Busbar connector alternative to electroplating
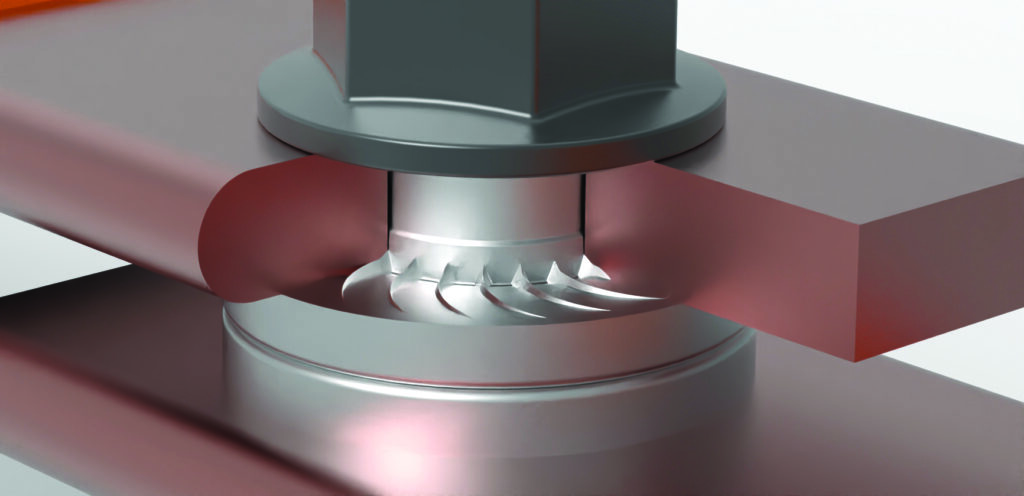
(Image courtesy of Penn Engineering)
Penn Engineering has developed a new technique to reduce the cost of busbar connections in electric vehicles, writes Nick Flaherty.
“The challenge is how to connect busbars,” says John O’Brien, global technologist at Penn Engineering. “One of the things we have seen is a move from cabling to busbars, driven by cost. Busbars are much cheaper for the same current than cables and more suited for automated assembly, which also gives lower cost.”
Electroplating with silver is adopted to reduce the electrical resistance of high-current busbar-to-busbar connections. However, electroplating can be expensive for aluminium and often requires that the busbars be shipped to an external electroplating supplier, and there is also the increasing cost of the silver to consider.
“We like silver for plating but it is too expensive as a conductor as you can end up plating a larger area than you need,” O’Brien says.
“So instead of the electroplating, we use the eConnect bushing that we have developed. This is an eyelash-shaped knurl that pierces the oxide layer. This is very effective on copper busbars and essential for aluminium,” he continues.
Bushing using a tapered shank gives good connectivity through a hole punched in the busbar, which is formed in a simple preparation process using a die press. A two-stage punch flares the hole on the reverse side. So, if the busbars are manufactured by an external company, they can also install the bushing at the same time, and it can all be installed in the press. Once the bushing is installed, it is used as an electroplated busbar without having to transfer it to an electroplater and back again.
The resistance of a single 100 mm2 copper busbar is 16 µΩ providing the theoretical minimum value. A punched hole with a loose connection has resistance of 105 µΩ, while electroplating the two busbars brings this down to 20 µΩ; with bushing, the resistance is also 20 µΩ.
With aluminium, the oxide is more of an issue because this increases the resistance. The resistance of a plain aluminium busbar is 26 µΩ, while that of a punched hole with a loose connection is a massive 397 µΩ. Electroplating with silver brings this down to 35 µΩ, which is the same value as that achieved with bushing. However, having to use cleaning and electrical grease means that the value is actually 63 µΩ.
“This means you are never getting down to 35 µΩ, and this puts engineers off using aluminium as a material. Electroplating aluminium with silver is also not very common because it can be quite tricky,” says O’Brien.
“Our parts are a copper alloy that’s silver plated, and we also offer tin and nickel plating for budget consideration or to minimise galvanic corrosion.”
