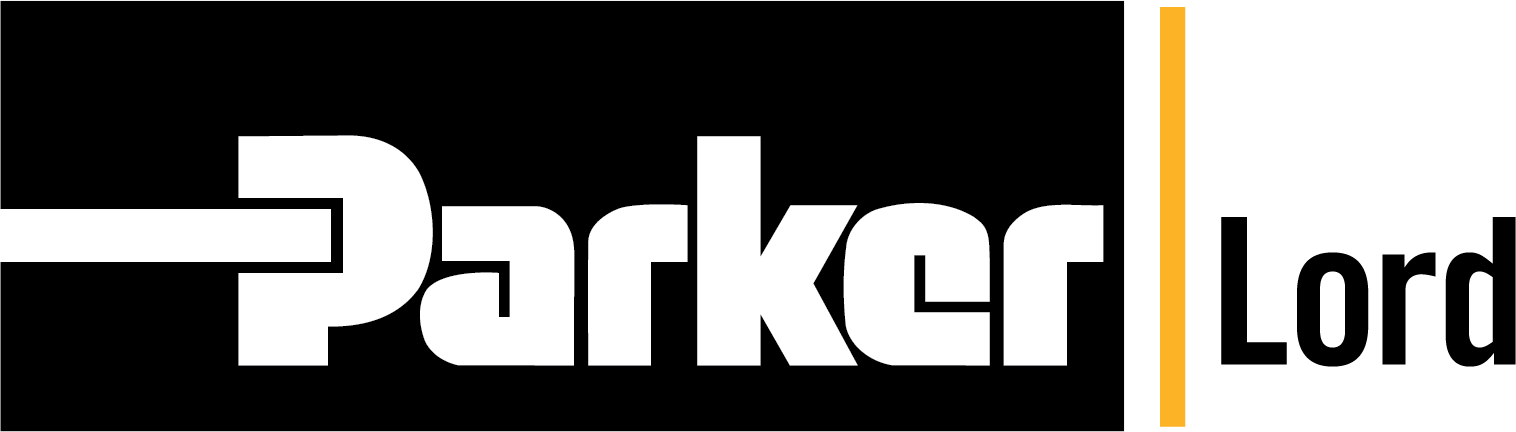
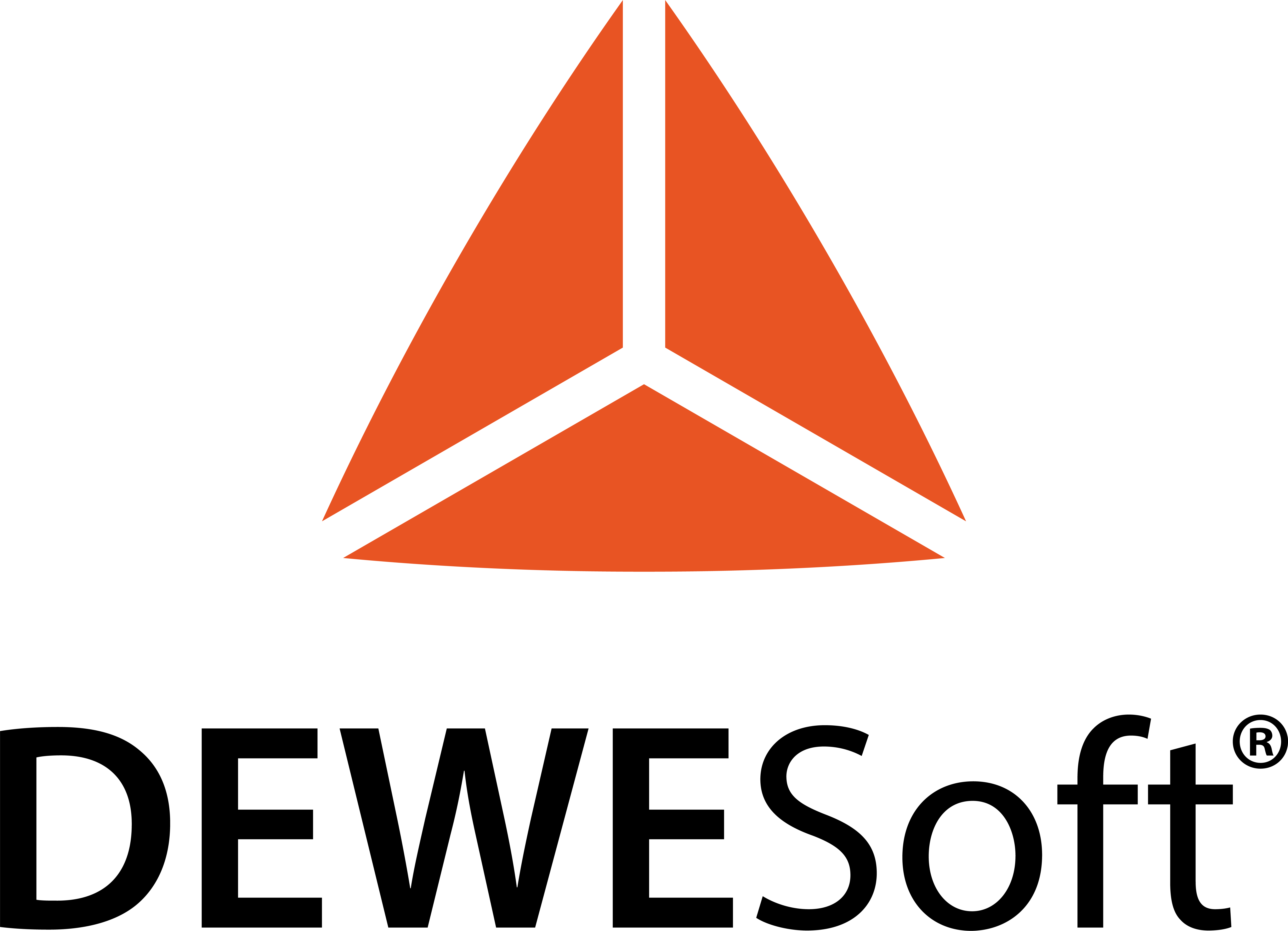