The standard bushing is rated at 500 A. In testing, it takes 500 A with a temperature rise of 30 C. “We do 1008 cycles with 45 min on, 15 min off at 500 A. This gives a temperature response curve and test electrical resistance with a 3000 A DC power source. The temperature was cycled from −40 to +125 C for 100 cycles, monitoring the resistance of the junction because sometimes there is a loss of continuity, and this monitoring had half a microsecond resolution.
“The aluminium busbars are also tested at 175 C to make sure there isn’t oxide growth.”
Penn is also working on a calculator to determine the cost savings of using bushing because this varies depending on the type and volume of the busbars.
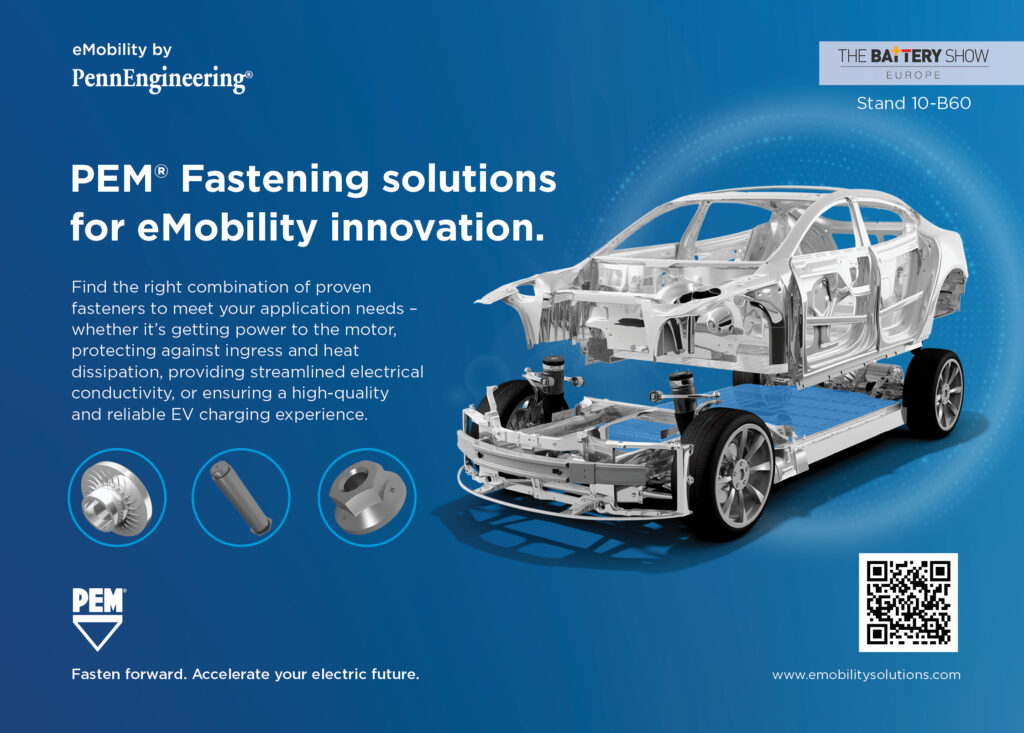
Click here to read the latest issue of E-Mobility Engineering.
ONLINE PARTNERS
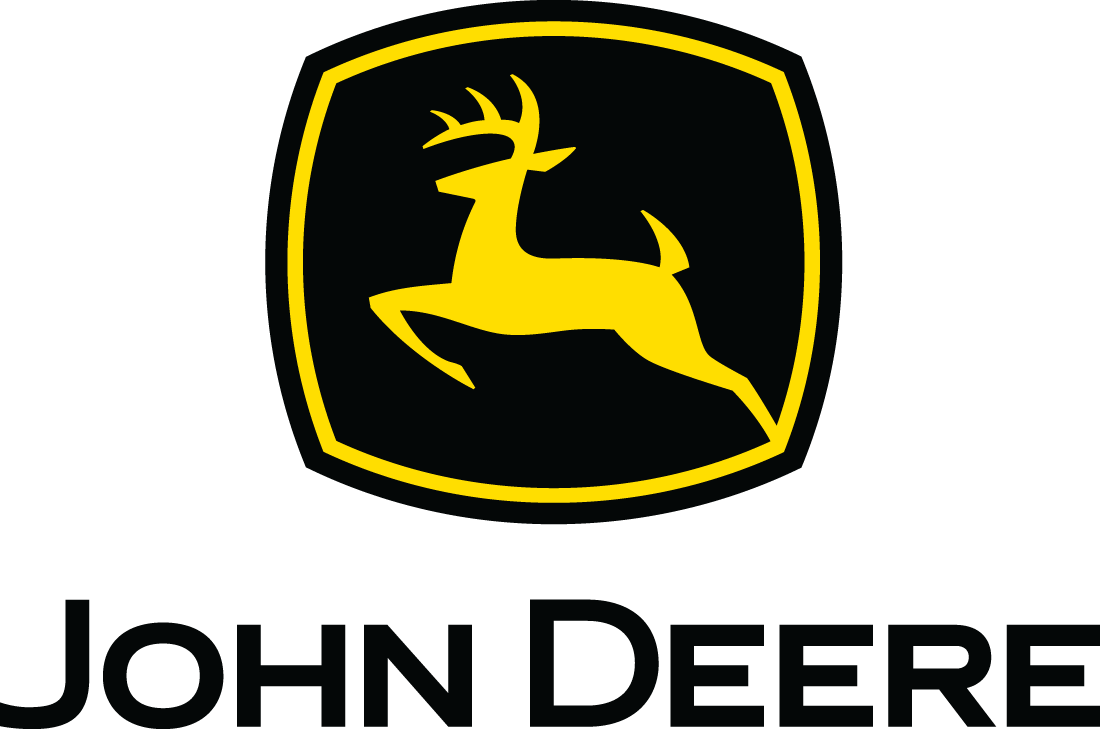
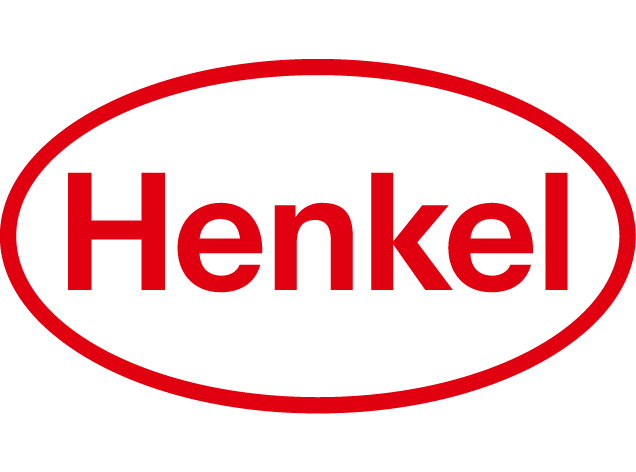