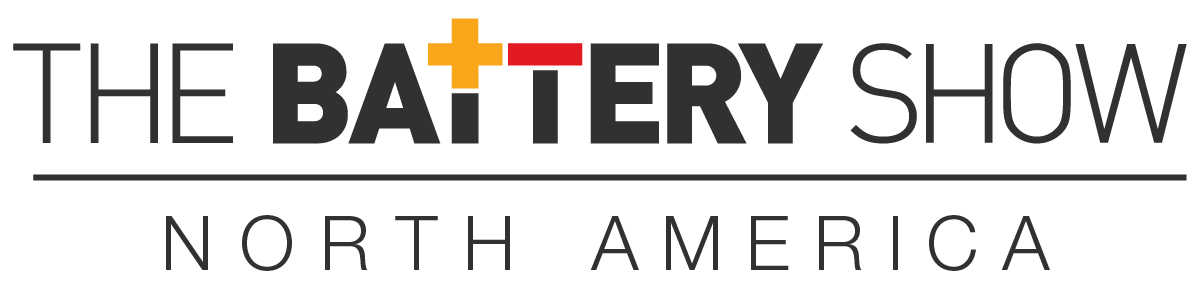
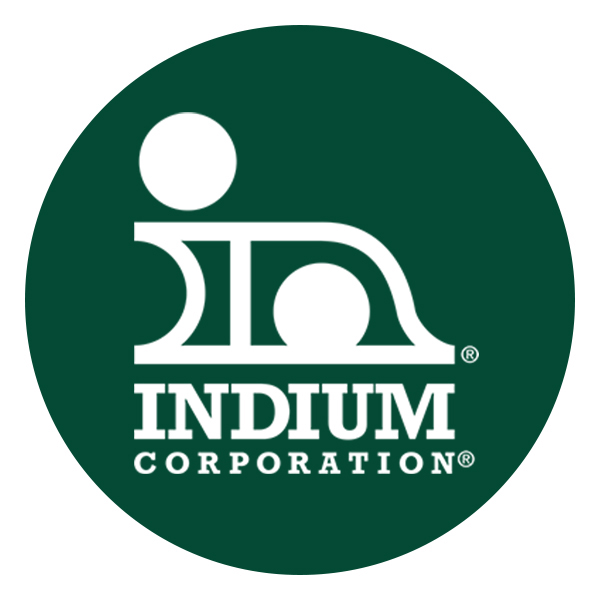