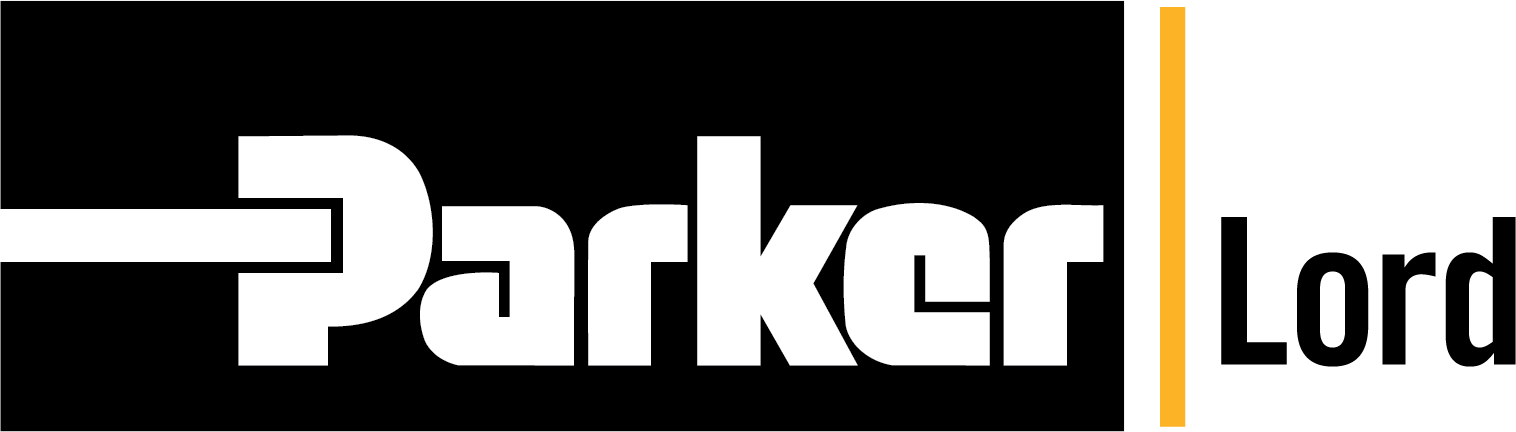
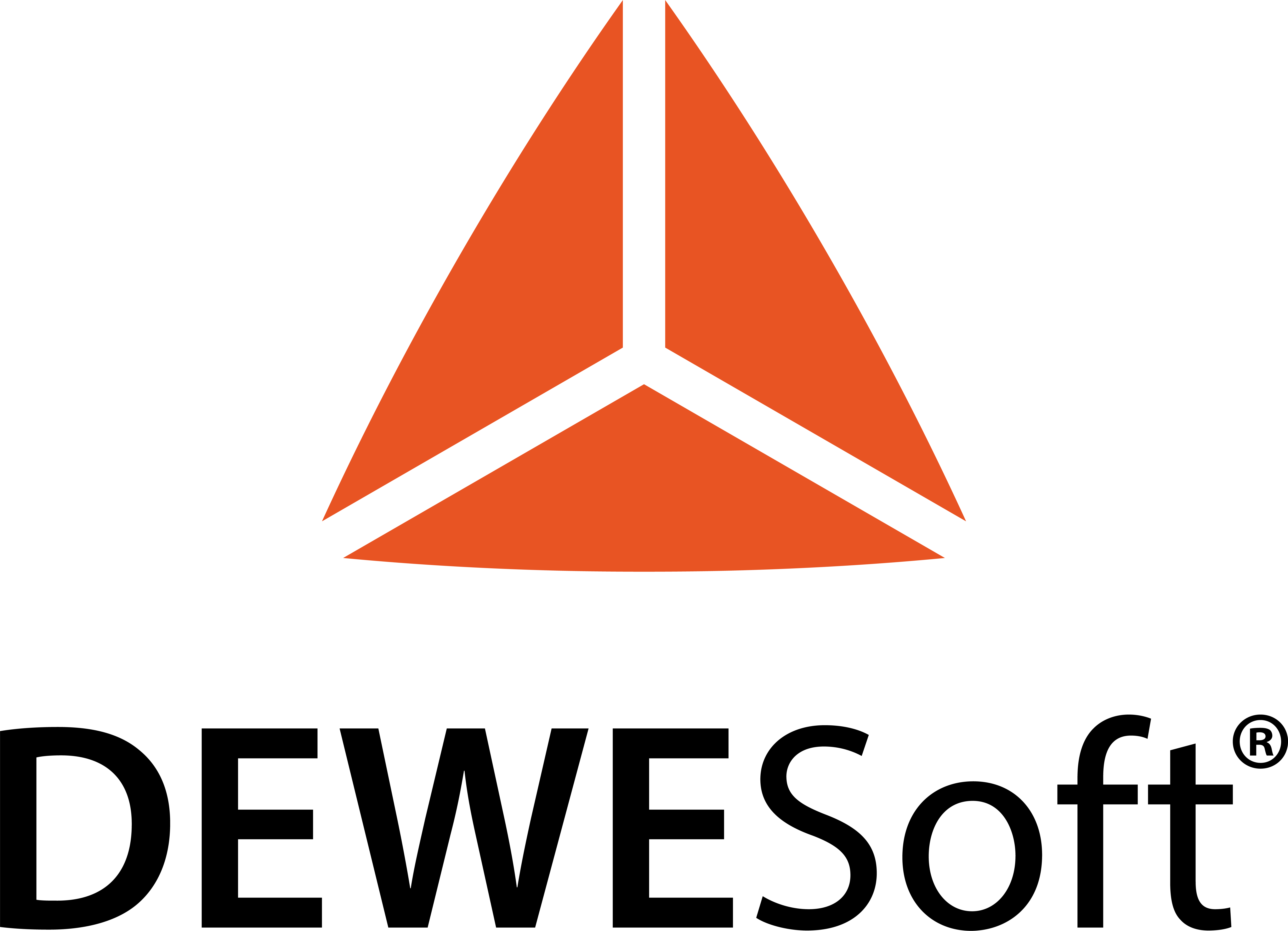
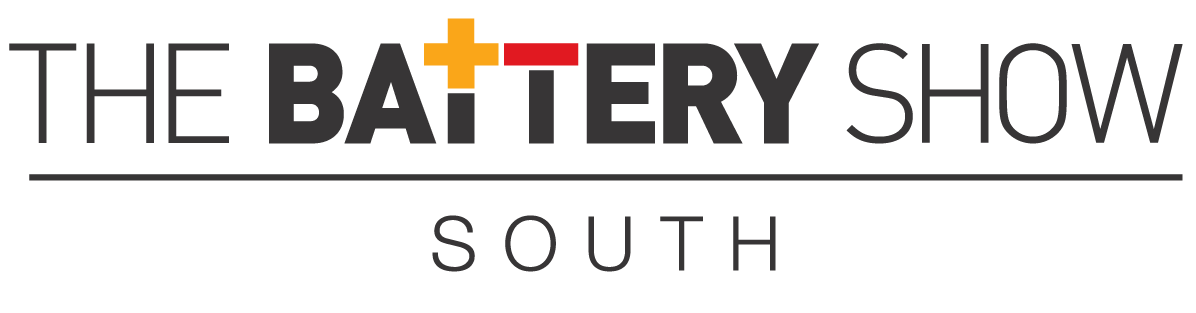
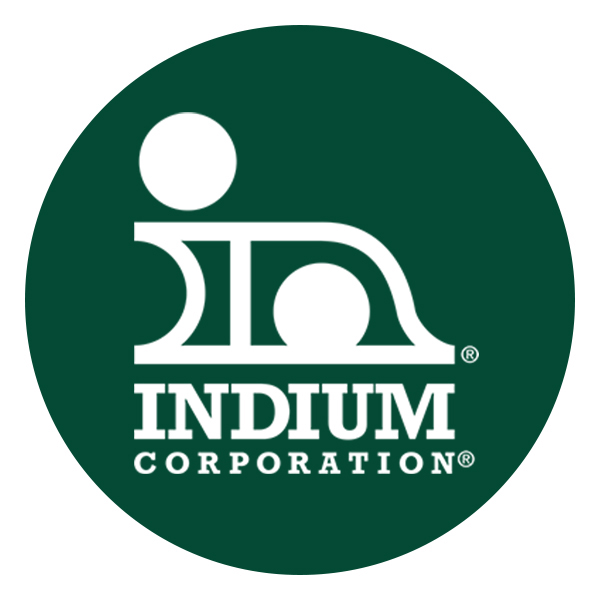