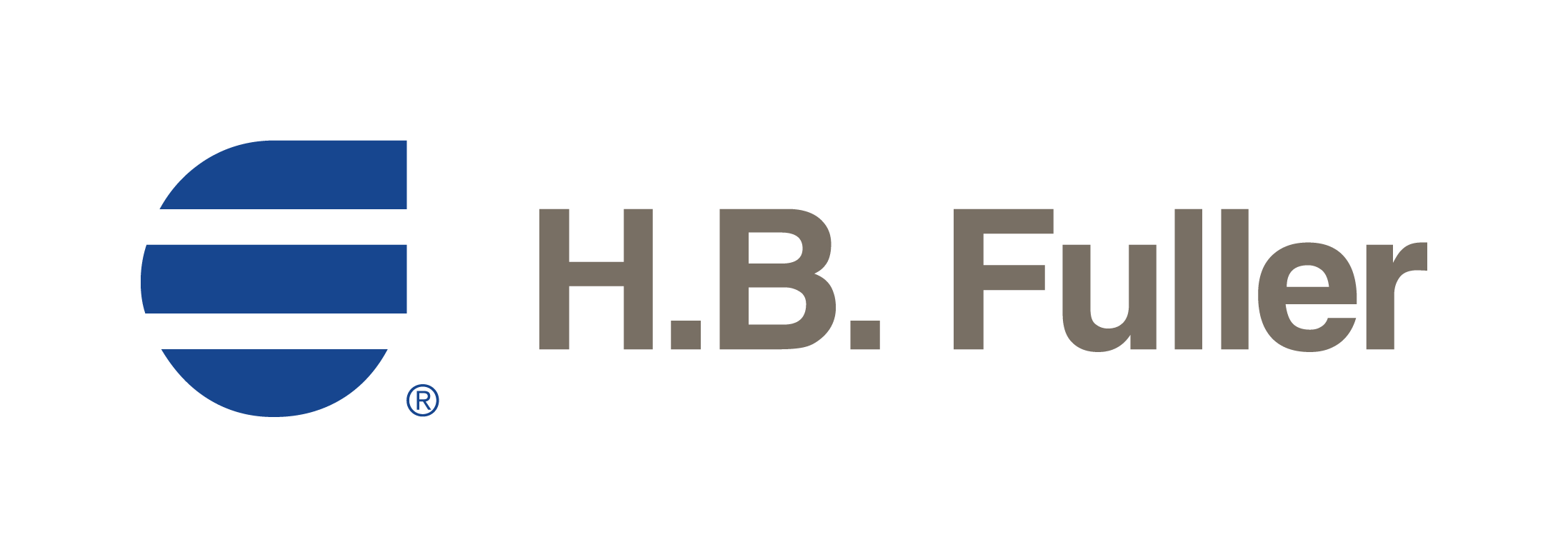
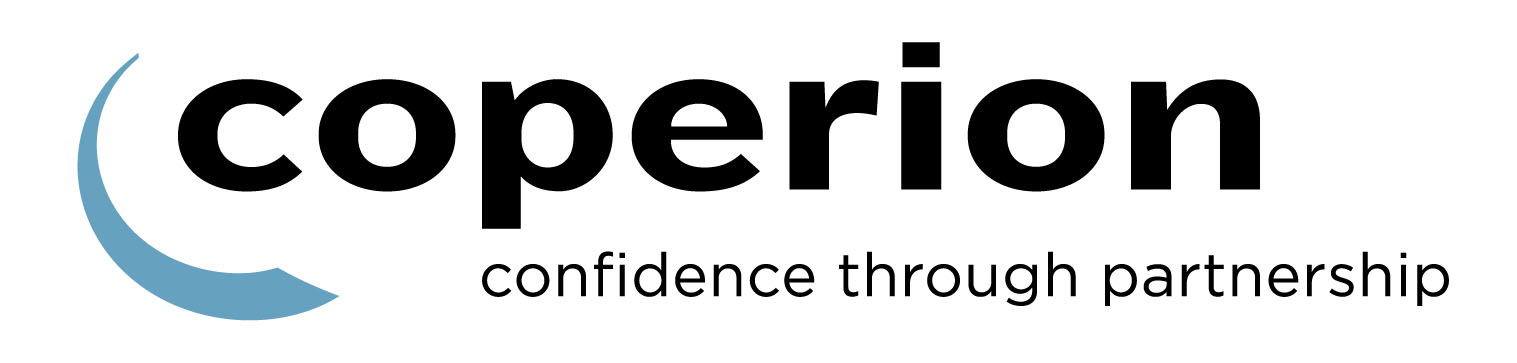