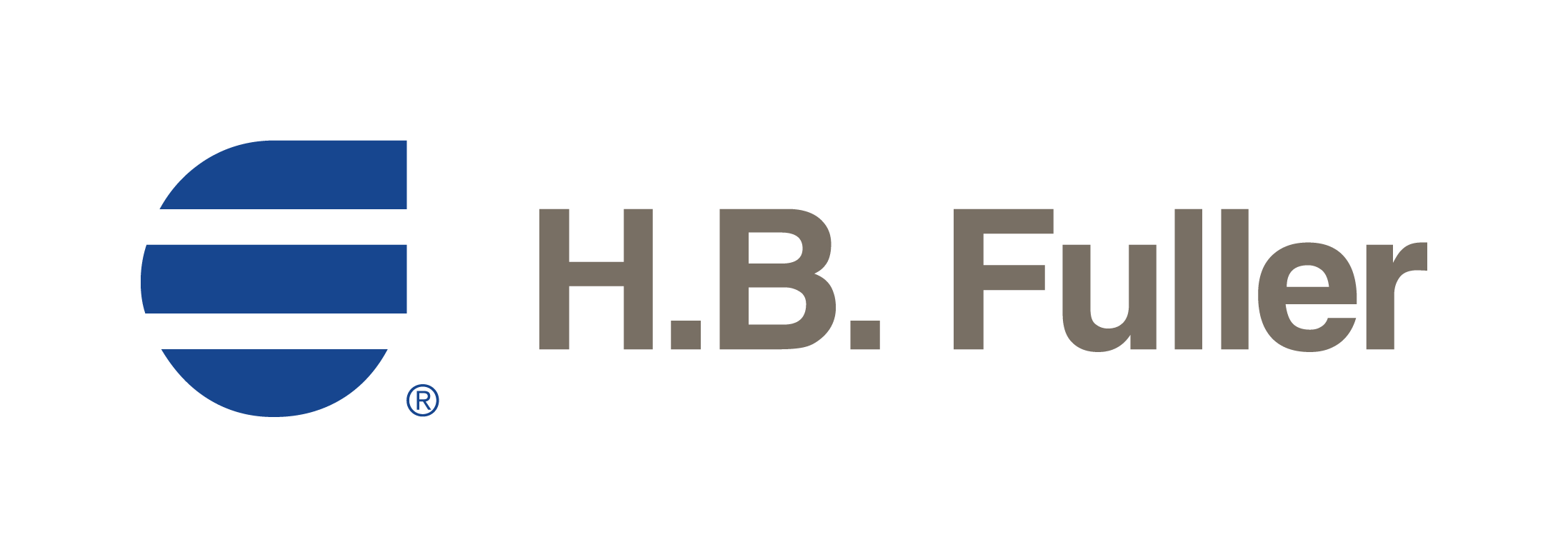
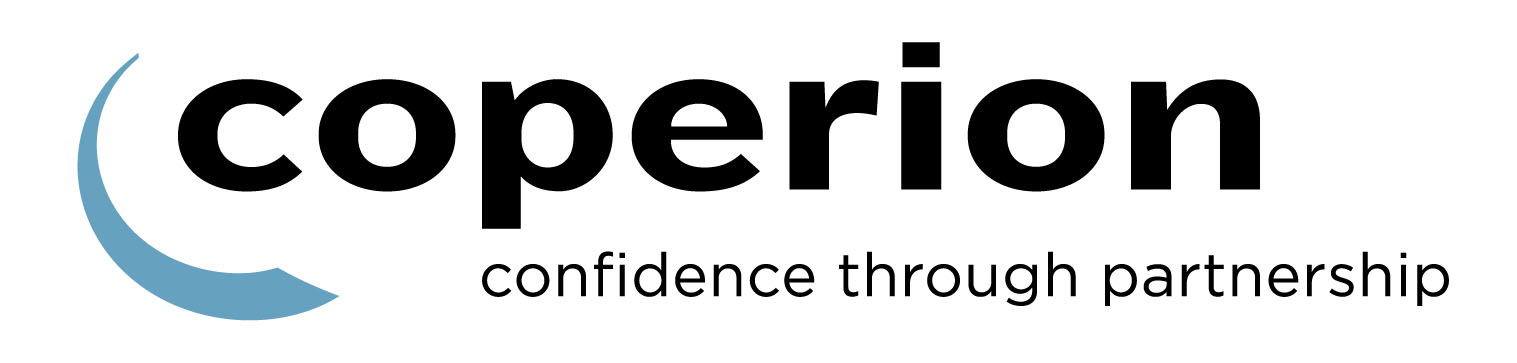